Penn A28 Series User manual

Application
These two-stage controls are designed to cover
a broad range of general purpose operating
temperature control applications in the
refrigeration, air conditioning, and heating fields.
Two SPDT switches permit independent control
circuits. Each switch may be wired for “open high”
or “close high” action, as required, providing
automatic changeover on heating-cooling or
similar applications. Models are available with
narrow differential on each switch. A jumper
across the “common” terminals is supplied as a
standard feature. Models are available with fixed
or adjustable interstage differential.
Important: A28 Series two-stage temperature
controls are intended to control equipment under
normal operating conditions. Where failure or
malfunction of an A28 temperature control could
lead to an abnormal operating condition that could
cause personal injury or damage to the equipment
or other property, other devices (limit or safety
controls) or systems (alarm or supervisory)
intended to warn of or protect against failure or
malfunction of an A28 temperature control must
be incorporated into and maintained as part of the
control system.
Operation
Figure 8 illustrates the operation of an A28 Series
control calibrated for cooling applications. On a
temperature increase to the dial setting, the circuit
between R and Y of the low stage switch (RYL)
closes.
Simultaneously, the circuit between R and B (RBL)
opens. On a further increase in temperature, the
high stage switch operates and closes RYHwhile
opening RBH. The reverse sequencing takes place
on a temperature fall.
Installation
Follow equipment manufacturer’s instructions if
provided. If instructions are not provided, proceed
as follows:
A28 Series Two-Stage Temperature Controls with NEMA 1 Enclosure
Installation Guide Part No. 996-318, Rev. E
Issue Date: May 2022
Risk of Electrical Shock.
Disconnect the power supply
before mounting and wiring to prevent possible
electrical shock. On multiple circuit units, more
than one circuit may have to be disconnected.
Mounting
Controls are normally mounted to a surface
through holes in the back of the case.
Important: On rough mounting surfaces use the
top two mounting holes only. When these controls
are mounted on an uneven surface using screws in
all four holes, the case can be twisted enough to
affect the control’s calibration and operation.
For closed tank applications without well assembly,
Part FTG13A-600R packing nut assembly may be
supplied. See Fig.4 for sequence of installation.
Place the parts over support tube section of the
element and place the bulb in the tank. Ensure the
tank is drained so the liquid level is below tank
opening.
Figure 1: Interior view showing high stage (left)
and low stage (right) switches
Tighten the 1/2 in. NPT adapter. Screw packing
nut into adapter with the retaining washers and
packing in place as shown.
Risk of Personal Injury.
In closed tank applications,
relieve any system pressure before loosening or
attempting to replace an existing bulb well.
To install models supplied with a bulb well, first
install the bulb well into the tank opening. Remove
bushing from the bulb well and slide the bushing
over capillary.
Place the bulb and bushing into the well. Push
bulb into position in bottom of the well. Tighten
set screw in end of the adapter to hold bulb in
position. See Fig. 5 for bulb well installation.
Figure 2: A28 control
Important: Do not dent or deform the sensing
bulb of this control. A dent or deformation will
change the calibration and cause the control to
cycle at a temperature lower than the dial setting.
When the bulb mounting clip is used to mount
the bulb near refrigerant tubing, be sure the sheet
metal screw does not pierce the tubing.
Wiring
Risk of Electrical Shock.
Disconnect the power supply
before mounting and wiring to prevent possible
electrical shock. On multiple circuit units, more
than one circuit may have to be disconnected.
Follow equipment manufacturer’s diagrams if
provided. Wire to conform to local, national, and
regional regulations. Wiring terminals of each
Pennswitch are color coded for convenience and
to simplify wiring. Red is the common terminal;
red to yellow circuit closes on temperature
increase, red to blue circuit opens on temperature
increase. Use copper conductors only.
Use terminal screws furnished (8-32 x 1/4 in.
binder head). Do not substitute screws of a
different size.
Figure 3: Style 1 swaged bulb with support tube
for clamp-on or closed tank applications
Figure 4: Part number FTG13A-600R packing nut
assembly. Use with Style 1 bulb with support tube
for direct immersion applications

www.penncontrols.com
® Johnson Controls and Penn are registered trademarks of Johnson Controls in the United States of America and/or other countries. All other trademarks used herein are the property of their respective owners.
© Copyright 2022 by Johnson Controls.
All rights reserved.
Figure 5: Bulb well for liquid immersion
applications where a temperature bulb may be
removed without draining tank
Figure 6: Snap-in plug removed and the knob in
line to assemble. Press the knob onto the slotted
shaft.
Adjustments
All models have fixed differential on
each Pennswitch. To adjust controls with
interstage differential, rotate adjusting wheel
counterclockwise to widen the differential
(increase spread). Use a small screwdriver and
insert into serrated wheel. (See Fig. 7)
Figure 7: Interstage differential can be increased
by rotating adjusting cam counterclockwise.
Knob or screwdriver slot adjustment of setpoint is
available.
Convertible adjustment models can be changed
from concealed screwdriver slot adjustment,
knob adjustment, or external screwdriver slot
adjustment. They are supplied with a snap-in plug
in the cover to provide concealed screwdriver slot
adjustment.
For exposed screwdriver slot adjustment remove
the snap-in plug. The convertible adjustment
models with remote bulb include a bulb mounting
clip.
Low stop is an integral part of the control and can
be adjusted by the sliding stop. To set low stop:
1. Remove cover from the control.
2. Set dial to temperature at which stop is
desired.
3. Loosen the stop screw, slide the screw to the
front of the temperature control against the
plastic step behind the dial and tighten the
screw. (See Fig. 10) Sometimes an exact stop
setting is not possible and the stop must be
set to the closest step corresponding to the
dial setting required.
4. Replace the cover.
Figure 8: Switch action of the two-stage control
for cooling applications. RBH, RYHindicates HI-
TEMP stage; RBL, RYL, indicates LO-TEMP stage.
“D” represents the differential between stages.
Figure 9: Typical wiring diagram of a refrigeration
compressor with single stage unloader. Two
compressor packages may be sequenced with
same circuit.
Checkout procedure
Before leaving the installation, observe at least
three complete operating cycles to be sure that all
components are functioning correctly.
Repairs and replacement
Field repairs must not be made. For a replacement
control, contact the nearest Johnson Controls
distributor.
Figure 10: The controls have a screw-type
adjustment stop. The stop screw must be loosened
and moved to the stop setting desired. Tighten
screw after setting is made.
A28AA, A28AB A28AJ
Volts, AC 120 208 240 277 120 208 240 277
Full load amp 16.0 9.2 8.0 –6.0 3.4 3.0 –
Locked rotor amp 96.0 55.2 48.0 –36.0 20.4 18.0 –
Non-inductive amp 16.0 9.2 8.0 7. 2 15.0 9.2 8.0 7.2
Pilot duty: 125 VA, 24 to 277 VAC
* Max connected load not to exceed 2000 VA.
Electrical ratings
APAC Single Point of Contact:
JOHNSON CONTROLS
C/O CONTROLS PRODUCT MANAGEMENT
NO. 32 CHANGJIANG RD NEW DISTRICT
WUXI JIANGSU PROVINCE 214028
CHINA
European Single Point of Contact:
JOHNSON CONTROLS
VOLTAWEG 20
6101 XK ECHT
THE NETHERLANDS
NA/SA Single Point of Contact:
JOHNSON CONTROLS
5757 N GREEN BAY AVE.
GLENDALE, WI 53209
USA
UK Single Point of Contact:
JOHNSON CONTROLS
TYCO PARK
GRIMSHAW LANE
MANCHESTER M40 2WL
UNITED KINGDOM
This manual suits for next models
3
Other Penn Control System manuals
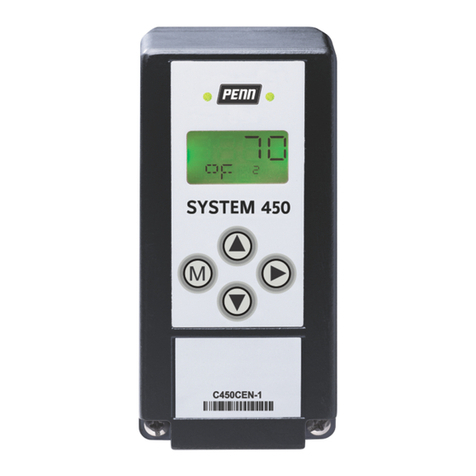
Penn
Penn System 450 Series User manual
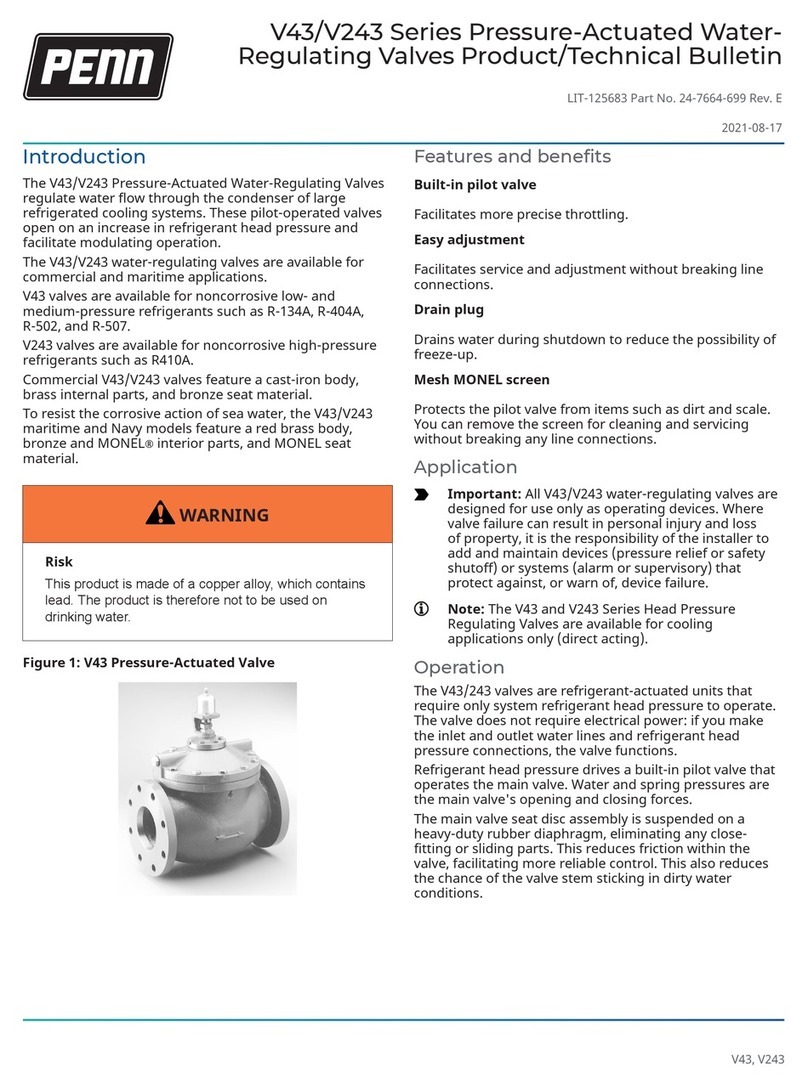
Penn
Penn V43 Series V243 Series Manual

Penn
Penn A421 Series User manual
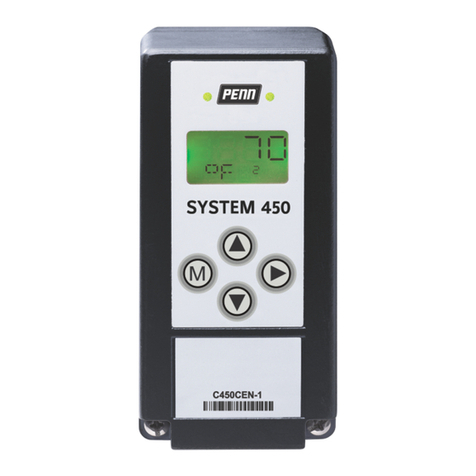
Penn
Penn System 450 Series Service manual
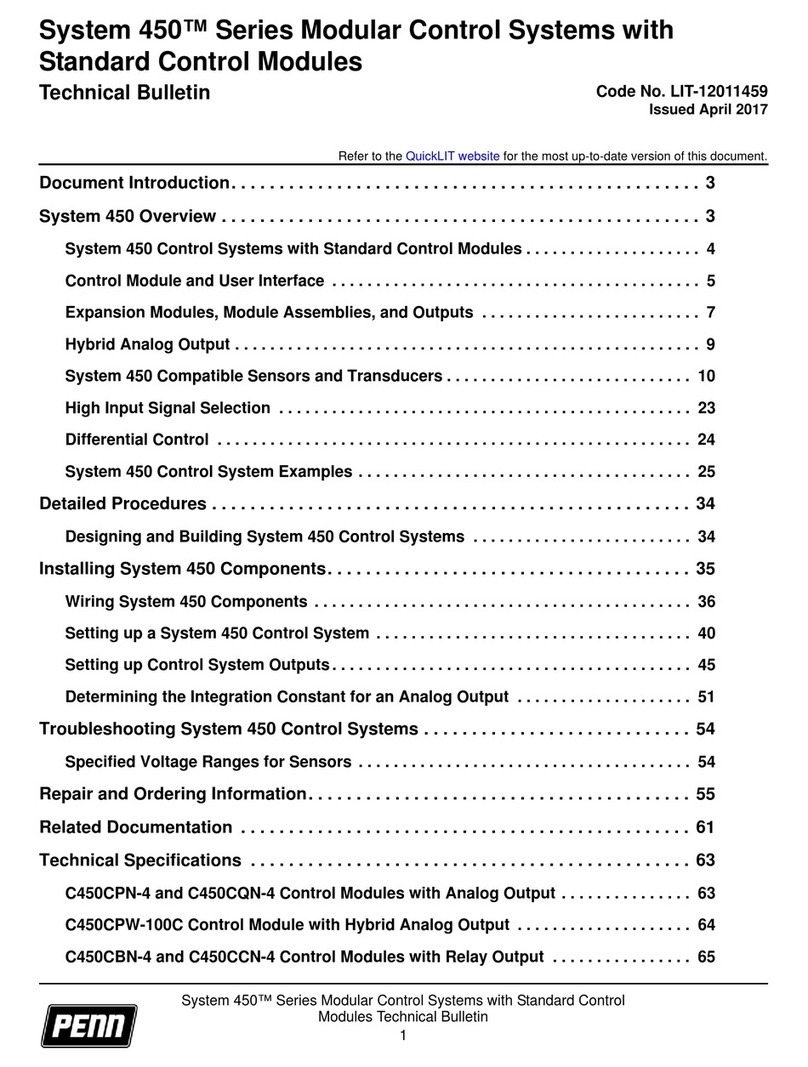
Penn
Penn System 450 Series Service manual
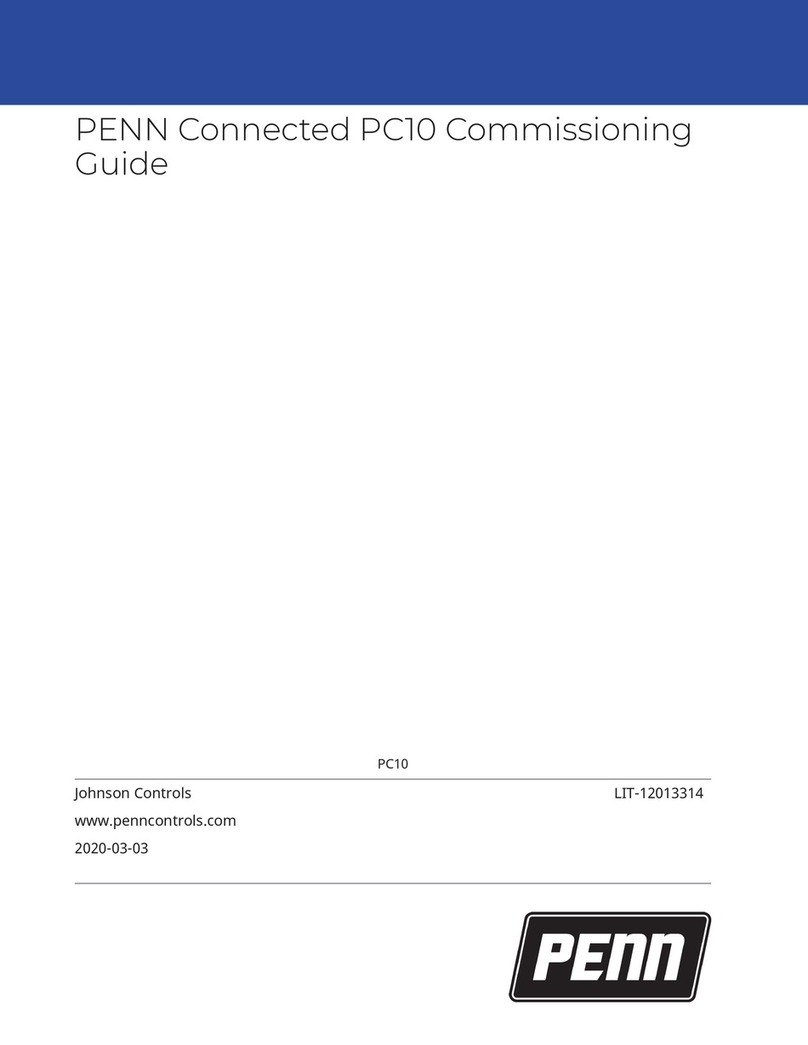
Penn
Penn Connected PC10 User manual

Penn
Penn P77 Series User manual
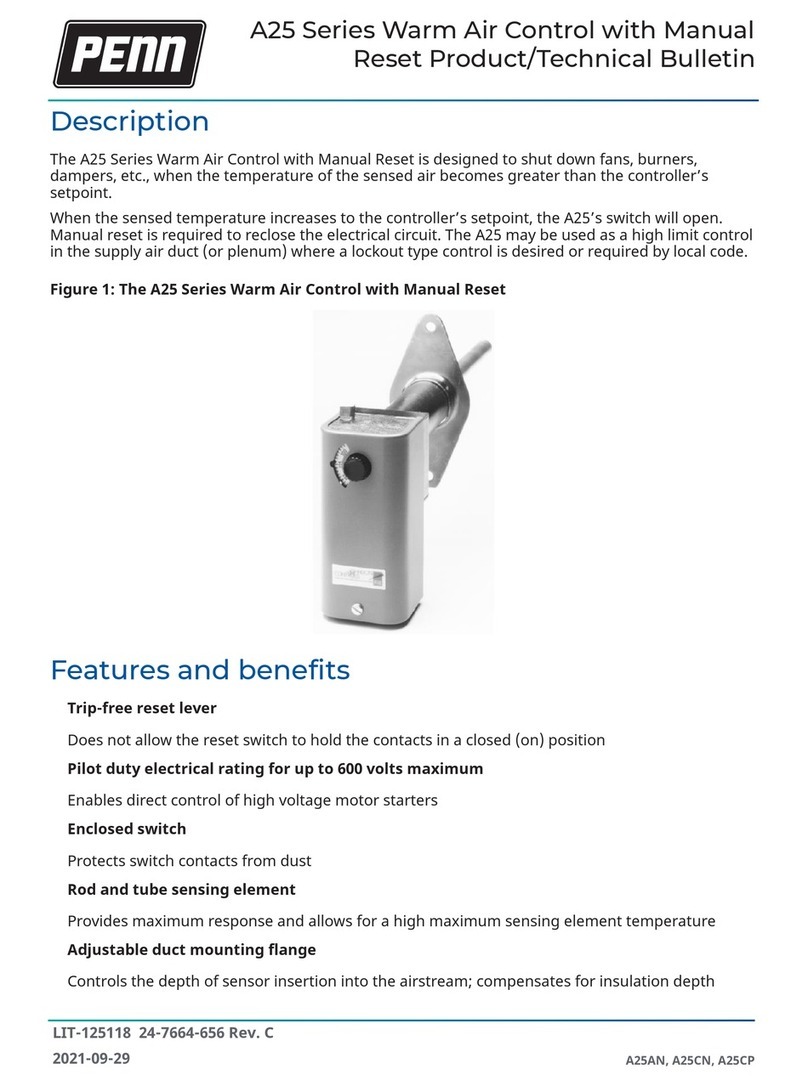
Penn
Penn A25 Series Service manual

Penn
Penn P78 Series User manual

Penn
Penn A421 Series User manual
Popular Control System manuals by other brands

VADDIO
VADDIO 999-8700-000 Installation and user guide
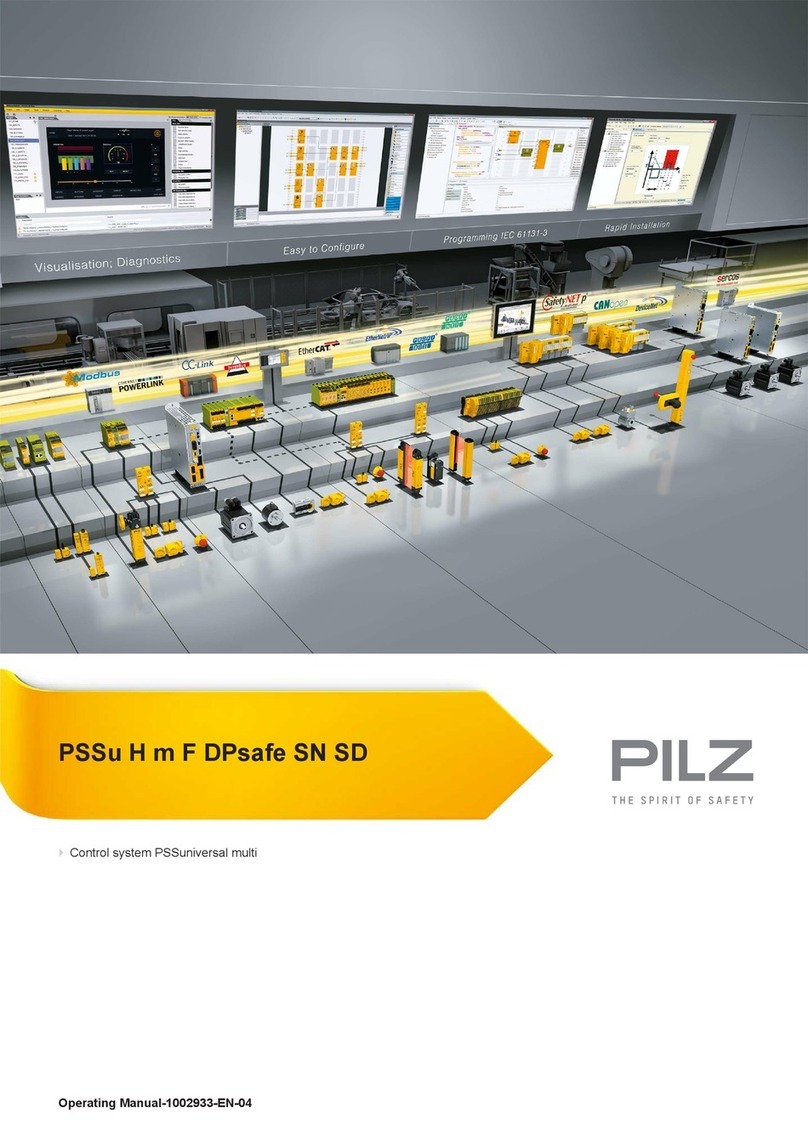
Pilz
Pilz PSSuniversal multi PSSu H m F DPsafe SN SD operating manual
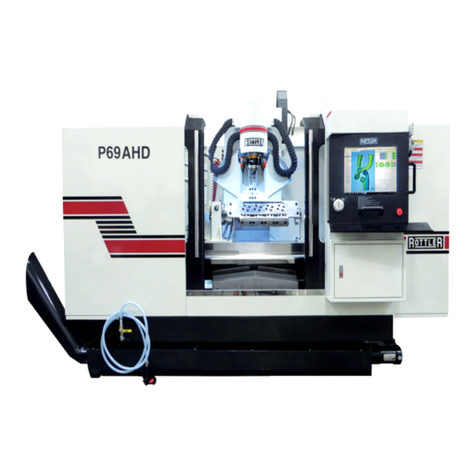
Rottler
Rottler P69AHD Operation and maintenance manual

iO HVAC Controls
iO HVAC Controls ZP3-HCMS Installation and operation instructions
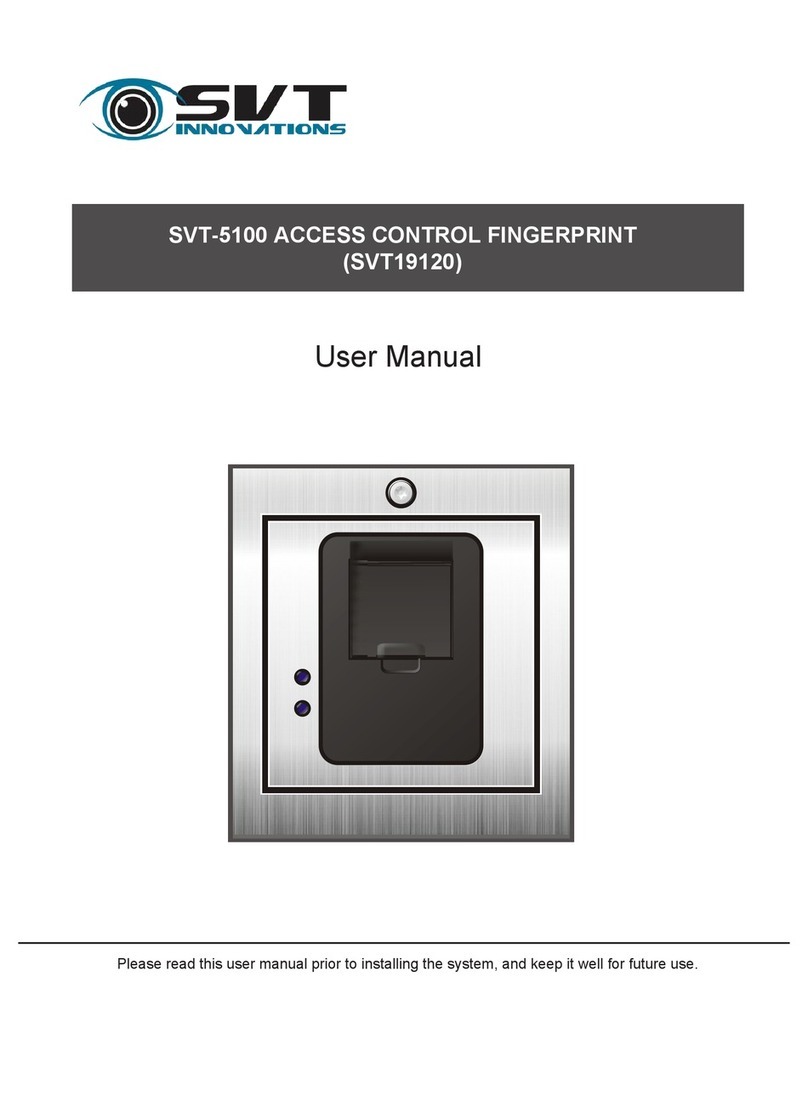
SVT
SVT 5100 user manual
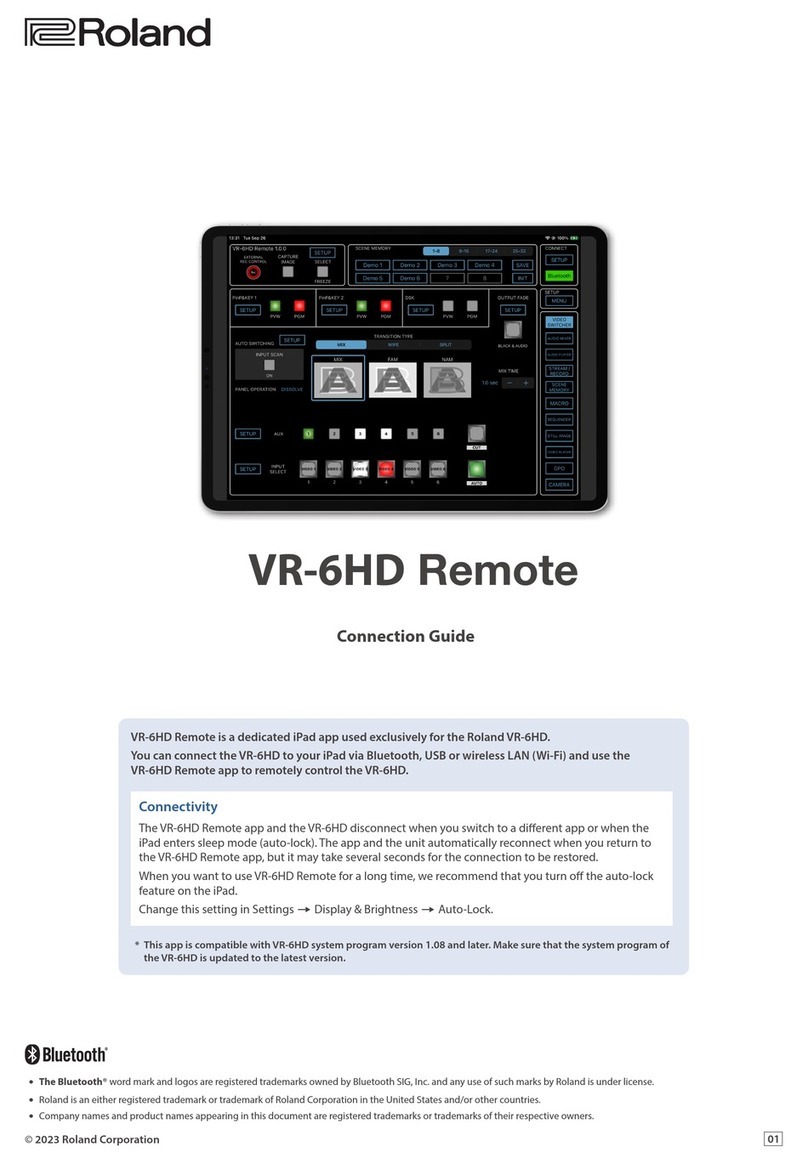
Roland
Roland VR-6HD Connection guide