Pepperl+Fuchs DA6-SSI/A-U User manual

DA6-SSI/A-U
SSI Display with analog output
FACTORY AUTOMATION
MANUAL

IX34510a_e.doc / Apr-11 Page 2 / 43
Safety Instructions
This manual is an essential part of the unit and contains important hints about
function, correct handling and commissioning. Non-observance can result in
damage to the unit or the machine or even in injury to persons using the
equipment!
The unit must only be installed, connected and activated by a qualified electrician
It is a must to observe all general and also all country-specific and application-
specific safety standards
When this unit is used with applications where failure or maloperation could cause
damage to a machine or hazard to the operating staff, it is indispensable to meet
effective precautions in order to avoid such consequences
Regarding installation, wiring, environmental conditions, screening of cables and
earthing, you must follow the general standards of industrial automation industry
- Errors and omissions excepted –
General instructions for cabling, screening and grounding can be found in the
SUPPORT section of our website http://www.pepperl-fuchs.com
Version: Description:
03b /af/hk//Feb 08 Range of PM z-eFraoc ptoors, iStiSonI and preselection mode
1 / 2 increase to [-199999, 999999];
load on the current output max. 300 Ohm
07a = 08a/kk/hk/Apr.09 Extensions: Linearization, Activation of serial transmission
09a/kk/hk/Feb.10 Extension from 25 to 32 bits
10a/kk/hk/June.10 Missing encoder alarm, remote start of serial string
DA6-SSI/A-U

IX34510a_e.doc / Apr-11 Page 3 / 43
Table of Contents
1. Terminal Assignment ..................................................................................................... 4
1.1. Power Supply................................................................................................................................5
1.2. Aux. Voltage Output .....................................................................................................................5
1.3. Control Inputs A, B and C .............................................................................................................5
1.4. Adjustable Analogue Output .......................................................................................................6
2. How to Operate the Front Keys...................................................................................... 8
2.1. Normal display state ....................................................................................................................8
2.2. Selection and Setting of Parameters...........................................................................................9
2.3. Teach operation..........................................................................................................................10
2.4. Set all parameters to “Default“ .................................................................................................10
2.5. Code Locking of the Keypad.......................................................................................................10
3. The Operator Menu.......................................................................................................11
3.1. Overview of Basic Parameters ...................................................................................................11
3.2. Overview of Operational Parameters.........................................................................................12
4. Setup Procedure............................................................................................................13
4.1. Basic Parameters........................................................................................................................13
4.2. Operational Parameters..............................................................................................................15
4.3. Additional Parameters for the Analogue Output ......................................................................18
5. Hints for Application .....................................................................................................26
5.1. Master and Slave Operation ......................................................................................................26
5.2. Evaluation of Encoder Bits .........................................................................................................27
5.3. Scaling of the Display.................................................................................................................28
5.4. Basic Modes of Operation..........................................................................................................29
5.5. Testing Functions........................................................................................................................33
5.6. Error Messages...........................................................................................................................33
6. Special Functions..........................................................................................................34
6.1. Linearization ...............................................................................................................................34
6.2. Manual Input or „Teaching“ of the Interpolation Points ...........................................................36
7. Technical Appendix.......................................................................................................38
7.1. Dimensions .................................................................................................................................38
7.2. Technical Specifications.............................................................................................................39
7.3. Parameter-List ............................................................................................................................40
7.4. Commissioning Form ..................................................................................................................42
DA6-SSI/A-U

IX34510a_e.doc / Apr-11 Page 4 / 43
1. Terminal Assignment
Display with analogue output
GND
17-30 VCD IN
1 2 3 4 5 6 7 8 9 10
Input A
Input B
GND
+24 VDC OUT
GND analogue
+/- 10 V analogue
0/4-20 mA analogue
PE
GND
230VAC
115 VAC
0 VAC
CLK
CLK
DAT
DAT
1 2 3 4
Input C (Reset)
DA6-SSI/A-U

IX34510a_e.doc / Apr-11 Page 5 / 43
1.1. Power Supply
The unit accepts DC supply from 17 V to 30 V when using terminals 1 and 2. The consumption
depends on the level of the supply voltage
(typical 130mA at 30V or 190mA at 17V, plus current taken from aux. output).
For AC supply the terminals 0 VAC, 115 VAC or 230 VAC can be used.
The total AC power is 7.5 VA.
The diagrams below show a dotted line for grounding to PE.
This connection is not really necessary, neither for safety nor for EMC. However, for some
applications, it may be desirable to ground the common potential of all signal lines.
When using this earthing option, please observe:
All terminals and potentials marked “GND“ will be earthed.
Please avoid multiple earthing, i.e. when you use a DC power supply where
the Minus is already connected to earth etc.
1.2. Aux. Voltage Output
Terminal 7 provides an auxiliary output of 24 VDC / 120 mA max. for supply of sensors and
encoders.
1.3. Control Inputs A, B and C
With models , input A is used to activate a serial transmission (rising edge, see 4.5.2).
Input B is not in use.
Input C operates as a Set / Reset input (static function, active "HIGH", see 5.3).
In the basic setup menu, the inputs can be configured to PNP (signal must switch to +) or to
NPN (signal must switch to -). This configuration is valid for all three inputs at a time.
The factory setting is always PNP.
Where NPN setting is used, please observe:
Open NPN inputs will always represent a logical HIGH state
Consequently, Input C has to be connected to GND externally to allow normal
operation. If unconnected, the unit would be kept in a continuous Reset state.
With models IX 348, also Input A must be tied to GND, and opening this connection will
generate a rising edge to start a serial transmission
Where your use 2-wire NAMUR type sensors, please select NPN, connect the negative
wire of the sensor to GND and the positive wire to the corresponding input.
DA6-SSI/A-U

IX34510a_e.doc / Apr-11 Page 6 / 43
Typical input circuit of control input
PNP
4,7k
GND GND
+24V int.
Input
4,7k
GND
Input
+24V int.
NPN
The minimum pulse duration on the Reset input (C) must be 5 msec.
1.4. Adjustable Analogue Output
A voltage output is available, operating in a range of 0 ... +10 V or –10 V ... +10 V according to
setting. At the same time, a current output 0/4 – 20 mA is available. Both outputs refer to the
GND potential and the polarity changes with the sign in the display. The outputs are
proportional to the display value and provide a 14 bits resolution.
The maximum current on the voltage output is 2 mA, and the load on the current output can
vary between 0 and max. 300 ohms.
The response time of the analogue output to changes of the encoder position is approx. 7 msec.
DA6-SSI/A-U

IX34510a_e.doc / Apr-11 Page 8 / 43
2. How to Operate the Front Keys
For setup and other operations the unit uses three front keys which subsequently will be
denominated as follows:
«
™
ENTER
(Input)
SET
(Setting)
Cmd
(Command)
The functions of the keys are depending on the actual operating state of the unit.
The following three operating states apply:
Normal display state
Setup state
a.) Basic setup
b.) Operational parameter setup
Teach operation
2.1. Normal display state
You can only change over to other operation states while the unit is in the
normal display state.
Change over to Key operation
Basic setup Keep ENTER and SET down simultaneously for 3 seconds
Operational
parameter setup
Keep ENTER down for 3 seconds.
Teach operation Keep Cmd down for 3 seconds
The Cmd key is only used to execute the Teach procedure with linearization. For more details
please refer to sections 6.1 and 6.2.
DA6-SSI/A-U

IX34510a_e.doc / Apr-11 Page 9 / 43
2.2. Selection and Setting of Parameters
2.2.1. How to select a parameter
The ENTER key will scroll through the menu. The SET key allows to select the corresponding
item and to change the setting or the numeric value. After this, the selection can be stored by
ENTER again, which automatically changes over to the next menu item.
2.2.2. How to change parameter settings
With numerical entries, at first the lowest digit will blink. When keeping the SET key
continuously down, the highlighted digit will scroll in a continuous loop from 0 … 9 , 0 … 9.
After releasing the SET key, the actual value will remain and the next digit will be highlighted
(blink). This procedure allows setting of all digits to the desired values. After the most
significant digit has been set, the low order digit will blink again and you can do corrections if
necessary.
With signed parameters, the high order digit will scroll from “0” to "9" (positive) followed by
“-“ and "-1" (negative)
2.2.3. How to store settings
To store the actual setting, press the ENTER key, which will also automatically scroll forward
the menu.
At any time the unit changes from programming mode to normal display operation, when you
keep the ENTER key down again for at least 3 seconds.
2.2.4. Time-out function
A “time-out” function will automatically conclude every menu level, when for a break period of
10 seconds no key has been touched. In this case, any changes which have not been confirmed
by ENTER yet would remain unconsidered.
DA6-SSI/A-U

IX34510a_e.doc / Apr-11 Page 10 / 43
2.3. Teach operation
The Time-out function will be switched off during all Teach operations
Key Function
«
ENTER will conclude or abort any Teach operation in progress
™
SET function is fully similar to normal set-up operation
Cmd will store the display value to the register and will change over to the
next interpolation point.
For details of the Teach procedure see section 6.2.
2.4. Set all parameters to “Default“
At any time you can return all settings to the factory default values.
The factory default settings are shown in the parameter listings in section 6.
When you decide to set all parameters to „default“, please be aware that all
previous settings will be lost and you will need to do the whole set-up
procedure once more
To execute the „Default“ setting function:
Power the unit down.
Press the ENTER key.
Power the unit up again while the ENTER key is kept down
2.5. Code Locking of the Keypad
When the code locking of the keypad has been switched on, any key access first results in
display of
To access the menu you must press the key sequence
«
™
«
™
«
within 10 seconds, otherwise the unit will automatically return to the normal display mode.
DA6-SSI/A-U

IX34510a_e.doc / Apr-11 Page 11 / 43
3. The Operator Menu
The menu provides one section with “Basic Parameters” and another section with “Operational
Parameters”. On the display you will only find those parameters which have been enabled by
the basic settings. E.g. when the Linearisation Functions have been disabled in the basic set-
up, the associated linearization parameters will also not appear in the parameter menu.
All parameters, as good as possible, are designated by text fragments. Even though the
possibilities of forming texts are very limited with a 7-segment display, this method has proved
to be most suitable for simplification of the programming procedure.
The subsequent table shows the general structure of the whole menu only.
Detailed descriptions of all parameters will follow in section 4.
3.1. Overview of Basic Parameters
DA6-SSI/A-U
SSI_Mode
SSI_Bits
SSI_Format
SSI_Baud Rate
SSI_Test
Characteristics
Brightness
Code Locking
Linearization Mode
Analogue Characteristics
Analogue Offset
Analogue Gain
DA6-SSI/A-U

IX34510a_e.doc / Apr-11 Page 12 / 43
3.2. Overview of Operational Parameters
DA6-SSI/A-U
Preselection 2
M-Factor
D-Factor
P-Factor
Decimal point
Hi_Bit (MSB)
Lo_Bit (LSB)
Direction
Error
Error_Polarity
Round Loop
Time
Reset
Zero Position
Analogue Begin
Analogue End
Ser_Value
P01_X *)
P01_Y*)
Æ Æ
P16_X *)
P16_Y *)
*) appears only when Linearization has been enabled in the Basic Menu
DA6-SSI/A-U

IX34510a_e.doc / Apr-11 Page 13 / 43
4. Setup Procedure
For better understanding the following sections 4.1 and 4.2 explain settings for the display only.
Model-specific settings for Analogue Output, Preselections and Serial Link will be explained
separately, later.
4.1. Basic Parameters
The subsequent settings are of unique nature and must only be made upon the very first setup.
The basic setup selects the desired operation mode of the unit, the input characteristics
PNP/NPN and the desired brightness of the LED display.
Menu Setting Range Default
SSI-Mode
Setting of Master Mode or Slave Mode
For details see section 5.1
SSI-Bits
Bit length of the SSI string
For more details see section 5.2
.....
SSI-Format:
Setting of the SSI code (Binary or Gray)
SSI-Baud Rate 0.1 ... 1000.9
kHz
100.0
kHz
SSI Test
SSI Self test functions (see 5.5.)
etc.
Characteristics *)
Switching characteristics of the Reset input
NPN: switch to "-" *)
PNP: switch to "+"
Brightness 100%
Brightness of the 7-segment LED display
20%, 40%, 60%
80% and 100%
*) Please observe hints given in chapter 1.3
DA6-SSI/A-U

IX34510a_e.doc / Apr-11 Page 14 / 43
Menu Setting Range Default
Code Locking
Interlock of keypad access (see 2.5)
no: Keypad accessible at any time
All: Keypad interlock for all functions
P-Free: Keypad interlock except for Preselection
Settings Pres 1 und Pres 2 (model IX 347)
Linearization Mode
For details please see 6.1 und 6.2.
no: Linearization is switched OFF *)
1-qua: Linearization settings for the positive range
only (negative values will appear as a mirror).
4-qua: Linearization over the full numeric range
*) The menu will not display any further linearization parameters
DA6-SSI/A-U

IX34510a_e.doc / Apr-11 Page 15 / 43
4.2. Operational Parameters
Menu Setting Range Default
M-Factor *):
Multiplying factor for the SSI value
(after consideration of possible bit blanking)
-9.999 … 9.999 1.000
D-Factor *):
Dividing factor for the SSI value
(after consideration of possible bit blanking)
0.001 … 9.999 1.000
P-Factor *):
This signed value will be added to the SSI result
(after consideration of possible bit blanking)
-199999
…
999999
0
Decimal Point
Setting according to the decimal formats shown in
the display
000000
00000.0
...
0.00000
00000.0
Display:
Display mode of the unit
norm: regular scaling of the display
359.59: Angular display format 359° 59' with use of
the Round Loop Function
norm
359.59
norm
Hi Bit **): 1 … 32 25
Bit Blanking Function: Defines the highest bit for
evaluation. To evaluate all encoder bits this
parameter has to be set to the total number of bits
according to setting
Lo Bit **): 1 … 31 1
Bit Blanking Function: Defines the lowest bit for
evaluation. To evaluate all encoder bits this
parameter has to be set to "01"
*) Scaling details are explained under 5.3
**) For more details about Bit Blanking see 5.2
DA6-SSI/A-U

IX34510a_e.doc / Apr-11 Page 16 / 43
Menu Setting Range Default
Direction
Parameter to negate the SSI value, resulting in
reversal of the direction of the encoder count.
riGht: ascending values with forward motion
LEFt:: decreasing values with forward motion
riGht
LEFt
riGht
Error: (please refer to 5.6)
Defines the control of presence of an encoder and
the location of the Error Bit in case of error.
00: No error bit available
Control of presence of an encoder is off
01: No error bit available
Control of presence of an encoder is on
>01: Location of the error bit
Control of presence of an encoder is on
0 ... 32 0
Error-Polarity *):
Defines the polarity of the Error Bit in case of error.
0: Error Bit is Low in case of error
1: Error bit is High in case of error
0
1
0
When an error occurs, „Err-b“ appears on the display.
The same function can also be used to monitor the Power Failure Bit of an encoder
(mostly called „PFB“).
Round Loop
Defines the number of encoder steps per revolution
with use of the Round Loop Function (see 5.4.2).
0: Normal display of the encoder data, no
Round Loop Function
>0: Number of steps per Round Loop Cycle
0 ... 999999 0
Time
Sets the update cycle of the display (and of the
analogue output or the switching outputs where
applicable). The fastest possible update time is
3 msec. respectively one telegram length including 4
pause clocks. With Slave operation the next update
will occur when the unit synchronizes again to the
Master pause following to the expiration of the
update time.
0.000 ... 1.009
sec
0.01 sec
DA6-SSI/A-U

IX34510a_e.doc / Apr-11 Page 17 / 43
Menu Setting Range Default
Reset
A Reset command is available to store the actual SSI
position to register „Zero Position“. As a result, the
display value will become zero at the actual encoder
position, and all further operation will refer to this
new datum point. The zero position remains
memorized also after power-down.
no: Reset function disabled
Front: Reset function by the front SET key
E_tErn: Reset function by the remote Reset input
FR u E: Reset via key and remote input
Zero Position: *)
Defines the zero position of the display. When you
set this parameter to e.g. "1024", the unit will
display zero when the encoder position is 1024.
Zero Position can be set directly via keypad or by
means of an external Reset command.
-199999
...
999999
0
P01_X **) Linearization Point 1_X
X value of the first interpolation point.
-199999
... 999999
999999
P01_Y Linearization Point 1_Y
Y value of the first interpolation point.
-199999
... 999999
999999
…
P16_X Linearization Point 16_X
X value of the 16. interpolation point.
-199999
... 999999
999999
P16_Y Linearization Point 16_Y
Y value of the 16. interpolation point.
-199999
... 999999
999999
*) Please observe that Parameter P_Fac will cause an additional displacement of the zero position
**) Parameters P01_X to P16_Y appear only when the linearization has been enabled in the basic menu
DA6-SSI/A-U

IX34510a_e.doc / Apr-11 Page 18 / 43
4.3. Additional Parameters for the Analogue Output
The following additional settings for the analogue output appear in the Basic Menu:
Menu Setting Range Default
Analogue Characteristics
You can set the following output options:
+/- 10 V (bipolar),
0 - 10 V (positive only),
4 - 20 mA
0 - 20 mA.
With setting +/-10 Volts the polarity of the output
voltage will follow the sign in the display
Analogue Offset:
Set this parameter to 0 when you expect your
analogue signal to start with 0 V (or 0 mA / 4 mA
respectively). Where another zero definition is
desired it can be set by this parameter. Setting of
e.g. 5.000 will already produce 5 volts with the
output in zero state.
-9,999..+9,999 0,000
Analogue Gain:
Parameter to set the analogue output swing. Setting
10.00 will allow full swing of 10 V or 20 mA, setting
8.00 will reduce the swing to 8 V or 16 mA.
00,00..99,99 10,00
The following Operational Parameters provide scaling of the analogue output:
Menu Setting Range Default
Analogue-Begin
Start value of the analogue conversion range
-199999...999999 0
Analogue-End
End value of the analogue conversion range
-199999...999999 100000
By means of these two parameters any window of the whole display range can be mapped onto
the analogue output.
DA6-SSI/A-U

IX34510a_e.doc / Apr-11 Page 19 / 43
The subsequent example shows how to convert the display range from 1400 to 2000 into an
analogue signal of 2 - 10 volts.
2
4
6
8
10
1000 2000 3000 4000 5000
SSI Display Value
Volts Analogue Output
A-ChAr = 0 - 10 V AnAbEG = 1400
OFFSEt = 2.000 AnAEnd = 2000
GAin = 8.00
All settings refer to the scaled values shown in the display of the unit,
and not to the original SSI encoder data
DA6-SSI/A-U

IX34510a_e.doc / Apr-11 Page 26 / 43
5. Hints for Application
5.1. Master and Slave Operation
Set register “Mode” to position “Master” when the unit should generate the clock signal for
the encoder. In this case the clock terminals (CLK) are configured as clock outputs.
CLK
7 (+24V out)
6 (GND)
Clock-
Clock+
(+24V)
GND
Data-
Data+
(optional)
SSI Encoder SSI Indicator
SSI Indicator with Master Operation
Screen
CLK
DAT
DAT
When your encoder receives already its clock from another device and the unit should only
“listen” to the communication, then set register “Mode” to “Slave”. In this case, both clock
terminals (CLK) are configured as inputs.
6 (GND)
SSI Indicator with Slave Operation
+-
Clock+
Clock-
Data+
Data-
SSI Encoder
Remote Master
Clock-
Clock+
Data-
Data+
CLK
DAT
CLK
DAT
SSI Indicator
Screen
Set registers “Bits”, “Format” and “Baud” according to the encoder you use.
You are free to set any baud rate in a range from 0.1 kHz to 1000.0 kHz. For technical reasons
however, in the upper frequency range, the unit itself in master mode can only generate one of
the following Baud rates accurately:
1000,0 kHz 888,0 kHz 800,0 kHz 727,0 kHz 666,0 kHz
615,0 kHz 571,0 kHz 533,0 kHz 500,0 kHz 470,0 kHz
444,0 kHz 421,0 kHz 400,0 kHz 380,0 kHz 363,0 kHz
347,0 kHz 333,0 kHz 320,0 kHz 307,0 kHz 296,0 kHz
285,0 kHz 275,0 kHz 266,0 kHz 258,0 kHz 250,0 kHz
DA6-SSI/A-U

IX34510a_e.doc / Apr-11 Page 27 / 43
With Master operation, therefore other settings will result in generation of the next upper or
lower value according to above list. With all settings <250.0 kHz the error between set rate and
generated rate becomes negligible.
It is mandatory to set the Baud rate also with Slave operation. In this case, however, the
setting serves only to determine the pause time for correct synchronization (pause is detected
after 4 clock cycles). The unit automatically synchronizes with every remote clock signal within
the specified Baud rate range.
5.2. Evaluation of Encoder Bits
This chapter explains the correlation between the Basic Parameter „BitS“ and the Operational
Parameters „Hi bit“ and „Lo bit“. The example below uses an encoder with 16 bits.
Unused Bits may be blanked out according to individual need
Whenever the number of bits (clock cycles) requested from the SSI Master is higher
than the real number of encoder bits, all excessive Bits must be blanked by
corresponding setting of parameters „Hi_bit“ and „Lo_bit“.
Basic Settings:
In general, parameter „BitS“ will always be set according to the real resolution of the encoder
(i.e. "BitS" = 16 with a 16 bit encoder). In this normal case the SSI telegram will not contain any
excessive bits.
With some applications (e.g. with Slave operation) it may however happen that the Master
transmits more clock cycles than the number of encoder bits (e.g. 21 clocks with a 16 bit
encoder). In such a case the master would always request 21 bits from the encoder, where the
encoder itself responds with 16 usable bits only, followed by 5 waste bits. These 5 excessive
bits must be blanked.
All standard SSI telegrams start with the most significant bit (MSB) and close with the least
significant bit (LSB). Unusable waste bits (X) will follow at the tail end. To blank these bits out,
in our example we would have to set „Hi bit“ to 21 and „Lo bit“ to 6 for proper evaluation of the
encoder information.
Hi Bit Î
Lo Bit Î
Requested
Bits (Clocks)
21
20
19
18
17
16
15
14
13
12
11
10
9
8
7
6
5
4
3
2
1
Usable Bits
(encoder) 16
15
14
13
12
11
10
9
8
7
6
5
4
3
2
1
X
X
X
X
X
DA6-SSI/A-U
Table of contents
Other Pepperl+Fuchs Monitor manuals
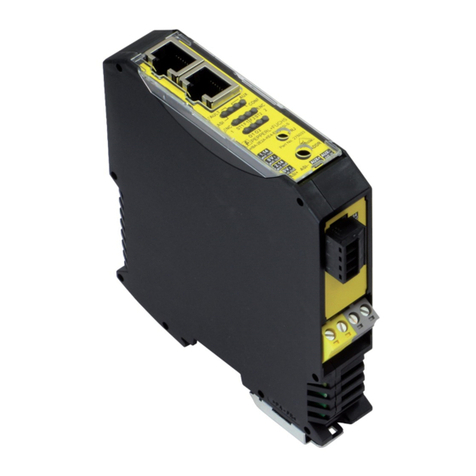
Pepperl+Fuchs
Pepperl+Fuchs VBA-2E2A-KE4-ENC/SSI-S User manual
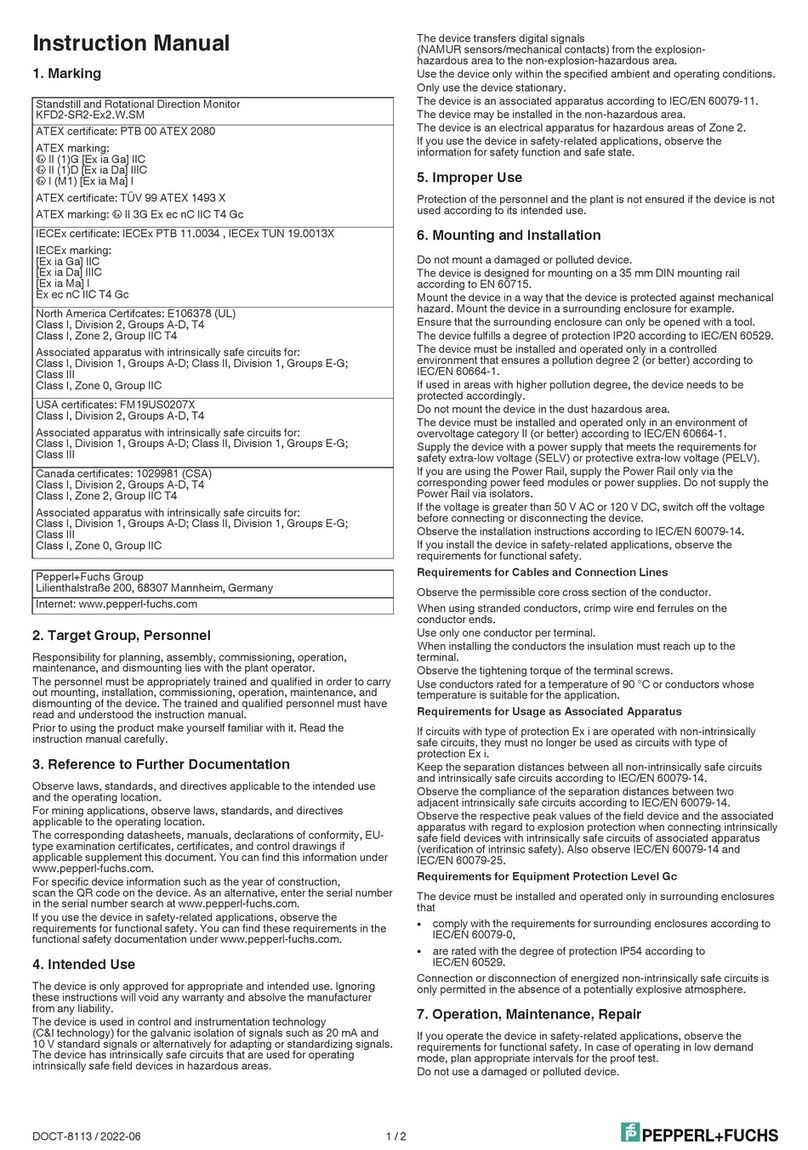
Pepperl+Fuchs
Pepperl+Fuchs KFD2-SR2-Ex2.W.SM User manual
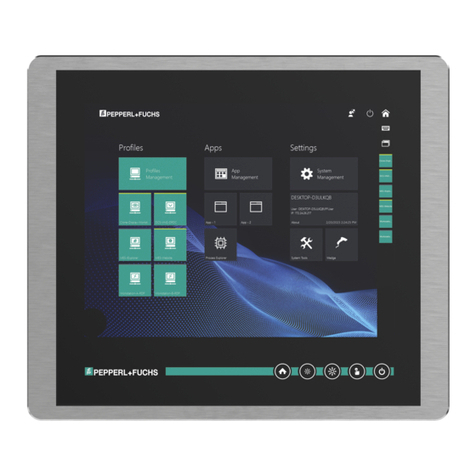
Pepperl+Fuchs
Pepperl+Fuchs DPU1100-J1 Series User manual
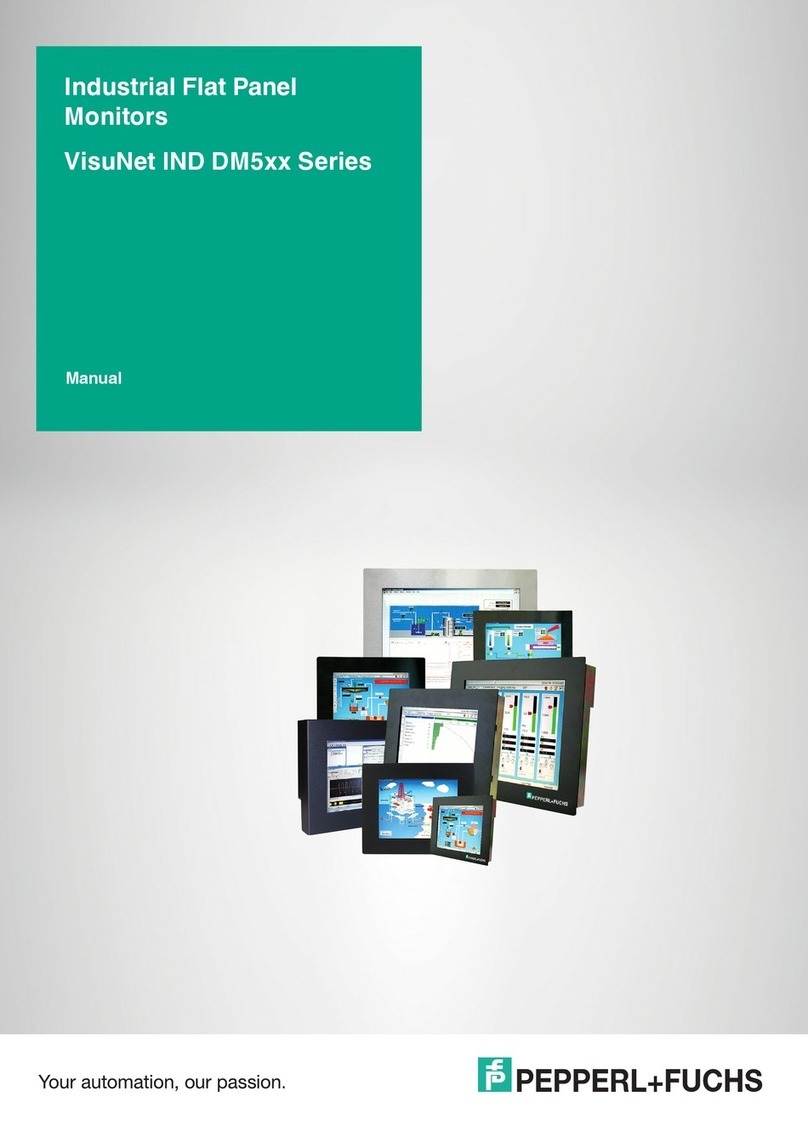
Pepperl+Fuchs
Pepperl+Fuchs VisuNet IND DM5 Series User manual
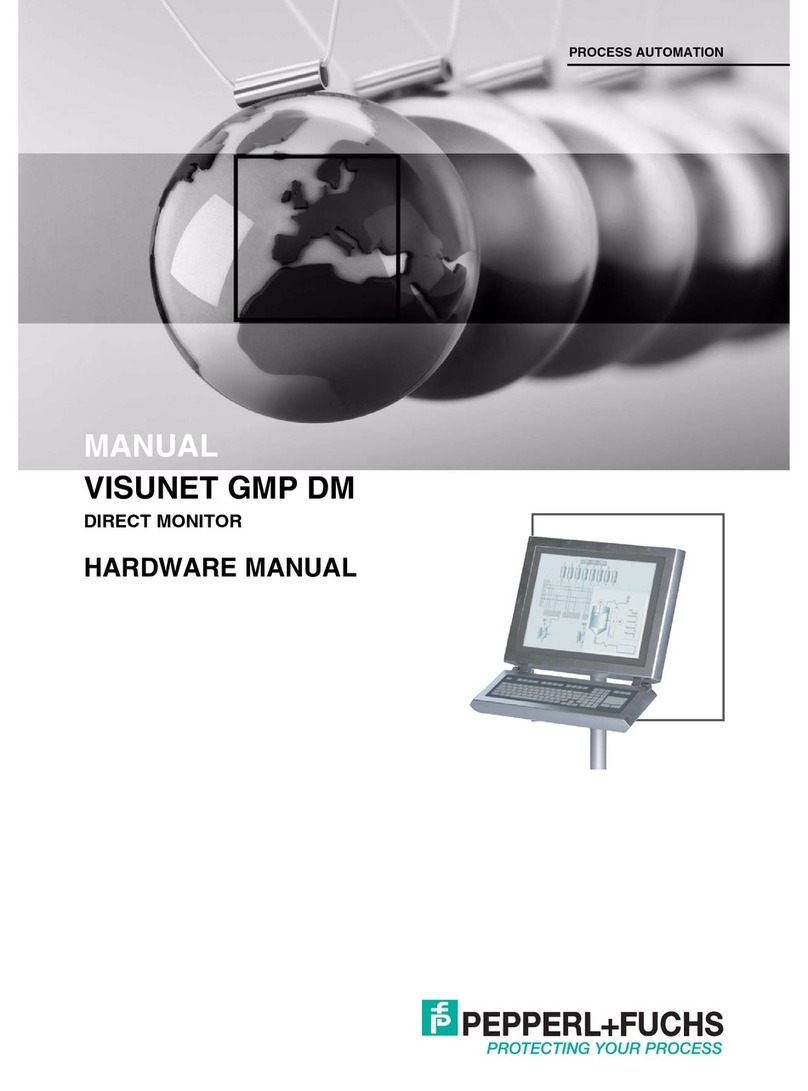
Pepperl+Fuchs
Pepperl+Fuchs VISUNET GMP DM User manual

Pepperl+Fuchs
Pepperl+Fuchs VisuNet DPU2100 Series User manual
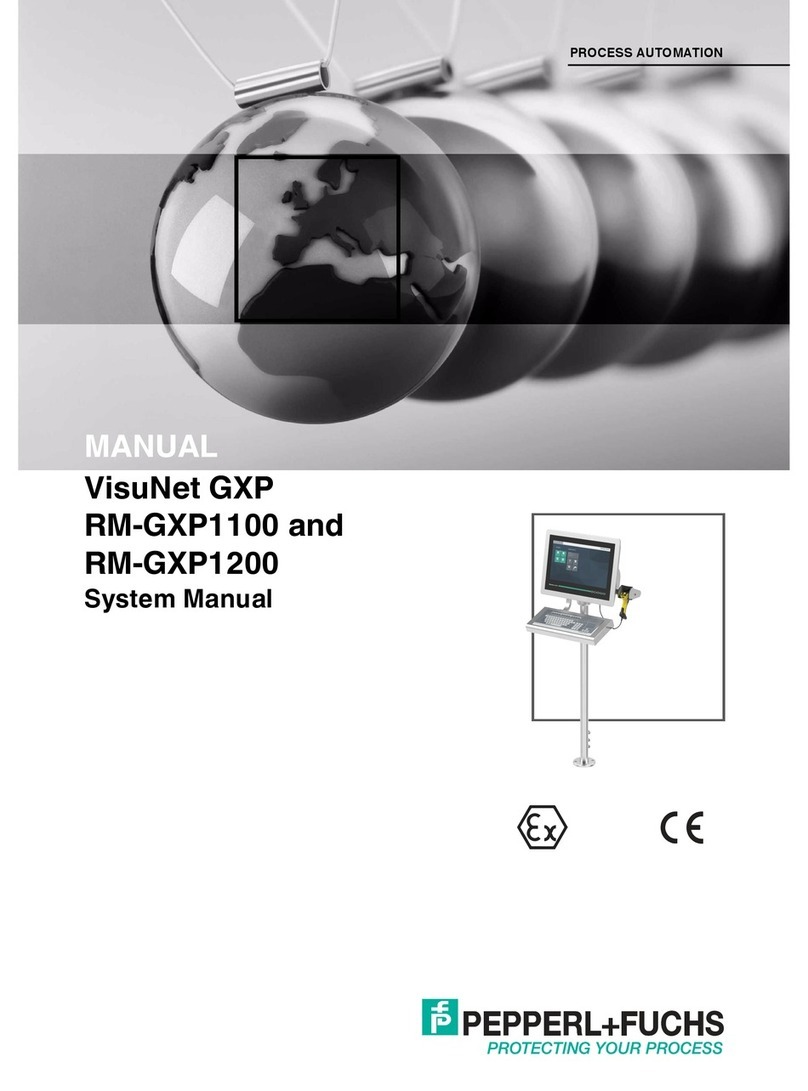
Pepperl+Fuchs
Pepperl+Fuchs VisuNet GXP Series User guide
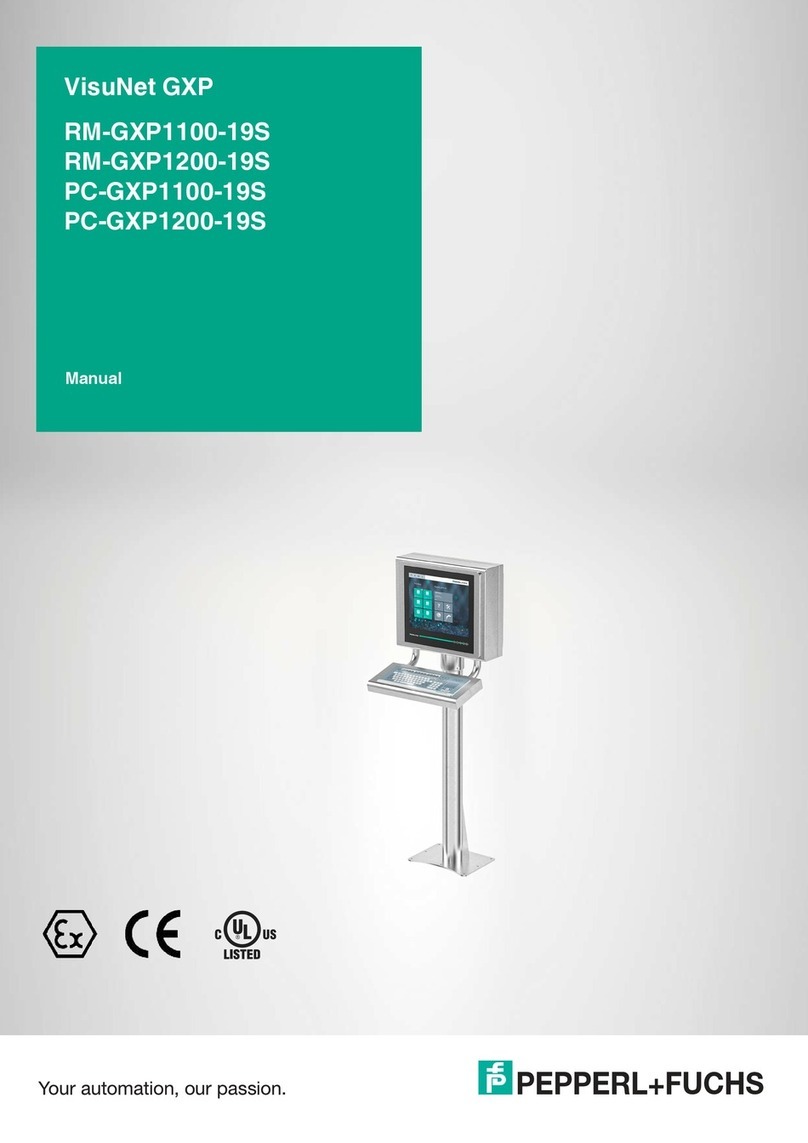
Pepperl+Fuchs
Pepperl+Fuchs VisuNet GXP Series User manual
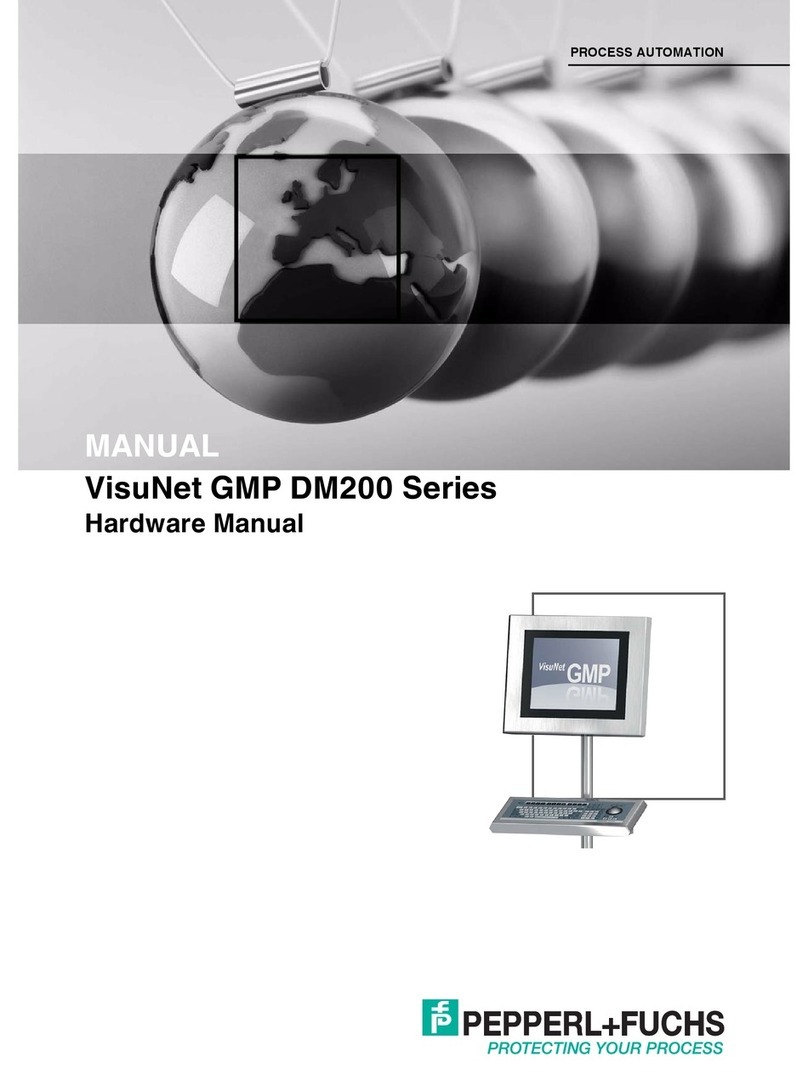
Pepperl+Fuchs
Pepperl+Fuchs VisuNet GMP DM200 Series User manual
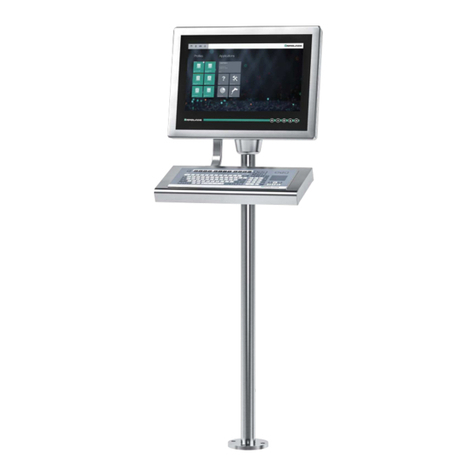
Pepperl+Fuchs
Pepperl+Fuchs VisuNet GXP RM-GXP1100-22F User manual