Physik Instrumente E-625.CR User manual

Physik Instrumente (PI) GmbH & Co. KG, Auf der Roemerstrasse 1, 76228 Karlsruhe, Germany
Phone +49 721 4846-0, Fax +49 721 4846-1019, Email info@pi.ws, www.pi.ws
PZ166E
E
-625 Piezo Servo Controller
User Manual
Version: 2.0.0
Date: 15.09.2021
This doc
ument describes the following products:
E-625.CR
Piezo servo controller, single channel, for
capacitive sensors
E-625.C0
Piezo servo controller, single channel, for
capacitive sensors, only analog control

The following company names and brands are registered trademarks of Physik Instrumente (PI) GmbH & Co.
KG:
PI®, NanoCube®, PICMA®, PILine®, NEXLINE®, PiezoWalk®, NEXACT®, Picoactuator®, PInano®, PIMag®,
Q-Motion®
The patents held by PI are found in our patent list: https://www.physikinstrumente.com/en/about-pi/patents
© 2021 Physik Instrumente (PI) GmbH & Co. KG, Karlsruhe, Germany. The text, photographs, and drawings in
this manual are protected by copyright. Physik Instrumente (PI) GmbH & Co. KG reserves all rights in this
respect. The use of any text, images and drawings is permitted only in part and only when indicating the
source.
Original instructions
First printing: 15.09.2021
Document number: PZ166E, BRo, Version 2.0.0
Subject to change. This manual is superseded by any new release. The latest respective release is available for
download (p. 3) on our website.

1About this Document 1
1.1 Objective and Target Audience of this User Manual.................................................. 1
1.2 Symbols and Typographic Conventions...................................................................... 1
1.3 Figures ........................................................................................................................ 2
1.4 Other Applicable Documents ..................................................................................... 2
1.5 Downloading Manuals................................................................................................ 3
2Safety 5
2.1 Intended Use .............................................................................................................. 5
2.2 General Safety Instructions ........................................................................................ 5
2.3 Organizational Measures............................................................................................ 6
3Product Description 7
3.1 Features and Applications .......................................................................................... 7
3.2 Model Overview ......................................................................................................... 7
3.3 Product View .............................................................................................................. 8
3.3.1 Front Panel .................................................................................................... 8
3.3.2 Rear Panel.................................................................................................... 11
3.4 Scope of Delivery...................................................................................................... 12
3.5 Accessories ............................................................................................................... 12
4Unpacking 13
5Installation 15
5.1 General Notes on Installing ...................................................................................... 15
5.2 Ensuring Ventilation ................................................................................................. 15
5.3 Connecting the E-625 to the Protective Earth Conductor........................................ 15
5.4 Connecting the Power Supply to the E-625 ............................................................. 16
5.5 Connect a Positioner to the E-625............................................................................ 17
5.6 Connecting a Signal Source to the E-625.................................................................. 18
5.7 Connecting a Measuring Device to E-625 ................................................................ 18
5.8 Connecting a PC for the Computer-Controlled Mode (only E-625.CR) .................... 19
5.8.1 Connecting the E-625.CR to a PC................................................................. 19
5.8.2 Interlinking the Controllers.......................................................................... 20
6Startup 23
6.1 General Notes on Startup......................................................................................... 23
Contents

6.2 Perform System Test ................................................................................................ 24
6.3 Adjust the Sensor Zero-Point ................................................................................... 27
7Operation 31
7.1 General Notes on Operation .................................................................................... 31
7.2 Operating Modes...................................................................................................... 32
7.2.1 Control Mode............................................................................................... 32
7.2.2 Servo Mode ................................................................................................. 33
7.3 Selecting the Operating Mode ................................................................................. 33
7.3.1 Selecting the Control Mode......................................................................... 33
7.3.2 Selecting the Servo Mode............................................................................ 34
8Adjustment of Internal Settings 35
8.1 General Notes on the Adjustment of Settings ......................................................... 35
8.2 Opening the Housing................................................................................................ 36
8.3 Adjustment Elements Inside the Housing ................................................................ 37
8.3.1 Jumper ......................................................................................................... 38
8.3.2 Switches....................................................................................................... 40
8.3.3 Potentiometers............................................................................................ 41
8.3.4 E-802 Servo Controller Submodule ............................................................. 41
8.4 Synchronizing the Sensors........................................................................................ 41
8.5 Adjusting Notch Filter and P-I Controller ................................................................. 43
8.5.1 Adjusting the Notch Filter............................................................................ 43
8.5.2 Setting the P-I Controller in Analog Mode .................................................. 46
8.6 Calibrating the Displacement of the Positioner ....................................................... 47
8.6.1 Adjusting the Sensor Range......................................................................... 48
8.6.2 Adjusting the Static Sensor Gain for Closed-Loop Operation...................... 51
8.6.3 Adjusting the Sensor Linearization .............................................................. 54
8.6.4 Digital Corrections (only E-625.CR).............................................................. 55
9Maintenance 57
9.1 Cleaning the E-625.................................................................................................... 57
9.2 Updating Firmware................................................................................................... 57
10 Troubleshooting 59
11 Customer Service 63
12 Technical Data 65
12.1 Specifications............................................................................................................ 65
12.1.1 Data Table.................................................................................................... 65
12.1.2 Maximum Ratings........................................................................................ 66

12.1.3 Ambient Conditions and Classifications ...................................................... 67
12.2 Operating Limits ....................................................................................................... 68
12.3 Dimensions ............................................................................................................... 69
12.4 Block Diagrams ......................................................................................................... 70
12.4.1 E-625.CR Block Diagram .............................................................................. 70
12.4.2 E-625.C0 Block Diagram............................................................................... 71
12.5 Pin Assignment ......................................................................................................... 72
12.5.1 PZT & SENSOR.............................................................................................. 72
12.5.2 Network ....................................................................................................... 72
12.5.3 E-625.CN Network Cable ............................................................................. 73
12.5.4 Power Supply Connector ............................................................................. 73
13 Old Equipment Disposal 75
14 Appendix 77
14.1 Lifetime of PICMA® Actuators .................................................................................. 77
14.2 European Declarations of Conformity...................................................................... 81


1 About this Document
E-625 Piezo Servo Controller PZ166E Version: 2.0.0 1
In this Chapter
Objective and Target Audience of this User Manual ..................................................................... 1
Symbols and Typographic Conventions ......................................................................................... 1
Figures............................................................................................................................................ 2
Other Applicable Documents......................................................................................................... 2
Downloading Manuals ................................................................................................................... 3
1.1 Objective and Target Audience of this User Manual
This user manual contains the information required for using the E-625 as intended.
It assumes that the reader has a fundamental understanding of basic servo systems as well as
motion control concepts and applicable safety procedures.
The latest versions of the user manuals are available for download (p. 3) on our website.
1.2 Symbols and Typographic Conventions
The following symbols and typographic conventions are used in this user manual:
DANGER
Immediate threat of danger
Failure to comply could lead to death or serious injury.
Precautionary measures for avoiding the risk.
NOTICE
Dangerous situation
Failure to comply could cause damage to equipment.
Precautionary measures for avoiding the risk.
INFORMATION
Information for easier handling, tricks, tips, etc.
1
About this Document

1 About this Document
2 Version: 2.0.0 PZ166E E-625 Piezo Servo Controller
Symbol/
Label
Meaning
1.
2.
Action consisting of several steps with strict sequential order
Action consisting of one or more steps without relevant
sequential order.
Bullet
p. 5
Cross-reference to page 5
RS-232
Label on the product indicating an operating element (example:
RS-232 interface socket)
Warning signs attached to the product that refer to detailed
information in this manual.
1.3 Figures
For better understandability, the colors, proportions, and degree of detail in illustrations can
deviate from the actual circumstances. Photographic illustrations may also differ and must not
be seen as guaranteed properties.
1.4 Other Applicable Documents
The devices and software tools from PI mentioned in this documentation are described in
separate manuals.
You can download all manuals mentioned hereafter in a zip file from our website. To download
the manuals, use the "E-816" and "PI software" links in the "A000T0081-Downloading Manuals
from PI.pdf" file which you can find in the \Manuals folder on the PI software CD.
All manuals are available on our website and can also be downloaded (p. 3) individually.
Component Document
E-802 servo controller submodule
PZ150E User Manual
E-816 computer interface submodule
PZ116E User Manual
GCS driver for use with NI LabVIEW
software
SM158E Software Manual
PI GCS 2.0 DLL
SM151E Software Manual
PIMikroMove
SM148E Software Manual

1 About this Document
E-625 Piezo Servo Controller PZ166E Version: 2.0.0 3
INFORMATION
The E-625.S0 and E-625.SR models for operation with strain gauge sensors are described in a
separate manual (PZ167E).
1.5 Downloading Manuals
INFORMATION
If a manual is missing or problems occur with downloading:
Contact our customer service department (p. 63).
Downloading Manuals
1. Open the website www.pi.ws.
2. Search the website for the product number (e.g., P-882) or the product family (e.g.,
PICMA® bender).
3. Click the corresponding product to open the product detail page.
4. Click the Downloads tab.
The manuals are shown under Documentation. Software manuals are shown under
General Software Documentation.
5. Click the desired manual and fill out the inquiry form.
The download link will then be sent to the email address entered.


2 Safety
E-625 Piezo Servo Controller PZ166E Version: 2.0.0 5
In this Chapter
Intended Use.................................................................................................................................. 5
General Safety Instructions............................................................................................................ 5
Organizational Measures ............................................................................................................... 6
2.1 Intended Use
The E-625 is a laboratory device according to DIN EN 61010. It is intended to be used in interior
spaces and in an environment which is free of dirt, oil and lubricants.
Corresponding to its design, the E-625 is intended for driving capacitive loads (e. g. piezo
ceramic actuators).
The E-625 must not be used for purposes other than those named in this user manual. In
particular, the E-625 must not be used to drive ohmic or inductive loads.
The E-625 can be used for static as well as dynamic applications.
Capacitive sensors must be used for closed-loop operation. PI positioners intended for
closed-loop operation already have the corresponding sensors. Other sensors can only be used
with PI approval.
2.2 General Safety Instructions
The E-625 is built according to state-of-the-art technology and recognized safety standards.
Improper use can result in personal injury and/or damage to the E-625.
Use the E-625 for its intended purpose only, and only when it is in perfect technical
condition.
Read the user manual.
Eliminate any malfunctions that may affect safety immediately.
The operator is responsible for the correct installation and operation of the E-625.
Install the E-625 near the power source so that the power plug can be quickly and easily
disconnected from the mains.
2
Safety

2 Safety
6 Version: 2.0.0 PZ166E E-625 Piezo Servo Controller
Use the supplied components (power supply, adapter, power cord) to connect the
E-625 to the power source.
If one of the supplied components for connecting to the power source has to be
replaced, use a sufficiently dimensioned component.
If a protective earth conductor is not or not properly connected, dangerous touch voltages can
occur on the E-625 in the case of malfunction or failure of the system. If there are touch
voltages, touching the E-625 can result in serious injury or death from electric shock.
Connect the E-625 to a protective earth conductor (p. 15) before starting.
Do not remove the protective earth conductor during operation.
If the protective earth conductor has to be removed temporarily (e.g., in the case of
modifications), reconnect the E-625 to the protective earth conductor before restarting.
If the E-625 is operated with an open housing, live parts are accessible. Touching the live parts
can result in serious injury or death from electric shock.
Only open the E-625 housing when you are authorized and have the corresponding
qualifications.
Before opening the housing, disconnect the E-625 from the power source by removing
the power plug.
When operating with an open housing, do not touch any components in the housing
aside from the adjustment elements described in this user manual.
2.3 Organizational Measures
User Manual
Always keep this user manual together with the E-625.
The latest versions of the user manuals are available for download (p. 3) on our
website.
Add all information from the manufacturer to the user manual, for example,
supplements or technical notes.
If you give the E-625 to a third party, include this user manual as well as other relevant
information provided by the manufacturer.
Do the work only if the user manual is complete. Missing information due to an
incomplete user manual can lead to serious or fatal injuries as well as damage to the
equipment.
Install and operate the E-625 only after you have read and understood this user
manual.
Personnel Qualification
The E-625 may only be installed, started, operated, maintained, and cleaned by authorized and
appropriately qualified personnel.

3 Product Description
E-625 Piezo Servo Controller PZ166E Version: 2.0.0 7
In this Chapter
Features and Applications ............................................................................................................. 7
Model Overview............................................................................................................................. 7
Product View.................................................................................................................................. 8
Scope of Delivery ......................................................................................................................... 12
Accessories................................................................................................................................... 12
3.1 Features and Applications
The E-625 piezo servo controller is a benchtop device that provides closed-loop and open-loop
control of the displacement of the positioner. The models E-625.CR and E-625.C0 work with
capacitive sensors that measure the position directly and without contact.
The integrated E-802 servo controller submodule has the slew rate limiter, the notch filter, and
the servo loop.
The notch filter improves the stability and enables a wider broad-band operation closer to the
mechanical resonant frequency of the piezo system.
The E-625.CR module is equipped with an E-816 computer interface submodule. This enables it
to offer the following additional functions:
Multi-axis network:
Several E-625.CR can be controlled from one single interface. A special network cable
sets up the communication between the individual controllers.
Waveform memory:
The user can save any function values in an internal table and output these with a
trigger. This makes it possible to reliably repeat and simply control motion profiles.
General Command Set (GCS):
For uniform control of nano and micropositioning systems, the universal command set
from PI is used. With GCS, control is independent of the hardware used so that various
positioning systems can be controlled together or new systems can be used with
minimum programming effort.
3.2 Model Overview
There are 2 standard versions of the E-625. They differ in regard to the available control modes
and the possibilities for use in network operation.
3
Product Description

3 Product Description
8 Version: 2.0.0 PZ166E E-625 Piezo Servo Controller
Model Description
E-625.CR
Piezo servo controller, single channel, for capacitive sensors;
analog mode and computer-controlled mode; network operation of several
devices
E-625.C0
Piezo servo controller, single channel, for capacitive sensors; only analog
mode; no network operation
3.3 Product View
3.3.1 Front Panel
Figure 1: E-625.CR front panel
ANALOG IN/WTT
SMB socket, coaxial input line grounded on the line conductor.
The use depends on the control mode which is set up with the Settings DIP switch block (see
below):

3 Product Description
E-625 Piezo Servo Controller PZ166E Version: 2.0.0 9
Control Function
Analog Mode
ANALOG IN/WTT is used as the input voltage for the target value
(depending on the servo mode interpreted as voltage or as position, see
below)
The input voltage should always be in the range of –2 to +12 V. The range
can be expanded to –3 to +13 V. However, this can reduce (p. 77) the
lifetime of the piezo actuator in the positioner and causes the overflow LED
to light up.
The input voltage can also be a computer-generated analog signal
(e.g., from a data acquisition board). You can generate this analog signal
with the NI LabVIEW driver from PI that is on the PI software CD. Note:
After installing the driver, it is necessary to activate the analog
functionality, see the file Analog_Readme.txt in the installation directory
(C:\ProgramData\PI\LabVIEW).
Computer-
controlled mode
(only E-625.CR)
ANALOG IN/WTT is used as the trigger input signal for the wave table
output and triggered motion (active HIGH; LOW: 0 to 0.5 V, HIGH: 3.0 to 5.0
V, maximum 10 V; max. frequency 400 Hz; min. pulse width: 200 μs).
Refer to the user manual for the E-816 computer interface submodule.
SENSOR MONITOR
SMB socket, coaxial output line with grounded line conductor and 0 to 10 V on the inner
conductor. Filtered and converted sensor output value with 0 to 10 V for the nominal travel
range. The output impedance is 10 kΩ.
RS-232 (only E-625.CR)
D-sub panel plug, (9-pole, male) for the serial connection to the PC. Refer to the user manual
for the E-816 computer interface submodule.
USB Socket (only E-625.CR)
Universal serial bus interface (USB-mini B(m) socket) for the serial connection to the PC. Refer
to the user manual for the E-816 computer interface submodule.
On Target LED, green
On-target signal from E-802 servo controller submodule. When the On Target LED comes on,
the distance from the target position is less than ±0.19 % of the travel range.
The signal (TTL, active low) is also applied to pin 6 of the Network D-sub socket on the rear
panel of the E-625 (p. 72).
Overflow LED, yellow
When the Overflow LED comes on, the amplifier is near to its range limit (piezo voltage outside
the range of –30 V to +130 V).
When the Overflow LED comes on in closed-loop operation (servo mode ON), a zero-point
adjustment (p. 27) can be necessary.

3 Product Description
10 Version: 2.0.0 PZ166E E-625 Piezo Servo Controller
Power LED, green
When the Power LED lights up continuously, the E-625 has been switched on.
Settings DIP Switch Block
Switch Position Function
1 (left)
ON (down)
Signal on ANALOG IN/WTT used as the analog input voltage
for specifying the target value
OFF (up)
Signal on ANALOG IN/WTT not used as the analog input
voltage for specifying the target value
2
ON (down)
Target value specified by the E-816 computer interface
submodule
OFF (up)
Target value not specified by the E-816 computer interface
submodule
3
ON (down)
Servo mode switched on (closed-loop operation)
OFF (up) Servo mode switched off (open-loop operation)
E-625.CR only: On the E-816 computer interface submodule,
the servo mode can be switched on with the SVO command.
4
ON (down)
Signal on ANALOG IN/WTT used as the trigger for the wave
table output or triggered motion
OFF (up)
Signal on ANALOG IN/WTT not used as the trigger for the
wave table output or triggered motion
The switches 1, 2 and 4 determine the control mode for the E-625 and consequently the usable
control sources.
Switch Analog Mode Computer-Controlled Mode (only E-625.CR)
1
ON
OFF
2
OFF
ON
4
OFF
ON
Setting the switches 1, 2 and 4 in an incompatible manner can result in unpredictable behavior.
Zero Potentiometer
A trimmer adjustment tool can be used on the Zero potentiometer for a zero-point adjustment
of the sensor. A zero-point adjustment can be necessary after longer operation (changes in
temperature) or if the load is changed.

3 Product Description
E-625 Piezo Servo Controller PZ166E Version: 2.0.0 11
PZT & SENSOR
Sub-D Mix 7W2 socket for connecting the positioner (p. 72):
Voltage output for the piezo actuator in the positioner. The piezo voltage is between
–30 and +130 V.
Input for the sensor signal from the positioner
3.3.2 Rear Panel
Figure 2: E-625 rear panel
Network
D-sub socket, 9-pole, female (p. 72) for the network connection (only E-625.CR; I2C-bus), the
synchronization of the sensor and the on-target signal from the E-802 servo controller
submodule.
The on-target signal shows that the distance from the target position is less than ±0.19 % of the
travel range. The signal (TTL, active low) is also applied to the On Target LED on the front panel
of the E-625.
Protective earth connector
The protective earth connector (threaded bolt marked with the symbol for the protective earth
conductor) has to be connected to a protective earth conductor, because the E-625 is not
grounded via the power adapter connector.

3 Product Description
12 Version: 2.0.0 PZ166E E-625 Piezo Servo Controller
DC IN 12–30 V
Panel plug for power adapter connector (p. 73). The C-501.15050H wide input range power
supply must be connected by using an adapter from barrel to Switchcraft (p. 16).
3.4 Scope of Delivery
Order
number
Components
E-625.CR
or
E-625.C0
Piezo servo controller according to order
C-501.15050H
Separate 15 V wide input range power supply for use with line voltages from
100 to 240 V AC and voltage frequencies of 50 or 60 Hz, with barrel connector.
K050B0002
Barrel-to-Switchcraft adapter for the power adapter connector
3763
Power cord
E-692.SMB
SMB/BNC adapter cable, 1.5 m (2 pcs.)
PZ300EK
Short Instructions for Housed Analog Piezo Electronics
PZ150E
User manual for the E-802 servo controller submodule
Only with E-625.CR:
C-815.34
Null modem cable for the connection to the PC
000036360
USB cable (USB-A(m)/USB-Mini-B(m)) for the connection to the PC
PZ116E
User manual for the E-816 computer interface submodule
C-990.CD1 PI software CD for digital electronics
Only with E-625.C0:
E500T0011
Technical Note for analog control with the NI LabVIEW driver from PI
3.5 Accessories
Order
Number
Description
E-625.CN
Network cable, 0.3 m, for interlinking two E-625 piezo servo controllers
(I2C-bus, sensor synchronization; for details see the pin assignment of the cable
(p. 73))
To order, contact our customer service department (p. 63).

4 Unpacking
E-625 Piezo Servo Controller PZ166E Version: 2.0.0 13
1. Unpack the E-625 with care.
2. Compare the contents with the scope of delivery according to the contract and the
delivery note.
3. Inspect the contents for signs of damage. If any parts are damaged or missing, contact
our customer service department (p. 63) immediately.
4. Keep all packaging materials in case the product needs to be returned.
4
Unpacking

This manual suits for next models
1
Table of contents
Other Physik Instrumente Controllers manuals
Popular Controllers manuals by other brands
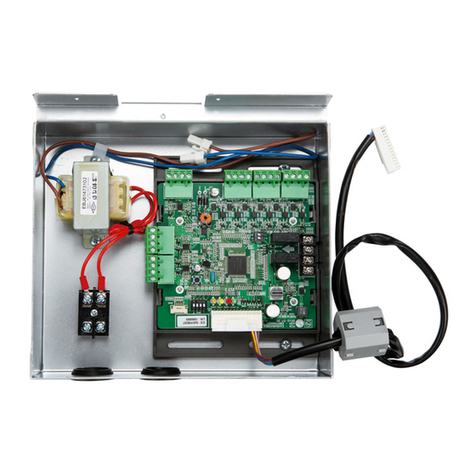
LG
LG PWFCKN000 installation manual
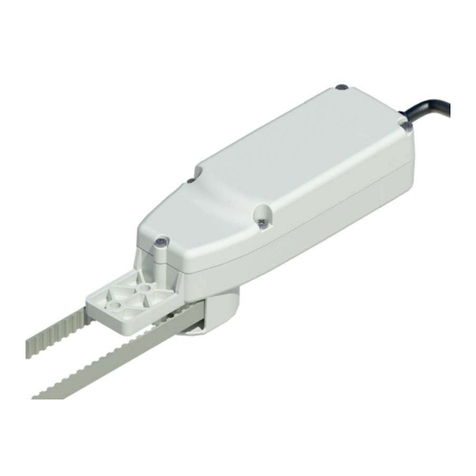
CHIAROSCURO
CHIAROSCURO SL80 Use and maintenance manual
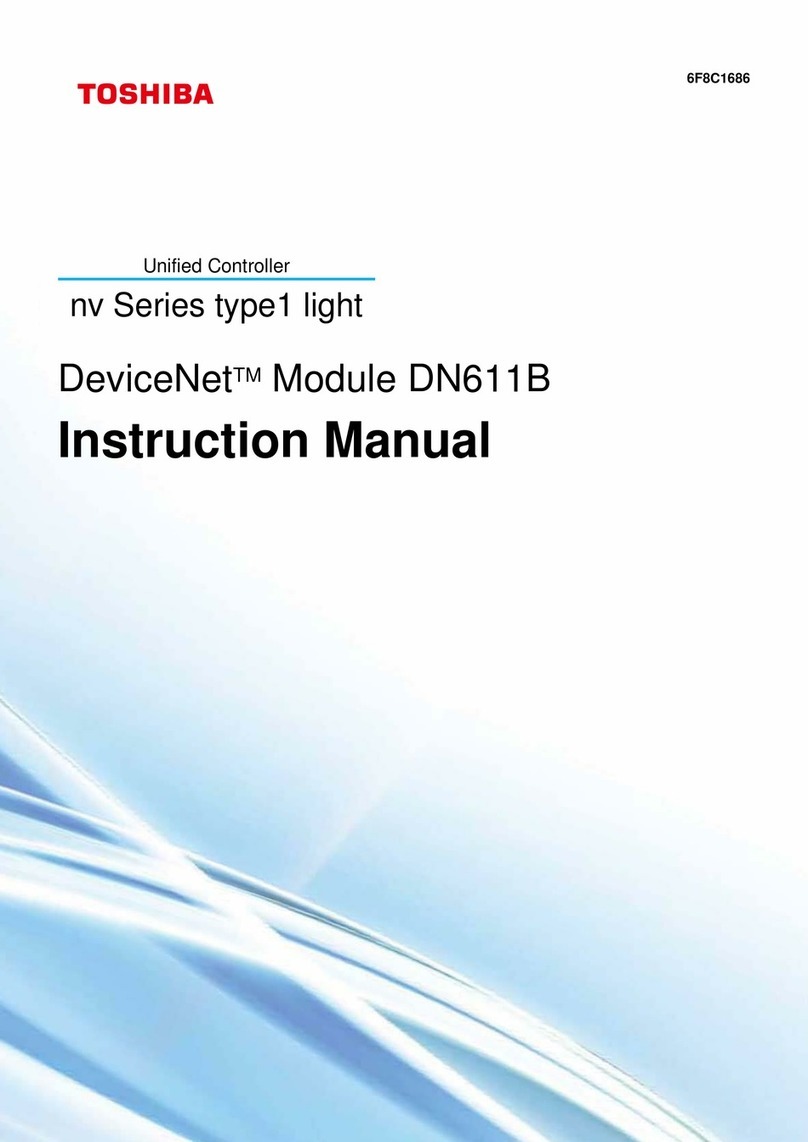
Toshiba
Toshiba DeviceNet nv Series instruction manual

Samson
Samson 43-8 Mounting and operating instructions
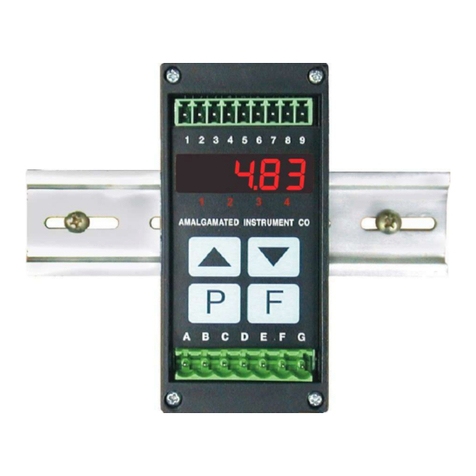
AMALGAMATED INSTRUMENT
AMALGAMATED INSTRUMENT RM4-AI Operation and instruction manual
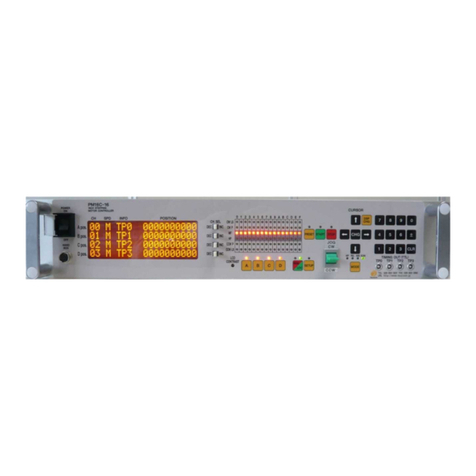
TSUJI ELECTRONICS
TSUJI ELECTRONICS PM16C-16 user manual