PPM ViaLiteHD HRx-C-HB-1 series User manual

ViaLiteHD
C-Band RF Fibre Optic Link
User Guide
HRx-C-HB-1
CR4067 11/03/2019
Pulse Power & Measurement Ltd, 65 Shrivenham Hundred Business Park, Watchfield, Swindon, Wiltshire SN68TY, UK
Tel +44 (0)1793 784389 Fax +44 (0)1793 784391 Email sales@vialite.com Web www.vialite.com

HRX-C-HB-1 C-BAND LINK HANDBOOK
2
Instrument Care and Safety Information
Please read the whole of this section before using your ViaLiteHD product. It contains important
safety information and will enable you to get the most out of your Fibre Optic Link.
Electrical Safety
The ViaLiteHD chassis is a Safety Class 1 product (having metal case directly
connected to earth via the power supply cable).
When operating the equipment note the following precautions:
Hazardous voltages exist within the equipment. There are no user serviceable
parts inside; the covers should only be removed by a qualified technician.
There are no user replaceable fuses in the chassis mounted equipment.
Replacement should only be carried out by a ViaLite Communications
technician.
The chassis earth stud SHOULD be connected to the safety earth.
When using a 2 pin power supply cable the chassis earth stud MUST be
connected to the safety earth.
The ViaLiteHD Power Supply Modules do not have an isolating switch on the
mains voltage inlet. For this reason, the ViaLiteHD Chassis must be installed
within easy reach of a clearly labelled dual pole mains isolation switch, which
supplies the equipment.
ESD Precautions
The ViaLiteHD RF Fibre Optic Link is equipped with high frequency active
electronics, without the correct handing they will be susceptible to damage.
Precautions for handling electro-static sensitive devices should be observed
when handling all ViaLiteHD modules.
Technicians should ensure that they use effective personal grounding (i.e.
ESD wrist strap etc.) when servicing the equipment.
Any equipment or tools used should be grounded to prevent static charge
build-up.
Good practice should be observed at all times for reference see relevant
standards. EN 61340-5-1, “Protection of Electronic Devices from Electrostatic
Phenomena –General Requirements”
Optical Safety
The ViaLiteHD RF Fibre Optic Transmitters contain optical sources (usually laser
diodes) operating at nominal wavelengths of 1270nm to 1610nm.
These devices are rated as EN60825-1:2007 as CLASS 1 radiation emitting
devices. A class 1 laser is safe under all conditions of normal use.
When operating the equipment note the following precautions:
Never look into the end of an optical fibre directly or by reflection either with
the naked eye or through an optical instrument.
Never leave equipment with radiating bare fibres –always cap the connectors.
Do not remove equipment external covers when operating.

HRX-C-HB-1 C-BAND LINK HANDBOOK
3
TABLE OF CONTENTS
1INTRODUCTION.............................................................................................................................5
1.1 The C-Band...........................................................................................................................5
1.2 Typical deployment ...............................................................................................................5
1.3 Care of fibre optic connectors...............................................................................................5
2SETTING UP AND UNDERSTANDING THE FIBRE OPTIC LINK.................................................6
2.1 Module operation ..................................................................................................................6
2.1.1 5HP standard plug-in modules ...................................................................................6
2.1.2 RF connectors.............................................................................................................7
2.1.3 Purple link modules.....................................................................................................7
2.2 Fibre optic cable & connectors..............................................................................................8
2.2.1 Connecting and disconnecting....................................................................................8
2.2.2 Cleaning optical connectors, cleaning before every use ............................................8
2.2.3 Cleaning optical connectors, high levels of contamination.........................................8
2.2.4 FC/APC Connectors ...................................................................................................9
2.2.5 SC/APC Connectors.................................................................................................10
2.2.6 E2000/APC Connectors............................................................................................10
2.2.7 Minimum bend radius................................................................................................10
2.3 Using the RF link module....................................................................................................11
2.3.1 Connecting the module.............................................................................................11
2.3.2 Front panel indicators, plug-in modules....................................................................11
2.3.3 LED indicator, purple modules..................................................................................11
2.3.4 Module summary alarm ............................................................................................11
2.3.5 Connecting to the summary alarm............................................................................12
2.3.6 Received light level (RLL) alarm...............................................................................12
2.3.7 Module analogue monitor .........................................................................................12
2.3.8 High power and DWDM transmitter modules, thermal load .....................................13
2.3.9 Operating in gain control modes...............................................................................13
2.4 Controlling RF modules.......................................................................................................14
2.4.1 Manual control, MGC................................................................................................14
2.4.2 Manual control, DIP switch functions........................................................................14
2.4.2.1 DIP switches - receiver MGC.....................................................................15
2.4.2.2 DIP switches - transmitter MGC ................................................................15
2.4.2.3 Manual gain control example.....................................................................16
2.4.2.4 DIP switches - control................................................................................16
2.4.3 Changing module RF gain........................................................................................17
2.4.4 Software control - via SNMP controller.....................................................................17
2.5 LNA/LNB and BUC DC feeds..............................................................................................17
2.5.1 LNA/LNB feed - transmitter modules........................................................................17
2.5.2 LNA/LNB feed efficiency - plug-in modules..............................................................17
2.5.3 LNA/LNB voltage boost - plug-in modules................................................................17
2.5.4 LNA feed - Purple link modules ................................................................................18
2.5.5 LNA feed –Voltage versus current characteristic ....................................................18
2.5.6 BUC feed - receiver modules....................................................................................18
2.5.7 Manual configuration of LNA/LNB and BUC feeds, plug-in modules.......................19
2.6 Module Interface ratings......................................................................................................19
2.6.1 Susceptibility to DC pulses from ViaLiteHD receivers..............................................19
2.6.2 Protection of ViaLiteHD equipment from DC pulses.................................................19
2.6.3 Logic interface, TTL 5V.............................................................................................19
2.6.4 Logic interface, I2C...................................................................................................20
2.6.5 Logic interface, Open Drain, output..........................................................................20
2.6.6 Power interface, +12V, input.....................................................................................20
2.6.7 Analogue interface, laser diode bias, output ............................................................20
2.6.8 Analogue interface, photodiode received light level, output .....................................20
2.6.9 Internally generated LNB power supply and tone.....................................................21
2.6.10RF connectors...........................................................................................................21
2.6.11Optical connections...................................................................................................21

HRX-C-HB-1 C-BAND LINK HANDBOOK
4
3SYSTEM INTEGRATION..............................................................................................................22
3.1 Link loss budget calculations ..............................................................................................22
3.2 Optical loss versus gain ......................................................................................................22
3.3 Optical loss versus noise figure ..........................................................................................22
3.4 Gain.....................................................................................................................................23
3.4.1 Effect of temperature on gain ...................................................................................23
3.5 Noise Figure........................................................................................................................24
3.6 Linearity (P1dB compression).............................................................................................24
3.7 Linearity (IP3 intermodulation)............................................................................................24
3.8 Spurious Free Dynamic Range (SFDR)..............................................................................25
3.9 Link delay............................................................................................................................26
3.10 RF isolation .........................................................................................................................26
3.10.1RF isolation, plug-in cards ........................................................................................26
3.11 Typical system configuration with fixed gain modules........................................................27
3.12 Commissioning of a communications link...........................................................................27
4PART NUMBERING......................................................................................................................28
4.1 Part numbering matrix.........................................................................................................28
4.2 Part numbering, DWDM wavelengths.................................................................................28
5MAINTENANCE AND FAULT FINDING GUIDE...........................................................................29
6FCC APPROVAL...........................................................................................................................30
7PRODUCT WARRANTY...............................................................................................................31

HRX-C-HB-1 C-BAND LINK HANDBOOK
5
1 Introduction
The ViaLiteHD RF Fibre Optic Links (FOLs) are a family of fibre opticallycoupled link systems designed
for the transmission of RF analogue signals over long distances for the communications market.
ViaLiteHD is a product brand manufactured by Pulse Power and Measurement Ltd (PPM).
ViaLite Communications is a division of Pulse Power and Measurement Ltd (PPM).
This handbook covers the following ViaLiteHD RF Link part numbers:
C-Band Transmitter modules (electrical –optical converter) with part numbers starting
oHRT-C
C-Band Receiver modules (optical - electrical converter) with part numbers starting
oHRR-C
For complete information and product familiarisation, this handbook should be read in conjunction with
all other relevant handbooks for your ViaLiteHD system.
1.1 The C-Band
The ViaLiteHD RF Fibre Optic C-Band Links are designed to cover the extended C-Band frequency
range (uplink and downlink) of 3.4 GHz to 7.1 GHz.
Usable performance can be utilised beyond this range encompassing 500 MHz to 8GHz (see the
relevant characterisation data in section 3).
1.2 Typical deployment
A typical system operates as follows.
The user’s RF electrical signal is input to the transmitter module, which contains RF signal conditioning
and laser control circuitry. The module modulates the intensity of a beam of light with the RF signal
which then travels through an optical fibre to the receiver module. The distance between transmitter
and receiver can range from 1m to 100km; distances in excess of 100km can be achieved with more
complex optical transport systems, depending on the system specified. The receiver module converts
the modulated light back into an electrical signal, which is available at the output of the module.
The C-band link is also designed for use in Dense wavelength division multiplexed (DWDM) systems.
In this scenario, multiple links each operating on a different wavelength of light are combined in a
multiplexer and sent down a single optical fibre path. At the receiving end, a de-multiplexer separates
the wavelengths for the corresponding receivers. See section 4.2 for wavelength options when
considering the transmitters. Receiver modules however are wideband and will respond to any
wavelength of light passed to them.
ViaLite Communications offer a design service for complex DWDM requirements including supply of
optical multiplexers, optical amplifiers, optical switches and dispersion compensators. On-site
commissioning and installation support is also available.
1.3 Care of fibre optic connectors
When the fibre optic cables are not connected, it is essential that the cable and equipment connectors
are protected by the dust caps provided with the system. Failure to do so may result in damage to the
fibre ends, which are critical to the system performance. Please refer to section 0 for fibre optic cable
handling details.

HRX-C-HB-1 C-BAND LINK HANDBOOK
6
2 Setting up and understanding the fibre optic link
This section describes the connections between your RF fibre optic transmitter (electrical –optical
converter) and receiver (optical - electrical converter) modules, and the operation of both modules in a
system.
Please read fully all relevant documents for information on installing your ViaLiteHD equipment before
commissioning your RF fibre optic link system.
2.1 Module operation
2.1.1 5HP standard plug-in modules
All ViaLiteHD plug-in modules are hot-swappable, so it is not necessary to power-down the chassis
before inserting a module. All standard optical connectors are retained by the module, so it will be
necessary to either disconnect any cables or have a sufficiently long service loop when removing
modules.
To install a 5HP standard module and matching interface plate
The protective covers on the connectors may be left in place.
Push the release button of the module handle down and simultaneously pull the top of the handle
towards you.
Align the module upright and perpendicular to the front face of the chassis so that the PCB slides
into the “crow’s feet” card guides top and bottom.
Gently push the module down its guide, applying pressure via the handle, you may also apply
pressure between the LED and test connector (where test connector is fitted as these are not
available on all module types).
As the module is fully mated the top of the handle should snap back and lock in position.
The pawls of the handle should be fully engaged in the matching slots.
If power is applied to the chassis the module power LED should light as soon as the module is fully
inserted
Remove protective covers and connect any interface cables
To remove a 5HP Standard module
Disconnect any cables if necessary
Push the release button of the module handle down and simultaneously pull the top of the handle
forwards.
Apply pressure via the handle and gently withdraw the module from the chassis.

HRX-C-HB-1 C-BAND LINK HANDBOOK
7
2.1.2 RF connectors
ViaLiteHD C-Band link products are fitted with 50 Ohm female SMA connectors.
The SMA connector is a semi-precision sub-miniature RF and microwave connector and to maintain
performance up to 8GHz, ensure that when not in use, the supplied RF connector dust caps are fitted.
If any dust or dirt is visible within the connector body, cleaning with compressed air before mating is
advised.
When attaching cables to these RF connectors, a torque wrench should be used to guarantee
tightening to 1.0 Nm.
2.1.3 Purple link modules
The Purple Link is a small, dustproof C-Band RF over fibre module available for both the transmitter
and receiver. The 15-way D-type connector provides connectivity for the Tx or Rx alarms, I2C setup
using the ViaLiteHD Programming Kit(HRx-HD-DEV103) and the external power supply (optional HPS-
CS-4).

HRX-C-HB-1 C-BAND LINK HANDBOOK
8
2.2 Fibre optic cable & connectors
All ViaLiteHD RF modules use single-mode (9µm/125µm) cable terminated in a range of optical
connectors detailed below. Cross-site fibre optic cables are available from ViaLite Communications
as either standard patch leads or heavy-duty multicore cables.
Warning!
Angle polished (APC) and standard (PC) connector must not be confused.
The two connector types are not interchangeable and mating one with the other will
damage both the cable and the module connectors.
The specification of optical connector is critical to the performance of the complete
fibre optic link. System performance can only be guaranteed with fibre optic cables
and connectors supplied by ViaLite Communications.
When FC/APC connectors are specified they must be “narrow key width”
2.2.1 Connecting and disconnecting
Before connecting optical fibres to the module or to each other, ensure that the mating connectors are
clean (see below).
2.2.2 Cleaning optical connectors, cleaning before every use
Optical connectors MUST be cleaned before use, even where they have been protected with dust caps.
A large percentage of performance issues can be attributed to dirty fibres.
For more details please read the cleaning instruction which accompanies the connector cleaning kit.
Details can also be found on the CD supplied with your equipment.
2.2.3 Cleaning optical connectors, high levels of contamination
If there are performance issues that are not resolved by basic cleaning, then the following procedure
should be used. If the level of contamination is high it will be necessary to repeat this procedure.
Cleaning items required
Lint free fibre cleaning tissues and/or cleaning sticks (normal cosmetic tissues produce dust and
are not acceptable).
Reagent grade Isopropyl Alcohol (IPA).
Air duster or filtered compressed air line.
Cable Connector Cleaning
Dampen a patch of cleaning tissue with IPA and clean all surfaces of the plug ferrule.
Using a dry cleaning tissue, dry the ferrule and clean the end face.
Peel the plastic cover from an unused ‘N’
cleaning pad.
Hold the connector between your thumb and
forefinger
Clean the connector using firm pressure by
swiping in a pendulum motion through each
segment of the ‘N’shape, following the
diagram
Do not swipe over the same space twice.

HRX-C-HB-1 C-BAND LINK HANDBOOK
9
Using the air duster, blow away any residue from the end of the connector.
Module Female Receptacle Cleaning (only recommended if problems are being experienced)
Either use an optical cleaning stick or twist a cleaning tissue to form a stiff probe, moisten either
with IPA. Gently push the probe into the receptacle and twist around several times to dislodge any
dirt.
Repeat the above process with a dry tissue.
Using the air duster, blow away any residue from the receptacle.
Important Notes
IPA is flammable. Follow appropriate precautions / local guidelines when handling and storing.
IPA can be harmful if spilt on skin. Use appropriate protection when handling.
It should only be necessary to clean the female receptacles on the modules if problems are being
experienced.
Warning!
Never inspect an optical fibre or connector with the naked eye or an instrument
unless you are convinced that there is no optical radiation being emitted by the
fibre. Remove all power sources to all modules, and completely disconnect the
optical fibres.
2.2.4 FC/APC Connectors
To connect FC/APC optical connectors follow these steps:
Remove the dust caps and align the white ceramic centre ferrule on the cable connector with the
mating receptacle.
There is a key (lug) on the side of the ferrule, which must match the keyway (gap) in the receptacle
shroud.
When they are aligned, gently push the plug home.
Finger tighten the knurled collet nut onto the threaded receptacle.
To disconnect follow these steps:
Using fingers fully unscrew the knurled collet nut, gently withdraw the connector.
Replace the dust caps on both the receptacle and the cable plug.
Warning!
It is possible to tighten the knurled collet without aligning the lug and gap. This
will result in poor light transmission. Check that the lug and gap are aligned
before tightening the knurled collet

HRX-C-HB-1 C-BAND LINK HANDBOOK
10
2.2.5 SC/APC Connectors
To connect SC/APC optical connectors follow these steps:
Remove the plug protective cover.
Align the connector keyway slot in the adaptor to the key of the plug.
Gently push the plug-into the adapter until a click is heard and the connector locks.
To disconnect follow these steps:
Grip the body of the plug and gently pull the plug from the adaptor, replace the protective cover.
Only connect SC/APC cable to SC/APC receptacles.
2.2.6 E2000/APC Connectors
All ViaLiteHD E2000 connectorised modules use E2000/APC. Clean the plug before inserting.
To connect E2000/APC optical connectors:-
Gently push the plug-into the E2000/APC adapter.
The cover will automatically disengage.
Push until a click is heard and the connector locks.
To disconnect:-
To disconnect, depress the lever at the rear of the connector and withdraw the connector.
The protective cover automatically engages when removed.
Only connect E2000/APC cable to E2000/APC adaptors.
2.2.7 Minimum bend radius
Because optical fibre is made of glass, it is important not to subject it to excessive stress. For this
reason, each type of cable has a minimum bend radius (MBR) specification, beyond which the cable
cannot be bent without permanent damage occurring. Systems using longer wavelength (i.e. 1550nm)
are less tolerant to small bend radii.
The minimum bend radius of standard SMF28 fibre optic cable fitted to ViaLiteHD modules is 50mm.
MBR specifications for ViaLite Communications supplied fibre optic cables are given in the ViaLite
Classic and ViaLiteHD System Handbooks Lxx-HB and Hxx-HB respectively.

HRX-C-HB-1 C-BAND LINK HANDBOOK
11
2.3 Using the RF link module
2.3.1 Connecting the module
Connect the transmitter module to the power source, cross-site fibre optic cable and RF signal as
described in section 2.1. The RF input signal applied to the signal connector should be within the
maximum and minimum signal levels given in the datasheet.
2.3.2 Front panel indicators, plug-in modules
Each plug-in module has three front panel LEDs for indication of the state of the module. The following
table shows the operation of the front panel LEDs which are dependent on module type.
Colour
Plug-in
Transmitter
Plug-in
Receiver
LED1
GREEN
NORMAL
Flashing GREEN
Programming
Programming
RED
Not used
Not used
No light
TX PSU fail
RX PSU fail
LED2
GREEN
NORMAL
Flashing RED fast
TX Alarm
Not used
Flashing RED slow
Not used
RX Alarm
RED
Not used
Not used
LED3
GREEN
I2C enabled
Flashing GREEN
I2C active
AMBER
I2C disabled
2.3.3 LED indicator, purple modules
These modules are fitted with a single LED for indication of the state of the module.
2.3.4 Module summary alarm
Each module has a single summary alarm, which registers the status of the module. Activation of this
alarm registers an internal fault and the module should be replaced with a spare and returned to your
local ViaLiteHD representative. The alarm state should be accompanied by a fault status on one of the
front panel status LEDs.
The summary alarm is indicated by use of open drain logic. The alarm logic is OPEN when in an
ALARM state and SHORT when in a NORMAL (non-alarm) state. The module will remain in an ALARM
state until the ALARM condition is cleared, there is no latching.
Colour
Blue
link
Yellow
link
LED
GREEN
Normal
RED
Alarm
No Light
No power
LED1
LED2
LED3

HRX-C-HB-1 C-BAND LINK HANDBOOK
12
2.3.5 Connecting to the summary alarm
The alarm output pin should be connected to a suitable current source (a positive voltage via a 10kohm
pull-up resistor is adequate). When the module is in a working (non-alarm) state, the alarm output pin
is short circuited to ground by the module. If the module enters an alarm state, the alarm pin is released
to a high impedance state and current is no longer drawn from the constant current source. In the case
of a positive voltage and pull-up resistor, the voltage on the alarm output pin will rise to indicate the
alarm state. It follows that, if a module is removed from the chassis, the alarm will be raised for that
module position.
The capability of the open collector is dependent on the module that provides it. The typical capability
of the Open Collector/Drain is 50mA maximum current sink and 15V maximum voltage (Vext).
Note: Modules fitted in a chassis may have their alarm lines pull up by other chassis equipment, such
as switch, splitter, summary alarm or SNMP and web controller modules.
2.3.6 Received light level (RLL) alarm
Receiver modules, monitor the average incoming received light level (RLL), if the power drops below
a pre-set threshold the module will generate an RLL alarm.
The RLL alarm threshold is set for a nominal input power of -15.0dBm
oNominal optical loss of 25.0dB @ 10.0dBm (10mW) TX
Under normal operating conditions the RLL alarm accuracy is +/-2dB; and +/-4dB under extreme
conditions.
2.3.7 Module analogue monitor
Each plug-in module has either one or two analogue monitor ports. These allow simple DC indication
of the status of either lasers or photodiodes fitted in the RF modules. The analogue monitor is available
on the chassis connector, see the chassis handbook. The analogue monitor functions are dependent
on the type of module. The monitor function(s) provided are shown in the table below.
Function
Single Transmitter
Single Receiver
Analogue monitor A
Not Used
Received light level
Analogue monitor B
Laser bias monitor
Not Used
Vext
Pull up
Resistor
Alarm
Ground
Internal to module External to module

HRX-C-HB-1 C-BAND LINK HANDBOOK
13
The performance of the analogue monitors is as follows
Monitor type
Operation
TX analogue,
current monitor
output
VIFL = 25 x IFWD
VIFL = Voltage output of the current monitor, in volts
IFWD = Average bias current of laser diode, in amps
Note: Normal operating range IFWD is 0 –120mA
RX analogue,
received light level
output
VRLL = 4.00 –[ 0.15 x ( 10.0 - POPT ) ]
VRLL = Voltage output of the received light level (RLL) monitor, in volts
POPT = Optical input power, in dBm
Note: Optical transmitter power is assumed to be +10dBm
2.3.8 High power and DWDM transmitter modules, thermal load
All DWDM modules have active thermal control to stabilise their laser operating wavelength. This
requirement produces additional heat loading in their deployed environments. For this reason extra
consideration is needed when planning the installation and deployment of these systems.
If the installed environment temperature is uncontrolled, there exists the possibility that at high
temperature, operating efficiency will be reduced. Furthermore, if the active thermal control is unable to
maintain laser operating temperature, a major alarm and module shutdown will ensue.
To maintain full operational temperature and efficiency we suggest that you take the following actions.
Do not place DWDM transmitters adjacent to each other
When using a 3U chassis if more than 4 modules are fitted, forced air cooling should be used (flow
rate ~100CFM or more)
If housing DWDM transmitters in an outdoor housing contact ViaLite Communications for more
details
2.3.9 Operating in gain control modes
Modules can be operated in four different gain control modes when operated with an SNMP and Web
controller module (ViaLiteHD part number HRC-3).
The SNMP and Web controller module is required for configuring the AGC modes which operate by
varying the RF gain of the card in 0.5dB steps in response to measurements of either optical or RF
power.
Manual control is also available; this can be set using the hardware DIP switches.
For more information on this feature, please see section 2.13 of the ViaLiteHD SNMP controller
handbook, HRC-3-HB.

HRX-C-HB-1 C-BAND LINK HANDBOOK
14
2.4 Controlling RF modules
ViaLiteHD RF links are factory set and ready to operate. However, they can be software controlled
(where an SNMP module is used in the same chassis) or manually controlled via the DIP switches fitted
on each module.
2.4.1 Manual control, MGC
The plug-in modules can be manually configured to set various operational parameters. The dual in
line package (DIP) switches SW1, SW2, SW3 control configuration and are located on the bottom side
of the PCB. These switches can be accessed by withdrawing the module by approximately one-third
of its length. Two sets of switches will be installed depending on the type of module. Details of the
function of each switch are given in the section below.
2.4.2 Manual control, DIP switch functions
Located on the bottom side of the module board, three DIP switches (SW1 to 3) provide manual control
of various functions. SW1 and SW2 are dedicated to manual gain control (MGC). Once TX_MGC_ON
or RX_MGC_ON is switched on, internal RF attenuators can be set directly to a desired level. SW3 is
used to control various common control functions.
All intelligent modules will be delivered with DIP switches all set to OFF (clear). Only special manual
gain control modules will be delivered with the DIP switches set to factory calibrated gain settings.
Single Transmitter
Single Receiver

HRX-C-HB-1 C-BAND LINK HANDBOOK
15
SW1 Top DIP switch bank
Single transmitter HRT
Single receiver HRR
Not fitted
RXMGC
Not fitted
RX –0.5dB
Not fitted
RX –1dB
Not fitted
RX –2dB
Not fitted
RX –4dB
Not fitted
RX –8dB
SW2 Middle DIP switch bank
Single transmitter HRT
Single receiver HRR
TXMGC
Not fitted
TX –0.5dB
Not fitted
TX –1dB
Not fitted
TX –2dB
Not fitted
TX –4dB
Not fitted
TX –8dB
Not fitted
SW3 Bottom DIP switch bank
Single transmitter HRT
Single receiver HRR
TX rst
TX rst (not used)
RX rst (not used)
RX rst
SNMP dis
SNMP dis
Tone
Tone (not used)
VSEL
VSEL (not used)
LNB
LNB (not used)
TXAGC
TXAGC(not used)
RXAGC (not used)
RXAGC
When viewed in the orientation illustrated, switching the DIP to the LEFT is OFF (clear) and to the
RIGHT is ON (set)
2.4.2.1 DIP switches - receiver MGC
The RF gain within the receiver function is the sum of all gain settings on SW1. The RF gain can be
changed in nominal steps of 0.5dB.
For special manual gain control modules record the factory setting of each gain step; this is the preset
gain of the receiver.
RXMGC ON = Manual gain control, OFF = Software control or at default setting
RX –0.5dB ON = Gain increased by 0.5dB nominal, OFF= no gain increase
RX –1dB ON = Gain increased by 1dB nominal, OFF= no gain increase
RX –2dB ON = Gain increased by 2dB nominal, OFF= no gain increase
RX –4dB ON = Gain increased by 4dB nominal, OFF= no gain increase
RX –8dB ON = Gain increased by 8dB nominal, OFF= no gain increase
When MGC is not in use, manual attenuation has to be set to zero, i.e. all poles with the same switch
should return to OFF position. Failure to do so may prevent the module from controlling the gain
correctly.
2.4.2.2 DIP switches - transmitter MGC
The RF gain within the transmitter function is the sum of all attenuator settings on SW2. The RF gain
can be changed in nominal steps of 0.5dB.
For special manual gain control modules record the factory setting of each gain step; this is the preset
gain of the transmitter.

HRX-C-HB-1 C-BAND LINK HANDBOOK
16
TXMGC ON = Manual gain control, OFF = Software control or at default setting
TX –0.5dB ON = Gain increased by 0.5dB nominal, OFF= no gain increase
TX –1dB ON = Gain increased by 1dB nominal, OFF= no gain increase
TX –2dB ON = Gain increased by 2dB nominal, OFF= no gain increase
TX –4dB ON = Gain increased by 4dB nominal, OFF= no gain increase
TX –8dB ON = Gain increased by 8dB nominal, OFF= no gain increase
When MGC is not in use, manual attenuation has to be set to zero, i.e. all poles with the same switch
should return to OFF position. Failure to do so may prevent the module from controlling the gain
correctly.
2.4.2.3 Manual gain control example
In this example we consider a receiver. The factory set values will typically be in the mid-range of the
allowable gain setting range, to allow the operator to both increase and decrease the gain of the unit if
desired.
Factory preset: TX–0.5dB =ON; TX–1dB =OFF; TX–2dB =ON; TX–4dB =ON; TX–8dB =OFF.
This is a total gain of 0.5 + 2 + 4 = 6.5dB [this will be the factory preset gain]
The operator wishes to increase the gain by 3dB from factory preset gain, he must increase the DIP
switch set gain from 6.5dB to 9.5dB
The new gain setting desired will be 9.5dB, made from the following steps 0.5 + 1 + 8, therefore set
the switches as shown below
TX –0.5dB = ON; TX –1dB = ON; TX –2dB = OFF; TX –4dB = OFF; TX –8dB = ON.
The new gain is now set to 9.5dB
Note: The gain of the link is the sum of the transmitter module and receiver module gains.
2.4.2.4 DIP switches - control
If you wish to use manual control we advise that you record the initial setting of each switch, this is the
preset configuration of the module. SW3 control functions are common to the whole module. The on-
board micro controllers can be manually reset by using TX_RESET and/or RX_RESET, they must
return to the OFF (clear) position to initiate the actual reset sequence.
Switching on SNMP_dis will disable the module I2C bus for that module. In this case, SNMP controller
or other I2C hosts will be unable to talk to the module.
RF auto gain control (AGC) function can be activated by setting TX_AGC_ON and RX_AGC_ON to ON
(set) position. However, AGC mode will be overridden by MGC mode if both modes are selected. These
will override module internal soft gain control. Some modules will have control functions indicated that
are not used, such as RX_rst in a single transmitter module. Switches for these “not used” positions
should always be left in the OFF (clear) position.
TX rst Reset TX microcontroller by moving switch from OFF > ON > OFF, ensure that it is
returned to the OFF position**
RX rst Reset RX microcontroller by moving switch from OFF > ON > OFF, ensure that it is
returned to the OFF position**
SNMP_dis ON = I2C bus disabled (module cannot be remotely accessed), OFF = I2C bus enabled
Tone ON = 22kHz tone present, OFF = 22kHz tone disabled
VSEL ON = Internal module LNB PSU voltage set to 18V, OFF = Internal module LNB PSU
voltage set to 13V
LNB ON = Internal module LNB PSU enabled, OFF = Internal module LNB PSU disabled
TXAGC* ON = TX AGC control function activate, OFF = TX AGC control function disabled
RXAGC* ON = RX AGC control function activate, OFF = RX AGC control function disabled
* Not available on manual control modules
** Card must be powered to perform the reset action, removing power will also reset a module

HRX-C-HB-1 C-BAND LINK HANDBOOK
17
2.4.3 Changing module RF gain
The link performance specifications apply when modules are operated in the factory preset
configuration. However, the gain of the modules can be changed to suit customer requirements.
The performance of the transmitter is highly dependent on the laser diode. Changing transmitter and
receiver gain will affect the sensitivity and linearity of the module. Detail of these effects are provided
in section 3.
2.4.4 Software control - via SNMP controller
ViaLiteHD RF links can be controlled via a ViaLiteHD SNMP control module when fitted in the same
chassis, see the SNMP controller module handbook for further details. The SNMP module offers control
via both a web interface and SNMP.
Remember if you wish to use software control the manual attenuation has to be set to zero, i.e. all poles
of the switch should return to the OFF position. Failure to do so may prevent the module from controlling
the gain correctly.
2.5 LNA/LNB and BUC DC feeds
The C-band modules have an option to present a DC voltage at the RF connector to power any
connected equipment capable of receiving its power this way.
Warning!
Precautions must be taken to ensure that any connected equipment is tolerant
of the DC voltages supplied.
2.5.1 LNA/LNB feed - transmitter modules
Transmitter modules may be used to provide a power feed via the RF connection to a preceding low
noise amplifier (LNA) or low noise block down converter (LNB).
The voltage source for this function can be supplied externally via a chassis connection or from the
module’s on-board voltage generator
The external DC paths (option 3) of a module may be accessed via the chassis connector for plug-in
modules (see your chassis handbook) or the 15 way D-Type connector for the purple modules.
The LNA/LNB option can be determined from the part number.
Modules in this range offer a variety of feed options, shown below.
0
No LNA feed
1
Internally generated +5 ± 0.5V at 80mA
2
Internally generated +12 ± 1V at 300mA
3
External Feed from chassis connector 0 to +28V at 350mA
5
Internally generated +13.4 ± 1 or +18.5 ± 1 selectable 350mA (up to 7.1GHz)
L
Internally generated +13.4 ± 1 or +18.5 ± 1 selectable 700mA (up to 6.0GHz)
2.5.2 LNA/LNB feed efficiency - plug-in modules
The power consumption of a transmitter is specified without allowance for LNA/LNB power. When
calculating power consumption the module efficiency of the LNA/LNB power supply at full load is 89%
typically and 80% minimum
2.5.3 LNA/LNB voltage boost - plug-in modules
The output voltage of any module equipped with an internal 13/18/22 volt power supply (option “5” and
“L”) can have its output voltage increased to allow for cable losses, the output voltage is increased by

HRX-C-HB-1 C-BAND LINK HANDBOOK
18
+1V nominally. This is implemented using the modules software configuration. This option is NOT
available on units equipped with +5V, +12V or external voltage feeds.
2.5.4 LNA feed - Purple link modules
Modules in this range offer an internally generated +5V or +12V feed and external feed only.
2.5.5 LNA feed –Voltage versus current characteristic
The LNA voltage is fed via a wideband choke (providing RF isolation) a low value resistor (used for
current monitoring) and a resettable fuse (providing protection). These elements add a series
impedance of approximately one ohm. The graph below shows how the voltage current characteristic
of a typical module with 12 volts fed to into the LNA feed via an external feed from the module connector
“LNA feed” pin.
When using LNA/LNB feeds care must be taken to allow for voltage drops through the input feed
network as well as voltage drops in the output feed network. For example RG58 may have a resistance
of up to 0.2 ohms per meter; this varies greatly between different types and constructions of cable.
Voltage measured at RF connector versus load current, input voltage 12V
NOTE: the graph shows the module operating beyond its specification limit to illustrate the margin of
safe operation, it should not be operated beyond its specification limit.
2.5.6 BUC feed - receiver modules
Receiver modules may optionally provide block up converter (BUC) power feeds. These provide a DC
path to the receiver RF output to provide power to a BUC or other connected module. The external DC
paths (option 3) of a module may be accessed via the chassis connector for Plug-in modules (see your
chassis handbook).
0
No LNA feed
1
Internally generated +5 ± 0.5V at 80mA
2
Internally generated +12 ± 1V at 300mA
3
External Feed from chassis connector 0 to +28V at 350mA
5
Internally generated +13.4 ± 1 or +18.5 ± 1 selectable 350mA (up to 7.1GHz)
L
Internally generated +13.4 ± 1 or +18.5 ± 1 selectable 700mA (up to 6.0GHz)
11.3
11.4
11.5
11.6
11.7
11.8
11.9
12
12.1
0 0.1 0.2 0.3 0.4 0.5 0.6 0.7 0.8 0.9
Voltage atRF connector (V)
Load Current(A)
LNA feed –Voltageversuscurrent

HRX-C-HB-1 C-BAND LINK HANDBOOK
19
2.5.7 Manual configuration of LNA/LNB and BUC feeds, plug-in modules
Some modules can be configured either by jumper or by switch to provide an LNA/LNB or BUC feed
either from an internally generated voltage or from the rear connector in the ViaLiteHD chassis. The
diagram below shows how these are set.
Units with LNA/ LNB internal power supplies (options 1, 2, and 5) will be delivered set to “internal”.
Units with external LNA power (option 3) will be set to “external”. Units with no LNA/LNB or BUC feed
(option 0) will normally have no headers fitted to positions J15 or J16.
Manual configuration of LNA/LNB/BUC DC power feeds
2.6 Module Interface ratings
2.6.1 Susceptibility to DC pulses from ViaLiteHD receivers
All receiver modules will create a 1-2Vpeak DC transient from the RF output at start up into a 50Ω load
(approximately 5V into a 1MΩ load). This may cause failure in some very sensitive spectrum analysers
or similar equipment. Please check before connecting your equipment. Contact ViaLite
Communications for more details.
2.6.2 Protection of ViaLiteHD equipment from DC pulses
All modules have AC coupled inputs and/or outputs and will be sensitive to large transients (>5V)
applied at the RF connector. This may result in permanent damage to the modules, particularly to low
frequency or wideband modules. DVB-T and L-Band HTS modules are designed to survive non
repetitive DC pulse of up to 36V. To increase protection, BUC feed option “B” can be specified for GPS
receiver modules to increases their robustness to DC pulses see section 2.5.6. Contact ViaLite
Communications for more details.
2.6.3 Logic interface, TTL 5V
Absolute maximum voltage rating -0.5 to +5.5V No damage
Input, Logic Low (max) <0.8V
Input, Logic High (min) >2.0V
Output, Logic Low (max) <0.4V no load
Output, Logic High (min) >4.8V no load
Drive capability 1k ohms
Short circuit protection No
TX
J4 (LNB)
up = external
down = internal
open = not connected
RX
up =
J10 (BUC)
up = external
down = internal
open = not connected

HRX-C-HB-1 C-BAND LINK HANDBOOK
20
2.6.4 Logic interface, I2C
Absolute maximum voltage rating -0.3 to +5.3V No damage
Input, Logic Low (max) <1.5V
Input, Logic High (min) >3.5V
Output, Logic Low (max) <0.6V no load
Output, Logic High (min) >4.3V no load
Drive capability 1k ohms
Short circuit protection No
2.6.5 Logic interface, Open Drain, output
For details of operation see 2.6.3
Operational pull up voltage 0 to 15V No damage
Maximum load current 50mA
Short circuit protection No
Note: Negative voltage on the output will be clamped by the FET body diode; you must ensure that
these do not exceed current rating.
Note: When fitted in a chassis with a controller card (i.e. SNMP and web controller or summary alarm
card) the alarm lines maybe loaded and pulled up, see chassis handbook
Note: When fitted in a chassis or enclosure adjacent to a RF switch or RF splitter card, alarm lines
maybe loaded and pulled up, see chassis handbook
2.6.6 Power interface, +12V, input
Nominal input voltage 12V
Maximum operational voltage range 11.5 to 13V
2.6.7 Analogue interface, laser diode bias, output
For details of operation see 2.6.7
Typical output voltage 1.25V for 50mA bias current
Typical output voltage range 0 to 2.5V
Maximum output voltage range -5 to +5V
Short circuit protection No
2.6.8 Analogue interface, photodiode received light level, output
For details of operation see 2.6.8
Typical output voltage 4.0V at 10 dBm optical input power
Typical output voltage range 1 to 4V
Maximum output voltage range 0 to +5V
Short circuit protection No
Table of contents
Other PPM Control Unit manuals
Popular Control Unit manuals by other brands
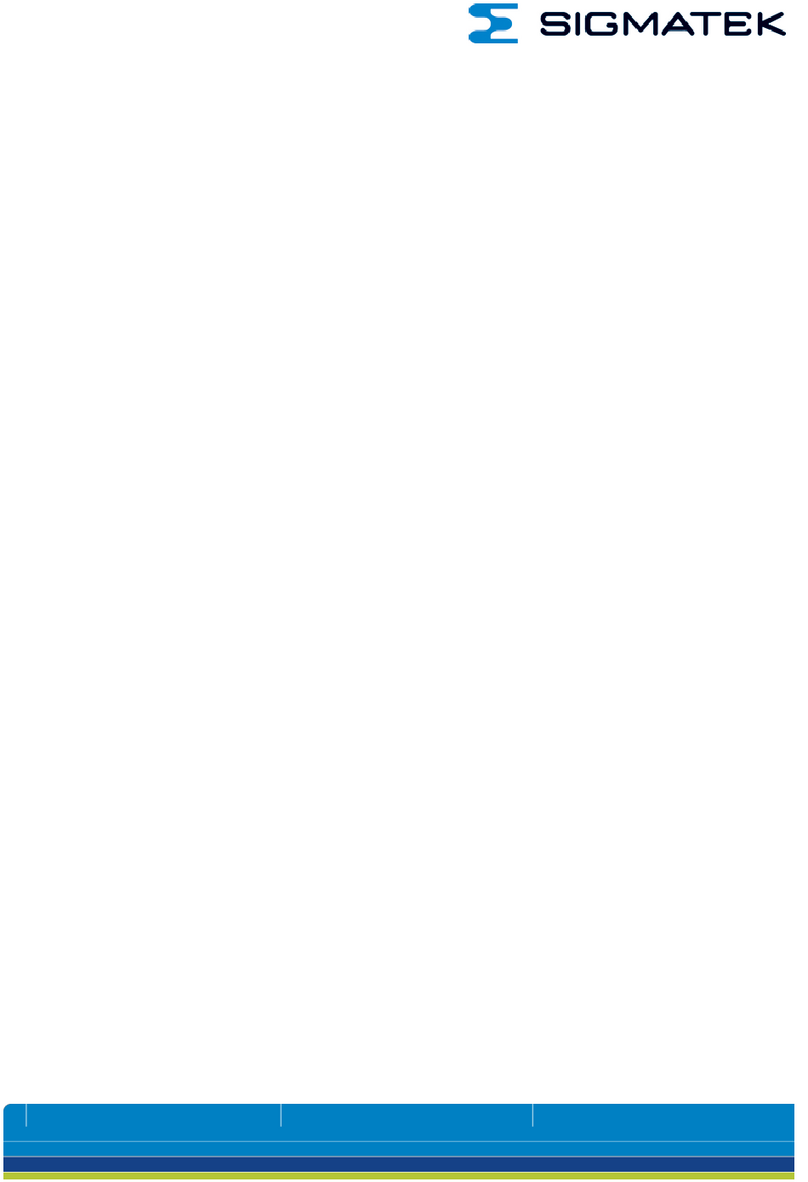
SIGMA TEK
SIGMA TEK AM 222 instruction manual

Murrelektronik
Murrelektronik IMPACT67-P instruction manual
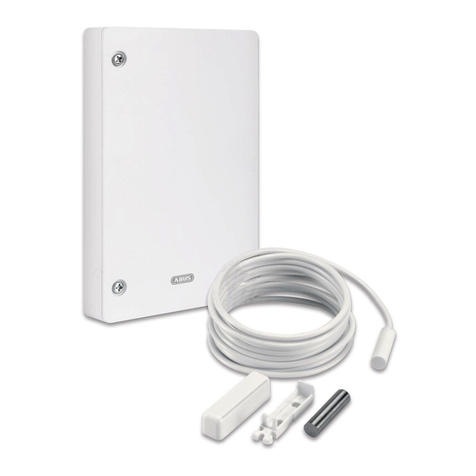
Abus
Abus FUMO50110 Installation instructions and user guide

3One data
3One data NPM301 Hardware manual

BOSSCO
BOSSCO 355AA DN15 manual

Proportion-Air
Proportion-Air QBS Series Installation & maintenance instructions