preVent ZSN1 User manual

ZSN1 Instruction Manual

2
Contents: Seite
Introduction 2
1. Regulator operation 3
2. Technical specification 3
3. Service conditions 5
4. Installation 5
5. Starting up 6
6. Handling 6
7. Maintenance and repair 7
8. Troubleshooting 8
9. Safety conditions 8
10. Utilization 8
11.
Spare part list 8
12. Drawings 9
13. Additional items 10
14. Contacting us 11
To ensure trouble-free and safe operation of the valve, it is essential to be familiar with the contents of this
ZSN1 Instruction Manual, and also with the general instructions for installation and operation, before installing
and operating the valve.
Failure to observe or comply with these operating instructions will invalidate the manufacturer’s guarantee and
liability. The manufacturer’s general conditions of sales and terms of delivery shall apply unless otherwise
stated.

3
1. REGULATOR OPERATIONS
The regulator combines three main units: (fig.5) valve (01), actuator (02) and adjuster (03).
The valve of the regulator is single ported valve with balanced plug. Two options the actuator is available: diaphragm spring-
loaded actuator (80 cm2) with clamped cases and diaphragm spring-loaded actuator (160 cm2) with cases jointed with bolts.
The adjuster of controlled pressure is mounted axially along with the valve and actuator. The pre-set spring tension is
already adjusted (60, 61, 62). The valve of the regulator is of fail-to-open type. The controlled pressure is delivered to the top
of actuator's (02) diaphragm through connection pipes and the shut off valve (24). The second chamber of the actuator is
vented to atmosphere with venting plug (25). As pressure increases and exceeds the pre-set adjuster's (03) spring tension
(60, 61, 62), the diaphragm is pushed down which results in changing the position of stem (37) and closing the valve with
plug (5) until the pressure reaches the pre-set level. The control pressure should be sampled downstream from the
regulator. The shut off valve (24) enables either choking or shutting off of the control pressure. It also vents the actuator's
chamber as well as protects actuator's diaphragm against hydraulic strokes.
2. TECHNICAL SPECIFICATION

4

5
3. SERVICE CONDITIONS
Following requirements must be met to provide reliable pressure regulator operation:
Prior to mounting the valve to the piping , the pipe should be thoroughly cleaned from dirt, rust, rolling and welding scale
and other foreign bodies.
Fit a FS 1 strainer upstream of the regulator
Don't fit the product which appears to be damaged while shipped or stored.
Damages should be repaired and the product should be inspected prior to start-up.
Remove shipping plugs, make sure that the valve is free of dirt and foreign bodies inside.
Make sure that the ambient temperature range is from -25 to 80°C
Clean the filter pack periodically.
Inspect the regulator at least once a year and remove internal impurities if necessary.
4. INSTALLATION
The regulator is designed to be fitted with flange connection. The adjuster should be in vertical position. Acceptable angle
deviation is 30°. It is necessary to direct the adjuster downward if the fluid temperature exceeds 100°C. If it is necessary to fit
the regulator in horizontal position, additional mounting bracket will be required.
The regulator should be fitted into the pipeline together FS-1 strainer, which should be mounted by the regulator's inlet
flange according to marking indicated at bodies of valve and strainer.
The minimal straight pipeline section should be at least five times longer downstream and upstream then the regulator's
valve diameter.
Both regulator and strainer should be protected against welding scale
The 6x1 copper connection pipe should be connected to actuator's chamber through shut off valve. Using connectors,
fittings and pipes of extensive length should be avoided due to their resisting features.
A pressure gauge should be mounted next to pressure sampling point.
It is necessary to mount a conditioning tank (fig. 4) for steam applicationat 150-200°C. Both tank and actuator's chamber
should be filled with water. Otherwise the diaphragm and actuators sealing would be damaged.

6
5. STARTING UP
During the mounting of the regulator, the shut off valve (24) should be closed tightly by the right turning the stem (see fig. 3
item. 2).
The pre-set adjuster (03) spring tension should be the smallest. As the connecting pipe is connected, open the shut off valve
so the fluid supply actuator's chamber.
Close the pressure shut off and loosen the screw plug (32) to vent the chamber. Tighten the screw plug until leakage stops
and open the shut off. According to the pressure level indicated on gauge set the desired pressure level tuning the adjuster's
(03) springs tension with screw (68). As the tension setting is verified, affix a seal to screw (68) using the appropriate
openings. The dynamic performance of the regulator is changed by controlling the flow of shut off valve (24).
6. HANDLING
On completing a start-up and adjusting no further service is necessary except periodical cleaning of the strainers pack.

7
7. MAINTANANCE AND REPAIR
As long as the warranty is not expired it is admissible only to adjust the springs' tension and eliminate diaphragm leakages
(29) by tightening actuator's (02) housing bolts.
Repair and maintenance service include:
- replacing the soft seat (2b)
- replacing the plug gasket (7)
- replacing the actuator's diaphragm (29) and stem sealing (33, 35).
7.1 REPLACING THE SOFT SEAT.
If the soft seat occurs to be leaky, proceed as follows:
a) shut off the fluid flow
b) close the shut off valve (24) and remove the connection pipe from the actuator unit
c) remove nuts (11) that fasten the pressing plate (3) and valve body (1)
d) Remove the actuator with the adjuster, the pressing plate (3) and the plug (5)
e) Remove the guiding sleeve (4) from the valve body (1)
f) Unscrew the seat using special seat wrench. Clean thoroughly the thread and areas where valve body contacts the seat.
g) Sealing/antiseizing compound (e.g. LOCTITE 767) should be applied to the threads prior to screwing the seat.
To reassemble, proceed in the reverse order. It is necessary to replace the bodygasket (9).
7.2 REPLACING THE BALANCED PLUG GASKET (7)
If it is necessary to replace the gasket of balanced plug, proceed as follows:
a) Follow the 7.1 a,b,c,d,e
b) Lift the connector (6) with plug until perpendicularly to the stem (37). Split stem and connector.
c) Unscrew the plug (5) form the connector (6).
d) Remove plug gasket (7) and put a new one.
To reassemble, proceed in the reverse order. Keep the same connection length for connector (6) and plug (5) as it was
before disassembling. Replace the body gasket (9).
7.3 REPLACING ACTUATOR'S DIAPHRAGM AND STEM SEALING.
If it is necessary to replace actuator's diaphragm (29) or/and stem sealing (33,35)of the actuator's stem (37), proceed as
follows:
a) Shut off the fluid flow remove the connection pipe.
b) Unfasten the adjuster's (03) screw, spring tension should be set at minimal level.
c) Unscrew both spring unit (60, 61, 62) and the screw (68) simultaneously to remove adjuster unit (03).
d) To separate actuator's stem (37) and screw (68) move sleeve (59) towards actuator and disconnect connector (58) and
ring (63).
e) Unscrew nut (31)
f) Unscrew nuts (11) and remove actuator unit (02) with all housing and plug (5) from the valve (01)
g) Lift the connector (6) with plug until perpendicularly to the stem (37). Split stem and connector.
h) Unscrew nuts (39) and disassemble bottom (18) and top actuator's housing.
i) Unscrew nut (26) and remove diaphragm plate (28) and used diaphragm (29).
j) Unbolt screw plug (32) and renew stem sealing (33, 35).
To reassemble, proceed in the reverse order. Renew gasket (9). Apply threadlocker (e.g. LOCTITE 243) to threaded
connection between adjuster and actuator units. Apply silicon based sealing compound UNISILIKON L50/ 2 to actuator's
stem, plug and guiding face of regulating screw. Apply antiseize LOCTITE 767 compound to thread of regulating screw.

8
8. TROUBLESHOOTING
a) Diaphragm housing (19) leakage:
- fasten the housing bolting,
- Replace the diaphragm (29) with a new one,
b) Stem or body gasket (9) leakage:
- Install new gaskets,
c) soft seat leakage:
- remove foreign matter from the inside of valve body,
- Install a new seat,
d) The regulator's erratic control
- inspect control pipes and shut off valve for clogging and clean them if necessary
- Install new diaphragm if damaged
- Inspect the lock connector (6, 8) for correct connection.
The stem (37) will relock as pressure is applied to diaphragm from the adjustor (03) side.
9. SAFETY CONDITIONS
Observe following rules for safe regulator service:
• Prior to removal the regulator from the pipeline or dismounting parts contacting the process fluid, make sure the parts are
not pressurized with the process fluid.
• Adjuster's springs are initially tensioned. The design of actuator protects them from full extension. For safety reasons
protect springs while they are being removed.
• If the conditioning tank is applied, it should be periodically inspected and refilled with water. The regulator should be
vertically oriented with the adjuster directed downward. The conditioning tank should be installed higher than actuator's
chamber to prevent the installation from aeration of and water outflow.
10. UTILIZATION
When the valve life time ends it is necessary to disassembly it. All parts should be segregated according type of material:
metal parts (non ferrous metals, stainless steel, carbon steel), rubber (diaphragms, gaskets) and plastics (packing, plastic
plugs, cable enters). These materials should be recycled according to rules for this kind of materials. The valve does
not contain any materials that are dangerous for the natural environment after the process of utilization.
11. SPARE PARTS
Basic spare parts: diaphragm (29), soft seat (2b), sealing components of plug (7) and stem (33, 35), valve body gasket (9).
Other spare parts of regulator are also available for customer request. The request should include regulator's specification:
type, size, spring range, Kvs rating and the part's name and number according to fig. 5

9
12.
DRAWINGS

10
13. ADDITIONAL ITEMS
Attached items:
• A nut and locking ring for connecting pipe/
Optional items for request:
• FS 1 strainer
• Connector for Ø 6 x 1 pipes
• Threaded fitting 1/4" NTP
• Ø 6 x 1 connection pipe
• Shut off valve
• Calibration wrench
• Seat wrench
• Conditioning tank

11
PRE-VENT GmbH
Sales - Production - Service
Piracher Straße 74
84489 Burghausen, Germany
fon +49 8677 98788-0
fax +49 8677 98788-80
Email:
Web: www.pre-vent.com
Manual version 1.1 07.11.2019
14. CONTACTING US
Details / specific information (Operating instructions with spare parts lists) are available for download on our website.
Table of contents
Other preVent Control Unit manuals
Popular Control Unit manuals by other brands
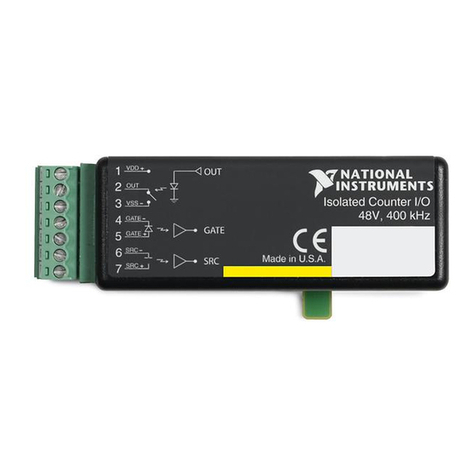
National Instruments
National Instruments SCC-CTR01 USER GUIDE AND SPECIFICATIONS
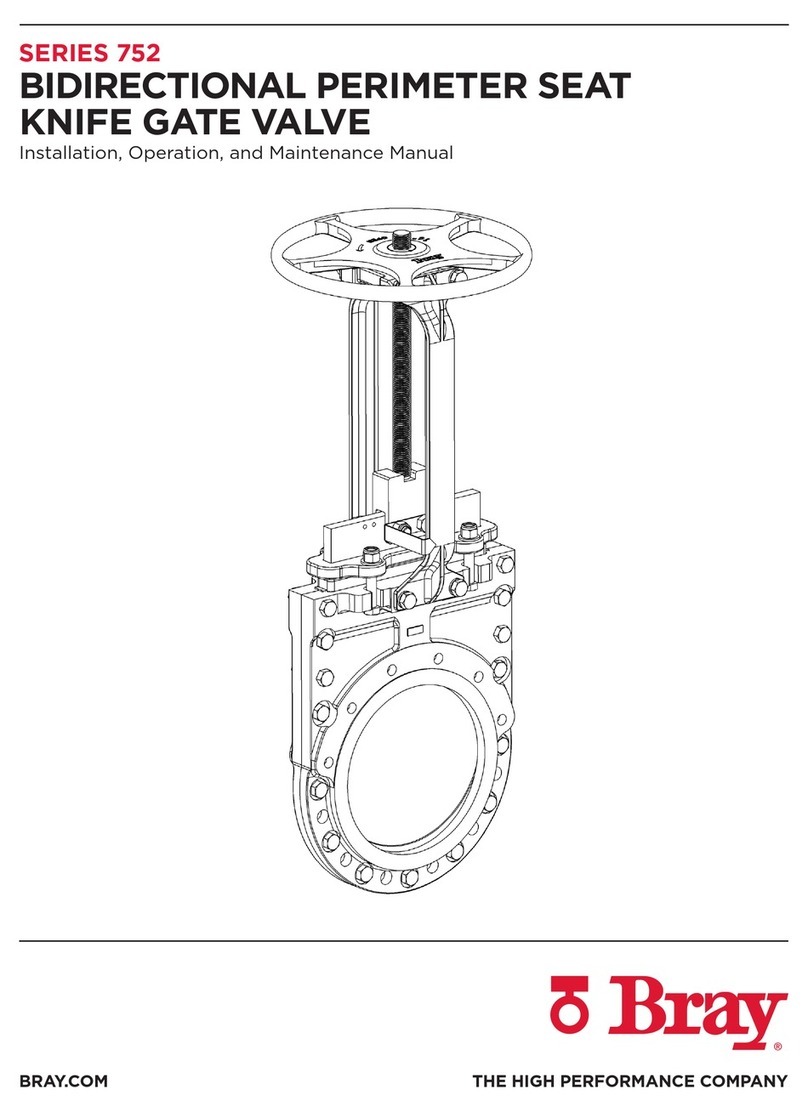
Bray
Bray 752 Series Installation, operation and maintenance manual

Trenz Electronic
Trenz Electronic TE0712 200 2C10 Series Schematics
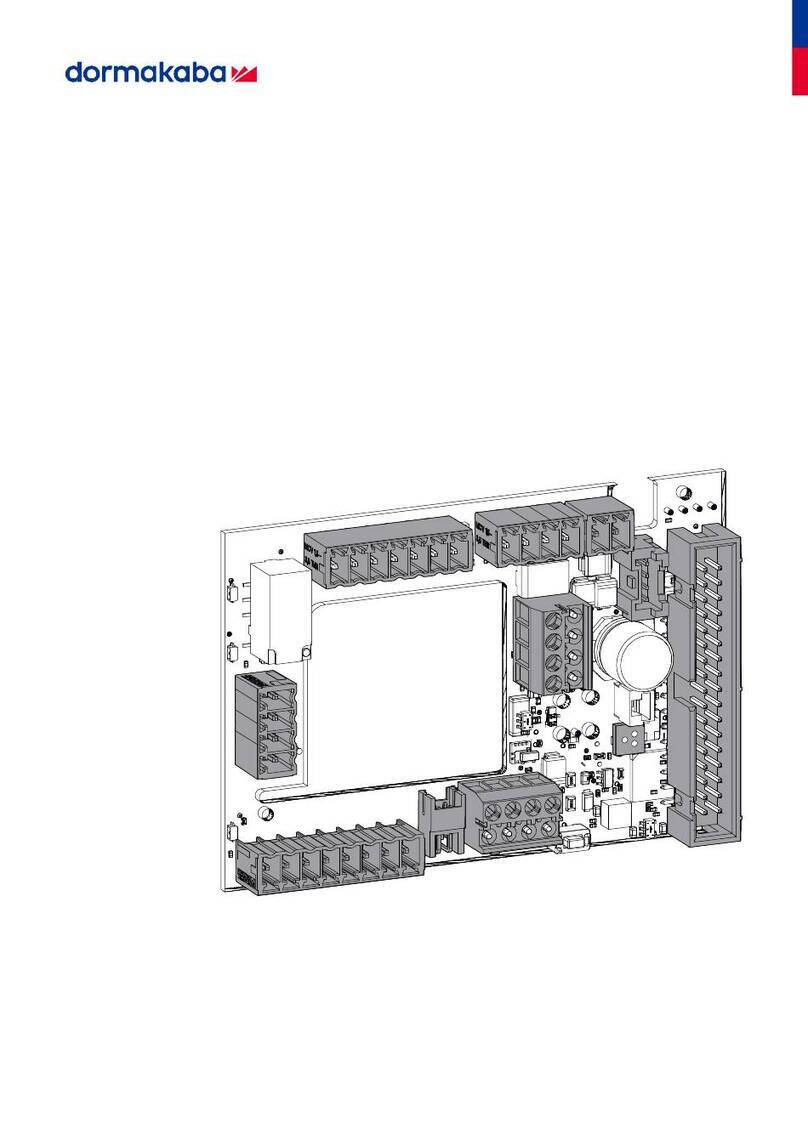
Dormakaba
Dormakaba ED connection board CAN Assembly instruction

Intelligent Appliance
Intelligent Appliance IA-2104-U user manual

Gan Systems
Gan Systems GS-EVB-HB-66508B-RN Technical manual