Prinzing ESC300 User manual

OPERATING INSTRUCTION
ESC300
Electronic Control Comfort
Read this operating instruction with care before
commissioning!

2
Date: 20-11-2014 Data name: esc300-2-v12a_EN ESC300 (swv-1.06)
Author: Heiko Lange Pages: 72 © P. Prinzing GmbH - 89173 Lonsee-Urspring (Germany)
Service: +49 (0) 7336 - 961018 * Option / depends on design
INFORMATION
The figure- and graphic expositions in this operating instruction might deviate partially a
little from your control, by viture of technical modification!
All features, components or parts marked with a * are options or accessories and because
of that not available on each control! Instructions and descriptions for extensions, addi-
tional equipment and -functions you can find enclosed to this operating instruction.
Please read this operating instruction with care before commissioning.
Keep this instruction with care for further assignment!
Service-Address
Before contacting our service note down the following...
- the specific name and model of the machine (name plate)
- the serial number of the machine (name plate)
- the displayed error message
In case of malfunctions and technical problems:
Phone: +49 (0) 7336 - 961018 or E-mail: [email protected]
For spare parts orders:
Phone: +49 (0) 7336 - 9610-0 • Fax: +49 (0) 7336 - 961050 • E-mail: [email protected]
Postal address: Peter Prinzing GmbH - Siechenlach 2 - 89173 Lonsee-Urspring, Deutschland
Or contact your local dealer.
Your customer number
(see invoice/delivery note) Serial number
(see name plate on the control)
------------------------------------- -------------------------------------

3
Date: 20-11-2014 Data name: esc300-2-v12a_EN ESC300 (swv-1.06)
Author: Heiko Lange Pages: 72 © P. Prinzing GmbH - 89173 Lonsee-Urspring (Germany)
* Option / depends on design Service: +49 (0) 7336 - 961018
Table of contents
1. Before using ...................................................................................................................................................... 6
1.1. Copyright .........................................................................................................................................................6
1.2. Intended using .................................................................................................................................................6
1.3. Used characters and symbols .........................................................................................................................7
1.4. Defi nition: ........................................................................................................................................................ 7
1.5. Overview components of the electronic control Comfort ESC300 .................................................................. 8
1.6. Functions of the electronic control Comfort .....................................................................................................9
2. Assembling and connection .......................................................................................................................... 10
2.1. Assembling the control ESC300 ...................................................................................................................10
2.2. Assembling the charge ESC300 ................................................................................................................... 11
2.3. Assembling the radio module ........................................................................................................................ 11
2.4. Assemble the control Expansion for alley 4 - 6 ............................................................................................. 11
2.5. Assemble the temperature sensor ................................................................................................................ 11
2.5.1 Assembling example for the control and its components ..............................................................................12
2.6. Electrical connection ..................................................................................................................................... 13
2.6.1 Cable types, line length and cable cross section .......................................................................................... 14
2.6.2 Connection of the electronic control - ESC300 ............................................................................................. 15
2.6.3 Connection expansion module - EXP300 .....................................................................................................15
2.6.4 Connection of the charging station ESC300 Charge ....................................................................................16
2.6.5 Connection optional equipment (end switch, push button, signal transmitter) .............................................. 16
3. Safety ............................................................................................................................................................... 17
3.1. General safety advices ..................................................................................................................................17
3.2. Behaviour in danger situations ......................................................................................................................17
3.3. Danger areas of the dung removal system ................................................................................................... 18
3.4. Danger by electric energy ............................................................................................................................. 18
3.5. Unattended operation (automatic) of the dung removal system ................................................................... 19
3.6. Danger of self-depended starting scraper .....................................................................................................19
3.7. Attach warning- and information signs .......................................................................................................... 19
4. The radio controlled remote ESC300 ............................................................................................................ 20
4.1. How to use the remote ESC300 ....................................................................................................................21
4.2. Display messages during the „operation mode“ ............................................................................................22
4.3. Display messages during the „setting mode“ ................................................................................................ 23
5. Commissioning ............................................................................................................................................... 24
5.1. Switch on the control ..................................................................................................................................... 24
5.2. Set language - date - time .............................................................................................................................24
5.3. Switch off or on again the alleys....................................................................................................................25
5.4. Commissioning of one alley .......................................................................................................................... 25
5.4.1 Chose motor type (nominal capacity) ............................................................................................................26
5.4.2 Do the motor test (rotating direction) ............................................................................................................27
5.5. Do the program „learning“ ............................................................................................................................ 27
5.6. Programs on the control ................................................................................................................................29
5.6.2 Program 1 (P1) - description ......................................................................................................................... 30
5.6.1 Program 2 (P2) - description ......................................................................................................................... 30
5.6.3 Program 3+4 (teaching) - description ............................................................................................................31
5.6.4 Set starting times in the schedule (Timer) .....................................................................................................33
6. Extended functions .........................................................................................................................................34
6.1. Function drive ................................................................................................................................................34
6.1.1 Connect signal device for „drive“ ...................................................................................................................35
6.2. Function slatted fl oor .....................................................................................................................................36
6.3. Function frost mode ......................................................................................................................................37
6.3.1 Set the parameters for the frost mode ..........................................................................................................38
6.3.2 Set the frost mode for an alley ...................................................................................................................... 39
6.4. Set the obstacle detection ............................................................................................................................. 40
6.5. Parking position .............................................................................................................................................41
6.6. Start the cross transport automatically ..........................................................................................................42

4
Date: 20-11-2014 Data name: esc300-2-v12a_EN ESC300 (swv-1.06)
Author: Heiko Lange Pages: 72 © P. Prinzing GmbH - 89173 Lonsee-Urspring (Germany)
Service: +49 (0) 7336 - 961018 * Option / depends on design
Original operating instruction
The German layout of this document is the original operating instruction.
Translation of the original operating instruction
All non german layouts of this document are translations of the original operating instruction.
Operating instruction ESC300
Version: 12b
Valid from software version control 1.12
© 2014
7. Operation with the ESC300 ............................................................................................................................ 43
7.1. Manual operation with the electronic control ESC300 ..................................................................................43
7.2. Automatic operation with the electronic control ESC300 .............................................................................. 44
7.2.1 Automatic operation by schedule (Timer) ...................................................................................................... 44
7.2.2 Automatic operation by frost mode ...............................................................................................................45
7.3. Operation of the control by external push button* ......................................................................................... 45
7.4. Switch over and off the scraper move by the end switch* ............................................................................. 45
8. Service ............................................................................................................................................................. 46
8.1. Change parameters and program settings ....................................................................................................46
8.1.1 Change the learned breaking current ............................................................................................................ 47
8.1.2 Change parameter program 2 (P2) ............................................................................................................... 48
8.2. Display system information ........................................................................................................................... 50
8.3. Do a system diagnosis .................................................................................................................................. 50
8.4. The signal output „cross transport“ and „error“ ............................................................................................. 51
8.5. The tension control ........................................................................................................................................52
8.6. Die SD-card (data saver) .............................................................................................................................. 52
8.6.1 Insert/extract the SD-card ............................................................................................................................. 53
8.6.2 Save parameters (export) ............................................................................................................................. 53
8.6.3 Load parameters (import) ..............................................................................................................................54
8.6.4 Logging on the SD-card ................................................................................................................................ 55
8.6.5 Software-Update with a SD-crad ...................................................................................................................55
8.7. Failure and error deletion .............................................................................................................................. 56
8.7.1 Error messages on the display - cause and deletion .................................................................................... 56
8.7.2 Error codes ....................................................................................................................................................57
8.7.3 Info messages (display glows yellow) ........................................................................................................... 58
8.7.4 Errors during the operation (display glows red) - cause and deletion ........................................................... 58
8.7.5 Further errors ................................................................................................................................................ 59
8.8. Batteries on the remote - care and replacement ........................................................................................... 60
8.9. Factory provided (Reset) ...............................................................................................................................61
9. Factory provided parameters ........................................................................................................................62
10. Disassembly and Disposal.............................................................................................................................63
11. Technical data ................................................................................................................................................64
12. Explorer menu ESC300 ..................................................................................................................................65
Electrical installation plan
Electrical connection plan

5
Date: 20-11-2014 Data name: esc300-2-v12a_EN ESC300 (swv-1.06)
Author: Heiko Lange Pages: 72 © P. Prinzing GmbH - 89173 Lonsee-Urspring (Germany)
* Option / depends on design Service: +49 (0) 7336 - 961018
einbauerkl_esc3_eng.indd - 2014-11-20
Declaration of Incorporation
Corresponding the EC-directive machines 2006/42/EC, annex II, no. 1 B
Herby we declare, that the undermentioned Dung Removal System including the parts belonging to and mounted parts
are corresponding to the primary safety and healthy requirements of the EC-Directive 2006/42/EC in their conception and
construction in the version market by us. Is is only allowed to commission the Dung Removal System, when it is sure, that
the Dung Removal System corresponds to the regulations of the EC-directive machines 2006/42/EC.
Manufacturer:
Peter Prinzing GmbH Phone +49 (0) 7336 / 9610-0
Siechenlach 2 Internet: www.prinzing.eu
Description:
Type/Model: Electronic Control Comfort - ESC-300
Consisting of: Box incl. 1x Control and up to 2x Relay, 1x Remote, 1x Charge, 1x Radio Module
Expandable with: EXP-300 with up to 3x Relay, additional radio module
Function: Control of up to 12 drive winches for a Wire Rope Dung Removal System
Serial-Number: See name plate
It explains the compliance with further following for the product applicable policies, regula-
tions and standards:
- EMV-directive: (2004/108/EC) dated 15. December 2004
- Transient emissions: EN 55011:2009 + A1:2010 class B
EN 61000-6-3:2007 + A1:2011
EN 61000-6-4:2007 + A1:2011
- Interference resistance: EN 61000-6-2:2005
The special technical documents corresponding annex VII B were created. They will be forwarded to the competent national
authority to a reasoned request in electronic form or by post.
Authorised person for the technical documentation:
Heiko Lange
Siechenlach 2
89173 Lonsee-Urspring (Germany)
Phone.: +49 (0) 7336 / 961018
Place/Date:
Lonsee-Urspring, 16.02.2012
Information to the authorized person for issuing this declaration:
Peter Prinzing, Manager
Signature:
Einbauerklärung

6
Date: 20-11-2014 Data name: esc300-2-v12a_EN ESC300 (swv-1.06)
Author: Heiko Lange Pages: 72 © P. Prinzing GmbH - 89173 Lonsee-Urspring (Germany)
Service: +49 (0) 7336 - 961018 * Option / depends on design
Before using
1. Before using
INFO
Please read this operating instruction with care before mounting and assembling the control
ESC300. Thereby you are able to avoid errors during the assembling/operation and you can
learn to use the characteristics and the functions of the ESC300 control in an optimal way.
If you have questions concerning the function or how to operate with the control, please
contact our service or your local dealer.
1.1. Copyright
The copyright for this installation and operating instruction belongs to the PRINZING Company. It is not allowed, neither
entire, nor partially duplicate it, publish it or for unauthorized using in function of competition, and not to inform others.
Deliberate infringements against this will be prosecuted.
1.2. Intended using
The „Electronic Control Comfort“ is only allowed to be used, to control drive winches for wire rope dung removal systems.
It is not allowed to use the comfort control for other operation purposes. Without a written approval of the Peter Prinzing
GmbH, it is not allowed to use the electronic control Comfort with other motor types or drive winches as stated in the techni-
cal data or an using which not correspondents with the stipulations.
The operator of the comfort control has to know how to work with the control and about the possible risks. Inform yourself
on this in the current legal regulations and stipulations, in the operating instruction or at the Peter Prinzing GmbH.
It is only allowed to use special equipment and additional controls with the comfort control which are stated in the order
confi rmation or in the technical data.
Not allowed are arbitrary rebuildings and variances on the electronic control comfort because of safety related reasons!
Changes on the hard- or software of the control are not allowed without permission of the Peter Prinzing GmbH.
ATTENTION!
If the electronic control Comfort is not used according to regulations, a secure operation
can not be ensured. Improper use must be avoided.
Not the manufacturer but the operator is responsible for personal injury and property
damage, which results of misapplication!

7
BA =
(x) =
/ =
=
=
=
=
1. Text =
- Text =
>>> Text =
Date: 20-11-2014 Data name: esc300-2-v12a_EN ESC300 (swv-1.06)
Author: Heiko Lange Pages: 72 © P. Prinzing GmbH - 89173 Lonsee-Urspring (Germany)
* Option / depends on design Service: +49 (0) 7336 - 961018
Before using
1.3. Used characters and symbols
In this operating instruction there might be the following symbols:
Operating instruction
The numbers in the brackets refer to the details of the pictures aside
Preceded number refers to the fi gure aside
Function available only after login (setter or service personnel)
Information - important information, tips and information for the operation
Attention - important information about the safety of the operating personnel and the machine
Description/explanation of technical terms and designations
Sequence
Numeration
Sequence of an act
1.4. Defi nition:
Drive winch
Motor driven drum to coil the drag rope, to pull a scraper over the walkway
Drive unit
A drive unit consists of two drive winches (optional one double winch) and is used to drive min. one dung scraper.
Alley
Means the walkway (optional two walkways) on which minimum one dung scraper is moving by a drive unit.
Home position
The position of the scraper, from where the automatic scraper drive starts and ends.
Teaching
Manual learning of a program cycle by order input on the remote during the scraper drive
Interval time
Time between the end of the last scraper drive and a new starting command
Parking position
Position of the scraper, to where the scraper moves after the end of the program 2. Thereby the scraper is parking in a
distance to the end stop. INFORMATION! - Parking position is not home position! Consider the description on page 41
Cyclic operation
The move of the scraper happens stepwise (drive - pause - drive - pause - and so on)

8
Date: 20-11-2014 Data name: esc300-2-v12a_EN ESC300 (swv-1.06)
Author: Heiko Lange Pages: 72 © P. Prinzing GmbH - 89173 Lonsee-Urspring (Germany)
Service: +49 (0) 7336 - 961018 * Option / depends on design
Before using
1.5. Overview components of the electronic control Comfort ESC300
The electronic control Comfort ESC300 consists of the following components:
(1) Basic unit ESC300 with
- 1x power supply
- 1x board Control with processor, SD-slot and software for the control. Inclusive connection for one alley with up
to 2 drive winches.
- up to 2x board relay to extend the control with one alley with each 2 drive winches
(2) ESC300 EXT-radio >>> external transmitter- and receiver module for the communication between the Remote
and the Control, wired. To strengthen the des radio signal, it is possible to connect max. 2 radio modules (in
series or parallel)
(3) ESC300 Remote >>> remote with display for settings and to operate with the control,
(4) ESC300 Charge >>> charging station inclusive power supply for the operating control „ESC300 Remote“
(5) EXP300 Expansions module >>> expansion for the system for alley 4 to 6. Consisting of max. 3x board relay
(6) Emergency stop button (min. 1x per alley)
(7) Temperature sensor
Optional equipment:
(8) External quadruple pushbutton per alley, wired, functions: start - stop - forward - backward
(9) End switch on the end of the walkway >>> for mechanical switch over and off of the scraper drive at the end of
the alley

9
Date: 20-11-2014 Data name: esc300-2-v12a_EN ESC300 (swv-1.06)
Author: Heiko Lange Pages: 72 © P. Prinzing GmbH - 89173 Lonsee-Urspring (Germany)
* Option / depends on design Service: +49 (0) 7336 - 961018
Before using
1.6. Functions of the electronic control Comfort
By the electronic control Comfort you are able to regulate the sequence and the functionality of your dung removal system.
By the control, the motors and the rope winches will be activated and monitored. It is possible to control up to 6 drive units
(alleys), independently of each other.
The check on the scraper movement happens by voltage- and time monitoring of the single motors.
Settings and operation with the control happens by a remote with graphic display. The control of the dung removal system
can be manual or automatically.
The manual control happens directly by the push button (on the remote or external push button*). Thereby the scraper can
be moved forward or backwards and the automatic can be started or stopped.
The automatic mode (automatic) of the control can be started manual, auto-scheduled by a timer or temperature-controlled
by a temperature sensor. During the automatic, it is possible to choose between 4 programs, which program have to start
automatically. These 4 programs are...
- Program 1 (P1) with standard sequence (forward/backward)
- Program 2 (P2) with predefi ned settings (animal detection and cyclic operation before the drop down/end)
- Program 3+4 (P3, P4) individual programmable programs by teaching² (scraper move free adjustable)
Additional there are the following functions on the control:
- Automatic detection of the connected drive units
- Voltage control and auto correction of the breaking currents when there are voltage fl uctuations (e.g. when there is a
photo voltaic -system)
- Manual deactivating of drive units (alleys) without data loss
- Automatic program start by a time table (timer) with 24 starting times/alley
- Antifreeze and freeze protection ba an automatic program start when the temperature falls below a value (freeze
operation)
- Automatic adjustment of the starting intervals during the freeze operation when the temperature falls/increases
- One way operation per each starting impulse for walkways with slatted fl oor
- Using the scraper as a cow driver by manual auto scheduled operation by the function „drive“
- Signal output for an additional control (e.g. cross transport)
- Journal function, update and data backup with SD-memory card
- Emergency operation in case of system failure by manual control of the scraper by a push button on the board
TIP
By elongation, dirt or one side coiling of the traction rope on the drum, the position of the
scraper may change slightly. For an accordingly function of the scraper system you should
mount min. one scraper stop (on the home position). Thereby it is possible to reference the
scraper position of each drive.
We would not recommend a operation without even one scraper stop. If you want to reduce
the load of the traction rope by a scraper stop, use the end switch to switch over or -off the
scraper drive.
One drive unit (for one walkway) consists of
- Minimum 1 scraper
- Maximum 2 wire rope winch
The drive unit will be described as alley in the operation instruction!
Teaching = Manual learning of a program cycle by order input (forward - backward - stop) on the remote during the
scraper drive.

10
Date: 20-11-2014 Data name: esc300-2-v12a_EN ESC300 (swv-1.06)
Author: Heiko Lange Pages: 72 © P. Prinzing GmbH - 89173 Lonsee-Urspring (Germany)
Service: +49 (0) 7336 - 961018 * Option / depends on design
Assembling and connection
2. Assembling and connection
INFO
Consider during the assembling, that there is a stable radio connection between the
control and the Charge with the remote.
The radio connection depends on the environment of the system. Armoured concrete
walls, metal matrix, steel beams, fodder mixing wagons or other obstacles might attenuate
the signal!
Consider the following points when mounting the components (equipment).
- Mount the control on a central, accessible place on a level surface.
- Into the feed line has to be mounted a main switch in a striking distance to the control.
- The charge module with the remote can be mounted independent to the position of the control ESC300 (e.g. in the
stall).
- Mount the external radio module as central as possible in the operation area of the dung removal system, in a height
of min. 2,5 m. Armoured concrete walls and metal structures might attenuate the signal!
- The equipment should not be exposed to extremely heat, cold or extreme thermal fl uctuations.
- Protect the equipment of splash water or direct insolation.
- Mount all necessary screwing (enclosed) and close after assembling all coverings and not used openings on the
equipment.
- If it is possible, mount the emergency stop button unapproachable for the animals (possible errors), viewable and ac-
cessible. According to the local conditions, you have to mount several emergency stop buttons.
- Use only allowed cables and lines and do not exceed the maximum length of the lines.
- Remove the battery protection fi lm on the backside of the REMOTE before fi rst using (pull the protection fi lm out of
the battery case!)
2.1. Assembling the control ESC300
Mount the control ESC300 by the delivered mounting straps (fi g. 10/2) on a fi rm
surface. Insert the cable only from the bottom of the control.
Connect on the control ESC300:
- Power feed line (400 V / 3~/PE, from the main switch).
- External radio module
- Motors rope winches for alley 1 - 3
- Emergency stop buttons
- Temperature sensor
- External push buttons* for alley 1 - 6
- End switch* (mechanical or inductive) for alley 1 - 3
- Contact for error messages*
- Contact for cross transport*
10/1
ESC300
Measurements: 400 x 300 x 180 mm
10/2
Mounting strap

11
Date: 20-11-2014 Data name: esc300-2-v12a_EN ESC300 (swv-1.06)
Author: Heiko Lange Pages: 72 © P. Prinzing GmbH - 89173 Lonsee-Urspring (Germany)
* Option / depends on design Service: +49 (0) 7336 - 961018
Assembling and connection
2.2. Assembling the charge ESC300
Mount the Charge in the radio range of the ESC300. Fix the Charge by the 4 fi xing
holes in the box.
Insert the cable for the power supply from below. On the Charge the Remote fi xed
and load.
On the ESC300 charge will be connected:
- A separate power feed line 230 V / 1~.
2.3. Assembling the radio module
Mount the radio module...
- in the centre of your range of movement with the remote, beginning from 2,5 m
height
- protected against clamminess as for example rain, splash water or similar
Do NOT mount the radio module...
- on armoured concrete walls or on steel structures or in a radius of approx. 1 m
to conducting metallic surfaces (cable lines, walls, doors)
- in direct range to other modules which are working with radio signals (WLAN
router, mobile phones, other radio stations)
Hereby you might have errors because of interference or electrostatic screen
Fix the radio module over the fi xing holes in the box in a way, that the cable inlet is
below. Cable-type and -length see .page 14
2.4. Assemble the control Expansion for alley 4 - 6
Mount the control Expansion EXP300 by the delivered mounting straps (fi g. 10/2).
Insert the cable only from below.
Consider the cable types and the max. length of the lines (see page 14)
On the control EXP300 will be connected:
- the power feed line (400 V / 3~ / PE, from the main switch).
- the data bus ESC300 <> EXP300
- the motors of the wire rope winch for alley 4 - 6
- End switch* (mechanical or inductive) for alley 4 - 6
2.5. Assemble the temperature sensor
You need the temperature sensor for the function „freeze operation“.
Mount the temperature sensor ground level and protected of direct insolation or
other heat radiation.
Consider during the assembling the maximum length of the line of 10 m.
11/1
ESC300 Charge incl. Remote
Meas.: 234 x 264 x 90 mm
11/3
EXP300
Meas.: 400 x 300 x 180 mm
11/2
External radio module
Meas.: 98 x 64 x 38 mm
11/4
Temperature sensor

12
4
1
2
3
5
5
AlleyCubicles
Waiting area
CubiclesAlley
Milking parlour
Engineering
room
Feed table
Date: 20-11-2014 Data name: esc300-2-v12a_EN ESC300 (swv-1.06)
Author: Heiko Lange Pages: 72 © P. Prinzing GmbH - 89173 Lonsee-Urspring (Germany)
Service: +49 (0) 7336 - 961018 * Option / depends on design
Assembling and connection
2.5.1 Assembling example for the control and its components
ATTENTION ! - The positions of the components are an example and not binding!
(1) Control ESC300 and main switch, for alley 4...6 you need an additional control EXP300
(2) ESC300 Charge with ESC300 Remote (accessible position in the stall for the operator)
(3) External radio module (height > 2,5 m)
(4) External push button* e.g. for the function „drive“
(5) Emergency stop button, mount minimum one emergency stop button per alley. We recommend a emergency
stop button round danger areas (e.g. wall openings, passages, drive winches), viewable and easy to mount .

13
Date: 20-11-2014 Data name: esc300-2-v12a_EN ESC300 (swv-1.06)
Author: Heiko Lange Pages: 72 © P. Prinzing GmbH - 89173 Lonsee-Urspring (Germany)
* Option / depends on design Service: +49 (0) 7336 - 961018
Assembling and connection
2.6. Electrical connection
The electrical connection of the control is only allowed to do by an authorized electronic specialist!
Inform yourself about the connected load of the control and the components before assembling. For the electrical connection
of the control and all of its components apply the current statutory provisions and operational stipulations (e.g. VDE 0100,
EN 60204-1/VDE 0113 part 1)
ATTENTION
Before connecting the control and during repair works on electric components of the
system switch the main switch of the control always on „0“ (OFF)!
Even when the main switch is switched off, the bushing clamps and the main switch are
energized!
Info
We assume no liability for damages resulting from wrong, unprofessional or non approved
electrical connections on the machine! To certificate a professional installation of the electric
system, the executing electrician has to provide an acceptance report / inspection sheet.
You can find an electrical connection plan for the control enclosed to this BA and in the
packing of the control.
Important information about the power supply of the control:
- The power supply for the entire control has to be lead over a shared main switch.
- It is not allowed to connect the feed line of the EXP300 directly to the ESC300. Connect the feed line of the EXP300
with the main switch, or use a conduit box.
- The charge will be connected self dependent from the control ESC300 (230 V/1~).
- Lines witch a cross section of max. 2,5 mm² can be connected (see scale page 14)
The following connected voltages are necessary for a failure-free operation:
- ESC300 (with control + relay) - 400 V / 3~/ PE / 50 Hz (no neutral wire)
- EXP300 (with relay) - 400 V / 3~/ PE / 50 Hz (no neutral wire)
- Charge - 230 V / 1~ / PE-N
Mount the emergency stop button:
Mount per walkway minimum one emergency stop button. By using several emergency stop buttons and an effective
positioning you are able to increase the safety of your dung removal system.
Mount the emergency stop buttons...
- on a accessible position, and also reachable for smaller persons (e.g. children)
- round danger areas (e.g. wall openings, gates, passages, dropping, drive winch)
- inaccessible for animals
ATTENTION!
If there is not minimum one emergency stop button connected on each alley, it is not al-
lowed to start the operation of the dung removal system!

14
Date: 20-11-2014 Data name: esc300-2-v12a_EN ESC300 (swv-1.06)
Author: Heiko Lange Pages: 72 © P. Prinzing GmbH - 89173 Lonsee-Urspring (Germany)
Service: +49 (0) 7336 - 961018 * Option / depends on design
Assembling and connection
2.6.1 Cable types, line length and cable cross section
Component Recommended
line type
Min.
number of
leads
Voltage Max.
length
Feed line (1) to the main switch NYM 5 x 1,5 (2,5) mm² 4 400 V / 3~ / 50 Hz ---
Feed line (1) to the ESC300 from the
main switch/ conduit box NYM 5 x 1,5 (2,5) mm² 4 400 V / 3~ / 50 Hz ---
Feed line (1) to the EXP300 from the
main switch/conduti box NYM 5 x 1,5 (2,5) mm² 4 400 V / 3~ / 50 Hz ---
Motor wire rope winch NYM 5 x 1,5 mm² 4 400 V / 3~ / 50 Hz 150 m
Emergency stop button (2) NYM 3 x 1,5 mm² 2 24 V DC 150 m
End switch mechanical (option) LiYCY 2 x 0,5 mm² ROHS 2 24 V DC 150 m
End switch proximity switch (option) LiYCY 3 x 0,5 mm² ROHS 3 24 V DC 150 m
External operating keys (Option) LiYCY 12 x 0,5 mm² ROHS 6 24 V DC 100 m
Temperature sensor NYM 3 x 1,5 mm² 2 5 V DC 10 m
Data bus Expansion LiYCY 5 x 0,5 mm² ROHS 5 24 V DC 5 m
Radio module (4) LiYCY 8 x 0,5 mm² ROHS 8 24 V DC 100 m
Transmitter / cross transport NYM 2 max. 250V-AC/4 A
max. 24V-DC/1 A ---
Safety shutdown board (3) - optional
(release cable from the control) NYM 3 x 1,5 mm² 2 24 V DC
see
emergency
stop
Type of terminals on the control Power supply + motors: plug-in screw AKZ 950 (PTR) max. 2,5 mm²
24V-lines: spring pressure terminal block Wago 250-503506 max. 1,5 mm²
Consider the following information about the list:
(1) Defi ne the cable cross section corresponding the motor power and the length of the line. If necessary mount a
conduit box after the main switch, to separate the feed line of the ESC300 and the EXP300.
(2) Emergency stop button - we recommend to mount min. one emergency stop button per drive unit (alley)!
The stated max. line length is the same as the cable length of the emergency stop line. By a series connection of
the emergency stop controls, there will be an effective line length of maximum 300 m.
(3) The controls release cable of the safety shutdown board to the ESC300 will be integrated into the emergency
stop line circuit and must be, according to this, considered for the maximum line length of the emergency stop.
(4) The used cable has to be screened and twisted. To increase the radio signal, it is possible to connect max. 2 radio
modules (concatenated in series or parallel). The max. line length per radio module is 100 m. This equates for 2
concatenated radio modules a length of max. 200 m.
Information about the lines for low voltage up to 24 V DC
It is not allowed to install current circuit with low voltage and mains voltage in the same wiring system. Consider for low
voltage lines, that there might be disturbances/malfunctions on the ESC300 by coupling of electromagnetic fi elds.
Do not lay the low voltage lines together with the electric power line, but separated with a spacer. Keep the length of the
lines as short as possible when there is low voltage.

15
ESC300 EXP300 ESC300 EXP300
AD
Date: 20-11-2014 Data name: esc300-2-v12a_EN ESC300 (swv-1.06)
Author: Heiko Lange Pages: 72 © P. Prinzing GmbH - 89173 Lonsee-Urspring (Germany)
* Option / depends on design Service: +49 (0) 7336 - 961018
Assembling and connection
2.6.2 Connection of the electronic control - ESC300
INFO
Into the feed line of the control you have to inte-
grate a main switch. Mount the main switch close
to the control, so that it is accessible when doing
maintenance works on the control.
The connection of the power feed line happens on the clamp power-inlet on the
board Control, on the left side on the control cabinet (fi g.15/1). The connection of
the phases L1-L2-L3 happens by a plug with screw terminals (fi g.15/3).
The connection of all earth conductors happens on the earth connector-terminal
strip on the left side of the box (fi g.15/2). A neutral wire will not be connected.
The power support of the boards relay 1+2 happens by the clamps extension.
These connections are pre-assembled factory provided and are easily to ex-
change.
2.6.3 Connection expansion module - EXP300
The power supply for the expansion module EXP300 happens, parallel to the
ESC300, by the main switch in the feed line. The feed line for the EXP300 will be
therefore connected parallel to the feed line of the ESC300 on the main switch.
Alternatively it is possible to mount an distribution box after the main switch and
connect there the feed lines. Connection examples see below - fi g.15/4+5
The connection on the EXP300 happens, same as for the ESC300, by the clamp
power supply and the earth connector-terminal strip (see description above chapter
2.6.2).
ATTENTION
It is not allowed to connect the power feed line for the
expansion module by the clamps „extension“on the
ESC300.
The cable length for the data bus is maximum 10 m!
15/1
Power connection (1) power connection
of boards relay (2)
15/2
Earth connector-terminal strip (3)
15/3
Terminal block
15/4
Power connection directly on the main switch
15/5
Power connection by the distribution box (AD)

16
Date: 20-11-2014 Data name: esc300-2-v12a_EN ESC300 (swv-1.06)
Author: Heiko Lange Pages: 72 © P. Prinzing GmbH - 89173 Lonsee-Urspring (Germany)
Service: +49 (0) 7336 - 961018 * Option / depends on design
Assembling and connection
2.6.4 Connection of the charging station ESC300 Charge
You need the charging station Charge to charge and store the Remote, and will be connected, independent of the control
ESC300 to the power supply For the Charge you need a connection voltage of 230 V / 1~.
Connect the charging station ESC300 Charge:
1. Open the transparent housing cover
Therefore press the closing on the right side to the inside (fig.16/1).
1. Loosen and extract all 4 screws (fi g:16/2) on the base plate
2. Take the base plate out of the box
Attention - Do not pull down the connected cable!
3. Connect the feed line (230 V~) to the connection clamp (fi g: 16/3)
4. Mount again the base plate and retighten the screws
16/2
Fastening screws base plate
16/1
Open/Closing on the box
16/3
Connection clamps
2.6.5 Connection optional equipment (end switch, push button, signal transmitter)
Optional equipment is not included to the standard-delivery and have to be always ordered additionally. Inform yourself
before connecting the additional equipment about the line length, -types and -cross sections in the installation plan.
The following equipment can be connected to the control:
End switch >>> On each end of the walkway it is possible to mount an end switch for the switch over- and off of the scraper
move without any load. You have to mount the end switch in a way, that the scraper can drive on easily and secure, to
guarantee a correct function.
Push button >>> It is possible to connect a tethered quadruple push button for the control of the alley. By the push button
you have the functions start - stop - forward - backward.
Signal transmitter >>> By optic or acoustic signal transmitters, errors or signals can be given.
If you have questions about the connection of the equipment, please contact our after sales service.

17
Date: 20-11-2014 Data name: esc300-2-v12a_EN ESC300 (swv-1.06)
Author: Heiko Lange Pages: 72 © P. Prinzing GmbH - 89173 Lonsee-Urspring (Germany)
* Option / depends on design Service: +49 (0) 7336 - 961018
Safety
3. Safety
The following safety advices are helping to avoid personal injuries and property damage. The operator of the dung removal
system has to assure, that general safety advices and regulations are considered and kept. Persons who are responsible
for the systems and the operation, as well as persons who are working with the dung removal system have to read and
understand the entire operating instruction. Inform yourself before the commissioning of the control about the position and
the correct condition of the safety- and protective devices.
Safety and protective devices are:
- Lockable main switch on the control
- Emergency stop button and safety shutdown board*
- Protective coverings and safety grid
3.1. General safety advices
1. Before commissioning the system, after the assembling and repair- and maintenance works, check the
entire assembling and the correct function of all safety and protective devices.
2. Before the maintenance and repair works on the dung removal system you have to switch off the control
and protect against undesired switch on (e.g. lock main switch)
3. Check before every manual start of the scraper drive
- that there are no persons in the working area of the scraper
- that the moving scraper means no danger for persons or animals
It is not allowed to:
- do repair and maintenance works on the system when it is switched on or during the operation
- arbitrary changes on the electronic control or on the components of the dung removal system
- operation methods, which derogate the security of the dung removal system.
- unattended operation of the system, if not all required safety and protective devices are working (see chapter 2.5).
Requirements provided by the customer:
To avoid danger areas between the scraper and solid building parts (e.g. wall breakthrough, doors, piles and parts of the
housing), you have to keep a safety distance of minimum 500 mm over the scraper path. An under usage of this safety
distance you have to clarify with the responsible Employer’s Liability Insurance.
The legal requirements are fully applicable. (e.g. VSG 2.1 § 16)
Technical safeguards for danger areas are e.g. connecting blocks on the danger area, trip wires or limited movement control
of the scraper.
3.2. Behaviour in danger situations
In visible or upcoming danger situations you have to:
- stop the system immediately by the emergency stop button, the STOP-button or by the main switch
- switch off the main switch and protect again undesired switch on (e.g. padlock)
- delete the danger cause or the error immediately
Only after deletion of the danger situation you can restart the operation and the system!

18
Date: 20-11-2014 Data name: esc300-2-v12a_EN ESC300 (swv-1.06)
Author: Heiko Lange Pages: 72 © P. Prinzing GmbH - 89173 Lonsee-Urspring (Germany)
Service: +49 (0) 7336 - 961018 * Option / depends on design
Safety
3.3. Danger areas of the dung removal system
Danger area Danger Safety measurements
Electric components Electric shock Close the system according to regulations
Mount coverings
Switch OFF the main switch before opening
Scraper Danger of being
crushed
Do NOT touch into the moving scraper
Safety distance to the moving scraper
Wall openings
Cross separations
Staff passages
Danger of being
crushed
Keep safety distance (> 500 mm over scraper)
Limited movement control (tactile operation) of the scraper
Mount the safety-connecting blocks
Drive rope Risk of stumbling Cover the rope or or guide it even with the ground
Attach indicator plates
Drive winches and guide pul-
leys
Danger of being
crushed
Danger of permeate
Risk of stumbling
Assembling according to regulations
Attach and mount the protective coverings
Check the safety distances
3.4. Danger by electric energy
ATTENTION!
Assembling-, connection- and repair works an den on electric components of the dung
removal system are only allowed to be done by specialized personnel.
After assembling-, repair- and maintenance works on the electric system you have to check
all safety devices. Note down the check corresponding the current valid regulations.
ATTENTION - Danger of electric shock!
When the main switch is switched off, there is still line voltage on the terminal clamps of
the control and on the main switch. Before opening the electrical device, always switch off
the main switch make sure that it can´t be switched on!
Consider the following advices:
- Do not work on energized parts.
- Lay the cables and lines in a way, that no thermal, mechanical or electromagnetic strain can infl uence them. Consider
the information in chapter „Assembling“.
- Mount all switches and coverings, close all openings according to regulations.
- Switch damaged or leaking electronic devices (control, switches, motors, and so on) strainless or replace them.
- Do the repair works on the electric parts only with approved tools.
- Replace damaged fuses by one of the same value

19
Systeem start
automatisch
GEVAAR
Date: 20-11-2014 Data name: esc300-2-v12a_EN ESC300 (swv-1.06)
Author: Heiko Lange Pages: 72 © P. Prinzing GmbH - 89173 Lonsee-Urspring (Germany)
* Option / depends on design Service: +49 (0) 7336 - 961018
Safety
3.5. Unattended operation (automatic) of the dung removal system
Unattended operation of the system means, that the connected rope winches turns self dependent and moves the respective
scraper, by an automatic sent starting command of the control.
The respective starting command has to be set and started by the person who is responsible for the control ESC300.
The following starting commands for an unattended operation are possible:
- Automatic start of a program by a schedule (timer)
- Automatic start of a program by temperature (freeze operation)
The following conditions have to be provided for an unattended operation of the dung removal system:
- Unauthorized persons (especially children) or animals are not allowed to enter the working area of the dung removal
system
- You have to exclude all injury risks for the animals which may occur from structural conditions (consider the minimum
height, use safety contact strips)
- All safety devices, especially the emergency stop have to be accessible and functional
- It is not allowed to do service-, maintenance- or cleaning works as well as other works (e.g. animal husbandry) in the
working area of the dung removal system
- Keep the entries to the working area of the dung removal closed and mount information plates (automatic starting
dung removal system) on the entries to the working area of the dung removal system
3.6. Danger of self-depended starting scraper
In the following situations the scraper starts automatically:
- „Automatic on“ ( ) >>> corresponding schedule from the starting position
- „Automatic on“ ( ) >>> corresponding schedule after manual stop in the walkway (to the next starting time)
- „Frost on“ ( ) >>> after reaching the switching on temperature in the set interval
- „Frost on“ ( ) >>> after „STOP“ in the set interval
- „Frost on“ ( ) >>> when „PAUSE“ after 600 sec
ATTENTION
Switch the main switch on “OFF” when doing repair- and maintenance works in the
working area of the scraper. Thereby you are able to avoid danger which can occur by the
automatic starting scraper.
3.7. Attach warning- and information signs
To increase the safety of your dung removal system and to avoid accidents, mount
the following information signs:
- „Machine starts automatically“ (fi g.19/1) >>> assemble on the drive winches.
These warning signs you will get with the delivery of your system.
- „Automatic starting dung removal system“ >>> assemble on all entries to the
working area of the dung removal system 19/1
Warning signs

20
Date: 20-11-2014 Data name: esc300-2-v12a_EN ESC300 (swv-1.06)
Author: Heiko Lange Pages: 72 © P. Prinzing GmbH - 89173 Lonsee-Urspring (Germany)
Service: +49 (0) 7336 - 961018 * Option / depends on design
The radio controlled remote ESC300
4. The radio controlled remote ESC300
Mode control during operation:
B = Operation (standard display)
E = Settings (in the menu)
1B > Opens the menu
E > Cancel an action during the insert
E > Stepwise backward navigation in the menu
E > Ends the teaching in program 3+4
2E > „Cross transport. “ON“ - defi ne position during teaching
3E > Continue teaching
E > Defi ne end of the alley
4
(Enter)
E > Open selection (submenu or menu item
E > Edit a chosen value
E > Save an edit value
B > Confi rm/receipt a message (e.g. error)
5B > Program change (upwards)
E > Navigation in the menu upwards
E > Rise a chosen value during the editing
6B > Program change (downwards)
E > Navigation in the menu downwards
E > Lower a chosen value during editing
7B > Change between alleys backwards
E > Positioning the cursor in the menu
8B > Change between alleys forward
E > Positioning the cursor in the menu
9
(Start)
Manual start of the automatic
Starts the scraper move of the displayed alley (1-6) with the chosen
program (P1...P4)
10
(Stop)
Button STOP
B > Stops the scraper move in the manual operation
E > Stops the scraper move during the teaching (= pause time)
B > Automatic:
- 1x press in the automatic = pause
- 2x press in the automatic = deletion
11
(Back)
Button for the manual operation
B > Moves the scraper back to the stop
E > Starts the backward movement during the teaching of P3 + P4
12
(Forw.)
Button for the manual operation
B > Moves the scraper forward to the stop
E > Starts the forward motion during the teaching of P3 + P4
20/1
Radio controlled remote ESC300
Table of contents
Popular Control Panel manuals by other brands
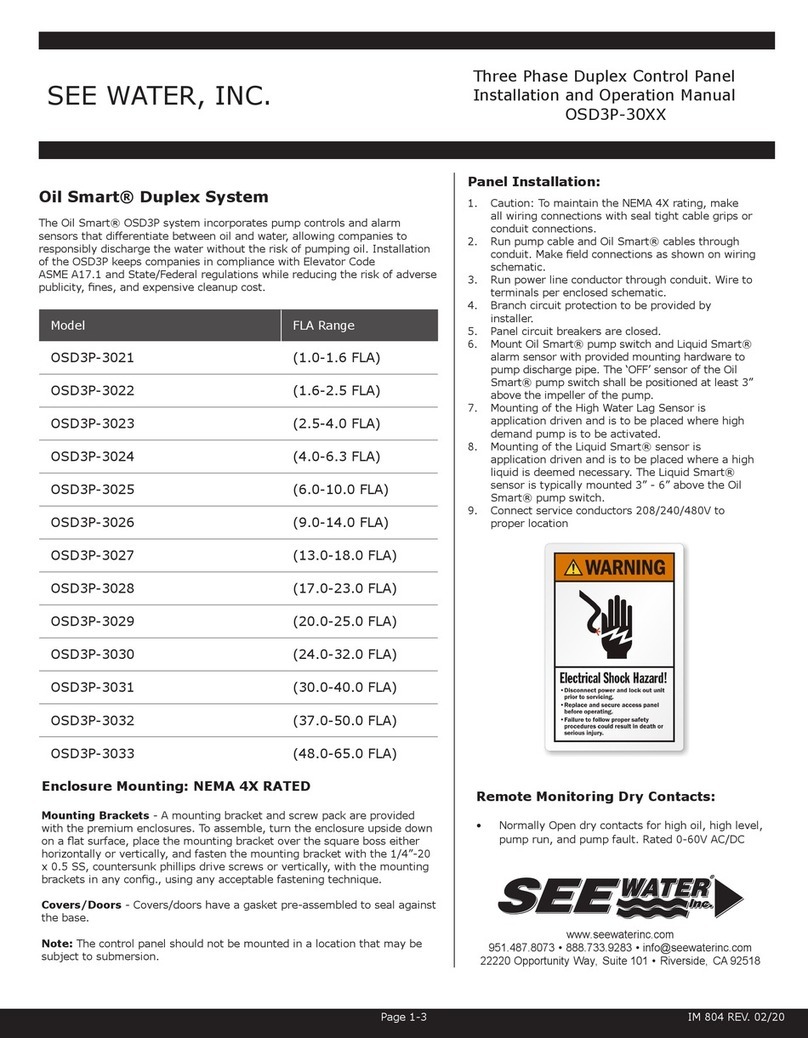
See Water
See Water Oil Smart OSD3P-30 Series Installation and operation manual
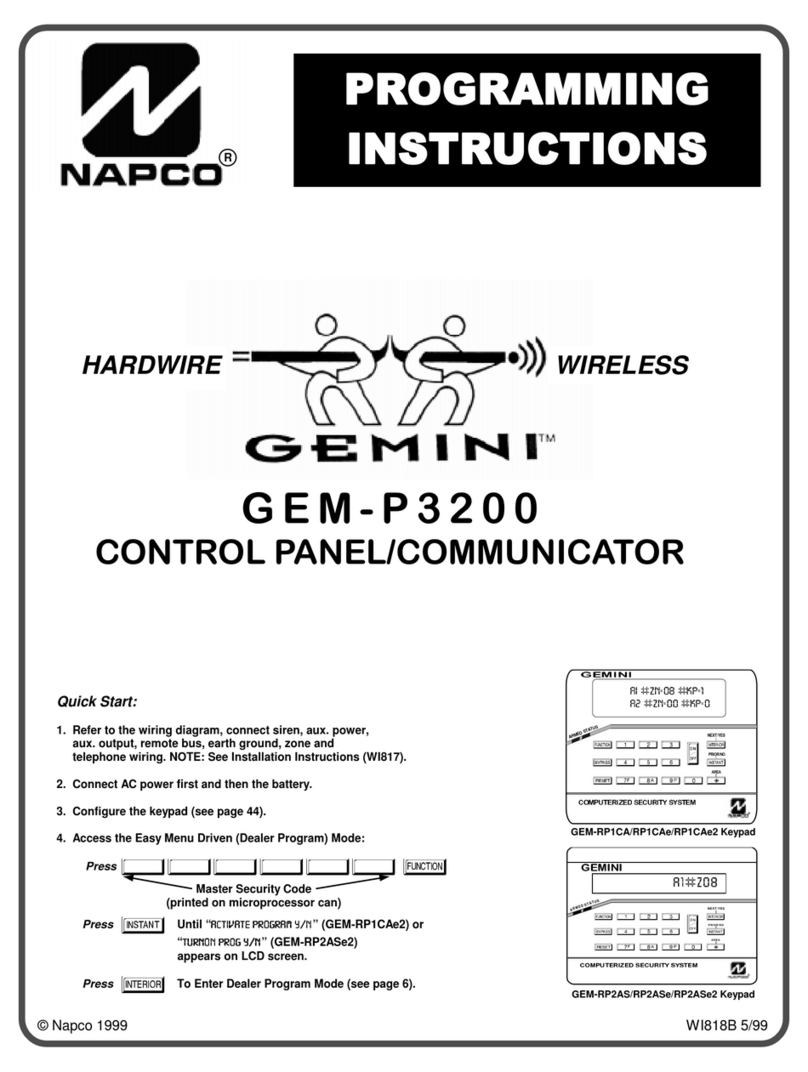
NAPCO
NAPCO Gemini GEM-P3200 Programming instructions
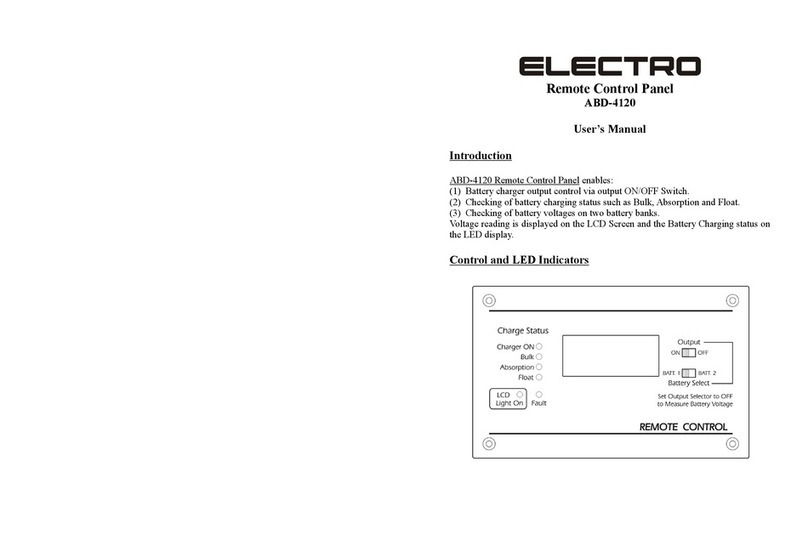
Electro
Electro ABD-4120 user manual
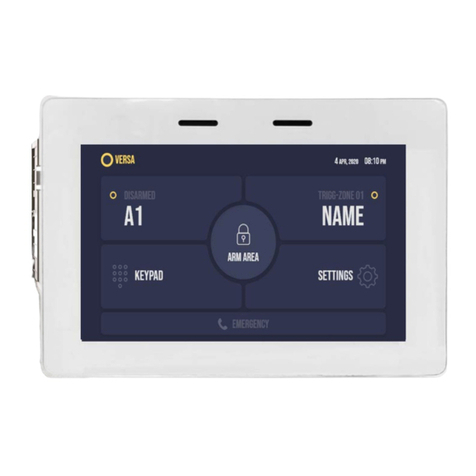
versa
versa IUI-SOL- VT5 Series quick start guide
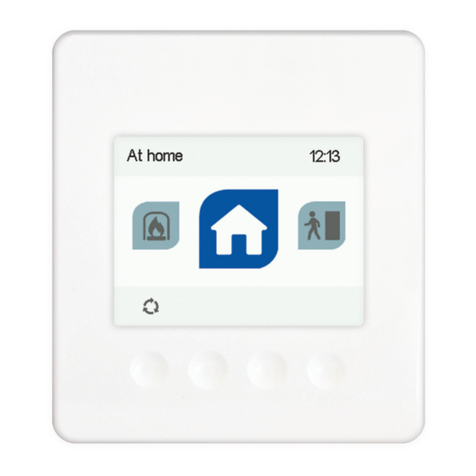
Vallox
Vallox MyVallox Control manual

Electronics Line
Electronics Line Prime Quick user guide