PRONOVA SSM 6000 User manual

User Manual
SSM 6000 CONTINUOUS
Date revised last: July 2007
Version 800C-07.07.EN
Software Version 3.01


This manual contains information concerning installation, operation and maintenance/service of the analyzer system.
Certain activities – such as replacing hardware components or changing internal settings – may only be carried out by
qualified personnel.
The manufacturer reserves the right to implement modifications at any time in order to adapt the user manual to the latest state of
the art. Any reproduction or distribution of the user manual or any parts thereof, including translated versions, are subject to written
approval.
The manufacturer does not assume any liability for errors or omissions, if any, in this documentation. Any liability for direct or indirect
losses or damage arising in conjunction with the delivery or use of this documentation is excluded to the extent permitted by law.
This device left the factory in an impeccable, safe condition. In order to maintain this condition and in order to ensure safe operation,
users must proceed in accordance with the information and warnings in this manual.
Please read this manual carefully before setting the device into operation!
All brands and their respective owners referred to in this manual are recognized and accepted. The manufacturer does not claim any
rights with regard to such brands.


SSM 6000 CONT
CONTENTS
800C-07.07.EN SSM 6000C User Manual 5
Table of contents
GENERAL SAFETY INFORMATION 9
1INTRODUCTION 11
1.1 Description and use of the device 11
1.2 Importance of the measured variables 12
2HARDWARE DESCRIPTION 13
2.1 Measuring characteristics 13
2.2 Elements of the analyzer 13
2.2.1 Process flow chart and measuring process 14
2.2.2 Display and control panel 16
2.2.3 Measuring-gas filter 17
2.2.4 Flow rate display and control 17
2.2.5 Measuring gas cooler (option) 18
2.2.6 Housing rinsing 18
2.2.7 Gas connections / safety features 19
2.2.8 Measuring-point switch (option) 19
2.2.9 Automatic shut-off valve (option) 20
2.2.10 Electrical connections 21
3HARDWARE INSTALLATION 22
3.1 Requirements for the plant of installation, power supply 22
3.2 Measuring input and output conditions, calibration gases 22
3.3 Scope of delivery, rating plate and test certificates 23
3.4 Dimension drawing of the SSM 6000 system 24
3.5 Installing the gas analyzer 25
3.5.1 Unpacking and assembling the gas analyzer 25
3.5.2 Electrical connections 25
3.5.3 Connecting the gas pipes 29
4USING THE GAS ANALYZER 31
4.1 Function keys 31
4.2 Starting a measurement 32
4.3 Menu structure 34

SSM 6000 CONT
CONTENTS
800C-07.07.EN SSM 6000C User Manual 6
5MENU AND FUNCTION OVERVIEW 35
5.1 Measuring parameters 35
5.1.1 Measuring interval 35
5.1.2 Alarm values 36
5.1.3 Single measurement 36
5.2 Calibration parameters 37
5.2.1 Gas types 37
5.2.2 Calibration gas concentrations 37
5.2.3 Start calibration 37
5.3 Device options 38
5.3.1 Datalogger 38
5.3.2 Analog measured-value outputs 43
5.3.3 Sensor data 44
5.3.4 Operation mode AUTO/MANUELL 45
5.3.5 DEVICE ID 45
5.3.6 Select language 45
5.3.7 Date/Time 45
6SETTING INTO OPERATION 46
6.1 Switching the gas analyzer on 46
6.2 Setting operating parameters 46
6.2.1 Setting date and time 46
6.2.2 Setting alarm values 46
6.2.3 Setting the measuring interval 47
6.2.4 Other settings 47
6.3 Checking the interface functions 48
6.4 Performing a test measurement 48
6.5 Starting normal measuring operations 49
7CALIBRATION 50
7.1 General information 50
7.2 Calibration setup and calibration gases 50
7.3 Recording the actual condition 51
7.4 Calibration procedure 52
7.5 Check measurement 53
7.6 Resuming measuring operations 53
7.7 Calibrating the oxygen sensor 54

SSM 6000 CONT
CONTENTS
800C-07.07.EN SSM 6000C User Manual 7
8MAINTENANCE, REPAIR, CUSTOMER SERVICE 55
9STATUS MESSAGES, TROUBLE-SHOOTING 57
9.1 Limit-value alarms 57
9.2 Trouble-shooting 57
10 WARRANTY CONDITIONS 58
11 APPENDIX 59
11.1 Technical specifications 61
11.2 Parts subject to wear and tear; spare parts 63
11.3 Declarations of conformity 64
11.4 Accessory connection cables 68
11.4.1 PORT 1 connection cable 68
11.4.2 PORT 2 connection cable 69
11.5 Connection diagrams – Analyzer versions A / B 71
The description of the PROFIBUS interface can be found at the end of this documentation.


SSM 6000 CONT
GENERAL SAFETY INFORMATION
800C-07.07.EN SSM 6000C User Manual 9
General safety information
The following safety information must always be observed during operation as well as during any maintenance and repair work on
this device. Non-compliance with safety measures or any other information or warnings contained in this user manual constitutes a
violation of safety standards underlying the design, manufacture and proper use of the device.
Non-compliance with such information can cause hazards for users and/or damage to the device! The manufacturer does not accept
any liability for losses or damage caused by non-compliance with such safety measures on the part of the customer.
In order to avoid any additional hazards, unauthorized modification of the device is not permitted. In the event that repair work is
necessary, the device should be returned to our technical office after prior notification.
Users are not permitted to open the device. Certain activities – such as replacing hardware components or internal settings – may
only be carried out by qualified personnel.
Devices which are suspected to be at fault or defective must be switched off and protected against unauthorized access until the
necessary repair/service work has been performed by expert personnel.
When working in explosive or flammable environments, do not operate the device without additional protection measures!
Proceed in accordance with the safety instructions applicable to the respective gases and calibration gas bottles or
cylinders!
Prior to performing any work on gas ducts or pipes, flush these with ambient air or nitrogen (N2) in order to avoid any
hazard due to toxic, explosive, flammable or harmful components of the measuring gas.
When connecting the device, make sure that the correct mains voltage is available, and proceed in accordance with the information
in the section titled "Requirements for the place of installation, power supply".
The analyzer is a safety-class 1 device, i.e. it is fitted with an earthing connection. Any interruption of the PE conductor inside or
outside the device, or opening of the PE connection can make the device a hazard. Deliberate interruption of the PE conductor is not
permitted.
The device comes with a power cable with earthed-contact plug and may only be connected to an earthed-contact receptacle. The
protective effect may not be rendered ineffective by using an extension cable without PE conductor.
Before performing any fault-finding or repair work, or before replacing any parts, disconnect the device from any voltage
sources! In the event that work must be performed on the live, opened device, this may only be carried out by an informed
expert who must be familiar with the related risks and hazards!


SSM 6000 CONT
INTRODUCTION
800C-07.07.EN SSM 6000C User Manual 11
1 Introduction
1.1 Description and use of the device
The SSM 6000 was specifically developed for analyzing biogenous process gases, such as biogas, sewage purification gas or
landfill gas. It is designed for the requirements of regular process control directly at plants and equipment and to this effect combines
quality sensor equipment for continuous gas analysis with multi-stage gas processing technology.
The full version is capable of analyzing the main gas types, i.e. methane, hydrogen sulphide, oxygen and carbon dioxide
respectively. The analyzer features ease of operation and a clear-cut display structure.
In terms of time and frequency of use, the SSM 6000 family can draw on the largest experience of all biogas analyzers available on
the market. The first analyzer developed in Europe specifically for continuous operation in biogas plants belongs to the SSM family
and has been in use since 1998. Several hundred SSM gas analyzers have been delivered up to now.
The demanding, strongly varying measuring conditions in biogas plants mean exacting requirements for gas analyzers for
continuous operation. Like in so many applications in biogas process technology, optimum adaptation to the difficult medium is the
decisive test. In order to increase service life, measuring precision and, above all, operational safety, Pronova has integrated a host
of additional functions into its SSM 6000 Classic which, in their totality, are quite unusual on the market:
- Limitation of the maximum hydrogen sulphide concentration at the H2S sensor(equipment specification is SSM6000
classic)
- Multi-stage measuring-gas processing, including measuring-gas cooling to 5°C for dehumidification sample gas (option)
- Pressure and temperature compensation of measured values
- Detonation protection EN 12874, housing rinsing in conjunction with the option measuring cooler
Hydrogen sulphide is measured by means of electrochemical sensors. Already at typical gas concentrations in biogas plants,
sensors of this kind can be subject to saturation with a reduction of signals and increased sensor wear or even sensor failure. The
SSM 6000 Classic prevents this by microprocessor-controlled, concentration-dependent dilution of measuring gases which keeps the
H2S gas concentration at the sensor at a level of below 25 ppm – even at levels of several 1000 ppm in the biogas. The sensor
hence always works in its optimum load range.
Advantages: Wide measuring range of 0 – 5000 ppm without exposing the sensor to excessive load or strain
Increased long running stability
Lower operating costs thanks to extended service life
Increased reliability of the measurement
Biogas contains components which are harmful for the sensors and system components, in particular, hydrogen sulphide which has
an aggressive action in conjunction with humidity. The SSM 6000 Classic hence comes with a measuring-gas cooler in order to
reduce high humidity levels and protect the sensors. The SSM6000 LT analyzer version is available with an optional measuring-gas
cooler.
Advantage: Reduced susceptibility to failure
Lower operating costs thanks to extended service life
Avoidance of volumetric errors thanks to constant measuring-gas dew point
Precision infrared sensors (IR sensors) are used to measure methane (CH4) and carbon dioxide (CO2). However, the measured
values supplied by these sensors are strongly dependent on temperature and air pressure due to the underlying measuring process.
Changes in air pressure due to changing climatic conditions, for example, can already cause relative changes in measured values in
the order of up to 10%. Changes of a similar magnitude also occur if a device is calibrated, for example, in Berlin (40 m above mean
sea level) and operated at an altitude of 600 m above mean sea level. With the SSM 6000, IR measurements are generally
subjected to temperature and pressure compensation.
Advantage: Increased measuring precision.

SSM 6000 CONT
INTRODUCTION
800C-07.07.EN SSM 6000C User Manual 12
Gas mixtures with critical concentration relationships between methane and oxygen are flammable. Although critical gas mixtures of
this kind are very rare in biogas plants, the utmost must be done in order to avoid the risk of ignition. In the SSM 6000, a detonation
protection unit separates the analyzer from the biogas plant. Furthermore, the interior of the device is flushed with ambient air, so
that no flammable gas mixture can occur in the device even in the case of pipe leaks.
Advantage: Increased safety.
1.2 Importance of the measured variables
Methane CH4
Methane is the only energy carrier in biogas worth mentioning. A high yield is hence vital for the profitability of the plant.
Furthermore, the methane concentration provides important information concerning the fermentation process and hence the
condition of the biogas plant. A decreasing concentration is the first sign of a disturbed fermentation process. Continuous monitoring
of the methane content hence makes it possible to search for and identify the causes of a problem at an early stage. Depending on
the purpose for which the biogas is used, the methane content must be within certain limits, for example, in order to permit its safe
use as a fuel in pilot injection units or in gas-fuelled spark ignition engines. Too high or low a methane content can cause damage to
the motor. Furthermore, too low a methane content strongly affects economic efficiency.
Hydrogen sulphide H2S
The block cogeneration plant burns the hydrogen sulphide contained in biogas to form SOxfrom which sulphurous or sulphuric acid
are produced in the presence of water. These acids lead to corrosion of those parts of your plant (for example, pilot injection unit or
gas-fuelled spark ignition engine) which contain nonferrous heavy metals. This is why hydrogen sulphide must be eliminated to the
largest extent possible.
Regular measurement of the hydrogen sulphide content provides a good indication of how good the biogas "desulphurization"
process is working.
Oxygen O2
In most plants, desulphurization of the biogas is accomplished by injecting additional ambient air oxygen into the process.
Experience has shown that an ambient air oxygen content of more than 5Vol.%ume does not lead to any further reduction of the
hydrogen sulphide content by biological degradation. Furthermore, higher concentration can reduce the reaction capability of
bacteria and a flammable gas mixture can occur in the fermenter. Monitoring the oxygen content in the biogas hence makes sense.
If too high a hydrogen sulphide level is measured even though the oxygen content is within the optimum range, insufficient
desulphurization must then be due to other causes. Possible explanations then include too low an ambient temperature for the
bacteria or too short a contact time during which the bacteria is exposed to the biogas.
Carbon dioxide CO2
Besides methane, carbon dioxide is the second largest quantitative component of biogas. Both components account for around 98%
of the volume. This is, however, only an approximate value because other gases, such as ammonia (NH3) or hydrogen (H2), can be
produced in more than insignificant concentrations during the fermentation process and hence occur in biogas. The total
concentration of methane, carbon dioxide, oxygen and nitrogen contained in the injected air should amount to around 100Vol.%ume.
The nitrogen concentration corresponds to around 3.8 times the O2concentration.
Hydrogen H2
The determination of the hydrogen content is becoming increasingly important for the assessment of the conversion processes in the
fermenter. Hydrogen is a pre-product and/or intermediate product of methane during the process of anaerobic decomposition, so that
monitoring of the hydrogen concentration enables an even faster detection of disturbances during the fermentation process.

SSM 6000 CONT
HARDWARE DESCRIPTION
800C-07.07.EN SSM 6000C User Manual 13
2 HARDWARE DESCRIPTION
2.1 Measuring characteristics
The SSM 6000 Continuous analyzer was developed for the continuous measurement of CH4, O2, CO2and for the discontinuous
determination of H2S and H2concentrations in biogenic gases. The table below contains details concerning measuring ranges, etc.
Gas type Measuring range Resolution Precision Measuring method Other
CH4 0 ... 100 Vol.%. 0,1 Vol.%. ±2% FS Two-beam IR Temperature and pressure compensation
H2S 0 ... 5.000 ppm 1 / 5 ppm ±5% FS Electrochemical Dilution stages 1:200/40/10/0
0 ... 1.000 ppm 1 ppm ±5% FS Electrochemical Without Dilution
H20 ... 1.000 ppm 1 ppm ±5% FS Electrochemical Without Dilution (instead of H2S)
O2 0 ... 25 Vol.%. 0,1 Vol.%. ±2% FS Electrochemical
CO2 0 ... 100 Vol.%. 0,1 Vol.%. ±2% FS Two-beam IR Temperature and pressure compensation
* The H2S measuring range depends on the analyzer version. H2S and H2measurement is carried out as a discontinuous process.
The following sections deal with operation, calibration and menu structure of the analyzer.
2.2 Elements of the analyzer
The front panel of the analyzer contains all the
controls necessary for operation:
1
2
3
4
5
6
7
8
9
10
11
12
13
14
15
16
17
Control and display panel
Aerosol filter
Air filter
Chemical filter
Fine dust filter
Flowmeter
Needle valves
Measuring-gas input with detonation protection
Measuring-gas outputs
Screw-type cable connection with power cable
Interfaces
Wall-mount support
Status display LEDs for measuring-gas cooler
Condensate pump
Condensate output
Ventilation air inlet
Ventilation air outlet
All electrical connections and gas connections are
located on the underside of the device.
Fig.: Front view of the analyzer

SSM 6000 CONT
HARDWARE DESCRIPTION
800C-07.07.EN SSM 6000C User Manual 14
2.2.1 Process flow chart and measuring process
Fig.: Process flow chart SSM6000Classic continuous
Fig.: Process flow chart SSM6000LT continuous
1
2
3
4
5
6
Detonation protection
Measuring-gas cooler
Hose pump
Aerosol filter
Fine dust filter
Measuring-gas pump (flow1)
7
8
9
10
11
12
Needle valve (flow1)
Flowmeter (flow1)
Chemical filter
Air filter
3/2-way solenoid valve
Measuring-gas pump (flow2)
13
14
15
16
Needle valve (flow2)
Flowmeter (flow2)
Measuring-point switch (option)
Shut-off valve (Option)

SSM 6000 CONT
HARDWARE DESCRIPTION
800C-07.07.EN SSM 6000C User Manual 15
The measuring gas is initially drawn in through the safety device (1) of the selected measuring point (15) and cooled down to 5°C in
the measuring-gas cooler (2). The hose pump (3) pumps the resultant condensate to the condensate discharge. The condensate
must be collected and disposed of by the equipment user. In order to remove dirt particles from the measuring gas, the dehumidified
measuring gas is directed through the aerosol filter (4) at the downstream end of the cooler. The measuring-gas pump (6) pumps the
processed measuring gas through the "flow 1" flowmeter (8) with needle valve (7) to the CH4, CO2and O2sensor and is
subsequently discharged through the "Gas out 1" outlet. These three gases are continuously measured, so that the current gas
concentrations are at all times displayed at the analyzer.
Since H2S measurement is a discontinuous process, the analyzer includes a second gas path. Following expiration of a set
measuring interval, filtered ambient air is first pumped to the H2S sensor in order to determine its zero point. The chemical filter (9)
and the air filter (10) eliminate foreign particles from the zero gas.
Depending on the H2S concentration in the biogas, this is then followed by several dilution stages in the case of the SSM6000
Classic analyzer version where defined amounts of ambient air are added to the biogas. As a result, the H2sensor will never be
exposed to more than 25 ppm irrespective pf the H2S concentration in the biogas.
In the case of the SSM6000 LT analyzer version, the biogas is directed to the H2S sensor undiluted. In order not to overstrain the
sensor, the average H2S concentration should be significantly lower than 200 ppm. The H2S measuring range of the SSM6000 LT
totals 1000 ppm.
The measuring-gas volume through the H2S channel is set at around 30 liters per hour by means of the "flow 2" flowmeter (14) and
the needle valve (13) of the analyzer. Since H2S measurement is a discontinuous process, the volume flow can only be set during
an H2S measuring cycle. The measuring gas of the H2S measurement is discharged into the open through the "Gas out 2" outlet.
The pipes and hoses used to discharge the measuring gas should be as short as possible and extend separately into the
open!
In the following analyzer version, all gas types are measured continuously. In order not to overstrain the H2S sensor, the average
H2S concentration should not exceed 50 ppm. The service life of the H2S sensor can only be vaguely defined with this configuration.
No warranty is hence assumed for the H2S sensor.
Fig.: Process flow chart SSM6000 continuous

SSM 6000 CONT
HARDWARE DESCRIPTION
800C-07.07.EN SSM 6000C User Manual 16
2.2.2 Display and control panel
The measured values are displayed for each gas type on the four-digit LED panels in the respective unit (Vol.% and ppm,
respectively). In the case of devices with reduced functionality, the displays of gas types not included in the functionality remain
inactive.
The status LEDs next to the measured values represent the status of the respective gas channel.
active (green) This gas type is currently being measured.
stand-by (yellow) The device is ready for operation, but the gas type in question in currently not being measured.
alarm (red) The last value measured was outside the set limits and hence triggered an alarm.
Settings and operating parameters of the analyzer can be entered and changed via the control panel. The user menus are displayed
on the four-line, backlit LC display.
Navigation through the user menus is possible in setup mode via the membrane keypad (esc, up, down, enter). The setup mode is
activated via the key-operated switch. Withdrawing the access key prevents changes in analyzer settings by unauthorized persons.
The analyzer is switched on and off via the "power" button.
Measured values Power switch
Membrane keypad Setup switch
LC displayStatus LEDs

SSM 6000 CONT
HARDWARE DESCRIPTION
800C-07.07.EN SSM 6000C User Manual 17
2.2.3 Measuring-gas filter
Several filters are integrated into the gas path of the SSM 6000 in order to protect the sensors and other components of the system.
The filters clean the biogas and the ambient air drawn in, thereby increasing both the service life of the sensors and the measuring
precision of the system.
Filter type Function
Aerosol filter Eliminates aerosols and larger dirt particles from the gas sample. Replacement is only necessary if filter
contamination is visible. (Material: glass and steel wool)
Air filter Filters the ambient air for zero-point determination of the H2S-channel. The zero-gas filter should be replaced
at least once a year. (Material: activated carbon)
Chemical filter The chemical filter is also used to filter the zero gas.The filter is slowly used up which can be easily seen by
gray discoloration of the filter material. The filter must be replaced by a new one at the latest when the pink
color of the filter material has vanished.
Fine-dust filters are additionally located at the downstream end of the filter cartridges. These fine dust filters must also be replaced
when strong contamination of the filter is found.
2.2.4 Flow rate display and control
The measuring precision depends, amongst other things, on the measuring-gas volume flows. The
measuring-gas volume flows are measured by the two flowmeters on the front panel of the SSM 6000
and can be adjusted by means of the needle valves located below the flowmeters.
Adjust the flow rates in such a manner that the floating indicators are located between the upper and
lower marks during measurement.
Flowmeter "flow 1" (left) 50 ... 65 liters per hour
"flow 2" (right) 15 ... 30 liters per hour
"Flow 2" adjustment is only possible during an H2S measuring cycle because the measuring-gas pump is inactive in
"stand-by" mode.

SSM 6000 CONT
HARDWARE DESCRIPTION
800C-07.07.EN SSM 6000C User Manual 18
2.2.5 Measuring gas cooler (option)
The SSM 6000 Classic analyzer version comes with a serial measuring-gas cooler. The SSM6000 LT is available with an optional
measuring-gas cooler.
Measuring-gas coolers are used in analyzer systems to process contaminated and humid measuring gases and to lower their dew
point. This reliably rules out the generation of condensate as well as the accumulation of dirt particles in the analyzer and other
system components. Adjusting a stable measuring-gas starting dew point avoids water vapor cross-sensitivity and volumetric errors.
The gas cooler works with an electronically controlled Peltier cooler. The design of the heat exchanger made of Duran glass favors
ideal flow conditions and ensures optimum lowering of the dew point to a stable value of 5°C.
A hose pump discharges the condensate produced into an external collecting tank. Status LEDs on the front panel indicate the
operating status of the gas processing unit. An alarm is generated when the set temperature is exceeded by 3°C.
The status LEDs indicate the current operating status of the cooler. When lit, the individual
status LEDs have the following meanings.
cooler "o.k."
cooler "active"
cooler "error"
The measuring-gas cooler is ready for operation. The actual temperature
of the cooler is within the pre-set temperature range of 5 ± 3°C.
The Peltier element is active. The frequency provides an indication of
the load exposure of the cooler.
The actual temperature of the cooler is outside the pre-set range of
5 ± 3°C.
Fig.: Status LEDs and hose pump on the front panel
The error LED can be activated for several reasons.
- After power-on, the measuring-gas cooler is not yet ready for operation. The cooler should have reached its operating
temperature and the "error" LED should go off after around 15 minutes.
- A measuring-gas cooler overload condition exists during operation as a result of the excessively high dew point of the inflowing
gas, or as a result an excessive volume flow or ambient temperature.
- The device is defective. Contact the manufacturer of the device in such a case.
During the measuring process, the hose pump transports the condensate produced to the "condensate out" outlet of the device.
2.2.6 Housing rinsing
In connection with the option measuring cooler the SSM6000 has got available additionally comes with a fan unit that discharges the
heat of the measuring-gas cooler and rinses the housing with ambient air. The flow rate of the fan totals around 56 cubic meters per
hour, so that the generation of a flammable gas mixture within the analyzer is safely prevented.
In order to avoid dirt accumulation inside the device, a particle filter at the air intake opening on the right side panel of the analyzer
ensures reliable filtering of dust and other contaminants. The housing filter must be checked at process-dependent intervals and
must be replaced when visible contamination is found.

SSM 6000 CONT
HARDWARE DESCRIPTION
800C-07.07.EN SSM 6000C User Manual 19
2.2.7 Gas connections / safety features
All gas connections are located on the underside of the analyzer. The connections are clearly marked and may not be exchanged.
The gas-carrying pipes are connected to the device by means of clamping-ring screw connections.
The following connections must be made: 1x Measuring gas in *
2x Measuring gas out
1x Condensate out
* Up to four measuring points with an automatic switching function are optionally available (refer to section 2.2.8).
The delivery includes 20 meters of PVC hose (an additional 10m per measuring point with the measuring-point switch option) and
the required connections.
In order to protect the biogas plant against flashback, a safety unit is installed at the measuring-gas input of the analyzer which
prevents flashback into the gas-carrying system of the plant in the case of pipe leakage.
The device is at present fitted with the F 510 detonation protection system according t EN 12874 / PTB 02 ATEX 4012X made of
stainless steel. The manufacturer's conformity declarations and test certificates for the safety and protection equipment are shown in
the appendix to this manual.
2.2.8 Measuring-point switch (option)
Depending on equipment enables the implementation of up to four measuring-gas inlets with detonation protection and 3/2-way
solenoid valves for switching between the measuring points.
The solenoid valves are controlled and the measuring points selected by the SSM 6000. A measuring process can be triggered
manually via the digital inputs at port 1 or the (optional) Profibus interface.
With the device in "MANUAL" mode, a measuring process can be started in stand-by mode at any time by pressing the <enter> key.
You are first prompted to select the measuring point via the <up> and <down> keys. Thereafter, press the <enter> key once again in
order to confirm the start of the measuring process.
The Analyzer comes with four digital inputs at Port 1 which are used to start the H2S measuring process and at the same time to
select the measuring point. The digital optocoupler inputs are assigned as follows and must be activated for around 1.5 seconds:
DI 01 - measuring point 1
DI 02 - measuring point 2 / valve 1
DI 03 - measuring point 3 / valve 2
DI 04 - measuring point 4 / valve 3
After the start of the measuring process, the analyzer simultaneously activates the corresponding measuring-point valve and/or the
pertinent digital output at plug connector PORT2. The digital inputs are not read again until a H2S measuring process has been
completed. After an H2S measuring cycle, the continuous measuring mode of the other components continues to be active until
another measuring point is selected or until the <esc> key is pressed in order to terminate the measuring cycle.
If the device is controlled via the digital inputs or via the Profibus interface, an H2S measuring interval of "9999" should be set in
order to avoid conflicts with the automatic measuring interval.

SSM 6000 CONT
HARDWARE DESCRIPTION
800C-07.07.EN SSM 6000C User Manual 20
2.2.9 Automatic shut-off valve (option)
The SSM6000 with the "continuous measurement" option is designed for pressures between –200 and +200 hPa at the measuring-
gas inlets in measuring mode. During measuring breaks and/or with the analyzer switched off, an overpressure of more than 5 hPa
at the measuring-gas inlet of measuring point 1 causes a continuous flow through the analyzer. Since the condensate pump is
inactive in stand-by mode, condensate can accumulate in the cooler during longer measuring breaks. When a measuring process
starts, this condensate would then be drawn into the gas system and could damage the analyzer. This means that the measuring-
gas supply for measuring point 1 must be interrupted during measuring breaks with admission pressures of more than 5 hPa,
using suitable means, such as an automatic stop valve.
The solenoid valve can be controlled via the "Measurement active" status output of the SSM 6000 on the underside of the analyzer
(port 2).
At the customer's request, the manufacturer can install a suitable stop valve (16) in the analyzer. The valve is then automatically
controlled by the analyzer. This feature is explicitly mentioned in the test and calibration certificate.
The measuring-gas inlets of measuring points 2 to 4 are closed during measuring breaks and when the analyzer is switched off, and
hence do not require an additional shut-off device.
Other manuals for SSM 6000
1
Table of contents
Other PRONOVA Measuring Instrument manuals
Popular Measuring Instrument manuals by other brands
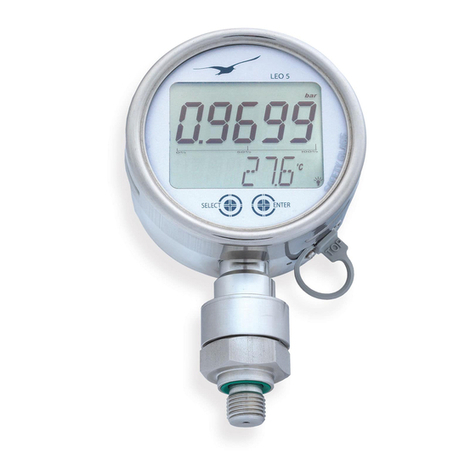
Keller
Keller LEO 5 operating instructions
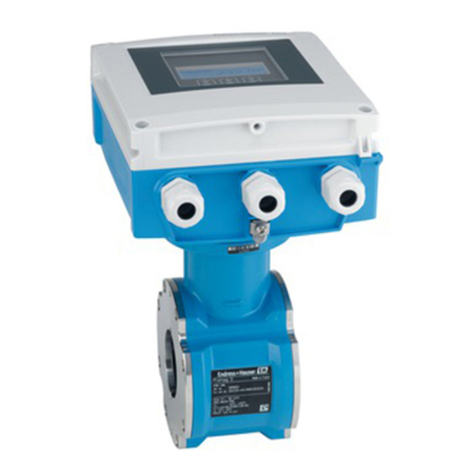
Endress+Hauser
Endress+Hauser Proline Promag D 400 HART operating instructions
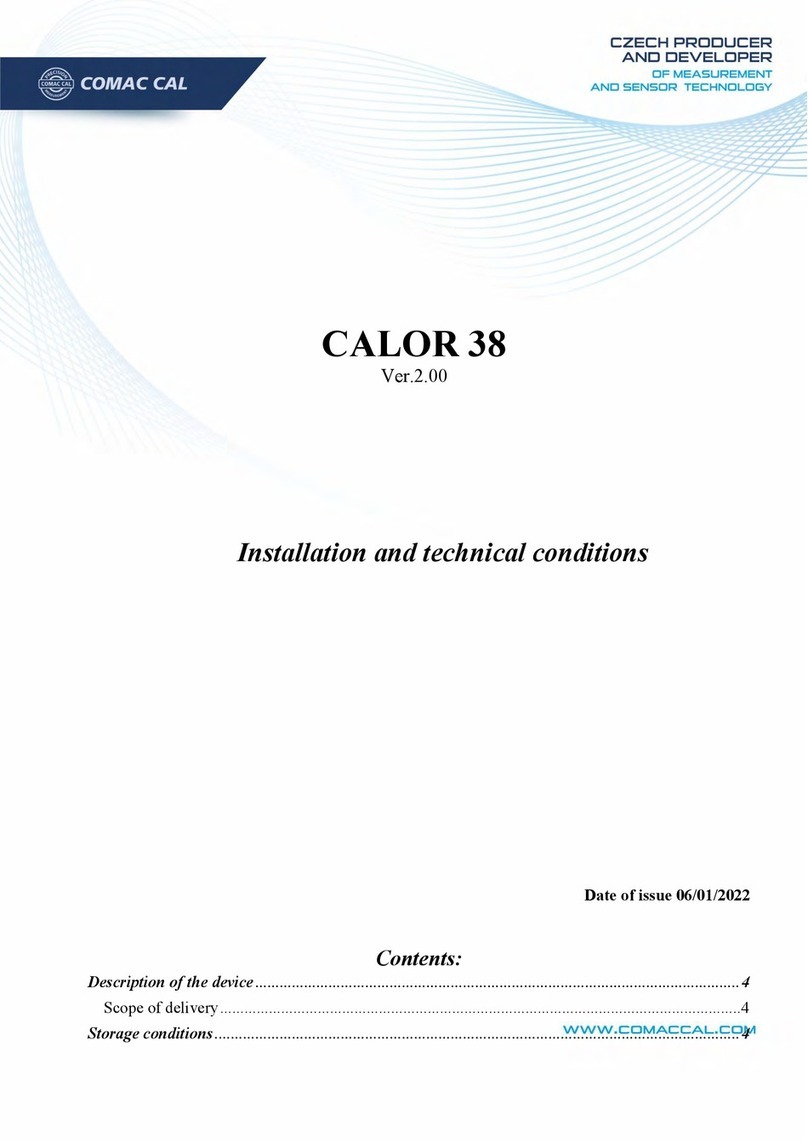
COMAC CAL
COMAC CAL CALOR 38 Installation and technical conditions
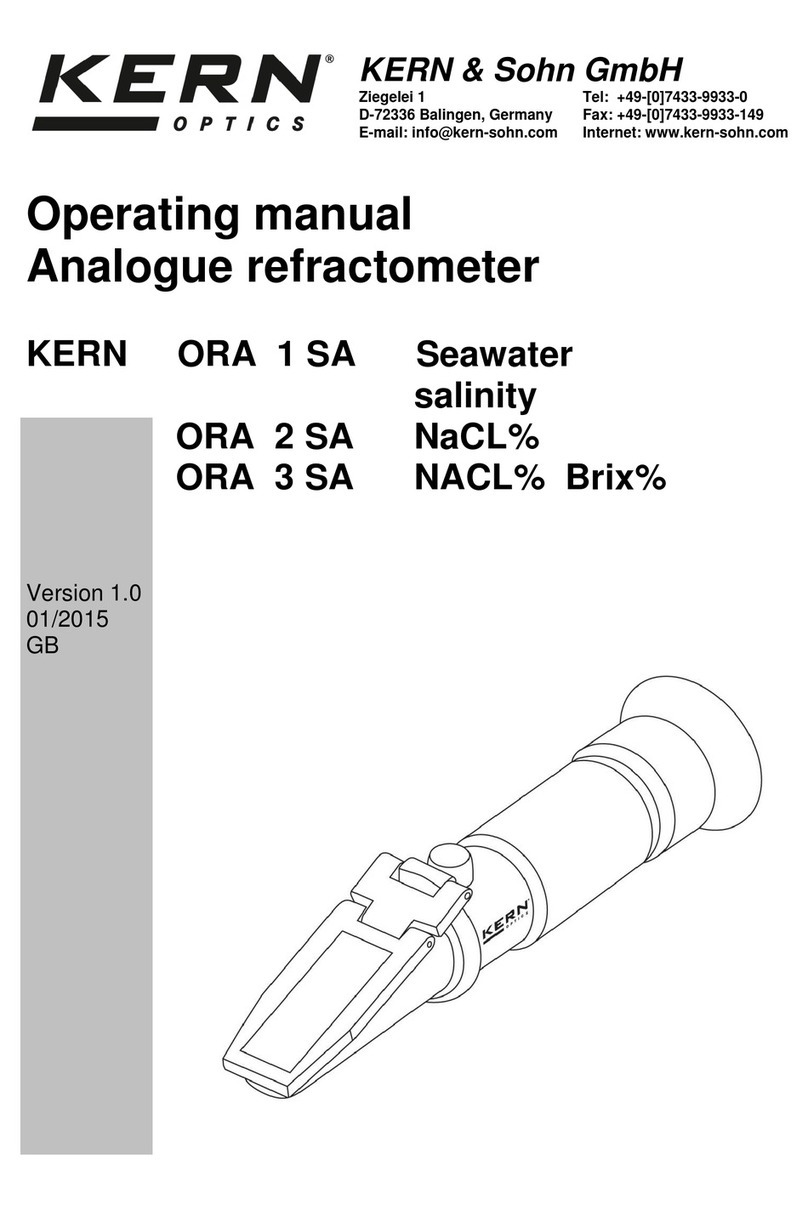
KERN Optics
KERN Optics ORA 2SA operating manual
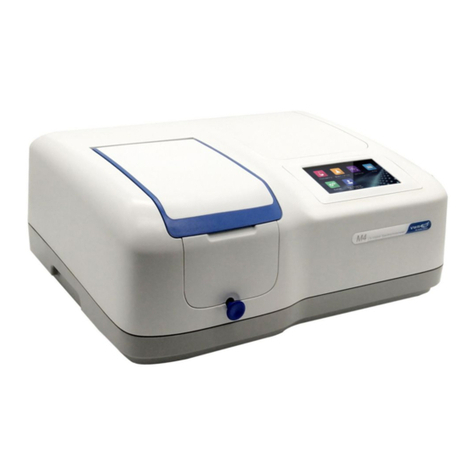
VWR
VWR M4 instruction manual

Thermo Scientific
Thermo Scientific Orion Star A111 reference guide
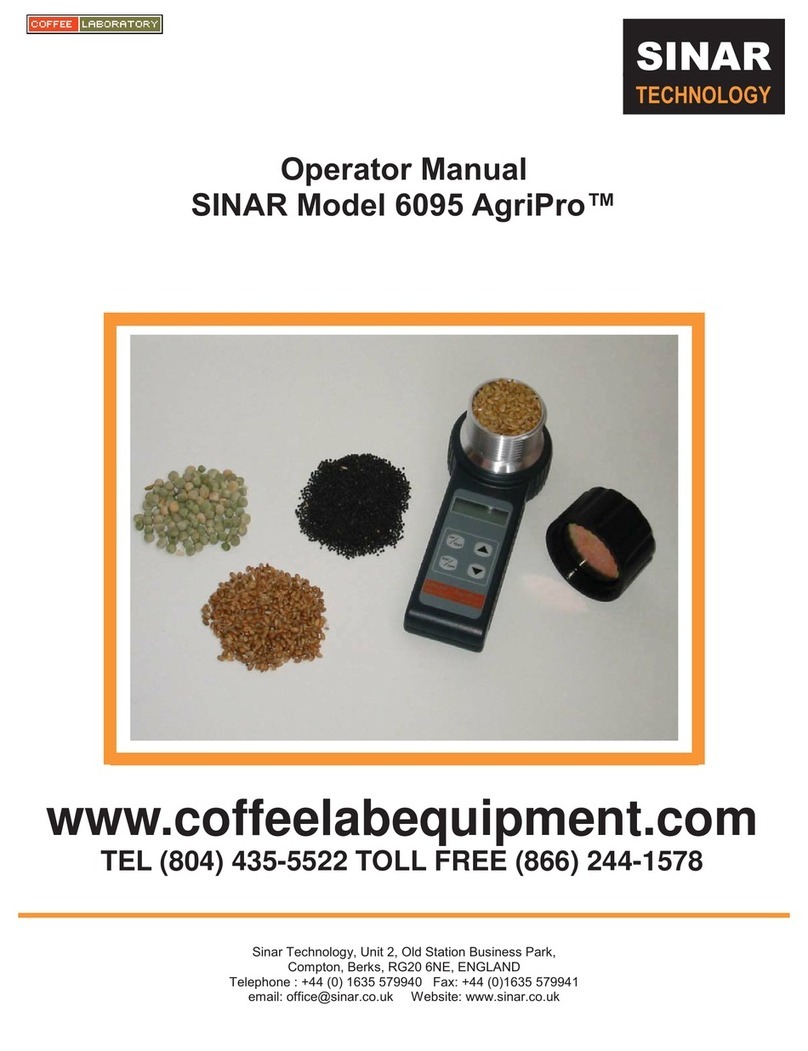
Sinar Technology
Sinar Technology 6095 AgriPro Operator's manual
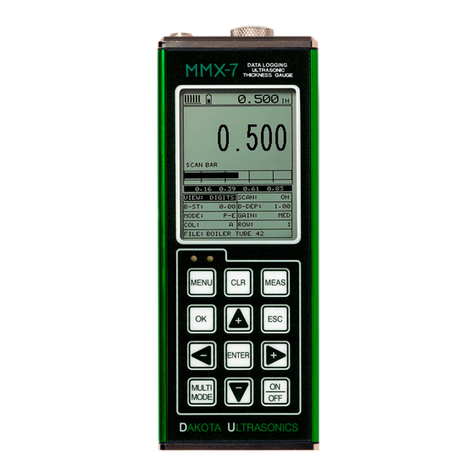
DAKOTA ULTRASONICS
DAKOTA ULTRASONICS MMX-7 Operation manual

ABB
ABB SM500F Instruction
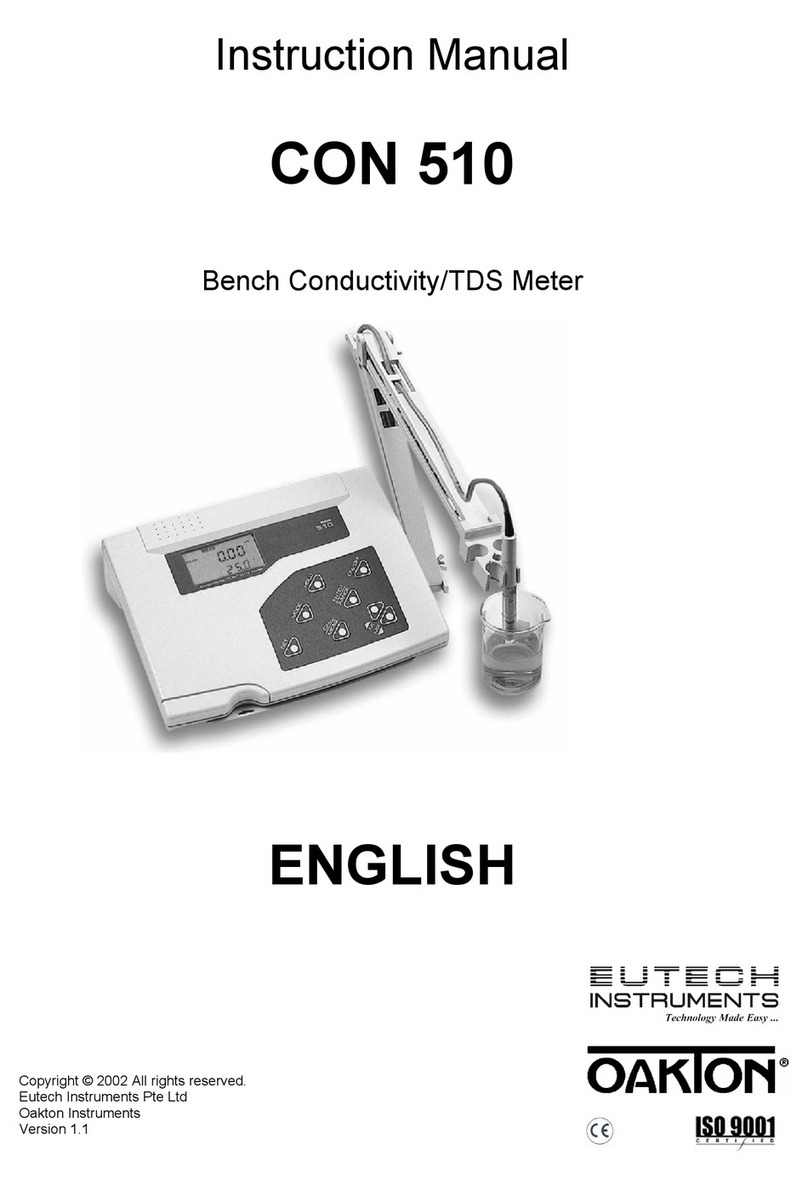
EUTECH INSTRUMENTS
EUTECH INSTRUMENTS Oakton CON 510 instruction manual
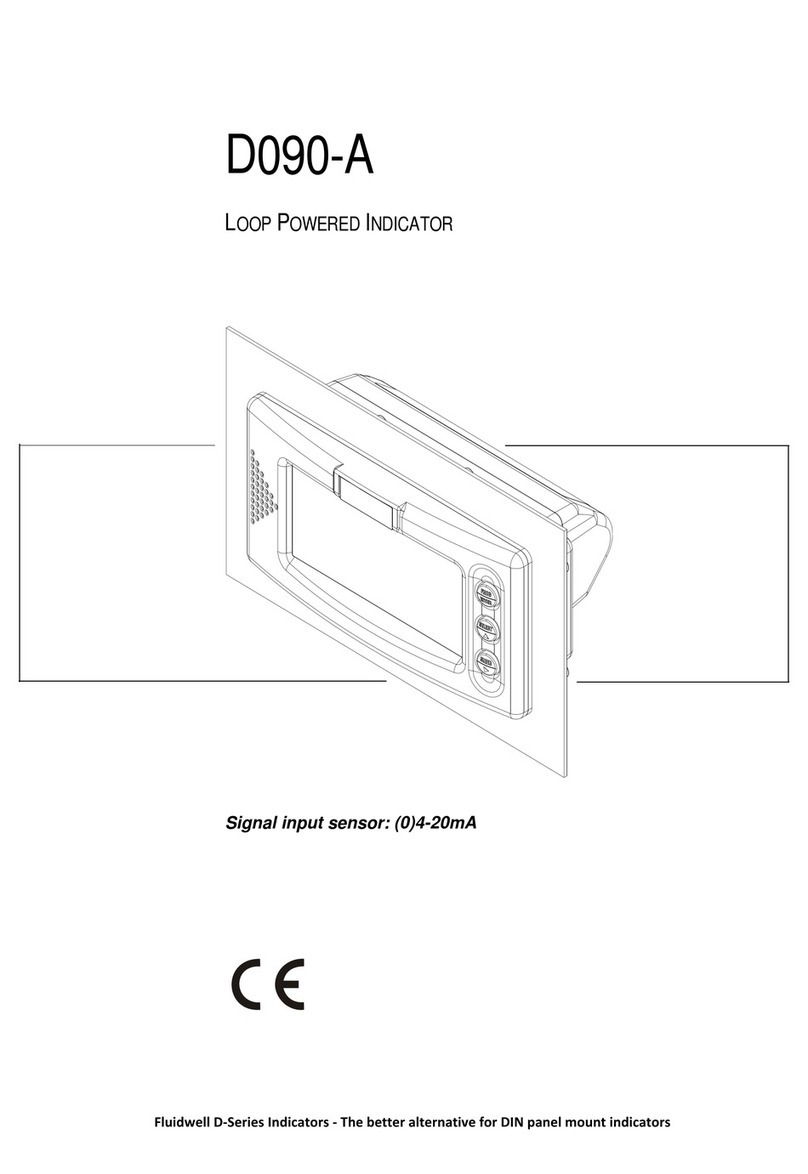
Fluidwell
Fluidwell D Series manual
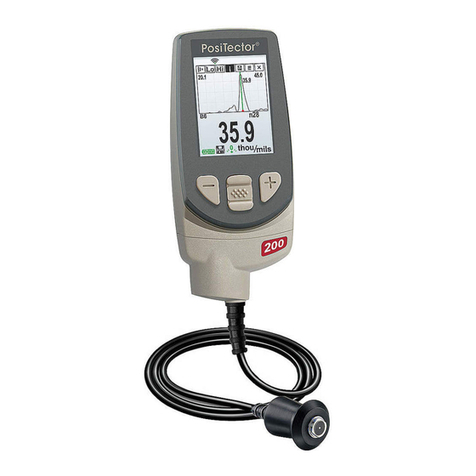
DeFelsko
DeFelsko PosiTector 200 instruction manual