Pulsafeeder ABC 50 Manual

ANALOG BOILER
CONTROLLER
MODEL ABC 50
INSTALLATION
OPERATION
MAINTENANCE
INSTRUCTION
®
$5.00 USA $6.25 CANADA
©1997 Pulsafeeder
72-500-06

2
ABC™ FACTORY SERVICE POLICY
Your ABC™ controller is a state of the art electronic based unit with on-board diag-
nostics. If you are experiencing a problem with your ABC™ controller, first consult
the troubleshooting guide in your operation and maintenance manual. If the prob-
lem is not covered or cannot be solved, please contact our Technical Services
Department for further assistance. Trained technicians are available to diagnose
your problem and arrange a solution. Solutions may include purchase of replace-
ment parts or returning unit to the factory for inspection and repair. All returns
require a Return Authorization number to be issued by Pulsafeeder. Parts purchased
to correct a warranty issue may be credited after an examination of original parts by
Pulsafeeder. Warranty parts returned as defective which test good will be sent back
freight collect. No credit will be issued on any replacement electronic parts.
Any modifications or out-of-warranty repairs will be subject to bench fees and costs
associated with replacement parts.
ABC™ WARRANTY
Pulsafeeder, Inc. warrants ABC™ control systems of its manufacture to be free of
defects in material or workmanship. Liability under this policy extends for 24
months from date of shipment. The manufacturer's liability is limited to repair or
replacement of any failed equipment or part which is proven defective in material or
workmanship upon manufacturer's examination. This warranty does not include
removal or installation costs and in no event shall the manufacturer's liability
exceed the selling price of such equipment or part. The manufacturer disclaims all
liability for damage to its products through improper installation, maintenance, use,
or attempts to operate such products beyond their functional capacity, intentionally
or otherwise, or any unauthorized repair. The manufacturer is not responsible for
consequential or other damages, injuries, or expense incurred through the use of its
products.
The above warranty is in lieu of any other warranty, whether expressed or implied.
The manufacturer makes no warranty of fitness or merchantability. No agent of
ours is authorized to provide any warranty other than the above.

CONTENTS
1. INTRODUCTION. . . . . . . . . . . . . . . . . . . . . . . . . 3
2. INSTALLATION . . . . . . . . . . . . . . . . . . . . . . . . . 4
3. OPERATION . . . . . . . . . . . . . . . . . . . . . . . . . . 8
4. ELECTRODE REMOVAL, CLEANING AND REINSTALLATION . . . . . 11
5. MAINTENANCE . . . . . . . . . . . . . . . . . . . . . . . . 12
6. TROUBLE SHOOTING GUIDE . . . . . . . . . . . . . . . . . . 13
7. ASSEMBLY DIAGRAMS AND PARTS LISTS. . . . . . . . . . . . 14
8. ABC SERIES LINE UP AND OPTIONS . . . . . . . . . . . . . . 16
1. INTRODUCTION
The Pulsafeeder ABC Controllers are used to control total dissolved solids
(TDS) in steam boiler systems, in terms of electrical conductivity measured in
microsiemens per cm (µS/cm). They are designed using the latest technology
with plug-in circuit boards.
The units are very accurate and easy to use. This simplified design provides
automated control at an economic cost.
The ABC Series comes standard with connections for AC power and blow
down activation.
3
ANALOG BOILER CONTROLLER
MODEL ABC 50
®

A. LOCATION:
The ABC Series Controllers are designed for ease of installation. Select a
mounting location convenient to electrical and plumbing connections and easily
accessible by the operator for cleaning and maintenance.
The enclosure is corrosion resistant and will stand up to most industrial envi-
ronments. Be sure unit is free from vapors and liquid spills (Refer to Fig. 1,
Typical Installation Diagram). Installation should comply with all national,
state and local codes.
2. INSTALLATION
Fig. 1, Typical Installation Diagram
ABC
ABC
4

B. MOUNTING:
Mount Controller vertically on a wall or a permanent
vertical support with adequate lighting and at a comfort-
able level (Refer to Fig. 2, Controller Dimensions).
C. ACCESSORIES:
(Available through your Pulsafeeder distributor or sales
representative, but not included as standard)
Boiler Conductivity Timed Sample:
1. Blowdown valve, solenoid and strainer or motor oper-
ated ball valve.
2. Needle valve or orifice union and plates for throttling
blowdown.
3. A full-port gate valve for isolation of blowdown
assembly.
4. A flush valve for sensor.
Boiler Conductivity Continuous Sample:
1. Blow down valve, solenoid and strainer or motor
operated ball valve.
2. Two needle valves or two orifice unions and plates for throttling blowdown.
3. A full-port gate valve for isolation of blowdown assembly.
4. A flush valve for sensor.
D. PLUMBING:
A flow rate of at least 1-3 gpm (gallons per minute)
at the electrode is required for proper operation.
Install hand valves on both sides of electrode for easy removal and periodic
maintenance.
Direction of flow should be in line with the arrow on probe assembly. Take
time to review Fig. 1, Typical Installation Diagram, and note locations of hand
valves, etc. for proper operation and maintenance of all components in the sys-
tem loop. The throttling valve must be adjusted so that water flows across the
probe, not steam.
5
Fig. 2, Controller Dimensions

E. ELECTRICAL:
The ABC controller has been designed to physically separate the high voltage
connections from low voltage connections. Use only 16 or 18 AWG wire for
conduit power and load connections.
1) High Voltage Connections:
Units must be wired by the customer, refer to Fig. 3 (also see Fig. 10) for
wiring the high voltage connections. The connector JP16 is for the AC input
voltage, JP4 and JP5 are relay driven AC outputs, they change simultaneous-
ly and have a maximum output of 5 amps.
The ABC 50 has two fuses for protection, a 1 amp fuse for the controller
power supply, and a 5 amp fuse for the relay output. Part numbers can be
found in the Trouble Shooting section.
Use the following table when connecting to JP4, JP5, and JP16:
CIRCUIT DESIGNATOR CONNECTION TYPE
BLK or NO/NC Line
WHT Return
GRN Ground
NOTE: Always use caution when making any electrical connection. Follow
all applicable electrical codes. The power supply should be disconnected
at the main before making any (high or low voltage) connections.
6
Fig. 3, High Voltage Wiring Diagram

2) Low Voltage Connection:
Please refer to Fig. 4, Low Voltage Connections (located on the front of the
control panel). Generally, low voltage wires are color coded to the designa-
tors printed on the front overlay. Make these connections after making the
high voltage connections and re-
assembling the panel to the front
of the unit.
The insulation on the low voltage
wires is stripped back approxi-
mately .25 inches at the factory.
To attach, push in and hold the
orange tab above the socket while
inserting the stripped lead.
Release the orange tab and pull
gently on the wire to seat it in the
connector and to insure a good
connection.
NOTE: Be careful not to push
the wire too far into the socket
such that the insulation is clamped by the connector.
CIRCUIT DESIGNATOR CONNECTION TYPE PROBE WIRE COLOR
RED Probe + Red
BLK Probe - Black
CLR Probe Temp. Comp. Clear, Green, or White
SHD Probe Wire Shield Silver (no Insulation)
NOTE: Do not connect the ground wire to the Shield (SHD) input. It is for
the shield of the probe cable only.
NOTE: The ABC 50 does not support temperature compensation. A tempera-
ture compensated probe may be used, but will yield non-temperature com-
pensated results.
7
Fig. 4, Low Voltage Wiring Diagram
The figure at right illustrates
how an actuated (motorized)
ball valve, which is used for
“blow down”, is connected to
the ABC 50.
It employs a normally open
(NO), a normally closed (NC),
and common (or neutral) con-
nections. In this example, the
first device is connected at JP5.
Location is behind control
panel (see Figure 3).

3. OPERATION
A. CONTROLS:
Refer to Fig. 5, Front Panel Diagram
and familiarize yourself with the con-
trols of your ABC unit.
Control LED: Used for electrode calibra-
tion and to indicate conductivity trip
point has been reached. (Indicates blow
down solenoid relay is active).
Power LED: Indicates unit is plugged in
and power is present on the circuit
board.
Cal: Calibration adjustment knob used to
calibrate unit conductivity.
Test Switch: Activates solenoid relay to confirm proper operation of externally
connected electrical devices (eg. blow down valve).
In Timed Sample Mode, the test switch initiates the blow down cycle.
Trip Point Knob/Scale: Also referred to as “set” or “control” point. Use the Trip
Point knob to set desired “trip” point to activate bleed and feed. This knob and
scale is also used during calibration.
B. CALIBRATION
The ABC 50 controller will require calibration periodically due to changes in
temperature, and the electrodes becoming dirty. Use the test switch to force a
system blow down if necessary for gathering a sample of system water.
NOTE: For best results, calibrate the ABC 50 at a conductivity as near to the
trip point as possible.
1) Make sure unit is mounted properly and all
plumbing and electrical connections are secure
before applying power to the unit.
2) Take a sample of the boiler water and mea-
sure the conductivity with a calibrated hand held
meter (Fig. 6). Take the sample at low pressure.
If your hand held meter is not temperature com-
pensated allow the sample to cool before mea-
suring the conductivity.
8
Fig. 6, Water sample reading
Fig. 5, Front Panel Diagram (cover in place)

3) Set the trip point knob to the conductivity measured by the hand held meter
(Fig. 7).
4) Turn the cal knob fully counter clockwise and momentarily activate the test
switch (Fig. 8). If the unit is in continuous mode you will need to wait 10 sec-
onds before slowly turning the cal knob clockwise. If the unit is in the timed
sample mode you will need to wait for the blow down interval to pass, 30 sec.,
1, 2, or 4 minutes before slowly turning the cal knob clockwise. When the con-
trol led turns off stop turning the cal knob, the unit is calibrated.
C. SETTING CONDUCTIVITY TRIP POINT
1) Turn Trip Point Knob to position
pointer on scale to desired trip point.
(See Fig. 9)
NOTE: All standard ABC units have a
differential control that has been
factory set to approximately 6% of
the Trip Point. This important fea-
ture prevents “chattering” (the rapid
on-off switching of the relay when
system conductivity hovers near the
trip point).
The minimum blow down interval in
Continuous Sample Mode is eight
seconds to allow for full movement of
a ball valve.
Fig. 9 Set Trip Point
Fig. 7 Position Trip Point Knob
Fig. 8 Turn Cal Adjust Knob
9

10
D. JUMPER SELECTIONS
The ABC controller can be operated in either timed or continuous mode, the
ABC controller has jumpers for selection of the operating mode and the time
intervals (Fig. 10).
CONTINUOUS MODE
For Continuous Mode operation, a jumper should be installed in position JP7.
JP6 should be empty.
NOTE: The minimum blow down interval in Continuous Sample Mode is eight
seconds to allow for full movement of a ball valve.
TIMED SAMPLE MODE
For Timed Mode operation, a jumper should be installed in JP6. JP7 should be empty.
The sample intervals available are 24 hours, 8 hours, 2 hours, and 30 minutes.
A jumper in JP8 selects 24 hours, JP9 selects 8 hours, JP10 selects 2 hours, and
JP11 selects 30 minutes. Jumper only one of the positions JP8 through JP11.
In the Timed Mode, there is a choice of 30 sec., 1, 2, or 4 minute blow down
intervals. A jumper in JP15 selects 30 seconds, JP14 selects 1 minute, JP13
selects 2 minutes, and JP12 selects 4 minutes. Jumper only one of the positions
JP12 through JP15.
NOTE: In the timed mode, the blow down interval will be at least the time
selected. If conductivity is still above the selected trip point (after selected
interval time has expired), blow down will continue until conductivity drops
below the selected trip point.
Fig. 10,
Jumper connection
locations.
Jumper connection
JP6 through JP15
Jumper connection
JP1, 2, 3, 17, and 18
High Voltage connections

11
JUMPER FUNCTION USER CHOICE
JP2, JP17 Selects 50 Hz operation Factory installed
JP3, JP18 Selects 60 Hz operation Factory installed
JP6 Selects Timed Sample Mode Select either JP6 or JP7
JP7 Selects Continuous Sample Mode
JP8 Selects a 24 hour time between sample intervals Select one of JP8 - JP11
JP9 Selects a 8 hour time between sample intervals
JP10 Selects a 2 hour time between sample intervals
JP11 Selects a 30 minute time between sample intervals
JP12 Selects a 4 minute blow down every sample interval Select one of JP12 - JP15
JP13 Selects a 2 minute blow down every sample interval
JP14 Selects a 1 minute blow down every sample interval
JP15 Selects a 30 second blow down every sample interval
4. ELECTRODE REMOVAL, CLEANING,
AND REINSTALLATION
A. REMOVING THE ELECTRODE
1) Remove power from the controller.
2) Remove pressure by shutting hand valves on both
sides of the electrode assembly (refer to Fig. 1,
Typical Installation Diagram).
3) Open flush valve to drain water from the electrode
piping, This will help removal of the electrode.
4) Unscrew electrode, and remove electrode by pulling
straight out. (See Fig.11, Electrode)
B. CLEANING ELECTRODE
1) Wipe the electrodes with a clean cloth. It is important to be sure to wipe the
sides of the electrodes as well as the ends.
2) Use fine grain emery cloth for stubborn stains.
3) Oils can affect probe performance. Do not touch probe surface. The probe
can be agitated in a mild solution of dish washing soap and water to remove
oils transferred during handling.
4) Some fouled electrodes might require dipping in a mild solution of muriatic
acid to remove fouling.
C. REINSTALLING ELECTRODE
1) Apply 4 wraps of Teflon tape to electrode thread. Reinstall electrode, paying
attention to the arrow on the electrode for direction of flow.
2) Close flush valve and open hand valves to reapply pressure to the flow
assembly.
NOTE: Open hand valves slowly to avoid water hammer.
3) Reapply power to the system and re-calibrate unit.
CROSS TEE
ELECTRODE
ASSEMBLY
WIRES TO
CONTROLLER
Fig. 11 Electrode

5. MAINTENANCE
A. SET UP A MAINTENANCE PROGRAM FOR
YOUR CONTROLLER.
Normally, the electronic circuitry in the controller will not require maintenance.
However, ambient temperature, humidity changes, and aging can affect the cali-
bration of the controller. Electrodes will become dirty over a period of time and
will require cleaning. The frequency of cleaning depends on the installation and
the water that comes in contact with the electrode.
During the first few months of operation, check the electrode each week. This
allows you to determine how often to clean the electrode. After the first few
months of operation, you will be able to establish a proper maintenance sched-
ule for your system. Check the electrode and controller calibration at least once
every two months. The more frequent the maintenance, the more assurance you
have of reliable controller performance.
By observing readings before and after electrode cleaning, you can determine
how often to clean the electrode. If no change or only a small change in read-
ings occurs, clean the electrode less often. If a large change in readings occurs,
clean the electrode more often. See Cleaning the Electrode on page 11 of this
manual.
B. ACCURACY AND READINGS
The conductivity of any solution changes with the temperature of that solution.
Without some method to compensate for these changes, a unit will consist of
the conductivity caused by the particular level of dissolved solids, plus or
minus the effect of temperature. The ABC 50 Controller is not compensated for
temperature. The user is responsible for maintaining consistent probe tempera-
tures at calibration and during operation.
12

13
6. TROUBLE-SHOOTING GUIDE
SYMPTOM POSSIBLE CAUSE SOLUTION
Power light is not on Blown fuse Replace fuse with Bussman PCC1 (1 amp)
or equivalent.
No power supplied Check line circuit breaker.
to unit
Relay fuse blows repeatedly External component Disconnect external loads. If
defective this prevents the fuse from blowing, plug
each external load in, one-by-one, until the
fuse blows. Repair or replace defective
component.
Motorized ball valve current Max. 5 amp resistive (Wickman 19733K,
requirements too great 5 amp or equivalent). Use a motor contactor
to control the valve.
Control light stays on Conductivity of water Check the conductivity of the
sampled is beyond water with a conductivity tester
range of controller and compare readings.
Probe leads Unplug probe leads, light should go off.
shorted Check lead for shorts.
Bleed valve plugged - no Clean or replace valve.
bleed off
Insufficient or no flow Remove obstruction in sample line.
past electrode.
Blow down line throttled too much Increase blow down rate.
Control light does not Leaking system Check blow down valves.
come on
Control light goes on and Electrode is air-bound Bleed air from electrode by
off every few minutes allowing water to completely
fill and flow through it to drain.
Adjust throttling valve so that only
water flows across the probe.
Check surface skimmer 4 to 4 inches below
surface
Wide variation in solution Poor circulation through Clean electrode.
conductivity electrode
Bleed rate exceeds Decrease bleed rate.
make-up water rate
Bleed rate too low Increase bleed rate.
Conductivity of solution Electrode fouled or dirty Clean or replace electrode.
is slowly rising
Bleed rate too low Increase bleed rate.
Bleed-off solenoid or other Inoperative solenoid valve Replace valve coil or valve as required.
electrical device being
operated by the controller
does not operate. Wiring between solenoid Rewire this connection. To check solenoid
valve and control defective valve, discon-
nect it from the controller and energize it
from a separate power source.
Improper voltage Check for correct valve coil voltage;
should be 115 VAC. (Optional 220 VAC.)
Improper pressure differential Check piping and pressure at your loca-
across solenoid valve tion to make sure at least the minimum
pressure exists across your solenoid.

7. ASSEMBLY DIAGRAMS AND PARTS LISTS
ENCLOSURE ASSEMBLY
ITEM QUAN. PART # DESCRIPTION
16 REF. 06-008-44 SCREW, 1/4-20 X, 500 LONG
15 REF. 11-037-10 INSERT, BRASS, 1/4-20
14 REF. 06-006-06 SCREW, 6-16 X, 1.00
LONG,SELF TAPPING
13 REF. 06-067-06 STANDOFF, 1/4 HEX,
1.75 LONG
12 REF. 05-057-02 KNOB, 1/4 INSERT
W/ SET SCREW
11 REF. 06-151-00 SCREW, #6-32
10 REF. 03-005-18 O-RING, .441 OD, .301 ID, .070 THK
9 REF. 11-006-01 ROLL PIN
8 REF. 06-028-06 SCREW
7 REF. 11-006-09 BRACKET, WALL FLOW MTG.
6 REF. 01-060-02 ENCLOSURE
5 REF. 02-092-04 MOUNTING PANEL
4 REF. 08-986-0012 MAIN ASS’Y ABC PCB
3 REF. 02-092-00 PANEL, MAIN PCB MTG.
2 REF. 03-005-60 GASKET, ENCLOSURE
1 REF. 02-092-02 COVER, CONTROLLER
14
1
2
3
7
5
6
8
2
4
12
10
2
9
2
11
4
14
2
13
4
15
4
16
4

15
ELECTRODE ASSEMBLY
ITEM QUAN. PART # DESCRIPTION
7 1 03-0132-00 CROSS, 1" 2000LBS
6 1 04-027-00 BN-1/EH-1RS BOILER PROBE
5 1 03-131-00 UNION, BOILER, 1/2" L500
4 2 03-180-00 NIPPLE, 1/2" X CLOSE, GALVANIZED
3 1 03-180-20 GASKET, ACCESS TEE, 1/2", OLKRG
2 1 03-180-10 COVER, ACCESS TEE, 1/2" OL10
1 1 03-178-00 ACCESS TEE 1/2" OT 1
NOTE: Use Teflon tape on all NPT fittings.
1
VENT ONLY - LEAVE OPEN
5
NOTE: ARROW MUST BE IN
DIRECTION OF FLOW
6
7
4
2

®
A Unit of IDEX Corporation
27101 Airport Road
Punta Gorda, FL 33982
Toll free: 1-800-333-6677
Phone: 1-914-575-3800
Toll free Fax: 1-800-456-4085
Fax: 1-941-575-4085
8. ABC BOILER CONTROLLER SERIES
A. KEY FEATURES:
• Front panel calibration.
• Front panel dial set point.
• Conductivity range 0-5,000 µS/cm.
• Blow down indicator LED.
• Relay test switch.
• Power indicator LED.
• Weather-tight enclosure designed to NEMA 4X.
• Wall mountable.
B. ABC MODEL STANDARD FEATURES:
ABC 50 Dial conductivity controller 0-5,000 µS/cm
ABC 101 Dial conductivity controller selectable scale
0-500, 1000, 2000, 5000, 10,000, and 20,000 µS/cm
ABC 102 Analog meter conductivity controller selectable dual
scale 0-500, 1000, 2000, 5000, 10,000, and 20,000 µS/cm
C. OPTIONS: SERIES AVAILABLE
M-3 4-20 mA Isolated output (08-986-08) 101/102
P 230 VAC @ 50/60 Hz service 50/101/102
R Conductivity; in-line type, max. pressure 50
250 psi, max. temp. 400ºF (04-750-02)
Table of contents
Other Pulsafeeder Controllers manuals
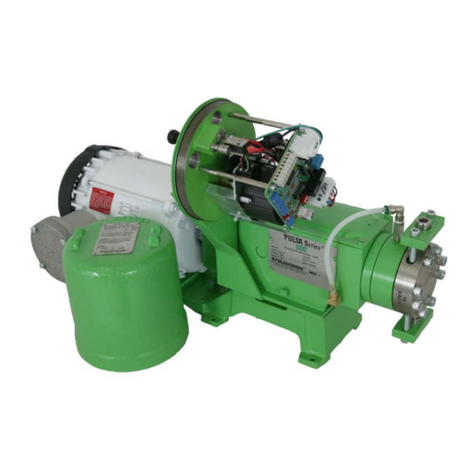
Pulsafeeder
Pulsafeeder ELMA NEMA 4X Instruction manual
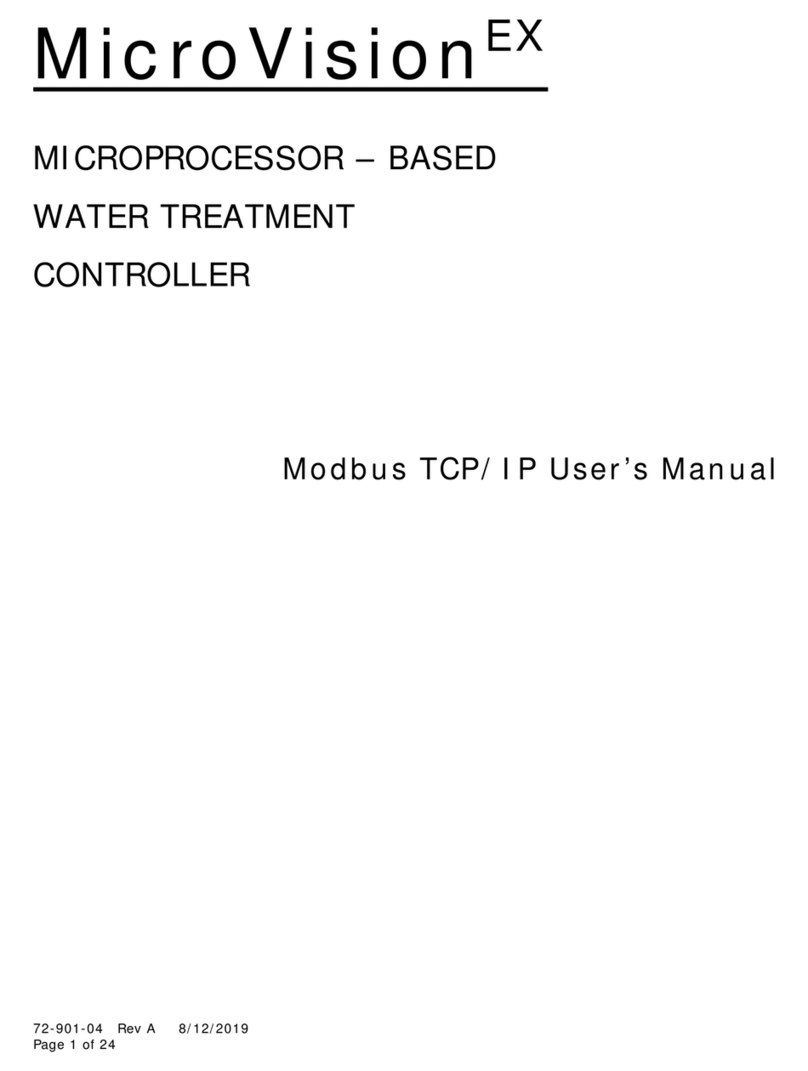
Pulsafeeder
Pulsafeeder MicroVision EX User manual
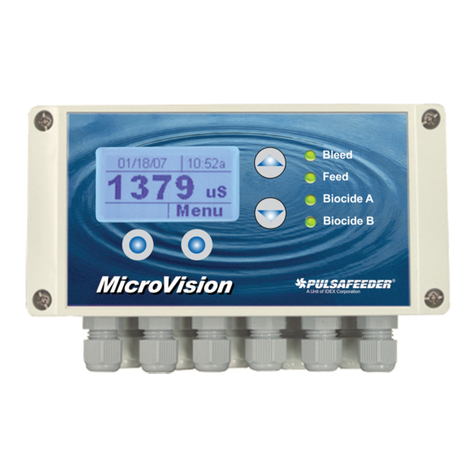
Pulsafeeder
Pulsafeeder MicroVision User manual
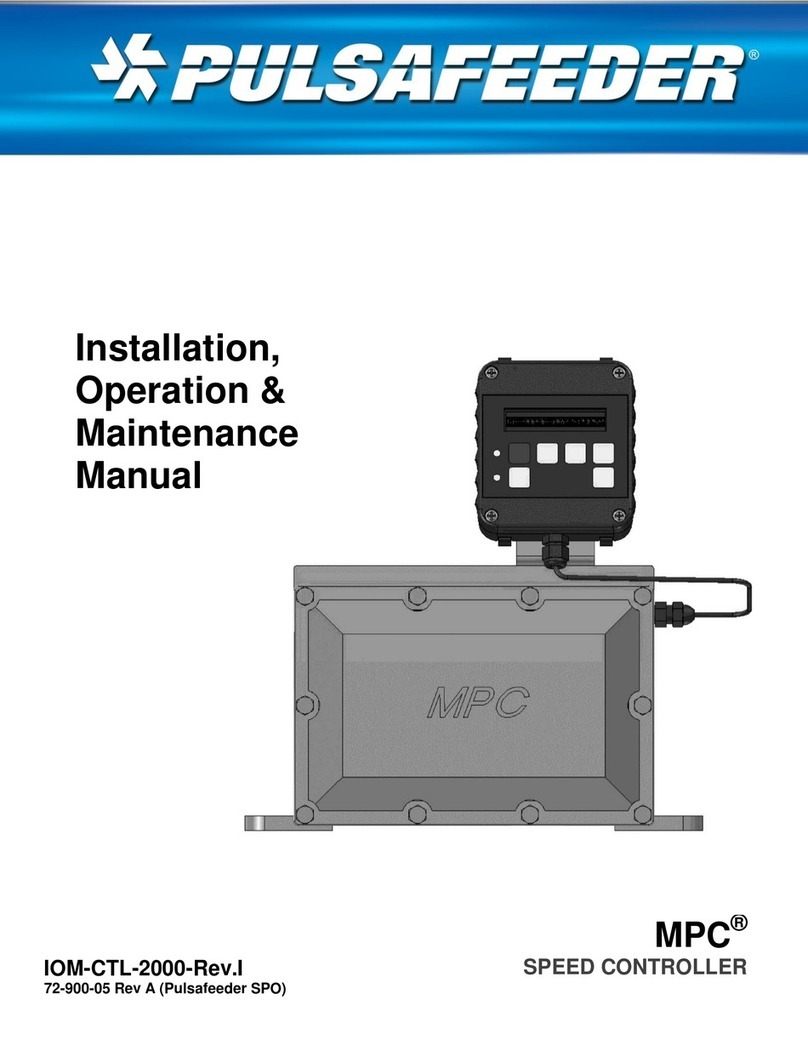
Pulsafeeder
Pulsafeeder MPC Instruction manual

Pulsafeeder
Pulsafeeder MicroVision EX User manual

Pulsafeeder
Pulsafeeder PULSAblue 3300 Series User manual
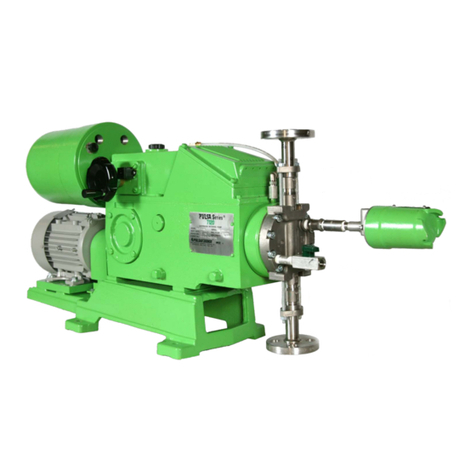
Pulsafeeder
Pulsafeeder PULSAmatic 7120 Manual