Pulsafeeder MicroVision EX User manual

72-900-06 Rev. F
Page 1 of 38
MicroVision
EX
MICROPROCESSOR –BASED
WATER TREATMENT
CONTROLLER
Installation Operation Manual

72-900-06 Rev. F
Page 2 of 38
Table of Contents
1. GENERAL WARNINGS ...............................................................................................................................4
2. MicroVisionEX FEATURES ..........................................................................................................................4
3. INSTALLATION ............................................................................................................................................6
3.1 Location......................................................................................................................................................6
3.2 Mounting Hardware ...............................................................................................................................6
3.3 Opening the Enclosure .........................................................................................................................6
3.4 Sensor Installation.................................................................................................................................7
3.5 TYPICAL INSTALLATION ......................................................................................................................7
3.6 IMPORTANT SYMBOL INFORMATION..............................................................................................8
3.7 ELECTRICAL WIRING ............................................................................................................................8
3.8 Flow Switch Input ................................................................................................................................12
3.9 Sensor (probe) Connection Input ..................................................................................................12
3.10Water Meter Input ...........................................................................................................................12
3.11 Drum Level Input .............................................................................................................................12
3.12 4-20mA Output .................................................................................................................................12
3.13 4-20mA Input ....................................................................................................................................12
3.13.1 Fluorometer –Trace Chemical ............................................................................................13
3.13.2 Calibrating PTSA Probe ..........................................................................................................14
3.14 Alarm Dry Contact Relay...............................................................................................................14
3.15 Keypad Operation ............................................................................................................................15
3.16 Communications (Optional) .........................................................................................................15
4. CONTROLLER PROGRAMMING.............................................................................................................16
4.1 Menu Map................................................................................................................................................16
4.2 Menu Navigation...................................................................................................................................16
4.3 Home screen ..........................................................................................................................................16
4.4 Main Menu...............................................................................................................................................17
4.5 Relay HOA ...............................................................................................................................................17
4.6 Configure .................................................................................................................................................17
4.6.1 Date/Time .......................................................................................................................................17
4.6.2 Digital Inputs .................................................................................................................................18
4.6.3 4-20mA Out and 4-20mA In....................................................................................................18
4.6.4 Gal/Lit ...............................................................................................................................................18
4.6.5 Meter Totals....................................................................................................................................18
4.6.6 Languages Menu...........................................................................................................................18
4.6.7 Display Settings ............................................................................................................................19
4.6.8 Password Setting..........................................................................................................................19
4.6.9 Software Version ..........................................................................................................................20
4.6.10 Factory Reset Function...........................................................................................................20
4.7 Settings....................................................................................................................................................20
4.7.1 Conductivity ...................................................................................................................................20
4.7.2 pH and ORP ....................................................................................................................................22
4.7.3 4-20mA Outputs (Optional Accessory)................................................................................24
4.7.4 4-20mA Inputs (Optional Accessory)...................................................................................24
4.8 Timers - Modes .....................................................................................................................................24
4.8.1 Timers –Pulse Timer ..................................................................................................................25
4.8.2 Timers –Percent Timer .............................................................................................................25
4.8.3 Timers - 28 day (Biocide Timer) ............................................................................................25
4.8.4 Timers –% Post Bleed...............................................................................................................26
4.8.5 Timers –Limit Timer (Bleed and Feed)...............................................................................26
4.8.6 Timers –Alarm..............................................................................................................................26

72-900-06 Rev. F
Page 3 of 38
4.8.7 Timers –Set Point Control Mode ...........................................................................................26
4.8.8 Timers –Disabled (Default).....................................................................................................27
4.8.9 Timers –Bio Tracking (In All Timer Modes) ......................................................................27
4.9 Communications ...................................................................................................................................27
4.10 USB........................................................................................................................................................27
4.10.1 USB Graphing Tool ..................................................................................................................28
4.10.2 USB Data log Timer and Tamper Codes:........................................................................28
4.11 Ethernet (Optional) .........................................................................................................................29
4.11.1 Programming your controller PulsaLink...........................................................................29
4.11.2 Setting Up Your Controller on PulsaLink .........................................................................29
5. FACTORY DEFAULTS ...............................................................................................................................30
6. TROUBLESHOOTING GUIDE.................................................................................................................32
7. MAINTENANCE...........................................................................................................................................33
7.1 Conductivity Sensor removal and cleaning................................................................................33
To remove the conductivity sensor from its tee for cleaning: ....................................................33
To clean conductivity sensor:..................................................................................................................33
7.2 pH sensor Information .......................................................................................................................33
7.2.1 Preparation .....................................................................................................................................33
7.2.2 Sensor Storage .............................................................................................................................34
7.2.3 Sensor Cleaning............................................................................................................................34
7.3 ORP Sensor Information....................................................................................................................34
7.3.1 ORP Maintenance and Troubleshooting ...............................................................................34
7.3.2 Testing ORP Sensor.....................................................................................................................34
7.3.3 Flow Sensor ....................................................................................................................................35
8. SPECIFICATIONS......................................................................................................................................35
9. FORSEABLE MISUSE ...............................................................................................................................36
10. MOUNTING HOLE PATTERN (Footprint)...........................................................................................37

72-900-06 Rev. F
Page 4 of 38
Introduction
The MicroVisionEX microprocessor based cooling tower controller has been designed to
monitor and control Total Dissolved Solids (TDS) in terms of electrical conductivity
measured in micro Siemens per centimeter (uS/cm). Some models also include pH, and
ORP control. A set point of the desired value to control is entered into the controller
through the front panel. As this limit is exceeded, a valve, pump or other control device
is activated via an onboard control relay to adjust the reading being measured.
1. GENERAL WARNINGS
Symbol hereinafter and upon the unit means WARNING!
If the equipment is used in a manner not specified by the manufacture, the overall
safety may be impaired.
The plug is considered mains power. Disconnection means should be readily
identifiable and easily accessible to the operator after install
Adequately rated and APPROVED/CERTIFIED power supply cord and plug (supplied
by Pulsafeeder), or cable gland suitable for the applicable country is to be attached
and replaced by manufacturer’s authorized qualified person or as per applicable local
and national regulations
Controller is for indoor use only and not suitable for wet location. Controller housing
is IP65 compliant and may be configured as such.
Verify the mains supply ratings (e.g. Volts, Amps, and Hz) where the controller is to
be powered from and ratings of the accessories as well as ratings of the controller’s
receptacles/outlets before powering up.
2. MicroVisionEX FEATURES
Toroidal Probe
MicroVisionEX uses a toroidal probe for conductivity measurement. The
measurement is made by passing an AC current through a toroidal drive coil,
which induces a current in the electrolyte solution. This induced current in turn,
induces a current in a second toroidal coil, called the pick-up toroid. The amount
of current induced in the pick-up toroid is proportional to the solution conductivity.
Output Relays
The control of the HANDS –OFF –AUTO (HOA) output relays can be controlled using the
HOA menu.
RELAY STATUS
LED COLOR
ON (FORCED ON FOR 5 MIN.)
AMBER
OFF
RED
AUTOMATIC ‘ON’
GREEN
AUTOMATIC ‘OFF’
OFF

72-900-06 Rev. F
Page 5 of 38
Drum Levels
Three (3) onboard dry contact inputs serve as Drum Level inputs. When a low level is
detected the unit will go into an alarm state and the low drum’s identity will be displayed
on the screen. The user can program the alarm to deactivate a timer if desired. Drum
level #1 is assigned to timer #1, drum level #2 is assigned to timer #2 and drum level
#3 is assigned to timer #3.
Flow Switch
MicroVisionEX has a dry contact flow switch input that will de-activate all of the control
output relays upon a no-flow indication. An alarm condition will be indicated and “Flow
Switch Alarm” will be displayed. This input is active closed:
Open = no flow; closed = flow.
If a flow switch input or other alarm condition exists, the LED’s on the front
panel will flash until the alarm condition is cleared.
4-20mA Outputs and Inputs
Optional 4-20mA inputs or outputs can be installed to increase the capabilities of the
MicroVisionEX. Connect 4-20mA equipment to the + and –terminals as shown on page 9.
Water Meter
MicroVisionEX has a dedicated water meter input that is capable of reading a dry contact
or Hall effect type water meter. Through programming this input can be used to signal a
pulse timer as well as totalizing water consumption. Some models offer up to six (6)
water meter inputs.
Alarm Relay
MicroVisionEX has a dedicated dry contact relay that can be used to interface with process
control equipment or visual indicators. This relay is un-powered.

72-900-06 Rev. F
Page 6 of 38
3. INSTALLATION
3.1 Location
Select a mounting location convenient to grounded (True Earth) electrical and
plumbing connections. It is recommended that the controller is mounted on a wall or
other vertical surface with adequate lighting at a comfortable level. Installation
should comply with all national, state, and local codes.
Avoid locations where the controller would be subjected to direct
sunlight, extreme cold, heat, or humidity {less than 36°F (2.2°C) or
greater than 122°F (50°C), or greater than 95% RH non-condensing,
direct sunlight, vibration, vapors, liquid spills, or EMI (electromagnetic
interference; e.g., strong radio transmission and electric motors.)
Install at less than 2000m above sea level.
SAFETY PROTECTION PROVIDED BY THE EQUIPMENT MAY BE IMPAIRED IF THE
EQUIPMENT IS USED IN A MANNER NOT SPECIFIED BY THE MANUFACTURER.
THIS CONTROLLER IS INTENDED FOR INDOOR USE ONLY AND NOT SUITABLE
FOR WET LOCATION.
3.2 Mounting Hardware
Mount the controller using the four (4) holes provided.
Typically, use a #8 screw or equivalent. The mounting screw should be appropriate
for the location mounting on, i.e., sheet metal screws for mounting onto sheet metal,
wood screws for mounting onto wood or wall studs, and hollow wall drywall anchors
for mounting to drywall. Mount should be designed for 7.5 Kg, 17 lbs.
Mount the unit ergonomically, such that the unit is visible without excessive
bending or lowering of the body, and not too high such that the internals are
not visible with opening the enclosure.
3.3 Opening the Enclosure
Loosen the knob that secures the clear front cover. Then loosen four (4) screws in
the four corners of the front of the controller and carefully swing the top of the case
forward.

72-900-06 Rev. F
Page 7 of 38
3.4 Sensor Installation
Conductivity
The controller is supplied with a temperature compensated toroidal conductivity probe
installed in a tee. The probe should only be installed where adequate flow is going around
and through the hole in the center of the probe in the tee provided.
pH and ORP
When ordered as a pH or ORP model the controller will be supplied with standard pH and
ORP probes. The probes are supplied installed in a tee. The probes should only be installed
where flow between 1 and 5 GPM is going around the probe.
Flow Switch
If the controller is provided with a flow switch, install the flow switch so that flow enters
into the bottom of the flow switch tee, and out the side of the tee. The flow switch must
always be installed in a vertical position so that the sensor wire is coming out of the top,
and the internal (red) flow shuttle is able to rise when there is flow and drop when there is
no flow. The flow switch is activated when 1 GPM (3,8 LPM) is going through it, and is
deactivated when the flow drops below 1 GPM (3,8 LPM).
3.5 TYPICAL INSTALLATION
Over pressurization of the plumbing can occur when cooling tower is higher than the
piping and controller system. Ensure all pressures have been accounted for. Verify piping
and sensor allowable temperatures are above maximum temperatures of the system.

72-900-06 Rev. F
Page 8 of 38
3.6 IMPORTANT SYMBOL INFORMATION
Warning indicates a condition that could cause damage to both the
equipment and the personnel operating it. Pay close attention to any
warning.
Primary Supply Ground must be connected to earth ground for safe
operation of the controller.
Chassis Ground –Connect the equipment’s ground wire here for safe
operation of external devices.
Notes to provide tips and hints
3.7 ELECTRICAL WIRING
CONTROLLER MUST BE WIRED IN ACCORDANCE WITH ALL APPLICABLE
ELECTRICAL CODES,NEC, CSA, EN, OR LOCAL AUTHORITY HAVING
JURISDICTION.
The MicroVisionEX electronic input circuitry is fuse protected on both the hot and
neutral inputs using a replaceable eight amp fuse (see page 9). For additional
protection of this instrument, use of a surge protector is recommended.
The controller should be connected to a dedicated power branch (i.e., its
own wiring, GFCI circuit breaker, etc.). For best results, the ground
should be independent (true earth) not shared.
A switch or circuit-breaker, marked as the unit’s disconnecting device
should be included in the installation. It should be in close proximity to
the unit and be easily reached by the operator.
Pre-wired controllers are supplied with a 3-wire grounded power cord and 3-wire
grounded receptacle cords for all controlled line voltage outputs.
Plug is considered as mains power disconnecting device which shall be readily
identifiable and easily accessible.

72-900-06 Rev. F
Page 9 of 38
RELAY BOARD CONNECTIONS
Energy Usage and Duty
The unit utilizes a variety of probes and input signals to control valves, pumps,
and numerous other devices. These items are not all used in a continuous
fashion. The typical unit has a complicated duty cycle dependent on application.
For 120V and a max of 8A, a typical duty cycle of 15 minutes on and 45 minutes
off can be used. This results in an energy calculation of
120V * 8A *Power Factor* 25%
The Power Factor is the cosine of the phase angle between the Current and
Voltage of an AC circuit. Typically, 0.8 is a good estimate for US power.
The 25% is the estimate of a typical duty cycle of 15 on and 45 off.
For 240V, the amperage remains constant.

72-900-06 Rev. F
Page 10 of 38
Relay Assignments
Relay 1
Relay 2
Relay 3
Relay 4
Relay 5
Relay 6
Relay 7
Relay 8
Dry contact
Model
OUT 1
OUT 2
OUT 3
OUT 4
OUT 5
OUT 6
OUT 7
OUT 8
P4
MVECXXX
Bleed
Timer 1
Timer 2
Timer 3
Alarm
MVEC5XX
Bleed
Timer 1
Timer 2
Timer 3
Timer 4
Alarm
MVECPXX
Bleed
pH
Timer 1
Timer 2
Timer 3
Timer 4
Timer 5
Timer 6
Alarm
MVECOXX
Bleed
ORP
Timer 1
Timer 2
Timer 3
Timer 4
Timer 5
Timer 6
Alarm
MVECPOX
Bleed
pH
ORP
Timer 1
Timer 2
Timer 3
Timer 4
Timer 5
Alarm
MVECPOM
Bleed
pH
ORP
Timer 1
Timer 2
Timer 3
Timer 4
Timer 5
Alarm
Conduit Models (Wiring High Voltage)
Conduit controllers have openings for conduit connections for hard wiring. Use only 18
AWG (1,2 mm²) stranded wire for conduit power and load connections. Supply (input)
power is connected via P10 located on the relay board. The top part of this terminal block
is removable to allow for easy access to the connector’s three (3) screws. For CE rated
models ensure all ferrites are installed in their specified configuration.
MAKE SURE THAT THE CONTROLLER VOLTAGE MATCHES THE INPUT VOLTAGE
AND OUTPUT VOLTAGES.DO NOT APPLY POWER UNTIL THIS CONDITION IS VERIFIED.
Make sure that all conduit connections are water tight.
The output relay terminal blocks are identified as: OUT 1 through OUT 8 these terminal
blocks can be removed in the same manner as P10. The first four relay outputs have a
N.O. and a N.C. connection, the others are N.O.
Ensure the snubber’s remain on
each of the relay outputs in the
specified wiring configuration.
Unit is to be connected to supply
mains by a qualified personnel in
accordance with local and
national codes e.g. NEC in the U.S. and CEC in Canada.
A suitable power disconnection means is to be provided
e.g. circuit breaker or switch which is identifiable and
easily accessible to the end user.

72-900-06 Rev. F
Page 11 of 38
DIGITAL BOARD CONNECTIONS
The low voltage connections are found on the top board.
Use 22-24 AWG (,76 mm²) wire for: flow switch, drum levels, dry alarm, and water meter
connections. A recommended wire is OMNI cable DS92203. These signal wires must be
run separate from AC power lines.
Clock Battery # 09-710-04
Low voltage signal wires, e.g., water meter, must be run separate from AC power lines.
Digital Input assignments
There are 5 digital inputs on base conductivity models and up to 10 on featured models.
Digital
Inputs
Input 1
Input 2
Input 3
Input 4
Input 5
Inputs 6 & 7
Inputs 8,9
and 10
Function
Flow
Switch
Drum
Level #1
Drum
Level #2
Drum
Level #3
Water
Meter
Water
Meter
Water Meter
Assignment
N/A
Timer #1
Timer #2
Timer #3
WM #1
WM #2 & 3
WM #4 to #6
Location
P1
P2
P3
P4
P5
P6 and P7
P8, P9, P10
Dry Contact
√
√
√
√
√
√
√
Hall Effect
√
√

72-900-06 Rev. F
Page 12 of 38
3.8 Flow Switch Input
It is recommended that a flow switch or auxiliary dry contact be used to make outputs
inoperative when the cooling tower is shut down. Connect detection wires to P1 to use
this interlock feature. This is active –closed: open = no flow; closed = flow.
If the controller does not have a flow switch, a jumper wire must be
connected across P1.
3.9 Sensor (probe) Connection Input
The controller is supplied with sensors prewired. Depending on the model, the
conductivity probe wires are connected to Probe 1, pH sensor on Probe 2, ORP sensor on
Probe 3, and Make up conductivity on Probe 4.
Always depressurize the unit prior to removing a sensor.
3.10 Water Meter Input
Connect the water meter to P5 on the top board. Some models have additional water
meters on P6 through P10. In order to wire a dry contact type water meter or contact
closure to a 3-port digital input, connect the two leads to the signal and ground ports.
3.11 Drum Level Input
The drum level connections are labeled as, P2 for Level 1, P3 for Level 2, and P4 for level
3. These are active closed: closed = low level; open = level is OK. The input can also be
reversed (NO or NC) in the programming.
3.12 4-20mA Output
The 4-20mA outputs, ordered separately, can be used to remotely measure any of the
controllers probe inputs and any of the 4-20mA inputs. Connect the 4-20mA receiving
equipment to the 4-20mA boards pins are marked + (positive) and –(negative). The
polarity must be observed for proper operation. The 4-20mA output current range is
approximately 0 mA to 24mA. Resistive load range should typically be 300 Ohms with a
max rating of 1200 Ohm.
3.13 4-20mA Input
Model dependent, MicroVision EX can support up to two 4-20mA analog inputs. The 4-
20mA inputs, ordered separately, can be used to receive and data log signals from
sensors that transmit a 4-20mA output. Connect the 4-20mA equipment to the 4-20mA
boards pins are marked + (positive) and –(negative). The polarity must be observed for
proper operation.
Each 4-20mA analog input supports 2 wire loop or transmitter powered configurations.
Input resistance load is approximately 265 Ohms. Input voltage range is commonly 12V
or 24V. Up to 60V is permissible.

72-900-06 Rev. F
Page 13 of 38
Tx Pwr
3.13.1 Fluorometer –Trace Chemical
The MicroVision EX can be optionally purchased panel mounted with a fluorometer, turner
LD2 or Pyxis ST-500 probe. From the factory, the probe comes prewired and calibrated.
Alternatively, the probe can be ordered separately, wired and programmed. Be sure to
observe the manufacturers wiring directions.
3.13.1.1 Turner Little Dipper™2
The turner is an inline fluorometer with a linear 4-20mA output which responds to trace
chemical. Typically is set to 4mA = 0 PPB and 20mA = 200 PPB probe has 4 wires; Red,
Black, Orange, and Brown. The red is the power supply voltage. Black is the Supply
ground. Orange is the positive current loop connection. Brown is the negative current loop
connection. The turner little dipper 2 requires an external power supply of 8-32 VDC (1W
Max)
Tx
Pwr

72-900-06 Rev. F
Page 14 of 38
3.13.1.2 Pyxis ST-500
The Pyxis ST-500 is also an inline fluorometer which outputs both a 4-20mA signal and a
RS-485 interface which responds to PTSA trace chemical. The ST-500 also has a 4-20mA
where 4mA = 0 PPB and 20mA = 200 PPB. Wiring the ST-500 is similar to the Little Dipper
2. The RS-485 bus is not used by the MicroVision EX (The blue and yellow wires). The
only wires necessary to terminate are power to the Pyxis and the 4-20mA loop (Brown or
white (4-20mA+) and Green (4-20mA-)). The clear wire should be connected to the
solution ground.
3.13.2 Calibrating PTSA Probe
4-20mA input probes require a 2 point calibration. In order to calibrate a Pyxis or Turner
inline fluorometer, navigate to the 4-20mA input in question. I.E. Menu -> Settings -> 4-
20mA In 1. For a PTSA probe the units are PPB. Select Type->PPB. Select Back. Scroll
down to Calibrate. For a 2 point calibration you will need a low point and a high point. The
best way to calibrate a low point is to put the probe in deionized water, uncontaminated
with any PTSA. You should see ~4mA as the actual signal. Enter “0000” on the top line.
Before exiting this page the high point will need to be calibrated. This is ideally done in the
actual flow assembly. Place the probe in the flow allow solution to flow across the sensor
to purge any air bubbles out of the sensor. Take a sample with a handheld meter be sure
the mA signal on the controller is stable and enter the high point, the value measured by
the handheld. Alternatively, to calibrate the high point of the sensor, buffer solutions can
be used. Fully submerge the sensor in the known buffer ensure to expel air bubbles which
may have formed on the optics. The known buffer needs to be within the range of the
probes sensing capabilities. Ensure the mA output from the probe has stabilized on the
MicroVision EX under the actual reading. Enter the known value as the high point, upon
hitting enter on the last digit the value will be saved and your probe successfully calibrated.
3.14 Alarm Dry Contact Relay
The alarm dry contact activates for all system alarms and is a volt free signal. Use P4 to
connect the alarm reporting equipment. This relay will close when an alarm condition
exists and will open when no alarm conditions are present. This connection is intended to
be used to signal external process control equipment or indicators (low voltage DC
operated buzzers or lamps) when an alarm condition is present. This relay is not
protected by a fuse and should not be used to voltages above 48VDC.

72-900-06 Rev. F
Page 15 of 38
FRONT PANEL DESCRIPTION
3.15 Keypad Operation
UP/DOWN - Dual function keys are used to move the select
(highlighted) box and to increase and decrease values.
O O - Soft keys used for various functions depending on the
currently displayed screen. The key’s function appears
above the key on the display.
3.16 Communications (Optional)
The MicroVision EX has a variety of cloud capable controllers. These controllers will ship
with a CAT5 cables with an RJ45 connection. To connect the MicroVision EX to PulsaLink,
Pulsafeeders cloud controller management software solution. The controller will need
internet access. Please terminate the provided RJ45 connection to an open internet port.

72-900-06 Rev. F
Page 16 of 38
4. CONTROLLER PROGRAMMING
4.1 Menu Map
4.2 Menu Navigation
MicroVisionEX uses four front panel buttons to navigate through the different menus. Use
these buttons to move up and down within a list of options or move right and left to enter
or change parameter values. In some cases the MicroVisionEX display will prompt the user
to press the different buttons to assist you in selecting or changing data.
Some menus may display highlighted menu options or a checkmark () next to a menu
option. The highlighted menu option is used to indicate that another menu will be displayed
if this option is chosen. The checkmark indicates that a particular control mode has been
selected.
4.3 Home screen
The Home Screen displays the system readings and operating information. This screen is
displayed during normal operation when there are no alarm conditions on the MicroVisionEX.
If an alarm condition occurs an alarm message will flash on the screen. The LED’s to the
right of the display will also flash indicating an alarm has occurred.
The MicroVisionEX will return to this screen if no buttons are pressed for five minutes after
entering a menu.

72-900-06 Rev. F
Page 17 of 38
4.4 Main Menu
The Main menu is the starting point for all subsequent programming menus.
Relay HOA –This menu allows for the control of the relay output states, either
manual off, or auto.
Configure –This menu allows for setting the time and date, display contrast, water
meter, etc.
Settings –This menu allows for setting the conductivity, pH and ORP configurations
Timers–This menu allows for setting the timers for the different feed modes.
Communications–This menu allows for exporting data, exporting settings,
importing settings and upgrading the O/S.
4.5 Relay HOA
From the HOA Outputs menu manually set the relay control outputs. This is useful for
servicing chemical pumps or troubleshooting electrical problems. First select the relay
output to be controlled then select the relay state.
Forcing the output to Auto may cause the control output to energize without warning.
4.6 Configure
From the Configure menu select from many different system configuration options.
Date/Time –Set the current date, date format, time, and time format.
Digital Inputs –Set the drum level settings, and water meter type and volume.
4-20mA Out- Activate or deactivate 4-20mA output options.
4-20mA In- Activate or deactivate 4-20mA input options.
Gal/Lit- Set the units that the controller displays.
Meter Totals- Display and/or reset the water meter totals.
Language –Change the controller displayed language.
Display Settings –Set the display, brightness, home screen display text, home
screen scroll rate, home screen alarm message size, and the display dampener.
Password –Set the user password.
Software Version –Displays the current software version.
Factory Restore –Restore the parameters to factory default
4.6.1 Date/Time
From the Date/Time menu set the date and time as well as the date and time display
formats.
Set Date –Set the current date.
Set Time –Set the current time.
Date Format –Pick the day/month/year format.
Time Format –Pick the 12-hour or 24-hour time of day format.

72-900-06 Rev. F
Page 18 of 38
4.6.2 Digital Inputs
4.6.2.1 Drum Level
From the Drum Level menu select how the timer output will respond to a low drum level
indication. The available choices are to allow the pump to continue to run, or have the
pump stop when its drum level goes low. Drum level #1 is always assigned to timer #1,
Drum level #2 is always assigned to timer #2, and drum level #3 is always assigned to
timer #3.
Alarm Trigger –Program the drum level to go into alarm when the drum level
switch contact is either open or closed.
Action on Alarm –Program the drum level input to either turn off the timer relay
on alarm or allow it to keep the relay on in automatic mode.
When a drum level goes low the controller will go into alarm regardless of this
setting. Re-filling a low drum may cause the pump control output to energize without
warning.
4.6.2.2 Water Meter
From the Water Meter menu select what type of water meter the controller is attached to.
Once the meter type has been entered the next setting will be for the gallons/liters per
pulse or K-factor, depending on the meter type.
Dry contact or Hall-effect water meter-Once the type is selected enter the
resolution or volume per pulse or pulses per gal/lit for hall effect.
Gal/pulse or K factor –enter the setting for the water meter connected.
4.6.3 4-20mA Out and 4-20mA In
Activate or deactivate the 4-20mA output or input options in this screen. Analog inputs and
outputs are upgrade options for all models. To install analog signal options, first activate
them in this screen, then power the unit down and then install the signal modules as
described in the upgrade kit instructions. When the 4-20mA inputs or outputs are activated
they will have their own program settings in the “Settings” menu.
4.6.4 Gal/Lit
Select the unit of measure for the controller to display for the water meter settings.
4.6.5 Meter Totals
In the meter totals screen view the water meter total values and the date they were last
reset and reset the total values to zero in this screen.
4.6.6 Languages Menu
Select the language the controller programming displays.
English
Spanish
Portuguese

72-900-06 Rev. F
Page 19 of 38
4.6.7 Display Settings
This menu is for setting how the controller display appears.
4.6.7.1 Brightness
Select this menu to set how bright the background is, Low, Medium, or High.
4.6.7.2 Display Line text
Select this menu to change what text is displayed on the two lines of the main home screen
display. (Pulsafeeder and MicroVision EX are the default)
4.6.7.3 Home Screen Display Scroll
Select this menu to set the speed that the home screen scrolls from displaying various
values, Low (30 seconds), Medium (10 seconds), or High (5 seconds), or OFF for no
scrolling of the main menu.
4.6.7.4 Display Alarm
Select this menu to set the size of the alarm messages that are displayed in the home
screen when they occur.
4.6.7.5 Display Dampener
The Display Dampener setting sets how often the actual conductivity reading is updated on
the Home Screen. This results in dampening of the controller response to sudden changes
in conductivity.
The controller takes a conductivity reading once every second. Increasing this value
above one second causes the controller to average the readings, hence, slowing down
the control functions.
4.6.8 Password Setting
The Controller has two Security Access Codes, each with different system privileges - an
Administrator and a User. An Administrator can access all functions of the controller. A
User level can only access those items selected by the administrator. A password level is
not required for access to the home menu.
Both passwords are active when Administrator level password is set. Conversely, both
passwords are inactive when the Administrator level password is set to 000000. Each
password consists of a six (6) digit numerical code.
The Administrator configures the following parameters to restrict User access to the
controller systems
The following is an example of the Security menu options:
Exit Home Screen = Limits access to only the Home Screen.
Relay HOA = Allows access to the Relay HOA menu.
Configure Menu = Allows access to the Configure menu.
Settings Menu = Allows access to the Settings menu.
Timer Menu = Allows access to the Timers menu.

72-900-06 Rev. F
Page 20 of 38
Calibration = Allows access to "probe Cal".
Download = Allows the user to export the data files.
Upload = Allows the user to import program settings.
USB Settings = Allows the user to change the USB settings.
Factory Reset = Restricts access to the factory reset feature.
Once the password is set the controller will require a password to access any of the
menus. If the password is lost or unknown it will be necessary to call technical
service to gain access to the controller menus.
4.6.9 Software Version
From the Software Version screen view the current software that is running in the
MicroVisionEX controller.
4.6.10 Factory Reset Function
The Factory Reset Function will reset all of its internal parameters to the factory default
values.
Be absolutely certain you want to reset all the parameters back to the factory
defaults. Once the reset takes place there is no way to retrieve the previous
parameters.
4.7 Settings
The Settings menu is for setting the control parameters for conductivity, pH and ORP.
4.7.1 Conductivity
Set point Type - A Set point is a setting at which the controller activates an output,
such as a solenoid valve or a metering pump on the relay outputs or dry contact
outputs. The type –Rising or Falling defines which side of the set-point the relay
activates. A Rising type means that the output activates when the input goes above
the set point. A Rising set point is commonly used in conductivity control where you
want to keep conductivity below a certain value. A Falling type activates the output
when the value goes below the set point.
Set point –This is the conductivity point where a bleed function will begin.
Differential –The differential setting controls when the bleed function stops. This
value subtracted from the conductivity set point causes the bleed function to stop.
Example: Rising Set point=1200, Differential=100, the bleed function begins when
the conductivity reaches 1200 and ends when the conductivity reaches 1100.
Other manuals for MicroVision EX
1
Table of contents
Other Pulsafeeder Controllers manuals
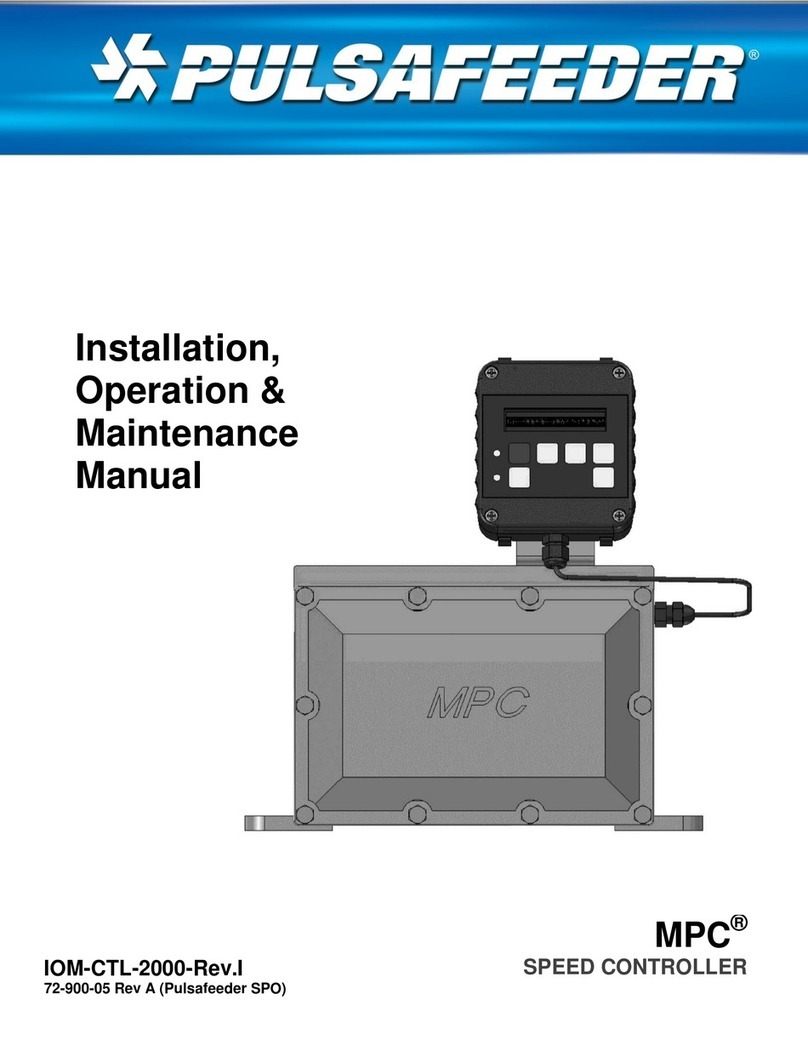
Pulsafeeder
Pulsafeeder MPC Instruction manual
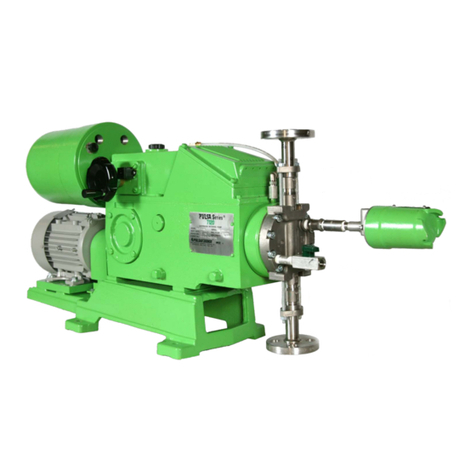
Pulsafeeder
Pulsafeeder PULSAmatic 7120 Manual
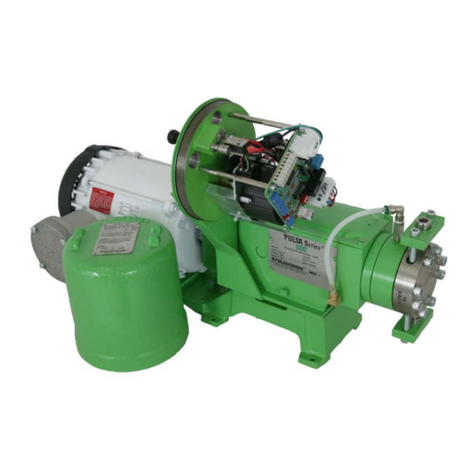
Pulsafeeder
Pulsafeeder ELMA NEMA 4X Instruction manual

Pulsafeeder
Pulsafeeder PULSAblue 3300 Series User manual

Pulsafeeder
Pulsafeeder ABC 50 Manual
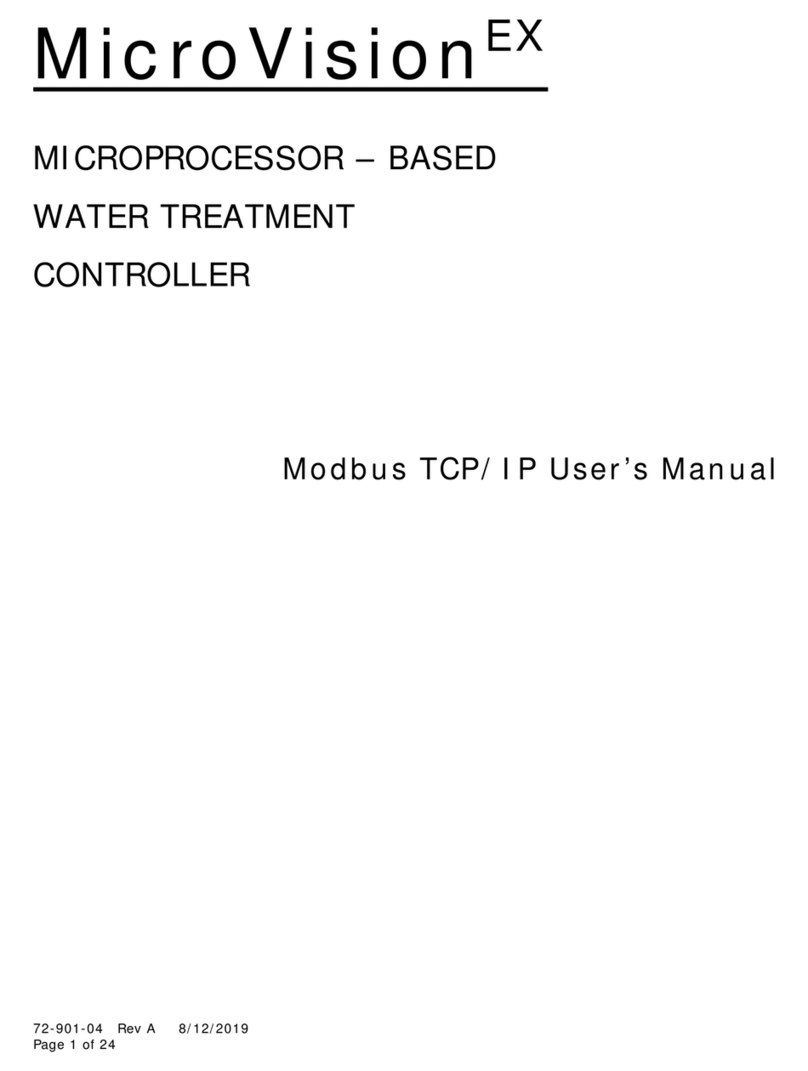
Pulsafeeder
Pulsafeeder MicroVision EX User manual
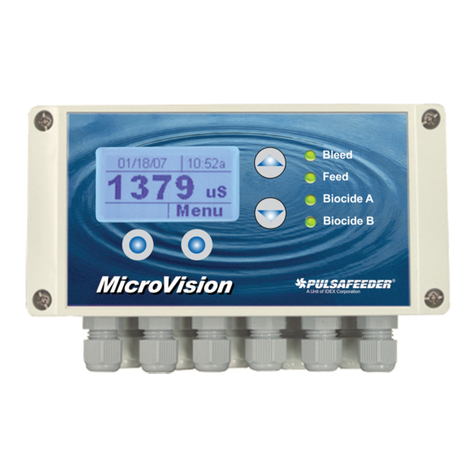
Pulsafeeder
Pulsafeeder MicroVision User manual