RCA BTF-5E1 User manual

www.SteamPoweredRadio.Com
2
LIST
OF
EQUIPMENT
E
S-560
6
43A
Qu
antity
Des
cri
ption
1 Power Determining
Kit
1
Blower:
0-7,
500
f
t.,
60
Hz,
or
0-3,000
ft
.,
60
Hz
3,000-6,500
ft
.,
50
Hz
or
7,500-11,
000
ft.
60
Hz
1 Rect
ifier
1 Plate Transformer
1 Power
Supply
1 Wire,
#2/0
AWG,
15
f
t.
1
Harmonic
Filter
87.5-108
MH
z. unpressurized
1 Namep
lat
e
1
Driver
Tube,
7203/4CX250B
1
PA
Tube,
4CX15,000A
,
Blower
Mounting
Kit
1 Frequency Determining Parts
2 tns-tr
uctlon
Book
, BTF-20E1
2 PowerConversion
Instruction
Addendum
•
Specify
fr
equency
DESCRIPTI
ON
PURPOSE
Referen
ce
Ml-560510A
Ml
-
560347-Al
Ml
-
560347
-3
Ml-560340-4
Ml-560341
-7
Ml-560342-6
Mt-560307-25
Ml-56
1
509
Ml-28180A
Ml
-
34726
Ml
-3
4725
Ml-560517
or
Ml
-
560705
ES-
560272C
'
IB-8027531-1
tB-8027981
RCA
Power
Conversion Kit,
ES
-
560643A,
prov
ides
for
conversion
of
the
RCA
BTF
-5E1 5
kW
FM
Transmitter
to
the
RCA BTF-20E1
20
kW
FM T
ransmitter
. Materials
supplied
are
identifi
ed
by
the
List
of
Equipment
in
this
Addendum
. Figure
numbers
are
referenced
to
illustrations
appearing
in
the
BTF-20E1 I
nstruction
Book,
IB
-
802753
1-1,
except
as
other
-
wise
noted.
Save shipping materi'als
for
use in
returning
to
RCA the
components
li
sted
bel
ow.
COMPONENTS
TO
BE
RETU
R
NED
TO
RC
A
Upo
n
modification
of
the
transmitter,
yo
ur
RCA
Representative
should
be r
equested
to
ob
tain
an
authorizat
i
on
(M
RA)
for
return
of
the
fo
llowing removed
components,
to
RCA M
eadow
Lands, Pa. This
is
important
since
the
price
of
the
conversion
kit
is
based
upon
receipt
of
these
items:
he
m
1
2
3
4
5
6
7
Quant
ity
1
1
1
1
Descrip
ti
on
Power Determining
Kit
Blower
Plate
Transformer
Harmo
n
ic
Fille
r
Blower
Mounting
Kit
Power
Supply
HV
Rectifier
Reference
Ml-560508
Ml-5
6
03
47-2
Ml
-34507
Ml
-
27967
-1
or
Ml
-279
67-2
Ml
-56
0518
Ml-560342-1
Mt-56034
0-1
TR
ANSMI
TT
ER
MODIFICA
TION
WARNI
NG
Always
disc
harge
and
gr
ound
circuits
prior
to
touching
them,
to
avoid personal injury
or
loss
of
life.
GE
NERAL
E
xperience
i
nd
i
cates
that
modification
of
the
transmitter
for this
power
increase
can
be
accomplished
by
three
men
working
three
nights
with
no
loss
of
air
time
for
stations
on
an
18-hour
operating
schedule. Following
is
a suggestec.
procedure.
FIRST
NIGHT
This
work
consists
of
replac
ing
the
5
kW
blower
with
the
20
kW
blower,
rewiring primary power,
if
necessary,
and
replacing
the
retlectometer
and
directional
coupler. Remove
5 kW
blower
after
removing air f
il
ters
and
manometer
panel
at
front
of
transmitter.
Then
proceed as follows:
1.
Bl
ower
In
sta
llati
on
. If
the
transmitter
is
to
be
operated
on
60
Hz
power
at
altitudes
above
7,500
feet
, the
larger blowel' (Ml-
560347
-
3)
is required. With
50
Hz power,
this
blower
is
required
above
3,000
feet. Blower
mounting
components
for
these
installations are supplied as
Ml-560705
,
which
al
so
includes
instructions
for
installing
the
blowe
r.
The
standard
bl
ower
model
Ml-5
60347
-A1
supplied
for
operation
below
7500
ft
,
(60
Hz)
and
3000
f
t.
(50
Hz) has
an
adjustable
vane. Before installing
this
blower, first
check
vane
setting
and
adjust,
if
necessary, as
shown
in Figure (a)
of
th
is
addendum.
IIOLOING SCREW !FAR
SIOE)
USE
l/8"
HE
X
AL
LEN
WRENCH
Figure (a). Bl
ow
er Va
ne
Se
tting
.

www.SteamPoweredRadio.Com
After
making adjustment, lock vane
in
place
with
Allen
lock
in
g screw, using 1
/8"
hex wrench.
The
vane should be
fully
open.
Install
M
I-560347
-A 1
blower
as
follows,
using
components
from
Kit
(Ml
-560517) and
with
reference
to
instal
lation
drawing figure (b)
of
this
addendum. Certain
Item
numbers
of
Ml-560517
are
identified
in
the
drawing.
..
Figure
(b
).
In
sta
llati
on
of Blower,
Mt
-5
60347-Al
.
a.
Using sixteen .
138"
(6)-32 x .
38"
long screws
(Item
SC)
and lockwashers
(Item
BG), install
four
shock
mounts
(Items 5 and
6)
on
top
of
blower
mounting
bracket
(Item
4).
The
20-pound shockmounts (I
tem
6)
should
be
assembled
to
the
mounting
holes
that
are
on
4-7/
8"
centers
and 1-3/
4"
from
the
right
angle bend in
the
bracket.
After
assembly, these shockmounts should
be
at
the
side
of
the
mounting
bracket nearest the
front
of
the
transmitter
cabinet.
b. Us
in
g
ten
.164"
(8)-32 screws
(Item
8A)
and ten
lockwashers (BF), attach
blower
exhaust cover assembly
(Item
1)
to
the
underside
of
the
blower
enclosure
top
cover.
c.
Mount
blower
air
boot
(
Item
2)
on
exhaust cover
assembly using
two
clamps (
It
em
3)
,
two
.164"
(8)-32 x .
50"
long screws
(Item
BB),
two
i/8 lockwashers
(Item
SF) and
two
#8 nuts (
It
em BN).
d.
As shown,
mount
blower
to
shockrnoun
ts,
using
the
.250"
(1/4)-20
hardware.
Orient
blower
so
that
outlet
scroll is adjacent
to
the
two
shockmounts
(Item
6).
e. Move assembled
blower
and
mounting
bracket
into
position
in
blower
enclosure,
positioning
blower
outlet
inside a
ir
boot.
Secure
blower
mounting
bracket
to
transmitter
base,
using
four
.3
12"
(5/
1
6)-18
x
.63"
long
bolts
(Item
BE)
and
four
.312"
(5/16) lockwashers
(Item
BJ).
f. Secure
air
boot
to
blower
using remaining clamps
(Item
3) and
#8
hardware (Items BB, BF and
8N).
g,
Replace
front
panel and
air
filters.
3
2. Primary Power Rewiring. Rewire
primary
power
source,
if
necessary,
to
handle
maximum
power
consumption
of
approximately
36,000
watts.
3. Reflectometer, Directional Coupler Replacement.
The
reflectometer, 1
Z5,
and
directional
coupler
, 1
Z7
(if
used),
must
be
replaced
with
their
high
power
counterparts
from
the
Power De
termining
K
it
.
To
remove 1Z5, open
left
hand back
door
and remove panel above plate resistors 1R25, 1R26 and
1R27
(figure ·14).
Be
careful
not
to
damage diodes when
removing 1
Z5
because diodes are loose
in
their
sockets when
the
DC
output
connectors are removed.
a. Install reflectometer, 1Z5,
iM
l
-560510A,
Item
8)
in
output
transmission line above
transmitter
rf
unit.
Use
transmission line coupling supp
li
ed
with
transmitter
rack. Each
transmission line coupling consists
of:
1
outer
sleeve
1
inner
conductor
connector
2 hose clamps
Install
two
de
output
connectors
PZ5-P1
and 1Z5-P2) at
the
mating
jacks
on
1
Z5.
Th
ese
connectors are connected
to
wires 241 and
245
(See
Figure 39). Check
that
a
diode
is
present
in
each ja
ck
on
125.
Secure
125
in
place using hose
clamp
(Item
20)
at
the
top
of
125
.
b.
The
special
miter
elbow
(Ml-560510A,
Item
17)
has
a
hole
provided
for
use
with
monitor
assembly (I
tem
19).
Position
monitor
assembly over
ho
le
in
side
of
elbow
so
that
rf
pickup
coil
enters
hole
without
toucning
the
sides.
Secure
in
p
la
ce
using
two
hose clamps
(Item
20).
NOTE:
Rf
pickup
coil may
be
positioned
for
best signal
pickup
by
removing
the
four
screws
which
hold
the coaxial
connector
in
p
la
ce, then
rotating
it
in
either
direction
for
maximum
pickup
(consistent
with
alignment
of
mounting
holes).
If
necessary,
pickup
co
il
may be altered
by
removing
or
adding turns
to
obtain
required signal.
c.
Mount
elbow,
with
monitor
assembly attached,
at
transmitter
output
using a transmission line coupling
(Item
18).
The
elbow
is
norma
l
ly
mounted
wi
th
the
long leg verticial
vertical.
d.
If
remote
contro
l is
not
planned, directional
coupler
127
may
be
omitted.
If
remo
te operation
is
to
be
used, install
directional
coupler,
127
(
Item
22)
at
open end
of
elbow,
using a transmission line coupling
at
each end
of
1Z7.
One transmission line coupling is used
for
connection
to
the
harmonic
filter.
For
additional i
nstruct
ions, refer
to
IB-B027531-1,
Page
16
e.
Using
the
shielded
wire
provided
(Item
23),
install
the
de
output
lead
from
127
to
1TB1
-1
i.
Ground
the
shield near
1T
B1, using
terminal
board
mounting
screw.

www.SteamPoweredRadio.Com
4
4. B
low
er
Rotat
io
n Check. Check
blower
for
proper
direction
of
rotation
to
pressurize
PA
and
driver
stag
es.
For
details on reversin~I bl
ower
ro
t
ation,
refer
to
IB-8027531-1,
Page
23
.
SECOND
NIGHT
5. Filament Transformer Repl
ace
ment. Replace
1T2
using the new
tra
nsformer supplied
(Ml-560510A,
Item
6).
Mount,
us
i
ng
hardware supplied
(Items
28B, 28C,
28K)
in
same
location
as
orig
inal
unit.
Refer
to
Wiring Diagram, figure
39, and
connect
ai;
previously
wired
on
pr
imary
side. Make
connections
from
secondary terminals
ot
1T2
to
PA
filament
feedthrough capaci
itors
1C
115
and 1C116, using
filament
connecting cables :;upplied (Items 9 and 10). Tighten
outer
nuts
on
lCl
15
and
1Cl
16
tightly
to
avoid
future
trouble
with
high
resistance contac
.t.
Do
not
tight
en
inner nuts on 1
C115
and
1C116
beyond finger
tight
,
or
the
ceramic insulator
may
be cracked.
The
PA
fi
l
ament
voltage should
be
set
to
approximately
6.3 volts before tl
he
PA
tube
is
installed.
Setting
of
the
filament
voltage
is
described
in
the BTF-20E1
instruction
book,
!-'ages
24
and 26.
6.
New
High
Vo
l
tage
Fi
lt
er. Install new
high
voltage
filter
capacitors, 1C7
ami
1C8
(Item
1), using
.375"-16
hardwa
re
supplied
(Item
16). Refer
to
figure
15
in
IB-802753
1-1. Install
new high voltage reactor 1
L3
(Item
3) at
location
shown
in
figu
re
15
in
IB
-802:7531·1. Position
as
shown
(in
figure 15),
Follow
wiring
diag1ram, figure 39, and
connect
high
voltage
leads
to
1L3.
Do
not
interchange high voltage wires
233
and
234.
7.
Filter
Capacitor Grounds. Refer
to
figure
39
and ins
tall
grounds
at
high voltage
filter
capacitors 1C7-2 and 1C8
-1
using
0
.128"
diameter
tinned
copper
wire
(Itern 12) and terminals
(Items 13 and 14)
as
required.
Also
connect a
jumper
using
the
0.
128"
bare
wire
between terminals 1C7-1 and 1C8-2.
Use
terminals required
(Ml-5605,0A
, Item 13).
8.
PA
Tube
arn
d 1C113 Removal. Remove PA tube
from
its
soc
k
et
and remove
plate
blocking
capacitor 1
C113
(See
figure 18).
9. 1
XV
10
3 S:
ocket
In
sta
ll
ation.
Remove
filler
plate
mounted
to
driver
stage shelf immediately
below
drive,· socket
1XV101. Retain
plate
mounting
hardware.
In
stall
1XV103
socket assemb
ly
(IVlI-56
0510A
, Item 15)
as
shown in figures
21
and
22
. U
se
the
4-
40
x
.38"
long screws and lockwashers
former
ly
used
to
hold
the
f
iller
plate in µlace.
In
sta
ll
s
up
pressor
network
1Z102
(
Item
24)
between
ce
nter
(contro
l
grid) terminal
of
1
><V
103
and
bottom
termina
l
(insulator
side)
of capaci
tor
1C102.
Connections
b1
~tween
1XV101
and 1
XV
103 are made
by
means
of
three
jump
er wires
which
are supplied connected
to
the 1
XV103
socket
assembly. Refer
to
Wiring
Diagram, fig
ur
e
39
and connect jumpers
as
follows:
Wire #57,
C134
to
C129
Wire
#58
,
C132
to
C139
Wire #59, C131
to
C128
Note
that
socket assembly
for
IXV103
(I
tem
15)
inc
ludes
a
clamp
assemb
ly
used
for
connection
to
the anode
of
driver
tube
IV
103
.
Refer
to
figure 22.
Mount
IV103
(7203/4CX250B)
in
socket
lXV103
and
mount
clamp
assembly loosely
on
anode
of
IV103
.
10
.
Plate
Strap
In
stallati
on
.
In
stall plate strap
(Ml
-
560510A,
Item
25) between
clamp
assembly and
to
the
junction
of
capacitor 1C111 and
in
ductor
IL
103.
11
.
PA
Tube Installation. Install new PA tube
(4CX
15000A)
observing procedures
outlined
in
the
instruction
book
. Then set new plate
blocking
capacitor 1C113
(Item
7)
down
over
top
of
PA
tube,
carefully
aligning 1C113
with
tube
and
socket
so
that
finger
stock
will
not
be damaged.
With
reference
to
note
below
and
to
figure 18, install and tighten
1Cl13
mounting
hardware (Items
28L
and 281) after orienting
1
Cl
13
as
required
to
connect
to
rf
choke 1
L07
NOTE:
The
12 10
-
32
x
.2
5"
long brass
screws are
to
be used
to
mount
1C
113
to
the
top
of
the spacer ring (Itern
157
in
figure
17);
while
on
the underside, the 10-32 x
.
75"
long plastic pan head screws are
to
mount
the
spacer ring
to
the
shelf
(Item
11
in
figure 17).
Do
not
use
metal screws
to
mount
the plastic
ring
to
the plastic
mounting
shelf. Install piastre screws at
10
·,
2-, 5· and 7-
o'clock
positions (the 6-o'cl
ock
metal screw bei
ng
nearest
front
of
cabinet).
Additional
screws cari
be
obtained
from
RCA
Parts and Accessories,
Deptford,
N.J.,
by
ordering
Stock
Number
249529.
12
. Meter 1
M4
Installation. Install meter bypass capacitor
1C10
(Item
2)
at
the
termina
ls
of
plate ammeter 1M4
(Item
4). M
ount
1M4
in
meter bezel
(Item
21) and install assembly
in
meter panel, replacing original
uriit.
Connect original
winng
at rear
of
1M4, referring
to
figure
39
for
wiring
information.
13. Frequency Determining Parts. Install frequency
determining
parts, replacing original parts and
following
procedure
in
transmitter
instruction
book
. In some
cases,
the
original
pa
rts are used.
14
.
Rectifier
Stack Removal. Remove and lay aside high
voltage
rectifier
stack (refer
to
figure
35
in
IB-8027529) and
screen voltage resistors 1R
15
and 1R16 (figure 16,
in
18·
8027531-1
).
The 6,300-ohm
res
istor
s,
1R
13
and 1R14
will
keep
the
screen e
ff
ect
ively
at
ground
for
the
next
few
steps.
15
.
Driver
and
PA
Tuning
. Power the
transmitter,
starting
the
plate
time
delay cycle. Place reflec
tom
eter
switch
1S3 ,n
th
e
DISABLE
position.

www.SteamPoweredRadio.Com
Press POWER LOWER
pushbutton
to
run
power
down
to
ze
ro
(when
plate
vo
ltage
is
turned
on).
Depress
PLATE
ON
pushbutton
and
hold
POWER
RAISE
pushbutton
depressed
un
til
driver
cathode
cu
rr
ent
increases
to
approximately
100
mA.
Adjust
DR
I
VER
PLATE
TUN
ING for
a
dip
in
driver
cathode
current.
Rotate
MULTIMETER
switch
1S2
to
th
e
PA
lg
position.
If
grid
curr
e
nt
is
low,
or
zero,
increase
dr
iver
output
by
pressing POWER
RAISE
pushbutton.
Do
not
exceed
400
mA
driver
cathode
current.
Obs
er
ve drive,
screen
current;
if
screen
current
exceeds
30
mA
and
PA
gr
id
current
is
low
(less
than
60
mA.)
it
will
be
necessary
to
reset
1nducto
1·s 1L111
and
1L
112
(See f
ig
ure
20
).
Note
that
in
some
transm
itters,
depending
upon
frequency,
the
induc
tor
s
may
not
be
used.
Adiust
inductors
1L111
and
1L
112
by
l
oosening
screws
and
sliding
inductors
as
required,
until
maximum
grid
current
1s
reached
with
minimum
screen
current
at
dip
of
cathode
current
in
lPA
.
Normal
driver
screen
current
shoulcl
be
5-15
mA.
(Typical
PA
grid
current
at
20
kW
power
o
utput
1s
abo
ut
80-110
mA.).
Retight
en screws.
1
6.
PA
Neutralization
.
Before
neutralizing
PA
sta
ge,
check
feedthrough
power
from
driver
stage, using
neutralization
setup
procedure
given in
transmitter
instruction
book.
If
with
normal
drive PA
feedthrough
power
is
over
one
watt,
it
will
be
necessary
to
neutralize
the
stage
as
described.
A
feedthrough
power
of
less
than
one
watt
should
be
possible.
17.
Connection
to
Dummy
Load
.
Shut
down
transmitte,,
Place
output
into
dummy
load.
Replace
screen
resistors
1R
15
and
1R
16
and
high
voltage
rectifier
stack.
Be
sure
that
shorting
bar
is clear,
Depress
POWER LOWER
pushbutton
1S12,
hold
ing
depressed
until
powerstat
1T5
is
at
zero
output
position.
18.
Tr
ans
mitt
er
Tun
eup.
Power
the
transmitter.
Apply
plate
voltage
and
start
to
raise
power.
With
approximately
1.5
amperes
plate
current,
peak
up
PA
gr
id
drive
by
tun
ing
DRIVER
PLATE
TUNING
and
PA
PLATE
TUNING
for
maximum
power
output.
Advance
power
output
to
previously
l
icensed
output
for
the
next
day's
operation.
Return
REFLECTOMETER
switch
1S3
to
the
NORMAL
positio
n.
WARNING
Never
leave
transmitter
in
DISABLE
position.
After
tr
ansmitter
is
tuned
and
up
to
power,
always
re
turn
1S3
to
NOR
MAL
operate
position.
THIRD
NIGHT
19
.
Harmonic
Filter
Replacement
(Ml-
561509).
Remove
original
harmon
ic
fi
l
ter
. Install
new
harmo
ni
c
filter
(a
horizontal
mounting
position
is
recommended).
The
filter
should
be
located
to
permit
a
reasonable
amount
of
ventilation.
Under
no
circums
t
ances
shou
ld
this
unpressuri
zed
5
filter
be
located
out
of
doors
where
"breathing"
of
the
un
it
,
due
to
temperature
changes.
may
lead
to
condensation.
The
alternate
pressurized
filter
(M
l
-56
1507
)
permits
filter
mounting
outdoors
01· i
ndoors
on
the
antenna
side
of
the
gas
stop.
When
installing
the
filter,
keep
in
mind
the
clearances
necessary for
the
various
size
transmission
line
inner
and
outer
conductors.
A
clearance
of
1/
8"
is
required
at
each
joint
for
all
miter
conductors
and
for
1-5/
8"
line i
nner
conductors.
Inner
conductors
of
3-1 /
8"
lines
require
a
clearance
of
3/
16"
at
each
joint.
Cl
eara
nces
required
by
other
line
sizes
should
be
determined
and
al
lowed
for. Be
sure
the
harmonic
filter
is
adequately
supported
from
the
ceiling
to
avoid excessive
strain
on
the
output
line.
Once
installed,
the
fil
ter
is
ready
for
operation
since
it
req
uires
no
tuning
or
adjustment.
20. Overload Relay
Sh
u
nt
Resistor. R
eplace
high
voltage
supp
ly
overload
rela
y
shunt
resistor
1R
24
with
new
resis
to
r
(Item
5).
Solde
r original leads
to
new
resistor. Refer
to
figure
39
lor
connections.
1R
24
is
located
on
transmitt
er
side panel
behind
variab
le
transformer
1T5
(See fi
gure
15).
21.
High
Voltage
Power
Supply
Removal.
Remov
e high
voltage
power
supply
by
disconnecting
the
three-phase
wiring
and
connections
to
plate
transformer.
Disconnect
and
label
high
voltage
lead
coming
from
transm
itter.
Disconnect
power
supply
grounding
strap.
Disconnect
and
label
control
circuit
leads
at
terminal
board
2TB
1
in
high
voltage
power
supply.
Eac:1
of
these
leads will
go
to
an
identically
numbered
terminal
in
the
new
pow
er
su
pply
cabinet.
Pull
out
all leads
and
lift
power
supp
ly case
clear
of
plate
transformer.
22.
Plate
Tran
s
former
Replacem
en
t.
Remove
original
plate
transformer.
Pl
ace
new
high
voltage
plate
transformer
3T1
in
posit
i
on
and
fasten
it
to
the
floor
. T
he
power
supply
cabinet
is
then
moved
into
position
over
the
transformer.
This
is
done
by
removing
the
lower
front
access panel
and
sliding
the
cabinet
into
place
over
the
transfo
rmer.
Be
sure
cabinet
is
centered
over
transform
er.
Then
fasten
cabinet
securely
to
the
fl
oor.
A safe clearance
of
at
least 2
½"
must
be
provided
between closest
point
of
plate transformer and power supply
ca
binet.
23
. Equipment Grounding. Care
should
be
tak
en
to
provide
an
adequate
ground
system
for
the
transmitter.
Before
power
is
applied
to
the
equipment,
the
following
ground
co
nnections
must
be
completed:
a.
Connect
power
supply
cabinet
to
main
transmitter
cabinet
using 1-1/
2"
wide
copper
strap.
This
connec
t
ion
should
be
made
from
one
of
the
copper-flashed
angle
brackets
welded
inside
the
power
supp
ly
cabinet
below
the
rectifier
mo
u
nt
ing shelf,
to
one
of
the
copper-flashed
side
channels
in
the
main
transmitter
rack.
b.
Connect
the
main
transmitter
cabinet
to
the
sta
t
ion
gr
ound
using 1-1/
2"
wide
copper
strap.
It
is
also
advisab
le '
to
connect
the
power
supp
ly
cabinet
to
the
station

www.SteamPoweredRadio.Com
6
ground using an equivalent
conductor.
If
intact,
the
copper
strap
originally supplied
should
be
satisfactory.
24.
Checking Grounds.
After
connections
have been
comp
l
eted
check
each
ground
for mechanical
strength
and
continuity.
All soldered joints
shou
ld
be
tested
for mechanical
strengt
h as well as
continuity.
25. Installation of Power Supply Components. It will be
necessary
to
install
and
wire in new
plate
contactor
2K1
and
circuit breaker
2S
1:
a.
Install
plate
contactor
2K1 (Ml-560510A,
Item
26)
on
contac
t
or
mounting
plate
in
power
supply,
Ml
-560342-6. This
plate
is
behind
the
iower
supply
front
panel
and
has
mounting
holes labeled
"A-8''
or
"W"
for
either
an Allen-Bradley
or
Westinghouse
contactor.
Use
mounting
hardware supplied (Items
28G,
28H, 281,
28J).
b. Install circuit
breaker
2S1
(Item
27)
adjacent
to
2K1 in power
supply
Ml-560342-6, using
two
.250"-20
x
5"
long screws (Item 28A), flat washers (I
tem
288),
lockwashers
(Item
28C)
and
hex
nuts
(Item
280)
in
the
lower
two
2S1
mounting
holes.
At
the
two
upper
mounting
holes for 2S1
in
stall spacer plate
(Item
29)
between
2S1
and
the
power
supply
cabinet
using
two
.250"-20
x
4"
long screws
(Item
28E)
and
special
nuts
(Item
28F).
Avoid overtightening 2S1
mounting
hardware
to
prevent
damage
to
the
plastic
breaker
housing. Install pressure
type
terminals supplied
(Item
30)
at
the
three
top
terminals
of
2S1. These are used
to
connect
to·
the
three-phase
power
source.
c. Using
the
size
2/0
power
cable
supplied
(Item
11). install
jumper
wires
from
the
bottom
term
inals
of
2S1
to
the
top
terminals
of
2K1. R
efer
to
the
transmitter
schematic
diagram, figure
38
for connections. Strip insulation from each
end
of
the
three jumpers
to
fit
the
pressure
type
connectors
on
2S1
and
2K1.
26.
High Voltage Rectifier Installation.
Mount
high
voltage rectifier assembly
(M
1-560340-4) in new
power
supply
cabinet. Place in position
on
ceramic insulators supplied as
part
of
power
supply. If necessary, move
two
of
the
insulators
to
the
position
marked
"M1-
560340-4"
on
the
power
supply
chassis. Secure
the
rectifier assembly in place, using
the
.190"
(10)-
32
hardware
supp
lied in place
at
the
tops
of
the
insulators.
Check high voltage grounding switch
2S4
for
free
operation. With
power
supply
cover
raised, use an
phmmeter
to
assure
that
2S4
grounds
the
high voltage positive terminal.
27.
Equipment
Connections.
a. Make necessary
connections
between
transmitter
cabinet
and
power
supply
cabinet,
referring
to
figures
38,
39
of
the
inst
ructio
n
book
and
Table 1
of
this
addendum.
Use
original, label
ed
wires
for
th
ese connections.
TABLE
1.
TRANSM
I
TTER
/POWER SUPPLY
INTERCONNECTIONS
F,om
Power Su
ppl
y
To
Tran
smitter
Terminal Terminal
2TB1-1 1TB1·1
2TB1-2
1TB
1-2
2TB1-3
1TB1-3
2TB
1
-4
1TB1
-4
2TB1-5 1TB1·5
2TB
1-6 1TB1-6
2TB1·7
1TB1·7
2TB1-8
1TB
1-8
2TB1-9 1
TB1-9
b. Using original wiring,
connect
high voltage
de
output
(at
high voltage rectifier assembly
connector
designated
HV+ in
power
supp
ly cabinet)
to
1TB1-101.
This
is
the
high
voltage
termina
l in the
upper
right
hand
corner
of
the
transmitter
cabinet
(v
iewed
from
the
rear).
c. In
power
supply cabinet,
connect
contactor
2K1
to
the
primary
of
transformer
3T1 using high
current
wire,
#2/G AWG
(Item
M
l-
560307-25).
d.
Also in
power
supply
cabinet,
connect
secondary
of
transformer
3T1
to
the
high voltage rectifier assembly
at
the
AC1,
AC2
and
AC3
terminals using high vo
lt
age wire
origina
ll
y supplied with
transmitter.
e. Remove protective
safety
shield from cir
cuit
hreaker
2S1 in
power
supply
cabinet,
and
connect
3-phase
power
source
of
proper
voltage
to
terminals 1, 2
and
3.
Replace protective
safety
shield.
Do
not
apply power
at
this
time.
f.
Check
all
connections
for
accuracy,
continuity
and
mechanical strength.
28,
low
Voltage Circuit Breaker Adjustment. Circuit
breaker
1
S6
gives fast acting
protection
against
short
circuit
conditions in low voltage
power
supply
circuitry.
To
prevent
spurious tripping,
dismount
1S6
and
adjust
trip
sett
ing
on
each
po
le
to
i
ts
highest value.
Remount
1S6.
29. Overload Relay Adjustment. It will
be
necessary
to
adjust
overload relays 1K1, 1K2
and·
1K4 (on
control
panel
behind
left
hand
cabinet
do
.
or)
to
carry
the
increased currents
caused
by
higher
power
operation.
This
is
accomplished
by
use
of
an
ammeter
of
the
proper
range in series with a 6-ampere
de
supply
wbich is adjustable
from
0.5
to
1
.5
volts. A
convenient
supply
is an
"A"
battery
such
-as
the
RCA VS006C in series wfth a
rheostat
of
from 5
to
10
ohms
maximum
resistance. When adjusting 1K2, use a
series rheost
at
of
approximately
one
ohm.
Remove relay
cover,
and
with
rheostat
set
for
maximum
resistance,
co
n
nect
supply
and
series
ammeter
across relay coil. Slowly decrease

www.SteamPoweredRadio.Com
resistance
to
o
bt
ain
current
reading given
in
Table
2.
Adjust
spring
tension
on
relay
so
that
it
pulls in
at
the
specified
current.
After
adjustment,
increase and d
ecrease
current
several times
to
check
operation.
Replace
rel
ay
covers.
TABLE
2. OV
ERLOAD
RELAY
SETTINGS
Relay Circu
it
Pull-in Current
1
K1
LV
Rectifier
1
.5
A
1K2
PA
Plate
Current
5.0A
1K4
Drfver
Cathode
Current
0.6A
30. Blower
Over
lo
ad
Relay (1K15) Adjustment. T he
overload
portion
of
1K
15
is
normally
tested
and
shipped
set
for
manual
reset
operation
only
.
This
is
done
to
avoid
accidents
which
could
possibly
occur
if
the
relay
should
operate
(shutting
down
the
transmitter)
,
and
then
automatically
recycle, energizing
transmitter
ci
rcuitry
while
operating
personne
l
are
investigating
the
cause
of
interruption
.
However,
the
relay
can
be
adjusted
for
automatic
reset
by
turning
the
small
screw
(next
to
the
manual
reset
button)
to
the
extreme
clockwise
posit
i
on
.
The
automatic
reset
option
may be desired in
remotely
controlled
stations
.
If
it
should
be
necessary
to
change
the
trip
setting
of
1K15,
use this
procedure
:
a. Remove snap-on
cover
from
overhead
rel
ay
part
of
1K15assembly.
b.
Adjust
variable
trip
setting
dial
to
desired
va
lu
e.
A
setting
of
6.5
amperes
is
recommended
in
BTF
-20E1
transmitters
using
the
M1-560347-A1
blower.
A
different
type
overload relay
is
used
with
the
Ml-560347
-3 high-altitude
blower. This relay,
part
of
Ml-560705,
should
be
set
at
8.5
amperes.
c. Replace
snap
-
on
cover
.
31.
Transformer Primary Check.
Ensure
that
the
primary
taps in use
on
plate
transformer
3T1
and
PA fi
lament
transformer
1T
2
are
compatible
with
the
line voltage source.
See
Table
3 in the
instruction
book.
7
32. Transmitter Tuning.
Power
the
tran
smitter.
Depress
POWER LOWER
pushbutton
to
reduce
power
output
consid
era
bly
from
last
operati
ng value.
Apply
plate voltage.
Tune
transmitter
and
adjust
power
as
described
in
BTF-20E
1
instruction
book,
IB-8027531
-1
.
33.
PA Saturation. If
problems
are
experienced
wi
th
AM
noise,
the
PA
stage
may
not
be
receiving
enough
dr
i
ve
to
saturate.
The
grid
current
of
this stage
shou
ld be
80
mils
or
more
and
could
be
as high as
250
mils
with
some
tubes.
Drive
may
be
increased by
setting
control
1R38
(figure 12)
to
raise
the
voltage
on
the
driver
screen. Also, PA plate
and
output
load
tuning
(figure
12)
should
be
touched
up
.
Saturation
and
limiting in
the
PA
can
be
detected
by
pushing
the
raise
power
but
to
n.
An
i
ncr
ease
in
final
plate
current
with
no
increase in
power
output
indicate
s t
hat
the PA
stage
is saturat
ed.
Wi
th
th
is
condit
io
n,
the
AM
noise level
should
be
normal.
34.
Nameplate C
hange.
Replace
BTF-5E1
transmitter
namep
l
ate
with
new
BTF-20E
1
nameplate,
M1-281
S0A.
EQUIPMENT
LOST
OR
DAMAGED
IN
TRANSIT
Unpack
and
thoroughly
insp
e
ct
equipment
upon
receipt.
If shortages
or
damag
ed
parts
are
found,
immediately
not
ify
RCA
and
the
carrier, and
secure
an
inspect
i
on
report
from
the
carrier.
Notification
of
equipment
loss
or
damage
must
be
made
in
writing
to
RCA,
Communications
Systems
Division,
Camden
,
New
Jers
ey
08102
WITHIN
15
DAYS
after
receipt
of
material.
WARRANTY
ITEMS
Parts
or
equipments
covered
by
warranty
may
be
replaced
by
contacting
the
local RCA Sales
Offic
e. Avoid delays
by
supplying
complete
i
nformation
such
as
Original Invoice
Number,
Ml-Number,
Type
Number, Model
Numb
er,
Ser
i
al
Number,
Stock
Number
and Description.
REPLACEMENT
PARTS
Rep
l
acement
parts
bearing a Stock Number
should
be
ordered
by
Item
Description
and
stock
Number
from
RCA
Parts
and
Accessories,
Deptford,
New
Jersey
08096
. Parts
listed
under
a Master Item (Ml-) Number
should
be
ordered
from
RCA,
Communications
Systems
Division,
Camden,
New
Jersey
08102.
Parts bearing
no
number
are
not
stocked.
This manual suits for next models
1
Table of contents
Other RCA Transmitter manuals
Popular Transmitter manuals by other brands
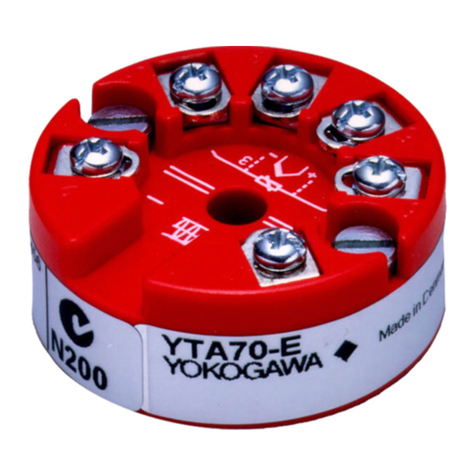
YOKOGAWA
YOKOGAWA vigilantplant YTA70 user manual
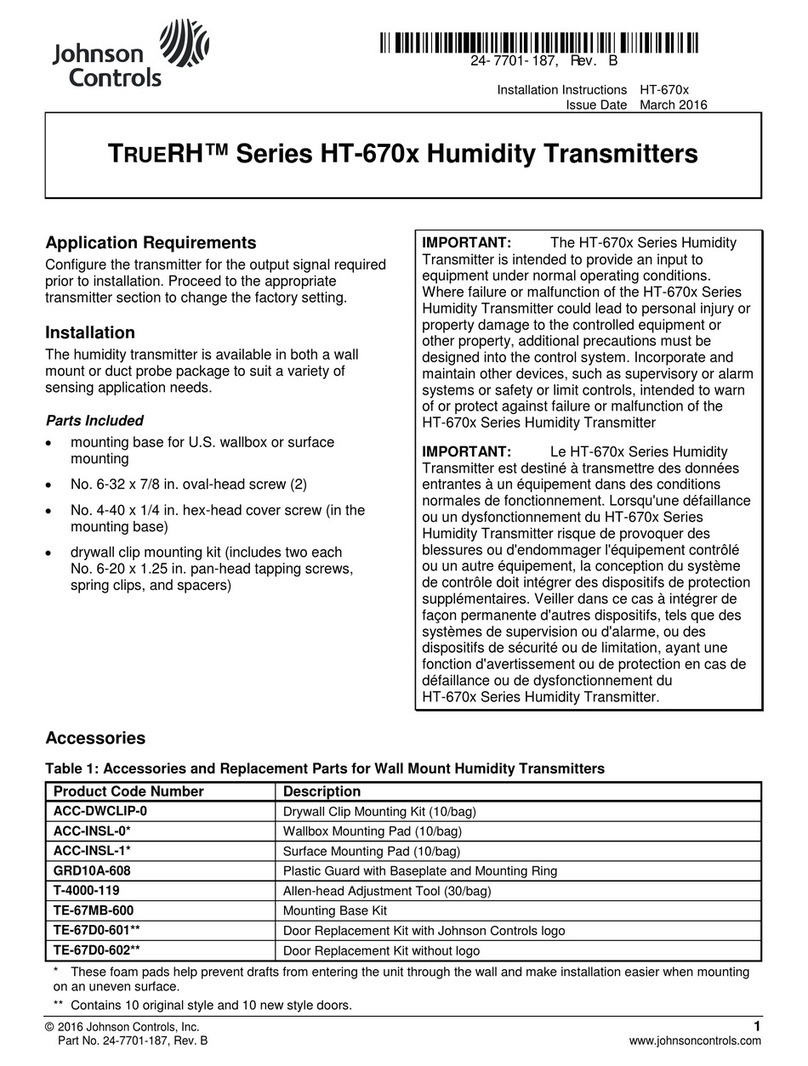
Johnson Controls
Johnson Controls TrueRH Series installation instructions
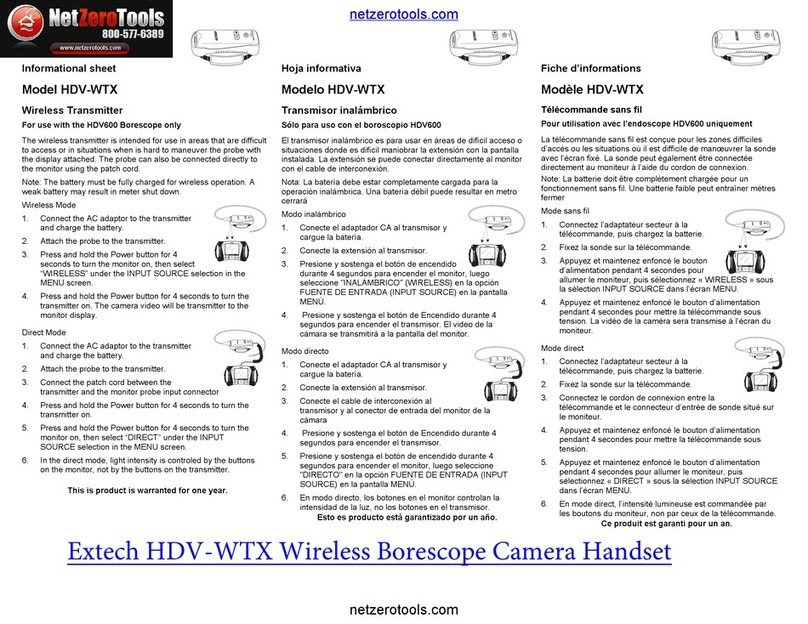
Extech Instruments
Extech Instruments HDV-WTX Informational sheet

Artel
Artel INFINITYLINK ILC103A manual
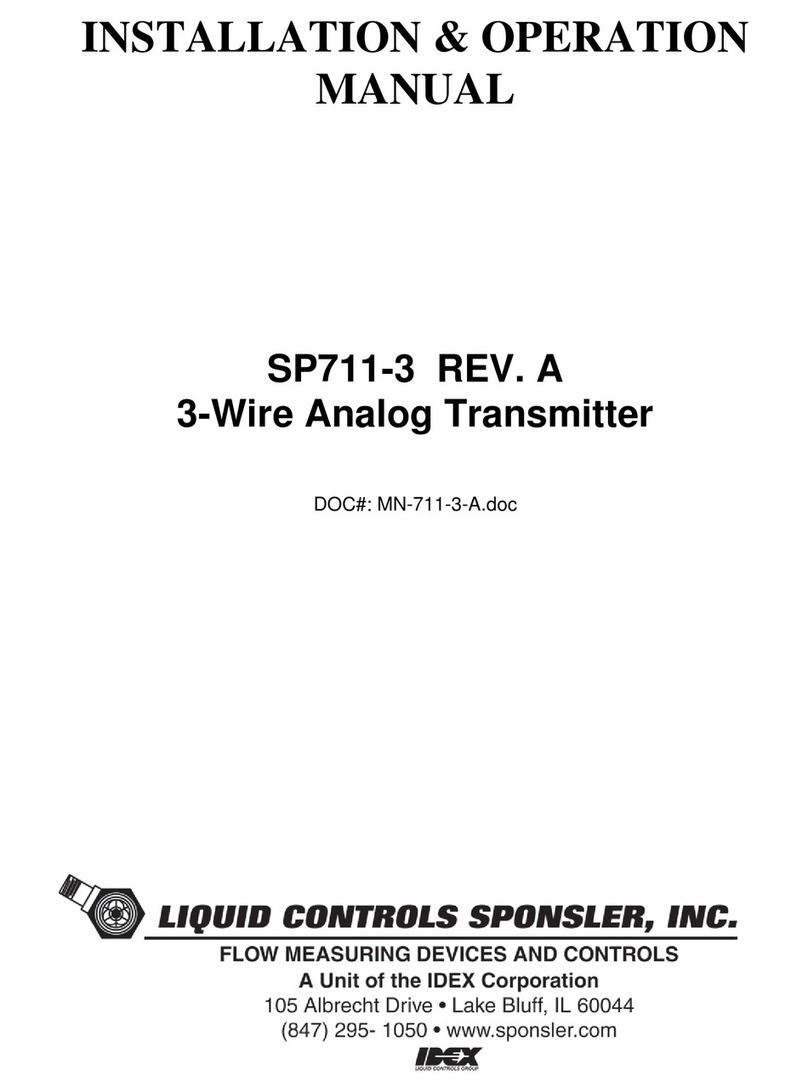
Liquid Controls
Liquid Controls SP711-3 Installation & operation manual
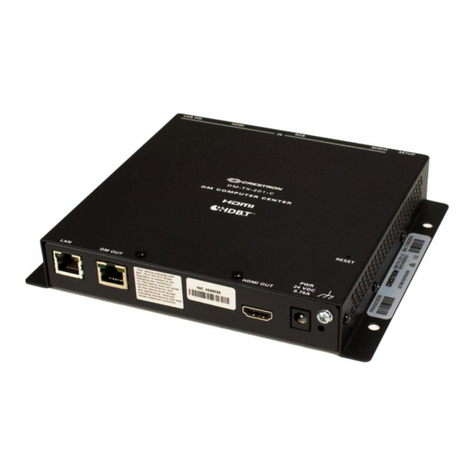
Crestron
Crestron DM-TX-201-C quick start