REMKO Smart Com User manual

Instructions for use
SD
Read the instructions prior to performing any task!
REMKO Smart Com
Activation of Smart Com for Smart Control Touch regulation
0239-2019-12 Edition 2, en_GB
to integrate the heat pump into a Smart Home system

Translation of the original instructions for use
Read these operating instructions carefully before commis-
sioning / using this device!
These instructions are an integral part of the system and must
always be kept near or on the device.
Subject to modifications; No liability accepted for errors or mis-
prints!

Table of contents
1 Safety and usage instructions............................................................................................................. 4
1.1 General safety notes....................................................................................................................... 4
1.2 Identification of notes...................................................................................................................... 4
1.3 Personnel qualifications.................................................................................................................. 4
1.4 Safety-conscious working............................................................................................................... 4
1.5 Safety notes for the operator........................................................................................................... 4
1.6 Safety notes for installation, maintenance and inspection.............................................................. 5
1.7 Dangers of failure to observe the safety notes................................................................................ 5
1.8 Unauthorised modification and changes......................................................................................... 5
1.9 Intended use................................................................................................................................... 5
1.10 Warranty........................................................................................................................................ 5
1.11 Transport and packaging............................................................................................................... 6
1.12 Environmental protection and recycling........................................................................................ 6
2 System requirements............................................................................................................................ 6
3Electrical wiring..................................................................................................................................... 7
4 Installing the Smart Com software.................................................................................................... 12
5 Checking that the Smart Com is enabled......................................................................................... 13
6 Configuring the Smart Com function ............................................................................................... 13
7 Data points........................................................................................................................................... 18
8 Application example........................................................................................................................... 26
9 Software update.................................................................................................................................. 28
10 Index..................................................................................................................................................... 30
3

1 Safety and
usage instructions
1.1 General safety notes
Carefully read the operating manual before com-
missioning the units for the first time. It contains
useful tips and notes such as hazard warnings to
prevent personal injury and material damage.
Failure to follow the directions in this manual not
only presents a danger to people, the environment
and the system itself, but will void any claims for
liability.
Keep this operating manual and the refrigerant
data sheet near to the units.
1.2 Identification of notes
This section provides an overview of all important
safety aspects for proper protection of people and
safe and fault-free operation.The instructions and
safety notes contained within this manual must be
observed in order to prevent accidents, personal
injury and material damage.
Notes attached directly to the units must be
observed in their entirety and be kept in a fully
legible condition.
Safety notes in this manual are indicated by sym-
bols. Safety notes are introduced with signal words
which help to highlight the magnitude of the danger
in question.
DANGER!
Contact with live parts poses an immediate
danger of death due to electric shock. Damage
to the insulation or individual components may
pose a danger of death.
DANGER!
This combination of symbol and signal word
warns of a situation in which there is immediate
danger, which if not avoided may be fatal or
cause serious injury.
WARNING!
This combination of symbol and signal word
warns of a potentially hazardous situation,
which if not avoided may be fatal or cause
serious injury.
CAUTION!
This combination of symbol and signal word
warns of a potentially hazardous situation,
which if not avoided may cause injury or mate-
rial and environmental damage.
NOTICE!
This combination of symbol and signal word
warns of a potentially hazardous situation,
which if not avoided may cause material and
environmental damage.
This symbol highlights useful tips and recom-
mendations as well as information for efficient
and fault-free operation.
1.3 Personnel qualifications
Personnel responsible for commissioning, opera-
tion, maintenance, inspection and installation must
be able to demonstrate that they hold a qualifica-
tion which proves their ability to undertake the
work.
1.4 Safety-conscious working
The safety notes contained in this manual, the
existing national regulations concerning accident
prevention as well as any internal company
working, operating and safety regulations must be
observed.
1.5 Safety notes for the operator
The operational safety of the units and compo-
nents is only assured providing they are used as
intended and in a fully assembled state.
nThe units and components may only be set up,
installed and maintained by qualified per-
sonnel.
nProtective covers (grille) over moving parts
must not be removed from units that are in
operation.
nDo not operate units or components with
obvious defects or signs of damage.
nContact with certain unit parts or components
may lead to burns or injury.
nThe units and components must not be
exposed to any mechanical load, extreme
levels of humidity or extreme temperature.
REMKO Smart Com
4

nSpaces in which refrigerant can leak sufficient
to load and vent. Otherwise there is danger of
suffocation.
nAll housing parts and device openings, e.g. air
inlets and outlets, must be free from foreign
objects, fluids or gases.
nThe units must be inspected by a service tech-
nician at least once annually. Visual inspec-
tions and cleaning may be performed by the
operator when the units are disconnected from
the mains.
1.6 Safety notes for installation,
maintenance and inspection
nAppropriate hazard prevention measures must
be taken to prevent risks to people when per-
forming installation, repair, maintenance or
cleaning work on the units.
nThe setup, connection and operation of the
units and its components must be undertaken
in accordance with the usage and operating
conditions stipulated in this manual and comply
with all applicable regional regulations.
nLocal regulations and laws such as Water
Ecology Act must be observed.
nThe power supply should be adapted to the
requirements of the units.
nUnits may only be mounted at the points pro-
vided for this purpose at the factory. The units
may only be secured or mounted on stable
structures, walls or floors.
nMobile units must be set up securely on suit-
able surfaces and in an upright position. Sta-
tionary units must be permanently installed for
operation.
nThe units and components should not be oper-
ated in areas where there is a heightened risk
of damage. Observe the minimum clearances.
nThe units and components must be kept at an
adequate distance from flammable, explosive,
combustible, abrasive and dirty areas or
atmospheres.
nSafety devices must not be altered or
bypassed.
1.7 Dangers of failure to observe
the safety notes
Failure to observe the safety notes may pose a risk
to people, the environment and the units. Failure to
observe the safety notes may void any claims for
damages.
In particular, failure to observe the safety notes
may pose the following risks:
nThe failure of important unit functions.
nThe failure of prescribed methods of mainte-
nance and repair.
nDanger to people on account of electrical and
mechanical effects.
1.8 Unauthorised modification
and changes
Modifications or changes to units and components
are not permitted and may cause malfunctions.
Safety devices may not be modified or bypassed.
Original replacement parts and accessories
authorised by the manufactured ensure safety. The
use of other parts may invalidate liability for
resulting consequences.
1.9 Intended use
The Smart Com function is to connect the Remko
Smart Control controller to a factory fitted interface.
Any different or additional use is a non-intended
use. The manufacturer/supplier assumes no lia-
bility for damages arising from non-intended use.
The user bears the sole risk in such cases.
Intended use also includes working in accordance
with the operating and installation instructions and
complying with the maintenance requirements.
The threshold values specified in the technical
data must not be exceeded.
1.10 Warranty
For warranty claims to be considered, it is essential
that the ordering party or its representative com-
plete and return the "certificate of warranty" to
REMKO GmbH & Co. KG at the time when the
units are purchased and commissioned.
The warranty conditions are detailed in the "Gen-
eral business and delivery conditions". Further-
more, only the parties to a contract can conclude
special agreements beyond these conditions. In
this case, contact your contractual partner in the
first instance.
5

1.11 Transport and packaging
The devices are supplied in a sturdy shipping con-
tainer. Please check the equipment immediately
upon delivery and note any damage or missing
parts on the delivery and inform the shipper and
your contractual partner. For later complaints can
not be guaranteed.
WARNING!
Plastic films and bags etc. are dangerous
toys for children!
Why:
- Leave packaging material are not around.
- Packaging material may not be accessible to
children!
1.12 Environmental protection
and recycling
Disposal of packaging
All products are packed for transport in environ-
mentally friendly materials. Make a valuable contri-
bution to reducing waste and sustaining raw mate-
rials. Only dispose of packaging at approved
collection points.
Disposal of equipment and components
Only recyclable materials are used in the manufac-
ture of the devices and components. Help protect
the environment by ensuring that the devices or
components (for example batteries) are not dis-
posed in household waste, but only in accordance
with local regulations and in an environmentally
safe manner, e.g. using certified firms and recy-
cling specialists or at collection points.
2 System requirements
Note the following!
Programming can only be carried out via a KNX
system integrator.
Programming cannot be carried out by REMKO
Service.
Prerequisite for using the Smart Com function:
1. Products with REMKO Smart Control con-
troller as of software level 4.24. Check the
software in the software version number
information & software control panel level.
Both versions must have level 4.24.
2. The integrated Gira 216800 interface can be
connected directly to the KNX bus.
The heat pump can also be commissioned
without integrating the KNX-BUS. For this pur-
pose, leave the plug connections of the network
cables in the delivery state: Touch display and
I/O module are connected to each other, the
network cable on the KNX module (plugged into
the I/O module connection) remains uncon-
nected.
In the LWM series heat pumps and the SQW
modular energy centres, the interface is not
installed at the factory. In this instance, it is
enclosed as a separate item. For these series,
the installation must then take place in a suit-
able position provided by the customer (e.g.
main control box of the house or separate sub-
distribution).
REMKO Smart Com
6

3 Electrical wiring
The connection cables for the power supply and
the connection to the KNX-BUS must be provided
by the customer.
The connection to KNX/EIB is established via a
bus connection terminal.
An IP interface requires additional operating
voltage for operation. Also refer to the manufactur-
er's documentation for this.
Only carry out the work described below when
the KNX module is supplied with voltage! If you
carry out the work described below without the
KNX module being supplied with power, the
heat pump cannot be commissioned.
Connect the terminals [3 & 4] of the already
installed KNX module with the on-site power
supply and the KNX-BUS. Now remove the RJ45
plug from the I/O module and plug it into the free
interface on the KNX module (labelled Touch Dis-
play [1]). Now take the free end of the network
cable attached to the interface [2] labelled I/O
module and plug it into the freed up socket in the
I/O module. (see Fig. 2 or Fig. 3)
21
4
3
Fig. 1: Terminal assignment on the IP interface
1: Touch display
2: I/O module
3: KNX-BUS
4: 24V DC
7

2
1
4
3
Fig. 2: HTS/WSP wiring diagram
1: Touch display
2: I/O module
3: KNX-BUS
4: 24V DC
2
1
4
3
Fig. 3: WKF wiring diagram
1: Touch display
2: I/O module
3: KNX-BUS
4: 24V DC
REMKO Smart Com
8

WKF/HTS/WSP IP interface functional diagram
L N
A
B
C
D
E
F
2
1
4
3
5
6 6
5
a
b
Fig. 4: Functional diagram for an IP interface
a WKF/HTS/WSP indoor unit
b: parts to be provided by the customer
A: KNX power supply (provided by the customer)
B: KNXnet/IP interface (2 x RJ45, factory fitted)
IP: 10.210.210.* (DHCP)
C: Ethernet router (building network, optional)
D: REMKO SMT controller (heat pump)
IP: 10.210.210.2 (fixed)
E: Touch display (heat pump)
IP: 10.210.210.1 (fixed)
F: USB/Ethernet adapter (optional)
1: Mains voltage (230V)
2: Auxiliary voltage (24V DC)
3: Bus voltage (29V throttled)
4: KNX-BUS
5: min. CAT 5 e
6: Twisted Pair
9

LWM/SQW IP interface functional diagram
L N
A
B
C
D
E
F
2
1
4
3
5
6 6
5
a
b
Fig. 5: Functional diagram for an IP interface
a LWM/SQW indoor unit
b: (Main) distribution provided by the customer
A: KNX power supply (provided by the customer)
B: KNXnet/IP interface (2 x RJ45, factory fitted)
IP: 10.210.210.* (DHCP)
C: Ethernet router (building network, optional)
D: REMKO SMT controller (heat pump)
IP: 10.210.210.2 (fixed)
E: Touch display (heat pump)
IP: 10.210.210.1 (fixed)
F: USB/Ethernet adapter (optional)
1: Mains voltage (230V)
2: Auxiliary voltage (24V DC)
3: Bus voltage (29V throttled)
4: KNX-BUS
5: min. CAT 5 e
6: Twisted Pair
REMKO Smart Com
10

Features of an IP interface
A KNXnet/IP interface has the following features:
nSimple connection to higher-level systems
thanks to the use of the internet protocol (IP)
nDirect access from any point in the IP network
to the KNX/EIB installation (KNXnet/IP tunnel-
ling)
nCross-building and cross-property communica-
tion (networking properties)
nLED displays (manufacturer-independent) for
operational readiness of KNX/EIB communica-
tion to IP communication
nEasy connection to the REMKO SMT controller
nETS (ETS = Engineering Tool Software) can be
connected easily
KNXnet/IP tunnelling interface to the bus
A direct connection from the REMKO Smart Con-
trol controller to the bus is established via a data
network and the IP interface. This enables access
to the KNX group addresses.
The IP interface must use a unique physical
address for each KNXnet/IP tunneling connec-
tion to ensure stable communication via
KNXnet/IP tunneling. These additional physical
addresses must not be identical to the unit's
physical address and are also not permitted to
be used by any other bus device. These phys-
ical addresses should therefore be assigned to
dummy units in the ETS.
Assigning additional physical address(es) (IP
interface)
Additional physical addresses are either assigned
using the ETS, via an automatic assignment func-
tion or by some manufacturers. For information on
the automatic address assignment procedure for
KNXnet/IP tunnelling, see the manufacturer's doc-
umentation. The unit checks which physical
addresses are already being used by other bus
units that are connected to the bus line. These
addresses are not used when assigning the
addresses.
NOTICE!
If additional bus devices are added at a later
time, one or several of the physical addresses
could be assigned more than once.
Assigning the IP address
If you have any questions on setting the IP
address parameter for the unit and the subnet
mask, as well as on DHCP
, contact the local net-
work administrator.
"In order to guarantee a stable connection
between the KNX interface and the SMT con-
troller, the network router that is used must be
configured so that a static IP address is
assigned to each of the units (or their MAC
addresses) when DHCP is used. Alternatively,
the SMT controller and the KNX interface can
be set to a fixed IP address by deactivating the
DHCP function. "
IP interface
The IP address for the IP interface is assigned via
ETS configuration or automatically by a DHCP
service in the IP network. Assigning and address
via a DHCP service enables changes to the IP
address without configuring the unit using the ETS.
The unit's MAC address that is applied to the unit
may also be required to configure the DHCP
service.
REMKO Smart-Control Touch
The IP address for the REMKO SMT controller is
assigned statically via the controller configuration,
automatically by a DHCP service in the IP network
or by the unit itself (AutoIP). Assigning and
address via a DHCP service enables changes to
the IP address without configuring the unit. The
unit's MAC address that is displayed in the "Basic
information/service" information menu may be
required to configure the DHCP service. If a DHCP
service is not available, the unit searches for its
own IP address (AutoIP). The controller and the IP
interface can therefore communicate directly using
a crossover cable, for example.
11

Function as delivered
As delivered, the following parameters are set
depending on the manufacturer:
nPhysical address of the IP interface: 15.15.255
(= FFFF hex)
nIP address assignment via DHCP
IP interfaces can be set to the factory settings.
This procedure deletes parameter settings.
For information on the procedure, see the man-
ufacturer's interface documentation.
4 Installing the
Smart Com software
The Smart Com function provides you with the
option of controlling your REMKO heat pump via a
KNX/EIB system.
The following pages describe installing the Smart
Com function on the REMKO Smart Control con-
troller.
NOTICE!
Before removing and inserting the SD card, the
system must be powered down!
1. After you have powered down the system,
remove the SD card from the I/O module.
Fig. 6: Removing the SD card
2. Insert the SD card for activating the Smart
Com function and turn on the power to the
system again. The installation then starts
automatically.
3. The installation of the Smart Com function is
finished when the default display is shown
again.
The activation process can be repeated with the
same SD card after a software update or re-
commissioning.
NOTICE!
IMPORTANT!
If you want to replace the complete Smart Con-
trol controller, a new Smart Com SD card is
required.
REMKO Smart Com
12

5 Checking that the
Smart Com is enabled
Check the status of the activation as follows:
User level
¯
Information
¯
Basic information
¯
Status
¯
Smart Com
¯
Activated Deactivated
Enabling the Smart Com function displays the acti-
vation at this level.
After the activation has been checked, switch off
the power to the heat pump again and replace the
SD card with the original card that you had
removed at the beginning.
After switching on the heat pump again, the instal-
lation of the Smart Com function is complete.
6 Configuring the
Smart Com function
The settings for the Smart Com function can be
made in the Expert level. To do so, touch the
REMKO logo in the upper right corner of the dis-
play.
User level
¯
Activate Expert level by touching the REMKO
logo at the top right
¯
Password input using “+/-”
(Password: 0321)
¯
Confirm password with “OK”
¯
Expert level
Enabling and programming
This function is not activated ex works. You must
set the following parameters to activate this func-
tion:
Expert level
¯
Settings
¯
Default settings
¯
Interfaces
¯
KNXnet/IP
Your KNXnet/IP data can be programmed at this
level.
First start with the physical address of the inter-
face.
KNXnet/IP
¯
IA for the KNX interface
13

The physical address setting for the KNX inter-
face is required to find the correct interface in a
network with multiple KNX interfaces. This
parameter setting must therefore match the
physical address of the KNX interface. For
instructions on setting the physical address, see
the operating manual for the KNX interface that
is used.
Set the physical address for the Smart Control
Touch controller.
If the setting is 0.0.0, an address that is assigned
by the interface is adopted. This address may
change each time the connection is established
again.
Use the controller's operating unit to set the
physical address for the SMT controller (tun-
neling connection address). The parameter is
only displayed when activating programming
mode and the setting is only adopted once pro-
gramming mode is deactivated. The physical
address for the SMT controller must be located
topologically in line with the KNX interface, i.e. if
the KNX interface has address 1.1.1, the con-
troller must receive address 1.1.2 or 1.1.3, for
example.
KNXnet/IP
¯
IA for the controller
Activating the Smart Com connection
The Smart Com connection can be activated once
the configuration has been adjusted.
KNXnet/IP
¯
Smart Com
¯
Activated Deactivated
After you activate the Smart Com function, communication objects such as those shown in the following
table are enabled to program the group address and communication flags.
Communication flags:
Parameter Option / area Factory setting Customer setting
Smart Com Activated / Deacti-
vated Deactivated
Interface search Unicast / multicast Multicast
IP for the KNX interface Enter the IP address 192.168.0.115
IA for the KNX interface 0.0.0 - 15.15.255 0.0.0
Multicast address Enter the IP address 224.0.23.12
IA for the controller 0.0.0 - 15.15.255 0.0.0
Programming mode Activated / Deacti-
vated Deactivated
REMKO Smart Com
14

After you activate programming mode, the following parameters are enabled for programming:
Parameter Option / area Factory setting Customer setting
On/off (switching) (C-CRWT)
0-15/0-7/0-255 (CW) 5 / 0 / 1
Heating/cooling (switching) (C-CRWT)
0-15/0-7/0-255 (CW) 5 / 0 / 2
Heating/cooling (status) (C-CRWT)
0-15/0-7/0-255 (CRT) 5 / 0 / 3
SMT operating mode (switching) (C-CRWT)
0-15/0-7/0-255 (CW) 5 / 0 / 45
SMT operating mode (status) (C-CRWT)
0-15/0-7/0-255 (CRT) 5 / 0 / 5
Outside temperature (C-CRWT)
0-15/0-7/0-255 (CRT) 5 / 0 / 6
Room set temperature (C-CRWT)
0-15/0-7/0-255 (CW) 5 / 0 / 7
Defrosting (status) (C-CRWT)
0-15/0-7/0-255 (CRT) 5 / 0 / 8
HW set temperature (C-CRWT)
0-15/0-7/0-255 (CW) 5 / 0 / 9
HW actual temperature (C-CRWT)
0-15/0-7/0-255 (CRT) 5 / 0 / 10
One-off hot water (C-CRWT)
0-15/0-7/0-255 (CW) 5 / 0 / 11
Alarm signal (status) (C-CRWT)
0-15/0-7/0-255 (CRT) 5 / 0 / 12
Unmix. HC actual temp. (C-CRWT)
0-15/0-7/0-255 (CRT) 5 / 0 / 13
1st mixed HC actual temp. (C-CRWT)
0-15/0-7/0-255 (CRT) 5 / 0 / 14
2nd mixed HC actual temp. (C-CRWT)
0-15/0-7/0-255 (CRT) 5 / 0 / 15
3rd mixed HC actual temp. (C-CRWT)
0-15/0-7/0-255 (CRT) 5 / 0 / 16
4th mixed HC actual temp. (C-CRWT)
0-15/0-7/0-255 (CRT) 5 / 0 / 17
Unmix. HC room temp. (C-CRWT)
0-15/0-7/0-255 (CW) 5 / 0 / 18
1st mixed HC room temp. (C-CRWT)
0-15/0-7/0-255 (CW) 5 / 0 / 19
2nd mixed HC room temp. (C-CRWT)
0-15/0-7/0-255 (CW) 5 / 0 / 20
3rd mixed HC room temp. (C-CRWT)
0-15/0-7/0-255 (CW) 5 / 0 / 21
15

Parameter Option / area Factory setting Customer setting
4th mixed HC room temp. (C-CRWT)
0-15/0-7/0-255 (CW) 5 / 0 / 22
Cooling circuit room temp. (C-CRWT)
0-15/0-7/0-255 (CW) 5 / 0 / 23
Unmix. HC humidity (C-CRWT)
0-15/0-7/0-255 (CW) 5 / 0 / 24
1st mixed HC humidity. (C-CRWT)
0-15/0-7/0-255 (CW) 5 / 0 / 25
2nd mixed HC humidity (C-CRWT)
0-15/0-7/0-255 (CW) 5 / 0 / 26
3rd mixed HC humidity (C-CRWT)
0-15/0-7/0-255 (CW) 5 / 0 / 27
4th mixed HC humidity (C-CRWT)
0-15/0-7/0-255 (CW) 5 / 0 / 28
Cooling circuit humidity (C-CRWT)
0-15/0-7/0-255 (CW) 5 / 0 / 29
Time (C-CRWT)
0-15/0-7/0-255 (CRT) 5 / 0 / 30
Date (C-CRWT)
0-15/0-7/0-255 (CRT) 5 / 0 / 31
Unmix. HC room target temp. (C-CRWT)
0-15/0-7/0-255 (CW) 5 / 0 / 32
1st mixed HC room target temp. (C-CRWT)
0-15/0-7/0-255 (CW) 5 / 0 / 33
2nd mixed HC room target temp. (C-CRWT)
0-15/0-7/0-255 (CW) 5 / 0 / 34
3rd mixed HC room target temp. (C-CRWT)
0-15/0-7/0-255 (CW) 5 / 0 / 35
4th mixed HC room target temp. (C-CRWT)
0-15/0-7/0-255 (CW) 5 / 0 / 36
Cooling circuit room target temp. (C-CRWT)
0-15/0-7/0-255 (CW) 5 / 0 / 37
Unmix. HC presence object (C-CRWT)
0-15/0-7/0-255 (CW) 5 / 0 / 38
1st mixed HC presence object (C-CRWT)
0-15/0-7/0-255 (CW) 5 / 0 / 39
2nd mixed HC presence object (C-CRWT)
0-15/0-7/0-255 (CW) 5 / 0 / 40
3rd mixed HC presence object (C-CRWT)
0-15/0-7/0-255 (CW) 5 / 0 / 41
4th mixed HC presence object (C-CRWT)
0-15/0-7/0-255 (CW) 5 / 0 / 42
Cooling circuit presence object (C-CRWT)
0-15/0-7/0-255 (CW) 5 / 0 / 43
REMKO Smart Com
16

Parameter Option / area Factory setting Customer setting
Unmix. HC operating mode (C-CRWT)
0-15/0-7/0-255 (CRT) 5 / 0 / 44
1st mixed HC operating mode (C-CRWT)
0-15/0-7/0-255 (CRT) 5 / 0 / 45
2nd mixed HC operating mode (C-CRWT)
0-15/0-7/0-255 (CRT) 5 / 0 / 46
3rd mixed HC operating mode (C-CRWT)
0-15/0-7/0-255 (CRT) 5 / 0 / 47
4th mixed HC operating mode (C-CRWT)
0-15/0-7/0-255 (CRT) 5 / 0 / 48
Cooling circuit operating mode (C-CRWT)
0-15/0-7/0-255 (CRT) 5 / 0 / 49
Heat pump energy (C-CRWT)
0-15/0-7/0-255 (CRT) 5 / 0 / 50
Heating energy (C-CRWT)
0-15/0-7/0-255 (CRT) 5 / 0 / 51
Hot water energy (C-CRWT)
0-15/0-7/0-255 (CRT) 5 / 0 / 52
In order to check the settings, you have the option of checking the following parameters at the
"Information/KNX/IP" level:
Level 2 menu item Level 3 menu item
KNXnet/IP
IP for the KNX interface
MAC for the KNX interface
IA for the KNX interface
IA of the SMT (I/O module)
KNX connection status
Programming mode
17

7 Data points
Data points
CO1)
Grp.-
addr. 2) Name 3) DPT 4) Size 5)
Communica-
tion flag 6) Function description
0 5/0/1 On/off
(Switching)
DPT 1.001
(DPT_Switch)
(0) Off
(1) On
1 bit C - W -
(0) Off: Switches room cli-
mate mode to standby
(1) On: Switches room cli-
mate mode to the operating
mode selected (by object
2) (i.e. to heating or
cooling)
1 5/0/2
Heating/
cooling
(Switching)
DPT 1.100
(DPT_Heat-
Cool)
(0) Cooling
(1) Heating
1 bit C - W -
(0) Cooling: Switches room
climate mode to cooling
(1) Heating: Switches room
climate mode to heating
2 5/0/3
Heating/
cooling
(Status)
DPT 1.100
(DPT_Heat-
Cool)
(0) Cooling
(1) Heating
1 bit C R - T
Returns the value 0
(cooling) if the current room
climate mode for the SMT
controller is also on cooling
(including cooling in auto-
matic mode)
3 5/0/4
SMT
Operating
mode
(Switching)
DPT 20.102
(DPT_HVAC-
Mode)
(0) Auto
(1) Comfort
(2) Standby
(3) Night (Eco)
(4) Protection
mode (frost/
heat)
1 byte C - W -
(0) Auto: The SMT con-
troller and all room control-
lers work in auto mode.
(1) Comfort: The SMT con-
troller works in comfort
mode. The room controllers
work in auto mode.
(2) Standby: The SMT con-
troller and all room control-
lers work in standby mode.
(3) Night (Eco): The SMT
controller and all room con-
trollers work in eco mode.
4 5/0/5
SMT
Operating
mode
(Status)
DPT 20.102
(DPT_HVAC-
Mode)
(0) Auto
(1) Comfort
(2) Standby
(3) Night (Eco)
(4) Protection
mode (frost/
heat)
1 byte C R - T
The Smart Control con-
troller transfers the oper-
ating mode (HVACMode)
from object 3 when the
KNX bus is changed.
REMKO Smart Com
18

CO1)
Grp.-
addr. 2) Name 3) DPT 4) Size 5)
Communica-
tion flag 6) Function description
5 5/0/6 Outside
temperature
DPT 9.001
(DPT_Value_Te
mp)
-273°C - 670
760°C
2 byte C R - T
The Smart Control con-
troller transfers the outside
temperature to the KNX
bus.
6 5/0/7
Room
target
temperature
DPT 9.001
(DPT_Value_Te
mp)
-273°C - 670
760°C
2 byte C R W T
The Smart Control con-
troller converts the "hotter/
colder" parameter setting
into a target value (e.g.
+2K corresponds to 22°C)
and sends this to the KNX
bus. This can be used by a
KNX room temperature
controller as the basic
target value.
7 5/0/8 Defrosting
(status)
DPT 1.001
(DPT_Switch)
(0) Off
(1) On
1 bit C R - T
The Smart Control con-
troller transfers the outdoor
unit's defrosting status to
the KNX bus (1 =
defrosting active).
8 5/0/9 HW target
temperature
DPT 9.001
(DPT_Value_Te
mp)
-273°C - 670
760°C
2 byte C - W -
The HW target temperature
is transferred from the KNX
bus to the Smart Control
controller.
9 5/0/10 HW actual
temperature
DPT 9.001
(DPT_Value_Te
mp)
-273°C - 670
760°C
2 byte C R - T
The Smart Control con-
troller transfers the HW
actual temperature to the
KNX bus.
10 5/0/11 One-off
hot water
DPT 1.017
(DPT_Trigger)
(0,1) Trigger
signal
1 bit C - W -
A trigger pulse activates/
deactivates the function
(regardless of the value
received)
11 5/0/12 Alarm signal
(Status)
DPT 1.005
(DPT_Alarm)
(0) No alarm
(1) Alarm
1 bit C R - T
The Smart Control con-
troller transfers a signal to
the KNX bus if there is a
malfunction.
12 5/0/13 Unmix. HC
actual temper.
DPT 9.001
(DPT_Value_Te
mp)
-273°C - 670
760°C
2 byte C R - T
The Smart Control con-
troller transfers the hot
water temperature
(average of the inlet tem-
perature and the return
temperature) to the KNX
bus.
19

CO1)
Grp.-
addr. 2) Name 3) DPT 4) Size 5)
Communica-
tion flag 6) Function description
13 5/0/14 1st mixed HC
actual temper.
DPT 9.001
(DPT_Value_Te
mp)
-273°C - 670
760°C
2 byte C R - T
The Smart Control con-
troller transfers the hot
water temperature
(average of the inlet tem-
perature and the return
temperature) to the KNX
bus.
14 5/0/15 2nd mixed HC
actual temper.
DPT 9.001
(DPT_Value_Te
mp)
-273°C - 670
760°C
2 byte C R - T
The Smart Control con-
troller transfers the hot
water temperature
(average of the inlet tem-
perature and the return
temperature) to the KNX
bus.
15 5/0/16 3rd mixed HC
actual temper.
DPT 9.001
(DPT_Value_Te
mp)
-273°C - 670
760°C
2 byte C R - T
The Smart Control con-
troller transfers the hot
water temperature
(average of the inlet tem-
perature and the return
temperature) to the KNX
bus.
16 5/0/17 4th mixed HC
actual temper.
DPT 9.001
(DPT_Value_Te
mp)
-273°C - 670
760°C
2 byte C R - T
The Smart Control con-
troller transfers the hot
water temperature
(average of the inlet tem-
perature and the return
temperature) to the KNX
bus.
17 5/0/18 Unmix. HC
room temper.
DPT 9.001
(DPT_Value_Te
mp)
-273°C - 670
760°C
2 byte C - W -
The room temperature is
sent from the KNX bus to
the Smart Control controller
and used for the circuit's
room temperature influ-
ence. The selection param-
eter for the room control
must be set to KNX for this.
18 5/0/19 1st mixed HC
room temper.
DPT 9.001
(DPT_Value_Te
mp)
-273°C - 670
760°C
2 byte C - W -
The room temperature is
sent from the KNX bus to
the Smart Control controller
and used for the circuit's
room temperature influ-
ence. The selection param-
eter for the room control
must be set to KNX for this.
19 5/0/20 2nd mixed HC
room temper.
DPT 9.001
(DPT_Value_Te
mp)
-273°C - 670
760°C
2 byte C - W -
The room temperature is
sent from the KNX bus to
the Smart Control controller
and used for the circuit's
room temperature influ-
ence. The selection param-
eter for the room control
must be set to KNX for this.
REMKO Smart Com
20
Table of contents
Other REMKO Control Unit manuals
Popular Control Unit manuals by other brands
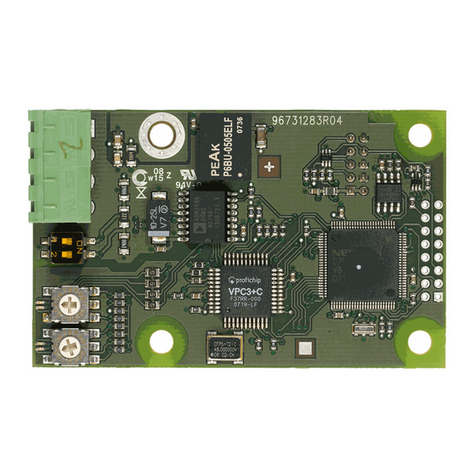
Grundfos
Grundfos CIM 150 Functional profile and user manual
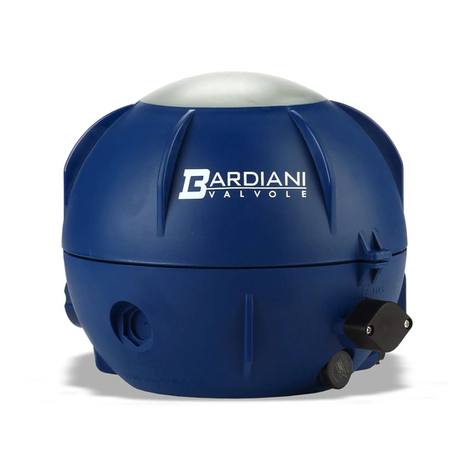
Bardiani Valvole
Bardiani Valvole GIOTTO TOP Instruction, use and maintenance manual
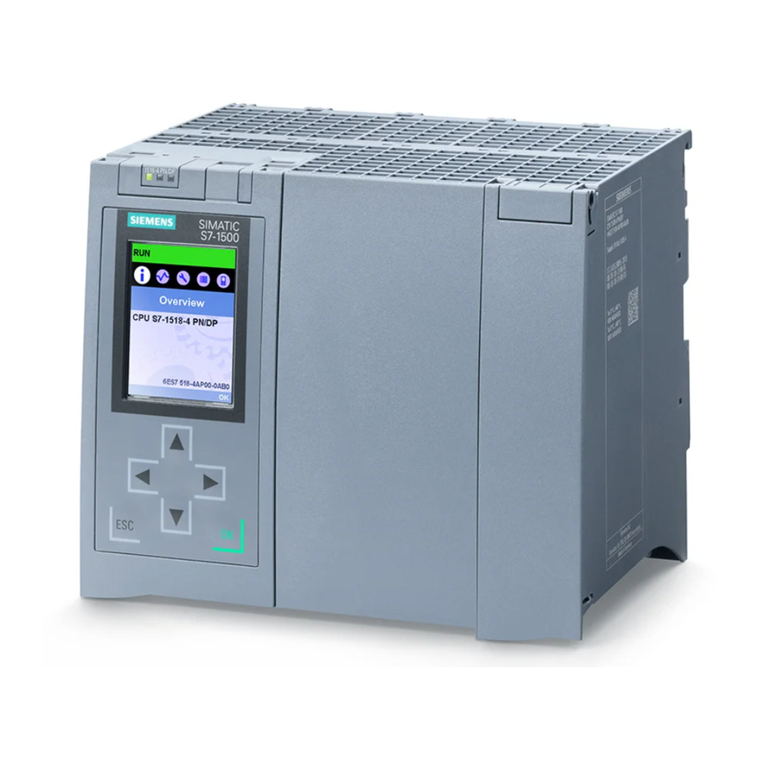
Siemens
Siemens Simatic S7-1500 manual
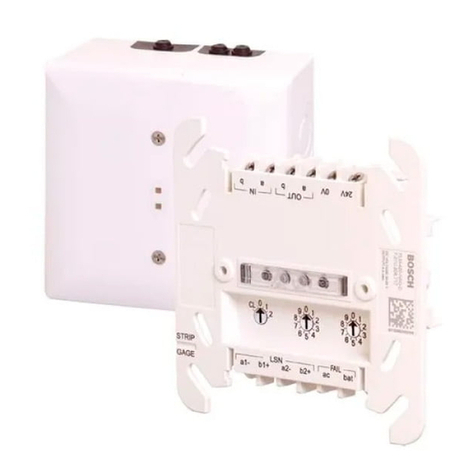
Bosch
Bosch FLM-I 420-S Product description/Installation manual
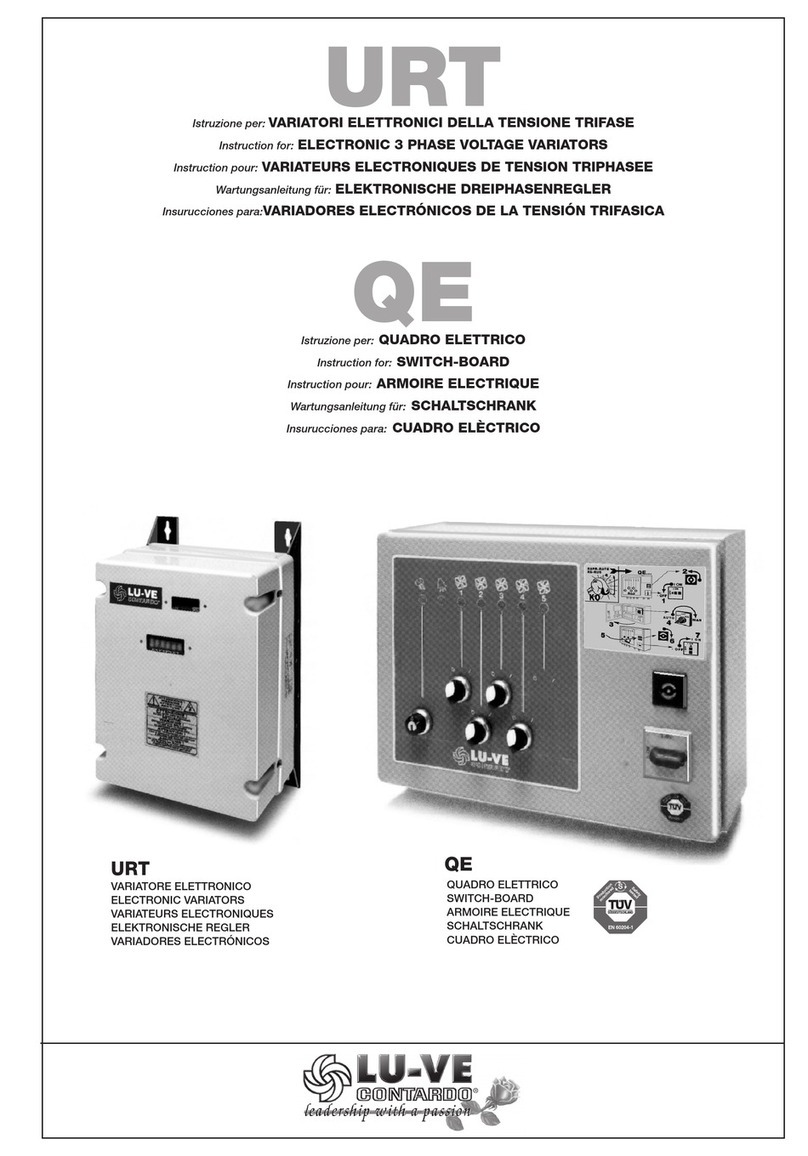
LU-VE
LU-VE URT312 Instruction
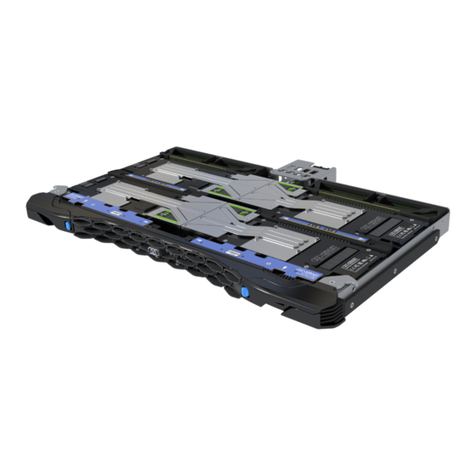
Amulet Hotkey
Amulet Hotkey MX7000 CoreModule quick start guide