RichAuto RichAuto-AutoNow-B15 User manual

Beijing RichAuto S&T Co., Ltd.
RichAuto-AutoNow-B15 Motion Control System
User’s Manual
Applied in B15 multi-spindle controller
FREE Download from
www.richnc.com.cn
北京锐志天宏科技股份有限公司
Beijing RichAuto S&T Co., Ltd.
Add:5F, No.4 building, No. 4 Yard, Shengmingyuan Road, Zhongguancun Life Science Park
Beiqing St., Changping District, Beijing 102206 China Tel/Fax:(+86)-010-53275118/53275119
Website1:www.richauto.com.cn Website2:www.richnc.com.cn

Beijing RichAuto S&T Co., Ltd.
Thank you for choosing RichAuto products!
This manual helps you be familiar with the company's products, and get information
about systems’ components、configuration etc.
This manual contains detailed knowledge of the system characteristics、operating procedures,
installation &commissioning, and safety precautions. Please read this manual carefully before
using the system and machine, which will help you to use it better.
Cautions:
1. It’s strictly prohibited in the strong interference and strong magnetic field environment.
Operating ambient temperature:0-70 ℃;Environment humidity: 0-90% (non-condensing).
2. Insert U disk in the correct direction. Do not pull out or insert 50-pin signal transmission cable
when system is powered on.
3. During the perform processing in U disk file, do not pull out the U disk to prevent the
interruption of data transmission.
4. Strictly prohibited metal, dust, and other conductive substances drop into the handheld
controller shell.
5. The machine casing shall be well grounded to ensure work safety and prevent interference.
6. Unauthorized removal is strictly prohibited, no internal user repairable parts.
7. For long time not using, please power off and keep it properly.
8. Be careful to prevent it from water, dust, fire when using.
9. Do not use the corrosive chemical solvents to clean the device.
10. Spindle motor bearing life and its speed is inversely proportional.
11. Graver is very sharp. Do not touch when it is running, in order to avoid injury; Do not use
handkerchiefs, scarves to approach it to prevent embroiled damage.

Beijing RichAuto S&T Co., Ltd.
Important statement:
The Company shall not be responsible for any loss caused by improper using or failure to
comply with the rules of operation.
Beijing RichAuto S&T Co., Ltd owns final interpretation of this manual, we reserves the rights to
revise all information in this manual, including data, technical details, etc.

Beijing RichAuto S&T Co., Ltd.
Content
Foreword……………………………………………………………………………………………………………………………..1
System introduction……………………………………………………………………………………………………..1
Performance characteristics…………………………………………………………………………………..…….1
Product parameters…………………………………………………………………………………………..…………2
Model List……………………………………………………………………………………….……………………………2
1. RichAuto system composition…………………………………………………………..……………………………3
1.1 System composition……………………………………………………………………………………….3
1.2 Components description………………………………………………………………………………....4
1.2.1 Handheld controller…………………………………………….…………..…………….4
1.2.2 Interface board……………………………………………………….………….………….5
1.3 Interface board installation dimensions……………………………………….…………………..5
1.4 System startup methods………………………………………………………….……………………….6
2. Handheld controller buttons introduction…………………………………………….………………………..6
2.1 Buttons introduction………………………………………………….…………………………………….6
2.2 Usage mode………………………………………………………………….………………………………….7
2.3 Detailed annotation for buttons……………………………………………….………………………8
3. Wiring description…………………………………………………………………………….……………………………10
3.1 interface board terminal…………………………………………………..………………………………10
3.2 I/O ports……………………………………………………………………….………………………………….11
3.3 Hardware wiring…………………………………………………………..…………………………………..12
3.4 Adjusting.. of machine tools and control systems……………………..………………..…….16
4. Menu description……………………………………………………………………………………….…………………..16
4.1 Menu classification…………………………………………………………………………………………..16
4.2 Menu details…………………………………………………………………………………………………….17
4.2.1 Machine setup…………………………………………….…………………………….……17
4.2.2 Auto pro setup………………………………………………………………………….…….24
4.2.3 System setup…………………………………………………………………….…………….27
4.2.4 Operate file……………………………………………………………………………..………31

Beijing RichAuto S&T Co., Ltd.
4.2.5 Version view…………………………………………………………………….…………….32
5. Machine operation……………………………………..………………………………………………………………….32
5.1 Return HOME…………………………………………………………………………………………………..32
5.2 Import processing file…………………………………………….………………………………………..33
5.3 Manual processing operation……………………………………………………….………………….33
5.3.1 Manual speed switching and adjustment…………………………………..…..33
5.3.2 Manual processing mode……………………………………………………..………..34
5.3.3 Manual testing input and output…………………………………….……………..35
5.3.4 Manual switching coordinate system…………………………………….……….35
5.4 Auto processing operation……………………………………………………………………………….36
5.4.1 Set workpiece origin………………………………………………………………………36
5.4.2 Select processing file……………………………………………………………………..37
5.4.3 Set processing parameters……………………………………………..……………..37
5.5 Processing operations………………………………………………………………………………….….38
5.5.1 Speed ratio & spindle state adjusting….………………………………....……..38
5.5.2 Suspend processing &position adjustment…………………………………….39
5.5.3 Breakpoint processing &power failure recover………………………………39
5.6 Advanced processing………………………………………………………………………………….……41
5.6.1 Array work………………………………………………………………………………….....42
5.6.2 Breakpoint processing....………………………………………..……………………..43
5.6.3 Manual tool change………………………….................................................43
5.6.4 Park work………………………………………………………………………………..…….43
5.6.5 Count boundary…………………………………………….………………………………44
5.6.6 Milling plane………………………………………………….………………………………45
5.6.7 Count work time…………………………………………….……………………………..46
5.6.8 View location line No…………………………………………….………………………46
5.6.9 Scale processing…………………………………..………………………………………..47
PS1. System upgrade operation………………………………………………………………………………………..48
PS2. “U disk mode” function introduction………………………………………………………………………..49
PS3. Servo wiring and parameters setting………………………………………………...………………………50

Beijing RichAuto S&T Co., Ltd.
PS4. G code reference list………………………………………………………………………………………………...57
PS5. Tool setting methods detailed explanation……………………………………………………………....59
PS6. Pulse equivalent calculation……………………………………………………………………………………..63
PS7. Common troubleshooting…………………………………………………………………………………………69
PS7.1 Handle screen prompt fault information solution……..............…………….…..69
PS7.2 Common problems during operation………………………………………………….……71
PS7.3 Electrical components and circuit problems……………..................................74

Beijing RichAuto S&T Co., Ltd.
1
Foreword
System introduction:
RichAuto CNC motion control systems are independently developed by Beijing RichAuto S&T
Co., Ltd. It can be widely applied to machinery, advertisement, woodworking, mold engraving
machines, laser, flame, plasma cutting machines, woodworking lathe, dispensing machine and
soon in the industry machine control field.
RichAuto make DSP as the core control system,High-speed processing operation which are
the microcontroller, PLC systems can’t match;Embedded structure,High degree of integration,
Strong stability, easy to installation and operation;support U disk, Removable storage card
reader,With USB Interface,High speed transfer,Plug and play . Fully offline work.
Performance characteristics:
1. System standard configuration is X, Y, Z axis motion control method, and supports the rotation
axis(C axis)control which enables the switch between rotary machining and plane processing .
Can be extended to X, Y, Z, C four-axis motion control to realize 4 axes linkages control.
2. Multiple I/O ports control. Standard equipped with I/O signal node which has 8 inputs and 7
output signals.
3. Support the standard G code, PLT format instructions; support domestic and international
mainstream CAM software, such as: Type3, Artcam, UG, Pro/E, MasterCAM, Cimatron, Ucancam
etc.
4. Provide with power failed protection. System automatically save the current processing
information in the moment of sudden power down (file name, current line number, work speed,
spindle state);After powered up and returned HOME position, the system automatically prompts
the user to restore the processing before power down which makes processing operations
become more humanity.
5. Support breakpoint memory, select file line No. processing. Can save 8 different breakpoint
processing information.
6. Multi-coordinate memory function. Provide 9 working coordinate system. The User can switch
among the 9 coordinates, each coordinate system can save a process origin information.
7. Support adjusting spindle operating frequency (or spindle rotate speed). The spindle frequency
is divided into 8 shifts. During processing, user can adjust shifts directly by keys without suspend
processing.
8. Support adjust speed ratio during operation. To adjust the speed ratio so as to change the
processing speed and travel speed, speed ratio values from 0.1-1. Increasing or decreasing 0.1 per
time.
9. Simple manual operate mode. In manual mode, the system provides 3 kinds of move modes,
including continuous, step (crawl), distance, become more simple and convenient.
10. Identifies M code, F code and other extended instructions, and it can also open a special code
based on user’s needs.
11. Built-in 512 M memory. Adapt USB communication port with high efficiency for file transfer.
Can read files in U disk and card reader directly.

Beijing RichAuto S&T Co., Ltd.
2
12. Unique handheld structure which can be hold with one hand. With LCD display and 24 keys
operation keyboard, intuitive and flexible operation, no longer rely on the computer, completely
offline operation.
13. Self-detection function. The system comes with I/O ports signal detection function, easy
remote maintenance.
Product parameters:
Model No. RichAuto-B15
CPU DSP Power down protection Support
Built in memory 512MB Breakpoint processing 8
Display screen 128*64Monochrome LCD
External supply voltage DC 24V
Communication
port U disk Manual mode Continuous, step,
distance
Linkage axis No. 3to 4axes Interpolate method Straight line, arc,
spline curve
Control signal 5V common anode Soft / hard limit Support
Driving system Stepper / servo motor Maximum pulse frequency
1MHz
Minimum input
unit 0.001mm Password protection Support
Languages Simplified Chinese, English, traditional Chinese, other languages can be
customized
Standard layout Handheld controller with USB adapter 1pc;50 pins cable 1 pc、I/O interface
board 1 pc, USB data cable 1 pc
Model List:
AutoNow
3 inches Monochrome screen
B1Xseries motion control
system
Model No. Name
B15 Cylinder multiple spindle

Beijing RichAuto S&T Co., Ltd.
3
1. RichAuto system composition
1.1 System composition
RichAuto control system contains the following parts:1pc of hand-held controller
(handle), 1pc of interface board, 1pc of 50-pin data transmission cable, 1pc of USB
communication cable.
RichAuto schematic diagram of system accessories
Hand-held controller Interface board
Both ends tenon type USB communication cable
data transmission cable

Beijing RichAuto S&T Co., Ltd.
4
1.2 Components description
1.2.1 Handheld controller
As shown below,including 6 parts:
1) LCD screen: 128 * 64 resolution LCD display,to display the machine motion, system settings
and other information.
2) Key area: Contains 24 buttons to set system parameter information and the machine
movement control operation.
3) U disk adapter: External memory like U disk and the card reader throw-over access port. It can
identify the files from external memory; System format is FAT16/32 format. This part can be
removed separately if it is damaged.
4) RichAuto LOGO
5) 50-pin cable socket: To realize the connection between the system and the machine tool via
50-pin cable. The motion signal given by the system is transmitted to the machine tool motion
actuator.
6) USB communication interface: The port of USB communication cable. It is used to connect the
handle and computer.
LCD Screen
RichAuto LOGO
U Disk Adapter
Key Area
USB Communication
Interface
50-pin Cable Socket

Beijing RichAuto S&T Co., Ltd.
5
1.2.2 Interface board
Between handle and machine tool is controlled by the interface board connection. The
connection ports contain 5 parts, as shown in the following figure:
Interface board
50-pin cable socket:To connect the handle and machine tool via 50-pin cable, and transmit
motion signal from system to the machine tool motion actuator.
Output signal terminal: To control spindle ON/OFF and spindle speed shifts etc.
Input signal terminal: The input end of machine origin, tool setting, servo driver alarm, hard
limit, E-stop, foot switch signals.
Power supply terminal: The input terminal of system switching mode power supply (DC 24V,
3A).
Motor driver control terminal: Driver control signal output terminals.
1.3 Interface board installation dimensions
Scale 1:1, unit mm
Motor
driver
control
X AXIS
Y AXIS
Z AXIS
C AXIS
50-pin cable socket
J7: Output signal terminal
J8: Input signal terminal
J10: Power supply terminal
DC24V

Beijing RichAuto S&T Co., Ltd.
6
1.4 System startup methods
RichAuto-B1X motion control system contains 2 starting methods:
Normal starting: Normal power on the system, after boot it will enter into HOME TYPE interface
and manual control interface.
Emergency starting: If normal starting cannot show any words or manual interface, emergency
starting is required.
Power off the system first, then push “ ” and keep pressing, power on the controller
and waiting for 3-4 seconds. Release“ ”, will get into Emergency State interface, user
could either select System Update or Format System or don’t restart the system directly without
any selection.
2. Handheld controller buttons introduction
2.1 Buttons introduction
RichAuto handheld control system has defined 24 operation buttons, each one provides
one or more functions in different working states:
Real photograph of pressing keys
2.2 Usage mode
RichAuto provides 2 modes of button operations, including one-touch key & Combination keys.
One-touch key:Press one key on the handheld controller keypad is executing the single key
operation.
Combination keys:Press two keys at the same time to achieve certain function is executing

Beijing RichAuto S&T Co., Ltd.
7
combination keys operation;The operation steps: press one main function key not release it,
meanwhile press a second auxiliary function key, and then release the two buttons at the same
time to realize the combination keys operation. For instance, the system upgrade combination
keys are “ ” + “ ”. When operation, user could push the main function key
“ ”first, push auxiliary function key“ ” then, at last release both of them at the
same time.
Commonly used combination keys:
Combination Keys Function
1
“ ”+“0-9” numeric key
Coordinates systems switching keys
0 is mechanical coordinate system
1-9are working coordinate system
2
“ ”+ “ ”
Switching spindle shifts in manual mode
3
“ ”+“ ”
Repeat last processing
4
“ ”+“ ”
Set current position as parking position
5
“ ”+“ ”
System upgrade
6
“ ”+“ ”
Input coordinate parameter to move the
equipment to that position
7
“ ”+“ ”
Exit keyboard detection interface
Note: Users can also find the corresponding combination keys operations list at the back of the
handle.

Beijing RichAuto S&T Co., Ltd.
8
2.3 Detailed annotation for buttons
Key Name Function
X axis positive/negative movement;
Menu up/down selection;
figure 1,5 input
Yaxis positive/negative movement;
work speed up/down selection;
figure 2, 6 input
Zaxis positive/negative movement;
spindle speed up/down selection;
figure 3,7 input
Set X axis and Y axis work origin;
figure 4 input
Set work origin of Z axis;
Figure 8 input
Operation of return machine zero point (HOME) in manual
mode; Figure 8 input
FAST/LOW motion state switching in manual mode;
work coordinate/ mechanical coordinate switching in auto
mode; figure 0 input
Decimal input;
spindle ON/OFF in manual mode
Enter MENU setting;
View work information during processing;
negative sign
Return reference point operation;
OK key of all selections, inputs, operations

Beijing RichAuto S&T Co., Ltd.
9
Manual motion states;
Continuous, step, distance 3 modes switching
RUN/ PAUSE processing file;
DELETE the input data;
Selection of different attribute in MENU
Motion parameter adjustment in manual mode;
processing termination;
Cancellation of various options, inputs and operations during
processing
Switch to spindle No.1
Switch to spindle No.2
Switch to spindle No.3
user-defined
Enable Z axis automatic tool setting function
Enable advanced processing function
Repeat machining same processing file
Breakpoint processing combination main function key
( support the figure 1 to 8)

Beijing RichAuto S&T Co., Ltd.
10
3. Wiring description
3.1 Interface board terminal
X axis signal output terminal
Y axis signal output terminal
Z axis signal output terminal
C axis signal output terminal
24V power supply input terminal
Analog output terminal
Output signal connecting terminal
Input signal connecting terminal

Beijing RichAuto S&T Co., Ltd.
11
3.2 I/O ports
Terminal
Name
Pin definition Pin functions
and parameters Attention matters
DC24V
24V+ Input power supply+ Provide 24V operating voltage for
the interface board after power
up.
Recommend to use DC 24V
(current = 3A) current
source
GND return circuit ground
X_AXIS
5V Xaxis common anode
signal
X-axis driver common anode
power supply terminal, 5V output
Do not impose any other
voltage on this pin.
PULSE
Xaxis pulse signal Output voltage ≧3V;
Drive current≦8mA
DIR Xaxis direction signal Output voltage≧3V;
Drive current≦8mA
SHIELD
Shield signal X-axis driver signal output shield
wire
Do not impose any other
voltage on this pin.
Y_AXIS
5V Yaxis common anode
signal
Y-axis driver common anode
power supply terminal,5V output
Do not impose any other
voltage on this pin.
PULSE
Yaxis pulse signal Output voltage≧3V;
Drive current≦8mA
DIR Yaxis direction signal Output voltage≧3V;
Drive current≦8mA
SHIELD
Shield signal Y-axis driver signal output shield
wire
Do not use this port as a
ground port.
Z_AXIS
5V Zaxis common anode
signal
Z-axis driver common anode
power supply terminal, 5V output
Do not impose any other
voltage on this pin.
PULSE
Zaxis pulse signal Output voltage≧3V;
Drive current≦8mA
DIR Zaxis direction signal Output voltage≧3V;
Drive current≦8mA
SHIELD
Shield signal Z-axis driver signal output shield
wire
Do not use this port as a
ground port.
C_AXIS
5V C axis common anode
signal
C-axis driver common anode
power supply terminal, 5V output
Do not impose any other
voltage on this pin.
PULSE
C axis pulse signal Output voltage≧3V;
Drive current≦8mA
DIR C axis direction signal Output voltage≧3V;
Drive current≦8mA
SHIELD
Shield signal C-axis driver signal output shield
wire
Do not use this port as a
ground port.

Beijing RichAuto S&T Co., Ltd.
12
3.3 Hardware wiring
Installation Requirements:Switching mode power supply(24V, 3A), it’s better to add a
filter to prevent the electric field interference. If origin detecting switch is different power supply
type, the special detecting switch power supply is needed. (Recommend 24V origin detecting
switch).
RichAuto motion control system realizes its control through the connection between the
interface board and CNC machine. Interface board terminal can be divided into input terminal
and output terminal:
Input terminal:INPUT SIGNAL terminal; Main power supply terminal.
Output terminal:X,Y,Z,C axis pulse signal output terminal; OUTPUT SIGNAL terminal.
Input terminal
Main power supply wiring:
INPUT terminal wiring:
1) Return ZERO point (HOME): X, Y Z axis wiring methods are the same
Mechanical switch NPN normally open proximity switch
Example of PNP normally open proximity switch:

Beijing RichAuto S&T Co., Ltd.
13
2) Tool setting: Simple constructed cutter touch-off plate
3) X5-X8:Default low level normally open
Take the driver alarm as example:
The alarm signal is normally closed, wiring method is series connection. Meanwhile, revise
the voltage definition of X5.
If the alarm signal is normally open, the wiring method is parallel connection. See as below,

Beijing RichAuto S&T Co., Ltd.
14
Output terminals wiring:
X axis pulse signal wiring (Y, Z axis pulse signal wiring is the same to X axis)
Step drive:
Servo drive: Σ-7 and Σ-V are the same wiring method
Brake wiring:
Yaskawa servo Σ-V series driver
First, ensure that the brake output is enabled, and then set Pn50F to 0300, and select brake
signal output terminal CN-29 and CN-30. Wiring is as follow,
Table of contents
Other RichAuto Control System manuals
Popular Control System manuals by other brands
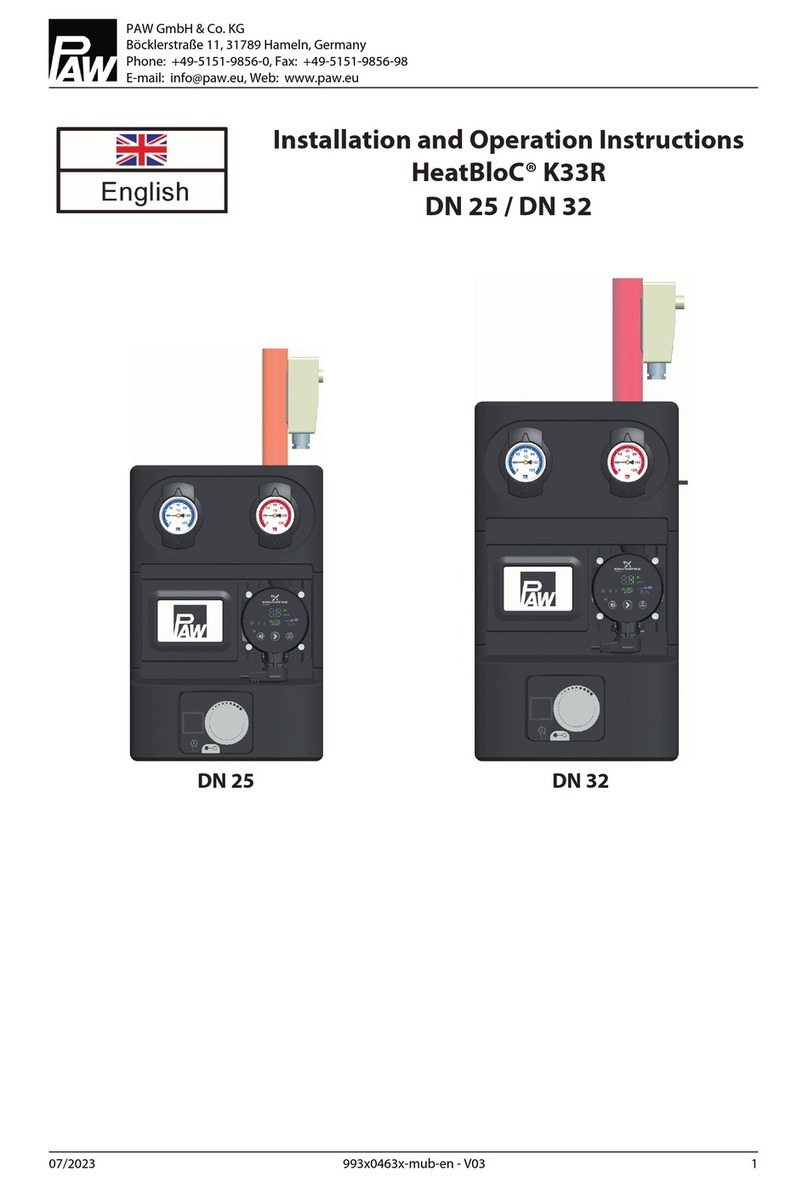
PAW
PAW HeatBloC K33R Installation and operation instruction
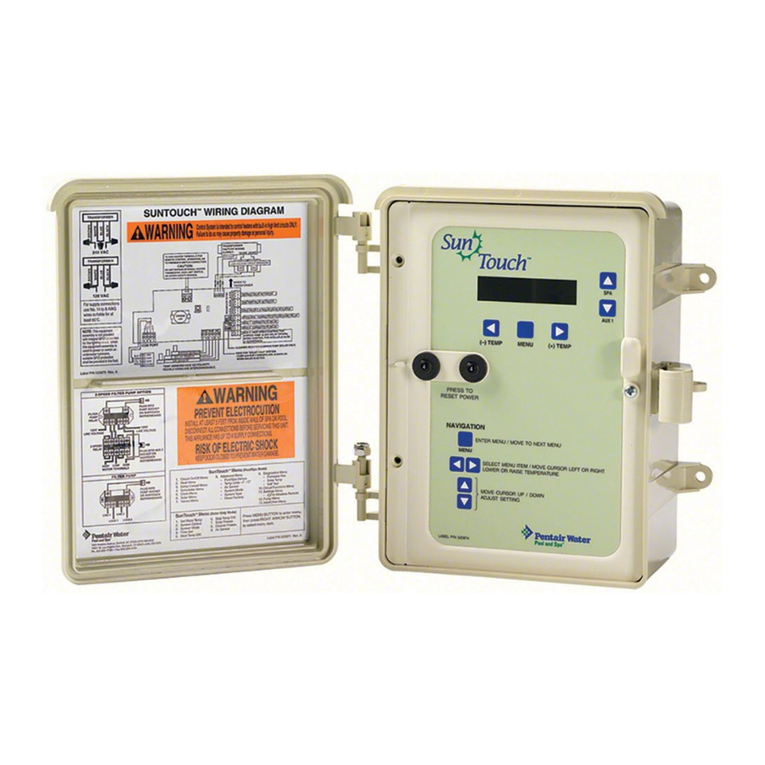
Pentair
Pentair Pool and Spa Control System SunTouch Installation and user guide
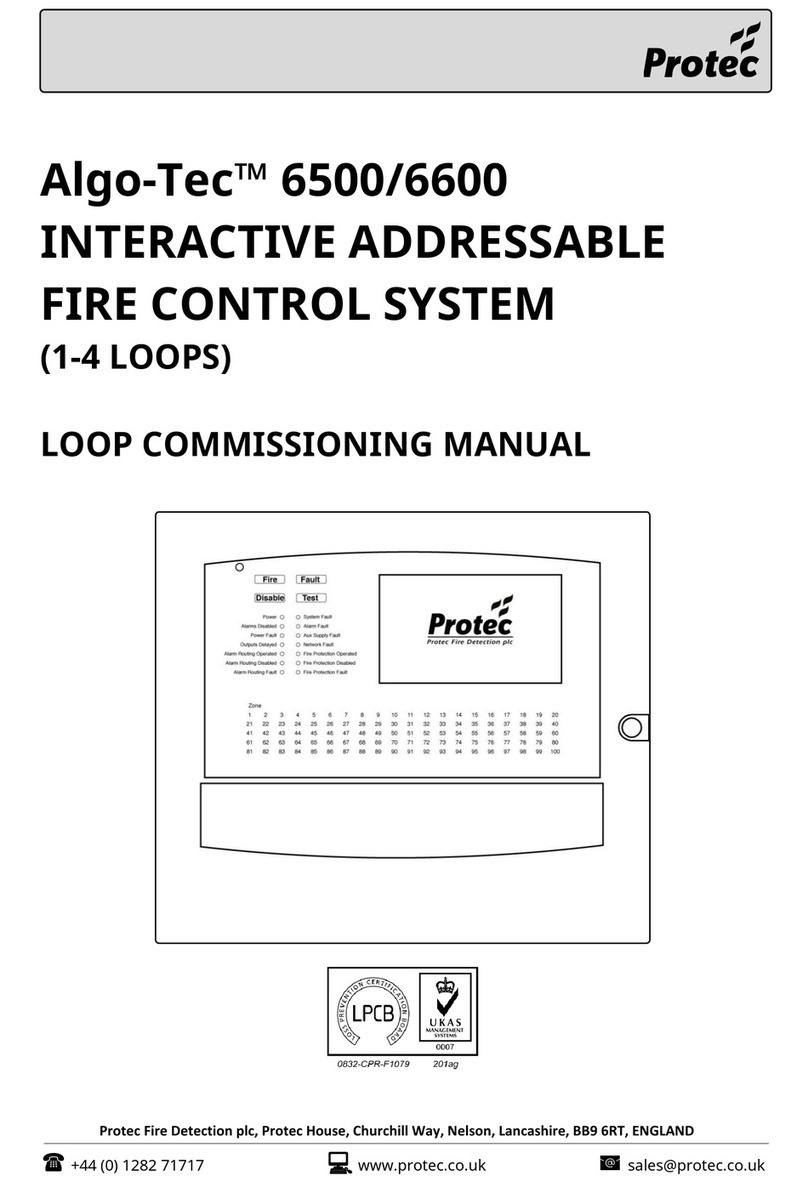
Pro-tec
Pro-tec Algo-Tec 6500 Commissioning manual
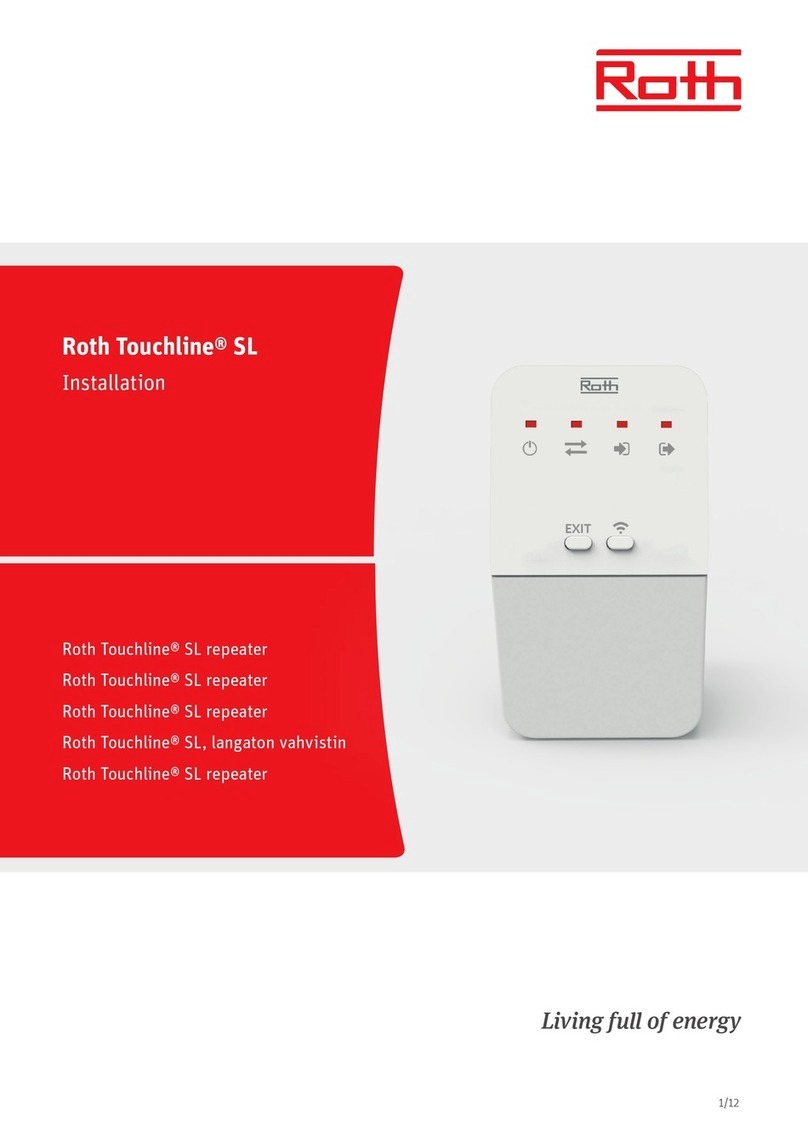
Roth
Roth Touchline SL Installation
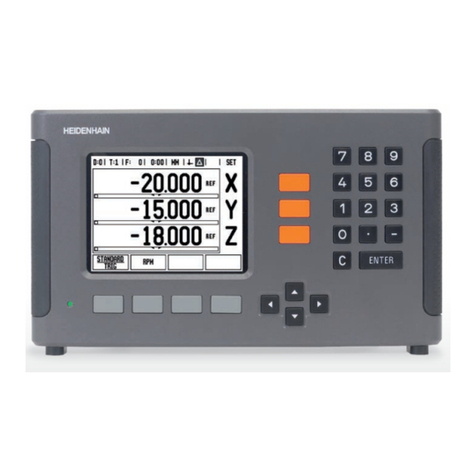
HEIDENHAIN
HEIDENHAIN ND 780 Installation instruction
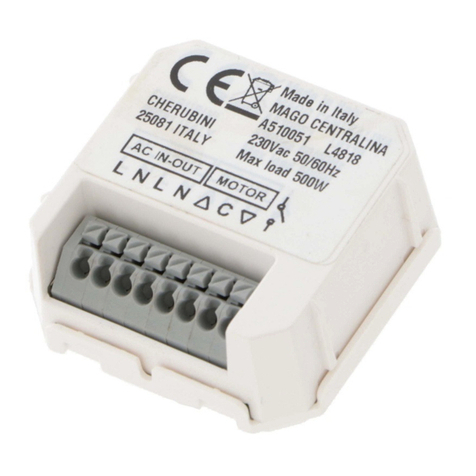
CHERUBINI
CHERUBINI MAGO instructions
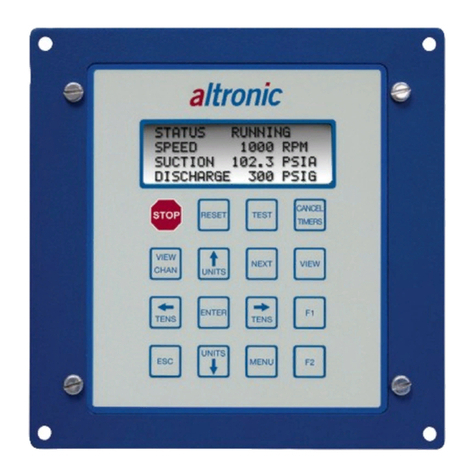
Altronic
Altronic DE-3000 operating instructions
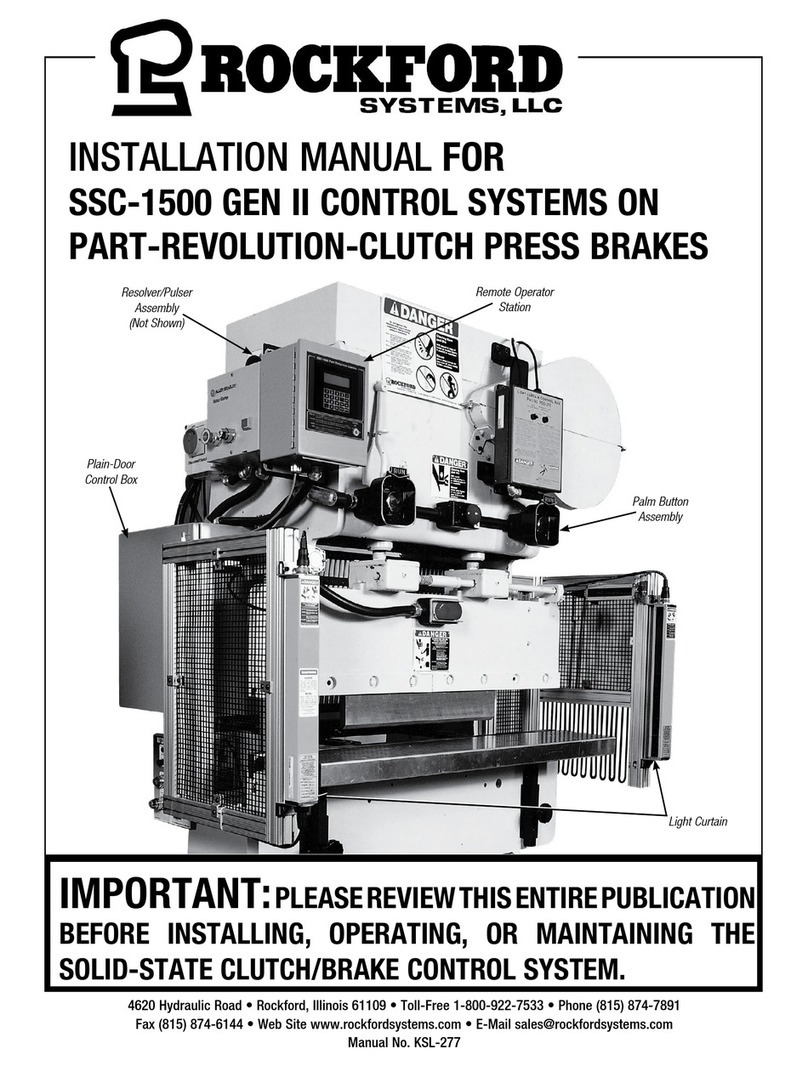
Rockford Fosgate
Rockford Fosgate SSC-1500 GEN II installation manual
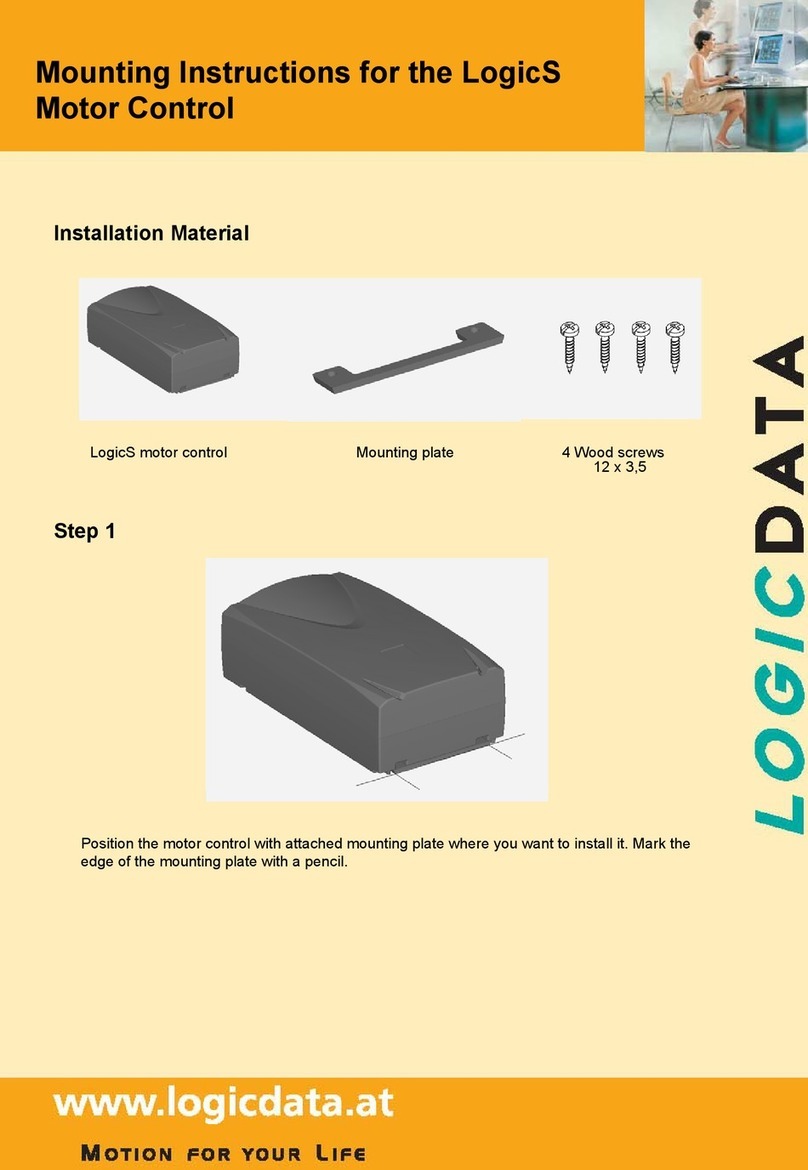
LOGICDATA
LOGICDATA LogicS Mounting instructions
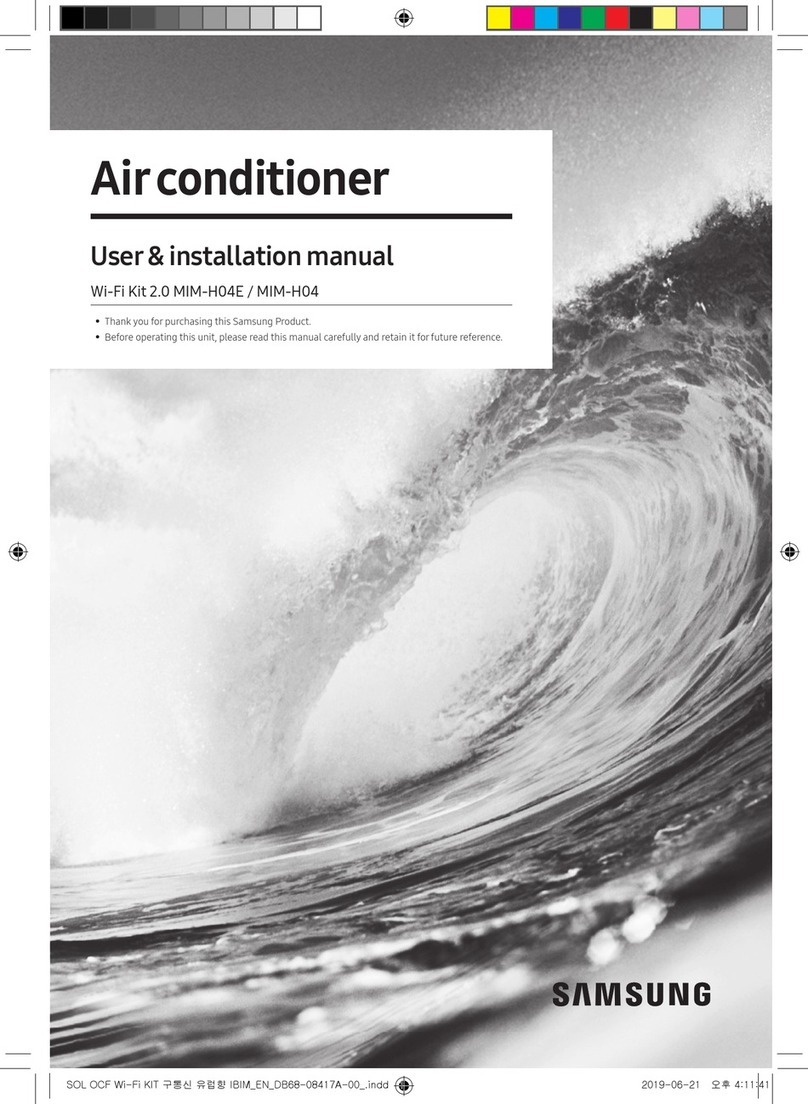
Samsung
Samsung Wi-Fi Kit 2.0 User & installation manual
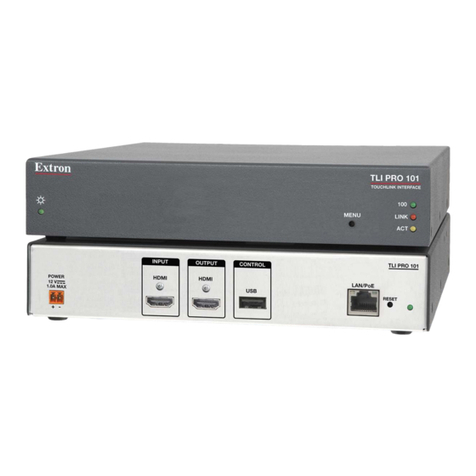
Extron electronics
Extron electronics TLI Pro 101 user guide
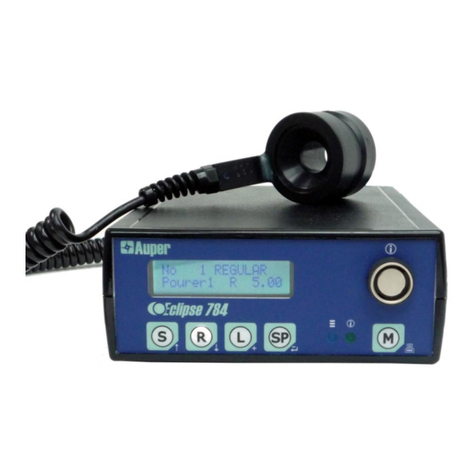
Auper
Auper Eclipse 784 B Quick user guide