RMG RMG 610 Guide

Osterholzstraße 45, D-34123 Kassel • P.O. Box 10 29 67, D-34029 Kassel
Phone 0049 561 5007-0 • Fax 0049 561 5007-107 • www.rmg.de
Operation and Maintenance 610.20
Spare Parts Edition 02/96
Pilot (RS 10d)
RMG 610
... providing all components you
need for reliability in gas supply

Table of contents
1.
2.
2.1
2.2
3.
3.1
3.2
3.3
3.4
4.
4.1
4.2
4.3
4.4
5.
5.1
5.2
5.3
General Instructions
Special Operation Instructions
Adjustment of the auxiliary pressure
Adjustement of the discharge valve
Special Maintenance Instructions
Auxiliary pressure stage
Control stage
Torque
Lubricants
Spare Parts Drawings RMG 610
Spare parts drawing RMG 610 with control stage tool N
and pilot intermediary part
Spare part drawing RMG 610 with pilot and auxiliary pressure stage
tool M
Spare parts drawing RMG 610
- Sleeve for auxiliary pressure stage with lever joint
- Spindle for discharge valve
- Lever bearing
Spare parts drawing pressure regulator for auxiliary pressure stage with
spare parts list
Spare Parts Lists
Spare parts list RMG 610
Spare parts list RMG 610
Spare parts list RMG 610
3
4
4
5
5
5
5
6
6
7
7
8
9
10
11
11
12
13
Seite
!Attention
... providing all components you
need for reliability in gas supply

1. General
Our leaflet 610.00 gives full information with technical data , different versions and dimensions of the pilot
RMG 610 (RS 10d).
Our brochure "General Operating Instructions for Gas Pressure Regulators and Safety Devices" will be
useful to fit the valve into the line, put it into service and find faults that might disturb its operation.
The construction, set-up, supervision and maintenance of gas pressure regulating stations are subject to
special technical rules which should be strictly observed, in particular those given by the DVGW Worksheets
G 490, G 491, and G 495.
The frequency of periodical maintenance to be foreseen for the safety shut-off valve RMG 711 should be
determined according to the prevailing service conditions and the type and composition of the gaseous
medium. We, therefore, abstain from imposing any fixed intervals and would rather refer you to the recommen-
dations given by the DVGW Worksheet G 495.
For maintenance all parts are to be cleaned and subjected to a thorough visual inspection. A visual inspection
should not be omitted when the course of operation or performance tests have shown lack of response
accuracy. Particular care should be given to the checking of sealings and diaphragms, as well as of all carrying
and movable parts, engagement and release systems of the tripping and measuring devices and of closing springs.
Damaged parts should be replaced by new ones.
The item numbers referred to in the maintenance instructions are identical with those of the spare parts drawings and
spare parts lists.
We recommend to keep all parts that are specially marked in the spare parts lists in stock for prompt maintenance
availability.
610.20 p. 3

Principal switch drawing of the pilot RMG 610 (RS 10d) with a switch gear
control stage
auxiliary stage
main valve
adjusting pressure
measuring line
discharge
line
discharge
throttle
setpoint adjuster
for auxiliary pressure
breathing line
breathing line
setpoint adjuster for outlet pressure
inlet pressure p outlet pressure p
ea
discharge valve
610.20 p. 4
gas pressure regulation unit
used in a pressure regulation device:
with direct following high guide network,
f.i. hand over stations
with direct following second pressure or
flow regulation valve, f.i. in a heat gas line
height of the auxiliary pressure over the
outlet pressure with a main valve
RMG 322, 332, 408, 409
approx. 1 - 2 bar
approx. 0,5 - 1 bar
RMG 200
approx. 2 - 4 bar
approx. 1 - 2 bar
2. Special Operation Instructions
2.1 Adjustment of the auxiliary pressure
The height of the adjusted auxiliary pressure influences the regulating procedure of the device.
To obtain a high precision of regulation, which is connected to a smaller closing pressure, an auxiliary pressure should be
adjusted as high as possible in the stabilization of the gas pressure regulation device.
According to the application the following advised values must be appplicated:
fine filter
protection cap

2.2 Adjustment of the discharge valve
The discharge valve is delivered from the plant with the main
adjustment. The necessary rotation of the spindle for this
adjustment is given on the picture situated on the pilot (see
drawing on the right).
By turning the spindle left to the bleed adjustment " - ", it is
possible to adapt the device to special operation instructions
-additionally to change the auxiliary pressure-
f.i. by regulation variations of "pressure picks" after a quick
closing of the stop organ preswitched.
Verstärkungseinstellung
Bleed adjustment
Adjustage d`amplification
X=
Grundeinstellung:
Linksdrehen bis Anschlag
X Umdrehungen nach rechts
Basic adjustment:
Turn anti-clockwise to the stop
turn spindle X times clockwise
Adjustage de base:
Tournez à gauche jusqu à l `arre
t
Apres à droite par X tours
610.20 p. 5
rotation
adjusting spindle
3. Special Maintenance Instructions
3.1 Auxiliary pressure stage (see page 8)
Diaphragm (68)
By dismantling, put the cover (69) off, put the diaphragm (68) on the side of the inlet pressure connection and
hang the diaphragm on the side outside the joint (80).
Sealing cone (81)
To dismantle the sealing cone, the screws (98) must be unscrewed and the complete joint (80)
must be put off. A mark of the sleeve corner (83) on the sealing surface of the sealing cone (81) is normal.
By installing the sealing cone, the position of the lever joint must be controlled after the installation of the joint and
newly adjusted if necessary.
The correct adjustment is given if the lever is manually put out (piston in closing position) and the superior corner of
the lever is parallel to the diaphragm support.
A possible and necessary correction is obtained by underlaying the different thicker sealing rings (51, 85) under the
intermediary piece.
3.2 Control stage - Tool M and N (see p. 6 and 8)
Control rod (16, 76)
The control rod must lightly slide in its conduction. By installing the new parts in the outlet pressure stage the
adjustment measure of the rod must be controlled according to the measurement tool and be corrected if necessary.
The adjustment measure must be put off according to the following drawing.
Adjustment measure for control stage tool N

610.20 p. 6
Beware:
Piston (23)
The piston of the control stage must lightly slide in its conduction.
The measure controls occur for an incorporated control pin (16, 76), that is to say the control rod
(20) is on the piston (23), the sleeve is still closed. The control rod is delivered with an excessive
length and must for this reason be shorted by replacing corresponding to the adjustment measure
and lastly borderless rounded .
3.3 Torque
30
2,5
3.4 Lubricants
part (to be greased slightly )
all o-rings,
all sliding surfaces and movable parts
adjusting screw (44, 116)
spring plate thread and recession
all fastening and
pipe screws
lubricant
silicone grease
mounting paste
high pressure
grease
part no.
00 027 081
00 027 091
00 027 058
(9)
(4)
Adjustement measure for control stage tool M
pos. no. torque
M in Nm
a

4. Spare Parts Drawings
4.1 Spare Part Drawing RMG 610 (RS 10d)
Pilot intermediary part with control stage tool N
610.20 p. 7
* Parts marked by an asterisk to be kept in stock maintenance

4.2 Spare Parts Drawing RMG 610 (RS 10d)
Control stage tool N, auxiliary pressure stage tool M
Control stage tool M
* Parts marked by an asterisk to be kept in stock for maintenance
610.20 p. 8

4.3 Spare Parts Drawing RMG 610 (RS 10d)
* Parts marked by an asterisk to be kept in stock for maintenance 610.20 p. 9
Sleeve for auxiliary pressure stage with lever joint
Sectional view A - C
Spindle for discharge line
partial view D Lever bearing
sectional view E - E

4.4 Spare Parts Drawing RMG 610 (RS 10d)
Pressure measuring unit for auxiliary pressure stage
pos. no.
150
151
152
153
154
description
pressure measuring unit
manometer union piece
protection against overpressure RMG 925
cap nut
compression joint
material
St/Ms
St
LM
St
St
part no.
pressure stage of the main valve
PN 16 PN 25 > PN 25
00 026 891
00 031 865
-
00 030 803
00 030 903
00 026 891
00 031 865
-
00 030 803
00 030 903
00 026 281
-
89 251 406
-
-
610.20 p.10
Material - key:
St
LM ... steel
... light metal Ms ... brass

5. Spare Parts Lists
5.1 Spare Part List RMG 610 (RS 10d)
pos.
no.
1
2*
3
4
5
-
-
-
-
-
6
7
8*
9
10
11
12
13*
14
15
16*
17*
18
19*
20*
21
22*
23*
24
25
26
27
28*
29
30*
31
32
33
34
-
-
-
-
-
Parts marked by an asterisk * to be kept in stock for maintenance
Material - key:
St
FSt
NSt
... steel
... spring steel
... stainless steel
NFSt
LM
Ms
... stainless spring steel
... light metal
... brass
KG ... rubber-like plastic
material
610.20 p.11
cap
o-ring
screw
hexagonal nut
spring plate, alternatively:
wh10 mbar to 40 mbar
wh20 mbar to 60 mbar
wh40 mbar to 120 mbar
wh80 mbar to 200 mbar
wh100 mbar to 500 mbar
diaphragm plate
hexagonal screw
o-ring
hexagonal nut
diaphragm plate
cylinder screw
superior lever bearing, complete
sealing ring
cylinder screw
intermediary ground
control pin 21 long
discharge jet
pressure spring
discharge cone
control rod
conduction disc
sealing ring
piston, already-made part 2nd stage
spring compensation piece
pressure spring
closing screw
body
control sleeve 2nd stage
pressure spring
o-ring
pressure piece
sealing screw
adjusting screw
spring compensation piece, alternatively:
wh10 mbar to 40 mbar
wh20 mbar to 60 mbar
wh40 mbar to 120 mbar
wh80 mbar to 200 mbar
wh100 mbar to 500 mbar
LM
KG
St
St
LM
LM
LM
LM
LM
St
St
KG
St
LM
St
Ms/NSt
KG
St
LM
NSt
Ms
FSt
NSt
Ms
Ms
LM
LM/KG
LM
FSt
Ms
LM
LM
NFST
KG
LM
Ms
Ms
St
St
St
St
St
description material order no.
10 012 139
00 020 307
10 017 650
00 013 138
10 016 679
10 017 661
10 017 661
10 017 661
10 016 681
10 016 672
00 010 054
00 020 353
00 005 692
10 017 654
00 006 044
10 017 669
00 008 032
00 006 543
10 017 588
10 017 930
10 017 608
10 017 886
10 017 591
10 017 603
10 017 610
00 018 688
10 017 893
10 017 614
10 017 639
10 017 606
10 024 341
10 017 884
10 014 020
00 020 003
10 017 600
10 017 927
10 012 140
10 014 931
10 014 931
10 014 931
10 014 933
10 014 933

5.2 Spare Part List RMG 610 (RS 10d)
pos.
no.
35
-
-
-
-
-
36
37
38
39
40
42
43
44*
45*
46
47
48
49*
50
51*
60*
61
62
63
64
65
66
67
68*
69
70
71
72
73
74
-
-
-
75
76*
610.20 p. 12
pressure spring, alternatively:
wh10 mbar to 40 mbar
wh20 mbar to 60 mbar
wh40 mbar to 120 mbar
wh80 mbar to 200 mbar
wh100 mbar to 500 mbar
threaded ring
cap nut
compression joint
dosing screw
threaded adapter
cover N
intermediary ring
diaphragm
sealing ring
inferior lever bearing, complete
cap nut
nozzle
sealing ring
union piece
sealing ring
USIT ring
cylinder screw
button headed dowel needle
adjusting poster
diaphragm plate
spring conduction plate
lever eye
rod screw
diaphragm
cover M
back-nut
pressure spring
spring compensation piece
regulation screw
pressure spring, alternatively:
wh 0,1 bar to 1,5 bar
wh 0,2 bar to 2,5 bar
wh 0,3 bar to 3,5 bar
sealing screw
control rod 17 long
FSt
FSt
FSt
FSt
FSt
LM
St
St
Ms
St+KG
LM
LM
KG
KG
Ms/NSt
St
St
KG
St
LM
St/KG
St
St
LM
St
LM
NSt
St
KG
LM
St
FSt
St
Ms
FSt
FSt
FSt
Ms
NSt
description material order no.
10 014 926
10 015 469
10 016 660
10 014 516
10 015 161
10 014 900
00 030 804
00 030 904
10 005 096
10 024 347
10 012 137
10 017 916
10 017 918
00 008 068
10 017 676
00 030 805
00 030 104
10 017 612
00 030 142
00 018 814
00 027 858
00 010 207
00 017 220
10 024 342
10 014 983
10 017 697
10 014 993
00 012 203
10 014 989
10 012 138
10 014 996
10 015 005
10 016 656
10 014 999
10 016 654
10 016 655
10 015 005
10 017 688
10 017 691
Parts marked by an asterisk * to be kept in srtock for maintenance
Material - key:
St
FSt
NSt
... steel
... spring steel
... stainless steel
NFSt
LM
Ms
... stainless spring steel
... light metal
... brass
KG
... rubber-like plastic
material

5.3 Spare Part List RMG 610 (RS 10d)
pos.
no.
80
81*
82
83*
84*
85*
86
87
88
89*
90
91
92
93*
94
95*
96*
97
98
99
100
610.20 p. 13
joint, premounted
sealing cone, 1st stage
piston guide
orifice
sealing ring
sealing ring
cap nut
compression ring
nozzle
sealing ring
intermediary piece
cap nut
spindle
o-ring
conduction screw
o-ring
safety disc
cap
cylinder screw
disc
bolt
Ms/NSt
KG
Ms
Ms
LM
LM
St
St
St
LM
Ms
St
Ms
KG
Ms
KG
St
K
St
St
St
description material order no.
10 014 452
10 014 473
10 014 470
10 014 462
00 018 811
00 018 815
00 030 803
00 030 903
00 030 110
00 018 689
10 017 640
00 030 802
10 024 343
00 021 133
10 024 344
00 020 382
00 019 193
00 026 414
00 010 596
00 008 279
10 020 042
Parts marked by an asterisk * to be kept in stock for maintenance
Material - key:
St
FSt
NSt
... steel
... spring steel
... stainless steel
NFSt
LM
Ms
... stainless spring steel
... light metal
... brass
KG
K
... rubber-like plastic material
... plastic material
Table of contents
Other RMG Controllers manuals
Popular Controllers manuals by other brands
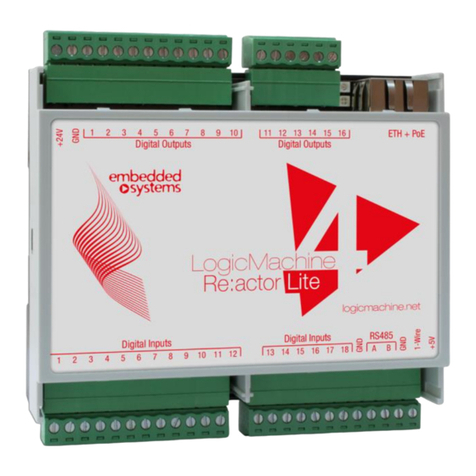
Embedded Systems
Embedded Systems LogicMachine Reactor Lite quick start guide
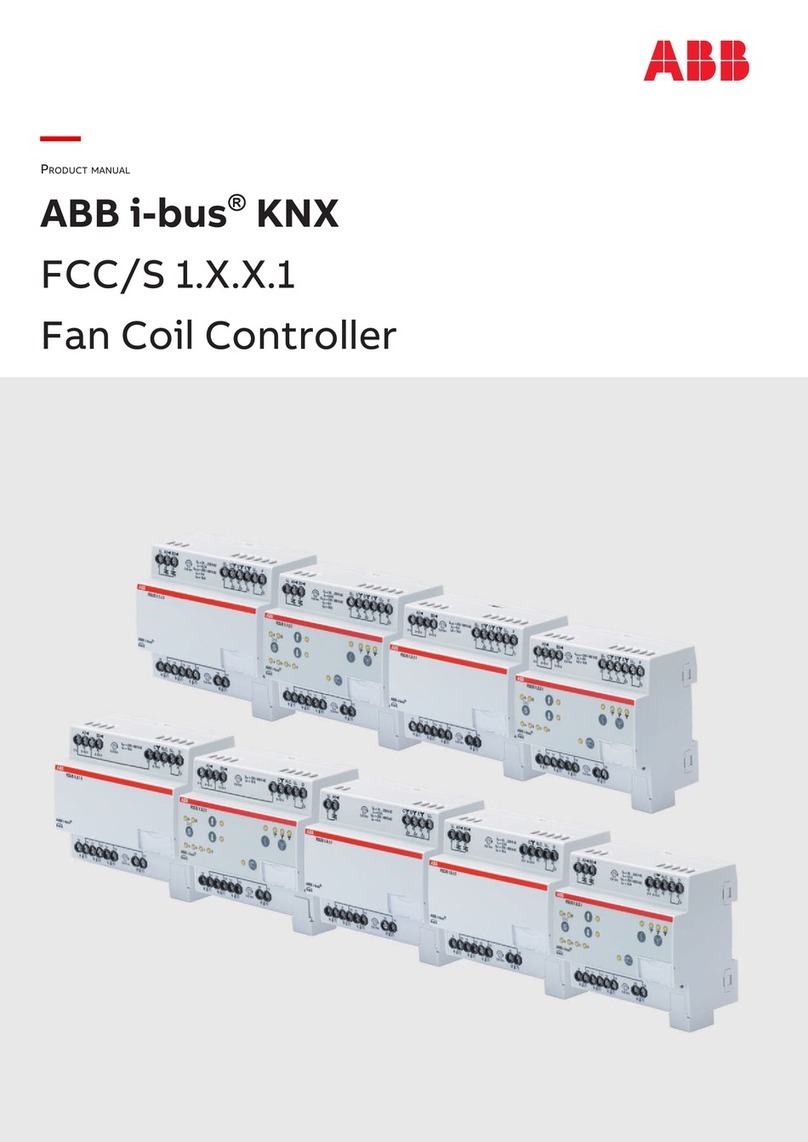
ABB
ABB i-bus FCC/S 1 1 Series product manual

nilan
nilan Compact P Polar EK 6 kW CTS 700 user guide
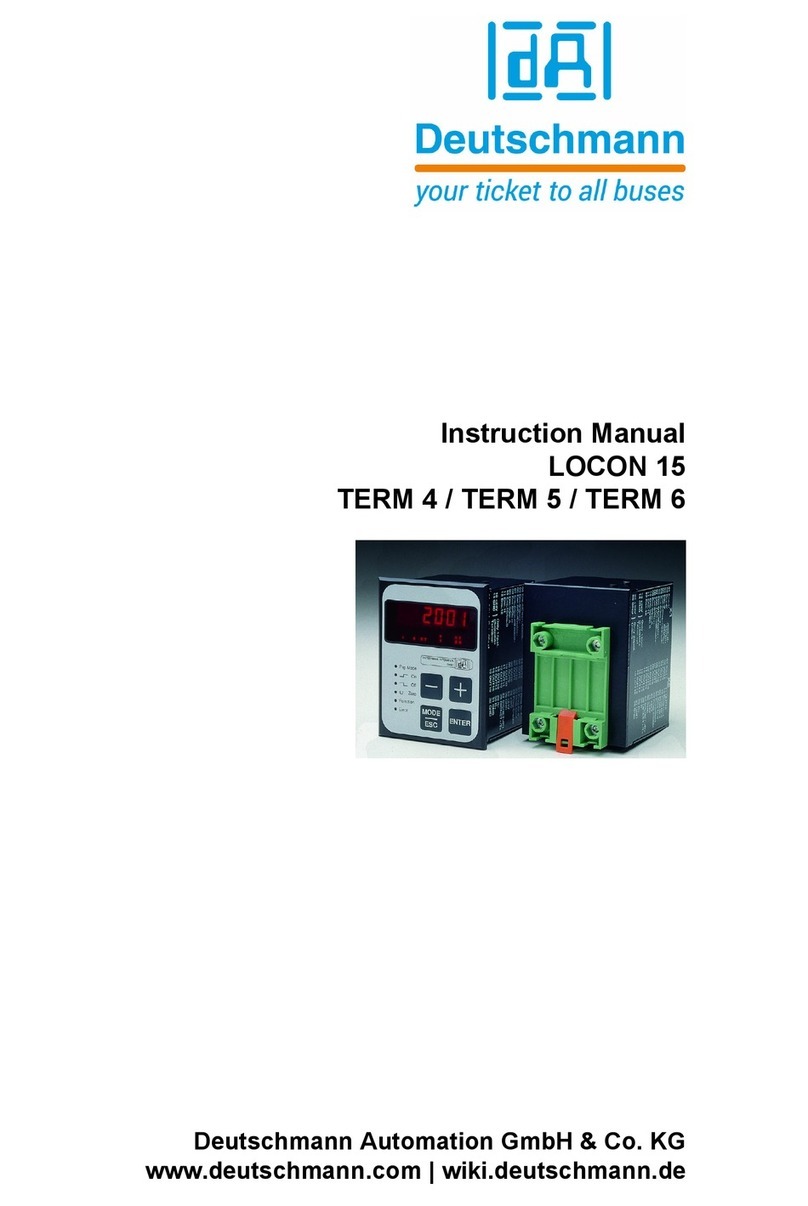
DEUTSCHMANN AUTOMATION
DEUTSCHMANN AUTOMATION LOCON 15 Series instruction manual
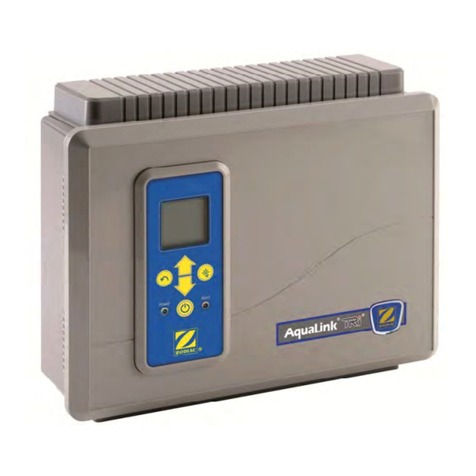
Zodiac
Zodiac AquaLink TRi installation manual
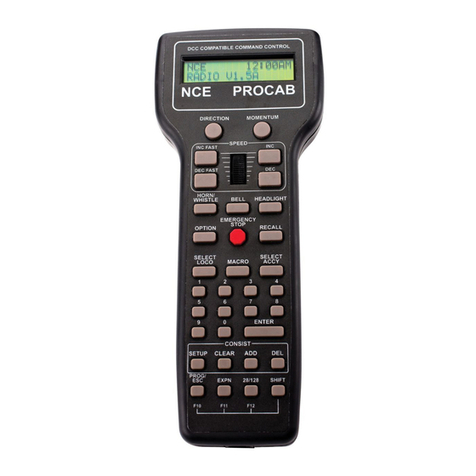
NCE
NCE Power Pro System reference manual