RMT DX5100 User manual

RMT Ltd.
Thermoelectric Cooler
Controller
DX5100
TECHNICAL MANUAL
RMT Ltd.
Moscow, 2014
Version 3.36

TEC Controller DX5100 Technical Manual RMT Ltd.
Page 2 / 56 Version 3.36 / 2014
WARRANTY
The company RMT Ltd. (further RMT) warranties the product DX5100 to be free from defects in material
and workmanship for a period of 1 year from date of shipment.
RMT also provides a 3-month warranty for the following parts and components included in the standard
delivery set of the product: the cables, program disks and documentation.
If the DX5100 fails during the warranty period for the reasons covered by this warranty, RMT will repair
or replace it or its parts.
For the warranty support a Consumer can address to the office of the company RMT or its sales
representative.
The product either repaired or replaced in whole or in part, will keep the warranty period from its start but
not less than 3 months.
TECHNICAL SUPPORT
For the technical support and repair within and after the warranty period, please, address to the office of
the company RMT or its sales representative:
In Russia and CIS
RMT Ltd
46 Warshavskoe shosse, Moscow 115230, Russia
Tel: +7-499-678-2082;
Fax: +7-499-678-2083
In Europe, the USA and other countries
TEC Microsystems GmbH
Schwarzschildstrasse 3, Berlin 12489, Germany
Phone: +49-(0)30-6789-3314
Fax: +49-(0)30-6789-3315
e-mail: info@tec-microsystems.com

RMT Ltd. TEC Controller DX5100 Technical Manual
Version 3.36 / 2014 Page 3 / 56
CONTENTS
1. INTRODUCTION.....................................................................................................................................5
1.1. Objective...........................................................................................................................................5
1.2. Features ...........................................................................................................................................5
2. TECHNICAL DATA.................................................................................................................................6
2.1. Specifications ...................................................................................................................................6
2.1.1. Performance 6
2.1.2. Common 6
2.1.3. Accuracy 7
3. DESCRIPTION........................................................................................................................................8
3.1. Basic Modules ..................................................................................................................................8
3.2. OEM Solutions..................................................................................................................................8
3.3. Digital Control Board DX5101 ..........................................................................................................9
3.3.1. Functional Scheme 10
3.3.2. Outlines 11
3.3.3. Connectors 11
3.3.4. Connections of thermistor 12
3.4. Power Board DX5102.....................................................................................................................13
3.4.1. Functional Scheme 14
3.4.2. Outlines 14
3.4.3. Connectors 15
3.4.4. Connections of TEC 15
3.5. Double-Channel Power Board DX5105..........................................................................................16
3.5.1. Functional Scheme 17
3.5.2. Outlines 18
3.5.3. Connectors 18
3.5.4. Connections of TEC 19
3.6. Power Board DX5109 (powerful)....................................................................................................19
3.6.1. Functional Scheme 20
3.6.2. Outlines 20
3.6.3. Connectors 21
3.6.4. Connections of TEC 22
3.7. Indication Board DX5103 ...............................................................................................................22
3.7.1. Functional Scheme 23
3.7.2. Outlines 23
3.7.3. Connectors 23
3.8. Interface Converter DX5106...........................................................................................................24
3.8.1. Functional Scheme 24
3.8.2. Outlines 25
3.8.3. Connectors 25
3.8.4. Drivers 25
3.9. Digital Input-Output Board DX5107................................................................................................27
3.9.1. Functional Scheme 27
3.9.2. Outlines 28
3.9.3. Connectors 28
3.9.4. Connections of Digital Input 29
3.10. TEC Controller OEM Models..........................................................................................................31
3.10.1. Module OEM 1 31
3.10.2. Module OEM 2 32
3.10.3. Module OEM 3 34

TEC Controller DX5100 Technical Manual RMT Ltd.
Page 4 / 56 Version 3.36 / 2014
3.10.4. Module OEM 4 36
3.10.5. Module OEM 5 37
3.10.6. Connecting optional boards (DX5103, DX5106, DX5107) 39
3.11. Network Configuration................................................................................................................... 40
3.12. Software......................................................................................................................................... 42
3.13. Operation Modes ........................................................................................................................... 42
3.13.1. Constant Temperature 42
3.13.2. Constant Voltage 43
3.13.3. Mode «Program» 43
3.13.4. T-Regulation (relay) 44
4. HOW TO GET STARTED .................................................................................................................... 47
4.1. Connections................................................................................................................................... 47
4.2. Presets........................................................................................................................................... 47
4.3. Diagnostics Function ..................................................................................................................... 48
4.4. Auto-PID Function ......................................................................................................................... 48
4.5. Working with RS232 and RS485................................................................................................... 49
4.6. Light Indication............................................................................................................................... 50
4.7. Working with Indication Board DX5103......................................................................................... 51
4.8. Storage and Recovery of Parameters ........................................................................................... 53
APPENDICES............................................................................................................................................. 55
4.9. Cables............................................................................................................................................ 55

RMT Ltd. TEC Controller DX5100 Technical Manual
Version 3.36 / 2014 Page 5 / 56
1. INTRODUCTION
1.1. Objective
Thermoelectric Controller DX5100 (further the Controller)
represents a precision-programmed device of management of
thermoelectric coolers (TECs, the Peltier modules).
In the device a bi-directional (heating and cooling) PID
regulation is realized.
Besides the PID regulation some additional modes of operation
are realized in the Controller: the DC voltage mode, T-regulation
and programming of an object temperature behavior with time.
The device allows maintaining a given temperature of a
thermoelectric (TE) cooler with high accuracy or programming
heating and cooling in time.
The function of diagnostics of an object of regulation - a TE cooler (TEC) is realized in the device. The
diagnostics includes the measurement of the TEC resistance at alternating current, of TE figure-of-merit and
of time constant. The function of the auto-tuning of the PID parameters is also implemented.
The device is based on a modular principle. By this principle the Controller is divided functionally and
physically into the control board and the Power Board in two variants: single-channel and two-channel, as
well as peripheral and additional modules - the indication board and the interface board.
The modular concept allows assembling the offered modules of the Controller configuration from one-
and two-channel into a network design of many channels (32) of regulation joint by the control protocol
RS485.
Every channel has an independent algorithm of work.
1.2. Features
-Bi-directional temperature regulation (heating and cooling) of a TEC with high accuracy
-Work with RTD sensor and thermistors of both NTC and PTC types
-One or two TECs controlled by one Controlling Board
-Power channels of two versions: high-power 4Aх8Vand low-power 3Aх5V
-TEC operation current and voltage range as ±4A и ±8V per channel.
-PID temperature regulation mode
-Constant voltage operation mode
-T-Regulation (relay) mode
-Mode of temperature programming in time
-Diagnostics of TEC performance by the Z-metering approach
-PID auto-tuning function
-Independent work without computer, based on preset and programmed start.
-Communication interfaces RS232 and RS485
-Network of up to 32 Channels is available jointed by RS485 bus
-Software for RS232 and RS485 protocols
-Protocol WAKE for user software programming (library provided).

TEC Controller DX5100 Technical Manual RMT Ltd.
Page 6 / 56 Version 3.36 / 2014
2. TECHNICAL DATA
2.1. Specifications
2.1.1. Performance
Name
Units
Value
Comments
Maximal Parameters, single-channel Power Board DX5102
Maximal current
A
4
Per channel
Maximal voltage
V
8
Maximal power
W
32
Maximal Parameters, double-channel Power Board DX5105
Maximal current
A
3
Per channel
Maximal voltage
V
5
Maximal power
W
15
Regulation channels number
2
with one DX5101
Maximal Parameters, single-channel Power Board DX5109 (powerful)
Maximal current
A
12
Per channel
Maximal voltage
V
8
Maximal power
W
96
Parameters of TEC voltage Regulation
Voltage Range
V
-8…+8
Accuracy of voltage regulation
mV
1
Resolution of voltage setting
mV
0.13
Resolution of measurement
V
6
Output ripple, not more
V
10
Efficiency of converters
%
85
Temperature Regulation
4-wire sensing
Yes
Setpoint range
°C
-70…150
Typical values. Depend
on thermistors type
Resolution
°C
0.001
Stability
°C
0.005
Accuracy
°C
0.5
Types of thermosensors
Platinum thermistor
Pt
Known T=f(R)
Other types of thermistors
NTC, PTC
Resistance range
Ohm
70…996K
Mode «Program»
Programs number, max
16
0..15
Program steps number, max
50
0..49
Steps number in a process
800
Programs in series
Program step duration, max
s
65 535
Time interval accuracy
s
1
Different operational modes when
temperature programming in time
Yes
Programs cascading
Yes
The given data are true for the ambient temperature 23±5°C and humidity 45±15%
2.1.2. Common
Name
Units
Value
Comments
Operation Modes
PID
Yes
TEC bi-directional
(heating and cooling)
Constant voltage
Yes
Temperature Program
Yes
Т-regulation (relay)
Yes
Possibility of Operation Modes Of
Regulation after Restarting
Yes
Remote control

RMT Ltd. TEC Controller DX5100 Technical Manual
Version 3.36 / 2014 Page 7 / 56
Communication Protocols
RS232, RS485
5 exchange rates
Programming
WAKE
BIN & SYM
Maximal number of channels in network
32 (128)
Combined by RS485
Programmable thresholds
Temperatures
2
Every Channel
Max voltage
1
Idle running power consumed, no more than
Single-Channel controller 4Aх8V
W
0.75
Double-Channel controller 4Aх8V
W
1.0
Double-Channel controller 3Aх5V
W
0.50
Operational temperatures range
°C
0…+45
Storage temperatures range
°C
-20…+60
Humidity
%
5…95%
Dimensions
Digital Board
mm3
55х55х6
DX5101
Single-Channel Power Board
mm3
55х55х10
DX5102
Double-Channel Power Board
mm3
55х55х10
DX5105
Indication Board
mm3
55х55х6
DX5103
Interface Converter USB-RS485
mm3
55х55х6
DX5106
Digital Input-Output Board
mm3
55х55х10
DX5107
Single-Channel Power Board DX5109
(powerful)
mm3
55х55х30
DX5109
2.1.3. Accuracy
The choice (from two possible values) of the thermistor measuring current is stipulated.
Thermistor current: 84 A or 1 A.
84 А
(resistance max 11,900 Ohm)
1 А
(resistance max 996,000
Ohm)
Rmax, no
more
(Ohm)
Resolution
(Ohm)
Rmax, no
more
(Ohm)
Resolution
(Ohm)
11896
1.75E-02
996000
1.46E+00
11896
1.00E-02
996000
8.40E-01
7435
5.38E-03
622500
4.50E-01
3718
3.08E-03
311250
2.58E-01
1859
2.03E-03
155625
1.70E-01
929
1.34E-03
77813
1.13E-01
465
8.86E-04
38906
7.42E-02
232
8.86E-04
19453
7.42E-02
Temperature resolutions for typical thermistors are given in the table below.
Units
Examples Pt
Examples NTC (for curve Y)
Pt100
Pt1000
NTC2200
NTC10000
Resistance
Ohm
100
1000
2200
10000
Temperature
range
K
203…423
203…423
218…333
218…333
Rmax
Ohm
150
1500
120516
547800
Thermistor
current
A
84
84
1
1
Resolution
Ohm
8.86E-04
2.03E-03
1.70E-01
4.50E-01
°C
2.30E-03
5.28E-04
1.19E-03
6.93E-04
for -55°C
1.99E-03
1.15E-03
for 25°C
2.42E-03
1.41E-03
for 65°C
Control accuracy
°C
0.01
0.005
0.005
0.005

TEC Controller DX5100 Technical Manual RMT Ltd.
Page 8 / 56 Version 3.36 / 2014
3. DESCRIPTION
The Controller is developed on a modular concept for flexible designing a complex control system of
TECs for various tasks.
3.1. Basic Modules
The base set of modules consists of the following units:
-Digital Control Board DX5101
-Power Board DX5102
-Double-Channel Power Board DX5105
-Power Board DX5109 (powerful)
-Indication Board DX5103
-Interface Converter (USB-RS485-RS232) DX5106
-Digital Input-Output Board DX5107
3.2. OEM Solutions
Modular concept provides possibility to create different types of OEM TEC controllers by combining the
modules.
From single-, two-channel to multichannel OEM systems are available with DX5100 concept, as well as
different specifications and options for particular applications.
OEM включает:
Возможные опции:
DX5101
DX5102
DX5105
DX5109
DX5103
DX5106
DX5107
OEM1
1
1
v
v
v
OEM2
1
2
v
v
v
OEM3
1
1
v
v
v
OEM4
1
1
v
v
v
OEM5
1
2
v
v
v
For fastening the boards there are 4 holes (=2.7mm, on the corners of the each board). The distance
between the axes of mounting holes - 49.4mm.
Any of the OEM kits can be complemented by options:
-Indication Board DX5103
-Interface Converter (USB-RS485-RS232) DX5106
-Digital Input-Output Board DX5107
Examples of Order:
OEM2 + DX5103 + DX5106
OEM3 + DX5103 + DX5106 + DX5107
DX5106
Important: In the OEM kits include cables, depending on the configuration. Drawings
cables (default) given in the appendix. If necessary, change the length of the cables, or their
structure (eg a connector at the free ends of the cable) - agree on proposed changes to the
RMT.

RMT Ltd. TEC Controller DX5100 Technical Manual
Version 3.36 / 2014 Page 9 / 56
3.3. Digital Control Board DX5101
The Digital Control Board is the head part of the Controller. The microcontroller is placed on it.
The Digital Control Board provides:
-TEC temperature control
-Temperature measurement
-Handling of Power Boards
-Communication with Indication Board control
-Test current for the diagnostics
-Communication with computer
-Programs and presets storage
-LED indication
For external commutations there are connectors located on two sides of the board.
For fastening the board there are 4 holes (dia=2.7mm, on the corners of the board).

TEC Controller DX5100 Technical Manual RMT Ltd.
Page 10 / 56 Version 3.36 / 2014
3.3.1.Functional Scheme
XP10 XP7
Driver
RS-232
Driver
RS-485
XP6
DAC
DC/DC 2 DC/DC 1
Programmer
XP9
Current ADC
XP5 XP2
U
I
XP3
Iforce12
Iforce22
Iforce11
Iforce21
DX5101
RS485
RS232
ITEC1 MEAS
UTEC1 SET
UTEC1 ON/OFF
I Zmetr
Present1
UTEC1 POLARITY
UTEC1 MEAS
ITEC2 MEAS
UTEC2 SET
UTEC2 ON/OFF
Present2
UTEC2 POLARITY
UTEC2 MEAS
Bus I2C
TTEC1
Sel_I_force1
Sel_I_force2
UPWR
TTEC2
Sel_I_force1
UPWR2 MEAS
UPWR1 MEAS
UPWR2 MEAS
I Zmetr
TTEC2
XP4
XP8
I2CPRG
EEPROM
TEC1TEC2
J1 XP1
Multiplexer
DIGITAL INPUT / OUTPUT

RMT Ltd. TEC Controller DX5100 Technical Manual
Version 3.36 / 2014 Page 11 / 56
3.3.2.Outlines
3.3.3. Connectors
General Description
Connector
Type
Connection
XP2
SM11B-SRSS-TB
TEC1 Power Board
XP3
SM11B-SRSS-TB
TEC2 Power Board
XP4
SM04B-SRSS-TB
TEC1 thermistor
XP5
SM04B-SRSS-TB
TEC2 thermistor
XP6
SM04B-SRSS-TB
I2C Bus
XP7
SM02B-SRSS-TB
RS-485
XP8
SM02B-SRSS-TB
RS-485
XP9
SM03B-SRSS-TB
Programmer jumper
XP10
SM03B-SRSS-TB
RS-232
Connectors XP2 (TEC1) and XP3 (ТЕС2) to the Power Board
Pin
Description
1
Voltage setting signal
2
Output voltage On/Off
3
TEC current
4
TEC polarity
5
TEC polarity
6
TEC «+» voltage measurement
7
TEC «-» voltage measurement
8
Z-meter current
9
Converter availability detector
10
Common
11
Supply voltage
Connectors XP4 (TEC1) and XP5 (ТЕС2) to thermistors
Pin
Description
1
+I force
2
+U sense
3
-U sense
4
-I force
Connector XP6 I2C Bus

TEC Controller DX5100 Technical Manual RMT Ltd.
Page 12 / 56 Version 3.36 / 2014
Pin
Description
1
+5 V
2
General
3
Signal SDA of bus I2C
4
Signal SCL of bus I2C
Connector XP7, XP8 - RS-485 interface
Pin
Description
1
Signal A of the interface RS-485
2
Signal B of the interface RS-485
Connector XP9 to programmer
Pin
Description
1
Programming signal
2
Microcontroller reset signal
3
Common
Connector XP10 - RS-232 Interface
Pin
Description
1
Signal TxD of interface RS-232
2
Signal RxD of interface RS-232
3
Common
3.3.4. Connections of thermistor
Due to the limitations of the 2-wire method, the 4-wire connection method shown in figure is
recommended for sensors <1kOhm.
Vm
I
Rw
T
Rw
UT
F+
F-
UIN
Vm
ITUT
F+
F-
UIN
S+
S-
Rw
Rw
Rw
Rw
4-Wire Connections
2-Wire Connections
With this configuration, the test current (I) is forced through the thermistor through the F+ and F- wires,
while the voltage across the thermistor is measured through a second set of wires connected to the S+ and
S- (sense) terminals. Although some small current may flow through the sense wires, it is usually negligible
and can generally be ignored for all practical purposes. Since the voltage drop across the sense wires is
negligible, the voltage measured by controller is essentially the same as the voltage across the thermistor
(VM= VT), and more accurate resistance and temperature measurements result from the following resistance
calculation:

RMT Ltd. TEC Controller DX5100 Technical Manual
Version 3.36 / 2014 Page 13 / 56
I
U
RT
T
The wires to thermistor should be twisted for reduction of pickups (separate for pair force –contacts 1, 4
and sense wires –contacts 2, 3).
1
2
3
4
T
From
contacts
1 and 2
From
contacts
3 and 4
1
2
3
4
T
From
contacts
1 and 2
From
contacts
3 and 4
4-Wire Connections
2-Wire Connections
XP4 or XP5
XP4 or XP5
In Digital Control Board DX5101 there is an opportunity to choose one of two possible values test
current (Iforce1 or Iforce2).
3.4. Power Board DX5102
The Power Board operates under the control of the Digital Control Board and provides:
-Voltage output to the object of regulation
-Voltage polarity control
-Protection of converter microcircuit from overheating and from limiting current excess
For external commutations there are connectors located on two sides of the board.
The board is attached to the heatsink, which has threaded holes for mounting the module to an external
heatsink (heat removal surface).
Attention! It is not allowed to remove heatsink.
Always put thermoconductive pad (enclosed) between heatsinks when placing on external
heatsink. Remove protection layer from the pad before installation.
External heatsinking is required for proper operation. Lack of proper heat dissipation may
result in considerably reduced operation temperature range and device failure.

TEC Controller DX5100 Technical Manual RMT Ltd.
Page 14 / 56 Version 3.36 / 2014
3.4.1. Functional Scheme
XP2 or XP3
DC/DC
XP1XP4XP5
DX5102
ITEC1 MEAS
UTEC1 SET
UTEC1 ON/OFF
I Zmetr
Present1
UPWR MEAS
UTEC1 POLARITY
UTEC1 MEAS
Uin=12V
J1 J2
3.4.2. Outlines

RMT Ltd. TEC Controller DX5100 Technical Manual
Version 3.36 / 2014 Page 15 / 56
3.4.3. Connectors
General description
Connector
Type
Connection
XP1
S4B-EH
Power supply
XP2, XP3
SM11B-SRSS-TB
Digital Control Board
XP4
S4B-EH
Thermoelectric cooler (ТЕС)
XP5
SM02B-SRSS-TB
Thermoelectric cooler (ТЕС)
Connector XP1- power supply
№
Description
1
+12 V
2
+12 V
3
0 V (common)
4
0 V (common)
Connectors XP2, XP3 to Digital Control Board
The connectors are in parallel (either should be used).
№
Description
1
Voltage setting
2
Output voltage On/Off
3
TEC current measurement signal
4
TEC polarity control
5
TEC polarity control
6
TEC «+» voltage measurement
7
TEC «-» voltage measurement
8
Diagnostics current
9
Converter availability detector
10
Common
11
Supply voltage
Connector XP4 to TEC
№
Description
1
+Utec (ТЕС is switched to cool)
2
3
-Utec (ТЕС is switched to cool)
4
Connector XP5 to TEC
№
Description
1
+Utec sense (measure)
2
-Utec sense (measure)
3.4.4. Connections of TEC
If it is not necessary to use a four-wire circuit of TEC voltage measurement, it is possible to connect the
jumpers J1 and J2 on the board close to the connector XP5. Connecting jumpers is done on Customer's
demand.

TEC Controller DX5100 Technical Manual RMT Ltd.
Page 16 / 56 Version 3.36 / 2014
1
2
3
4
4-Wire Connections
2-Wire Connections (jumpers J1 and J2 must be on the board)
XP4
1
2
XP5
TEC
From contact 1
+
1
2
3
4+
XP4
TEC
3.5. Double-Channel Power Board DX5105
The Power Board operates under the control of the Digital Control Board and provides:
-Two voltages output to object of regulation
-Voltage polarity control
-Protection of the converter microcircuits from overheating and from the excess of the limiting current
For external commutations there are connectors located on two sides of the board.
The board is attached to the heatsink, which has threaded holes for mounting the module to an external
heatsink (heat removal surface).
Attention! It is not allowed to remove heatsink.
Always put thermoconductive pad (enclosed) between heatsinks when placing on external
heatsink. Remove protection layer from the pad before installation.
External heatsinking is required for proper operation. Lack of proper heat dissipation may
result in considerably reduced operation temperature range and device failure.

RMT Ltd. TEC Controller DX5100 Technical Manual
Version 3.36 / 2014 Page 17 / 56
3.5.1.Functional Scheme
XP1
DC/DC
XP7XP2XP3
ITEC1 MEAS
UTEC1 SET
UTEC1 ON/OFF
I Zmetr
Present1
UPWR MEAS
UTEC1 POLARITY
UTEC1 MEAS
Uin=12V
XP4
DC/DC
XP5XP6
DX5105
ITEC2 MEAS
UTEC2 SET
UTEC2 ON/OFF
I Zmetr
Present2
UPWR MEAS
UTEC2 POLARITY
UTEC2 MEAS
Uin=12V
J1 J2
J3 J4

TEC Controller DX5100 Technical Manual RMT Ltd.
Page 18 / 56 Version 3.36 / 2014
3.5.2.Outlines
3.5.3.Connectors
General Description
Connector
Type
Connection
XP1
SM11B-SRSS-TB
Digital Control Board
XP2
S2B-EH
Thermoelectric cooler ТЕС1
XP3
SM02B-SRSS-TB
Thermoelectric cooler ТЕС1
XP4
SM11B-SRSS-TB
Digital Control Board
XP5
S2B-EH
Thermoelectric cooler ТЕС2
XP6
SM02B-SRSS-TB
Thermoelectric cooler ТЕС2
XP7
S4B-EH
Supply
Connectors XP1 (ТЕС1) and XP4 (ТЕС2) – to Digital Control Board
Pin
Description
1
Voltage setting
2
Output voltage On/Off
3
TEC current measurement signal
4
TEC polarity control
5
TEC polarity control
6
TEC «+» voltage measurement
7
TEC «-» voltage measurement
8
Diagnostics current
9
Converter availability detector
10
Common
11
Supply voltage
Connector XP2 (ТЕС1) and XP5 (ТЕС2) – to TECs
Pin
Signal description
1
+Utec (TEC is switched to cool)
2
-Utec (TEC is switched to cool)
Connector XP3 (ТЕС1) and XP6 (ТЕС2) – to TECs
№
Description
1
+Utec sense (measure)
2
-Utec sense (measure)
Connector XP7 –power supply
Pin
Description

RMT Ltd. TEC Controller DX5100 Technical Manual
Version 3.36 / 2014 Page 19 / 56
Pin
Description
1
+12 V
2
+12 V
3
0 V (common)
4
0 V (common)
3.5.4. Connections of TEC
TEC connection in the four-wire circuit of voltage measurement is carried out according to the figure
below:
1
2
4-Wire Connections
2-Wire Connections
jumpers J1 and J2 (J3 and J4) must be on the board
XP2 (XP5)
1
2
XP3 (XP6)
TEC1
(TEC2)
From contact 1
+
1
2
XP2 (XP5)
TEC1
(TEC2)
+
If it is not necessary to use a four-wire circuit of TEC voltage measurement, it is possible to connect the
jumpers J1 and J2 on the board close to the connector XP3 (UTEC1) and (or) the jumpers J3 and J4 on the
board close to the connector XP6 (UTEC2). Connecting jumpers is done on Customer's demand.
3.6. Power Board DX5109 (powerful)
The Power Board operates under the control of the Digital Control Board and provides:
-Voltage output to the object of regulation
-Voltage polarity control
-Protection of converter microcircuit from overheating and from limiting current excess
For external commutations there are connectors located on two sides of the board.
For fastening the board there are 4 holes (dia=2.7mm, on the corners of the board).
The board includes a heatsink, fan cooled.

TEC Controller DX5100 Technical Manual RMT Ltd.
Page 20 / 56 Version 3.36 / 2014
3.6.1. Functional Scheme
XP3 or XP4
DC/DC
XP1XP5XP6
DX5109
ITEC1 MEAS
UTEC1 SET
UTEC1 ON/OFF
I Zmetr
Present1
UPWR MEAS
UTEC1 POLARITY
UTEC1 MEAS
Uin=12V
J1 J2
3.6.2. Outlines
Table of contents
Popular Controllers manuals by other brands
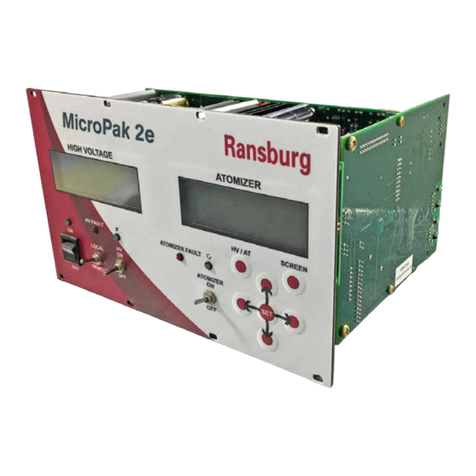
Carlisle
Carlisle Ransburg MicroPak 2e Service manual
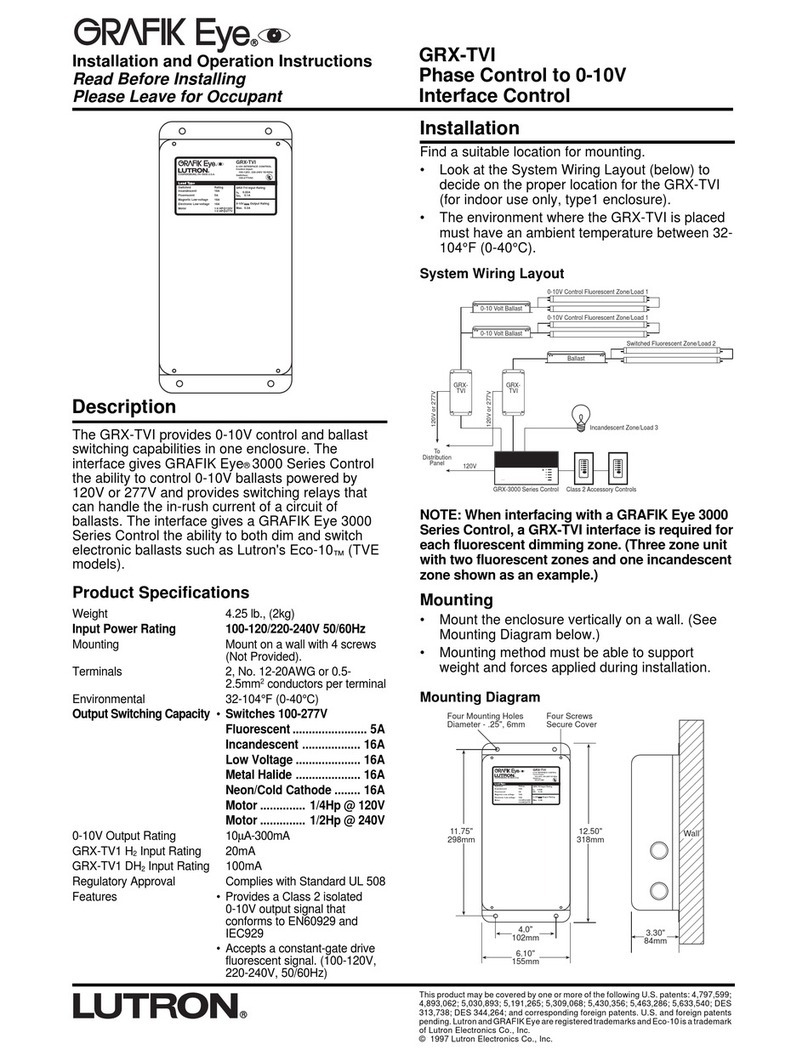
Lutron Electronics
Lutron Electronics Grafik Eye GRX-TVI Installation and operating instructions
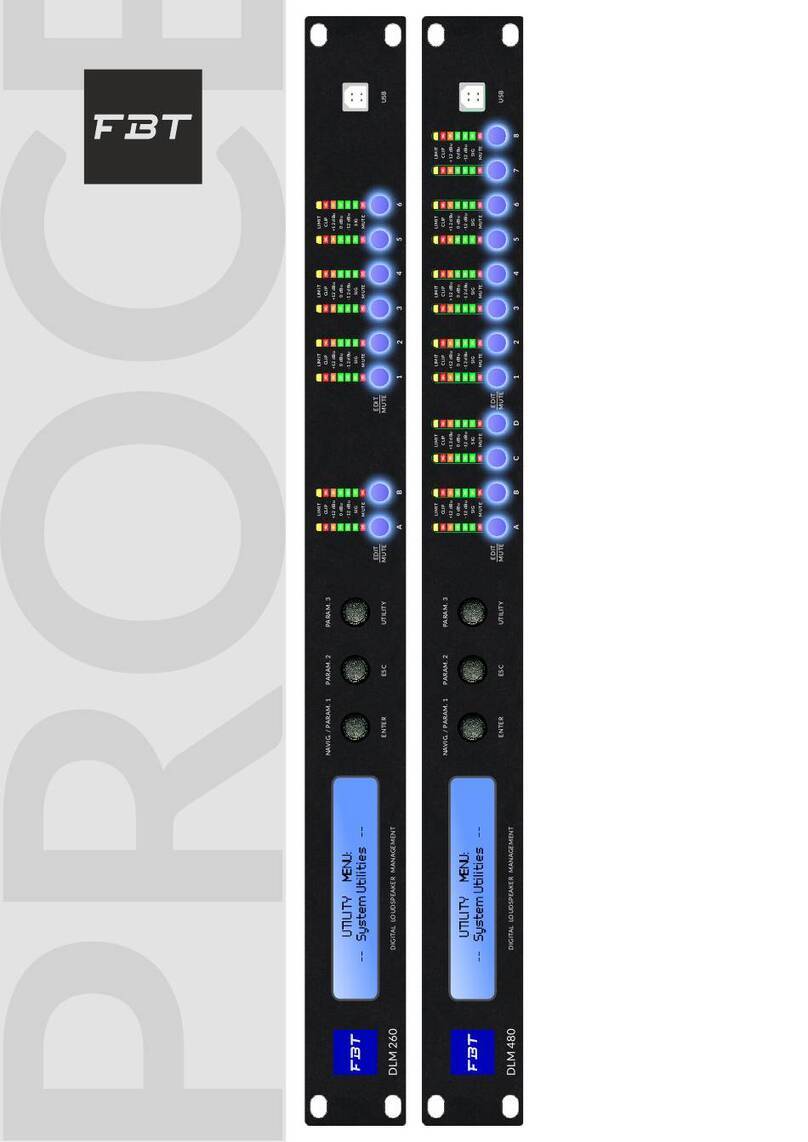
Fbt
Fbt DLM 260 operating manual
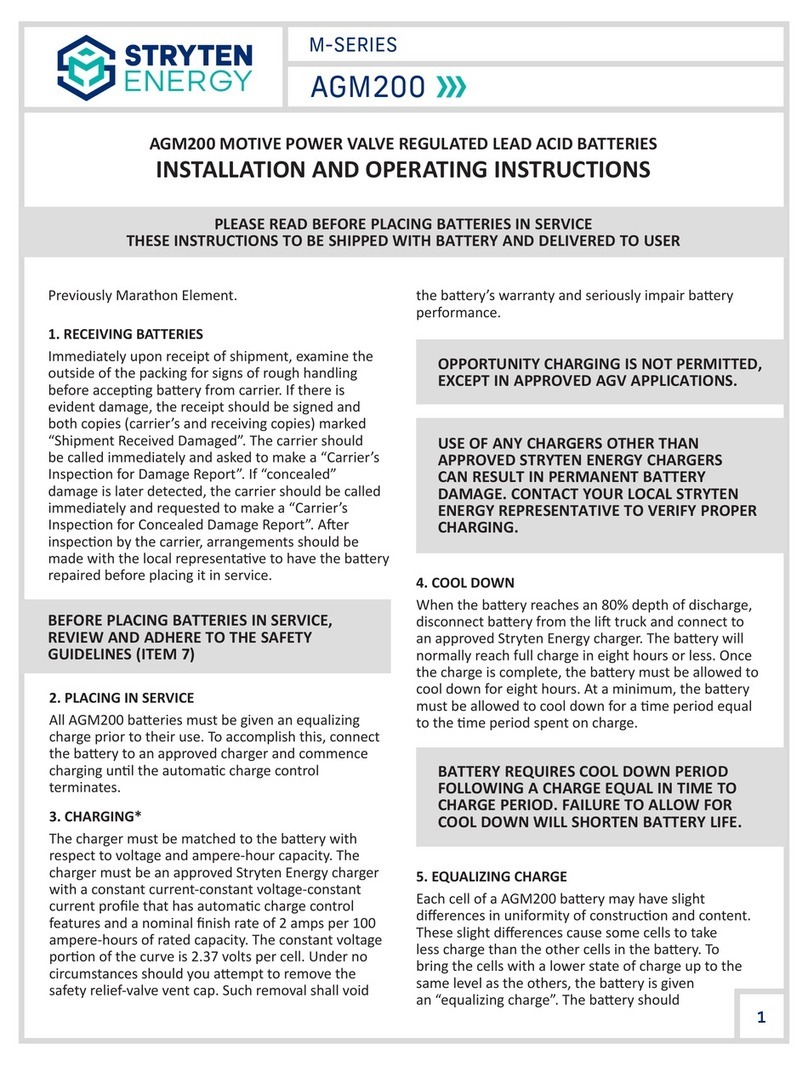
Stryten Energy
Stryten Energy M Series Installation and operating instructions
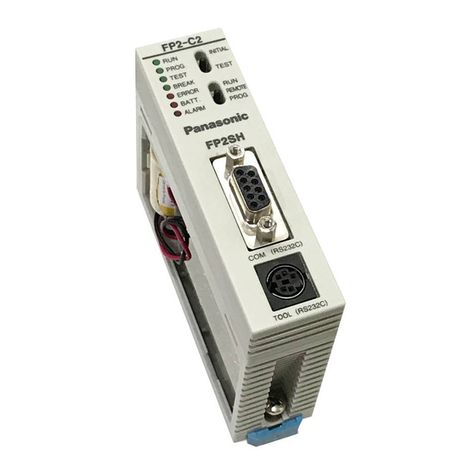
Panasonic
Panasonic FP-E Programming manual
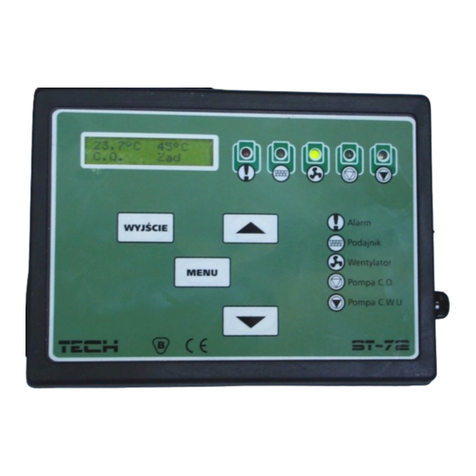
TECH
TECH ST-77 Manual guide