Roger PR611 User manual

Installation Guide
for
PR611 and PR621 v1.0
Access Controllers
Rev. B

PR611 and PR621 Installation guide Rev.B EN 2009-11-06
Page 2of 13
Introduction
This document contains minimum information that is necessary to properly install the device and to
perform its initial testing. Full description of the controller has been included in the general
user guide for the PRx11 series controllers, which is available at www.roger.pl.
The controller can be programmed manually or with a PC. Connecting the controller to the PC
requires utilization of the relevant communication interface (UT-2, UT-2USB, UT-4 or RUD-1)
however the RUD-1 is most suitable for this purpose because provides 12V DC output which can be
used to supply programmed device. Manual programming can be performed locally using the
device’s keypad (PR611 only) or using an additional, PRT series reader connected to the main
PR611/PR621 controller unit (the reader connected to programmed controller should be equipped
with a keypad and configured to “RACS mode address ID0”). Later, for device’s programming a so
called Programming Cards can be used. Programming Cards are standard proximity cards which
were assigned specific programming functions. Programming Cards can be defined during device’s
configuration process.
Note: The PR611/PR621 require the PR Master 4.3.1 or higher.
Controller Installation
The controller can be installed both inside and outside of buildings and does not require additional
protections against rainfalls (snowfalls) as well as humidity. All the electrical connections can be
done only when the power supply is disconnected. The new, factory-made controller, has the
address ID=00 and is equipped with the programmed MASTER card delivered with a new device. The
card can be used for the initial testing of the device after the installation.
All the devices connected to the AC system’s RS 485 communication bus should have the common
minus (GND). In order to ensure this, all the GND terminals of power supply units used in the
system should be connected together with the separate wire. The other solution is to individually
ground (connect to earth) each of GND terminals. However, the latter solution is not recommended,
because when grounding potentials in different locations of installation are not the same, the
equalizing current will flow through the system’s power supply lines. That in turn, can cause
disruption of system work or even its damage.
Readers can be installed on metal surfaces but in such cases the reading distance reduction should
be expected. The reading distance reduction effect can be minimized by installing readers on the
non-metal plate spacer. The thickness of such spacer should be at least 10 mm. The distance
between two proximity readers should not be less than 0.5m. In case the two readers are mounted
on opposite sides of the same wall it is recommended that they not create the same geometrical
axis. If this is not possible, a metal plate beneath each of the readers should be installed.
Additionally, between each reader and the plate the non metallic spacer of minimal 10 mm thickness
should be put.
The controller is equipped with 6 installation holes in bottom of the enclosure. The distance between
two of them placed horizontally is 60 mm, which make it possible to install the device in the
standard flush-mounted gang box.
Note: Under no circumstances the positive terminals of the power supply units in the system would
be connected together. The note applies also for the supply leads available in controllers with its
own power supply (e.g. PR411, PR402).
Address Setting
Before the controller is connected to the communication bus of the RACS, the unique address (ID
number) should be assigned to it. A new address setting can be performed during the Memory
Reset procedure or from the PC with managing program. In order to change the address from the
PC, the controller should be connected using the communication interface (UT-2, UT-2USB, UT-4 or
RUD-1) however the most preferred is RUD-1 which provides 12V CD output to supply the
programmed unit. Then the controller should be find using PR Master program, and finally its
destination address should be assigned. The RACS 4 supports addresses from the 00–99 range.

PR611 and PR621 Installation guide Rev.B EN 2009-11-06
Page 3of 13
Presence of two or more devices having the same address causes the communication bus conflict
and makes a proper communication with the device impossible.
Note: A new controller can be connected to the existing system without the necessity to change its
address, however only under condition that no controller existing in the system has the address
identical to the address of the newly connected device (e.g. 00). After the controller is connected to
the communication bus, it should be found in the management software and the destination address
should be assigned to it.
Power Supply
The controller requires 12V DC nominal power supply. The power should be connected to the +12V
line (positive terminal) and the GND (negative terminal). Apart from powering function, the GND
terminal plays also the role as reference potential for the RS485 bus’ communication lines, IN1-IN3
inputs and CLK/DTA interface lines.
Connecting Door Unlocking Device
In majority of cases, door unlocking devices have inductive characteristics. It means that turning off
the current flowing through the device may cause the electrical overvoltage condition which can
interfere with the controller operation. In extreme cases it may lead to the controller’s hanging up.
Moreover, the presence of overvoltages causes quicker attrition of the relay’s contacts. In order to
limit negative impact of overvoltages, it is necessary to utilize a semiconductor diode of general use
e.g. 1N4007 (one piece of such diode is delivered with the controller). It should be connected as
close as possible to the inductive element (electric strike or magnetic lock). The door lock device
element can be supplied from the same power source as the controller but for such purpose the
separate pair of wires should be used and connected directly to the power supply’s terminals.
Output Lines
All the controller’s inputs (IN1, IN2 i IN3) have identical electric structure and can be configured as
lines of NO or NC type. The NO input is triggered by applying supply minus to it, the NC input must
be normally shorted to the supply minus (GND) and is triggered by disconnecting it form the minus.
Every input is internally connected (pulled up) to the power supply plus (+12V) through a 5.6kΩ
resistor.
Relay Outputs
The relay output REL1 offers one switched contact rated 24V/1.5A. The relay’s contacts are
internally protected against overvoltages by semiconductor elements. However this does not take
the responsibility out of the installer to eliminate interferences from inductive elements by an
additional diode. It is forbidden to use relay output to switch voltages above 30V because this for
sure will cause damage to the semiconductor elements protecting the relay’s contacts. In the normal
state (the relay is off) the NC-COM contacts are shorted. In the triggering state (the relay is on) the
NO-COM contacts are shorted. In case of lack of the power, the REL1 output is in the off state.
Transistor Outputs

PR611 and PR621 Installation guide Rev.B EN 2009-11-06
Page 4of 13
There are two transistor outputs (IO1 and IO2) available in the controller. The lines are of the open
collector type, i.e. in the normal (off) state represent high impedance and in the triggering state
(the output is on) they short to supply minus. The IO1/IO2 lines can switch current up to max 1A
DC while voltage connected to the output must not exceed 15V DC. In case of over-current state,
the IO1/IO2 lines are automatically switched off and the controller automatically restarts.
Note: If you observe that triggering IO1/IO2 output makes device to restart it might suggest that
current switched by the output exceeds its maximum allowed level.
RS485 Communication Bus
The RS485 bus consists of two signal lines A and B. In the RACS 4 any communication bus topology
can be used (star, tree or any combination of the two), in other words RACS 4 accepts free bus
topology. The matching resistors (terminators) connected at the ends of transmitting lines are also
not required. In majority of cases communication works without any problems using any cable type
(ordinary telephone cable, shielded or unshielded twisted pair etc. e) but the recommended one is
an unshielded computer twisted pair one. Using shielded cables should be limited to installations
liable to strong electromagnetic interferences. RS485 communication standard used in the RACS 4
guarantees a proper communication in a distance up to 1200 meters and features a high resistance
to interferences. For communication on longer distances, the UT-3 or UT-4 interface should be used.
A pair of UT-3 interfaces increases communication distance by additional 1200 m, and using an UT-4
interface makes possible to utilize communication through a computer network (LAN or WAN).
Connecting Readers and Extension Modules
The controller can cooperate with one additional reader of PRT series configured to RACS mode with
ID0 address. It can also cooperate with XM-2 I/O extension module. Both an additional reader and
an extension module can be connected to the controller using the same CLK and DTA lines. For CLK
and DTA lines any type of cables can be used as well. The guaranteed communication distance is
150 meters. Each device connected to CLK/DTA lines must have its individual address from 0–15
range. This address should be set up before particular device is connected to the controller.
Note: Devices communicating using the RACS Clock & Data standard (e.g. PRT readers) can be
connected to the controller with cables significantly longer than 150m (even up to 500m), but the
communication in such conditions is not guaranteed by the vendor.
Memory Reset
The Memory Reset procedure clears all existing controller settings, restores factory ones, and
enables for enrolment of the new MASTER card/PIN and new ID number (address) of the controller.
After Memory Reset, the controller automatically switches to normal working mode.
Simplified Memory Reset Procedure (version 1)
This method clears entire memory and allows for programming of a MASTER card however doesn’t
allow for programming of the controller’s address (address is set to ID=00). This procedure doesn’t
require use of a keypad.
•Remove all connections from CLK and DTA lines
•Short CLK and DTA lines
•Restart device (switch power supply off and then on or short RST contacts for a while) – all
the LED indicators on the reader will be lit
•Remove the bridge between CLK and DTA lines — the LEDs on the reader will be off, and the
LED OPEN (green) will start flashing
•While the LED OPEN is flashing, read any card — this will be the new MASTER card
•The reader will restart automatically and return to normal mode of operation

PR611 and PR621 Installation guide Rev.B EN 2009-11-06
Page 5of 13
Simplified Memory Reset Procedure (version 2)
This method clears entire memory and allows for programming a MASTER card and allows to set ID
address. This procedure doesn’t require use of a keypad.
•Remove all connections from CLK and IN3 lines
•Short CLK and IN3 lines
•Restart device (switch power supply off and then on or short RST contacts for a while) – all
the LED indicators on the reader will be lit
•Remove the bridge between CLK and IN3 lines — the LEDs on the reader will be off, and then
the LED STATUS and LED OPEN (green) will start flashing
•While the LED OPEN is flashing, read any card — this will be the new MASTER card then
move to the next step where you will program controller’s ID number (address)
•Read MASTER card X times where X must be equal to the first digit of the required address
then wait for two short beeps
•Read MASTER card Y times where Y must be equal to the second digit of the required address
•The reader will restart automatically and return to normal mode of operation
Full Memory Reset Procedure
This procedure can be performed directly from the controller’s keypad (if the controller has it) or
from an additional PRT series reader connected to the controller through CLK and DTA lines. The
reader used for this should be configured to the RACS mode address ID0 and be equipped with a
keypad. Full Memory Reset procedure clears entire memory and allows for programming a MASTER
card and PIN as well as setting up a new address (ID number).
•Remove all connections from CLK and DTA lines.
•Short CLK and DTA lines.
•Restart device (switch power supply off and then on or short RST contacts for a while) – all
the LED indicators on the reader will be lit.
•Remove the bridge between CLK and DTA lines — the LEDs on the reader will be off, and the
LED OPEN (green) will start flashing.
•If the controller is equipped with keypad go to the next step if not then without switching the
power off connect an external PRT series reader to it. It should be configured to the RACS
mode address=ID0. The rest of the steps should be performed using this additional reader.
•Enter a new MASTER PIN code (3-6 digits) followed with the [#] key or skip this step
pressing the [#] key alone.
•Read any card — it will be a new MASTER card — or skip this step by pressing the [#] key.
•Enter two digits (from 00 to 99 range). These digits program a new ID address of the
controller. Eventually, instead of programming controller’s address can press the [#] key
alone. In the latter case, the controller will automatically assume address ID=00.
•After this action, the reader will restart automatically and return to normal working mode
(enters Armed mode).
After Memory Reset procedure, controller resumes its work with default configuration settings. You
can then initially test its operation using a MASTER ID card or PIN (if they were programmed). Using
the MASTER card or PIN once, activates a relay output REL1 for 4 seconds and LED OPEN in on
along with REL1. Using it twice switches the IO1 output to the opposite state, and changes a current
controller’s armed mode (LED STATUS changes its color).

PR611 and PR621 Installation guide Rev.B EN 2009-11-06
Page 6of 13
Firmware Upgrade
During manufacturing process controller is programmed with a latest available version of firmware.
The firmware can be later upgraded to newer versions. Detailed description of the firmware upgrade
procedure can be found in the Firmware upgrade.pdf manual available at www.roger.pl. Loading an
upgraded firmware to the controller is done using RS485 communication bus and does not require
dismounting the device from the place of installation. RogerISP is the software used for upgrading
firmware (it can be downloaded at www.roger.pl ). After the firmware is upgraded, always perform
the Memory Reset procedure and assign a proper ID address to the controller. If the controller
being upgraded worked in the RACS system before, you need to assign to it appropriate ID address
after the upgrade (the same which it was assigned before the upgrade). Then, you need to go to the
PR Master managing software, and run the command:
/Subsystems/Controllers/Commands/Restart, verify type and version – the operation will
update data related to the controller’s firmware version in the RACS system database.
Note: Together with the controller’s firmware upgrade, you need also to update the managing PR
Master software.

PR611 and PR621 Installation guide Rev.B EN 2009-11-06
Page 7of 13
Installation Notes
•Installer should install the device in such a way that, when needed, he has access to a
connecting cable (contacts) as well as to the reader programming contacts (pins RST and
FDM).
•Before the controller is installed, it is recommended to assign the destination address (ID
number) to it.
•Together with the controller a proximity MASTER card is delivered. Nevertheless, for the
MASTER card function any proximity card of the EM 125 KHz standard can be programmed
later.
•When the MASTER card or PIN is lost or stolen, it can be programmed from scratch.
•The reader should be mounted on the vertical piece of the wall, close to a door being
controlled.
•All the electrical connections should be done only when the power supply is disconnected.
•In case of installation on metal surfaces, it is recommended to put a non-metallic spacer
under the reader, which should be at least 10 millimeters thick.
•When it is necessary to install readers on opposite sides of the same wall and in the same
geometrical axis, a metal plate should be put between the readers, and the readers should be
installed on a non-metallic spacer 10 mm thick at a minimum.
•It is recommended that the reader be installed at a distance not lower than 0.5 m from the
other reader.
•All the devices communicating between themselves (readers, extension modules, controllers)
should have be connected to the same, common minus potential.
•Optionally, system supply minus can be earthed in one arbitrary selected location. Do not
connect system supply minus to the earth in more than one place.
•Because of relatively low magnetic field, the reader should not interfere with other devices’
operation, however its operation can be disrupted by devices generating a strong
electromagnetic field.
•In case when the range of card reading is significantly lower than specified in the technical
documentation, changing reader’s installation location should be considered.
•A silicone diode of general use e.g. 1N4007 should be always connected in parallel the door
locking device (magnetic lock, electric strike, relay, contactor) — one piece of such diode is
delivered with the controller. It should be connected as close as possible to the inductive
element.
•Door locking equipment should be powered using a separate pair of wire connected directly
to power supply output terminals.
•Powering door lock directly from reader’s supply contacts can cause pervading interference to
an electronic module and disrupt the device’s operation.

PR611 and PR621 Installation guide Rev.B EN 2009-11-06
Page 8of 13
Connections
Name Terminal
number
(for
products
equipped
with screw
terminals)
Wire Color
(for versions
equipped with pig
tail cable)
Purpose
+12V 1 Red Positive power supply contact, 10–15V DC
GND 2 Black Negative power supply contact and reference
potential for RS485 communication bus, inputs
and CLK/DTA interface
IN1 3 Pink IN1 input line, internally connected to the power
supply plus (+12V) through a 5.6kΩresistor
IN2 4 Blue IN2 input line, internally connected to the power
supply plus through a 5.6kΩresistor
IN3 5 White-yellow IN3 input line, internally connected to the power
supply plus through a 5.6kΩresistor
RS485-B 6 Green-white RS485 communication bus, B line
RS485-A 7 Brown RS485 communication bus, A line
CLK 8 White RACS Clock & Data communication interface,
CLOCK line
DTA 9 Green RACS Clock & Data communication interface,
DATA line
TMP-A 10 Yellow Anti-sabotage contact, line A, rated 24V/50mA
TMP-B 11 Grey Anti-sabotage contact, line B, rated 24V/50mA
IO2 12 Green-brown IO2 transistor output of open collector type, rated
15V DC/1.0A
IO1 13 Yellow-brown IO1 transistor output of open collector type, rated
15V DC/1.0A
REL1-NC 14 Grey-pink REL1 relay output, contact normally closed rated
24V/1.5A
REL1-COM 15 Red-blue REL1 relay output, common contact, rated
24V/1.5A
REL1-NO 16 Violet REL1 relay output, contact normally open rated
24V/1.5A

PR611 and PR621 Installation guide Rev.B EN 2009-11-06
Page 9of 13
Technical Data
Supply voltage 10-15 VDC
Current consumption PR611: average 70 mA
PR621: average 50 mA
Tamper Isolated contact, NC type, 50 mA/24V rated
Reading distance Up to 15 cm for ISO cards (depends on card type and quality)
Proximity cards EM 125 KHz (EM4100/4102 compatible)
Distances RS485 comm. bus: up to 1200m
Between an additional reader and the controller: max 150 m
Between a reader and XM-2/XM-8 expansion modules: max 150 m
Environmental class
(according to EN
50131-1)
Class IV, outdoor general conditions, temperature: –25°C- +60°C,
relative humidity: 10 to 95%
Dimensions PR611: 115 X 80 X 35 mm
PR621: 85 X 85 X 27 mm
Weight ~ 120g
Certificates CE

PR611 and PR621 Installation guide Rev.B EN 2009-11-06
Page 10 of 13
Ordering Information
PR611 PR611 controller, standard version, connection via pig tail cable
PR621 PR621 controller, standard version, connection via screw terminals
RM-2 Module consisting of two relay outputs rated 1.5A/24V each with one switched
contact NO/NC. Relay contacts are protected against overvoltages using metal-
oxide varistors (MOVs). Relays can be triggered by applying low as well as
high triggering signal. Triggering of relay is indicated by LED on the module’s
board.
RM-2 PCB RM-2 PCB module without enclosure
XM-2 Input/output addressable extension module provides two input lines NO/NC
and two relay outputs with one switched contact NO/NC rated 1.5A/24V. Relay
contacts are protected against overvoltages using metal-oxide varistors
(MOVs). Triggering of each relay is indicated by a LED installed on the
module’s board. Communication with parent device can be performed using
CLK/DTA lines. The module can be located in a distance of 150 m from the host
device (controller).
XM-2 PCB XM-2 PCB module without enclosure
UT-2 RS232-RS485 communication interface
UT-2USB USB-RS485 communication interface
RUD-1 USB-RS485 communication interface with 12V DC/150mA supply output
UT-4 Ethernet-RS485/RS232 communication interface
Contact
Roger sp. j.
82-416 Gościszewo
Gościszewo 59
Tel.: +48 55 272 01 32
Fax: +48 55 272 01 33
Technical support PSTN: +48 55 267 01 26
Technical support GSM +48 664 294 087
e-mail: [email protected]
Such symbol on the product or its package means that the
product should not be disposed together with other wastes,
because it may cause negative effects to environment and
humans health. User is responsible for delivering used equipment
to the allotted locations for gathering used electrical and
electronic devices. Detailed information on recycling can be found
at relevant local authorities, in a disposing company or in a place,
where the product was bought. Separate gathering and recycling
of such wastes contributes to natural resources protection and is
safe for humans health and for natural environment. The
equipment’s weight is shown in the guide.

PR611 and PR621 Installation guide Rev.B EN 2009-11-06
Page 11 of 13

PR611 and PR621 Installation guide Rev.B EN 2009-11-06
Page 12 of 13

PR611 and PR621 Installation guide Rev.B EN 2009-11-06
Page 13 of 13
Other manuals for PR611
1
This manual suits for next models
1
Table of contents
Other Roger Gateway manuals
Popular Gateway manuals by other brands
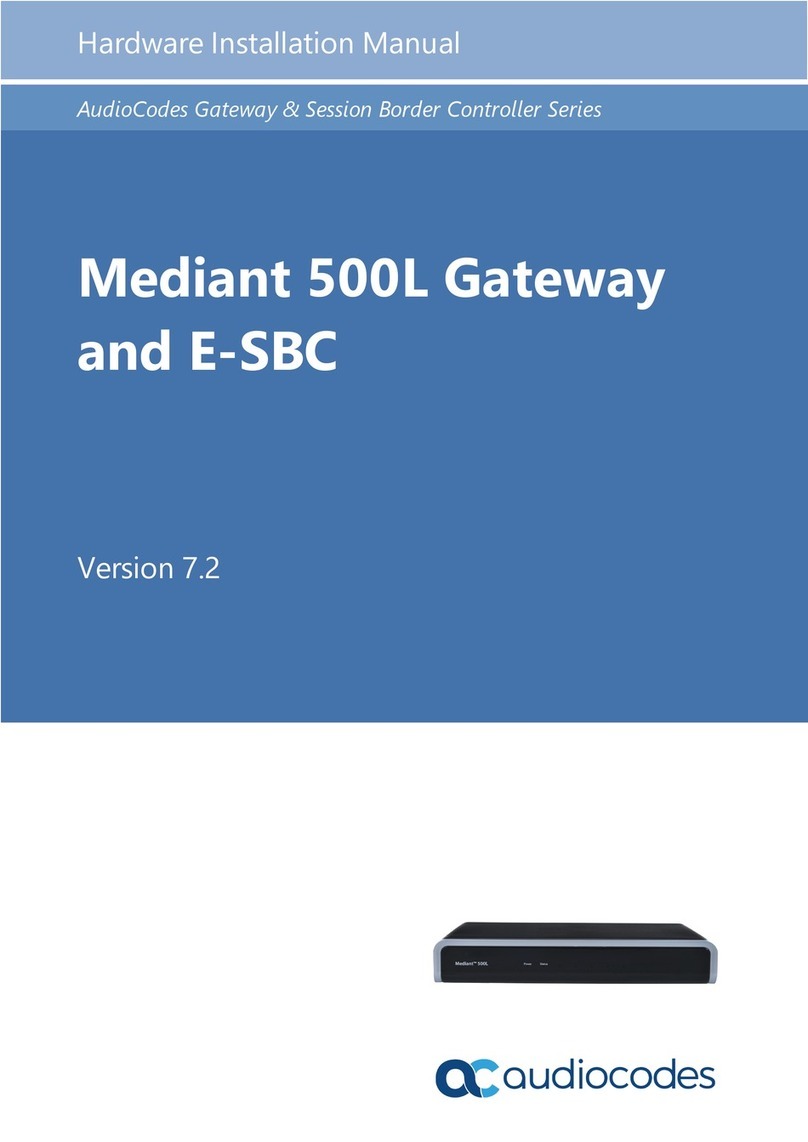
AudioCodes
AudioCodes Mediant 500L MSBR Hardware installation manual
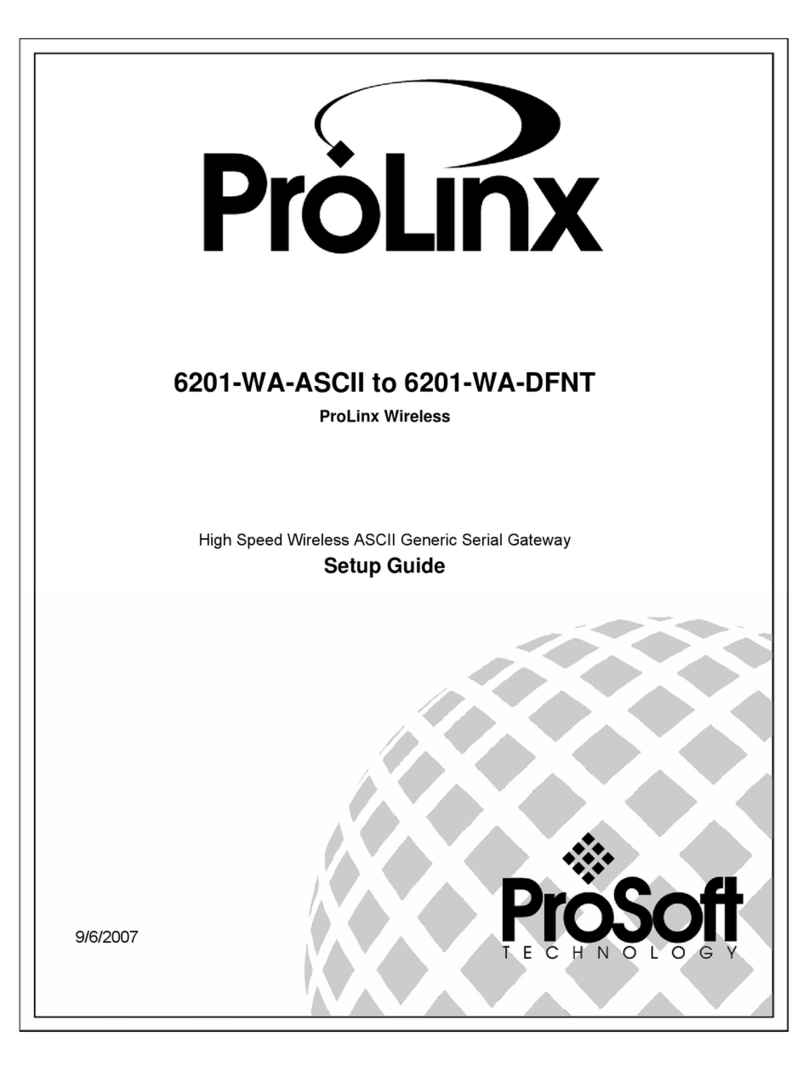
ProLinx
ProLinx 6201-WA-ASCII Setup guide
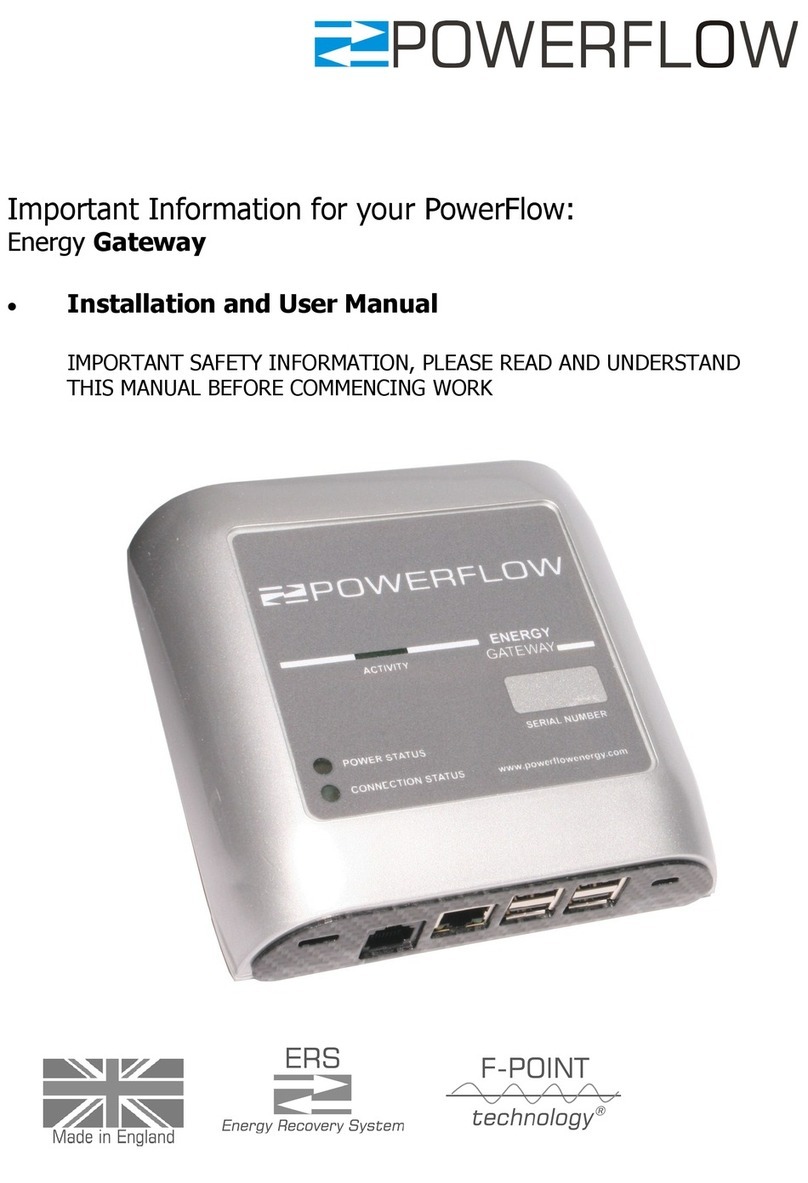
PowerFlow
PowerFlow Energy Gateway Installation and user manual
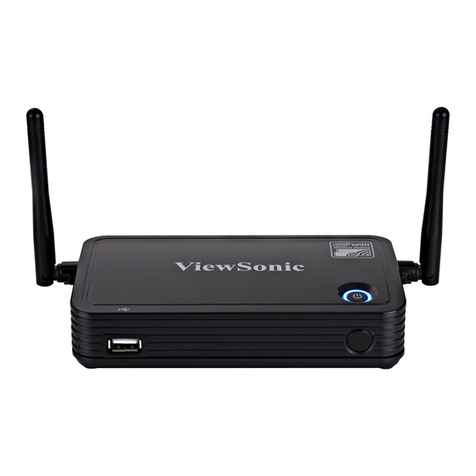
ViewSonic
ViewSonic WPG-370 user guide
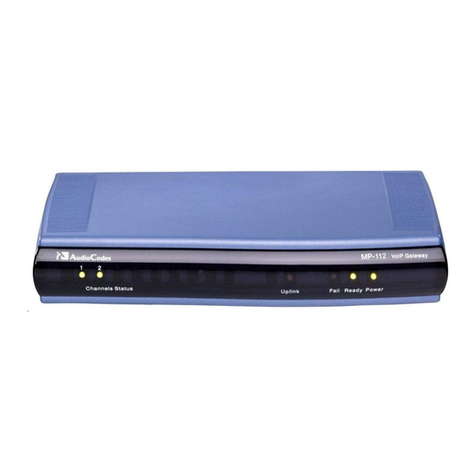
AudioCodes
AudioCodes MediaPack MP-124 user manual
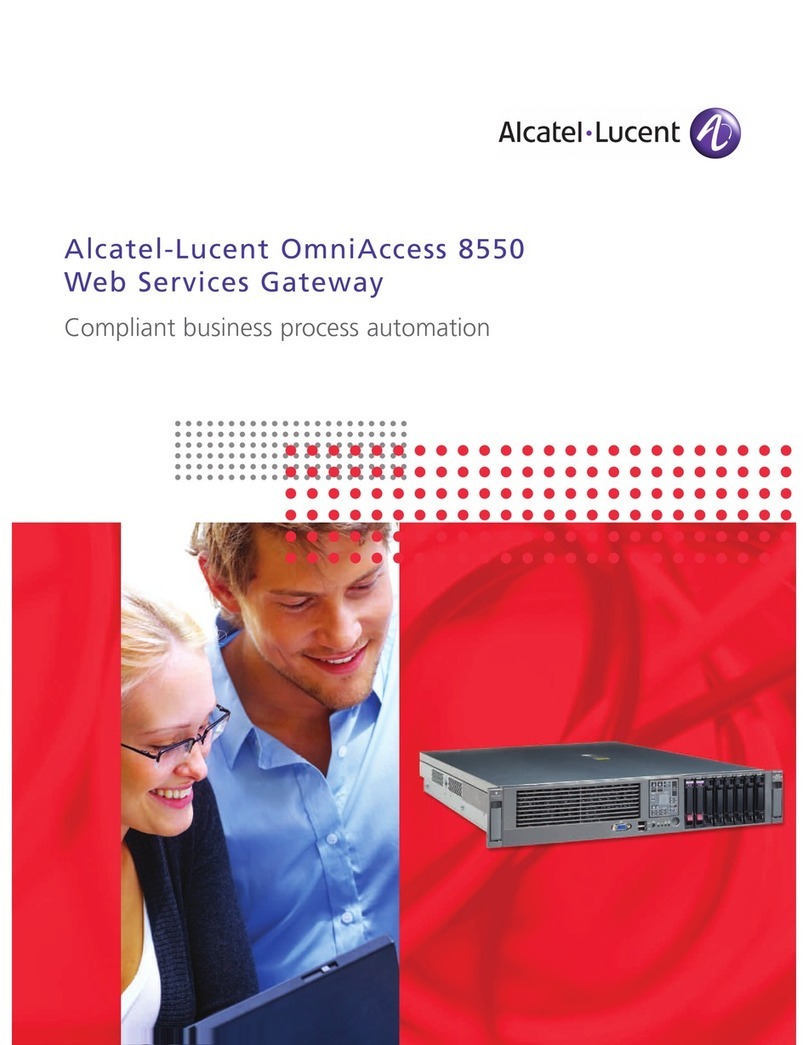
Alcatel-Lucent
Alcatel-Lucent OmniAccess 8550 brochure