RTA BFR3000 Specification sheet

BFR3000 – Modbus Router
Product User Guide
Software Build Date: December 17th 2015
Version 3
Platform: N34
Real Time Automation, Inc. 1 1-800-249-1612

Trademarks
All other trademarks and registered trademarks are the property of their holders.
Limited Warranty
Real Time Automation, Inc. warrants that this product is free from defects and functions properly.
EXCEPT AS SPECIFICALLY SET FORTH ABOVE, REAL TIME AUTOMATION, INC. DISCLAIMS ALL OTHER WARRANTIES, BOTH
EXPRESSED AND IMPLIED, INCLUDING BUT NOT LIMITED TO IMPLIED WARRANTIES OF MERCHANTABILITY OR FITNESS FOR A
PARTICULAR APPLICATION. THIS LIMITED WARRANTY GIVES YOU SPECIFIC LEGAL RIGHTS. YOU MAY ALSO HAVE OTHER
RIGHTS, WHICH VARY FROM STATE TO STATE.
The examples and diagrams in this manual are included solely for illustrative purposes. Because of the many variables and requirements
associated with any particular application, Real Time Automation, Inc. cannot assume responsibility or liability for actual use based on the
examples and diagrams. Except as specifically set forth above, Real Time Automation and its distributors and dealers will in no event be liable
for any damages whatsoever, either direct or indirect, including but not limited to loss of business profits, income, or use of data. Some states
do not allow exclusion or limitation of incidental or consequential damages; therefore, the limitations set forth in this agreement may not apply
to you.
No patent liability is assumed by Real Time Automation with respect to use of information, circuits, equipment, or software described in this
manual.
Government End-Users
If this software is acquired by or on behalf of a unit or agency of the United States Government, this provision applies: The software (a) was
developed at private expense, is existing computer software, and was not developed with government funds; (b) is a trade secret of Real Time
Automation, Inc. for all purposes of the Freedom of Information Act; (c) is “restricted computer software” submitted with restricted rights in
accordance with subparagraphs (a) through (d) of the Commercial “Computer Software-Restricted Rights” clause at 52.227-19 and its
successors; (d) in all respects is proprietary data belonging solely to Real Time Automation, Inc.; (e) is unpublished and all rights are reserved
under copyright laws of the United States. For units of the Department of Defense (DoD), this software is licensed only with “Restricted Rights”:
as that term is defined in the DoD Supplement of the Federal Acquisition Regulation 52.227-7013 (c) (1) (ii), rights in Technical Data and
Computer Software and its successors, and: Use, duplication, or disclosures is subject to restrictions as set forth in subdivision (c) (1) (ii) of the
Rights in Technical Data and Computer Software clause at 52.227-7013. If this software was acquired under GSA schedule, the U.S.
Government has agreed to refrain from changing or removing any insignia or lettering from the Software or documentation that is provided or
from producing copies of the manual or media. Real Time Automation, Inc.
© 2016 Real Time Automation, Inc. All rights reserved.
Real Time Automation, Inc. 2 1-800-249-1612

Overview ....................................................................................................................................................... 4
Getting Started.............................................................................................................................................. 5
Powering The Gateway ................................................................................................................................. 6
Accessing the Main Page............................................................................................................................... 7
Error: Main Page Does Not Launch........................................................................................................... 8
Operation Mode Selection............................................................................................................................ 9
Committing Changes to the Settings ..........................................................................................................10
Network and Hardware Configuration ....................................................................................................... 11
Network Configuration ........................................................................................................................... 11
Hardware Configuration .............................................................................................................................12
Modbus TCP/IP Client to/from Modbus RTU/ASCII Slave(s) ...................................................................... 13
Modbus Configuration ............................................................................................................................15
Diagnostics .............................................................................................................................................. 16
LED Behavior ...........................................................................................................................................17
Modbus TCP/IP Servers to/from Modbus RTU/ASCII Master..................................................................... 18
Modbus Configuration ............................................................................................................................20
Diagnostics .............................................................................................................................................. 21
LED Behavior ...........................................................................................................................................22
Modbus TCP/IP Client to/from Modbus RTU/ASCII Master ....................................................................... 23
Modbus Configuration ............................................................................................................................25
Diagnostics .............................................................................................................................................. 26
LED Behavior ...........................................................................................................................................27
Export/Import Configuration ...................................................................................................................... 28
Export Configuration...............................................................................................................................28
Import Configuration ..............................................................................................................................28
Utilities ........................................................................................................................................................ 29
Operation Mode...................................................................................................................................... 29
Logging .................................................................................................................................................... 29
Security Configuration ............................................................................................................................ 30
Security - Log In.......................................................................................................................................31
Upgrade Firmware ..................................................................................................................................31
Reset Router............................................................................................................................................32
Completing the Installation.........................................................................................................................33
Real Time Automation, Inc. 3 1-800-249-1612

Overview
The BFR3000 Modbus router can move messages between Modbus RTU or Modbus ASCII
networks and Modbus TCP/IP networks.
To configure the router you will set the router’s network settings, configure device specific
parameters for initial operation, and integrate the device into your application.
If at any time you need further assistance do not hesitate to call Real Time Automation support.
Support Hours are Monday-Friday 8am-5pm CST
Toll free: 800-249-1612
Real Time Automation, Inc. 4 1-800-249-1612

Getting Started
You will need the following:
The BFR3000 router
The provided CD-ROM
oIPSetup.exe can also be downloaded:
http://www.rtaautomation.com/product/460-gateway-support/
A PC with an internet browser
oFirefox / Internet Explorer / Google Chrome compatible
The supplied Ethernet crossover cable
A 8-28 VDC power source
Real Time Automation, Inc. 5 1-800-249-1612

Powering The Router
The following steps will allow you to properly and safely power the router.
1. Connect a 24VDC power source to the router.
a. The unit draws 125 mA at 24VDC
b. The router has a voltage operating range from 8-28VDC,
24VDC is recommended.
Hazardous Environment Power & Installation Instructions
This equipment is suitable for use in Class I, Division 2, Groups A, B, C and D, or non-
hazardous locations only.
WARNING – EXPLOSION HAZARD - Do not disconnect equipment unless power has been removed or
the area is known to be non-hazardous.
WARNING – EXPLOSION HAZARD - Substitution of components may impair suitability for Class I,
Division 2.
THIS EQUIPMENT IS OPEN-TYPE DEVICE AND IS MEANT TO BE INSTALLED IN AN ENCLOSURE
SUITABLE FOR THE ENVIRONMENT SUCH THAT THE EQUIPMENT IS ONLY ACCESSIBLE WITH THE
USE OF A TOOL.
WARNING – POWER JACK (Barrel Connector, J1) IS FOR MAINTENANCE USE ONLY AND MAY ONLY BE
USED WHILE THE AREA IS KNOWN TO BE FREE OF IGNITIBLE CONCENTRATIONS OF FLAMMABLE GASES
OR VAPORS. IT IS NOT TO BE CONNECTED UNDER NORMAL OPERATION.
In Hazardous Environments the unit must be powered with between 12-24 VDC, 860 mA (6 W) max.
Supervised. The unit is certified to be operated at -40°C to 50°C.
Warning improper wiring will cause unit failure
Use the Barrel Connector OR the Screw
Terminals power connection, NOT both
Real Time Automation, Inc. 6 1-800-249-1612

Accessing the Main Page
The following steps will help you access the browser based configuration of the router. By
default, DHCP is enabled. If the router fails to obtain an IP address over DHCP it will Auto IP
with 169.254.X.Y.
1) Insert the provided CD-ROM into a computer also on the network.
2) Run the IPSetup.exe program from the CD-ROM.
3) Find unit under “Select a Unit”.
a. Change IP address to match that of your PC if DHCP has failed.
i. You will know DHCP has failed if the router’s IP address is AutoIP at
169.254.X.Y.
ii. If successful, it will say DHCP’d at ex: 192.168.0.100 however your DCHP Client
is set up.
4) Click Launch Webpage. The Operation Mode Selection page should appear.
Default setting is set to DHCP. If DHCP fails, default IP Address is 169.254.x.y
CB34EX
Real Time Automation, Inc. 7 1-800-249-1612

Error: Main Page Does Not Launch
If the Main Page does not launch, please verify the following:
1. Check that the PC is set for a valid IP Address
a. Open a MS-DOS Command Prompt
b. Type “ipconfig” and press enter
c. Note the PC’s IP Address, Subnet, and Default Gateway
2. The router must be on the same Network/Subnet as the PC whether it’s set up for
DHCP/Static.
Once you have both devices on the same network, you should be able to ping the router using a
MS-DOS Command Prompt.
The screenshot above shows a router that is currently set to a static IP Address of
192.168.0.100.
If you are able to successfully ping your router, open a browser and try to view the main page
by entering the IP Address of the router as the URL.
Real Time Automation, Inc. 8 1-800-249-1612

Operation Mode Selection
Upon startup, you will be directed to the Operation Mode Selection page. There are 3 modes of
operation to select from:
•Modbus TCP/IP Client to Modbus RTU/ASCII Slave(s) – Use this mode to connect up to
5 Modbus TCP/IP Client devices with up to 255 Modbus RTU/ASCII Slaves.
•Modbus TCP/IP Server(s) to Modbus RTU/ASCII Master – Use this mode to connect up
to 255 Modbus TCP/IP Server devices with a Modbus RTU/ASCII Master.
•Modbus TCP/IP Client to Modbus RTU/ASCII Master – Use this mode to connect up to 5
Modbus TCP/IP Client devices with a Modbus RTU/ASCII Master.
1) Under the mode you would like to configure, select if the Modbus slave or master
device is RTU or ASCII from the dropdown.
2) Press the Select button to continue with the set up.
Real Time Automation, Inc. 9 1-800-249-1612

Committing Changes to the Settings
♦Changes made to the settings of the router will not take effect until the router is
restarted.
♦Changes will not be stored if the router’s power is removed prior to rebooting.
♦The router detects changes and will prompt you with a red notice box to reboot the
router after change.
♦NOTE: The router does not need to be restarted after every change. Multiple changes
can be made before a restart, but they will not be committed until the router is
rebooted.
♦The webpage will redirect to our rebooting page shown below.
♦After the router has restarted, which can take up to 15 seconds, the router will
automatically redirect to the diagnostics page. You will know the save was successful if
the red box is no longer present.
If you don’t understand the load screen reference you need to add Stanley Kubrick’s
2001: Space Odyssey to your must watch list. We recommend finding a Betamax version.
Real Time Automation, Inc. 10 1-800-249-1612

Network and Hardware Configuration
The Network and Hardware Configuration area is where you assign a description, change the IP
Settings and serial port settings.
Network Configuration
1) From the navigation menu, select Network and Hardware under Configuration.
2) Enter a User Description to help identify the router.
3) Enter IP Address, Subnet, Default Gateway, and DNS information.
NOTE: Changes can only be made on the webpage to the IP Address, Subnet, Default Gateway,
and DNS Gateway when the IP Settings parameter is set to “Use the Following IP Address.”
4) Once you are done configuring the Description and the Network Settings, click the Save
Parameters button.
If you are changing the IP Address of the router, the change will not take effect
until the unit has been rebooted. After reboot, you must enter the new IP
Address into your browser to access the configuration screens.
It is recommended to leave the DNS Gateway set to 0.0.0.0 and the Ethernet Link as
Auto-Negotiate.
Real Time Automation, Inc. 11 1-800-249-1612

Hardware Configuration
The Hardware Configuration page is where you set port specific parameters. These settings must match
the settings of the device(s) that you are connecting to.
When you have completed your port configuration, click the Save Parameters button.
The default jumper configurations are set up for the following serial modes:
Port 0 - RS485
Port 1 – RS232
If you require a different serial mode, please refer to the
Hardware_Jumper_Configuration.pdf on the CD to make jumper changes.
Real Time Automation, Inc. 12 1-800-249-1612

Operation Mode:
Modbus TCP/IP Client to/from Modbus
RTU/ASCII Slave(s)
Modbus RTU
Slave(s)
Modbus TCP/IP
Client
Real Time Automation, Inc. 13 1-800-249-1612

Modbus TCP/IP Client to/from Modbus RTU/ASCII
Slave(s)
In this mode of operation up to 5 Modbus TCP/IP Clients may send/receive messages from up
to 255 Modbus RTU Slave device(s).
The Modbus TCP/IP Client requests are transparently passed to Modbus RTU slaves. The Unit ID
field on Modbus TCP/IP is used as the Modbus RTU Slave ID field when transmitted on the serial
network.
•No other message fields are modified.
•If a TCP/IP Client tries to access a Slave device that is not connected then the router will
provide timeouts.
Real Time Automation, Inc. 14 1-800-249-1612

Modbus Configuration
1) From the navigation menu, select Modbus under Configuration.
RTU Master
2) Response Timeout: Enter the amount of time the router will wait for the response from
the Modbus RTU/ASCII Slave(s) before declaring a message has timed out.
TCP/IP Server
3) TCP/IP Port: Enter the port that the TCP/IP Server will have so that the TCP/IP Client can
communicate. Port 80 is not allowed.
4) Inactivity Timeout: Enter the amount of time the router will wait for communication
from the Modbus TCP/IP Client device before it closes the connection.
5) Modbus Client IP Address: Select from the dropdown how restrictive the TCP/IP Server
should be about incoming Modbus TCP/IP Client connections:
a. Unrestricted – Allows any Modbus TCP/IP Client to make a connection to the
TCP/IP Server in the router.
b. Restricted – Allows only the Modbus TCP/IP Clients at the specified IP Addresses
to make a connection to the TCP/IP Server in the router.
6) When finished, press the Save Parameters button to save the changes made on this
page. If settings have changed, you will be prompted to reboot the router for the
changes to take effect.
Real Time Automation, Inc. 15 1-800-249-1612

Diagnostics
From the navigation menu, select Diagnostics under Diagnostics.
Pressing the Clear button will clear out the all counts.
This table is organized the following way:
Device Name – Modbus RTU/ASCII Slave ID that the router is communicating with.
Current State – Displays the current state of each row. There are 3 states:
oOK: Requests being sent out are getting valid responses.
oError: The last request sent out got an error response from the Modbus
RTU/ASCII side.
oTimeout: The last request sent out did not get a response within the timeout
period specified.
Requests – Number of Modbus Requests sent to slave device.
Responses – Number of Modbus Responses sent from slave device.
Errors – Number of Error Messages sent from slave device.
Timeouts – Number of Timeout Messages from slave device.
Overall Total row – This row displays the total of all the values in that column.
Current # TCP Connections Open – This displays the number of Modbus TCP/IP Client
connections to the router.
RTU Error (Slave ID), RTU Error (CRC), RTU Error (Late Response) – These are errors that may
occur when the Modbus RTU/ASCII network has problems. These values should be 0 in a
functional system.
Real Time Automation, Inc. 16 1-800-249-1612

LED Behavior
LED 1 : Modbus TCP/IP
Blink
Green
No current TCP Connections
a) Have never had any TCP Connections
b) Had TCP Connections but all of them have timed out and are now closed
Solid
Green
At least 1 TCP Connection is made and is communicating to the router
Off
Ethernet cable is unplugged
LED 2 : Modbus RTU/ASCII
Blink
Green
No RTU/ASCII Connection has ever been made
Solid
Green
All RTU/ASCII Connections are valid and are communicating to the router within the
Inactivity Timeout configured
Blink
Red
Inactivity Timeout has been reached for one or more Slaves. Will remain in this state
until a valid message is received for the Slave ID that is currently in a Timeout state.
Real Time Automation, Inc. 17 1-800-249-1612

Operation Mode:
Modbus TCP/IP Servers to/from Modbus
RTU/ASCII Master
Modbus TCP/IP
Server
Modbus RTU
Master
Real Time Automation, Inc. 18 1-800-249-1612

Modbus TCP/IP Server(s) to/from RTU/ASCII Master
In this mode of operation a Modbus RTU/ASCII Master can connect up to 255 Modbus TCP/IP
Server devices. The Modbus RTU message sent to a Slave ID is converted to a Modbus TCP/IP
message and mapped to a corresponding Modbus TCP/IP address, Port and Unit ID.
•No other message fields are modified.
•Modbus Slave ID’s can be mapped to any Modbus TCP/IP Unit ID and IP Address.
•Multiple Modbus TCP/IP Unit ID’s can share a single IP address.
Real Time Automation, Inc. 19 1-800-249-1612

Modbus Configuration
1) From the navigation menu, select Modbus under Configuration.
TCP/IP Client
2) Response Timeout: Enter the amount of time the router will wait for the response from
the Modbus TCP/IP Server(s) before calling the message a timeout and closing the
connection.
RTU Slave
3) Inactivity Timeout:Enter the amount of time the router will wait for communication
from the Modbus RTU Master device before it raises an alarm.
a. Modbus RTU LED will turn red
Map your RTU Slave IDs to TCP/IP Addresses
4) Number of Devices: Number of mappings.
5) RTU Slave ID: Slave ID on Modbus RTU. This field must be unique.
6) TCP/IP Address: Enter the Ethernet TCP/IP address of the Modbus TCP/IP Server.
7) TCP/IP Port: Enter which port number will be used. Port 80 is not allowed.
8) TCP/IP Unit ID: Enter the Unit ID for the Modbus TCP/IP Server.
9) When finished, press the Save Parameters button to save the changes made on this
page. If settings have changed, you will be prompted to reboot the router for the
changes to take effect.
Real Time Automation, Inc. 20 1-800-249-1612
Table of contents
Popular Network Router manuals by other brands
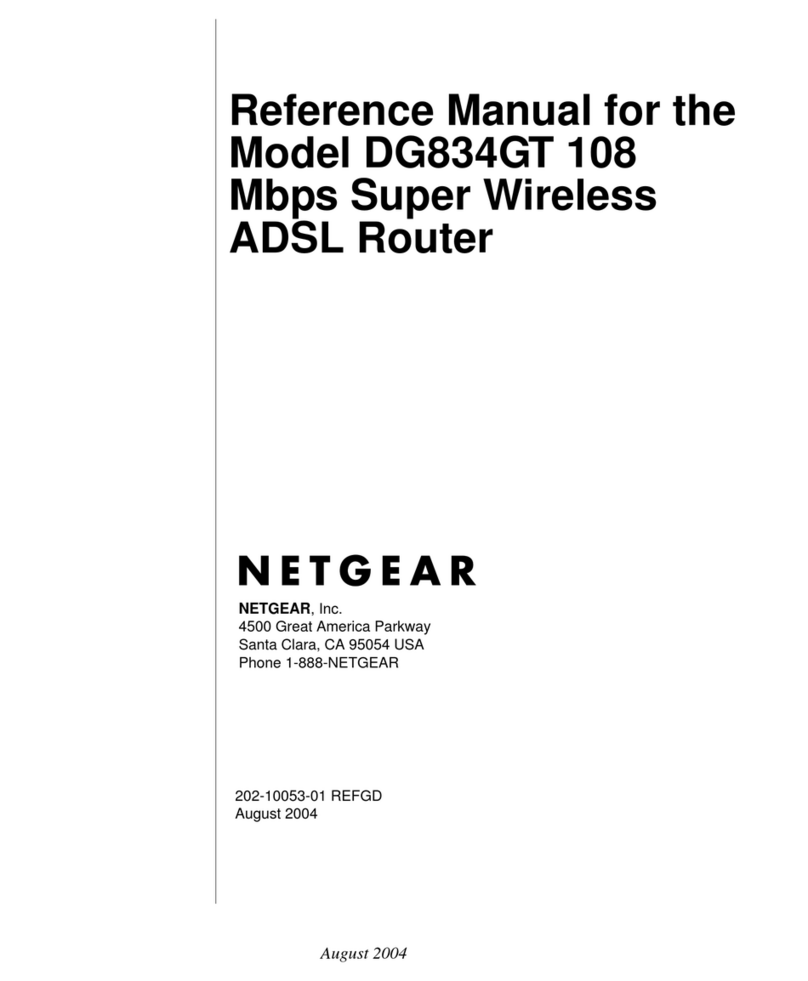
NETGEAR
NETGEAR DG834GT - 108 Mbps Super G Wireless ADSL... Reference manual
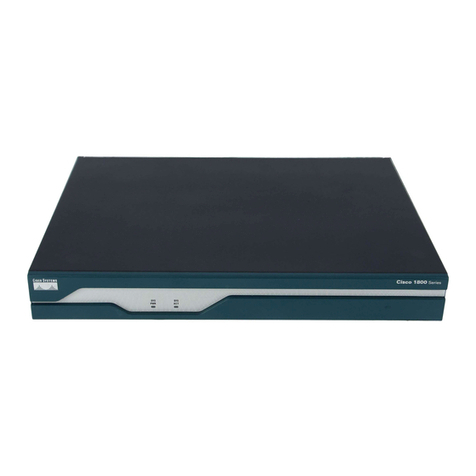
Cisco
Cisco 1841 - 3G Bundle Router datasheet
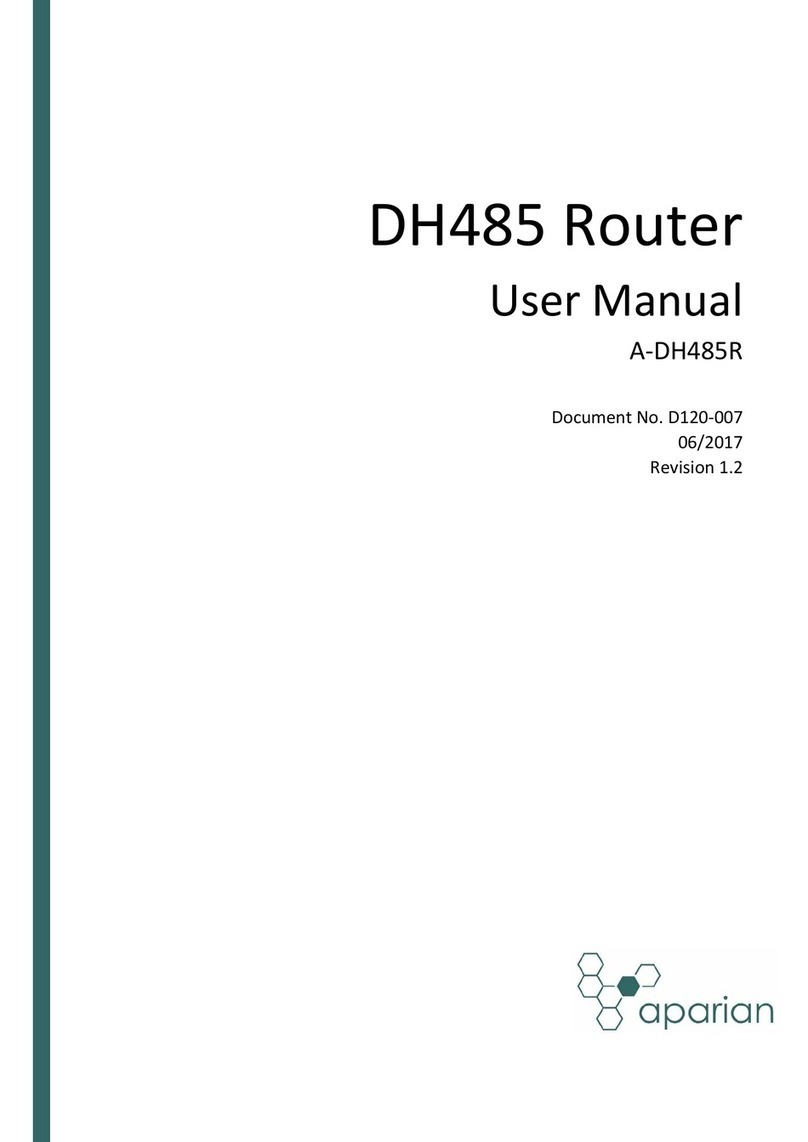
APARIAN
APARIAN DH485 user manual

Eco House Comfort
Eco House Comfort FHZ1000 Installation and user guide
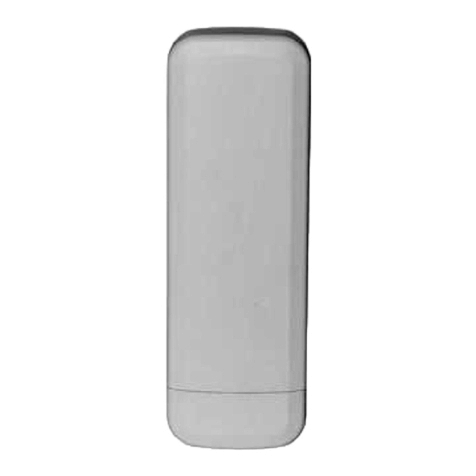
Yunlink
Yunlink CPE850D quick start guide
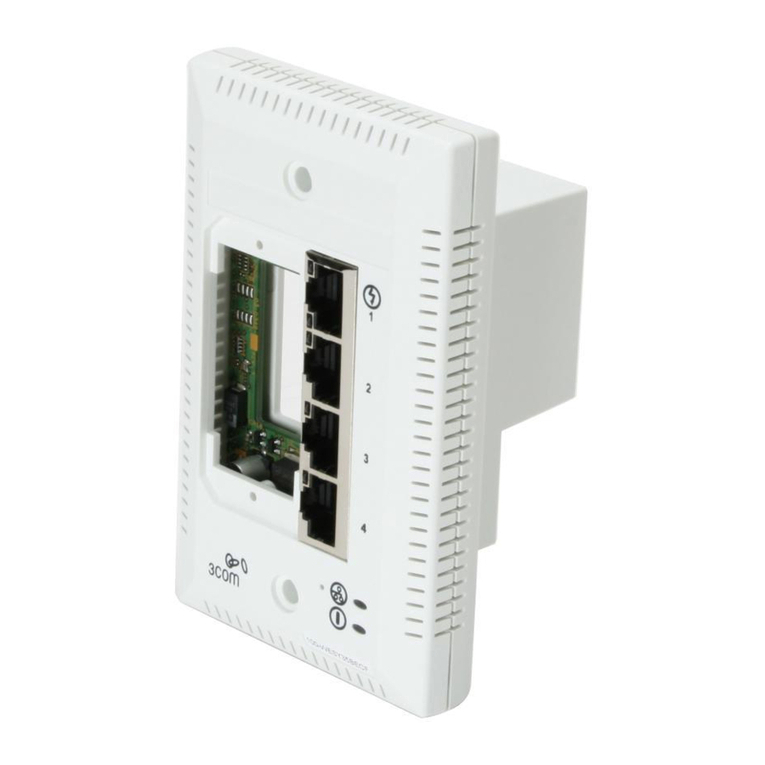
3Com
3Com 3CNJ100 - IntelliJack Switch installation guide