samlexsolar SCC-30AB User manual

30 Amp
Solar Charge
Controller
SCC-30AB
Owner's
Manual
Please read this
manual before
operating your
charge controller.

2
1. Safety Instructions.............................................................................................. 3
2. General Description of PV / Solar System.......................................................... 5
3. General information - Batteries ...................................................................... 15
4. Introduction and Features ............................................................................... 28
5. Construction, Layout and Controls.................................................................. 33
6. Installation and Operation .............................................................................. 38
7. Troubleshooting ............................................................................................... 45
8. Specications.................................................................................................... 47
9. Warranty ........................................................................................................... 49
INDEX

3
1
SAFETY INSTRUCTIONS
Please read these instructions before installing or operating the Charge Controller to prevent per-
sonal injury or damage to the Charge Controller.
General
Installation and wiring compliance
•Installation and wiring must comply with the local and National Electrical Codes and must
be done by a certied electrician.
Preventing electrical shock
•The negative system conductor should be properly grounded. Grounding should comply
with local codes.
•Disassembly / repair should be carried out by qualied personnel only.
•Disconnect all input and output side connections before working on any circuits
associated with the Charge Controller. Turning the on/off control on the Charge
Controller to off position may not entirely remove dangerous voltages.
•Be careful when touching bare terminals of capacitors. The capacitors may retain high
lethal voltages even after the power has been removed. Discharge the capacitors before
working on the circuits.
Installation environment
•The Charge Controller should be installed indoor only in a well ventilated, cool, dry
environment.
•Do not expose to moisture, rain, snow or liquids of any type.
Preventing re and explosion hazards
•Working with the Charge Controller may produce arcs or sparks. Thus, the Charge
Controller should not be used in areas where there are inammable materials or gases
requiring ignition protected equipment. These areas may include spaces containing
gasoline powered machinery, fuel tanks, battery compartments.
Precautions when working with batteries
•Batteries contain very corrosive, diluted sulphuric acid as electrolyte. Precautions should
be taken to prevent contact with skin, eyes or clothing.
•Batteries generate hydrogen and oxygen during charging, resulting in evolution of
explosive gas mixture. Care should be taken to ventilate the battery area and follow the
battery manufacturer’s recommendations.
•Never smoke or allow a spark or ame near the batteries.

4
1
SAFETY INSTRUCTIONS
•Use caution to reduce the risk of dropping a metal tool on the battery. It could spark or short
circuit the battery or other electrical parts and could cause an explosion.
•Remove metal items like rings, bracelets and watches when working with batteries. The
batteries can produce a short circuit current high enough to weld a ring or the like to metal
and cause a severe burn.
•If you need to remove a battery, always remove the ground terminal from the battery rst.
Make sure that all the accessories are off so that you do not cause a spark.
Charge Controller related
•Please ensure the input voltage fed to the Charge Controller does not exceed 50 VDC to
prevent permanent damage to the Charge Controller. Ensure that the maximum Open
Circuit Voltage Voc of the 12 V nominal Solar Panel / Solar Array is less than 50 V. If two 12 V
nominal Solar Panels are being used in series to make a 24 V nominal Solar Array, make sure
that the maximum Open Circuit Voltage Voc of each of the 12 V Panels is less than 25 V.
•Do not exceed the maximum current rating of 30 A. The Short Circuit Current of the Solar
Array should be less than 30 A.
•Do not exceed a battery voltage of 24V (nominal) . Do not use a battery less than 12V.
•Charge only 12, or 24 volt Lead-Acid batteries when using the standard battery charging
programs or Ni-Cd batteries when DIP Switch number 2~4 is in the ON position.
•DO NOT short circuit the PV array or load while connected to the controller. This will damage
the controller.
•The controller should be protected from direct sunlight. Ensure adequate space for air ow
around the controller’s face plate.
•Do not install in a sealed compartment with batteries.
•Never allow the solar array to be connected to the controller with the battery disconnected.
This can be a dangerous condition with high open-circuit solar voltage present at the
terminals.
•Use only copper wire with minimum 75°C insulation rating, and between 10 AWG (5.2 mm2)
and 14 AWG (2.1 mm2) gauge.
•The Negative system conductor should be properly grounded. Grounding should comply with
local codes.

5
2
GENERAL DESCRIPTION OF PV / SOLAR SYSTEM
What is Photovoltaic (PV)?
The word ‘photo-voltaic’ is derived from two different words; the word ‘photos’,
from the Greek, meaning light and the word ‘voltaic’ developed from the name of the
Italian scientist, Volta, who studied electricity. This explains what a PV system does: it
converts light energy from the sun into electrical energy.
What is in a Photovoltaic (PV) system?
Non Grid-tied PV / Solar System
PV/Solar Panel (Module) or Array
Charge Controller
Battery
DC-AC Power Inverter
To AC
Loads
Solar Array
Charge
Controller/Protection
DC-AC Power Inverter
To AC
Loads
Power to
and from grid
Two-way Metering
Fig. 2.1. Non Grid-tied PV System–Block Diagram
Fig. 2.1 shows a Block Diagram of a typical non-grid tied Photovoltaic (PV) System
with its main components. It consists of a PV / Solar Panel (Module), Charge Controller,
Batteries and Power Inverter. The PV / Solar Panel (Module) or Array converts the
solar light energy into DC electrical energy. The Charge Controller conditions the DC
electrical voltage and current produced by the PV / Solar Panel (Module) or Array to
charge a battery. The battery stores the DC electrical energy so that it can be used
when there is no solar energy available (night time, cloudy days etc). DC loads can be
powered directly from the PV / Solar Panel (Module) / Battery. The inverter converts
the DC power produced by the PV / Solar Panel (Module) / stored in the battery into
AC power to enable powering of AC loads.

6
2
GENERAL DESCRIPTION OF PV / SOLAR SYSTEM
Grid-tied PV / Solar System
Fig. 2.2 shows a Block Diagram of a typical Grid-tied PV / Solar System. In this system,
the Solar Panels (Modules) / Arrays directly feed to an inverter and the inverter is
connected to an Electricity Transmission and Distribution System (referred to as the
Electricity Grid) such that the system can draw on the Grid’s reserve capacity in times
of need, and feed electricity back into the Grid during times of excess production.
PV/Solar Panel (Module) or Array
Charge Controller
Battery
DC-AC Power Inverter
To AC
Loads
Solar Array
Charge
Controller/Protection
DC-AC Power Inverter
To AC
Loads
Power to
and from grid
Two-way Metering
Fig. 2.2. Grid-tied PV / Solar System – Block Diagram
In order to safely transmit electricity to your loads and to comply with your power
provider’s grid-connection requirements, you may need the following additional
items:
•Power conditioning equipment.
•Safety equipment.
•Meters and instrumentation.

7
2
GENERAL DESCRIPTION OF PV / SOLAR SYSTEM
PV / Solar Cell
12cm
Fig. 2.3. PV / Solar Cell
The basic element of a PV System is the photovoltaic (PV) cell, also called a Solar Cell.
An example of a PV / Solar Cell made of Mono-crystalline Silicon is shown in Fig. 2.3.
This single PV / Solar Cell is like a square, but with its four corners missing (it is made
this way!).
Theory of Operation of PV / Solar Cell
Sunlight (photons)
External circuit
Encapsulate seal
Top electrical contact
P-Type material
(Boran-doped Silicon)
N-Type material
(Phosphorous-doped Silicon)
P/N junction
Base contact
Fig. 2.4. Construction and Working of PV / Solar Cell
A PV / Solar Cell is a semiconductor device that can convert solar energy into DC
electricity through the “Photovoltaic Effect” (Conversion of solar light energy into
electrical energy). When light shines on a PV / Solar Cell, it may be reected, absorbed,
or passes right through. But only the absorbed light generates electricity.

8
2
GENERAL DESCRIPTION OF PV / SOLAR SYSTEM
When light enters the PV / Solar Cell, some of the “Photons” (packets of electro-
magnetic wave energy) from the light energy are absorbed by the semiconductor
atoms. The energy of the absorbed light is transferred to the negatively charged
electrons in the atoms of the solar cell. With their newfound energy, these electrons
escape from their normal positions in the atoms of the semiconductor photovoltaic
material and become part of the electrical ow, or current, in an electrical circuit. A
special electrical property of the PV / Solar Cell – a built-in electric eld – provides the
force, or voltage, needed to drive the current through an external load, such as a
light bulb.
To induce the built-in electric eld within a PV / Solar Cell, two layers of somewhat
differing semiconductor materials are placed in contact with one another (See Fig. 2.4).
One layer is an N-type semiconductor (e.g. Phosphorus doped Silicon) with an abundance
of “Electrons”, which have a Negative electrical charge. The other layer is a P-type
semiconductor (e.g. Boron doped Silicon) with an abundance of ”Holes”, which have a
Positive electrical charge.
Although both materials are electrically neutral, N-type silicon has excess Electrons and
P-type silicon has excess Holes. Sandwiching these together creates a P-N Junction at their
interface, thereby creating an electric eld.
When N-type and P-type silicon come into contact, excess electrons move from the
N-type side to the P-type side. The result is a buildup of Positive charge along the
N-type side of the interface and a buildup of Negative charge along the P-type side.
Because of the ow of electrons and holes, the two semiconductors behave like a battery,
creating an electric eld at the surface where they meet – the P/N Junction. The electrical
eld causes the electrons to move from the semiconductor toward the Negative surface,
where they become available to the electrical circuit. At the same time, the Holes move in
the opposite direction, toward the positive surface, where they await incoming electrons.
The electrical current is fed to the external load through the top electrical contact surface
(normally in the form of a grid) and the bottom base contact.
The Open Circuit Voltage Voc of a PV /Solar Cell is just under 0.6 V
Factors Affecting Voltage and Current Output of the PV / Solar Cell
The amount of electric current generated by photon excitation in a PV / Solar Cell at
a given temperature is affected by the incident light in two ways:
•By the intensity of the incident light.
•By the wavelength of the incident rays.

9
2
GENERAL DESCRIPTION OF PV / SOLAR SYSTEM
The materials used in PV / Solar Cells have different spectral responses to incident
light, and exhibit a varying sensitivity with respect to the absorption of photons at
given wavelengths.Each semiconductor material will have an incident radiation
threshold frequency, below which no electrons will be subjected to the photovoltaic
effect. Above the threshold frequency, the kinetic energy of the emitted
photoelectron varies according to the wavelength of the incident radiation, but
has no relation to the light intensity. Increasing light intensity will proportionally
increase the rate of photoelectron emission in the photovoltaic material. In actual
applications, the light absorbed by a PV cell will be a combination of direct solar
radiation, as well as diffused light bounced off of surrounding surfaces. PV / Solar
Cells are usually coated with anti-reective material so that they absorb the maximum
amount of radiation possible.
The output current of the PV / Solar Panel (Module) can increase due to what is
known as the “Edge of the Cloud Effect”. As the sun moves into a hole between the
clouds, your solar panels will see full direct sunlight combined with reected light
from the clouds! They will absorb more energy than they could on a cloudless day!
Thus, a factor of 1.25 times the Short Circuit Current Isc is recommended when sizing
the current capacity of the Charge Controller.
The output current of the PV / Solar Cell has a positive Temperature Coefcient – The
output current increases with the rise of temperature. However, it is negligible – less
than 0.1 % / °C of the Short Circuit Current Isc.
The output voltage of the PV / Solar Cell has a Negative Temperature Coefcient –
The output voltage increases with decrease in temperature. For example, a Silicon Cell
has a Temperature Coefcient of – 2.3 mV / °C / Cell. Hence, during cold winter days,
the voltage will rise. As a Rule of Thumb, the voltage rating of the Charge Controller
should be sized as 1.25 times the Open Circuit Voltage rating Voc of the PV /
Solar Panel (Module) to ensure that the Charge Controller is not damaged due to
over-voltage.

10
2
GENERAL DESCRIPTION OF PV / SOLAR SYSTEM
PV Cell Types
PV cells are most commonly made of Silicon, and come in two varieties, crystalline and
thin-lm type, as detailed in Table 2.1
Cell types include Mono-crystalline Silicon, Poly-crystalline Silicon, Amorphous Silicon
(a-Si), Gallium Arsenide (GaAs), Copper Indium Diselenide (CuInSe2, „CIS“), Cadmium
Telluride, or a combination of two materials in a tandem cell.
Bulk type / Wafer-based (Crystalline)
Mono Crystalline Si Poly Crystalline Si Poly Crystalline Band
Pros High efciency High efciency with
respect to price -
Cons Increased manufacturing cost caused by the
supply shortage of silicon -
Thin lm type
Amorphous Si CIGS CdTe Polymer organic
Pros Low price
Low price
Able to automate
all manufacturing
process
Low manufacturing
Can be more efcient (still
in research)
Cons Low efciency Low efciency
Table 2.1. PV Cell Types
PV Module / Panel and PV Array
To increase their utility, a number of individual PV cells are interconnected together
in a sealed, weatherproof package called a Panel (Module). For example, a 12 V Panel
(Module) will have 36 cells connected in series and a 24 V Panel (Module) will have 72
PV Cells connected in Series.
To achieve the desired voltage and current, Modules are wired in series and parallel
into what is called a PV Array. The exibility of the modular PV system allows
designers to create solar power systems that can meet a wide variety of electrical
needs. Fig. 2.5 shows PV cell, Panel (Module) and Array.

11
2
GENERAL DESCRIPTION OF PV / SOLAR SYSTEM
Cell
Module
Array
Fig. 2.5. PV cell, Module and Array
The cells are very thin and fragile so they are sandwiched between a transparent
front sheet, usually glass, and a backing sheet, usually glass or a type of tough plastic.
This protects them from breakage and from the weather. An aluminum frame is tted
around the module to enable easy xing to a support structure.
The picture in Fig. 2.6 shows a small part of a Module with cells in it. It has a glass
front, a backing plate and a frame around it.
Aluminum
frame
Glass
front
Backing
Sheet
PV Cell
Fig. 2.6. Construction of a typical Mono-crystalline PV / Solar Panel

12
2
GENERAL DESCRIPTION OF PV / SOLAR SYSTEM
Bypass Diodes
As mentioned, PV / Solar cells are wired in series and in parallel to form a PV / Solar
Panel (Module). The number of series cells indicates the voltage of the Panel (Module),
whereas the number of parallel cells indicates the current. If many cells are connected
in series, shading of individual cells can lead to the destruction of the shaded cell or
of the lamination material, so the Panel (Module) may blister and burst. To avoid such
an operational condition, Bypass Diodes are connected anti-parallel to the solar cells
as in Fig. 2.7. As a consequence, larger voltage differences cannot arise in the reverse-
current direction of the solar cells. In practice, it is sufcient to connect one bypass
diode for every 15-20 cells. Bypass diodes also allow current to ow through the PV
module when it is partially shaded, even if at a reduced voltage and power. Bypass
diodes do not cause any losses, because under normal operation, current does not
ow through them.
+-
load
bypass diodes
A K
Figure 2.7. Parallel PV cell with bypass diodes
Current (I), Voltage (V) and Power (P) Curves of a PV / Solar Panel
(Module) and how the PV / Solar Panel (Module) is rated -
Voc , Vmp , Isc , Imp , Pmax
Fig. 2.8. Current (I), Voltage (V) and Power (P) Curves

13
2
General Description of pV/solar system
A Current (I) versus Voltage (V) Curve of a PV / Solar Module (“I-V” Curve) shows the
possible combinations of its current and voltage outputs. A typical I-V curve for a 12 V
Module is shown in Fig. 2.8.
The power in a DC electrical circuit is the product of the voltage and the current.
Mathematically,
•Power (P) in Watts (W) = The Current (I) in Amperes (A) X the Voltage (V) in Volts (V)
i.e. W = V x A
A PV / Solar Cell or a Panel (Module) produces its maximum current when there is
no resistance in the circuit, i.e. when there is a short circuit between its Positive and
Negative terminals. This maximum current is known as the Short Circuit Current and is
abbreviated as Isc. When the Cell / Panel (Module) is shorted, the voltage in the circuit
is zero.
Conversely, the maximum voltage occurs when there is a break in the circuit. This is
called the Open Circuit Voltage (Voc). Under this condition, the resistance is innitely
high and there is no current, since the circuit is incomplete. Typical value of the open-
circuit voltage is located about 0.5 – 0.6 V for Crystalline Cells and 0.6 – 0.9 V for
Amorphous Cells.
These two extremes in load resistance, and the whole range of conditions in between
them, are depicted on the I-V Curve. Current, expressed in Amps, is on the vertical
Y-axis. Voltage, in Volts, is on the horizontal X-axis.
The power available from a photovoltaic device at any point along the curve is just
the product of Current (I) in Amps (A) and Voltage (V) in Volts (V) at that point and is
expressed in Watts. At the short circuit current point, the power output is zero, since
the voltage is zero. At the open circuit voltage point, the power output is also zero,
but this time it is because the current is zero.
Maximum Power Point and Rated Power of PV / Solar Panel (Module)
There is a point on the knee of the I-V Curve where the maximum power output
is located and this point is called the Maximum Power Point (MPP). The voltage and
current at this Maximum Power Point are designated as Vmp and Imp.
The values of Vmp and Imp can be estimated from Voc and Isc as follows:
Vmp ≈(0.75 – 0.9) Voc
Imp ≈(0.85 – 0.95) Isc

14
2
General Description of pV/solar system
The rated power of the PV / Solar Module in Watts (Pmax) is derived from the above
values of voltage Vmp and current Imp at this Maximum Power Point (MPP):
•Rated power in Watts, Pmax = Vmp X Imp
Example of I-V Curve and Ratings of a 12 V PV / Solar Panel
Fig. 2.9. Example of I-V Curve and Ratings of a 12 V PV / Solar Panel
The I-V Curve for a typical 12 Volt PV / Solar Panel is shown in Fig. 2.9.
This Maximum Power Point in the example curve given above is where Vmp
is 17 Volts, and the current Imp is 2.5 amps. Therefore, the rated or the maximum
power Wmax in watts is 17 Volts times 2.5 Amps, or 42.5 Watts.
Standard Test Conditions (STC) for Specifying PV / Solar Modules
The I-V curve is also used to compare the performance of PV / Solar Modules.
The curve is, therefore, generated based on the performance under Standard Test
Conditions (STC) of sunlight and device temperature of 25 °C. It assumes there is
no shading on the device. Standard sunlight conditions on a clear day are assumed
to be 1,000 Watts of solar energy per square meter (1000 W/m2or 1 kW/m2). This is
sometimes called one sun, or a peak sun. Less than one sun will reduce the current
output of the PV device by a proportional amount. For example, if only one-half sun:
(500 W/m2) is available, the amount of output current is roughly cut in half.

15
3
GENERAL INFORMATION: BATTERIEs
Battery Types
There are several different types of battery chemistries like Lead-Acid, Nickel-Iron
(Ni-Fe), Nickel-Cadmium (Ni-Cad) etc. The batteries consist of individual cells that can
be connected in series to obtain the required battery voltage. Batteries are either
sealed (also called Valve Regulated Lead Acid - VRLA) or non-sealed / vented / ooded /
wet cell.
Nickel-Iron (Ni-Fe) and Nickel-Cadmium (Ni-Cad) Battery
Nickel-Iron (Ni-Fe) and Nickel-Cadmium (Ni-Cad) (also called alkaline batteries) have
a nominal cell voltage of 1.2 volts per cell. The nominal voltage of a Ni-Cad / Ni-Fe
battery bank can be made the same as a lead acid bank just by juggling the number
of cells (10 cells for 12 volts, 20 cells for 24 volts and 40 cells for 48 volt systems).
However, the Ni-Cad / Ni-Fe battery bank must be charged to a higher voltage to fully
recharge and will drop to a lower voltage during discharging compared to a similarly
sized lead acid type battery.
Lead Acid Battery
A Lead Acid battery consists of a number of 2 V nominal cells (actual voltage of the
cell is 2.105 V) that are connected in series e.g. a 12 V nominal battery will have six,
2 V nominal cells in series (actual voltage of the 6 cells will be 2.105 x 6 = 12.63 V).
Each 2 V nominal cell in this battery consists of an independent enclosed compartment
that has Positive and Negative Plates (also called Electrodes) dipped in electrolyte
that is composed of diluted Sulphuric Acid – solution of 33.5% v/v Sulphuric Acid and
water. In a fully charged battery, the Positive Plate is in the form of Lead Dioxide, the
Negative Plate is in the form of Lead and the Sulphuric Acid in the electrolyte has the
maximum concentration of 33.5% v/v.
Electrochemical Reactions during Charging and Discharging
of Lead Acid Battery
Electrical power in the Lead Acid Battery is produced by reversible electrochemical
reactions as follows:
During discharging, the Sulphuric Acid in the electrolyte reacts with the Positive
and Negative plates resulting in conversion of the active materials in the two plates
to Lead Sulphate. At the same time, electrons are released that create the electrical
current that ows to the load. The concentration of Sulphuric Acid in the electrolyte is
reduced as the battery gets discharged (the electrolyte becomes pure water when the
battery is fully discharged).

16
3
GENERAL INFORMATION: BATTERIEs
During charging, reverse electrochemical reactions take place. Under the inuence
of the charging voltage fed to the battery by the external battery charger / charge
controller, electrons are fed back to the battery and the Lead Sulphate at the Positive
and Negative Plates is converted back to Lead Dioxide at the Positive Plate and Lead
at the Negative Plate and the concentration of Sulphuric Acid is restored (will revert to
33.5% v/v when the battery is fully charged).
Gassing due to Excessive Overcharging
During charging, the battery is required to be charged in a controlled manner in
the nal Absorption Stage (2.4 V per cell at 25 ºC / 77 ºF or 14.4 V for a 12 V battery
at 25 ºC / 77 ºF) that restores the last 20% to 30% of the capacity. On completion of
this stage of charging, the Lead Sulphate at the Positive and Negative Plates is fully
converted back to Lead Dioxide at the Positive Plate and Lead at the Negative Plate.
Any further charging at this voltage or higher than this voltage results in electrolysis
of water in the electrolyte to Hydrogen and Oxygen and this undesirable condition
contributes to waste of energy. This process is known as “gassing”. Gassing is also
produced during the timed Equalization Stage (performed only for vented /ooded /
wet cell batteries) when the battery is intentionally overcharged (2.5 to 2.6 V per cell
/ 15 to 15.6 V for 12 V batteries) so that weaker cells are brought up to the full charge
too (equalized).
Non-sealed / vented / ooded / wet cell batteries have open vents to release
Hydrogen and Oxygen produced during gassing. The above un-intentional electrolysis
of water during overcharging results in loss of water and reduces the level of the
electrolyte in this type of batteries. When the level of the electrolyte is reduced, the
upper portion of the plates in the cells will not be immersed in the electrolyte and
will result in loss of battery capacity. Hence, these types of batteries are required to
be topped up with distilled water periodically to ensure that the plates in the cells
are fully immersed in the electrolyte. Some non-sealed / vented / ooded / wet cell
batteries come with catalytic caps to recombine any emitted Hydrogen and Oxygen.
Sealed / VRLA batteries are designed to recombine the Hydrogen and Oxygen back
into water and hence, Sealed / VRLA batteries are not required to be topped up with
distilled water. That is why these batteries are also called maintenance free batteries.
Sealed / VRLA batteries use safety valves to release any excessive gas pressure built
up inside the battery due to malfunction or overheating. If this happens (e.g.,
by overcharging) the valve vents the gas and normalizes the pressure, producing
a characteristic acid smell. Valves can sometimes fail however, if dirt and debris
accumulate, allowing pressure to build up that will result in damage to the battery.

17
3
GENERAL INFORMATION: BATTERIEs
Sealed Lead Acid (SLA) or Valve regulated Lead Acid (VRLA) Batteries
Sealed Lead Acid (SLA) batteries or Valve Regulated Lead Acid (VRLA) batteries can
either be Gel Cell or AGM (Absorbed Glass Mat). In a Gel Cell battery, the electrolyte
is in the form of a gel. In AGM (Absorbed Glass Mat) battery, the electrolyte is soaked
in Glass Mat. In both these types, the electrolyte is immobile. There are no rell caps
and the battery is totally sealed. Hydrogen and Oxygen released during the charging
process is not allowed to escape and is recombined inside the battery. Hence, there
is no water loss and the batteries are maintenance free. These batteries have safety
valves on each cell to release excessive pressure that may be built up inside the cell.
The Gel Cell is the least affected by temperature extremes, storage at low state of
charge and has a low rate of self discharge. An AGM battery will handle overcharging
slightly better than the Gel Cell.
Non Sealed (Vented / Flooded / Wet Cell) Lead acid Batteries
In a non-sealed / vented / ooded / wet cell battery, each individual cell compartment
has a rell cap that is used to top up the cell with distilled water and to measure
the specic gravity of the electrolyte using a hydrometer. When fully charged, each
individual cell has a voltage of approximately 2.105 V and electrolyte specic gravity
of 1.265. As the cell discharges, its voltage and specic gravity drop. Thus, a healthy,
fully charged, 12 V nominal battery with each of the 6 cells fully charged to 2.105 V
will measure a standing voltage of 12.63 V at 25 ºC / 77 ºF. Also, in a healthy battery,
all the individual cells will have the same voltage and same specic gravity. If there is
a substantial difference in the voltages (0.2 V or higher) and specic gravities of the
individual cells, the cells will require equalization.
Construction of Battery Cell Plates - Lead Antimony and Lead
Calcium Batteries
During construction, both the Positive and the Negative plates are similar. Both the
plates consist of a rectangular grid made out of alloyed Lead with rectangular holes in
it as shown in Fig 3.1 below:
Fig 3.1. Grid structure of Positive and Negative Plates in a Lead Acid Battery

18
3
GENERAL INFORMATION: BATTERIEs
The holes in the grid of the plates are lled with a paste of active material made
out of a mixture of Red Lead and 33% dilute Sulphuric Acid (different manufacturers
use modied mixtures). The paste is pressed into the holes in the grid. This paste
remains porous and allows the Sulphuric Acid in the electrolyte to react with the
lead inside the plate increasing the surface area many fold. At this stage, the Positive
and Negative plates are identical. Once dry, the plates are then stacked together
with suitable separators and inserted in the battery container. After the electrolyte
has been added to the cell, the cell is given its rst “Forming Charge”. During this
“Forming Charge”, the Lead paste in the Positive plate gradually turns to Lead
Dioxide (chocolate brown color), and the Lead paste in the Negative plate turns to
Sponge Lead (slate gray color). Such charged cell is ready to be used.
The above grid structure of the plates is made from a Lead alloy. A pure Lead grid
structure is not strong enough by itself to stand vertically while supporting the active
material. Other metals in small quantities are alloyed with Lead for added strength
and improved electrical properties. The most commonly alloyed metals are Antimony,
Calcium, Tin, and Selenium.
The two most common alloys used today to harden the grid are Antimony and
Calcium. Batteries with these types of grids are sometimes called “Lead-Antimony”
and & “Lead-Calcium” batteries. Tin is added to Lead-Calcium grids to improve
cyclability
The major differences between batteries with Lead-Antimony and Lead-Calcium
grids are as follows:
•Lead-Antimony batteries can be deep cycled more times than Lead-Calcium batteries.
•Flooded Lead-Antimony batteries require more frequent maintenance as they near end-of-
life since they use an increasing amount of water and require periodic equalization charges.
•Lead-Calcium batteries have lower self-discharge rates and therefore, will draw less current
while kept in storage
SLI (Starting, Lighting, Ignition) Batteries
Everybody is familiar with the SLI batteries that are used for automotive starting,
lighting, ignition and powering vehicular accessories. SLI batteries are designed to
produce high power in short bursts for cranking. SLI batteries use lots of thin plates
to maximize the surface area of the battery for providing very large bursts of current
(also specied as Cranking Amps). This allows very high starting current but causes the
plates to warp when the battery is cycled. Vehicle starting typically discharges 1%-
3% of a healthy SLI battery’s capacity. The automotive SLI battery is not designed for
repeated deep discharge where up to 80 % of the battery capacity is discharged and
then recharged. If an SLI battery is used for this type of deep discharge application,
its useful service life will be drastically reduced.

19
3
GENERAL INFORMATION: BATTERIEs
This type of battery is not recommended for the storage of energy for inverter
applications. However, they are recommended as starting battery for the back-up
generator.
Deep Cycle Lead Acid Batteries
Deep cycle batteries are designed with thick-plate electrodes to serve as primary
power sources, to have a constant discharge rate, to have the capability to be deeply
discharged up to 80 % capacity and to repeatedly accept recharging. They are
marketed for use in recreation vehicles (RV), boats and electric golf carts – so they may
be referred to as RV batteries, marine batteries or golf cart batteries.
Units of Battery Capacity – Ampere Hours (AH) and Reserve Minutes (RC)
The battery capacity is the measure of the electrical energy the battery can store
and deliver to a load. It is determined by the amount of current any given battery can
deliver over a stipulated period of time. The energy rating is expressed in Ampere
Hours (AH). As a bench mark, the battery industry rates batteries at 20 Hour rate i.e.,
the number of Amperes of current the battery can deliver for 20 Hours at 80 ºF (26.7 ºC) till
the voltage drops to 10.5 Volts for 12 V battery and 21 V for 24 V battery. For example,
a 100 AH battery will deliver 5 Amperes for 20 Hours.
Battery capacity is also expressed as Reserve Capacity (RC) in minutes. Reserve
capacity is the time in minutes for which the battery can deliver 25 Amperes at 80 ºF
(26.7 ºC) till the voltage drops to 10.5 Volts for 12 V battery and 21 V for 24 V battery.
Approximate relationship between the two units is as follows:
Capacity in AH = Reserve Capacity in RC minutes x 0.6
Typical Battery Sizes
The Table below shows details of some popular battery sizes:
BCI* GROUP BATTERY VOLTAGE, V BATTERY CAPACITY, AH
27 / 31 12 105
4 D 12 160
8D 12 225
GC2** 6 220
* Battery Council International ** Golf Cart
Table 3.1. Popular Battery Sizes

20
3
GENERAL INFORMATION: BATTERIEs
Reduction in Usable Capacity at Higher Discharge Rates
As stated above, the rated capacity of the battery in AH is normally applicable at
a discharge rate of 20 Hours. As the discharge rate is increased, the usable capacity
reduces due to “Peukert Effect”. This relationship is not linear but is more or less
according to the Table below:
HOURS OF DISCHARGE USABLE CAPACITY
20 100 %
10 87 %
8 83 %
675 %
5 70 %
3 60 %
2 50 %
1 40 %
Table 3.2. Battery Capacity versus Rate of Discharge
Using the above Table will show that a 100 AH capacity battery will deliver 100% (i.e.
full 100 AH) capacity if it is slowly discharged over 20 hours at the rate of 5 Amperes.
However, if it is discharged at a rate of 50 Amperes then theoretically, it should
provide 100 AH ÷ 50 = 2 hours. However, the Table above shows that for 2 hours
discharge rate, the capacity is reduced to 50% (i.e. 50 AH). Therefore, at 50 Ampere
discharge rate the battery will actually last for 50 AH ÷ 50 Amperes = 1 Hour.
State of Charge (SOC) of a Battery
The “Standing Voltage” of a battery can approximately indicate the State of Charge
(SOC) of the battery. The “Standing Voltage” is measured after disconnecting any
charging device(s) and the battery load(s) and letting the battery “stand” idle for 3
to 8 hours before the voltage measurement is taken. The Table 3.3 shows the State of
Charge versus Standing Voltage for a 12 volt battery system at around 80 ºF (26.7 ºC).
For 24-volt systems, multiply by 2; for 48-volt systems, multiply by 4.
Other manuals for SCC-30AB
1
Table of contents
Other samlexsolar Controllers manuals
Popular Controllers manuals by other brands

Samson
Samson 3375 Mounting and operating instructions
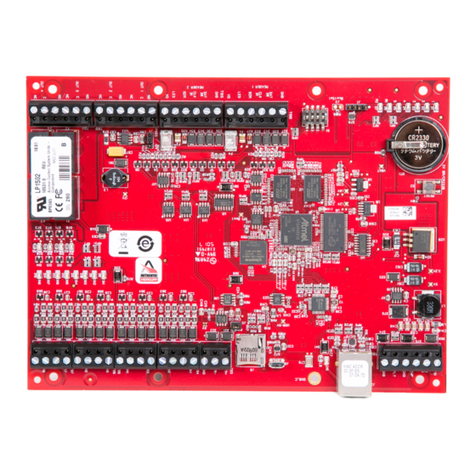
HID
HID Mercury LP1502 Installations and specifications
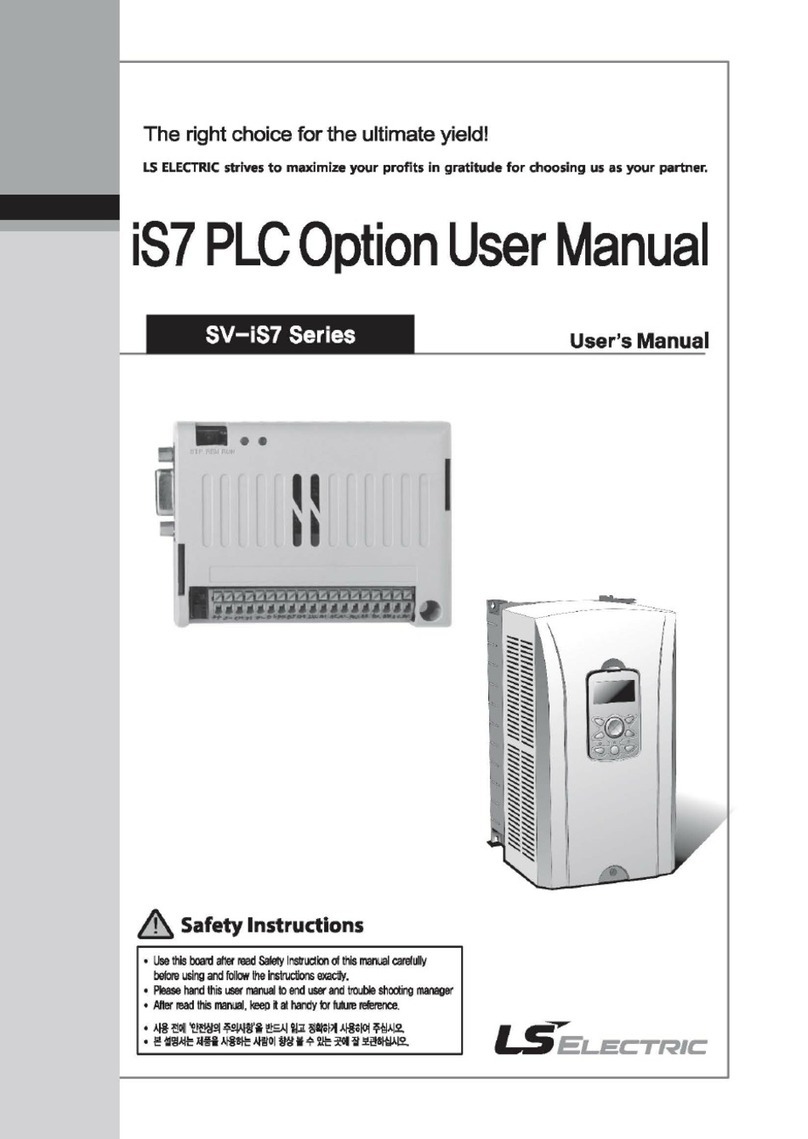
LS ELECTRIC
LS ELECTRIC SV-iS7 Series user manual
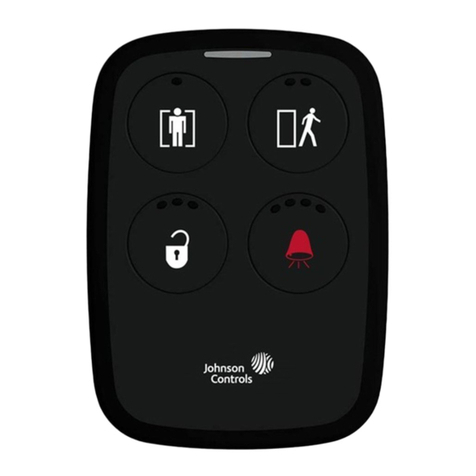
Johnson Controls
Johnson Controls ARC30 quick start guide
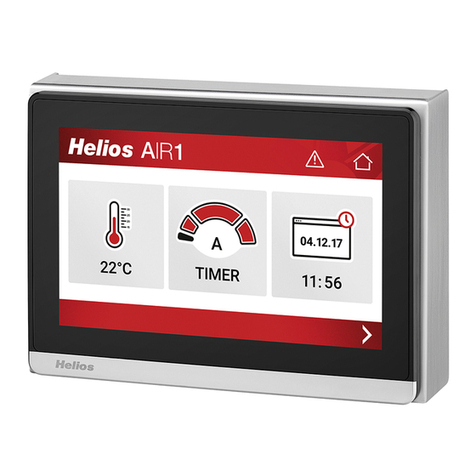
Helios
Helios AIR1-BE TOUCH Installation and operating instructions
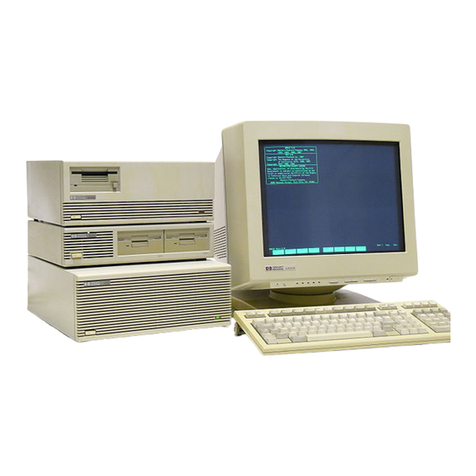
HP
HP 9000 Series 300 owner's guide