samlexsolar SCC-30AB User manual

30 Amp
Solar Charge
Controller
SCC-30AB
Owner's
Manual
Please read this
manual before
operating your
charge controller.

2
1. Safety Instructions .............................................................................................. 3
2. General Description of PV / Solar System .......................................................... 5
3. General information - Batteries ...................................................................... 15
4. Introduction and Features ............................................................................... 24
5. Construction, Layout and Controls .................................................................. 30
6. Installation and Operation .............................................................................. 34
7. Troubleshooting ............................................................................................... 41
8. Specications .................................................................................................... 43
9. Warranty ........................................................................................................... 44
INDEX

3
1
SAFETY INSTRUCTIONS
Please read these instructions before installing or operating the Charge Controller to
prevent personal injury or damage to the Charge Controller.
General
Installation and wiring compliance
• Installation and wiring must comply with the local and National Electrical
Codes and must be done by a certied electrician.
Preventing electrical shock
• The negative system conductor should be properly grounded. Grounding
should comply with local codes.
• Disassembly / repair should be carried out by qualied personnel only.
• Disconnect all input and output side connections before working on any
circuits associated with the Charge Controller. Turning the on/off control on
the Charge Controller to off position may not entirely remove dangerous
voltages.
• Be careful when touching bare terminals of capacitors. The capacitors may
retain high lethal voltages even after the power has been removed. Discharge
the capacitors before working on the circuits.
Installation environment
• The Charge Controller should be installed indoor only in a well ventilated,
cool, dry environment
• Do not expose to moisture, rain, snow or liquids of any type.
Preventing re and explosion hazards
• Working with the Charge Controller may produce arcs or sparks. Thus, the
Charge Controller should not be used in areas where there are inammable
materials or gases requiring ignition protected equip ment. These areas may
include spaces containing gasoline powered machinery, fuel tanks, battery
compartments.
Precautions when working with batteries
• Batteries contain very corrosive diluted sulphuric acid as electrolyte.
Precautions should be taken to prevent contact with skin, eyes or clothing.
• Batteries generate hydrogen and oxygen during charging resulting in
evolution of explosive gas mixture. Care should be taken to ventilate the
battery area and follow the battery manufacturer’s recommendations.
• Never smoke or allow a spark or ame near the batteries.

4
1
SAFETY INSTRUCTIONS
• Use caution to reduce the risk of dropping a metal tool on the battery. It could
spark or short circuit the battery or other electrical parts and could cause an
explosion.
• Remove metal items like rings, bracelets and watches when working with
batteries. The batteries can produce a short circuit current high enough to weld a
ring or the like to metal and thus cause a severe burn.
• If you need to remove a battery, always remove the ground terminal from the
battery rst. Make sure that all the accessories are off so that you do not cause a
spark.
Charge Controller related
• It is to be ensured that the input voltage fed to the Charge Controller does not
exceed 50 VDC to prevent permanent damage to the Charge Controller. Ensure
that the maximum Open Circuit Voltage Voc of the 12 V nominal Solar Panel /
the Solar Array is less than 50 V. If two 12 V nominal Solar Panels are being used
in series to make a 24 V nominal Solar Array, make sure that the maximum Open
Circuit Voltage Voc of each of the 12 V Panels is less than 25 V.
• Do not exceed the maximum current rating of 30 A. The Short Circuit Current of
the Solar Array should be less than 30 A
• Do not exceed a battery voltage of 24V (nominal) . Do not use a battery less than
12V.
• Charge only 12, or 24 volt Lead-Acid batteries when using the standard battery
charging programs or Ni-Cd batteries when DIP Switch number 2~4 is in the ON
position.
• DO NOT short circuit the PV array or load while connected to the controller. This
will damage the controller.
• The controller should be protected from direct sunlight. Ensure adequate space
for air ow around the controller’s face plate.
• Do not install in a sealed compartment with batteries.
• Never allow the solar array to be connected to the controller with the battery
disconnected. This can be a dangerous condition with high open-circuit solar
voltage present at the terminals.
• Use only copper wire with minimum 75°C insulation rating and between 10 AWG
(5.2 mm2) and 14 AWG (2.1 mm2) gauge.
• The Negative system conductor should be properly grounded. Grounding should
comply with local codes.

5
2
GENERAL DESCRIPTION OF PV / SOLAR SYSTEM
What is Photovoltaic (PV)?
The word ‘photo-voltaic’ is derived from two different words; the word ‘photos’,
from the Greek, meaning light and the word ‘voltaic’ developed from the name of the
Italian scientist, Volta, who studied electricity. This explains what a PV system does: it
converts light energy from the sun into electrical energy.
What is in a Photovoltaic (PV) system?
Non Grid-tied PV / Solar System
PV/Solar Panel (Module) or Array
Charge Controller
Battery
DC-AC Power Inverter
To AC
Loads
Solar Array
Charge
Controller/Protection
DC-AC Power Inverter
To AC
Loads
Power to
and from grid
Two-way Metering
Fig. 2.1. Non Grid-tied PV System–Block Diagram
Fig. 2.1 shows a Block Diagram of a typical non-grid tied Photovoltaic (PV) System
with its main components. It consists of a PV / Solar Panel (Module), Charge Controller,
Batteries and Power Inverter. The PV / Solar Panel (Module) or Array converts the
solar light energy into DC electrical energy. The Charge Controller conditions the DC
electrical voltage and current produced by the PV / Solar Panel (Module) or Array to
charge a battery. The battery stores the DC electrical energy so that it can be used
when there is no solar energy available (night time, cloudy days etc). DC loads can be
powered directly from the PV / Solar Panel (Module) / Battery. The inverter converts
the DC power produced by the PV / Solar Panel (Module) / stored in the battery into
AC power to enable powering of AC loads.

6
2
GENERAL DESCRIPTION OF PV / SOLAR SYSTEM
Grid-tied PV / Solar System
Fig. 2.2 shows a Block Diagram of a typical Grid-tied PV / Solar System. In this system,
the Solar Panels (Modules) / Arrays directly feed to an inverter and the inverter is
connected to an Electricity Transmission and Distribution System (referred to as the
Electricity Grid) such that the system can draw on the Grid’s reserve capacity in times
of need, and feed electricity back into the Grid during times of excess production.
PV/Solar Panel (Module) or Array
Charge Controller
Battery
DC-AC Power Inverter
To AC
Loads
Solar Array
Charge
Controller/Protection
DC-AC Power Inverter
To AC
Loads
Power to
and from grid
Two-way Metering
Fig. 2.2 Grid-tied PV / Solar System – Block Diagram
In order to safely transmit electricity to your loads and to comply with your power
provider’s grid-connection requirements, you may need the following additional
items:
• Power conditioning equipment
• Safety equipment
• Meters and instrumentation.

7
2
GENERAL DESCRIPTION OF PV / SOLAR SYSTEM
PV / Solar Cell
12cm
Fig. 2.3. PV / Solar Cell
The basic element of a PV System is the photovoltaic (PV) cell, also called a Solar Cell.
An example of a PV / Solar Cell made of Mono-crystalline Silicon is shown in Fig. 2.3.
This single PV / Solar Cell is like a square but with its four corners missing (it is made
this way!).
Theory of Operation of PV / Solar Cell
Sunlight (photons)
External circuit
Encapsulate seal
Top electrical contact
P-Type material
(Boran-doped Silicon)
N-Type material
(Phosphorous-doped Silicon)
P/N junction
Base contact
Figure 2.4: Construction and Working of PV / Solar Cell
A PV / Solar Cell is a semiconductor device that can convert solar energy into DC
electricity through the “Photovoltaic Effect” (Conversion of solar light energy into
electrical energy). When light shines on a PV / Solar Cell, it may be reected, absorbed,
or passes right through. But only the absorbed light generates electricity.

8
2
GENERAL DESCRIPTION OF PV / SOLAR SYSTEM
When light enters the PV / Solar Cell, some of the “Photons” (packets of electro-
magnetic wave energy) from the light energy are absorbed by the semiconductor
atoms. The energy of the absorbed light is transferred to the negatively charged
electrons in the atoms of the solar cell. With their newfound energy, these electrons
escape from their normal positions in the atoms of the semiconductor photovoltaic
material and become part of the electrical ow, or current, in an electrical circuit. A
special electrical property of the PV / Solar Cell – a built-in electric eld – provides the
force, or voltage, needed to drive the current through an external load, such as a
light bulb.
To induce the built-in electric eld within a PV / Solar Cell, two layers of somewhat
differing semiconductor materials are placed in contact with one another (See Fig. 2.4).
One layer is an N-type semiconductor (e.g. Phosphorus doped Silicon) with an abundance
of “Electrons”, which have a Negative electrical charge. The other layer is a P-type
semiconductor (e.g. Boron doped Silicon) with an abundance of” Holes”, which have a
Positive electrical charge.
Although both materials are electrically neutral, N-type silicon has excess Electrons and
P-type silicon has excess Holes. Sandwiching these together creates a P-N Junction at their
interface, thereby creating an electric eld.
When N-type and P-type silicon come into contact, excess electrons move from the
N-type side to the P-type side. The result is a buildup of Positive charge along the
N-type side of the interface and a buildup of Negative charge along the P-type side.
Because of the ow of electrons and holes, the two semiconductors behave like a battery,
creating an electric eld at the surface where they meet – the P/N Junction. The electrical
eld causes the electrons to move from the semiconductor toward the Negative surface,
where they become available to the electrical circuit. At the same time, the Holes move in
the opposite direction, toward the positive surface, where they await incoming electrons.
The electrical current is fed to the external load through the top electrical contact surface
(normally in the form of a grid) and the bottom base contact.
The Open Circuit Voltage Voc of a PV /Solar Cell is just under 0.6 V
Factors Affecting Voltage and Current Output of the PV / Solar Cell
The amount of electric current generated by photon excitation in a PV / Solar Cell at
a given temperature is affected by the incident light in two ways:
• By the intensity of the incident light.
• By the wavelength of the incident rays.

9
2
GENERAL DESCRIPTION OF PV / SOLAR SYSTEM
The materials used in PV / Solar Cells have different spectral responses to incident
light, and exhibit a varying sensitivity with respect to the absorption of photons at
given wavelengths.Each semiconductor material will have an incident radiation
threshold frequency, below which no electrons will be subjected to the photovoltaic
effect. Above the threshold frequency, the kinetic energy of the emitted
photoelectron varies according to the wavelength of the incident radiation, but
has no relation to the light intensity. Increasing light intensity will proportionally
increase the rate of photoelectron emission in the photovoltaic material. In actual
applications, the light absorbed by a PV cell will be a combination of direct solar
radiation, as well as diffused light bounced off of surrounding surfaces. PV / Solar
Cells are usually coated with anti-reective material so that they absorb the maximum
amount of radiation possible.
The output current of the PV / Solar Panel (Module) can increase due to what is
known as the “Edge of the Cloud Effect”. As the sun moves into a hole between the
clouds, your solar panels will see full direct sunlight combined with reected light
from the clouds! They will absorb more energy than they could on a cloudless day!
Thus, a factor of 1.25 times the Short Circuit Current Isc is recommended when sizing
the current capacity of the Charge Controller
The output current of the PV / Solar Cell has a positive Temperature Coefcient – The
output current increases with the rise of temperature. However, it is negligible – less
than 0.1 % / °C of the Short Circuit Current Isc
The output voltage of the PV / Solar Cell has a Negative Temperature Coefcient –
The output voltage increases with decrease in temperature. For example, a Silicon
Cell has a Temperature Coefcient of – 2.3 mV / °C / Cell. Hence, during cold winter
days, the voltage will rise. Hence, as a Thumb Rule, the voltage rating of the Charge
Controller should be sized as 1.25 times the Open Circuit Voltage rating Voc of the PV
/ Solar Panel (Module) to ensure that the Charge Controller is not damaged due to
over-voltage.

10
2
GENERAL DESCRIPTION OF PV / SOLAR SYSTEM
PV Cell Types
PV cells are most commonly made of Silicon, and come in two varieties, crystalline and
thin-lm type, as detailed in Table 2.1
Cell types include Mono-crystalline Silicon, Poly-crystalline Silicon, Amorphous Silicon
(a-Si), Gallium Arsenide (GaAs), Copper Indium Diselenide (CuInSe2, „CIS“), Cadmium
Telluride, or a combination of two materials in a tandem cell.
Bulk type / Wafer-based (Crystalline)
Mono Crystalline Si Poly Crystalline Si Poly Crystalline Band
Pros High efciency High efciency with
respect to price -
Cons Increased manufacturing cost caused by the
supply shortage of silicon -
Thin lm type
Amorphous Si CIGS CdTe Polymer organic
Pros Low price
Low price
Able to automate
all manufacturing
process
Low manufacturing
Can be more efcient
(still in research)
Cons Low efciency Low efciency
Table 2.1 PV Cell Types
PV Module / Panel and PV Array
To increase their utility, a number of individual PV cells are interconnected together
in a sealed, weatherproof package called a Panel (Module). For example, a 12 V Panel
(Module) will have 36 cells connected in series and a 24 V Panel (Module) will have 72
PV Cells connected in series
To achieve the desired voltage and current, Modules are wired in series and parallel
into what is called a PV Array. The exibility of the modular PV system allows
designers to create solar power systems that can meet a wide variety of electrical
needs. Fig. 2.5 shows PV cell, Panel (Module) and Array.

11
2
GENERAL DESCRIPTION OF PV / SOLAR SYSTEM
Cell
Module
Array
Figure 2.5. PV cell, Module and Array
The cells are very thin and fragile so they are sandwiched between a transparent
front sheet, usually glass, and a backing sheet, usually glass or a type of tough plastic.
This protects them from breakage and from the weather. An aluminum frame is tted
around the module to enable easy xing to a support structure.
The picture in Fig. 2.6 shows a small part of a Module with cells in it. It has a glass
front, a backing plate and a frame around it.
Aluminum
frame
Glass
front
Backing
Sheet
PV Cell
Fig. 2.6. Construction of a typical Mono-crystalline PV / Solar Panel

12
2
GENERAL DESCRIPTION OF PV / SOLAR SYSTEM
Bypass Diodes
As mentioned, PV / Solar cells are wired in series and in parallel to form a PV / Solar
Panel (Module). The number of series cells indicates the voltage of the Panel (Module),
whereas the number of parallel cells indicates the current. If many cells are connected
in series, shading of individual cells can lead to the destruction of the shaded cell or of
the lamination material, so the Panel (Module) may blister and burst. To avoid such an
operational condition, Bypass Diodes are connected anti-parallel to the solar cells as in
Fig. 2.7. As a consequence, larger voltage differences cannot arise in the reverse-current
direction of the solar cells. In practice, it is sufcient to connect one bypass diode for
every 15-20 cells. Bypass diodes also allow current to ow through the PV module when
it is partially shaded, even if at a reduced voltage and power. Bypass diodes do not cause
any losses, because under normal operation, current does not ow through them.
+-
load
bypass diodes
A K
Figure 2.7: Parallel PV cell with bypass diodes
Current (I), Voltage (V) and Power (P) Curves of a PV / Solar
Panel (Module) and how the PV / Solar Panel (Module) is rated -
Voc , Vmp , Isc , Imp , Pmax
Fig. 2.8 Current (I), Voltage (V) and Power (P) Curves

13
2
GENERAL DESCRIPTION OF PV/SOLAR SYSTEM
A Current (I) versus Voltage (V) Curve of a PV / Solar Module (“I-V” Curve) shows the
possible combinations of its current and voltage outputs. A typical I-V curve for a 12 V
Module is shown at Fig. 2.8.
The power in a DC electrical circuit is the product of the voltage and the current.
Mathematically,
• Power (P) in Watts (W) = The Current (I) in Amperes (A) X the Voltage (V) in Volts
(V) i.e. W = V X A
A PV / Solar Cell or a Panel (Module) produces its maximum current when there is
no resistance in the circuit, i.e. when there is a short circuit between its Positive and
Negative terminals. This maximum current is known as the Short Circuit Current and is
abbreviated as Isc. When the Cell / Panel (Module) is shorted, the voltage in the circuit
is zero.
Conversely, the maximum voltage occurs when there is a break in the circuit. This is
called the Open Circuit Voltage (Voc). Under this condition, the resistance is innitely
high and there is no current, since the circuit is incomplete. Typical value of the open-
circuit voltage is located about 0.5 – 0.6 V for Crystalline Cells and 0.6 – 0.9 V for
Amorphous Cells.
These two extremes in load resistance, and the whole range of conditions in between
them, are depicted on the I-V Curve. Current, expressed in Amps, is on the vertical
Y-axis. Voltage, in Volts, is on the horizontal X-axis.
The power available from a photovoltaic device at any point along the curve is just
the product of Current (I) in Amps (A) and Voltage (V) in Volts (V) at that point and is
expressed in Watts. At the short circuit current point, the power output is zero, since
the voltage is zero. At the open circuit voltage point, the power output is also zero, but
this time it is because the current is zero.
Maximum Power Point and Rated Power of PV / Solar Panel (Module)
There is a point on the knee of the I-V Curve where the maximum power output
is located and this point is called the Maximum Power Point (MPP). The voltage and
current at this Maximum Power Point are designated as Vmp and Imp.
The values of Vmp and Imp can be estimated from Voc and Isc as follows:
Vmp ≈ (0.75 – 0.9) Voc
Imp ≈ (0.85 – 0.95) Isc

14
2
GENERAL DESCRIPTION OF PV/SOLAR SYSTEM
The rated power of the PV / Solar Module in Watts (Pmax) is derived from the above
values of voltage Vmp and current Imp at this Maximum Power Point (MPP):
• Rated power in Watts, Pmax = Vmp X Imp
Example of I-V Curve and Ratings of a 12 V PV / Solar Panel
Fig. 2.9. Example of I-V Curve and Ratings of a 12 V PV / Solar Panel
The I-V Curve for a typical 12 Volt PV / Solar Panel is shown in Fig. 2.9.
This Maximum Power Point in the example curve given above is where Vmp is 17 Volts,
and the current Imp is 2.5 amps. Therefore, the rated or the maximum power Wmax in
watts is 17 Volts times 2.5 Amps, or 42.5 Watts.
Standard Test Conditions (STC) for Specifying PV / Solar Modules
The I-V curve is also used to compare the performance of PV / Solar Modules.
The curve is, therefore, generated based on the performance under Standard Test
Conditions (STC) of sunlight and device temperature of 25 °C. It assumes there is
no shading on the device. Standard sunlight conditions on a clear day are assumed
to be 1,000 Watts of solar energy per square meter (1000 W/m2 or 1 kW/m2). This is
sometimes called one sun, or a peak sun. Less than one sun will reduce the current
output of the PV device by a proportional amount. For example, if only one-half sun
(500 W/m2) is available, the amount of output current is roughly cut in half.

15
3
GENERAL INFORMATION: BATTERIES
Types of Batteries
There are several different types of battery chemistry including liquid Lead-Acid,
Nickel-Iron (NiFe), Nickel-Cadmium (Ni-Cd), alkaline, and gel-cell. Batteries are either
sealed or vented. Simply, there are only two principal types of batteries: starting and
deep-cycle.
Starting batteries are designed for high cranking power, but not for deep cycling.
Used as energy storage, they will not last long in a deep cycle application. Starting
batteries use lots of thin plates to maximize the surface area of the battery. This allows
very high starting current but lets the plates warp when the battery is cycled. This
type of battery is not recommended for the storage of energy in solar applications.
However, they are recommended as starting battery for the back-up generator.
Deep cycle batteries are the type of battery best suited for use with inverters. The
physical dimension of the plates is thicker and the active material that holds the
charge is denser to increase cycle life. The “deep cycle” type of battery is designed to
have the majority of their capacity used before being recharged. They are available in
many sizes and in either “non-sealed” or “sealed” types.
Usual battery inverters are optimized for use with lead acid batteries that have
a nominal voltage of 2.0 volts per cell. Ni-Cd/NiFe batteries (also called alkaline
batteries) have a nominal cell voltage of 1.2 volts per cell. The nominal voltage of a
Ni-Cd / NiFe battery bank can be made the same as a lead acid bank just by juggling
the number of cells (10 cells for 12 volts, 20 cells for 24 volts and 40 cells for 48 volt
systems). However, the Ni-Cd/NiFe battery bank must be charged to a higher voltage
to fully recharge and will drop to a lower voltage during discharging compared to a
similarly sized lead acid type battery.
State of Charge (SOC) of the Battery
One important parameter that denes the energy content of the battery is the State
of Charge (SOC). This parameter indicates how much charge is available in the battery
referring to its capacity. It is the ratio of the difference of the rated capacity in Ampere
Hours (Ah) and the net Ah discharged or charged since the last full SOC. For example,
in a 100Ah capacity battery, if the net Ah discharged is 20 Ah, then the SOC is 80% ie
(100 Ah – 20 Ah) divided by 100 Ah. SOC is also called Residual Capacity.
Generally, the voltage of the battery cell is taken as the basis for calculating SOC
or the remaining capacity. Results can vary widely depending on actual voltage
level, temperature, discharge rate and the age of the cell and compensation for
these factors must be provided to achieve a reasonable accuracy. Fig 3.1 shows the
relationship between the Open Circuit Voltage and the Residual Capacity at constant

16
3
GENERAL INFORMATION: BATTERIES
temperature and discharge rate for a high capacity Lead Acid cell. Note that the cell
voltage diminishes in direct proportion to the remaining capacity.
Fig 3.1 SOC versus Open Circuit voltage
The Lead-Acid Batteries
A basic equivalent circuit of the Lead-Acid battery is modeled by a voltage source
with an equilibrium voltage (VE) in series with an internal resistor (Rin) (see Fig 3.2). It
must be noted here that this conguration can describe only a current state because
the magnitude of VE and Rin are not actually constant, but is function of many
parameters such as state of charge (SOC), temperature, current density, and aging of
the battery.
VB
Vin
IB
Rin
VERload
VB
VB
Vin
IB
IB
Rin
Rin
VE
VERload
Rload
Fig 3.2. Basic equivalent circuit of the Lead-Acid battery for a current state

17
3
GENERAL INFORMATION: BATTERIES
Furthermore, it is to consider that these parameters depend also on the current
direction (charging or discharge). When the battery were at rest or under open-circuit
condition VB = VE. When current is drawn from the battery, the voltage will be lower
than VE. When current is owing into the battery, the terminal voltage will be higher
than VE. For example, at each moment during discharge phase the terminal voltage
can be derived as follow:
VB =VE – Vin (3.1)
=VE – Rin× IB (3.2)
where: VB
= terminal voltage [V]
VE = equilibrium voltage [V]
Vin = internal loss voltage [V]
Rin = internal resistance [Ω]
IB = discharge current [A]
Obviously, higher discharge current results in reduction of the terminal voltage.
Therefore, to specify the state of the battery by the battery voltage, discharge current
should be also measured.
In case of discharge, the minimum voltage level acceptable for a Lead-Acid battery
is dened as discharge voltage threshold. Falling below this threshold is called deep
discharge, with which the battery may suffer damage. In case that the battery is
left longer after deep discharge, lead of the support structure is converted to lead-
sulphate in rough-crystalline form, which during charging can be only bad or cannot
be converted again anymore. As a result, the battery loses a part of its storage
capacity; besides loss of support structure arises as well.
In practice, harmful deep discharge is to be prevented: the loads will be compulsory
disconnected from battery as soon as the discharge voltage threshold is reached
i.e. with the help of a so-called deep discharge protection (DDP). This threshold is
basically given in the data sheets by the manufacturer for different discharge currents.
Preferably, the value of this threshold should depend on the discharge current. The
relation between the discharge current and the voltage during discharge for the Lead-
Acid battery is presented in Figure 3.3.

18
3
GENERAL INFORMATION: BATTERIES
Fig 3.3: Discharge characteristic curves
Figure 3.3 shows the discharge prole of a typical battery type at several constant
current rates. The typical end-of-discharge voltage at these discharge rates can
also be noticed where the voltage starts to drop steeply. Moreover, the end-of-
discharge voltage varies between 1.75-1.9 V, depending on the battery type and the
discharge current. Higher service capacity is obtained at the lower discharge rates.
At higher discharge rates, the electrolyte in the pore structure of the plate becomes
depleted, and it cannot diffuse rapidly enough to maintain the cell voltage. However,
intermittent discharge, which allows time for electrolyte diffusion will improve the
performance under high discharge rates
Gassing
With 2.3 V – 2.4 V, namely the so-called Gassing Voltage, gas is developed at the
electrodes in the battery, by which the water is decomposed into hydrogen (H2)
and oxygen(O2). Both gases mix together in the battery providing detonating gas
(explosive!) and escape through ventilation opening in the vent plug. With the
gassing, the battery also loses water, which must be relled according to maintenance
within regular intervals. The gas is the unwelcome secondary reaction of the chemical
conversion during charging because current is consumed for the electrolysis and,
therefore, the storage efciency of the battery is made worse unnecessarily.

19
3
GENERAL INFORMATION: BATTERIES
After the gassing voltage is exceeded, voltage stays approximately constant. The
whole charging current during this period results in H2 and O2, which is dened
as loss.
Freezing of electrolyte
For applications with low ambient temperature, the Lead-Acid battery must also be
protected against freezing of electrolyte. The risk of freezing depends on the state of
charge. Figure 3-4 illustrates the freezing limit as a function of the state of charge.
- 80°
- 60°
- 40°
- 20°
0°
0 20 40 60 80 100
State of charge [%]
Temperature [°C]
slushy until hard
- 80°
- 60°
- 40°
- 20°
0°
0 20 40 60 80 100
State of charge [%]
Temperature [°C]
slushy until hard
Figure 3-4: Freezing limit of a Lead-Acid battery dependent on the State of Charge
Cycle life of Lead-Acid batteries
The cycle life refers to a capability of the battery to withstand a certain number of
charge/discharge cycles of given Depth of Discharge (DOD). Since the lifetime of the
battery also depends on the average depth of discharge during cycling (expressed in
percentage (%) of rated capacity), the cycling capability may be more conveniently
expressed by multiplying this average depth of discharge by the battery lifetime
expressed in number of cycles. The result is called the Nominal Cycling Capability,
which is expressed as the number of equivalent 100 % nominal capacity cycles.
The starter battery typically has a low cycling capability of less than 100 nominal
cycles, which means that it is able to withstand for example 500 cycles of maximally
20 % depth of discharge. The battery appropriate for PV application requires a good
cycling capability of at least 500 nominal cycles, which means that it should be able to
withstand for example 1000 cycles of 50 % depth of discharge (Fig. 3-5).

20
3
GENERAL INFORMATION: BATTERIES
Figure 3-5: Cycle life as a function of deep of discharge
Battery capacity
Previously, the storage capacity of a battery is expressed in Ah (Ampere-hours)
showing how many hours a certain current can be taken from the charged battery
until the battery is discharged, i.e. until the battery voltage drops to the discharge
voltage threshold.
Nowadays, it might be more favorable to express a battery capacity in dischargeable
energy, namely Wh (Watt-hours) or kWh (kilowatt-hours). However, these two ways of
expressing the battery capacity are equivalent because they are related via the battery
voltage, i.e. Ah × V = Wh.
Unfortunately, the capacity of a battery is not a constant quantity, but depends
on the amount of discharge current. The manufacturers, therefore, give the rated
capacity of their batteries always with regard to a certain discharge current.
The so-called Rated Battery Capacity refers to the capacity of the battery under given
standard conditions: it is common practical to dene the rated capacity at 20 °C by
discharging the battery with a Rated Battery Current (I20), which refers usually to a
constant current, with which the battery will be completely discharged in 20 hours.
Some battery manufacturers indicate the 100-hour discharge capacity for batteries
intended for PV applications. When comparing such capacity, it should be remembered
that, for a given battery, the 100-hour capacity is always at least 15 % higher than the
20-hour capacity .
Table of contents
Other samlexsolar Controllers manuals
Popular Controllers manuals by other brands

Samson
Samson 3375 Mounting and operating instructions
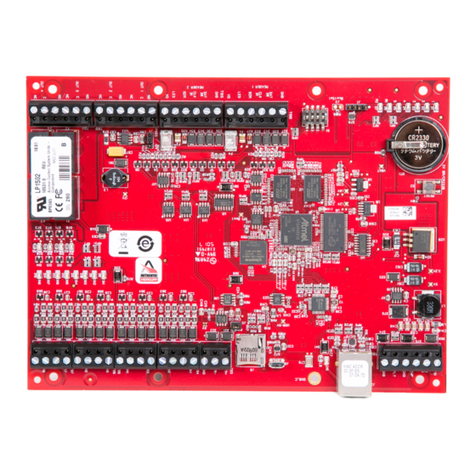
HID
HID Mercury LP1502 Installations and specifications
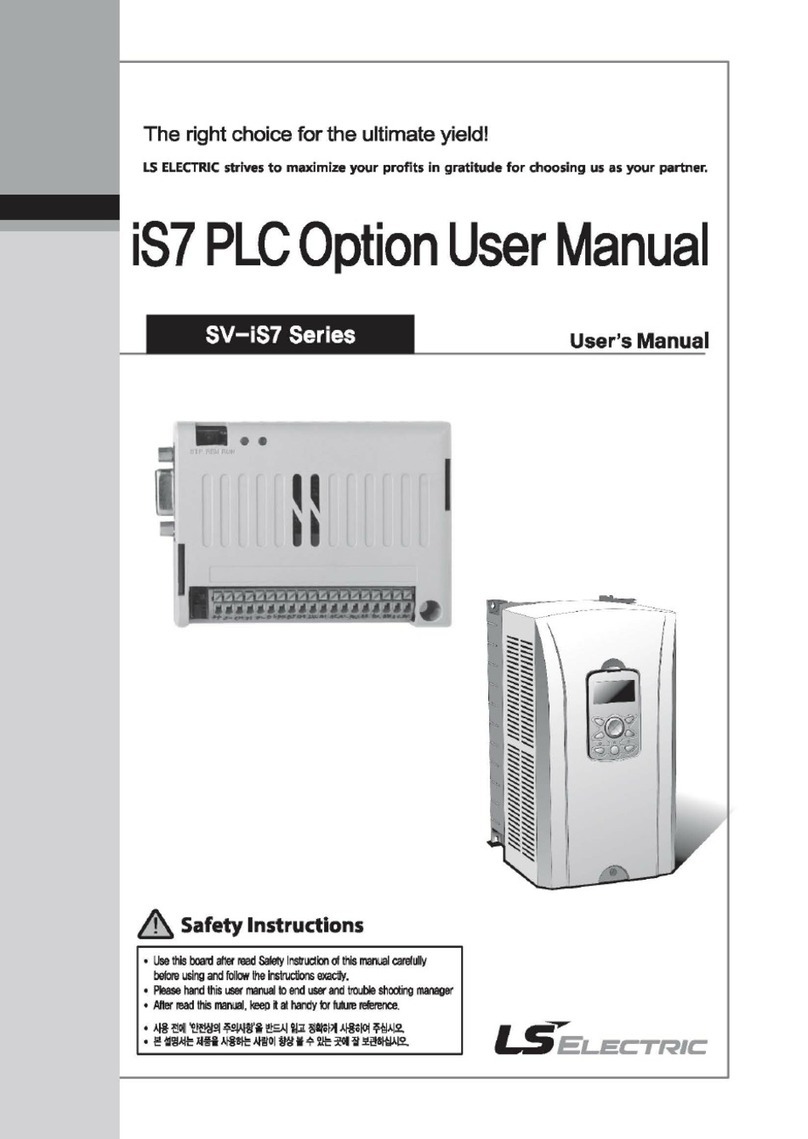
LS ELECTRIC
LS ELECTRIC SV-iS7 Series user manual
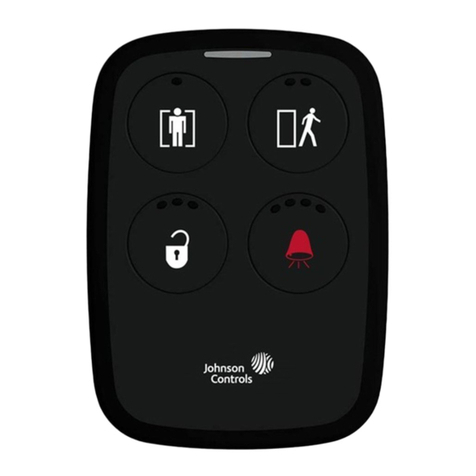
Johnson Controls
Johnson Controls ARC30 quick start guide
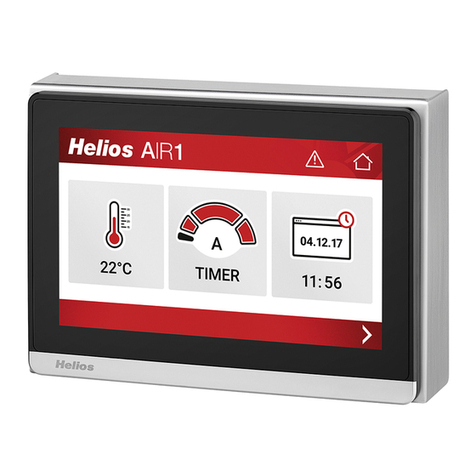
Helios
Helios AIR1-BE TOUCH Installation and operating instructions
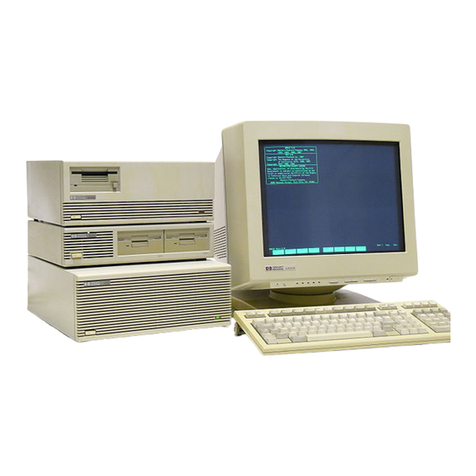
HP
HP 9000 Series 300 owner's guide