SANKI MFC-S3B-F User manual

Electromagnetic Feeder Controller
Instruction Manual
【Standard + Feedback Type】
MFC-S3B-F
MFC-S6B-F
This Instruction Manual is applicable to
Electromagnetic Feeder Controller version
1 and later.
Confirm the version information displayed
upon powering ON.
Read the Manual carefully beforehand to ensure the safe use of the Controller.
After reading, store the Manual within reach so as to be ready for rereading.
The dealer is requested to be sure to deliver the Manual to the end user.


1/ 32
Contents
1.Introduction 2
2.Before Using 2
3.Precautions for Safety 2
4.Name of Each Part 4
5.First-Time Use 6
6.Input/Output Connections 7
7.Operation Panel 12
7-1.Explanation of Operation Panel
7-2.Displayed Mode
7-3.Setting Function
7-4.Preparation for Operation
8.Operation and Amplitude Adjustment Method 16
9.Added Function 23
9-1.Soft start and soft stop functions
9-2.Overflow Sensor Timer Function
9-3.Operation Signal Delay Output Timer Function
9-4.Output Voltage Limit Setting
10.”io” Mode Setting Function 24
11.Remote Unit(RCU-3A)25
12.Parameter Setting Method 26
13.Guard and Alert 28
14.Troubleshooting 29
15.Options 29
16.Specifications 30
17.Outside Dimensional Drawing 31
18.Warranty 32

2/ 32
1. Introduction
Thank you for your selection of our Electromagnetic Feeder Controller, a digital controller for
electromagnetic feeder (“Controller”).
The electromagnetic feeder is a parts feeder that operates by using the mutual power of alternating
electromagnet and energy accumulated in the leaf spring.
In combination with the dedicated digital feedback controller, the Controller can be operated easily
and efficiently without requiring any difficult adjustment. Parts feeding speed may stably be
controlled by mounting a piezoelectric vibration sensor.
Before connecting the electromagnetic feeder and performing subsequent adjustment, read the
Manual carefully to ensure proper use of the excellent functions of the electromagnetic parts
feeder.
2. Before Using
Before unpacking, be careful not to have an impact or vibration on the packing.
Unpack, and check the following:
(1) Isn’t there any damage caused during transport?
(2) Are the rating, capacity and model on the nameplate exactly what you have ordered?
If there is any problem, contact the dealer.
3. Precautions for Safety
Be sure to read the Manual carefully before the installation, operation, maintenance, checkup, etc.
of the Controller to ensure your familiarity with the Controller, safety information and precautions.
In the Manual, the safety precautions are divided into “DANGER” and “CAUTION” according to
their severities.
DANGER
If the Controller is handled improperly, a dangerous situation could be
caused, and the possibility of death or injury is assumed.
CAUTION
If the Controller is handled improperly, a dangerous situation could be
caused, and the possibility of medium or minor injury or partial damage is
assumed.

3/ 32
DANGER
・Do not service the controller in the Power-ON status. To avoid an electric shock, be sure to turn
OFF the power supply before starting the service.
・Do not disassemble, remodel or repair the controller, or an electric shock, a fire or injury could be
caused. For repair, ask the dealer.
・Do not remove the front cover while the controller is in the Power-ON status, or an electric shock
could be caused.
・Do not put or insert anything in or into the controller, or an electric shock or a fire could be
caused.
・Do not use the controller near explosive or flammable gas, or a fire could be caused.
・Do not splash water or liquid, or an electric shock or a fire could be caused.
・If smoke, odor or abnormal noise is emitted or other abnormality is detected, shut down the
controller immediately. If the controller is used in the abnormal status, a fire could be caused.
contact the dealer.
・If the controller is not operated for a long time, shut down the controller. If the controller is left
live as it is, a fire could be caused.
・Connect the power cable and the output cable as instructed in the Manual to avoid an electric
shock and a fire.
・Do not forcedly bend, pull or pinch the power cable or the output cable, or an electric shock or a
fire could be caused.
・Ground the earth terminal and the ground prescribed portions without fail, or an electric shock
could be caused. When working on grounding to a high position or a shaky stand, because fall or
tumble could be caused conditionally, take measures to prevent fall or tumble.
・Do not conduct megger testing for any terminals other than the input terminal.
CAUTION
・Do not use the controller for an piezoelectric parts feeder or the like.
・Do not turn ON/OFF the power supply frequently, or failure could be caused.
・Do not start/stop the vibrator with an electromagnetic contactor or the like on the output side,
or failure could be caused.
・Do not perform welding work on the feeder side in the Power-ON status.
・Do not perform welding work on the feeder side when the feeder and the controller are in the
connected status.
・Do not remove the nameplate, the seal, or the like.
・When installing the controller, hold and fix it firmly and properly.
・Do not transport or carry the controller in the piled-up status, even in the packed status, or they
could fall, causing injury.
・Do not place the controller outdoors, in a humid place or in a place with excessive temperature
change.
・Do not pile up the controller two-tired or more, even in the packed status.
・When disposing of the controller, dispose it properly as general industrial waste.

4/ 32
4. Name of Each Part
Operation panel removed status
Relay output
terminal block (B)
Vibration sensor input cable
[P4 cord] (1m)
Dedicated cable for feedback
Power cable (1m)
Rubber bush
Operation panel fixing
screw (2 locations)
When attaching/detaching
the operation panel, carefully
watch out for disconnection,
pinching, etc.
Overflow sensor input cable
[P3 cord] (0.1m)
Power,Output
terminal block
Operation panel
Operation panel
connecting wire
Operation panel
Output cable (1m)
External control
terminal block (S)
External control
terminal block (A) for
added function
Vibration sensor
connector
Earth

5/ 32
Terminal block No.
Wiring to the external signal terminal block (screw-less)
While holding down the button on the terminal block with a flat-blade screwdriver or similar,
insert the wire into the wire insertion hole. Then, detach the flat-blade screwdriver to release
the button, and the wire will be fixed.
Applicable wire size
・Terminal block (A), (S)
Stranded wire: AWG26 - 20
Solid wire: AWG26 - 20
Wire strip length: 10 –11mm
・Terminal block (B)
Stranded wire: AWG22 - 14
Solid wire: AWG22 - 14
Wire strip length: 9 –10mm
Terminal block (A)
Signal name
Wire insertion hole
Lever
Board side connector for P4 cord
[Connected]
Terminal block (S)
Terminal block (B)
Output
Power

6/ 32
5. First-Time Use
Starting operation flow
Input/output connection
Power cable, Output cable
Vibration sensor
Overflow sensor
External signal
Solenoid valve,etc.
Parameter setting
Amplitude control
[in1] and [in2] input logic
Amplitude adjustment
Constant-voltage mode (0u = 0) Constant-amplitude mode (0u = 1)
↓
Feedback adjustment
Added function
Set the timer for soft start, sensor input and solenoid valve output.
Normal operation
Operation according to external signal and overflow sensor.

7/ 32
5. Input/Output Connections
1) Vibratory feeder drive connection
Confirm that the power supply is in the OFF status. Then, connect the output cable of the
controller to the feeder cable of the electromagnetic feeder.
The connector wire colors should be identified as follows:
※1: Do not connect to a piezo feeder.
※2: Do not operate with no load.
※3: Be sure to ground the feeder.
2) Power source connection
Connect the power cable to the single-phase power source.
Do not turn ON the power supply until the whole wiring work is completed.
※1: Be sure to connect to the utility power source.
※2: Adjust the input voltage to the rated voltage of the vibrator.
※3: Be sure to ground the controller.
※4: Do not perform the ON/OFF control on the input power supply side.
3) Vibration sensor connection
Connect the vibration sensor to perform constant amplitude control.
(1) Mounting of vibration sensor
Fix the vibration sensor (Accessory) onto the top of the vibrating body of the feeder or the
horizontal surface of the vibration part of the bowl chute or the like (in such a way that the
arrow printed on the sensor looks horizontal) with M4 bolt. In mounting the vibration sensor,
be careful not to allow the vibration sensor body and the feeder cable to interfere with other
parts. In determining the mounting direction of the vibration sensor, it should be noted that the
lead wire side of the vibration sensor corresponds to the parts transfer direction.
100-120VAC
200-240VAC
Lead wire
Feeder cable
Black
White
Electromagnetic
feeder
Mounting of
vibration sensor
Horizontal surface of
vibration part
Overflow sensor
Vibration sensor (KS-3)
[Accessory]
Parts transfer direction

8/ 32
(2) Connection of the vibration sensor
Connect the vibration sensor input cable (P4 cord) of the Controller to the Vibration Sensor
(KS-3).
※1. The vibration sensor input cable (P4 cord) is connected to the on-board connector. To
replace the input cable, replace it by a dedicated cable at the on-board connector.
Confirm the power-OFF status, and then detach the operation panel.
Note that the operation panel is connected to the controller main body with a connecting
wire. When attaching/detaching the operation panel, carefully watch out for the
connecting wire to avoid disconnection or pinching.
※2. Limit the total length of the cable between the controller and the feeder (vibration sensor)
to 4m.
To extend the cable, be sure to use the dedicated cable of our make.
In wiring each cable, detach the wiring from the power cable.
4) Overflow sensor [in2 input] connection
Connect the overflow sensor to the terminal of the overflow sensor input cable (P3 cord).
The connection enabled sensor can use the NPN open collector output.
(The PNP open collector output sensor cannot be connected.)
※1. The input cable (P3 cord) of the overflow sensor is connected to the terminal block [in2
Input].
※2. When the overflow sensor is not connected, set as “Parameter No. 07=Lo.”
※3. The power outlet of the Controller is of 24VDC, 160mA. Watch out for the total
consumption current of the overflow sensor, solenoid valve, etc. to ensure that it will not
exceed the power outlet capacity.
[Terminal connector signal name of P3 cord] Internal circuit
Red [24V terminal No. A0] –Sensor brown wire
Black [0V terminal No. A6] –Sensor blue wire
White [Signal terminal No. A2] –Sensor black wire
Sensor: Black
Sensor: Blue
Sensor: Brown

9/ 32
5) External signal [in1 Input] connection
Connect the external signal to operate/stop the feeder in addition to the overflow sensor.
When the external signal is used, set parameter as “Parameter No. 06 = hi.”
※1. To connect the external signal, the operation panel should be removed.
Confirm that the power supply is in the OFF status. Then, detach the operation panel.
After the connection is completed, attach the operation panel, and then turn ON the power
supply.
The operation panel is connected to the main unit of the controller with a connecting wire.
When attaching/detaching the operation panel, carefully watch out for disconnection or
pinching.
To operate the start/stop of the controller according to external control signal, either method
of non-voltage contact signal or voltage signal (24VDC) can be used.
Make connection to the external control terminal block by using the method ①or ②below
while watching out for the signal to be used and the connection method. When wiring, be careful
not to make mistake about the polarity.
The current of 24VDC and 10mA or less flows between [S+] and [S-]. Carefully select the
connection device (e.g., minute current relay).
①No-voltage contact signal ②Voltage signal (24VDC)
[Relation between [in1 Input] and [in2 Input]]
①When [in1] is in the operating condition, [in2] is enabled.
②When both [in1] and [in2] are in the operating condition, the feeder starts operation.
Signal input status
Feeder operation condition
Setting: hi
Setting: Lo
in1 Input
Parameter No. 6
Connection ①:
Close
Connection ②:
24VDC
Operation condition
Stop
Connection ①:
Open
Connection ②:
0V
Stop
Operation condition
in2 Input
Parameter No. 7
Sensor signal: O N
Operation condition
Stop
Sensor signal: OFF
Stop
Operation condition
□: Default
Short circuit
No-voltage
contact
Example of circuit to be
arranged by customer
Internal circuit
Internal circuit
Example of circuit to be
arranged by customer

10 / 32
6) External output
(1) Operation signal output out1 [Relay contact output 250VAC, 3A]
Signal synchronous with the feeder output
(2) Operation signal output out4 [Open collector output 24VDC, 80mA or less]
Signal synchronous with the feeder output
(3) Operation signal delay output out3 [Open collector output 24VDC, 80mA or less]
According to the timer settings, ON rises up earlier than the feeder output, and OFF rises
behind the feeder output.
(4) Alarm signal, error signal output out2 [Relay contact output 250VAC, 3A]
When the parameter is set to “Parameter No. 08,” the function can be switched to the parts
shortage signal and error output.
①AL = Parts shortage signal: Outputted if [in2 input] continues for the set time (Parameter
No. 0n).
②Er = Error signal: Outputted if error stop (e.g., overcurrent error) is caused.
※1. The power outlet of the controller is of 24VDC, 160mA.
Watch out for the total consumption current of the overflow sensor, solenoid valve, etc. to
ensure that it will not exceed the power outlet capacity.

11 / 32
7) Speed switching function
The operation pattern can be switched by powering ON/OFF the external signal [in3 Input] in
the operation mode (“A” mode).
Operation mode
A
n
Operation patten No.
1
2
1
2
Display according to
external signal
out1
out2
out1
out2
Display according to
panel setting
Invalid
Invalid
P1
P2
in3 input status
OFF
ON
OFF
ON
※Patterns “P3” and “P4” shown on the display cannot be controlled by external signals.
a) Operation pattern switching method for each operation mode
(1) “A” mode
Turn ON/OFF the external signal [in3 Input].
(2) “n” mode
①Turn ON/OFF the external signal [in3 Input].
②Switch to P1/P2 in the panel setting.
b) Amplitude adjustment method for each operation pattern
①The amplitude is adjusted in the “n”mode.
②When the Func key is pressed 3 times, the PAT lamp blinks, displaying [out1].
③Each time the Freq▲key is pressed, the display changes in order of “P1”→“P2”→
“P3”→“P4”→“out1.”When the Freq▼key is pressed, the display changes in the
reverse order of the above.
④Press the Set key when “P2”is in display (to adjust the amplitude in the operation pattern
2).
※To switch the operation pattern to No. 2 according to the external signal, press the Set
key when “out1”is in display to turn [in3 Input] into the ON status.
⑤The PAT lamp lights up, and the voltage% is displayed.
⑥Adjust the amplitude by referring to “8. Operation and Amplitude Adjustment Method.”
⑦When the adjustment of both the patterns 1 and 2 is completed, start operation in the “A”
mode. In the “A” mode, the setting is forced to be switched to the external signal.
[Internal circuit]
Example of circuit to be
arranged by customer

12 / 32
7. Operation Panel
7-1. Explanation of Operation Panel
1) Pilot lamps
No
Name
Function
①
Data display
A 7-segment, 4-digit LED
Displays voltage, frequency, each settings and error codes.
②
Frequency pilot lamp
ON when the data display is showing frequency
③
Voltage % pilot lamp
ON when the data display is showing voltage
④
Operation pilot lamp
Indicates the output condition of the controller.
ON: The Controller is in operation under external control.
Blinking: The Controller is in forced operation by the ON/OFF key.
Long OFF and blinking: The Controller is at a forced stop by the
ON/OFF key.
⑤
Parameter mode pilot
lamp
ON: The parameter setting is in process.
Blinking: The speed magnification change setting is in process (only
for 0u:1 in the “A” mode).
⑥
Operation mode pilot
lamp
ON: “A” mode (operation)
OFF: “n” mode (adjustment)
Blinking: The function setting selection is in process.
⑦
Constant-amplitude
control pilot lamp
ON: Constant-amplitude control (for 0u:1 in the “A” mode)
OFF: Constant-voltage control (for 0u:0 in the “A” mode and the
“n”mode)
⑧
Frequency lock pilot
lamp
ON: The frequency is locked.
OFF: The frequency lock is released.
⑨
Operation pattern
setting pilot lamp
ON: Panel setting (only for setting in the “n” mode)
OFF: External signal setting
Blinking: The function setting selection is in process.

13 / 32
2) Operation keys
No
Name
Description
A
ON/OFF key
Performs forced operation and forced stopping.
B
Func key
Brief pressing: Switches the function setting.
Long pressing: Switches the mode between the parameter mode and the
normal mode.
C
Set key
Brief pressing: Changes and locks the data.
Long pressing: Saves the data (voltage, frequency, vibration quantity).
D
Vol ▲key
Normal mode: When pressed briefly when the frequency is being displayed,
the frequency display switches to the voltage display.
“A” mode; The voltage cannot be changed.
When the magnification change setting is uLoc, the
speed magnification can be changed.
“n” mode; Adjusts the output voltage.
Parameter mode: Selects the parameter No.
E
Vol ▼key
F
Freq ▲key
Normal mode: When pressed briefly when the voltage is being displayed,
the voltage display switches to the frequency display.
“A” mode; The frequency cannot be changed.
“n”mode; Adjusts the frequency.
Function setting is in display: Each function setting can be changed.
Parameter mode: Changes the parameter data.
G
Freq ▼key
*Long pressing: Continually press the key for 2 sec.
7-2. Display Mode
1) Normal mode
Displays and sets the output voltage, the frequency and the function setting on the data display
area.
Upon turning ON the power supply, this display appears.
A mode ⇒Displays the output voltage and the frequency, and displays and sets the function
setting.
n mode ⇒Displays and sets the output voltage and the frequency, and saves their data.
Displays and sets the function setting.
2) Parameter mode (Pilot lamp ⑤FUNC is ON.)
Shows and sets the parameter on the data display. (Details⇒P.26)
Depending on the operation mode, the parameter that can be set is differing.
A mode ⇒Displays and sets the parameter that needs to be changed during operation.
n mode ⇒Displays and sets all parameters.
To switch the display mode, press the Func key long for 2 sec.
Regardless of the display mode, operation and stopping through the panel and under the external
control is enabled.

14 / 32
7-3. Setting the Function
This operation can be performed when the normal mode (output voltage, frequency) is in display.
Each time the Func key is pressed, the pilot lamps ⑤-⑨ blink sequentially, and each function
setting item is displayed on the data display area. The function setting to be displayed when the
Func key is pressed differs according to the operation mode and the amplitude control setting as
follows:
(a) “A” mode (for the setting other than the setting of (b))
Voltage (Frequency) →⑥AUTO →⑨PAT →Voltage
(b) “A”mode (only for setting of 0u:1 and 0L:oF)
Voltage (Frequency) →⑥AUTO →⑨PAT →⑤FUNC →Voltage
(c) “n”mode
Voltage (Frequency) →⑥AUTO →⑧FLOCK →⑨PAT →Voltage
To select the setting, press the Freq▲key or Freq▼key. To execute the setting change, press
the Set key.
When the setting change is completed, the voltage is displayed.
If the process is brought forward to the next item by pressing the Func key without pressing the
Set key during the setting change, the setting will not be changed.
※If there is no key operation for over 5 min, the voltage is displayed.
(1)AUTO :Selects the operation mode.
Data display
Mode
Function
A
A mode
(operation mode)
The feeder operates according to each operation pattern
settings.
The feeder operates according to the amplitude control setting
(0u setting).
The voltage and the frequency themselves cannot be changed.
n
n mode
(adjustment mode)
The feeder operates according to each operation pattern
setting or panel setting.
The feeder operates with VVVF.
Sets the voltage frequency, and adjusts the amplitude.
(2)F-LOCK :Sets the frequency lock
Sets whether the frequency should be locked or not in the “n” mode.
(3)PAT :Switches the operation pattern.
Px (x=1-2): Displays the panel setting. (Setting is enabled only in the “n”mode.)
outx (x=1-2): Displays the operation pattern of the external signal [in3] status.

15 / 32
(4)FUNC :Locks/unlocks the magnification change setting.
“A” mode: Enabled and displays only in the amplitude control setting (0u: 1) and the remote
unit setting (0L: oF).
Loc: Locks. (The speed magnification cannot be changed. Displays “「 ̄」” in the decimal
point section of the voltage setting.)
uLoc: Unlocks. (The speed magnification can be changed. Displays the value of the decimal
places of the voltage setting.)
7-4. Preparation for Operation
Before powering ON the Controller, recheck the model, specifications, the drive rating and power
voltage of the Controller to confirm no discrepancy, and also recheck the connections to confirm
no wrong connection. Particularly when external signal is used, be careful not to mistake the
polarity.

16 / 32
8. Operation and Amplitude Adjustment Method
U100
io01
0.
0.
A
n
0.0
Func key
Freq▲▼ keys
Set key
※Next, go to <③ Parameter setting>.
Program version
“io” mode
Initial screen:
Output%
①Power ON
②Switching from the
operation mode to the
adjustment mode
The following are displayed in this order:
(Each 2 seconds)
AUTO lamp goes out, and the mode
is switched to the adjustment mode.
<Adjustment mode>
⇒
In this mode, the frequency and the output%
can be adjusted, and all parameters can be set
and changed.
①Data display area
②Frequency pilot lamp
③Voltage% pilot lamp
④Operation pilot lamp
⑤Parameter pilot lamp
⑥Operation mode pilot lamp
⑦Constant amplitude control
pilot lamp
⑧Frequency lock pilot lamp
⑨Operation pattern setting
:
ON
:Blinking
:OFF
<Lamp status>
(A) ON/OFF key
(B) Func key
(C) Set key
(D) Vol▲key
(E) Vol▼key
(F) Freq▲key
(G) Freq▼key
Operation panel

17 / 32
0.0
0A0.0
0u 0
0u 0
0u 1
0u 1
0.0
Press the
Func key long
for 2 sec.
Vol▼key
※ Usage during constant
voltage mode, change 0u to 0,
confirm that 0u=0, and go to
the next operation.
Set key
Freq▲▼ keys
Change 0u to 1.
Set key
The normal mode screen
appears.
Output% screen
Blinking
Blinking
※Next, go to <③ Adjustment of amplitude>.
③Parameter setting
Press the
Func key long
for 2 sec.
The parameter mode
screen appears.
※When the Set key is pressed after value setting, the
set value is saved.
※If the Vol
▲▼ keys are pressed without pressing the
Set key in the change process, the changes will not
be saved but cancelled.
If there is no key operation for over 5 min, the normal
mode screen (voltage display) will be forced to
reappear.
※This section describes the change of the parameters
No. 0u. Any other parameter can be changed in the
same way.
When the Vibration
Sensor KS
-3 is not used,
[Constant voltage mode]
When the Vibration Sensor
KS
-3 is used,
[Constant amplitude mode]

18 / 32
0.0
0.0
180.0
90.0
0.0
10.0
120.0
120.3
10.0
※Next, go to <③ Adjustment of amplitude>.
ON/OFF
key
※Adjust the frequency to the frequency
that raises the work feeding speed to the
fastest.
Freq▲▼ keys
※Raise the frequency by several tenths
of one Hz to the point at which the work
feeding speed is the fastest.
First, make an adjustment aiming the
output% at around 10%.
Vol▲▼ keys
Vol▲▼ keys
※To next page
Freq▲▼ keys
Vol▲▼ keys
④Adjustment of amplitude
※Perform the
following in the
forced operation:
Freq▲▼ keys
※If the voltage is
too high or too low,
change the voltage%.
※For the distinction between the
full wave and the half wave, confirm
the model, etc. of the drive.
In the case of half wave, set the frequency to 90Hz by
using the Freq▲▼ keys.
<Meaning of RUN lamp status>
ON: In operation by remote control
OFF: Operation at a stop (when remote
control is OFF)
Quick blinking: In forced operation
Slow blinking: Forced operation at a stop
* Forced operation means
⇒ Forcedly starting/stopping the operation by
pressing the ON/OFF button whether the
operation is remote-controlled or not
In the case of full wave,
the frequency is set to
180Hz (factory setting).
In the case of half wave,
the frequency is set to
90Hz.
This manual suits for next models
3
Table of contents
Other SANKI Controllers manuals
Popular Controllers manuals by other brands
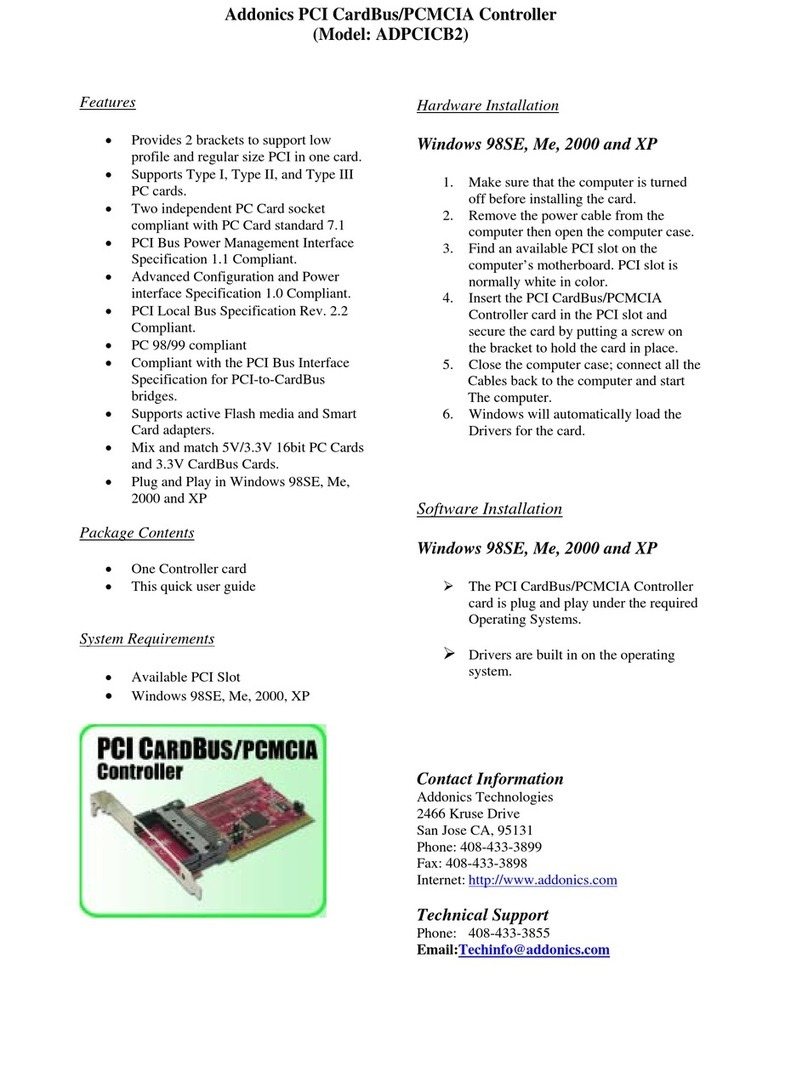
Addonics Technologies
Addonics Technologies ADPCICB2 install guide

Castle Creations
Castle Creations Pixie-7P quick start guide
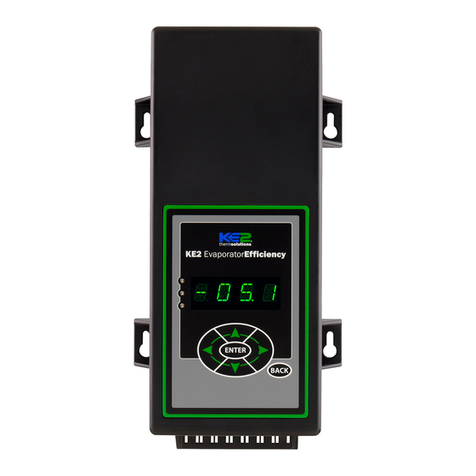
KE2 Therm Solutions
KE2 Therm Solutions 20844 quick start guide

Beckett
Beckett Heat Manager 61572 04 brochure
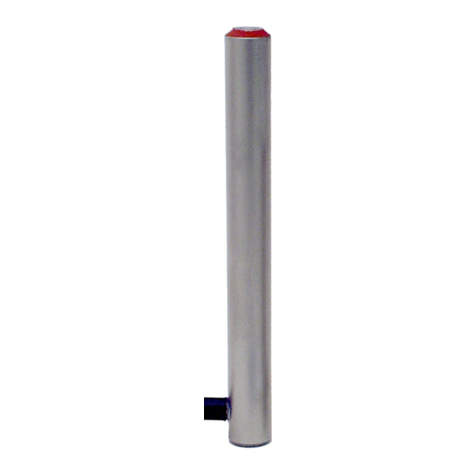
PI
PI PICMA P-840 Short instructions
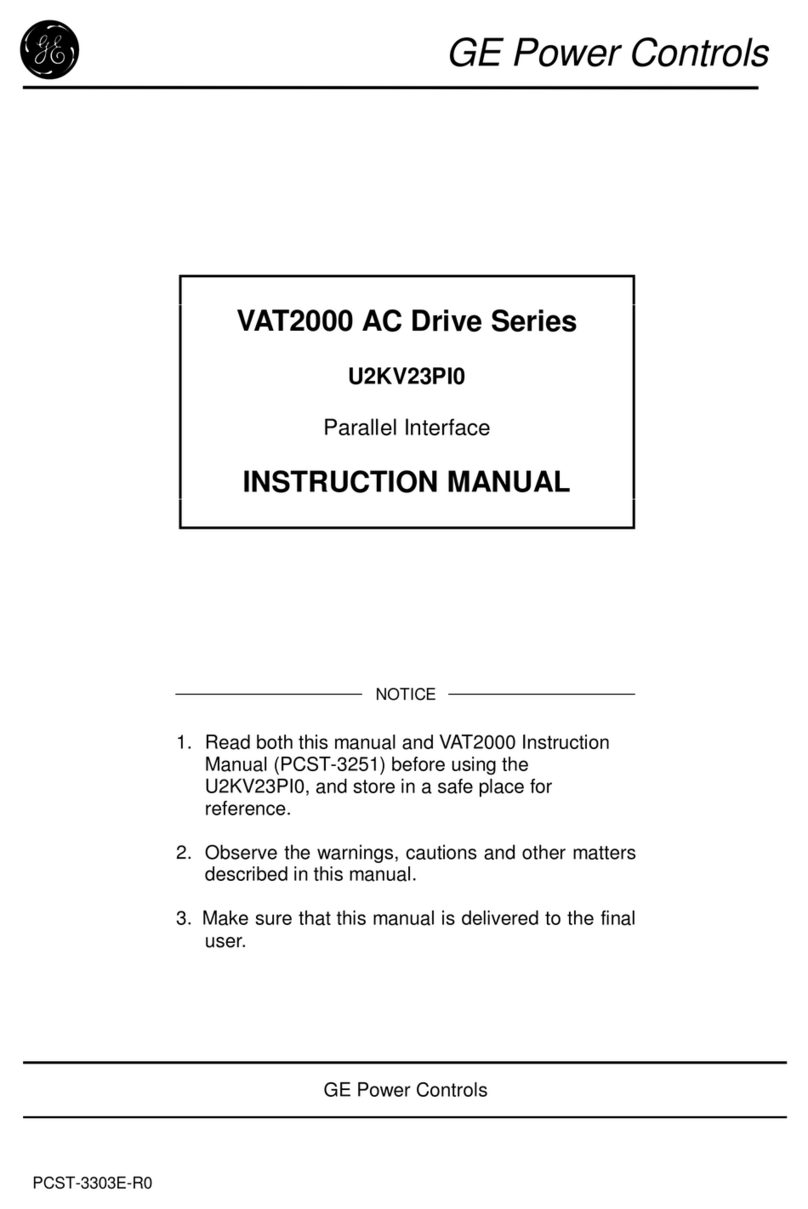
GE
GE VAT2000 Series instruction manual