Sanyo Denki PE Series User manual

C
#########################<RXU#)LUVW#2QOLQH#5HVRXUFH#IRU
###########################################&RQWUROV/#'ULYHV/#DQG#0RWRUV
Sanyo Denki
PE Servo System
Installation and Operation Manual
Sales & Technical Support
8:30 a.m. to 5:30 p.m. EST
Toll Free: 1.888.531.8213
Atlanta Area: 770.497.8086
Fax: 770.497.8666
Support@MotionOnline.com
Automation Intelligence
Motion Products
™
System Integratio
n
2855 Premiere Parkway, Suite A
Duluth, Georgia 30097-4902
Issued: 27-Apr-00
Downloaded from Arrow.com.

PE Manual Copyright © 2000 Automation Intelligence, Inc. Issued: 27-Apr-00
Table of Contents
INTRODUCTION.............................................................................................................5
About this Guide....................................................................................................................................................... 5
Safety ........................................................................................................................................................................ 7
Technical Support..................................................................................................................................................... 9
Product Family Overview ....................................................................................................................................... 10
INSTALLATION ............................................................................................................12
Chapter Overview ................................................................................................................................................... 12
Unpacking and Inspection Procedure...................................................................................................................... 13
Inspection Test........................................................................................................................................................ 14
Amplifier Installation.............................................................................................................................................. 17
Motor Installation....................................................................................................................................................22
Installation Check List ............................................................................................................................................30
WIRING.........................................................................................................................31
Chapter Overview ................................................................................................................................................... 31
Wiring Precautions.................................................................................................................................................. 33
Applicable Wire Sizes.............................................................................................................................................34
Input Power.............................................................................................................................................................35
Leakage Current...................................................................................................................................................... 35
Connection Diagram with P2 Motor .......................................................................................................................36
Connection Diagram with P3 Motor .......................................................................................................................37
TB Connector..........................................................................................................................................................38
Input/Output Internal Circuits.................................................................................................................................39
CN1 Control Connector .......................................................................................................................................... 41
CN2 Motor Encoder Connector .............................................................................................................................. 45
Operator Terminal................................................................................................................................................... 46
External Regeneration Resistors ............................................................................................................................. 47
Wiring Check List................................................................................................................................................... 53
SYSTEM CONFIGURATION.........................................................................................54
Chapter Overview ................................................................................................................................................... 54
Using the Remote Operator.....................................................................................................................................55
Quick Setup............................................................................................................................................................. 57
Amplifier Parameters .............................................................................................................................................. 59
Amplifier Tuning.....................................................................................................................................................83
Jogging.................................................................................................................................................................... 86
Monitor Screen........................................................................................................................................................88
Alarm Trace Screen.................................................................................................................................................89
OPERATION .................................................................................................................91
Chapter Overview ................................................................................................................................................... 91
Pre-Operation..........................................................................................................................................................92
Power On Sequence ................................................................................................................................................93
Stop Sequences .......................................................................................................................................................94
Servo OFF Sequence...............................................................................................................................................96
Alarm Reset Sequence ............................................................................................................................................98
Overtravel Sequence ............................................................................................................................................... 99
Downloaded from Arrow.com.Downloaded from Arrow.com.

PE Manual Copyright © 2000 Automation Intelligence, Inc. Issued: 27-Apr-00
MAINTENANCE AND TROUBLESHOOTING ............................................................100
Chapter Overview .................................................................................................................................................100
Maintenance.......................................................................................................................................................... 101
Troubleshooting.................................................................................................................................................... 101
SPECIFICATIONS ......................................................................................................111
Chapter Overview .................................................................................................................................................111
Acceleration and Deceleration Time.....................................................................................................................112
Dynamic Brake...................................................................................................................................................... 113
Miscellaneous Servo Motor Specifications...........................................................................................................114
INDEX .........................................................................................................................115
Downloaded from Arrow.com.Downloaded from Arrow.com.Downloaded from Arrow.com.

PE Manual Copyright © 2000 Automation Intelligence, Inc. Issued: 27-Apr-00
List of Tables
Table 1: Manual Syntax................................................................................................................................................6
Table 2: Valid Drive Systems.....................................................................................................................................11
Table 3: Amplifier Environmental Requirements .......................................................................................................20
Table 4: Power Dissipation.........................................................................................................................................20
Table 5: Motor Environmental Requirements............................................................................................................. 22
Table 6: Motor IP Rating............................................................................................................................................ 25
Table 7: Allowable Radial and Thrust Loads.............................................................................................................. 29
Table 8: Applicable Wire Sizes .................................................................................................................................. 34
Table 9: Power Supply Capacity Requirement............................................................................................................35
Table 10: System Leakage Current .............................................................................................................................35
Table 11: TB Connector Pin Assignments.................................................................................................................. 38
Table 12: CN1 Internal Circuits..................................................................................................................................39
Table 13: CN1 Pin Assignments.................................................................................................................................41
Table 14: CN2 Pin Assignments.................................................................................................................................45
Table 15: Amplifier Regeneration Power.................................................................................................................... 47
Table 16: Regeneration Resistor Selection .................................................................................................................50
Table 17: Quick Setup Steps....................................................................................................................................... 58
Table 18: Monitor Mode Page Descriptions...............................................................................................................88
Table 19: Alarm Mode Page Descriptions..................................................................................................................89
Table 20: Amplifier Alarm Codes...............................................................................................................................90
Table 21: Amplifier Status Display............................................................................................................................. 92
Table 22: Holding Brake Specifications ................................................................................................................... 114
••‘’••‘’
Downloaded from Arrow.com.Downloaded from Arrow.com.Downloaded from Arrow.com.Downloaded from Arrow.com.

PE Manual Copyright © 2000 Automation Intelligence, Inc. Issued: 27-Apr-00
Introduction
About this Guide
This chapter covers the following topics:
About this Guide ............................................................................................................5
In this Chapter 5
Introduction 5
Manual Organization 5
Syntax Information 6
Safety.............................................................................................................................. 7
Technical Support ..........................................................................................................9
Online Support 9
E-Mail Support 9
Telephone Support 9
Field Service 9
Product Family Overview.............................................................................................10
Amplifiers 10
Motors 10
Systems 11
Remote Operator 11
Cables 11
External Regen Resistors 11
This guide provides you with information needed to install, operate, and maintain PE
model servo amplifiers and matching motors.
This guide consists of the following chapters:
Chapter 1. Introduction provides an overview of the Safety issues associated with the
application of servo motors and amplifiers, informs you about all your
product support options, and finally provides an overview of the PE family
of amplifiers, the P2 and P3 family of motors, and system options and
accessories.
Chapter 2. Installation provides detailed directions that take you step by step from
unpacking your system, through installing the motor and installing the
amplifier, and concludes with an installation check list.
Chapter 3. Wiring describes how to wire a system. Starting first with a summary table
indicating recommended wire sizes, followed by connection diagrams, and
concluding with details for connecting external regeneration resistors and
the remote operator. Detailed connector pin assignments are provided as
well as a partial schematic for input and output signals.
In this Chapter
Introduction
Manual
Organization
Downloaded from Arrow.com.Downloaded from Arrow.com.Downloaded from Arrow.com.Downloaded from Arrow.com.Downloaded from Arrow.com.

PE Manual Copyright © 2000 Automation Intelligence, Inc. Issued: 27-Apr-00
6
Chapter 4. System Configuration describes how to use the remote operator and then
walks you through the configuring and tuning of your system. This chapter
concludes with a detailed description of each amplifier parameter.
Chapter 5. Operation chapter provides a detailed description of the sequence and
timing of operation within the amplifier.
Chapter 6. Maintenance and Troubleshooting provides you with a recommended
maintenance program designed to keep your system in top operating
condition. Should you experience any difficulty with your system, a
detailed troubleshooting guide is provided to help you restore normal
operation quickly.
Chapter 7. Specification section includes detailed specifications for PE drive systems.
This includes a detailed reference for all the amplifier parameters.
To help you locate and interpret information easily, this guide uses consistent visual cues
and text formats. The different symbols and typefaces displayed in this guide are used for
the following purposes:
Table 1: Manual Syntax
‘This symbol is used to identify important information of which you should
take note.
üü DANGER, WARNING or CAUTION require accompanying information
notices to prevent potential personal injury and equipment damage.
DANGER: Indicates an imminently hazardous situation which, if not
avoided, will result in serious injury or death. This signal word is limited
to the most extreme situations.
WARNING: Indicates a potentially hazardous situation which, if not
avoided, could result in serious injury or death.
CAUTION: Indicates a potentially hazardous situation which, if not
avoided, may result in equipment damage or minor or moderate injury.
Earth Gnd Protective conductor terminal, Earth Ground.
Chassis Gnd Chassis terminal, Not a protective ground.
Syntax
Information
Downloaded from Arrow.com.Downloaded from Arrow.com.Downloaded from Arrow.com.Downloaded from Arrow.com.Downloaded from Arrow.com.Downloaded from Arrow.com.

PE Manual Copyright © 2000 Automation Intelligence, Inc. Issued: 27-Apr-00
7
Safety
DANGER
üü Only qualified personnel familiar with the construction and operation of this
equipment and the hazards involved should install, adjust, operate, or service
this equipment. Read and understand this manual and other applicable manuals
in their entirety before proceeding. Failure to observe this could result in severe
injury or loss of life.
DANGER
üü The user is responsible for conforming with all applicable local, national, and
international codes. The wiring examples in this manual are intended only as a
guide. Wiring practices, grounding and disconnects, and over-current protection
are of particular importance. Failure to observe this could result in severe injury
or loss of life.
DANGER
üü Do not operate the system in an explosive atmosphere. Failure to observe this
could result in severe injury or loss of life and equipment damage.
WARNING
üü Perform the initial power-up with the motor shaft disconnected from the load and
the shaft key removed. Improper wiring or undiscovered shipping damage could
result in undesired motion. Be prepared to remove power if excessive motion
occurs. Failure to observe this precaution could result in bodily injury.
WARNING
üü Large leakage currents exist in AC line filters. They must be grounded properly
before applying power. Filter capacitors retain high voltages after power is
removed. Before handling the equipment, voltage should be measured to
determine safe levels. Failure to observe this precaution could result in severe
bodily injury.
WARNING
üü Avoid damaged cables. Cables may be damaged by applying excessive stress,
placing a heavy object on them, or cutting them. Damaged cables may result in
electrical shock which can cause severe bodily injury and damage equipment.
Downloaded from Arrow.com.Downloaded from Arrow.com.Downloaded from Arrow.com.Downloaded from Arrow.com.Downloaded from Arrow.com.Downloaded from Arrow.com.Downloaded from Arrow.com.

PE Manual Copyright © 2000 Automation Intelligence, Inc. Issued: 27-Apr-00
8
CAUTION
üü Observe all installation directions. Failure to do so may result in injury, damage
to equipment, or poor performance.
1. Make sure nothing obstructs or impedes ventilation around the amplifier.
2. Observe all mounting clearance distances around the unit.
3. Never install the system in a location where water, or other fluids, may be
splashed, or in a flammable gas atmosphere.
4. Never place objects on this equipment. Doing so may result in damage,
burns or fire.
5. Avoid strong shocks to equipment. This may result in injury or damage to
equipment.
WARNING
üü During normal operation, the amplifier, motor and peripheral equipment could
become hot enough to cause a burn.
Downloaded from Arrow.com.Downloaded from Arrow.com.Downloaded from Arrow.com.Downloaded from Arrow.com.Downloaded from Arrow.com.Downloaded from Arrow.com.Downloaded from Arrow.com.Downloaded from Arrow.com.

PE Manual Copyright © 2000 Automation Intelligence, Inc. Issued: 27-Apr-00
9
Technical Support
The most convenient and effective method for support is online at our web site
www.MotionOnline.com
In addition to this manual, you may download our Handbook of AC Servo Systems,
application notes and answers to frequently asked questions from this site.
Questions can be submitted via e-mail and in most cases our Technical Support staff will
reply the same day, but in all cases you will receive a reply before the end of the next
working day. Send your email questions to:
support@MotionOnline.com
Automation Intelligence maintains a Technical Support center that is staffed weekdays
(except holidays) between 8:30 AM and 5:30 PM Eastern Standard Time.
xTelephone: 770-497-8086
xFacsimile: 770-497-8666
Field service is not included in the product warrantee in order to keep our product cost
low, but it is a service that Automation Intelligence provides. Request for field service
may be made to the Technical Support staff (see above). Automation Intelligence must
receive a Purchase Order before the Technical Support engineer departs.
Online Support
E-Mail Support
Telephone
Support
Field Service
Downloaded from Arrow.com.Downloaded from Arrow.com.Downloaded from Arrow.com.Downloaded from Arrow.com.Downloaded from Arrow.com.Downloaded from Arrow.com.Downloaded from Arrow.com.Downloaded from Arrow.com.Downloaded from Arrow.com.

PE Manual Copyright © 2000 Automation Intelligence, Inc. Issued: 27-Apr-00
10
Product Family Overview
Sanyo Denki designs and manufactures a wide range of servo and stepper drives. Seven
models from the PE and PV families are available to you from Automation Intelligence
via MotionOnline.com (this manual covers the PE family of drives).
xPE2A015 15A
xPE2A030 30A
xPE2A050 50A
xPE0A100 100A
xPE0A150 150A
xPV1A015 15A
xPV1A030 30A
Sanyo Denki designs and manufactures a wide range of servo and stepper motors.
Fourteen (7 without brakes and 7 with brakes) models from the P2 and P3 families are
available to you from Automation Intelligence via MotionOnline.com.
xP20B10150D 1.5kW 4.9Nm
xP20B10250D 2.5kW 8.8Nm
xP20B13300D 3.0kW 10.8Nm
xP20B13500D 5.0kW 18.1Nm
xP30B04010D 100W 0.35Nm
xP30B06040D 400W 1.37Nm
xP30B08075D 750W 2.55Nm
Amplifiers
Motors
Downloaded from Arrow.com.Downloaded from Arrow.com.Downloaded from Arrow.com.Downloaded from Arrow.com.Downloaded from Arrow.com.Downloaded from Arrow.com.Downloaded from Arrow.com.Downloaded from Arrow.com.Downloaded from Arrow.com.Downloaded from Arrow.com.

PE Manual Copyright © 2000 Automation Intelligence, Inc. Issued: 27-Apr-00
11
From these motors and amplifiers, the following 10 systems can be assembled. All the
systems can operate up to 4,500 RPM, the power listed is continuous at 3,000 RPM, and
the torque listed is continuous at 0 RPM.
Table 2: Valid Drive Systems
PV Amplifiers PE AmplifiersMotor Model WNm
15A 30A 15A 30A 50A 100A 150A
P30B04010D 100 0.35 ~~
P30B06040D 400 1.37 ~~
P30B08075D 750 2.55 ~~
P20B10150D 1500 4.9 ~
P20B10250D 2500 8.8 ~
P20B13300D 3000 10.8 ~
P20B13500D 5000 18.1 ~
The remote operator is required to set/change all the parameters in the PE and PV
amplifiers. The remote operator is not required for operation and may therefore be shared
between all the drives in a system. The same remote operator is used for the PE and PV
amplifiers.
To lower life-cycle cost and improve reliability, Automation Intelligence requires
customers to use Sanyo Denki motor power and feedback cables. These cables may be
ordered in standard or custom lengths. Standard cables are usually available directly from
stock.
Optional external regeneration resistors are available to extend the continuous
regeneration power of the amplifier.
Systems
Remote Operator
Cables
External Regen
Resistors
Downloaded from Arrow.com.Downloaded from Arrow.com.Downloaded from Arrow.com.Downloaded from Arrow.com.Downloaded from Arrow.com.Downloaded from Arrow.com.Downloaded from Arrow.com.Downloaded from Arrow.com.Downloaded from Arrow.com.Downloaded from Arrow.com.Downloaded from Arrow.com.

PE Manual Copyright © 2000 Automation Intelligence, Inc. Issued: 27-Apr-00
Installation
Chapter Overview
This chapter contains a guide for the installation of the amplifier and matching motor,
from unpacking the equipment, performing an initial test, to mounting it in panels.
Chapter Overview.........................................................................................................12
Unpacking and Inspection Procedure...........................................................................13
Unpack the Amplifier 13
Inspection 13
Inspection Test.............................................................................................................14
Minimum Wiring 14
Set Key Parameters 15
Jog Operation 15
Amplifier Installation ................................................................................................... 17
General Requirement 17
Mounting and Clearance Requirements 18
Amplifier Environmental Requirements 20
Power Dissipation 20
Enclosure Size 21
Motor Installation......................................................................................................... 22
Environmental Requirements 22
Motor Mounting 23
Motor Orientation and Cable Routing 25
Connecting the Load to the Motor 26
Bearing Load Specifications 29
Installation Check List.................................................................................................. 30
Downloaded from Arrow.com.Downloaded from Arrow.com.Downloaded from Arrow.com.Downloaded from Arrow.com.Downloaded from Arrow.com.Downloaded from Arrow.com.Downloaded from Arrow.com.Downloaded from Arrow.com.Downloaded from Arrow.com.Downloaded from Arrow.com.Downloaded from Arrow.com.Downloaded from Arrow.com.

PE Manual Copyright © 2000 Automation Intelligence, Inc. Issued: 27-Apr-00
13
Unpacking and Inspection Procedure
ƒBefore opening packages, verify that the model numbers of the box match your order.
If they do not, please contact Automation Intelligence, see page 9 Technical Support.
ƒAfter opening, verify that the model numbers on the product match the box. If they
do not, please contact Automation Intelligence, see page 9 Technical Support.
ƒAfter unpacking, verify that the servo amplifier and motor are free from any physical
damage that may have occurred during shipment. If you find damage, contact your
Buyer to make a claim with the shipper.
ƒPerform the Inspection Test to verify functionality of the system.
Unpack the
Amplifier
Inspection
Downloaded from Arrow.com.Downloaded from Arrow.com.Downloaded from Arrow.com.Downloaded from Arrow.com.Downloaded from Arrow.com.Downloaded from Arrow.com.Downloaded from Arrow.com.Downloaded from Arrow.com.Downloaded from Arrow.com.Downloaded from Arrow.com.Downloaded from Arrow.com.Downloaded from Arrow.com.Downloaded from Arrow.com.

PE Manual Copyright © 2000 Automation Intelligence, Inc. Issued: 27-Apr-00
14
Inspection Test
WARNING
üThe parameter settings at the start of this inspection test are assumed to be
factory default settings. If this is not the case, the inspection test may not be
successful even though there is nothing wrong with the servo amplifier or motor.
Also, at the conclusion of the test, some amplifier parameters may not be
returned to the initial state.
WARNING
üDamage during shipment could cause erratic motion or a run-away condition.
Therefore the motor should be securely held down during this test and no load
should be attached to the shaft.
During this Inspection Test you will use the Remote Operator to change parameters and
jog the motor. If you have any trouble, refer to the Maintenance and Troubleshooting
chapter on page 100. If you still have difficulty, refer to page 9 for details on the various
methods for contacting the Technical Support team.
1. Wire 230Vac to the rand tterminals of the servo amplifier terminal block.
2. Wire 230Vac to the R, S, and Tterminals of the servo amplifier terminal block and
earth ground to á
3. Connect the motor power cable to the U, V, Wand áterminals of the servo amplifier
using the supplied cable.
4. Connect the encoder to the servo amplifier CN2 connector using the supplied cable.
5. Connect the Remote Operator to the OP connector on the servo amplifier.
6. If the motor has a brake, apply the specified 24Vdc to release the brake.
Minimum Wiring
OP
CN2
r
t
R
S
T
U
V
á
W
á
n
230 VAC
o
230 VAC r
Remote
Operator
q
Feedback
Cable
s
Holding Brake
Power Supply
p
Power
Cable
Servo Motor
Servo Amplifier
Downloaded from Arrow.com.Downloaded from Arrow.com.Downloaded from Arrow.com.Downloaded from Arrow.com.Downloaded from Arrow.com.Downloaded from Arrow.com.Downloaded from Arrow.com.Downloaded from Arrow.com.Downloaded from Arrow.com.Downloaded from Arrow.com.Downloaded from Arrow.com.Downloaded from Arrow.com.Downloaded from Arrow.com.Downloaded from Arrow.com.

PE Manual Copyright © 2000 Automation Intelligence, Inc. Issued: 27-Apr-00
15
Motor Type
1. Turn ON the control power, the 230Vac attached to the rand tterminals. The
power LED should turn ON and a dash should appear in the middle of the 7-segment
display.
xThe remote Operator Screen should display the [Push Mode Key] screen
and a beep should sound.
2. Enable System Parameter changes using the Remote Operator.
xPress [ON / Mode]and íto enter the parameter set mode.
xPress the \key until you have switched to page 13 where you can set the
Func3 parameters.
xPress the ìkey to change bit 7to a 1.
xPress the [WR] key to save the change.
3. Set the motor type.
xPress [ON / Mode] and ìto enter the parameter select mode.
xPress the \key until you have switched to page 9where you can set the
motor type parameters.
xPress the [and ]keys to change to the proper type.
xPress the [WR] key to save the change.
xCycle the control power supply OFF and back ON.
1. To simplify wiring for this Inspection Test, the overtravel limits will be set for
normally open limit switches.
xPress [ON / Mode] and íto enter the parameter set mode.
xPress the Zand \keys to switch to page 10 where you can set the user
interface functions.
xPress the [key twice and the ìkey once to change bit 5to a 1.
xPress the [WR] key.
2. Enable Test mode operation using the Remote Operator. Jogging and Auto-tuning
are in the test mode.
Set Key
Parameters
Jog Operation
Downloaded from Arrow.com.Downloaded from Arrow.com.Downloaded from Arrow.com.Downloaded from Arrow.com.Downloaded from Arrow.com.Downloaded from Arrow.com.Downloaded from Arrow.com.Downloaded from Arrow.com.Downloaded from Arrow.com.Downloaded from Arrow.com.Downloaded from Arrow.com.Downloaded from Arrow.com.Downloaded from Arrow.com.Downloaded from Arrow.com.Downloaded from Arrow.com.

PE Manual Copyright © 2000 Automation Intelligence, Inc. Issued: 27-Apr-00
16
xPress the \key three times to switch to page 13 where you can set the
Func3 parameters.
xPress the [key and the ìkey to change bit 6to a 1.
xPress the [WR] key. Bit 6will return to 0when the control power is turned
OFF.
3. Turn ON the bus power (R, S, and T), the 230Vac attached to the R, S, and T
terminals. The three horizontal bars in the 7-segment display should be ON.
4. Jog the motor.
xPress the [ON / MODE] key and the é.
xPress the ]then the ìkey and the [WR] key. This will set the jog speed
to 10 RPM.
xA rotating figure ;will appear on the 7-segment display.
xContinue pushing the [key. The remote operator will continuously beep
and the motor will rotate counterclockwise (CCW) at 10RPM when viewed
looking at the motor shaft.
xRelease the [key, and press the ]key. Again the remote operator will
continuously beep and the motor will rotate clockwise (CW) at 10RPM.
5. Exit Jogging.
xPush the 0key and then the [ON/Mode] key to exit the test mode.
xA “d” will flash in the 7-segment display.
6. Re-enable the overtravel limits.
xPress [ON / Mode] and íto enter the parameter set mode.
xPress the Zand \keys to switch to page 10 where you can set the user
interface functions.
xPress the [key twice and the íkey once to change bit 5to a 0.
xPress the [WR] key.
7. Turn OFF the 230Vac bus power (R, S, and, T)
8. Turn OFF the 230Vac control power (r, t)
9. If the motor has a brake, turn OFF the brake power, activating the brake.
This completes the Inspection Test. If you have any trouble please call Technical
Support, see page 9.
Downloaded from Arrow.com.Downloaded from Arrow.com.Downloaded from Arrow.com.Downloaded from Arrow.com.Downloaded from Arrow.com.Downloaded from Arrow.com.Downloaded from Arrow.com.Downloaded from Arrow.com.Downloaded from Arrow.com.Downloaded from Arrow.com.Downloaded from Arrow.com.Downloaded from Arrow.com.Downloaded from Arrow.com.Downloaded from Arrow.com.Downloaded from Arrow.com.Downloaded from Arrow.com.

PE Manual Copyright © 2000 Automation Intelligence, Inc. Issued: 27-Apr-00
17
Amplifier Installation
Condition Recommended Precautions
Amplifier In An
Enclosure The temperature inside an enclosure may be higher than the
outside temperature, depending on the power loss of internal
equipment and the dimensions of the box.
Be sure to determine the dimensions of the box, cooling method,
and panel layout so that the temperature around the amplifier will
be kept lower than 55C.
Amplifier Near A
Vibrating Source Install the amplifier with a shock absorber to dampen the vibration
that is transmitted directly to amplifier.
Amplifier Near A
Heat Source Shield the amplifier so that convection or radiation does not raise
the temperature near the amplifier above 55C.
Corrosive Gas
Environment If the amplifier is operated for a long time in a corrosive
environment then contact failure will occur at contact points (e.g.,
connectors). Therefore, never install the amplifier in a corrosive
gas environment.
Explosive Or
Combustible Gas
Environment
Never install the amplifier in an explosive gas or combustible gas
environment. Relays and contactors, which generate arcs (sparks)
inside boxes and hot parts such as regeneration brake resistor may
become ignition sources, causing a fire or explosion.
Dust And Oil
Environments Never install the amplifier in an environment containing dust or oil
mist. Dust and oil mist which adheres to or accumulates on the
amplifier will result in damage to the amplifier from lower
insulation resistance or leakage currents between conductors or
components.
Electrical Noise
Environments Induction noise will enter input signals and the power supply
circuit, causing the amplifier to malfunction. When installing the
amplifier in an electrically noisy environment, take proper
measures such as inserting a noise filter, shielding, or suppressing
the noise source.
General
Requirement
Downloaded from Arrow.com.Downloaded from Arrow.com.Downloaded from Arrow.com.Downloaded from Arrow.com.Downloaded from Arrow.com.Downloaded from Arrow.com.Downloaded from Arrow.com.Downloaded from Arrow.com.Downloaded from Arrow.com.Downloaded from Arrow.com.Downloaded from Arrow.com.Downloaded from Arrow.com.Downloaded from Arrow.com.Downloaded from Arrow.com.Downloaded from Arrow.com.Downloaded from Arrow.com.Downloaded from Arrow.com.

PE Manual Copyright © 2000 Automation Intelligence, Inc. Issued: 27-Apr-00
18
Install the amplifier vertically as shown in the figure below, with the indicated clearances.
Because the amplifier uses convection cooling it may not be mounted horizontally.
Provide the indicated space above, below and to the side of the amplifier for air flow. If
this space cannot be provided, install a fan to increase air flow around the amplifier.
Mounting and
Clearance
Requirements
50 mm or more
50 mm or more
Back Surface
Mounting
4-M5
A
C
A B C D
PE2A015 225mm NA 25mm NA
PE2A030 225mm NA 25mm NA
PE2A050 225mm NA 75mm NA
50 mm or more
50 mm or more
Back Surface
Mounting
4-M5
A
C
Cut-out
for
Cooling
Fins
D
B
Cooling
Air Flow
90 mm
or more
A B C D
PE0A100 225mm t197mm 75mm t117mm
PE0A150 225mm t197mm 75mm t142mm
Fins
Downloaded from Arrow.com.Downloaded from Arrow.com.Downloaded from Arrow.com.Downloaded from Arrow.com.Downloaded from Arrow.com.Downloaded from Arrow.com.Downloaded from Arrow.com.Downloaded from Arrow.com.Downloaded from Arrow.com.Downloaded from Arrow.com.Downloaded from Arrow.com.Downloaded from Arrow.com.Downloaded from Arrow.com.Downloaded from Arrow.com.Downloaded from Arrow.com.Downloaded from Arrow.com.Downloaded from Arrow.com.Downloaded from Arrow.com.

PE Manual Copyright © 2000 Automation Intelligence, Inc. Issued: 27-Apr-00
19
50 mm or more
50 mm or more
Front Surface
Mounting
4-M5
A
C
5 mm or more Front
Surface
Cut-out
D
B
A B C D
PE2A015 225mm t212mm 25mm t62mm
PE2A030 225mm t212mm 25mm t62mm
PE2A050 225mm t212mm 75mm t127mm
50 mm or more
50 mm or more
Front Surface
Mounting
4-M5
A
C
A B C D
PE0A100 225mm t212mm 75mm t127mm
PE0A150 225mm t212mm 75mm t152mm
Front
Surface
Cut-out
D
B
Cooling
Air Flow
90 mm
or more
Fins
Downloaded from Arrow.com.Downloaded from Arrow.com.Downloaded from Arrow.com.Downloaded from Arrow.com.Downloaded from Arrow.com.Downloaded from Arrow.com.Downloaded from Arrow.com.Downloaded from Arrow.com.Downloaded from Arrow.com.Downloaded from Arrow.com.Downloaded from Arrow.com.Downloaded from Arrow.com.Downloaded from Arrow.com.Downloaded from Arrow.com.Downloaded from Arrow.com.Downloaded from Arrow.com.Downloaded from Arrow.com.Downloaded from Arrow.com.Downloaded from Arrow.com.

PE Manual Copyright © 2000 Automation Intelligence, Inc. Issued: 27-Apr-00
20
The amplifier should be installed in an environment that meets these requirements.
Table 3: Amplifier Environmental Requirements
Item Specification
Ambient Temperature
Operating
Non-operating
0 to 55C
32° to 131°F
-20 to 65C
-4° to 149°F
Humidity Maximum 90% Non-condensing
Vibration Maximum 0.5G 10 to 55Hz
Shock Maximum 2G
Air Quality Dust-free
Oil-free
Non-corrosive
Non-combustible
Non-explosive
During operation, the amplifier dissipates power that results in cabinet heating. The
following table lists power dissipation values for valid system configurations. These
values assume continuous rated load operation. Calculate the cabinet cooling
requirements using the power dissipation information and the formulas below. For
PE0A100 and PE0A150 amplifiers, details are provided for the power dissipated in the
heatsink.
Table 4: Power Dissipation
Power Dissipation [W]Drive Model Motor Model
Total PCB Heatsink
PE2A015 P30B04010D 19 - -
PE2A030 P30B06040D 31 - -
PE2A030 P30B08075D 46 - -
PE2A050 P20B10150D 100 - -
PE0A100 P20B10250D 170 98 72
PE0A100 P20B13300D 175 103 72
PE0A150 P20B13500D 260 150 110
Power dissipation values shown in the table do not include values for the internal
regeneration resistor.
When using an external regeneration resistor, the internal resistor is disconnected.
Amplifier
Environmental
Requirements
Power Dissipation
Downloaded from Arrow.com.Downloaded from Arrow.com.Downloaded from Arrow.com.Downloaded from Arrow.com.Downloaded from Arrow.com.Downloaded from Arrow.com.Downloaded from Arrow.com.Downloaded from Arrow.com.Downloaded from Arrow.com.Downloaded from Arrow.com.Downloaded from Arrow.com.Downloaded from Arrow.com.Downloaded from Arrow.com.Downloaded from Arrow.com.Downloaded from Arrow.com.Downloaded from Arrow.com.Downloaded from Arrow.com.Downloaded from Arrow.com.Downloaded from Arrow.com.Downloaded from Arrow.com.
This manual suits for next models
14
Table of contents
Other Sanyo Denki Servo Drive manuals
Popular Servo Drive manuals by other brands
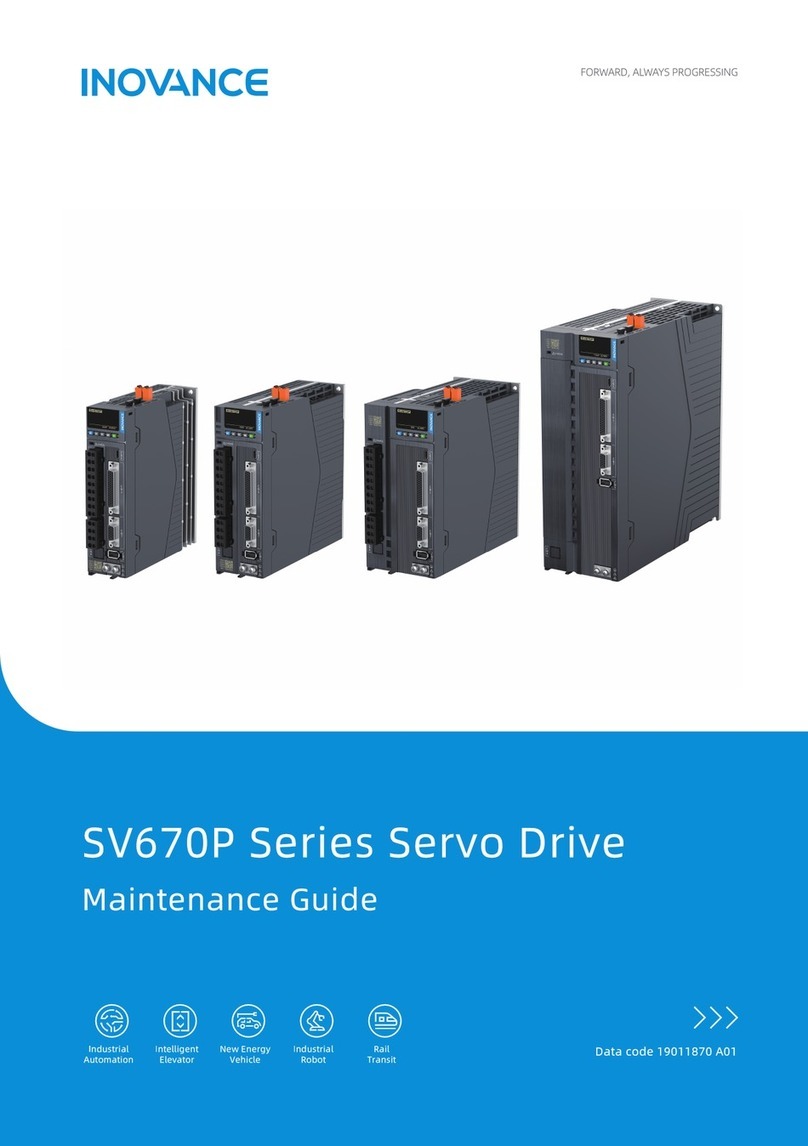
Inovance
Inovance SV670P Series Maintenance Guide
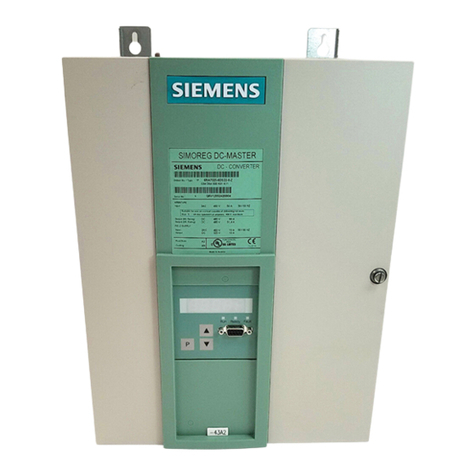
Siemens
Siemens SIMOREG DC Master 6RA7028-6DS22 operating instructions
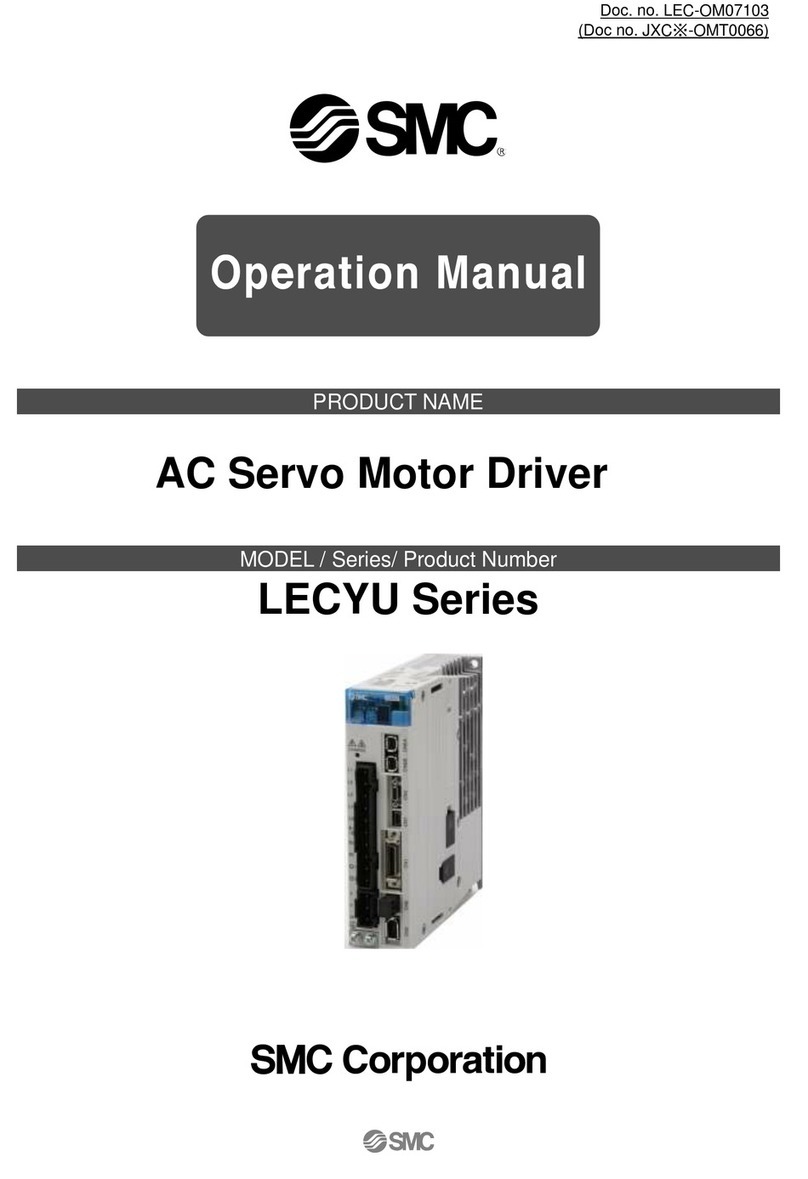
SMC Networks
SMC Networks LECYU Series Operation manual
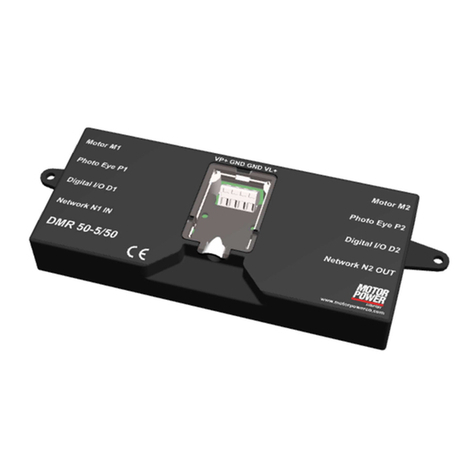
Motor Power Company
Motor Power Company DMR 50-5 installation guide
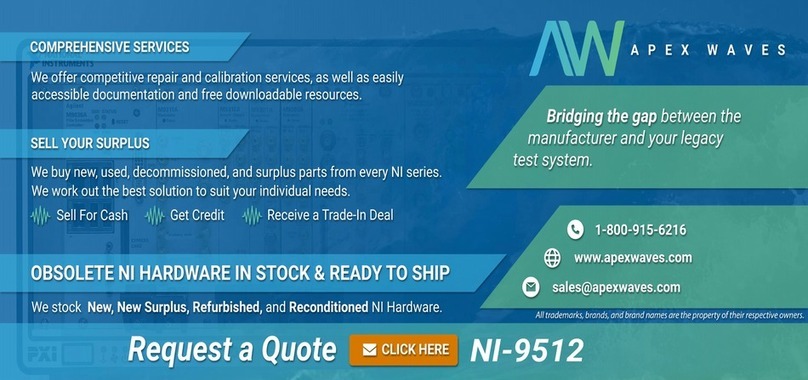
National Instruments
National Instruments NI 9512 C Series Getting started

YASKAWA
YASKAWA SGD7S-R70A20A023F40B product manual