SGS BJ2 User manual

FOR YOUR SAFETY
PLEASE READ THESE INSTRUCTIONS CAREFULLY
AND RETAIN THEM FOR FUTURE USE.
OWNER’S MANUAL
PROFESSIONAL
BOTTLE JACK

SPECIFICATION
MODEL MAX CAPACITY MIN HEIGHT MAX HEIGHT
BJ2 2 TON 181 345
BJ2S 2 TON 181 345
BJ5 5 TON 216 413
BJ5S 5 TON 216 413
BJ8 8 TON 230 457
BJ10 10 TON 230 460
BJ12 12 TON 230 465
BJ15 15 TON 230 460
BJ20 20 TON 242 452
BJ32 32 TON 285 465
BJ50 50 TON 300 480
BJ2D 2 TON 148 276
BJ5D 5 TON 185 355
BJ8D 8 TON 190 365
BJ10D 10 TON 195 375
BJ15D 15 TON 205 390
BJ20D 20 TON 217 407
BJ30D 32 TON 230 360
TBJ4 4 TON 265 610
TBJ5 5 TON 225 500
TBJ10 10 TON 210 520
TBJ10L 10 TON 125 225
TBJ12 12 TON 240 590
WWW.SGS-ENGINEERING.COM PAGE 2

INSPECTION
BEFORE EACH USE A VISUAL INSPECTION SHALL BE MADE FOR ABNORMAL CONDITIONS
SUCH AS CRACKED WELDS, DAMAGED, BENT, WORN, LOOSE OR MISSING PARTS. THIS JACK
SHOULD BE INSPECTED IMMEDIATELY IF IT IS BELIEVED TO HAVE BEEN SUBJECTED TO AN
ABNORMAL LOAD OR SHOCK. OWNER/OPERATORS SHOULD BE AWARE THAT REPAIR OF
THIS JACK REQUIRES SPECIALISED EQUIPMENT AND KNOWLEDGE.
OPERATION
THE OWNER IS RESPONSIBLE FOR MAINTAINING ALL DECALS AND WARNING LABELS AND
MAINTAINING THE UNIT IN GOOD WORKING ORDER. SAFETY INFORMATION SHOULD BE EM-
PHASISED AND UNDERSTOOD PRIOR TO USAGE. THIS JACK SHALL BE INSPECTED AS PER THE
INSTRUCTION MANUAL BEFORE EACH USE.
IT IS THE OWNER’S/OPERATORS’ RESPONSIBILITY TO STUDY ALL WARNINGS, OPERATING
AND MAINTENANCE INSTRUCTIONS CONTAINED ON THE PRODUCT LABEL AND WITHIN
THIS INSTRUCTION MANUAL TO ENSURE PROPER OPERATION OF THIS JACK. THE OWNER/
OPERATOR SHALL RETAIN THESE PRODUCT INSTRUCTIONS FOR FUTURE REFERENCE.
THIS JACK SHALL BE MAINTAINED IN ACCORDANCE WITH THE PRODUCT INSTRUCTIONS. NO
ALTERATIONS SHALL BE MADE TO THIS JACK.
PAGE 3

MAINTENANCE
MONTHLY MAINTENANCE IS RECOMMENDED. LUBRICATION IS CRITICAL TO JACKS AS THEY
SUPPORT HEAVY LOADS. ANY RESTRICTION DUE TO DIRT, RUST OR CORROSION CAN CAUSE
EITHER SLOW MOVEMENT OR RAPID JERKS DAMAGING THE INTERNAL COMPONENTS. THE
FOLLOWING STEPS ARE DESIGNED TO KEEP THE JACK MAINTAINED AND OPERATIONAL.
1. LUBRICATE THE RAM, LINKAGES, SADDLE AND PUMP MECHANISM WITH LIGHT OIL.
2. VISUALLY INSPECT THE JACK FOR CRACKED WELDS, BENT, LOOSE OR MISSING PARTS
AND HYDRAULIC OIL LEAKS.
3. IF THIS JACK IS FOUND TO BE DAMAGED IN ANY WAY OR OPERATING ABNORMALLY IT
SHOULD BE REMOVED FROM SERVICE UNTIL REPAIRED BY A SGS SERVICE CENTRE.
4. CLEAN ALL SURFACES AND MAINTAIN ALL LABELS AND WARNINGS.
5. CHECK AND MAINTAIN THE RAM OIL LEVEL.
6. CHECK THE RAM EVERY 3 MONTHS FOR SIGNS OF RUST OR CORROSION. CLEAN AS
NEEDED AND WIPE WITH AN OILY CLOTH. WHEN NOT IN USE ALWAYS LEAVE THE SAD-
DLE AND RAM FULLY RETRACTED.
ALWAYS STORE THE JACK IN THE FULLY LOWERED POSITION. THIS WILL HELP PROTECT
CRITICAL AREAS FROM CORROSION. DO NOT USE BRAKE OR TRANSMISSION FLUIDS OR
REGULAR MOTOR OIL AS THEY CAN DAMAGE THE SEALS. ALWAYS REFILL WITH HYDRAULIC
JACK OIL.
OWNER/OPERATORS SHOULD BE AWARE THAT THE REPAIR OF THIS JACK REQUIRES SPE-
CIALISED EQUIPMENT AND KNOWLEDGE. ONLY FACTORY AUTHORISED PARTS, LABELS AND
DECALS SHALL BE USED ON THIS EQUIPMENT. AN ANNUAL INSPECTION OF THIS JACK BY
A SGS REPAIR CENTRE IS RECOMMENDED TO ENSURE THE JACK MAINTAINS AN OPTIMUM
OPERATING CONDITION.
WWW.SGS-ENGINEERING.COM PAGE 4

CHECK THE OIL LEVEL (FIG 4)
1. TURN THE RELEASE VALVE ANTI CLOCKWISE TO ALLOW THE RAM TO FULLY RETRACT. IT
MAY BE NECESSARY TO APPLY FORCE TO THE SADDLE TO LOWER THE RAM.
2. REMOVE THE INSPECTION PLATE.
3. WITH THE JACK IN THE LEVEL POSITION REMOVE THE OIL FILL PLUG. STAND THE JACK
IN THE VERTICAL POSITION WITH THE HANDLE SOCKET DOWN. THE OIL SHOULD BE
LEVEL WITH THE BOTTOM OF THE FILL HOLE. IF NOT, TOP UP BUT DO NOT OVERFILL.
ALWAYS FILL WITH NEW, CLEAN HYDRAULIC JACK OIL.
4. REPLACE FILL PLUG AND INSPECTION PLATE.
5. CHECK JACK OPERATION.
6. PURGE AIR FROM THE SYSTEM AS REQUIRED.
SYSTEM AIR PURGE
1. TURN THE RELEASE VALVE ANTI CLOCKWISE ONE FULL TURN TO OPEN.
2. PUMP THE HANDLE EIGHT FULL STROKES.
3. TURN RELEASE VALVE CLOCKWISE TO CLOSE THE VALVE.
4. PUMP THE HANDLE UNTIL THE RAM REACHES MAXIMUM HEIGHT AND CONTINUE TO
PUMP SEVERAL TIMES TO REMOVE AIR TRAPPED IN THE RAM.
5. CAREFULLY AND SLOWLY PINCH THE OIL FILL PLUG TO RELEASE TRAPPED AIR.
6. TURN THE RELEASE VALVE ANTI CLOCKWISE ONE FULL TURN AND LOWER THE RAM TO
THE LOWEST POSITION. USE FORCE ON THE SADDLE IF NECESSARY.
7. TURN THE RELEASE VALVE CLOCKWISE TO THE CLOSED POSITION AND CHECK FOR
PROPER PUMP ACTION. IT MAY BE NECESSARY TO PERFORM THE ABOVE MORE THAN
ONCE TO ENSURE ALL THE TRAPPED AIR IS VENTED.
PAGE 5

RAISING A VEHICLE
1. MAKE SURE THE JACK AND VEHICLE ARE ON A HARD LEVEL SURFACE.
2. ALWAYS SET THE VEHICLE HANDBRAKE AND CHOCK THE WHEELS.
3. CONSULT THE VEHICLE OWNER’S MANUAL TO ASCERTAIN THE LOCATION OF JACKING
POINTS AND POSITION THE JACK BENEATH THE LIFT POINT.
4. TURN THE RELEASE VALVE CLOCKWISE TO THE CLOSED POSITION. (FIG 1)
5. IF NEEDED, TURN THE EXTENSION SCREW ANTI CLOCKWISE UNTIL IT COMES INTO
CONTACT WITH THE VEHICLE. (FIG 2)
6. TO RAISE THE VEHICLE PUMP UP AND DOWN. (FIG 3)
7. PLACE JACK STANDS BENEATH THE VEHICLE AT LOCATIONS RECOMMENDED BY THE
VEHICLE MANUFACTURER. DO NOT WORK UNDER THE VEHICLE WITHOUT THE USE OF
JACK STANDS. JACKS ARE NOT DESIGNED TO MAINTAIN HEAVY LOADS FOR LONG PE-
RIODS OF TIME. DO NOT ATTEMPT TO PLACE JACK STANDS SIMULTANEOUSLY UNDER
BOTH ENDS OF A VEHICLE OR ALONG ONE SIDE OF A VEHICLE.
8. TURN THE RELEASE VALVE SLOWLY ANTI CLOCKWISE TO LOWER THE VEHICLE ONTO
THE JACK STANDS.
LOWERING A VEHICLE
1. TURN THE RELEASE VALVE CLOCKWISE TO THE CLOSED POSITION.
2. PUMP THE HANDLE TO LIFT THE VEHICLE OFF THE JACK STANDS.
3. REMOVE THE JACK STANDS. DO NOT GET UNDER THE VEHICLE WHILE THE VEHICLE IS
BEING LOWERED.
4. TURN THE RELEASE VALVE SLOWLY ANTI CLOCKWISE TO LOWER THE VEHICLE ONTO
THE GROUND.
WWW.SGS-ENGINEERING.COM PAGE 6

HANDLE
RELEASE VALVE
EXTENSION
SCREW
FIG 1 FIG 2
FIG 3
PUMP
HANDLE
SAFETY VALVE
PUMP
FIG 4
OIL PLUG
OIL LEVEL
FILL TO RIM OF OIL PLUG HOLE
PAGE 7

WARNING
• READ AND UNDERSTAND ALL WARNINGS AND INSTRUCTIONS PRIOR TO USE.
• DO NOT OVERLOAD THIS JACK BEYOND ITS RATED CAPACITY.
• THIS JACK IS A LIFTING DEVICE ONLY.
• THIS JACK IS DESIGNED FOR USE ON HARD LEVEL SURFACES ONLY.
• THE LOAD MUST BE SUPPORTED BY JACK STANDS ONCE RAISED.
• DO NOT DOLLY OR MOVE THE VEHICLE WHILE IT IS ON THE JACK.
• LIFT ONLY ON AREAS AS SPECIFIED BY THE VEHICLE MANUFACTURER.
• ONLY ATTACHMENTS AND/OR ADAPTORS SUPPLIED BY SGS SHALL BE USED.
• NO ALTERATIONS TO THE JACK SHALL BE MADE.
• FAILURE TO HEED THESE WARNINGS MAY RESULT IN DAMAGE TO THE JACK AND/OR
FAILURE RESULTING IN PERSONAL INJURY OR PROPERTY DAMAGE.
• INSPECT THE JACK BEFORE EACH USE.
TROUBLESHOOTING
PROBLEM POSSIBLE CAUSE ACTION
JACK WILL NOT LIFT TO FULL
HEIGHT
LOW OIL LEVEL CHECK OIL LEVEL AND REFILL IF
NECESSARY
JACK WILL NOT HOLD LOAD RELEASE VALVE NOT CLOSING
OIL CONTAMINATED
PUMP VALVES NOT SEALING
CYLINDER RAM BINDING
CONTACT CUSTOMER SERVICE
LIFT ARM WILL NOT LOWER CYLINDER RAM BINDING
PARTS WORN
INTERNAL DAMAGE
BROKEN RETURN SPRING
LIFT ARM LINKAGE BENT OR
BINDING
CONTACT CUSTOMER SERVICE
JACK FEELS SPONGY WHEN
LIFTING
SEE AIR PURGE SECTION PURGE TRAPPED AIR
FOR YOUR SAFETY
PLEASE READ THESE INSTRUCTIONS CAREFULLY
AND RETAIN THEM FOR FUTURE USE.

EC Declaration of Conformity
This is an important document and should be retained
MANUFACTURER’S NAME:
TYPE OF EQUIPMENT:
PART NUMBERS:
I, the undersigned, hereby declare that the equipment specied above
conforms to the above European Communities Directive(s) and
Standard(s).
PLACE:
DATE: (Signature)
Robert Wyatt
Company Secretary
Derby, UK
24th JUNE 2017
SGS Engineering (UK) Ltd
SGS Engineering (UK) Ltd
West Side Park
Raynesway
Derby, DE21 7AZ
Bottle Jack
BJ2, BJ2S, BJ5, BJ5S, BJ8, BJ10,
BJ12, BJ15, BJ20, BJ32, BJ50, BJ2D,
BJ5D, BJ8D, BJ10D, BJ15D, BJ20D,
BJ30D, TBJ4, TBJ5, TBJ10, TBJ10L,
TBJ12
EN 1494:2000/A1:2008
AfPS GS 2014:01 PAK
2006/42/EC Machinery Directive (MD)
APPLICATION OF EC COUNCIL DIRECTIVES / STANDARD:
This manual suits for next models
22
Table of contents
Other SGS Jack manuals
Popular Jack manuals by other brands

Tundra
Tundra TUNJKSER03L user manual
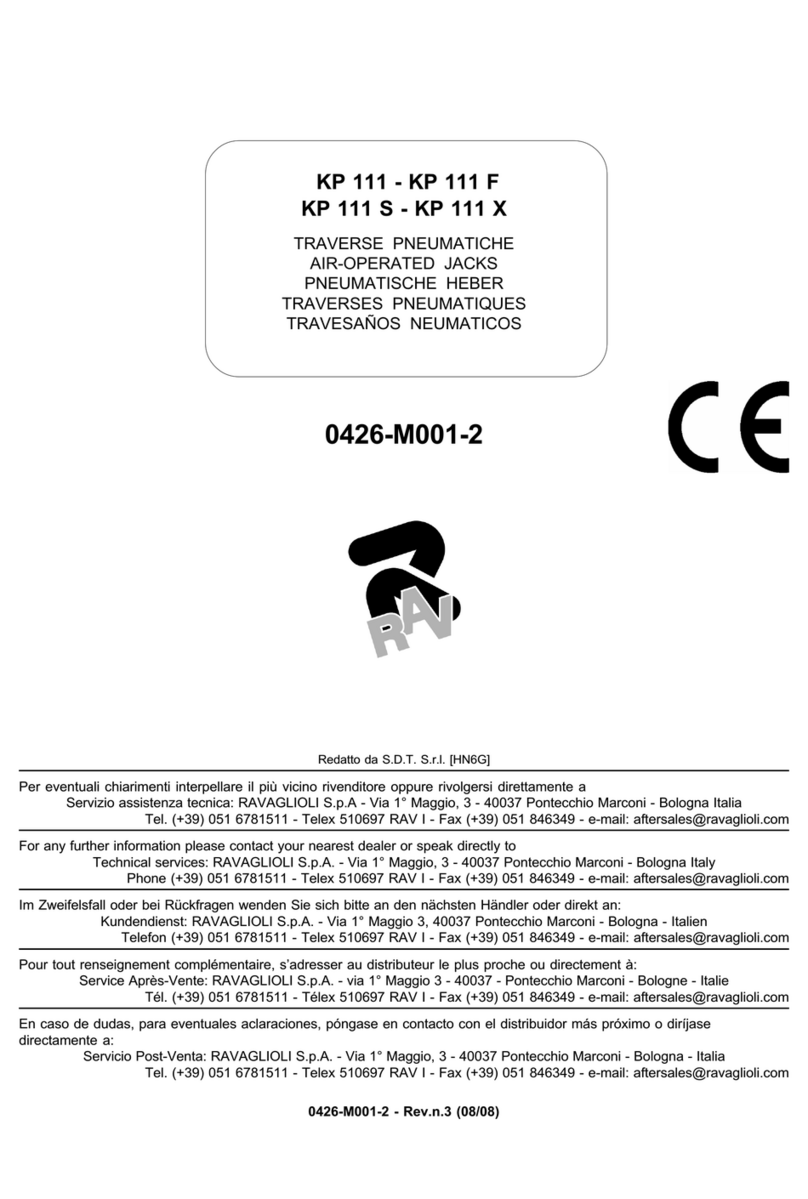
Ravaglioli
Ravaglioli KP 111 manual

Husky
Husky HB3000 Assembly, Installation, Operation and Maintenance Instructions
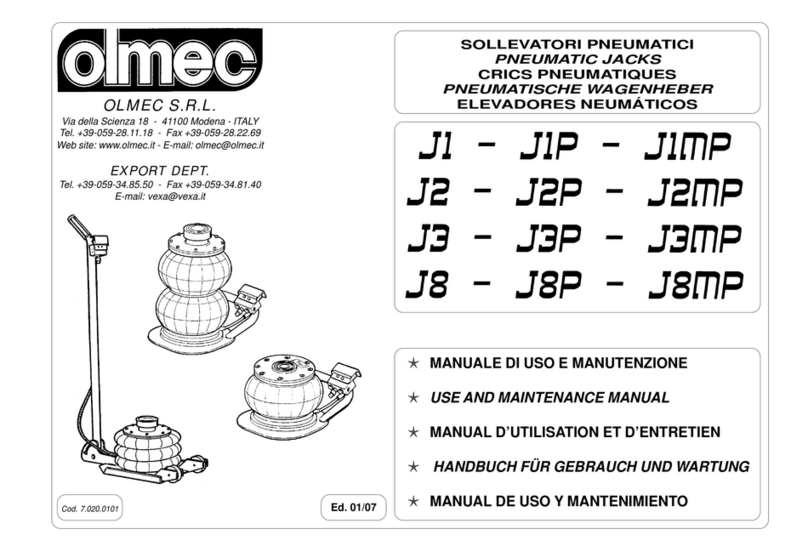
OLMEC
OLMEC J1 Use and maintenance manual
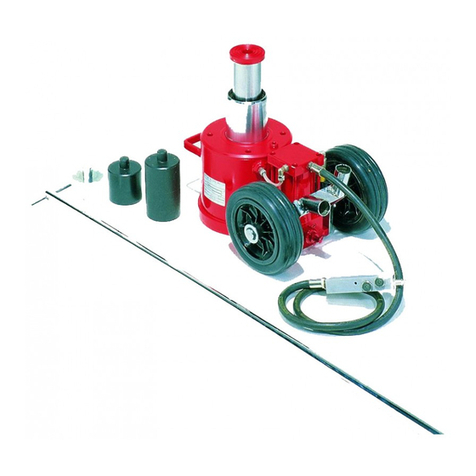
Cattini Oleopneumatica
Cattini Oleopneumatica YAK 300 Operating and maintenance manual
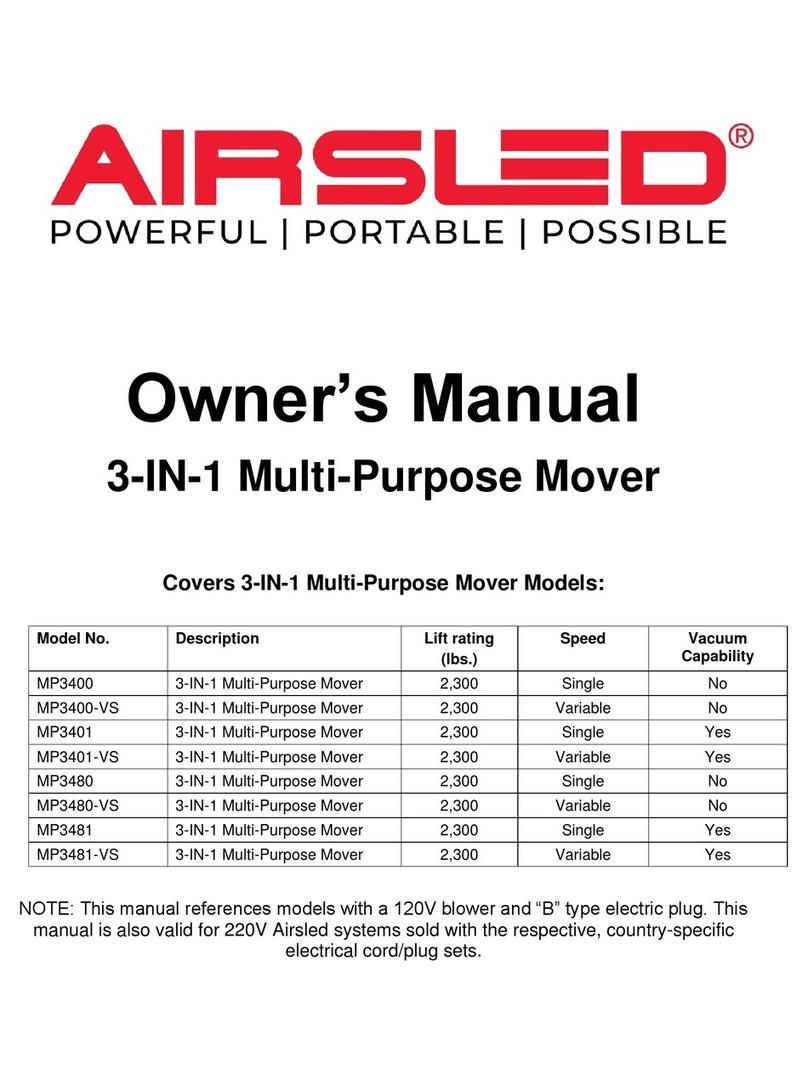
AIRSLED
AIRSLED MP3400-VS owner's manual