Sharp PA-W1400 User manual

PA-W1400
SHARP
=
SERVICE
MANUAL
CODE:
00ZPAW1410S2E
PERSONAL
WORD
PROCESSOR
PA-W1400
mopEL
PA-W1410
Va
;
CONTENTS
=
3
|
Hh)
Generales
ciao
Leche
eA
|
Feet
Meads
cheats
amie
oath
Sofas
uly
1-1
2:
-SPOCificatOns®
.2.5:.5vete
eh
arcy
ass,
orth
wey
Oa
an
ane
eee
2-
3]
Mechanical
descriptions
.............0
0.00
cece
cee
ee
eee
3-1
|
4]
Electrical
descriptions
........
0...
eck
ccc
ene eee
canes
4-
5]
Disassembly
andre-assembly
...........
00.0
cc
cece
eee
eeee
5-
|
6)
AGIUSIMORIS
2
sei-0s
tere
Colies
ncaad
veka
cid
byadesamadieen.
6-1
(]
Electrical:
Set.
ups7s
tasted
veg
acta
een
Hatciaa
sua
caweee
7-
8]
Liibrications
:
2.05
2scves
cache
ae
ooset
wn
ake
Genta
SL
ack
peed
oa
os
7-1
9]
Basic
functional
checks
0.0.0...
0...
e
cece
cece
eee
eens
9-
|
|
10)
TOUDISSHOOHNG
s
calc
cet
aa
wie
y
ams
ugne
in
sHeue
gieen
deadline
10-1
|
11]
}/DIagnOStiC
s..\c-20
ace
tang tata
ia
wines
eed
S
bacns
God
Le
cidie
lS
11-
|
12]
Parts
layout
and
circuit
diagram
......
0.0...
c
cece
eee
ee
12-
*
Parts
guide
This
document
has
been
published
to
be
used
for
ft
les
at
SHARP
CORPORATION
the
contents
are
subject
to
change
without
aatioe

[1]
General
The
PA-W1400/PA-W1410
is
a
portable
personal
word
processor
that
has
the
ordinary
electronic
typewriter
(ET)
functions
and
the
text
editing
functions
of
a
common
word
processor
(WD)
that
can
be
switch
selected.
It
has
the
following
features:
What
the
PA-W1400
differs
from
the
PA-W1410
is
in
the
liquid
crystal
display
panel
and
backlight
circuit.
The
PA-W1410
has
the
backlight
feature.
There
is
a
different
method
for
the
liquid
crystal
display
unit
depending
on
the
availability
of
the
backlight
feature.
@
An
80
characters
x
16
lines
large
size
screen
liquid
crystal
display
with
a
tilt
mechanism.
The
backlight
is
adopted
for
the
PA-W1410,
while
it
is
not
used
by
the
PA-W1400.
(1)
Electrical
circuit
The
main
control
PWB
consists
of
a
power
supply,
mechanical
drive,
keyboard
control,
beeper
drive,
liquid
display,
and
data
storage
(memory,
floppy
disk).
(2)
Block
diagram
The
figure
below
shows
the
block
diagram
for
the
printer
block,
key-
board
block,
floppy
disk
block,
power
supply
block,
and
main
control
PWB.
PA-W1400
@
Internal
single
floppy
disk
drive
@
Use
of
a
96-character
replaceable
printwheel
(non-cassette
type)
@®
The
accessory
floppy
disc
includes
the
following
program
for
sales
promotion
of
the
product.
Please
print
and
utilize
it.
The
sample
of
print
data
showing
as
next
page.
(Operation)
CODE]
+
Power-ON
Block
diagram
AC(V)
50/60H2
+
Power
supply
unit
Printer
mechanical
unit
Lop
unit
Switch
Head
cable
>|
T
CITT
a
al]
Carriage
motor
Carriage
G
home
position
sensor
Main
control
PWB
unit
(EI
Paper
teed
motor
i]
l
FDD
unit
Keyboard
unit
NOTE:
The
LCD
unit
service
parts
is
available
with
it
assembled
in
the
LCD
cabinet.
Since
it
would
be
probable
that
an
open
line
or
a
contact
failure
may
occurs
at
the
junction
between
the
PWB
and
the
LCD
because
of
corrosion,
if
the
LCD
PWB was
left
stored
by
itself
for
a
long
period
of
more
than
three
month,
it
needs
to
be
stored
with
the
LCD
assembled
to
the
LCD
cabinet
with
‘screws,
Although
the
assembly
is
made
available
for
the
ser-
vice
parts,
it
has
to
be
returned
to
its
original
state
if
the
LCD
PWéB
was
removed
for
parts
replacement.
Refer
to
a
later
Paragraph
discussing
“LCD
unit
disassembly
and
re-assemb-
ly"
for
details
of
assembly.

PA-W1400
(Printing
sample)
INTRODUCING
SHARP'S
WORD
PROCESSORS
This
innovative
product
from
Sharp
Corporation
is
a
fully
dedicated
word
processing
system
with
MS-DOS
Compatible
Disk
Format.
This
is
an
all-in-one
system
consisting
of
an
LCD
Display
with
Backlight
(PA-W1410
only)
for
easier
viewing,
a
printer,
a
3.5"
Disk
Drive
and
a
full
Function
Keyboard.
This
Word
Processor
is
easy
to
use
with
many
Menu
Driven
Functions
and
preset
Function
Keys,
all
you
do
is
press
one
key
and
you're
on
your
way
to
a
flawlessly
typed
text,
then
store
it
on
the
disk
for
future
use.
With
the
Merge
Print
feature
you
can
insert
names,
addresses
etc.,
to
all
your
letters
and
reports
automatically.
And
with
the
Form
Fill-in
feature
you
can
easily
complete
preset
forms
in
a
fraction
of
time
than
the
old
manual
way.
Sharp's
Word
Processor
can
be
used
for
Faster,
Efficient
and
Convenient
word
processing
tasks
or
with
a
touch
of
one
key
use
it
as
an
electronic
typewriter.
THIS
ADVANCED
PRODUCT
ALSO
HAS
MANY
BUILT-IN
FEATURES:
*
An
easy
to
read
80
character
x
16
line
LCD
Backlit
Screen
(PA-W1410
only).
*
A
built-in
50,000
character
Memory.
*
An
MS-DOS
Compatible
Disk
with
720KB
per
disk
storage
capacity
for
unlimited
memory.
*
A
15
cps
Bidirectional
Letter
Quality
Daisy
Wheel
Printer.
An
80K
word
Spelling
Dictionary
with
on-line
Thesaurus.
*
Usage
Checker
checks
for
11
punctuation
and
grammatical
errors.
*
Word
Processing:
*
Block
Move/Delete/Copy
*
Search
and
Replace
*
Auto
Insert
*
Merge
Print
*
Page
Formatting
*
View
Page
Layout
*
Form
Fill-in
*
Auto
Storing
*
Disk
and
File
Utilities
*
ASCII
Text
Conversion
Printing
Controls:
*
Auto
Return
*
Auto
Center
*
Auto
Bold
*
Auto
Underline
*
Auto
Indent
*
Word
Count
*
Auto
Justification
*
Auto
Decimal
Tab
*
Capital
Lock
*
Superscript
*
Subscript
_
_*
Plush
Right
Correction
Systems:
:
*
Word
Correction
*
Two
Line
Correction
Memory
*
Relocate
*
Micro
Backspace
*
Word
Backspace
*
Character
Correction
This
Word
Processor
will
make
your
most
difficult
typing
task
easy.
Each
page
you
type
will
convince
you
that
you've
made
a
wise
choice
in
your
purchase
of
Sharp'
sWord
Processor.
-

PA-W1400
(3)
Cautions
[2]
Specifications
1.
Be
sure
to
disconnect
the
power
supply
plug
before
disassembly.
2.
The
power
must
be
turned
off
when
installing
or
removing
the
eae
F
PWB.
(1)
Specification
3.
Hold
the
connector
area
when
fastening
or
unfastening
the
con-
Xx
1
The
ribbon
(1)
must
always
be
used
in
pair
with
the
correction
nector.
Never
manipulate
the
cable.
tape
(2).
Otherwise,
it
may
fail
to
correct.
4.
Do
not
bend
the
carriage
wire
too
often
as
it
is
not
robust
against
bending.
MODEL
5
abe
SPECIFICATIONS
PAW
1400/1410.
5.
Lubrication
must
be
done
to
the
specific
areas
only.
SRINTING
6.
The
LCD
unit
must
be
stored
in
a
state
assembled
to
the
cabinet,
Print
speed
15
cps,
Bidirectional
print
in
order
to
avoid
possible
occurrence
of
contact
failure
and
Printwheel
96
characters,
removable
(Non
cassette
damage
that
may
occur
if
it
was
left
by
itself.
type)
7.
CAUTION:
This
model
has
two
power
switches:
(1)
the
main
Print
pitch
10
or
12
power
switch
in
the
left
rear
side
of
the
body,
and
(2)
the
POWER
WIDTH
key
in
right
upper
side
of
the
keyboard.
Paper
13
inches
If
the
power
is
turned
off
by
pressing
the
POWER
key
in
the
Typing
10
inches
keyboard
before
turning
off
the
main
power
switch,
the
following
RIBBON
TYPE
Correctable
carbon
film,
power
ON
procedure
requires
pressing
of
the
POWER
key
in
the
approx.
50,000
charactors
Meypoee:
CORRECTION
TABLE
|Lift-off
correctable
carbon
film,
approx.
1,200
characters
.
KEYBOARD
(4)
Tools
required
Alphanumerickeys
|
44
2
ce
Key
buffer
32
The
following
tools
are
required
for
servicing.
Selt-repeat
keys
Return,
Backspace,
Space
Bar,
Left
Arrow,
Right
Arrow,
Up
Arrow,
Down
Part
code
Name
Arrow,
Auto
Correction,
the
Code
and
Up
Arrow
keys,
the
Code
and
Down
Ariow
UKOGM1068CSZZ
Loupe
(x15)
keys
Set
of
allen
wrenches
UKOGM0050CSZZ
DISPLAY
O27
18,
28
29-98)
Type
PA-W1400:
Liquid
Crystal
Display
OOPCB-1G102A/
Key
top
removing
tool
PA-W1410:
Liquid
Crystal
Display
with
0.1~5.0
mm
thickness
backlight
UKOGMO075C8ZZ
gauge
Capacity
80
character
x
16
line
(640
x
200
dets)
UKOGM5001BCZZ
Tension
gauge
(3.0
kg)
MEMORY
f
,
‘
UKOGM2024CSZZ
LCD
removing
tool
Amma
Correction
|2
line
(Max.
256
characters
per
line}
UKOG-5013BCZZ
Wheel
wrench
Bulit-in
Memory
50K
byte
DISK
DRIVE
Type
Built-in,
3.5
inch
(DSDD)
Micro
Floppy
Disk
Format
“MS-DOS
disk
format
compatible
Capacity
720K
byte/disk
‘SPELLING
Fer
cope
Nee,
DICTIONARY
OCHFLOILG311S
Grease
(Floil
G-3118)
ho
eae
meee
peated
jser's
Di
.
Is
UROG=0
1850822
Sotaw
grease
(No.
400)
Thesaurus
Approx.
15,000
entry
words
and
approx.
150,000
synonyms
POWER
Approx.
45
watts,
AC
voltage
(+105)
50/60Hz
ENVIRONMENTS
Operating
41
to
104°F
(5
to
40°C)
Temperature
Ambient
Humidity
_|20
to
85%
RH,
w/o
condensation
DIMENSIONS
16.46"(W)
x
15.71"(D)
x
4.92"(H)
/418(W)
x
399(D)
x
125(H)
mm
WEIGHT
PA-W1400:
Approx.
16.1
Ibs.
(7.3
Ig)
PA-W1410:
Approx.
16.5
Ibs.
(7.59)
OPTIONAL
ACCESSORIES
ay
{Beate}
Correctable
carbon
film
ribbon
Lift-off
correction
tape
(dual
pack)
@
'ZX-3FS1]
Except
|Fabric
ribbon
ZX-4CT
[U.S.A
|
Cover-up
correction
tape
(dual
paci)
Reference
to
"[2]-(2).
Option
print
vn
eels",
(3)
Print
wheels

PA-W1400
(2)
Option
print
wheels
The
print
wheel:
appricable
varies
according
to
the
destination.
For
details,
refer
to
the
"DESTINATION
TABLE"
in
the
parts
guide.
Tyee
|
NeenaPtcn
|
CSANS
|
amber
COURIER
10
270-176
ZX-9176H
PRESTIGE
ELITE
12
|
270-020
ZX-9020H
H
CUBIC
1012
270-046
ZX-9046H
SCRIPT
12
270-032
2ZX-9032H
CUBIC
1215
270-046
ZX-0964H
MADELEINE
PS
270-052
ZX-9052H
COURIER
10
269-176
ZX-9176L
CUBIC
1012
269-046
ZX-9046L
fs
SCRIPT
12
|
269-032
2X-9032L,
LIGHT
ITALIC
12
|
269-067
ZX-9067L
TILE
1215
269-125
ZX-9125L
MADELEINE
PS
|
269-052
2X-9052L
COURIER
10
268-176
2X-9176M
CUBIC
1012
|
268-046
ZX-9046M
M
SCRIPT
12
268-032
ZX-0932M
LIGHT
ITALIC
12
268-067
ZX-9067M
TILE
1215
|
268-125
ZX-9125M
MADELEINE
PS
|
268-052
2X-9052M
COURIER
10
267-176
2X-9176N
CUBIC
1012
|
267-046
2X-9046N
N
SCRIPT
12
267-032
ZX-9032N
LIGHT
ITALIC
12
|
267-067
ZX-9067N
TILE
1215
267-125
ZX-9125N
MADELEINE
267-052
ZX-9052N
NOTE:
A
non-cassette
type
printwheel
is
used
for
this
model.
Be-
cause
it
has
a
different
mechanism
with
the
printwheel
in
the
cassette
housing,
be
sure
to
use
the
specific
type.
Note
that
you
cannot
use
the
printwheel
with
the
housing.

[3]
Mechanical
descriptions
(1)
General
Since
the
mechanical
unit
of
this
model
shares
the
use
with
that
of
the
PA-3140II,
procedures
are
identical
to
disassembly,
re-assembly,
and
adjustments.
(Only
the
hammer
unit
specially
prepared
for
this
model.)
This
mechanism
is
made
more
simple
by
eliminating
the
adjustment
locations
as
compared
with
the
conventional
model
and
designed
with
high
reliability
with
more
rigidity
incorporated.
1.
Paper
feed
mechanism
The
paper
feed
mechanism
employs
the
pulse
motor
drive
system
which
works
to
rotate
the
platen
via
the
pinion
gear
®
and
idler
gear
@
when
the
paper
drive
signal
is
given
from
the
main
PWB.
As
it
uses
a
pulse
motor,
it
can
feed
the
paper
with
ease
in
both
forward
and
backward
directions.
Paper
is
fed
by
1/96"
per
pulse,
and
the
detent
works
1/24".
Mechanical
fine
adjustment
is
not
provided.
Fine
adjustment
is
per-
formed
by
means
of
software.
The
pulse
motor
@
and
the
idler
gear
@,
both
mounted
on
the
flexible
PF
holder
©,
are
pulled
by
the
spring
©
toward
the
platen
gear
©
with
a
fixed
force.
This
keeps
zero
clearance
between
the
idler
gear
@
and
the
platen
gear
©,
and
no
adjustment
is
necessary.
IFig.
3-1]
PA-W1400
2.
Paper
release
mechanism
As
shown
in
Fig.
3-4,
when
the
paper
release
lever
©
is
moved
in
the
arrow
direction
(A),
the
feed
roll
holder
support
@
rotates
in
the
direction
C
around
the
pivot
B.
This
allows
the
feed
roll
holder
@
to
move
downward,
releasing
the
feed
roll
@
from
contact
with
the
platen
®.
(Fig.
3-2)
—
{Fig.
3-2]
3.
Carriage
structure
and
driving
method
(Structure)
The
carriage
unit
consists
of
the
following
drive
blocks.
@®
Printwheel
drive
motor
(WH
motor)
@
Ribbon
lift/feed
drive
motor
(RB
motor)
@®
Print
hammer
solenoid
(HM
solenoid)
(Drive
system)
The
carriage
is
driven
by
the
carriage
motor
(CR
motor),
located
on
the
right
side
frame
of
the
printer,
via
the
carriage
timing
belt.
(Home
position)
Immediately
after
power
on,
the
carriage
starts
to
the
left
of
the
platen.
When
it
reached
the
mechanical
left
margin,
the
sensor
switch
on
the
left
side
of
the
printer
mechanism
is
pushed
by
a
needle-
shaped
lever
that
protrudes
from
the
left
side
of
the
carriage
and
the
carriage
momentarily
stops.
Then,
it
moves
to
right
to
the
leftmargin
and
stops
at
the
first
printing
position.
[Fig.
3-3]

PA-W1400
4,
Printwheel
home
positioning
mechanism
The
printwheel
can
be
set
at
its
home
position
by
the
zero
sense
lever
@
and
the
stepping
motor
@
driven
printwheel
flange
@,
in
the
reduction
of
1:4,
After
power
on,
the
carriage
and
the
printwheel
are
set
at
their
home
positions.
During
home
positioning
of
the
carriage,
the
zero
sense
lever
©
contacts
the
main
frame
at
the
left
mechanical
margin
and
moves
in
the
arrow
direction
A,
and
the
zero
sense
lever
stopper
®
engages
with
the
printwheel
flange
@
stops
its
motion,
the
printwheel
flange
®
driving
motor
@
disengages,
to
complete
home
positioning.
(Fig.
3-4)
IFig.
3-4]
NOTE:
As
there
is
no
significant
difference
from
the
conventional
model,
Either
the
cassette
type
or
non-cassette
type
printwheel
may
be
used
if
some
of
parts
are
replaced,
though
it
may
not
be
done
by
the
user.
5.
Ribbon
dirve
and
correction
mechanism
The
ribbon
is
taken
up
by
the
pulse
motor
and
the
cam
is
driven
by
the
same
motor
to
lift
the
correction
tape.
The
motor
is
installed
on
the
ribbon
holder
which
is
different
from
the
predecessor
model,
in
order
to
avoid
some
problem
in
the
mechani-
cal
action
and
parts
accuracy
of
the
drive
train
which
was
necessary
to
transmit
mechanical
power
to
the
ribbon
holder
that
shift
up
and
down
with
the
predecessor
model.
There
is
no
home
position
sensor
used
in
this
new
mechanism,
but
the
home
position
is
established
by
disengaging
the
motor
at
the
end
of
the
cam
slit.
(Cam)
A
cylindrical
cam
is
used
which
consists
of
two
parts
(cam
A,
cam
B)
because
of
parts
molding
and
it
has
three
positions
described
next.
@®
Print
and
ribbon
The
cams
rotate
idle
during
the
ribbon
feed
feed
position:
operation.
®
Standby
position:
The
cams
rest
in
this
position
for
a
certain
period
after
the
printing
has
been
completed.
The
cams
ascend
to
this
position
to
make
correction.
@®
Correct
position:
View
of
cam
transition
@
?
Cam
slit
CAM
B
rE
10
210240
eer
ere
re
wo
90
6)
9120180
pig
300
Ribbon
holder
shitt
[Fig.
3-6]
Since
the
cam
is
installed
on
the
moving
side
(ribbon
holder)
and
a
follower
pin
on
the
stationary
side
(carriage
base),
up
and
down
of
the
cam
slit
and
the
ribbon
holder
vertical
action
are
opposite
to
the
conventional
type.
6.Hammer
solenoid
driving
Ahammer
is
driven
by
the
hammer
solenoid
to
print
a
character
using
the
print
ribbon.
The
correct
tape
is
used
to
erase
the
character
typed.
A
different
current
carrying
time
exists
for
the
hammer
solenoid
to
print
a
character.
(Ex):
*
(Acharacter
with
a
small
surface
area)...Shorter
current
car-
rying
time
H
(A
character
with
a
larger
surface
area)...Longer
current
carrying
time
Print
wheel
—
‘Typing
ribbon
or
correction
tape

PA-W1400
[4]
ELECTRICAL
SECTION
plousjos
Jenup
JOJO!
td
Jenup
ASI
(1)
K
|
4JojOow
au
Aiddns
samod
eaqeBou
G07
(oLvsMvd
40)
Aluo)
unosto
qY6y)
yoRg
ull
9
X
O8
(iequp
win)
feued
GOT
eq1~001
@d0'1d0'S'W
L£dd~00d
SMA‘SOA‘S0A
(exkqyize)
WWHSd
vlWd-~0Vd
M3U'SVO'SVY
LVS~0VS:
(erkqyiv9)
WEG
4as~oas
OVS
{uellosjuoo
ysip
Addo)
Circuit
diagram
ods
41aSay
904
=}
zas~0as
;
|
sac
inal
LWS~0VS:
BLYS-~FIVS
awe
(wou
sew)
{
eoepequl
10}0W)
}
sseooe
WYO
eoeyoiu!
jeued
GO1
oid
sse908
WVHSd
yoo
NOISNVdX:
sng
ByeQ/SSe.PPY:
s010U
HMA

PA-W1400
(1)
outline
of
electrical
section
The
CPU
of
this
model
is
M50734SP,
which
is
a
C-MOS
8-bit
single-
chip
microcomputer
composed
of
the
M50740
CPU
core,
clocked
serial
I/O,
A-D
convertor,
watch
dog
timer,
and
35
lines
of
parallel
/O.
The
CPU
has
iMB
direct
access
memory
space
and
35
lines
of
VO
ports.
The
gate
array
(G.A.)
UPD65027G
is
provided
in
the
peripheral
of
the
CPU,
composing
the
bank
circuit.
ROM's
of
4MB
and
256KB,
dynamic
RAM
of
256KB,
and
static
RAM
(1051832)
of
256KB
are
used
to
store
all
control
programs
and
data
for
spell
check,
thesaurus,
and
grammar.
The
CR
(carrier)
motor,
WH
(wheel)
motor,
and
KEY
are
controlled
through
the
CPU
I/O
ports.
The
RB
(ribbon)
motor,
PF
(paper
feed)
motor,
HAMMER-solenoid,
LCD,
and
FDD
(floppy
disk
drive)
are
controlled
through
the
exten-
sion
ports
of
the
gate
array.
The
CPU
pin
configuration
and
block
diagram
are
shown
below:
CPU
block
diagram
XIN
XQUT
&
Program
counter
PCH
(8)
Program
counter
Pol
(8)
VREF
‘Accumulator
AB)
xe)
P4
&
analog
NO
port
Input
AN
u0(8)
sciK
isto
ADB(8)
P3(6)
‘Address
bus
A
‘Address
&
data
bus
A/D
VO
port
P3
WA
RD
SYNC
ALE
RESET
Voo(Sv)
VoC(Ol
“OO
Index
rapist
|
Index
register
(8)
CPU
pin
configuration
PO4/STBOUT
POS/OME
POBTXD
POTIRKD
PIO
Py
Pia
P13
Pia
VO
port.PO
VO
port.Pt
VO
port,P2:
VO
port.Pa:
P37
RESET
XIN
XOUT
(Ov)
vss
Reset
input
Clock
input
Clock
output
PUEEEPT
EEE
Eee
ea
teehee
Proscalor
PRE
1
(8)
Prosealer
PRE
2
(8)
‘Stack
pointer
S@)
Prescaler
PRE
3
(6)
99
fonicol
circuit
PIL@)
28)
WO
por
P2
P16)
VO
por
Pt
voc(sy)
POS/BUSTYOUT
POZCNTR
POWINT2
POOINTT
woout
Watchdog
timer
AorD0
VO
portPO
2qRB
overflow
output
AVI
agp
AgD3
Aaa
ASIDS
Asie
ArO7
‘Adress
latch
ALE
enable
output
ES
ESE EES
i
Address
Idata
bus
a
"Address
bus
VO
por.P4
Timer
1
TH)
Trstruction
ropistor
(8)
Timer
2
12(6)
Tratruction
JOME
decoder
Timer
3
13.(8)
Control
instruction
PWM
OUT.
Timer
§
18
@)
Timer
W.
we)
ONT
Timor
X
TX
(8)
INT
XD
Busy!
out
VO
pen
PO

PA-W1400
PA-W1410/1400
CPU
(M50734)
Pin
Configuration
Pin
|
CPUsignal
|
Cir
gram
; :
CPU
signal
|
Circuit
diagram
j
'
ad
nae
signal
name
|
YO
Signal
function
Neel
Sian
signal
name.
|
“0
Signal
function
Software
power
key
sense
|
|
33
P40
3
|_|
Default
print
pitch
(10/12)
1
Po4
PKY
1
signal
i
Pat
“4
1
|
Digital
tab
division
symbol
2
DWE
DME
°
Data
memory
access
(Jy)
_
signal
45
pas
-
,
|
Defautt
print
pressure
3
Pos
‘SCAN8
©
|
Data
scan
signal
(line
8)
(High/Low)
4
PO7
SCAN9
©
|
Data
scan
signal
(line
9)
36
p43
DISKCHANGE
|
1
Disk
change
generation
5
PIO
SCANO
Q
|
Data
scan
signal
(line
0)
signal
6
Pit
‘SCANT
(©
|
Data
scan
signal
(line
1)
37
VREF
GND
—
|
Power
source
(GND)
7
Pi2
‘SCAN2
©
|
Data
scan
signal
(line
2)
38
RD
RD
©
|
Data
read
timing signal
8
P13
‘SCANS
©
|
Data
scan
signal
(line
3)
39
WR
WR
©
|
Data
write
timing
signal
9
P14
‘SCAN4
(©
|
Data
scan
signal
(line
4)
[40
® ®
©
|
System
clock
signal
10
PIS
‘SCANS:
©
|
Data
scan
signal
(line
5)
41
|
syNc SYNC
°
conn
ee
read
11
PI6
SCANG
©
|
Data
scan
signal
(line
6)
jiming
signe”.
[2
iy
SCANT
©
|
Data
scan
signal
(ine
7)
|
42
AIS
AIS
(©
[Address
bus
signal
(bit
15)
|
Carriage
motor
excitement
43
A14
A14
©
|
Address
bus
signal
(bit
14)
|
13
P20
cM4
©
|
phase
signal
(-
B
phase)
44
A13 AIS
©
|
Address
bus
signal
(bit
13)
|
44
ral
Gas
©
|
Carriage
motor
excitement
45
A12
AI2
©
|
Address
bus
signal
(bit
12)
phase
signal
(—
A
phase)
46
Alt Alt
(©
|
Address
bus
signal
(bit
11)
45
p22
M2
°
Carriage
motor
excitement
47
A10
A10
|
Address
bus
signal
(bit
10)
phase
signal
(B
phase)
48
‘AQ
AQ
©
|
Address
bus
signal
(bit
9)
Carriage
motor
excitement
|
|
49
AB
AB
(©
|
Address
bus
signal
(bit
8)
16
P23
CMt
°
9)
a
Sone
(A
—
-
50
|
ALE ALE
0
|
Address
latch
timing
signal
el
motor
excitement
A
Ate)
Lares
WM4
_|
©
|
phase
signal
(-B
phase)
st
|
A7/07
aro?
|
vo
|
aeeressidata
bus
elgrell
Wheel
motor
excitement
7
18
_
wus
©
|
chase
signal
(-A
phase)
52
|
A6/D6
Aedes
=|
v0
mae
bus
signal
Wheel
motor
excitement
;
ig
F26.
wn.
©
|
chase
signal
(B
phase)
53
|
As/DS
A5/D5
|
VO
oreo
bus
signal
Wheel
motor
excitement
:
=
re
Mi
©
|
phase
signal
(A
phase)
54.
|
Aaa
aaa
=|
v0
foveal
bus
signal
24
P30
SENSEO
|
|_|
Key
sense
signal
(bit
0)
:
‘Address/data
bus
signal
22
P3t
SENSE1
1
[Key
sense
signal
(bit
1)
55
|
Aa/03
A3/D3
VO
|
pit
3)
2
[23
P32
SENSE2
|
1_|Key
sense
signal
(bit
2)
Addresses
gos
sgtal
[2a
P33
SENSES
|
1
|
Key
senso
signal
(bit
3)
Be
|.
Aes
A2D2
|
HO
wit
2)
25
P34
‘SENSES
|_|
Key
sense
signal
(bit
4)
=
er
aii
Vo
|
Address/data
bus
sigral
26
P35:
SENSES
|_|
Key
sense
signal
(bit
5)
(bit
1)
27
P36
SENSE6
|_|
Key
sense
signal
(bit
6)
538
|
ao/Do
A0/DO
vo
|
Address/data
bus
signal
28
P37
SENSE?
_|_1_|
Key
sense
signal
(bit
7)
(bit
0)
"os
29
|
RESET
RESET
|_|
System
reset
signal
59
|
woout
|
woouT
|
0
Baral
log
timer
outpvt
so
|
XIN
XIN
\
Saleen
a
ee
_
|
|
Cartage
origin
detecinng
signal
XOUT
ae
rol
eager
pte
1
|
Pot
HM
©
|
Hammer
drive
signal
Power
source
(GND)
62
Po2
BDRV
(©
|
Buzzer
drive
signal
63
P03
To
°
FDC
data
transmission
halt
signal
Power
source
(+5V)

PA-W1400
PA-W1410/1400
Gate
Array
Pin
Configuration
Signal
function
vo
Signal
function
1
VoD
|
—
|
Power
supply
(+5V)
—
|
+5V
power
XOUT
|__|
Clock
output
1_|
Internal
gate
reset
signal
XIN
1
[
Clock
input
‘©
|
Hammer
drive
signal
wR
1
[CPU
data
write
timing
signal
(©
_|
Power
OFF
signal
®
1_[
CPU
bus
oycle
signal
(©
|
LCD
scan
start
signal
AIS
|_|
CPU
address
bus
(Bit
15)
©
|
LCD
data
latch
timing
signal
AI4
|_|
CPU
address
bus
(Bit
14)
©
|
LCD
data
shift
lock
signal
XE]
|_|
CPU
address
bus
(Bit
13)
©
|
LOD
drive
power
AC—conversion
signal
22
1_|
CPU
address
bus
(Bit
12)
©
|
ECD
data
(bit
0)
Att
1_|
CPU
address
bus
(Bit
11)
©
|
LCD
data
(bit
1)
A10
1
|
CPU
address
bus
(Bit
10)
‘©
|
LCD
data
(bit
2)
a9
1
|
CPU
address
bus
(Bit
9)
‘©
|
LCD
data
(bit
3)
AB
1
[
CPU
address
bus
(Bit
8)
©
|
Ribbon
motor
exciting
phase
signal
(—B
phase)
ALE
1_|
Address
latch
enable
‘©
_|
Ribbon
motor
exciting
phase
signal
(B
phase)
GND__|
—
|
GND
=
[GND
GND
|
—
|
GNO
=
[GND
7
‘AD7
__|
VO
|
CPU
address/Data
bus
(Bit7)
©
_|
Ribbon
motor
exciting
phase
signal
(A
phase)
18
Kd6__|
UO
|
CPU
address/Data
bus
(Bit
6)
‘©
|
Ribbon
motor
exciting
phase
signal
(—A
phase)
19
ADS__|
VO
|
CPU
address/Data
bus
(Bit
5)
©
|
Wheel
motor
drive
signal
20
AD4
|
VO
|
CPU
address/Data
bus
(Bit
4)
©
|
Ribbon
motor
drive
signal
Fal
‘AD3__|
VO
|
CPU
address/Data
bus
(Bit
3)
©
|
Paper
feed
motor
drive
signal
22
‘AD2___
|
VO
|
CPU
address/Data
bus
(Bit
2)
©
|
Paper
feed
motor
exciting
phase
signal
(A
phase)
23
D1
__|
VO
|
CPU
address/Data
bus
(Bit
1)
©
|
Paper
feed
motor
exciting
phase
signal
(—A
phase)
24
‘ADO
_|
VO
|
GPU
address/Data
bus
(Bit
0)
©
|
Paper
feed
motor
exciting
phase
signal
(B
phase)
GND
[—
[GND
©
|
Paper
feed
motor
exciting
phase
signal
(—B
phase)
26
|
SWi__|
VO
|
Switch
inputt
©
|
Carriage
motor
drive
signal
sw2__|_1_|
Switch
input2
©
|
Floppy
disk
controller
select signal
28
[|
SW3__|
1
_|
Switch
inputs
(©
|
SOS
ROM
select
signal
29
|
swa__|_1_|
Switchinputa
(©
_|
4M
mask
ROM
select
signal
30
voo
|
—
|
Switch
input
—
|
45V
power
31
GND__|
—
[GND
—
[GND
32
PDS
_|
VO
|
Pseudo—SRAM
data
bus
(bit
3)
©
|
System
address
bus
signal
(bit
14)
33
PD2__|
VO
|
Pseudo—SRAM
data
bus
(bit
2)
‘©
|
System
address
bus
signal
(bit
15)
34
PD4
1/0
|
Pseudo—SRAM
data
bus
(bit
4)
©
|
System
address
bus
signal
(bit
16)
35
PD1__|
VO
|
Pseudo—SRAM
data
bus
(bit
1)
©
|
System
address
bus
signal
(bit
17)
36
PDS
_|
VO
|
Pseudo—SRAM
data
bus
(bit
5)
(©
_|
System
address
bus
signal
(bit
19)
37
PDO
_|
VO
|
Pseudo—SRAM
data
bus
(bit
0)
©
|
System
address
bus
signal
(bit
18)
38
PD6__|
VO
|
Pseudo—SRAM
data
bus
(bité)
—
|
@ND
39
PD7__|
VO
|
Pseudo—SRAM
data
bus
(bit7)
©
_|
System
address
bus
signal
(bit
7)
40
[GND
|
—
|
GND
©
|
System
address
bus
signal
(bit
4)
41
PAO__|
O
|
Pseudo—SRAM
address
bus
(bit
0)
©
|
System
address
bus
signal
(bit
3)
42
|
VCE
|
0
|
Pseudo—SRAM
select
signal
‘©
|
System
address
bus
signal
(bit
5)
43
PAI__|
O
|
Pseudo—SRAM
address
bus
(bit
1)
©
|
System
address
bus
signal
(bit
2)
44
|"
PA10
|
O
|
Pseudo—SRAM
address
bus
(bit
10)
©
|
System
address
bus
signal
(bit
6)
45
PA2__|
©
|
Pseudo—SRAM
address
bus
(bit
2)
©
_|
System
address
bus
signal
(bit
1)
46
[|
VOE
|
0
|
Pseudo—SRAM
data
output
allowing
signal
©
|
Dynamic
RAM
low
address
strobe
47
PA3__|
©
|
Pseudo—SRAM
address
bus
(bit
3)
©
_|
System
address
signal
(bit
0)
48
|
PAI?
|
©
|
Pseudo—SRAM
address
bus
(bit
11)
(©
|
Dynamic
RAM
data
write
timing
signal
49
PA4__|
©
|
Pseudo—SRAM
address
bus
(bit
4)
©
|
Dynamic
RAM
collum
address
strobe
50
PAS
|
©
|
Pseudo—SRAM
address
bus
(bit
9)
‘©
|
Notconnected.
51
PAS__|
O
|
Pseudo—SRAM
address
bus
(bit
5)
|_|
LCD
data
reversion
command
signal
52
PAB__|
©
|
Pseudo—SRAM
address
bus
(bit
8)
VO
|
System
data
bus
(bit
6)
53
PAB
__|_O
|
Pseudo—SRAM
address
bus
(bit
6)
VO
[
System
data
bus
(bit
7)
54
|
PAIS
|
©
|
Pseudo—SRAM
address
bus
(bit
13)
VO
|
System
data
bus
(bit
5)
55
PA7
__|
©
|
Pseudo—SRAM
address
bus
(bit
7)
VO
|
System
data
bus
(bit
4)
56
|
WWE
|
0
|
Pseudo—SRAM
data
write
timing
signal
VO
|
System
data
bus
(bit
2)
37
|
PAI2
|
©
|
Pseudo—SRAM
address
bus
(bit
12)
VO
|
System
data
bus
(bit
1)
58
|
_pAI4
|
O
|
Pseudo—SRAM
address
bus
(bit
14)
VO
|
System
data
bus
(bit
3)
59
|
DME
|
|
|
Datamemory
select
signal
UO
|
System
data
bus
(bit
0)
60
|
and
|
—[|GND
—
|
GND

[Description]
This
circuit
is
composed
of
the
six
functional
blocks:
the
power
source
block,
the
mechanism
drive
block,
the
key
control
block,
the
buzzer
drive
block,
the
LCD
block,
and
the
data
storage
block
(memory,
floppy
disk).
1.
Power
source
block
This
block
generates
DC
voltages
from
the
commercially
available
power
source
and
generates
the
circuit
reset
signal.
DC
power
circuit
block
diagram
Sig
hal
ei
|
eee
=
of]
veer
[fears
|
femotor
|
[aera
[Gea
re
LEE
mae
rs
cu
rr
PA-W1400
ne
ear
i
Ahi
Lees
hia
a)
ili
able
#
py
s
ii
=
oe
elena
de
ba
te
~~.
=
ae
(1)
DC
power
generating
block
DC
power
voltages
used
in
this
circuit
are
+15V,
-5V,
and
-24V.
The
block
diagram
of
the
DC
power
generating
block
is
shown
below:
1)
Transformer
and
rectifying
circuit
In
this
circuit,
the
commercially
available
power
is
transformed
into
the
secondary
voltage
(about
AC30V)
by
the
low-frequen-
cy
transformer,
then
rectified
by
DB1,
and
smoothed
by
C1
and
C2.
2)
Power
ON/OFF
circuit
When
the
power
key
is
pressed
OFF
without
storing
fre
data
prepared
in
this
machine,
this
circuit
confirms
storage
of
the
data
then
shuts
off
the
power
with
the
software.
‘To
supply power,
the
power
key
on
the
keyboard
is
pressed
to
turn
on
the
flip-flop
composed
of
Q1
and
Q2,
starting
me
self-
‘excited
switching
of
the
+15V
generating
circuit.
To
turn
off
the
power,
the
power
key
on
the
keytoard
is
pressed,
and
the
CPU
1-pin
becomes
0.8V
or
less.
It
isssensed
by
the
software.
After
confirming
the
power
OFF,
RSTI_
signal
at
gate
array
64-pin
is
made
high
to
tum
on
Q7.
As
a
result,
Q1
and
Q2
are
turned
off
and
the
self-excited
switchin,
of
the
+15
generating
circuit
is
stopped,

PA-W1400
3)
+15V
generating
circuit
When
Q2
in
the
power
ON/OFF
circuit
is
turned
on,
the
base
voltage
of
Q5
is
increased
through
R11
to
turn
on
Q5,
resul-
tantly
turning
on
Q12
and
Q13.
Thus
the
emitter
voltage
of
Q13is
increased
to
about
35V.
When
ZD6
cathode
voltage
increased
to
15V
or
more
through
L20,
Q4
base
voltage
increases
to
go
into
saturated
state,
turning
off
Q5,
then
turning
off
Q12
and
Q13.
When
the
power
transistor
Q13
is
turned
off,
a
counter-
electromotive
force
is
generated
by
the
energy
stored
in
L20,
and
the
power
is
discharged
through
D8.
When
ZD6
cathode
voltage
falls
below
+15V,
Q4
is
turned
off,
turning
on
Q§,
then
turning
on
Q12
and
Q13.
By
repeating
the
above
operation,
the
output
is
maintained
at
a
constant
level.
10s
cpu
(2)
Reset
signal
generating
block
4)
-24V
generating
circuit
This
circuit
utilizes
mutual
inductance
of
L20
in
the
+15V
generating
circuit
to
perform
full-wave
rectification
with
D4
~
D7.
Q8
is
turned
on
by
ZD1
(+30V)
to
generate
-24V.
The
-24V
is
used
as
the
negative
power
for
the
LCD
panel.
this
voltage
varies
the
contrast
of
the
LCD.
Time
lag
is
provided
to
the
negative
power
of
the
LCD
and
LCD
control
signal
for
Q9,
Q11,
and
Q10.
For
details
of
time
lag,
refer
to
the
reset
circuit
description.
5
4+5V
generating
circuit
This
circuit
stabilizes
+5V
with
the
Watt
resistor
and
5V
three-
terminal
regulator.
con
seo
ASE
COMED
This
block
generates
four
kinds
of
reset
signals:
CPU
reset
signal,
gate
array
reset
signal,
floppy
disk
controller
reset
signal,
and
liquid-crystal
negative
power
reset
signal.
‘These
signals
monitor
and
generate
+15V.
The
timing
chart
of
the
power
ON
and
OFF
is
shown
below:
Reset
timing
chart
AC
SW
OFF
AC
SW
ON
DB1+PIN
(Rectitying
bridge)
+15V
+5V
LCD
negative
chart
PKY
PsT1
‘CPU
RESET
&
LCD
negative
power
applying
signal
GATE
ARRAY
RESET
When
the
power
is
supplied,
the
CPU
reset
signal
is
charged
from
15V
through
R35
to
C16.
It
is
kept
low
until
C16
+
pin
voltage
exceeds
ZD2
VZ
(+4/2V).
When
it
exceeds
VZ,
the
reset
signal
becomes
high.
In
the
case
of
power
OFF,
the
reset
signal
be-
comes
low
from
high
when
+15V
becomes
about
10V.
Since
the
gate
array
reset
signal
must
be
released
at
least
4us
in
advance
to
the
CPU
reset
signal
in
order
to
take
synchionization
with
the
CPU
bus
cycle,
it
is
released
in
advance
to
the
CPU.
The
floppy
disk
controller
reset
signal
has
the
opposite
polarity
to
the
CPU.
Since
the
liquid-crystal
power
reset
signal
must
be
reeased
at
least
10ms
later
than
the
gate
array
reset
signal
when
the
power
is
supplied,
and
must
be
reset
at
latest
simultaneously
when
the
power
is
cut
off,
it
is
reset
at
the
same
timing
as
the
CPU
reset
signal.
2.
Mechanism
drive
block
This
block
is
composed
of
the
drive
section
of
the
four
pulse
motors;
CR
(CARRIER),
WH
(wheel),
RB
(ribbon),
and
PF
(paper
eed);
the
hammer
solenoid
drive
section,
and
the
CARRIER
origin
detecting
section.
(1)
Pulse
motor
drive
section
The
pulse
motor
is
controlled
by
the
motor
drive
signal
which
turns
‘on/off
the
power
applied
to
the
motor
and
the
motor excitag
signal
which
determines
the
motor
rotation
position.
The
motor
drive
signal
uses
the
gate
array
port
for
all
the
four
motors.
The
motor
exciting
signal
uses
the
CPU
port
2
(12~20
pin)
for
CR
and
WH
and
the
gate
array
port
for
RB
and
P=.
The
four
sections
of
this
block
have
virtually
same
drive
circuit
composition
and
the
same
control
system
though
the
motor
drive
devices
are
different.
Therefore
description
is
made
ony
on
the
CARRIER
motor.

Ses
Si
Te,
“Sim
te
ag,
Sr
“1
$B
omen
=
emo
PA-W1400
(ar
cue
ae
ay
so7s4sP
=
5
wr
Se
sree
2
Hs
phe
ee
He
&
th
=
if
t
tie
He
a
a
beter
=
=
Te
Each
exciting
phase
signal
outputted
from
the
CPU
is
amplified
by
IC6
and
used
to
determine
the
CR
motor
exciting
position.
By
making
CR
motor
drive
signal
(CDRV)
from
the
gate
array
high,
Q23
and
Q22
are
turned
on
and
+15V
is
applied
to
the
common
terminal
of
CR
motor,
increasing
the
motor
current.
While
by
making
CDRV
low,
Q23
and
Q22
are
turned
off
to
apply
the
standby
current
to
the
CR
motor
through
R58.
The
control
is
performed
by
two-phase
excitement
shown
in
the
timing
below.
The
current
applied
to
the
motor
common
terminal
is
controlled
by
the
CDRV.
1/10"
Spacing
timings
‘CORV
1
P23
(CM1)
—
P22
(CM2)
——
P21
(CM3)
‘P20
(CM4)
ifetalsislel7is;
9
[so
[oat
|
12
ad
“About
48ms
sal
(2)
Hammer
control
section
This
circuit
makes
the
hammer
ON
signal
from
the
gate
array
high
to
turn
on
Q20
and
Q19,
conducting
the
hammer
solenoid.
HY
>
ona
(3)
CARRIER
origin
detecting
section
When
the
CARRIER
comes
to
the
origin,
the
CPU
60
pin
be-
comes
low
(max. 0.8V)
and
is
detected
by
this
circuit.
wv
ico
Res
cPU
ws
Jt
one
wsoresp
°|2
ap
cn
<—
woe
ap
AO?“
caamien
ZERO
SENSE
3.
Key
control
block
This
circuit
uses
the
CPU
port
as
scan
line
(output)
and
sense
line
(input),
and
recognizes
the
pressed
key
with
the
combination
of
them.
The
scan
line
output
timing
is
as
shown
below:
This
machine
recognizes
78
keys
with
combination
of
10
scan
lines
and
8
sense
lines.
(The
right
and
left
shift
keys
are
common.)
The
key
matrix
is
as
shown
below:
(Key
scan
timing
and
cycles)
soavo
“FT
Scant
JTL.
scan2_|
J
im!
SCAN
3
n
aml
SCAN
4
J
ml
scans
_|
FT
SCAN
6
SCAN
7
SCAN
8
SCAN
9
ml
1
i
n
}¢e——11ms
>|
ber
(Keyboard
matrix)
SCANS
SCANS
SCANO
SCAN
Z
scanz
Z
scana
Z
scans
9
PtH
‘SCANS,
Pit
‘
SCANG
SCANT
DSS133
x
10
Lt
SENSEO
SENSES
SENSES
26)
A
senses
Ti
SeNse7
B
XXUXY

PA-W1400
4.
Buzzer
drive
block
This
circuit
utilizes
the
CPU
rectangular
waveform
output
function
to
output
rectangular
waveforms
from
port
0
bit
2
(IC9
62-pin),
driving
the
buzzer.
‘The
buzzer
oscillation
frequencies
are
about
4KHz
for
alarm
sound
and
about
600Hz
for
confirmation
sound.
5.
Liquid
crystal
display
block
This
circuit
is
composed
of
a
gate
array
and
a
pseudo-SRAM.
The
pseudo-SRAM
is
used
for
storing
displayed
data.
The
gate
array
mediates
with
the
CPU
for
access,
converts
data read from
the
pseudo-SRAM
into
data
for
the
LCD
unit,
and
outputs
the
data
with
display
control
signals
to
the
LCD
unit.
The
LCD
unit
control
signal
timing
is
shown
below:
LCD
unit
control
signal
timing
‘Second
tie
data
vansmassion
=A
A
A
«gt
the
data
rarsmission
/\
200th
ine
data
transmission
A
Fre
you
aims
138m6
M
iaeye
Pr 26
cycle
6.
Data
storing
block
This
block
is
composed
of
the
ROM
which
enables
data
reading,
RAM
which
can
be
read from
and
written
into,
and
the
floppy
disk
which
is
outside
the
PWB.
The
CPU
memory
map
is
shown
below
and
description
is
made
for
each
component.
CPU
memory
map
When
DME
is
high
(program
area)
When
DME
is
low
(program
area)
System
RAM
|
Maker
use
area
|
|
FG
stat
register
ROM
(Bank
0)
Mask
ROM.
FROM
(Common
area)
‘Mask
ROM
(1)
ROM
(Read
Only
Memory)
This
circuit
is
composed
of
a
4MB
mask
ROM
and
a
256KB
EPROM.
The
256KB
EPROM
is
SOS
ROM
which
is
not
installed
usually.
The
4MB
mask
ROM
pin
configurations
are
shown
bellow:
4MB
Mask
ROM
pin
configuration
Pin
description
AIT
AS
AT
5
Ag
AG
[]
Ato
AS
Att
A4
Oar
Ag
[]
ata
A2
Als
At
Oats
AO
Date
CELf10
31]
BYTE
eno
(14
30
[7]
GND
o£/0E
(]
12
29
|]
D15/A-
1(Note
1)
poL}13
28
|]
07
Ds
14
27
p14
ors
26
|]
pe
oe
[]16
25[_]
p13
pe(17
24]
Ds
dio
L]18
23[_]
p12
o3[]19
22[]
D4
DW
20
21
vec
Pin
name
AI~A17
Address
input
DO~D15
Data
output
CE
Chip
enable
input
Output
enable
input
(Note
2)
Byte
word
select
input
Power
pin
(SV)
(Note
1)
When
the
bit
composition
is
set
as
byte
mode,
29-pin
works
as
the
address
input
pin
(A-1).
When
the
bit
com-
position
is
set
as
word
mode,
it
works
as
the
dzfta
output
pin
(D15).
Bit
composition
setting
is
made
wth
BYTE
input
pin.
A-1
is
the
lowest
address
pin
in
the
byte
mode.
(Note
2)
The
active
level
of
OE/OE
is
mask
programmah
@.

(2)
RAM
(Random
Access
Memory)
This
circuit
is
composed
of
a
64K
x
4
bit
DRAM
(Dynamic
RAM),
32KB
pseudo-SRAM
(pseudo
Static
RAM,
TC51832),
and
gate
array.
When
the
CPU
makes
access
to
these
memories,
the
gate
array
performs
address
conversion
and
generates
read
timing
signal
and
refreshes
DRAM
memory.
The
DRAM
read/write
timing,
refresh
timing,
pseudo-SRAM
readiwrite
timing,
DRAM
pin
configurations,
and
pseudo-SRAM
pin
configurations
are
shown
below:
DRAM
Pin
description
oefh
[18]
vss
vor
[2
17)
04
voz
[3
16]
CAS
WE
[4
15]
VO3
RAS;
ae
as
[6
[ra]
at
as
[7
|
[12]
az
aa
[|
[11]
as
vec
[9
[10]
a7
Pin
name
Address
input
Line
address
strobe
Row
address
strobe
Column
address
strobe
AWE
‘Address
bus
(SAN:
n=0~7)
Data
bus
(SDn:
n-0~7,
PA-W1400
DRAM
(Dynamic
RAM)
read
cycle
timing
chart
Address
bus
(An:
n=0~7)
Data
bus
(Dn
:
ne0-7)
DRAM
(Dynamic
RAM)
retresh
cycle
timing
chart
Pseudo
—
SRAM
Pin
description
(TOP
VIE!
=
When
CE
is
LOW
and
OE
is
LOW,
tie
doves
data
VO
dopa
"data ouput
erate”
Note:
High:
2.4V
~
VDD.
LOW:
GND
~
0.8V

PA-W1400
Pseudo-SRAM
access
timing
chart
FDC
(Floppy
Drive
Controller)
‘signal
voE
«
x<
BEE
abagw
ezeo.
868
eScg
vor
BeSEeSSbSesaszae
VWE
=
seo;
SRRREKERARKL
SSS
SS]
oonoe
(PAN
:
n=O~14)
NC.
2
63)/—°OEM3
FLT
3
fe)
62}+-—roDS0
bus
on
n=0-7)
SIDE
6
61}-—oGnp2
Data
bus
GND20-——45
60/-—oDS1
(PDn
:
n=0~7)
FLTR:
6
59f-—rODS2
HDLD:
7
58{-——OGND2
GNOD20—78
57}-—*0DS3
(3)
Floppy
disk
NCO—19
56}-—>ODENt
.
55}-—OGND2
This
circuit
is
composed
of
a
3.5
inch
2DD
(double
side
double
Fe
sa{—e0DENO
density}floppy
disk
drive
(FDD)
and
a
floppy
disk
controller
(FDC)
eet
be
eaoGunt
(IC
name:
uPD72068GF).
Rapes
Fe
pPD72068G
52}—oxBa
The
FOC
pin
functions
are
as
shown
below:
ACTL
i
ENRW’
Floppy
disk
controller
pin
functions
Rae
‘
se
MSELO—*117
Signal
function
finger
Read/write
head
select
signal.
Head
1
at
LOW,
‘Roo
4
[SPE
|
O
|
heado
at
Hic.
we
i_|_
aside
|_1_|
FD
media
replaced
at
LOW.
re
go_[
READY
|
1
|
FDDreadiwrite
enable
at
LOW.
nco—|
79
|
RDATA
|
1
|
Read
data
from
FDD
exv1o—
ifthe
write
protection
notch
of
FO
media
is
set
78
|
WAT
|
|
|
atprotection
side,
LOW
is
inputted.
77
|
trKo
|
1
|
LOW
when
FDD
head
isat
the
most
outward
track.
vel
Be
LOW
when
wit
data
are
wansmited
ene
74
|
WOATA
|
©
|
Write
data
to
the
FDD.
FDD
head
shift
timing
signal.
73
|
STEP
|
©
|
4
track
tor
1
pulse.
i
ain
|
o.
|
FD
head
shit
direction
signal.
HIGH
when
shifting
the
head
outward.
FD
media
rotating
motor
rotation
start
signal.
89.
FMO:
©
|
Lowwhen
starting
rotation.
Drive
select
signal.
be
_
©
|
Lowwhen
input
signal
from
FDD
is
significant.
44
|
INDEX
|
1
|
LOW
when
FD
media
track
begins.
Device
hardware
reset
signal.
48
|
RESET
|!
|
Ach
when
resetting.
48
RD
|_|
Read
timing
signal
rom FOC
to
CPU.
LOW
when
reading
daia.
oe
a
|_|
Data
writing
timing
signal
from
CPU
to
FDC.
LOW
when
writing
data,
21
i
|
|
OPU
read/write
destination
select
signal.
LOW
when
selected
as
destination.
22 AO
|__|
FDC
intemal
register
select
signal.
25
Do_|_vO_|
FDC-GPU
readwrite
data
pin
(bit
0)
26
Dt
VO_|
FDC-CPU
readwrite
data
pin
(bit
1)
a7
D2__[
VO
|
FOC-CPUreadiwrite
data
pin
(bit
2)
28
D3___[
VO
|
FDC-CPUreadhwrite
data
pin
(bit
3)
30 D4
|
WO
|
FDC-CPU
read/write
data
pin
(bit4)
a
D5
|
WO_|
FDC-CPU
read/write
data
pin
(bit
5)
32
D6__|
WO
|
FOC-CPU
readiwrite
data
pin
(bit
6)
34
07
|
WO
|
FOC-CPU
readiwrite
data
pin
(bit7)
=
ie
|_|
FDD-FDC
data
transmission
halt
signal.
HIGH
when
halting.
Note
1:
High
:2.4V
~
VDD
Lo
IND
~
0.8V
Note
2:
FDC
=
Floppy
Disk
Controller
FDD
=
Floppy
Disk
Drive
Note
3:
Pins
not
listed
above
are
not
used
or
for
fixed
signals.

[5]
DISASSEMBLY
AND
ASSEMBLY
*
This
chapter
describes
the
disassembly
procedure.
For
assembly
procedure,
reverse
the
disassembly
procedure.
For
the
procedure
which
requires
special
care,
[Note
for
disas-
sembly/assembly)
is
provided.
For
lubrication,
refer
to
the
section
on
lubrication
and
greasing
given
hereinafter.
Disassembly
and
assembly
procedures
must
be
performed
deliberately
in
order
to
assure
the
reliability
of
the
product.
*
Descriptions
for
simple
and
easy
replacement
of
units
and
parts
are
omitted.
1.
Upper
cabinet
(Fig.
5-1,
Fig.
5-2)
(1)
2)
(3)
Remove
platen
knob
L
and
R
@.
Remove
four
screws
@.
Use
two
(-)
screwdrivers
and
pick
sections
@
to
open
the
upper
and
the
lower
cabinets.
[Fig.
5-2]
[Fig.
5-1]
PA-W1400
Lift
the
right
side
of
the
upper
cabinet
and
remove
from
the
platen
shaft
right
side
®.
Slide
the
upper
cabinet
to
the
left
to
separate
it
from
the
lower
cabinet.
(6)
Remove
the
display
unit
from
the
cable.
[Note
for
disassembly/assembly]
a.
Before
opening
or
assembling
the
upper
cabinet,
be
sure
to
remove
the
display
unit
cable
from
the
main
PWB
or
attach
it
to
the
main
PWB.
(The
display
unit
cable
is
assembled
in
the
upper
cabinet.)
b.
As
shown
in
Fig.
5-2,
when
opening
or
assembling
the
upper
cabinet,
be
careful
not
to
hit
the
PF
holder
spring
©
in
the
left
side
of
the
mechanism
unit.
(If
the
spring
is
stretched
out,
replace
it
with
a
new
one.)
(See
Fig.
5-2.)
c.
When
installing
the
upper
cabinet,
carefully
protect
the
LCD
cable
from
being
caught
by
the
printer
unit
and
the
key
top.
(4)
(5)
2.
LCD
unit
(See
Fig.
5-3.)
(1)
(2)
Remove
the
upper
cabinet.
(See
"1.
Upper
cabinet”
above.)
Place
the
upper
cabinet
upside
down.
Use
the
LCD
removing
tool
(UKOGM2024CSZZ)
to
push
projection
®,
lift
the
LCD
unit
towards
®,
and
remove
it
from
the
guide
section.
(There
are
two
projections
in
the
both
sides.)
Move
friction
arm
@
in
the
direction
©
to
remove
it
from
LCD
unit
®.
(there
are
two
friction
arms
in
both
side.)
Remove
the
one
side
of
tilt
spring
@
from
section
©
of
the
LCD
unit.
(Two
sides.)
Remove
LCD
unit
®.
At
that
time,
remove
also
the
cable
from
the
LCD
unit.
(3)
(4)
LCD
removing
tool
(UKOGM2024C8Zz)
IFig.
5
[Note
for
disassembly/assembly]
a.
Friction
arm
@
and
friction
spring
@
are
heavily
greased
with
screw
grease
(UKOG-0185CSZZ).
Be
careful
to
the
greasi,
b.
Aheavy
pressure
on
the
liquid
crystal
glass
may
break
the:glass.
c.
If
friction
spring
@
is
not
greased
with
screw
grease,
bessure
to
apply
about
0.29
of
screw
grease
to
the
whole
surface
oi
-friction
spring
@.
(for
details,
refer
to
"Lubrication
and
greasing.")

PA-W1400
3.
LCD
cabinet
(Fig.
5-4)
(1)
Remove
the
upper
cabinet.
(See
"1.
Upper
cabinet.")
(7)
Remove
LCD
unit
©
and
volume
knobs
@
and
@.
(Handle
with
(2)
Remove
the
LCD
unit.
(See
"2.
LCD
unit.")
care.
They
are
fragile.)
(3)
Putthe
LCD
unit
upside
down,
and
remove
four
screws
©.
(8)
Remove
connector
©)
o
invertor
unit
@
and
remove
CCFT
ek.
‘
(cool
cathode
ray
tube)
®.
(4)
Insert
a
screwdriver
into
position
®
to
open
the
display
cabinet
o
BQ.
Postion,
©1099
iia
eas
(9)
Remove
two
stay
rubbers
A
@
and
stay
rubber
B
@.
(5)
Remove
the
four
screws
@
and
remove
the
stay
angle
@.
(10)
Remove
the
invertor
unit
@
from
two
pawis
on
display
cabinet
A
(Be
careful
that
the
installing
direction
differs
in
the
PA-W1400
®.
and
the
PA-W1410.)
(11)
Remove
correction
sheet
@.
(6)
Use
point
©
as
a
fulcrum
to
lift
section
®
towards
©
and
(12)
Remove
two
tilt
pins
@
and
two
tile
springs
@
from
display
remove
back
board
@).
(Lift.section
@
towards
©
in
order
not
cabinet
A@.
‘
to
make
contact
with
CCFT
(cool
cathode
ray
tube)
®.
Pe
i
|
|
=
ae)
iy
s
1
PA-W1400
f
¢
PA-W1410
The
chipped
part
Fig.
5-4)

(Description
on
the
tilt
mechanism)
The
tilt
mechanism
functions
to
set
the
LCD
unit
to
a
desired
angle.
LCD
unit
@
is
liked
with
arm
@
(the
link
shaft)
and
a
friction
is
applied
to
arm
@.
@
Upper
cabinet
@®
Lop
unit
eS
@
Friction
spring
IFig.
5-5]
(Descriptions
on
the
backlight
and
the
photoconductive
plate)
+
The
PAW1410
employs
the
edge-light
system
backlight.
The
light
emitted
from
CCFT
(cool
cathode
ray
tube)
©
is
radiated
on
the
‘edge
of
the
photoconductive
plate
to
illuminate
the
LCD
evenly.
@
Correction
sheet
Vv,
@
Stay
angle
LCD
PWB
unit
Photoconductive
plate
IFig.
5-6]
Bent
portion
IFig.
5-7]
Note:
Be
careful
to
the
photoconductive
plate
mounting
direction.
‘The
transparent
surface
must
come
onto
the
CCFT,
and
the
notched
surface
must
come
onto
the
stay
angle.
*
The
CCFT
(cool
cathode
ray
tube)
is
driven
and
controlled
by
the
invertor
unit.
PA-W1400
(Note
for
disassembly/assembly)
a.
b.
c.
4.
(1)
(2)
(3)
(4)
<A
(1)
(2)
(3)
(4)
Before
servicing
work,
be
sure
to
turn
off
the
power
source.
Be
careful
not
to
allow
foreign
materials
to
enter
the
unit.
Cover
the
photoconductive
plate
with
the
correction
sheet
to
in-
hibit
leakage
of
light.
|.
Be
careful
to
the
mounting
directions
of
the
stay
angle
and
the
photoconductive
plate.
(refer
to
Fig.
5-5
and
Fig.
5-6.)
.
Carefully
treat
the
CCFT
and
the
LCD
unit
because
they
are
fragile.
Keyboard
unit
(Refer
to
Fig.
5-8.)
Remove
the
upper
cabinet.
(For
removing
procedure,
refer
to
(5)-1,)
Put
down
the
shaded
portion
of
fixing
paw!
®
in
the
arrow
direction
and
release
the
lock.
Lift
the
keyboard
in
the
arrow
direction
and
remove
it.
Disconnect
the
keyboard
flat
cable
©
and
©
from
the
main
Pwe.
ssembly
procedure>
Set
the
dent
portion
of
the
keyboard
to
fixing
pawl
@).
Two
ribs
are
provided
at
the
lower
rear
side
of
the
board.
Insert
the
ribs
into
holes
©
and
©.
Bend
the
shaded
portion
of
paw!
in
the
arrow
direction
and
hang
on
the
lock.
Confirm
insertion
of
the
key
angle
projection.
a.
5.
(1)
(2)
(3)
(4)
6)
IFig.
5-8]
(Note
for
disassembly/assembly)
When
the
board
is
hanged
on
fixing
pawl
@,
do
not
rotate
in
direction
of
®.
.
Do
not
bend
fixing
pawl
@
excessively.
.
The
flat
cable
terminal
must
not
be
folded.
|.
Check
that
key
angle
@
projection
and
section
©
of
ke
yboard
unit
D.
Mechanical
unit
(Refer
to
Fig.
5-9.)
Remove
the
upper
cabinet.
(For
removal
procedure,
refer
to
(5}1.)
Remove
keyboard
unit
(.
(For
removal
procedure,
refer
to
[5}-
4)
Remove
two
screws
@
which
are
fixing
mechanical
unit
@
to
lower
cabinet
©.
Disconnect
cable
connectors
@,
©,
D,
and
®
(wiiéch
are
connected
with
main
PWB
@)
from
the
mechanical
unit.
Remove
mechanical
unit
@.
This manual suits for next models
1
Table of contents
Other Sharp Computer Hardware manuals
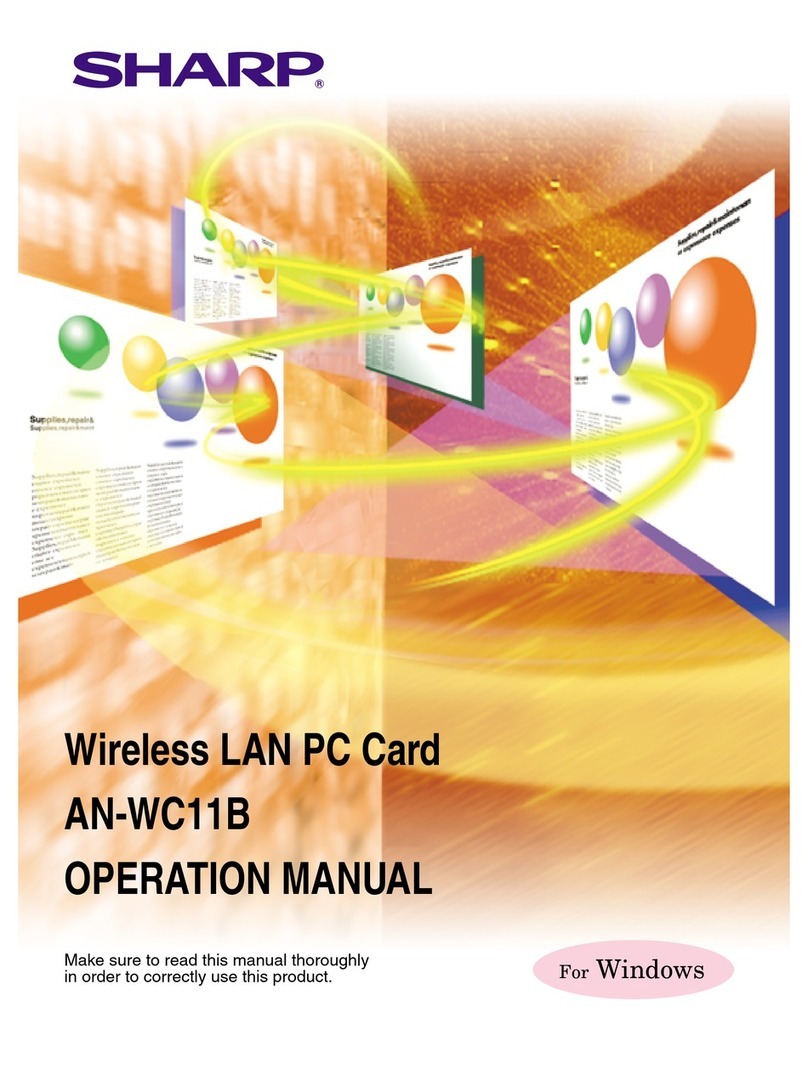
Sharp
Sharp AN-WC11B User manual
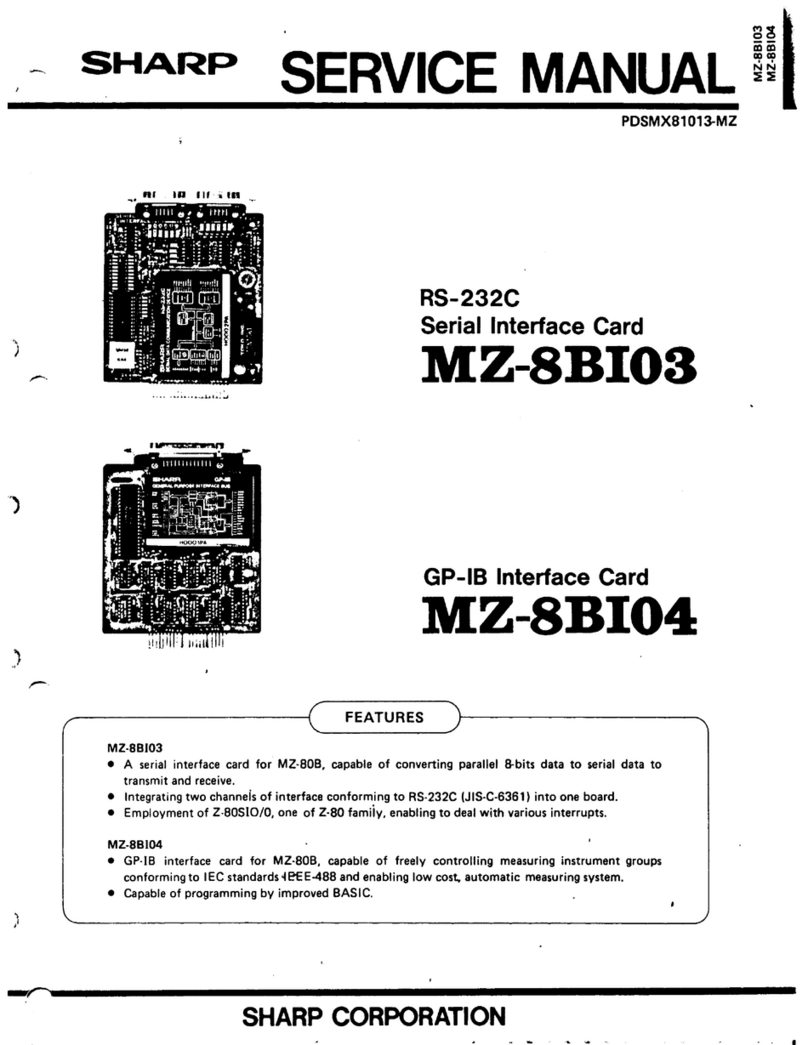
Sharp
Sharp MZ-8BI03 User manual
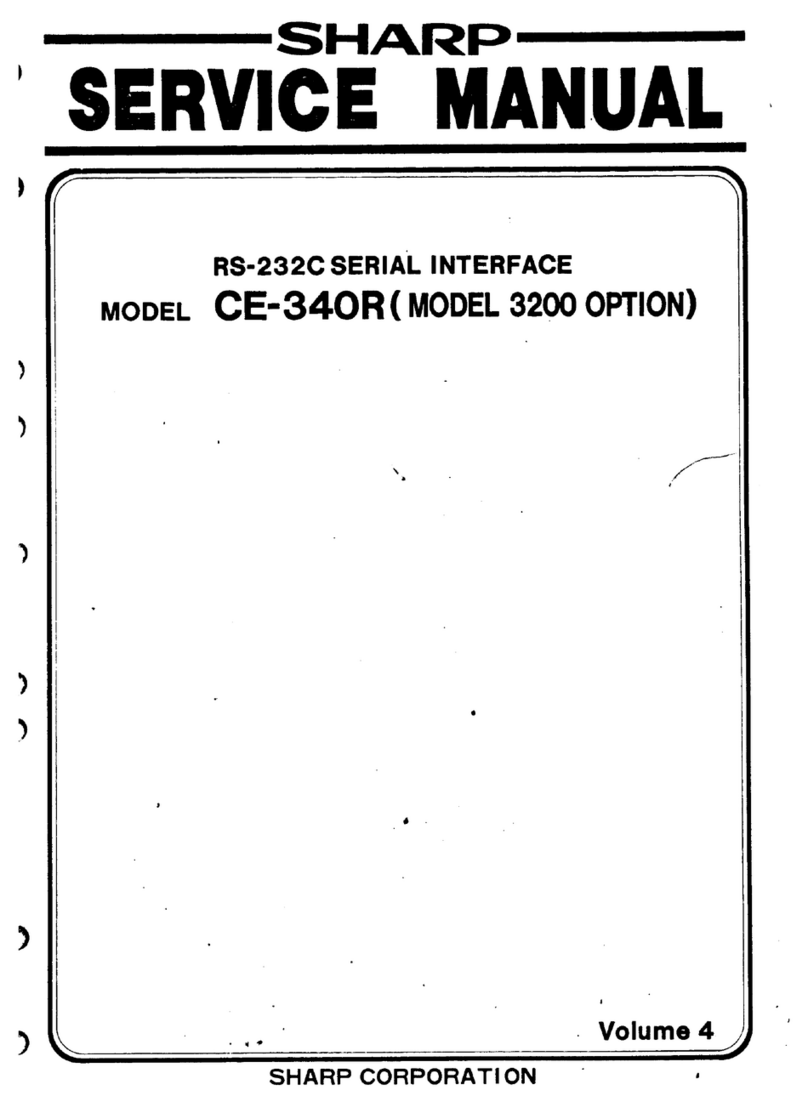
Sharp
Sharp CE-340R User manual
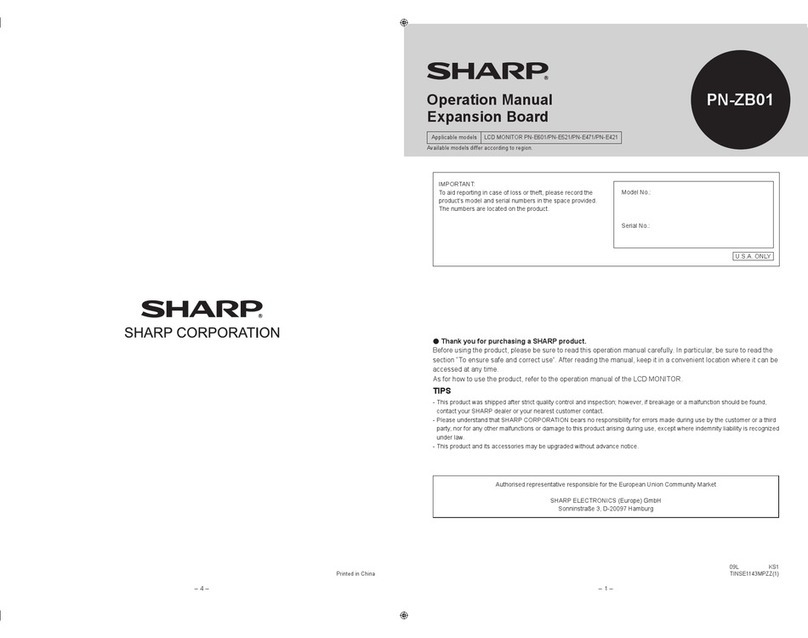
Sharp
Sharp PN-E471R User manual

Sharp
Sharp JW-20FL5 User manual
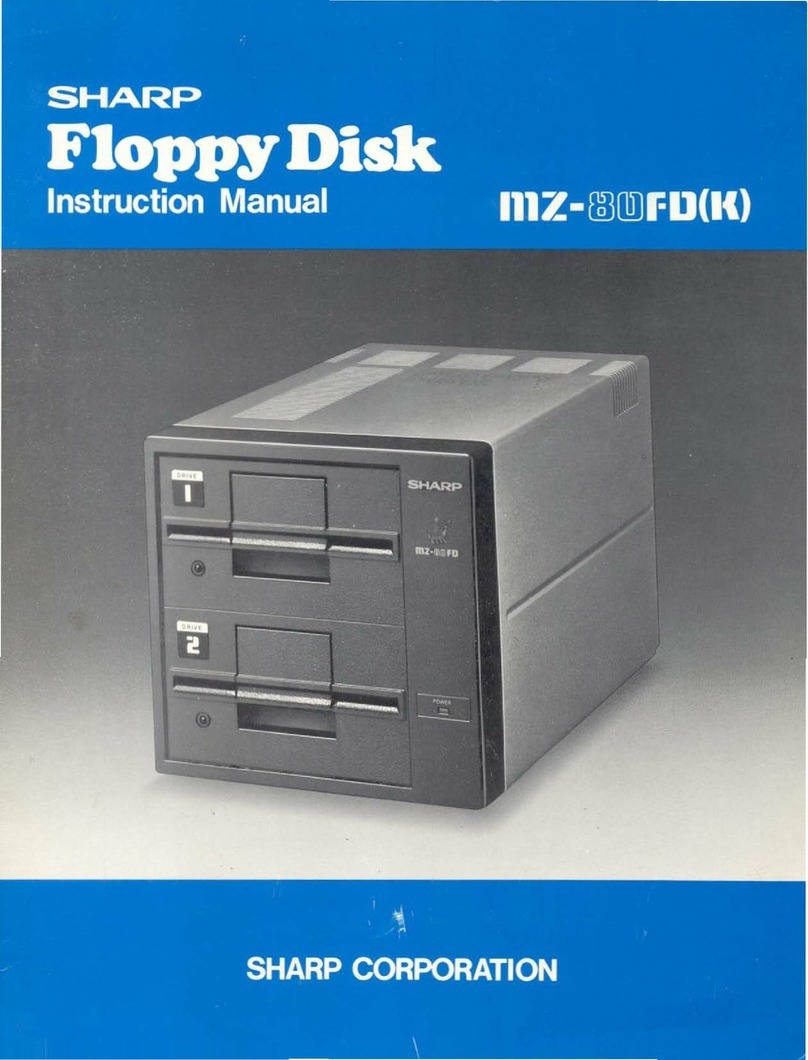
Sharp
Sharp MZ-80FD(K) User manual
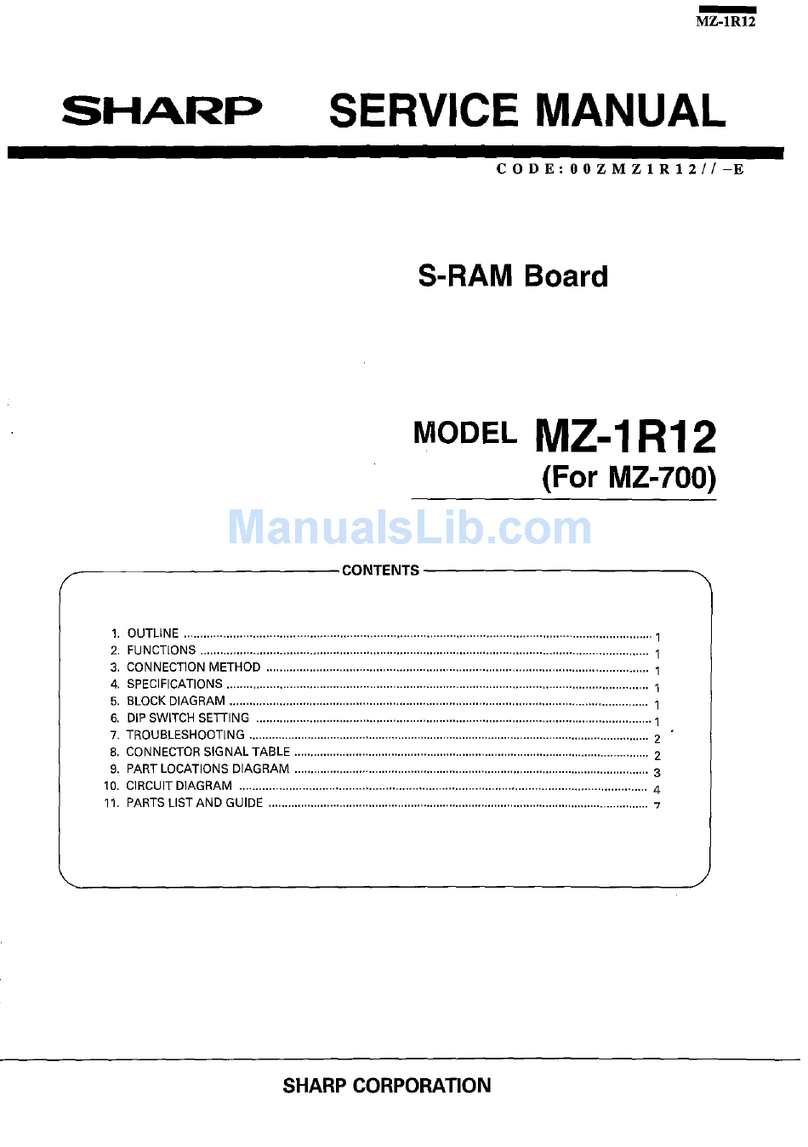
Sharp
Sharp MZ-1R12 User manual

Sharp
Sharp PN-ZB01 User manual
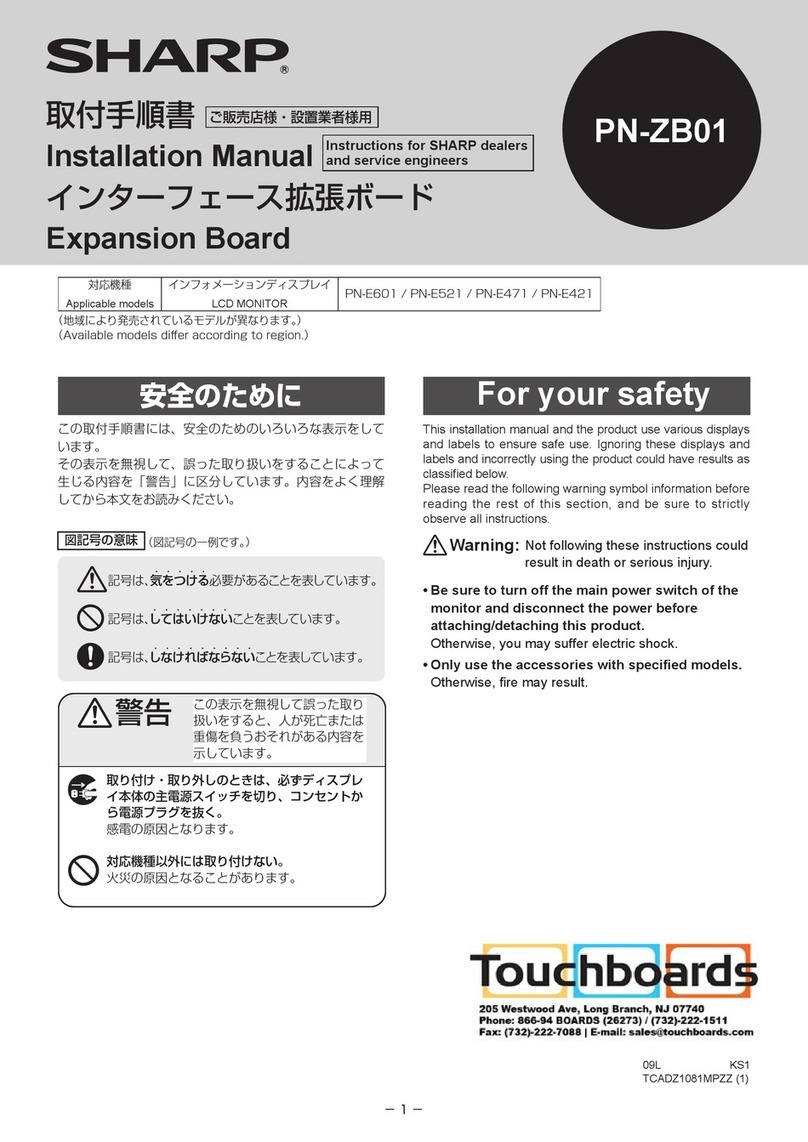
Sharp
Sharp PN-ZB01 User manual
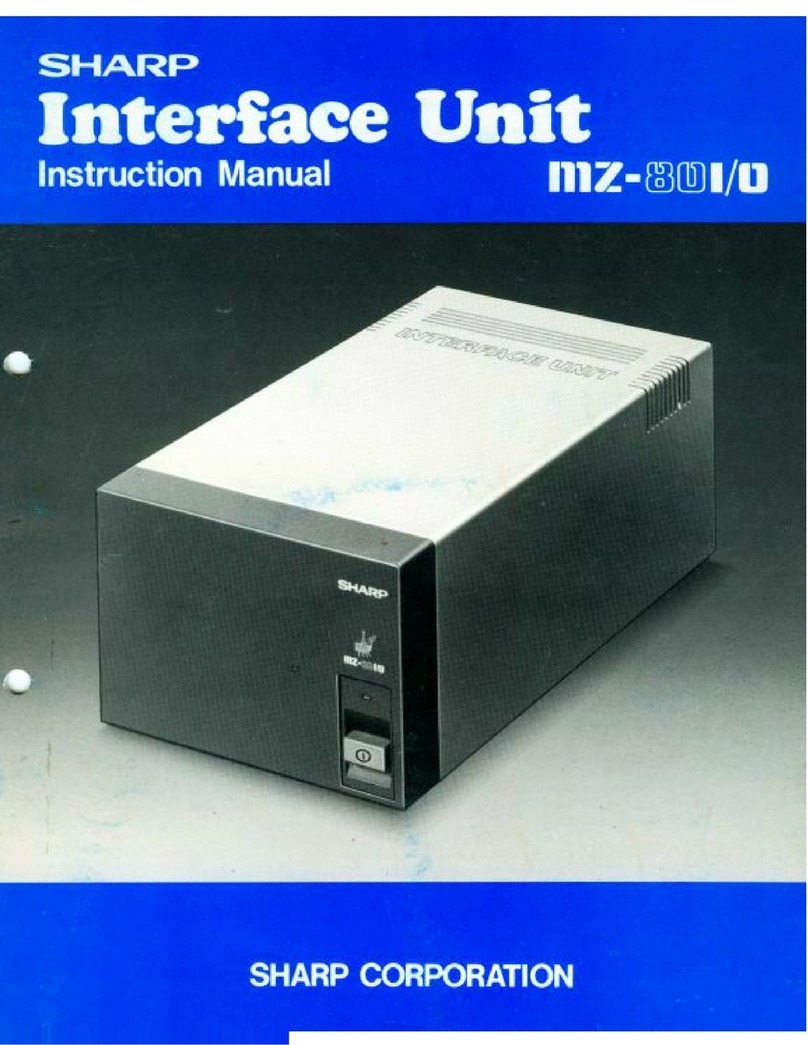
Sharp
Sharp MZ-801/0 User manual