Sices DST4602 Manual

The following indications have been used to identify the safety messages in this manual:
WARNING! This indication is used in the safety messages for risks which, unless avoided, can
cause malfunction or damage to property or persons.
This area, which is composed by a display and buttons, allows the visualization of the configuration parameters, the
plant status, the electrical measures, the engine analogue and digital measures, the digital IN/OUT signals acquired
and the historic visualization of the events and the measures.
The navigation is organized in menus and pages. The UP and DOWN buttons allow the vertical moving through menus
and configuration parameters. The LEFT and RIGHT buttons allow to move through pages of the same menu. The
ENTER allows to access the PROGRAM submenus, to enable the value adjustment. ACK allows to silence the horn
and to acknowledge a Warning/Alarm.
The EXIT button allows to return to the previous menu, to cancel an adjustment in progress. The SHIFT button allows
to increase up to x10 the movement of values or to vary the display light. Depending on the environmental lighting
conditions, a contrast adjustment may be required in order to view the display correctly. Press the buttons sequence
SHIFT + LEFT to decrease the contrast and SHIFT + RIGHT to increase it.
This area, composed by buttons and LEDs or key switch, allows the choice of the operating mode of the plant:
PROGRAM-OFF/RESET, MANUAL, AUTOMATIC-TEST.
In order to modify the operating mode, it is necessary to press the
UP or DOWN button for some seconds. The LED on, in relation to
the symbols, indicates the current operating mode on the device.
With the key switch version, it is necessary to turn the key to the
correct position.
•PROGRAM –OFF/RESET (Engine Stopped): In this mode, the
control and switching commands are disabled. In this status, no
faults (warning/alarm) are revealed. By means of buttons UP and
DOWN, view page PROGRAMMING. Press ENTER to access the configuration menu and adjust the available
parameters (some parameters may require a password).
•MAN. (Engine Started/Stopped): In this mode, the control commands are enabled. It is
possible to start the engine by pressing the START button and stop the engine with the
STOP button. With genset running and electrical measurements in tolerance, it is possible
to use the GCB button to open/close the GCB circuit breaker/changeover switch with
possible synchronisation, according to the configuration and
status of the plant.
•
In parallel with Mains powering the LOAD; if the button is
pressed, it activates the fast unload ramp before the circuit
breaker opens.
In case no ramp is needed, simply keep the GCB button
pressed for a few seconds and until the circuit breaker opens.
The MCB button is used to open and/or close the Mains contactor/circuit breaker to the Load. With engine not
running, you can open the Mains MCB circuit breaker by pressing and holding the MCB button for at least 5 (five)
seconds.
Evolution

INFORMATION! For some types of plants, the sequences depend on the Software and Hardware
configuration of the plant during the installation activity.
•AUTO (Engine Started/Stopped automatically): In this mode, according to the operating conditions, the device
starts the genset (START), manages the GCB closing if needed, and checks the electrical measurements.
WARNING! The STOP button, causes the stop of the Generator if running and the activation
of a lockout, unless configured otherwise.
According to the configuration set, if the Genset operation is no longer required, the device carries out the
power discharge and/or open the GCB and carries out the engine cooling for the time set. Once the cooling is
over, it stops the engine (STOP).
WARNING! Assigning an incorrect value to one or more parameters can cause malfunctioning or
damage to things and/or people. The parameters changes must be carried out only by skilled personnel.
Parameters may be password protected (see par. Access codes).
In order to adjust the parameters, it is necessary to enter the PROGRAMMING menu (page P.XX).
The access to the parameters programming mode can be protected by 3or 4different PASSWORD levels (it
depends on the device), which are listed in order of priority.
1. SICES Password (Only for Parallel plants)
2. Maker Password
3. System Password
4. User Password
If the password is lost, you can reconfigure it using a higher level password. Contact the technical support if
the “MAKER” password is lost.
Enter the authentication password on page 1.1.1.Authentication. To access, enter the various menus and
submenus following the path: PROGRAMMING, 1. SYSTEM, 1.1 Safety , 1.1.1. Authentication The (000-Access
Code) page of the Safety 1/02 menu requires the setting of the access code if one or more passwords have been
assigned. The password is not assigned if equal to 0.The set access code remains in the memory for about 10
minutes after programming has been completed. After that, it must be entered again to access the programming
mode.
Parameters settings
In the PROGRAMMING page, enter the submenus with the ENTER button. Use the UP and DOWN buttons to select
the submenu required and the ENTER button to access it. Select the submenu or the parameter required with the UP
and DOWN buttons. By pressing ENTER, you enable the adjustment of the parameter value that is signalled by the
square brackets [..] flashing. Use the UP and DOWN buttons to change the value and press ENTER to confirm or
EXIT to cancel the change. If the square brackets are replaced by the symbols < >, it means that the change of the
parameter value is not allowed. This can happen for lack of Password authorizations or in case you are trying to change
a parameter in a mode that is not allowed: some parameters can be changed only in PROGRAM –OFF/RESET mode.
Press EXIT to exit the programming menu.
Language selection
To select a different language from the one set, view the screen S.03 (BOARD STATUS) using the navigation buttons.
To change the LANGUAGE press ENTER: the square brackets [..] will flash. Use the UP and DOWN buttons to check
the languages available, then press ENTER to confirm. EXIT cancels the change.
Parameters for protections and alarms
The protections and the alarms are usually adjustable by means of proper variables. Usually, the intervention time
related to the protection can be configured too.
By setting the acquisition time at 0 (zero), the protection is deactivated.
Parameter description
U.M.
Value
Parameter description
U.M.
Value
SYSTEM
P.0107
Primary of C.T. auxiliary current
A
5
P. 0001
Maker password
0
P.0139
Secondary of C.T. auxiliary current
A
5
P. 0002
System password
0
P.0109
Transformer type for aux. current
0
P. 0003
User password
0
P.0130
Usage of auxiliary current
0
P. 0802
Plant type
4
P.0317
Currents unbalance threshold
%
5.0
MAINS
P.0318
Currents unbalance delay
s
0

Parameter description
U.M.
Value
Parameter description
U.M.
Value
P. 0116
Mains/Bus nominal voltage
V
400
P. 0481
Load thresholds mode
0
P. 0119
Mains/Bus number of phases
3
P. 0482
Initial delay
s
5
P. 0201
Mains measures hysteresis
%
2.5
P. 0483
Low power threshold
%
0.0
P. 0203
Mains low voltage threshold
%
80.0
P. 0484
Low power delay
s
60
P. 0204
Mains high voltage threshold
%
110.0
P. 0485
High power threshold
%
0
P. 0205
Mains presence delay
s
30
P. 0486
High power delay
s
3
P. 0206
Mains fault delay
s
2
ENGINE
P. 0236
Mains low frequency threshold
%
90.0
P. 0700
Engine type
0
P. 0237
Mains high frequency threshold
%
110.0
P. 0703
Control level via Can-Bus
0
P. 0238
Mains voltage unbalance threshold
%
10.0
P. 0709
Action on Can-Bus fault
1
P. 0847
MCB supplied by the Mains?
1
P. 0710
Idle speed
rpm
800
P.0126
Mains/Bus sensor usage
0
P. 0110
Pick-up teeth number
0
P.0855
MCB mode
1
P. 0125
Engine nominal power
kW
0
GENSET
P. 0210
Starting pulse duration
s
5
P. 0102
Generator nominal voltage
V
400
P. 0211
Starting attempts number
3
P. 0101
Generator number of phases
3
P. 0212
Pause between starting attempts
s
5
P. 0854
GCB mode
1
P. 0213
Stopping pulse duration in excitation
s
20
P. 0105
Nominal frequency
Hz
50
P. 0214
Stopping cycle duration
s
20
P. 0202
Generator measures hysteresis
%
2.5
P. 0215
Cooling cycle duration
s
45
P. 0106
Generator nominal power
kVA
0
P. 0333
Pick-up over speed threshold
%
120.0
P. 0218
Delay before supply
s
5
P. 0334
Pick-up over speed delay
s
0.5
P. 0219
Contactors swap delay
s
2
P. 0331
Over speed (frequency) threshold
%
120.0
P. 0301
Minimum voltage threshold
%
75.0
P. 0332
Over speed (frequency) delay
s
0.5
P. 0302
Minimum voltage delay
s
3
P. 4017
Oil pressure sensor type
0
P. 0303
Maximum voltage threshold
%
112.5
P. 4025
Cooling temperature sensor type
0
P. 0304
Maximum voltage delay
s
3
P. 4033
Fuel level sensor type
0
P. 0305
Minimum frequency threshold
%
90.0
P. 0335
Cooling liquid high temp. threshold
°C
92
P. 0306
Minimum frequency delay
s
5
P. 0336
Cooling liquid high temp. delay
s
2
P. 0307
Maximum frequency threshold
%
110.0
P. 0337
Cooling liquid max. temp. threshold
°C
110
P. 0308
Maximum frequency delay
s
5
P. 0338
Cooling liquid high temp. delay
s
2
P. 0309
Maximum current threshold
%
90.0
P. 0339
Low oil pressure threshold
Bar
1.5
P. 0310
Maximum current delay
s
10
P. 0340
Low oil pressure delay
s
2
P. 0311
Short circuit threshold
%
500
P. 0341
Min. oil pressure threshold
Bar
1.2
P. 0312
Short circuit delay
s
0.5
P. 0342
Min. oil pressure delay
s
2
P. 0313
Power reverse threshold
%
10.0
P. 0343
High fuel level threshold
%
90
P. 0314
Power reverse delay
s
10
P. 0344
High fuel level delay
s
2
P. 0315
Voltage unbalance threshold
%
2.5
P. 0345
Low fuel level threshold
%
10
P. 0319
Required phase sequence
0
P. 0346
Low fuel level delay
s
2
P. 0320
Action on wrong phases sequence
1
P. 0347
Min. fuel level threshold
%
5
P. 0321
Loss of excitation threshold
kvar
0
P. 0348
Min. fuel level delay
s
20
P. 0323
Action on max. current/short circuit
8
P. 0349
Delay for belt break
s
20
P. 0324
50V-51V protections enable
0
P. 0353
Cooling liquid low temp. threshold
°C
10
P. 0350
Maximum power threshold
%
100.0
P. 0354
Cooling liquid low temperature delay
s
0
P. 0351
Maximum power delay
s
0
P. 0357
Protection for belt break
8
P. 0352
Action on maximum power
1
P. 0400
Fuel pump mode
0
P. 0107
C.T. Primary
A
5
P. 0402
Fuel pump activation threshold
%
15
P. 0139
C.T. secondary
A
5
P. 0403
Fuel pump deactivation threshold
%
80
P. 0124
CT connection
0
P. 0405
Fuel pump and electrovalve delay
s
2.0
P. 0131
Connection for auxiliary current
0
P. 0404
Fuel pump maximum activation time
s
0
Supply voltage:
8..33Vdc
Operating temperature:
-25°C .. 60°C
Current consumption
1100 mA max
External dimensions:
260(L)x202(H)x79(D)mm
Genset rated frequency:
50/60 Hz
Panel cut-out
240(L)x172(H)mm
Other manuals for DST4602
2
This manual suits for next models
1
Other Sices Computer Hardware manuals
Popular Computer Hardware manuals by other brands
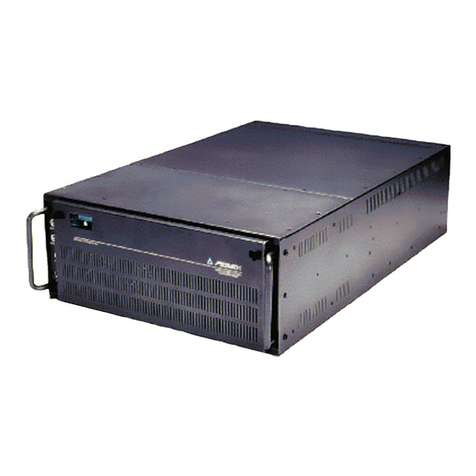
Peavey
Peavey MediaMatrix MM-950 Specifications
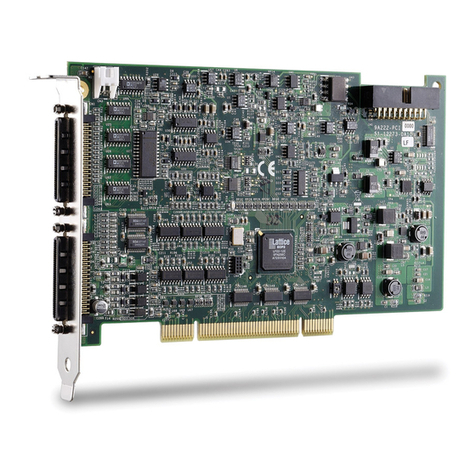
ADLINK Technology
ADLINK Technology NuDAQ PCI-9222 user manual
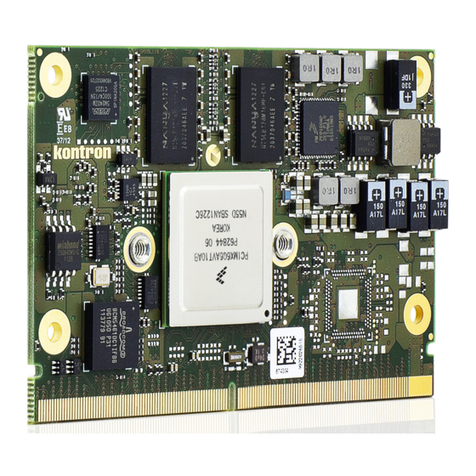
Kontron
Kontron SMARC-sAMX6i user guide
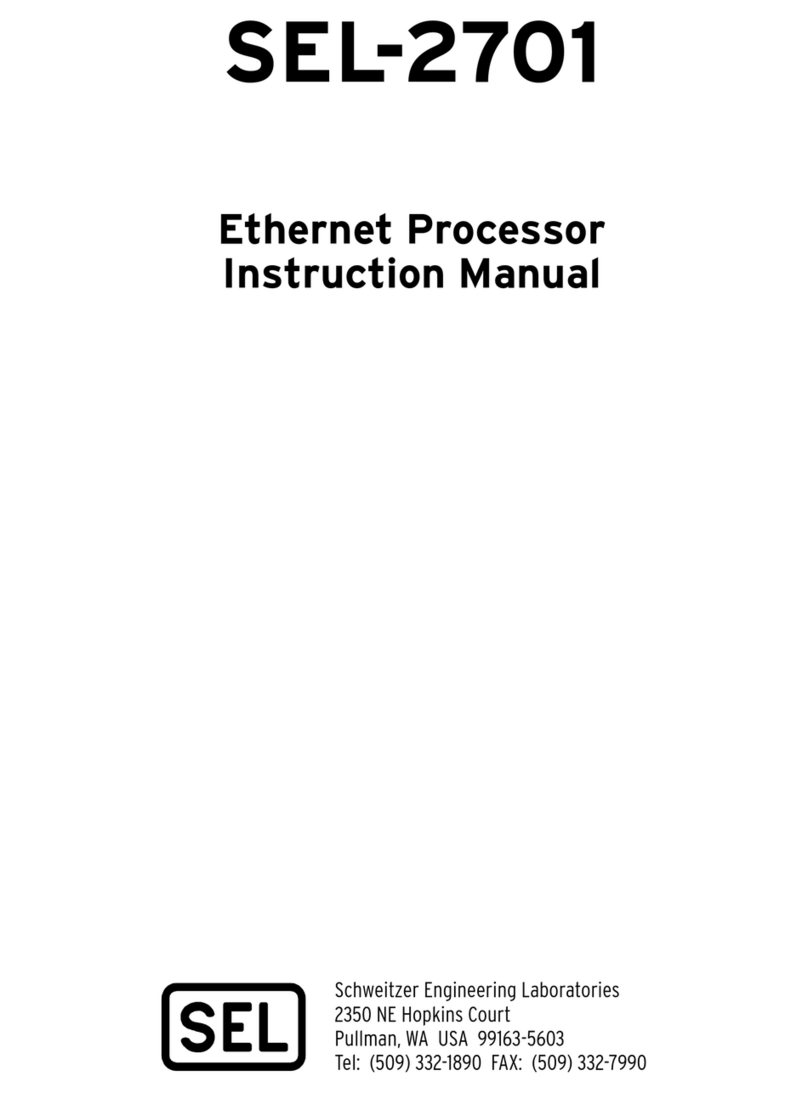
Schweitzer Engineering Laboratories
Schweitzer Engineering Laboratories SEL-2701 instruction manual
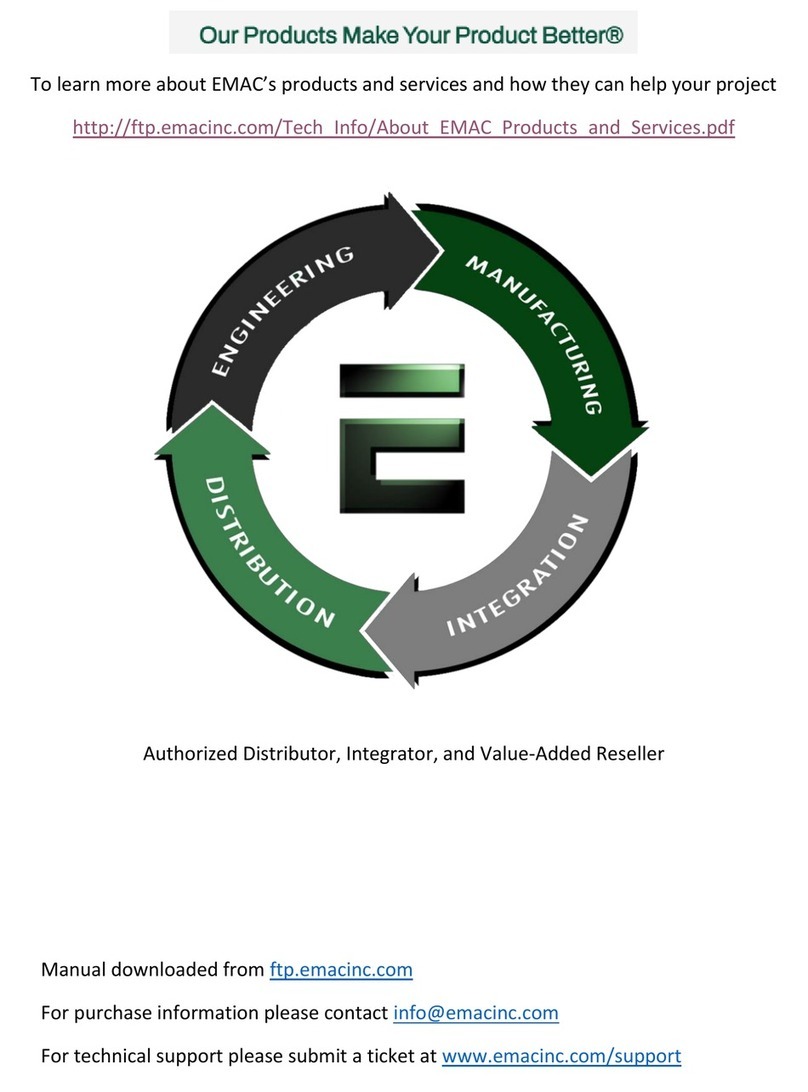
EMAC
EMAC CPC-2400 user manual
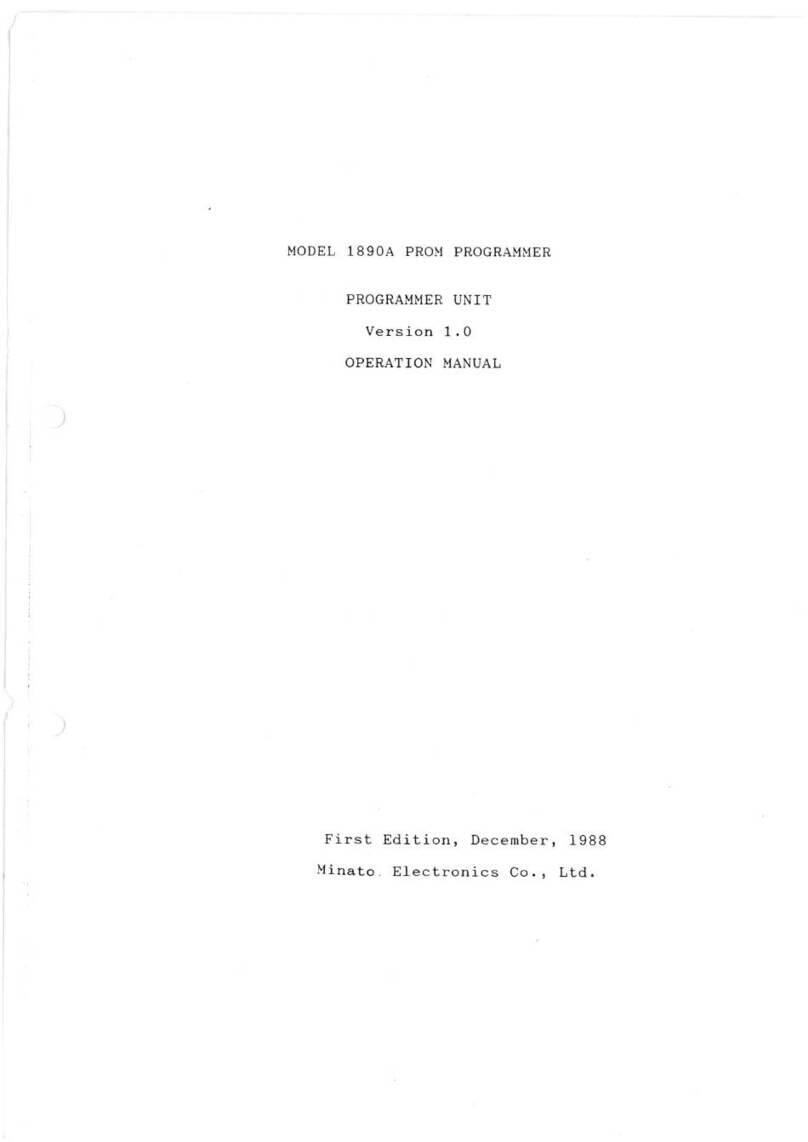
MINATO
MINATO 1890A Operation manual