Stem NC97 User manual

Functioning
The NC97 Module can control the state of two contacts (safety Reed sensors,
emergency stop button, mechanical safety switches, interlocks for mobile guards): the
output is activated by pressing and releasing the START button only if the contacts of
two sensors are closed. The opening of even only one input contact, leads to a safety
situation, by putting the safety outputs in open state and by preventing the closing
even after the re-closing of the contact and the pressure of the START button.
If the NC97 is used to control emergency stop button, after the intervention of the
device, the reset of the command shall not restart the machinery but only permit
restarting (EN 60204-1, §9.2.3.4.2, EN ISO 13850, §4.1.4).
If the NC97 is used to control interlocks for mobile guards, the reclosing or resetting
of an interlock safeguard shall not initiate hazardous machine operation
(EN 60204-1, §9.3.1).
Shorting terminals Y1-Y2-X1, the restart of the device is automatic (in this case A2
has not to be connected to start circuit); the behavior of the machinery to the restart
of the device - or the not automatic restart of the dangerous elements of the
machinery - depends on the realization of the command circuit of the machinery
according to the risk evaluation effected by the user.
If the emergency stop command has only one N.C. contact, it must be connected
between the positive supply contact (L+) and the A1 contact; if no safety sensors are
connected to the unit, S11-S12 and S21-S22 have to be bridged .
Safety category 4 is granted only if (see connection diagram):
- to interrupt the load are used two relays, each connected to an input of
the safety unit;
- the NC auxiliary contacts of the relays controlled by the control unit (Ka, Kb)
are inserted in the feedback loop.
The safety is ensured by using guided contacts, by the redundance and by the
interconnection schematic of the contacts.
The responsibility to choose the adequate components for safety applications, for
example guided contacts safety relays, falls to the user.
Safety Precautions
Safety switches fullfills a personal protection function; they must not be bypassed
(bridging the contacts), moved, removed or otherwise made ineffective. Incorrect
installation or manipulation can lead to severe injuries to personnel. The
manufacturer or the technician that intall the machinery is responsible for correct
and safe overall function.
Auxiliary output 41/42/54 gives informations about the state of the device; it must
not be used as a safety output.
The NC97 is not proper for the operation in presence of ionizing and not ionizing
radiations (rays X, microwaves, laser, ultraviolet rays)
(EN 60204-1, §4.4.7).
!
Description
The NC97 safety relay is created for use in safety circuit intended by
EN 60204-1, EN ISO 13849-1, EN ISO 13850, EN ISO 14119:2013.
This module is based upon the use of guided-contact safety relays.
!
Electrical Connection
Electrical connection must be performed by authorized personnel only following the
indications of EN ISO 13849-1 and EN ISO 13849-2.
All the electrical inputs must either be isolated from the mains supply by a separate
coils safety transformer in accordance with EN IEC 61558-2-6 with limited output
voltage in the event of a defect or by another equivalent movable mechanism.
The supply have to be connected in a permanently way and using a cable with a
maximum lenght of 10 m; the sonsors have to be connected to the unit using cables
with a maximunum lenght of 30 m.
The outputs of the relays have a maximum current of 3 A; the supply connected to
the outputs must be protected from overcurrents by devices adequate to the loads
that have to be protected.
All the output contacts must have an adequate protective circuit for capacitive and
inductive loads.
All the inductive and capacitive loads connected to the power supply must be
connected to appropriate interference suppressors.
Assembly
Installation must be performed by authorized personnel only.
The NC97 control unit must be assembled in a suitable operating area (switch
cabinet, protective housing, at least IP 54) and installed by clipping it to a standard
35 mm top-hat rail.
Setup
If the control unit does not appear to function when operating voltage is applied
(green "Power" LED does not light up), it must be returned unopened to the
manufacturer.
Check whether the safety outputs are being switched (see LED display) by activating
the two inputs and START.
Service and Inspection
The correct functioning of the NC97 safety unit must be controlled by the operator
and/or by the control circuit of the machine in which it is used periodically (at the
beginning of every shift), by checking:
-correct switching function of each sensor by checking:
a) that the opening of the single sensor / safety guard will cause the opening of
the safety outputs (13-14 / 23-24)
b) that the closure of the same sensor / safety guard will cause the closing of
the safety outputs (13-14 / 23-24) as a result of a startup command
- secure mounting of components
- correct connection fixing.
The monitoring function of the unit is done at every switching cycle.
If with all safety guards closed and following the eventual start command, the
safety device does not activate its safety outputs, do not turn off and turn on the
device, then proceed to the checking of the possible safety guard open and
perform the above tests in point a ) and b)
In the event of damage or wear and tear, the damaged system component must
be replaced.
Liability coverage is void under the following circumstances:
- if instructions are not followed
- non-compliance with safety regulations
- installation and electrical connection not performed by authorized personnel
- non-implementation of functional checks
- tampering with the product
Operating instructions for safety control unit mod. NC97 - Original instructions -
Subject to technical modifications without notice, no liability will be assumed for any detail. © STEM S.r.l. 1SMA NC97 0000 rev.10_02/22 pag.1
Connection diagram
Main inputs
S22
Supply
24 V
ac/dc
S21
N
Feedback
control loop * 3
M
M
Ka
Kb
L2L1 L3
L
Signal
output
K2K1K2K1
14
13 23S12S11 X1 24 Safety
outputs
K3
5442
+-
~~
A1 41Y2Y1A2
Start
S12S11 X1
-
~
Y2Y1A2
- Automatic start- Manual start
*If it is not necessary to control the NC auxiliary contacts of the relays via a
feedback loop, short-circuit terminals S12 and X1.
Feedback
control loop *
1) Machinery safety applications:
2) Interlocks for mobile guards with NO + NC contacts
(EN ISO 14119;
cat.4 EN ISO 13849-1;
EN 60204-1, §9.3)
3) Emergency stop button (S1) with NO+NO contacts
in accordance with EN ISO13850
(stop category 0, EN ISO 13850;
EN 60204-1, §9.2.3.4;
cat 4 EN ISO 13849-1)
-
+
S22S11S12 S21
S21
S22
S12
S11
+
-
-
S22S11S12 S21
+
more than one sensor (up to 30)
(cat.3 EN ISO 13849-1)
S22S11S12 S21
-
+
one sensor (S1)
with NO+NO contacts
(cat.4 EN ISO 13849-1)
4) Emergency stop button (S1) with 1 N.C. contact in accordance with EN
ISO13850 (stop category 0, EN ISO 13850;
EN 60204-1, §9.2.3.4; cat 4 EN ISO 13849-1 if one or
no* sensor is connected to the unit; cat 3 EN ISO 13849-1 if more
than one sensor are connected to the unit)
S1
Power supply
24 V ac/dc
A1 A2
L1 +
L2 -
Inputs
*Short the inputs
if they are not used
for a 2NO contacts sensor.
S22S11S12 S21
Sensor 1
Sensor 2
Sensor 3
Sensor n
S2 S1
S1
S1

Subject to technical modifications without notice, no liability will be assumed for any detail. © STEM S.r.l. 1SMA NC97 0000 rev.10_02/22 pag.2
Operating instructions for safety control unit mod. NC97 -Original instructions -
PWR
LED
Outputs 13-14 e 23-24 : OPEN
Power supply
Function
CH2
CH1
State
on
off
off
Green
Color
Green
Green
Output 41-42 : OPEN
CH2
CH1
Green
Green
on
on
Technical data
Pressure: 86 ... 106
Relative humidity: 5% ... 95%
Temperature: -25 ... +70
Pressure: 86 ... 106
Relative humidity: 4% ... 100%
max: 0,5A @ 24 Vdc
IP20
750 mA PTC
EMC compliance
Approvals
Auxiliary output parameters
Weight
External fuse at the output
Safety output switching power
Minimum switching current @ 10 V
Safety Outputs switching voltage
Vibration resistance
Usage category / Electrical Life
(SAFETY outputs)
Safety outputs terminals
Parameter
Dimensions
Housing material
Mechanical life 7
10 cycles
4 A gG (according to IEC EN 60269-1)
10
13 -14, 23 - 24
24 -15% / +10% (AC 50 ÷ 60 Hz)
@24Vdc: 25 min, 70 max; @24Vac: 110 min, 220 max
2
Temperature: -5 ... +55
114,5 x 99 x 22,5
Value
160
PA
VA
VAC
mA
V ac/dc
kPa
°C
mA
kPa
g
mm
°C
Unit
41 - 42 NO; 41 - 54 NCAuxiliary output terminals
Switching current AC-1 / Electrical life
Stop category (EN ISO 13850)
240 (max)
720 (max)
3 A (safety outputs) / >10 cycles
5
In accordance with
0
35 mm DIN standard rail
Screw terminals
Housing conditions
Operating conditions
Connection type
Supply voltage
Pollution degree
Degree of protection (IEC 60529)
Current consuption
Assembly
Internal fuse on the supply
AC-15: 1,4 A / 240 V (inductive load, cosΦ=0,3) / 10 c.
DC-13: 1A / 24 V / 10 cycles
5
5
LED Table
Frontal
view
Dimensions
CH2
CH1
Power
S1
S2
13-14 / 23-24
Timing diagram for manual start
Max input sensor resistance 200 ohm
t1 t1
Cat. 4(1 safety sensor)
Safety category (EN ISO 13849-1)
MTTFd
TM20 (for MTTFd = 100 years)
years
nop (number of operations / year)
30 100
N. op. /
year
65000 19200
years
PFHd
30
65000
56
31500
100
19200
e e d d e
Cat. 3 (more than 1 sensor)
Output 41-54 : CLOSED
Outputs 13-14 e 23-24: CLOSED
Output 41-42 : CLOSED
Output 41-54 : OPEN
t1
S1
S2
13-14 / 23-24
Timing diagram for automatic start
(Y1- Y2 - X1 bridged)
start
S21S12 S 11S 22
54 142442
41 13
Y2
X1 23
A1 A2 Y1
9,54 x 10
30
Output response time - automatic start (t2) ms
150
Output response time - manaul start (t1) ms
t3 t3 t3
t2 t3 t2t2 t3 t3
20
OFF state response time (t3) ms
-8 2,47 x 10
-8 2,65 x 10
-7 1,03 x 10
-7 4,29 x 10
-8
PL (EN ISO 13849-1)
Power Source (input)
Input Terminals Voltage Max. Current
A1-A2 24Vac/dc 220mA / 70mA
Auxiliary Outputs (SAFETY)
Output Terminals Contacts Type General Use
Or Resistive
13-14
23-24 NO 3A/240Vac Res
Pilot Duty
1.4A/240Vac 1A/24Vdc
Installation Notes
UL CERTIFICATION REQUIREMENTS
Environmental Ratings
Max. Surrounding Air Temperature: 55°C
Pollution Degree: 2
Environmental designation
Open type equipment
Use with min. 60°C copper (CU) conductor only
Terminal tightening torque: 5-7 LbIn
(0,56-0,79 Nm)
Signaling Outputs (SIGNAL)
Output Terminals Contacts Type Nom. Ratings
41-54 NC 0.5A/24Vdc
41-42 NO
TÜV IT 0948 16 MAC 0077 B
EN 60068-2-6, EN 60947-5-3
EN 61000-6-2, EN 61000-6-3,
IEC 61326-3-1, EN 60947-5-3
EN 60204-1, IEC 60664-1,
EN ISO 13849-1, EN ISO 13849-2,
EN ISO 14119, EN ISO 13850
STEM S.r.l. via della Meccanica, 2 I-27010 Cura Carpignano Pavia Italia Tel. +39 0382 583011 Fax +39 0382 583058 www.stemsrl.it stem@stemsrl.it
4
Rated impulse withstand voltage (Uimp) kV
250
Rated insulation voltage (Ui) V
III
Overvoltage category

STEM S.r.l. via della Meccanica, 2 I-27010 Cura Carpignano Pavia Italia Tel. +39 0382 583011 Fax +39 0382 583058 www.stemsrl.it stem@stemsrl.it
NC97 connection diagram for Hall safety sensors
PINK S12
S22
S21
BLACK
WHITE
BROWN
GREY
S1 S11
1
2
n
sensori connessi
in serie sullo
stesso canale
(nmax = 10)
S12
S22
S21
WHITE
BLUE
S11
PINK
WHITE
BROWN
BLUE
S1
BROWN
PINK S2
BLUE
GREY
Operating instructions for safety control unit mod. NC97 -Original instructions -
BLACK GREY BLACK
S12
S22
S21
WHITE
BLUE
S11
WHITE
BROWN
BLUE
BROWN
PINK
BLACK
GREY
BLACK
WHITE
BROWN
BLUE
S1
BLACK
PINK
WHITE
BROWN
BLUE
S1
GREY
BLACK
PINK
PINK
GREY GREY
Sn-1 Sn
¹ Activation, deactivation and reset distances are influenced by
ferromagnetic materials. All the data applies to the frontal
direction of approach and a center offset of 0,0 mm.
All the distances have a tolerance of ±1 mm.
² Data also for coded magnets
³ Current consuption of each sensor connecte to the safety unit.
The current consuption of the unit depends on number of connected sensors.
(Imax tot= Imax NC97 + n xImax sensor; nmax = 10).
Connection options
N. of sensors
M140 H1N51H G3 > 20< 13 > 18
M120 H1N52H G3 > 15< 6 > 12
M110N25H G3 > 13< 5 > 11
M25
M113
N30H G3
M30
>13< 5 > 10
Housing Material ²
Parameter
Technical data (*also for activation magnets)
Storage conditions ²
Operating conditions ²
Degree of protection (IEC 60529) ²
Supply voltage (Vs)
Internal fuse
Current consuption ³
Output switching voltage
Max output current
Approval
In accordance with ²
EMC compliance
Vibration and shock resistance ²
Classification (EN ISO 14119)
Not present; the protection against possible over-currents
has to be guarenteed by the power supplier of
the sensors (ex. safety control unit)
Relative humidity: 5% ÷ 95%
Pressure: 86 ÷ 106
35 max
20 ÷ 35 (=power supply voltage)
20 ÷ 35
TYPE 4
IP67
15
glass-fiber reinforced PPS
Temperature: -20 ÷ +80
Relative humidity: 4% ÷ 100%
Pressure: 86 ÷ 106
Temperature: -25 ÷ +70
Value
kPa
Vdc
mA
V dc
mA
Unit
kPa
°C
°C
Connections cable with terminals
Activation
Magnet
Sensor
Shape
Reset
Distance
[mm] ¹
Activation
Distance
Son [mm] ¹
Deactivation
Distance
Soff [mm] ¹
Subject to technical modifications without notice, no liability will be assumed for any detail. © STEM S.r.l. 1SMA NC97 0000 rev.10_02/22 pag.3
B10d (EN ISO 13849-1) 20x10
6cicli
TÜV IT 0948 16 MAC 0077 B
EN 61000-6-2, EN 61000-6-3,
IEC 61326-3-1, EN 60947-5-3
EN 60204-1, EN ISO 13849-1,
EN ISO 14119 (Type 4)
EN 60068-2-6, EN 60947-5-3
Other Stem Control Unit manuals
Popular Control Unit manuals by other brands
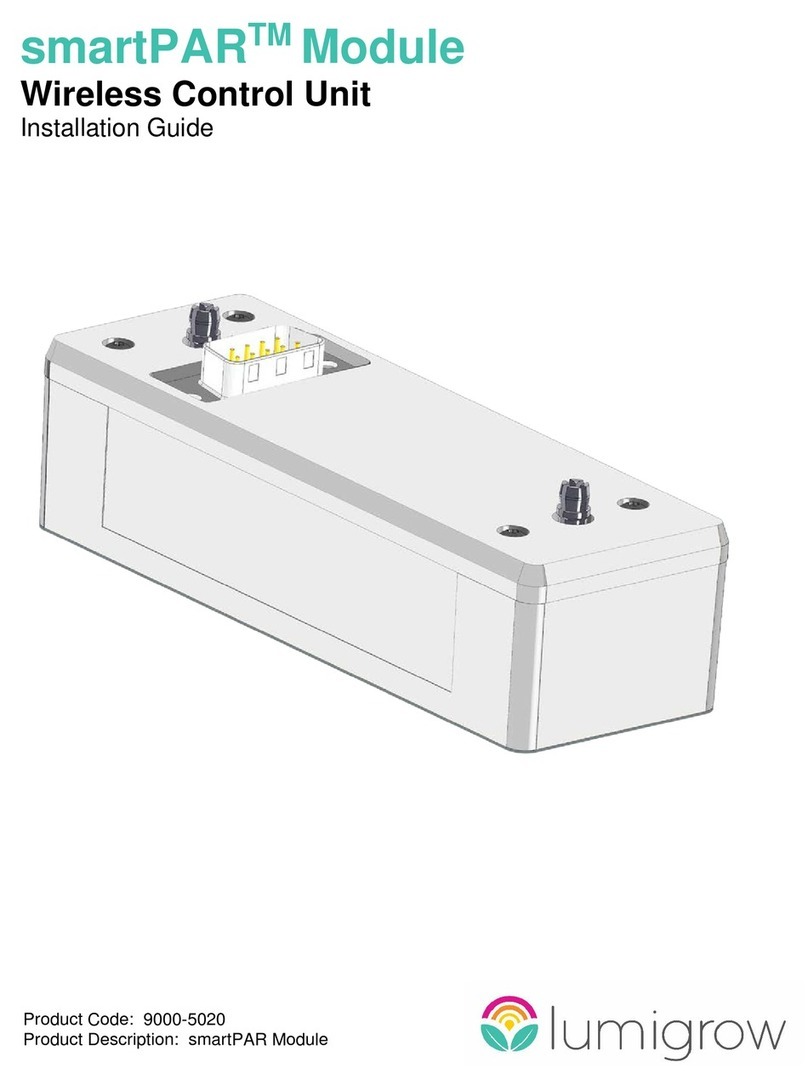
LumiGrow
LumiGrow smartPAR installation guide
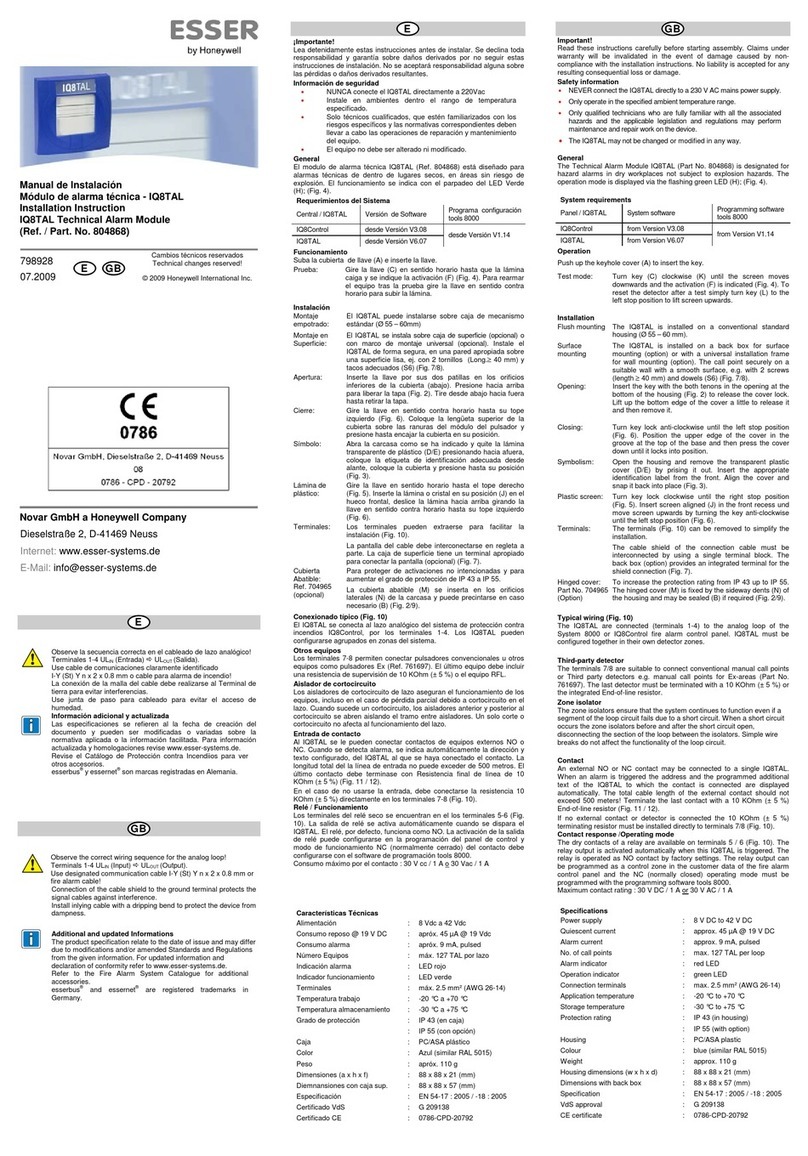
Honeywell
Honeywell Esser IQ8TAL Installation instruction
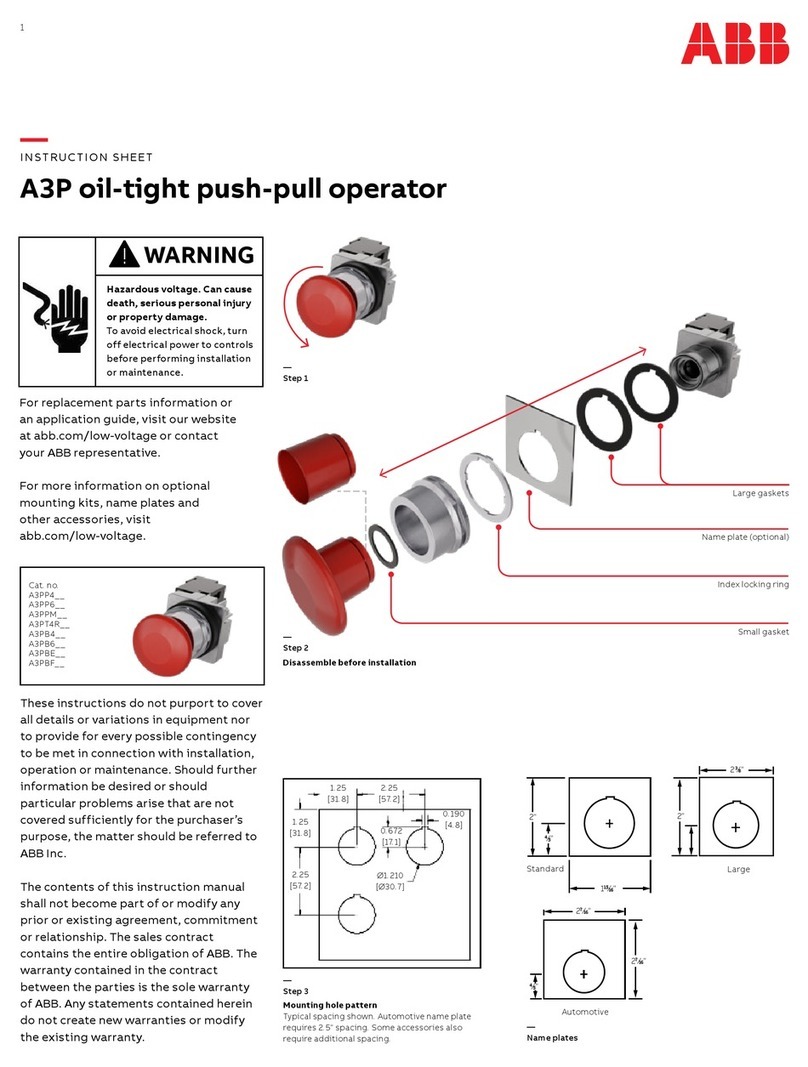
ABB
ABB A3 Series instruction sheet

Mitsubishi Electric
Mitsubishi Electric NZ2GF2B-60TCTT4 user manual
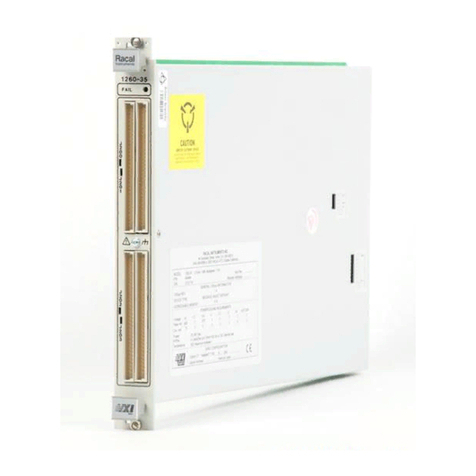
Racal Instruments
Racal Instruments 1260 user manual
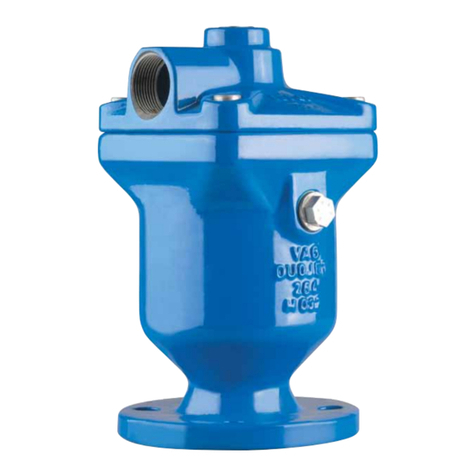
Vag
Vag DUOJET Series Operation and maintenance instructions