Syntec LA596-4H User manual

LA596-4H Product Manual
匯出日期:2024-02-01
修改日期:2023-12-25

联达产品/LEANTEC Products
–
LA596-4H Product Manual
–2
About this user manual

联达产品/LEANTEC Products
–
LA596-4H Product Manual
–3
•
•
•
•
•
Thank you for buying our robot products.
The manual records the precautions for correct installation and use of the solution.
Please read the manual and other related manuals carefully before install and use the
solution.
Please keep properly after reading the manual for future accessible anytime.
Unauthorized copy or reproduction of partial or full contents of this manual is prohibited.
The contents of this manual are subject to change at any time without prior notice.
Please correct us if you found any wrong contents or anything which is needed for
improvement.
Except as expressly stated in this manual, any contents in this manual shall not be construed
as any warranty or guarantee by the Company for personal loss, damage to property, or
specific applicability, etc.
The Company shall not be liable for accidental or consequential injury arising out of the use of
this manual and the products described therein.
Manual content
This manual contains the following instructions:
Installation of robots
The use of robots
Maintenance of robots
Reading object
This manual is oriented toward:
Installers
Technician
Warranty
The robot and its optional components are delivered after go through the company's strict
quality control, testing and inspection, and the performance is confirmed to meet the
company's standards.
Within the warranty period of the delivered products, the company will provide free repairs
for malfunctions that occurred during normal use. (For warranty period, please consult your
regional salesperson.)
However, the customer will be charged for repairs (even within the warranty period) if:
1.Damages or failures caused by improper use and incorrect use without following the
manual.
2.Failures caused by the customer's unauthorized disassembly.
3.Damages caused by improper adjustment or unauthorized repair.
4.Damages caused by natural disasters such as earthquake and flood.

联达产品/LEANTEC Products
–
LA596-4H Product Manual
–4
Warning
1.If the use of robots or related equipment exceeds the conditions of use and product
specifications described in this manual, the warranty will be invalid.
2. The Company shall not be liable for any fault or accident, or even personal injury or death
caused by the use of the products.
3. The Company cannot foresee all possible risks and consequences. Therefore, this manual
cannot warn the user of all possible risks.
Inquiry
For the repair/inspection/adjustment of the robot, please contact our after-sales department.
If no after-sales department is recorded, please contact your local distributor.
To save your time, please prepare the following items before contacting:
- Controller name/serial number
- Robot name/serial number
- Software name/version
- Problems with the system

联达产品/LEANTEC Products
–
LA596-4H Product Manual
Contents–5
•
•
•
•
•
•
•
•
•
•
•
•
•
•
•
•
•
•
•
•
•
•
•
•
•
•
•
•
•
•
•
•
•
•
•
•
•
•
•
•
•
•
•
•
•
•
•
•
•
•
1 Contents
Contents
Safety
About This Chapter
Safety Terms
Safety Signage
Risk Explanation
Safety Features
Emergency Stop
Enable Switch
Workplace Safety Guidelines
Overview
Personal Safety
Operate the Teach Pendant
Recovery From Emergency Stop
Safety Considerations for Manual Mode
Safety Considerations for Automatic Mode
Emergency Handle
Product overview
Overview of Robot System
Load capacity
Function and purpose
Basic principles and main technologies applied
Overview of Robot Structure
Technical parameters
Specification
Robot workspace
Output flange
Load diagram
Electronic Control Box Specification
The installation
Environmental Conditions
On-site installation
Transportation
Installation
Mechanical Interface
Electrical connections
Wiring connection
Grounding Instructions
User Wiring
IO Wiring Definition
Function Test
Check before Power-on
Power-on abnormality check
Check the Mastering position, direction and software limit of each axis of the robot
Test procedure of Automatic Mode
Maintenance
About safety during maintenance
Troubleshooting
Maintenance plan
Check interval

联达产品/LEANTEC Products
–
LA596-4H Product Manual
Contents–6
•
•
•
•
•
•
•
•
•
•
•
•
•
•
•
•
•
•
•
•
•
•
Tightening of hexagon socket screws
The maintenance of synchronous belt
2nd-axis synchronous belt maintenance
3rd-axis synchronous belt maintenance
4th axis synchronous belt maintenance
5/6th axis synchronous belt maintenance
Waterproof Sealant Instructions
Corresponding Model
Model of sealant
Usage and precautions
Zero point
About mechanical home
Zero point calibration
Calibration steps
Appendix
Appendix 1: IP67 Reinforcement Kit Installation
1.1 Corresponding Model
1.2 Part List
1.3 Pneumatic Wiring Schematic
1.4 Installation Procedure
1.5 Mounting
1.6 Maintenance Precautions

联达产品/LEANTEC Products
–
LA596-4H Product Manual
Safety–7
•
•
•
•
•
•
•
•
•
•
2 Safety
2.1 About This Chapter
Explanation
This chapter outlines the safety guidelines that must be adhered to when using the robot.
Before operating the robot, it is crucial to thoroughly read and understand the information
provided in this chapter.
This chapter will introduce the safety principles and procedures to be observed when using
LEANTEC industrial robots.
Personnel Categories
The users can be classified into the following three types:
Operators:
Powering the system on or off
Initiating or stopping programs
Resolving system alarm conditions
Programmers:
In addition to the tasks performed by operators
They can also conduct programming of the robotic arm
Technicians:
In addition to programmer tasks
They can also conduct robot repairs
Both programmers and technicians are required to undergo specialized training provided
by the original equipment manufacturer.
2.2 Safety Terms
2.2.1 Safety Signage
About Safety Signage
When operating the robot according to the instructions in this manual, there may be different
levels of danger. Therefore, near instructions that may cause danger, there will be special
safety signage prompt boxes to emphasize the need for users to be cautious. The content in
the prompt box includes:
An icon representing the safety level and its corresponding name, such as Warning,
Danger, Tip, etc.
A brief description explaining the consequences if the operator does not eliminate the
danger.
Operational instructions on how to eliminate the danger.
Safety Level

联达产品/LEANTEC Products
–
LA596-4H Product Manual
Safety–8
Signa
ge
Name Explanation
Dang
er
Contents marked with this label, if not operated as prescribed, may cause severe or even
lethal injuries to personnel and can also result in significant damage to the robot.
Operations associated with such dangers include coming into contact with high-voltage
components inside the control cabinet, entering its workspace while the robot is in
operation, and so on.
Warni
ng
Warning: The current operation may pose risks to personnel safety, leading to severe or even
fatal injuries.
Electr
ic
Shock
Dang
er
Caution: The current operation may involve the risk of electric shock to personnel, resulting
in severe or even fatal injuries.
Alert Contents marked with this label, if not operated as prescribed, may lead to personal injury
and may also cause damage to the robot itself.
Anti-
Static
(ESD)
Caution: Components involved in the current operation are sensitive to static electricity;
failure to follow proper procedures may result in damage during the process.
Tip Used to convey important information or prerequisites.
2.2.2 Risk Explanation
Description
Signage Name Explanation
Crushing Operators and maintenance personnel
entering the robot's range during debugging,
maintenance, inspection, or tool clamping
may pose a risk of injury.

联达产品/LEANTEC Products
–
LA596-4H Product Manual
Safety–9
Signage Name Explanation
Pinch Maintenance personnel are at risk of pinch
hazards when approaching components with
moving parts during maintenance operations.
Impact Operators and maintenance personnel
entering the robot's range during debugging,
maintenance, inspection, or tool clamping
may be at risk of impact injuries.
Friction Operators and maintenance personnel
entering the robot's range during debugging,
maintenance, inspection, or tool clamping
may be at risk of friction-related injuries.
Parts Ejection Operators and maintenance personnel
entering the robot's range during debugging,
maintenance, inspection, or tool clamping
may face the risk of tools or workpieces flying
out if improperly secured, leading to the
potential for serious injuries.
Fire A fire may occur in the event of a short circuit,
wire or device ignition in the electrical circuit,
posing the risk of serious injuries.
High-Temperature
Surface
Maintenance personnel, when conducting
equipment inspections and maintenance,
may face the risk of burns by coming into
contact with the high-temperature surfaces of
the robot.
Warning
Any robot in motion is a potential lethal mechanical entity!
When in operation, a robot may perform movements that deviate from expectations or even behave
irrationally. Moreover, moving robots carry significant energy, and in the event of a collision, they can
cause severe injuries or damage to personnel and equipment within their working range.

联达产品/LEANTEC Products
–
LA596-4H Product Manual
Safety–10
Eliminating Hazards
Operation Reference Information
1 Before starting the operation of the robot,
ensure that all emergency stop devices have
been correctly configured and installed.
Emergency stop devices include safety doors, safety light
curtain, safety mats, etc.
2 During the robot programming process, it is
essential to ensure that the person entering
the robot's workspace is equipped with the
teach pendant.
To avoid that personnel outside the workspace didn't
aware of those inside, and use the teach pendant to
operate the robot.
3 Before initiating the execution of the robot
program, ensure that there are no personnel
present in the robot's workspace.
Arm Signage Explanation
Signage Name Explanation
Collision
Hazard
Warning
The robotic arm must
maintain a safe distance
during operation to avoid
collisions.
Specification
Label
Label indicating the
specifications and
production date of the
robotic arm.

联达产品/LEANTEC Products
–
LA596-4H Product Manual
Safety–11
•
•
•
•
•
•
Signage Name Explanation
Grounding
Symbol
The robotic arm must be
grounded to prevent the risk
of electric shock.
Electric Shock
Hazard
Warning
Caution: There is a risk of
electric shock with the
robotic arm. Exercise extra
caution.
Caution
Warning
Exercise caution when
operating the arm;
anticipate arm movements
in advance for safety.
2.2.3 Safety Features
Explanation
The Syntec system provides a safety interface to handle safety-related signals and offers
external safety signal interfaces such as safety doors and safety light curtain.
Safety signals include:
Emergency stop signal
Safety door signal
Reset signal
Enable device signal
Mode selection signal
Servo ready signal
2.2.4 Emergency Stop
Definition of Emergency Stop
Emergency Stop is the highest-priority function in the robotic system. Pressing the
Emergency Stop button triggers an immediate stop, halting all robot control functions.
Each joint will rapidly decelerate to zero, and the motor power will be cut off, engaging
the brakes. The control system switches to an emergency stop state, which persists until
manually reset.

联达产品/LEANTEC Products
–
LA596-4H Product Manual
Safety–12
To restore the system to normal operation, a manual reset operation must be
performed. This involves releasing the Emergency Stop button and then manually
pressing the Servo Ready button on the control pendant.
Emergency Stop Button
By default, the robotic system is equipped with two emergency stop buttons, pressing
either of which triggers an emergency stop. One is installed on the control cabinet, and
the other is mounted on the teach pendant.
Tip
Emergency Stop is only intended for an immediate halt of the robot's operation in dangerous situations.
Tip
Emergency Stop should not be used as a regular program stop, as doing so may cause additional and
unnecessary wear on the robot's brake system and transmission, eventually reducing the robot's lifespan.

联达产品/LEANTEC Products
–
LA596-4H Product Manual
Safety–13
Additionally, during the deployment of the robot, your system integrator may install
additional emergency stop buttons. Please contact your system integrator or refer to the
robot workstation documentation for more information.
2.2.5 Enable Switch
It is a special switch with 2 stages, having 3 positions. It is effective only when the enable
switch is pressed and held in the middle position. Releasing or pressing it firmly to the
bottom will deactivate it.
It needs to be pressed together with other buttons to prevent accidental activation.

联达产品/LEANTEC Products
–
LA596-4H Product Manual
Safety–14
No. Name
①Position 1
②Position 2
③Position 3
④Light Press
⑤Heavy Press
⑥Release

联达产品/LEANTEC Products
–
LA596-4H Product Manual
Safety–15
2.3 Workplace Safety Guidelines
2.3.1 Overview
About Robot
Regardless of the speed of motion, industrial robots pose significant potential dangers. A
pause or wait in the program's execution can be followed by a very rapid and hazardous
movement command. Even if you are familiar with the current robot's motion trajectory
and patterns, the robot's movement in automatic mode can still be altered by external
signals without any warning.
Therefore, it is essential to adhere to safety regulations when entering the robot's
workspace.
About the Installation Site for Robots
The location for installing the robot needs to be sufficiently spacious. It is crucial to
ensure that even when all joints of the robot are fully extended, the wrist tool or the tip
of the workpiece will not come into contact with walls, safety fences, or the robot's
control box. Otherwise, there is a risk of collisions with the robot, leading to injuries to
personnel and damage to equipment.
•
•
Tip
The enable switch is mounted on the back of the teach pendant and can only enable jogging or program
execution when pressed to the middle position. Releasing it or pressing it to the bottom to make the operation
ineffective.
To ensure the safe use of the teach pendant, the following requirements must be observed:
The enable switch must be functional under all circumstances.
During programming and debugging, the safety latch switch can be released when robot movement is
not required.
Anyone entering the robot's workspace must carry the teach pendant to prevent inadvertent robot startup
when internal personnel are unaware.
Warning
It is strictly prohibited to use external devices to jam the enable switch, keeping it continuously in the middle
position!

联达产品/LEANTEC Products
–
LA596-4H Product Manual
Safety–16
No. Name
①Over 1000mm
②Robot Motion Range
③Robot Motion Range Including the
Clamping Fixture
④Safety Door
⑤Safety Fence
⑥Robot Control Box
About This Section

联达产品/LEANTEC Products
–
LA596-4H Product Manual
Safety–17
•
•
•
•
•
•
•
•
This section refers to the safety standards GB 11291.1 and GB 11291.2. It will introduce
some basic safety regulations for end-users of robots. However, due to space
constraints, it may not cover every specific scenario.
2.3.2 Personal Safety
Basic Principle
There are a few simple principles that must be followed in order to operate a robot
safely:
All of the operating procedures must beprofessionally evaluated and based on
relevant industrial safety regulations.
Operators who work with robots must wear safety equipment suitable for the
working environment before performing operations, such assafety vests, safety
shoes andsafety helmets.
When personnel encounter danger or other emergency and abnormal
situations due to the robot, please press the emergency stop button
immediately. After eliminating the hazard, perform the reset according to the
instructions in the manual.
Keep an eye out for moving tools, such as drills, saws, etc. installed on the
robot. Make sure the tools stop working before approaching the robot.
Be aware of work piece surface or robot body. The temperature of robot motor
and outer shell may be very high after working for long time.
Pay attention to the robot'sgripperand the objects it is holding. If the gripper is
opened, the workpiece may fall and cause injury to personnel or damage to
equipment. In addition, the grippers used by the robot can be very powerful
and can cause damage if not used properly.
Pay attention to the electrical components inside the robot and control
cabinet. Even if the power has been cut, the energy retained in the device can
be very dangerous.
Climbing on robot arm is prohibited.
Precautions for using hydraulic and pneumatic
•
•
•
•
•
•
•
Warning
Relevant education training and permission is a must for the person installing the robot.
In order to protect personal safety, the installation procedures in this manual and related industrial
safety regulations must be followed.
Control box should be away from high voltage and other component that generate electromagnetic
field, to prevent the electromagnetic interference which may cause deviation or malfunction of the
robot.
The robot may damage or malfunction if non-original manufacture components used.
Be careful of the heat source generated by the controller and servo motor.
Do not excessively bend the power signal cable. Otherwise, it may cause unexpected danger.
The teach pendant removed from the control cabinet should be properly stored in a safe place away
from the robot workstation or control cabinet. The operator should not be misled to think that the teach
pendant is still connected to the control cabinet and try to use the unconnected teach pendant to stop
the robot when facing dangerous situation.

联达产品/LEANTEC Products
–
LA596-4H Product Manual
Safety–18
•
•
•
•
•
•
•
•
•
•
2.3.3 Operate the Teach Pendant
Explanation
The teachpendantequipped with Syntec system is manufactured with advanced
electronic components. In order to avoid failure or damage during use, please follow the
following requirements.
Handheld teach pendants are developed, manufactured and tested in accordance with
relevant industry standards and are intended for use only as described in this manual. If
you follow the requirements in this manual, the teach pendant controller will not cause
personal injury or damage in normal use.
Operation and Cleaning
Handle it lightly to avoid falling, throwing or a strong impact on teachpendant.
Otherwise, it may cause malfunction.
If the teach pendantexperiences a strong shock, verify that the enable switch and
emergency stop button are still in normal working conditions before using again.
When you do not use the teaching device, please store it properly to avoid accidental
dropping.
Avoid tripping over your own cable when using the teach pendant.
Do not operate the touch screen with sharp objects, such as a screwdriver, pen tip, etc.
Otherwise, the touch screen may be damaged. Operate with a finger or a stylus on top
of the pointer.
Clean the touch screen often, dust and small particles of impurities may cause the
touch screento malfunction.
Do not use chemical solvents, detergents or washing surfaces to clean the teach
pendant. Use a softcloth and a small amount of water to scrub.
When not using the USB interface, the protective adhesive cap must be properly
fastened. Otherwise, exposure to dust may cause interface failure.
Pendant Cable
Ensure that the staff does not trip over the teach pendantcable and causes theteach
pendantto fall.
Do not squeeze theteach pendantcable. Otherwise, it may damage the inner core.
•
•
Danger
When using hydraulic and pneumatic in operation, the clamped workpiece may fall due to insufficient
pressure or gravity.
The hydraulic and pneumatic systems need to be equipped with safety valves for emergency use.
Danger
When personnel enter the safety enclosure, they must carry the teach pendant to ensure that the robot is under
their control, and only manual mode should be used to operate the robot.

联达产品/LEANTEC Products
–
LA596-4H Product Manual
Safety–19
• Do not place the teachpendantcable at sharp edges, as this may damage the cable
sheath.
2.3.4 Recovery From Emergency Stop
Explanation
The reset operation must be performed when the system is in an emergency stop state
in order to return to the normal state. The reset process is very simple but very
important to ensure that the robot system is not put into production operation in a
dangerous state.
Emergency Stop Button
All button-type emergency stop devices have a safety lock mechanism that must be
manually released after being pressed to reverse the emergency stop state of the device.
Leantec robot emergency stop buttons are released by rotation, with the direction of
rotation marked on the surface of the button.
Reset the External Stop Device
All external safety devices such as safety gates, safety light grating, etc. have some type
of safety locking mechanism. If your robot workstation uses an external safety device,
consult your system integrator for moredevices reset information.
Recovery from E-Stop
Operation
1 Confirm that the hazardous condition causing the emergency stop has been addressed and that the hazard
source is no longer present.
2 Reset a safety device that causes an emergency stop.
3 Press the "Servo Ready" button on the teach pendant to restore the system from a non-ready state.
2.3.5 Safety Considerations for Manual Mode
About Manual Mode
In manual mode, the movement of the robot is under manual control. The robot can be
jog or run only if the enable switch is in the middle position.
Manual mode is used for robot program writing and debugging and participating in the
commissioning of the workstation.

联达产品/LEANTEC Products
–
LA596-4H Product Manual
Safety–20
Bypass External Safety Signals
In manual mode, signals from external safety devices such as safety doors and safety
light grating will be bypassed. The system will not be in emergency stop state even if the
safety door is opened in manual mode to facilitate commissioning.
2.3.6 Safety Considerations for Automatic Mode
About Automatic Mode
The automatic mode is used to run the robot program during the formal production
process.
The enable switch will be bypassed in automatic mode, so the robot can operate automatically
without personnel involved.
Enable External Safety Signals
External safety signals such as safety door and safety light curtain will be enabled in
automatic mode, and an emergency stop will be triggered when the safety gate is
opened.
Safe Fault Recovery in Processing Production
In most cases, robots are part of a production line. Therefore, when robots malfunction,
it not only affects the robot workstation itself but also may impact other parts of the
production line when issues occur in those areas. Therefore, failures recovery plan
should be designed by personnel who is very familiar with the production line to
improve safety.
For example, on a production line, the robot needs to grab the workpiece from a
conveyor belt. In case of a robot failure, in order to ensure that the production process is
not interrupted, the conveyor belt should be kept in operation while the robot is being
repaired. At this time, the robot maintenance personnel should consider additional
safety measures for working beside the conveyor belt in operation.
Another example, when a welding robot is removed from a production line for routine
maintenance, other robots associated with the same process must also be stopped to
prevent human injury.
2.3.7 Emergency Handle
Handling of Light Fire
In the event of imminent fire danger or fire that has already started but not yet spread,
do not panic, remain calm and extinguish the flames with the fire extinguishing
equipment provided at the scene. Do not use water to extinguish the fire caused by a
short circuit.
Other manuals for LA596-4H
1
Table of contents
Other Syntec Robotics manuals
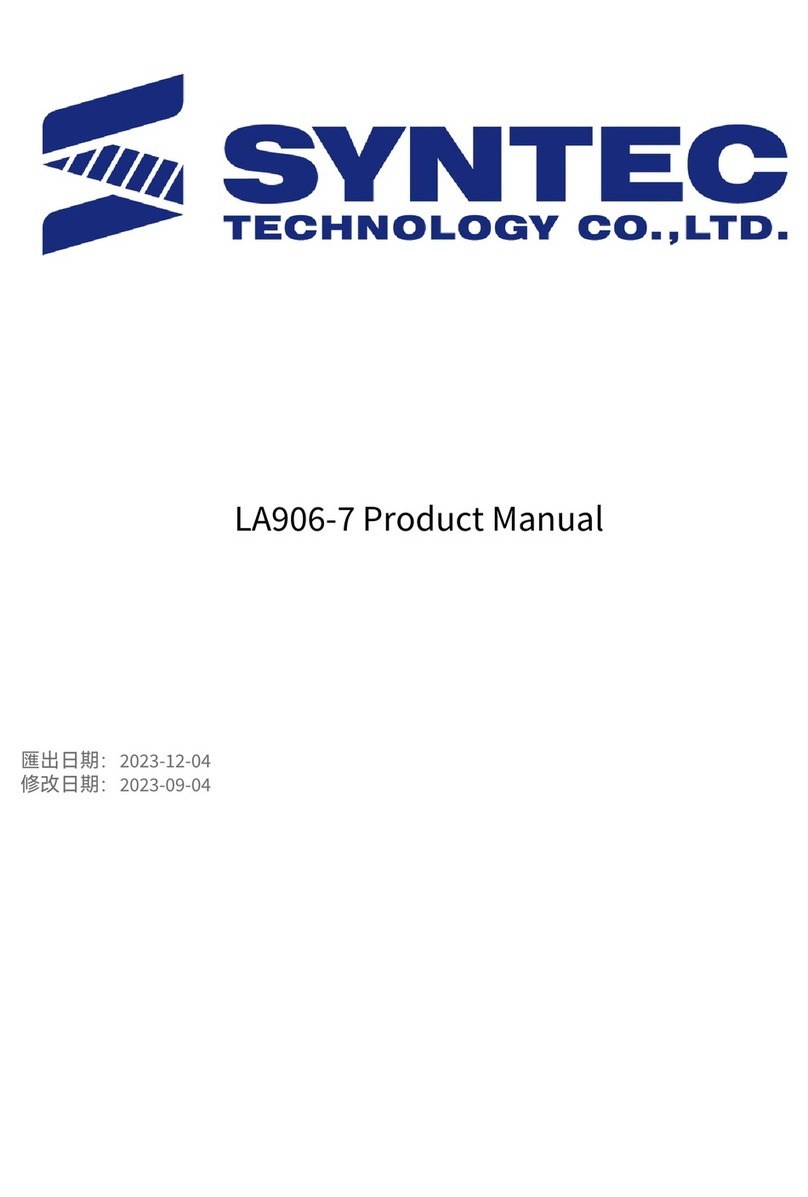
Syntec
Syntec R Series User manual
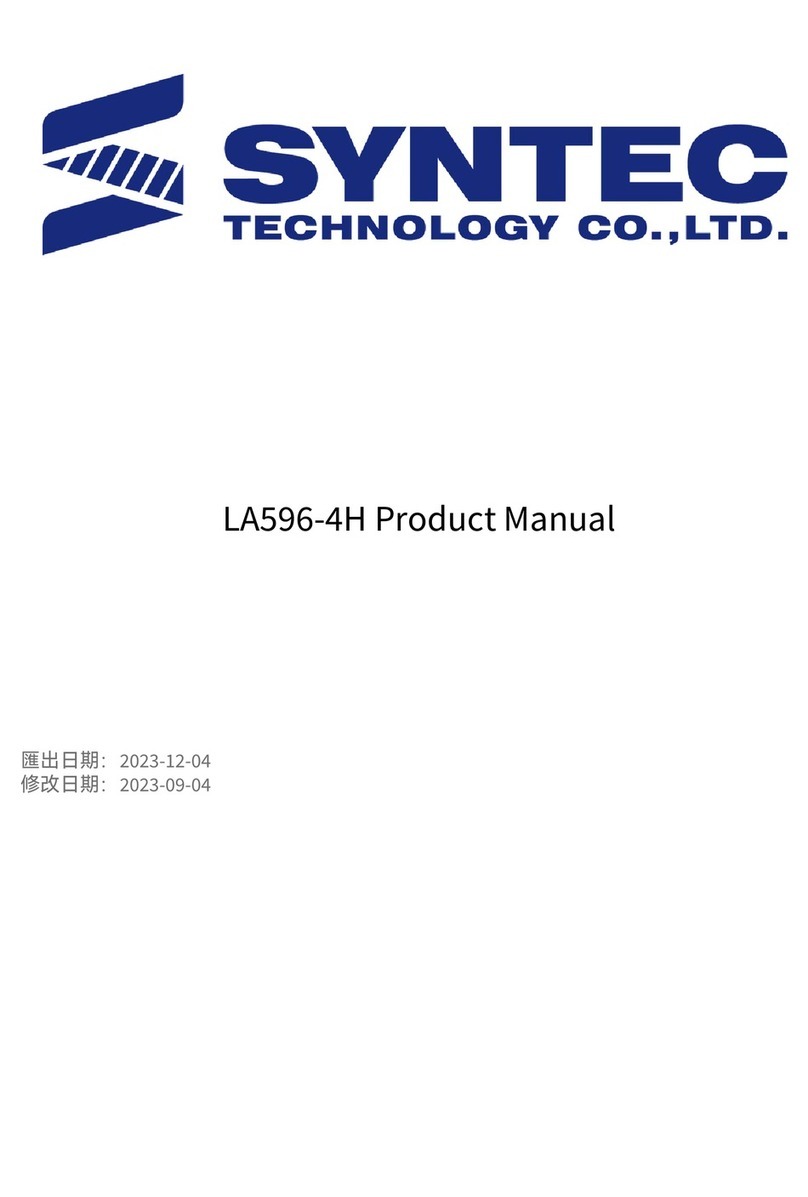
Syntec
Syntec LA596-4H User manual
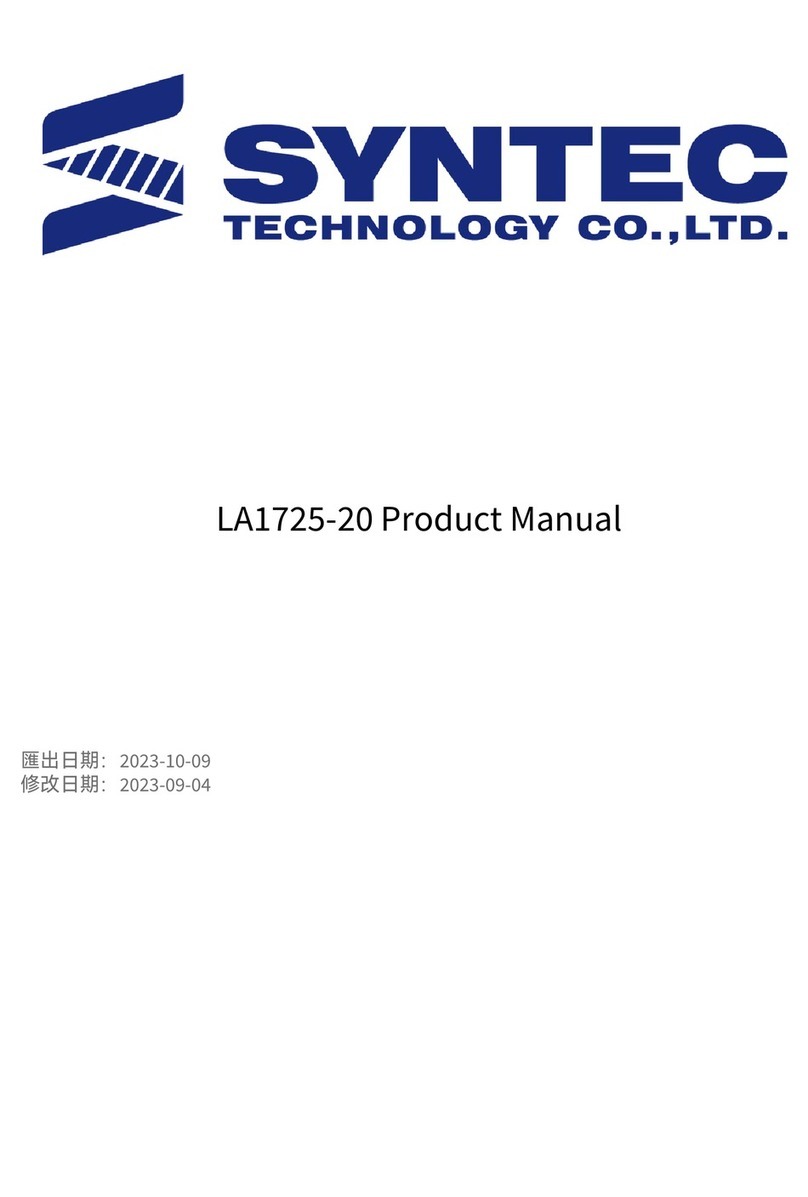
Syntec
Syntec LA1725-20 User manual
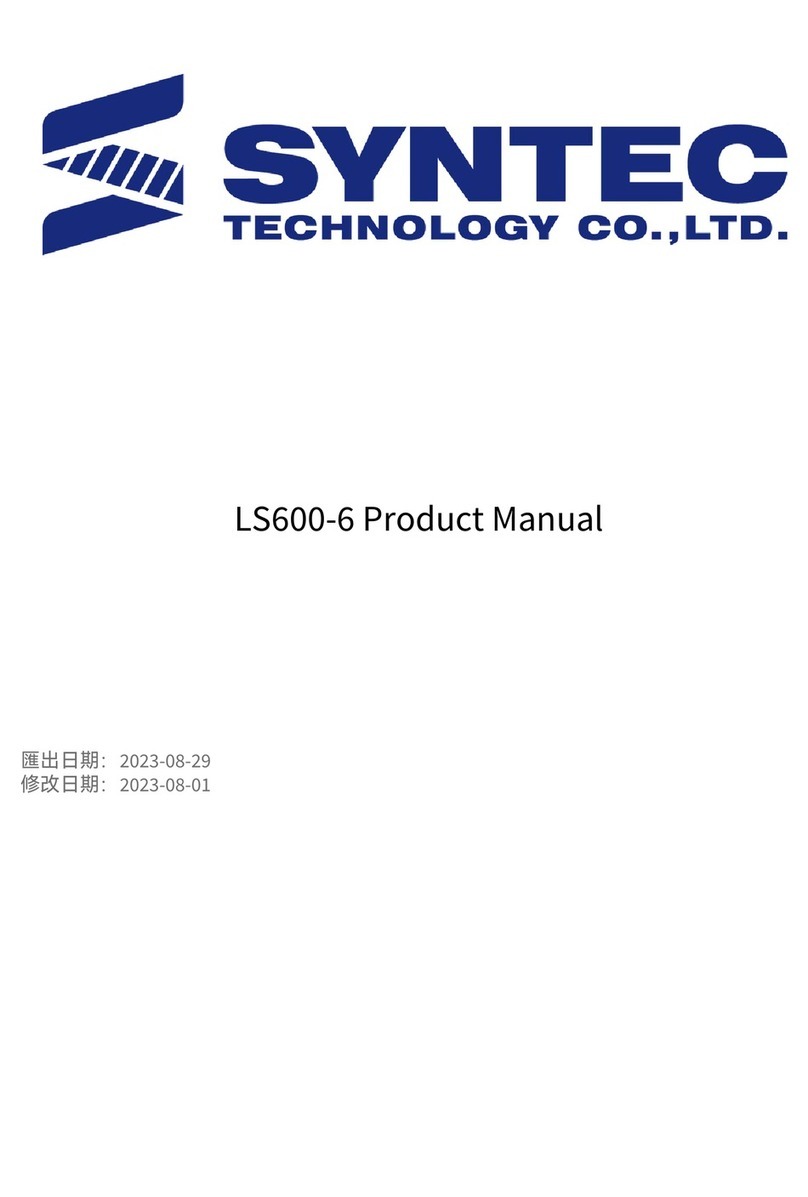
Syntec
Syntec LEANTEC LS600-6 User manual
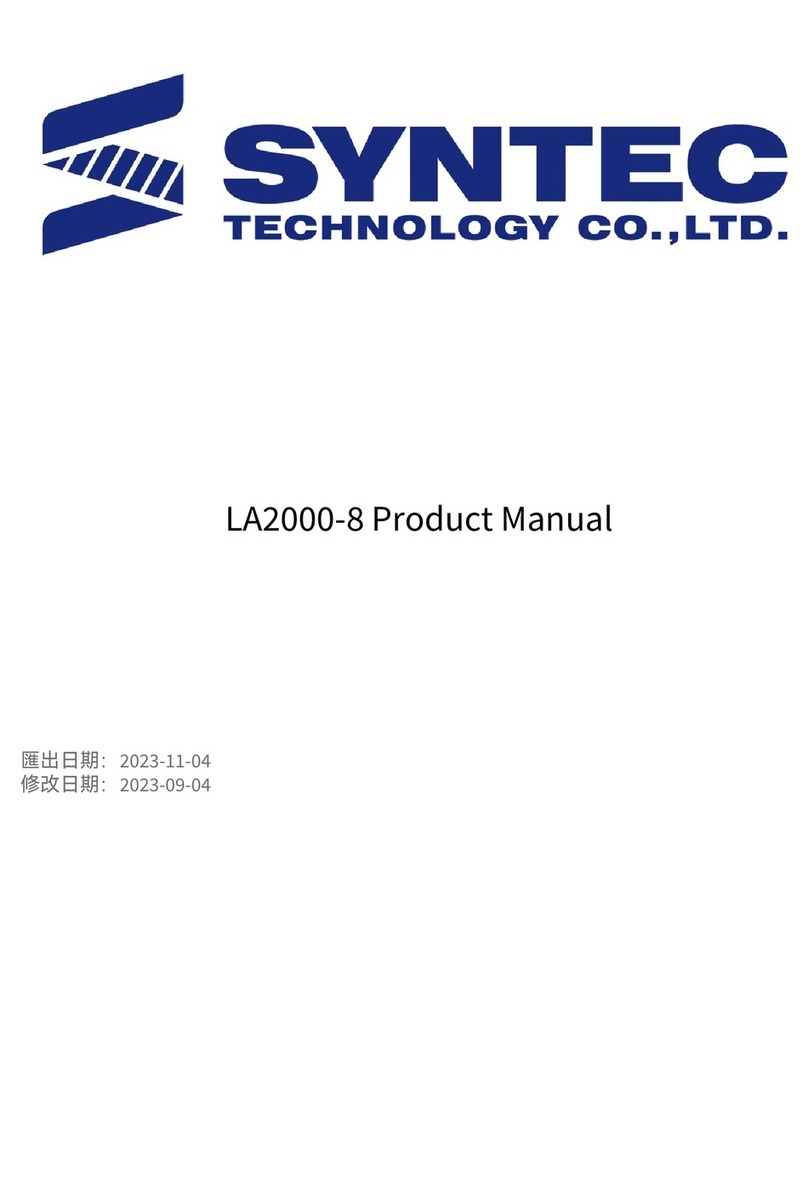
Syntec
Syntec LA2000-8 User manual

Syntec
Syntec LA2100-60 User manual
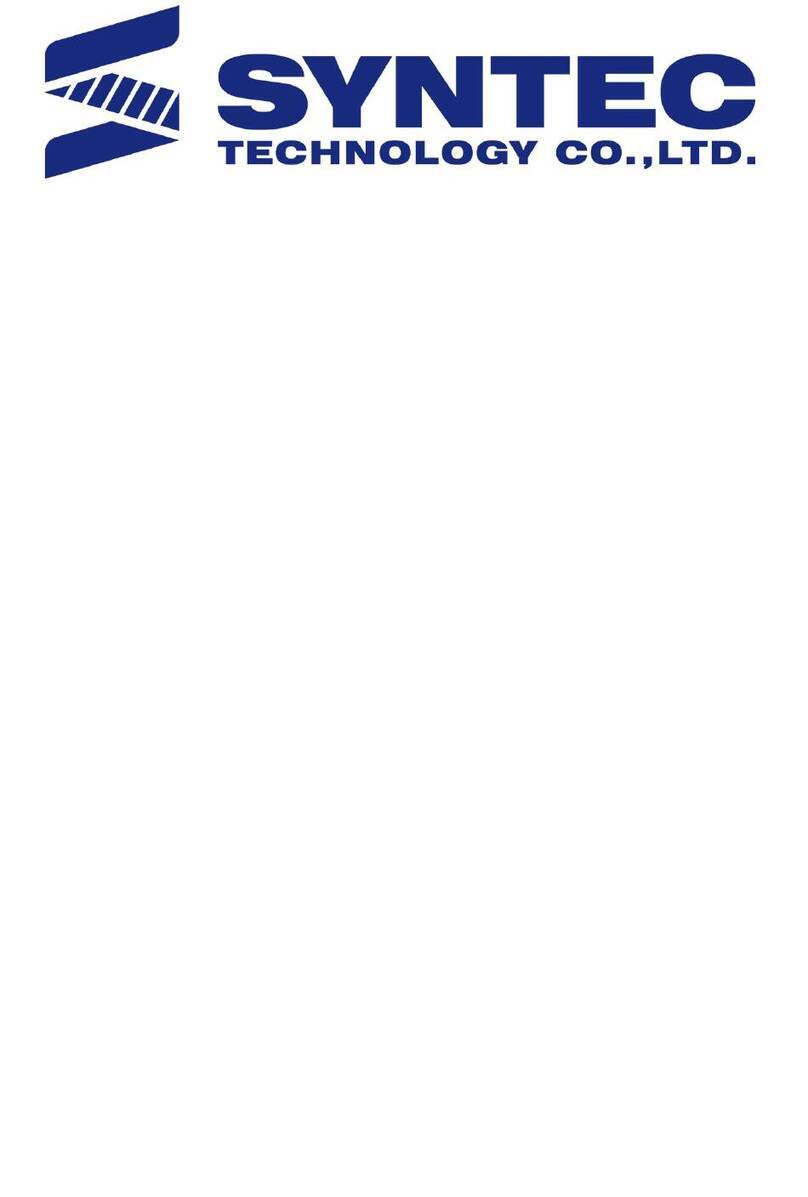
Syntec
Syntec R Series User manual
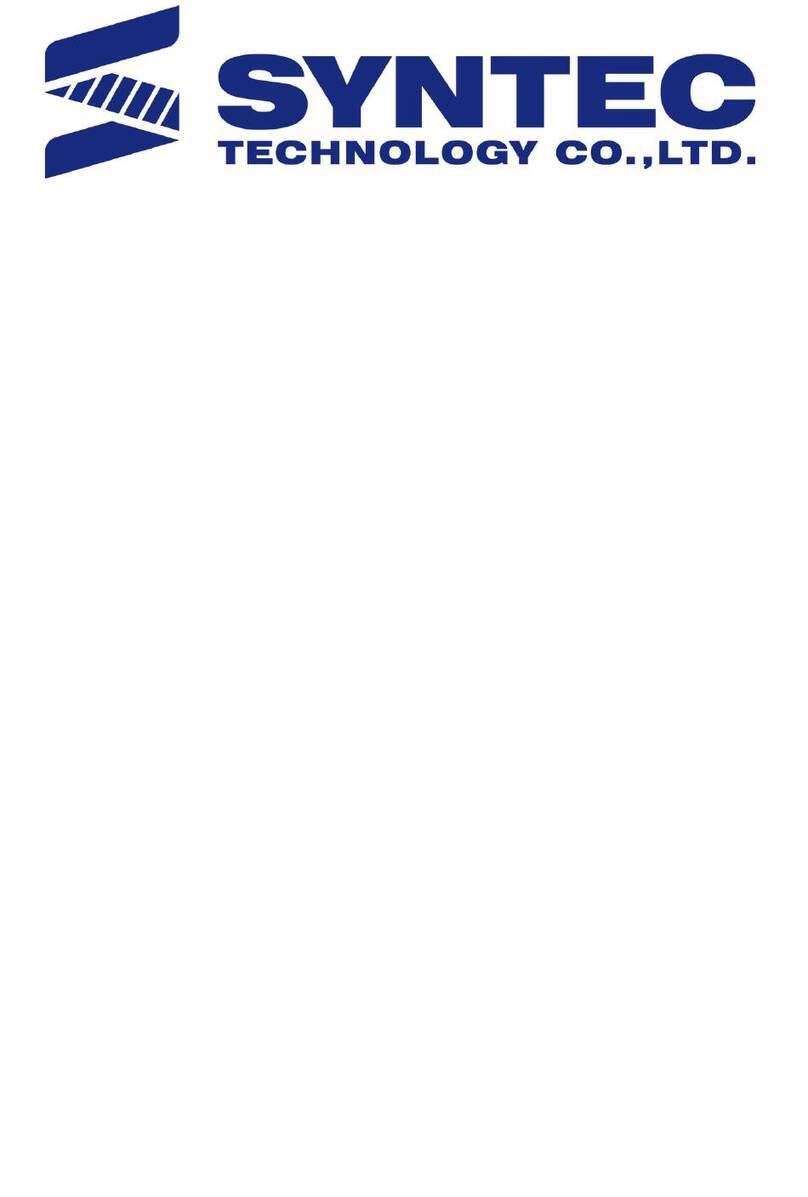
Syntec
Syntec K Series User manual
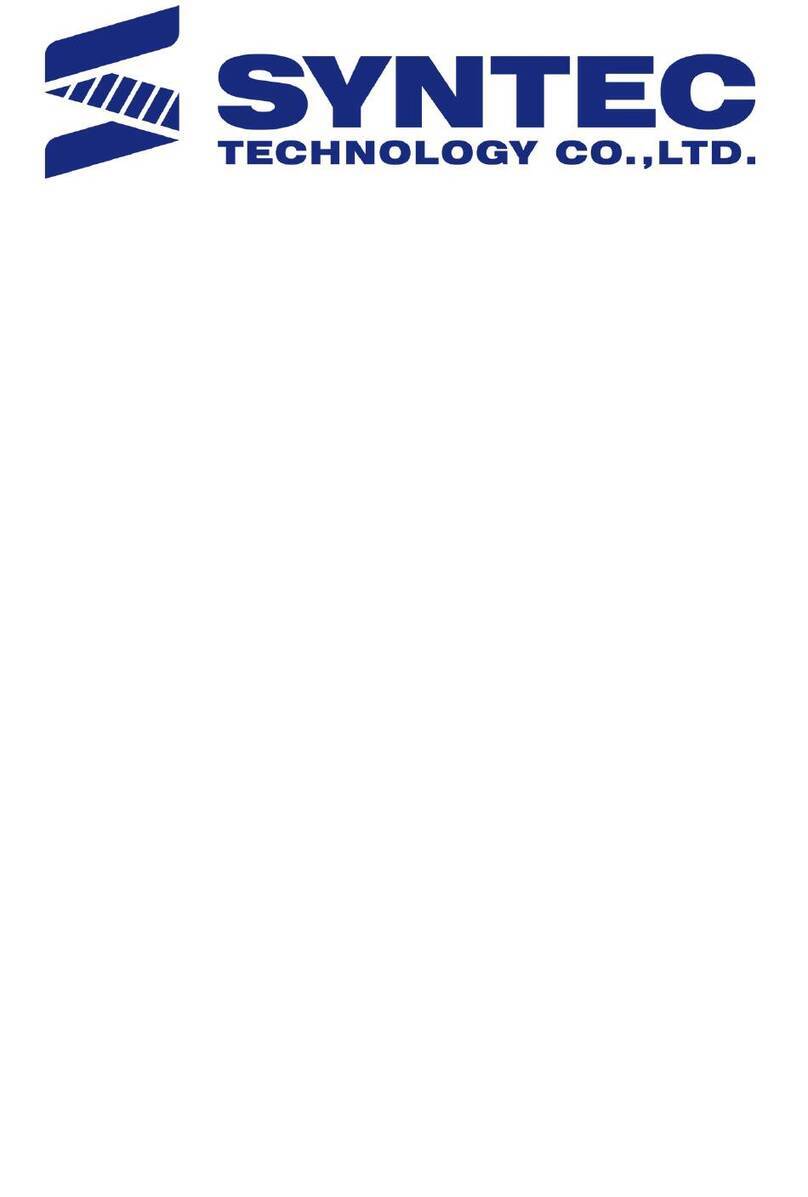
Syntec
Syntec LA1725-20 User manual
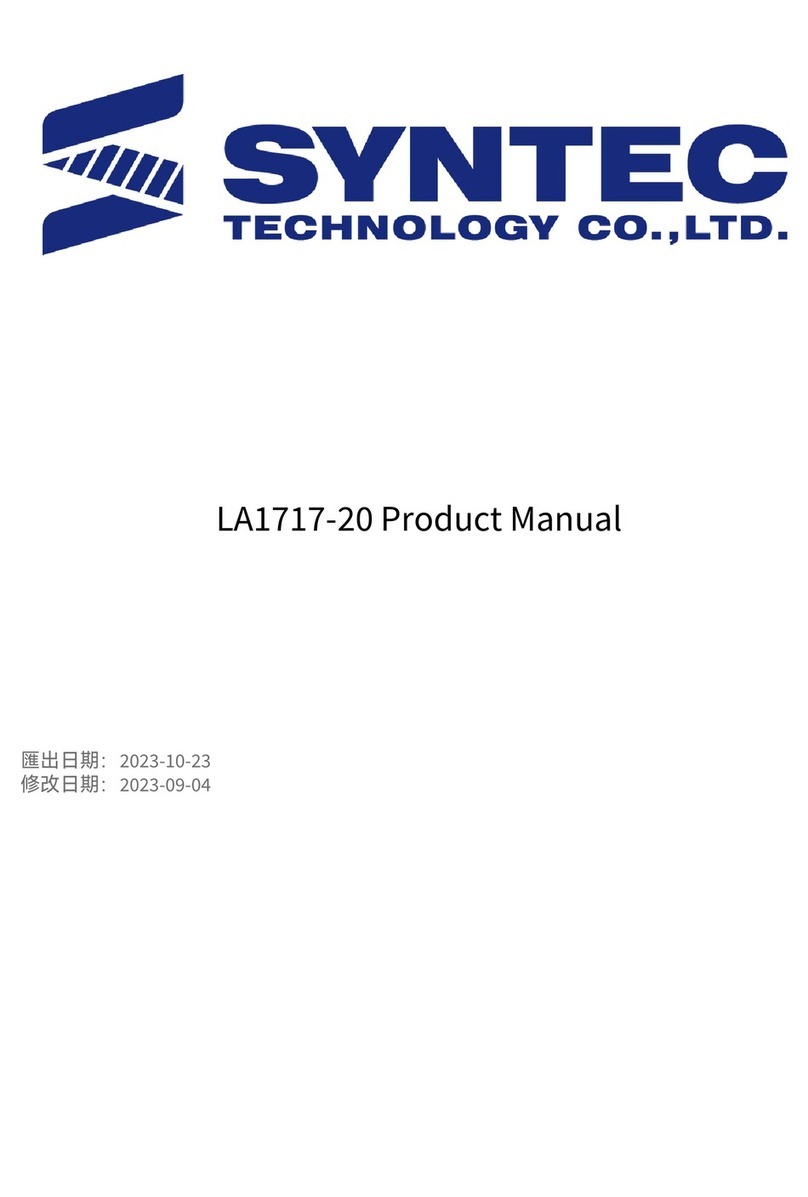
Syntec
Syntec C Series User manual