TASKING iSystem Cypress CYT2B9 Instructions for use

Cypress CYT2B9 Emulation Adapter
Hardware User Manual
V2.6, November 2023
isystem.com/start

General safety instructions
Please read the following safety precautions carefully before putting this device to use to avoid
any personal injuries, damage to the instrument, or to the target system. Use this instrument
only for its intended purpose as specified by this manual to prevent potential hazards.
Use included power cord and power supply
The enclosed power supply has been approved for use by iSYSTEM. Please contact iSYSTEM if
you need to consider an alternative power.
Use grounding wire
Prior to applying power to either the BlueBox or the target, connect the device and the target sys-
tem together with the included grounding wire. This is to avoid potential damage caused by any
voltage difference between the device and the target system.
Use proper overvoltage protection
Ensure proper protection to avoid exposing the BlueBox device or the operator to overvoltage
surges (e.g. caused by thunderstorm, mains power).
Do not operate without cover
Do not operate the device with cover removed.
Avoid circuit and wire exposure
Do not touch exposed components or wires when the device is powered.
Do not operate with suspected damage
If you suspect damage may have occurred, the BlueBox device must be inspected by qualified
service personnel before further operation.
Do not operate the device outside its rated supply voltage or environ-
mental range
Consult with iSYSTEM before using equipment outside of the parameters provided in this
manual.
This symbol is used within the manual to highlight further safety notices.

Contents
Introduction .......................................................................................................................................... 4
Package content ................................................................................................................................ 5
Adaptation packages content .............................................................................................................. 6
Operation ............................................................................................................................................... 8
Adaptation setups ................................................................................................................................... 9
Screws ....................................................................................................................................................................................................................................11
Configuration .......................................................................................................................................... 12
Connectors .............................................................................................................................................. 16
Power supply package ......................................................................................................................... 17
Standalone operation ........................................................................................................................... 18
Mechanical information ............................................................................................................. 19
Accessories ......................................................................................................................................... 21
User Notes .......................................................................................................................................... 22

Introduction
Cypress CYT2B9 Emulation Adapter is based on the 176-pin CYT2B98CA superset device and
provides full trace capabilities for the
·
64-pin
·
80-pin
·
100-pin
·
144-pin
Traveo II CYT2B9 Adaptation, where trace port is not available or lacks the full trace capability.
The Emulation Adapter might differ in some peripherals from the target device; there-
fore, the device datasheet should be checked.
Cypress CYT2B9 Emulation Adapter supports following debug and trace interfaces:
·
JTAG or SWD debug interface;
·
MTB trace to trace Cortex-M0+ program execution; Trace data is stored in 4KB dedicated RAM
memory and read out through JTAG or SWD;
·
ETM/ITM trace to trace Cortex-M4 program execution; Trace data is connected to the external
trace port (CPU port P18_4 – P18_7 or P22_0 – P22_3) which then connects to 20-pin
1.27mm CoreSight Debug Adapter;
·
ETB trace to trace Cortex-M4 program execution; Trace data is stored in 8KB dedicated RAM
memory and read out through JTAG or SWD;
·
Serial wire viewer (SWV) and printf() style debugging through a Single Wire Output (SWO)
“trace” pin on Cortex-M4.
Emulation Adapter can also be used as a standalone device for microcontroller evaluation pur-
poses or for development and test of an embedded application ahead of target board availabil-
ity.
More information about our products on www.isystem.com or via sales@isystem.com.

Package content
Cypress CYT2B9 Emulation Adapter is delivered with all components required for Standalone
operation. Adaptation package for the Target board and the Power adapter must be ordered
separately.
Cypress CYT2B9
Emulation Adapter
Power supply package
Power converter
Power adapter
Ordering code:
IEA-CYT2B9
Ordering code:
IEA-PS
Ordering code:
IT9V-PS
GND Wire
Crystal 16MHz
Ordering code: BB-WIRE

Adaptation packages content
Target Adaptation
Conversion boards connect between the Emulation Adapter and the matching Solder part which
is being soldered on the Target side.
Pin number
Conversion board
Type
Solder part
64
IEA-CYT2B9-ATQ64
Fixed
IA64ATQ-SOLDER
IEA-CYT2B9-ATQ64W
Flex
IA64ATQ-SOLDER
80
IEA-CYT2B9-ATQ80
Fixed
IA80ATQ-SOLDER
IEA-CYT2B9-ATQ80W
Flex
IA80ATQ-SOLDER
100
IEA-CYT2B9-TQ100
Fixed
IA100TQ-SOLDER
144
IEA-CYT2B9-TQ144
Fixed
IA144TQ-SOLDER
Fixed Adaptation
The adaptation is elivered with a slot screw, which can be used to achieve a more solid and
stable fixing of the Conversion board and the Solder part.
Conversion board
Solder part
Flex Adaptation with Wire adapter
This part provides a flexible connection of the Emulation Adapter to the Solder part as an altern-
ative to the fixed connection.
Conversion board
Solder part

Measurement board
The Measurement board connects between the Emulation Adapter and the Conversion board.
Embedded targets often do not have access to all the MCU pins / connected signals to connect
with measurement equipment (oscilloscope, logic analyzer), its use provides easy access to all
MCU pins. It is delivered together with an Layout board (chip signals are clearly marked), which
is placed over the Measurement board.
Measurement board (optional)
Layout board example for the Measurement
board
Ordering code:
IAMCYT2B

Adaptation setups
Fixed Adaptation

Flex Adaptation

Screws
Slot screw
The Slot screw (30mm) is used to fix the Conversion board to the Solder part. The setup be-
comes mechanically more robust.Screw the Conversion board to the Solder part first, before the
Emulation Adapter is attached on top and watch out not to break out the Solder part, e.g., if you
accidentally hit the Emulation Adapter from the side.
Short Hexagon socket screw
Short Hexagon socket screw, which comes with the Solder part, is not applicable with this Emu-
lation Adapter setup.

Configuration
J1: Target reset configuration
Jumper J1 connects the Emulation Adapter reset line and the user target board reset line and is
populated by default. EA also features a Reset push button (SW1).
If having problems establishing the initial debug session with the Emulation Adapter, remove J1
and try again.
J2 and J3: Clock source configuration
Jumpers J2 and J3 select clock source for the emulation device.
Position 1-2 (default position) selects the crystal circuit oscillator on the user target board.Posi-
tion 2-3 selects an external clock source (Q1 socket on the Emulation Adapter).
The Emulation Adapter may not operate when your target board’s crystal circuit is
used as the clock source. Typical design guideline is that the crystal should be as
close as possible to the microcontroller. The crystal on your target board might not os-
cillate in conjunction with the Emulation Adapter when the clock lines (TP21_2,
TP21_3) between the crystal and the emulation device on the Emulation Adapter be-
come too long, thus affecting the impedance of the crystal circuit.
Enclosed in the Emulation Adapter package is a separately packed 16 MHz crystal.
The crystal can be used as a 16MHz external clock (XOSC) source to the emulation
device. If a different clock frequency is required, insert appropriate crystal into the Q1
socket and replace C24 (default 10pF populated) and C25 (default 10pF populated)
accordingly. Crystal socket Q1 is per default not populated (NP).
Crystal socket Q1below:

J4 - J13: Trace port configuration
Soldered jumpers are by default placed to connect ARM
CoreSight 20 connector trace signals to port P18 (J9 – J13). If
P18 on user target board is used for any other purpose than
trace, Emulation Adapter allows changing the trace source to
port P22 (J4 – J8) with relocation of the jumpers.
Soldered jumpers J4-J13 on EA on the image below:
Default position on P18
Optional position on P22

winIDEA configuration
By default, P18 port pins (P18_3 – P18_7) or P22 port pins (P22_0 – P22_4) are set as GPIO
pins. To configure these pins as trace pins in winIDEA, open Hardware menu / CPU Options /
Analyzer tab and add a script CYT2Bx_TraceInit.cpp in the SoC Initialization section. Via the
Parameters options and depending on the user target board configuration allocate:
·
TRACE CLOCK Port to PORT 18 (or PORT 22),
·
TRACE DATAn PORT to PORT 18 (or PORT 22).
More information in winIDEA Help.

P2: Power supply configuration
Emulation Adapter Power supply is configured via the unshrouded 26-pin 2.54 mm header
(P2).
Signal direction
Signal
Pin
Pin
Signal
Signal direction
Target board
VDDA
1
2
CVDDA
Emulation device
Target board
VREFH
3
4
CVREFH
Emulation device
Not Connected
NC
5
6
NC
Not Connected
Target board
VDDIO_1
7
8
CVDDIO_1
Emulation device
Target board
VDDIO_2
9
10
CVDDIO_2
Emulation device
Target board
VDDD
11
12
CVDDD
Emulation device
Not Connected
NC
13
14
NC
Not Connected
Not Connected
NC
15
16
NC
Not Connected
Not Connected
NC
17
18
NC
Not Connected
Not Connected
NC
19
20
NC
Not Connected
Ground
GND
21
22
GND
Ground
Ground
GND
23
24
GND
Ground
Ground
GND
25
26
KEY
P2 Signal description
Signal Direction is described from the BlueBox perspective.
By default, all jumpers are set to connect your target power supply to the microcontroller resid-
ing on the Emulation Adapter . Only pins 1-2, 3-4, 7-8, 9-10 and 11-12 must be bridged but for
the convenience and ease of use all jumpers are set, except for pins 5-6 and 25-26.
Pin 26 is the polarizer key preventing incorrect connection of the IEA-PS Power converter, when
being plugged in.
If a different power source is used (e.g. a Standalone operation), remove all jumpers and apply
3V3 or 5V to:
·
CVDDA (pin 2),
·
CVREFH (pin 4, apply the same voltage as on VDDA),
·
CVDDIO_1 (pin 8),
·
CVDDIO_2 (pin 10),
·
CVDDD (pin 12).
Enclosed Power supply package (Power converter and Power adapter) simply plugs into the P2
header row, providing the necessary power supply for Emulation Adapter operation.
LED D1 indicates, if power is supplied to the Emulation Adapter. Refer to the microcontroller doc-
umentation for more details about power voltage designations.
P3 – P6: Emulation device pinout
P3, P4, P5, P6 pinouts match the pinout of the emulation device (176QFP). Refer to the micro-
controller documentation for pin assignment.
J14 and J15: GND connecting points
J14 and J15 provide grounding points on the EA.

Connectors
P1: CoreSight 20 connector
CoreSight 20 connector P1 exposes debug and trace signals and has the following pinout on
the Emulation Adapter side:
Signal
Pin
Pin
Signal
CVDDA
1
2
TMS_SWDIO
GND
3
4
TCK_SWDCLK
GND
5
6
TDO_SWO
NC
7
8
TDI
GND
9
10
RESETn
GND
11
12
TRACECLK
GND
13
14
TRACEDATA[0]
GND
15
16
TRACEDATA[1]
GND
17
18
TRACEDATA[2]
GND
19
20
TRACEDATA[3]
Debug and Trace CoreSight 20 connector pinout
Signal Direction is described from the BlueBox perspective.
Be aware that debug and trace signals from the Emulation adapter superset device are
not connected to the target board. They are exposed only to the connectors on the
Emulation adapter.

Power supply package
A Power supply package, which is delivered with the Emulation Adapter, is required when:
·
The Emulation Adapter is used as a standalone device .
·
The target board doesn’t provide an accurate supply voltage.
·
The target board doesn’t provide sufficient current for the Emulation Adapter operation.
The Power converter can supply either 3.3 V or 5 V. Array of jumpers J0 – J9 select 3.3 V or 5 V
voltage on the P3 connector, which connects to the Emulation Adapter.
Signal
Pin
Pin
Signal
NC
1
2
J0
NC
3
4
J1
NC
5
6
J2
NC
7
8
J3
NC
9
10
J4
NC
11
12
J5
NC
13
14
J6
NC
15
16
J7
NC
17
18
J8
NC
19
20
J9
GND
21
22
GND
GND
23
24
GND
GND
25
26
KEY
P3 connector and J0-J9 jumper correlation table
For example, when J2 is in the 3V3 position, it supplies 3.3 V to pin 6 of the P3 connector. When
J2 is in 5V position, it supplies 5 V to pin 6 of the P3 connector pin.
Be careful not to supply 5 V to the microcontroller power supply pin which has de-
clared maximum voltage 3.3 V! Refer to microcontroller documentation for detailed in-
formation.
External power supply requirements:
Min Voltage
Max Voltage
Min Power
8 V
12 V
5 W

Standalone operation
Emulation Adapter is delivered with all components required for a Standalone operation.
Power supply
Use enclosed IEA-PS Emulation Adapter Power converter and adapter.
Clock source
If user target’s crystal circuit microcontroller oscillator (if available) is not an adequate clock
source, insert appropriate crystal into the Q1 socket, replace the default 10pF C24 and C25 ca-
pacitors when necessary and place jumpers J2 and J3 in 2-3 position.

Mechanical information
Side view of the Solder part
Solder part solder pad view
Top view of the Solder part
Side view of the Emulation adapter complete setup - QFP Fixed Adaptation
Top view of the Emulation
Adapter
Top view of the Conversion board

Solder parts
In the case of soldering the Solder part manually, it’s highly recommended to prolong the solder
pad E on the outer side (e.g., for 1.5–2 mm) during the PCB design. Note that without this modi-
fication, it’s very difficult to solder the Solder part manually.
Recommended PCB footprint dimensions:
Unit (mm)
A
B
C
D
E
K
L
IA64ATQ-SOLDER
12
1.505
13.0
13.0
2.3
14
14
IA80ATQ-SOLDER
14
1.505
15.0
15.0
2.3
16.0
16
IA100TQ-SOLDER
16.5
1.125
17.0
17.0
2.15
19.55
19.55
IA144TQ-SOLDER
22
1.125
23.0
23.0
2.15
25.05
25.05
Use the Surface Mount Technology (SMT) to solder the Solder parts to the user target
board instead of the original microcontroller. iSYSTEM provides this soldering service
on request too.
Emulation Adapter
Unit (mm)
M
N
P
R
S
T
V
IEA-CYT2B9
70
70
32.6
38
47.5
IEA-CYT2B9-xxxx
70
70
To view Emulation Adapter schematics, use the short link isystem.com/schematics.
Table of contents
Other TASKING Adapter manuals
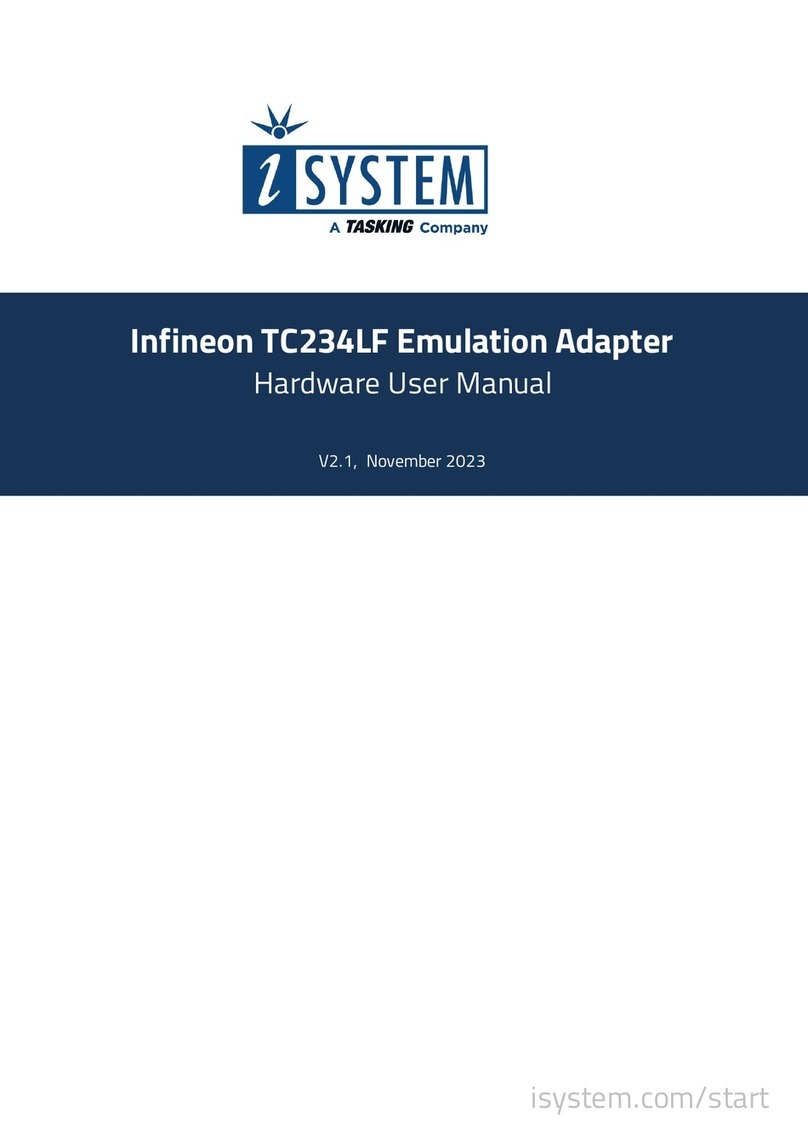
TASKING
TASKING iSYSTEM Infineon TC234LF Instructions for use
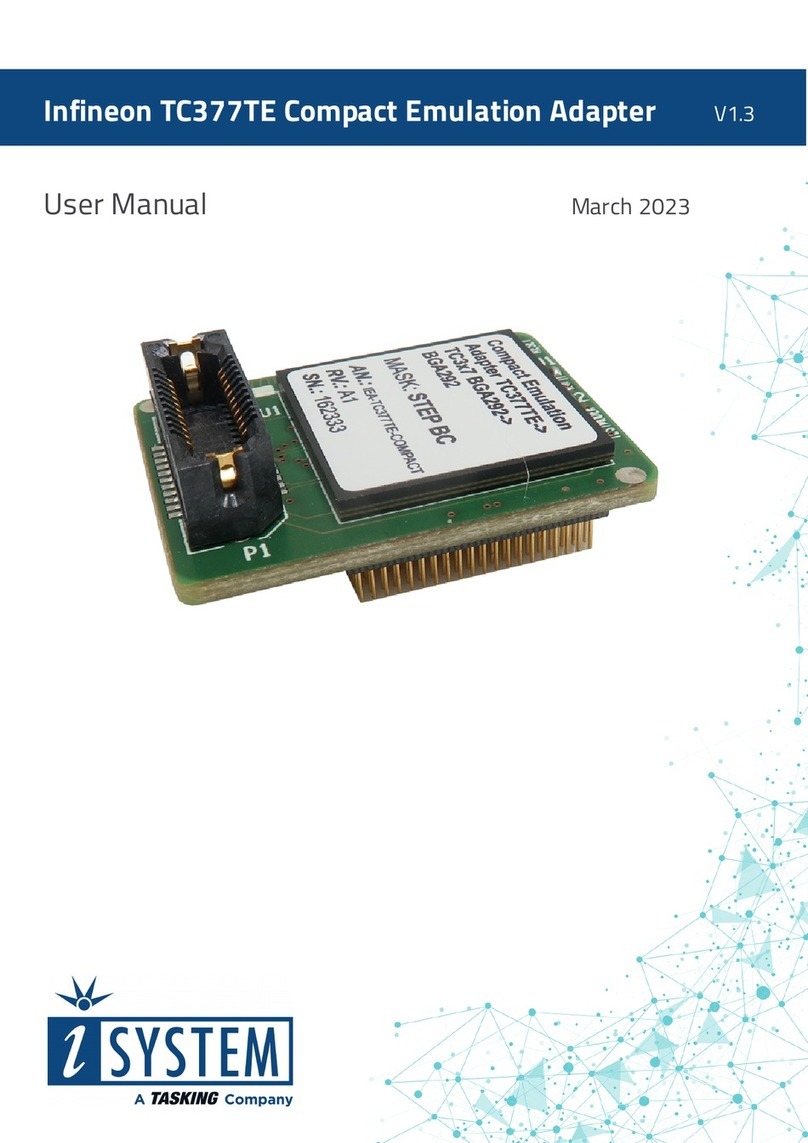
TASKING
TASKING iSYSTEM Infineon TC377TE User manual
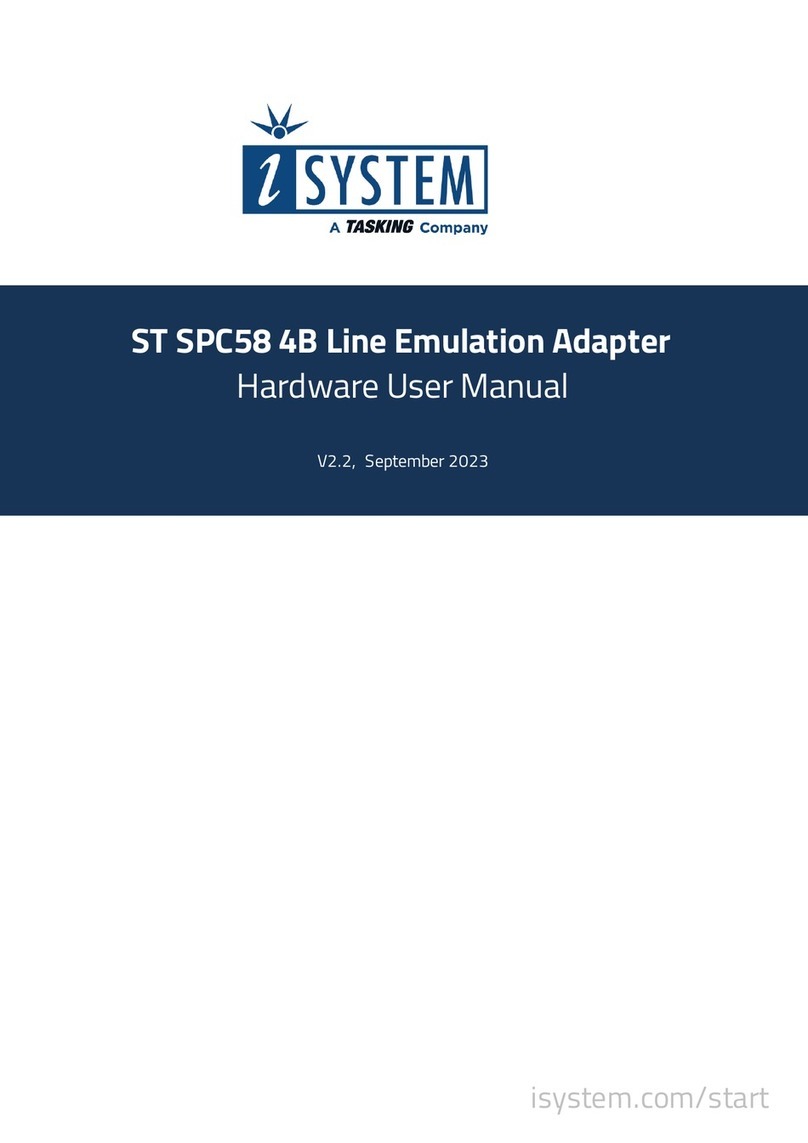
TASKING
TASKING iSYSTEM ST SPC58 4B Instructions for use
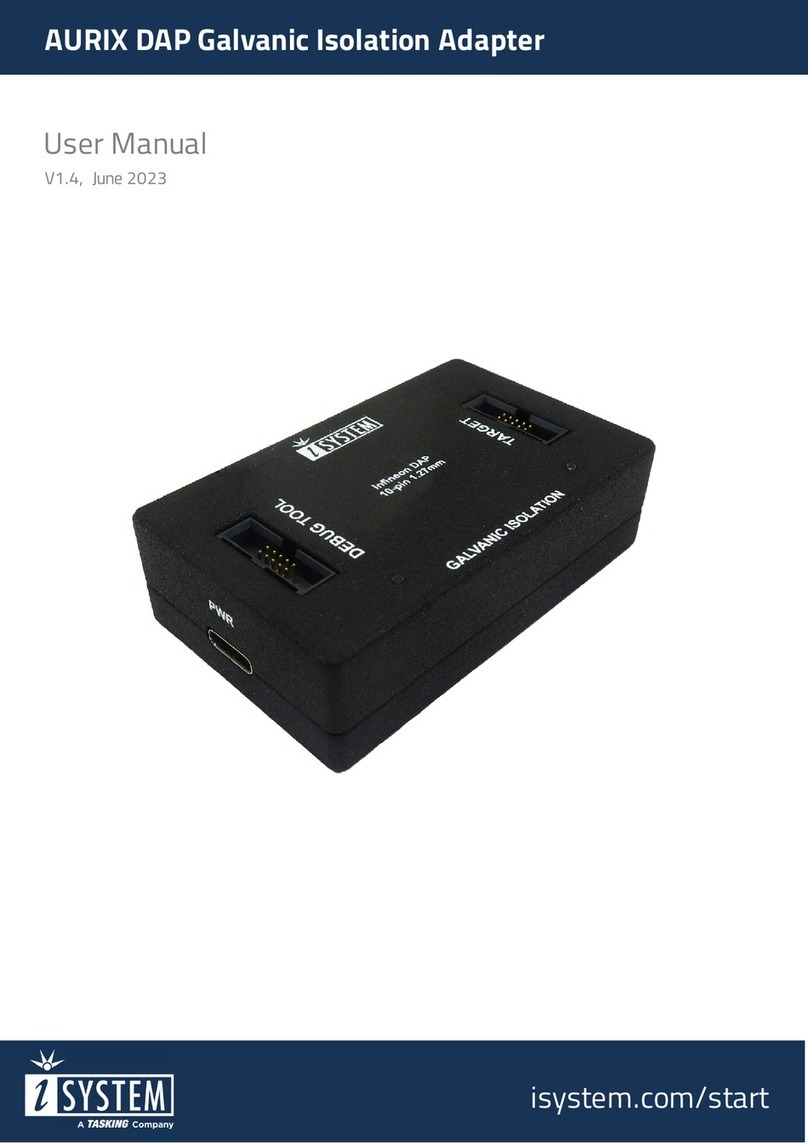
TASKING
TASKING iSYSTEM AURIX DAP User manual
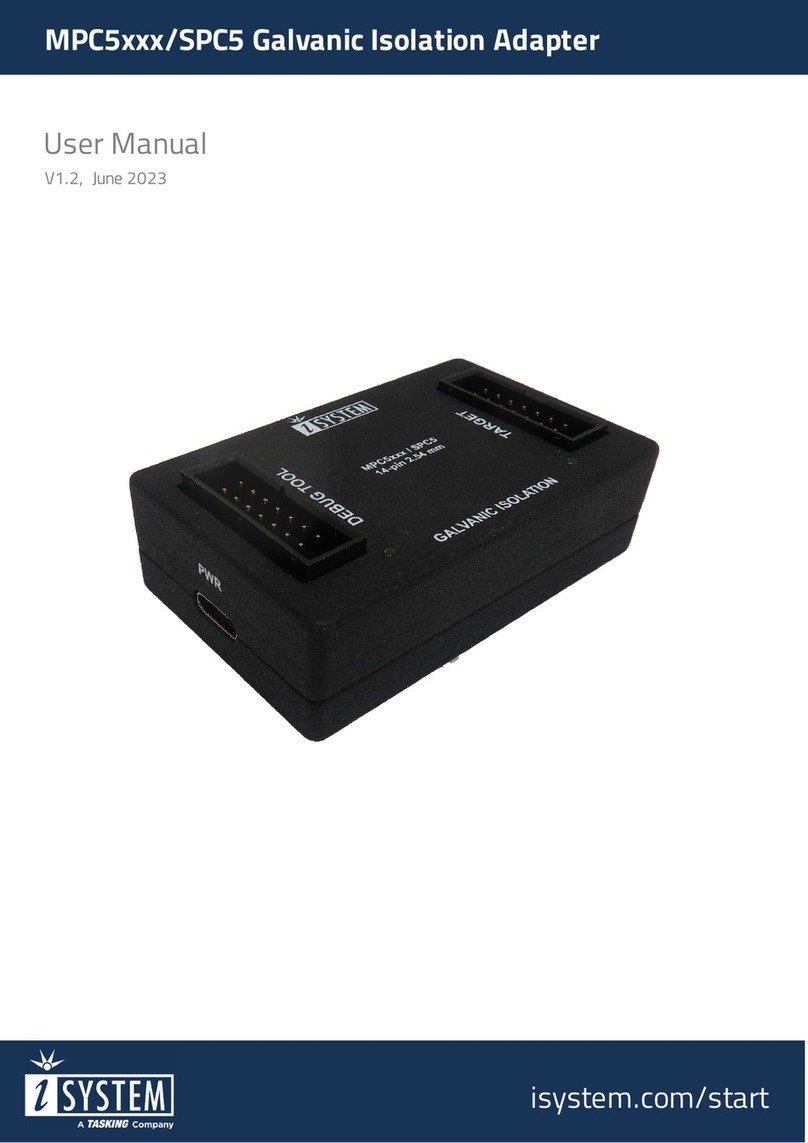
TASKING
TASKING iSYSTEM Aurora MPC5 Series User manual
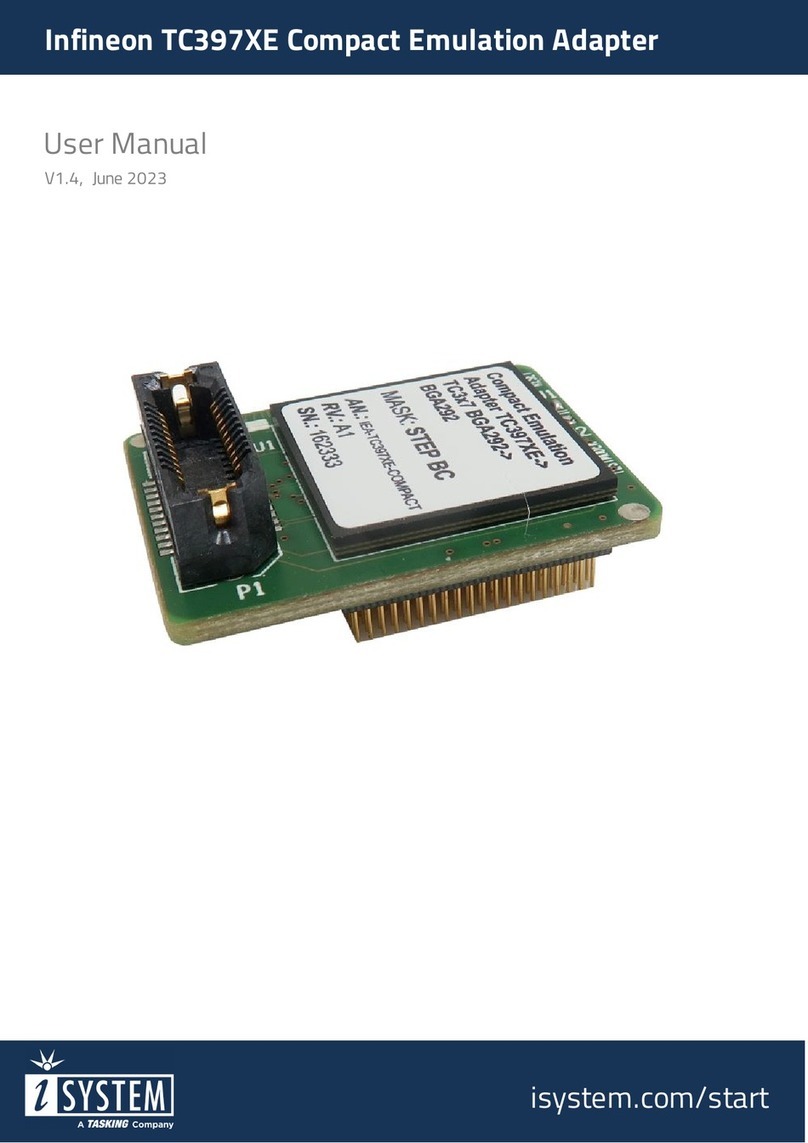
TASKING
TASKING iSYSTEM Infineon TC397XE User manual
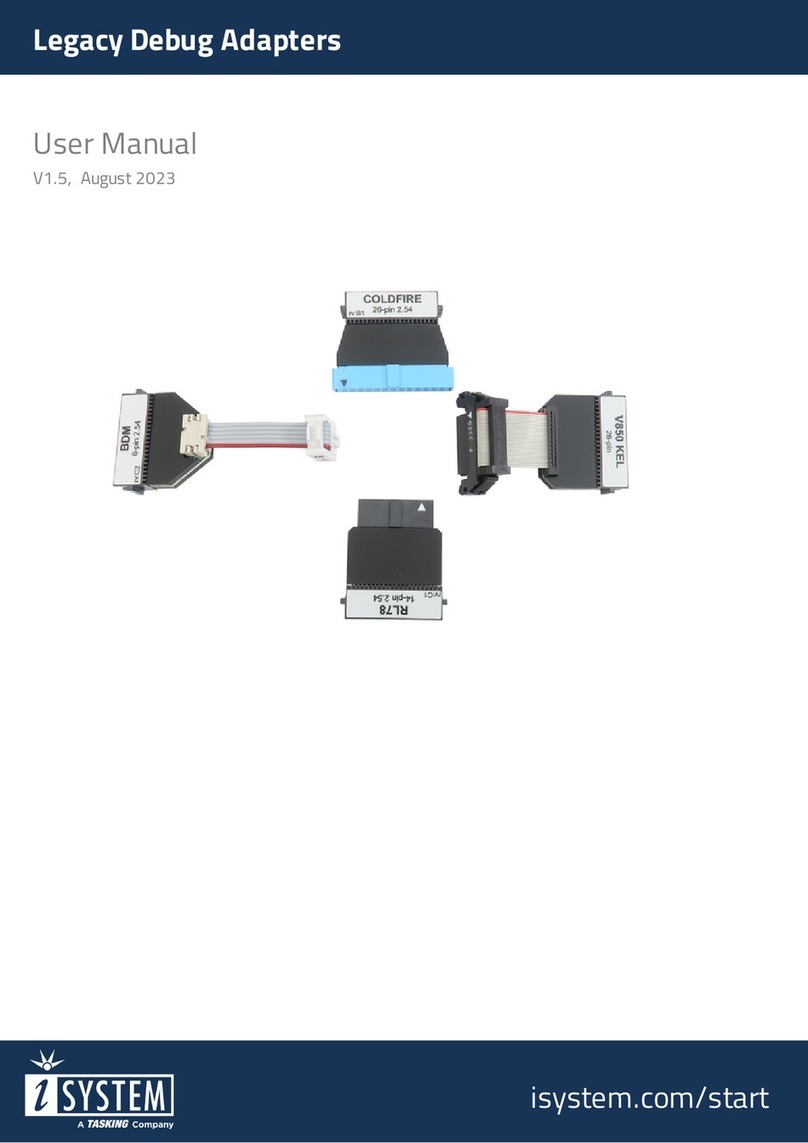
TASKING
TASKING iSYSTEM IC50130 User manual
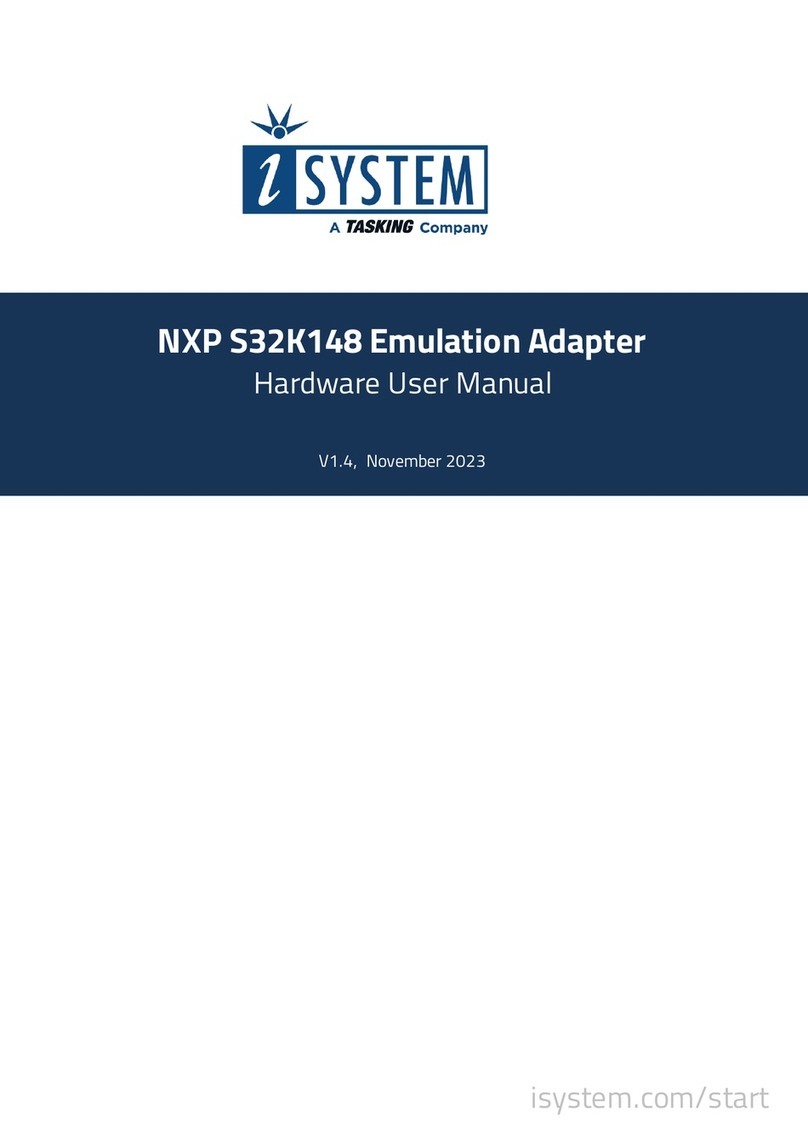
TASKING
TASKING iSYSTEM NXP S32K148 Instructions for use
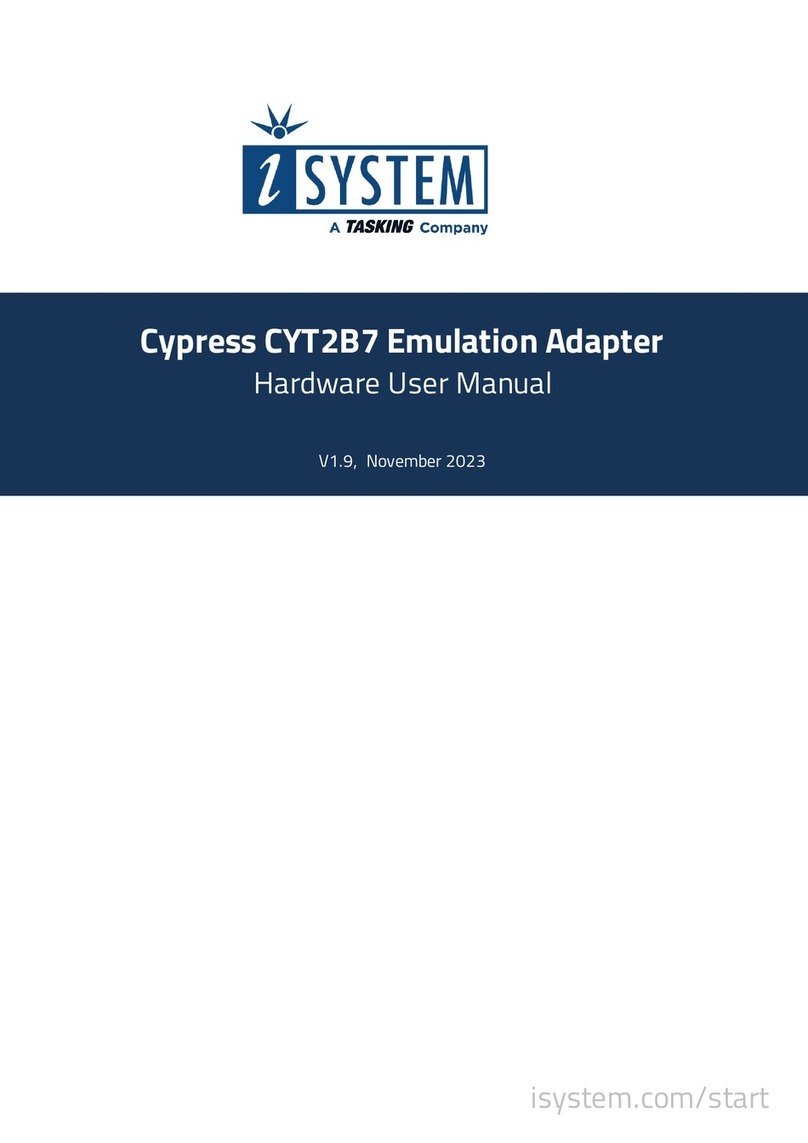
TASKING
TASKING iSYSTEM Cypress CYT2B7 Instructions for use
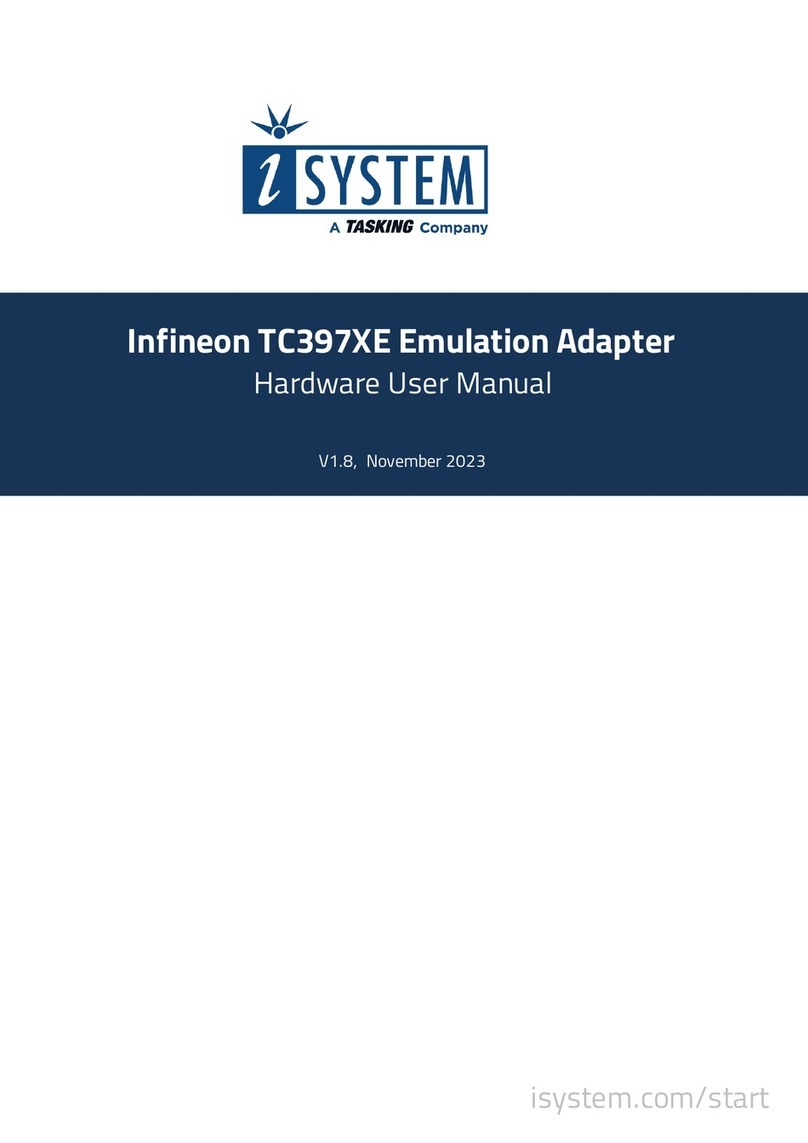
TASKING
TASKING iSYSTEM Infineon TC397XE Instructions for use