TECH ST-450zPID User manual


ST – 450 z PID
Declaration of Conformity No. 61/2010
Hereby, we declare under sole responsibility that the ST-450
zPID 230V 50Hz thermoregulator manufactured by TE H,
headquartered in Wieprz 1047A, 34-122 Wieprz, is compliant
with the Regulation by the Ministry of Economy. (Journal of Laws
Dz.U. 155 Item 1089) of July 21, 2007 implementing provisions
of the Low Voltage Directive ( VD) 2006/95/EC of January 16,
2007.
The ST-450 zPID controller has been tested for
electromagnetic compatibility (EM ) with optimal loads applied.
For compliance assessment, harmonized standards were
used:
PN-EN 60730-2-9:2006.
- 2 -

ST – 450 z PID
ATTENTION!
High voltage!
Make sure the regulator is disconnected from
the mains before working on the power
supply (cable connections, device installation,
etc.)!
All connection works must only be carried out
by qualified electricians.
Before activating the controller, measure the
motor resetting efficiency and inspect wire
insulation.
- 3 -


ST – 450 z PID
I. Description
Temperature controller ST–450 zPID is intended for use with
central heating boilers equipped with feeding screw. It controls water
circulation pump, domestic hot water pump, floor heating pump,
circulation pump, blower (fan) and fuel feeder. It incorporates a valve
control module and can operate with two mixing valves (via additional
ST-61 modules), conventional (two-state) room controller or RS-port
communication, GSM module or Ethernet module.
The advantage of the controller is the ease of use. The user can change all
parameters using a pulser knob. Another advantage is a large and easy-to-
read display where the current boiler operation is shown.
Exemplary view of the main screen:
The ST-450zPID controller is a regulator with a continuous output signal
utilizing the PID regulation algorithm. In this type of controller the blow-in
power is calculated on the basis of the measurement of the temperature of the
boiler and the temperature of flue gas measured on the outlet of the boiler.
Operation of the fan proceeds on an ongoing basis and the blow-in power
depends directly than the measured boiler temperature, the temperature of flue
gas and the difference of these parameters from their preset values.
Stable maintenance of the set temperature without any unnecessary
adjustments and oscillations is the advantage of a regulator with PID.
When using this type of controller with a flue gas outlet sensor, savings in
fuel combustion may reach up to more than ten percent; The outlet water
temperature is very stable, which affects the longer life span of the exchanger
(boiler). hecking the temperature of flue gas at the outlet from the boiler
causes low emission of dusts and gases harmful for the environment. Thermal
energy from the flue gas is not wasted and released to the chimney, but used
for heating.
- 5 -

ST – 450 z PID
Below we present the results of tests conducted with the use of the Tech
controller with PID control:
and the same controller without PID control:
Any comments concerning the program should be reported to the boiler's
manufacturer.
Each controller should be set individually for personal needs, depending on the
type of fuel used for burning as well as the type of the boiler. The TE H
company shall not be liable for any incorrect settings of the controller.
I.1. Basic terms
Firing – The cycle starts after the flue gas temperature has reached the defined
value provided that it does not drop below that level for a period of 30 seconds
(factory-set firing time).
Operation – After completion of firing cycle the controller enters the operation
cycle and a message reading “PID:OPERATION” appears on the display. It is
the basic operation status of the controller where the blowing operation and fuel
feeding are performed automatically following the PID algorithm and the
temperature is fluctuating around the temperature preset by the user. Should
the temperature rise unexpectedly 5° above the pre-set value a so-called
supervision mode is activated.
Supervision mode– It is activated automatically if the temperature exceeds
the pre-set value by more than 5° in the operation mode. In such a case the
controller changes PID operation to manual settings (according to parameters
- 6 -

ST – 450 z PID
stored in the installation menu >> Supervision mode) to reduce the circulation
water temperature and a message “PID:SUPERVISION” appears in the
display.
Damping – If the flue gas temperature drops below the predefined value and
does not rise above that level for a period of 300 seconds (factory-set damping
time) the controller enters the damping mode. When in that mode both blower
and feeder are stopped and the display reads “PID:DAMPED”.
II. Functions of the regulator
This chapter describes the functions of the regulator, the method of
changing the settings as well as navigation in the menu which is made using
the pulse generator (knob). The boiler's operational parameters are displayed
on the main screen of the controller. The user selects the operation mode and a
number of settings of the boiler according to their own needs.
II.1. Homepage
During normal operation of the regulator, the main page is visible on the
graphic display. Depending on the operation mode, one of the following
screens is displayed.
Pressing the knob of the pulse generator brings the user to the first
level menu. The first three menu options are shown on the display. Turn the
knob to move to subsequent options. Press the knob to select a given function.
Similar actions are made when changing parameters. To introduce changes it is
necessary to approve them by pressing the pulse generator when the
APPROVE message is shown. If the user does not want to make any changes
in a given function, they should press the pulse generator when the CANCE
message is shown. To exit the menu select the exit option.
If necessary, you can use the standby mode button located on the
controller housing to rapidly turn off all actuators. This is an additional
safeguard feature for use in an emergency situation that allows you to power
down all controller actuators (fan, pump, valve).
NOTE: Power is not disconnected from the controller when it is in standby mode.
II.2. Screen view
You can use this function to select one of four thermoregulator operation
main screens:
➔H screen (displays the current mode of operation of the boiler),
➔main valve (displays the operating parameters of the main valve),
➔valve 1 (displays the operating parameters of additional valve 1)
➔valve 2 (displays the operating parameters of additional valve 2)
- 7 -

ST – 450 z PID
NOTE: To enable the views showing valve parameters the respective valves
must be pre-installed and configured properly by a installation fitter.
II.3. Firing
This function helps to fire the boiler easily. After initiation of fire the user will
start the automatic firing cycle. Selection of optimum working parameters will
allow the boiler to enter the operation mode smoothly by using the PID
function.
II.4. Preset temperature of the central heating system
The option is used to set the boiler temperature. The user can change the boiler
temperature within the range of 45º to 80º . The preset central heating
system temperature can also be changed directly in the main screen of the
controller by turning the pulser knob.
Additionally, the preset central heating system temperature can be adjusted
using the room temperature reduction function (see Item II.15) and the weekly
control function (see Item II.6). The preset temperature is a sum of all those
values but it may not exceed the range of 45º to 80º .
II.5. Set-point DHW temperature
This function allows you to set your required set-point temperature for
domestic hot water. You can adjust this temperature within a range from 40O
to 75O.
II.6. Manual operation
For the user's convenience, the regulator has been equipped with a
- 8 -

ST – 450 z PID
Manual operation module. In this function, each executive device (the feeder,
the blow-in, the H pump, the HUW pump, the circulation pump and the floor
pump) is activated and deactivated independently of the others.
Pressing the pulse generato activates the engine of the chosen device.
This device remains activated until the pulse generator is pressed again.
The blow-in power, where the user has the possibility to set any rotational
speed of the fan in manual operation, is additionally available.
II.7. Operation mode
In this function, the user selects one of four options of the
boiler's operation.
▪House heating
When you select this option the controller switches over to a mode where
heating is provided only to heat the central heating circuit. The central heating
pump begins to run above the pump activation temperature (factory set at
38O - see Section III.g). The pump will turn off below this temperature (minus
a hysteresis of 2° ).
▪Boiler tank priority
In this mode, the boiler tank (hot water) pump will be switched on first to run
until the set-point temperature is reached (see Section II.e), after which the
- 9 -

ST – 450 z PID
pump will be turned off and the H circulating pump will be enabled.
The central heating pump will run all the time until the boiler tank temperature
drops below its set-point by the hot water hysteresis value. At that moment the
H pump will turn off and the HW pump will turn on (both pumps operating
alternately).
In this mode the fan and the feeder are run only up to 62O as measured at the
boiler (instantaneous set-point) so as to prevent overheating of the boiler.
NOTE: The boiler must be fitted with check valves on the central heating and
hot water pump circuits. The valve mounted on the hot water pump is to
prevent drawing hot water from the boiler tank.
▪ Pumps in parallel
In this mode both pumps begin to run together (in parallel) above the pump
activation temperature. However, these temperatures may vary for each pump,
depending on your settings (see Sections III.g-h). When this is so one of the
pumps will switch on earlier than the other one, but after both thresholds are
crossed both pumps will run together. The central heating pump will run all the
time while the hot water pump will turn off when the boiler tank set-point
temperature is reached. It will turn on again when the temperature drops by the
preset HW hysteresis value below its set-point.
▪Summer mode
Once this function is activated the central heating pump will be off and the DHW
pump will turn on above the preset activation temperature (see Section III.h)
and will work continuously until the temperature drops below the activation
temperature by the hot water hysteresis value or until the following conditions
are met:
(boiler temperature) + 2° ≤ (boiler tank temperature)
In summer mode you only enter the set-point temperature of the boiler, which
is also understood to mean the set-point temperature of the boiler tank.
II.8. Weekly control
The function is used to programme daily changes in the boiler
temperature. The preset temperature deviations are within the range of +/-
100.
- 10 -

ST – 450 z PID
Step #1:
The user needs to set current time and date first (Installer menu > lock).
Step # :
The user sets temperature values for individual days of the week (Set mode 1):
Monday– Sunday
Select specific hours and required deviations from the preset temperature (how
many degrees the temperature should rise or drop) for each day of the week.
Additionally, the preset values can be copied to facilitate the operation.
Example
Monday
preset: 3 00 , temp. -100 (temperature change– 100)
preset: 4 00 , temp. -100 (temperature change – 100)
preset: 5 00 , temp. -100 (temperature change – 100)
In such a case, if the temperature preset on the boiler is 60º , it will drop
10º to 50º between 3 a.m. and 6 a.m. on Monday.
As an alternative to the temperatures being preset separately for
individual days, the temperatures can also be set collectively, in the second
mode, for the working days (from Monday to Friday) and the weekend
(Saturday and Sunday) separately - Set mode 2.
Monday - Friday; Saturday - Sunday
Similarly to the previous mode it is necessary to select specific times and
required deviations from the temperature preset for the working days (Monday
- Friday) and the weekend (Saturday, Sunday).
Example
Monday - Friday
preset: 3 00 , temp. -100 (temperature change – 100)
preset: 4 00 , temp. -100 (temperature change – 100)
preset: 5 00 , temp. -100 (temperature change – 100)
Saturday - Sunday
preset: 16 00 , temp. 50 (temperature change +50)
preset: 17 00 , temp. 50 (temperature change +50)
preset: 18 00 , temp. 50 (temperature change +50)
In this case, if the preset boiler temperature is 60º , the temperature will drop
10º to 50º between 3 a.m. and 6 a.m. on each day from Monday to Friday.
However, the temperature will rise 5º to 65º during weekend (Saturday,
Sunday) between 4 p.m. and 7 p.m.
Step #3:
The user enables one of two preset modes (Mode1, Mode2) or disables the
weekly control option.
Once the mode is enabled the value of the deviation currently set is displayed
on the main page of the controller next to the preset central heating system
- 11 -

ST – 450 z PID
temperature. This, additionally, indicates that the weekly control is active.
Data deletion function is a simple method to remove all previously saved
weekly programme settings to enter new settings.
II.9. Fuel size
This option is used to select one of two fuel sizes: coarse or fine. Appropriate
blowing power and fuel supply rate are selected for each of the sizes.
II.10. Room temperature reduction
After the room controller reaches the preset room temperature, the preset
boiler temperature (set in the installation menu - see Item III.16) will drop by
the value set there. The reduced temperature will not be lower however than
the preset minimum central heating temperature.
Example: Temperature preset on the boiler: 55º
Room temperature reduction: 15º
Minimum temperature set on the boiler: 45º (factory setting)
Once the preset room temperature is reached (indicated by the room controller)
the temperature preset on the boiler will drop to 45º i.e. only 10º although
the room temperature reduction is 15º . At the same time a message reading
"!-10º" will be shown in the main display next to the preset boiler temperature.
II.11. Factory settings
The controller is pre-configured for its operation. However, its settings should
be modified to meet your individual needs. You can return to the factory
settings at any time. If you enable the factory settings option you will lose all
of your own boiler settings, which will replaced with the settings saved by the
boiler manufacturer. From now on you can re-set your own parameters of the
boiler.
II.12. About the program
You can use this function to check the software version installed in the
boiler controller.
- 12 -

ST – 450 z PID
III. Installation menu
The functions of the installation menu should be set by the person
installing the boiler or service personnel of the manufacturer.
III.1. Fan coefficient
This function is used to control the fan power. The control is based on shifting
the fan performance curve up or down. If the blowing rate in the whole control
range is too low/high, the coefficient should be increased/decreased accordingly
to ensure proper efficiency of the fan operation.
Malfunctioning of the blowing system is most frequently caused by relatively
large differences between voltages supplied to individual units, which has a
significant impact on the fan operation.
III.2. Feeding coefficient
Fuel feeding coefficient is intended to optimize the feeder operation so as to
ensure that fuel is fed to the furnace in proper quantities. This function allows
setting the percentage increase or decrease of fuel being supplied.
Once the proper fuel size is selected in the main menu it is possible, by using
the coefficient, to adapt precisely the fuel quantity to be fed by the feeder to
the furnace.
III.3 TECH controller
A room controller can be connected to ST-450zPID controller. This
function allows configuring the controller by selecting “ON” option. Additionally,
the user may check the programme version of the room controller.
After connection of TE H controller the user may check and change the
preset temperature of the central heating system, hot domestic water and the
mixing valve. Additionally all boiler controller alarms are displayed. When the
operation involves the mixing valve the user may preview the current external
temperature while viewing the main screen with the valve parameters.
After TECH Controller option is enabled a letter "P" appears in the upper
part of the display in the main screen of the controller. A flashing letter "P"
indicates that the temperature in the room is too low. As soon as the required
room temperature is reached the letter "P" stops flashing and stays on.
ATTENTION: No external voltage can be connected to the room controller
output.
III.4. Valve
ST-450zPID controller incorporates a mixing valve control module. The below
options are used to set the operation of the mixing valve:
1. Valve state
The function allows disabling the valve temporarily without the need to
- 13 -

ST – 450 z PID
remove it completely. Once it is re-enabled no registration is required
2. Set-point valve temperature
This setting is used to set the circuit temperature to be maintained by the
mixing valve. This is the main temperature based on which the room
thermostat reduction function is to be run (see Section III.a.10). The room
thermostat reduction function is set separately for the H system (setting in the
user menu) and separately for each of the valves.
3. Temperature control
This parameter determines the sampling (control) frequency of the water
temperature downstream of the valve for the central heating or hot water
system. If the sensor indicates a change in temperature (deviation from set-
point), then the solenoid will open or close partially by a preset step to restore
the set-point temperature.
4. Opening time
You can use this function to set the time for the full opening of the valve,
that is to say, how long it takes to open the valve to 100%. This time should be
selected according to your valve actuator (shown on the nameplate).
5. Single step
You can use this function to set a percentage value for a single step in the
operation of valve opening, that is to say the maximum percentage value of
opening or closing that the valve can move in a single step (maximum
movement of the valve in one measurement cycle).
6. Minimum opening
Use this function to set the minimum value for valve opening. Below this
value, the valve will not close shut.
- 14 -

ST – 450 z PID
7. Type of valve
You can use this option to select the type of valve: central heating or
floor type.
8. Weather program (weekly valve program)
In order to enable the weather function an outdoor sensor should be
installed in a place not exposed directly to sunlight or weather conditions.
After installing and connecting the sensor the Weather program function must
be enabled in the controller menu.
For the valve to work properly enter set-point temperatures (downstream
of the valve) for the following four intermediate outside temperatures:
TEMP. FOR -20
TEMP. FOR -10
TEMP. FOR 0
TEMP. FOR 10
Heating curve - curve which is used to determine the set-point temperature of
the controller based on the outside temperature. In our controller this curve is
established based on four temperature set-points selected for their respective
outside temperatures. Set-point temperatures must be provided for the
following outside temperatures: -20º , -10º , 0º and 10º .
Where in our controller:
- 15 -

ST – 450 z PID
XA = -20º , X = 0º ,
XB = -10º , XD = 10º ,
YA, YB, Y , YD – set-point valve temperatures for their corresponding outside
temperatures: XA, XB, X , XD
After weather control is enabled the valve set-point parameter is
calculated based on the heating curve. By changing this parameter you can
decrease or increase all the weather control settings.
9. Return protection
This feature allows you to enable protection for the boiler from excessively
cold water returning from the main circuit, which could cause the boiler to suffer
from low-temperature corrosion. The return protection function works to ensure
that when the temperature is too low the valve will close partially until the short
circuit of the boiler reaches the desired temperature. This feature also protects
the boiler from a dangerously high return temperature to prevent water from
boiling.
When this function is enabled you need to set the minimum and maximum
return temperatures.
- 16 -

ST – 450 z PID
10. Room controller – the option is used to define the room controller type to
operate with the valve. The following options are available:
oOff – State of the room controller has no impact on the valve settings.
oStandard controller – A two-state controller. This setting applies to the
controller connected directly to the valve control module (ST-61) for external
valves (valve 1 & 2). For internal valve, in turn, the setting applies to the
controller connected directly to ST-450zPID controller.
oTE H controller– ontroller with RS communication function.
oProportional control – Available only with TE H controllers with RS
communication. It operates properly after configuration of the preset valve
change option and the difference in room temperatures.
•Room temperature reduction – Once the room controller has reached
the preset room temperature, the preset valve temperature will drop by the
value indicated here. (The option is unavailable if Proportional control has been
selected).
•Change of the valve presetting – The setting determines the number of
degrees the valve temperature will rise or drop with a unit change of the room
temperature (see: Room temperature difference). The function is active only
with TE H room controller and is directly related to “Room temperature
difference” parameter.
Room temperature difference – The setting determines the unit change in
current room temperature (accurate to 0.1° ) which triggers the predefined
change in the valve preset temperature (The function is active with TE H room
controller only).
11. Factory settings
This parameter allows you to restore the mixing valve settings saved by
the manufacturer. By restoring the factory settings you will not change the
valve type setting (central heating or floor type).
III.5. Valve 1
NOTE: ontrol with an additional valve (1 or 2) is only possible after you
purchase and connect the controller to an additional control module (ST-61),
- 17 -

ST – 450 z PID
which is not provided as standard equipment with the controller. In order to
control two valves you need to connect two ST-61 modules.
The options presented in this chapter are used to adjust the operating
settings of an additional mixing valve. In order for the valve to work properly
and meet your expectations it should be configured with its parameters set like
in the case of the main valve.
1. Registration
To register an additional valve enter the serial number of the control
module of the ST-61 mixing valve servo (look for the five-digit number on the
cover of this module). Without this number the valve cannot be activated.
2. Switch on
Setting as for the main valve - see Section III.4.1
3. Set-point valve temperature
Setting as for the main valve – see Section III.4.2
4. Temperature control
Setting as for the main valve – see Section III.4.3
5. Opening time
Setting as for the main valve – see Section III.4.4
6. Single step
Setting as for the main valve – see Section III.4.5
7. Minimum opening
Setting as for the main valve – see Section III.4.6
8. Type of valve
Setting as for the main valve – see Section III.4.7
9. Weather program (weather control)
Setting as for the main valve – see Section. III.4.8
10. Return protection
Setting as for the main valve – see Section III.4.9
11. Additional sensors
When two mixing valves are used and you select this function you will be able
to select the sensors from which temperature data are to be retrieved for a
valve (for return and outside temperature sensors). Temperatures can be
retrieved from the sensors of the valve being set (Own) or as per the controller
sensors (Main controller).
- 18 -

ST – 450 z PID
12. Room thermostat reduction
Setting as for the main valve – see Section III.4.10
13. Factory settings
Settings as for the main valve – see Section. III.4.11
14. Valve removal
This function is used to completely remove a valve from the controller
memory. Valve removal is used for example when removing or replacing a
module (the new module requires to be registered again).
15. About the program
When this option is selected the display will show the software
version of the active valve module.
III.6. Valve 2
All settings for valve 2 are made in the same way as in the case of valve 1.
III.7. GSM module
NOTE: ontrolling of this type is possible after purchasing and connecting, to
the controller, the additional control module ST-65 which is not attached to the
regulator as a standard feature.
The GSM module is an optional device cooperating with the boiler
controller, enabling remote control of the boiler operation with the use of a
mobile phone. The User is notified with a text message on each alert of the
boiler controller, and by sending an appropriate text message at any time, he
or she receives a return message with the information on the current
temperature of all sensors. After entering an authentication code it is also
possible to remotely change the set temperatures.
The GSM module can also operate independently from the boiler
controller. It has two inputs with temperature sensors, single contact input for
use in any configuration (detecting short circuit/opening of contacts) and one
controlled output (e.g. possibility to connect additional contactor to control any
electrical circuit).
When any temperature sensor reaches the preset deactivation
temperature, maximum or minimum, the module will automatically send a text
message with such information. It is similar in the case of a short-circuit or
opening of contact input, which may be used e.g. for simple protection of
property.
If ST-450 controller is equipped with an additional GSM module, in order to
activate this device, it is required to start the activated option (MENU> Installer
menu> GSM module> Activated).
- 19 -

ST – 450 z PID
III.8. Internet module
NOTE: ontrolling of this type is possible after purchasing and connecting, to
the controller, the additional control module ST -500 which is not attached to
the regulator as a standard feature.
The Internet module is a device enabling remote control of the boiler over
the Internet or local network . On the home computer screen the user controls
the condition of all boiler system devices and the operation of each device is
presented in the animated form.
Apart from the possibility to view the temperature of every sensor, the
user has the possibility of introducing changes of the set temperatures for both
the pumps and the mixing valves.
After activating the Internet module and selecting the DH P option, the
controller will automatically download such parameters from the local network
as: IP address, IP Mask, Gateway address and DNS Address. In the case of any
problems with downloading network parameters of the existing network, there
is a possibility of setting these parameters manually. The method of obtaining
local network parameters has been described in the instructions for the Internet
module.
The function Reset module password may be used when the User, on the
login page, has changed the factory user's password to his or her password.
When a new password is lost, it is possible to return to the factory password
after resetting the module password.
III.9. Pump activation temperature
The option is used to set the activation temperature for central heating and
domestic hot water pumps (the temperature is measured on the boiler). None of
the pumps will operate if the temperature is lower than the preset one. If the
actual temperature is higher than the preset one the pumps are working but
they operate depending on the operation mode (see: pump operation modes)
III.10. DHW hysteresis
Use this option to set your set-point temperature hysteresis at the boiler tank.
This is the maximum difference between the set-point temperature (your
required temperature for the boiler tank when the pump turns off) and the
temperature when its operation is to resume.
Example: The set-point temperature is 55° and the hysteresis value is 5o.
- 20 -
Table of contents
Other TECH Thermostat manuals
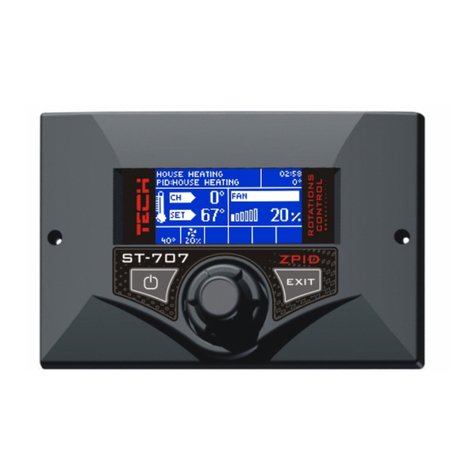
TECH
TECH ST-707 User manual
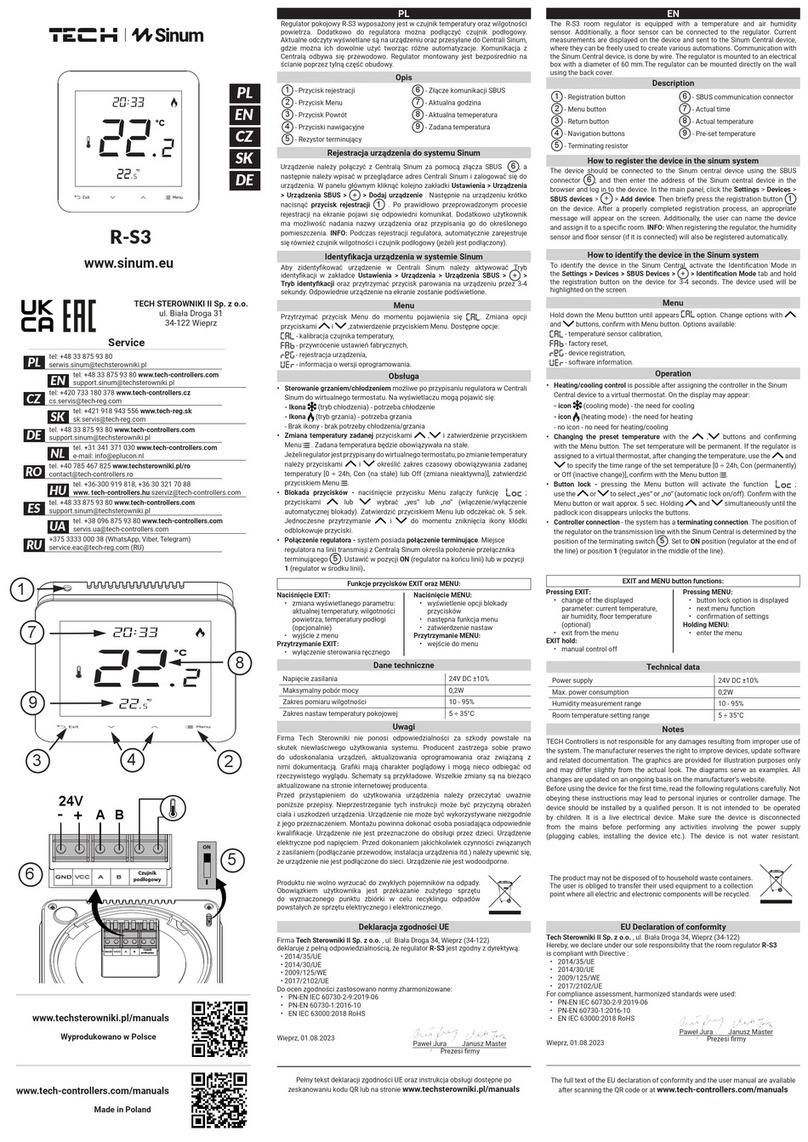
TECH
TECH Sinum R-S3 User manual

TECH
TECH ST-37 Assembly instructions
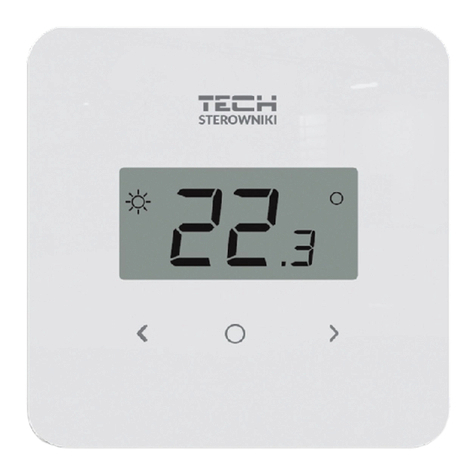
TECH
TECH EU-R-8b Plus User manual
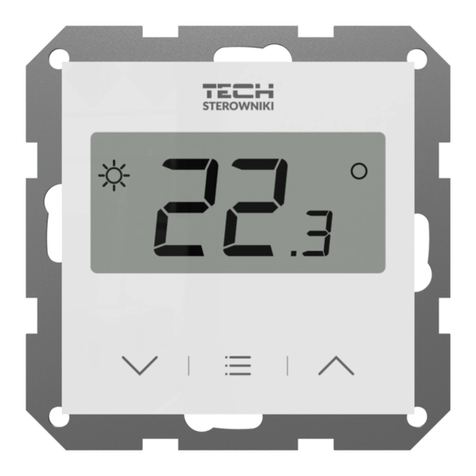
TECH
TECH EU-F-8z User manual
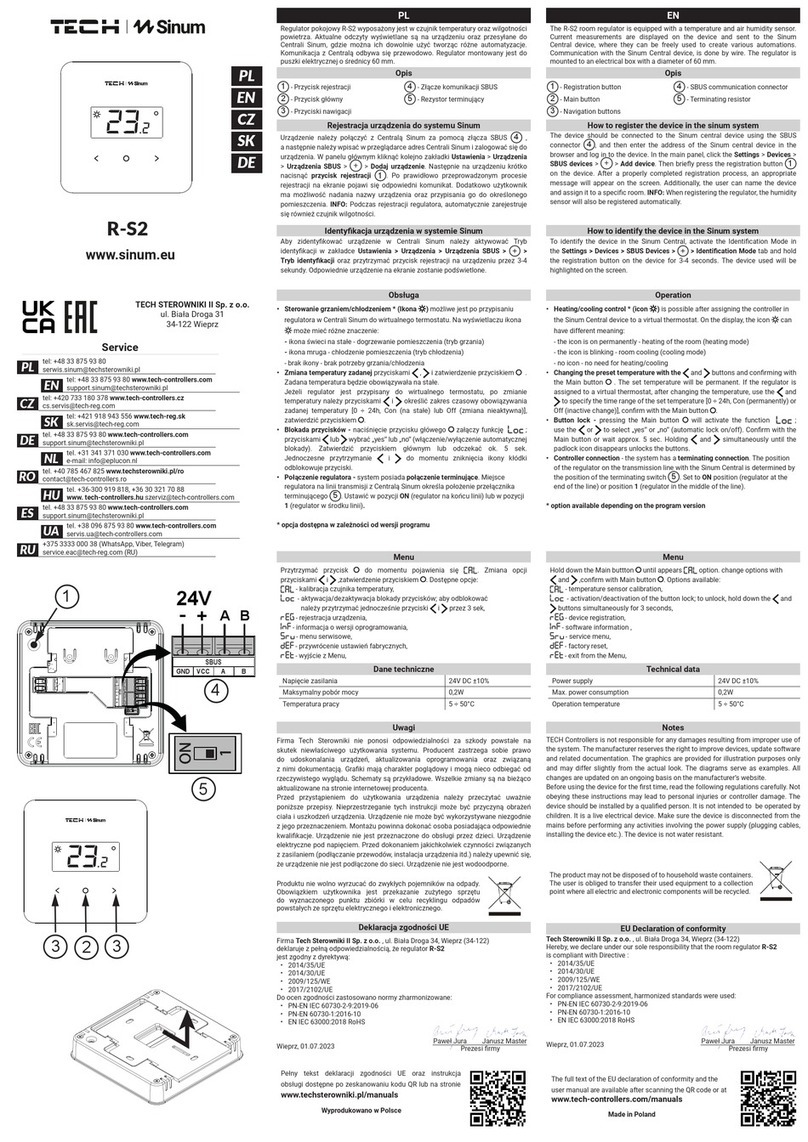
TECH
TECH Sinum R-S2 User manual
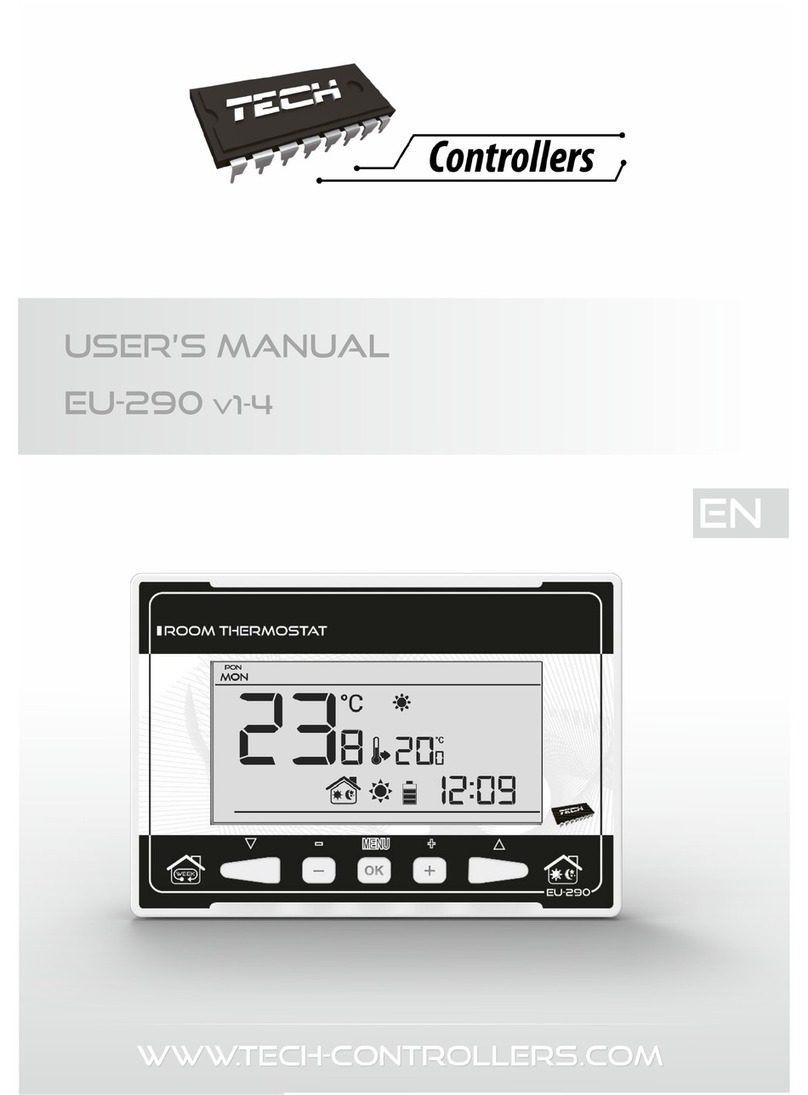
TECH
TECH EU-290 v1 User manual
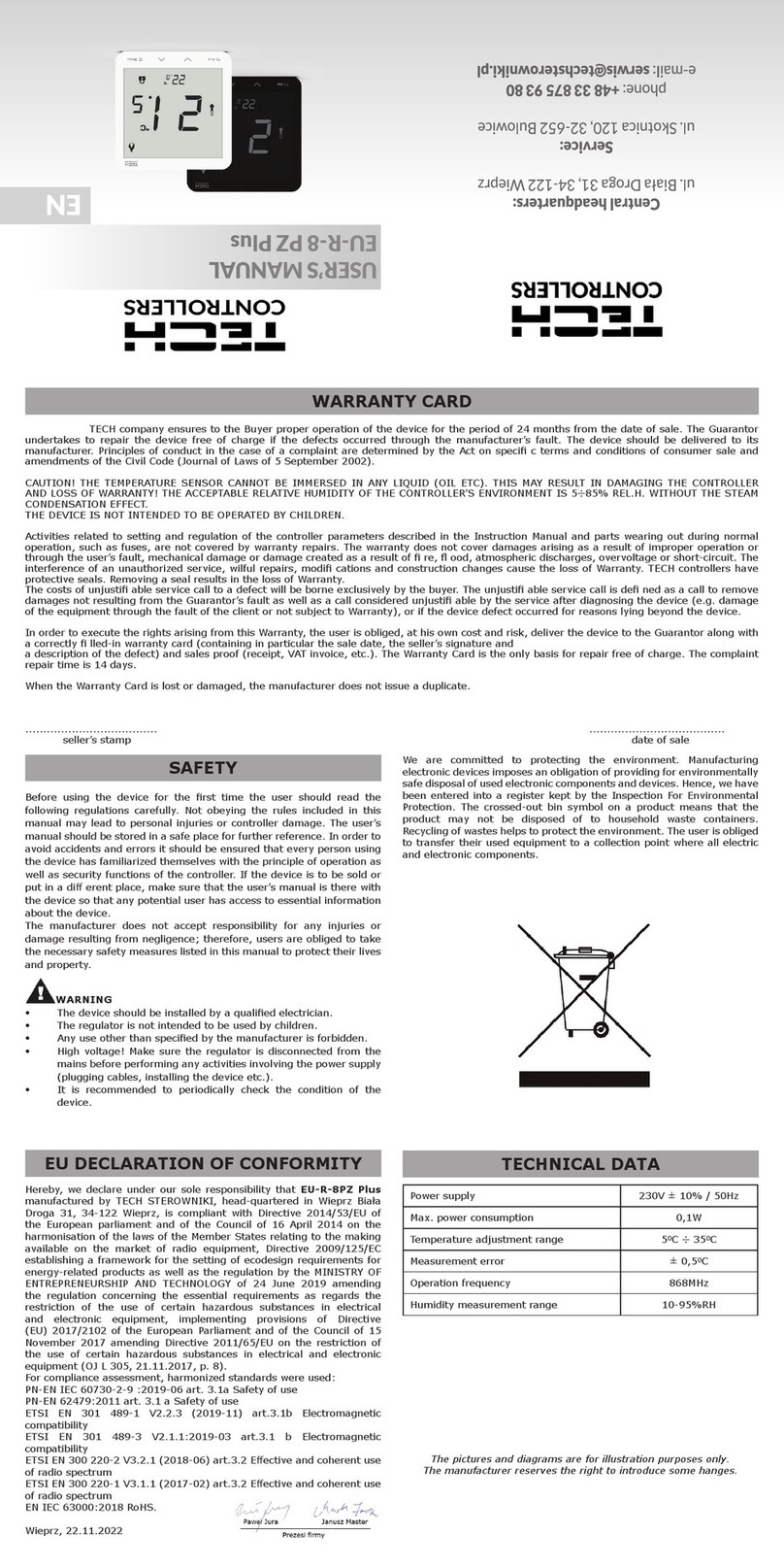
TECH
TECH EU-R-8PZ Plus User manual
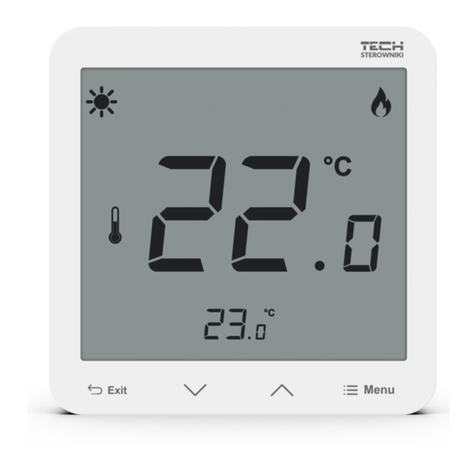
TECH
TECH EU-R-8s Plus User manual
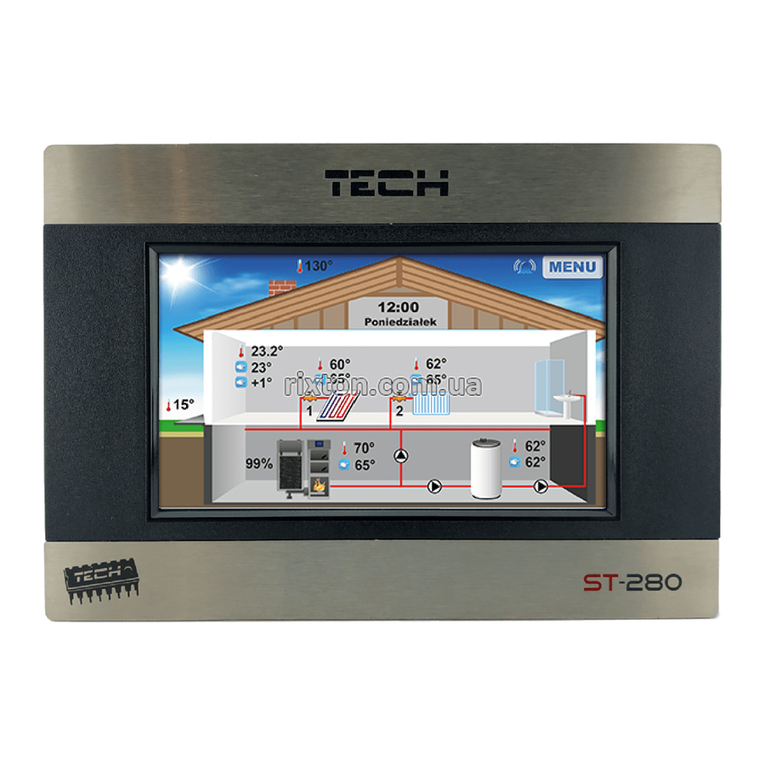
TECH
TECH ST-280 User manual
Popular Thermostat manuals by other brands
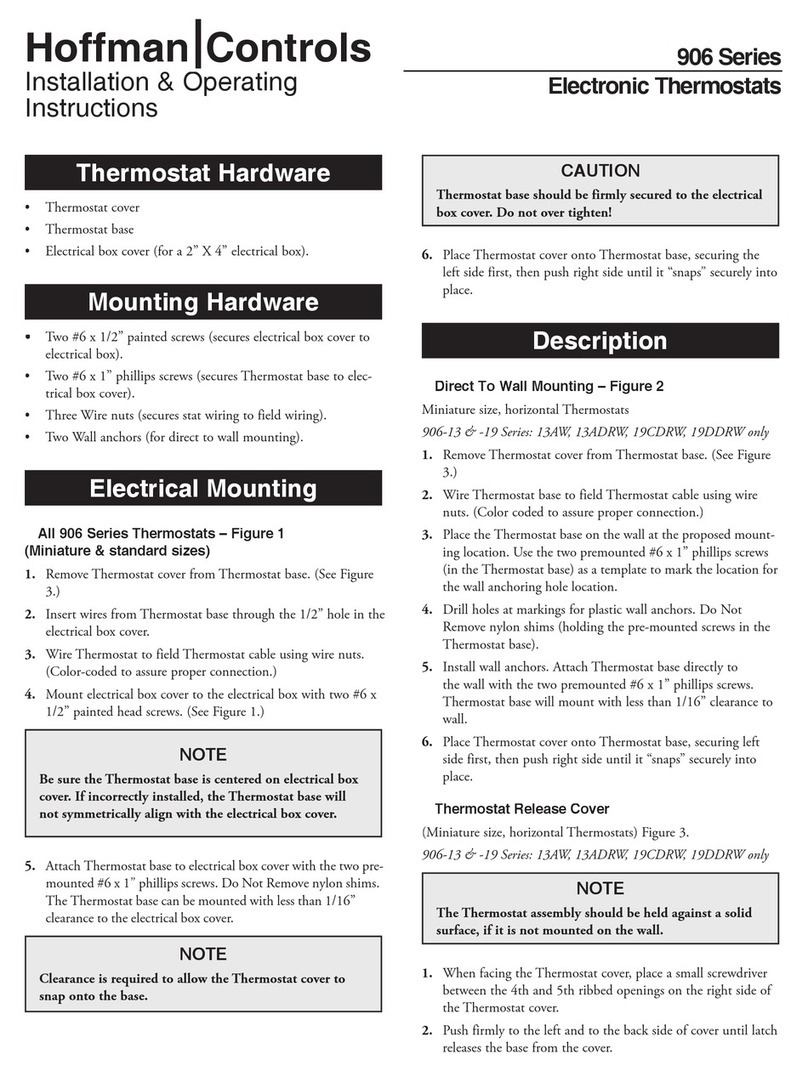
Hoffman
Hoffman 906 Series Installation & operating instructions
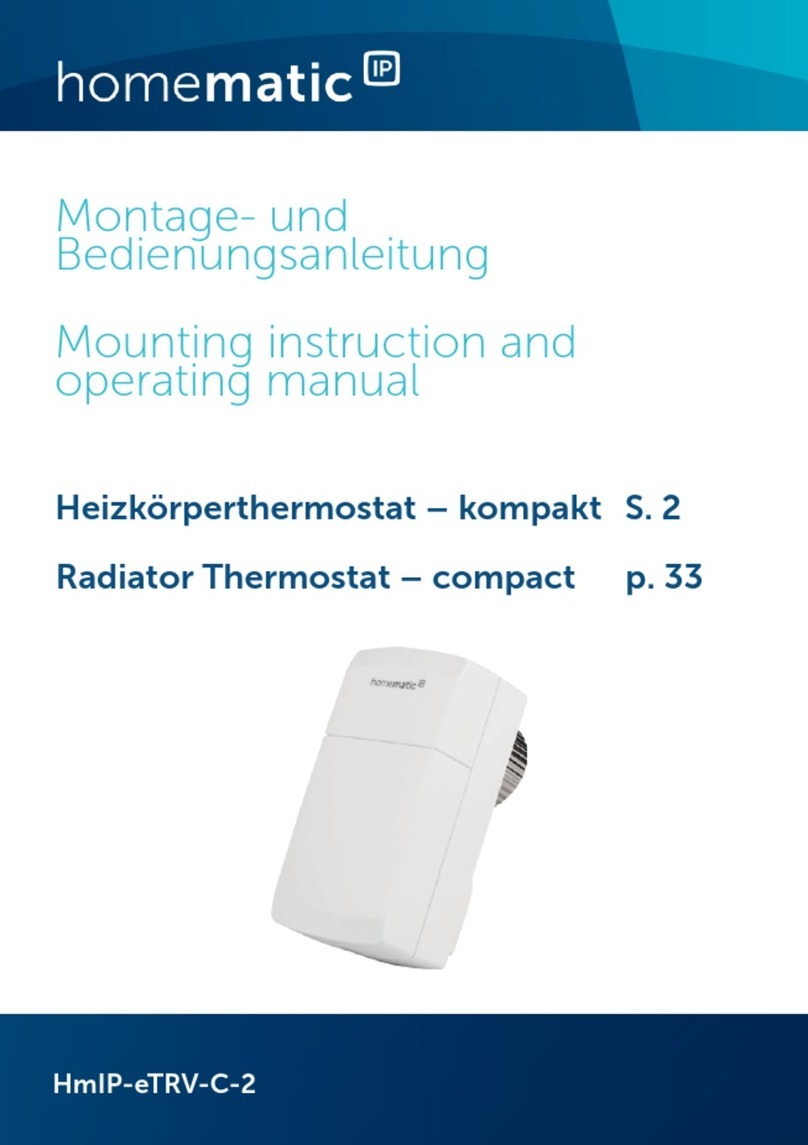
HomeMatic
HomeMatic HmIP-eTRV-C-2 Mounting instruction and operating manual

Honeywell
Honeywell TH7000 Series installation guide

Riello
Riello Hi, Comfort 100 installer and user manual
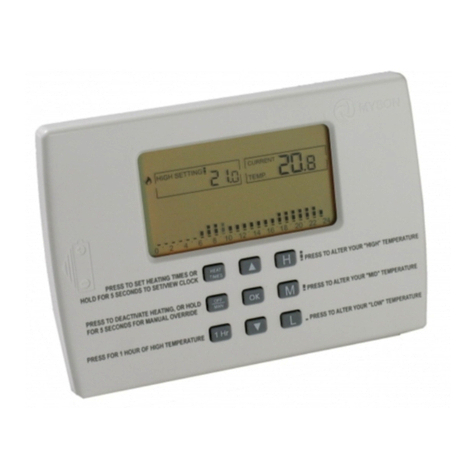
Myson
Myson MPRT MS installation instructions
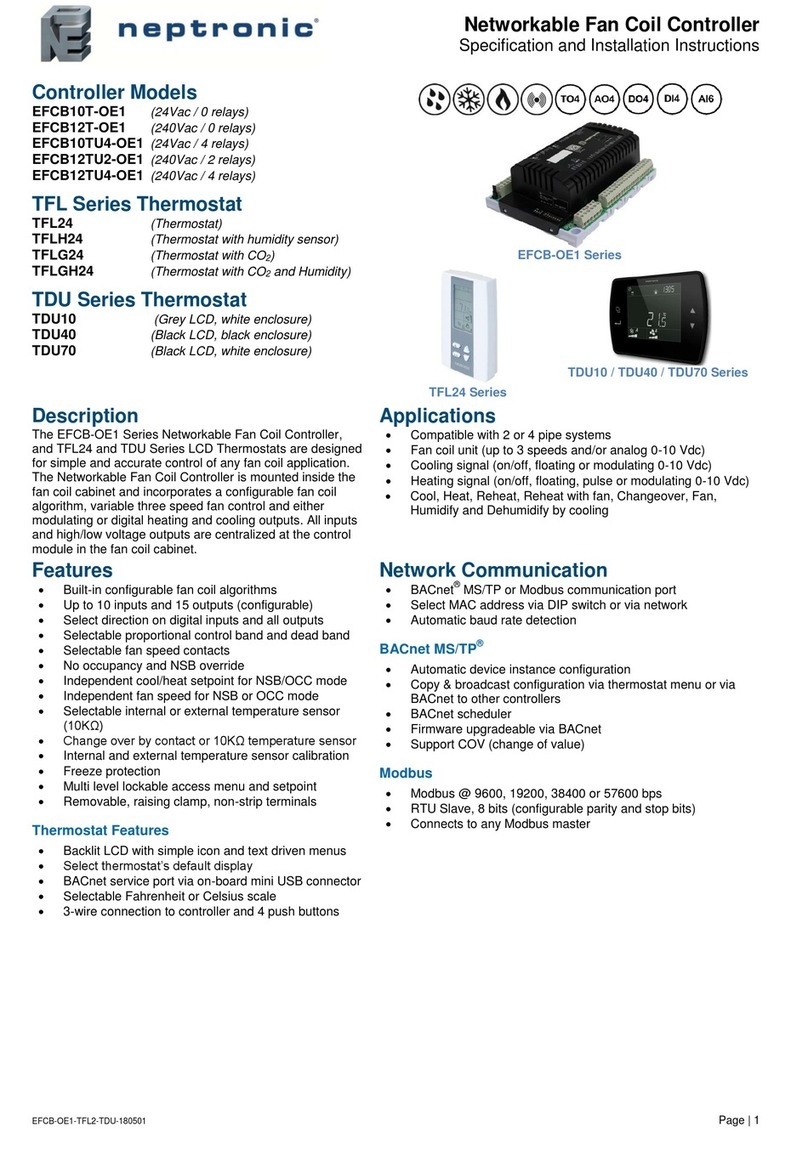
Neptronic
Neptronic EFCB12T-OE1 Specification and installation instructions