TECHTOP TD20 Series User manual


TD20 Series VFD Contents
i
Contents
1 Safety Precautions ............................................................................................................................1
1.1 Safety definition.........................................................................................................................1
1.2 Warning symbols .......................................................................................................................1
1.3 Safety guide...............................................................................................................................2
2 Product Overview..............................................................................................................................4
2.1 Quick start-up ............................................................................................................................4
2.2 Product specification..................................................................................................................5
2.3 Name plate ................................................................................................................................7
2.4 Type designation key.................................................................................................................7
2.5 Rated specifications...................................................................................................................8
2.6 Structure diagram ......................................................................................................................8
3 Installation Guide.............................................................................................................................10
3.1 Mechanical installation.............................................................................................................10
3.2 Standard wiring........................................................................................................................12
3.3 Layout protection .....................................................................................................................16
4 Keypad Operation Procedure .........................................................................................................18
4.1 Keypad introduction.................................................................................................................18
4.2 Keypad displaying....................................................................................................................20
4.3 Keypad operation.....................................................................................................................21
5 Function Parameters.......................................................................................................................24
6 Fault Tracking..................................................................................................................................85
6.1 Maintenance intervals..............................................................................................................85
6.2 Fault solution ...........................................................................................................................88
7 Communication Protocol................................................................................................................95
7.1 Brief instruction to Modbus protocol.........................................................................................95
7.2 Application of the VFD .............................................................................................................95
7.3 RTU command code and communication data illustration......................................................100
Appendix A Technical Data..............................................................................................................114
A.1 Ratings..................................................................................................................................114
A.2 Marking .................................................................................................................................115
A.3 EMC regulations....................................................................................................................115
Appendix B Dimension Drawings....................................................................................................117
B.1 External keypad (optional) structure ......................................................................................117
B.2 VFD chart..............................................................................................................................118
Appendix C Peripheral Options and Parts......................................................................................120
C.1 Peripheral wiring....................................................................................................................120
C.2 Power supply.........................................................................................................................121
C.3 Cables...................................................................................................................................121
C.4 Fuse......................................................................................................................................123
C.5 Reactors................................................................................................................................124
C.6 Filter......................................................................................................................................124
C.7 Braking components..............................................................................................................125
Appendix D Further Information......................................................................................................128
D.1 Product and service inquirie ..................................................................................................128
D.2 Feedback of TECHTOP VFD manuals ..................................................................................128

TD20 Series VFD Safety Precautions
-1-
1 Safety Precautions
Please read this manual carefully and follow all safety precautions before moving, installing, operating
and servicing the variable-frequency drive (VFD). If ignored, physical injury or death may occur, or
damage may occur to the devices.
If any physical injury or death or damage to the devices occurs for ignoring to the safety precautions in
the manual, our company will not be responsible for any damages and we are not legally bound in any
manner.
1.1 Safety definition
Danger:
Serious physical injury or even death may occur if not follow relevant
requirements
Warning:
Physical injury or damage to the devices may occur if not follow relevant
requirements
Note:
Physical hurt may occur if not follow relevant requirements
Qualified electricians:
People working on the device should take part in professional electrical
and safety training, receive the certification and be familiar with all steps
and requirements of installing, commissioning, operating and maintaining
the device to avoid any emergency.
1.2 Warning symbols
Warnings caution you about conditions which can result in serious injury or death and/or damage to the
equipment, and advice on how to avoid the danger. Following warning symbols are used in this manual:
Symbols
Name
Instruction
Abbreviation
Danger
Danger
Serious physical injury or even death
may occur if not follow the relative
requirements
Warning
Warning
Physical injury or damage to the
devices may occur if not follow the
relative requirements
Do not
Electrostatic
discharge
Damage to the PCBA board may occur
if not follow the relative requirements
Hot sides
Hot sides
Sides of the device may become hot.
Do not touch.
Note
Note
Physical hurt may occur if not follow
the relative requirements
Note

TD20 Series VFD Safety Precautions
-2-
1.3 Safety guide
•Only qualified electricians are allowed to operate on the VFD.
•Do not carry out any wiring and inspection or changing components when the power
supply is applied. Ensure all input power supply is disconnected before wiring and
checking and always wait for at least the time designated on the VFD or until the DC
bus voltage is less than 36V. Below is the table of the waiting time:
VFD module
Minimum waiting time
1PH 110V
0.4–1.1kW (0.5–1.5HP)
5 minutes
1PH 220V
0.4–2.2kW (0.5–3HP)
5 minutes
3PH 220V
0.4–0.75kW (0.5–1HP)
5 minutes
3PH 460V
0.75–2.2kW (1–3HP)
5 minutes
•Do not refit the VFD unauthorized; otherwise fire, electric shock or other injury may
occur.
•The base of the radiator may become hot during running. Do not touch to avoid hurt.
•The electrical parts and components inside the VFD are electrostatic. Take
measurements to avoid electrostatic discharge during relevant operation.
1.3.1 Delivery and installation
•Please install the VFD on fire-retardant material and keep the VFD away from
combustible materials.
•Connect the braking optional parts (braking resistors, braking units or feedback
units) according to the wiring diagram.
•Do not operate on the VFD if there is any damage or components loss to the VFD.
•Do not touch the VFD with wet items or body, otherwise electric shock may occur.
•Solid-state motor overload protection is performed when the VFD runs at 150% of
FLA.
•The VFD does not provide motor over-temperature protection.
Note:
•Select appropriate moving and installing tools to ensure a safe and normal running of the VFD and
avoid physical injury or death. For physical safety, the erector should take some mechanical
protective measurements, such as wearing exposure shoes and working uniforms.
•Ensure to avoid physical shock or vibration during delivery and installation.
•Do not carry the VFD by its cover. The cover mayfall off.
•Install away from children and other public places.
•The VFD cannot meet the requirements of low voltage protection in IEC61800-5-1 if the altitude of
the installation site is above 2000m.
•The leakage current of the VFD may be above 3.5mA during operation. Ground with proper
techniques and ensure the grounding resistor is less than 10Ω. The conductivity of PE grounding
conductor is the same as that of the phase conductor (with the same cross sectional area).

TD20 Series VFD Safety Precautions
-3-
•R, S and T are the input terminals of the power supply, while U, V and W are the motor terminals.
Please connect the input power cables and motor cables with proper techniques; otherwise the
damage to the VFD may occur.
1.3.2 Commissioning and running
•Disconnect all power supplies applied to the VFD before the terminal wiring and
wait for at least the designated time after disconnecting the power supply.
•High voltage is present inside the VFD during running. Do not carry out any
operation except for the keypad setting.
•The VFD may start up by itself when P01.21=1. Do not get close to the VFD and
motor.
•The VFD can not be used as "Emergency-stop device".
•The VFD can not be used to break the motor suddenly. A mechanical braking
device should be provided.
Note:
•Do not switch on or off the input power supply of the VFD frequently.
•For VFDs that have been stored for a long time, check and fix the capacitance and try to run it again
before utilization (see Maintenance and Hardware Fault Diagnose).
•Cover the front board before running, otherwise electric shock may occur.
1.3.3 Maintenance and replacement of components
•Only qualified electricians are allowed to perform the maintenance, inspection, and
components replacement of the VFD.
•Disconnect all power supplies to the VFD before the terminal wiring. Wait for at
least the time designated on the VFD after disconnection.
•Take measures to avoid screws, cables and other conductive matters to fall into
the VFD during maintenance and component replacement.
Note:
•Please select proper torque to tighten screws.
•Keep the VFD, parts and components away from combustible materials during maintenance and
component replacement.
•Do not carry out any isolation and pressure test on the VFD and do not measure the control circuit of
the VFD by megameter.
1.3.4 What to do after scrapping
•There are heavy metals in the VFD. Deal with it as industrial effluent.

TD20 Series VFD Product Overview
-4-
2 Product Overview
2.1 Quick start-up
2.1.1 Unpacking inspection
Check as follows after receiving products:
1. Check whether the packing box is damaged or dampened. If yes, contact local dealers or
TECHTOP CANADA INC. offices.
2. Check the model identifier on the exterior surface of the packing box is consistent with the
purchased model. If no, contact local dealers or TECHTOP CANADAINC. offices.
3. Check whether the interior surface of packing box is abnormal, for example, in wet condition, or
whether the enclosure of the VFD is damaged or cracked. If yes, contact local dealers or TECHTOP
CANADA INC. offices.
4. Check whether the nameplate of the VFD is consistent with the model identifier on the exterior
surface of the packing box. If no, contact local dealers or TECHTOP CANADA INC. offices.
5. Check whether the accessories (including user's manual and control keypad) inside the packing
box are complete. If not, please contact with local dealers or TECHTOP CANADA INC. offices.
2.1.2 Application confirmation
Check the machine before beginning to use the VFD:
1. Check the load type to verify that there is no overload of the VFD during work and check whether
the power degree of the VFD needs to be modified.
2. Check that the actual current of the motor is less than the rated current of the VFD.
3. Check that the control accuracy of the load is the same of the VFD.
4. Check that the incoming supply voltage is correspondent to the rated voltage of the VFD.
2.1.3 Environment
Check as follows before the actual installation and usage:
1. Check that the ambient temperature of the VFD is below 40°C . If exceeds, derate 1% for every
additional 1°C . Additionally, the VFD can not be used if the ambient temperature is above 50°C .
Note: For the cabinet VFD, the ambient temperature means the air temperature inside the cabinet.
2. Check that the ambient temperature of the VFD in actual usage is above -10°C . If not, add heating
facilities.
Note: For the cabinet VFD, the ambient temperature means the air temperature inside the cabinet.
3. Check that the altitude of the actual usage site is below 1000m. If exceeds, derate1% for every
additional 100m.
4. Check that the humidity of the actual usage site is below 90% and condensation is not allowed. If
not, add additional protection VFDs.
5. Check that the actual usage site is away from direct sunlight and foreign objects can not enter the
VFD. If not, add additional protective measures.
6. Check that there is no conductive dust or flammable gas in the actual usage site. If not, add

TD20 Series VFD Product Overview
-5-
additional protection to VFDs.
2.1.4 Installation confirmation
Check as follows after the installation:
1. Check that the load range of the input and output cables meet the need of actual load.
2. Check that the accessories of the VFD are correctly and properly installed. The installation cables
should meet the needs of every component (including reactors, input filters, output reactors, output
filters, DC reactors, braking units and braking resistors).
3. Check that the VFD is installed on non-flammable materials and the calorific accessories (reactors
and brake resistors) are away from flammable materials.
4. Check that all control cables and power cables are run separately and the routation complies with
EMC requirement.
5. Check that all grounding systems are properly grounded according to the requirements of the VFD.
6. Check that the free space during installation is sufficient according to the instructions in user's
manual.
7. Check that the installation conforms to the instructions in user's manual. The VFD must be
installed in an upright position.
8. Check that the external connection terminals are tightly fastened and the torque is appropriate.
9. Check that there are no screws, cables and other conductive items left in the VFD. If not, get them
out.
2.1.5 Basic commissioning
Complete the basic commissioning as follows before actual utilization:
1. Autotune. If possible, de-coupled from the motor load to start dynamic autotune. Or if not, static
autotune is available.
2. Adjust theACC/DEC time according to the actual running of the load.
3. Commission the device via jogging and check that the rotation direction is as required. If not,
change the rotation direction by changing the wiring of motor.
4. Set all control parameters and then operate.
2.2 Product specification
Function
Specification
Power
input
Input voltage (V)
Voltage class
Allowable voltage fluctuation
AC 1PH 110V–120V
-10%–+10%
AC 1PH 200V–240V
AC 3PH 200V–240V
AC 3PH 380V–480V
-15%–+10%
Input current (A)
Refer to the rated value
Input frequency (Hz)
50Hz or 60Hz Allowed range: 47–63Hz
Power
Output voltage (V)
0–input voltage

TD20 Series VFD Product Overview
-6-
Function
Specification
output
Output current (A)
Refer to the rated value
Output power (kW)
Refer to the rated value
Output frequency
(Hz)
0–400Hz
Technical
control
feature
Control mode
SVPWM, SVC
Adjustable-speed
ratio
Asynchronous motor 1: 100 (SVC)
Speed control
accuracy
±0.2% (SVC)
Speed fluctuation
±0.3% (SVC)
Torque response
<20ms (SVC)
Torque control
accuracy
10%
Starting torque
0. 5Hz/150% (SVC)
Overload capability
150% of rated current: 1 minute
180% of rated current: 10 seconds
200% of rated current: 1 second
Running
control
feature
Frequency setting
method
Digital setting, analog setting, pulse frequency setting,
multi-step speed running setting, simple PLC setting, PID
setting, MODBUS communication setting
Shift between the set combination and set channel.
Auto-adjustment of
the voltage
Keep a stable voltage automatically when the grid voltage
transients
Fault protection
Provide comprehensive fault protection functions:
overcurrent, overvoltage, undervoltage, overheating, phase
loss and overload, etc.
Peripheral
interface
Analog input
1 input (AI2): 0–10V/0–20mA; 1 input (AI3): -10–10V
Analog output
2 inputs (AO1, AO2): 0–10V/0–20mA
Digital input
4 common inputs, max. frequency: 1kHz;
1 high speed input, max. frequency: 50kHz
Digital output
1 Y1 terminal output; 2 programmable relay outputs
Relay output
2 programmable relay outputs
RO1A NO, RO1B NC, RO1C common terminal
RO2A NO, RO2B NC, RO2C common terminal
Contact capacity: 3A/AC250V
Others
Mountable method
Wall and rail mountable
Temperature of the
running environment
-10–50°C, derate above 40°C
Protective degree
Note:

TD20 Series VFD Product Overview
-7-
Function
Specification
1. The VFD with plastic casing should be installed in metal
distribution cabinet, which conforms to IP20 and of which
the top conforms to IP3X.
2. Install device in pollution degree 2 environment
Cooling
Air-cooling
Braking unit
Embedded
EMI filter
Optional filter: meet the degree requirement of IEC61800-3
C2, IEC61800-3 C3
Safety
Meet the requirements of CE, UL and CUL
Overvoltage category
1PH&3PH 240V: Used in Canada only: "Transient surge
suppression shall be installed on the line side of this
equipment and shall be rated 240V (phase to ground),
240V (phase to phase), suitable for overvoltage category
III, and shall provide protection for a rated impulse
withstand voltage peak of 4kV" or equivalent.
3PH: Used in Canada only: "Transient surge suppression
shall be installed on the line side of this equipment and
shall be rated 480V (phase to ground), 480V (phase to
phase), suitable for overvoltage category III, and shall
provide protection for a rated impulse withstand voltage
peak of 6kV" or equivalent.
2.3 Nameplate
Figure 2-1 Nameplate
2.4 Type designation key
The type designation contains information on the VFD. The user can find the type designation on the
type designation label attached to the VFD or the simple nameplate.
E509291
IND. CONT. EQ
TD20-2R2G-4
2.2 kW/3 HP
AC 3PH 380V–480V 5.8A 50/60 Hz
AC 3PH 0V–Uinput 5.5A 0Hz–400Hz
Techtop Canada Inc. TechtopCanada.com
S/N: Made in China

TD20 Series VFD Product Overview
-8-
TD20 –2R2G –4
①②③
TD Figure 2-2 Product type
Key
No.
Detailed description
Detailed content
Product abbreviation
①
Product abbreviation
TD20
TD20 is short for Topdrive20
Rated power
②
Power range + Load type
2R2—2.2kW
G—Constant torque load
Voltage degree
③
Voltage degree
S1: AC 1PH 110V–120V
S2: AC 1PH 200V–240V
2: AC 3PH 200V–240V
4: AC 3PH 380V–480V
2.5 Rated specifications
Model
Rated
output
power (kW)
Rated
output
horsepower
(HP)
Rated input
current (A)
Rated
output
current (A)
TD20-0R4G-S1
0.4
0.5
8.1
2.5
TD20-0R7G-S1
0.75
1
15.1
4.2
TD20-1R1G-S1
1.1
1.5
20
5.8
TD20-0R4G-S2
0.4
0.5
6.5
2.5
TD20-0R7G-S2
0.75
1
9.3
4.2
TD20-1R5G-S2
1.5
2
15.7
7.5
TD20-2R2G-S2
2.2
3
20
10
TD20-0R4G-2
0.4
0.5
3.7
2.5
TD20-0R7G-2
0.75
1
5.0
4.2
TD20-0R7G-4
0.75
1
3.4
2.5
TD20-1R5G-4
1.5
2
5.0
4.2
TD20-2R2G-4
2.2
3
5.8
5.5
2.6 Structure diagram
Below is the layout figure of the VFD (take the VFD of 0.75kW as the example).

TD20 Series VFD Product Overview
-9-
6
12
8
10
7
3
2
5
1
9
11
4
Figure 2-3 Product structure
Serial No.
Name
Illustration
1
External keypad port
Connect the external keypad
2
Port cover
Protect the external keypad port
3
Cover
Protect the internal parts and components
4
Hole for the sliding cover
Fix the sliding cover
5
Trunking board
Protect the inner components and fix the cables of the
main circuit
6
Nameplate
See Product Overview for detailed information
7
Potentiometer knob
Refer to the Keypad Operation Procedure
8
Control terminals
See Electric Installation for detailed information
9
Main circuit terminals
See Electric Installation for detailed information
10
Screw hole
Fix the fan cover and fan
11
Cooling fan
See Maintenance and Hardware Fault Diagnose for
detailed information
12
Fan cover
Protect the fan
Note: In above figure, the screws at 4 and 10 are provided with packaging and specific installation
depends on the requirements of customers.

TD20 Series VFD Installation Guide
-10-
3 Installation Guide
The chapter describes the mechanical installation and electric installation.
•Only qualified electricians are allowed to carry out what described in this chapter.
Please operate as the instructions in Safety Precautions. Ignoring these may
cause physical injury or death or damage to the devices.
•Ensure the power supply of the VFD is disconnected during the operation. Wait for
at least the time designated after the disconnection if the power supply is applied.
•The installation and design of the VFD should be complied with the requirement of
the local laws and regulations in the installation site. If the installation infringes the
requirement, our company will exempt from any responsibility.Additionally, if users
do not comply with the suggestion, some damage beyond the assured
maintenance range may occur.
3.1 Mechanical installation
3.1.1 Installation environment
The installation environment is the safeguard for a full performance and long-term stable functions of the
VFD. Check the installation environment as follows:
Environment
Conditions
Installation site
Indoor
Environment
temperature
-10°C –+50°C , and the temperature changing rate is less than 0.5°C /minute.
If the ambient temperature of the VFD is above 40°C , derate 1% for every
additional 1°C .
It is not recommended to use the VFD if the ambient temperature is above
50°C .
In order to improve the reliability of the device, do not use the VFD if the
ambient temperature changes frequently.
Please provide cooling fan or air conditioner to control the internal ambient
temperature below the required one if the VFD is used in a close space such as
in the control cabinet.
When the temperature is too low, if the VFD needs to restart to run after a long
stop, it is necessary to provide an external heating device to increase the
internal temperature, otherwise damage to the devices may occur.
Humidity
RH≤90%
No condensation is allowed.
Storage
temperature
-40°C –+70°C , and the temperature changing rate is less than 1°C /minute.
Running
environment
condition
The installation site of the VFD should:
keep away from the electromagnetic radiation source;
keep away from contaminative air, such as corrosive gas, oil mist and

TD20 Series VFD Installation Guide
-11-
Environment
Conditions
flammable gas;
ensure foreign objects, such as metal power, dust, oil, water can not enter into
the VFD (do not install the VFD on the flammable materials such as wood);
keep away from direct sunlight, oil mist, steam and vibration environment.
Altitude
Below 1000m
If the altitude is above 1000m, derate 1% for every additional 100m.
Vibration
≤ 5.8m/s2 (0.6g)
Installation
direction
The VFD should be installed on an upright position to ensure sufficient cooling
effect.
Note:
•TD20 series VFDs should be installed in a clean and ventilated environment according to enclosure
classification.
•Cooling air must be clean, free from corrosive materials and electrically conductive dust.
3.1.2 Installation direction
The VFD may be installed in a cabinet.
The VFD needs be installed in the vertical position. Check the installation site according to the
requirements below. Refer to chapter Dimension Drawings in the appendix for frame details.
3.1.3 Installation manner
The VFD can be installed in two different ways, depending on the frame size:
a) Wall mounting (for all frame sizes)
b) Rail mounting (for all frame sizes, but need optional installation bracket)
Figure 3-1 Wall mounting
Figure 3-2 Rail mounting
Note: The minimum space ofAand B is 100mm. H is 36.6mm and W is 35.0mm.

TD20 Series VFD Installation Guide
-12-
3.2 Standard wiring
3.2.1 Connection diagram of main circuit
R
S
TW
V
U
PE
M
(+) PB
Three-phase
380V~480V
50/60Hz
Brake resistor
Input
reactor
Input
filter
Fuse
Output
reactor
Output
filter
L
NW
V
U
PE
M
(+) PB
Single-phase
200V~240V
50/60Hz
Brake resistor
Input
reactor
Input
filter
Fuse
Output
reactor
Output
filter
Figure 3-3 Connection diagram of main circuit
Note:
•The fuse, braking resistor, input reactor, input filter, output reactor, output filter are optional parts.
Please refer to Peripheral Optional Parts for detailed information.
•Remove the yellow warning labels of PB, (+) and (-) on the terminals before connecting the braking
resistor; otherwise, poor connection may occur.
3.2.2 Terminals figure of main circuit
Figure 3-4 1PH terminals of main circuit
Terminal
Terminal name
Function
L
Power input of the main circuit
1-phase AC input terminals which are generally
connected with the power supply.
N
U
The VFD output
3-phase AC output terminals which are generally
connected with the motor.
V
W
PB, (+)
Braking resistor terminal
PB and (+) are connected to the external resistor.

TD20 Series VFD Installation Guide
-13-
Terminal
Terminal name
Function
PE
Grounding terminal
Each machine should be grounded.
Figure 3-5 3PH terminals of main circuit
Terminal
Terminal name
Function
R, S, T
Power input of the main circuit
3-phase AC input terminals which are generally
connected with the power supply.
U, V, W
The VFD output
3-phase AC output terminals which are generally
connected with the motor.
PB, (+)
Braking resistor terminal
PB and (+) are connected to the external resistor.
PE
Grounding terminal
Each machine should be grounded.
Note:
•Do not use asymmetrically motor cables. If there isa symmetrically grounding conductor in the motor
cable in addition to the conductive shield, connect the grounding conductor to the grounding terminal
at the VFD and motor ends.
•Route the motor cable, input power cable and control cables separately.
•When selecting C3 input filters, connect the filters in parallel at the input side of the VFD.
3.2.3 Wiring of terminals in main circuit
1. Connect the ground line of input power cable to the ground terminal of VFD (PE) directly, and
connect 3PH input cable to R, S and T and fasten up.
2. Connect the ground line of motor cable to the ground terminal of the VFD, and connect the 3PH
motor cable to U, V, W and fasten up.
3. Connect the brake resistor which carries cables to the designated position.
4. Fasten up all the cables on the outside of the VFD if allowed.

TD20 Series VFD Installation Guide
-14-
3.2.4 Wiring diagram of control circuit
Multi-function input terminal 1
Multi-function input terminal 2
Multi-function input terminal 4
High speed pulse input collector
Multi-function input terminal 3
Open collector input optional
Y1 output
Analog output
Analog output
Relay 1 output
Relay 2 output
S1
S2
S3
S4
HDI
COM
PW
+24V
PE
+10V
AI2
AI3
PE
GND
AI2
V I
Y1
COM
AO1
AO2
V I
VI
AO1
AO2
0–10V/0–20mA
0–10V/0–20mA
COM
COM
485 485+
485-
RO1A
RO1B
RO1C
RO2A
RO2B
RO2C
Figure 3-6 Wiring of control circuit
3.2.5 Terminals of control circuit
ON
GND
Figure 3-7 Terminals of control circuit
Type
Terminal
name
Function
description
Technical specifications
Communication
485+
485
communication
485 communication interface
485-
Digital
input/output
S1
Digital input
1. Internal impedance: 3.3kΩ
2. 12–30V voltage input is available
3. The terminal is the dual-direction
input terminal
4. Max. input frequency: 1kHz
S2
S3
S4
HDI
High frequency
input channel
Except for S1–S4, this terminal can
be used as high frequency input
channel.
Max. inputfrequency: 50kHz
Duty cycle: 30%–70%
PW
Digital power
supply
To provide the external digital power
supply
Voltage range: 12–30V

TD20 Series VFD Installation Guide
-15-
Type
Terminal
name
Function
description
Technical specifications
Y1
Digital output
Contact capacity: 50mA/30V
COM
Common terminal of the open
collector output
Analog
input/output
+10V
External 10V
reference power
supply
10V reference power supply
Max. output current: 50mA
As the adjusting power supply of the
external potentiometer
Potentiometer resistance: 5kΩ
above
AI2
Analog input
1. Input range:AI2 voltage and
current can be chosen:
0–10V/0–20mA; AI3: -10V–+10V.
2. Input impedance:voltage input:
20kΩ; current input: 500Ω.
3.Voltage or current input can be
set by dip switch.
4. Resolution: the minimum AI2/AI3
is 10mV/20mV when 10V
corresponds to 60Hz.
AI3
GND
Analog reference
ground
Analog reference ground
AO1
Analog output
1. Output range: 0–10V or 0–20mA
2. The voltage or the current output
is depended on the dip switch.
3. Deviation±1%, 25°C when full
range.
AO2
Relay output
RO1A
Relay 1 NO
contact
RO1 relay output, RO1A NO, RO1B
NC, RO1C common terminal
RO2 relay output, RO2A NO, RO2B
NC, RO2C common terminal
Contact capacity: 3A/AC250V
RO1B
Relay 1 NC contact
RO1C
Relay 1 common
contact
RO2A
Relay 2 NO
contact
RO2B
Relay 2 NC contact
RO2C
Relay 2 common
contact
3.2.6 Input/Output signal connection figure
Please use U-shaped contact tag to set NPN mode or PNP mode and the internal or external power

TD20 Series VFD Installation Guide
-16-
supply. The default setting is NPN internal mode.
U-shaped contact
tag between
+24V and PW
U-shaped contact
tag between
COM and CME
Figure 3-8 U-shaped contact tag
If the signal is from NPN transistor, please set the U-shaped contact tag between +24V and PW as
below according to the used power supply.
S1
S2
COM
PW
+24V
COM
+24V
S1
S2
COM
PW
+24V
COM
+24V
+24V
Figure 3-9 NPN modes
If the signal is from PNP transistor, please set the U-shaped contact tag as below according to the used
power supply.
S1
S2
COM
PW
+24V
COM
+24V
S1
S2
COM
PW
+24V
COM
+24V
Figure 3-10 PNP modes
3.3 Layout protection
3.3.1 Protecting the VFD and input power cable in short-circuit situations
Protect the VFD and input power cable in short circuit situations and against thermal overload.
Arrange the protection according to the following guide.

TD20 Series VFD Installation Guide
-17-
Input cable
VFD
Fuse
Figure 3-11 Fuse configuration
Note: Select the fuse as the manual indicated. The fuse will protect the input power cable from damage
in short-circuit situations. It will protect the surrounding devices when the internal of the VFD is short
circuited.
3.3.2 Protecting the motor and motor cables
The VFD protects the motor and motor cable in a short-circuit situation when the motor cable is
dimensioned according to the rated current of the VFD. No additional protection devices are needed.
•If the VFD is connected to multiple motors, a separate thermal overload
switch or a circuit breaker must be used for protecting each cable and
motor. These devices may require a separate fuse to cut off the short-circuit
current.
3.3.3 Implementing a bypass connection
It is necessary to set power frequency and variable frequency conversion circuits for the assurance of
continuous normal work of the VFD if faults occur in some significant situations.
In some special situations, for example, if it is only used in soft start, the VFD can be conversed into
power frequency running after starting and some corresponding bypass should be added.
•Never connect the supply power to the VFD output terminals U, V and W.
Power line voltage applied to the output can result in permanent damage to
the VFD.
If frequent shifting is required, employ mechanically connected switches or contactors to ensure that the
motor terminals are not connected to theAC power line and VFD output terminals simultaneously.

TD20 Series VFD Keypad Operation Procedure
-18-
4 Keypad Operation Procedure
4.1 Keypad introduction
The keypad is used to control TD20 series VFDs, read the state data and adjust parameters.
Figure 4-1 Keypad
Note: The external keypads are optional (including the external keypads with and without the function of
parameter copying).
Serial
No.
Name
Description
1
State LED
RUN/TUNE
LED off means that the VFD is in the stopping
state; LED blinking means the VFD is in the
parameter autotune state; LED on means the VFD
is in the running state.
FWD/REV
FED/REV LED
LED off means the VFD is in the forward rotation
state; LED on means the VFD is in the reverse
rotation state
LOCAL/REMOT
LED for keypad operation, terminals operation and
remote communication control
LED off means that the VFD is in the keypad
operation state; LED blinking means the VFD is in
the terminals operation state; LED on means the
VFD is in the remote communication control state.
TRIP
LED for faults
1
2
3
4
5
6
This manual suits for next models
11
Table of contents
Other TECHTOP DC Drive manuals
Popular DC Drive manuals by other brands
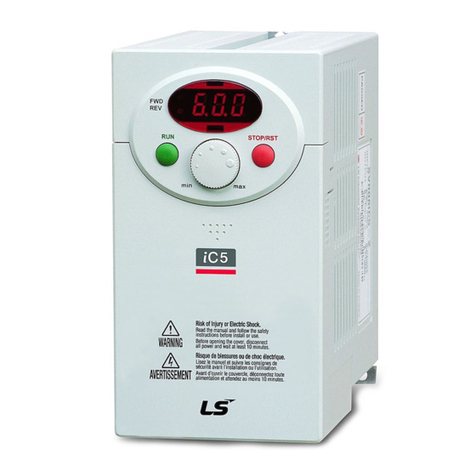
LSIS
LSIS SV008iC5-1F manual

Hubbell
Hubbell Universal Hose Reel-Chain Drive UH28 Installation and maintenance instructions
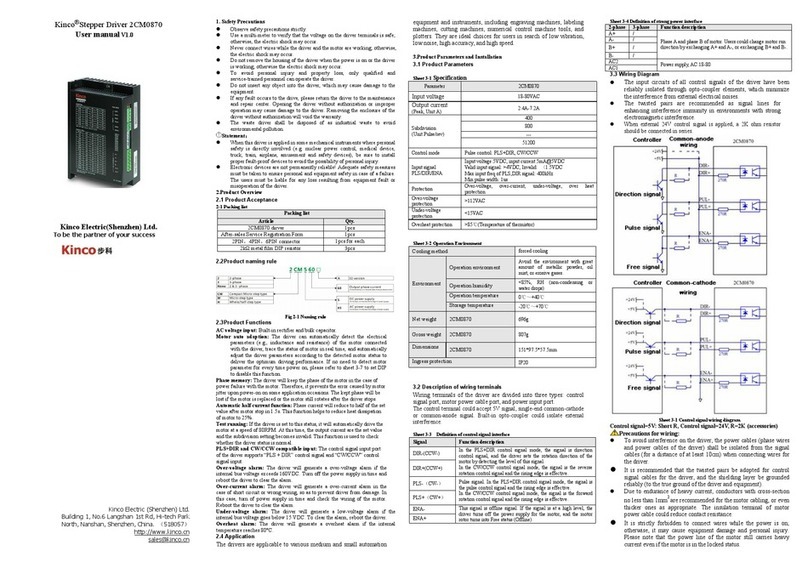
Kinco
Kinco 2CM0870 user manual

GFA
GFA ELEKTROMAT SI 55.10-40,00 installation instructions
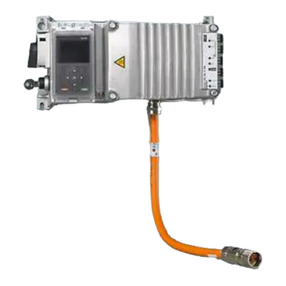
SEW-Eurodrive
SEW-Eurodrive MOVIMOT flexible MMF1 C/DBC Series operating instructions

YASKAWA
YASKAWA V1000 MMD quick start guide