Timotion JP3 User manual

User Manual-JP3
Version C May 2020
1 of 20
1
A
User Manual
JP3

User Manual-JP3
Version C May 2020
2 of 20
2
Contents
Contents .....................................................................................................................................................................2
Glossary .....................................................................................................................................................................3
1. General.................................................................................................................................................................4
About this manual ................................................................................................................................................................... 41.1
Target Personnel ..................................................................................................................................................................... 41.2
Warranty.................................................................................................................................................................................... 41.3
Transport and storage............................................................................................................................................................ 41.4
Packaging ................................................................................................................................................................................. 51.5
Support ...................................................................................................................................................................................... 51.6
Disclaimer ................................................................................................................................................................................. 51.7
Notification and warnings...................................................................................................................................................... 51.8
1.8.1 Mounting/dismounting the actuator...................................................................................................................... 5
1.8.2 Operation..................................................................................................................................................................... 6
1.8.3 Equipment power off ................................................................................................................................................ 6
1.8.4 Duty cycle.................................................................................................................................................................... 6
1.8.5 Temperature............................................................................................................................................................... 6
2. Installation ...........................................................................................................................................................7
Mechanical installation........................................................................................................................................................... 72.1
2.1.1 Mounting notice ......................................................................................................................................................... 7
Electrical installation ............................................................................................................................................................... 82.2
2.2.1 Important notice ........................................................................................................................................................ 8
2.2.2 Cable ............................................................................................................................................................................ 9
2.2.3 Inrush current ...........................................................................................................................................................10
Wiring definitions...................................................................................................................................................................112.3
2.3.1 Limitations for limit switches / output signals ..................................................................................................11
2.3.2 Two limit switches to cut the current (without signal output) ........................................................................12
2.3.3 Two limit switches to cut the current and an additional limit switch for signal output .............................13
2.3.4 Two limit switches send the signal and an additional limit switch sends a signal at specific stroke
positions..................................................................................................................................................................................14
2.3.5 Two limit switches send the signal output .........................................................................................................15
2.3.6 Two limit switches and a single Hall sensor ......................................................................................................16
2.3.7 Two limit switches and double Hall sensors......................................................................................................17
3. Product specifications........................................................................................................................................18
2D drawings............................................................................................................................................................................183.1
Ordering key............................................................................................................................................................................193.2
4. Troubleshooting .................................................................................................................................................20

User Manual-JP3
Version C May 2020
3 of 20
3
Glossary
The following terms and acronyms are being used in this manual.
Vm+: The positive pole of power input.
Vm-: The negative pole of power input.
RPM: Number of turns per minute.
AWG: American wiring gauge.
LS: Limit switch installed inside the outer tube.
Up LS: Upper limit switch is installed in fully extended end of stroke.
Low LS: Lower limit switch is installed in fully retracted end of stroke.
Mid LS: Middle limit switch is installed and the position is set by customer’s request.
N.C.: It is the pin of limit switch which is normally short circuit and changed to open when the switch is
triggered.
N.O.: It is the pin of limit switch which is normal open and changed to short circuit when the switch is
triggered.
C.: It is the common pin of limit switch when the circuit is either open or short.
Vp: The reference voltage input to POT signal.
Vout: The POT signal wire output value.

User Manual-JP3
Version C May 2020
4 of 20
4
1.General
About this manual1.1
This user manual is provided to the manufacturer of the equipment or system rather than end users. This
manual provides information needed to install, use and maintain the TiMOTION products. Manufacturers are
responsible to provide a user guide to the end users using the relevant safety information passed from this
manual.
This manual contains installation directions as well as technical data for the TiMOTION industrial electric
linear actuators. Carefully read through each section of the user manual before the equipment is unpacked,
installed or operated. Please note all the dangers, warnings, cautions and notes stated in this manual. Please
follow the instructions provided in this manual to ensure safe reliable operation.
Target Personnel1.2
Please allow qualified mechanical and electrical professionals perform all installation, maintenance and
replacement of the TiMOTION products. Please keep the products away from people who do not have the
required experiences or knowledge of the product.
Warranty1.3
In general, TiMOTION provides a 24 month warranty on Industrial Motion actuators based on the
manufacturing date. The warranty is valid only if the equipment is properly operated and maintained correctly.
The application of the product is the responsibility of the buyer. TiMOTION makes no representation or
warranty as to the suitability of the product for any particular use or purpose.
Transport and storage1.4
The actuator should only be stored and transported in the original TiMOTION packaging. The temperature
during transportation and storage must be between -40 to +85°C (-40 to +185°F). Please avoid shocks to
the package. If the package is damaged, check the actuator for visible damage and notify the carrier and
TiMOTION.

User Manual-JP3
Version C May 2020
5 of 20
5
Packaging1.5
The sample order packaging contains the product and this manual. For large quantity orders, packaging may
vary and TiMOTION reserves the right to change it.
Support1.6
If any technical support or information is needed for this product, please contact your TiMOTION sales
engineer. You can also visit https://www.TiMOTION.com/en for the product or contact information.
Disclaimer1.7
This user manual has been written based on our current technical knowledge. TiMOTION is constantly
working on updating the product information. We reserve the right to carry out technical modifications.
Notification and warnings1.8
1.8.1 Mounting/dismounting the actuator
Please read through this user manual before working on the equipment that the actuator is or shall be a
part of.
Adhere to the information contained in this user manual and on the product label. Never exceed the
performance limits stated herein.
Be sure the actuator is not in operation.
Ensure the actuator is free from loads that could be released during mounting or dismounting.
Refrain from unplugging any cables or connectors during operation or with power on.
Immediately stop using the actuator if it seems faulty or damaged. Notify your TiMOTION sales
engineer so corrective actions can be taken.
Never disassemble the actuator, as that will compromise the sealing and could impact the function of
the actuator. Disassembly voids warranty.
Grease may be present on the extension tube. Contact with the grease is non-hazardous. Please refrain
from removing the film.

User Manual-JP3
Version C May 2020
6 of 20
6
1.8.2 Operation
Be sure the actuator is correctly mounted as indicated in the user instructions.
Be sure the equipment can be moved easily over the actuator’s whole working area.
Be sure the actuator is connected to a main electricity supply/transformer with the correct voltage,
specified on the actuator label.
Be sure that the connection bolts are secured safely and can withstand the wear.
Stop the actuator immediately if anything unusual is observed.
Ensure there is no side load present on the actuator.
Only use the actuator within the specified working limits.
Refrain from having any contact with the actuator.
1.8.3 Equipment power off
Switch off the main supply to prevent any unintentional operation.
Regularly check for extraordinary wear.
1.8.4 Duty cycle
The standard duty cycle is 10%.
If the product is customized, please refer to the approval drawings.
1.8.5 Temperature
The operating temperature range is +5°C ~+65°C.
The operational temperature range at full performance is +5°C ~+45°C.

User Manual-JP3
Version C May 2020
7 of 20
7
XX
2.Installation
Mechanical installation2.1
2.1.1 Mounting notice
Use solid mounting pins with the proper dimension and support them at both ends.
Note
Correct
Wrong
Please mount the actuator with
the mounting pins of correct
dimension and without threaded at
both ends of the attachments.
Do not mount the actuator with
the pins in different rotated angles,
this could cause stress on the nut
during operation.
The load should act along the
stroke axis of the actuator from
the front attachment, inner tube to
the rear attachment. Off center or
side loads may cause bending and
lead to failure.
Be sure the mounting pins must
be parallel to each other. If the
pins are not parallel to each other
the actuator might be bend and
could be damaged.
XY

User Manual-JP3
Version C May 2020
8 of 20
8
Electrical installation2.2
2.2.1 Important notice
Make sure the leads/cables leading to the motor are rated to handle the maximum current.
To reduce the chance of a crushing hazard, we recommend an emergency stop.
If you are not using soft stop on a DC-motor, a short peak of high voltage will be sent towards the power
supply. When selecting the power supply, please ensure it is able to withstand the peak of high voltage.
To reduce the chance of interference, refrain from placing signal cables along power cables.
Use a two-wire system to prevent ground loop.
Please use shielded signal cables with applications that can be sensitive or if there is interference risk.
Please note, using long cables in combination with small lead cross sections and low voltages could
lead to a malfunction due to voltage drop.
Use spark protection on relays and other coil operated devices.
Please be sure the power to the actuator is off before working on the actuator and the wiring.

User Manual-JP3
Version C May 2020
9 of 20
9
2.2.2 Cable
The actuator is supplied with a power cable (and/or signal cable). The standard cable, for industrial
applications, has/have flying leads in the end for the user’s equipment connections.
*Please refer to the approval drawing of any customized cable/connector.
Cable without signal:
Cable with signal:
Φ1.5mm
mm
Φ4.6mm
mm
Power cable: 20AWG
Power cable: 20AWG
Power cable: 26AWG
Φ1.5mm
mm
Φ5.0mm
mm
Φ1.0mm
mm

User Manual-JP3
Version C May 2020
10 of 20
10
2.2.3 Inrush current
When the actuator starts to work, there is an inrush current to the motor that will be less than 0.2 seconds
(up to four times the rated current).
Please select a power supply that is able to withstand the inrush current. Also, all contacts, including
switches and relays, should be selected with caution.

User Manual-JP3
Version C May 2020
11 of 20
11
Wiring definitions2.3
Shown below are the standard wiring definitions of the actuator. If your actuator is ordered with customized
wiring, please contact TiMOTION sales for detailed information.
2.3.1 Limitations for limit switches / output signals
In general, the JP3 cable can have a maximum of 6 pins–(2 power wire pins and/or up to 4 signal wire pins)
The function limitations for limit switches to output signals are shown in the table below:
Functions for limit switches
Signal output
Without
POT
Single Hall
Double Hall
2 limit switches to cut the current
OK
2.3.2
OK
2.3.8
OK
2.3.6
OK
2.3.7
2 limit switches to cut the current
one additional limit switch for signal output
OK
2.3.3
x
x
x
2 limit switches for signal output
OK
2.3.5
x
x
x
2 limit switches for signal output
one additional limit switch for signal output
OK
2.3.4
x
x
x
* OK = Selectable
** x = Not Compatible
Note:
Please contact the TiMOTION sales engineer if the signal outputs are customized.

User Manual-JP3
Version C May 2020
12 of 20
12
2.3.2 Two limit switches to cut the current (without signal output)
The actuator is equipped with two limit switches to cut the current of the motor when the actuator moves to
the end of each stroke and without any output signal.
Wire
AWG
Description
Spec
Yellow
20
Connect to Vm+ to extend the actuator.
Connect to Vm- to retract the actuator.
24V version: Input voltage 18~32 V DC.
12V version: Input voltage 9~16 V DC.
Green
20
Connect to Vm- to extend the actuator.
Connect to Vm+ to retract the actuator.
Yellow
Green

User Manual-JP3
Version C May 2020
13 of 20
13
2.3.3 Two limit switches to cut the current and an additional limit switch for
signal output
The actuator is equipped with two limit switches to cut the current of the motor when the actuator moves to
the end of each stroke, and an additional limit switch sends out the signal at specific stroke positions.
Wire
AWG
Description
Spec
Yellow
20
Connect to Vm+ to extend the actuator.
Connect to Vm- to retract the actuator.
24V version: Input voltage 18~32 V DC.
12V version: Input voltage 9~16 V DC.
Green
20
Connect to Vm- to extend the actuator.
Connect to Vm+ to retract the actuator.
White
26
Connect to common pin (C.)
The signal is potential free and independent
from the motor power circuit.
The signal is short circuit when the actuator
moves to the position where the middle
limit switch is triggered.
The middle limit switch is installed at the
position upon customer’s request and
physically preset in factory which is not
adjustable. The middle limit switch, installed
in position by customer request, is factory
preset and non-adjustable.
Connect the middle limit switch signal with
max 32V, <1A.
Black
26
Connect to normal closed pin (N.C.)
Yellow
Green
Red
Black

User Manual-JP3
Version C May 2020
14 of 20
14
2.3.4 Two limit switches send the signal and an additional limit switch sends
a signal at specific stroke positions
The actuator is equipped with two limit switches at the end of the strokes. When the actuator moves to the
end of each stroke, each limit switch sends out the end of stroke voltage signal and an additional limit switch
sends out the signal at specific stroke positions.
Wire
AWG
Description
Spec
Yellow
20
Connect to Vm+ to extend the actuator.
Connect to Vm- to retract the actuator.
24V version: Input voltage 18~32 V DC.
12V version: Input voltage 9~16 V DC.
Green
20
Connect to Vm- to extend the actuator.
Connect to Vm+ to retract the actuator.
Red
26
Connect to common pin (C.)
The signal, NOT potential free, actively
outputs voltage at the end of each stroke
and when the actuator moves to the position
where the middle limit switch is triggered.
Both the white and blue signal wires are a
normal closed circuit when the actuator is in
the middle of the stroke.
The middle limit switch, installed in position
by customer request, is factory preset and
non-adjustable
Connect the middle limit switch signal with
max 32V, <1A.
White
26
Connect to up limit switch normal closed
pin (N.C.)
Blue
26
Connect to low limit switch normal closed
pin (N.C.)
Black
26
Connect to middle limit switch normal
closed pin (N.C.)
Yellow
Green
Red
White
Blue
Black

User Manual-JP3
Version C May 2020
15 of 20
15
2.3.5 Two limit switches send the signal output
The actuator is equipped with two limit switches. When the actuator moves to the end of each stroke, each
limit switch sends out the end of stroke voltage signal at the same time.
Wire
AWG
Description
Spec
Yellow
20
Connect to Vm+ to extend the actuator
Connect to Vm- to retract the actuator
24V version: Input voltage 18~32 V DC
12V version: Input voltage 9~16 V DC
Green
20
Connect to Vm- to extend the actuator
Connect to Vm+ to retract the actuator
Red
26
Connect to common pin (C.)
The signal is potential free and
independent from the motor power circuit.
The signal is short circuit when the
actuator moves to each end of stroke.
Connect the limit switches signal with
max 32V, <1A.
White
26
Connect to up limit switch normal closed
pin (N.C.)
Blue
26
Connect to low limit switch normal closed
pin (N.C.)
Yellow
Green
Red
White
Blue

User Manual-JP3
Version C May 2020
16 of 20
16
2.3.6 Two limit switches and a single Hall sensor
The actuator is equipped with two limit switches to cut the current of the motor when the actuator moves to
the end of each stroke, and with a single Hall sensor sending position signal output.
Wire
AWG
Description
Spec
Yellow
20
Connect to Vm+ to extend the actuator
Connect to Vm- to retract the actuator
24V version: Input voltage 18~32 V DC
12V version: Input voltage 9~16 V DC
Green
20
Connect to Vm- to extend the actuator
Connect to Vm+ to retract the actuator
Red
26
+5V DC input signal power for Hall sensor
board.
Hall sensor output signal type is square
wave with Hi voltage 5V and Low voltage
0V, and with the output current of 0.1A
(please refer to the approval drawing for the
resolution and details).
Hall sensor circuit is independent to motor
power circuit.
White
26
Output Hall sensor signal during the
actuator moves.
Black
26
Hall sensor signal ground.
Yellow
Green
Red
White
Black

User Manual-JP3
Version C May 2020
17 of 20
17
2.3.7 Two limit switches and double Hall sensors
The actuator is equipped with two limit switches to cut the current of the motor when the actuator moves to
the end of each stroke, and with double Hall sensors sending position signal output.
Wire
AWG
Description
Spec
Yellow
20
Connect to Vm+ to extend the actuator
Connect to Vm- to retract the actuator
24V version: Input voltage 18~32 V DC
12V version: Input voltage 9~16 V DC
Green
20
Connect to Vm- to extend the actuator
Connect to Vm+ to retract the actuator
Red
26
+5V DC input signal power for Hall sensor
board.
Hall sensor output signal type is square
wave with Hi voltage 5V and Low voltage
0V, and with the output current of 0.1A
(please refer to the approval drawing for the
resolution and details).
S1 leads 90 degrees’ phase to S2.
Hall sensor circuit is independent to motor
power circuit.
White
26
Output Hall sensor signal S1 during the
actuator moves.
Blue
26
Output Hall sensor signal S2 during the
actuator moves.
Black
26
Hall sensor signal ground.
Yellow
Green
Red
White
Blue
Black
S1
S2

User Manual-JP3
Version C May 2020
18 of 20
18
3.Product specifications
2D drawings3.1

User Manual-JP3
Version C May 2020
19 of 20
19
Ordering key3.2
*Please contact your TiMOTION sales engineer for the latest revision ordering key.

User Manual-JP3
Version C May 2020
20 of 20
20
4.Troubleshooting
Please find the table which lists the symptoms, possible cause and recommend action.
If the problem could not be solved, please contact your TiMOTION sales engineer.
Symptom
Possible cause
Action
Motor runs but spindle does not
move
Gearing system or spindle
damaged
Please contact your TiMOTION sales
engineer.
No motor sound or movement
The actuator is not properly
connected to the power
supply
Check the connection to the power
supply or the external control unit
Customer fuse burned
Check the fuse
Cable damaged
Please contact your TiMOTION sales
engineer.
Excessive power consumption
Misalignment or overload in
the application
Align or reduce the load
Try running the actuator without load
Actuator cannot lift full load or
motor runs too slowly
Insufficient power supply
Check the power supply is properly
plugged in
Load is higher than specified
Reduce the load
No signal or incorrect feedback
output
Cable damaged
Please contact your TiMOTION sales
engineer.
Wrongly connected
Check the wiring
Signal is constantly high/low
Run the actuator to full extension and
retraction
Reconnect the cables and set parallel
configuration again
Table of contents
Other Timotion Controllers manuals
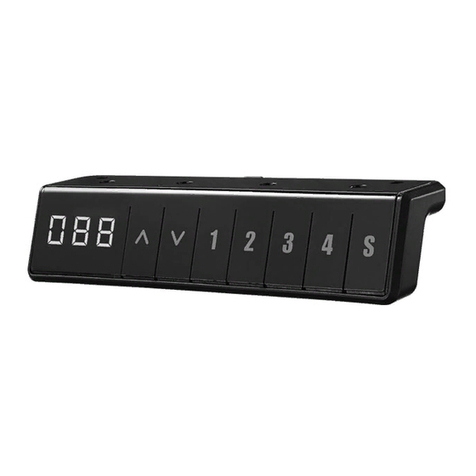
Timotion
Timotion TDH6 User manual
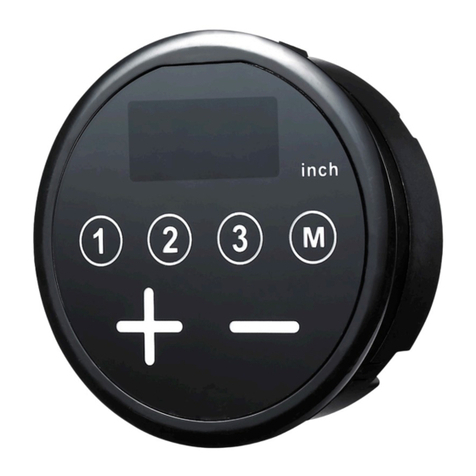
Timotion
Timotion TDH2 User manual
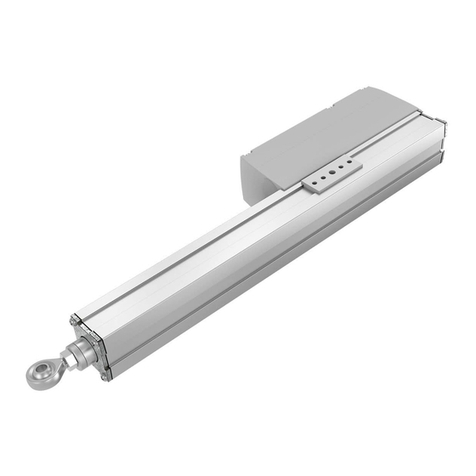
Timotion
Timotion VN1 User manual
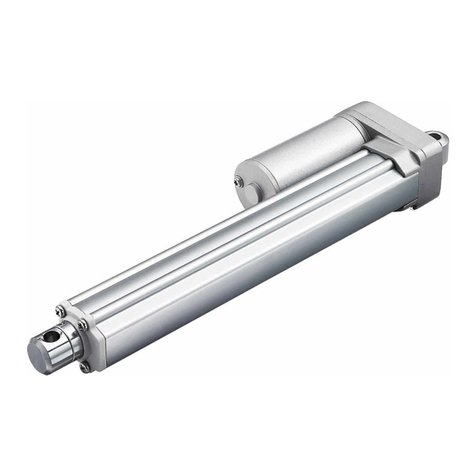
Timotion
Timotion TA2P User manual
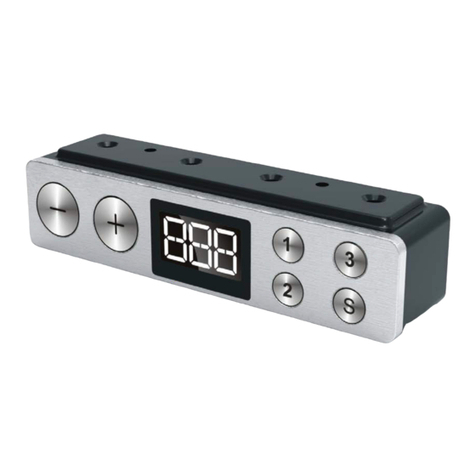
Timotion
Timotion ADJUSTME TDH3 User manual
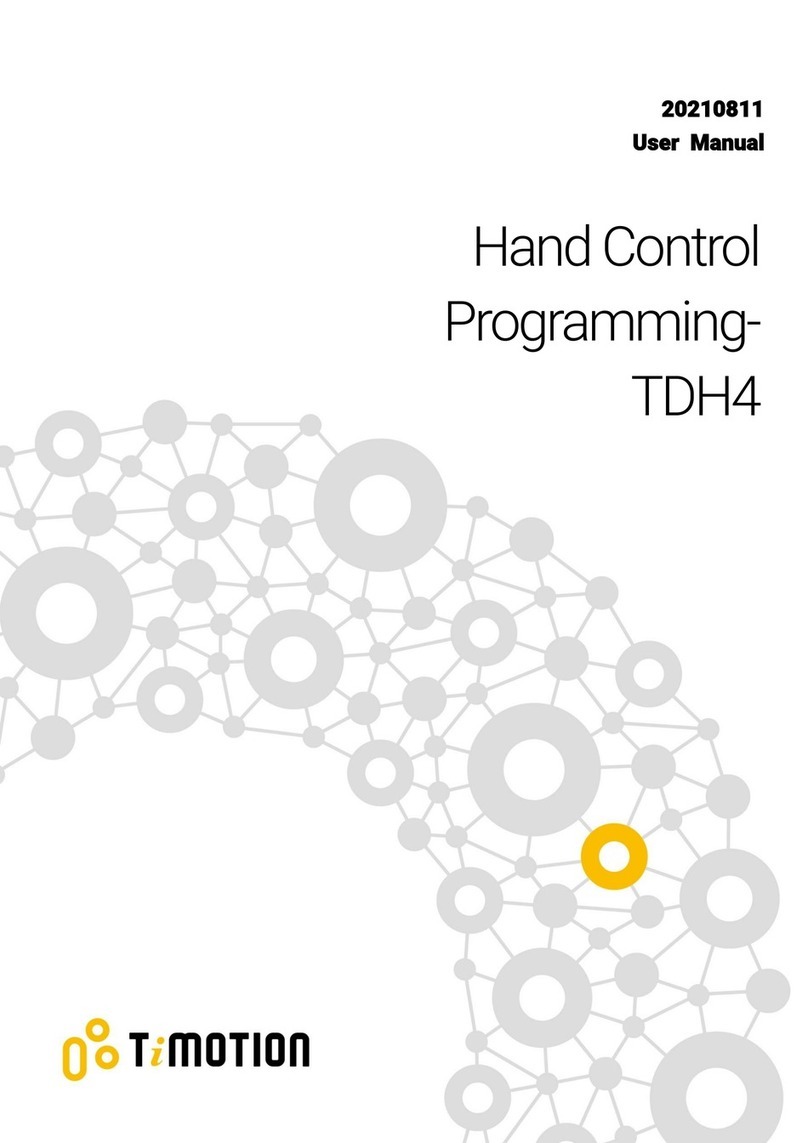
Timotion
Timotion TDH4 User manual
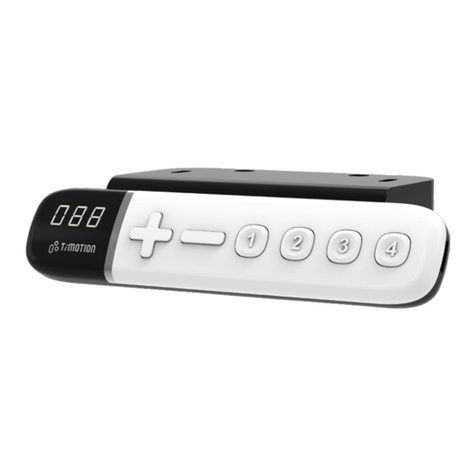
Timotion
Timotion TDH13P User manual
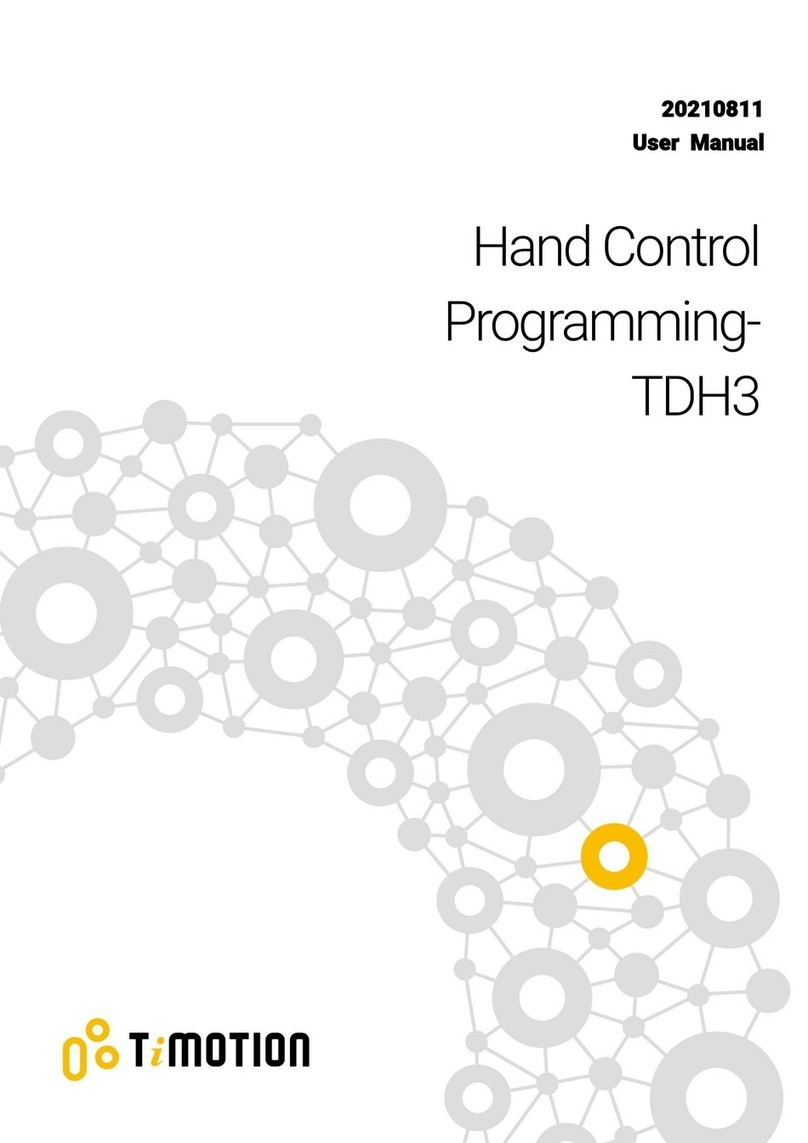
Timotion
Timotion ADJUSTME TDH3 User manual
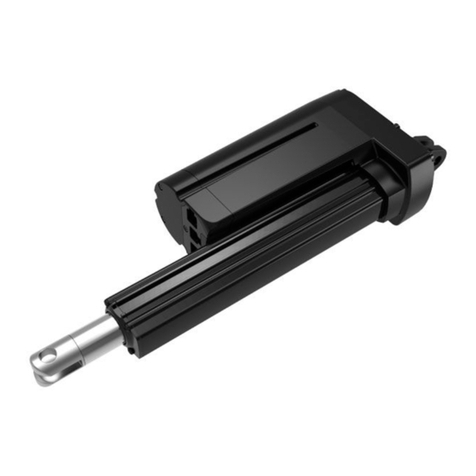
Timotion
Timotion MA2T User manual
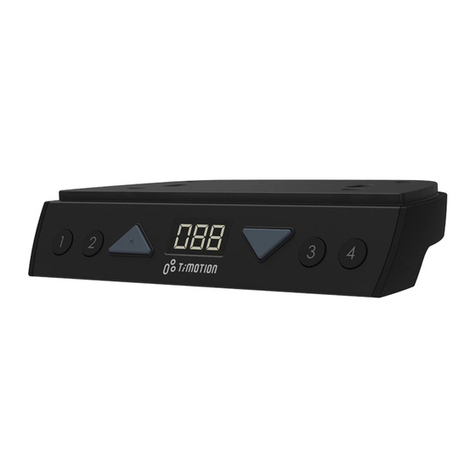
Timotion
Timotion TDH5PR User manual
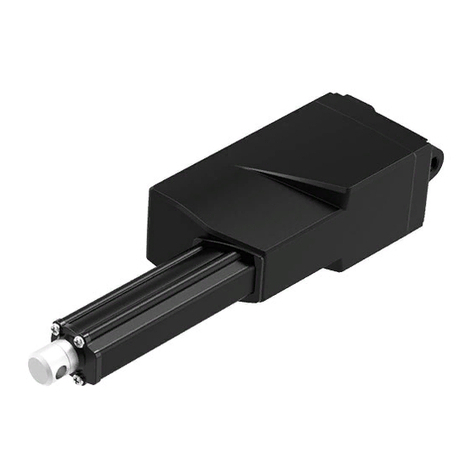
Timotion
Timotion MA5 User manual
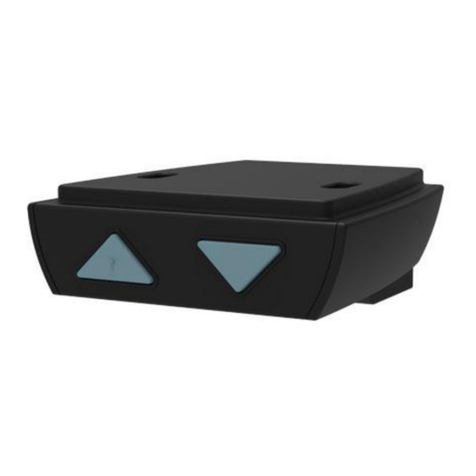
Timotion
Timotion TDH15 User manual
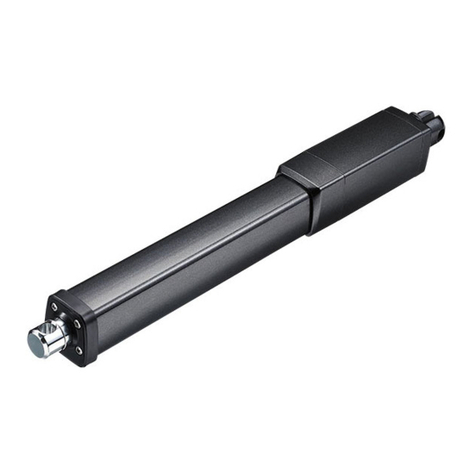
Timotion
Timotion JP4 User manual
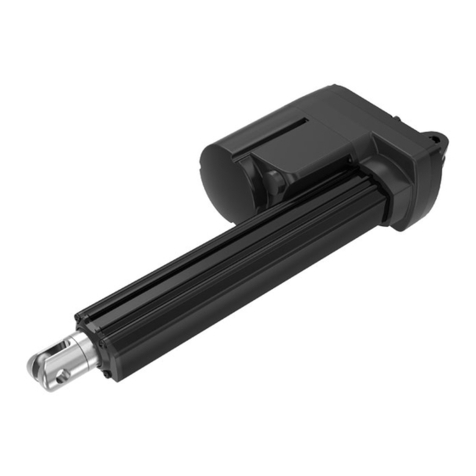
Timotion
Timotion MA2 User manual
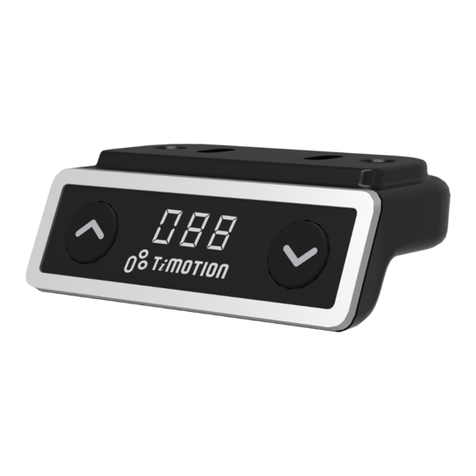
Timotion
Timotion TDH8D User manual
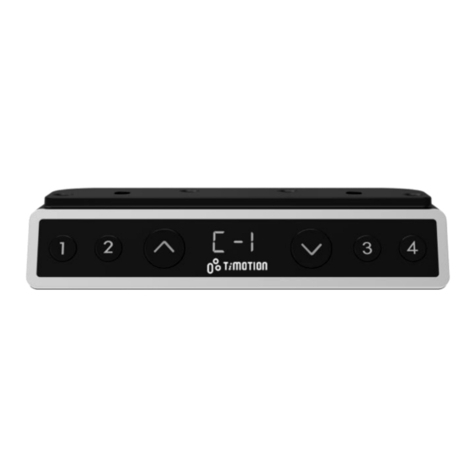
Timotion
Timotion TDH8P User manual
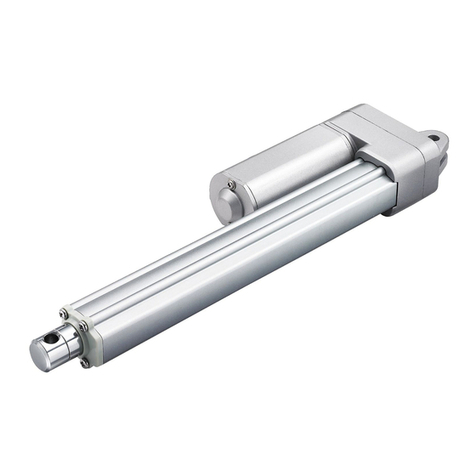
Timotion
Timotion TA16 User manual
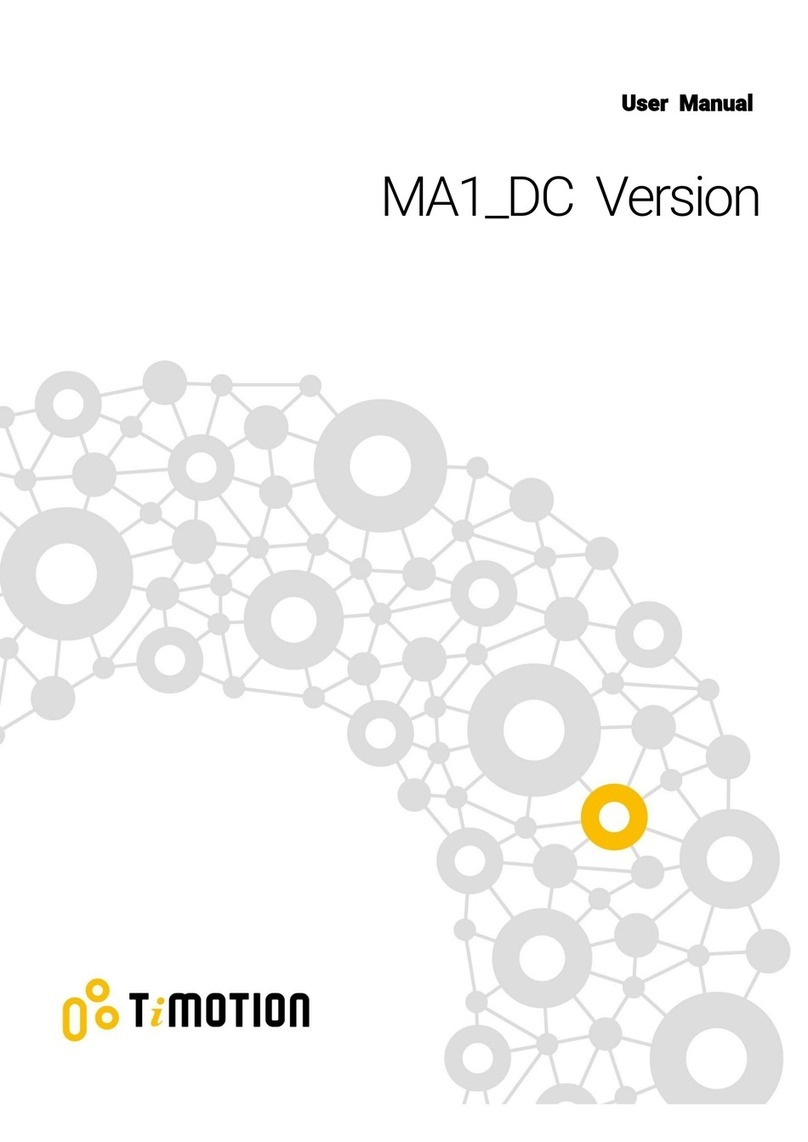
Timotion
Timotion MA1_DC User manual
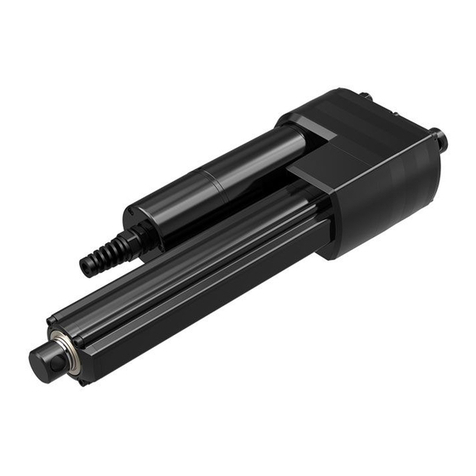
Timotion
Timotion MA1_AC User manual
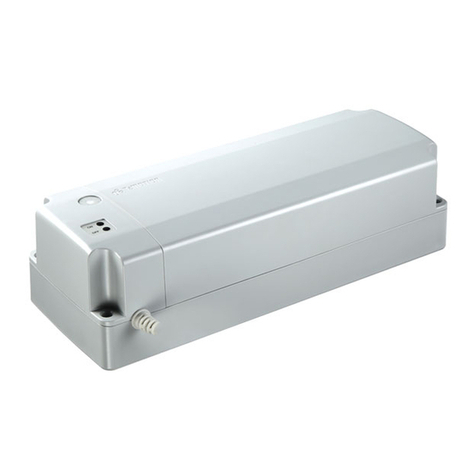
Timotion
Timotion TBB6 User manual