TOPTEK TOPVERT E1 Series User manual

ISO 9001:2008
TOPTEK ELECTRONICS CORPORATION
QUICK START
快速安裝手冊
全功能泛用經濟型 無感電流向量控制 變頻器
High performance general purpose compact drive
Sensorless Vector Controlled AC drive


TOPVERT E1Series
E-
1
Thank you for choosing TOPTEK’S TOPVERT E1 Series Drive. TOPVERT E1 Series are Sensorless
current vector control high-performance drive. They were manufactured by adopting high-quality
components, material and incorporating the latest microprocessor technology available.
Copyright statement
All information in this Quick start manual are Toptek’s intellectual property. Even we had done our best
to make this manual but is unable to guarantee 100% correct.
Based on " Never Stop for better but perfect accomplished " quality policy, our product permanently
in the journey which perfectly strives for perfection to the pursue,
Therefore we reserve the right to change the information in this manual without prior notice.
But we will continue the latest edition document in our website, for free download.
http://www.toptek.biz
Getting Started
This manual will be helpful in the installation, parameter setting, troubleshooting, and daily
maintenance of the drives. To guarantee safe operation of the equipment, read the following safety
guidelines before connecting power to the Drives. Keep this operating manual handy and distribute to
all users for reference.
Always read this manual thoroughly before using TOPVERT E1 Series Drives.
DANGER! AC input power must be disconnected before any maintenance.
Do not connect or disconnect wires and connectors while power is applied to the
circuit. Maintenance must be performed by qualified technicians.
CAUTION! There are highly sensitive MOS components on the printed circuit boards. These
components are especially sensitive to static electricity.
To avoid damage to these components, do not touch these components or the circuit
boards with metal objects or your bare hands.
DANGER! A charge may still remain in the DC-link capacitor with voltages even if the power has
been turned off.
To avoid personal injury, please ensure that power has turned off before operating
Drive and wait ten minutes for capacitors to discharge to safe voltage levels.
CAUTION! Ground the TOPVERT E1 using the ground terminal.
The grounding method must comply with the laws of the country where the Drive is to
be installed. Refer to Basic Wiring Diagram.
DANGER! The Drive may be destroyed beyond repair if incorrect cables are connected to the
input/output terminals. Never connect the Drive output terminals U/T1, V/T2, and
W/T3 directly to the AC main circuit power supply.
CAUTION! The final enclosures of the Drive must comply with EN50178. (Live parts shall be
arranged in enclosures or located behind barriers that meet at least the requirements
of the Protective Type IP20.
The top surface of the enclosures or barrier that is easily accessible shall meet at
least the requirements of the Protective Type IP40).
(TOPVERT E1 Series corresponds with this regulation.)
W A RNING

TOPVERT E1Series
E-
2
CAUTION! Heat sink may heat up over 70℃(158℉), during the operation. Do not touch the
heat sink.
CAUTION! The rated voltage for the drive must be ≤240V (≤480V for 460V models, ≤600V
For 575V models) and the mains supply current capacity must be ≤5000A RMS
(≤10000A RMS for the ≥40hp (30kW) models).
CAUTION! The leakage current between chassis and earth could be up to 22mA.
CAUTION! The load motor should meet IEC:60034-1 standard.
Nameplate Information
Example for E1 Series 3HP/2.2kW 230V 1&3-Phase , RS-485 Serial port was installed.
Model Explanation
Explanation of Production control data
● Please contact the dealers immediately should any discrepancy occurred.
E1-2M2P2-E01-08 T2509001
Model:TOPVERT E1-2M2P2-E01
Input Specifications
Production control data
Output Frequency Range
Model number
Output Specifications
Barcode (Firmware code:3.008)
CE certification
(FRN:3.008)
1 3 0~240V 11A 4.2kVA 2.2kW/3Hp
Production Number
Production Month: 1~9 = Jan. to Sep.
O=Oct. N=Nov. D=Dec.
Production Year: 0~9=2010~2019
Production Factory: T = Taiwan factory
Option Code or custom-made code
Model:
E1 series 230V 1&3 Phase 2.2kW / 3Hp
Motor V/F selecting Preset (Pr0-02)
E1-2M2P2-xxx-08 T 2 5 09001
Applicable Motor Capacity
0P2= 0.2kW 0P4= 0.4kW
0P7= 0.75kW 1P5= 1.5kW
2P2= 2.2kW 3P7= 3.7kW
Option Code or customer made code
E01 = RS-485 Serial port was installed
Toptek
AC drive Family
AC Power source
11= 115V 1 Phase
2M= 230V 1&3 Phase
23= 230V 3Phase
43= 460V 3 Phase
E1 Series
Hardware version
Blank: original version
A: version A
B: version B
Z: version Z
TOPVERT E1-2M 2P2 x-xxx

TOPVERT E1Series
E-
3
STANDARD SPECIFICATIONS
TOPVERT E1
series High performance general purpose compact drive
Control Characteristics
Output frequency range 0.1 - 600Hz, Programmable
Overload endurance 150% of rated current for 1 minute/10 minutes, Ta <=40, 200% of rated current for 3 seconds
Maximum output voltage Proportional to Input Voltage, 3-Phase output
Power factor/Efficiency Power factor no lower than 0.95,Efficiency no lower than 95% at full load
Control system SPWM (Sinusoidal Pulse Width Modulation) vector control, 2 control modes :V/F, SVC
Speed control range
V/F mode 20:1; SVC mode 120:1
Output frequency resolution Analog input: 10 Bit(1/1024), Digital input: 0.01Hz, Fly-Shuttle dial input: 0.01Hz
Output frequency accuracy Analog input:
Within ±0.2% of max. output frequency (25℃±10℃).
Digital input: Within
0.01% of set output frequency
PWM carrier Frequency 0.7 -18kHz,Adjustable (Some models are limited)
Torque characteristics auto-torque boost, auto-slip compensation; starting torque can be 150% at 1.0Hz
Skip frequency Setting range 0.00 -600Hz, Max. 6 points, skip width are adjustable
Accel/Decel time 0.1-60000 seconds ( 2 Independent settings for Accel/Decel Time)
Stall prevention 0 to 250% of Rated Current, independent adjustable both in acceleration and constant speed operation.
DC Braking
DC Braking both when start up and stop , Braking Current Level: 0 to 125% of rated output current. Braking time: 0
to 60 seconds. Braking Start-Point when stop: 0.1-600Hz
Dynamic braking Braking torqueApprox. 20%(10%E.D.). Dynamic Brake chopper built-in in
V/F Pattern 2 of adjustable Random V/F curve. Constant Torque curve & Reduced Torque curve are available.
O
PERATING
Characteristics
Frequency Setting
Keypad
By an Encoder style Fly-Shuttle dial. (setting resolution 0.01Hz/0.1Hz/1Hz/10Hz adjustable)
External
Signal 0 ~ +10VDC((Input impedance 20kΩ),4 ~20mA DC ((Input impedance 250Ω),
Multi-Function Inputs 1 ~ 4 (15 Steps Jog, up/down), PLC run, RS-485 port MODBUS protocol
Operation Setting
Keypad
Set by RUN, STOP and JOG. Switch-able between Keypad and External signal
External
Signal 2 wire control(FWD/STOP、REV/STOP、RUN/STOP、FWD/REV), 3 wire control, FWD, REV, MI1 to MI6 can be
combined to offer various modes of operation, RS-485 serial interface MODBUS protocol
Multi-Function Digital Input
(DI)
(4 terminals)
Multi-step selection 0 to 15, first to second accel/decel switches, accel/decel inhibit, Input the counter, Pause Stop,
EF Input, Emergency Stop, auxiliary motor control is invalid,ACI/AVI speed command selection,, Reset, PLC Run,
Jog, Up/Down command, Sink/Source selection, Parameter team selection…etc, up to 43 functions.
Multi-Function Output Indication
(DO)
(4 indications, 2 of them are
optional)
Include a form C relay contact, a form A relay contact and 2 Open collector output. They can be programmed to
below indications: Drive Operating, FrequencyAttained, zero speed, Base Block, Over torque,
Fault Indication, Local/Remote indication, PLC Operation indication, andAuxiliary Motor Output, Drive ready for
use, IGBT over-heat indication …etc, up to 63 functions.
Multi-Function Analog
Input
(AI)
AVI: 0 ~ +10VDC((Input impedance 20kΩ), ACI: 4 ~20mA DC ((Input impedance 250Ω). 2 different Input terminals
can be programmed to 15 functions
Multi-Function Analog Output
(AO) IncludeAVO, They can be programmed to Proportional to output frequency, output current, voltage, frequency
command or motor's speed …etc, up to 15 functions.
Fault Indication The output will be activated when faults occur (User may get 1 or up to 4 indications from below terminals
:
Relay
contact point RA, RB, RC. or 2 Open-collector
Communication function RS-485 serial port, MODBUS protocol, ASCII & RTU. (Baud rate up to 125 k bps) (Optional)
Other Functions
PID feedback control, Flying start, Automatic voltage regulation (AVR), 2 accel./decel time selection , Auto-
optimum
accel./decel. Time, S-curves, External fault interlock, External fault reset, Auto Restart after fault, 16 Fault records,
Automatic energy–saving, Upper/Lower limit, Programmable pulse output, Password protection, Pump and Fan
process control, Sleep/Wakeup function , Auto-Tuning, By-Pass, Y-Delta control,. Bi-Directional Speed search,
Reverse inhibit, Automatic torque boost & slip compensation, 16-
step PLC run, 16 step preset speed, Coast or ramp
to stop, Random V/F curve, Mechanical brake release control, IGBT/ Heatsink temperature display & Pre-warning,
Quiet operation mode (No noise), User define Multi-function display, Over torque detection, Over current/voltage t
stall prevention, Sink/Source (NPN/PNP) mode, Electronic Thermal Relay, Internal Counter, DC injection brake both
in start and stop, Dynamic brake, Controlled cooling Fan, Removable keypad operator, Programmable
Multi-Function DI,DO,AI,AO and Ry terminals.
Intelligent Protection
Functions
Self-testing,AC source Over Voltage, Phase loss, Over Voltage, Over Current, Under Voltage, Over Torque,
External Fault, Motor over-load, IGBT Over-temperature, Heat-sink Over-temperature, Electronic thermal, Ground
Fault, Output short circuit, Stall Prevention, Fuse protection, IGBT short circuit , Drive Over Load ,
DC bus capacitor
life monitoring, Auto carrier frequency adjust according temperature, 16 Trip records, Run information of
latest Fault
such like DC-BUS voltage, Output voltage/Frequency/Current, Command frequency, IGBT temperature, Heat-sink
temperature….etc.
Digital Keypad
(PU-02 Digital Keypad with copy
function and PU-03 Digital Keypad
with LCD display are available as an
option)
Eight Function keys: Access Run, Stop, Reset/ Digit Shift, Forward/ Reverse run, Display mode, Keypad Enable,
Programming data and Jog operation…etc.
One Encoder style Fly-Shuttle dial: Sets the parameter number and changes the numerical data
One 6 digits 7 segment display: Display the Setting frequency/actual operation frequency, Output
current/Voltage, motor speed, Fault trip User defined unit(up to 88 type)…etc.
Six LED Display for status indication: Display the Drive run/stop status, Forward/Reverse run status, Keypad
enable, and Frequency command source.
One RJ-45 connector: Removable Keypad, remote control distance up to 150 meters.
Environment
Certificate
Complies with CE (EN61800-3) standard
Temperature
Ambient: -10 ~ +40 /℃ ℃
(-10 ~ + 50 )℃ ℃
(Non-Condensing and not frozen). Storage: -20 ~ +60℃ ℃
Humidity
Below 98%R.H. (Non-Condensing)
Vibration
Below 20Hz: 1G, above 20Hz: 0.6G
Installation Location
Altitude 1,000 m or lower, keep away from corrosive gasses, liquid and dust
*TOPVERT all series are designed and manufactured base on CNS, IEC, CE and UL standard.

TOPVERT E1Series
E-
4
1
-
Phase
, 100 ~ 120VAC, 50/60 Hz
(
Tolerance Range
:90 ~ 132V,47 ~ 63Hz)
Output Voltage
:200~240VAC
Model Applicable Motor
(230V 4 P) Rated Output Source
Enclosure Construction
TOPVERT
E1-xxxxx
Power
(kW)
Horse
Power
(Hp)
Capacity
(kVA)
Current
(A) Voltage
(V) Frequency
(Hz) Current
(A) Cooling
Methods
Protection
Methods
(IP/NEMA)
Net
Weight
(kg)
Frame
Code
110P2 0.2 0.25 0.6 1.5 3- Phase,
0-240
(Max) 0.1- 600
2.9 Fan-
cooled
IP 20
NEMA 1
E1-A
110P4 0.4 0.5 1.2 3 5.7
110P7 0.75 1 2 5 9.5
111P5 1.5 2 3 7.5 14
1
&3
Phase, 200~240VAC, 50/60 Hz
(
Tolerance Range: 180~264V, 47~63Hz)
Model Applicable Motor
(230V 4 P) Rated Output Source
Enclosure Construction
TOPVERT
E1-xxxxx
Power
(kW)
Horse
Power
(Hp)
Capacity
(kVA) Current
(A) Voltage
(V) Frequency
(Hz) Current
(A) Cooling
Methods
Protection
Methods
(IP/NEMA)
Net
Weight
(kg)
Frame
Code
2M0P4 0.4 0.5 1.2 3 3- Phase,
0-240
(Max) 0.1-600
5.7 Fan-
cooled
IP 20
NEMA 1
1.24
E1-S
2M0P7 0.75 1 2 5 9.5 1.28
2M1P5 1.5 2 3 7.5 14 1.32
2M2P2 2.2 3 4.4 11 21 1.68
E1-A
3
-
Phase, 200~240VAC, 50/60 Hz
(
Tolerance Range: 180~264V, 47~63Hz)
Model Applicable Motor
(230V 4 P) Rated Output Source
Enclosure Construction
TOPVERT
E1-xxxxx
Power
(kW)
Horse
Power
(Hp)
Capacity
(kVA) Current
(A) Voltage
(V) Frequency
(Hz) Current
(A) Cooling
Methods
Protection
Methods
(IP/NEMA)
Net
Weight
(kg)
Frame
Code
233P7 3.7 5 6.8 17 3- Phase,
0-240
(Max) 0.1-600 19 Fan-
cooled
IP 20
NEMA 1 1.68
E1-A
3
-
Phase, 380~480VAC, 50/60 Hz
(
Tolerance Range: 323~528V, 47~63Hz)
Model Applicable Motor
(460V 4 P) Rated Output Source
Enclosure Construction
TOPVERT
E1-xxxxx
Power
(kW)
Horse
Power
(Hp)
Capacity
(kVA) Current
(A) Voltage
(V) Frequency
(Hz) Current
(A) Cooling
Methods
Protection
Methods
(IP/NEMA)
Net
Weight
(kg)
Frame
Code
430P4 0.4 0.5 1.3 1.6 3- Phase,
0-460
(Max) 0.1-600
1.8
Fan-
cooled
IP 20
NEMA 1
1.57
E1-S
430P7 0.75 1 2.4 3 3.3 1.57
431P5 1.5 2 3.3 4.2 4.6 1.62
432P2 2.2 3 4.8 6 6.6 1.64
E1-A
433P7 3.7 5 6.8 8.5 9.4 1.74

TOPVERT E1Series
E-
5
Basic Wiring Diagram
Main Circuit Terminal Explanations
Terminal Symbol Content Explanation
R(L1),S(L2),T(L3) AC source input terminals, to be connected to commercial power.
Ensuring the power voltage and the maximum current possible supplied
is meet the driver nameplate.
U(T1),V(T2),W(T3) Drive output terminals for motor connections
⊕/B1, B2 Connections for Brake Resistor (optional) .
⊕/B1, ΘConnecting terminals of the external Dynamic Brake Unit.
(DC Bus, power source terminals)
Ground terminals, please have these terminals grounded following the
third-type grounding of 230V series and the special grounding of 460V
series within the electrician regulations
B2
B1
NFB
None Fuse Breaker
Main circuit
Motor
M
3~
U(T1)
W(T3)
V(T2)
+
R(L1)
M.C.
T(L3)
[ Use R(L1), S(L2) for 1-phase models]
S(L2)
Braking Resistor (Option)
TDBR
Remark: ◎
◎◎
◎→
→→
→Main circuit ○
○○
○→
→→
→Control circuit →
→→
→Shielded leads & Cable ( ) →
→→
→Factory default →
→→
→option
3-Phase
power source
-
Photo-coupler output common terminal
Open collector output 1
(pre-set speed attained 1 (forward only))
48VDC/50mA
MO1
MCM
Analog voltage output -- 0~10VDC/2mA
(output frequency)
Analog Signal Common
AVO
ACM
R1A
R1B
R1C
Contact output 1
(indicates malfunction)
240VAC/2.5A, 120VAC/5A, 24VDC/5A
Multi-
function
Relay
output
(Ry)
(DO)
(AO)
Multi-
function
Analog
output
Multi-
function
Digital
output
+12V 20mA
0~10V (20KΩ)
ACM
4~20mA (250Ω)
+12V
VR : 5~10 KΩAVI
ACI
Multi-function Analog signal command
(Frequency Command)
Source Mode
E
FWD / STOP
(Multi-Step2)
(Multi-Step3)
(Multi-Step4)
(Multi-Step1)
REV / STOP
FactoryDefault
Control signal input
Reference of external power
MI1
MI2
MI3
MI4
FWD / STOP
(Multi-Step2)
(Multi-Step3)
(Multi-Step4)
(Multi-Step1)
REV / STOP
Digital Signal Common
DCM
*Don´t apply any voltage
directly to those terminals
24V
FWD
REV
FactoryDefault
E
24V
+
-
Use internal power source
Useexternalpowersource
(AI)
Control signal input
12
3
Sink Mode
Multi-
function
Analog
input
MI1
24V
FWD
REV
MI2
MI3
MI4
DCM
Multi-
function
Digital
input
(DI)
Serial
port
Control circuit
TOPVERT E1
RS-485 Serial port option kit
87654321
Pin assignment :
1: Reserved 2: Reserved
3: GND 4: SG- 5: SG+ 6: +5V
7: Reserved 8: Reserved
SW1
Source
(Sink)

TOPVERT E1Series
E-
6
Control Terminal Explanations
Terminal
Symbols
Explanation on the Terminal Function Factory Default
Digital inputs
(Use the shielded twisted-pair cables to prevent operating faults)
MI1 Multi-function input selection 1
(3-wire STOP-designated terminal) multi-step speed command 1
MI2 Multi-function input selection 2 multi-step speed command 2
MI3 Multi-function input selection 3 multi-step speed command 3
MI4 Multi-function input selection 4 multi-step speed command 4
FWD FWD RUN-STOP command
REV REV RUN-STOP command
DCM Digital control signal - the common end
Relay contact outputs
Separate these control circuit wiring from wiring for other control terminals
R1A Multi-function relay 1 output contact (NO / a) Resistive Load
5A(N.O.)/3A(N.C.) 240VAC
5A(N.O.)/3A(N.C.) 24VDC
Inductive Load
1.5A(N.O.)/0.5A(N.C.) 240VAC
1.5A(N.O.)/0.5A(N.C.) 24VDC
Refer to Pr.2-19, Pr.2-20
R1B Multi-function relay 1 output contact (NC / b)
R1C Multi-function relay 1 output contact
– the common end
Voltage source for digital signal and Frame Ground
(Use the shielded twisted-pair cables to prevent operating faults)
E Shield terminal
24V Digital control source signal
Reference point is DCM +24V 50mA
Analog Inputs and outputs
Analog input signals are easily affected by external noise. Use shielded twisted-pair cables for
wiring and keep it as short as possible (<20m) with proper grounding. Basically the shield sheath
should coonect to the E terminal, but If the noise is inductive, connecting the shield to terminal
ACM can bring improvement.
+12V Auxiliary reference power Reference point is ACM
+12V 20mA
ACM Analog control signal - the common end
AVI Multi-Function analog voltage command The maximum operation
frequency corresponding to 0~+10V
ACI Multi-Function analog current command The maximum operation
frequency corresponding to
4~20mA
AVO Multi-function analog voltage output
(0~10VDC, 2mA) Output frequency
Digital outputs
(Use the shielded twisted-pair cables to prevent operating faults)
MO1 Multi-function output terminal 1 (photo coupler) pre-set speed attained
(Max 48VDC 50mA)
MCM Multi-function output terminal (photo coupler) –
the common end

TOPVERT E1Series
E-
7
Description of the Digital Keypad
Digital Keypad PU-01 function descriptions
Digital Keypad PU-02 function descriptions
It keeped all function in PU-01 and add on Parameter Read/Write/Storage/Copy
function. (Valid for Firmware version 2.xx and after only)
FWD REV EXT PU
PU-02
PU
JOG DISP F/R
RUN STOP
RESET
Read/Save
Press PU and RESET
together to operate
Read and Save functions
Main Display
Display t
he drive status such as
frequency,
current, voltage,
parameter
setting value
and alarm contents.
Data modification/Program Dial
Rotate to modification for settings, parameters
and output frequency adjustment.
Press to Read or Enter datas
RESET
FWD REV EXT PU
Part number
Status Display……
…………
…… Display the driver's current status
When "PU" lights, RUN/STOP is controlled by PU-01.
When"PU" is dark, RUN/STOPis set by Pr0-19.
When "EXT" lights, frequency command is set by Pr0-18.
When"EXT" is dark,frequency command is controlled by PU-01
When "REV" lights, Drive is in reverse operation.
When "FWD" lights, Drive is in forward operation.
Left /Reset key
Moves cursor to the left.
Reset errors.
FWD/REV
Direction key
Display Selection key
Changes between different
display mode.
STOP key
Programming Unit key
Enable the keypad. It can determine
the source of RUNSTOP
Jog Operation key
Press this key to execute
JOG frequency opeation
RUN key
PU-01
PU
JOG
DISP
F/R
RUN STOP
RUN indication STOP indication

TOPVERT E1Series
E-
8
Digital Keypad PU-03 function descriptions
It is an user programmable LCD graphical and text display.
Explanations of Display Messages
Messages Displayed
Descriptions
Display master frequency command of the drive
(Press the DISP key to read)
Display actual operation frequency output to the motor from the drive
(Press the DISP key to read)
Display output current to motor
(Press the DISP key to read)
Display User-selected content on Pr0-07
(Press the DISP key to read)
Display Read/Save selected content (For PU-02 only)
(Press the DISP key to read)
F W D R E V E X T P U
F W D R E V E X T P U
F W D R E V E X T P U
F W D R E V E X T P U
FW D REV EX T PU
100%
FWD REV EXT PU
RESET
Main Display
Display t
he drive status such as f
requency,
current, voltage,
parameter
setting value
and alarm contents.
Part number
Shift /Reset key
Moves cursor to shift the digit. Reset errors.
FWD/REV Direction key
Display selection key
Changes between different display mode.
STOP key
Jog Operation key
Press this key to execute JOG frequency opeation
RUN key
PU-03
Data modification/Program Dial
Rotate to modification for settings, parameters
and output frequency adjustment.
Press to read or enter data
PU
JOG
DISP
F/R
RUN STOP
RUN indication STOP indication
6000.00Hz 9999.99A
6000.00Hz
Status Display……
…………
……
Display the driver's current status
When "PU" lights, RUN/STOP is controlled by PU-03.
When "PU" is dark, RUN/STOP is set by Pr0-19.
When "EXT" lights, frequency command is set by Pr0-18.
When "EXT" is dark,frequency command Is controlled by PU-03
When " " Is lights
:
Timer run function is proceeding
When "REV" lights, Drive is in reverse operation.
When "FWD" lights, Drive is in forward operation.
JProgramming Unit key
Enable the keypad.
It can determine the source of Run/Stop

TOPVERT E1Series
E-
9
4-3 Operation Steps
4-3-1 Selecting display mode
4-3-2 Setting parameters (For example, to set Pr0-07 = 2)
The specified parameter item
(Rotate and press the dial to modification, read and Enter)
(Press to display those parameters which data are different from
factory default)
Value of the parameter content
(Rotate the dial to modify for setting parameters)
If the “End” message is displayed , for about 1 second, it is an
indication that the data has been accepted and saved to the internal
memory.
RESET
FW D REV E XT P U
To setting parameter
Power-up Display
Press then
rotate
FWD REV EXT PU
Modify data to 2
Press then
rotate
FWD REV EXT PU
Success to set parameter.
FWD REV EXT PU
Press
Press 0.5sec
FWD REV EXT PU
To setting parameter
FWD REV EXT PU
DISP
Press twice
Press
FWD REV EXT PU
Select Pr 0-07
to be modified
To scrolling between F page, H page, A page and U page by pressing the DISP key
User defined Multi-
Function Display
DISP
Output current to motor
Press
DISP
Actual operation
frequency output to the
motor from the drive
Press
DISP
Master frequency
command of the drive
Press
FWD REV EXT PU FWD REV EXT PU FWD REV EXT PU
DISPPress
FWD REV EXT PU
FW D REV EXT PU
FW D REV E XT PUFW D REV E XT PU

TOPVERT E1Series
E-
10
4-3-3 To run (For example, to run 50 Hz from PU)
4-3-4 Parameters READ/SAVE Operation (For PU-02 only)
(Parameter copy can execute between same drive model only)
To run setted 50.00Hz
Set master frequency
to 50.00Hz
(Use left key for quick
data entry)
RUN
Press
FW D R EV EXT PU
FW D REV EXT PU
RESET
To shift data
Rotate
To setting direction,
FW D/REV
F/R
Press
FW D REV EXT PU
To enable PU
PU
Press
FW D REV EXT PU
To display actualoutput frequency
to the motor
DISP
Press
FWD REV EXT PU
Selections:
Read1
Save1
Read2
Save2
Rotate
PU
Press 2 key
simultaneously
RESET
To read parameter
FWD REV EXT PU
To save parameter
PU
Press 2 key
simultaneously
RESE T
FWD REV EXT PU
Parameter Save
accomplished
FWD REV EXT PU
Parameter Read
accomplished
FWD REV EXT PUFWD REV EXT PU

TOPVERT E1Series
E-
11
FUNCTIONS and PARAMETER SUMMARY
★
=This parameter cannot be set
during operation.
◎
:Available in Firmware Version
2.xx and after only.
☉
:Available in Firmware Version
3.xx and after only.
{ }Parameter no. in
Firmware Version 1.xx
[ ] :optional
Group 0: System parameters
Parame
ters Functions Settings Factory
Setting User
★
Pr0-00
Model display Display according to the model number Read Only
★
Pr0-01 Rated output current to
motor Display according to the model number Read Only
★
Pr0-02 Parameter Reset
(Motor V/F selecting)
10: Parameter reset for
60Hz - 230/460V motor application
8
9: Parameter reset for
50Hz - 220/380V motor application
8: Parameter reset for
60Hz - 220/380V motor application
7: Parameter reset for
50Hz - 230/460V motor application
6: Parameter reset for
60Hz - 240/415V motor application
◎
5: Parameter reset for
50Hz - 240/415V motor application
◎
Pr0-03
Password Input (The Key)
0~9999 0
Pr0-04
Password set (The Lock) 0~9999 0
Pr0-05
Parameter Locking Level
Bit0
0
All parameters are readable,
b00000
1
Parameters after Pr0-05 cannot read
”Err” message will displayed when try
to read.
Bit1
0
Enable Frequency Command.
1
Disable frequency command
Bit2
0
Enable run command from PU
1
Disable run command from PU
Pr0-06
Power on display
selection
0: Frequency command value
0
1: Actual output frequency (Hz)
2: Output current
3: User defined contents on Pr0-07
Pr0-07
Versatile display
0: Motor speed (RPM)
0
1: DC-Bus Voltage (Vdc)
2: Actual output voltage (Vac)
3: Output voltage command value (Vac)
4: PID feedback frequency value (Hz)
5: Running step no. of MSS run
6: Sleep time (Pr8-07)
7: Auto-Restart after Fault (Pr6-10)
8: PID frequency command value (Hz)
9: (Factory Reserved)
10: Output power factor angle ( º )
11: Counter value
12: Over-Torque detection time 1 (Pr5-17)
13: (Factory Reserved)
14: Dwell Time at Accel. (Pr6-14)
15: Dwell Time at Decel. (Pr6-16)

TOPVERT E1Series
E-
12
16: DC Braking time in Start-up (Pr6-01)
17: DC Braking Time during stop (Pr6-02)
18: Remain time of the executing MSS Run
19: (Factory Reserved)
20: (Factory Reserved)
21: Accumulated power-up Day (day)
22: Accumulated power-up time (hh:mm)
23: (Factory Reserved)
24: (Factory Reserved)
25: (Factory Reserved)
26: The signal of AVI analog input (Vdc)
27: The signal of ACI analog input (mAdc)
28: (Factory Reserved)
29: (Factory Reserved)
30~33: (Factory Reserved)
34: Over-Torque detection level 1 (Pr5-16)
35: Motor 1 Auto torque boost (Pr5-01)
36~37: (Factory Reserved)
38: Stall level while run in constant torque area
(Pr5-12)
39〜52: (Factory Reserved)
53: Output power (kW)
54: Output capacity (kVA)
55:(Factory Reserved)
56: The temperature of IGBT module--TH1 ( °C)
57: The temperature of environment or fin
(TH2) (°C)
58: (Factory Reserved)
59: (Factory Reserved)
60: Drive overload accumulated time (OL)
61~63:(Factory Reserved)
64: DC Bus voltage upon a fault (Vdc)
65: Output voltage upon a fault (Vac)
66: Output frequency upon a fault (Hz)
67: IGBT module temperature upon a fault
( °C) ◎
68: Output current value upon a fault (Aac)
69︰Temperature of Fin or environment
upon a fault ( °C) ◎
70~86︰(Factory Reserved)
87: DC Bus ripple voltage (Vdc) ◎
88: (Factory Reserved) ◎
Pr0-08
User-Defined coefficient
K
0~39 (no use) 0
40~60000 (the corresponding value
for Pr1-00-- the max. frequency).
Pr0-09
The decimal places 0~3 (0=Without d.p., 1= 1 digit d.p., )
(2=2 digit d.p., 3=3 digit d.p.) 0
Pr0-10
Firmware version Read-only x.xx
Pr0-11 EPROM store set
Bit0
0
FWD/REV direction command will be
store
b00000
1
FWD/REV direction command not store
Bit1
0
Frequency command from PU will be
store
1
Frequency command from PU not store
Bit2
0
RS-485 frequency command will be
store
1
RS-485 frequency command not store
Bit3
0
Up/Down frequency command will be
store

TOPVERT E1Series
E-
13
1
Up/Down frequency command not
store
Bit4
0
Changed parameter will be store
1
Changed parameter not store
Pr0-12
Auto Accelerate/
Decelerate
0: Linear Acc, linear Dec.
0
1: Auto Acc, linear Dec.
2: Linear Acc, auto Dec.
3: Auto Acc, auto Dec.
4: Linear Acc,/Dec., auto to prevent stall.
★
Pr0-13
Accelerate/ Decelerate
time unit
0: 0.01 Second 01: 0.1 Second
2: 1 Second
Pr0-14
PWM Carrier frequency
upper bound 0=0.7kHz 10
1~18kHz
Pr0-15
PWM Carrier frequency
lower bound 0=0.7kHz 10
1~18kHz
Pr0-16
Automatic Voltage
Regulation (AVR)
0: Enable Automatic Voltage Regulation
0
1: Disable Automatic Voltage Regulation
2: Disable Automatic Voltage Regulation while in
decele
Pr0-17
Automatic Energy-Saving
Operation (AESO)
and others
Bit0
0
Disable Automatic Energy-Saving
Operate
b00000
1
Enable Automatic Energy-Saving
Operate
Bit1
0
Allow output voltage over source
voltage
1
Maximum output voltage equals to
source voltage
Bit2
0
For constant torque load application.
1
For variable torque load application.
Bit3
0
Regen-torque no slip compensation
1
Regen-torque with slip compensation
Bit4
0
Low noise mode operation
1
Quiet mode operation
Pr0-18
Source of the frequency
command
0: From PU
0
1: From RS485 communication port
2: From external analog signal
3: From external Up/Down terminals
4: (Factory Reserved)
Pr0-19
Source of the operation
command
0: From RS485 communication port or PU
0
1: From external terminals or PU
2: From PU
3: From external terminals
Pr0-20
Stop/ Run/safety lockout
Bit0
0
Ramp to stop
b00000
1
Coast to stop
Bit1
0
Terminal command not run after reset
1
Terminal command restart after reset
Bit2
0
Line start Lockout is enabled
1
Line start Lockout is disabled
Bit3
0
FWD/REV go through zero point
1
FWD/REV go not through zero point
Bit4
0
Linear Accel/Decel at high speed zone
1
S-curve Accel/Decel at high speed
zone
Pr0-21
Direction limit 0: Enable Forward/Reverse operation 0
1: Disable Reverse operation
2: Disabled Forward operation

TOPVERT E1Series
E-
14
Pr0-22
Waiting time to restart
after stop 0.00~60.00sec 0.00
Pr0-23
Cooling fan control & PID
direction
Bit0
0
Fan on while power on
b00000
1
Fan on while run command effect
Bit1
0
(Factory Reserved)
1
Bit2
0
(Factory Reserved)
1
Bit3
0
PID reverse operation allow
1
PID reverse operation not allow
Bit4
0
(Factory Reserved)
1
Pr0-24
Resolution of dial
0=0.01 Hz
1
1=0.10Hz
2=1.00Hz
3=10.00 Hz
★
◎
Pr0-25
Parameter select 0: Team A 01: Team B
2: Select Team A or Team B by MI3
Group 1: Basic parameters
Parame
ters Functions Settings Factory
Setting User
★
Pr1-00
Maximum operation frequency 3.00~600.00Hz 60.00/
50.00
★
Pr1-01
1st Frequency 1 (Fbase 1)
(Base frequency 1 ) 0.00~600.00 Hz 60.00/
50.00
Pr1-02
1st Voltage 1 (Vbase 1)
(Motor rated voltage 1) 230V models: 0.0~255.0V 230.0
460V models: 0.0~510.0V 460.0
★
Pr1-03
2nd Frequency 1 (Fmid 1)
(Middle frequency 1) 0.00~600.00 Hz 0.50
Pr1-04
2nd Voltage 1 (Vmid 1)
(Middle voltage 1) 230V models: 0.0~255.0V 5.0
460V models: 0.0~510.0V 10.0
★
Pr1-05
3rd Frequency 1 (Flow 1)
(Low-point frequency 1) 0.00~600.00 Hz 0.50
Pr1-06
3rd Voltage 1 (Vlow 1)
(Low-point voltage 1) 230V models: 0.0~255.0 5.0
460V models: 0.0~510.0V 10.0
Pr1-07
0Hz Voltage 1 (V0Hz 1)
(Output voltage at 0Hz) 230V models: 0.0~25.5 0.0
460V models: 0.0~51.0V
Pr1-08
Start-up frequency 0.00~600.00 Hz 0.50
Pr1-09
Output frequency Upper limit 0.0~150.0% of Maximum operation
frequency (Pr1-00) 110.0
Pr1-10
Output Frequency Lowerl limit 0.0~100.0% of Maximum operation
frequency (Pr1-00) 0.0
Pr1-11
1st Acceleration time 0.00~60000 Sec 10.00
Pr1-12
1st Deceleration time 0.00~60000 Sec 10.00
Pr1-13
2nd Acceleration time 0.00~60000 Sec 10.00
Pr1-14
2nd Deceleration time 0.00~60000 Sec 10.00
Pr1-15
JOG Acceleration time 0.00~60000 Sec 10.00
Pr1-16
JOG Deceleration time 0.00~60000 Sec 10.00
Pr1-17
JOG frequency 0.00~600.00 Hz 6.00
Pr1-18
1st/2nd
Acceleration/Deceleration
Switching frequency 0.00~600.00 Hz 0.000
Pr1-19
S-Acc. departure time when
accelerate 0.00~12000 Sec 0.00
Pr1-20
S-Acc. arrival time when
accelerate 0.00~12000 Sec 0.00

TOPVERT E1Series
E-
15
Pr1-21
S-Dec. departure time when
decelerate 0.00~12000 Sec 0.00
Pr1-22
S-Dec. arrival time when
decelerate 0.00~12000 Sec 0.00
Pr1-23
{Pr1-29}
Offset voltage while decelerate 230V models: -50.0~50.0 V 0.00
460V models: -100.0~100.0 V
★
Pr1-24
{Pr1-23}
Skip Frequency 1 upper limit 0.00~600.00Hz 0.00
★
Pr1-25
{Pr1-24}
Skip Frequency 1 lower limit 0.00~600.00Hz 0.00
★
Pr1-26
{Pr1-25}
Skip Frequency 2 upper limit 0.00~600.00Hz 0.00
★
Pr1-27
{Pr1-26}
Skip Frequency 2 lower limit 0.00~600.00Hz 0.00
★
Pr1-28
{Pr1-27}
Skip Frequency 3 upper limit 0.00~600.00Hz 0.00
★
Pr1-29
{Pr1-28}
Skip Frequency 3 lower limit 0.00~600.00Hz 0.00
★
◎
◎◎
◎
Pr1-30
Skip Frequency 4 upper limit 0.00~600.00 Hz 0.00
★
◎
◎◎
◎
Pr1-31
Skip Frequency 4 lower limit 0.00~600.00 Hz 0.00
★
◎
◎◎
◎
Pr1-32
Skip Frequency 5 upper limit 0.00~600.00 Hz 0.00
★
◎
◎◎
◎
Pr1-33
Skip Frequency 5 lower limit 0.00~600.00 Hz 0.00
★
◎
◎◎
◎
Pr1-34
Skip Frequency 6 upper limit 0.00~600.00 Hz 0.00
★
◎
◎◎
◎
Pr1-35
Skip Frequency 6 lower limit 0.00~600.00 Hz 0.00
★
◎
◎◎
◎
Pr1-36
1st Frequency 2 (Fbase 2)
(Base frequency 2 ) 0.00~600.00 Hz 60.00/
50.00
◎
◎◎
◎
Pr1-37
1st Voltage 2 (Vbase 2)
(Motor rated voltage 2) 230V models: 0.0~255.0V 230
460V models: 0.0~510.0V 460
★
◎
◎◎
◎
Pr1-38
2nd Frequency 2 (Fmid 2)
(Middle frequency 2) 0.00~600.00 Hz 0.50
★
◎
◎◎
◎
Pr1-39
2nd Voltage 2 (Vmid 2)
(Middle voltage 2) 230V models: 0.0~255.0V 5.0
460V models: 0.0~510.0V 10.0
★
◎
◎◎
◎
Pr1-40
3rd Frequency 2 (Flow 2)
(Low-point frequency 2) 0.00~600.00 Hz 0.50
★
◎
◎◎
◎
Pr1-41
3rd Voltage 2 (Vlow 2)
(Low-point voltage 2) 230V model: 0.0~255.0V 5.0
460V model: 0.0~510.0V 10.0
★
◎
◎◎
◎
Pr1-42
0Hz Voltage 2 (V0Hz 2)
(Output voltage at 0Hz) 230V models:0.0~25.5 0.0
460V models:0.0~51.0V

TOPVERT E1Series
E-
16
Group 2: Digital Input/Output parameters
Parame
ters Functions Settings Factory
Setting User
★
Pr2-00
External operation 0: 2-wire mode 1- FWD/STOP, REV/STOP 0
1: 2-wire mode 2- RUN/STOP, REV/FWD
2: 3-wire mode -RUN,STOP, FWD/REV
★
Pr2-01
Multi-Function Digital input
MI1 0: No definition 1
★
Pr2-02
Multi-Function Digital input
MI2 1: Multi-step speed command 1 2
★
Pr2-03
Multi-Function Digital input
MI3 2: Multi-step speed command 2 3
★
Pr2-04
Multi-Function Digital input
MI4 3: Multi-step speed command 3 4
★
Pr2-05
(Factory Reserved) 4: Multi-step speed command 4 5
★
Pr2-06
(Factory Reserved)
5: External Reset
14
6: Clear counter
7: 1st and 2nd acceleration/ deceleration time
select
8: Acceleration/deceleration inhibit
9: Force the frequency command from AVI
10: Force the frequency command from ACI
11: (Factory Reserved)
12: Emergency stop
13: Disable PID function
14: External fault input (EF)
15: B.B. traces from the bottom upward
16: B.B. traces from the top downward
17: Force operation command to external
18: Cancel the auto acceleration/ deceleration
function
19: FWD JOG command
20: REV JOG command
21: JOG command
22: Cancel PLC Run
23: Pause PLC Run
24: Up command
25: Down command
26: Zero speed is replaced by DC braking
27: Pause
28: Disable dwell function
29: Disable traverse function
30: Disable Speed search during start-up
31: Disable EEPROM write function
32: Counter Trigger input (MI2 only)
33~41: (Factory Reserved)
42: Motor Select ◎
43: Confirm signal of Motor selection ◎
44: Disable reverse operation ◎
45: Disabled forward operation ◎
Pr2-07
UP/DOWN command mode
Bit 0
0
Up command-Accel by the Acc. time
b00000
1
Up command-Accel by Pr2-08 setting
Bit 1
0
Down Command-Decel by the Dec.
time
1
Down Command-Decel by Pr2-08
setting
Bit 2
(Factory Reserved)

TOPVERT E1Series
E-
17
Bit 3
0
FWD/REV terminals act by edge
trigger
1
FWD/REV terminals act by level
trigger
Bit 4
0
(Factory Reserved)
1
(Factory Reserved)
Pr2-08
UP/DOWN command rate 0.01~1.00Hz/msec (10~1000Hz/sec) 0.01
Pr2-09
Digital Input terminal
debounce time 0.001~30.000 Sec 0.005
Pr2-10
Polarity of Digital Input
terminals
00000~007FF h00000
(0=Close circuit enable 1=Open circuit enable)
Pr2-11 Target count value 0~65500 0
Pr2-12
Pre warn count value 0~65500 0
Pr2-13
Digital pulse output gain 1~20 1
Pr2-14
Pre-set arrival frequency 1 0.00~600.00 Hz 60.00/
50.00
Pr2-15
Pre-set arrival frequency 1
bandwidth 0.00~600.00 Hz 2.00
Pr2-16
Pre-set arrival frequency 2 0.00~600.00 Hz 60.00/
50.00
Pr2-17
Pre-set arrival frequency 2
bandwidth 0.00~600.00 Hz 2.00
Pr2-18
Polarity of Digital output
terminals 00000~0003F h00000
◎
Pr2-19
Delay time of Digital output
terminals 0.000~60.000 Sec 0.003
Pr2-20
{Pr2-19}
Multi-Function Digital output
1- Relay 1 0: No definition 11
Pr2-21
{Pr2-20}
(Factory Reserved) 1: Drive in run 1
Pr2-22
{Pr2-21}
Multi-Function Digital output
3 - MO1 2: Master frequency attained 1
(Both Forward and Reverse) 5
Pr2-23
{Pr2-22}
(Factory Reserved) 3: Master frequency attained 2
(Both Forward and Reverse)
◎
◎◎
◎
Pr2-24
(Factory Reserved) 4: Pre-set speed attained 1
(Both Forward and Reverse) 9
◎
◎◎
◎
Pr2-25
(Factory Reserved) 5: Pre-set speed attained 1
(Forward only) 0
6: Pre-set speed attained 2
(Both Forward and Reverse) 0
7 : Pre-set speed attained 2
(Forward only)
8: Drive in decel
9: Drive ready for operate
10: Low voltage alarm (LU, LUr)
11: Fault Indication
12: Base block (B.B.) Indication
13: Zero Speed (including shutdown)
14: Zero speed (while in run)
15: Terminal count value attained
16: Pre warn count value attained
17: PLC Run running
18: PLC Run paused
19: A step of PLC Run completed
20: PLC Run completed
21: OH1 pre–warning indication
22: Dwell Accel/Decel in execution
23: External operation mode indication
24: Over-torque 1 (ot1)
25: (Factory Reserved)

TOPVERT E1Series
E-
18
26: Software brake output (MO1 only)
27: Auxiliary Motor no. 1
28: Auxiliary Motor no. 2
29: Auxiliary Motor no. 3
30: Over-torque 2 (ot2)
◎
31: OH2 pre–warning indication
◎
32: Motor selection output (Pr5-49)
◎
33~47: (Factory Reserved)
48: Master speed executing
49: PLC Run step 1 executing
50: PLC Run step 2 executing
51: PLC Run step 3 executing
52: PLC Run step 4 executing
53: PLC Run step 5 executing
54: PLC Run step 6 executing
55: PLC Run step 7 executing
56: PLC Run step 8 executing
57: PLC Run step 9 executing
58: PLC Run step 10 executing
59: PLC Run step 11 executing
60: PLC Run step 12 executing
61: PLC Run step 13 executing
62: PLC Run step 14 executing
63: PLC Run step 15 executing
64~79: (Factory Reserved)
◎
◎◎
◎
Pr2-26
(Factory Reserved)
(Factory Reserved) 0
◎
◎◎
◎
Pr2-27
(Factory Reserved)
◎
◎◎
◎
Pr2-28
(Factory Reserved)
Group 3: Analog Input/Output parameters
Parame
ters Functions Settings Factory
Setting
User
Pr3-00
Addition Function of the Analog
Inputs 0: Enable addition function 0
1: Disable addition function
Pr3-01
Analog input noise filter time 0.00~2.00 sec 0.10
Pr3-02
Valid
for
ACI
(Pr3-0
6) AVI Analog Input
0: No functions
1
1: Frequency command
2: To adjust 1st Acceleration/deceleration time)
(same as Pr1-11, Pr1-12)
3: Over Current stall prevention level during
constant speed run on the constant torque
region (same as Pr5-12)
4: Over Current stall prevention level during accel
on the constant torque region (same as Pr5-10)
5: Over-Torque detection level 1 (ot1)
(same as Pr5-16)
6: Motor 1 Torque boost level (same as Pr5-01)
7: Auxiliary command when main frequency
command is AVI only
8: Auxiliary command when main frequency
command is ACI only
9: (Factory Reserved)
10: Auxiliary command of master frequency
command
11: PID feedback signal
12: PID offset signal (same as Pr7-05)
13: DC Braking current level (same as Pr6-00)
Other manuals for TOPVERT E1 Series
1
This manual suits for next models
14
Table of contents
Other TOPTEK DC Drive manuals
Popular DC Drive manuals by other brands
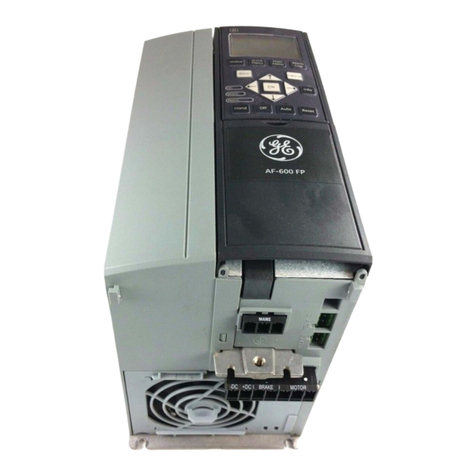
GE
GE AF-600 FP Series user guide

Romac Industries Inc.
Romac Industries Inc. 371-00 operating manual
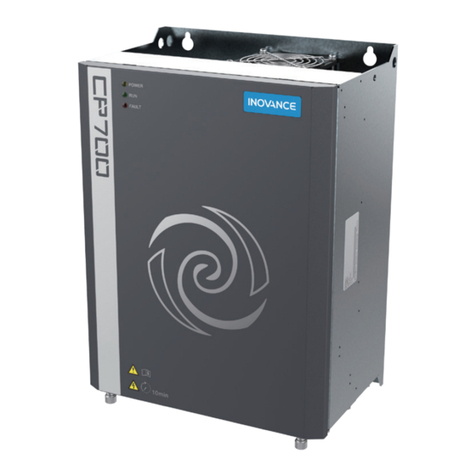
Inovance
Inovance CP700 Series user guide
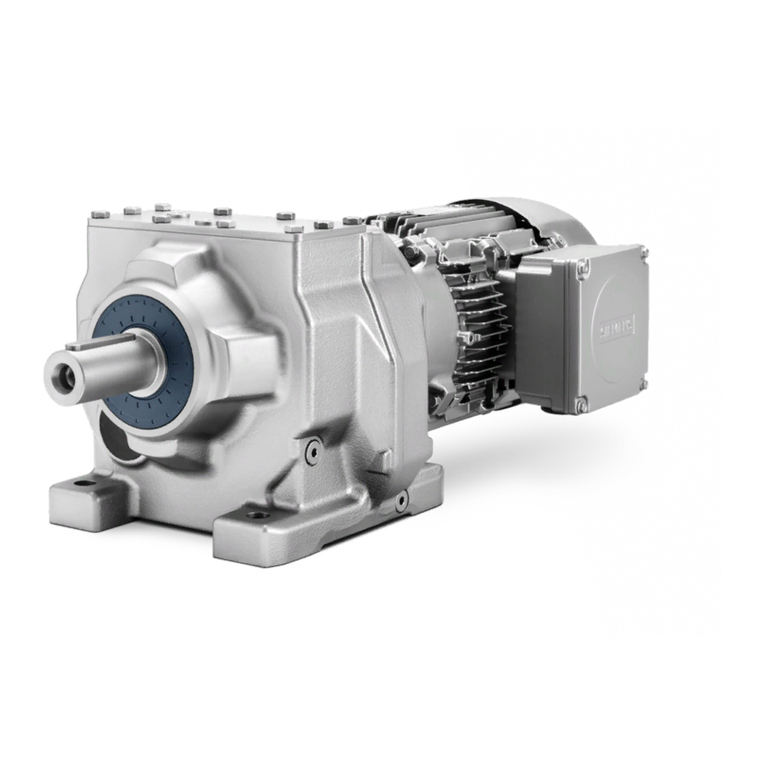
Siemens
Siemens SIMOGEAR BA 2030 operating instructions

Shihlin electric
Shihlin electric SDE-010A2U manual

Motor City Wash Works
Motor City Wash Works ROCKRHYD Series installation manual