Tornado 99795 Manual

1
TORNADO INDUSTRIES, LLC
3101 WICHITA COURT
FORT WORTH, TX 76140
PHONE: 800-VACUUMS
FAX: 817-551-0719
WWW.TORNADOVAC.COM
Operations & Maintenance Manual
For Commercial Use Only
BR 40/66 RIDE-ON SCRUBBER
MODEL NO: 99795
Form No. L9795AB02/17©Tornado Industries, LLC. All rights reserved
https://harrissupplyind.com-ToOrderPartsCall608-268-8080

Long Term Buyer Protection Limited Warranty
10 Years*
Plastic water tanks and Rotationally-molded bodies
2 Years*
Parts on all Tornado cleaning equipment
1 Year*
Labor on all Tornado cleaning equipment
1 Year*
Warranty on batteries, one year prorated
All battery warranties are handled directly by the battery manufacturer, on a one year prorated basis
Tornado Industries, LLC. (Tornado) warrants to the end/user customer that the Tornado product(s) will
be free from defects in material and workmanship for the duration(s) described below. This limited
warranty DOES NOT cover machines and/or components subject to normal wear and tear, damage
that occurs in shipping, failures resulting from modication, accident, unsuitable operating environ-
ment, misuse, abuse, neglect, or improper maintenance by you. For full details, contact your Autho-
rized Tornado Distributor, Service Center, or the Tornado Technical Service Department. Tornado
sales and service representatives are not authorized to waive or alter the terms of this warranty, or to
increase the obligations of Tornado under the warranty.
Terms subject to change without notice
1. Except all Windshears™ Blowers, Storm, TV2SS, Side and Downdraft, Insulation Blowers, CV 30,
CV 38, CK14/1 PRO, CK 14/2 PRO, SWM 31/9, CK LW13/1, CK LW 13/1 ROAM, CV 38/48 Dual,
PV6, PV10, PV6 ROAM, Wall Mount Vacuum and all chargers are warranted for 1 (one) year for both
parts and labor.
2. All non-wear item parts purchased after warranty expiration are warranted for 90 days.
3. Warranty starts from the date of sale to the consumer or, at Tornado’s discretion, 6 months after
the dealer purchased the unit from Tornado, whichever comes rst.
4. The EB 30 is warranted for a period of 90 days for both parts and labor.
5. The warranty on engines used on propane powered equipment is limited to motor manufacturer’s
warranty.
6. Ride-on Scrubbers are warranted for 24 months, parts, 6 months labor or 1,000 hours, whichever
occurs rst.
Note: Tornado, The Latest Dirt, Floorkeeper,
Carpetkeeper, Carpetrinser, Carpetrinser/Dryer,
Headmaster, Taskforce, PAC-VAC, T-Lite, Glazer,
Windshear, Max-Vac and Trot-Mop are trademarks
of Tornado Industries
Website: www.tornadovac.com
Phone 1-800-VACUUMS
Fax 817-551-0719
Address 3101 Wichita Court
Fort Worth, TX 76140
Form F2662.©2017. All rights reserved
1-800-VACUUMS 90 Years of Cleaning Innovation A Tacony Company
https://harrissupplyind.com-ToOrderPartsCall608-268-8080

3
NOTES
https://harrissupplyind.com-ToOrderPartsCall608-268-8080

4
SUMMARY
LEGEND PANEL OF CONTROLS 5
LEGEND MACHINE 6
TECHNICAL DESCRIPTION 7
INTRODUCTORY COMMENT 8
GENERAL RULES OF SECURITY 8
SYMBOLOGY 9
OPTIONAL ACCESSORIES 9
BEFORE USE 10
Handling of the packed machine 10
Unpacking of the machine 10
Access to the battery compartment 10
Battery installation and setting of
the battery type 10
Assembling of the rollbar 10
Battery recharger 10
Batteries recharging 10
Batteries disposal 10
Connection battery connector
and switching on of the machine 11
Batteries charge level indicator 11
Hour meter 11
Squeegee assembly 11
Adjustment of the squeegee 11
Adjustment side rubbers 12
Brushes assembly and disassembly 12
Side brush assembly and disassembly 13
FLOOR CLEANING 13
Recovery tank 13
Detergent solution tank 13
STARTING OF THE MACHINE 13
Forward and backward movement 14
Horn 14
Working brake 14
Emergency-parking brake 14
Automatic squeegee lifting
when going backwards 14
Working in automatic mode 15
Working in manual mode 15
Side brush 16
Working adjustments 16
Flow adjustment of the detergent
solution 16
Adjustment of the brushes pressure 16
Electric protection 16
Overow device 17
STOP OF THE MACHINE
AFTER CLEANING OPERATION 17
DAILY MAINTENANCE 17
Recovery tank emptying and cleaning 17
Emptying and cleaning of the
collection box 17
Suction lter cleaning 18
Brushes cleaning 18
Squeegee cleaning 18
WEEKLY MAINTENANCE 18
Rear squeegee rubber check 18
Check of the side rubbers 19
Squeegee hose cleaning 19
Cleaning of the solution tank
and of the outer lter 19
TWO-MONTHLY MAINTENANCE 19
Front squeegee rubber check 19
SIX-MONTHLY MAINTENANCE 19
Splash guard rubber check of the
side brush 19
Check of the brakes 19
TROUBLESHOOTING GUIDE 19
The suction motor does not work 19
The brushes motor does not work 20
The traction motor does not work 20
The water does not come down
onto the brushes or is insufcient 20
The machine does not clean properly 21
The squeegee does not dry perfectly 21
Excessive foam production 21
PROGRAMMED MAINTENANCE 22
RECOMMENDED BRUSHES 22
https://harrissupplyind.com-ToOrderPartsCall608-268-8080

5
LEGEND CONTROL PANEL
1.DISPLAY VISUALIZATION
2.PUSH BUTTON VISUALIZATION HOUR METER (DIS-
PLAY)
3.PUSH BUTTON VISUALIZATION BRUSHES PRES-
SURE SET (DISPLAY)
4.ADJUSTMENT SELECTOR BRUSHES PRESSURE
5.KEY SWITCH
6.PUSH BUTTON HORN
7.CONTROL PANEL FUNCTIONS
8.SELECTOR FORWARDS/BACKWARDS
9.SELECTOR SPEED
10.SOLUTION VALVE LEVER
11.SWITCH WATER OPENING (SOLENOID VALVE)
12.SELECTOR MODE OF FUNCTIONING
13.SWITCH SIDE BRUSH ACTIVATED
14.SELECTOR UP/DOWN BRUSHES
15.SELECTOR UP/DOWN SQUEEGEE
16.SWITCH SUCTION MOTORS
17.SIGNAL LAMP PARKING BRAKE ON
18.SIGNAL LAMP SUCTION MOTORS ON
19.SIGNAL LAMP DETERGENT SOLUTION LOW
20.SIGNAL LAMP RECOVERY TANK FULL
21.SIGNAL LAMP SQUEEGEE DOWN
22.SIGNAL LAMP BRUSHES DOWN
23.SIGNAL LAMP BRUSHES ROTATION
24.SIGNAL LAMP WATER OPEN (SOLENOID VALVE)
25.SIGNAL LAMP SIDE BRUSH ACTIVATED
26.SIGNAL LAMP RESTORATION LIQUID LEVEL
BRAKES
https://harrissupplyind.com-ToOrderPartsCall608-268-8080

6
LEGEND MACHINE
1.RECOVERY TANK
2.SOLUTION TANK
3.SEAT
4.DRIVE WHEEL
5.SCREW CAP FOR INLET DETERGENT SOLUTION
6.BLINKING LIGHT
7.ROLLBAR
8.INSPECTION CAP RECOVERY TANK
9.SQUEEGEE HOSE
10.PLUG EXHAUST HOSE RECOVERY TANK
11.EXHAUST HOSE RECOVERY TANK
11.EXHAUST HOSE RECOVERY TANK
12.SQUEEGEE ASSEMBLY
13.PANEL CONTROLS
14.LEVER BLOCK/RELEASE PARKING BRAKE
15.COVER ELECTRICAL LAYOUT
16.BUMPER
17.PEDAL ACCELERATOR
18.TRACTION MOTOR WHEEL
19.SIDE BRUSH
20.BOTTOM PLATE
21.BRUSHES BASE GROUP
22.REAR WHEELS
https://harrissupplyind.com-ToOrderPartsCall608-268-8080

7
TECHNICAL DESCRIPTION U/M BR 40/66
Cleaning width mm/in 1000/40
Squeegee width mm/in 1300/51
Working capacity, up to sqm/h/sqft/h 7000/75,347
Diameter front cylindrical brush mm/in 1506
Diameter rear cylindrical brush mm/in 280/11
Diameter side brush mm/in 285/11
Front brush rpm rpm 933
Rear brush rpm rpm 500
Side brush rpm rpm 200
Pressure on the cylindrical brushes kg/lbs 110/242 max
Pressure on the side brush kg/lbs 35/77
Brushes motor W/A 1800/50
Motor side brush W/A 150/4
Traction motor W/A 1200/33
Suction motors W/A 2x570/2x16
Suction vacuum mbar/in water lift 190/76
Type of drive autom.
Movement speed I-II km/h/mph 4.5-7/2.7-4.3
Maximum gradient % 10
Solution tank l/gal 235/62
Recovery tank l/gal 250/66
Machine length mm/in 2025/80
Machine height (without rollbar) mm/in 1330/53
Machine height (with rollbar and without blinking light) mm/in 1795/71
Machine height (with rollbar and blinking light) mm/in 1965/77
Machine width (without squeegee) mm/in 1165/46
Machine width with side brush in operating position mm/in 1250/49
Weight of the machine (empty and without batteries ) kg/lbs 670/1477
Capacity of the batteries Ah 5 500
Weight of the batteries kg/lbs 600/1323
Compartment of the batteries mm/in 655x640x530/26x25x21
Acoustic pressure level (in conformity with EN 60704-
1)
dB (A) <70
Class III
Protection level IP X3
Tension V 36
https://harrissupplyind.com-ToOrderPartsCall608-268-8080

8
INTRODUCTORY COMMENT
Your new Tornado unit is a high
quality, precision-made product.
All parts used in the manufac-
turing of this unit have passed
rigid quality control standards
prior to assembly. Please safe-
guard the original receipt /
invoice. If you experience any
problems with your unit during
the warranty period, the original
receipt / invoice will act as proof
of purchase. Contact Tornado
for any warranty inquiries.
GENERAL RULES OF SECU-
RITY
IMPORTANT SAFETY IN-
STRUCTIONS
READ AND UNDERSTAND
ALL INSTRUCTIONS BEFORE
USING THIS UNIT
Read and understand this own-
er’s manual and all labels on
the unit before operating. Safety
is a combination of common
sense,staying alert and knowing
how your unit works. Use this
unit only as described in this
manual. Use only manufactur-
er’s recommended attachments.
To reduce the risk of personal
injury or damage to your unit
use only Tornado recommended
accessories.
The rules below have to be fol-
lowed carefully in order to avoid
damages to the operator and to
the machine.
-Read the labels carefully on the
machine. Do not cover them for
any reason and replace them
immediately if damaged.
-The machine must be used ex-
clusively by authorized staff that
have been instructed in its use.
-During the use of the machine,
pay attention to other people
and especially to children.
-In case of danger act imme-
diately upon the emergency
brake.
-Leaving the machine in parking
position, take off the key and act
upon the parking brake.
-Do not mix different detergents,
avoiding harmful odours.
-Storage temperature: between
-77°F and 131°F (25°C and
+55°C).
-Perfect operating temperature:
between 32°F and 104°F (0°C
and40°C).
-The humidity should be be-
tween 30 and 95%.
-Do not use the machine in ex-
plosive atmosphere.
-Do not use acid solutions which
could damage the machine and/
or persons.
-Do not use the machine on sur-
faces covered withi nammable
liquids or dusts (for example
hydrocarbons, ashes or soot).
-In case of re, use a powder
re-extinguisher.
Do not use water.
-Do not strike shelvings or scaf-
foldings, where there is danger
of falling objects.
-Adapt the working speed to the
adhesion conditions: particu-
larly, slow down before narrow
curves have to be faced.
-Do not use the machine on
areas having a higher gradient
than the one stated on the num-
ber plate.
-The machine has to carry out
simultaneously the operations
of washing and drying. Different
operations must be carried out
in restricted areas prohibited
to non-authorized personnel.
Signal the areas of moist oors
with suitable signs.
-If the machine does not work
properly, check by conducting
simple maintenance proce-
dures. Otherwise, ask for tech-
nical advice from an authorized
assistance centre.
-Where parts are required, ask
for ORIGINAL spare parts from
an authorized dealer.
-Use only ORIGINAL brushes
indicated in the paragraph
“RECOMMENDED BRUSHES".
-For any cleaning and/or main-
tenance operation take off the
power supply from the machine.
-Do not take off the protections
which require the use of tools to
be removed.
-Do not wash the machine with
direct water jets or with high wa-
ter pressure nor with corrosive
material.
-Every 200 working hours have
a machine check through an
authorized service department.
-In order to avoid scales on the
solution tank lter,do not ll the
detergent solution many hours
beforethe machines’ use.
-Before using the machine,
check that all panels and cov-
erings are in their position as
indicated in this use and main-
tenance manual.
-Restore all electrical connec-
tions after any maintenance
operation.
-Provide for the scrapping of the
material of normal wear follow-
ing strictly the respective rules.
-When, your machine has to
stop activity, provide for the
appropriate waste disposal
of its materials,especially
oils, batteries and electronic
components,and considering
that the machine itself has,
where possible, been construct-
ed using recyclable materials.
https://harrissupplyind.com-ToOrderPartsCall608-268-8080

9
Symbol denoting the switch
for the water opening and
the signal lamp that the
water is open.
Symbol denoting the func-
tioning of the solution valve
adjusting the ow of the
detergent solution.
Indication of the maximum
temperature of the detergent
solution. It is placed near the
charging hole of the solution
tank.
Symbol denoting the selec-
tion of the operation mode
in manual.
Symbol denoting the selec-
tion of the operation mode
in automatic.
Symbol denoting the selec-
tion of the mode at the end
of the washing and transfer.
Symbol denoting the activa-
tion and the signal lamp
brushes down.
Symbol denoting the activa-
tion of the brushes up.
Symbol denoting the activa-
tion and the signal lamp of
the side brush.
Symbol denoting the signal
lamp of the brushes rotation.
Symbol denoting the push
button to visualize on the
display the brushes pres-
sure set.
Rollbar lowered of 120 mm
Movable working lights
OPTIONAL ACCESSORIES
Symbol denoting the
functioning of the adjust-
ment selector of the
brushes pressure.
Symbol denoting the acti-
vation and the signal lamp
squeegee down.
Symbol denoting the acti-
vation of the squeegee up.
Symbol denoting the
switch and the signal lamp
of the functioning of the
suction motors.
Symbol denoting the
charge level of the batter-
ies.
Symbol denoting the push
button to visualize the hour
meter on the display.
Symbol denoting the selec-
tion of the forward/back-
ward movement.
Symbol denoting the
selection switch of the
operation speed.
Symbol denoting the
signal lamp of the parking
brake on.
Symbol denoting the key
switch.
Symbol denoting the push
button of the horn.
Symbol denoting the sig-
nal lamp of low detergent
solution.
Symbol denoting the
signal lamp of overow of
the recovery tank.
Symbol denoting the
signal lamp of restoration
level liquid brakes.
Symbol denoting the
open book. Indicates that
the operator has to read
the manual before the
use of the machine.
Warning symbol.
Read carefully the sec-
tions marked with this
symbol, for the security of
both the operator and the
machine.
https://harrissupplyind.com-ToOrderPartsCall608-268-8080

10
BEFORE USE
HANDLING OF THE PACKED MACHINE
The machine is supplied with suitable
packing for fork lift truck handling.
The total weight is 1587 lbs.720 kg.
Packing dimensions:
Base: 84” x 50” 213 cm x 125 cm
Height: 65” 165 cm
ATTENTION:
Do not place any packings on top.
UNPACKING OF THE MACHINE
1. Remove the external packing.
2. Move the machine backwards, as
indicated in the gure, avoiding heavy
contacts to mechanical parts.
3. Keep the pallet for further transport.
ACCESS TO THE BATTERY COMPART-
MENT
1. Bring the machine on a level surface.
2. Rotate the seat platform forward up to
the blocking of the support arm.
3. When completed, close the battery com-
partment, after releaseing the support arn,
reposition the seat platform.
BATTERY INSTALLATION AND SETTING
OF THE BATTERY TYPE
The machine is equipped either with bat-
teries in serial connection or elements of
DIN-type assembled together and connect-
ed in series for a total of 36 Volt, placed
in its appropriate compartment under the
seat platform and must be handled using
suitable lifting equipment (due to weight,
considering the type of batteries chosen,
and coupling system).
The batteries must be in accordance with
CEI 21-5 Norms.
ATTENTION:
The machine and its battery check card
are factory set for the use of traditional
lead batteries.
CHECK THE SETTING OF THE CHECK
CARD (see under paragraph "BATTER-
IES CHARGE LEVEL INDICATOR").
In case of GEL batteries installation, it is
necessary to set the battery check card.
Please contact the authorized technical
assistance.
ATTENTION:
Strictly follow manufacturer/distributor
indications for the maintenance and re-
charge of the batteries. All installation and
maintenance operations must be executed
by specialized staff, using suitable protec-
tion accessories.
For batteries installation it is necessary to
reach the battery compartment as indi-
cated under paragraph “ACCESS TO THE
BATTERY COMPARTMENT”.
1. Place the batteries in its compartment.
2. Connect the terminals, respecting the
polarities, avoiding contact with other
parts that could create short circuit.
ASSEMBLING OF THE ROLLBAR
For packing reasons the support of the
blinking light is supplied disassembled.
Proceed as follows:
1. Take off the four xing screws (1) from
the rollbar.
2. Place the rollbar into their seats (2) on
the tank.
3. Fasten the screws passing them in the
same order in their holes foreseen on the
support.
4. Complete the assembly connecting the
connectors (3) to supply the blinking light
and the working lights (optional).
BATTERY CHARGER
Make sure that the battery charger is
suitable for the installed batteries both
for their capacities and type (lead/acid
or GEL and equivalent).
In the plastic bag containing the use and
maintenance you will nd the coupling
connector for the charger. It must be as-
sembled onto the cables of your charger,
following the instructions given by the
manufacturer.
ATTENTION:
This operation must be carried out by
qualied staff. A wrong or faulty cable
connection can cause serious damages to
persons or equipment.
BATTERIES RECHARGING
1. Plug the connector (3) of the battery
charger into the battery connector.
2. Proceed with the charging.
ATTENTION:
Never charge a GEL battery with a non
suitable charger. Strictly follow the
instructions supplied by the batteries
and charger manufacturer.
In order not to cause permanent damages
to the batteries, it is necessary to avoid
their complete discharge, providing for the
charging within a few minutes after the
batteries discharge signal starts blinking.
NOTE: Never leave the batteries com-
pletely discharged even if the machine is
not used. In case of traditional batteries,
please check the electrolyte level every 20
charging cycles and eventually top them
up with distilled water. Never leave the
batteries discharged for more than two
weeks.
ATTENTION:
For the recharge of the batteries it is nec-
essary to follow strictly all the indications
given by the manufacturer/distributor. All
the installation and maintenance opera-
tions must be carried out by qualied staff.
Danger of gas exhalations and emis-
sion of corrosive liquids. Fire danger:
do not approach with free ames.
BATTERIES DISPOSAL
It is compulsory to hand over exhausted
batteries, classied as dangerous waste,
to an authorized institution according to
the current laws.
https://harrissupplyind.com-ToOrderPartsCall608-268-8080

11
CONNECTION BATTERY CONNECTOR
AND SWITCHING ON OF THE MACHINE
Once the battery recharging has been
completed:
1. Disconnect the connector of the battery
charger from the battery connector (1).
2. Connect then the battery connector (1)
to the machine connector (2).
To start any function of the machine, it
is necessary to rotate clockwise the key
switch (5). Rotating it counterclockwise
any function will be switched off.
BATTERIES CHARGE LEVEL INDICA-
TOR
WHEN THE MACHINE IS SWITCHED
ON, ON THE DISPLAY (1) APPEAR
IN ORDER THE FOLLOWING INFOR-
MATION:
1. the version (for example A003) of soft-
ware installed on the machine.
2. the setting of the battery check card
which can be:
GE 36: check card set for GEL batteries.
or
Pb 36: check card set for lead batteries.
ATTENTION:
After a few seconds of the indication 10%
and after this, the blinking of the four lines,
all the functions stop automatically. With
the remaining charge it is anyhow pos-
sible to nish the drying operation before
proceeding to the charge station.
3. The batteries charge level indicator is
digital and remains xed on the display.
The battery charge level starts from 100,
which indicates the 100% of the total
charge and decreases by 10 to 10. When
the charge level reaches 20%, the display
starts blinking, so you are about the end of
working.
SQUEEGEE ASSEMBLY
1. Insert the two screws (3) situated on the
upper part of the squeegee (2) inside the
slots present on the support.
2. To block the squeegee tighten the stud
bolts (3).
3. Insert the squeegee hose (4) into its
coupling, respecting its position as indi-
cated in the gure.
ADJUSTMENT OF THE SQUEEGEE
In order to have a perfect drying result
through the squeegee, the rear rubber
must have the lower bending uniformly ad-
justed in all its length. For the adjustment,
the suction motor has to be switched on
and the brushes have to function together
with the detergent solution.
If the lower part of the rubber is bent too
much
Take off the pressure rotating the wing nut
(5) counterclockwise.
If the lower part of the rubber is not bent
enough
Increase the pressure rotating the wing nut
(5) clockwise. Check that the wheels which
adjust the height do not rest on the oor,
in this case adjust them as indicated in
paragraph "Height adjustment".
If the bending is not uniform
Adjust the squeegee inclination rotat-
ing counter-clockwise the wing nut (6) to
increase the bending in the central part, or
clockwise to increase the bending on the
ends.
Height adjustment
Once the pressure and inclination of the
squeegee have been adjusted, it is neces-
sary to x this optimum condition and
make the wheels slightly touch the oor.
Rotate clockwise the registers (7) to lower
the wheels or counterclockwise to raise
them. Both wheels must be adjusted the
same. To act upon the register (7) loosen
at the same time the two milled ring nuts,
adjust the height acting on the upper one
and then x the adjustment screwing and
blocking the lower one.
HOUR METER
The machine is equipped with an hour
meter located on the same display (1) of
the battery charge level indicator. Pressing
the button (2), the rst data indicates the
working hours and after a few seconds the
working minutes are shown.
https://harrissupplyind.com-ToOrderPartsCall608-268-8080

12
ATTENTION:
Every type of oor requires a specic
adjustment. For example, concrete oors
(where the friction tends to be high) need
little pressure, while smooth oors (ceram-
ics) need higher pressure.
If the cleaning operations are always made
on the same type of oor, the adjustment
only needs to be made as a result of the
rubber wear.
ADJUSTMENT SIDE RUBBERS
To adjust the side rubbers, it is necessary
to act upon the knob (1). Screwing down,
more pressure is given and unscrewing,
pressure is being taken off. The reason
for the adjustment is to obtain an uniform
rubber bending.
NOTE: If the rubber should lower in the
rear part, it is necessary to restore the cor-
rect bending by acting upon the screw (2).
BRUSHES ASSEMBLY AND DISASSEM-
BLY
Normally, the machine is delivered with the
brushes assembled.
To assemble and disassemble the brush-
es:
1. Position the selector (4) for the adjust-
ment of the brushes pressure on position
P1.
2. Activate the machine (see under para-
graph “STARTING OF THE MACHINE”)
positioning the selector (12) to the right to
choose the manual mode (MAN).
3. Activate the selector (14) of up/down
of the brushes base to lower the brushes.
Once that it is lowered, the brushes begin
to turn.
4. Turn the key counterclockwise to turn off
the machine.
ATTENTION:
To carry out brushes assembly operations
with the electric supply on, may cause
damages to hands.
ATTENTION:
This operation must be carried out using
gloves to protect from contact with danger-
ous solutions.
5. Open the bar of the right side rubber
after having released it pulling the stop (1)
upwards.
6. Take off the stop (2) then unscrew and
take off the knob so to open the blocking
support as shown in the gure.
7. Extract the support plates (3) and (4)
of the brushes pulling them outwards by
holding their handles.
8. Extract the rear brush (5) and the front
brush (6).
9. When reassembling the rear brush (5)
pay attention to the bristles design, so that
it will be assembled always in the same
direction as shown in the gure.
https://harrissupplyind.com-ToOrderPartsCall608-268-8080

13
10. During the reassembly of the brush
(6), insert it into the brush base from the
part where the seat is deeper (about 1.5”
40mm). The opposite part with a depth of
about .5” 13,5mm has to be towards the
support plate.
11. Place the support plates (3) and
(4) into their position, then the blocking
support, screw down the knob and insert
once more the stop (2) and nally reposi-
tion and block the bar of the side rubber
through the stop (1).
ATTENTION:
The brushes must be inserted easily with-
out using tools in order not to damage or
force them.
Use only brushes supplied with the ma-
chine or the ones indicated in the para-
graph “RECOMMENDED BRUSHES”. The
use of other brushes can compromise the
washing result.
SIDE BRUSH ASSEMBLY AND DISAS-
SEMBLY
The machine is equipped with a side brush
that permits the unit to clean near the right
side borders.
To assemble the brush, the device has to
be in rest position at machine stop.
ATTENTION:
To carry out brushes assembly operations
with the electric supply on, may cause
damages to hands.
ATTENTION:
This operation must be carried out using
gloves to protect from contact with danger-
ous solutions.
1. Keep the push button (1) pressed that
blocks the rotation of the brush plate.
2. Insert the brush into its plate seat un-
derneath the brush base turning it until the
three metal buttons are properly seated
in their slots; rotate the brush to push the
button towards the coupling spring until it
gets blocked.
The gure shows the rotating direction for
the brush coupling. To release it, rotate the
opposite direction.
FLOOR CLEANING
RECOVERY TANK
Verify that the squeegee hose couplings
(1/2) are correctly inserted into their seats
and that the exhaust hose plug (4) placed
in the rear part of the machine is well
closed.
Check that the inspection cap (3) placed
on the upper part of the tank is well closed.
Finally, verify the correct tightening of the
closing lever (5) of the cleaning door (6)
placed in the lower part of the tank.
DETERGENT SOLUTION TANK
The capacity of the detergent solution tank
is indicated in the technical data.
Open the screw plug placed in the left part
of the machine and ll the detergent solu-
tion tank with clean water at a maximum
temperature of 122°F 50°C. Add the liquid
detergent in the percentage and conditions
foreseen by the manufacturer. To avoid ex-
cessive foam presence, which could cause
problems to the suction motors, use the
minimum percentage of detergent. Screw
down the plug to close the solution tank.
The switching on of the signal lamp of low
detergent (19) indicates that the detergent
solution is nearly exhausted.
ATTENTION:
Always use low foam detergent. To avoid
excessive foam, before begining operation,
introduce into the recovery tank a minimum
quantity of anti-foam product.
Never use pure acid.
STARTING OF THE MACHINE
A safety device avoids the machine’s
movement if the operator is not seated
correctly.
To switch on the machine:
1. Sit on the seat.
2. Turn the key switch (5) clockwise to
switch on the machine.
3. Check the charge level of the batteries
on the display (1).
4. With the selector (12) in central position
(BREAK WASHING) the transfer opera-
tions of the machine are carried out (see
under paragraph “FORWARD AND BACK-
WARD MOVEMENT").
5. Moving the selector (12) to the left, the
automatic (AUTO) functioning is chosen.
Moving it to the right, the functioning of the
machine becomes manual (MAN):
A. If the selector (12) is in position (AUTO)
the machine activates and deactivates
all the working functions in an automatic
mode (see under paragraph “WORKING
IN AUTOMATIC MODE”).
B. If the selector (12) is in position (MAN)
every function of the machine has to be
activated or deactivated manually (see
under paragraph “WORKING IN MANUAL
MODE”)
https://harrissupplyind.com-ToOrderPartsCall608-268-8080

14
FORWARD AND BACKWARD MOVE-
MENT
It is recommendable to always carry out
the mere transfer of the machine in mode
(BREAK WASHING).
To proceed to activate the movement of
the machine:
1. Sit on the seat.
2. Turn the key switch (5) clockwise to
switch on the machine.
3. Check the charge level of the batteries
on the display (1).
4. Release the parking brake. If the brake
was applied, the signal lamp (17) would
be switched on (see under paragraph
"EMERGENCY-PARKING BRAKE”).
5. Bring the selector (12) in central posi-
tion (BREAK WASHING) to carry out the
mere transfer of the machine. In fact, in
this mode the washing functions of the ma-
chine are not working and only the traction
system functions.
6. Select the driving direction with the
selector (8).
7. Press the accelerator pedal placed on
the right side to start the machine.
8. Adjust the driving speed in forward
choosing the slow one (at the maximum
you can reach 2.8 mph 4.5 km/h) or, press-
ing the same selector (9) upwards, the
faster one (at the maximum you can reach
4.3 mph 7 km/h) can be obtained.
In backward movement, when the machine
is moving, an intermittent warning device is
activated.
9. The machine is equipped with an auto-
matic system that reduces the speed when
the drive direction is changed. The speed
reduction is higher as the curve is sharper.
The speed returns again normally as soon
as the machine gets out from the curve
and it runs along straight paths.
HORN
The machine is equipped with a horn
which is activated pressing the push button
(6).
WORKING BRAKE
The machine is equipped with a hydrau-
lic braking system that acts on the rear
wheels.
To brake it is sufcient to press the pedal
placed at the left side of the steering col-
umn while releasing the accelerator pedal.
EMERGENCY-PARKING BRAKE
In case of an emergency pull the lever
of the emergency and parking brake (1)
placed on the left side of the seat.
On the instrument board the signal lamp
(17) comes on which signals that the park-
ing brake is applied.
To release the parking brake press the but-
ton (2) placed at the nal part of the brake
lever (1) and simultaneously lower it to the
end.
AUTOMATIC SQUEEGEE LIFTING
WHEN GOING BACKWARDS
When selecting the backwards movement
the squeegee is brought automatically to
the upper position. It will then lower again
in the following forward movement.
This happens both in automatic and in
manual mode in order to protect the integ-
rity of the squeegee.
https://harrissupplyind.com-ToOrderPartsCall608-268-8080

15
WORKING IN AUTOMATIC MODE
The automatic operation is useful to sim-
plify the operator’s work.
1.Activate the machine (see under
paragraph“STARTING OF THE MA-
CHINE”) putting the selector(12)into the
left position to choose the automatic func-
tion (AUTO).
2.Check that the lever (10) is in the posi-
tion of optimum ow, depending on the
type of oor and the type of dirt (see under
the paragraph “FLOW ADJUSTMENT OF
THE DETERGENT SOLUTION”).
3.Selecting the forward with the selector
(8), pressing the accelerator pedal and
adjusting the speed of the forward move-
ment with the selector (9), the machine
starts to move and in automatic mode all
the working functions are activated. In
fact, automatically both the brushes base
as the squeegee go down, the brushes
begin to turn, the solenoid valve opens to
permit the detergent solution to ow down
onto the brushes and the suction system
is activated to recover the dirty water from
the oor.
Selecting the backward movement with the
selector (8) the squeegee lifts automatical-
ly and will then return to lower itself during
the next forward movement.
If the accelerator pedal is released for
more than 3seconds, automatically all the
functions are switched off and both the
brushes base as the squeegee are lifted.
Pressing the pedal again, the machine
starts to move again and in automatic
mode all the working functions are reacti-
vated.
WORKING IN MANUAL MODE
The manual model is useful when, in
special cases, it is necessary to carry
out separately only the washing with the
brushes or only the drying of the oor.
ATTENTION:
The washing and drying functions, when
they are not carried out simultaneously,
represent an improper use of the machine
(see under paragraph “GENERAL RULES
OF SECURITY”). If they are carried out
separately, it is necessary to forbid the
working areas to the passage of non-au-
thorized personnel and to signal the areas
of moist oors with suitable signs.
Activate the machine (see under para-
graph “STARTING OF THE MACHINE”)
positioning the selector (12) to the right to
choose the manual mode (MAN).
TO CARRY OUT THE WASHING WITH
ONLY THE BRUSHES:
1.Activate the selector (14) of up/down of
the brushes base to lower the brushes.
Once that it is lowered, the brushes begin
to turn. The signal lamp (22) indicates that
the brushes base is in the working position,
while the signal lamp (23) signals that the
brushes are turning.
2.Press the switch (11) to open the sole-
noid valve and permit the detergent solu-
tion to lower onto the brushes. The signal
lamp (24) will come on to indicate that the
solenoid valve is open.
3.Check that the lever (10) is in the posi-
tion of optimum ow, depending on the
type of oor and the type of dirt (see under
the paragraph “FLOW ADJUSTMENT OF
THE DETERGENT SOLUTION”).
TO CARRY OUT THE FUNCTION OF
ONLY DRYING:
1.Activate the selector (15) of up/down
squeegee to lower the squeegee. The sig-
nal lamp (21) indicates that the squeegee
is in the working position.
2.Press the switch (16) of the suction mo-
tors to start the suction system. The signal
lamp (18) indicates that the machine is
drying.
Selecting the sense of drive in forward with
the selector (8), pressing the accelerator
pedal and adjusting the speed of the for-
ward movement with the selector (9), the
machine starts to proceed and in automatic
mode all the working functions previously
set are activated.
ATTENTION:
In manual mode every function of the
machine has to be activated or deactivated
manually.
https://harrissupplyind.com-ToOrderPartsCall608-268-8080

16
SIDE BRUSH
The machine is equipped with a side brush
that permits it to clean near the right side
borders.
The function is activated by acting upon
the switch (13) both in manual and in auto-
matic mode. The signal lamp (25) indicates
that the side brush is active and in the
working position.
WORKING ADJUSTMENTS
In both automatic and manual mode, dur-
ing the rst feet/metres check:
1. that the adjustment of the detergent
solution ow is sufcient to wet the oor
uniformly avoiding leakage of detergent
from the splash guards (see
under paragraph “FLOW ADJUSTMENT
OF THE DETERGENT SOLUTION”).
2. that the squeegee adjustment guar-
antees a perfect drying result (see under
paragraph “ADJUSTMENT OF THE
SQUEEGEE”).
3. that the brushes pressure permits an
efcient washing action as it relates to the
dirt and the speed (see under paragraph
“ADJUSTMENT OF THE BRUSHES
PRESSURE”).
FLOW ADJUSTMENT OF THE DETER-
GENT SOLUTION
To adjust the detergent solution quantity
that ows down onto the brushes it is nec-
essary to act upon the solution valve knob
(10) placed on the upper part of the side
instrument board, rotating counterclock-
wise to increase it and clockwise to reduce
it up to closure of the ow.
The side brush has an independent water
ow adjustment, with a solution valve (11)
placed under the frame near the brush
itself.
Please remember that the side brush does
not have a scrubbing function but simply
moves the dirt towards the center of the
machine.
ADJUSTMENT OF THE BRUSHES
PRESSURE
Both in automatic and in manual mode it is
possible through the selector (4) to adjust
the brushes pressure on the oor in eight
established levels. During the operation,
youcan visualize on the display (1) the
value of the brushes motor by pressing the
button (3).
ATTENTION:
In order not to overload the brushes motor,
it is convenient to reduce the brushes pres-
sure going from smooth oors to rough
ones (ex. concrete).
The presence on the display (1) of a
blinking warning from P2 to P8 indicates
that the pressure level set determines an
overload of the brushes motor. It is
therefore necessary to reduce the pressure
to the level where the blinking warning
stops
ELECTRIC PROTECTION
The machine is equipped with an electron-
ic system of protection for all components
that carry out functions of power or control.
This device blocks the defective compo-
nent and indicates on the display (1)
the corresponding alarm from ”AL01” to
“AL20”. The last two gures indicate the
number of the alarm code.
ATTENTION:
To restore the functioning of the compo-
nent, turn the machine off and on again us-
ing the key switch. If the problem persists,
please contact the authorized technical
assistance
https://harrissupplyind.com-ToOrderPartsCall608-268-8080

17
OVERFLOW DEVICE
In order to avoid serious damage to the
suction motors, the machine is equipped
with a oat that intervenes when the re-
covery tank is full, closing the suction, the
switching on of the signal lamp (20) for the
signalling of the full recovery tank and
consequently the drying to stop.
When this happens, it is necessary to emp-
ty the recovery tank (see under paragraph
“RECOVERY TANK EMPTYING AND
CLEANING”).
ATTENTION:
The mode (BREAK WASHING) is specic
for the transfer at the end of the cleaning
operation.
To start the cleaning operation again:
A. by positioning to the left the selector
(12) into position (AUTO) one can start
again to work in an automatic mode.
B. by positioning to the right the selector
(12) into position (MAN) the machine re-
establishes the functions pre-set manually.
STOP OF THE MACHINE AFTER
CLEANING OPERATION
IN AUTOMATIC OR MANUAL WORKING
MODE:
1. A the end of the washing cycle put
the selector (12) into the central position
(BREAK WASHING). In this way automati-
cally the brushes lift, the solenoid valve
shuts down and it is possible to nish the
drying operation.
2. When the accelerator pedal is released
for more than 3 seconds, the squeegee
raises itself and the suction switches off
automatically.
3. After three seconds, the accelerator can
be pressed again, if a machine's transfer
has to be made (the transfer can be car-
ried out also if the pedal is never lifted, in
this case the squeegee gets lifted and
the suction stop automatically after 15
seconds).
4. Turn the switch key counterclockwise to
switch off the machine.
5. Apply the parking brake (see under
paragraph “EMERGENCY-PARKING
BRAKE”).
DAILY MAINTENANCE
ATTENTION:
All the maintenance and cleaning opera-
tions that refer to the following components
that are in contact with liquids and there-
fore:
• solution and recovery tanks
• collection box
• solution and recovery lters
• squeegee with their rubbers and hoses
• brushes
must be carried out using gloves to protect
from contact with dangerous solutions.
RECOVERY TANK EMPTYING AND
CLEANING
1. Hold the exhaust hose (1) placed in the
rear part of the machine after having taken
it off from its xing support.
2. Take off the plug (2) from the exhaust
hose acting upon its lever (3) and empty
the recovery tank into appropriate contain-
ers, in compliance with the respective rules
for liquid disposal.
3. Unscrew and take off the upper inspec-
tion cap (4).
4. Rinse the inside of the tank with a water
jet through the inspection hole paying at-
tention to clean also the protection of the
oat switch placed right under the hole.
5. In case there should be solid waste or
encrustation on the bottom of the tank, it is
possible to use the lower cleaning door (6).
To open it, it is necessary to act upon the
lever (7) to release the closing bracket (8).
6. Reassemble all parts.
ATTENTION:
Do not open the lower cleaning door if
the recovery tank contains water, check
through the upper inspection cap that it is
empty.
EMPTYING AND CLEANING OF THE
COLLECTION BOX
The machine is equipped with a collection
box for the solid dirt.
At the end of the cleaning operation it is
necessary to empty and to clean it with a
water jet.
For the emptying and the cleaning of the
box it is convenient to bring the brushes
base in working position:
1. Position the selector (4) for the adjust-
ment of the brushes pressure on position
P1.
2. Activate the machine (see under para-
graph “STARTING OF THE MACHINE”)
positioning the selector (12) to the right to
choose the manual mode (MAN).
3. Activate the selector (14) of up/down of
the brushes base to lower the brushes.
https://harrissupplyind.com-ToOrderPartsCall608-268-8080

18
4. Turn the key counterclockwise to turn off
the machine.
ATTENTION:
To carry out above operations with the
electric supply on, may cause damages to
hands.
ATTENTION:
This operation must be carried out using
gloves to protect from contact with danger-
ous solutions.
5. Open the bar of the right side rubber
after having released it pulling the stop (1)
upwards (1).
6.Open the door (2).
7.Extract the box holding its handle (3). For
its handling, it is convenient to use the two
wheels present on the opposite part of the
handle.
8.Empty the box into appropriate contain-
ers, in compliance with the respective rules
for liquid disposal.
9.Put the collection box back into its posi-
tion paying attention to the correct placing
of the sliding rollers.
10. Close the door (2) and reposition the
bar of the side rubber.
SUCTION FILTER CLEANING
1.Rotate the seat platform forward up to
the blocking of the support.
2.Take off the upper hose (1).
3.Unhook the closing lever (2).
4.Take off the plate with the lters (3) and
wash it with care.
5.Reassemble all parts.
BRUSHES CLEANING
Disassemble the brushes and clean them
with a water jet (for the brushes disas-
sembly see under paragraph “BRUSHES
ASSEMBLY AND DISASSEMBLY" and
"SIDE BRUSH ASSEMBLY AND DISAS-
SEMBLY”).
ATTENTION:
To carry out brushes disassembly op-
erations with the electric supply on, may
cause damages to hands.
SQUEEGEE CLEANING
Keeping the squeegee clean guarantees
the best drying result.
For cleaning it is necessary to:
1.Take off the squeegee hose (4) from the
coupling.
2.Disassemble the squeegee (2) from its
support (1) loosening the stud bolts (3) and
then remove the squeegee.
3.Clean with care the internal part of the
squeegee inlet eliminating residual dirt.
4.Clean with care the squeegee rubbers.
5.Reassemble all parts.
WEEKLY MAINTENANCE
REAR SQUEEGEE RUBBER CHECK
Check the squeegee rubber for wear and
eventually turn or replace it.
For the replacement it is necessary to:
1.Take off the squeegee (see under
paragraph“SQUEEGEE CLEANING”).
2.Unscrew the screws (1) that block the
rubber blade and take off the rubber.
3.Turn the rubber to a new side or replace
it.
To reassemble the squeegee reverse the
above operations, inserting the rubber on
the guides and blocking it with the rubber
holder blade.
https://harrissupplyind.com-ToOrderPartsCall608-268-8080

19
CHECK OF THE SIDE RUBBERS
With the brushes assembled, the side rub-
bers must touch the oor. If they are worn,
they have to be replaced.
To replace the rubbers:
1.Open the bars of the right and left side
rubber after having released them by pull-
ing the stops (1) upwards.
2.Take off the xing screws (2) of the inner
rubber blades and replace the rubber.
4.Reassemble all parts.
SQUEEGEE HOSE CLEANING
Weekly or in case of insufcient suction, it
is necessary to check that the squeegee
hose is not obstructed. To clean it, proceed
as follows:
1.Take off the hose (1) from the squeegee
coupling.
2.Wash the inside of the hose with a water
jet.
3.To reassemble the hose reverse the
above operations.
CLEANING OF THE SOLUTION TANK
AND OF THE OUTER FILTER
1.Bring the machine to an appropriate
place for the detergent solution draining.
2.Unscrew the solution tank cap (1).
3.Unscrew the cap of the exhaust lter (2)
and take off the lter. Be careful not to lose
the gasket of the cap.
4.Open the solution valve adjustment (see
under paragraph “FLOW ADJUSTMENT
OF THE DETERGENT SOLUTION”), so
that the detergent solution ows down into
appropriate containers.
5.Rinse with a water jet the solution tank
and the components of the lter.
6.Reassemble all parts.
NOTE: If needed it is possible to wash only
the components of the outer solution lter
as mentioned above by closing the solution
valve adjustment (see under paragraph
“FLOW ADJUSTMENT OF THE DETER-
GENT SOLUTION”), so that the detergent
solution remains in the solution tank.
TWO-MONTHLY MAINTENANCE
FRONT SQUEEGEE RUBBER CHECK
Check the wear of the squeegee rubber
and eventually replace it.
For the replacement it is necessary to:
1.Take off the squeegee (see under para-
graph “SQUEEGEE CLEANING”).
2.Unscrew the wing nuts in the front part of
the squeegee.
3.Take off the rubber holder blade.
4.Replace the front rubber.
5.Reassemble all parts.
SIX-MONTHLY MAINTENANCE
SPLASH GUARD RUBBER CHECK OF
THE SIDE BRUSH
With the brush assembled, the splash
guard of the side brush must slightly touch
the oor. If the rubber is worn, it has to be
replaced.
The device has to be in rest position at
machine stop.
ATTENTION:
To carry out above operations with the
electric supply on, may cause damages to
hands.
To replace the rubber:
1.Take off the side brush (see under
paragraph“SIDE BRUSH ASSEMBLY AND
DISASSEMBLY”).
2.Take off the screws (1) that block the
rubber blade and replace the rubber.
3.Reassemble all parts.
CHECK OF THE BRAKES
Check the braking efcacy of both rear
wheels. Should the braking be insufcient,
please contact the authorized technical
assistance.
TROUBLESHOOTING GUIDE
NOTE: The machine is equipped with a
control system of the main functions with
indication on the display of a probable mal-
function with alarm codes: AL 01, AL 02,
etc. The alarm 20 is general and foresees
an additional check of the quantity of blink-
ings to be read on the led on the chopper
card.
ATTENTION:
If with the key switch positioned clock-
wise to switch on the machine the display
and other functions are not activated,
it is necessary to check the batteries'
connection to the machine (see under
paragraph “CONNECTION BATTERIES'
CONNECTION AND SWITCHING ON OF
THE MACHINE”). If the problem persists,
please contact the authorized technical
assistance.
THE SUCTION MOTOR DOES NOT
WORK
1.Verify that the key switch (5) is posi-
tioned clock-wise to switch on the ma-
chine. In presence of alarm signals it is
necessary to switch off and on again the
machine to restore the functionality.
2.Check the charge level of the batteries
on the display (1).
3.Verify having activated correctly the
function of drying (see under paragraph
“STARTING OF THEMACHINE”).
4.If, both in mode (MAN) and (AUTO),
the signal lamp (18) is on but the suction
system does not work,it is necessary to
check the connection of the suction motor
plugs situated in the compartment behind
the seat.
5.Check that the recovery tank is not full.
6.Check that the oat switch (2) in the
recovery tank is assembled correctly.
If the problem persists, please contact the
authorized technical assistance
https://harrissupplyind.com-ToOrderPartsCall608-268-8080

20
THE BRUSHES MOTOR DOES NOT
WORK
1.Verify that the key switch (5) is posi-
tioned clock-wise to switch on the ma-
chine. In presence of alarm signals it is
necessary to switch off and on again the
machine to restore the functionality.
2.Check the charge level of the batteries
on the display (1).
3.Verify having activated correctly the
function of washing with the brushes (see
under paragraph“STARTING OF THE
MACHINE”).
4.If, both in mode (MAN) and (AUTO), the
signal lamp (23) is on but the brushes do
not turn, please contact the authorized
technical assistance.
If the problem persists, please contact the
authorized technical assistance.
THE TRACTION MOTOR DOES NOT
WORK
1.Sit on the seat.
2.Verify that the key switch (5) is posi-
tioned clock-wise to switch on the ma-
chine. In presence of alarm signals it is
necessary to switch off and on again the
machine to restore the functionality.
3.Check the charge level of the batteries
on the display (1).
4.Check through the signal lamp (17) that
the parking brake is not applied (see under
paragraph “EMERGENCY PARKING
BRAKE”).
5.Check that the selector (8) is in the
movement position.
6.Press the accelerator pedal placed on
the right side to start the machine.
If the problem persists, please contact the
authorized technical assistance.
THE WATER DOES NOT COME DOWN
ONTO THE BRUSHES OR IS INSUFFI-
CIENT
1.Verify that the key switch (5) is posi-
tioned clock-wise to switch on the ma-
chine.
2.Check the charge level of the batteries
on the display (1).
3.Verify having activated correctly the
function of washing with the brushes (see
under paragraph“STARTING OF THE
MACHINE”).
4.Check that the solution valve is open
(see under paragraph “FLOW ADJUST-
MENT OF THE DETERGENTSOLU-
TION”).
5.If, both in mode (MAN) and (AUTO), the
signal lamp (24) is on but the detergent
solution does not come down onto the
brushes, it is necessary to:
a.check the level of the liquid in the tank.
b.check that the solution lter is clean (see
under paragraph “CLEANING OF THE
SOLUTIONTANK AND OF THE OUTER
FILTER”).
If the problem persists, please contact the
authorized technical assistance.
https://harrissupplyind.com-ToOrderPartsCall608-268-8080
Table of contents
Other Tornado Scrubber manuals

Tornado
Tornado BR 13/1 Manual
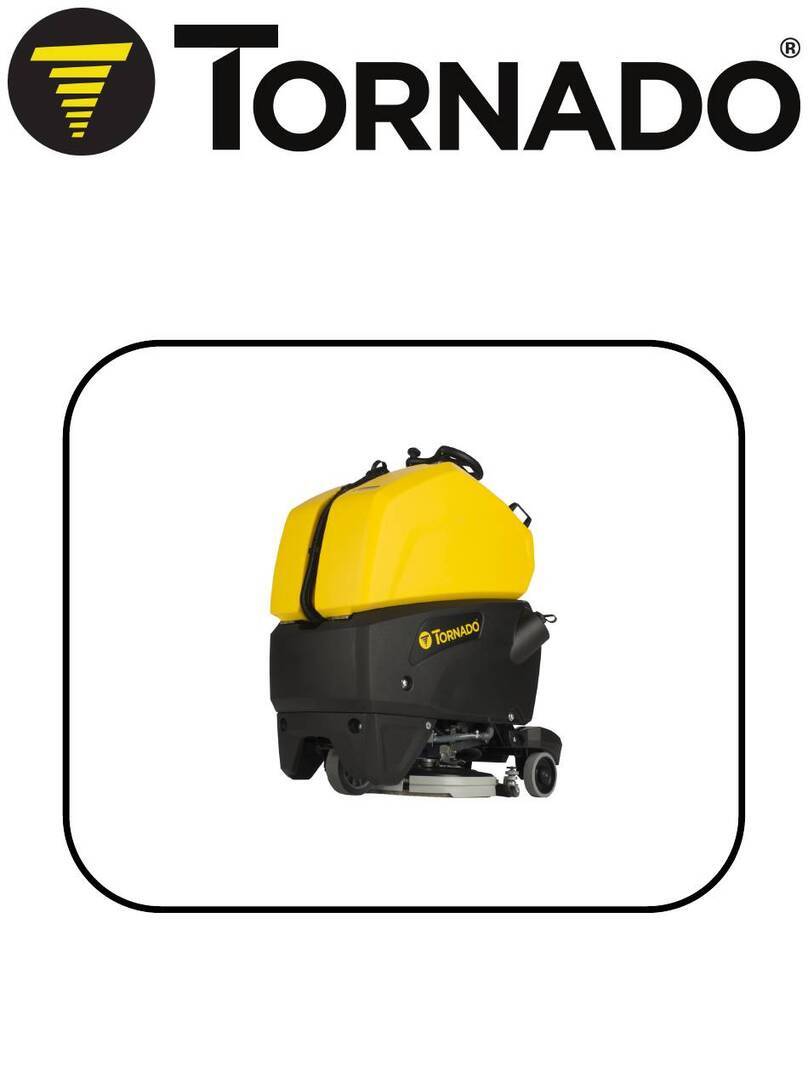
Tornado
Tornado TS120-S59-U User manual
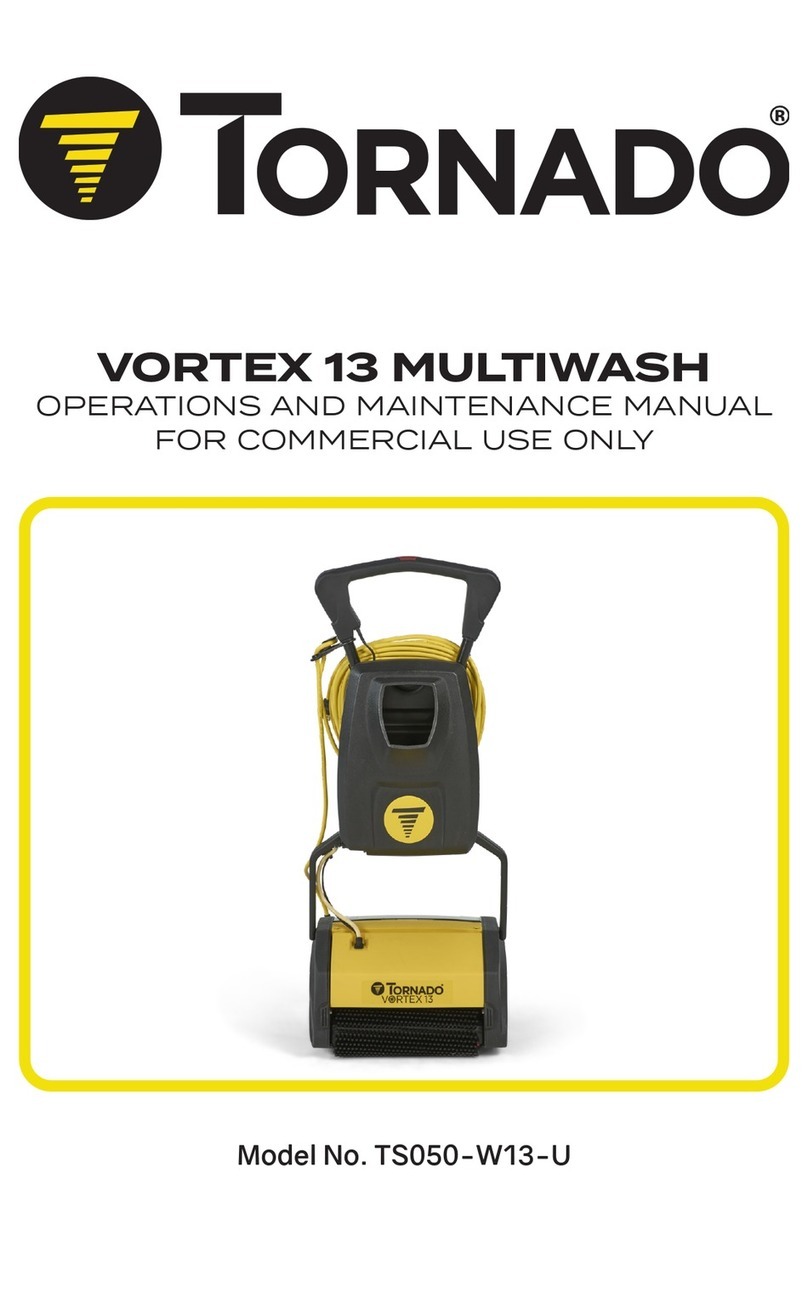
Tornado
Tornado VORTEX 13 MULTIWASH User manual
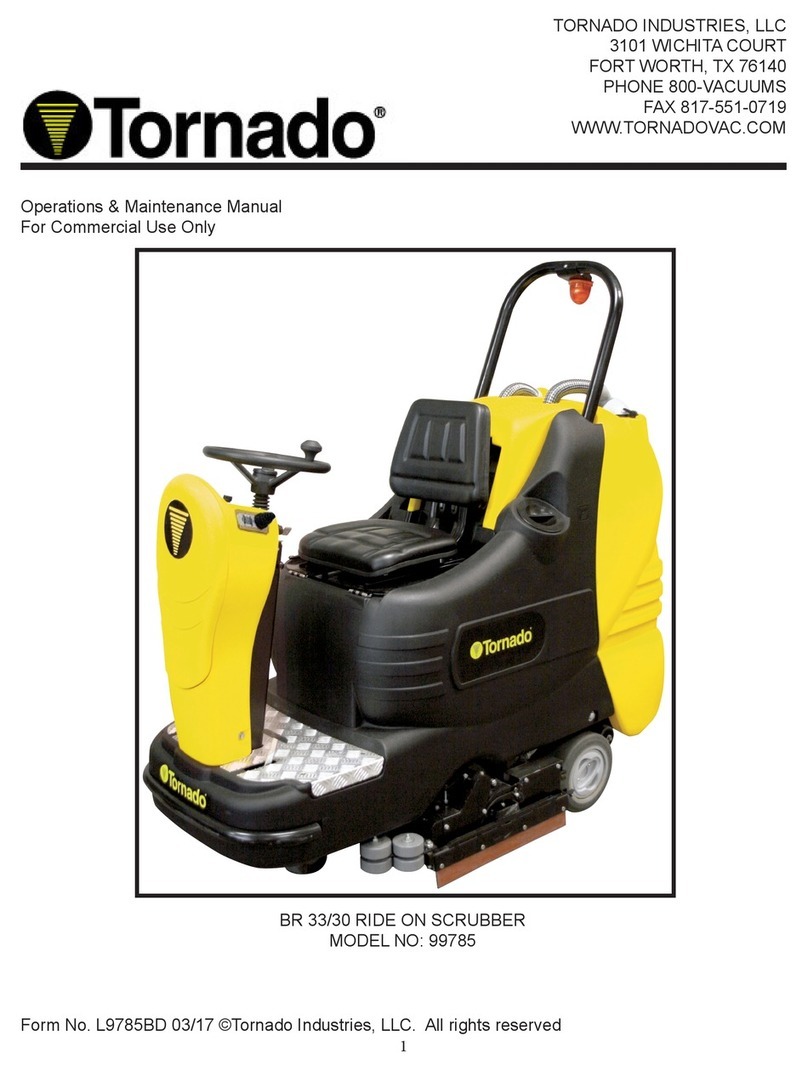
Tornado
Tornado BR 33/30 Manual
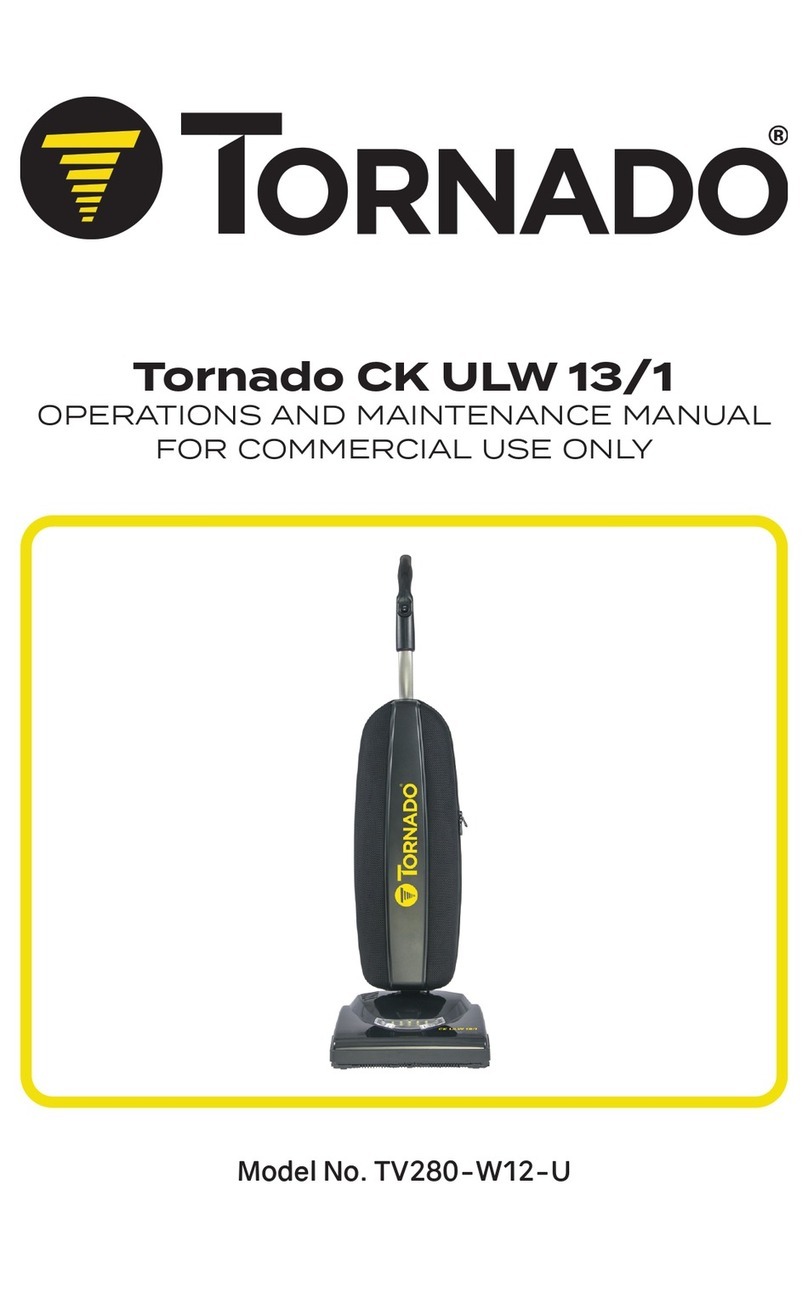
Tornado
Tornado CK ULW 13/1 User manual
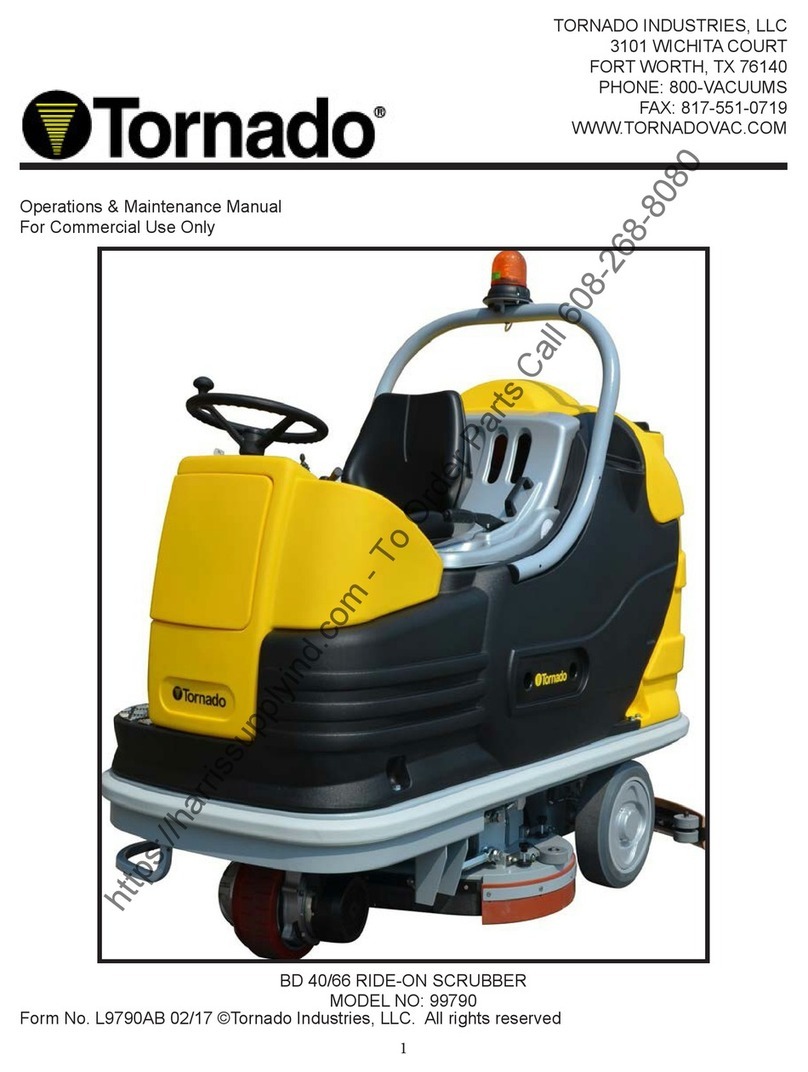
Tornado
Tornado 99790 Manual
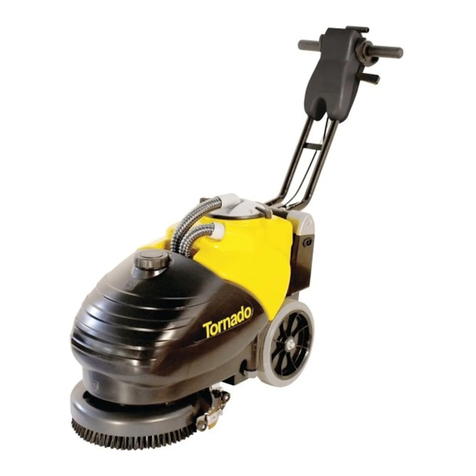
Tornado
Tornado ExSELLerate BD 14/4 Manual
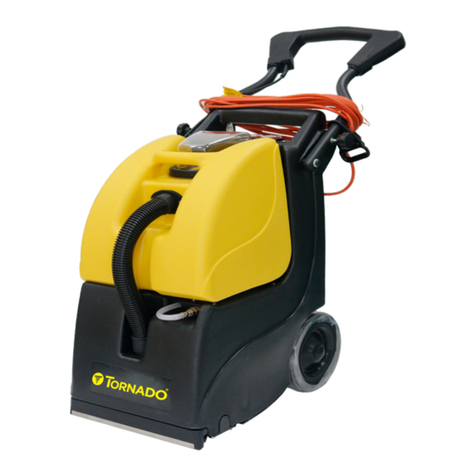
Tornado
Tornado 98103 Manual
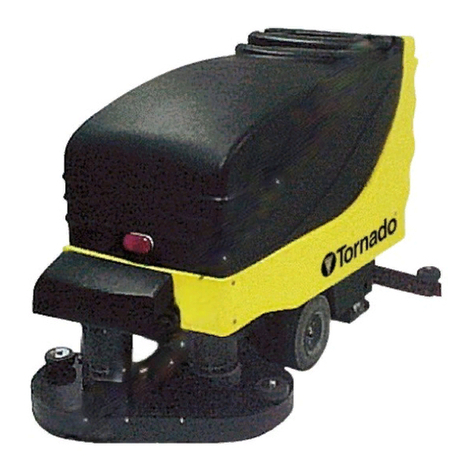
Tornado
Tornado Floorkeeper 99328 User manual

Tornado
Tornado BR 28/27 Manual
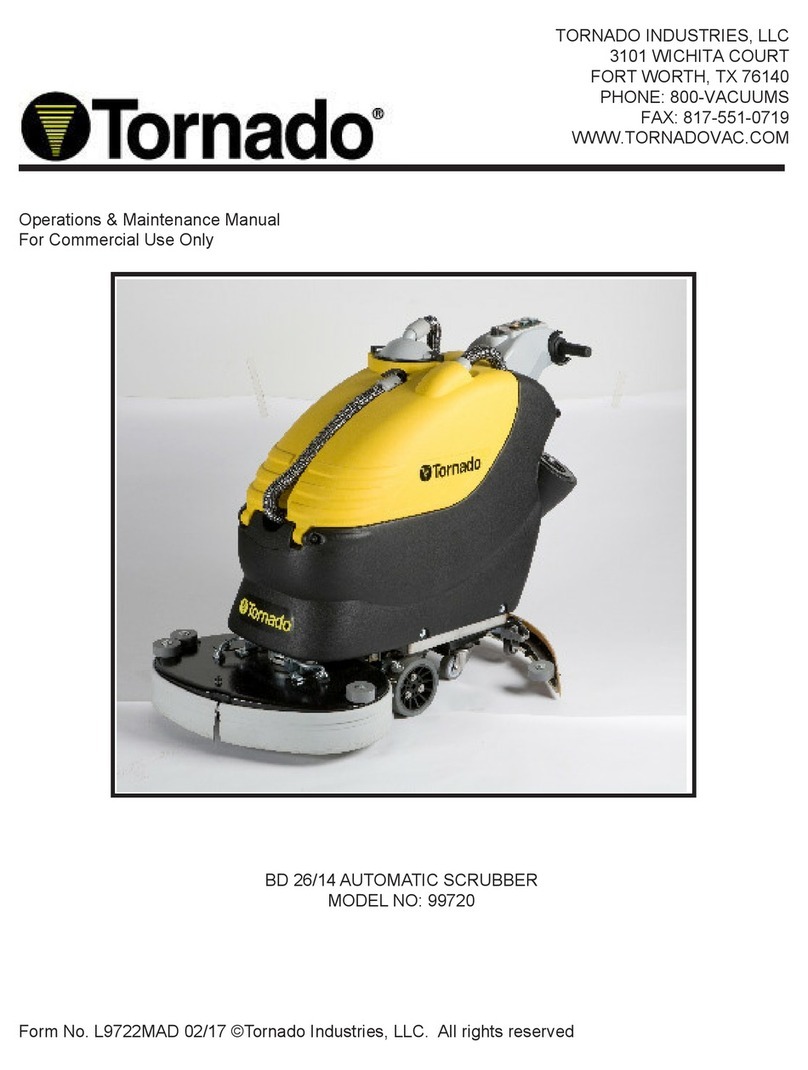
Tornado
Tornado BD 26/14 Manual

Tornado
Tornado ECO 500 AW Series Manual
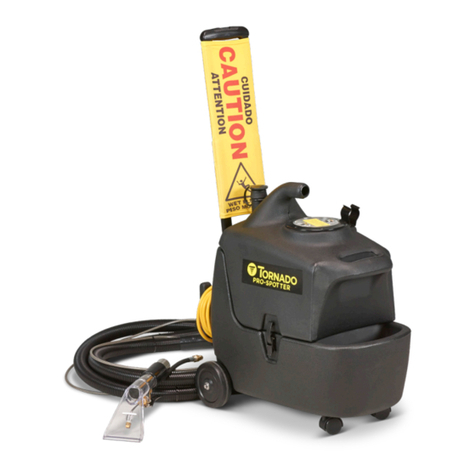
Tornado
Tornado TE010-G03-U User manual
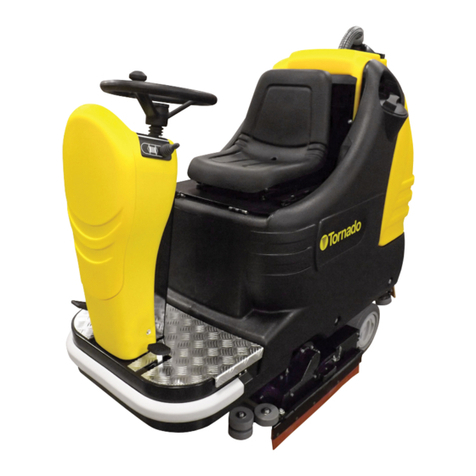
Tornado
Tornado BR 28/27 Manual

Tornado
Tornado 99680 BD 20/10 User manual
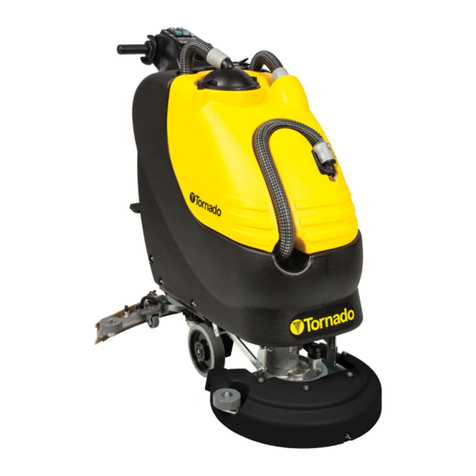
Tornado
Tornado BD 20/11L Manual
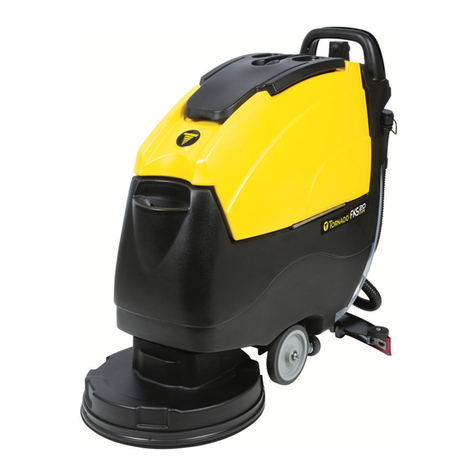
Tornado
Tornado Floorkeeper 20 PD/99120B Manual
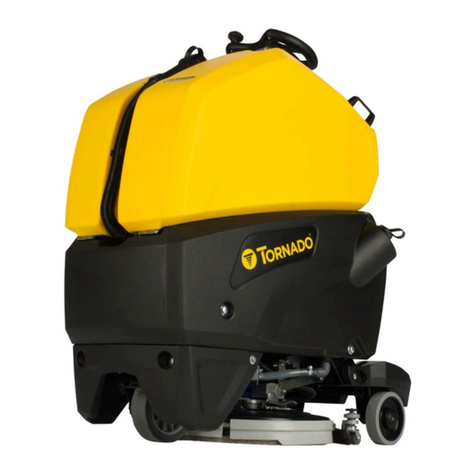
Tornado
Tornado BDSO 20/21 Manual
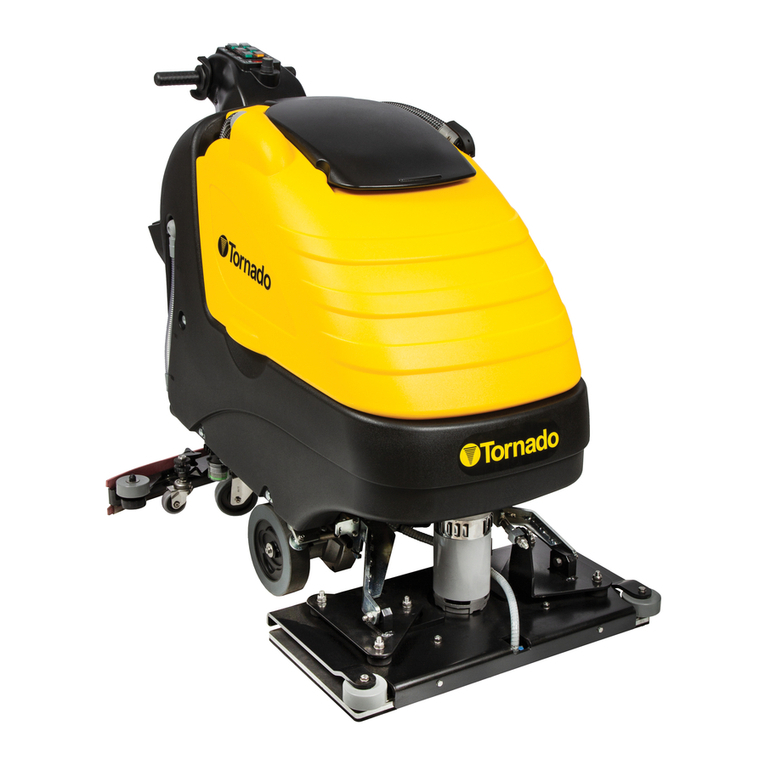
Tornado
Tornado OB 28/20 Manual

Tornado
Tornado 99772 Manual