Toshiba GRD130-210 User manual




















This manual suits for next models
1
Other Toshiba Relay manuals
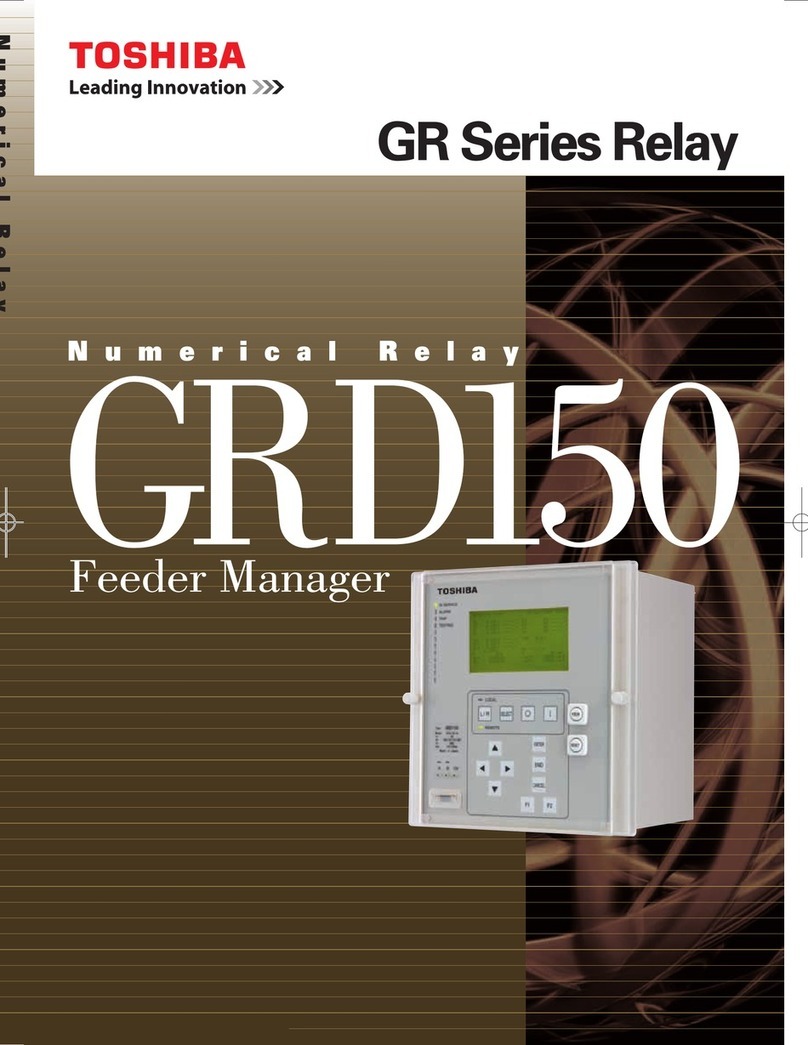
Toshiba
Toshiba GRD150 User manual

Toshiba
Toshiba GR 200 Series User manual

Toshiba
Toshiba GRT100 Series User manual
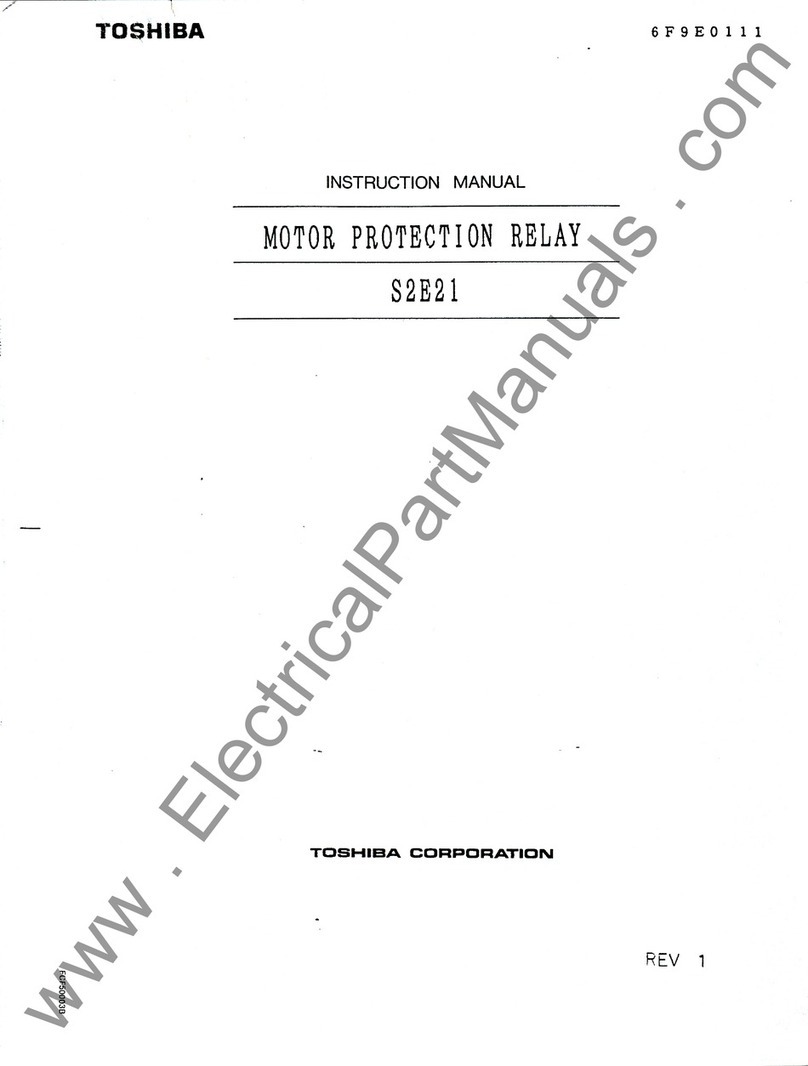
Toshiba
Toshiba S2E21 User manual

Toshiba
Toshiba GRD110 User manual

Toshiba
Toshiba GRZ100 User manual

Toshiba
Toshiba GRZ100-211B User manual
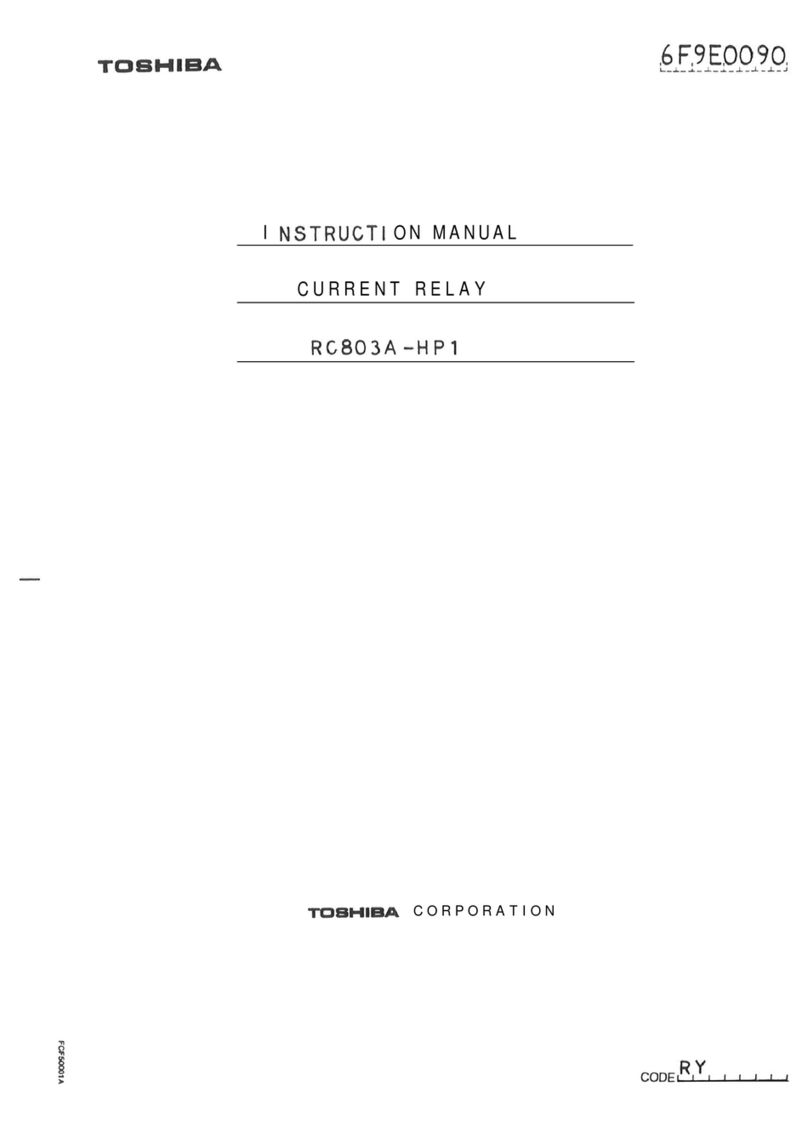
Toshiba
Toshiba Current Relay RC803A-HP1 User manual
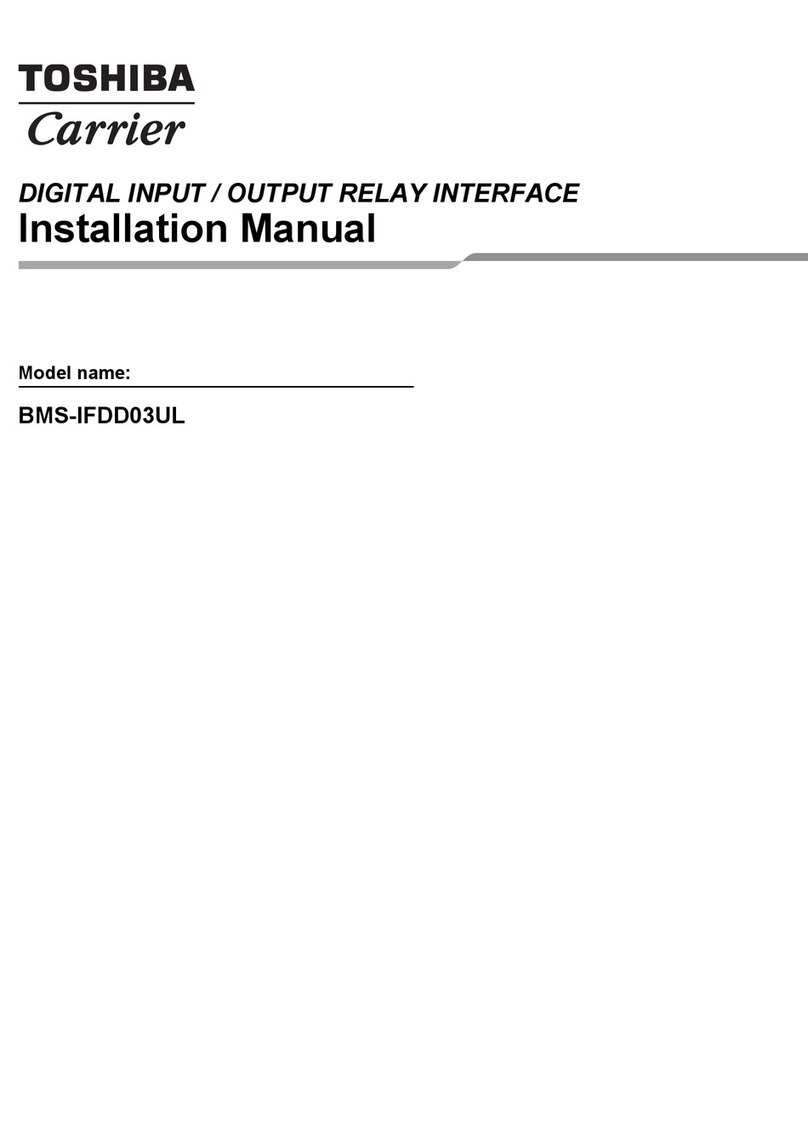
Toshiba
Toshiba BMS-IFDD03UL User manual
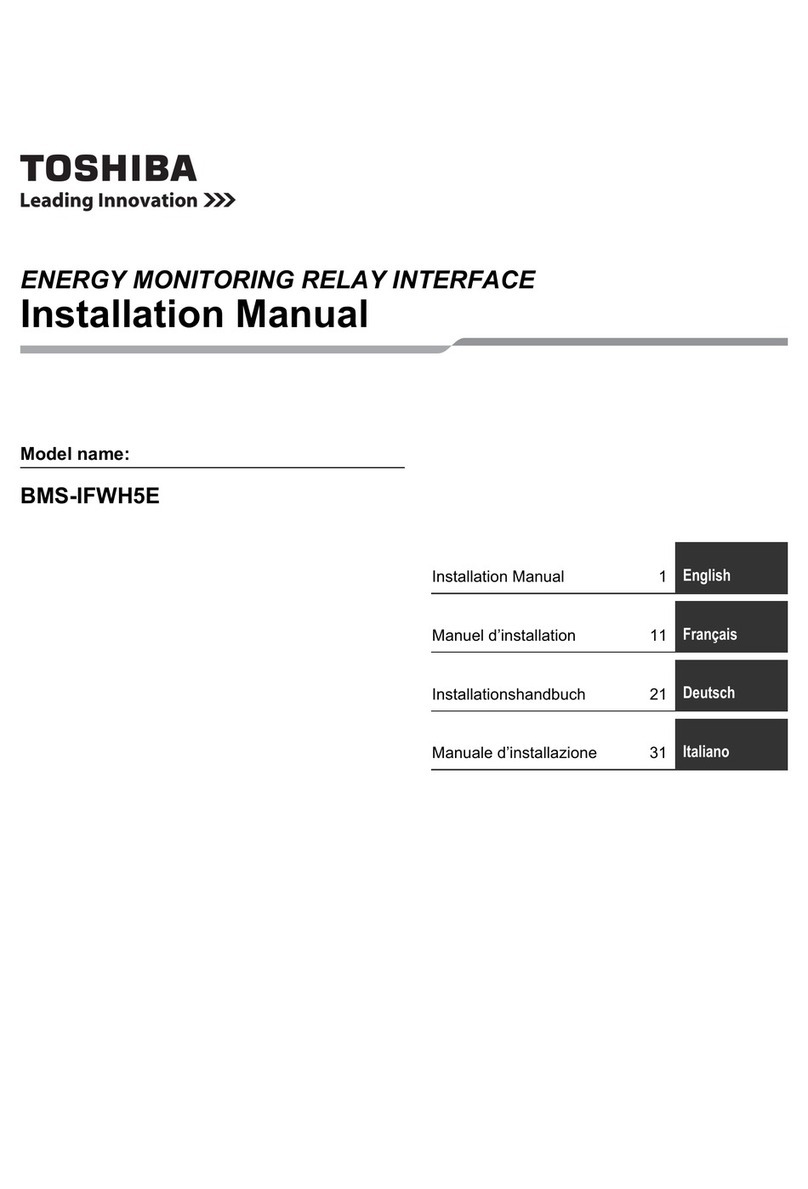
Toshiba
Toshiba BMS-IFWH5E User manual
Popular Relay manuals by other brands
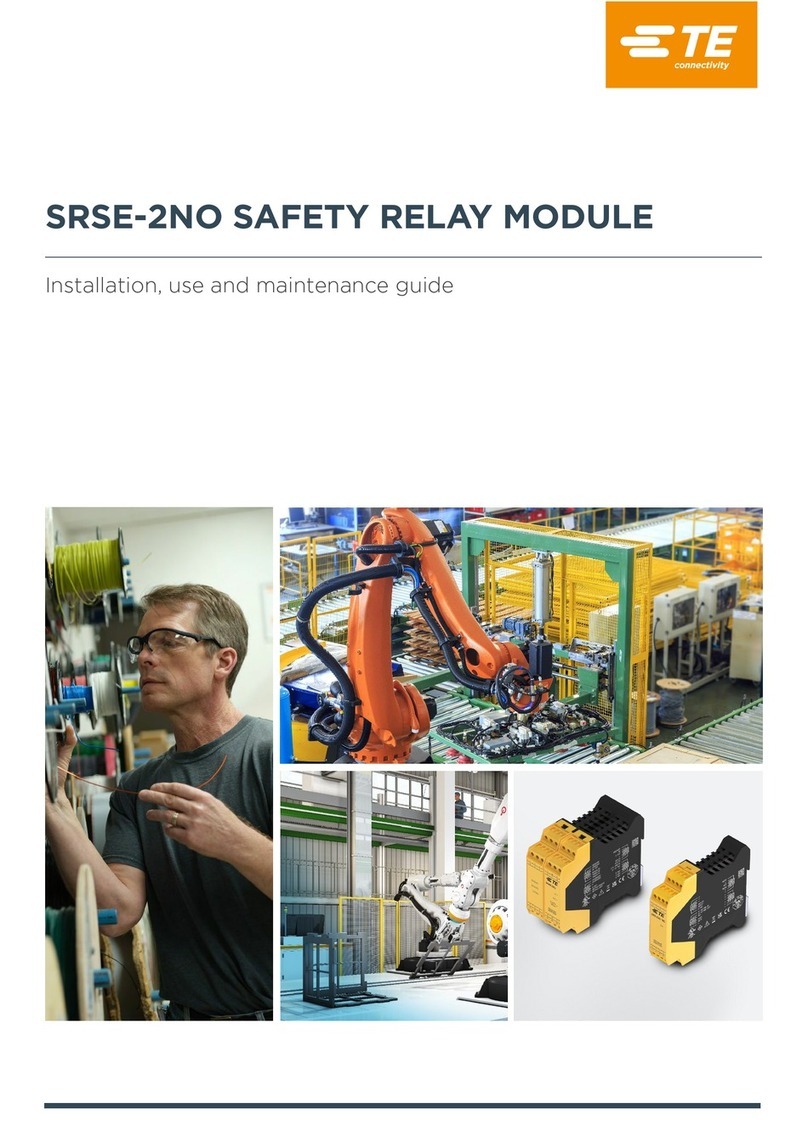
TE Connectivity
TE Connectivity SRSE-2NO Installation, use and maintenance guide

FOR-A
FOR-A MFR-RULINK Operation manual
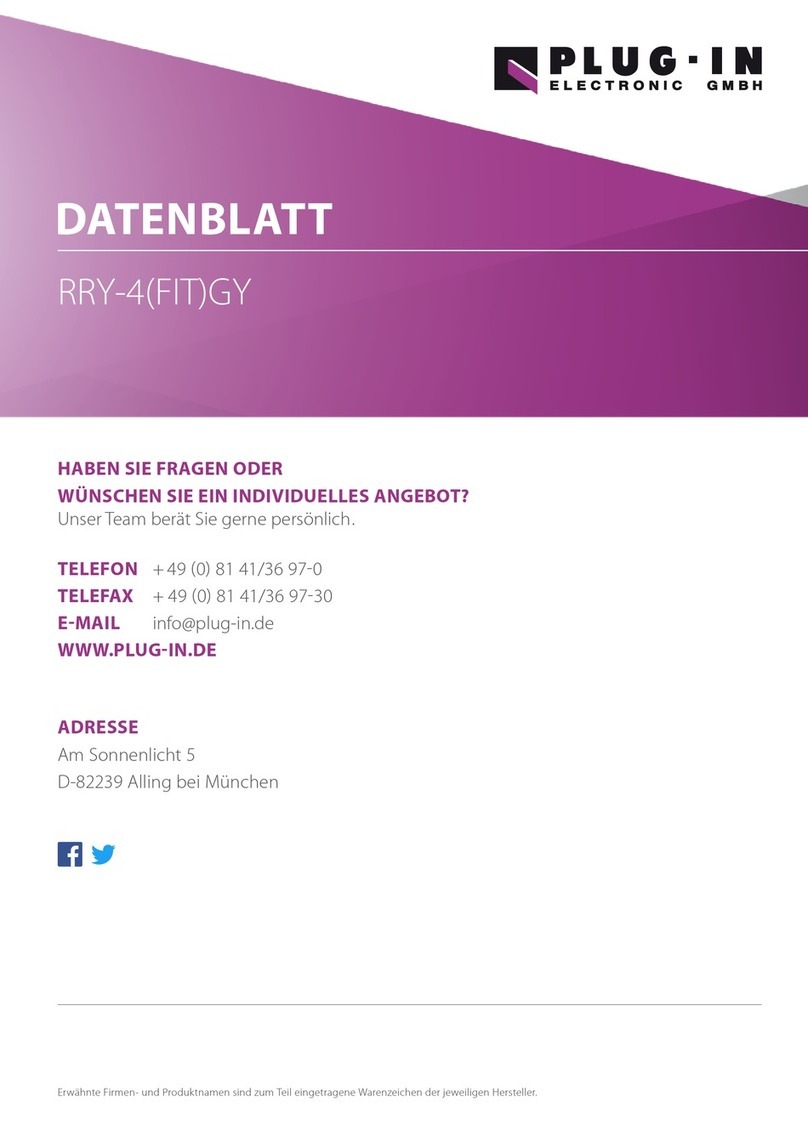
Contec
Contec F&eIT Series First step guide
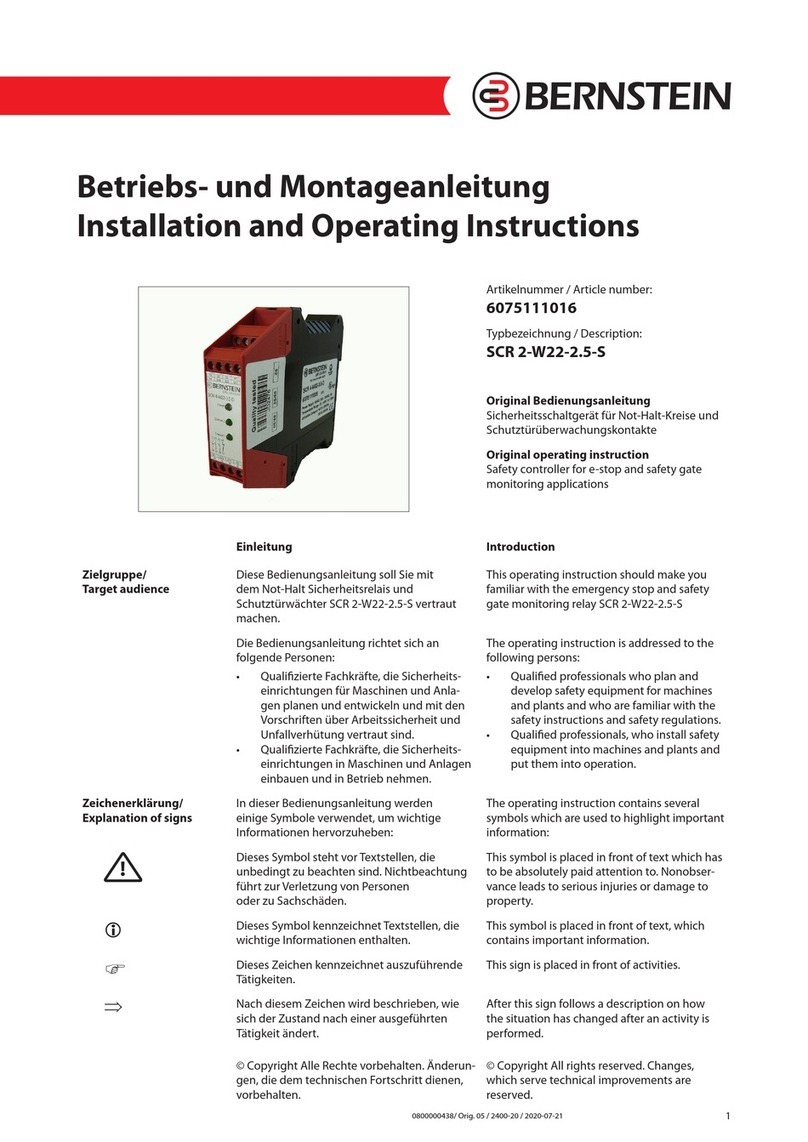
BERNSTEIN
BERNSTEIN SCR 2-W22-2.5-S Installation and operating instructions
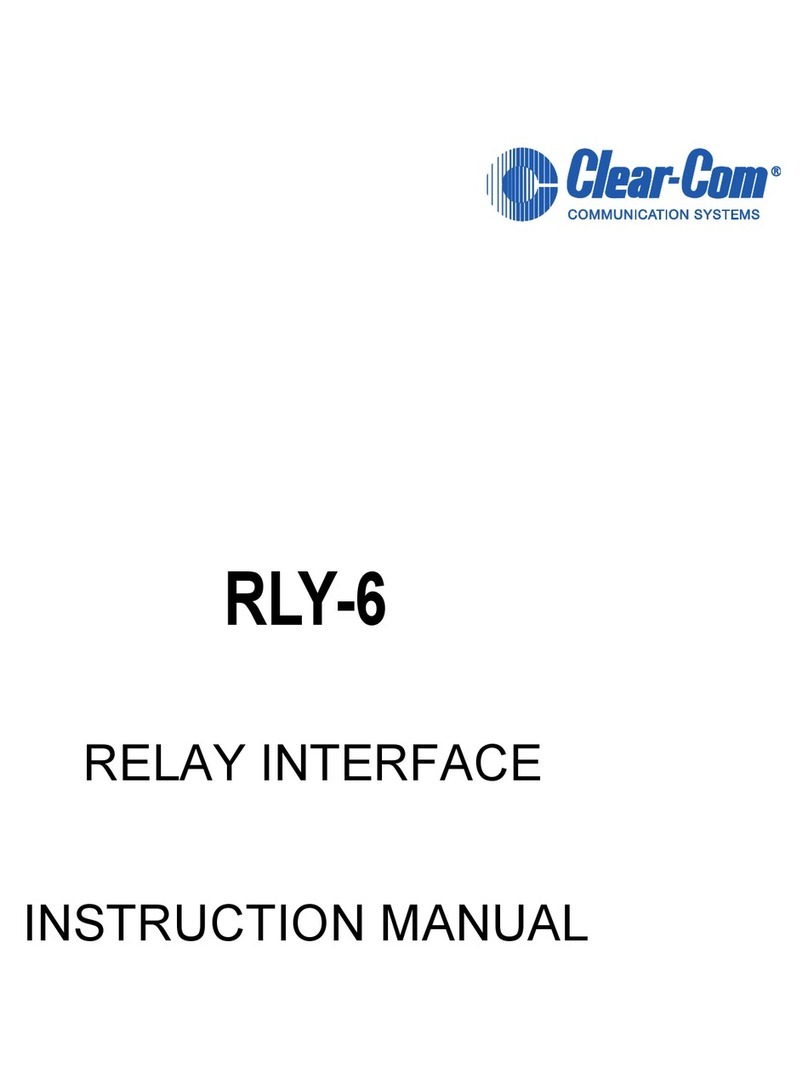
Clear-Com
Clear-Com RLY-6 instruction manual
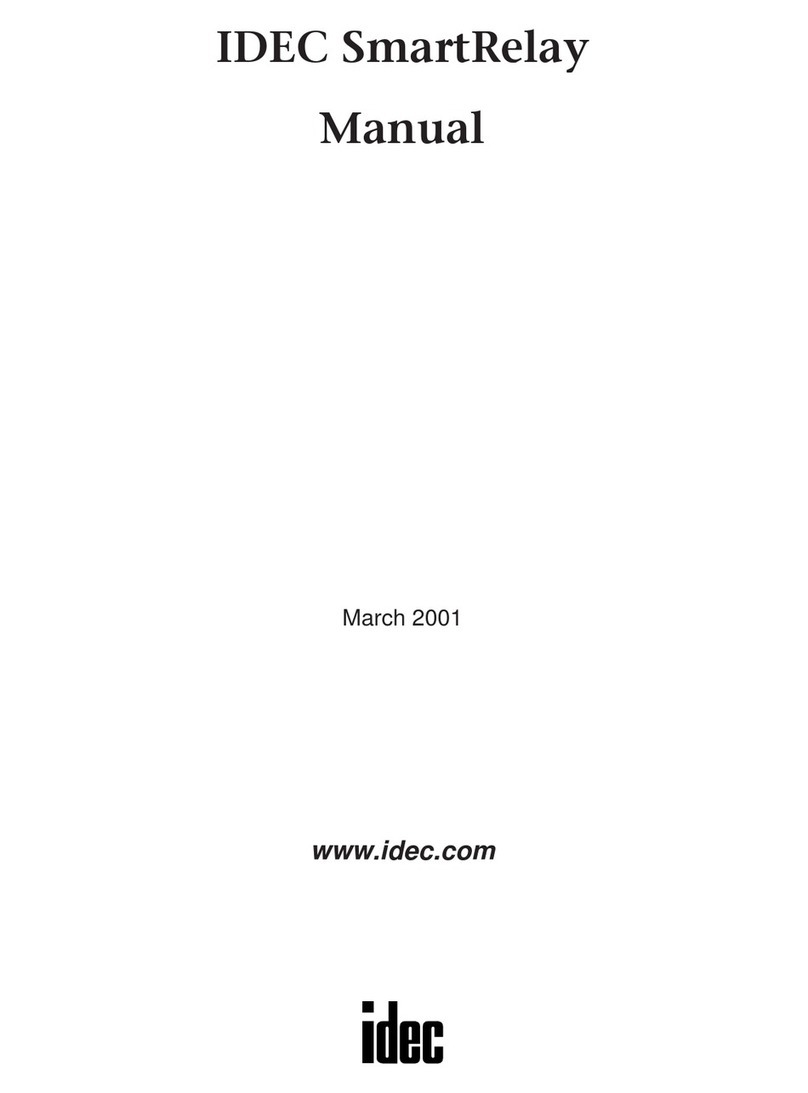
IDEC
IDEC SmartRelay FL1A-H12RCE manual
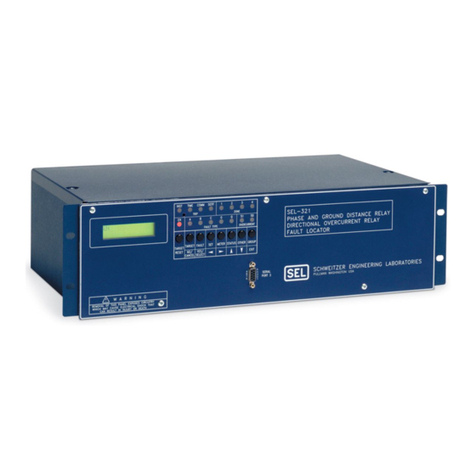
Schweitzer Engineering Laboratories
Schweitzer Engineering Laboratories SEL-321-3 instruction manual
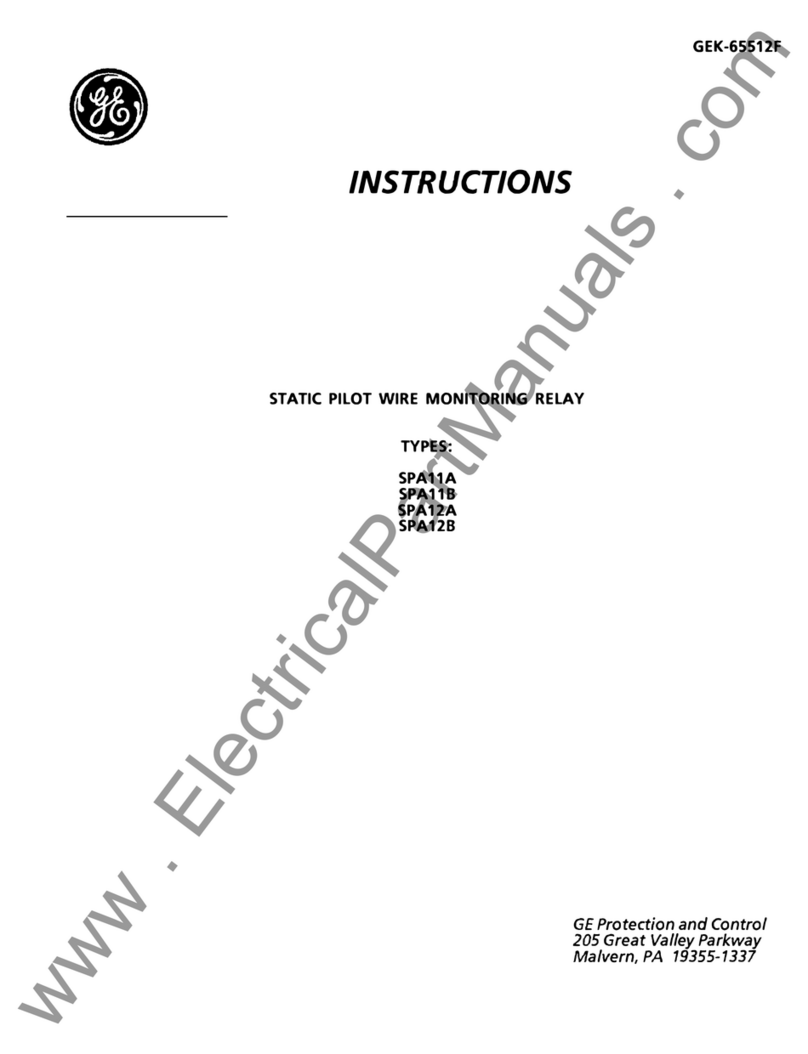
GE
GE SPA11A instructions
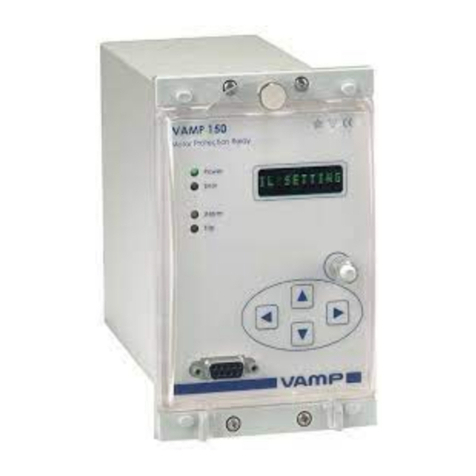
VAMP
VAMP VAMP 150 Operation and configuration instructions
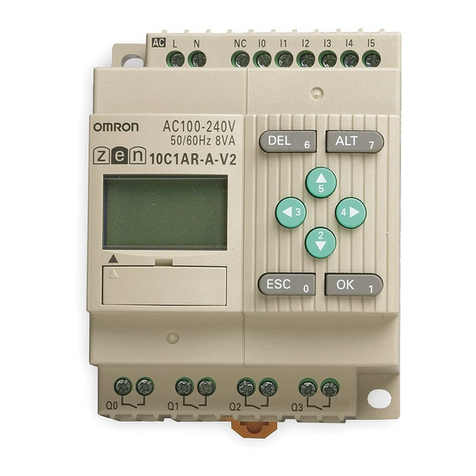
Omron
Omron ZEN Communications manual
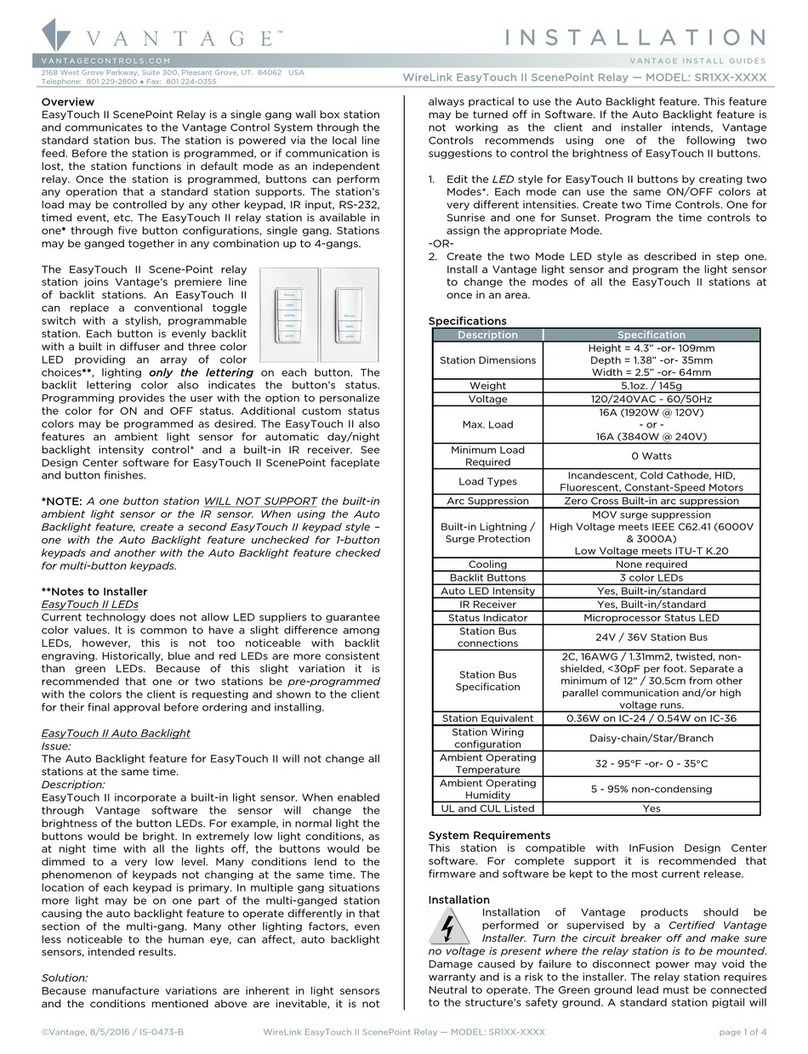
Vantage Hearth
Vantage Hearth WireLink EasyTouch II ScenePoint SR1 Series Installation

Basler
Basler BE1-87G instruction manual