Tsuruga 471C Installation guide

Tachometer
471C
Quick Manual

Contents
471C
Introduction ·····················································1
About this booklet ·········································································1
Precautions ··················································································1
Installation precautions··································································2
Nomenclature···················································3
Operation panel ············································································3
Rear panel····················································································5
Installation·······················································6
Installation conditions ····································································6
Accessories···················································································6
Mounting method··········································································7
Dismounting·················································································8
Wiring method··············································································9
Terminal layout and explanation ···················································· 11
Usage of Function Code···································16
Function code list ········································································ 16
Setting method of code No. ·························································· 17
Function setting method······························································· 18
Usable Operation ············································22
Change comparison values of SV1 and SV2
················································· 22
Teaching function ········································································ 23
Adjustment of analog output (Option)
················································· 24
Restore to the factory setting
································································ 25
Specification···················································26
Option Output·················································28
PhotoMOS compare output ··························································· 28
Analog output············································································· 32
BCD output (Digital output) ·························································· 34

Introduction
471C 1
Introduction
This model is tachometer. Signal from rotor is displayed as rotation speed.
About this booklet
Thank you for purchasing our Tachometer 471C. Before use of the product, read this quick
manual carefully and thoroughly, and keep it available for routine reference.
If the product is not used in the specified way decided by manufacturer, the functions protected
and guaranteed by manufacturer may be lost.
The following symbol marks are used in this quick manual for the safety use of the product.
! Warning
This is the warning to avoid danger. Severe injure or fatal accident
may occur to the user in case the product is mishandled.
! Caution
This is the caution to avoid danger. Minor injury to the user or
physical obstacle may occur in case the product is mishandled.
Precautions
For the safe use of this product, users must follow the following warning and caution.
! Warning
There is no power on-off switch on the model 471C. It immediately starts
to operate by connecting with power supply.
Never touch the terminals when power is ON. There may be risk of
electric shock.
! Caution
The rated data for warm up is specified for more than 15 minutes.
When the front panel or the case becomes dirty, wipe it with soft cloth. If
the dirt is difficult to remove, wipe it lightly with the soft moist cloth with
mild detergent diluted with water and finish by wiping with a dry cloth.
Do not use organic solvent like benzene or paint thinner as they may
deform or discolor the surface of the case.

Introduction(contd.)
2 471C
Installation precautions
For the safe use of this product, users must follow the following caution.
! Caution
If the product is installed inside the cabinet, provision for the proper heat
dissipation should be done to prevent the temperature exceeding more
than 50 ℃inside the cabinet.
Do not mount the product narrow distance. The rise of temperature may
decrease the life of the product.
Do not use the products in the following places. It may be the cause of
damage or malfunction.
*Wet place (rain, water drops), direct sunlight
*Place having high temperature, humidity, dust and corrosive gases
*Place having excessive noise, waves, static electricity
*Place having lots of vibration and shock
Store the product in the specified temperature range between -20℃to
65℃.

Nomenclature
471C 3
Nomenclature
Operation panel
No.
Name
Function
①
Display1
Process value (Current value) is displayed.
Red or green can be selected for display color.
②
Over
Light on when display1exceeds 999999.
Display color: Red
③
MEM
Light on when memory-enable set is ON (Code No.40).
Display color: Red
④
P・B
Light on when P.B is displayed.
Display color: Red
⑤
SV1
Either peak value or comparator value set by customer can
be displayed.
Display color: White
⑥
SV2
Either bottom value or comparator value set by customer
can be displayed.
Display color: White
⑦
Unit
Pasting position of Unit sticker
⑧
Comparative
display
The comparison status of the comparison output is
displayed.
⑨
SET Display
Light on during setting mode.
OVER SET
ENTER
MODE
P・B
MEM
P・B
(COMP)
rpm
⑤SV1 ⑥SV2
HH H L LL
①Display 1
④P・B⑦Unit
⑧Comparative display
⑨SET Display
②Over
⑩Setting key
⑪P・B Key
③Memory Display

Nomenclature(contd.)
4 471C
No.
Name
Function
⑩
Setting key
MODE
During measurement mode:Change to Setting mode,
Adjustment mode
During setting mode:Change to each code No.
▼(COMP)
During measurement mode: Set comparison value
During setting mode: Select the digit to change
▲
During measurement mode: Teaching function
(Except when switching to diagnosis mode)
During setting mode:Change of setting value
ENTER
During measurement mode:Invalid
During setting mode:Set value changed to saved
measurement mode
⑪
P・B key
P・B
During measurement mode:Reset Peak and Bottom
value
During setting mode: Setting mode changes to
measurement mode without
saving the set value.
Liquid Crystal Display
0
1
2
3
4
5
6
7
8
9
DP
minus
0
1
2
3
4
5
6
7
8
9
.
-
A
B
C
D
E
F
G
H
I
J
K
L
M
N
O
P
Q
R
S
T
U
V
W
X
Y
Z
A
B
C
D
E
F
G
H
I
J
K
L
M
N
O
P
Q
R
S
T
U
V
W
X
Y
Z

471C 5
Rear panel
No.
Name
Function
⑫
Terminal A1 to A6
A1, A2:Sensor power supplies
A3, A4:Input terminals
A5, A6:Vacant terminals
⑬
BCD output
connector
Open collector NPN transistor output
Terminal RS-232C
B1 to B5:RS-232C communication
B6: Vacant terminal
Terminal RS-485
B1: + B2: - B4, B5: Terminal resistances
B3, B6: Vacant terminals
⑭
Terminal C1 to C6
C1 to C4: Input terminals of controlling comparator
C5, C6: Analog output terminals
⑮
Terminal D1 to D6
D1 to D6: HH, H, L and LL output terminals
⑯
Terminal E1 to E6
E1, E3: Power supply terminals
E5: Ground terminal
E2, E4, E6: Vacant terminals
※⑬, ⑭and ⑮are option specification
1
2
3
4
5
6
A B C D E
12 13 14 15 16

Installation
6 471C
Installation
Installation conditions
Power supply
AC100 to 240V 50/60Hz, DC24V
Voltage tolerance of
power supply
AC90 to 250V,DC24V±10%
Power consumption
During AC100V: Approx. 9VA,During AC200V: Approx. 12VA
During 24VA: Approx. 200mA
Operating ambient
temperature
0
to
50℃, 40
to
85%RH(No condensation)
Storage temperature
-20
to
65℃(No condensation)
Weight
Approx. 300g
Mounting method
Tighten from behind the panel with exclusive mounting bracket.
Insulation resistance
Measuring input terminals
–
External Case DC 500 V, More than 100 M
Ω
Power supply terminal
–
External Case DC 500 V, More than 100 M
Ω
Power supply terminal
–
Measuring input DC 500 V, More than 100 M
Ω
Measuring input terminals
–
BCD output DC 500 V, More than 50 M
Ω
Measuring input terminals
–
Analog output DC 500 V, More than 50 M
Ω
Withstand voltage
Measuring input terminals
–
External Case AC 2000 V for one minute
Power supply terminal
–
External Case AC 2000 V for one minute
Power supply terminal
–
Measuring input AC1500 V for one minute
Measuring input terminals
–
BCD output, RS-232C, RS-485 AC 500 V for one minute
Measuring input terminals
–
Analog output AC 500 V for one minute
Protective structure
Front operation unit IP65, Case part except front side IP20,
Terminal block IP00
Accessories
Make sure that the following items are included with product supplied.
・471C main unit ・Bracket 2pcs. ・Waterproof packing
・Quick Manual (This booklet)
(For the model with RS-232C or RS-485, exclusive quick manual is included.)
・Unit Sticker
・Connector (2m with flat cable) (In case of BCD Output model)

471C 7
Mounting method
Mounting pitch
Panel cutout dimensions: 92 0
+0.8×45 0
+0.6mm
Panel thickness: 0.6 to 3.5mm(Degree of protection IP65)
3.6 to 10mm(Degree of protection IP20)
If the material of the panel is aluminum, it may
be deformed due to its weak strength. So, it is
recommended to use the thickness of
aluminum panel sheet with at least 1.5mm.
Mounting pitch(Refer to the Right figure)
Mounting method to panel
1Insert the main unit fitted with the waterproof packing into the hole, from the panel
front, and insert the attached bracket to the ditch on both sides of the main unit.
Press the bracket as shown by arrow ①until the main unit is stably stays and fix the
bracket. Do not remove it as the packing acts as stopper too. Refer to the side view
drawing of the bracket mounting shown below.
2To fix the main unit more firm, press the back part (center part) of the bracket
indicated by arrow ②by screwdriver, which enhances the stopper strength.
! Caution
When the bracket is pressed by minus screwdriver, press it to the
direction as shown in arrow ②.
The pressing of other part may cause the damage of bracket.
min.30
min.75
min.130
ECBA D
①
②
①
Push ②
Side view of bracket mounting
Top view of bracket mounting
Bracket
Panel to mount
Waterproof packing

Installation(contd.)
8 471C
Dismounting
1The lever lock of bracket can be released by extending the lever outward about 1 mm
by fingers as shown in figure below.
2Keep extending the lever outward, slide the bracket backward of the main unit and
remove it from the ditch.
! Caution
The extension of the lever or the stress to it by metallic piece like
screwdriver for a long time may damage the lever.
ECBA D
Lever
Extend the lever about
1mm and releases the
lock
Enlarged view of
bracket inside
Bracket lock releasing

471C 9
Wiring method
Remove the terminal base cover of the rear side terminal and conduct the wiring. Make sure
that the terminal base cover is attached after wiring. If both options of comparison output and
analog output are used, first complete the wiring of the comparison output and then start the
wiring of analog output.
Notes for wiring
! Warning
To avoid an electrical shock, turn the power off when wiring.
Do not conduct wiring at moistened place or by wetted hands. There may
be risk of electric shock.
Do not touch the terminals when turning the power on. There may be risk
of electric shock.
! Caution
Power supply and load should be within the suitable range as prescribed
in specification. Negligence may cause the damage of products.
Power supply should reach the rated power within a second.
After the power is OFF, pause more than 10 seconds before the power ON
again.
Do not use the product with wrong wiring. It may be the cause of product
damage.
◆
Others caution during wiring
Always use input line and power line independently. If input line and power line are wired in
parallel, it may cause an in stability of the display.
When the auxiliary relay is operated by the relay output to run the electro- magnetic switch
or big size relay, take the noise preventive measures.
In case that the noise is frequently occurred, it will be effective to store the product in the
shielded housing or to insert the power source line filter or insulated transformer.

Installation(contd.)
10 471C
About the crimp terminal
Direction of crimp terminal
Recommended crimp terminal:V1.25-FS3
(Made of Fuji Terminal Industry Co., Ltd)
Ext. diameter of covered cable:Max.φ3.3
Terminal screw:M3
Crimp terminal: Refer figure at the right
! Caution
For the column B (RS-232C and RS-485), column C and D terminal blocks,
apply just one crimp terminal per terminal location.
Do not wire the parallel connection, using two crimp terminals
(overlaying) at the same terminal location. It stresses the internal PCB
and may cause the failure or trouble. As for the A column and E column
terminal blocks, up to two crimp terminals per terminal location are
acceptable.
1
2
3
4
5
6
AB C D E
6
18.25
9.5
5.85
5.8

471C 11
Terminal layout and explanation
Rear side terminal
! Caution
・Replacement of the above terminal units by customers themselves is
prohibited because it may be the cause the damage of the product.
1
2
3
4
5
6
▲
AB C D E
Term
NC
-
+
B6
B5
B4
B3
B2
B1
NCNC
SG
CS
RD
RS
SD
Term
1
2
3
4
5
6
7
8
9
10
11
12
13
14
15
16
17
18
4
2
8
1
4
2
8
1
4
2
8
1
4
2
8
1
4
2
8
1
4
2
8
1
10
10
10
10
10 10
E1
E2
E3
E4
E5
E6
N C
N C
AC100~240V
BCD_LATCH
SYNC
19
20
21
22
23
24
25
26
27
28
29
30
31
32
33
34
35
36
GND
DP1
DP2
DP3
DP4
D1
D2
D3
D4
D5
D6
HH
H
L
LL
0
1
2
3
4
5
POL
OUTPUT ENABLE
DATA COM
DATA COM
DATA COM
C1
C2
C3
C4
C5
C6
A1
A2
A3
A4
A5
A6
COM
NC
NC
SIG1
SIG2
OVER
H-COM
L-COM
SENSOR
DC24V
+
-
NC
M.COM
M.SEL1
M.SEL2
M.SEL4
Sensor power supply
BCD output
Analog output
Power supply
At optional RS-232C output At optional RS-485 output
At optional BCD output
At optional
analog output
When there is no option,
it becomes NC (Vacant terminal).
A.OUT+
A.OUT-
B C D
a terminal block)
(B column is
a terminal block)
(B column is
EA
RS-485RS-232C
At optional
comparion output
Measuring input
Comparison output(With selected memory
for comparison)
NC: Non contact terminal
Do not use it.
NC: Non contact terminal
Do not use it.
NC: Non contact terminal
Do not use it.

Installation(contd.)
12 471C
Power supply connection
Connect the power supply at terminal No. E1-E3.
Power supply voltage is mentioned on the
terminal nameplate at the time of shipment.
○AC power supply
AC100 to 240V 50/60Hz
Permissible range AC 90 to 250V
○DC power supply
DC 24V
Permissible range DC24V±10%
! Caution
Do not use the voltage out of permissible range. It may be the cause of
equipment damage.
Power on / off, power supply should reach up to rated voltage or shut
down within 1 second.
After the power is OFF, pause more than 10 seconds before the power ON
again.
GND (ground) terminal
In case of frequent noise generation on the power source line, it is
effective to earth the ground terminal directly to the ground. If the
instrument is not affected by environmental noise, the grounding can be
omitted. In this case, take care for the ground terminal not to touch
other input terminals, as it is charged with neutral electric potential of
power source voltage.
1
2
3
4
5
6
AB C D E
+
-
1
2
3
4
5
6
AB C D E
GND for
power supply
GND for
power supply
AC power supply
DC power supply

471C 13
Connection of input signal
Power supply for the sensor is connected from terminal No.
A1-A3. If the power supply of sensor is applied from
external sources, the connection of terminal No. A1 will not
be required. When sensor power source is not used, A1 will
be vacant and do not used it for other purpose.
○+Sensor power supply
Connection example of(+V、0V)
○Connection example of measurement input
! Caution
If sensor power supply terminal A1 is accidentally short-circuited with
COM terminal A2, it may cause malfunction of the product.
1
2
3
4
5
6
A B C D E
A1
A2
A3
A4
A5
A6
COM
SIG1
SIG2
SENSOR
NC
NC
Sensor output
(Open collector)
+V0V
Power supply
for sensor
A1
A2
A3
A4
A5
A6
COM
SIG1
SIG2
A1
A2
A3
A4
A5
A6
COM
SIG1
SIG2
0V
OUT
SENSOR SENSOR
NC
NC
NC
NC
4.0~30V
0~1.5V
No voltage contact or
NPN open collector sensor sensor
Voltage pulse output

Installation(contd.)
14 471C
Connection of selected memory for comparison
Input signals is set during the selection of memory of
comparative setting value. The configuration is as below.
Refer P.28 to confirm the Enable /Disable function of
comparative output.
Connection of analog output
The analog output can be obtained from
the Terminal No.C5-C6. Use analog
output within the specified range of
allowable load resistance.
(Refer Page 26『Model Configuration』)
Connection of comparison outputs (HH,H,L,LL)
Comparison output can be obtained in terminal No.
○
D2 -○
D1 、○
D2 -○
D3 、○
D5 -○
D4 and ○
D5 -○
D6 .
Equal NG
Equal GO
Displayed value≧
Higher (HH) set value
Displayed value>
Higher (HH) set value
HH:○
D2
-○
D1
Displayed value≧
High(H) set value
Displayed value>
High(H) set value
H:○
D2
-○
D3
Displayed value≦
Low(L) set value
Displayed value<
Low(L) set value
L:○
D5
-○
D4
Displayed value≦
Lower(LL) set value
Displayed value<
Lower(LL) set value
LL:○
D5
-○
D6
Contact capacity:AC/DC250V 200mA
1
2
3
4
5
6
A B C D E
1
2
3
4
5
6
A B C D E
1
2
3
4
5
6
A B C D E
C1
C4
C5
C6
C2
C3
M.COM
M.SEL1
M.SEL2
M.SEL4
+5V
Less than 10mA
Photocouplers M.COM
M.SEL1/2/4
Switch
471C internal
C1
C2
C3
C4
C5
C6
A.OUT+
A.OUT-

471C 15
Connection of BCD output
The configuration of 6 digits data output open collector
(NPN) is shown as the connector arrangement of BCD
output in page 11.
Control input pin 16 BCD_LATCH, 17 OUTPUT ENABLE are
shown in P.11 as the connector arrangement.
Accessory: Cable (5808-05) 2m
Connector (8822E-036-171-F, Kel Corp.)
Electrical schematic diagram
1
2
3
4
5
6
A B C D E
▲Mark
▲Mark
Lower cable No.19~36
Upper cable No.1~18
Upper cable
No.1(Brown)
Upper cable
No.18(Gray)
Lower cable
Lower cable
No.19(White)
No.36(Blue)
0V
24V
(0V)
OUT
OUT
0V
DC24V
DC24V
IN
IN
IN
IN
IN
16 BCD_LATCH
0
0
0
0
471C
15 OVER
1 1×10
2 2×10
4 8×10
3 4×10
18,35,36DATA COM
ENABLE
17 OUTPUT
DC power supply
Transistor output unit
Controller side
Transistor output unit
Darington

Usage of Function Code
16 471C
Usage of Functio n Code
Function code list
●Display functions
Code
№
Function
Display1
Setting range
Default
Value
00
Key protect
KEY.
OFF, ON
OFF
01
Scale α
SCAL
000001E-9 to 999999E-0
000001E-0
02
Decimal point
DP
0/0.0/0.00/0.000/0.0000/0.00000
0
03
Input frequency filter
FLTR.
0.02kHz/10kHz/30kHz/100kHz
10kHz
04
Display cycle
RATE
00.1 to 19.9s
01.0
05
Number of moving average
M.AVE.
01 to 10
1
06
Min. revolution No.
MIN.R.
000000 to 999999
000000
07
Cut-off time
CUT
000.1 to 150.0
006.0
08
Predicted function
P.F.
OFF(Invalid)/ON(Valid)
OFF
09
Display of SV1, SV2
SUB.
OFF-OFF, PM-BM / OFF,HH,H,L,LL,PM-BM
*1)
PM-BM
10
Display switch-off function
TURN.
0(OFF)/1(All display)/2(SV1, SV2),
0 to 99 minutes
0.01
11
Display color
COLO.
R(Red), G(Green)
G(Green)
*1)Display settings of HH,H,L,LL become enable, when comparison output function is on.
●Option comparison output function(HH,H,L,LL)
Code
№
Function
Display1
Setting range
Default
Value
40
Memory-enable
MEM.
OFF(Invalid)/ON(Valid)
OFF
41
HH compared value
AL.HH
000000 to 999999 *2)
999999
42
H compared value
AL. H
000000 to 999999 *2)
999999
43
L compared value
AL. L
000000 to 999999 *2)
000000
44
LL compared value
AL.LL
000000 to 999999 *2)
000000
45
Hysteresis
HYS.
01 to 99
01
50
Power-on delay
P.DLY
1 to 99 seconds
1
51
HH comparison function
FRM.HH
OFF/ON
ON
52
H comparison function
FRM. H
OFF/ON
ON
53
L comparison function
FRM. L
OFF/ON
ON
54
LL comparison function
FRM.LL
OFF/ON
ON
55
Comparison condition
EQUL
GO (Equal ‘GO’), NG (Equal ‘NG’)
GO
*2)The settings of MEM 1 to 8 become enable, when code No.40 ’Memory-enable’function is on.
●Option BCD output, Analog output
Code
№
Function
Display1
Setting range
Default
Value
70
BCD logic switching
B.PN
0: Negative, 1: Positive
0: Negative
76
Digit selection
D.SEL.
0 (Last 4digits), 1 (Middle 4 digits),
2 (First 4 digits)
0
79
Full-scale
A.FUL.
0 to 9999
9999

471C 17
Measurement
Operation
Mode Setting
(Set Code No.)
●Option RS-232C, RS-485 output
Code
№
Function
Display1
Setting range
Default
Value
80
Baud rate
BAUD.
4800, 9600, 19200bps
9600bps
81
Parity
PARIT
non(None), odd(Odd no.), even(Even no.)
non
82
BCC switching
BCC
ON, OFF
OFF
83
Device number
RS.NO.
0 to 99
00
Setting method of code No.
This is the basic input method of function code.
Following the setting of the Code No., perform the function setting on the following pages.
Identification of the key color during
set up is as follows.
Black key: Valid key
White key: Invalid key
[
Common during the Setting mode
]
During setting mode, if the key is not
operated for about 5 minutes, the
operation returns into measurement
mode automatically. At this time, the
setting contents are not saved.
Again, if P・B key is pressed for more
than 1 second, the setting value
which may be under changing
process becomes invalid and returns
to measuring process.
MODE
▲
SET
SET
SET
MODE
Press 1 sec.
Confirm
Select the Code №
,▲
To function setting

Usage of Function Code(contd.)
18 471C
Mode
Setting
(Set number)
Mode
Setting
(Item setting)
Function setting method
The following is an example of the input function setting. Refer this page when changing to the
setting other than factory setting value. Continue the following operation of the function setting
after completion of setting method of code No. mentioned in previous page (page 17).
Code No.01『Scale α』
Code No.02『Decimal point』
Mantissa and exponent portion of scale αcan
be set.
display=f×α
f:Input frequency, α: Scale value
Setting range:
000001×10-9 to 999999×10-0
The decimal point at an arbitrary position can
be lit up. The decimal point is not linked with
the setting of Scale α.
It's just a function to display the decimal point
of indication externally.
Setting range:
0/0.0/0.00/0.000/0.0000/0.00000
Ex.)Change from 000001E1-0 to 166666E-3.
Ex.)Change from 0.00 to 0.0.
▲
MODE
MODE
▲
MODE
MODE
MODE
SET
SET
SET
SET
▲
To code No. setting To measurment
operation
1sec.
ENTER
Code №02
1sec.
ENTER
1sec.
ENTER
Displays of
current setting
(Save)
Memorize
exponent portion
Change the position of
1sec.
ENTER
▲
MODE
▲
MODE
ENTER
MODE
SET
SET
To code No. setting
Code №01
To measurment
operation
1sec.
ENTER
Displays of
current setting
1sec.
ENTER
MODE
MODE
MODE
SET
SET
SET
1sec.
(Save)
Memorize
,▲
Change
mantissa portion
Change
exponent portion
ENTER
1sec.
ENTER
1sec.
,▲
Table of contents
Other Tsuruga Measuring Instrument manuals
Popular Measuring Instrument manuals by other brands

Thermo Scientific
Thermo Scientific Eutech COND 6+ Operation instructions
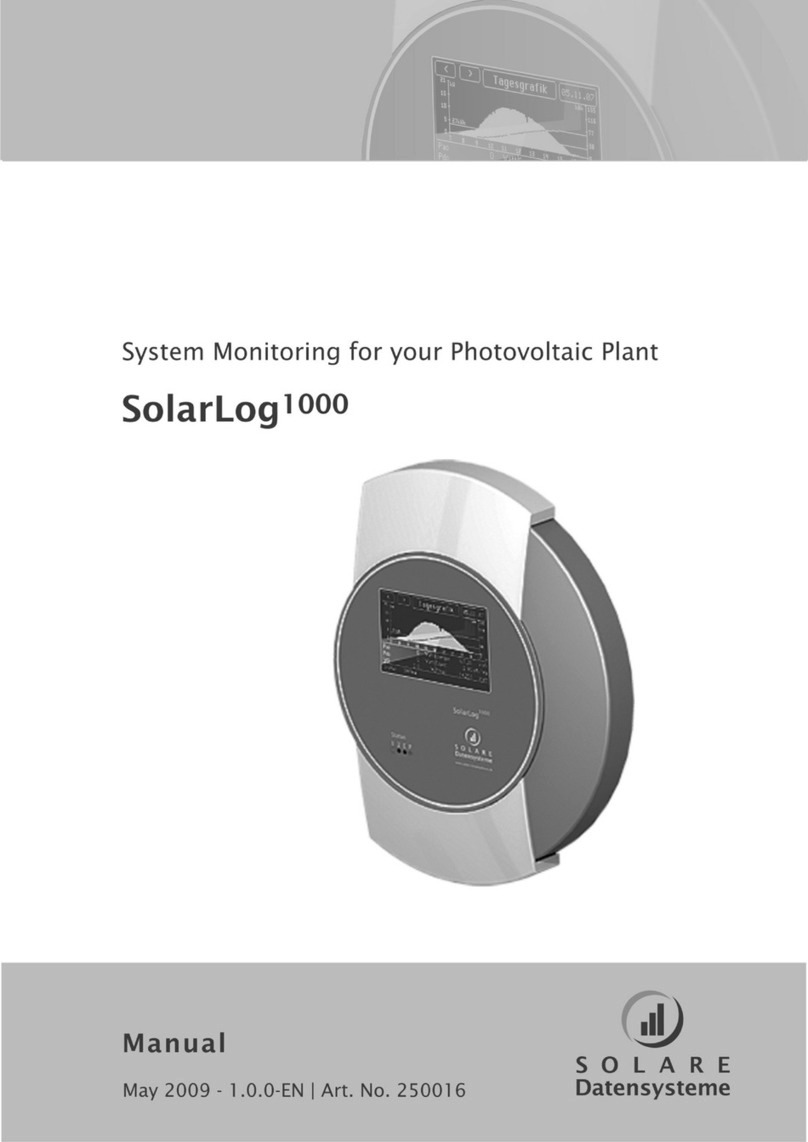
Solare Datensysteme
Solare Datensysteme Solar-Log 1000 manual
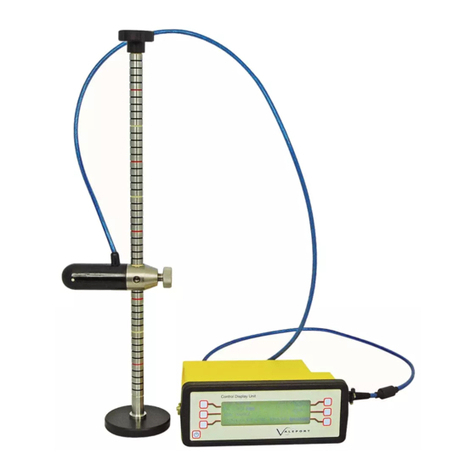
Valeport
Valeport 801 EM operating manual
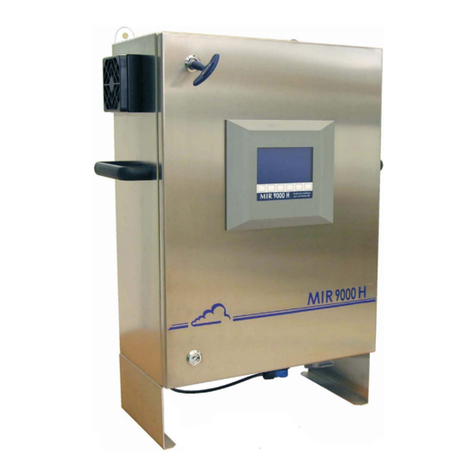
Environnement
Environnement MIR 9000H Technical manual
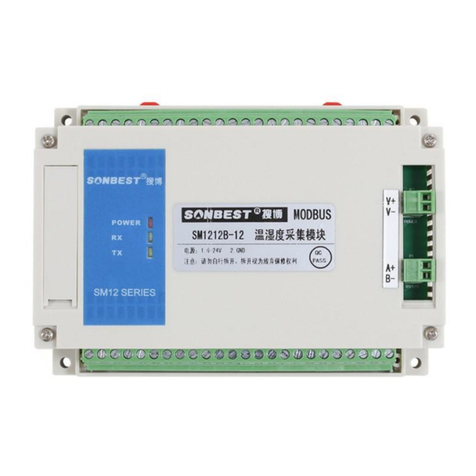
SONBEST
SONBEST SM1212B-12 user manual

Sper scientific
Sper scientific 850070 instruction manual
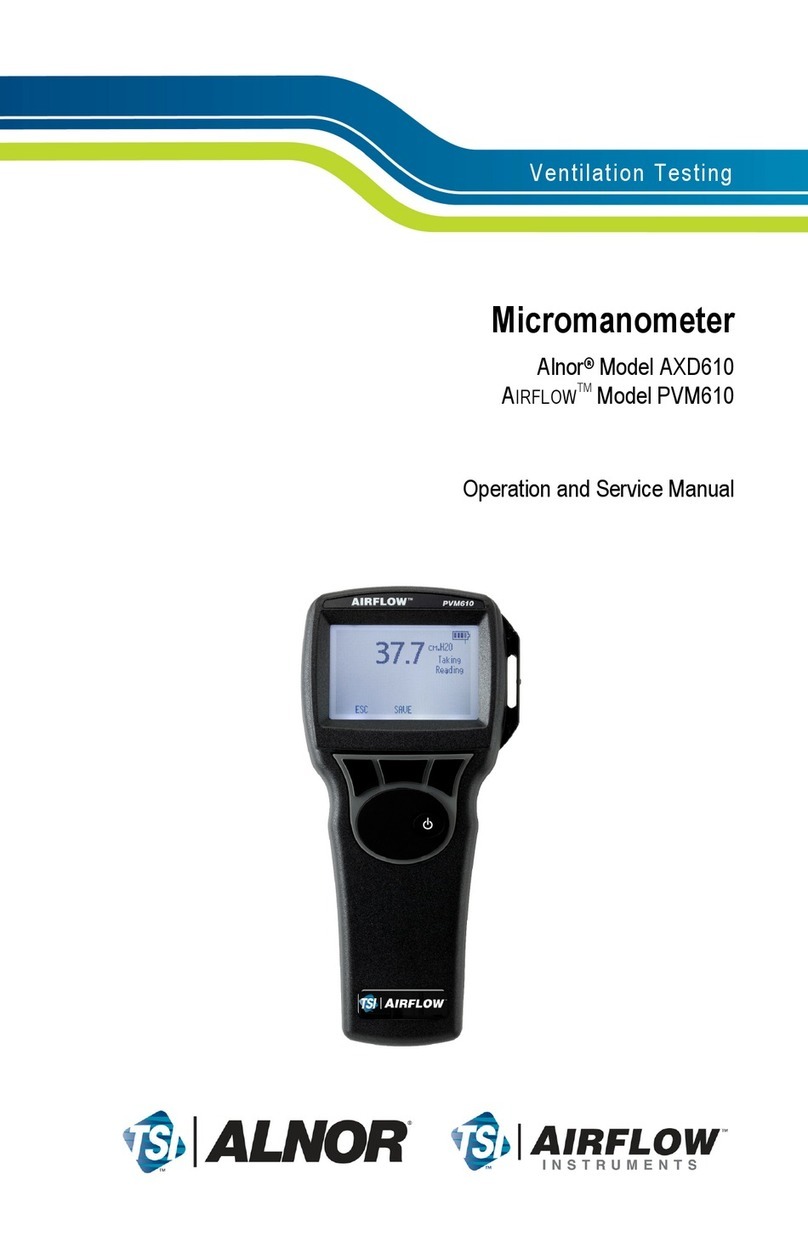
Airflow
Airflow AXD610 Operation and service manual
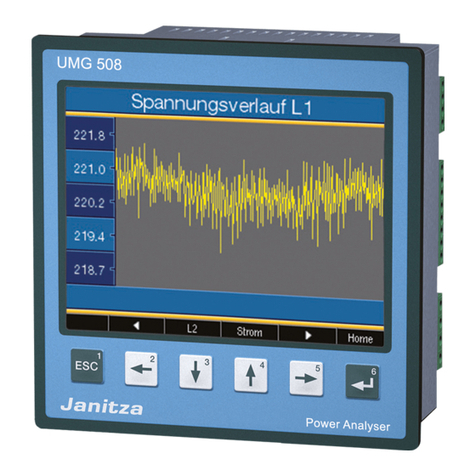
janitza
janitza UMG 508 operating manual

Particle Measuring Systems
Particle Measuring Systems LASAIR II 310 Operator's manual

Sper scientific
Sper scientific 840006 instruction manual
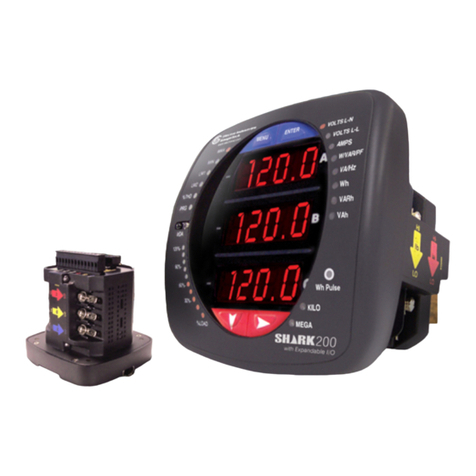
Electro Industries
Electro Industries Shark 200 Installation & operation manual
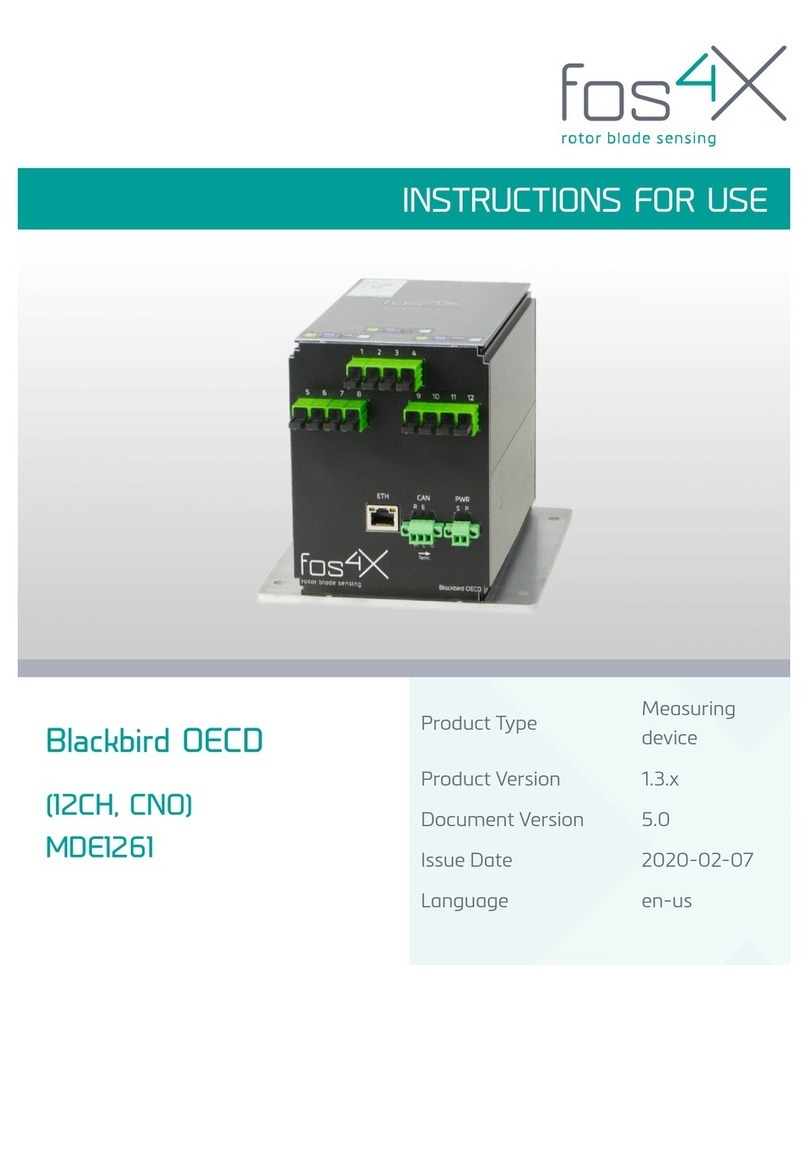
fos4X
fos4X Blackbird OECD Instructions for use