Unitek Classic Q1 Series User manual

M A N U A L
Classic Q1
4 Quadrant circular current-free
Thyristor Motor Controller
Part 1 Thyristor Motor Controller Q1
Part 2 Analog Control Electronics REG-xx
Industrie Elektronik
G m b H
Hans-Paul-Kaysser-Straße 1
71397 Leutenbach –Nellmersbach
Edition /
Version
Tel.: 07195 / 92 83 –0
Fax: 07195 / 92 83 –129
info@unitek-online.de
www.unitek-online.de
08/2016
V
01

Basic information
Classic Q1
1
Contents
2Basic information ............................................................................................................. 2
2.1 Safety regulations............................................................................................................... 2
2.2 Regulations and guidelines ................................................................................................ 2
2.2 General information and features ..................................................................................... 4
2.3 Technical data .................................................................................................................... 5
2.4 Specifications ..................................................................................................................... 6
2.5 Interfaces............................................................................................................................ 6
3Mechanical installation .................................................................................................... 7
3.1 Mounting............................................................................................................................ 7
3.2 Transformer choke............................................................................................................. 9
4Electrical installation ...................................................................................................... 10
4.1 Connection diagram ......................................................................................................... 10
4.2 Circuit diagram ................................................................................................................. 11
4.3 Important CE notes .......................................................................................................... 12
4.4 Connections...................................................................................................................... 13
4.5 Power connections........................................................................................................... 14
4.6 Motor connection ............................................................................................................ 15
4.7 Actual value connection l ................................................................................................. 16
5Settings.......................................................................................................................... 17
5.1 Control parameters of the current controller.................................................................. 17
5.2 Signals............................................................................................................................... 18
5.3 Commissioning Q1 x/x-x with REGxx................................................................................ 19
5.4 Protocol (commissioning)................................................................................................. 21
6Troubleshooting............................................................................................................. 23
6.1 Troubleshooting ............................................................................................................... 23
6.2 Functional errors .............................................................................................................. 24
7Guarantee...................................................................................................................... 25
7.1 Guarantee......................................................................................................................... 25

Basic information
Classic Q1
2
Safety regulations
2Basic information
2.1 Safety regulations
In principle electronic equipment is not fault proof!
Caution - High voltage
Shock hazard! / Danger to life!
Before installation or commissioning begins, this manual must be thoroughly read and
understood by the skilled technical staff involved. If any uncertainty arises, the manufacturer or
dealer should be contacted.
The devices are power electric parts (EB) used for regulating the energy flow in high-voltage
systems.
Protection rating IP00.
The control and power connections may be voltage-carrying
without the axis operating!
Measure the voltage prior to any disassembly!
2.2 Regulations and guidelines
The devices and their associated components can only be installed and switched on where the
local regulations and technical standards have been strictly adhered to.
EU Guidelines
2004/108/EG, 2006/95/EG, 2006/42/EG
EN 60204-1, EN292, EN50178, EN60439-1,
EN61800-3, ECE-R100
ISO 6469, ISO 26262, ISO 16750, ISO 20653, ISO12100
IEC/UL:
IEC 61508, IEC364, IEC664, UL508C, UL840
VDE Regulations/TÜV Regulations:
VDE100, VDE110, VDE160
Regulations of the statutory
accident insurance and prevention
institution:
VGB4

Basic information
Classic Q1
3
2.2 Regulations and guidelines
The user must ensure that in the event of:
- device failure
- incorrect operation
- loss of regulation or control
the axis will be safely de-activated.
It must also be ensured that the vehicles, machines, equipment,
or vehicles are fitted with device independent monitoring and
safety features.
Unearthed systems (e.g. vehicles) must be protected by means
of independent insulation monitors.
Man as well as property must not be exposed to danger at any
time!
Assembly
- should only be carried out when all voltages have been removed and the units are secured
- should only be carried out by suitably trained personnel
Installation
- should only be carried out when all voltages have been removed and the units are secured
- should only be carried out by suitably trained personnel for electrics
- should only be carried out in accordance with health and safety guidelines
Adjustments and programming
- should only be carried out by suitably trained personnel with knowledge in electronic drives and
their software
- should only be carried out in accordance with the programming advice
- should only be carried out in accordance with safety guidelines
CE
When mounting the units into vehicles, machines, and installations the proper operation of the
units may not be started until it is ensured that the machine, the installation, or the vehicle
comply with the regulations of the EC machinery directive 2006/42/EG, the EMC guideline
2004/108/EG, and the guideline ECE-R100.
On the described installation and test conditions (see chapter ‘CE notes’) it is adhered to the EC
guideline 2004/108/EG including the EMC standards EN61000-2 and EN61000-4.
A manufacturer's declaration can be requested.
The manufacturer of the machine or installation is responsible for observing the threshold values
demanded by the EMC laws.
QS
Test results are archived with the device serial number by the manufacturer for a period of 5
years.
The test protocols can be asked for.

Basic information
Classic Q1
4
General information and features
2.2 General information and features
This manual description of the basic unit is only valid in
connection with the manual for the control electronics
(e.g. REGxx).
Build
- Switch cabinet built-in devices
- Acc. to the VDE, DIN, and EG regulations
- Standard control electronics REG
- Basic device as intrinsically safe power section with current controller
- Uncontrolled field supply unit
- Optional units
Galvanic isolation between
- Power section and housing
- Power section and control electronics
The distances of air gaps and leakage paths adhere to the VDE standards (>8mm).
Components
- Completely isolated thyristor modules, comfortably over-dimensioned
- Only components customary in trade and industrially standardized
- LED displays
- Precision trimming potentiometer for precise adjustment
- Dip-switch for the system setting
Features
Series Classic Q1
Thyristor controller for dc motors
Power range 2.7 to 12 KW
Driving and braking in all 4 quadrants
Energy feedback
Intrinsically safe power section
Fast analog current control
Circular current-free double bridge circuit
Optional uncontrolled field rectifier
26-pole interface
Features of the control electronics used:
see MANUAL REGxx or third-party product
Optional units
Min. torque-free break 10ms
PI-setting by means of two 4-position switches
The control electronics is plugged to the front side and readily accessible
Connecting terminals are used as far as possible
Heavy current connections must be connected via power terminals
The output stage is a counter-parallel double bridge circuit
Anwendung
DC motors for circular current-free 4Q operation

Basic information
Classic Q1
5
Technical data
2.3 Technical data
Q1 230/180-x
Power connection:
200 … 250 V~
Auxiliary voltage connection:
200 … 250 V~
Output voltage:
± 180 V=
Cooling:
self cooling
Q1 230/180
15
25
40
Input current
A~
16.5
27.5
44
Output current
- peak 5s
- continuous
A=
A=
30
15
50
25
80
40
Electric power
kW
2.7
4.5
7.2
Dimensions
mm
200x240x100
200x240x100
200x240x127
Weight
kg
Fuses
(fast acting)
Input
Output
A
A
20
35
30
50
50
63
Mains choke
Type
K78-16
K84-25
K84-50
mH
1.2
0.7
0.5
Motor choke
Type
El 135A-16
EI 135B-24
EI 150B-40
mH
33
16
7
Q1 400/300-x
Power connection:
360 … 440 V~
Auxiliary voltage connection:
360 … 440 V~
Output voltage:
max. ± 300 V=
Cooling:
self cooling
Q1 400/300
15
25
40
Input current
A~
16.5
27.5
44
Output current
- peak 5s
- continuous
A=
A=
30
15
50
25
80
40
Electric power
kW
4.5
7.5
12.0
Dimensions
mm
200x240x100
200x240x100
200x240x127
Weight
kg
Fuses
(fast acting)
Input
Output
A
A
20
35
30
50
50
63
Mains choke
Type
K78-16
K84-25
K84-50
mH
1.2
0.7
0.5
Motor choke
Type
EI 135B-16
EI 150C-24
UI 120B-40
mH
45
30
15
(Inductivity for larger armature circuits on request)

Basic information
Classic Q1
6
Specifications
2.4 Specifications
Common specification
Mains frequency
50 or 60 Hz ±5 %
Protection rating
IP 00
Format
VDE 0100 group C / VDE 0160
Humidity rating
Class F acc. to DIN 40040
Site of installation
< 1000m above sea level
Operating temperature range
0 ... 45°C
Extended operating range
up to 60°C reduced by 2%/°C
Storage temperature range
-30°C to + 80°C
Amplification
Input signal
0…± 10 V=
Output
0… ± 200 % type current
Enable
> + 10 Volt
Current control loop circuit
Control precision
± 2 %
Control range
1:50
Over-current limiting
10 Sec. 200 % type current
Speed control loop circuit (see MANUAL REG)
Control precision (without actual value error)
± 0.1 %
Control range
> 1:300
2.5 Interfaces
Interface control electronics X3
Function
Connector no.
+ 24 V
±10 %
X3: 1 and 2
+ 15 V
±2 %
X3: 3 and 4
- 24 V
±10 %
X3: 5 and 6
- 15 V
±2 %
X3: 7 and 8
Device zero GND
0
X3: 9, 10, 11, 12, 13, 14
l –command value (GND)
0
X3: 15
l –command value (signal)
+10 V=
X3: 16
Current controller enable
+10 V=
X3: 17
Disable 1
+10 V=
X3: 18
Disable 2
+10 V=
X3: 19
Not connected
not connected
X3: 20
I (current) actual
±5 V=
X3: 21
Over-current power section
+10 V=
X3: 22
Ignition angle 1
+ 10 V=
X3: 23
Ignition angle 2
+10 V=
X3: 24
Drive ready BTB
+10 V=
X3: 25
Not connected
not connected
X3: 26

Mechanical installation
Classic Q1
7
Mounting
3Mechanical installation
3.1 Mounting
Adjustments
Switch S1
Pl circuitry
Current controller RVl-1
Switch S2
Pl circuitry
Current controller RVl-2
Switch S3
60 Hz setting
Contact 1,2 to ON
LED displays
Enable
Enable
green
enabled
Current command value
Current controller
RVl-1
green
control active
Current controller
RVl-2
green
control active
The luminous intensity depends on the trigger angle.
Disable logic
Bridge 1
green
Bridge 1 enabled
Disable logic
Bridge 2
green
Bridge 2 enabled
3-1 ED-Q1-Maßbild-M006-2

Mechanical installation
Classic Q1
8
Mounting
3-2 Q1-Q2-Maßbild-M006-2-1

Mechanical installation
Classic Q1
9
Transformer choke
3.2 Transformer choke
Rated current Q1-x-x-
15
25
40
Auto-transformer
Type
TU4/70
UI120-B
TU5/50
UI150-A
TU5/70
UI150-B
Dimensions a b c
mm
160x145x205
200x130x255
200x155x255
Weight
kg
16
21
28
Mains choke
Typ
K78-16
K84-25
K84-50
Dimensions a b c
mm
72x90x120
72x95x122
72x95x122
Weight
kg
1.5
1.8
1.8
Motor choke 180 V
Typ
El 135A-16
El 135B-24
Ul 150B-40
mH
33
16
7
Dimensions a b c
mm
115x120x145
115x130x145
128x132x185
Weight
kg
7
8,2
10,6
Motor choke 300 V
Typ
El 135B-16
UI 150C-24
UI 120B-40
mH
45
30
15
Dimensions a b c
mm
115x130x143
128x142x185
160x150x270
Weight
kg
8,2
12,10
16
Model UI
Model K, EI
c
ab

Electrical installation
Classic Q1
10
Connection diagram
4Electrical installation
4.1 Connection diagram
4-1 Q1-Anschlussplan-A016-2

Electrical installation
Classic Q1
11
Circuit diagram
4.2 Circuit diagram
4-2 Q1-Schaltplan-S068-1

Electrical installation
Classic Q1
12
Important CE notes
4.3 Important CE notes
The devices adhere to the EU guidelines 89/336/EWG of the technical EMC standards EN 61000-2
and 61000-4 provided that the following conditions are observed.
-The device, the power choke, and the filter capacitors are mounted on a 500x500x2mm
mounting plate.
-The mounting plate must be connected to ground using a 10mm² wire.
-The motor housing must be connected to ground using a 10mm² wire.
-The device ground X1:8 must be connected to the mounting plate using a 2.5mm² wire.
-Device PE screw must be connected to the mounting plate using a 4mm² wire, l = 50mm.
Two-phase connection
Mains choke type: see techn. data
Filter capacitors: 0.5 µF/600 V~ 2 x 1µF (x) + 2 x 0.5µF (y)
Conductor length between device and
mains choke <250 mm
Motor connection:
Motor conductors: l = 1.5 m, shielded
Tacho and all control conductors shielded l = 1.5 m, shielded
Shielding connected to PE
4-3 Q1-A-EMV-1

Electrical installation
Classic Q1
13
Connections
4.4 Connections
The order of the connections to the connector no. or the connection terminals is obligatory.
The input and output conductors may be altered or supplemented in accordance with the
electrical standards. All further advice is non-obligatory.
Adhere to:
- Connections and operating instructions
- Local regulations
- EU guideline 89/392/EWG
- VDE and TÜV regulations and Trade body guidelines
The controllers are delivered with an auxiliary
voltage input for 230 or 400V~.
The current consumption is 0.1 A.
The fuses F1 and F2 are rated for field current
(2.5 A f).
Auxiliary voltage and field supply are both
connected to the plug-in terminal X5.
The phase position of the auxiliary voltage and the
power supply voltage must correspond to each
other.
X5:14 corresponds to terminal 15 and X5:17
corresponds to terminal 16.
Field voltage
230 V~ connection equal to 210 V=
400 V~ connection equal to 360 V=or
210 V= to N across terminal X5:18
The max. field current is 1.5 A.
The field current is not monitored.
In case the field fuse F1 fails the
device is switched off.
Note:
Observe the type plate / control voltage XXX
4-4 Q1-Q2-Hilfsspannung-1
4-5 Q1-Q2Feld230-210-1
4-6 Q1-Q2-Feld-400-210-1
4-7 Q1-Q2-Feld400-360-1

Electrical installation
Classic Q1
14
Power connections
4.5 Power connections
Direct power connection:
The power connections must be protected by
means of fast acting fuses.
The power choke inductance must be >200H.
The phases of the power connection and the auxiliary
voltage must be equal.
There is an internal watchdog for the power connection.
If the power supply or the fuses fail, the device switches off
and the BTB contact opens.
Power connection via an auto-transformer:
Usually an auto-transformer is used.
The transformer performance is determined by the
permanent current and the secondary voltage.
Fast acting fuses F must be installed between the
transformer and the control unit.
The fuses are monitored concerning failure via the mains monitoring system.
The phases of the transformer voltage and the auxiliary voltage must be equal.
The contactor contacts before the transformer must be rated according to the starting current of
the transformer.
Protect the transformer by means of slow fuses.
Important:
For transformer secondary voltages < 230 V~ the
resistors R2 and R3 of the power section must be
adapted in the factory.
Specification on order: Transformer voltage
Operation with a 60Hz current supply:
When operating with a mains frequency of 60Hz the
contacts 1 and 2 of the DIP-switch S3 must be set to ON.
4-8 Q1-Netz-direkt-1
4-9 Q1-Netz-Spartrafo-1

Electrical installation
Classic Q1
15
Motor connection
4.6 Motor connection
Connection for a positive command value
Motor –
Motor +
Terminal
Terminal
X10:12
X10:10
Note:
Armature choke inductance:
L [mH] = UA/ IAx 2.4
Motor conductors must be
shielded.
Dynamic over-current:
The rated current of the
choke must be mind. 0.7
times the set peak current
so that the choke does not
reach the saturation range.
Conductor cross-section (minimal)
Type current
A
15
25
40
Mains power supply
mm²
1.5
2.5
4
Motor connection
mm²
1.5
2.5
4
A fuse F must be installed in the armature circuit. This fuse must be monitored and in case of
failure the control unit must be disconnected from the power supply.
Switching in the armature circuit
- DC circuit disconnected from the mains
- Enable disabled
Caution:
In case of incorrect switching >>> switch-off arc
Mains failure–Brake resistor
Break contact of the mains contactor K1
Dimension
Resistance RNB = max. armature voltage/2x type current
Braking effect only when the field is excited!
Important:
The power lines must be shielded and laid separately from the control
lines!
Electromagnetic interferences >>> see CE notes
K1 RNB
-L4
-F4.1
-
M
A2
(B)
A1
X10: 10 X10:
+
12
4-10 Q1-Motor-1

Electrical installation
Classic Q1
16
Actual value connection l
4.7 Actual value connection l
Tacho control
Suitable actual value encoders
- DC tacho generators
- Brushless tachogenerators with evaluation electronics
- Incremental encoder with evaluation electronics
Note: AC or three-phase current tachos with rectification
are not suitable.
Connection
Tacho line shielded, connect the shield to the device.
Tacho lines must be laid separately from the power lines (EMC).
Control electronics (adhere to MANUAL REG)
For a positive command value
Positive tacho X 1:8b
Negative tacho X 1:9
Shield X 1:8
Armature voltage control
For 4Q control with a small control range
(up to 1:50) and low demands on accuracy
and dynamics it is possible to use the
armature voltage as actual value signal.
Ground-referenced actual value
Fuses 2 x 0.1A directly at the tap of the armature voltage
Armature voltage >180 V= additional resistors
Use the (manufacturer) EXZU-UA1 device.
Note: adhere to the MANUAL REG
A potential-free armature voltage control is possible by using the
Unitek unit QTV 2-3.
X1: +-
8
REGx
8b 9
TG
M
10 12
1
X10:
*
* nur bei U >180V
0.1A
0.1A A
(B)
2
-L4
A
M
X1: 8b8 9
X10:
-F4.1
10 12
REGx
4-11 Q1-Tachoregelung-1
4-12 Q1-Ankerspannungsregelung-1

Settings
Classic Q1
17
Control parameters of the current controller
5Settings
5.1 Control parameters of the current controller
-The current control characteristics of the power sections can adjusted.
-The PI characteristics of the controller RVI-1 is set by the 4-position DIP switch S1.
-The PI characteristics of RVI-2 is set by switch S2.
-All switches are closed on delivery of the devices.
-This corresponds to the position for the lowest armature circuit inductance.
-The proportional amplification can be changed via the contacts 1 and 2.
-The integral time constant can be changed via the
contacts 3 and 4
Note:
Any current controller optimization must be checked by means of an
oscilloscope.
Measuring point X2 : 111 (REG) against GND
Measured values:
± 2.5 Veff according to type current
± 5 Veff according to peak current
Oscillogram - current adjustment (measured across REG - X2 : 111)
5-3 Q1-Q2-Oszillogramm-Strom-1
Fig. 1
Optimal adjustment
Fig. 2
Amplification too high
Fig. 3
Low P-amplification
Some important functions are indicated by LEDs.
Current controller enable (enable) and current command value directions (RVI-1 or RVI-2).
The green LEDs indicate the active states.
P
P
I
I
P
Imax
150K
47K
P-Anteil
100K I-Anteil
RVI
13
0,22µF
0,22µF
S1 od. S2
2
47K 40,33µF
5-2 Q1-Q2-Schalter-Strom-1
5-1 Q1-Q2-PI-Strom-1

Settings
Classic Q1
18
Signals
5.2 Signals
BTB signal X3:25 >+10 V
Error X3:25 <+10 V
Errors
Voltage error
24V, 15V, -15V
Input fuse defective / undervoltage
In case of errors or failure the power section is immediately
internally disabled without delay.
Power measurements
Measuring instruments
Multimeter for current and voltage
Shunt or clamp-on ammeter = ~
Measuring errors
Mean value >>> Effective value
corresponding to the form factor
approx. 1 to 5%
Measured values with a positive command value
Voltage: X10:10 negative X10:12 positive
Max. 0.75 x power supply voltage
with 400 V~ >>> 300 V=
Current: Ammeter in the motor circuit
5s 200%, continuously 110% type current
Measured values on REGxxx (selectable - see MANUAL REGxx)
Speed X2:109 ±5 V or ±10 V for ±100% speed
Current X2:111 ±5 V or ±10 V for ±100% type current
IA
X10:
-L4
A
U
M
V
A
-F4.1
11 X10: 12
5-4 Q1-Motor-Mess-1

Settings
Classic Q1
19
Commissioning Q1 x/x-x with REGxx
5.3 Commissioning Q1 x/x-x with REGxx
Check the connections prior to any commissioning.
Observe the type plate!
Basic power connections Q1
Mains connection
Power
Terminal
X10:15, X10:16
Mains connection
Auxiliary voltage
Terminal
X5:14, X5:17
Field
Terminal
X5:18
Mains connection
A1/A2
Terminal
X10:10, X10:12
Motor connection
F1/F2
Terminal
X5:19, X5:20
Field connection
PE
Earth screws PE on the housing
Basic control connections REGxx
Enable
Contact between X1:3 and X1:4
Command value
Signal X1:6
GND X1:8a
Actual value
Signal X1:9
GND X1:8b
Shields
X1:8
Control electronics REGxx
Switch
S4
P-ampl.
Position 4
Switch
S5
I-comp.
Position 4
Switch
S8
D-ampl.
Position 8
Switch
S9
Actual value
Position 8
Potentiometer
I1
Peak current
10%
Potentiometer
I2
Peak current
10%
Potentiometer
ID
Continuous current
100%
Potentiometer
XP
Amplification
50%
Potentiometer
INT
Integrator
Left full scale
Potentiometer
nmax
Speed
Left full scale
Potentiometer
Offset
Offset
50%
This manual suits for next models
8
Table of contents
Other Unitek Controllers manuals
Popular Controllers manuals by other brands
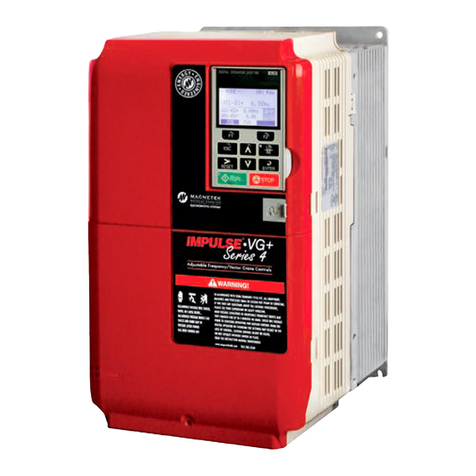
Magnetek
Magnetek Impulse G+ series 4 instruction manual
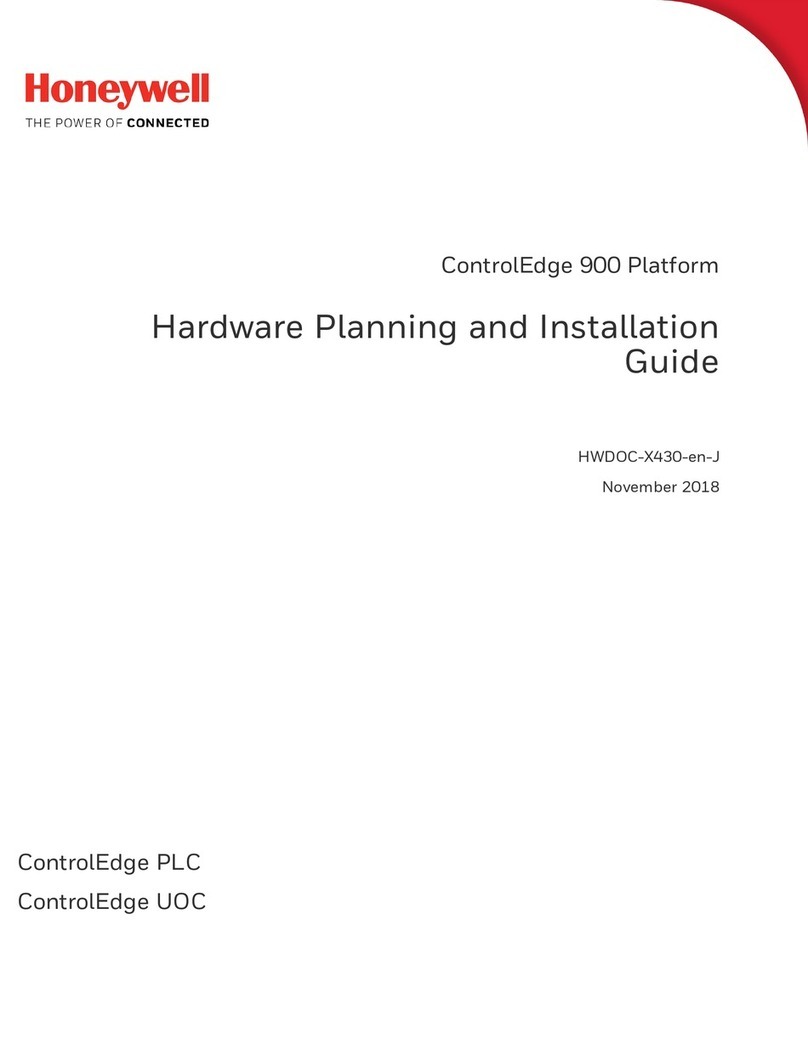
Honeywell
Honeywell ControlEdge 900 platform Hardware Planning and Installation Guide
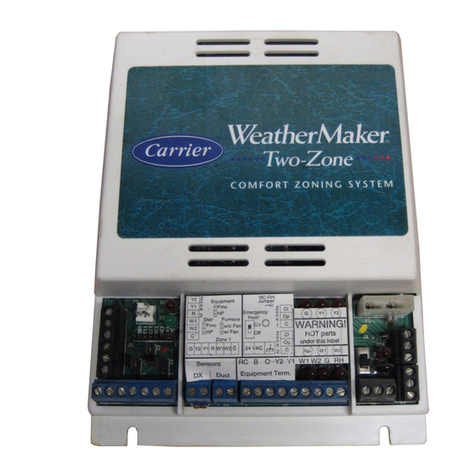
Carrier
Carrier WEATHERMAKER ZONEKIT2ZCAR Installation and start-up instructions
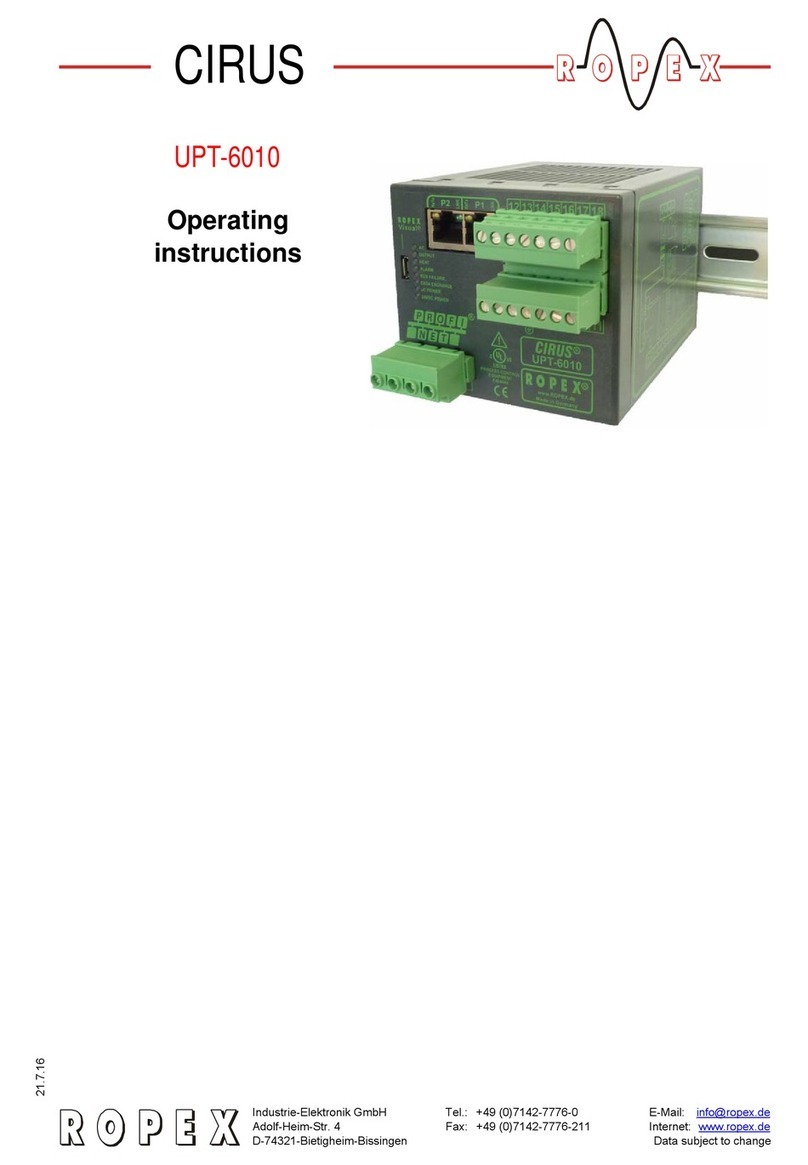
Ropex
Ropex CIRUS UPT-6010 operating instructions

Novar
Novar lingo installation instructions

Cumberland
Cumberland PNEG-881 Installation and operation manual