Vibration Research VR8500 User manual


VR8500
Table of Contents
VR8500………………………………………………………….....3
Setting up the Hardware………………………………………….3
Establishing communication with PC…………………………...4
Input Configuration (setting sensitivities for inputs)………….. 6
System Limits (shaker limits and moving mass)………………..7
System Check……………………….……………………………. 7
SineVIEW test set-up……………………………………………. 9
RandomVIEW test set-up……………………………………….12
ShockVIEW test set-up (Classical Shock)……………………...14
FDRVIEW test set-up……………………………………………16
Automatic Report generation…………………………………...18
Tips & Tricks……………………...………………………….......20

VR8500
2

VR8500
3
VR8500:
Thank you for purchasing a VR8500 vibration control system from Vibration Research Corp. We
appreciate your business. Vibration Research Corp. is continually upgrading the features and capabilities
of our products. Please visit our website (www.vibrationresearch.com) regularly to download the latest
available VibrationVIEW software for your VR8500 controller.
Also, in the event your have questions regarding your system you can either contact the V.R.C.
representative from whom your controller was purchased, or contact our product support staff directly at
support@vibrationresearch.com or call 616-669-3028 from 8-5 Eastern, Monday-Friday.
SETTING UP THE HARDWARE:
Connecting the VibrationVIEW I/O hardware:
1. Set up the computer in the conventional configuration, with power cables, mouse, keyboard, and
monitor.
2. Connect the VR8500 network port to the dedicated network card in the computer using the included
yellow crossover cable. If your VR8500 is labeled "Adapter Cable Required", the included red
adapter cable and metallic CAT5 in-line coupler MUST be connected between the yellow crossover
cable and the network port of the VR8500.
3. Connect the line cord to the VR8500. The power input will automatically switch for voltage 90-
250VAC and 50/60 Hertz.
4. Connect the shaker amplifier's input to the Drive output connector on the rear of the VR8500.
5. Connect an accelerometer to Channel 1 of the VR8500. Other accelerometers can be connected to
Channels 2,3 and 4.

VR8500
4
Connecting two or more VR8500 units
1. Two or more VR8500 units require a network switch.
2. Connect the first VR8500 to port 1 on the switch. Additional VR8500's can be connected to port 2,3,
and 4 on the switch. Connect the computer to highest numbered
port with the supplied cable.
3. Connect 120 VAC power cords to each of the VR8500's.
4. Connect the shaker amplifier's input to the Drive output connector
on the first VR8500. For systems controlling two shakers simultaneously, connect the second
shaker’s amplifier input to the Drive output connector on the second VR8500.
5. Connect accelerometer channels 1-4 to channels 1-4 of the first VR8500, accelerometer channels 5-8
to channels 5-8 on the second VR8500, accelerometer channels 9-12 to channels 9-12 on the third
VR8500 accelerometer and channels 13-16 to channels 13-16 on the fourth VR8500, etc. up to 32
channels.
ESTABLISHING COMMUNICATION WITH PC:
Configuring the VR8500
1. Set up the dedicated network card for
VibrationVIEW. Select the network card
dedicated to the VR8500 from the
Network Connections applet in Control
Panel ("Start --> Settings --> Control
Panel --> Network Connections" in Win
XP). Your network connection will
display the name assigned when the
network card was installed, typically
"Local Area Connection 2". Double click
on the "Local Area Connection 2" and
click on the "Properties" button.
2.
Remove the check marks from "Client for
Microsoft Networks", and "File and
Printer Sharing for Microsoft Networks."
Select Internet Protocol (TCP/IP) and
click the "Properties" button to continue.

VR8500
5
3. Assign address 192.168.3.10 and subnet mask 255.255.255.0 as shown in the Internet Protocol (TCP/
IP) Properties dialog box. If multiple network cards are installed in the computer the IP address can
be adjusted. Other recommended values are 192.168.2.10 and 192.168.4.10, although any Class C or
Class D subnet will work. Click the OK button to return to the previous dialog
4. Click the Advanced tab in the Properties dialog box. Make sure Internet Connection Sharing for this
connection is unchecked (NOT enabled).
5. VibrationVIEW must be configured to use the appropriate network connection after the network is
setup. Start VibrationVIEW by double-clicking the VibrationVIEW icon on the desktop. Select the
Configuration..Hardware menu command.

VR8500
6
6. Select the network card previously
configured. Typically this will be
192.168.3.10. Click the apply button.
7. Your VR8500 serial number will be added to
the drop down menu for Channels 1-4 when
it initially connects to the computer. Select
the appropriate VR8500 serial number to
configure channels 1-4 and, optionally,
channels 5-8, channels 9-12, and 13 through
32 (in blocks of 4 channels). The VR8500
control boxes are assigned addresses from the
range listed in the Control Boxes Address
parameters. This does not need to be
changed.
INPUT CONFIGURATION (setting sensitivities for inputs):
The inputs must be configured for each connected
accelerometer. Each input can be configured as
single ended, differential and optionally capacitor
coupled. Single ended inputs can also provide a
constant current source to power your
accelerometers. Other types of accelerometers
such as charge coupled accelerometers require
external conditioning. Be sure to enter the proper
calibration factor (in mV/g) for each channel.
If the connected accelerometer has TEDS
(Transducer Electronic Data Sheet) containing the
calibration information, simply click the “Read
TEDS” button and the information will
automatically be entered.
When the appropriate values are entered, click the
"OK" button. The new accelerometer sensitivity
factors will take effect immediately.
Note: Be sure to check the “Accel power source” box if you want the VR8500 to provide the constant
current source to your accel.

VR8500
7
SYSTEM LIMITS (shaker limits and moving mass):
The controller checks the system specifications to
determine if the shaker is able to perform the current test.
The shaker force, velocity and displacement limit values
only need to be entered once when the system is first
configured. The fixture and product masses that are
required to properly compute the acceleration limits of the
shaker must be entered every time the fixture or product
mass is changed.
To set the system limits, select the Configuration..System
Limits menu command. In the dialog box, select either the
system matching your setup or enter the specifications of
your system. These specifications should be listed in the
manual for your shaker system.
To enter the system mass, select the Configuration..System
Mass menu command. Enter the masses for all the shaker
parts on your system. If your system does not have one of
the listed parts, enter zero for that item's mass. The sum of
these mass values is used to calculate the maximum
operating acceleration for your system using Newton's law:
Force = mass * acceleration
SYSTEM CHECK:
To verify that the input and output levels and frequencies are correct, perform the following procedure:
1. Select the Test..System Check menu command to switch the system into
System Check mode.
2. Select the Configuration..Inputs menu command. Verify that your
accelerometer sensitivity and power source settings are configured
appropriately. The constant current source is enabled in this dialog box.
If you are using constant current accelerometers or a conditioner that
requires a constant current source make sure the "Accel power source" is
checked. Click the "OK" button.
3. For Electro Dynamic shakers, enter a frequency of 30 Hz and a
displacement of 0.1 inches (peak-to-peak) in the System Check Control
Center. These are the default values. For Servo Hydraulic shakers, set
to 20 Hz and 0.05 inches (peak-to-peak).
4. Verify that the input levels are near zero (double right-click on the graph
to autoscale).

VR8500
8
5. Click the "Auto" button. The output level should slowly ramp up until the shaker approaches a 0.1-
inch peak-to-peak displacement (0.05 inches if using the Servo Hydraulic recommended set-up).
6. If the shaker does not move, click the "Stop" button to turn the output off. Verify that the Drive
output connector from the VR8500 is
connected to the shaker amplifier's input,
that the amplifier is turned on and that
the amplifier output is connected to the
shaker. Return to step 4.
7. If the shaker still does not move, connect
the Drive output connector of the
VR8500 to an oscilloscope or true RMS
voltmeter, set the output voltage level to
0.5 volts (0-to-peak) and verify that you
have a 0.5 volt (0-to-peak) amplitude
reading (0.35 volts RMS). If the Drive
output connector is not measuring 0.35
volts RMS, your system may require
calibration.
8. If the shaker vibrates, but the input
waveform remains flat, click the "Auto"
button a second time so that the text on
the "Auto" button is dark and the output stops ramping up. Check the accelerometer cables to verify
that they have good connections and that the accelerometer conditioning equipment is turned on. If
you are using the internal current source to power the accelerometer, verify that "Accel power
source" on Configuration..Inputs dialog box is checked. If there still is no input signal, connect the
conditioned accelerometer signal to an oscilloscope or voltmeter and verify that you see a voltage
reading. If there is no reading, click the "Stop" button to turn the output off, replace the
accelerometer cable, accelerometer and/or the accelerometer conditioning equipment with devices
known to be working and return to step 4. Note:
most problems are due to bad cable connections.
9. Once you get both an output and an input signal,
use a displacement measurement tool to verify that
the shaker peak-to-peak displacement matches the
value shown in the System Check Control Center.
If it does not match, select the
Configuration..Inputs menu command to verify
that the accelerometer sensitivity settings match
the calibrated values for the accelerometers you
are using.
Note: To use the V Scope Displacement Measurement Tool – tape or hold firmly on shaker head so
that it moves in the direction of vibration (see arrows). The lines will blur and intersect at the
0.1 inch mark on the measurement tool if the shaker is moving as directed above (0.05 for the
servo hydraulic set-up). If the lines don’t intersect there, check that your accelerometer
sensitivities are set correctly (and power source on, if required).

VR8500
9
SineVIEW TEST SET-UP:
Click the New Test button and
select “Sine” to begin defining a
new Sine test. This will guide you
through the following series of
configuration dialog boxes. Default values will be supplied for all parameters. If you are unsure about a
parameter, use the default value (click the “Help” button in the lower right corner of the Settings window
for specific Help information). After all the values for each dialog tab are entered, click the next tab to
advance to the next set of information for setting up the test.
1. Sine Profile - The amplitude and
frequency breakpoints and the
desired control parameters
(acceleration, velocity or
displacement) for the test are
entered here. Use the scrollbar to
scroll through the defined segments
and the Insert/Delete buttons to add
or remove segments. The small
arrow next to the numbers on the
left of the window indicates the
current insertion/deletion point. A
test may be composed of over 1000
segments.
2. Sine Schedule - The duration of the
test is entered here. Durations may
be entered in time duration, number
of sweeps or number of cycles. The
test schedule is also used to
schedule sweeps scaled to different
amplitude levels and to select one or
more fixed frequency tones.
3. Sine Sweep - Your sweep rate is set
next. Enter the sweep rate and click the drop box to select the desired units.
4. Sine Parameters - The feedback control parameters for the test are entered here. For most tests, the
parameters may be left at their default values. In some cases (such as when the control accelerometer
sees a large resonance) these values will need to be tuned.

VR8500
10
5. Sine Limits - The tolerance and abort limits for
the test are entered here. The control tolerance
and abort limits apply to the control signal. If
monitoring channels are being used, enable the
appropriate channels in the Sine Channels
dialog box and enter the plus and minus abort
limits for the monitor channel. All limits are
measured in dB relative to the demand signal
at the active frequency.
The tolerance lines are reference lines shown
on the graphs (brown dashed lines) and are
used to determine when the controller goes
from “Starting” to "Run" mode when starting a
test (Run button is Yellow during “Starting”
and changes to Green when “Running”).
The Plus and Minus aborts are limits that,
when exceeded, cause the test to abort. The
control abort lines are shown on the graphs as
solid red lines.
The maximum output voltage limits, both absolute (Max Output parameter) and relative to the
measured acceleration level (Max System Gain parameter) are also entered here. These parameters
are safety limits that will cause the test to abort when something goes wrong (for example, when an
accelerometer cable comes loose.)
Refer to the "How to tune Sine controller
parameters" section in the manual for more
information on how to determine the
appropriate Max Output and Max System Gain
parameters for your test.
6. Sine Channels - The control channels for the
test are selected here, as well as a way to
combine the selected control channels and
whether or not to use tracking filters for either
the control channel or the monitor channel
inputs.
7. Sine Data Storage - The directory, into which
the data generated by this test will be stored, is
entered here. Data can be automatically stored
at a regular time interval, sweep interval, at the
end of each level (levels are defined using the
Schedule dialog box) and at the end of the test.
Select the check boxes for your desired data
storage times and enter the desired interval
times/cycles.

VR8500
11
At this point the test definition is complete. Click the "Finish" button to close the dialog box. You will be
asked if you want to save the test definition to the hard drive. Click the "Yes" button; enter the desired
name and click the "Save" button to save the test.
To access parameters for specialized tests, select the Test..Edit Test Settings menu command (or use the
toolbar button "Settings") and click the Resonance, Notching or Step Test tabs.
Additional Tips & Tricks for SineVIEW
To show a large display of Frequency and input readings, select View..Sine Big Display (Ctrl+B).
Click ‘Enable Manual Controls’ to manually control the frequency and amplitude of the sine tone
Left mouse click on frequency toggles sweep down
Righ mouse click on frequency toggles sweep up
Double-click frequency steps to integer Hz values
Mouse scroll wheel increases or decreases the dB level of the test
When defining the sweep rate in sine, you can change the sweep rate from “oct/min” to “min/sweep
(Logarithmic)” to see how long one sweep will take.

VR8500
12
RandomVIEW TEST SET-UP:
To run a preset test profile, click on the Test Type button and select “Random”. Next, click the Open Test
button and select a profile. Or, to define your own profiles, click the New Test button and select
“Random” to begin defining a new Random test. This will guide you through the following series of
configuration dialog tabs. Default values will be supplied for all parameters. If you are unsure about a
parameter, use the default value (click the “Help” button in the lower right corner of the Settings window
for specific Help information). After all the values for each dialog tab are entered, click the next tab to
advance to the next set of information for setting up the test.
1. Random Table - The amplitude and
frequency breakpoints for the test are
entered here. Use the "Insert" and
"Delete" buttons to add or remove
segments. The small arrow next to the
numbers on the left of the window
indicates the current insertion/deletion
point.
2. Random Schedule - The duration and
output amplitude for the test are entered
here. Durations are entered in time,
using the format hours:minutes:seconds.
3. Random Parameters - The feedback
control parameters for the test are entered
here. For most tests the parameters may
be left at their default values. In some
cases (such as when the control
accelerometer sees a large resonance)
these values will need to be tuned.
4. Random Limits - The tolerance and abort
limits for the test are entered here. All
limits are measured in dB relative to the
demand signal. The tolerance lines are
reference lines shown on the graphs
(brown dashed lines) and are used to
determine when to switch to "Run" mode
when starting a test. When the number
of lines outside the abort limits exceeds
the "Max Outlier %", the test will be aborted. The abort lines are shown on the graphs as solid red
lines.
The Max System Gain and Output Threshold parameters are safety limits that depend on your
particular shaker and amplifier. Refer to the "How to tune Random controller parameters" section in
the manual for more information on how to tune these parameters for your system.
The maximum output voltage limit is also entered here. This parameter limits the maximum output
voltage produced by the controller.

VR8500
13
5. Random Channels - The control channels are selected here, as well as averaging or extremal channel
combination methods.
6. Random Data Storage - The directory into which the data from this test will be stored is selected here.
Data can be automatically stored on a regular time interval, at the end of each level (levels are
defined using the Schedule dialog box) and at the end of the test. Select the check boxes for your
desired data storage times and enter the desired interval times.
At this point the test definition is complete. Click the "Finish" button to close the dialog box. You will be
asked if you want to save the test definition to the hard drive. Click the "Yes" button; enter the desired
name and click the "Save" button to save the test.
To access parameters for specialized tests, select the Test..Edit Test Settings menu command (or use the
toolbar button "Settings") and click the R-o-R, S-o-R, Notching or Import Test tabs.
Additional Tips & Tricks for RandomVIEW
To see the full spectrum outside of the control band, select Graph..Edit Graph Settings (Ctrl+G)and
clear the check box for “Show Only Active Lines”.
When generating random profiles from recorded data, the high Hz content that drops off and has no
significant levels can be quickly removed by selecting the last significant Hz in the table and clicking
Last.

VR8500
14
ShockVIEW TEST SET-UP:
Click the New Test button and select “Shock” to begin defining a new Shock test. This will guide you
through the following series of configuration dialog tabs. Default values will be supplied for all
parameters. If you are unsure about a parameter, use the default value (click the “Help” button in the
lower right corner of the Settings window for specific Help information). After all the values for each
dialog tab are entered, click the next tab to advance to the next set of information for setting up the test.
1. Pulse - The desired pulse width, shape and amplitude for the test are entered here. Also, the
allowable pre-pulse and post-pulse
acceleration levels are entered here as
a percentage of the pulse peak
acceleration level.
2. Schedule - The duration of the test, in
number of pulses, is entered here. The
schedule also may be used to enter
levels scaled to different amplitudes.
3. Parameters - The parameters that
control the behavior of the control
loop are entered here. The parameters
generally may be left at the default
settings. Refer to the "How to tune
Shock controller parameters" section
for more information on how to fine-
tune these parameters for your system.
4. Limits - The tolerance and abort limits
for the test, set as a percentage of the
peak output and measured relative to
the demand time waveform, are
entered here. The tolerance lines are
reference lines shown on the graphs
(brown dashed lines) and are used to
determine when to switch to "Run"
mode when starting a test. The Plus
and Minus
aborts are limits that, when exceeded,
cause the test to abort. The limits on
the allowable drive voltage are also
entered here.
5. Channels - Select which channel or
channels you want to use as the control signal here. When selecting multiple channels, the time
waveforms of the selected channels are averaged together.

VR8500
15
6. Data Storage - The directory into which the data from the test will be stored is selected here. Data
can be automatically stored at a regular pulse interval, at the end of each level (levels are defined
using the Schedule dialog box) and at the end of the test. All pulses that lie outside of the defined
tolerance lines can also be stored.
At this point the test definition is complete. Click the "Finish" button to close the dialog box. You will be
asked if you want to save the test definition to the hard drive. Click the "Yes" button; enter the desired
name and click the "Save" button to save the test.
To access parameters for specialized tests, select the Test..Edit Test Settings menu command (or use the
toolbar button "Settings") and click the Import, Breakpoints or SRS tabs.
Additional Tips & Tricks for ShockVIEW
To limit shaker displacement, use the “Square Shape” setting on the Pulse tab. Also, be sure to un-check
the “Mil-STD pulse limits” on the Limits tab if MIL-STD settings aren’t required.

VR8500
16
FDRVIEW TEST SET-UP:
Click the New Test button and select “Field Data Replicator” to begin defining a new FDR test. This will
guide you through the following series of configuration dialog tabs. Default values will be supplied for
all parameters. If you are unsure about a parameter, use the default value (click the “Help” button in the
lower right corner of the Settings window for specific Help information). After all the values for each
dialog tab are entered, click the next tab to advance to the next set of information for setting up the test.
1. Playback - The name of the playback file, the record
level and the sample rate for that file are entered here.
There are also buttons for exporting and importing
waveform data. For details on importing and
exporting waveform
data, refer to the "How to import and export Field
Data Replicator waveforms" section. As an option,
the playback file can also be recorded at this time, by
pressing the "Record Playback File" pushbutton.
2. Record - The playback file can be optionally recorded
at this time. The record option is accessible by
pressing the "Record Playback File" pushbutton on
the "Playback" tab. Enter the desired sample rate in
the sample rate dialog, select the connected channel,
and press the "Next >" button to start data-recording.
Press "Next >" again to stop recording, and enter the
storage data file name. The wizard will return to the
playback tab, where the newly recorded file is now
ready for playback.
3. Schedule - The time duration of the test is entered
here. The test schedule also is used to schedule
durations where the output signal is scaled to different
amplitudes.
4. Parameters - The feedback control parameters are
entered here. In most cases the default values will be sufficient. Refer to the "How to tune Field
Data Replicator controller parameters" section of the manual for more information on how to tune the
parameters specifically for your system.
5. Limits - The abort limits for the test are entered here. The control (Ch1) abort limit applies to the
control signal, measured using the accelerometer connected to channel 1. The Output Drive limits
are also entered here.

VR8500
17
6. Filter - The frequency range over which the controller will
operate is entered here. Typically one would select
control from 0 Hz up to 40% of the sampling rate. If you
wish to filter out low frequencies to limit the displacement
requirements or filter out high frequencies to avoid shaker
resonances, a smaller frequency range can be specified.
You can also enable Notch Filtering here. By placing a
check in the Enable Notch checkbox, you may specify a
frequency range to filter out.
7. Data Storage - The directory into which the data from this
test will be stored is selected here. Data can be
automatically stored at a regular time interval, at the end
of each level (levels are defined using the Schedule dialog
box) and at the end of the test. Select the check boxes for
your desired data storage times and enter the desired
interval times.
At this point the test definition is complete. Click the "Finish"
button to close the dialog box. You will be asked if you want
to save the test definition to the hard drive. Click the "Yes"
button; enter the desired name and click the "Save" button to
save the test.

VR8500
18
AUTOMATIC REPORT GENERATION:
Reports are generated using mail merge type processing. The program reads in a template file, substitutes
data values and graphs in place of keywords, and writes the resulting data to an output file. The template
files can be either plain text or Rich Text Format files. Plain text files can have data values but no graphs.
Rich Text Format files (using extension .rtf) can contain data values and graphs, as well as any text
formatting and other graphics elements that can be inserted into an RTF file. From the VibrationVIEW
software, click on the Help menu and select “Help” and click on the last item in the “How To” section,
which is “Create Customized reports” to see the different keywords and examples for reporting as well as
information on using Forms.
The default templates are stored in subdirectories of the directory c:\Program
Files\VibrationVIEW\Templates. Sine templates are stored in the Sine subdirectory, Random templates
in the Random subdirectory, etc. To create custom reports, new templates can be created using a RTF
editor file and stored in the appropriate directory. One suitable RTF file editor is WordPad, a part of
Windows 95/98/NT/XP that is usually installed under Start..Programs..Accessories..WordPad. If this
program is not installed on your computer, it can be added by selecting it in the "Add/Remove Programs"
control panel, Windows Setup tab, listed under "Accessories". Most Windows Word-Processor programs
will also read and write RTF files.
To automatically generate a report during a test,
go to Settings..Schedule and click on the “Insert”
button in the lower left corner to add a step to the
schedule. Use the dropdown list and select a report
option (view report, save report, etc).
Another feature that can be used with automatic
reporting is the Forms tool. See the Help file or
Manual for more detailed information on
incorporating forms into your test and customized
reports.
Data entry forms can be used to schedule data entry
at any time during the test. Typically a data entry
form is used to record test setup at the start of a test.
The most recent data entry form data is accessable
from the report.
The forms are html (hypertext markup languague)
files which typically are located in
C:\VibrationVIEW5\Program
Files\Templates\Sine\Forms, C:\VibrationVIEW5
\Program Files\Templates\Random\Forms,
C:\VibrationVIEW5\Program
Files\Templates\Shock\Forms, or

VR8500
19
C:\VibrationVIEW5\Program Files\Templates\DataReplay\Forms. The html file can contain any html
element which can be displayed by Internet Explorer. A typical html form file contains a single form with
controls for text entry. The text can be automatically inserted into the test report. With a form the data
entry can occur during test setup, and the appropriate report run at the end of the test.
An HTML Form is a section of a document containing normal content, markup, special elements called
controls (checkboxes, radio buttons, menus, etc.), and labels on those controls. Users generally
"complete" a form by modifying its controls (entering text, selecting menu items, etc.), before submitting
the form to VibrationVIEW for processing.
Automated Help File:
The Stop Code section Info button links to the appropriate section of
the Help File that explains the stop code and possible reasons for the
code.
The Help button in the lower right corner of all Configuration menu windows or Settings windows link to
the section of the Help File that explain each of the entries in these windows.
Table of contents
Other Vibration Research Control System manuals
Popular Control System manuals by other brands

GUARDIAN GEAR
GUARDIAN GEAR ZW8198 Assembly instructions

LEGRAND
LEGRAND QMotion QzHub3 Guide
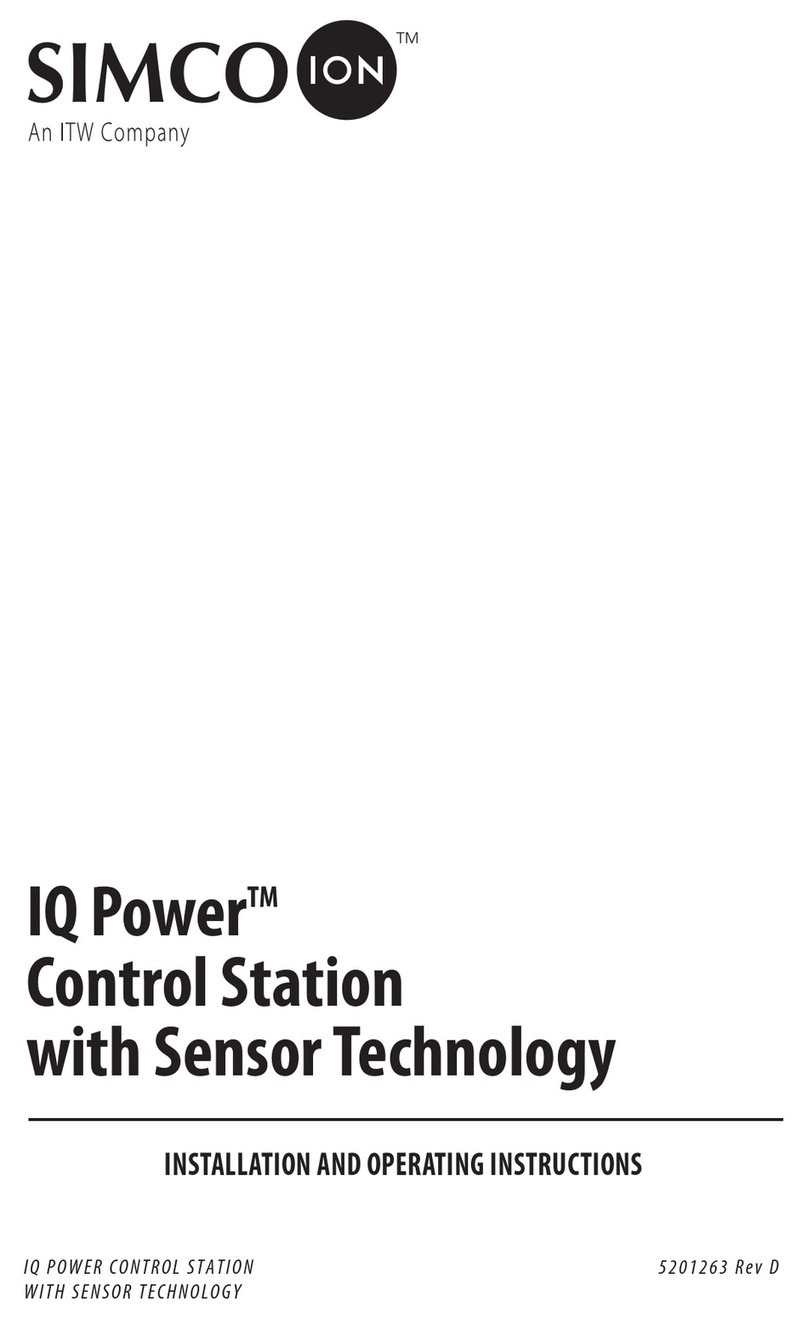
Simco-Ion
Simco-Ion IQ Power Installation and operating instructions
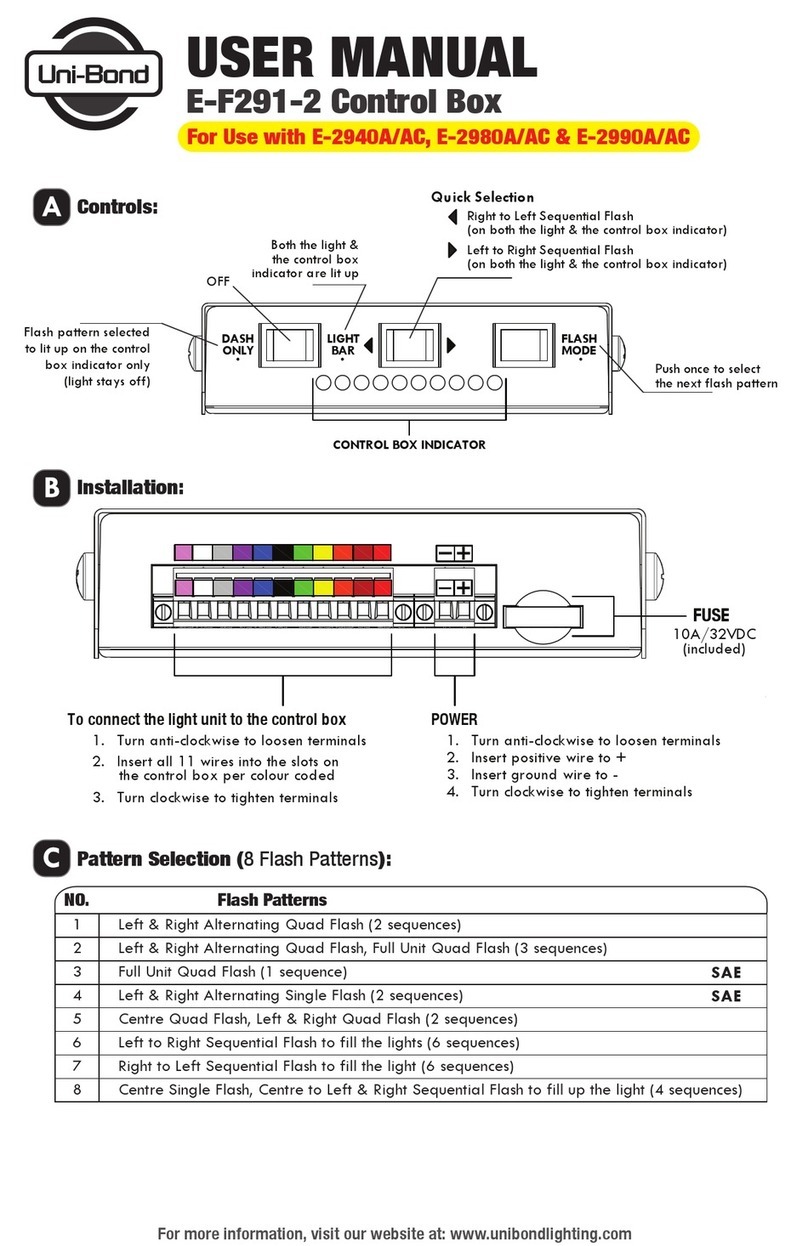
Uni-bond
Uni-bond E-F291-2 user manual
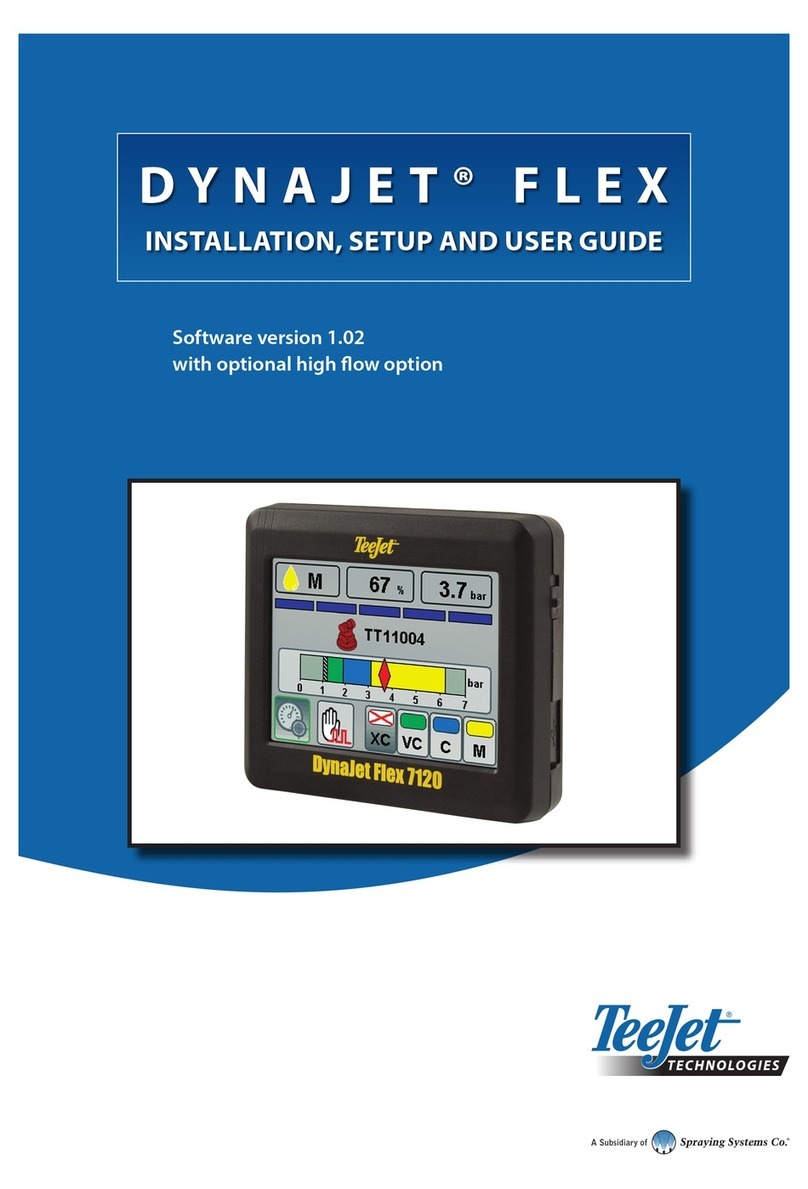
TeeJet Technologies
TeeJet Technologies DynaJet Flex Series INSTALLATION, SETUP AND USER GUIDE
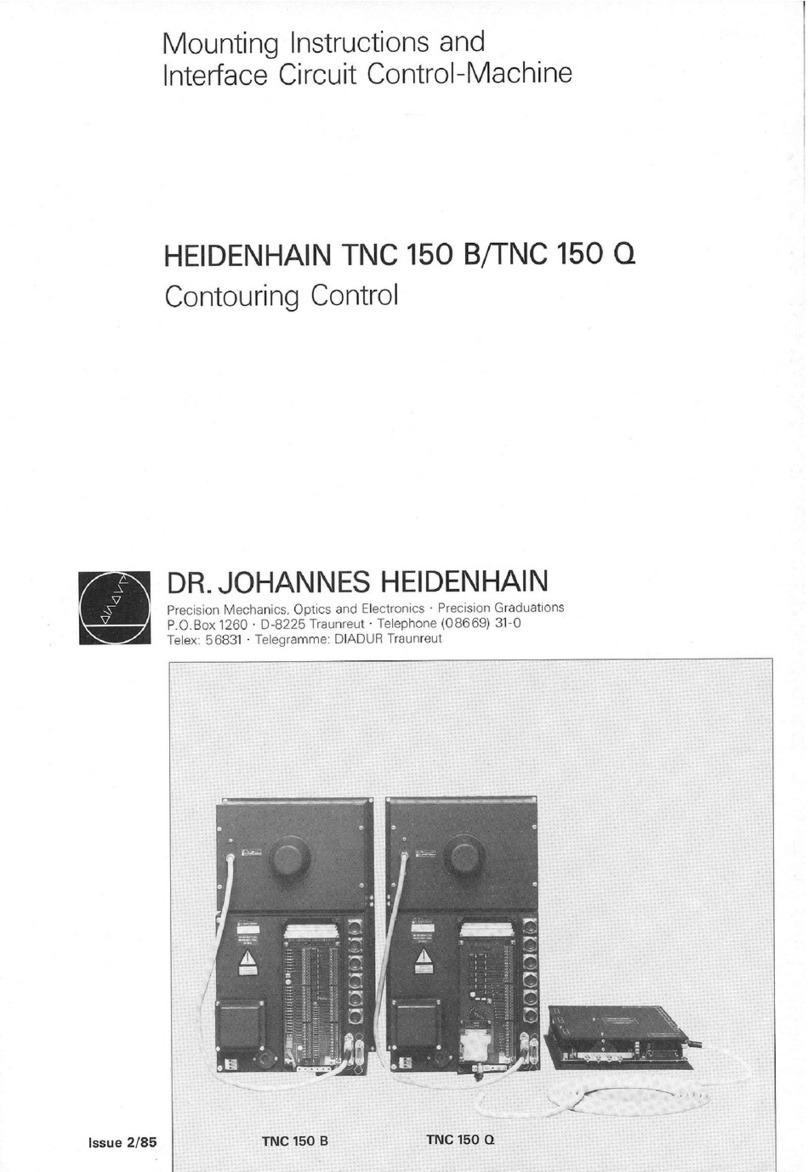
HEIDENHAIN
HEIDENHAIN TNC 150 B Mounting instructions