Vogt BP360 User manual

SERVICE MANUAL
BP360

NOTICE
This manual is the property of the owner of this particular Vogt Ice,
LLC machine.
Model #____________________ Serial #____________________
It is to be left on the premises with this machine at all times. After
start-up, it should be stored in a safe place where it can be readily
available when needed for future reference in maintaining
troubleshooting or servicing.
Failure to comply with this notice will result in unnecessary
inconvenience and possible additional expenses.
This manual is intended as an informational tool for the installation,
operation, maintenance, troubleshooting, and servicing of this
equipment. If an existing situation calls for additional information not
found herein, we suggest that you contact your distributor first. If
further assistance or information is needed, please feel free to contact
the factory at 502-635-3000 or FAX at 502-635-3024.
IMPORTANT: The Warranty Registration/Start-Up Report found in the
front of this manual is to be completed and returned to the factory
promptly after the official start-up.
Please return to: Vogt Ice, LLC
1000 W. Ormsby Ave.
Suite 19
Louisville, KY 40210

Vogt Ice, LLC
1000 W. Ormsby Ave, Ste. 19
Louisville, KY 40210
502-635-3235
FAX 502-635-3024
Vogt Order No.:
THIS FORM MUST BE SENT TO VOGT TO
ACTIVATE WARRANTY
Warranty Registration / Start-Up Form
BP360 Automatic Ice Block Press
Model Number:
Serial Number:
This form must be filled out completely and signed by the customer in order to assure acceptance by Vogt
Date of Start-Up:
Form Completed By:
Distributor
Company Name:
Phone:
Address:
City:
State:
Zip:
Service Company
Company Name:
Phone:
Address:
City:
State:
Zip:
Customer (Location of Equipment)
Company Name:
Phone:
Address:
City:
State:
Zip:
PRE-OPERATION CHECK
OPERATION CHECK
Machine room suitable 38°F min., 110°F max.
Motor Power Supply _____ V _____ PH _____ Hz (machine
not running)
Control Power Supply _____ V _____ PH _____ Hz (machine
not running)
Water supply and drains connected properly
Machine securely mounted to floor
Oil cooler water supply and return plumbed
Water injection supply plumbed
Ice supply system properly attached to ice chute
Wired contacts from photovoltaic to ice supply system
Tools clear of machine and compacting chamber
Instruction manual and warranty certificate left on-site
Name of person left with: _________________________
Motor Power Supply _____ V _____ PH _____ Hz (machine running)
Control Power Supply _____ V _____ PH _____ Hz (machine running)
Proper direction of rotation on hydraulic pump motor
Machine cycles properly
Hydraulic motor amps RLA _____ Actual _____
Water injection timer set properly
Compact hold delay set properly
Compact hold delay light on panel turns on once per cycle
Pressure gauge on manifold achieves 2000 PSIG when compacting block
Comments:
Technician Signature:
End User Signature:
I certify that I have performed all of the above procedures

Vogt Ice, LLC
Manufacturers of Quality Ice Machines
Located in Louisville, Kentucky since 1880
Sales –1-800-959-8468
Service –1-502-635-3000
Parts –Your Local Distributor
Call your local distributor first for all of your parts and service needs

i
Table of Contents
Model BP360 Automatic Ice Block Press
Chapter 1 Introduction ........................................................................................................................................................1-1
A Brief History of Our Company.......................................................................................................................................1-1
Vogt Energy-Savings Tube-Ice® Machines .......................................................................................................................1-1
Preview ............................................................................................................................................................................1-1
Important Safety Notice...................................................................................................................................................1-1
Safety Symbols and What They Mean .............................................................................................................................1-2
Assembly Drawing Model BP360.....................................................................................................................................1-3
Chapter 2 Receipt of Your Vogt Ice Machine.......................................................................................................................2-1
Inspection.........................................................................................................................................................................2-1
Safety Valves....................................................................................................................................................................2-1
Machine Room.................................................................................................................................................................2-1
Storage (Prior to Installation and Start-Up).....................................................................................................................2-2
Vogt Model Nomenclature ..............................................................................................................................................2-2
Chapter 3 Installing Your Vogt Ice Machine.........................................................................................................................3-1
Water Supply and Drain Connections..............................................................................................................................3-1
Ice Supply.........................................................................................................................................................................3-2
Ice Cut-Off Slide ...............................................................................................................................................................3-2
Light Intensity...................................................................................................................................................................3-2
Space Diagram .................................................................................................................................................................3-3
Wiring Diagram and Electrical Connections.....................................................................................................................3-4
Phase Check, Voltage Imbalance and Current Imbalance ...............................................................................................3-4
Phase and Rotation Check ...........................................................................................................................................3-4
Voltage Imbalance .......................................................................................................................................................3-5
Current Imbalance .......................................................................................................................................................3-5
Installation Review : A Checklist ......................................................................................................................................3-6
Chapter 4 How Your Vogt Ice Machine Works.....................................................................................................................4-1
Component Listing...........................................................................................................................................................4-1
Arrangement of Components ..........................................................................................................................................4-1
Principle of Operation......................................................................................................................................................4-2
Chapter 5 Start-Up and Operation.......................................................................................................................................5-1
Start-Up Procedure..........................................................................................................................................................5-1
Shut-Down Procedure......................................................................................................................................................5-1
Ice Supply System Considerations ...................................................................................................................................5-1
Operating Tips..................................................................................................................................................................5-2
Chapter 6 Electrical Controls and Functions........................................................................................................................6-1

ii
System Controllers...........................................................................................................................................................6-1
Solenoid Valves ............................................................................................................................................................6-1
Limit Switches ..............................................................................................................................................................6-1
Photovoltaic Sensor .....................................................................................................................................................6-1
Hydraulic Pressure Switch............................................................................................................................................6-2
Time Delay Relays ........................................................................................................................................................6-2
Chapter 7 Maintenance .......................................................................................................................................................7-1
Cleaning Procedure..........................................................................................................................................................7-1
Hydraulic System..............................................................................................................................................................7-1
Limit Switches ..................................................................................................................................................................7-1
Lubrication .......................................................................................................................................................................7-1
Preventive Maintenance..................................................................................................................................................7-1
Daily..............................................................................................................................................................................7-1
Weekly (In addition to Daily checks)............................................................................................................................7-2
Monthly (In addition to Weekly checks)......................................................................................................................7-2
Yearly (In addition to Weekly and Monthly checks)....................................................................................................7-2
For the Manager ..............................................................................................................................................................7-2
Items to Check..............................................................................................................................................................7-2
Why You Should Do This..............................................................................................................................................7-2
Preventive Maintenance Form ........................................................................................................................................7-3
Chapter 8 Troubleshooting..................................................................................................................................................8-1
List of Symptoms..............................................................................................................................................................8-1
Chapter 9 Service Operations ..............................................................................................................................................9-1
Limit Switches ..................................................................................................................................................................9-1
Hydraulic System..............................................................................................................................................................9-1
Hydraulic Leaks ................................................................................................................................................................9-1
Directional Valves ............................................................................................................................................................9-1
Chapter 10 Tables and Charts............................................................................................................................................10-1

1-1
Chapter 1 Introduction
A Brief History of Our Company
The Henry Vogt Machine Co. was founded as a small machine shop in Louisville, Kentucky in 1880. In 1938, Vogt built the
first Tube-Ice® machine and revolutionized the ice-making industry. Our first “sized-ice” machine quickly replaced the
old can-ice plants, which required much hard labor and large amounts of floor space for freezing, cutting, and crushing
ice by hand.
The Henry Vogt Machine Co. eventually sold its Tube-Ice® division to Vogt Ice, LLC. Since that time, Vogt Ice, LLC
acquired Turbo Refrigeration® in 1989, a company which has become a market leader of plate ice equipment.
With the strong history of these two brands, Vogt Ice, LLC carries on the tradition as one of the world’s leading
producers of ice-making equipment.
Vogt Energy-Savings Tube-Ice® Machines
Today, Vogt Tube-Ice® machines enjoy a well-earned reputation as the most energy efficient, dependable ice-making
equipment in the world.
Using as little as one-half to one-third the energy required by competitors’ icemakers, Tube-Ice® machines produce the
same amount of ice –in restaurants, sports arenas, packing plants, and wholesale operations around the globe –at
great savings.
In addition, Tube-Ice® machines are renowned for their long life, giving many customers more than 35 years of
dependable service. Ask someone who owns one.
Preview
All the skill in engineering and fabrication that we have learned in over a century of experience is reflected in the BP360.
This heavy duty machine is specifically designed to use hydraulic pressure to fuse ice fragments into a solid ice block.
This manual is designed to assist you in the installation, start-up, and maintenance of your unit. Your Vogt Ice machine
will give you a lifetime of service when you install it, maintain it, and service it properly.
Please read your manual carefully before attempting installation, operation, or servicing of this professionally designed
piece of equipment.
If you have additional questions, please call your distributor. Also, feel free to phone the factory direct at
1-502-635-3000 or 1-800-853-8648.
Important Safety Notice
This information is intended for use by individuals possessing adequate backgrounds of electrical, hydraulic and
mechanical experience. Any attempt to repair major equipment may result in personal injury and property damage.
The manufacturer or seller cannot be responsible for the interpretation of this information, nor can it assume any
liability in connection with its use.

1-2
This is an automatic machine. Motors and hydraulic rams may start without warning. Check that all electrical service is
disconnected and locked out before attempting to work on the unit.
Never open control panels without first observing “lock out and tag out” procedures on the electrical service.
This machine operates under high oil pressure. When servicing hydraulic lines, relieve the system pressure before
opening any lines. Always keep the area around the machine clean of hydraulic fluids.
Never operate the machine without the safety guards that have been provided. Covers and hoppers to shield operators
from the hydraulic cylinders and ice cut-off slide have been provided from the manufacturer.
Never attempt to adjust the ice cut-off slide while the machine is in operation.
Any conveyors associated with the operation of the machine must be sufficiently guarded to prevent injury.
Safety Symbols and What They Mean
Prior to installation or operation of the BP360 machine, please read this manual and be familiar with its contents.
Before you operate, adjust or service this machine, you should read this manual, understand the operation of this
machine, and be aware of possible dangers.
These Safety Symbols will alert you when special care is needed. Please heed.
! DANGER !
Indicates an immediate hazard and that special precautions
are necessary to avoid severe personal injury or death
! DANGER !
! WARNING !
Indicates a strong possibility of a hazard and that an
unsafe practice could result in severe personal injury
! WARNING !
! CAUTION !
Indicates that hazards or unsafe practices could result
in personal injury or product or property damage
! CAUTION !

1-3
Assembly Drawing Model BP360
Figure 1 –BP360 General Arrangement

2-1
Chapter 2 Receipt of Your Vogt Ice Machine
! WARNING !
Only service personnel experienced in hydraulic system operation
and qualified to work with high voltage electrical equipment
should be allowed to install or to work on this machine
! WARNING !
Inspection
As soon as you receive your machine, inspect it for any damage. If damage is suspected, note it on the shipper’s papers
(i.e., the trucker’s Bill of Lading). Immediately make a separate written request for inspection by the freight line’s agent.
Any repair work or alteration to the machine without the permission of Vogt Ice, LLC can void the machine’s warranty.
The machine was shipped with a full tank of ISO 32 hydraulic fluid. Visually check all lines for mechanical damage. If a
leak is suspected, contact the Vogt Ice, LLC service department to obtain authorization for repair.
The machine also contains a series of limit switches, shown in the P&ID in Section 4. Visually check that the switches are
intact and were not damaged during shipping. If damage is suspected, contact the Vogt Ice, LLC service department to
obtain authorization for repair.
! CAUTION !
The approximate weight of the machine is 2400 lbs.
Use only the appropriate equipment with adequate
loading capacity to move and install the machine.
! CAUTION !
Safety Valves
This machine has been provided with pressure safety valves that are installed in the hydraulic system to prevent over-
pressurization. In the event that these valves open, the excess fluid pressure will be vented into the hydraulic reservoir,
which is constantly at atmospheric pressure. These safety valves have been preset by the factory. Do not adjust them.
Machine Room
The machine must be located inside of a suitable building, fully protected from outside elements. It was designed to be
operated between 38°F and 100°F. Heat from other sources (sunlight, furnaces, condensers, etc.) and unusual air
currents may affect the operation or life cycle of the machine and should be avoided. It is not capable of operating in
cold rooms, freezers, or other locations where the ambient temperature can drop below 38°F. Ambient temperatures in
excess of 100°F can be detrimental to the hydraulic system, as it may be unable to cool the oil sufficiently.
Electrical components are rated NEMA 1, and should not be located in a hazardous area or sprayed with water. The
machine should be installed on a drainable drip pan or in an area where water will not stand, but readily drain away
from the machine. See Space Diagrams, Figure 3thru Figure 5, for clearances and utility connections. Ambient
temperatures in excess of 100°F can be detrimental to the electrical devices and control equipment.

2-2
Storage (Prior to Installation and Start-Up)
The machine must not be stored in an area that may reach temperatures in excess of 100°F in order to prevent damage
to the electrical controls.
Vogt Model Nomenclature
The machine nameplate is located on the front of the control panel. The model number and machine description are
located in the top left hand corner. The following figure can be used to verify that the correct model number has been
received:
Figure 2 –Block Press Model Number Structure

3-1
Chapter 3 Installing Your Vogt Ice Machine
! WARNING !
Only service personnel experienced in hydraulic system operation
and qualified to work with high voltage electrical equipment
should be allowed to install or to work on this machine
! WARNING !
Important Notice:
The Warranty Registration / Start-Up Form must be completed and returned to Vogt Ice, LLC to initiate and to ensure
a full warranty. A postage paid envelope is provided or you may fax the report to 1-800-770-8648.
An appropriate location for installation must be selected considering the following factors:
1. The maximum material flow through the BP360 in an eight (8) hour period is 28,800 lbs.
2. The operating oil temperature must be stabilized between 100°F and 110°F in order to maintain ideal conditions
for the hydraulic system components in order to minimize wear.
3. Floor drains should be provided at the machine installation location. Water may be released from the machine
when ice blocks are formed.
4. The machine is not capable of operating in locations where the ambient temperature can drop below 38°F.
Temperatures below this point can cause the ice to freeze up the machine, preventing operation, and possibly
leading to equipment damage.
Water Supply and Drain Connections
This ice block press has two (2) water supply connections: one (1) for the oil cooler, and one (1) for the water injection
system.
An oil cooler is installed on the machine for the purposes of preventing the hydraulic oil system from overheating. Use of
this oil cooler may not be required in every instance of installation, depending on the usage rate of the machine and the
environmental factors of the equipment location. Maximum flow is 10 GPM at 85°F. The oil temperature range is 60°F
minimum and 120°F maximum. The ideal operational temperature is between 100°F and 110°F.
A water injection system is included to allow water into the compacting chamber to allow the ice block to fuse
completely. The amount of water to be injected depends on the nature of the ice being fed into the machine. Ice with a
wet surface or “snow” will require little to no additional water to fuse completely. Ice with a dry surface, particularly if
the pieces are large, will require more water to form a solid ice block.
This water injection system activates automatically during the machine cycle, but requires proper set-up by the
operator. Two (2) provisions are included in the machine to control the amount of water that is injected each cycle. The
first is a flow control valve that is manually adjusted to set the flow rate of the water into the machine. The second is a
time delay relay (TDR-2), which determines the length of time of the injection from 0.1 to 10 seconds. Trial and error is
necessary to properly set these variables.

3-2
Ice Supply
The BP360 is designed to feed ice automatically into the compacting chamber. The machine control panel is supplied
with terminals to connect the ice block press to the ice supply system. These terminals allow the BP360 to start and stop
the ice supply system based on the operational state of the machine.
! CAUTION !
Failure to connect the ice supply system to the ice block press
control panel terminals could result in machine malfunction
! CAUTION !
A specially designed ice hopper is included on the BP360 to allow the machine to receive the correct amount of ice
fragments to compact the block and to release freely on each cycle. For the automatic feed feature to function reliably,
all of the ice supplied for the next block cycle must be in the hopper. No ice should be in any transition between the ice
supply system and the ice hopper. Any ice in one of these transitions will cause the BP360 to jam.
! DANGER !
This machine contains moving hydraulic cylinders
Ensure that operator access to the ice hopper is not possible during operation
Serious injury can result
To ensure operator safety, install fully enclosed transition pieces between
the ice supply system and the ice hopper on the BP360
! DANGER !
Ice Cut-Off Slide
The ice cut-off slide sets the volumetric measurement of ice fragments that will form the solid block inside of the
machine. Four height settings are provided as slots in the side of the ice hopper. Check that the cut off slide is properly
aligned to one of these slots before starting operation.
Installed on the machine from the factory is a clear plastic guard that surrounds the ice cut-off slide. This guard must
remain in place at all times during operation to avoid serious physical injury. Access to the rear of the slide is made
available for the purpose of setting the desired slide height; however, the slide height should NEVER be adjusted while
the machine is running.
Light Intensity
Cycle control of the BP360 is achieved through a set of mechanical limit switches and a photovoltaic sensor. Operation
of the photovoltaic can be affected by the intensity of light in the location of installation. Consider installing light shades
over the ice hopper if the photovoltaic is not properly responding.

3-3
Space Diagram
Figure 3 –Service Access Requirements
Figure 4 –Overall Dimensions

3-4
Figure 5 –Utility Connections
Wiring Diagram and Electrical Connections
! WARNING !
Only service personnel experienced in hydraulic system operation
and qualified to work with high voltage electrical equipment
should be allowed to install or to work on this machine
! WARNING !
Refer to the table below to properly size wiring connections. The wiring diagram has been attached at the end of this
manual for reference. A fused disconnected must be provided near the machine. Connect three (3) phase power to the
main contactor for operation of the BP360 motor. The control circuit requires an independent 115V/1/60Hz source. A
rotation check of the hydraulic pump motor is required (See Error! Reference source not found.).
Standard Voltages
F.L.A.
Min. Ampacity (A)
Max. Fuse (A)
Min. Wire Size (AWG,
THHN or equal)
208 / 230 V, 3 ph,
60 Hz
54.0
67.6
120
#6
460 V, 3 ph, 60 Hz
27.0
33.8
60
#10
115V, 1 ph, 60 Hz
Control Circuit
10.0
15
10
#14
Phase Check, Voltage Imbalance and Current Imbalance
! CAUTION !
DO NOT attempt to start the machine without
ensuring proper rotation of the hydraulic motor
! CAUTION !
Phase and Rotation Check
The hydraulic pump motor rotation is set at the factory, but must be checked at installation. Motor rotation must match
the directional arrow on the housing of the pump. Prior to starting the motor, the pump head must be primed according
to the notice in Chapter 5 Start-Up and Operation.

3-5
Voltage Imbalance
Voltage imbalances can cause motors to overheat and fail. The maximum voltage imbalance between any two legs
should be no greater than 2%.
Example:
Supply Voltage = 230-3-60
Voltage Readings: AB = 220 Volts
BC = 225 Volts Average = (220 + 225 + 227)/3 = 224 Volts
AC = 227 Volts
(AB) 224-220 = 4 Volts (Highest Deviation)
(BC) 225-224 = 1 Volts % Voltage Unbalance = 100 x (4/224) = 1.78% “Acceptable”
(AC) 227-224 = 3 Volts
! CAUTION !
Contact your local electric utility company
if the supply voltage imbalance exceeds 2%
! CAUTION !
Current Imbalance
A voltage imbalance will cause a current imbalance, but the opposite does not necessarily exist. A loose terminal
connection, buildup of dirt, or carbon on one set of contacts can cause a higher resistance on one leg than on the other
two legs. Current follows the path of least resistance. If terminal connection L1 is loose or dirty, then L2 and / or L3 will
have a higher current. Higher current causes more heat to be generated in the motor windings.
The maximum acceptable current imbalance is 10%.
Example:
Current Readings: L1 = 96 Amps
L2 = 91 Amps Average = (96 + 91 + 98)/3 = 95Amps
L3 = 98 Amps
(L1) 96-95 = 1 Amps
(L2) 95-91 = 4 Amps (Highest Deviation) % Current Unbalance = 100 x (4/95) = 4.2% “Acceptable”
(L3) 98-95 = 3 Amps

3-6
Installation Review : A Checklist
Machine securely mounted to floor
Motor power supply connected
Control panel power supply connected
Hydraulic oil cooler water supply and return plumbed
Water injection valve supply water plumbed
Ice supply system properly installed to machine
Contacts from photovoltaic wired to ice supply system
All tools clear of machine and compacting chamber

4-1
Chapter 4 How Your Vogt Ice Machine Works
Component Listing
The list below contains the major components that are used on the BP360.
•Hydraulic Pump
•Hydraulic Pump Motor
•Hydraulic Reservoir Tank
•Main Hydraulic Cylinder
•Opposing Hydraulic Cylinder
•Main Cylinder Directional Solenoid Valve
•Opposing Hydraulic Cylinder Directional Solenoid Valve
•Hydraulic Line Pressure Switch
•Hydraulic Line Pressure Relief Valve
•Hydraulic Line Return Filter
•Hydraulic Line Suction Screen
•Four (4) Limit Switches
•Photovoltaic Sensor
•Ice Cut-Off Slide
•Plastic Ice Hopper
•Compacting Chamber
•Water Injection Solenoid Water Flow Valve
•Water-Cooled Oil Cooler
Arrangement of Components
The main cylinder (long stroke cylinder) has a rectangular stainless steel pressure pad mounted on the end of the piston
rod. When the main cylinder is fully retracted, the pressure pad is just within the feed end of the stainless steel
compacting chamber. As the main cylinder extends, the pressure pad moves the entire length of the compacting
chamber. At full extension, the pressure pad protrudes slightly beyond the discharge end of the compacting chamber.
Attached to the top edge of the pressure pad is a flat stainless steel pressure pad follower.
The opposing cylinder (short stroke cylinder) is mounted horizontally at the discharge end of the compacting chamber. A
rectangular stainless steel resistance pad is mounted on the end of the piston rod. When the opposing cylinder is fully
extended, the resistance pad will nearly touch the discharge end of the compacting chamber. This effectively closes off
the discharge end of the compacting chamber. Attached to the resistance pad (located above and forward of it), is the
flat stainless steel ice cut-off slide. As the opposing cylinder extends, the ice cut-off slide moves to close off the ice
hopper.

4-2
Principle of Operation
! DANGER !
This machine contains moving hydraulic cylinders
Ensure that operator access to the ice hopper is not possible during operation
Serious injury can result
! DANGER !
The BP360 is designed to produce solid ice blocks continuously at the rate of 360 blocks per hour, provided that a
sufficient supply of ice fragments are available. The machine assembly includes a hydraulic pump that operates two (2)
horizontally mounted hydraulic cylinders. The actions of these cylinders are directionally opposed.
When the machine power switch is turned on, the hydraulic pump starts and begins to build hydraulic pressure in the
system until it reaches operational condition. The photovoltaic sensor will detect the amount of light present in the ice
hopper and send a start or stop signal through the control panel terminal set to the ice supply system, depending on
whether or not ice is present in the hopper. Once the photovoltaic registers that ice is in the hopper, the ice supply
system to the machine will stop, the main cylinder will retract, and the opposing cylinder will extend. All of these actions
occur simultaneously.
As the opposing cylinder extends, the ice cut-off slide cuts through the top of the ice in the ice hopper. This allows for
consistency in the size of block produced. When the opposing cylinder is at full extension, the ice cut-off slide will fully
close off the ice hopper. The cylinder remains in the extended position to close off one end of the compacting chamber.
The ice cut-off slide is directly connected to the opposing cylinder.
When the main cylinder is fully retracted, the ice contained in the hopper beneath the ice cut-off slide drops into the
compacting chamber. The main cylinder trips a limit switch (LS-4) at full retraction that sends a signal to the control
panel to reverse the direction of the cylinder. This allows the cylinder to extend. LS-4 also energizes the time delay relay
(TDR-2) that activates the water injection solenoid valve. The water injection solenoid valve will remain open for the
length of time determined by the knob position on the relay inside of the control panel.
The extending main cylinder pushes the ice from underneath the hopper towards the now stationary opposing cylinder.
The ice block begins to form as the ice fragments are trapped between the pads on the cylinders. Hydraulic line
pressures will rise as the forming ice block creates resistance for cylinders until the pressure switch set point is reached.
The set point on the switch is factory set at 2000 PSI. By loosening the set screw and using a hex key, the switch can be
adjusted. The switch should always be set between 1500 PSI and 2000 PSI. Activation of the pressure switch energizes
the compact hold delay, TDR-1. After the timer stops, the opposing cylinder will retract.
By the retraction of the opposing cylinder, the end of the compacting chamber is exposed to allow the main cylinder to
push the ice block out of the machine. Additionally, it will cause the ice cut-off slide to open up the ice hopper and allow
the next batch of ice fragments to fall into the hopper to form the next ice block. As the ice drops into the ice hopper,
the photovoltaic sensor will detect the need for more ice to be sent to the machine. It will then turn on the ice supply
system to provide additional ice to the machine.
The main cylinder will continue to extend, pushing the newly formed ice block out of the machine, and down onto the
exit slide provided. When the main cylinder reaches full extension, it contacts limit switch (LS-2) to signal the start of the
next forming cycle. As the ice block exits the machine, it contacts limit switch (LS-5) to signal the control system that the
block is free from the machine. When the photovoltaic sends a “stop ice feed” signal, and when LS-1, LS-2, and LS-5 are
activated, the next forming cycle will start.

4-3
The BP360 is designed to return to a de-energized state in the event of a power failure, or when the machine is shut
down. In this condition, the main cylinder is fully extended, and the opposing cylinder is fully retracted. This de-
energized state is also maintained if the ice feed supply has been exhausted during operation. This guarantees that all
ice supply systems and the compacting chamber are empty of ice at the end of an operating period. Attached to the end
of this manual is the P&ID for the machine. This diagram provides a visual layout of the system.
Table of contents
Popular Power Tools manuals by other brands
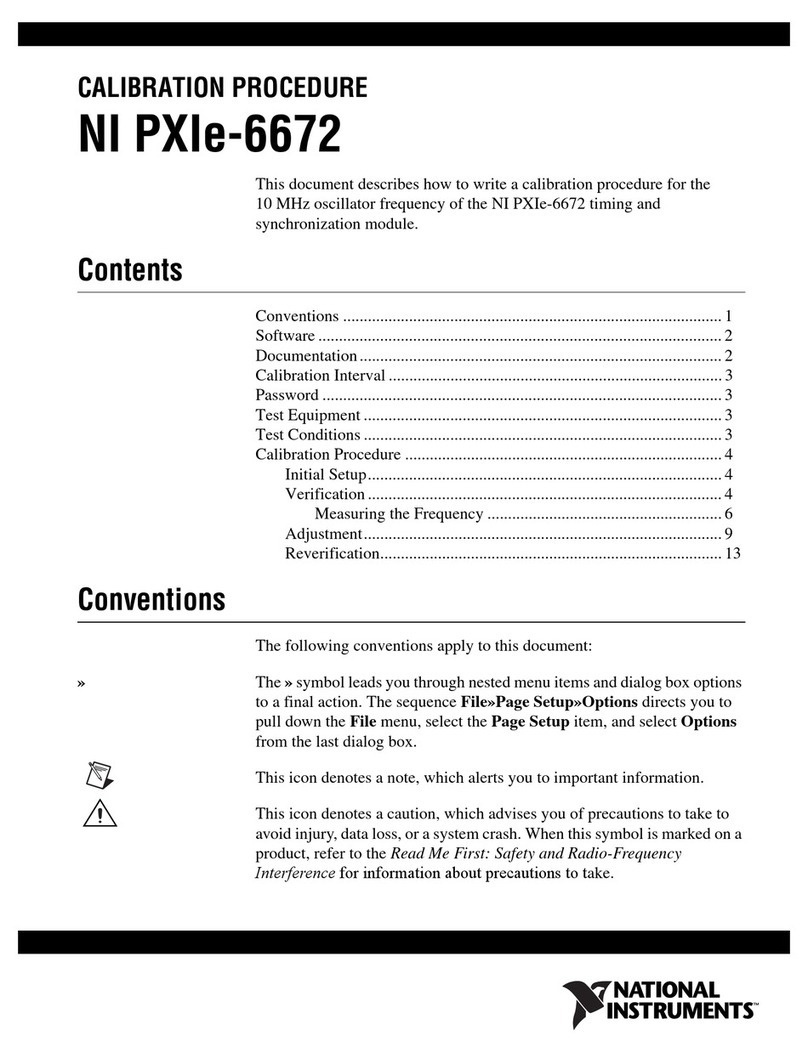
National Instruments
National Instruments Network Adapter NI PXIe-6672 CALIBRATION PROCEDURE
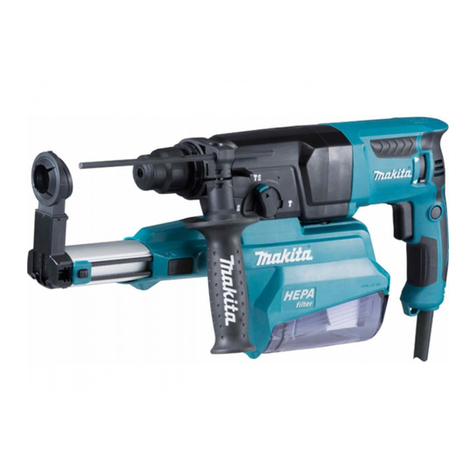
Makita
Makita HR2650 instruction manual
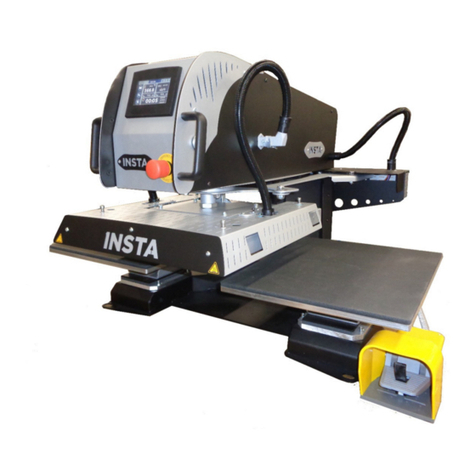
Insta
Insta 780 Operation and maintenance manual

Makita
Makita 5093DZ instruction manual

Milwaukee
Milwaukee 2860-20 Operator's manual
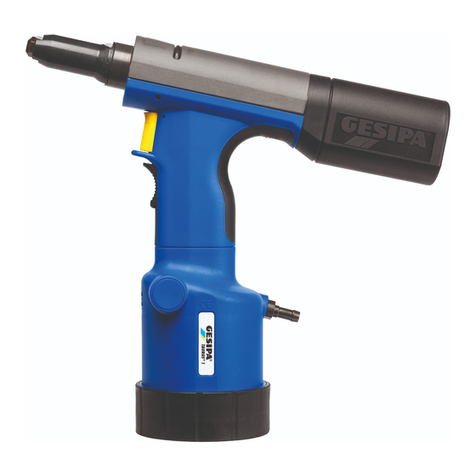
Gesipa
Gesipa Taurus 1-4 Operating manual with spare parts list