WÜRGES HV 6 W User manual

E
10/99 1/4
vibrationmotors
HV 6 W
Instructions of operation
and
List of spares
Important remark concerning the personal safety of operators
These instructions must be understood by each operator,
who is in charge of the assembly, putting into operation,
maintenance and repair work of vibration motors. The same
applies to supplementary instructions for modified
equipment.
Our vibration motors have been manufactured in
accordance with the latest art. In case of use as provided,
they are sure to operate.
Unauthorized changes with the motors and specific
execution for the client are excluded from the manufactures
guarantee for resulting damage.
It is an implied feature of vibration motors that they
generate destructive forces. In case of improper use, these
destructivforces are apt to cause danger, e.g. the motor or
components thereof can drop uncontrolled after getting
loose from the fastening means. As a precaution, safety
measures must be adopted.
When performing maintenance or repair work, the vibration
motor must be disconnected from the power system.
Putting vibration motors into operation without protective
cover is forbidden, because risk of accident may result.
Instructions for mounting vibration motors
General
Vibration motors must be mounted only on equipment with
plane surfaces, which are resistant to bending. These
surfaces must not be subject to tensions.
Only screws of grade 8.8 and nuts of grade 6 must be used.
The screws must be secured from slackening, e. g. by spring
washers or the like.
Posterior tightening of screws and nuts
After the first two hours of operation the screws or nuts
must be checked for tight seating. Subsequent inspections
shall be performed once daily. In case of necessity the
screws or nuts must be retightened.
The minimum torques are for: M10 = 55 Nm
M12 = 90 Nm
If the screws have slackened, danger of
breakage of the feet of the vibrator is
impending.
screwplate vibratorfoot
correct correct wrong
Anweisung zum elektrischen Anschluß
Dangerous Voltage!
Non-compliance can cause death, serious
bodily injury or property damage.
General
The power connection must be established only by an
electrician. The voltage and frequency must be that, which
is indicated on the machine plate (230 V , 50/60 Hz). The
vibration motor must be connected only to power supply
which is in agreement with the VDE regulations.
! !
!

10/99 2/4
To secure the motor from overload, it must be connected in
series with a terminal circuit breaker (1A).
Power connection
The power connection must be established only by a
flexible cable. We recommend to use the following cable
type: ÖLFLEX 540 P 2,5². Plastic cables are not suitable.
The connection cable must be laid in a manner which
excludes inherent vibrations and any load by traction.
Kunststoffkabel sind ungeeignet.
1. Kabelmantel ca. 8 cm entfernen
2. Den Schutzleiter 1-2 cm Länger belassen als die Adern
der Phasen.
3. Provide the ends of the strands with terminals or
compression cable sockets. Never fasten the terminals
or sockets by soldering, as in default of this the strands
tend to break behind the soldered spots in case of
vibration.
4. Introduce the cable into the the terminal box and
establish the connection as shown in the diagram.
5. When tightening the cap screw of the screw joint, it
must be observed that the cable jacket is still fully
seized by the seal. If this is not observed, the cable is
not firmly clamped, not relieved from traction, and not
waterproof.
6. Close again carefully the terminal box with seal and
screws..
7. The power cable must be fastened firmely shortly
behind the cable gland. This first fastening of the cable
and the motor should by no means be movable against
each other. The cable has to be installed in such a way
that it does not start vibrating itself and that it is not
subject to any tractional forces.
8. When putting the vibration motor into operation the
power input must be examined. Should this be larger
than the data on the mashine plate, the trouble can be
remedied by reducing the centrifugal force.
9. Now and again it must be checked that there are no
spots which are subject to friction.
Admitted operating temperature
Outside on the housing not higher than 80°C.
This limit may be surpassed by too high a power input, if
the speed which is indicated on the mashine plate is not
reached, with the result that the winding may burn out. The
reason may be too high a centrifugal force for the case
which is existing or a construction of insufficient resistance
to bending. The trouble can be set by reducing the
centrifugal force.
Setting the centrifugal force
Provide that no different centrifugal force had been
indicated in the order sheet, the motor has been set for the
full centrifugal force. In order to be able to change the
centrifugal force both protective covers must be taken off.
Once the protective covers are taken off, the centrifugal
force may be changed as desired. But it must be observed
that the adjustment is the same on both sides.
This is achieved by removing the screws or nuts from the
armature on both sides and by transposing the flywheels by
180°. With this the centrifugal force is reduced by twice the
value of the transposed flywheels. But in the case, the
removed flywheels must be replaced by spacers. (Please
compare the corresponding list of spares).
One flywheel on each side generates a centrifugal forces of
65 daN at 5000 min-1.
Nach dem Verstellen müssen gelöste
Schrauben wieder befestigt werden und die
Schutzhauben unbedingt wieder montiert
werden. Ansonsten besteht Unfallgefahr.
!

10/99 3/4
Maintenance
Motors surfaces must be kept free from accumulations of
dirt in order to make sure sufficient cooling. Now and
again, the connection cable must be checked for abrasions.
After the first two hours of operation the lock screws must
be retightened. Subsequent inspections for tight seating of
the screws shall be performed once a day. The bearings of
our motors need no maintenance in normal cases. These
bearings have a grease filling for life.
In case of wear of the bearing, the motors shall be taken
out of service and the special bearings shall be replaced.
We recommed to send these motors to the manufacturers in
order to have these repaired. Only when doing so you may
be sure to get motors repaired properly.
If you proceed to disassemble the motors yourselves or to
replace bearings, the workplace must be kept clean. No dirt
particles must be allowed to get into the interior of the
motors. Never use cleaning wool, but non-fluffy cleaning
cloths for cleaning motor components.
Never make the motors run without
flywheels, because in such cases the bearings
could be destroyed!
Maintenance of the carbon brushes
After every 250 hours of operation the carbon brushes
should be checked for wear. Remove the protective cover.
Push back the clamping rocker of the carbon brush holder
and carefully take out the brushes out of the holder with a
pair of pliers. Carbon brushes of less than 8 mm length
should be replaced. The wires of the brushes are fitted with
cable terminals and connected to the carbon brush holder.
Make sure that the brush cables cannot get into contact with
the bearing cover during operation. Deposited carbon dust
can be removed with compressed air of not more than 15
psi.
Spares
When placing orders for spares, please refer to the list of
spares.
Further informations is given in the drawings of spares.
WÜRGES take over guarantee only for the use of their
original spares.
We point out to the fact that spares, which are not delivered
by WÜRGES have not been tested by WÜRGES. Using
spares from other manufacturers can impare predetermined
qualities which are inherent in the construction and thereby
influence negatively the active or passive safety. WÜRGES
reject any claim whatsoever, resulting from the use of
spares from other manufacturers.
Please keep in mind that many cases, own specifications
exist for components of WÜRGES and other manufacturers
and that WÜRGES deliver always spares according to the
latest art.
!

05/03 4/4
When placing orders for spares, never forget to mention the required number of pieces, the type or number; for
illustration no. 12 also the voltage and periodicity.
Fig. No. Order No. Pieces Fig. No. Order No. Pieces Fig. No. Order No. Pieces
146001 1 8 21301 417 50711 1
260101 1 9 21801 818 50801 1
300401 110 22551 219 75311 8
401401 111 24101 220 75801 1
501731 212 27001 10 21 75931 2
602511 213 29491 1
721101 416 50301 2
WÜRGES ⋅Vibrationstechnik GmbH
Daimlerstraße 9
D-86356 Neusäß/Augsburg
telephone: 0049/(0)821/463081
telefax: 0049/(0)821/463084
e-Mail: [email protected]
Internet: http://www.wuerges.de
Other WÜRGES Engine manuals
Popular Engine manuals by other brands
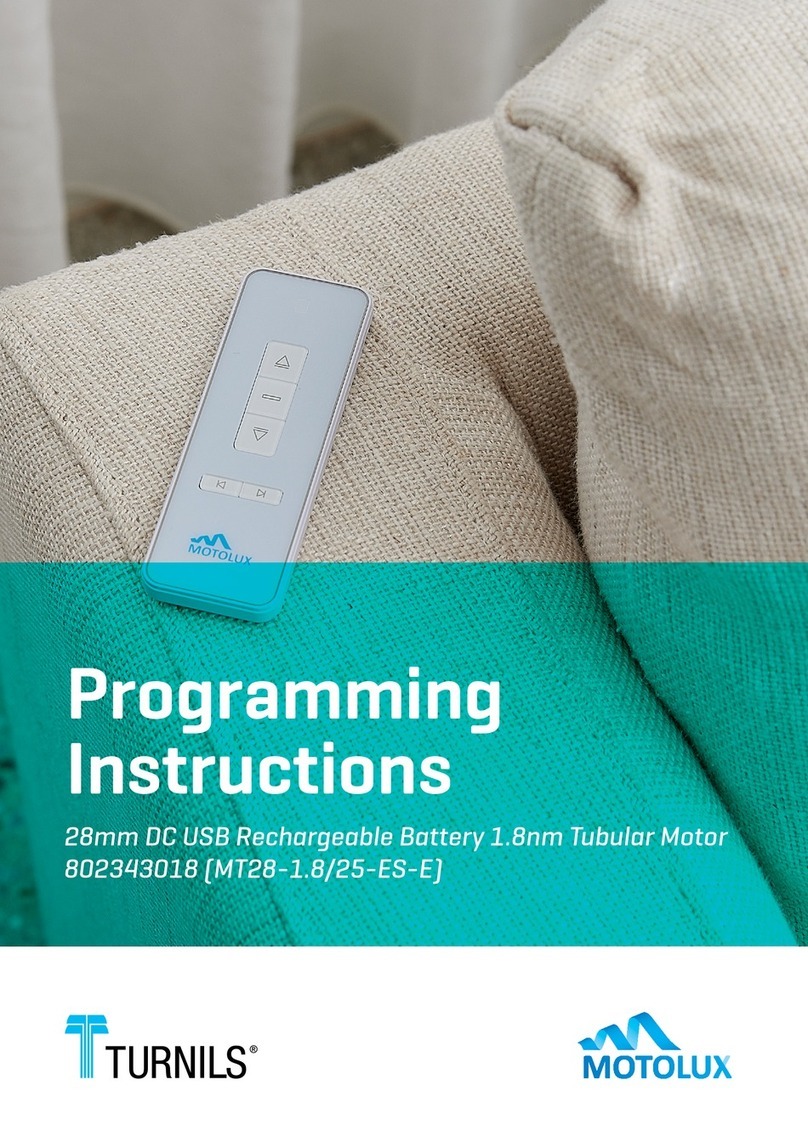
HunterDouglas
HunterDouglas MOTOLUX TURNILS 802343018 Programming instructions

US MOTORS
US MOTORS Titan Horizontal Installation, operation and maintenance manual

woodmizer
woodmizer G13 Safety, Operation, Maintenance & Parts Manual
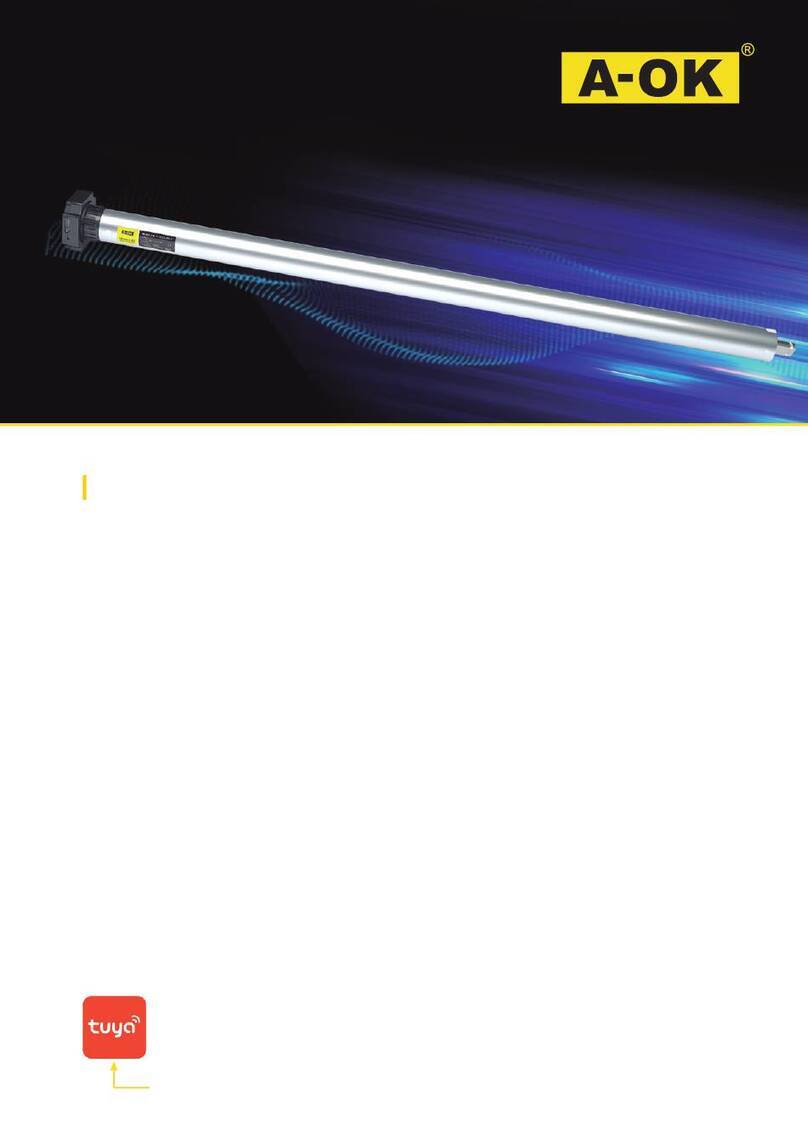
AOK
AOK AM15 PLUS L manual

Oriental motor
Oriental motor BLV Series operating manual
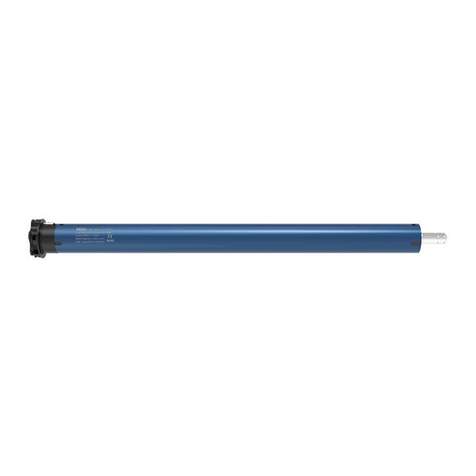
AOK
AOK BASIC AM45 quick start guide
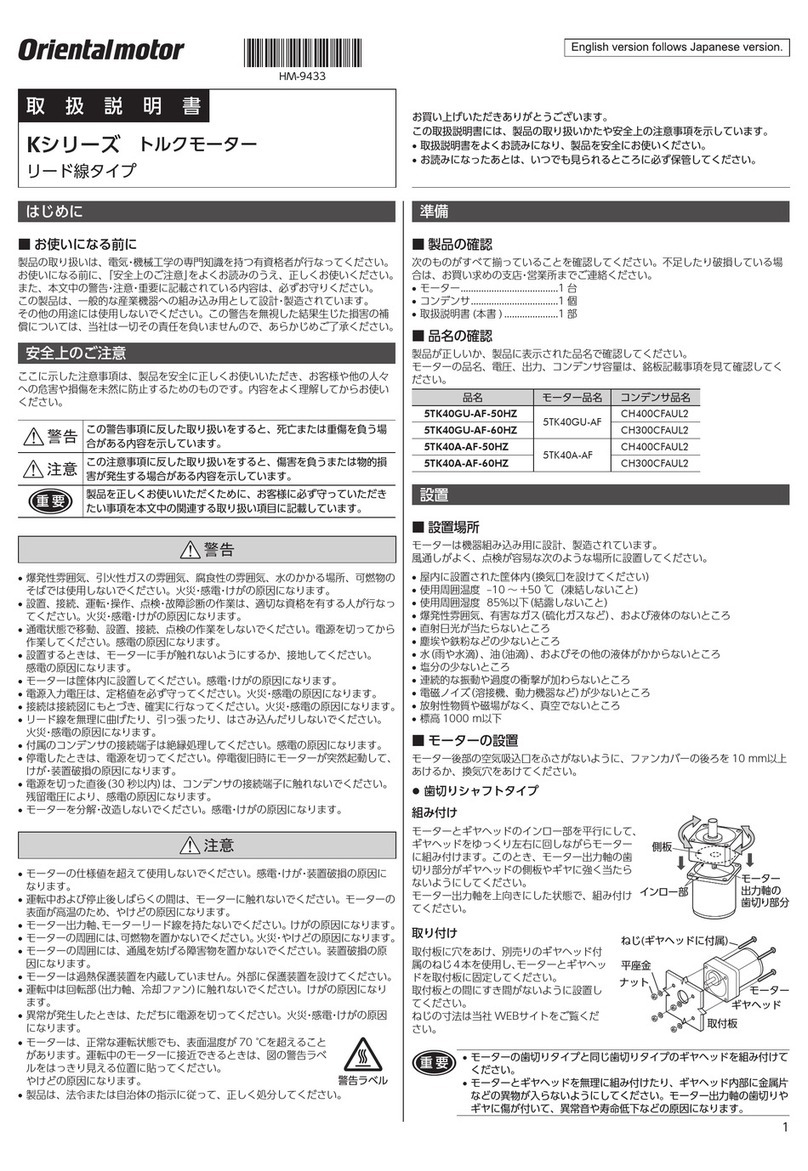
Oriental motor
Oriental motor K Series operating manual
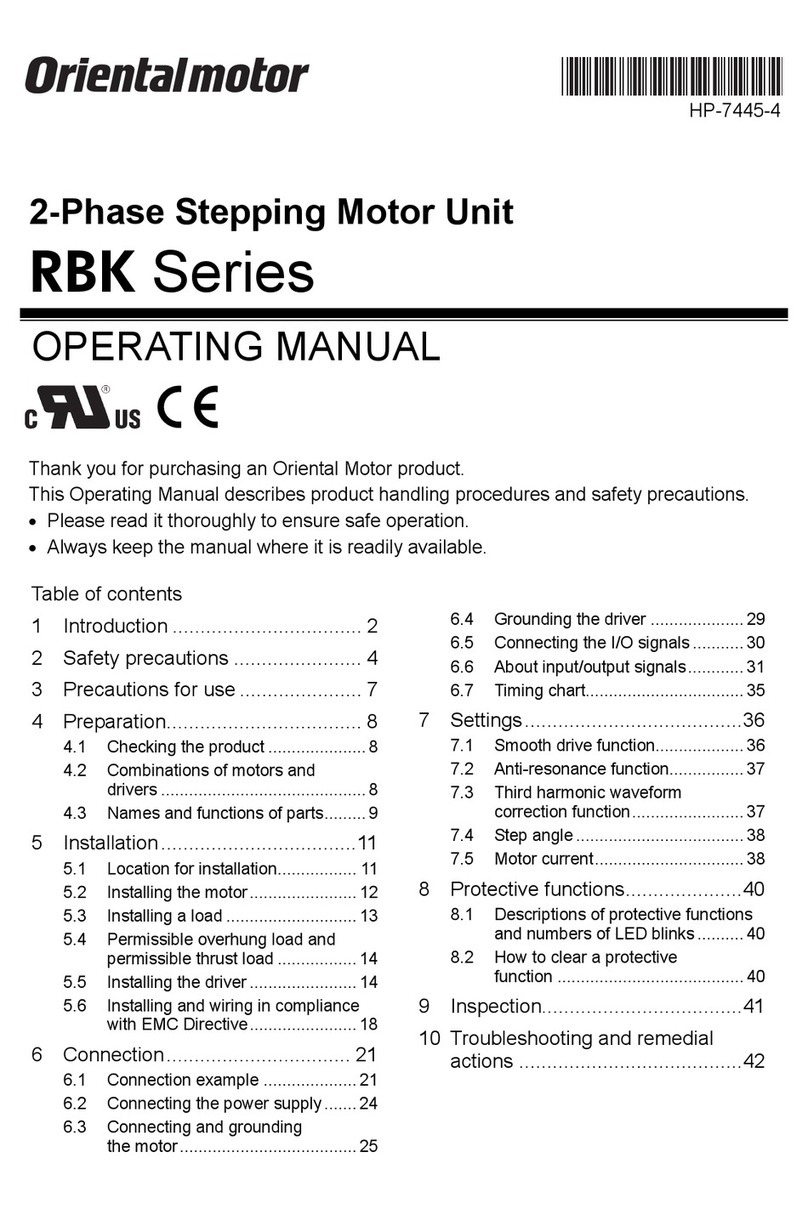
Oriental motor
Oriental motor RBK Series operating manual
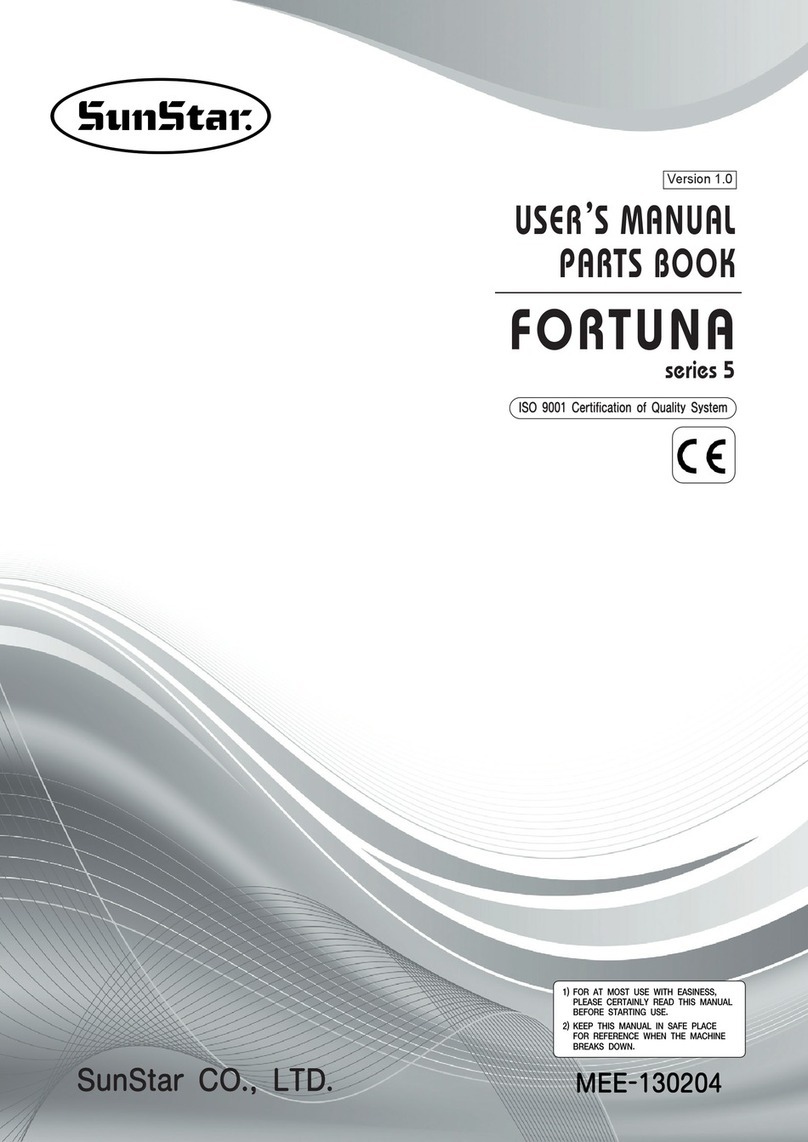
SunStar
SunStar Fortuna 5 Series user manual
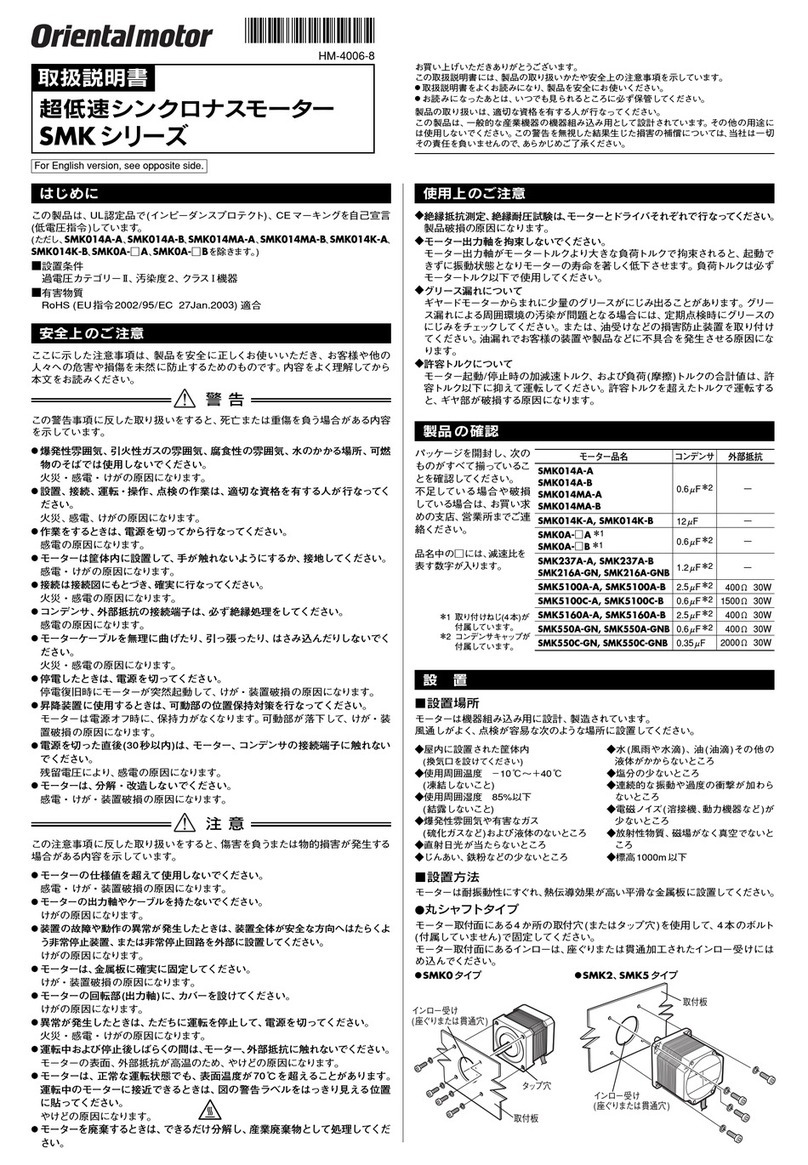
Oriental motor
Oriental motor SMK Series operating manual
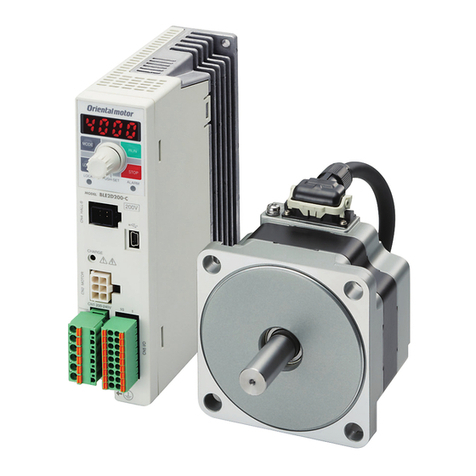
Oriental motor
Oriental motor BLE Series operating manual
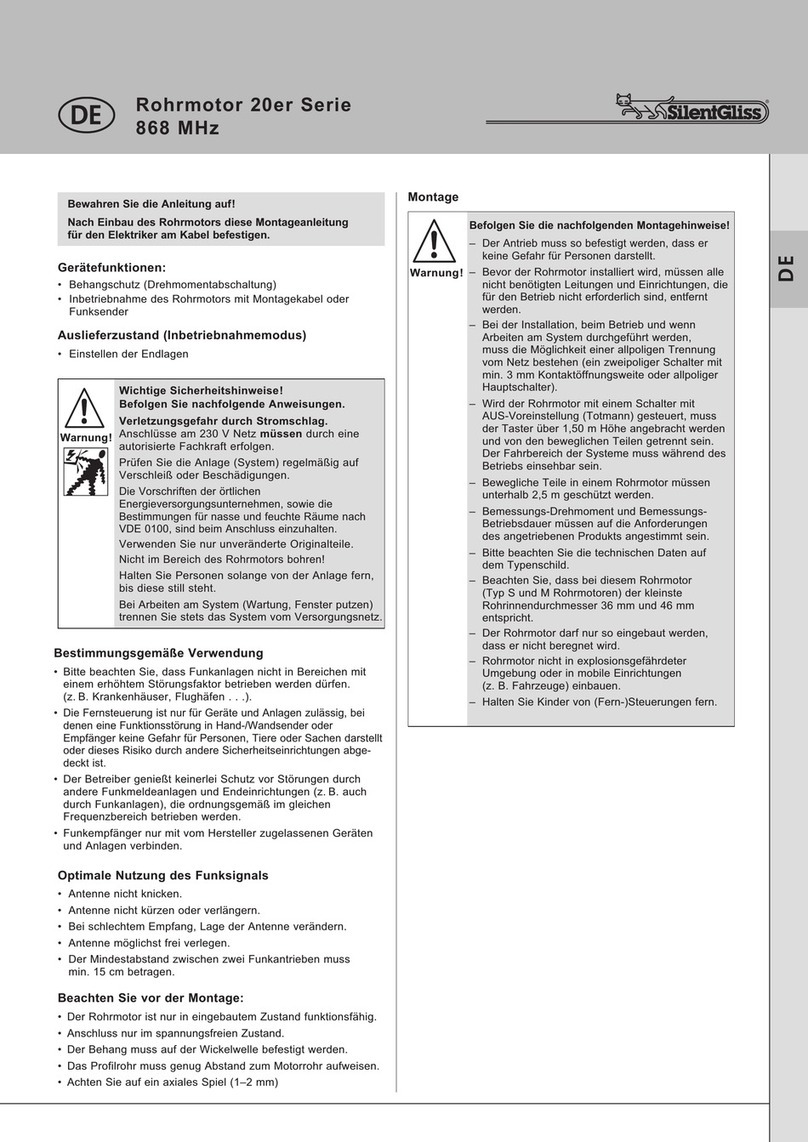
Silent Gliss
Silent Gliss 20 Series instructions