WÜRGES HVE/VFLE Series User manual

II 2G Ex e II T3
II 2D Ex tD A21 IP65 T120°C
Würges Vibrationsmotoren GmbH
Boschstraße 9
D-86356 Neusäß
Telephone +49 821 999824-00
Telefax +49 821 999824-10
E-Mail [email protected]
Web www.wuerges.de
Translation of the Original Instruction Manual
Installation and Operating Instructions
Electric Vibrators HVE/VFLE Series

2
1. General Information Page 3
2. Symbols Used Page 4
3. Safety Page 5
3.1. Intended use
3.2. Skilled personnel qualifications
3.3. General safety instructions
4. Technical Data Page 7
4.1. Type designation
4.2. Nameplates
4.3. Design and function
5. Transport and Storage Page 9
6. Installation and Startup Page 10
6.1. Assembly/Installation
6.2. Electrical connection
6.3. Temperature monitoring
7. Centrifugal Force Setting Page 13
8. Servicing and Maintenance Page 15
9. Spare Parts Page 16
10. Disposal and Recycling Page 19
11. Warranty Page 19
Appendix Page 20
• EU Declaration of Conformity
Contents

3
Würges electric vibrators HVE/VFLE are de-
signed and built to state-of-the-art standards
and operate safely if used as intended.
They conform to Category 2 for explosion
hazardous areas of Dust Zone 21/22 and Gas
Zone 1/2.
The provisions of EN 61241-1-2 have to be
heeded, e.g. pertaining to temperatures and
dust accumulations.
The Operating Instructions have to be read
and understood by every person at the user’s
company who is assigned with assembly,
setting up, start up, the maintenance and
repair of vibration motors. This also applies
for additional instructions in case of modified
devices.
The instruction manual must be
read carefully and in full before
using the vibrator motors.
1. General Information

4
The following information and hazard symbols are used in these installation and operating
instructions:
2. Symbols Used
ATTENTION Important information regarding operations or
procedures to which particular attention is to
be paid.
EXPLOSION HAZARD Refers to the possibility of fatal, severe or
irreversible injuries caused by use of the
product in an explosive atmosphere.
HAZARD Refers to the possibility of fatal, severe or
irreversible injuries caused by live parts.
WARNING Refers to the possibility of fatal, severe or
irreversible injuries caused by general hazards.
HOT SURFACE Refers to the possibility of severe or irrevers-
ible injuries caused by touching hot surfaces.
DISCONNECT Refers to the fact that the motor must be
MOTOR FROM MAINS disconnected from the electricity mains and
secured against being switched back on
again before any work is carried out on the
motor.
ENVIRONMENTALLY Refers to the obligation to ensure environ-
COMPATIBLE DISPOSAL mentally compatible disposal.

5
3.1. Intended use
Electric vibrators are not independently
functioning machines. They are used as the
drives of vibrating machines such as vibratory
conveyor troughs, conveyor pipes, screening
machines, grading/sorting machines and
knock-out grids.
These machines use vibrations to screen,
convey, remove, compact and sort or grade.
Any other use is deemed to be not as inten-
ded or misuse.
Electric vibrators are designed to generate
forces that can be destructive.
The vibrating machine must be designed for
the forces generated by the electric vibrators.
The operator shall bear responsibility for the
operation of vibration motors in explosion
hazardous areas.
3.2. Skilled personnel qualifications
The installation/assembly, startup and main-
tenance may only be carried out by authorised
and qualified skilled personnel.
3. Safety

6
3.3. General safety instructions
Electric vibrators generate vibrations. The owner of vibration machines must
protect their employees against actual or possible risks to their health and safety
caused by the effect of vibrations.
Würges Vibrationsmotoren GmbH refuses to accept the responsibility for any
damage to property or personal injuries if technical changes have been made to
the product or the instructions and regulations in this instruction manual have
not been noted and followed.
Live parts can cause severe or fatal injuries.
Electric vibrators must be safely disconnected from the electricity mains before
any work is carried out on them. The required procedure is as follows:
1. Switch off vibrator motor
2. Secure against being switched back on again
3. Test for safe disconnection from the power supply
4. Allow the vibrator motor to cool
Do not touch the vibrator motors while they are running or soon after switching
them off. The surface temperature of the vibrator motors can reach such high
values during operation that there is a risk of burns.
Always use a torque wrench when tightening screws or bolts! Tightening
torques see page 10. Attention to maximum tightening torques on page 14.
Vibrator motors of the HVE/VFLE series may be deployed in the explosion hazar-
dous areas 1/2 and 21/22.
The permissible ambient temperature must be between -20°C and +40 °C.

7
1 Type designation
2 Centrifugal force
3 Mains voltage
4 Nominal current
5 Starting current/nominal
current ratio
6 Heating time
7 Power input
8 Mains frequency
9 Year built
10 Power factor cos φ
11 Speed
12 Serial number
HVE 2 / 2 - 6
4.2. Nameplate
4.1. Type designation
4. Technical Data
Number of poles
Size/
Basic working moment Working moment

8
4.3 Design and function
The electric drive of the HVE model range is
an asynchronous motor.
The stator in the HVE 2 and VFLE 2 sizes
was cast under vacuum thus forming a fixed
assembly with the housing. There are unbal-
anced eccentric discs on the motor shaft
ends.
The unbalance is a rotating body whose mass
is unequally distributed in its rotational sym-
metry, and so causes a vibration as it turns.
This vibration can be dosed via weights and
counterweights.
Please see the data sheet of the motor for
additional technical specifications, or our
catalogue.
Possible voltage variants:
Motor type Hz V
HVE/VFLE 2/2 50 42 – 550
HVE/VFLE 2/2 60 42 – 550
HVE/VFLE 2/4 50 42 – 400
HVE/VFLE 2/4 60 42 – 440

9
When they are delivered the motors must be
checked for visible transport damage!
If the motor is visibly damaged
it must not be started up. The
vibratory motor must be examined
and if necessary returned to the
manufacturer for repair.
Until they are installed the electric vibrators
should be stored in enclosed, dry rooms at a
max. ambient temperature of 40°C.
Vibrator motors must always be stood on their
bases or footings!
Do not stack vibrator motors!
Do not lift up the motor by its
installed connection cable.
Note and follow the local accident prevention
regulations.
5. Transport and Storage

10
Minimum tightening torques
M 5 M 8 M 10 M 12
8 Nm 30 Nm 55 Nm 90 Nm
6.1. Assembly/Installation
Electric vibrators can be installed in any
installation position. Vibrator motors may only
be built on to machines with flat, oil, grease
and paint-free and flexurally rigid mounting
surfaces.
Surface quality
Only bolts in quality class 8.8 > EN ISO 4014
(DIN 931);
EN ISO 4017 (DIN 933) and nuts in quality
class 6 > 8.8 EN ISO 4032 (DIN 934) may be
used.
The bolts must be secured against mechani-
cal loosening by means of spring lock was-
hers DIN 127 Form A, DIN 7980 or Schnorr
washers.
The fixing bolts must be checked
for secure fit after approx. two
operating hours and if necessary
retightened. Other checks should
be carried out daily!
Improper fixing results in the
breakage of the feet of the
vibratory motor.
6. Installation and Startup
Mounting plate
Vibrator foot/flange
correct correct incorrect
✓ ✓

11
The electric connection may only be carried out
by an electrician or electrically instructed person
acc. to EN-60204-1.
The mains voltage and frequency must corres-
pond to the data on the type plate. Device may
only be connected to an electrical power sys-
tem that corresponds to the VDE regulations.
HVE 2/VFLE 2 equipment is factory-equipped
with flexible cable.
Use only cable type OELFLEX FD robust C
4G1,52 or H07 RN-F 4G1,52.
Use a conductor with a cross section of 4 mm²
≤A ≤6 mm² to connect the external equipoten-
tial equalisation.
The motor connection line has to be securely
fastened approx. 0.5 m after leaving the motor.
The first line attachment point and the motor
shall not be moveable against each other. The
connecting cable has to be laid in such a way
that natural vibrations are being avoided and
there will be no tensile load.
Check the current input when the motor is ope-
rated for the first time. It should be greater than
the value stated on the type plate, remedy the
situation by decreasing the centrifugal force
(see Chapter 7).
Check the line for chafe marks from time to
time and eliminate the cause for this where
applicable.
If two counter-rotating motors are installed, it is
necessary to ensure that if one motor fails, both
motors are switched off.
6.2. Electrical connection
Electric vibrators must be safely dis-
connected from the electricity mains
before work is carried out on them.
The required procedure is as follows:
1. Switch off vibrator motor and secure
against being switched back on again
2. Check for safe isolation from supply
3. Allow the motor to cool

12
Speed control
Speed control using frequency
converters is prohibited!
6.3. Temperature monitoring
The permitted ambient temperature range is
from -20°C to +40 °C. Even when affected
by an external source of heat or cold, the
temperature must not fall below or rise beyond
those limits.
To protect against inadmissible temperature
rise in overload conditions, a protective device
must be installed with current-controlled,
delayed breaking capacity. The installed con-
trolling and breaking device must be adjusted
to the nominal current of the motor.
If the motor is used in potentially explosive
gas zones, the controlling and breaking device
must be certified in compliance with Directive
2014/34/EU and the marking must include the
symbol II(2)G. If the motor is used in potenti-
ally explosive dust zones, the marking must
include the symbol II(2)D. In addition, such
protective device must be chosen so that the
motor is provided with thermal protection on
the occurrence of a short circuit, with the rotor
being locked. This requirement is regarded as
being fulfilled, if the breaking time is less than
the permitted temperature rise time appropria-
te to the Temperature Class. The motors must
only be used for continuous operation (S1)
and only for normal starting duties, with the
latter occurring only infrequently and during
which there is no significant temperature rise.
Should the specified current be exceeded, the
speed indicated on the marking plate is pro-
bably not reached. A possible cause for that
can be too high a force for the application or
a construction which is insufficiently resistant
to bending. By reducing the centrifugal force it
can be corrected.

13
Crushing hazard when setting the
centrifugal force. Ensure that the
armature is fixed. Note and follow
the safety instructions on page 6!
If no special centrifugal force setting has been
ordered, the motor is set to maximum centri-
fugal force in the factory.
The centrifugal force has a direct effect on
the vibration amplitude of the machine and
the power input of the motor.
To adjust the centrifugal force, dismantle both
protective covers and undo the unbalance
fixing.
7. Centrifugal Force Setting
With HVE 2 and VFLE 2 motors the centrifugal
force is adjusted in steps by means of push-
on unbalance plates.
The number of plates changed rotated
through 180° must be the same at both ends
of the shaft, i.e. they must be symmetrical
(see Fig.). The unbalance plates can also be
removed for fine adjustment, they must then
be replaced by spacer discs.
The centrifugal force is reduced by turning the
unbalance plates through 180° at both ends.
correct incorrect
✓ ✕

14
Centrifugal force adjustment by means of push-on unbalance plates
The centrifugal force of the motor reduces
as follows if the push-on unbalance plates are
rotated through 180° or removed:
Speed 2-pole, 3000 min-1
Motor Centrifugal force
rotated through 180° removed
HVE/VFLE 2/2 220 N 110 N
Speed 4-pole, 1500 min-1
Motor Centrifugal force
rotated through 180° removed
HVE/VFLE 2/4 55 N 27,5 N
After the centrifugal force has
been adjusted the loosened bolts
and nuts must be retightened and
the protective covers must be re-
fitted (see page 10 for tightening
torques). Otherwise there is a risk
of accidents! To ensure water-
tightness ensure that the seals
are intact when dismantling and
installing the protective covers.
Damaged seals must be replaced.
Never operate motors without
unbalance plates. This causes
damage to the bearings.
Running the motors without the
protective covers is forbidden!
Maximum tightening torque of screw at
the shaft end
M 8
15 Nm

15
Lubrication
The bearings of the vibrating motors of the
HVE series are lubricated for life. Maintenance
of the bearings for this equipment is not
required.
The theoretical bearing life is:
Motor type f = 50 Hz f = 60 Hz
HVE/VFLE 2/2-6 7500 h 5500 h
HVE/VFLE 2/2-4 30000 h 20000 h
HVE/VFLE 2/2-2 65000 h 65000 h
HVE/VFLE 2/4 150000 h 150000 h
If there are any signs of wear or when the
theoretical bearing life is being reached, the
equipment should immediately be removed
from operation and the special bearings
replaced.
In this case, we recommend the equipment
to be sent to the manufacturer for repair (or
with any other damage). It is the only way to
ensure professional repair.
The electric vibrators must al-
ways be disconnected from the
electricity mains before any work
is carried out on it!
1. Switch off vibrator motor
2. Secure against being switched
back on again
3. Test for safe disconnection from
the power supply
4. Allow the vibratory motor to cool
Maintenance work to be carried out
regularly
• The surfaces of the motors must be kept
free from dirt in order to ensure adequate
cooling.
• Check the connection cable for chafe
marks and if applicable remove whatever is
causing them.
• Check xing bolts for secure t and if
necessary retighten.
• Check the seals.
The fixing bolts must be retight-
ened after approx. two operating
hours (following startup). Other
checks should be carried out
daily.
8. Servicing and Maintenance

16
To order spare parts, please refer to the spare
parts list of the respective motor (see drawings
on pages 17/18).
Please always give the following information
with each order for spare parts:
• Motor type
• Motor number
• Description, item and position number of
the part
• Required quantity
For further information, please refer to the
exploded views given in the spare parts list.
We only provide warranty for the original spare
parts supplied by us.
We expressly point out that spare parts and
accessories that are not original parts supplied
by us have not been tested and approved by
us. Installing and/or using such products can
therefore cause negative changes to the spe-
cified design properties and therefore impair
active and/or passive safety.
Würges does not accept any liability what-
soever or provide any warranty for damage
caused by the use of non-original spare parts
and accessories.
9. Spare Parts

17
Spare parts list HVE 2
Pos. Nomenclature Ord.-No. Pieces
HVE HVE HVE HVE HVE HVE HVE HVE
2/2 2/2-2 2/2-4 2/2-6 2/4 2/4-4 2/4-6 2/4-9
1 Housing complete HVE 2/2 – 1 1 1 1 – – – –
1 Housing complete HVE 2/4 – – – – – 1 1 1 1
2 Protective cap HVE – 2 2 2 2 2 2 2 2
3 Screw for protective cap – 4 4 4 4 4 4 4 4
4 Armature – 1 1 1 1 1 1 1 1
5 Terminal box lid 00401 1 1 1 1 1 1 1 1
6 Screw for terminal box lid 21301 4 4 4 4 4 4 4 4
7 Anchor securing screw 22551 2 2 2 2 2 2 2 2
8 Bearing 24301 2 2 2 2 2 2 2 2
9 Washer 27001 2 2 2 2 2 2 2 2
10 Flyweight 75311 8 12 16 26 8 16 26 40
11 Terminal box seal 75801 1 1 1 1 1 1 1 1
12 O-ring 75911 2 2 2 2 2 2 2 2
13 Spacer tube 76401 2 2 2 2 2 2 2 2
Cable – 2 m 2 m 2 m 2 m 2 m 2 m 2 m 2 m
15 ATEX cable gland 29711 1 1 1 1 1 1 1 1

18
Spare parts list VFLE 2
Pos. Nomenclature Ord.-No. Pieces
VFLE VFLE VFLE VFLE VFLE VFLE
2/2 2/2-2 2/2-4 2/4 2/4-2 2/4-4
1 Housing complete VFLE 2/2 – 1 1 1 1 1 1
1 Housing complete VFLE 2/4 – 1 1 1 1 1 1
2 Protective cap VFLE – 2 2 2 2 2 2
3 Screw for protective cap – 4 4 4 4 4 4
4 Armature – 1 1 1 1 1 1
5 Terminal box lid 00401 1 1 1 1 1 1
6 Screw for terminal box lid 21301 4 4 4 4 4 4
7 Anchor securing screw 22551 2 2 2 2 2 2
8 Bearing 24301 2 2 2 2 2 2
9 Washer 27001 2 2 2 2 2 2
10 ATEX cable gland 29711 1 1 1 1 1 1
Cable – 2 m 2 m 2 m 2 m 2 m 2 m
12 Flyweight 75311 8 12 16 8 12 16
13 Therminal box seal 75801 1 1 1 1 1 1
14 O-ring 75911 2 2 2 2 2 2
15 Spacer tube 76401 2 2 2 2 2 2
16 Protective cap HVE – 1 1 1 1 1 1

19
Packaging materials and motor components
must be disposed of in an environmentally
compatible way.
Steel:
Unbalance plates, armature and rotor, bolts,
nuts and bearing
Aluminium:
Housing, protective covers, terminal box cover
and nameplate
PE:
Seals/gaskets
Copper and synthetic resin:
Winding
You can return the motors to us
for proper disposal!
They must be delivered to us
carriage paid.
10. Disposal and Recycling
Würges provides warranty for 1 year, begin-
ning with delivery, for all new vibrating motors.
Warranty expires when:
• the motor is connected wrong, or connec-
ted with wrong voltage,
• the motor fails because of missing or wrong
electric protection,
• there were changes made to the motor,
• the motor was damaged during transport,
• the motor was not installed as shown in
chapter 6,
• the motor was connected with wrong cable,
• there is misuse/not intended use,
• the instructions of the manual are not
followed.
11. Warranty

20
The manufacturer
Würges Vibrationsmotoren GmbH, Boschstr. 9, 86356 Neusäß hereby declares:
The explosion-proof electric vibrator motors of the series
HVE / VFLE
are conform with the following directives:
2014/34/EU (ATEX)
2014/30/EU (EMC)
2011/65/EU (RoHS)
Following harmonised standards were applied:
EN ISO 12100 / 2011* EN 60079-7 / 2007*
EN 60034-1 / 2015* EN 61241-0 / 2007
EN 61000-6-2 / 2011 EN 61241-1 / 2005
EN 61000-6-4 / 2011
EN 60079-0 / 2007*
(The standard mentioned in the EC-type Examination Certificate PTB 03 ATEX 3047 has already been replaced by this later
issue. The Manufacturer declares compliance for the product also being in line with the requirements of the current issue of
the standard since the changed requirements of the new issue of the standard are not relevant for this product.)
Following notified bodies have been involved:
TÜV Rheinland Nr. 0035 (QS-System Test)
PTB Braunschweig Nr. 0102 (Prototype Text)
Commissioning is prohibited until it has been determined that the machine(s) stated overleaf into which
the incomplete machine(s) will be installed conform to the provisions of the Machine Directive.
Neusäß, 31.10.2019
Würges Vibrationsmotoren GmbH
Dipl.-Ing.(FH)
Philipp Würges
Managing Director
EU Declaration of Conformity
This manual suits for next models
3
Table of contents
Other WÜRGES Engine manuals
Popular Engine manuals by other brands
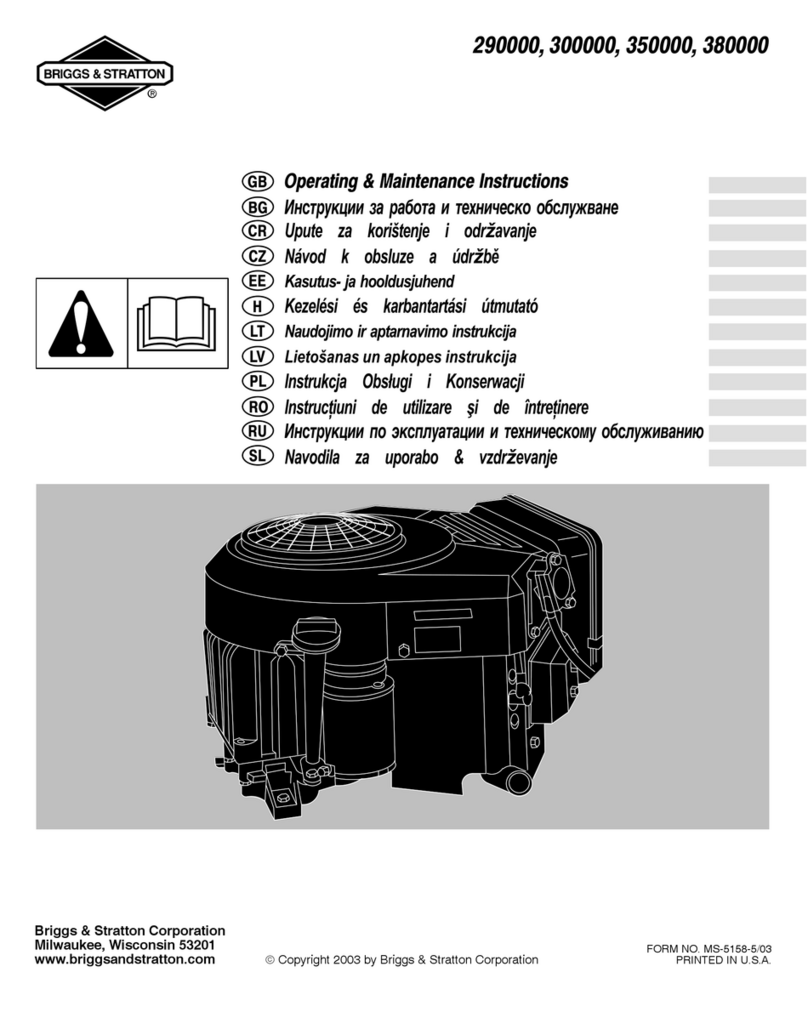
Briggs & Stratton
Briggs & Stratton Vanguard 290000 Operating & maintenance instructions
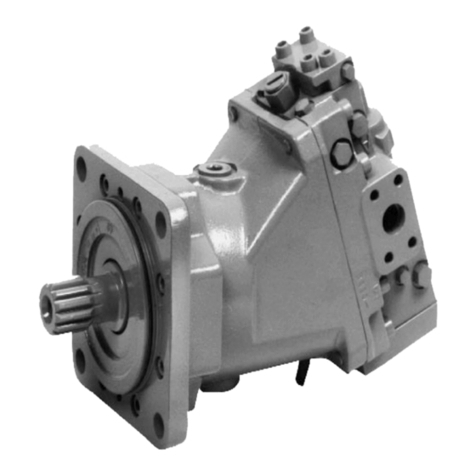
Danfoss
Danfoss 51 Series Service manual
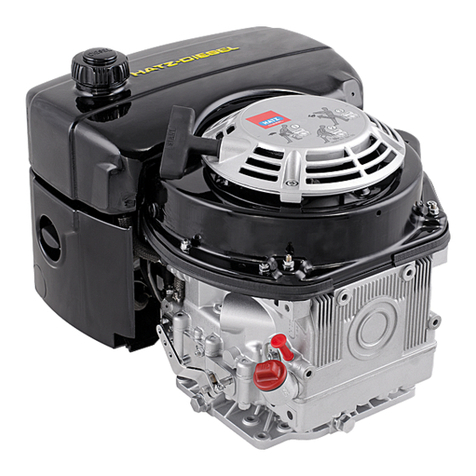
Hatz
Hatz 1B30V Instruction book
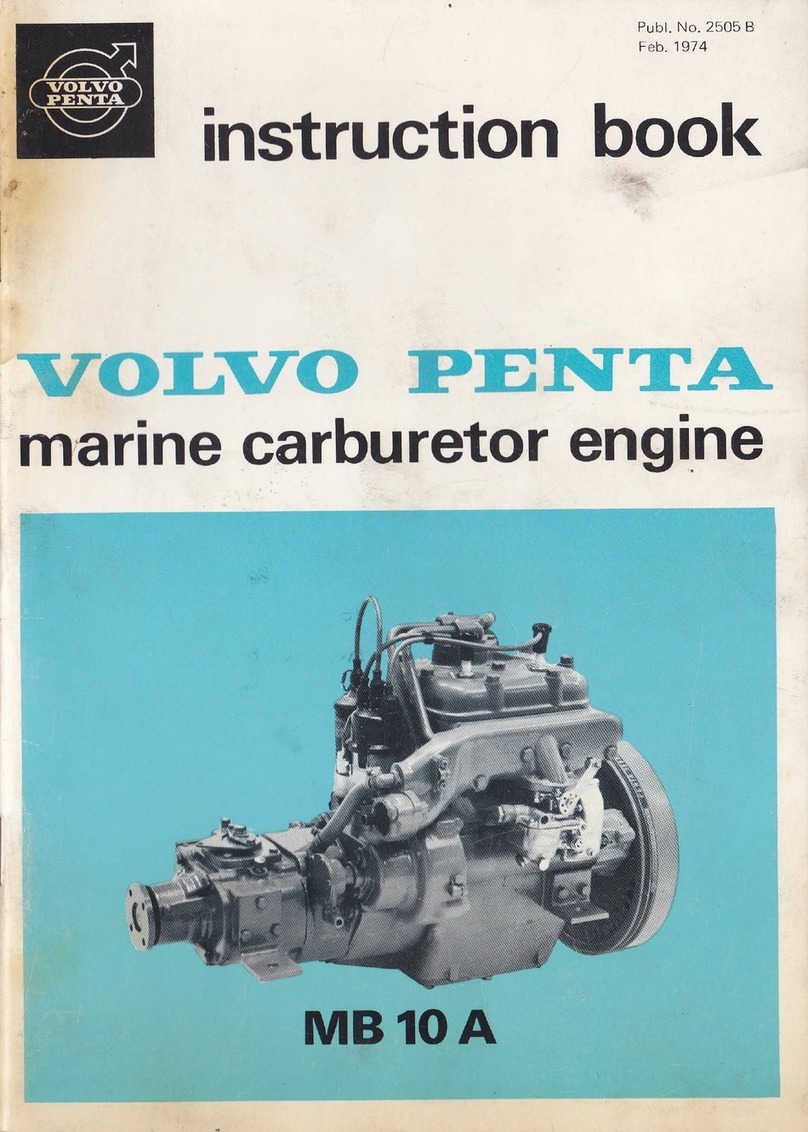
Volvo Penta
Volvo Penta MB 10 A Instruction book
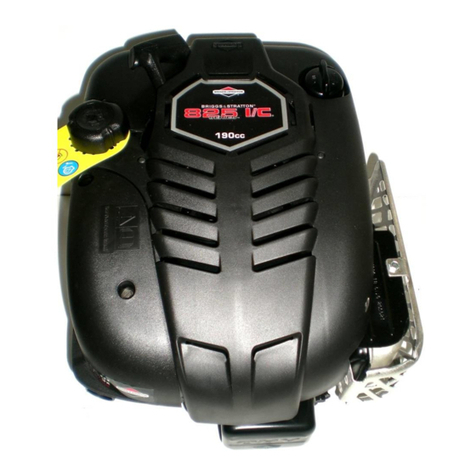
Briggs & Stratton
Briggs & Stratton Intek 825 Series Operator's manual

Sealey
Sealey VSE2510 instructions
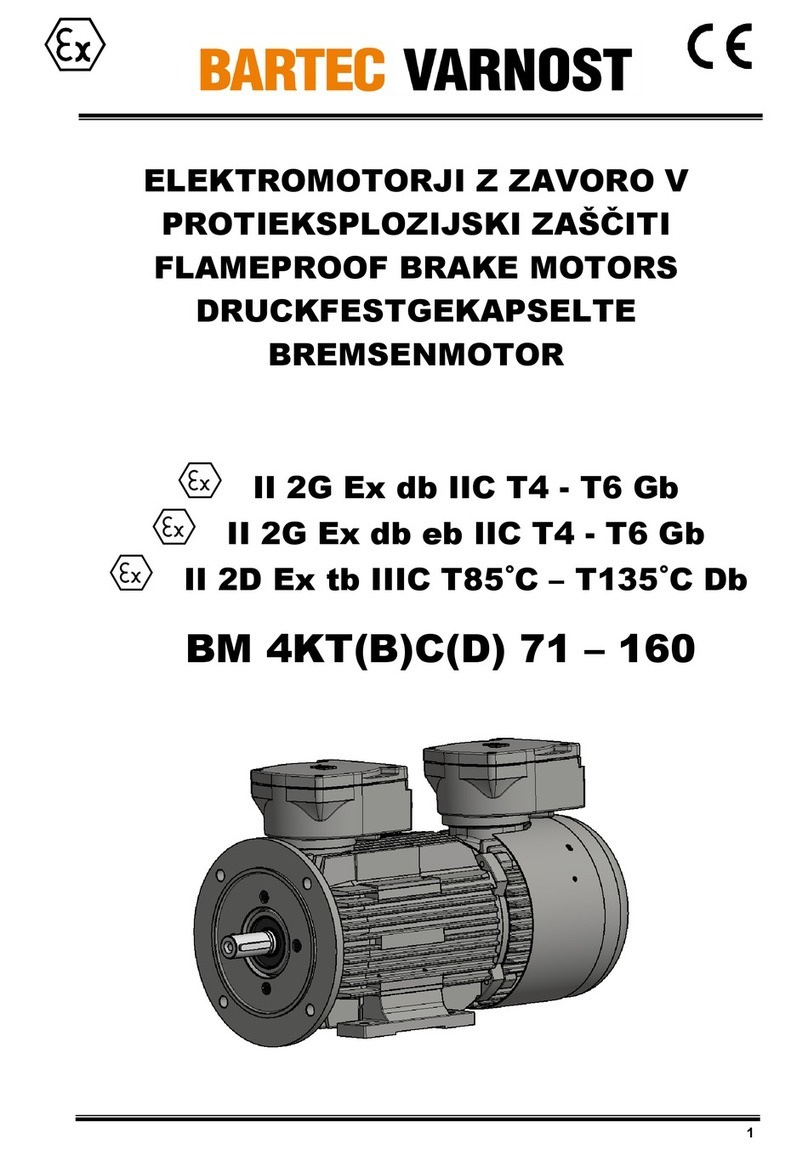
Bartec Varnost
Bartec Varnost BM 4KTC71 manual
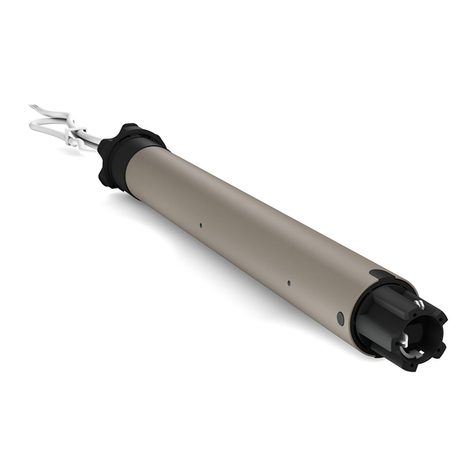
DELTA DORE
DELTA DORE TYMOOV 6F2 quick start guide
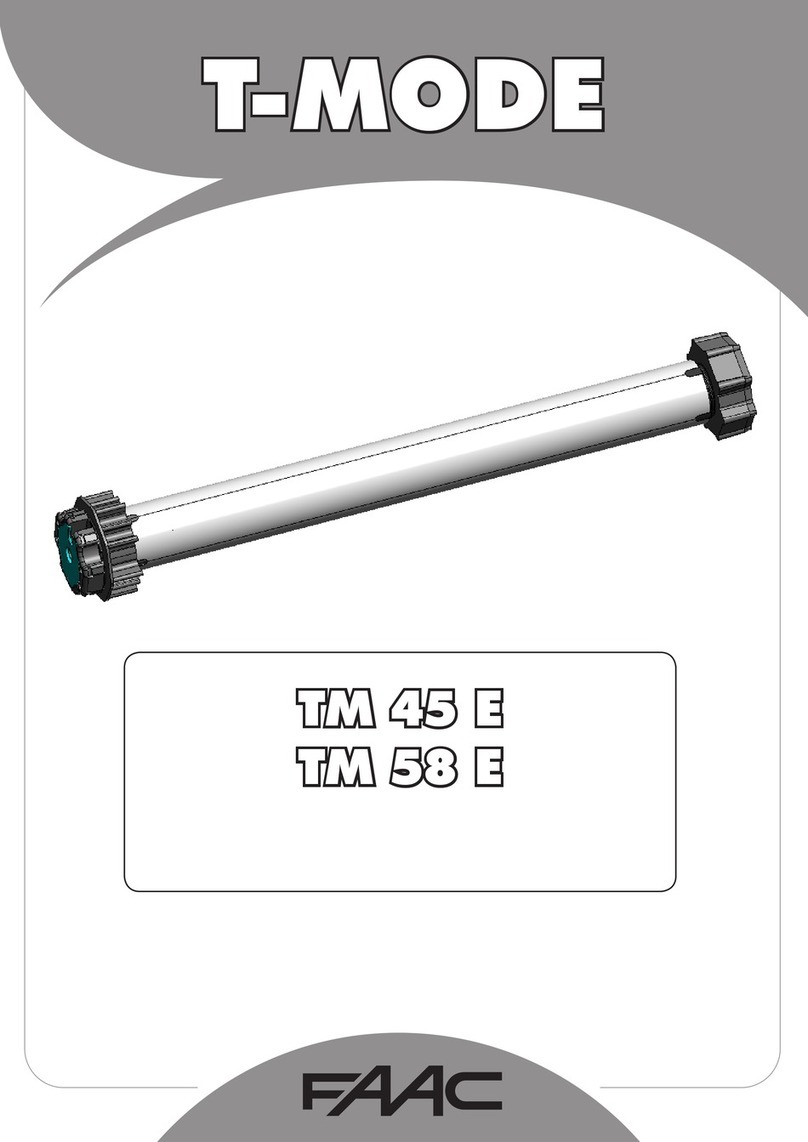
FAAC
FAAC T-MODE TM 45 E manual

Tecumseh
Tecumseh LH195SA/LH195SP (HSSK40-55) Operator's manual
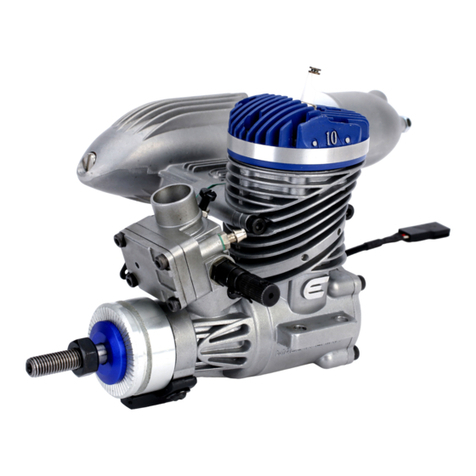
Evolution
Evolution EVOE10GX user manual

MerCruiser
MerCruiser 350 Magnum EFI GEN+ Alfa One Operation and maintenance manual