WAGNER EPG-SPRINT Operational manual

II 3(2)D IP64 80°C
P_01110
%
Tribo Corona
5
4
3
2
1
120
100
80
60
40
30
20
15
10
5
μA
μA
0
10
20
30
40
50
60
70
80
90
100
Ø
12
10
11
9
8
m /h
5.0
4.0
3.0
2.0
6.0
3
5.5
4.5
3.5
2.5
2.2
2x
kV
90
80
70
60
50
40
30
20
10
100
m/h
4.0
3.0
2.0
1.0
0.5
0.4
0.3
0.2
0.1
1.5
EP
G
SP
R
I
NT
0102
Universal Control Unit for
Powder Coating Guns
EPG-SPRINT
Version 08 / 2010
Translation of the original
Operating manual


3
EPG-SPRINT.
OPERATING MANUAL
VERSION 08/2010 ORDER NUMBER DOC 2305222
Contents
1 ABOUT THESE INSTRUCTIONS 5
1.1 Languages 5
1.2 Warnings, notes and symbols in these instructions 5
2 GENERAL SAFETY INSTRUCTIONS 6
2.1 Safety instructions for the operator 6
2.1.1 Electrical plant and units 6
2.1.2 Personnel qualifications 6
2.1.3 A safe work environment 6
2.2 Safety instructions for staff 7
2.2.1 Safe handling of WAGNER powder spray units 7
2.2.2 Earth the unit 7
2.2.3 Material hoses 7
2.2.4 Cleaning 7
2.2.5 Handling powder paints 8
2.3 Using in accordance with the instructions 8
2.4 For use in potentially explosive areas 8
2.4.1 Using in accordance with the instructions 8
2.4.2 Explosion protection identification 8
2.5 Safety features 9
3 WARRANTY AND CONFORMITY DECLARATIONS 10
3.1 Important notes on product liability 10
3.2 Warranty claim 10
3.3 CE-conformity 11
3.4 FM-Identification 12
4 DESCRIPTION 13
4.1 Fields of application, using in accordance with the instructions 13
4.2 Delivery scope 14
4.3 Technical data 14
4.4 Control functions 16
4.4.1 Operating elements frontside 16
4.4.2 Connections on the rear side of the EPG-SPRINT unit 20
5 PREPARATIONS FOR STARTING UP 22
5.1 Connecting the manual gun 23
5.2 Connecting the automatic spray guns 24
5.3 Grounding 25
5.3.1 Grounding of the powder coating system 26
6 STARTING UP AND OPERATING 27
6.1 Preparations for starting up 27
6.1.1 Gun detection 27
6.1.2 Basic and factory settings 28
6.2 Coating programs 28
6.2.1 “Double click“ program (high dynamic remote) 29
6.3 Air high output mode (high powder output) 30
6.3.1 Combining the air outputs 30
6.3.2 Activate high output mode (C17) 31

4
EPG-SPRINT.
OPERATING MANUAL
VERSION 08/2010 ORDER NUMBER DOC 2305222
Contents
6.4 Changing and saving programs 34
6.4.1 Programs no. 1-4 34
6.4.2 Programs no. 5-50 35
6.5 Setting and changing the coating parameters 36
6.5.1 Setting the overall air quantity 36
6.5.2 Setting the powder feed quantity 37
6.5.3 Setting the additional air (atomizing/ionising/Tribo air quantity) 38
6.5.4 Setting the high-voltage 39
6.5.5 Display of actual high-voltage value 40
6.5.6 Setting the current limiting 41
6.5.7 Displaying actual value of current limiting 42
6.5.8 Setting the U/I characteristics 43
6.6 Rinse function 45
6.6.1 Hose purge function 45
6.6.2 Cleaning purge function 45
6.6.3 Procedure for cleaning purging 46
6.7 Disposal 47
7 ELIMINATION OF FAULTS 48
7.1 Warnings E01-E04 48
7.2 Malfunctions E11-E43 50
8 SPARE PARTS 52
8.1 How to order spare parts? 52
8.2 EPG-SPRINT control unit 53
8.3 Accessories 53
ATTACHMENT DEVICE CONFIGURATION 54
BRIEF DESCRIPTION 63
1 Changing the parameters 64
2 Calling / changing / saving programs 1-4 64
3 Calling / changing / saving programs 5-50 64

5
EPG-SPRINT.
OPERATING MANUAL
VERSION 08/2010 ORDER NUMBER DOC 2305222
The operating manual is available in the following languages:
Language: Order No. Language: Order No.
German English
French Dutch
Italian Spanish
Danish Swedish
Hungarian Polish
Czech Finnish
Russian Slovenian
Croatian Rumanian
Hebrew Portuguese
1.2 WARNINGS, NOTES AND SYMBOLS IN THESE INSTRUCTIONS
1 ABOUT THESE INSTRUCTIONS
1.1 LANGUAGES
2305220 2305222
2305224 2310775
2305225 2305226
2310774 2310773
2311177
Warning instructions in this manual point out particular dangers to users and equipment
and state measures for avoiding the hazard.These warning instructions fall into the follo-
wing categories:
Danger - imminent danger.Non-observance will result
in death, serious injury and serious material damage.
Warning - possible danger. Non-observance can result
in death, serious injury and serious material damage.
Caution - a possibly hazardous situation. Non-obser-
vance can result in minor injury.
Note - provide information on particular characteristics and how to proceed.
Caution - a possibly hazardous situation. Non-obser-
vance can cause material damage.
SIHI_0100_GB
DANGER
This line warns of the hazard!
Possible consequences of failing to observe the warning instruc-
tions. The signal word points out the hazard level.
The measures for preventing the hazard and its consequences.
SIHI_0103_GB
WARNING
This line warns of the hazard!
Possible consequences of failing to observe the warning instruc-
tions. The signal word points out the hazard level.
The measures for preventing the hazard and its consequences.
SIHI_0101_GB
CAUTION
This line warns of the hazard!
Possible consequences of failing to observe the warning instruc-
tions. The signal word points out the hazard level.
The measures for preventing the hazard and its consequences.
SIHI_0102_GB CAUTION
This line warns of the hazard!
Possible consequences of failing to observe the warning instructions. The signal word
points out the hazard level.
The measures for preventing the hazard and its consequences.
4HISOPERATINGMANUALCONTAINSINFORMATIONONTHEOPERATIONREPAIRANDMAINTENANCEOF
THEUNIT
!LWAYSOBSERVETHESEINSTRUCTIONSWHENOPERATINGTHEUNIT
4HISEQUIPMENTCANBEDANGEROUSIFITISNOTOPERATEDINACCORDANCEWITHTHISMANUAL
#OMPLIANCE WITH THESE INSTRUCTIONS CONSTITUTES AN INTEGRAL COMPONENT OF THE WARRANTY
AGREEMENT

6
EPG-SPRINT.
OPERATING MANUAL
VERSION 08/2010 ORDER NUMBER DOC 2305222
2 GENERAL SAFETY INSTRUCTIONS
2.1 SAFETY INSTRUCTIONS FOR THE OPERATOR
2.1.1 ELECTRICAL PLANT AND UNITS
2.1.2 PERSONNEL QUALIFICATIONS
2.1.3 A SAFE WORK ENVIRONMENT
+EEPTHESEOPERATINGINSTRUCTIONSTOHANDNEARTHEUNITATALLTIMES
!LWAYSFOLLOWLOCALREGULATIONSCONCERNINGOCCUPATIONALSAFETYANDACCIDENTPREVEN
TION
%NSURETHATTHEUNITISOPERATEDANDREPAIREDONLYBYTRAINEDPERSONS
To be provided in accordance with the local safety requirements with regard to the
operating mode and ambient influences.
May only be maintained by skilled electricians.
Must be operated in accordance with the safety regulations and electrotechnical
regulations.
Must be repaired immediately in the event of problems.
Must be put out of operation if they pose a hazard.
Must be de-energized before work is commenced on active parts.
Secure the control unit against being switched back on without authorisation. Inform
staff about planned work.
Observe electrical safety regulations.
ªEnsure that the floor of the working area is anti-static (measurement in accordance
with EN 1081).
ªEnsure that all persons within the working area wear anti-static shoes.
ªEnsure that gloves that are being worn, are made of conductive material.
ªThe powder release must be electronically interlocked with the powder spray system
exhaust equipment.
ªExcess coating material (overspray) must be collected up safely.
ªEnsure that there are no ignition sources such as naked flame, glowing wires or hot
surfaces in the vicinity. Do not smoke.
ªMaintain sufficient quantities of suitable fire extinguishers and ensure that they are
serviceable.
ªThe operating company must ensure that an average concentration of powder paint
in the air does not exceed 50% of the lower explosion limit (LEL = max. permitted
concentration of powder to air). If no reliable LEL value is available, the average
concentration may not exceed 10g/m³.

7
EPG-SPRINT.
OPERATING MANUAL
VERSION 08/2010 ORDER NUMBER DOC 2305222
2.2.1 SAFE HANDLING OF WAGNER POWDER SPRAY UNITS
2.2.2 EARTH THE UNIT
2.2.3 MATERIAL HOSES
2.2 SAFETY INSTRUCTIONS FOR STAFF
➞Only use original Wagner powder hose.
Always follow the information in these instructions, particularly the general safety
instructions and the warning instructions.
Always follow local regulations concerning occupational safety and accident
prevention.
Under no circumstances should persons with pacemakers be in the area where the
high-voltage field between the spray gun and the workpiece to be coated builds up!
Never point the powder spray gun at people.
Before all work on the unit, in the event of work interruptions and functional faults:
– Switch off the energy/compressed air supply.
– Secure the powder spray gun against actuation.
– Relieve the pressure from the powder spray gun and unit.
– By functional faults: Identify and correct the problem, proceed as described in chap.
“Trouble shooting“.
The electrostatic charge may, in certain cases, give rise to electrostatic charges on the
device.These can involve with unloading transmitting or flame formation.
ªEnsure that the device is grounded before each coating process.
ªEarth the workpieces being painted.
ªEnsure that all persons inside the working area are earthed, e.g. that they are wearing
antistatic shoes.
ªGrounding cables must be checked regularly to ensure that they are serviceable
(see EN 60204).
2.2.4 CLEANING
De-energize the unit electrically.
Disconnect the pneumatic supply line.
Relieve the pressure from the unit.
Secure the control unit against being switched back on without authorisation.
Only mobile industrial vacuum cleaners of design 1 (see EN 60335-2) may be used for
getting rid of dust build-ups.

8
EPG-SPRINT.
OPERATING MANUAL
VERSION 08/2010 ORDER NUMBER DOC 2305222
2.3 USING IN ACCORDANCE WITH THE INSTRUCTIONS
7!'.%2ACCEPTSNOLIABILITYFORANYDAMAGEARISINGFROMINCORRECTUSE
5SETHEUNITONLYTOWORKWITHTHEMATERIALSRECOMMENDEDBY7!'.%2
/PERATETHEUNITONLYASANENTIREUNIT
$ONOTDEACTIVATESAFETYEQUIPMENT
5SEONLY7!'.%2ORIGINALSPAREPARTSANDACCESSORIES
2.2.5 HANDLING POWDER PAINTS
Take note of the processing regulations laid down by the manufacturer of the powder
paint being used, when preparing or processing the powder.
Take note of the manufacturer’s advice and the relevant environmental protection
regulations when disposing of powder paints.
Implement the prescribed safety measures, in particular the wearing of safety glasses
and safety clothing as well as the use of protective hand cream.
Use dust masks or breathing apparatus.
To ensure sufficient protection of health and the environment,only operate the device
in a powder booth or at a spray wall with activated ventilation (exhaust air).
2.4.1 USING IN ACCORDANCE WITH THE INSTRUCTIONS
2.4.2 EXPLOSION PROTECTION IDENTIFICATION
2.4 FOR USE IN POTENTIALLY EXPLOSIVE AREAS
The EPG-SPRINT control units are intended for use with powder spray guns of types A-P up
to 2 mJ in accordance with the prototype test PTB 06 ATEX 5003.
The EPG-Sprint control unit may be used in the dust explosion zone (zone 22) under the
following conditions:
●Control unit correctly fitted in rack.
●Rack correctly and securely sealed on rear with associated cover.
The device is suited for use in areas at risk from explosions, in accordance with Test
Certificate PTB 06 ATEX 5003.
II 3D IP 64 80°C
CE: Communautés Européennes
Ex: Symbol for explosion protection
II: Unit class II
3: Category 3 (zone 22)
D: Ex-atmosphere dust
IP64: Protection class 64
80°C: Temperature class: max. surface temperature < 80°C; 176°F

9
EPG-SPRINT.
OPERATING MANUAL
VERSION 08/2010 ORDER NUMBER DOC 2305222
2.5 SAFETY FEATURES
Plates bearing information for the user have been attached to the work openings of the
powder coating booth.
The plate size corresponds to the standard category Ø 100 mm; 3.94 inches.
The label plates, which must be attached, are shown below.
High-voltage!
In the control cabinet:
(25 mm; 0.98 inches)
Voltage before main
switch.
Forbidden for unauthorized
persons!
Explosive atmosphere!
Forbidden for persons
with a cardiac pacemaker!
Follow the instructions in
the operating manual!
Fire, open light and
smoking prohibited!
Wear electrostatically
conductive footwear!
Danger of crushing!
Risk of tripping!
Do not jump on the
booth floor!
Danger of slipping

10
EPG-SPRINT.
OPERATING MANUAL
VERSION 08/2010 ORDER NUMBER DOC 2305222
3 WARRANTY AND CONFORMITY DECLARATIONS
3.1 IMPORTANT NOTES ON PRODUCT LIABILITY
3.2 WARRANTY CLAIM
!SARESULTOFAN%#REGULATIONEFFECTIVEASFROM*ANUARYTHEMANUFACTURERSHALL
ONLYBELIABLEFORHISPRODUCTIFALLPARTSCOMEFROMHIMORAREAPPROVEDBYHIMANDIFTHE
DEVICESAREPROPERLYlTTEDOPERATEDANDMAINTAINED
)FOTHERMAKESOFACCESSORYANDSPAREPARTSAREUSEDTHEMANUFACTURER@SLIABILITYCOULDBE
FULLYORPARTIALLYNULLANDVOID
4HEUSAGEOFORIGINAL7!'.%2ACCESSORIESANDSPAREPARTSGUARANTEESTHATALLSAFETYRE
GULATIONSAREOBSERVED
This equipment is covered by the following manufacturing warranty.
We will at our discretion repair or replace free of charge all parts which within 24 months
in single-shift, 12 months in 2-shift or 6 months in 3-shift operation from date of receipt by
the Purchaser are found to be wholly or substantially unusable due to causes prior to the
sale, in particular faulty design, defective materials or poor workmanship.
The terms of the warranty are met at our discretion by the repair or replacement of the
unit or parts thereof. The resulting costs, in particular shipping charges, road tolls, labour
and material costs will be borne by us except where these costs are increased due to the
subsequent shipment of the unit to a location other than the address of the purchaser.
This warranty does not cover damage caused by:
Unsuitable or improper use, faulty installation or commissioning by the purchaser or a
third party, normal wear, negligent handling, defective maintenance, unsuitable coating
products, substitute materials and the action of chemical, electrochemical or electrical
agents, except when the damage is attributable to us.
This warranty does not cover damage caused by:
Unsuitable or improper use, faulty installation or commissioning by the purchaser or a
third party, normal wear, negligent handling, defective maintenance, unsuitable coating
products, substitute materials and the action of chemical, electrochemical or electrical
agents, except when the damage is attributable to us.
Components not manufactured by Wagner are subject to the warranty terms of the
original maker.
The replacement of a part does not extend the warranty period of the unit.
The unit should be inspected immediately upon receipt.
To avoid loss warranty, aniy apparent defect should be notified to us or the dealer in
writing within 14 days from date of sale of the unit.
The right to commission warranty services to a third party is reserved.
Warranty claims are subject to proof of purchase by submitting an invoice or delivery
note. If an inspection finds damage not covered by the present warranty, the repair will be
carried out at the expense of the purchaser.
Note that this warranty does not in any way restrict legally entitled claims or those
contractually agreed to in our general terms and conditions.
J.Wagner AG

11
EPG-SPRINT.
OPERATING MANUAL
VERSION 08/2010 ORDER NUMBER DOC 2305222
3.3 CE-CONFORMITY
EPG-SPRINT 2305227
Herewith we declare that the supplied version of
- EPG-SPRINT, order no. 2305109
complies with the following provisons applying to it:
- 94/9/EG (Atex-directive)
- 2004/108/EG (Electro-magnetic compatibility (EMC) guideline)
- 2002/95/EG (RoHs-directive)
- 2002/96/EG (WEEE-directive)
Applied standards, in particular:
- DIN EN 1127-1: 2008
- DIN EN 50050: 2007
- DIN EN 50177: 2007
- DIN EN 50053-2: 1990
- DIN EN 61241-0: 2007
- DIN EN 61241-1: 2005
- DIN EN 61241-14: 2005
- DIN EN 60529: 2000
- DIN EN 61000-6-2: 2000
- DIN EN 61000-6-4: 2002
- BGI 764
Marking:
CE Certificate of Conformity
The certificate is enclosed with this product.The certificate of conformity can be reordered
from your WAGNER representative, quoting the product and serial number.
Part number:

12
EPG-SPRINT.
OPERATING MANUAL
VERSION 08/2010 ORDER NUMBER DOC 2305222
FM approved for CL II, Div 2 Grps E, F, & G
Power Pack EPG-Sprint FM
P/N 2305127
In accordance with control document:
2309729
P_01109
Output 100kV max.
In accordance with control document: 2309729
Ambient Temperature 45C / IP54
For Electro. Fin. Appl. CL. II Spray Materials
P_01089
Overvoltage Category II
and pollution Degree 2
P_01088
3.4 FM-IDENTIFICATION
FM Approved for US and Canada
This power pack, identified on attached label, is FM approved for use in Class II, Division 2,
Groups E, F, & G hazardous (classified) locations.
The spray gun, identified on inscription on top of gun housing, is FM approved for use in
Electrostatic Finishing Applications using Class II, Spray Materials.
In using Control Document P/N 2309729 the approved Power Pack and spray guns
including accessories can be identified for correct combination.
This control document is included in the packing, but can reordered anytime from Wagner
under P/N 2309729.

13
EPG-SPRINT.
OPERATING MANUAL
VERSION 08/2010 ORDER NUMBER DOC 2305222
4 DESCRIPTION
4.1 FIELDS OF APPLICATION, USING IN ACCORDANCE WITH THE INSTRUCTIONS
The EPG-SPRINT control unit can be used as a stand-alone unit in manual coating systems
or can be connected to the PrimaTech automatic system together with other units.
●When a Corona gun is connected, Corona current scale and the high-voltage supply
and control unit are active.
●When a Tribo gun is connected, the Tribo current scale is activated, while the
high-voltage supply and control unit are deactivated.
The control unit recognizes whether a manual or automatic spray gun is connected.
If an automatic gun is connected, then the control unit can only be controlled via the
CCM Prima interface.
The following powder coating guns can be connected to the EPG-SPRINT:
Manual spray guns
●Corona spray gun PEM-C3, PEM-C4, PEM-C4-Ergo
●Tribo spray gun PEM-T3
Automatic spray guns
●Corona spray gun PEA-C3, PEA-C4
●Corona spray gun PEA-C3XL, PEA-C4XL
●Tribo spray gun PEA-T3
●Tribo spray gun PEA-T3XL
●Angled spray gun PEA-C3A, PEA-C4A (not PTB approved)
Older or other gun types may only be connected to the control unit after first checking
their suitability with Wagner.
WARNING
Incorrect use!
Risk of injury and damage to the equipment.
➞Only connect original Wagner spray guns to the EPG-SPRINT
control unit.
➞The PEM-C3R and PEM-T3R manual spray guns cannot be
connected to the EPG-SPRINT control unit.

14
EPG-SPRINT.
OPERATING MANUAL
VERSION 08/2010 ORDER NUMBER DOC 2305222
Quantity Order No. Designation
1 2305109 EPG-SPRINT (for manual and automatic systems)
1 2305127 EPG-SPRINT FM (for USA)
The standard equipment includes:
1 2305227 Declaration of conformity
1 2305220 Operating manual German
1 see chapter 1.1 Operating manual in the local language
4.2 DELIVERY SCOPE
Dimensions:
Height 136 mm; 5.35 inches
Width 270 mm; 10.63 inches
Depth (without operating elements) 200 mm; 7.87 inches
Weight 3.3 kg; 7.28 lb
Electrical:
Mains (AC) 85 VAC-250 VAC
Frequency 47 Hz-440 Hz
Input power max. 40 W
Output voltage max. 22 Vpp
Output current max. 0.9 A
High-voltage 10-100 kV (adjustable in 1 kV steps)
Corona current limitation 5 µA-120 µA (adjustable in 1 µA steps)
Tribo current measurement 0 µA-5 µA (resolution 0.5 µA)
Tribo current low level warning 0 µA-5 µA (adjustable in 0.1 µA steps)
Tribo current cut off higher than 12 µA
(ATEX: switch the unit off )
Protection class IP 64
Explosion zone II 3(2)D 80°C; 176°F
4.3 TECHNICAL DATA

15
EPG-SPRINT.
OPERATING MANUAL
VERSION 08/2010 ORDER NUMBER DOC 2305222
Pneumatic:
Compressed air input pressure 0.6-0.8 MPa; 6-8 bar; 87-116 psi
Air quantity max. 15 m³/h
Summation of the dosage and feed air 2-6 m³/h
Gun air 0.05-4.0 m³/h
Required compressed air quality as per
ISO 8573.1
3.5.2
Connection hose diameter 8 mm; 0.315 inches
Ambient conditions:
Operating temperature range 5-45°C; 41-113°F
SIHI_05034_ENG
WARNING
Outgoing air containing oil!
Risk of poisoning if inhaled.
Provide water-free and oil-free compressed air (quality standard
3.5.2 as per ISO 8573.1) 3.5.2 = 5 μm / +7°C; 44.6°F / 0.1 mg/m³.
SIHI_05054_ENG
CAUTION
Compressed air quality, accessories
Danger of equipment damage.
Operate the control unit only with the prescribed compressed air quality.
Only use the control unit with original Wagner accessories.
Disregard of these conditions leads to expiring the warranty.
Ambient conditions:
If low temperature powders are used,the ambient temperature may have to be lower than
30°C; 86°F.
Volume measures:
For volumes,specified in Nm³ (standard cubic meters). One cubic meter of a gas at 0°C;32°F
and 1.013 bar is called norm cubic meter. 1 Nm³/h = 35.3ft³/h; 1 bar = 14.504 psi.

16
EPG-SPRINT.
%
Tribo Corona
5
4
3
2
1
120
100
80
60
40
30
20
15
10
5
μA
μA
0
10
20
30
40
50
60
70
80
90
100
Ø
12
10
11
9
8
m /h
5.0
4.0
3.0
2.0
6.0
3
5.5
4.5
3.5
2.5
2.2
2x
kV
90
80
70
60
50
40
30
20
10
100
m /h
4.0
3.0
2.0
1.0
0.5
0.4
0.3
0.2
0.1
1.5
EPG
SPRINT
P_01111
OPERATING MANUAL
VERSION 08/2010 ORDER NUMBER DOC 2305222
4.4 CONTROL FUNCTIONS
28 27 30 29 31 32 37 35 24
1 Illuminated display: High-voltage
●Lights up green.
●Display range: 0-100 kV
Resolution 10 kV
●Single LED display: Preset value of high-voltage.
●Bar graph LED: Set voltage.
2 Illuminated display: Corona or Tribo current
●Lights up green.
Tribo scale:
●When a Tribo gun is connected and selected.
●Bar graph LED: when powder feed is activated.
●Display range: 0-5 µA
Resolution 0.5 µA
Corona scale:
●When a Corona gun is connected and selected.
●Display and adjusting range: 0 [5]-120 µA,
0 [5]-20 µA resolution 5 µA,
20-40 µA resolution 10 µA,
40-120 µA resolution 20 µA.
●Single LED display: Application point of current limiting.
●Bar graph LED: Corona current.
34 36 33
4.4.1 OPERATING ELEMENTS FRONTSIDE
1 2 3 4 20 22 23 18 13 1921
12
8
11
7
10
6
9
25
26
16
17
15
14
5

17
EPG-SPRINT.
OPERATING MANUAL
VERSION 08/2010 ORDER NUMBER DOC 2305222
3 Display: Tribo gun
●Lights up when a Tribo gun is connected and selected.
4 Display: Corona gun
●Lights up when a Corona gun is connected and selected.
5 Push button: Program for surface parts
6 Push button: Program for second-coating
7 Push button: Program for profiles
8 Push button: Program for double clickk
●To access the program, press the trigger lever on the spray gun twice in quick
succession and hold down.
9 Display LED: Program for surface parts
●Lights up green when the surface part program is selected.
10 Display LED: Program for second-coating
●Lights up green when the second-coating program is selected.
11 Display LED: Program for profile parts
●Lights up green when the profile part program is selected.
12 Display LED: Program for double click
●Lights up green, when the double click program is selected.
13 Display LED: Fault
●Lights up, when a malfunction at the unit occurs.
14 Display LED: Automatic gun
●Lights up, when an automatic gun is connected.
15 Push button: Standby
●To switch into standby mode.
●High-voltage and powder feed cannot be activated in standby mode.
●To reactivate normal mode, press the button again.
16 Display LED: Standby
●Lights up when the unit is in standby mode.
17 Push button: Rinse
●To activate the injector and the hose rinsing.
18 Display LED: Rinse
●Lights up blue, when the rinse function is acivated.

18
EPG-SPRINT.
OPERATING MANUAL
VERSION 08/2010 ORDER NUMBER DOC 2305222
19 Display LED: 7 segments, three-digit number
●Indicates the exact value depending on the activated function:
“Overall air quantity; atomizing, ionising and Tribo air; additional recipes;
high-voltage; current limiting; powder quantity“.
●Displaying error number about malfunctions and warnings.
20 Push button: Overall air quantity
●To activate the function, the value is precisely adjusted with the rotary controller 24
and is indicated in the LED display 19.
●Adjusting range: 2-6 m³/h
●Resolution: 0.05 m³/h
21 Push button: Atomizer, ioniser,Tribo air
●To activate the function, the value is precisely adjusted with the rotary controller 24
and is indicated in the LED display 19.
●Adjusting range: 0.1-4 m³/h
●Resolution: 0.05 m³/h
22 Display LED: Overall air
●Lights up yellow, when the setting “Overall air“ is selected.
23 Display LED: Atomizer, ioniser, Tribo air
●Lights up yellow, when the setting “Atomizing, ionising and Tribo air“ is selected.
24 Universal rotary controller
●Dynamic digital rotary controller with 32 positions per revolution.
●Adjustment speed is proportional to rotational speed.
●Used to set: “Overall air quantity; atomizer, ioniser, Tribo air; additional recipes;
high-voltage; current limiting; powder quantity“.
●For setting parameter values in configuration mode.
25 Push button: Additional programs
●To activate the function, the additional program is set with rotary controller 24 and
is indicated in LED display 19.
●Selection of programs 5 to 50.
26 Display LED: Additional programs
●Lights up yellow when an additional program is selected.
27 Push button: High-voltage
●To activate the function, the high-voltage is set with the rotary controller 24 and is
indicated in the LED display 19.
●Adjusting range: 10-100 kV
●Resolution: 1 kV
28 Display LED: High-voltage
●Lights up yellow.The high-voltage is selected and can be adjusted using knob 24.
29 Push button: Current limiting

19
EPG-SPRINT.
OPERATING MANUAL
VERSION 08/2010 ORDER NUMBER DOC 2305222
●To activate the function, the current limiting is set with the rotary controller 24 and
is indicated in the LED display 19.
●Adjusting range: 5-120 µA
●Resolution: 1 µA
30 Display LED: Current limiting
●Lights up yellow. The current limiting is selected and can be adjusted using
knob 24.
31 Push button: Characteristic slope
●To switch the characteristic slope.
●Display with LED 32.
32 Display LED: Characteristic slope
●Lights up green.
●Lower LED characteristic curve, flat.
●Middle LED characteristic curve, medium.
●Upper LED characteristic curve, steep.
33 Illuminated display: Powder quantity
●Lights up green.
●Display range: 0-100%
●Resolution: 3.33%
●Single LED display: Set point (high-voltage and powder are deactivated).
●Bar graph LED: Actual value (high-voltage and powder are activated).
34 Illuminated display: Overall air quantity
●Lights up green.
●Display range: 2-6 m³/h
●Resolution: 0.2-0.5 m³/h
●Single LED display: Set point (high-voltage and powder are deactivated).
●Bar graph LED: Actual value (high-voltage and powder are activated).
35 Illuminated display: Atomizing/ionising/Tribo air quantity
●Lights up green.
●Display range: 0.1-4 m³/h
●Resolution: 0.1-1.0 m³/h
●Single LED display: Set point (high-voltage and powder are deactivated).
●Bar graph LED: Actual value (high-voltage and powder are activated).
36 Push button: Powder quantity
●To activate the function, the high-voltage is set with the rotary controller 24 and is
indicated in the LED display 19.
●Adjusting range: 1-100%
●Resolution: 1%
37 Display LED: Powder quantity
●Lights up yellow, when the powder quantity is selected.

20
EPG-SPRINT.
For operation in Zone 22 all ports
must be fitted with a plug or the
protection cap.
Für den Betrieb in der Zone 22
müssen alle Anschlüsse mit Stecker
oder Schutzkappe versehen sein.
Prim. Fuse
Sicherung
1.0 AT
(slow blow)
Hauptschalter
Main switch
Spraygun
Sprühpistole Remote
Fernsteuerung
Ausgang zur Pistole
Output to gun I max. 0,9 A
U max. 22 Vpp
Dosage air
Dosierluft
Feeding air
Förderluft Atomizing air
Zerstäuberluft
Mains
power
input
Netz-
eingang
Mains
power
output
Netz-
ausgang
Air input
Lufteingang
6.....8 bar
87..116 psi
Do NOT disconnect under tension!
NICHT unter Spannung trennen!
I
OType / Typ:
Serial No.:
Serie Nr.:
Voltage:
Spannung:
Line Power:
Eingangsleistung:
Prot. Class:
Schutzklasse:
EPG-SPRINT
85-250 VAC 47-440 Hz
max. 40 W
IP 64
CH 9450 Altstätten
J. Wagner AG Made in Switzerland
PTB 06 ATEX 5003 1. Ergänzung
Tested / Geprüft EN50050, EN50177
II 3(2)D IP64 80ºC
0102
2 1 10
13 4 3 5 9 8 7 13
611 12
P_01112
14
14
CUS
FM
APPROVED
Overvoltage Category II
and Pollution Degree 2
FM approved for CL II, Div 2 Grps E, F, & G
Power Pack EPG-Sprint FM
P/N 2305127
In accordance with control document:
2309729
OPERATING MANUAL
VERSION 08/2010 ORDER NUMBER DOC 2305222
4.4.2 CONNECTIONS ON THE REAR SIDE OF THE EPG-SPRINT UNIT
1 Mains switch
0 = The control unit is deactivated.
I = The control unit is activated.
2 Primary fuse
●1 ampere slow-acting.
3 Mains power input
●Universal input: 85 VAC-250 VAC
4 Mains power output
●Direct, not through the mains switch.
●To loop the mains through the PrimaTech system.
5 Knurled nut
●To connect the system ground.
6 Compressed air inlet
●Pressure range: 0.6-0.8 MPa; 6-8 bar; 87-116 psi
●Air quantity: max. 15 m³/h
●Connection hose diameter 8 mm; 0.315 inches.
Other manuals for EPG-SPRINT
1
Table of contents
Other WAGNER Control Unit manuals
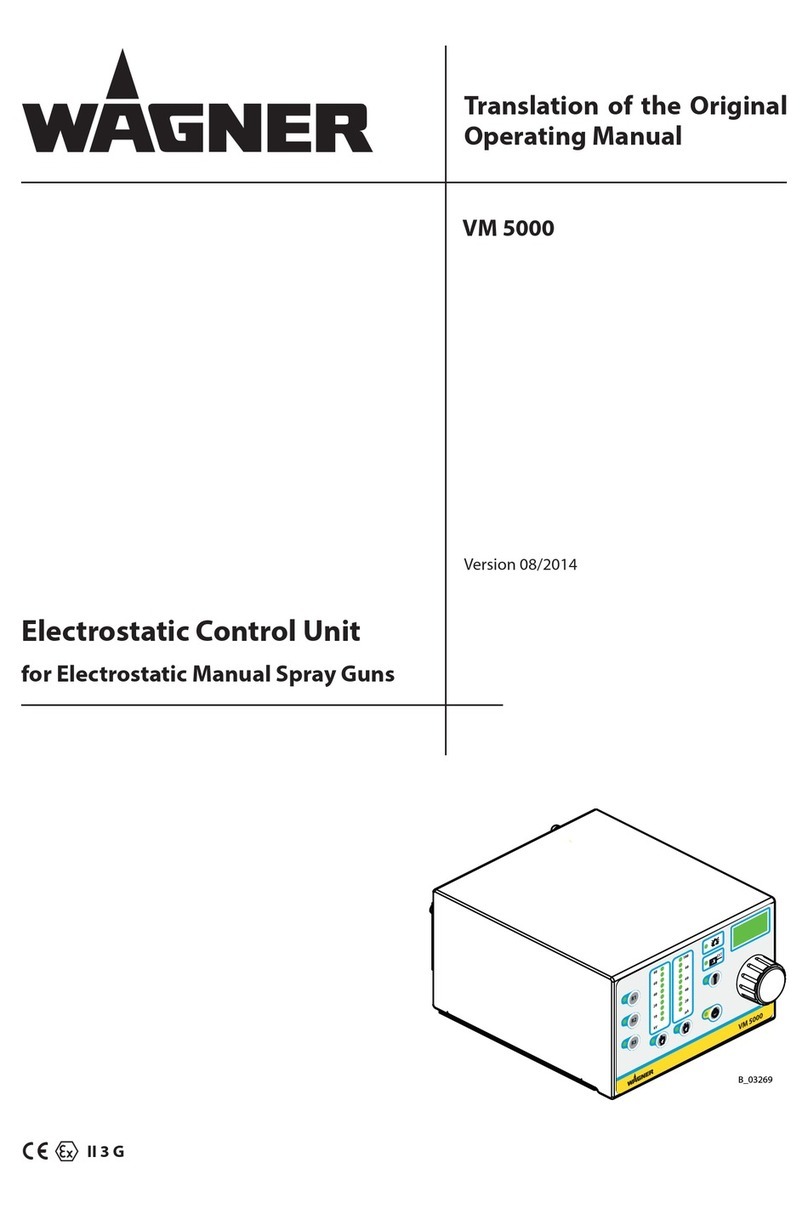
WAGNER
WAGNER VM 5000 User manual
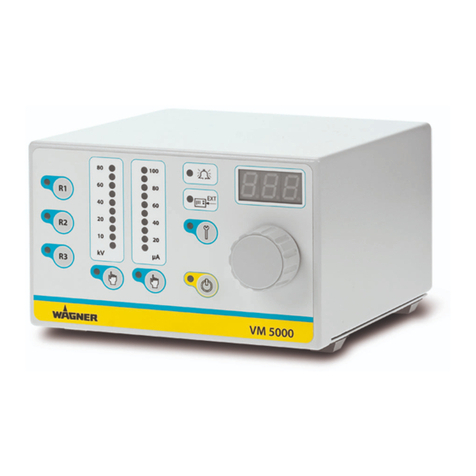
WAGNER
WAGNER VM 5000 Operational manual
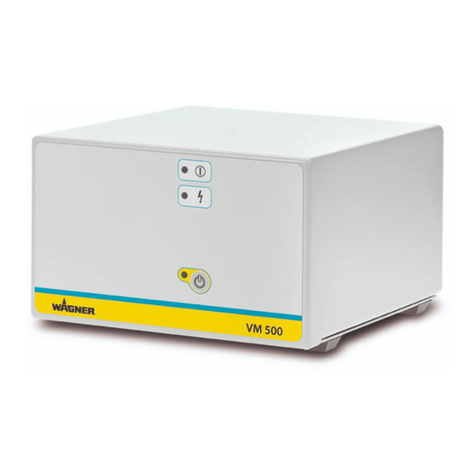
WAGNER
WAGNER VM 500 Operational manual
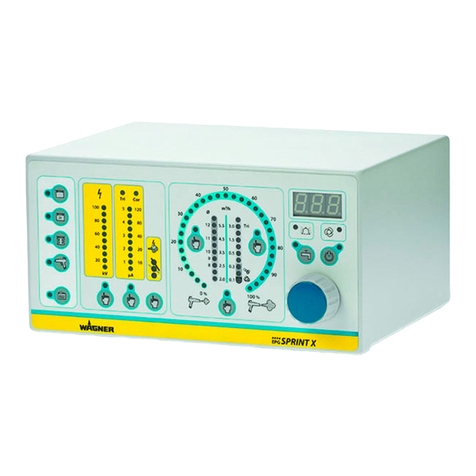
WAGNER
WAGNER EPG-Sprint X User manual

WAGNER
WAGNER EPG-SPRINT XE Operational manual

WAGNER
WAGNER VM 5000 User manual
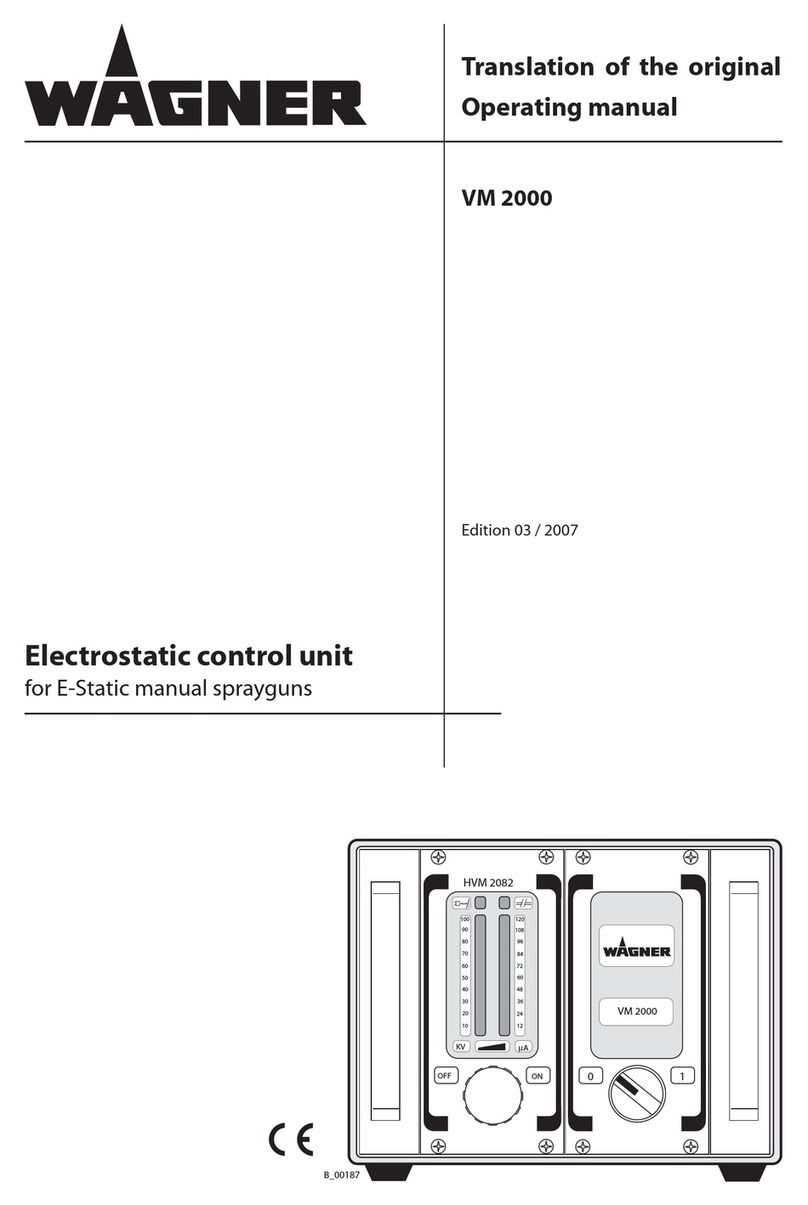
WAGNER
WAGNER VM 2000 Operational manual
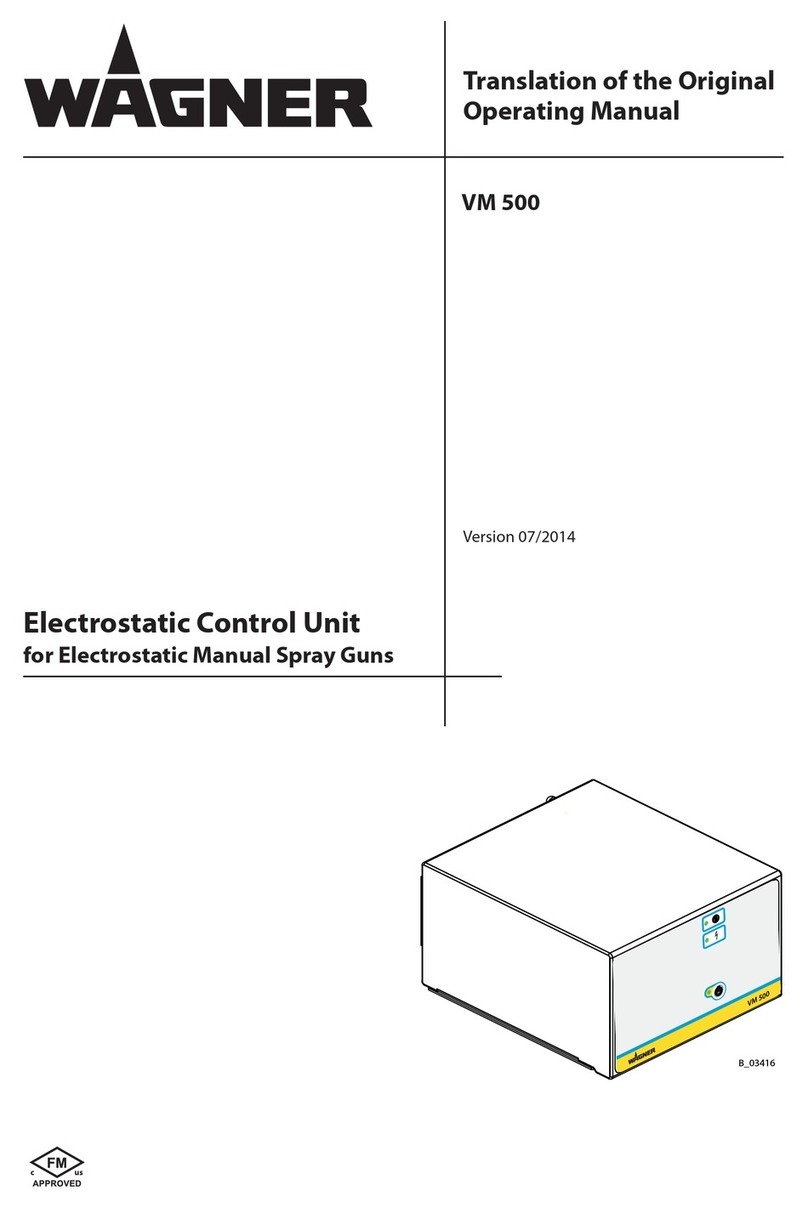
WAGNER
WAGNER VM 500 Operational manual
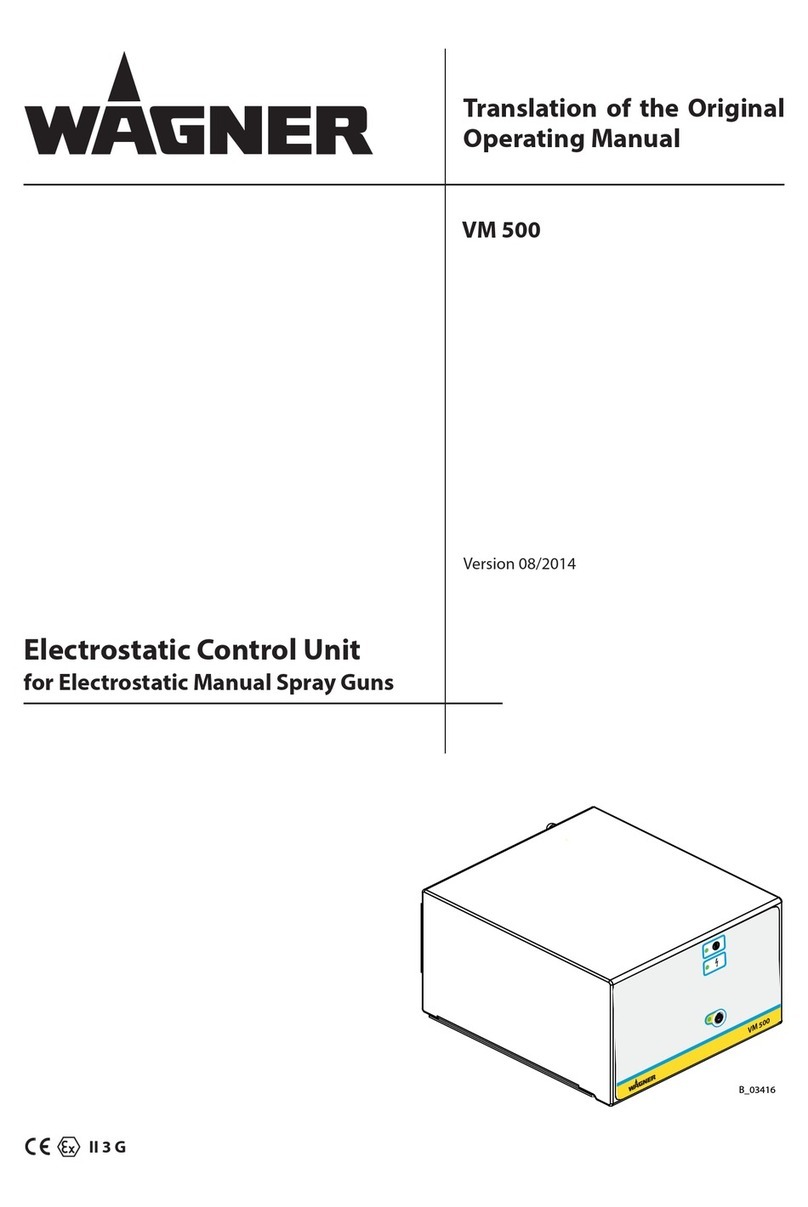
WAGNER
WAGNER VM 500 Operational manual

WAGNER
WAGNER PV 100 Operational manual