White Knight CPC-1 User manual

Manual Version 1.0.1 Manual Part# 18200-LM-0037
CPC-1: Closed Loop Controller Manual
Manual available online at wkfluidhandling.com

Manual version 1.0.1
Manual content and data are subject to change without notification. The most recent version of the manual can be found online at:
http://wkfluidhandling.com/owners-manuals
Page Left Intentionally Blank

Manual Version 1.0.2
Table of Contents
1. System Recommendations .................................................................................................................................2
1.1 Precautions .......................................................................................................................................................2
1.2 System Environment Recommendations/Requirements ..................................................................................2
1.3 Installation Advantages .....................................................................................................................................2
1.4 Getting Started ..................................................................................................................................................3
2. Parts List .............................................................................................................................................................4
2.1 CPC-1 Closed Loop Controller .........................................................................................................................4
2.2 Power Adapter with Crimp Pins ........................................................................................................................5
2.3 Cable: 26 Pin & 44 HD D-Sub to Wire Leads ...................................................................................................5
2.4 Breakout Board: 26 Pin HD D-Sub to Screw Terminals ...................................................................................5
2.5 Din Rail Power Supply ......................................................................................................................................5
2.6 Quick connect boards. Using field wire-able connectors to make connections easier. ....................................5
3. Non-Stock Items Needed....................................................................................................................................6
3.1 I/P Air Regulator ................................................................................................................................................6
3.2 Pressure Transducer ........................................................................................................................................6
3.3 Flow Meter ........................................................................................................................................................6
4 System Overview .....................................................................................................................................................6
5 Setup .......................................................................................................................................................................7
5.1 Plumbing the system .........................................................................................................................................7
5.2 Supply Air Pressure ..........................................................................................................................................7
5.3 Wiring Setup ......................................................................................................................................................7
5.3.1 Powering the CPC-1 ......................................................................................................................................8
5.3.2 Digital Connections ........................................................................................................................................8
5.3.2.1 Power Digital Ports: ....................................................................................................................................8
5.3.2.2 Digital Input Ports ........................................................................................................................................9
5.3.2.3 Digital Output Ports .................................................................................................................................. 10
5.3.3 Analog Connections .................................................................................................................................... 11
5.3.3.1 Common Ground ..................................................................................................................................... 11
5.3.3.2 Supplemental low power supply .............................................................................................................. 12
5.3.3.3 Analog Inputs ........................................................................................................................................... 12
5.3.3.4 Analog Outputs ........................................................................................................................................ 13
5.3.3.5 Wiring Summary ...................................................................................................................................... 13
6 PC to CPC-1 Communication: .............................................................................................................................. 14
6.1 Ethernet Connection: ..................................................................................................................................... 14
6.2 RS-232 Connection: ....................................................................................................................................... 14
7 Desktop Software ................................................................................................................................................. 14
7.1 Installation ...................................................................................................................................................... 14

1 Manual version 1.0.2
7.2 Using the software ......................................................................................................................................... 14
7.2.1 Controls Window ......................................................................................................................................... 15
7.2.1.1 Sensor Gauges ........................................................................................................................................ 15
7.2.1.2 System Alarms ......................................................................................................................................... 16
7.2.1.3 Operation Mode setup ............................................................................................................................. 16
7.2.1.4 Additional Menu Items ............................................................................................................................. 16
7.2.2 Setup Window ............................................................................................................................................. 18
7.2.2.1 Process Settings ...................................................................................................................................... 18
7.2.2.2 Analog I/O Settings .................................................................................................................................. 19
7.2.2.3 Digital I/O Settings ................................................................................................................................... 20
7.2.3 Advanced Window ...................................................................................................................................... 21
7.2.3.1 Terminal Tab ............................................................................................................................................ 21
7.2.3.2 Customize PID Gains Tab ....................................................................................................................... 21
7.2.3.3 Configurations Tab ................................................................................................................................... 22
8 Standalone Operation ........................................................................................................................................... 22
8.1 Using Digital Communication ......................................................................................................................... 23
8.1.1 Operation Mode .......................................................................................................................................... 23
8.1.2 Set Point Modification ................................................................................................................................. 23
8.1.3 Leak Detect Reset ...................................................................................................................................... 23
9 Troubleshooting .................................................................................................................................................... 24
9.1 Issues connecting to CPC-1 via Ethernet, preform the actions below ........................................................... 24
9.2 Issues Connecting to CPC-1 via RS-232, preform the actions below ........................................................... 24
9.3 Issues with Stable Flow ................................................................................................................................. 24
10 Appendix 1: 44 Pin D-Sub Connection Table ..................................................................................................... 26
11 Appendix 2: 26 Pin HD D-Sub Connection Table ............................................................................................... 29
12 Appendix 3: Dimensional Drawings .................................................................................................................... 32
13 Ordering Instructions .......................................................................................................................................... 33

2 Manual version 1.0.2
1. System Recommendations
1.1 Precautions
1.2 System Environment Recommendations/Requirements
1.3 Installation Advantages
DO NOT OPEN CONTROL BOX
Do not open the control box. White Knight is not responsible for any damage caused by opening the
Control Box.
Environmental Temperature
This product is rated to withstand environmental temperatures up to 70°C.
Grounding
All electrical components must be grounded to minimize risk of sparks. Follow proper procedures for
grounding all products in the system.
Flow and Pressure Monitoring
The CPC-1 is able to take in both a pressure transducer and flow meter signals at the same time. While
only one is needed for the desired control process, the other can be input for monitoring and
troubleshooting purposes.
Non-stock Items Needed
The Closed Loop Control system makes use of several off the shelf items that White Knight does not
supply. There is a large variety of products and suppliers and the end user may obtain their preferred
product. See section 3 of this manual for detailed descriptions of needed parts.
System Limitations
The CPC controls the parameters of the system based off of the selected pump and would not protect
system components that are not rated as high as the pump the controller is programmed to control.
Flow and Pressure
White Knight recommends the installation of a pressure transducer as well as a flow meter to allow for
increased monitoring as well as the ability to switch between flow and pressure control within a system
without any addition or change to system components.

3 Manual version 1.0.2
1.4 Getting Started
Installing the CPC-1 for the first time it is recommended that you follow these steps:
1) Verify that you received all of the components that you ordered. Note: cables and breakout board for the
controller are options that can be selected at the time of purchase.
2) Check that you have a compatible power supply to power the controller. See Section 5.3.1
3) Check that you have a compatible communication cable for setting up the controller. See Section 6
4) Download the setup software from www.wkfluidhandling.com/cpc-1.
5) Verify that your computer is able to connect to the controller.
a) Power up the controller with correct power source
b) Connect the communication cable correctly. (Ethernet cables should go from the controller to a network
switch, not your PC)
c) Install and launch the Smart Control Software.
d) The connections dialog should appear at launch. Verify that your controller appears on the list and click
the connect button. See Section 7.2
e) Once connectivity is verified disconnect from the software, and disconnect power and communication
cable.
6) Install CPC-1 in the desired location.
7) Connect 44 pin and 26 pin connectors and use the wiring guide in Section 5.3.2 and 5.3.3 to connect system.
8) Connect to controller (same as before) and configure the CPC-1 settings to match your system needs.

4 Manual version 1.0.2
2. Parts List
#
Description
Part Number
Component
2.1
Control Box
CPC-1
Standard
Power Adapter With Crimp Pins
Standard
2.4
44 Pin HD D-Sub to Screw Terminals
8600-XX-0018
Optional
2.3
44 Pin HD D-Sub to wire leads Cable 1-Meter
8600-XX-0013
Optional
2.4
26 Pin HD D-Sub to Screw Terminals
8600-XX-0019
Optional
2.3
26 Pin HD D-Sub to wire leads Cable 1-Meter
8600-XX-0014
Optional
2.5
24 Volt Power Supply - 60 Watt
8600-XX-0015
Optional
* For size of items in parts list see section 12
2.1 CPC-1 Closed Loop Controller
The CPC-1 control box is a small I/O communication device that controls the supply air pressure to the pump in
order to maintain either flow or pressure changes. The control box has:
• 44-pin HD D-Sub Connector: Sends and receives digital signals.
• Indicator Lights: Show when each digital signal is active.
• 26-pin HD D-Sub Connector: Sends and receives analog signals.
• Power Port: Takes 18-36 VDC input to power the controller.
• Ethernet Connector: Can be used by the setup software to configure the controller.
• RS 232 serial communication: Can be used by the setup software to configure the controller.
Figure 1 shows an image of the CPC-1 controller. Note: the production version will come with a din rail mount,
where the beta version does not.
Power port
Ethernet
Indicator Lights
44-Pin Connector for
Digital Communications
26-Pin Connector for
Analog Communications
RS-232 Serial Port
Figure 1: The CPC-1 Controller and its communication ports.

5 Manual version 1.0.2
2.6 Quick connect boards. Using field wire-able connectors to make connections easier.
2.2 Power Adapter with Crimp Pins
2.3 Cable: 26 Pin & 44 HD D-Sub to
Wire Leads
2.4 Breakout Board: 26 Pin HD D-Sub
to Screw Terminals
2.5 Din Rail Power Supply
Analog Output Connectors:
•Pin 1: 24 VDC Power
•Pin 2: Ground
•Pin 3: Voltage Output
•Pin 4: Voltage Reference
•Pin 5: Current Output
•Pin 6: Current Reference
Analog Input Connectors:
•Pin 1: 24 VDC Power
•Pin 2: Ground
•Pin 3: Analog Input
•Pin 4: Voltage Reference
•Pin 5 & 6: If Input is a
current input jumper two
pins together.
Note: Temp Connector has
different pinouts.
Power Connectors:
•Pin 1: Ground
•Pin 2: 24 VDC Power

6 Manual version 1.0.2
3. Non-Stock Items Needed
The Closed Loop Control system makes use of several off the shelf items that White Knight does not supply.
There is a large variety of products and suppliers so the end user may obtain their preferred products. Below is a
brief description of these components and the CPC-1 interface requirements.
3.1 I/P Air Regulator
An electronic proportional air regulator is required for the closed loop control system. Minimum specifications for
I/P air regulator are:
• Supports a pressure range from 0 to 100 PSI.
• Supports air flow requirement for selected WK pump. (See pump’s manual)
• Ability to set pressure using analog signal*.
* The CPC-1 only supports analog voltage analog outputs (0-5 VDC, 0-10 VDC), if an analog current signal (0-20
mA or 4-20mA) is required then the 4-20 mA Expansion Board or a signal conditioner is required.
3.2 Pressure Transducer
A pressure transducer is only required for systems in which pressure control is desired. However, for systems that
are using flow control a pressure transducer can be added into the system for system monitoring. The minimum
specifications for the pressure transducer are:
• Support the full range of system pressures up to 100 PSI
• Output pressure reading via analog signal*
* If the pressure transducer outputs an analog current signal then a 500 ohms resistor or smaller can be
connected between the signal and ground connections to convert the signal to a voltage signal. (The 4-
20 mA Analog Expansion Board will already have a 250 ohm resistor correctly placed for this conversion)
3.3 Flow Meter
A flow meter is only required for systems in which flow control is desired. However, for systems that are using
pressure control a flow meter can be added into the system for system monitoring. The minimum specifications
for the flow meter are:
• Support the full range of system flows.
• Output flow reading via analog signal*
* If the flow meter outputs an analog current signal then a 500 ohms resistor or smaller can be connected
between the signal and ground connections to convert the signal to a voltage signal. (The 4-20 mA
Analog Expansion Board will already have a 250 ohm resistor correctly placed for this conversion)
4 System Overview
Closed loop control is a self-monitoring system that will maintain one process variable independent of changes in
the system. The CPC-1 closed loop controller has two different control modes:
Pressure Control – Uses feedback from a pressure transducer to maintain a set line pressure at a
desired point in the system. Pressure transducers are able to detect small changes in the system with little to no
time delay. Thus a pressure controlled system is more responsive to changes in the system, such as a point of
use with multiple valves that open and close frequently. A pressure control system can also be used to maintain
flow in the system where a fixed pressure through a fixed orifice can result in a steady flow.
Flow Control – Uses feedback from a flow meter to maintain a desired flow rate in the system. Flow
meters generally use a rolling average to detect flow in the system, which results in a less responsive sensor.

7 Manual version 1.0.2
Thus a flow controlled system is slow to respond to changes in the system. Flow control processes are frequently
used in plating or mixing operations where the flow doesn’t change, but where the filter may clog over time. The
flow control will slowly adjust the pressure as flow restrictions build up in a filter. Using flow control can lengthen
the usable life of a filter because the control will maintain the correct flow.
The CPC-1 is able to take in both a pressure transducer and flow meter signals at the same time. While only one
is needed for the desired control process, the other can be input for monitoring and troubleshooting purposes.
Note: White Knight does not supply pressure transducers or flow meters. See Non-Stock Items Needed for more
information about selecting a pressure transducer and flow meter.
5 Setup
5.1 Plumbing the system
Assemble the system plumbing as normal and include the correct sensors that are required for the closed loop
control process; a pressure transducer for pressure controlled systems or a flow meter for flow controlled
processes. These sensors should be placed in the critical path close to the point of use. In some cases it may be
advantageous to add both sensors into the system; this will allow additional flexibility for implementing closed loop
control allowing the end operator to monitor both sensors, and have the ability to switch control methods.
5.2 Supply Air Pressure
The supply air going into the closed loop control system should be set to 100 PSI. The supply air is then directed
into the air regulator. The air regulator controls how much air is supplied to the pump and pulse dampener. See
Figure 2 for illustration of the air flow.
5.3 Wiring Setup
The CPC-1 has the following on device connections interfaces:
Fluid to
Pump
PLC
Commands
Pressure
Transducer
Air
Regulator
Pulse
Dampener
WK Pump
Supply Air
Fluid to
System
Flow
Meter
CPC-1
Analog Flow Signal
Analog Pressure Signal
Figure 2: Control Process diagram where elements shown in green can be obtained from a
third-party distributer. Note: Depending on which model of I/P Air regulator is selected they
may be two separate components or they may be one consolidated unit.

8 Manual version 1.0.2
• 18-36 VDC Power Connector
• Ethernet/PoE Connection
• Serial to RS-232 connection
• 44 Pin HD D-Sub connection for Digital Communications
• 26 Pin HD D-Sub connection for Analog Communications
5.3.1 Powering the CPC-1
There are two methods of powering the CPC-1: 18-36 VDC power connector and Power over Ethernet, PoE. By
default the CPC-1 is setup to use the external power adapter. Simply connect an appropriate DC power to the
connector as shown in Figure 3.
To setup PoE find the jumpers on the bottom face of the controller that are labeled EXT and PoE, see Figure 4.
Move the jumpers from EXT to PoE locations. Now the Power over Ethernet connection can be used.
5.3.2 Digital Connections
5.3.2.1 Power Digital Ports:
The digital ports are not powered by the controller. An external power supply is required in order for the digital
ports to be active. Use Table 1 for digital port power connections.
Pin Name
Pin #
Wire Color
Designation
Levels
Notes
Power:
Source
Outputs
15
Red/
Black Stripe
Power Source
12-24 VDC
The voltage input into these pins power
all of the source type outputs.
* The voltage input will equal the voltage
output from these ports.
27
Red/
White Stripe
Ground Reference
0 VDC
Power:
Sink Outputs
8
Green
Power Source
12-24 VDC
The voltage input into these pins will
power the sink type outputs.
11
Orange
Ground Reference
0 VDC
Figure 3: External Power Connector
Figure 4: External power / Power over Ethernet Selection jumpers.
PoE EXT
Default setup supporting external power shown.
Table 1: Wire connections for powering the digital ports. All ports
should be connected.

9 Manual version 1.0.2
5.3.2.2 Digital Input Ports
Digital inputs by default are set to receive signals from a high voltage reference connection. However each digital
input can be configured to receive the signal from the low voltage reference. To configure high or low voltage
reference ports use the desktop software.
Pin Name
Pin #
Wire Color
Designation
Levels
Notes
Digital Input:
Line Pressure
Control
On/Off
[DI_0]
7
Brown
Reference High VDC
24 V = Not Active, Off
0 V = Active, On
These Three digital inputs
control how the controller
will operate. In the case
that multiple signals are
received by the controller,
then the system will chose
the operations mode in
the following priority:
1. Line Pressure Control
2. Flow Rate Control
3. Supply Pressure Control
The priority system allows
the user to setup a
Pressure or Flow control
operation during active
process, and a basic supply
pressure control to
operate when the system
is inactive to keep the fluid
moving.
33
Light Green/
Red Stripe
Reference Low VDC
0 V = Not Active, Off
24 V = Active, On
Digital Input:
Flow Rate Control
On/Off
[DI_1]
22
Gray/
Black Stripe
Reference High VDC
24 V = Not Active, Off
0 V = Active, On
3
Red
Reference Low VDC
0 V = Not Active, Off
24 V = Active, On
Digital Input:
Supply Pressure
Control
On/Off
[DI_2]
36
Yellow/
Red Stripe
Reference High VDC
24 V = Not Active, Off
0 V = Active, On
18
Green/
Black Stripe
Reference Low VDC
0 V = Not Active, Off
24 V = Active, On
Digital Input:
Analog Set Point
On/Off
[DI_3]
6
Blue
Reference High VDC
24 V = Not Active
0 V = Active
The set point for each
operation mode can be set
though the set point
analog port. This digital
input tells the controller to
use the analog port to as
the set point for the active
control mode.
32
Gray/
Red Stripe
Reference Low VDC
0 V = Not Active
24 V = Active
Digital Input:
Reset Leak Alarm
[DI_4]
21
Brown/
Black Stripe
Reference High VDC
24 V = Not Active
0 V = Active
Once a leak has been
detected by the system,
the controller will shut off
the pump. This digital port
is used to deactivate the
leak alarm so that normal
pump operation can
continue.
2
White
Reference Low VDC
0 V = Not Active
24 V = Active
Power:
Input High
37
Violet/
Red Stripe
Reference Voltage High
12-24 VDC
The Voltage input into this pin will be the
reference for all digital high inputs.
Power:
Input Low
19
Orange/
Black Stripe
Reference Voltage Low
0 VDC
The Voltage input into this pin will be the
reference for all digital low inputs.
Table 2: Digital Input Connection Table, Continued on next page

10 Manual version 1.0.2
Pin Name
Pin #
Wire Color
Designation
Levels
Notes
Digital Input:
Leak Detect Input
[DI_5]
35
Pink/
Red Stripe
Reference High VDC
24 V = Not Active
0 V = Active
Send leak detect inputs
into this digital port
17
Violet/
Black Stripe
Reference Low VDC
0 V = Not Active
24 V = Active
Digital Input:
Left Proximity
Sensor/ Counter
[DI_6]
5
Violet
Reference High VDC
24 V = Not Active
0 V = Active
If operating a pump with
end stroke detection
instead of a shuttle
operated pump the left
and right proximity sensor
inputs need to be
connected to these digital
ports. The left proximity
switch input will be used
to count cycles.
For those using a shuttle
pump and want the
controller to preform cycle
counting, then a pressure
switch can be connected
to the pump. See pump's
owner’s manual for
details.
31
Blue/
White
Stripe
Reference Low VDC
0 V = Not Active
24 V = Active
Digital Input:
Right Proximity
Sensor
[DI_7]
20
Blue/
Black Stripe
Reference High VDC
24 V = Not Active
0 V = Active
1
Black
Reference Low VDC
0 V = Not Active
24 V = Active
5.3.2.3 Digital Output Ports
The CPC-1 is able to send out digital communication to other devices. There are two types of digital outputs:
voltage sink and voltage source. By default the voltage source outputs are active. Each digital communication can
be configured to the voltage sink output using the desktop software.
Pin Name
Pin #
Wire Color
Designation
Levels
Notes
Digital Output:
Line Pressure
Control Status
[DO_0]
26
Orange/
White Stripe
Sink: Connect To
ground when closed
Relay Open = Not Active
Relay Closed = Active
These digital outputs have
been designated to notify
the user which mode the
controller is operating in.
If none are on, then the
controller has been
turned off.
44
Light Green/
Green Stripe
Source: Connect to
power when closed
Relay Open = Not Active
Relay Closed = Active
Digital Output:
Flow Rate
Control Status
[DO_1]
40
Red/
Green Stripe
Sink: Connect To
ground when closed
Relay Open = Not Active
Relay Closed = Active
14
White/
Black Stripe
Source: Connect to
power when closed
Relay Open = Not Active
Relay Closed = Active
Digital Output:
Supply
Pressure
Status
[DO_2]
10
Light Blue
Sink: Connect To
ground when closed
Relay Open = Not Active
Relay Closed = Active
29
Brown/
White Stripe
Source: Connect to
power when closed
Relay Open = Not Active
Relay Closed = Active
Digital Output:
Leak Alarm
[DO_3]
25
Pink/
Black Stripe
Sink: Connect To
ground when closed
Relay Open = Not Active
Relay Closed = Active
This output is to notify
the user that a leak has
been detected.
43
Light Blue/
Green Stripe
Source: Connect to
power when closed
Relay Open = Not Active
Relay Closed = Active
Table 3: Digital Output Communications Table, Continued on next page

11 Manual version 1.0.2
Pin Name
Pin #
Wire Color
Designation
Levels
Notes
Digital Output:
Control Limit
Alarm
[DO_4]
39
Orange/
Green Stripe
Sink: Connect To
ground when closed
Relay Open = Not Active
Relay Closed = Active
This alarm is to indicate to
the user when the system
is operating outside of the
defined control limits.
13
Pink
Source: Connect to
power when closed
Relay Open = Not Active
Relay Closed = Active
Digital Output:
System Limit
Alarm
[DO_5]
9
Gray
Sink: Connect To
ground when closed
Relay Open = Not Active
Relay Closed = Active
This alarm is to notify the
user that the system is
operating near the
maximum capacity of the
system. This often occurs
when the system has an
obstruction that has built
up over time.
28
Violet/
White Stripe
Source: Connect to
power when closed
Relay Open = Not Active
Relay Closed = Active
Digital Output:
Left Solenoid
Valve
[DO_6]
39
Orange/
Green Stripe
Sink: Connect To
ground when closed
Relay Open = Not Active
Relay Closed = Active
These outputs are
designated to operate a
pump with end stroke
detection. Each digital
port will open an air valve
that will shift the air in
the pump.
13
Pink
Source: Connect to
power when closed
Relay Open = Not Active
Relay Closed = Active
Digital Output:
Right Solenoid
Valve
[DO_7]
9
Gray
Sink: Connect To
ground when closed
Relay Open = Not Active
Relay Closed = Active
28
Violet/
White stripe
Source: Connect to
power when closed
Relay Open = Not Active
Relay Closed = Active
5.3.3 Analog Connections
Each analog connection is configurable 0-10 VDC Input/output. To configure the analog ports to the specific
application use the desktop software.
5.3.3.1 Common Ground
The CPC-1 uses one common ground for all analog signals. Connect one of the common ground connections to
the system’s common ground, and then the others can be used as grounds for external devices.
Pin Name
Pin #
Wire Color
Designation
Default Setup
Note
Reference:
Common Ground
15
Red/
Black Stripe
Ground
0 VDC
These connections are
for referencing a
common ground. At
least one should be
connected to your
system's common
ground. And the others
can be used for your
sensors.
Reference:
Common Ground
12
Light Green
Ground
0 VDC
Reference:
Common Ground
9
Gray
Ground
0 VDC
Reference:
Common Ground
6
Blue
Ground
0 VDC
Table 4: Table of ground references for analog signals

12 Manual version 1.0.2
5.3.3.2 Supplemental low power supply
Some sensors will need a 12 VDC power that may not be available on the existing equipment. A 12VDC power
supply is available for purchase from White Knight.
Pin Name
Pin #
Wire Color
Designation
Default Setup
Note
Power Output:
+12 VDC
2
White
Power source
12 VDC
These are low current
power supplies that can
be used to power
sensors if necessary.
Power Output:
-12 VDC
20
Blue/
Black Stripe
Power Source
- 12 VDC
5.3.3.3 Analog Inputs
All analog inputs are expecting a 0-10 VDC signal. Using the desktop software these ports can be configured for
one of three different configurations: 0-5 VDC, 0-10 VDC, or 4-20 mA with a resistor bridging the signal and
common ground. 4 - 500 ohm resistors have been included with the beta order for the purpose of converting 4-20
mA signals to voltage signals.
Pin Name
Pin #
Wire Color
Designation
Default Setup
Note
Analog Input:
Flow Meter Signal
[AI_0]
23
Light Blue/
Black Stripe
Customizable
0-10 VDC Input
0..10 VDC = 0..100%
Analog input for flow
control mode process
variable.
Analog Input:
Pressure
Transducer Signal
[AI_2]
14
White/
Black Stripe
Customizable
0-10 VDC Input
0..10 VDC = 0..100%
Analog input for
pressure control
mode process
variable.
Analog Input:
Set Point Signal
[AI_3]
22
Gray/
Black Stripe
Customizable
0-10 VDC Input
0..10 VDC = 0..100%
Analog input for
setting process
Analog Input:
Temperature Signal
[AI_1]
5
Violet
Customizable
0-10 VDC Input
0..10 VDC = 0..100%
Analog input for
temperature sensor.
Table 5: Table of analog input values used

13 Manual version 1.0.2
5.3.3.4 Analog Outputs
All analog outputs have been configured to 0-10 VDC outputs. These outputs can be configured to a 0-5 VDC or
0-10 VDC using the desktop software. If a 4-20 mA output is required then an external signal conditioner will be
required (not supplied by White Knight).
Pin Name
Pin #
Wire Color
Designation
Default Setup
Note
Analog Output:
Flow Rate Signal
[AO_0]
18
Green/
Black Stripe
Customizable
0-10 VDC Output
0..10 VDC = 0..100%
These analog outputs
echo out the current
value of each sensor. In
the configured output
signal condition.
Analog Output:
Temperature Signal
[AO_1]
26
Blue/
White Stripe
Customizable
0-10 VDC Output
0..10 VDC = 0..100%
Analog Output:
Pressure Signal
[AO_2]
8
Green
Customizable
0-10 VDC Output
0..10 VDC = 0..100%
Analog Output:
Air Regulator Signal
[AO_3]
17
Violet/
Black Stripe
Customizable
0-10 VDC Output
0..10 VDC = 0..100%
This signal is to be sent
to the air regulator that
is to maintain the
process.
5.3.3.5 Wiring Summary
Table 6: I/O vs. CPC-1 Function Wiring requirements

14 Manual version 1.0.2
6 PC to CPC-1 Communication:
6.1 Ethernet Connection:
The Ethernet connection is available for PC to CPC-1 communications. These communications are available for
setting up the software, and for on screen controls. After the controller has been setup the settings can be saved
and disconnected to be run as a standalone unit. The CPC-1 uses two industry standard Ethernet connection
protocols TCP/IP and UDP/IP, the controller will automatically respond in the format in which it is connected.
When connecting to the WK Controller to a local network. The WK Controller will look to the server to assign it an
IP address; this is supported on both DHCP and BOOT-P server protocols.
6.2 RS-232 Connection:
An RS-232 connection can be created through the 9 pin serial port on the box. When opening the software the
RS-232 port will show as a COM port and will give two baud rate options, 19200 and 115000. The default baud
rate is 115000, however the slower 19200 baud rate can be selected by placing a jumper on the connection
labeled 19.2 on the upper left side of the control box.
7 Desktop Software
7.1 Installation
Download the WK Smart Control installation software from www.wkfluidhandling.com/cpc-1. Run the installation
software by double clicking on the executable, and follow the on screen prompts. Software requires windows XP
or newer version of windows.
7.2 Using the software
1. Open “WK Smart Control” software.
2. Wait for connections window to appear, See Figure 5 for a screen shot of the connections window.
Figure 5: Image of Connections Window with examples of appearance
CPC-1 Connected via Ethernet
CPC-1 Connected via RS-232

15 Manual version 1.0.2
3. Select the CPC-1 from the list (if the controller does not show up, then check that the controller is connected
to the correct network. See trouble shooting section for more details. Click cancel and on the controls screen
click connect to try connecting again) Note: all active comports will show up in the connections. If connecting
via serial port you may want to open the device manager to determine which com port relates to the CPC-
1
4. After you have connected to the CPC-1 then the controls window will appear, See Figure 6.
7.2.1 Controls Window
The controls window is the main window for the smart control interface. This window shows the current readings
from the sensors, the system alarm notifications, the mode controls with set point adjuster, and the main menu.
7.2.1.1 Sensor Gauges
Each sensor gauge displays the current value for that sensor as seen by the controller. The gauge limits are set in
the setup window when specifying the analog I/O. Each gauge has a black pointer showing the current value for
that sensor, and a small gray marker, that shows what the current set point for the operation mode. Note: When
no sensor is connected, then the pointer will stay at a position about 25% of the maximum value.
Figure 6: Controls window, showing sensor dials, alarms and process control modes.

16 Manual version 1.0.2
7.2.1.2 System Alarms
There are four system alarms available through the smart control interface:
• Control Limit - Shows when the system is operating outside of the set process control limits defined by
the user.
• System Limit – Shows when the system is operating near maximum capacity. The point threshold for this
alarm is defined by the user.
• Maintenance Alarm – Shows when the pump has reached its maintenance limit set by the user. In order
for this alarm to function an end of cycle signal needs to be sent to the controller, such as a pressure switch.
Note: This alarm is available currently only through the software interface.
• Leak Detect – Shows when a leak has been detected by the system. The pump will be stopped by the
controller, and will not restart until the leak reset button is pressed (see section 8.1.3).
7.2.1.3 Operation Mode setup
There are three controls for the operation mode; each has a specific roll to play in setting up the control mode.
• Input Method Switch – This switch enables the user to change where the controller looks to receive
operation mode settings.
o On Screen Controls – When the “on screen controls” option is enabled, then the controller will
look for operation mode controls from the software interface.
o Digital I/O – When the digital I/O is enabled, than the controller will look to the digital inputs to
receive its operation mode settings.
• Operation Mode Dial – Operation mode sets how the controller will operate. This dial will only be
operational if a controller is connected and if the on screen controls are enabled.
o Flow Control – Uses the flow meter as the control variable for the system. The user will need to
specify the desired set point for flow control operation. The system will vary the supply pressure to
maintain the desired average flow rate.
o Pressure Control – Uses the pressure transducer as the control variable for the system. The user
will need to specify the desired set point for the flow control operation. The controller will vary the
supply pressure to maintain the desired average flow rate.
o Supply Air Control – This enables an uncontrolled system process to be used. This is specifically
helpful when testing a system for leaks, or can also be used for recirculation routines.
o Off – When the controller is not to send any air pressure to the pump
• Set Point Dial – The set point dial is used to modify the set point for each operation mode. The dial limits
will automatically be adjusted to the process variable’s limits.
7.2.1.4 Additional Menu Items
From the controls window there are additional controls available.
• Connect – Quickly connect when no controller is connected, just select the connect button, and the
connection screen will appear.
• Disconnect – Quickly disconnect from the current controller. (note: before disconnecting the user should
save the current setting if critical changes were made.)
• Save – This will save the current settings to the device’s nonvolatile memory, which gets loaded when a
power cycle occurs.
• Setup – This brings up the setup window which enables the user to specify process, analog I/O, and Digital
I/O settings. See section 5 for more details.
• Maintenance – This brings up the maintenance window with allows the user to view the current cycle count,
cycle rate, and maintenance limits. The user can also modify the maintenance limits.
• Graph – This brings up the time lapse graph for the end user to view the current process values as they
occur.

17 Manual version 1.0.2
• Stepper Demo – This brings up a specialized window that was created for testing stepper valves, but can
also be used to send a 0-5 analog signal to two other connected devices.
• Advanced – This brings up the advanced window which enables the user to modify the PID settings in the
controller to get the optimal response for their system. This interface also gives technicians the ability to
send messages directly to the controller using the terminal.
• Modify IP Address – This brings up an option to modify the IP Address settings for the CPC-1. The CPC-
1 Can be configured to have a fixed IP Address specified by the user, or the IP Address can be left open
to be set by the DHCP Network.
• Update Controller Firmware – In cases where the controller’s version does not match the desktop
software’s version then a controller update may be necessary. The update controller firmware feature will
install the controller firmware that matches the software version.
Table of contents
Popular Controllers manuals by other brands
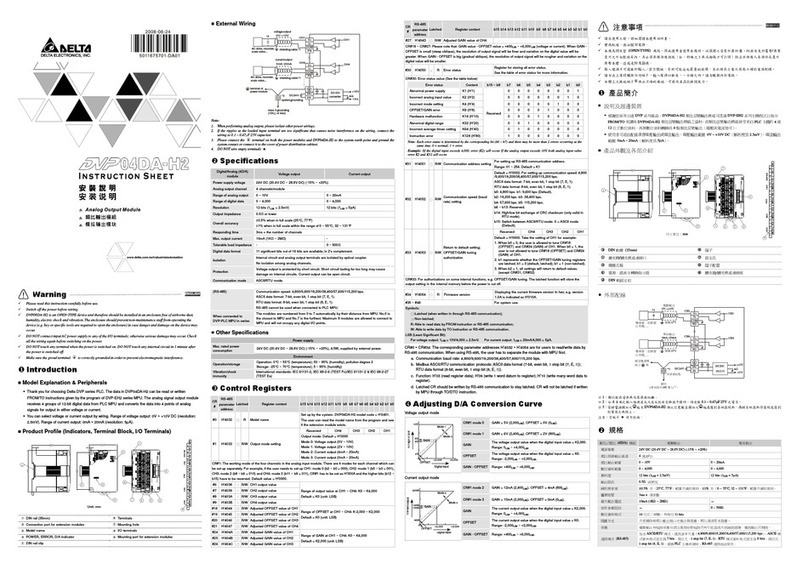
Delta Electronics
Delta Electronics Programmable Logic Controller DVP04DA-H2 instruction sheet
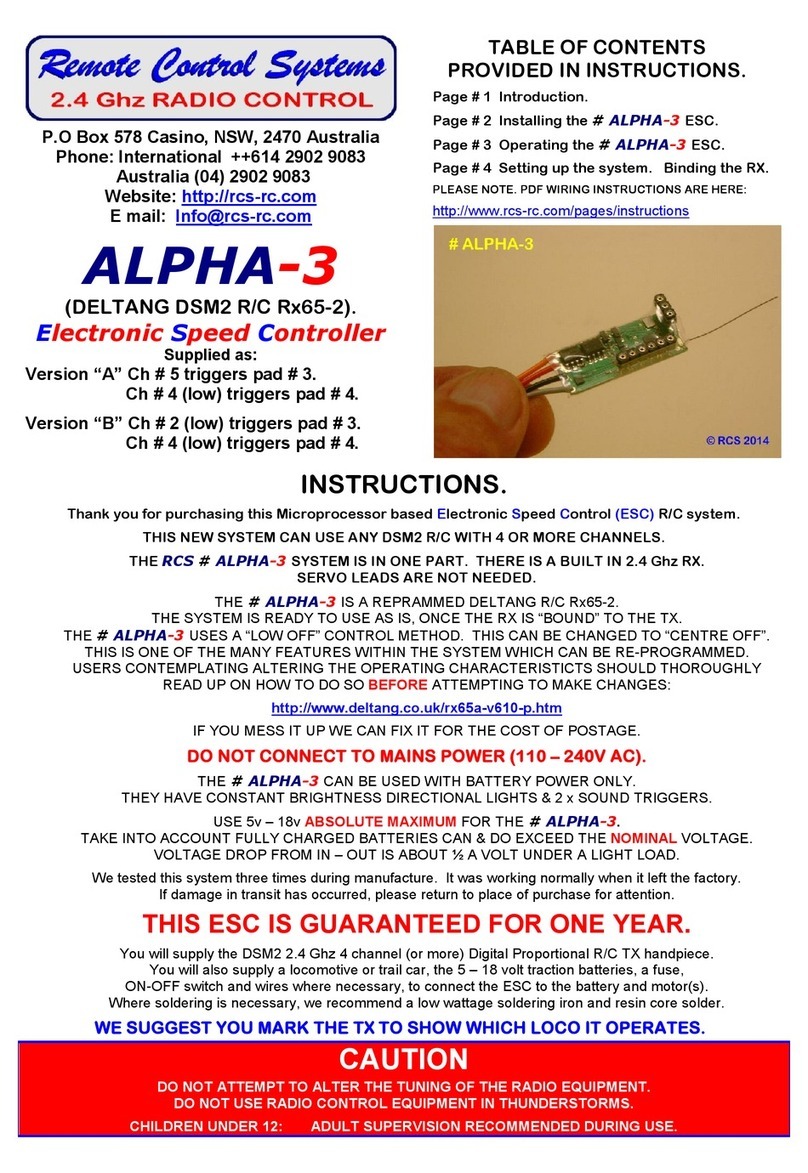
Remote Control Systems
Remote Control Systems ALPHA-3 instructions
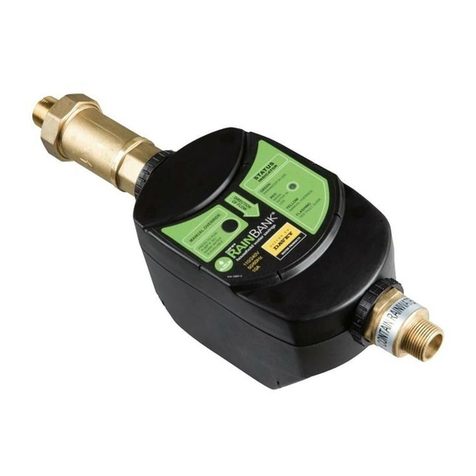
Davey
Davey RainBank KRBS1 installation instructions
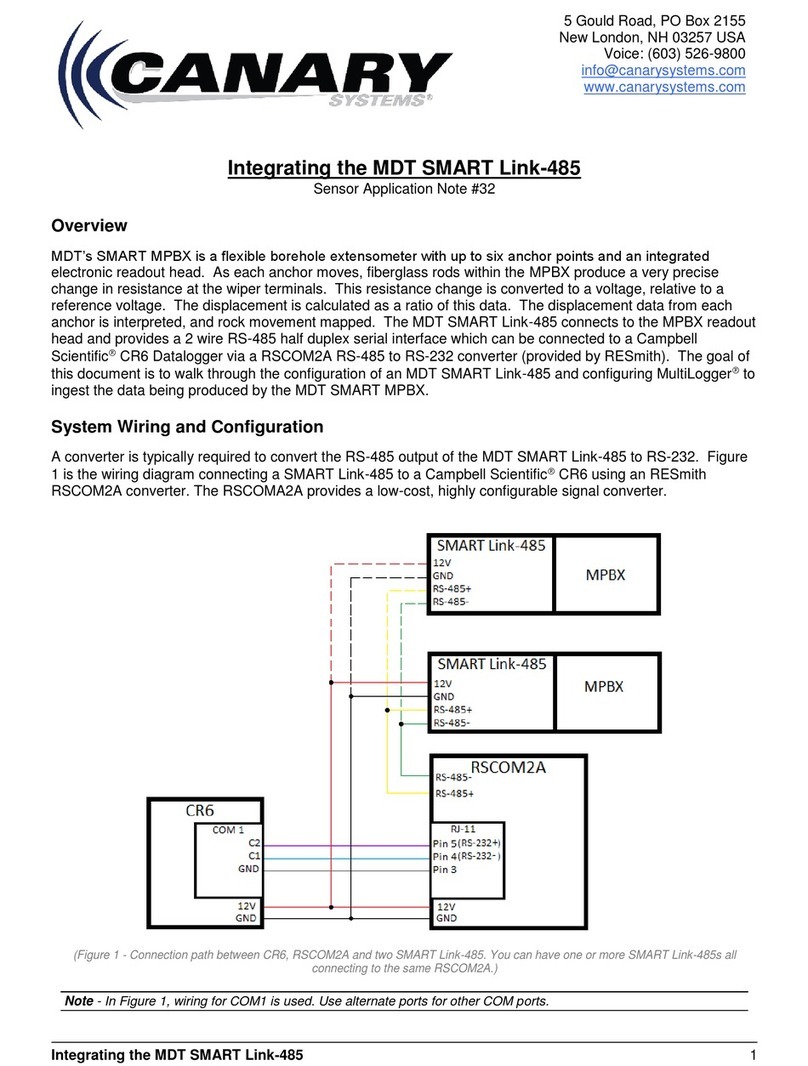
Canary Systems
Canary Systems MDT SMART Link-485 manual
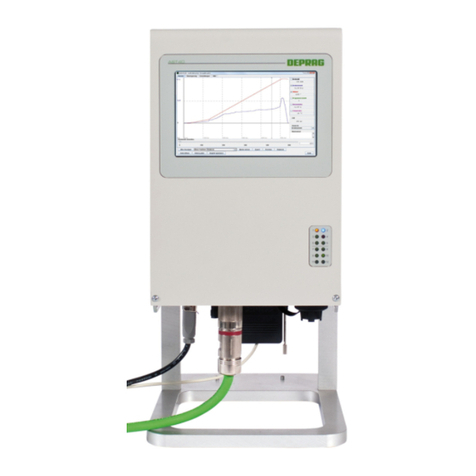
Deprag
Deprag AST40-1 Operating instruction booklet
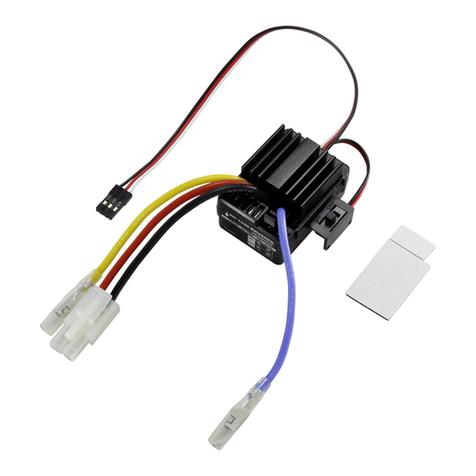
Reely
Reely WP40 manual
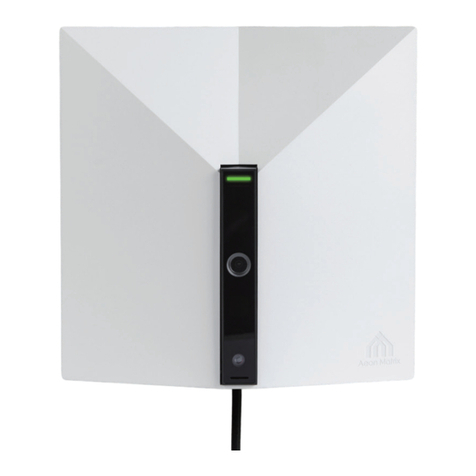
Yardian
Yardian Pro user guide
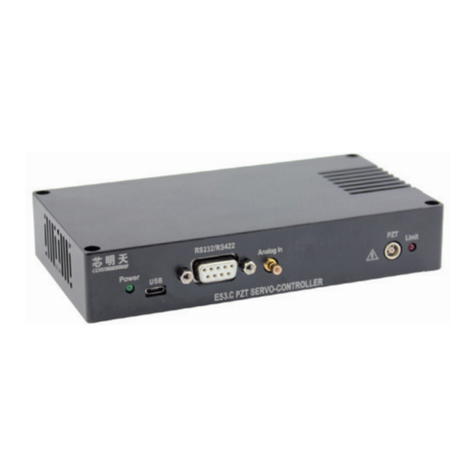
Coremorrow
Coremorrow E53.C Series user manual
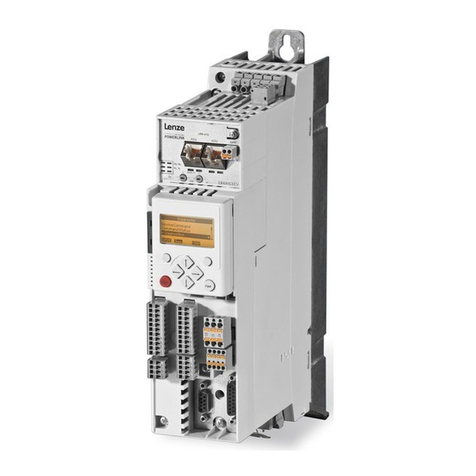
Lenze
Lenze L-force HighLine C 8400 Series Reference manual
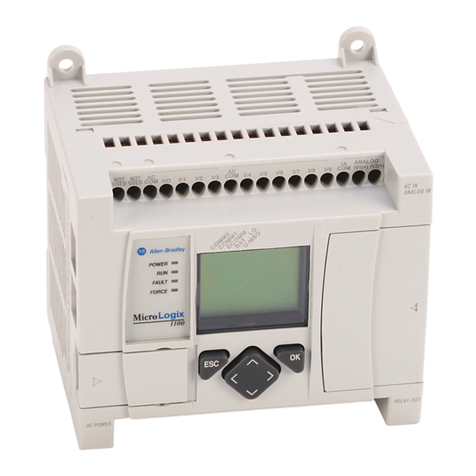
Rockwell Automation
Rockwell Automation 1763-L16AWA installation instructions

Johnson
Johnson JCRL120P2 Owners and installation manual

Emerson
Emerson Fisher 1052 instruction manual