Wieland SNO 4083KM User manual

Instructions
(Translation of the original instructions)
SNO 4083KM
Wieland Electric GmbH
Brennerstraße 10-14
D-96052 Bamberg
Tel. +49 (0) 951 / 9324 -0
Fax +49 (0) 951 / 9324 -198
www.wieland-electric.com
Doc. # BA000773 – 11/2014 (Rev. H) SNO 4083KM EN 8
Basic device for EMERGENCY STOP and safety door applications
•Basic device according to EN 60204-1:2007 and EN ISO 13849-1:2007 for single or
two-channel EMERGENCY STOP monitoring.
•PL e / category 4 according to EN ISO 13849-1:2007
•SILCL 3 according to DIN EN 62061:2005
•Stop category 0 according to DIN EN 60204-1
•Manual or automatic start
•With / without crossover detection
•Feedback circuit for monitoring external contactors
•Three enabling current paths, one messaging current path
•Evaluation unit for BWS 4 according to EN 61496-1
•Usage according to EN 81-1 and EN 50156-1
•For connection in series with a pressure sensitive mat according to EN 1760-1
Device versions
SNO 4083KM-A DC 24 with screw terminals, pluggable
SNO 4083KM-A AC 115-230 V with screw terminals, pluggable
SNO 4083KM-C DC 24 V with spring-loaded terminals, pluggable
SNO 4083KM-C AC 115-230 V with spring-loaded terminals, pluggable
Front view
Supply LED green, power supply indicator
K1, K2 LED green operating and status display for relays K1, K2 and the
safety circuits.
SAFETY REGULATIONS
•
Installation, commissioning, modification and retrofitting
must only be performed by a qualified electrician.
•Disconnect the device / the system from the power supply
before starting work. In the case of installation and system
errors, mains voltage can be present on the control circuit in
the case of non-galvanically isolated devices.
•Observe the electrotechnical and professional trade associa-
tion safety regulations for installation of the equipment.
•Opening the case or other manipulation voids any war-
ranty.
•In the case of improper use or any use other than for the
intended purpose, the device must no longer be used and
any warranty claim is void. Invalidating causes can be:
strong mechanical loading of the device, such as occur
when falling or voltages, currents, temperatures, humidity
outside the specifications.
•Always check all safety functions in accordance with the
applicable regulations during initial commissioning of your
machine / system and observe the specified inspection
cycles for safety devices.
WARNING
•
Take the following safety precautions before starting
installation / assembly or dismantling:
1. Disconnec
t the device / the system from the power
supply before starting work.
2. Secure the machine / system against being switched on
again.
3. Confirm that no voltage is present.
4. Ground the phases and short to ground briefly.
5. Cover and shield neighbouring live parts.
6. The devices must be installed in a switch cabinet with a
protection class of at least IP54.
•Limited contact protection! Protection class according to
EN 60529:
−Case / terminals: IP40 / IP20.
−Finger-proof according to EN 50274.
1Proper use
The devices are safety switching devices. They must only be
used as components of safety equipment on machines that is
intended for the protection of persons, material, functions and
machinery.
2Function
The device is a two-channel safety switching device for EMER-
GENCY STOP equipment according to EN 60204-1. It performs
self-monitoring during each ON-OFF cycle and is equipped with
positively driven relays. The device is suitable for connection in
series with short-circuiting pressure sensitive mats, pressure
sensitive bumpers or switching edges with 4-wire technology
(without a monitoring resistor).
Basic function: After applying the supply voltage to the
terminals A1/A2 and closed safety inputs, the enabling current
paths are closed when a valid reset signal is established at S34.
The enabling current paths are opened when the safety inputs
are opened / de-energized.
Operating modes / System functions
•Single-channel or two-channel actuation
•With or without crossover detection
•Manual start (triggering with falling edge)
•Automatic start
•Evaluation of signal transmitters featuring equivalent or non-
equivalent switching

Doc. # BA000773 – 11/2014 (Rev. H) SNO 4083KM EN 9
NOTE
•
The performance level (PL) and safety category in accord-
ance with EN ISO 13849-1 depend on the external wiring,
the application case, the choice of control device and how
this is physically arranged on the machine.
•The user must carry out a risk assessment in accordance
with ISO 14121-1.
•The entire system / machine must undergo validation in
accordance with the applicable standards on the basis of this.
•The stated performance level will only be achieved if, taking
into account the prevailing device load (see EN ISO 13849-1
Table C.1) and the application case, an average number of
switching cycles per year is not exceeded (see EN ISO
13849-1, C.2.3 and Table K.1). Assuming that the B10d
value is 400,000 for the maximum load, the maximum cycle
number would be 400,000 / 0.1 x 30 = 133,333 switching
cycles per year.
•
The safety-related characteristics only apply when the relays
are switched at least once per year.
•
Operating the device other than specified can result in
malfunctions or destruction of the device.
•
The device must be checked to ensure it is in perfect
working order before commissioning, after replacement of
modules and/or in the case of changes to an installation that
has already undergone acceptance.
•
For operation at 115–230 V AC, the operating equipment of
the control circuits must be designed for a rated voltage of
300 V. Basic isolation between supply and control circuits.
•
The specified times must always be adhered to when
operating the device; otherwise, the device may become
locked. Locking may be reversed by opening the safety
inputs in the proper manner.
•
The expansion units of the SNE series or external contactors
with positively-driven contacts can be used for duplicating
the enabling current paths
NOTE
•
The contacts must be fused with maximum 6 A operating
class gG.
•
Control outputs S11 and S21 are equipped with overload
protection (for short circuits). Once the cause of the error
has been rectified, the device is ready for operation again
after approx. 3 s.
•
The control inputs and outputs are only used for the con-
nection of control devices and not for the connection of
external consumers such as lamps, relays or contactors.
•
External loads must be equipped with a suitable protection
circuit for the load (e.g. RC elements, varistors, suppressors,
etc.) in order to reduce electromagnetic interference and
increase the service life of the output switching elements.
•
The application-specific standards must be observed when
installing and operating the device.
•
In the case of an external incoming supply for inputs S12
and S22 (e.g. via the OSSD of electrosensitive protective
equipment (installation 3) there is no assurance that the
relays can be deactivated by interrupting or isolating the
supply voltage at A1 / A2. The relays are deactivated when
the safety circuits are opened.
•The safety functions have not been checked by UL. The
certification process has been carried out in accordance
with the requirements for general applications as stipulated
by UL508.
3Mounting
4Terminal diagram
SNO 4083KM… DC 24 V
SNO
4083KM
… AC
115
-
230
V
Mounting
Dismantling
1.
Attach the device to the DIN
rail.
2.
Snap the device on to the
DIN rail by applying slight
pressure in the direction of
the arrow.
3. Press the
device down in
the direction of the arrow.
4.
While pressed down,
detach the device from the
latching (in the direction
indicated by the arrow) and
remove it from the DIN rail.

Doc. # BA000773 – 11/2014 (Rev. H) SNO 4083KM EN 10
5Function diagrams
Equivalent actuation with manual start (installation 1, 2, 3, 4, 5, 8)
A1
S11
S12 (CH1)
S22 (CH2)
LED K1
LED K2
S34 (Reset)
13/14
23/24
33/34
41/42
tB
tStBR
tM
tA
tR1
tStBR tM
tA
tR2
tW
Non-equivalent actuation with automatic start (installation 6, 7)
A1
S11
S12 (CH1)
S22 (CH2)
LED K1
LED K2
S34 (Reset)
13/14
23/24
33/34
41/42
tB
tA
tR1
tStA
tR2
tW
Notice:
LED blinking
LED permanently lit

Doc. # BA000773 – 11/2014 (Rev. H) SNO 4083KM EN 11
6Installation
1 – EMERGENCY STOP button, single-channel 2 – EMERGENCY STOP button, two-channel without
crossover detection
S12 S22 S21 S11 S14
S22
S12 S21 S11 S14
3
–
Safety light curtain BWS type 4, two
-
channel with
crossover detection by BWS1)
4
–
EMERGENCY STOP button, two
-
channel with
crossover detection
BWS type 4
with OSSD
S12 S22 S21 S11 S14
S11 S12 S21 S22 S14
5
–
Pressure sensitive mat, two
-
channe
l with crossover
detection
6
–
Solenoid switch, two
-
channel, non
-
equivalent, with
crossover detection
S11 S21 S22 S12 S14
Safety mat
S11 S21 S12 S22 S14
Type SMA
actuated
7 – Reset, automatic, with and without feedback circuit
8
–
Reset, manual, monitored, with and without
feedback
circuit
S11 S34
K11 ... K13
S11 S34
S21 S34
K11 ... K13
S21 S34
1 ) These installation types are not suitable for devices where UB= 115-230 V AC.

Doc. # BA000773 – 11/2014 (Rev. H) SNO 4083KM EN 12
9
–
Power supply
1
0
–
Outputs
A1 A2
L+ / L1 M / N
14
13
24
23
34
33
42
41
K1
K2
K11 K12 K13
L+/L1
M/N
7Contact load derating
I²
–
Total current
8Relay service life
UL508
Switching cycles
Switching current [A]

Doc. # BA000773 – 11/2014 (Rev. H) SNO 4083KM EN 13
9Dimensions
SNO 4083KM
-
A screw terminal
SNO 4083KM
-
C spring
-
loaded terminal
10 Technical data
Function
EMERGENCY STOP relay
Function indicator 3 LEDs, green
Power circuit
Rated voltage U
N
24 V DC 115–230 V AC
Operating voltage range U
B
: 0.85–1.2 × U
N
20.4 to 28.8 V DC 97 to 253 V AC
Rated power 1.6 W 1.8 W / 4.0 VA
Nominal frequency 50-60 Hz
Standby time 1.2 s max.
Control circuits
Input voltage 19.2 to 28.8 V DC
Input current (typ. / max.) S12/S22
S14/S34
25 / 100 mA
3 / 5 mA
Response time (manual start t
A1
, autom. start t
A2
) 250 ms
Minimum activation time tM(manual start, min. /
max.)
125 ms / 5 s
Standby time for reset t
BR
> 4 ms
Recovery time t
W
120 ms
Release time t
R
(typ. / max.) 12 / 35 ms
Synchronous time monitoring t
S
1.5 s / 0.5 s (SNO 4083KM-A 0,5S)
Test pulse S11: length / interval 4 ms / 200 ms
Test pulse S12, S22: length / interval (Installation 3) < 0.8 ms / > 5.5 ms
Test pulse ratio S12, S22: length / interval (Installation
3)
< 7 %
Test pulse length t
TR
, of the incoming test pulse < 16 ms
Delay time tD(time between test pulse and incoming
test pulse)
< 48 ms
Max. line resistance per channel
2
)
24 V DC (5 + ((1.176 × U
B
/ 24 V) – 1) × 200)
Ω
115–230 V AC 12
Ω
Output circuits
Enabling current paths
13/14, 23/24, 33/34
Messaging current paths
41/42
Contact Normally open Normally closed
Contact type Positively driven
Contact material Ag alloy, gold plated
Rated switching voltage U 230 V AC
Max. thermal permanent current
I
TH
6 A 2 A
Max. total current I
N
2
55°C 25 A
2
(UL 508: 9 A
2
)
65°C 9 A
2
Utilisation category AC-15 U
e
230 V, I
e
5 A
DC-13 U
e
24 V, I
e
5 A
Short circuit protection 6 A class gG fuse,
fuse integral < 100 A²s
Conditional short-circuit current 1000 A
Mechanical service life 10
7
switching cycles
2 ) If only one of the channels on a 2-channel device is used, the value is halved.

Doc. # BA000773 – 11/2014 (Rev. H) SNO 4083KM EN 14
Terminals and connection data
Screw terminals
Spring
-
loaded ter
minals
(TWIN)
Single-core or finely stranded 1 x 0,2 mm² bis 2,5 mm²
2 x 0,2 mm² bis 1,0 mm²
1 x 0,2 mm² bis 1,5 mm²
Finely stranded with wire-end ferrule according to
DIN 46228
1 x 0,25 mm² bis 2,5 mm²
2 x 0,25 mm² bis 1,0 mm²
1 x 0,25 mm² bis 1,5 mm²
AWG conductor size (only use Cu wires) 26–14 24–16
Maximum tightening torque 0,5 bis 0,6 Nm (5-7 lbf-in)
Stripping length 7 mm
General data
Air gap and creepage paths between the circuits EN 60664-1
Output circuits 1 13/14 and 23/24
Output circuits 2 33/34 and 41/42
Power circuit A1/A2
Control circuits S11, S12, S21, S22, S14 and S34
Safety separation
– Rated voltage 300 V
– Overvoltage category IV (6kV)
Output circuits 1 — Output circuits 2
Output circuits 1 and 2— Power circuit
Output circuits 1 and 2— Control circuits
Basic insulation
– Rated voltage 300 V
– Overvoltage category III (4kV)
Output circuits 1
Output circuits 2
Power circuit — Control circuits (only 115-230 V AC)
Protection class according to EN 60529
case/terminals
IP40 / IP20
Ambient operating temperature –25 to +65 °C (UL508: -25 to +55°C)
Storage temperature –25 to +75 °C
Weight 0.2 kg
Standards EN ISO 13849-1, EN 62061, EN 81-1, EN 50156-1
Certifications TÜV, cULus
11 Error codes and correction
Flashing code
(SUPPLY
-
L
ED)
2
Crossover, can be rectified during operation
3
Process error, failure to observe the correct sequence for two-channel actuation, can be rectified during opera-
tion by repeating the actuation sequence correctly
4
Synchronous time error, synchronous time exceeded in the case of two-channel actuation, can be rectified
during operation by adhering to the synchronous time
5
Maximum reset actuating time exceeded, can be rectified during operation by repeating the reset with the
correct time
6
Configuration error, can be rectified by ensuring the correct terminal assignment for the required configuration,
the device has to be switched off and on again
7
Permissible input voltage limits undershot / overshot at S12 and S22, can be rectified by setting the correct
supply voltage, the device has to be switched off and on again
8
Device temperature too high, can be rectified by reducing the contact loads or the ambient temperature, the
device has to be switched off and on again
≥
12
Internal monitoring event, please replace the device and contact after sales service
If an error is still indicated even after the cause has been rectified, inputs S12, S22, S14 and S34 must be kept open during
power-on (e.g. pull out the connector). The error should then be cleared and you can perform a restart with the required installa-
tion by means of a power-off and power-on operation.
Other manuals for SNO 4083KM
1
Table of contents
Other Wieland Measuring Instrument manuals
Popular Measuring Instrument manuals by other brands

Milkotester
Milkotester Master Pro operating instructions
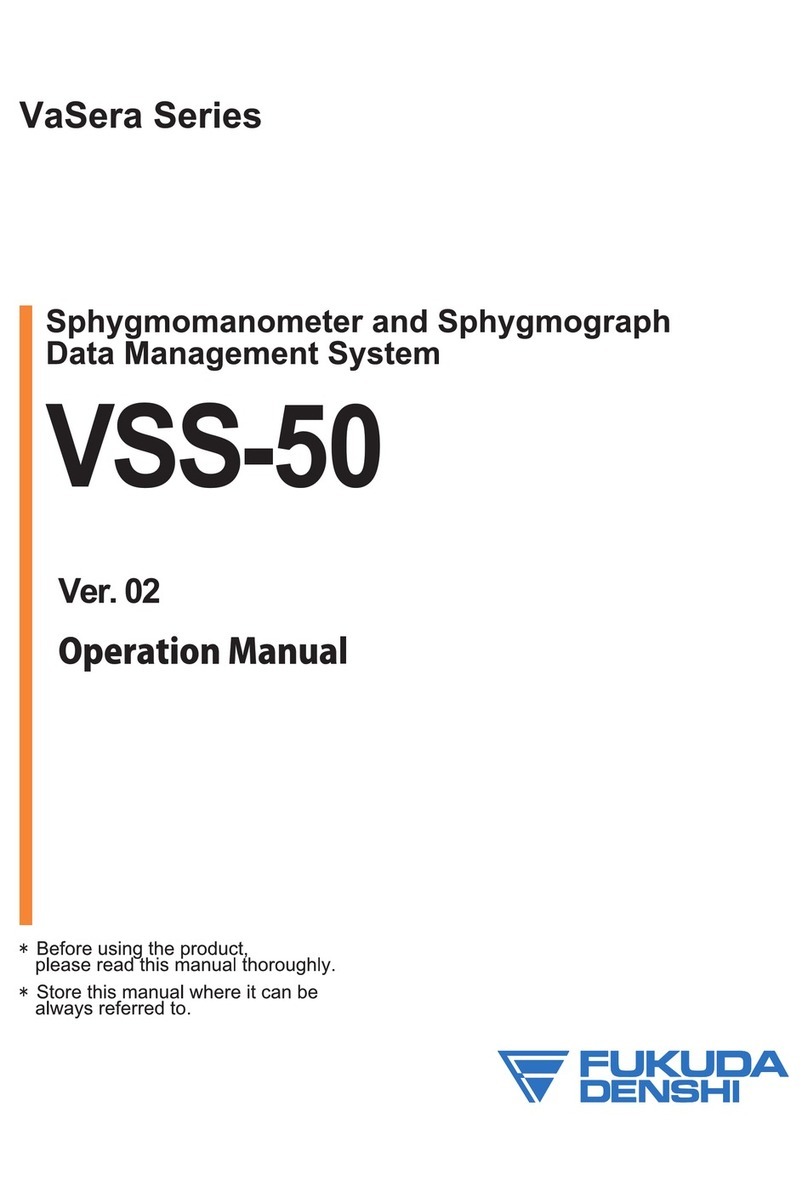
Fukuda Denshi
Fukuda Denshi VaSera Series instruction manual
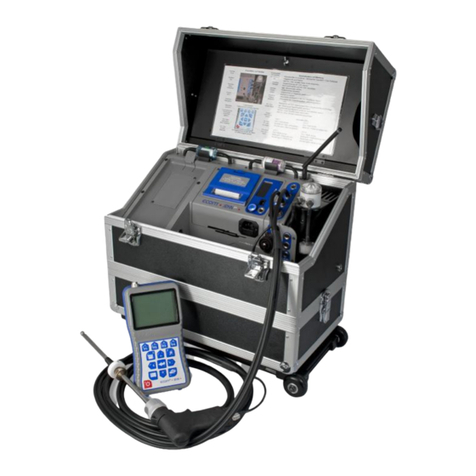
Ecom
Ecom J2KNpro Tech operating instructions
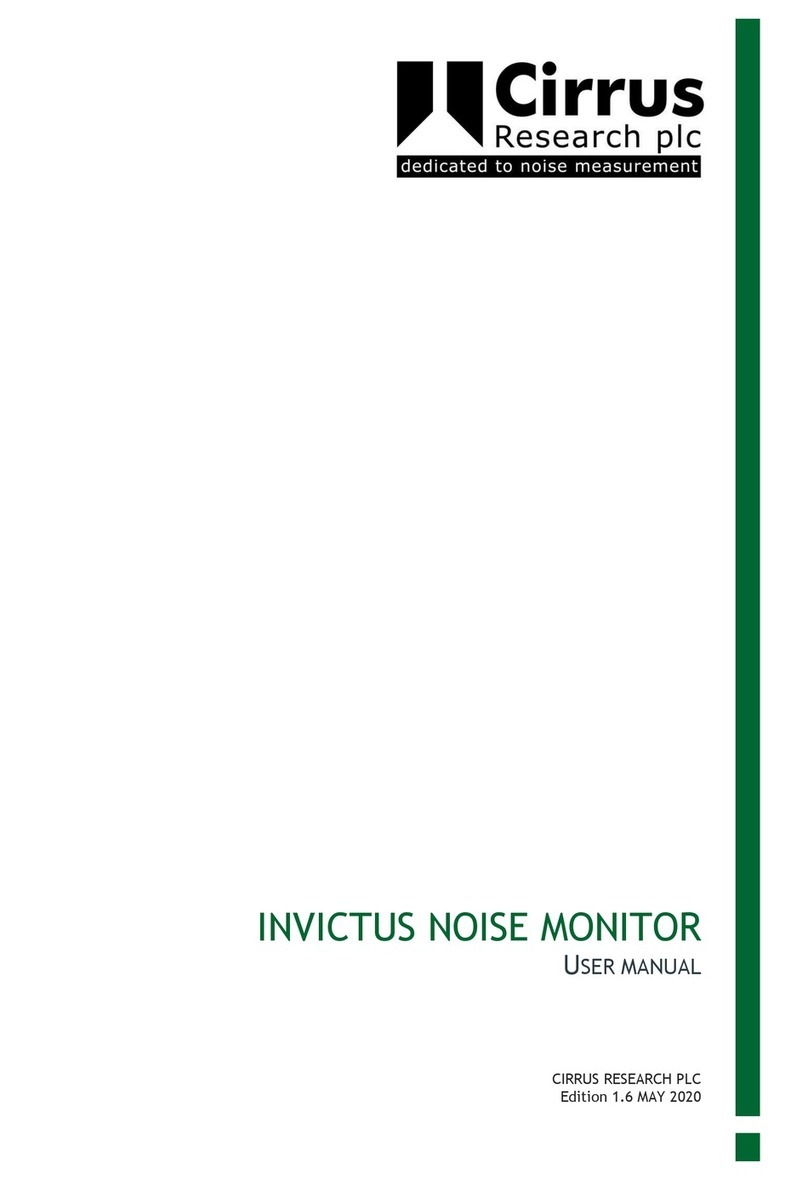
Cirrus
Cirrus INVICTUS user manual
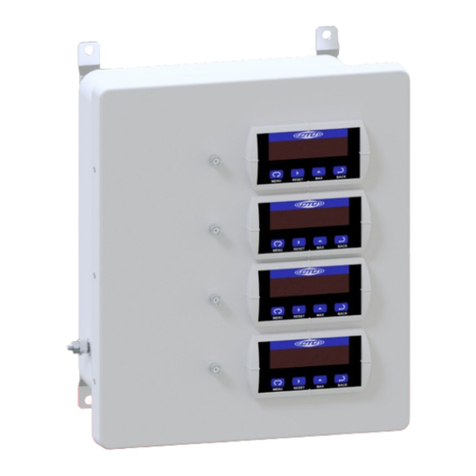
CTC Union
CTC Union SCD111 Series product manual

PCE Health and Fitness
PCE Health and Fitness PCE-T 238 user manual