Wilo Control Booster CC User manual

Pioneering for You
2 552 577-Ed.01 / 2020-12-Wilo
Wilo-Control CC-Booster (CC, CC-FC, CCe)
en Installation and operating instructions

Fig. 1a:
Comfort Control
6
1
7
8
2
3
1
Fig. 1b:
Comfort Control
6
1
7
8
2
3
1

Fig. 1c:
Comfort Control
4
1
6
8
2
3
1
6
7
5
Fig. 1d:
Comfort Control
4
18
2
3
1
6
7
5

Fig. 1e:
Comfort Control
8
1
2
3
6
1
Fig. 2:
Fig. 3:

Fig. 4a:
Fig. 4b:
Fig. 4c:

English
2WILO SE 12/2020
1 General information ..............................................................................................................................3
2 Safety ......................................................................................................................................................3
2.1 Symbols and signal words in the operating instructions .................................................................................. 3
2.2 Personnel qualifications ........................................................................................................................................ 3
2.3 Danger in the event of non-observance of the safety instructions ................................................................ 3
2.4 Safety consciousness on the job .......................................................................................................................... 3
2.5 Safety instructions for the operator ................................................................................................................... 4
2.6 Safety instructions for installation and maintenance work ............................................................................. 4
2.7 Unauthorised modification and manufacture of spare parts ............................................................................ 4
2.8 Improper use .......................................................................................................................................................... 4
3 Transport and temporary storage .......................................................................................................4
4 Application (Intended use) ................................................................................................................... 4
5 Product information .............................................................................................................................. 5
5.1 Type key ................................................................................................................................................................ 5
5.2 Technical data ........................................................................................................................................................ 5
5.3 Scope of delivery ................................................................................................................................................... 5
5.4 Accessories ............................................................................................................................................................. 6
6 Description and function ...................................................................................................................... 6
6.1 Description of the product (Fig. 1) ....................................................................................................................... 6
6.1.1 Function description .............................................................................................................................................. 6
6.1.2 Set-up of the switchgear ...................................................................................................................................... 6
6.2 Function and operation ......................................................................................................................................... 6
6.2.1 Switchgear operating modes ................................................................................................................................ 7
6.2.2 Motor protection ................................................................................................................................................... 8
6.2.3 Operation of the switchgear ................................................................................................................................ 9
7 Installation and electrical connection ...............................................................................................10
7.1 Installation ............................................................................................................................................................10
7.2 Electrical connection ...........................................................................................................................................10
8 Commissioning .....................................................................................................................................14
8.1 Factory setting .....................................................................................................................................................14
8.2 Checking the motor direction of rotation .........................................................................................................14
8.3 Setting the motor protection .............................................................................................................................15
8.4 Signal transmitters and optional modules ........................................................................................................15
9 Maintenance .........................................................................................................................................15
10 Faults, causes and remedies ...............................................................................................................15
10.1 Fault display and acknowledgement .................................................................................................................15
10.2 History memory for the faults ............................................................................................................................15
11 Appendix ..............................................................................................................................................17
11.1 ModBus: Data types .............................................................................................................................................17
11.2 ModBus: Parameter overview .............................................................................................................................17

English
Installation and operating instructions Wilo-Control CC-Booster 3
Installation and operating instructions
1 General information
About this document
The language of the original operating instruc-
tions is German. All other languages of these
instructions are translations of the original oper-
ating instructions.
These installation and operating instructions are
an integral part of the product. They must be kept
readily available at the place where the product is
installed. Strict adherence to these instructions is
a precondition for the intended use and correct
operation of the product.
These installation and operating instructions cor-
respond to the relevant version of the product and
the underlying safety standards valid at the time
of going to print.
EC-Declaration of conformity:
A copy of the EC-Declaration of conformity is an
integral part of these installation and operating
instructions.
If a technical modification is made to the designs
named in the declaration without our prior agree-
ment, or the declarations made in the installation
and operating instructions on product/personnel
safety are not observed, this declaration is no
longer valid.
2Safety
These installation and operating instructions con-
tain basic information which must be adhered to
during installation, operation and maintenance.
For this reason, it is mandatory that these installa-
tion and operating instructions are read by the
service technician and the responsible qualified
personnel/operator before installation and com-
missioning.
Not only must the general safety instructions
listed under this main "Safety" section be adhered
to, but also the special safety instructions that are
marked by danger symbols and included under the
following main sections.
2.1 Symbols and signal words in the operating
instructions
Symbols:
General danger symbol
Danger due to electrical voltage
NOTICE
Signal words:
DANGER!
Acutely dangerous situation.
Non-observance will result in death or
extremely serious injuries.
WARNING!
The user could suffer (serious) injuries.
"Warning" implies that (serious) injury to
persons is probable if this information is disre-
garded.
CAUTION!
There is a risk of damaging the product/unit.
"Caution" implies that damage to the product is
likely if this information is disregarded.
NOTICE:
Useful information on handling the product. It
draws attention to possible problems.
Information that appears directly on the product,
such as
•direction of rotation arrow,
• identifiers for connections,
• rating plate,
• warning stickers,
must be strictly complied with and kept in a fully
legible condition.
2.2 Personnel qualifications
The installation, operation and maintenance per-
sonnel must have the appropriate qualifications
for this work. The area of responsibility, responsi-
bility and monitoring of the personnel are to be
ensured by the operator. If the personnel do not
possess the necessary knowledge, they are to be
trained and instructed. This can be carried out, if
necessary, by the product manufacturer at the
operator’s request.
2.3 Danger in the event of non-observance of the
safety instructions
Non-observance of the safety instructions can
result in the risk of injury to persons and damage
to the environment and the product/unit. Non-
observance of the safety instructions will render
any claims for damages null and void.
In particular, non-observance can, for example,
result in the following risks:
• danger to persons due to electrical, mechanical
and bacteriological factors,
• damage to the environment due to leakage of
hazardous materials,
•material damage,
• failure of important product/unit functions,
• failure of required maintenance and repair
procedures.
2.4 Safety consciousness on the job
The safety instructions included in these installa-
tion and operating instructions, the existing
national regulations for accident prevention,
together with any operator’s internal working,
operating and safety regulations are to be com-
plied with.

English
4WILO SE 12/2020
2.5 Safety instructions for the operator
This appliance is not intended for use by persons
(including children) with reduced physical, sensory
or mental capabilities, or who lack experience and
knowledge, unless they have been given supervi-
sion or instruction concerning the use of the
device by a person responsible for their safety.
Children should be supervised to ensure that they
do not play with the device.
• If hot or cold components on the product/the unit
lead to hazards, measures must be taken on-site
to prevent them from being touched.
• Guards for moving components (such as the cou-
pling) must not be removed whilst the product is
in operation.
• Leakages (e.g. from the shaft seals) of hazardous
fluids (which are explosive, toxic or hot) must be
discharged so that no danger to persons or to the
environment arises. National statutory provisions
are to be complied with.
• Highly flammable materials should always be kept
a safe distance from the product.
• Danger due to electrical current must be elimi-
nated. Local directives or general directives [e.g.
IEC, VDE etc.] and instructions from local energy
supply companies must be adhered to.
2.6 Safety instructions for installation and
maintenance work
The operator must ensure that all installation and
maintenance work is carried out by authorised and
qualified personnel who have sufficiently familiar-
ised themselves with the installation and operat-
ing instructions by studying them in detail.
Work on the product/unit must only be carried out
when at a standstill. The procedure described in
the installation and operating instructions for
shutting down the product/unit must be strictly
observed.
Immediately after completing work, all safety and
protective devices must be put back in position
and/or recommissioned.
2.7 Unauthorised modification and manufacture of
spare parts
Unauthorised modification and manufacture of
spare parts will impair the safety of the product/
personnel and void the manufacturer’s declara-
tions regarding safety.
Modifications to the product are only permissible
following consultation with the manufacturer.
Original spare parts and accessories authorised by
the manufacturer ensure safety. The use of other
parts will absolve the manufacturer of liability for
any consequences arising therefrom.
2.8 Improper use
The operational reliability of the supplied product
is only guaranteed if used as intended and in
accordance with section 4 of the installation and
operating instructions. The limit values must on
no account fall under or exceed those values
specified in the catalogue/data sheet.
3 Transport and temporary storage
Immediately after receiving the product:
• Check product for transport damage,
• In the event of damage in transit, take the neces-
sary steps with the forwarding agent within the
respective time limits.
CAUTION! Risk of property damage!
Incorrect transport and temporary storage can
cause damage to the product.
• The switchgear is to be protected against mois-
ture and mechanical damage.
• It must not be exposed to temperatures outside
the range of -10 °C to +50 °C.
4 Application (Intended use)
The CC switchgear is used for automatic, conven-
ient control of pressure-boosting systems (single
and multi-pump systems).
The field of application is water supply in residen-
tial towers, hotels, hospitals, offices and industrial
buildings.
When used in conjunction with suitable signal
transmitters, the pumps offer low-noise and
energy-saving operation. The performance of the
pumps is adapted to the constantly changing
requirements in the heating / water-supply
system.
Intended use also includes compliance with this
manual.
Any other use is regarded as non-intended use.

English
Installation and operating instructions Wilo-Control CC-Booster 5
5Product information
5.1 Type key
5.3 Scope of delivery
• CC-Booster switchgear
• Circuit diagram
• CC-Booster installation and operating
instructions
• Frequency converter installation and operating
instructions (only for CC... FC version)
• Factory test report
e.g.: Wilo-Control CC-B 3x10A T34 DOL FC WM
CC
CCe
Comfort Control switchgear for fixed
speed pumps
Comfort Control switchgear for electronic
pumps
Pressure boosting application
4 x Number of pumps 1 – 6
10 Max. rated current per pump in amperes
[A]
T Mains connection:
M = alternating current (1~)
T = three-phase current (3~)
34 Rated voltage:
2 = 220 – 230 V
34 = 380 – 400 V
DOL Pump activation type:
DOL = direct
SD = star-delta
FC With Frequency Converter
WM Installation type:
WM = Switchgear is mounted on a
mounting bracket (wall mounted)
BM = Floor model (base mounted)
5.2 Technical data
Mains supply voltage [V]: See rating plate
Frequency [Hz]: 50/60 Hz
Control voltage [V]: 24 VDC; 230 VAC
Max. current consumption [A]: See rating plate
Protection class: IP54
Max. fuse protection on mains side [A]: See circuit diagram
Ambient temperature [°C]: 0 to +40 °C
Electrical safety: Pollution degree II

English
6WILO SE 12/2020
5.4 Accessories
Accessories must be ordered separately:
(see also Wilo-Select)
6 Description and function
6.1 Description of the product (Fig. 1)
6.1.1 Function description
The Comfort switchgear, controlled by a program-
mable logic controller (PLC), is used to control
pressure-boosting systems with up to 6 single
pumps. The pressure of a system is controlled as a
function of the load with appropriate signal trans-
mitters. The controller acts on a frequency con-
verter (CC-FC version), which in turn influences
the speed of the base-load pump. A modification
of the speed changes the volume flow and thus
the rated power of the pressure-boosting system.
Only the base-load pump is speed-controlled.
Uncontrolled peak-load pumps are switched on
and off automatically according to load require-
ments, while the base-load pump handles
fine-tuning to the pre-set setpoint.
In the CCe version, each pump has an (integrated)
frequency converter.
6.1.2 Set-up of the switchgear
The set-up of the switchgear is dependent on the
performance of the pumps that are to be con-
nected, and the version (CC, CC-FC, CCe) (see:
Fig. 1a CC direct starting; Fig. 1b CC star-delta
starting, Fig. 1c CC-FC direct starting; Fig. 1d
CC-FC star-delta starting, Fig. 1e CCe). It consists
of the following main components:
• Main switch: Switches the switchgear on/off
(item 1).
• Touch display: Display of operating data (see
menus) and the operating status. Menu selection
and parameter input possible via touch sensitive
surface (item 2).
• Programmable logic controller: Modular design
PLC with power supply unit. The configuration
depends on the system (item 3).
• Frequency converter: Frequency converter for
load-sensitive speed control of base-load pump -
only available for CC-FC version (item 4).
• Motor filter: Filter for ensuring a sinusoidal motor
voltage and for suppressing voltage peaks - only
in the CC-FC version (item 5).
• Fuse protection for drives and frequency con-
verter: Fuse protection for the pump motors and
the frequency converter. For devices with
P2 ≤ 4.0 kW: Motor protection switch. On the CCe
version: Circuit breaker for the fuse for the pump
mains supply cable (item 6).
• Contactors/contactor combinations: Contactors
for switching on the pumps. In devices with
P2 ≥ 5.5 kW, including the thermal tripping
devices for excess current protection (default
value: 0.58 * IN) and the time relay for the star-
delta switchover (item 7).
• Manual-0-Automatic switch: Switch for selecting
the pump operating modes "manual" (emergency/
test operation on the mains; motor protection
available), "0" (pump switched off – no activation
possible via PLC) and "auto" (automatic mode
enabled via PLC) (item 8).
The speed of every pump (0 – 100 %) can be set
in manual mode with the manual control in the
CCe version.
6.2 Function and operation
DANGER! Risk of fatal injury!
When working on the open switchgear, there is
a danger of electric shock from touching the live
components.
The work must only be carried out by qualified
personnel!
Option Description
Signal module Relay output module for outputting individual operation
signals and fault signals
DDC and control module Input terminal assembly for switching potential-free control
contacts
GSM module Mobile radio module for dialling into GSM networks
GPRS module Mobile radio module for dialling into GPRS networks
WebServer Controller module for connection to Internet or Ethernet data
transmission
Communication module "ProfiBus DP" Bus communication module for "Profibus DP" networks
Communication module "CanOpen" Bus communication module for "CanOpen" networks
Communication module "LON" Bus communication module for "LON" networks
Communication module "ModBus RTU" Bus communication module for "ModBus" networks
Communication module "BACnet" Bus communication module for "BACnet" networks
Mains switching External auxiliary device for switching to redundant supply
network
Other options on request

English
Installation and operating instructions Wilo-Control CC-Booster 7
NOTICE:
After connecting the switchgear to the supply
voltage, as well as after every mains interruption,
the switchgear returns to the operating mode set
before the power interruption.
6.2.1 Switchgear operating modes
Normal operation of switchgears with fre-
quency converter - CC-FC version (see Fig. 2)
An electronic signal transmitter (measurement
range to be set in menu 4.3.2.3) supplies the con-
trol variable actual value as a 4...20 mA current
signal. Then the controller maintains the system
pressure constant by means of the comparison of
the setpoint/actual value (for setting of the refer-
ence setpoint › see menu 3.1).
If there is no "external off" signal and no fault, the
base-load pump with load-sensitive speed con-
trol starts when its start level œ is undershot.
If the power requirement cannot be met by this
pump, the switchgear switches on a peak-load
pump and, if the requirement increases further,
other peak-load pumps (start level: Ÿ). The peak-
load pumps run at constant speed, the speed of
the base-load pump is controlled to the
setpoint ¢ in each case.
If the requirement drops until the controlling
pump is working in its lower performance range
and no peak-load pump is required any longer in
order to meet the requirement then the peak-load
pump switches off (stop level: ¡). The base-load
pump switches off independently via the zero-
flow cut-off (stop level: ž). If the pressure drops
again below the start level œ, then the pump
restarts.
The parameter settings required for switching on
and off the peak-load pump (switching level Ÿ/
¡; delay times) can be set in menu 4.3.3.2. A
selection can be made between the same switch-
off level for all pumps and pump-specific switch-
off level. The system suggests pump-specific
switch-off levels. For this it is necessary to enter
Qnom and H0 in menu 1.2.
To avoid pressure peaks when switching on or
pressure troughs when switching off a peak-load
pump, the speed of the base-load pump can be
raised or reduced during these switching opera-
tions. Corresponding frequency settings of these
so-called peak filters can be undertaken in
4.3.5.1 – page 2.
Normal operation of switchgears without
frequency converter – CC version (see Fig. 3)
The controlled variable is taken from comparison
of the setpoint/actual value for switchgear with-
out a frequency converter (mains operation) or
with a faulty frequency converter. Because there
is no possibility of load-sensitive speed adapta-
tion of the base-load pump, the system works as
a two-point controller between œ/ž or Ÿ/¡.
The peak-load pump is activated and deactivated
in the manner described above.
For switching off the base-load pump, a separate
switching threshold ž can be set in menu 4.3.3.1.
Normal operation of switchgear in the CCe ver-
sion (see Fig. 4)
A selection can be made between 2 operating
modes for switchgear in the CCe version. The set-
ting parameters described for switchgear CC…FC
are used each time for this.
The cascade mode corresponds in its operation to
the normal operation of switchgears in the CC…FC
version (see Fig. 2), whereby the peak-load pumps
are activated with maximum speed.
In Vario mode (see Fig. 4), one pump starts as a
load-sensitive speed-controlled base-load pump
(Fig. 4a). If the required power requirement can no
longer be met by this pump at maximum speed,
another pump starts and takes over the speed
control. The previous base-load pump continues
at max. speed as a peak-load pump (Fig. 4b). This
procedure is repeated at increasing load until the
maximum number of pumps is reached (here:
3 pumps – see Fig. 4c).
If demand falls, the controlling pump will be
switched off when the minimum speed is reached
and a former peak-load pump takes over control.
The switchgear has the following additional oper-
ating modes whose parameterisation is described
on the user interface:
Zero-flow cut-off
To avoid the pump running without water con-
sumption, the switchgear performs a zero-flow
test that may lead to pump deactivation where
necessary.
Pump cycling
Various pump cycling mechanisms are used selec-
tively to ensure that the load is distributed as
evenly as possible between all pumps and to
thereby balance the running times of the pumps.
Standby pump
One pump can be defined as the standby pump
and is available in the event that another pump
fails.
Pump test run
To avoid longer standstill times, a cyclic test run of
the pumps is provided.

English
8WILO SE 12/2020
Fault-actuated switchover of multi-pump
system
Switchgears with frequency converter – CC-FC
version:
If the base-load pump has a fault, it is switched off
and another pump is switched onto the frequency
converter. If the frequency converter has a fault,
the switchgear switches to "auto without fre-
quency converter" operating mode with the asso-
ciated control characteristics.
Switchgears without frequency converter –
CC version:
If the base-load pump has a fault, it is switched off
and one of the peak-load pumps is managed by
the switchgear as a base-load pump.
Switchgears in the CCe version:
If the base-load pump has a fault, it is switched off
and another pump takes over the control function.
As a result of a fault of the peak-load pump, it is
always switched off and a further peak-load pump
(if necessary, also the standby pump).
Low water
A low water signal can be sent to the switchgear
via a normally closed contact based on the signal
from a suction-side pressure switch, break tank
float switch or optional level relay.
Monitoring of maximum and minimum pressure
Limit values for safe system operation can be set.
Ext. Off
It is possible to deactivate the switchgear exter-
nally using a normally closed contact. This func-
tion takes precedence; all pumps are deactivated.
Operation in the event of a sensor fault
In the event of a sensor fault (e.g. wire break), the
behaviour of the switchgear can be defined.
Operating mode of the pumps
The operating mode of the respective pump can
be specified with the PLC (manual, off, auto) dur-
ing activation.
Emergency operation
In the event of the control failing, there is the
option to commission the pumps individually by
means of the manual-0-auto switch (Fig. 1a-e;
item 8) on the mains (or per manual control with
individually settable speed for each pump – only
CCe version). This function takes precedence over
pump activation by the control.
Setpoint changeover
The switchgear can work with 3 different set-
points.
Remote setpoint adjustment
Remote adjustment of the setpoint is possible
using an analogue current signal (optional voltage
signal) by means of the corresponding terminals
(acc. to circuit diagram).
Constant speed
Constant speed mode is possible via an analogue
current signal (optional voltage signal) using the
corresponding terminals (according to circuit
diagram).
Logic reversal of the collective fault signal (SSM)
The required logic of the SSM can be set.
Function of the collective run signal (SBM)
The required function of the SBM can be set.
Fieldbus connection
The switchgear is prepared for connection
via ModBus TCP as standard. Connection is estab-
lished via an Ethernet interface (electrical connec-
tion as per chapter 7.2).
The switchgear works as a Modbus slave. Basic
settings are adjusted on the user interface.
Different parameters can be read and also
changed to some extent via the Modbus interface.
An overview of individual parameters and a
description of the data types used are shown in
the appendix.
Pipe filling
The pipe filling function can be activated to avoid
pressure peaks when filling empty pipelines or
pipelines under low pressure.
6.2.2 Motor protection
Excess temperature protection
Motors with an WSK (thermal winding contact)
signal an excess winding temperature to the
switchgear by opening a bimetal strip contact. The
connection of the WSK is carried out according to
the circuit diagram.
Faults on motors that are equipped with a tem-
perature-dependent resistor (PTC) for excess
temperature protection can be detected using
optional evaluation relays.
Excess current protection
Motors on switchgears up to and including 4.0 kW
are protected by motor protection switches with
thermal and electromagnetic trip triggers. The
trigger current must be set directly.
Motors on switchgears from 5.5 kW are protected
by thermal motor protection relays. These are
installed directly on the motor protections. The
trigger current must be set and is 0.58 * Inom with
the Y-∆ starting of the pumps used.
All motor protection devices protect the motor
during operation with the frequency converter or
in mains operation. Pump faults which reach the
switchgear result in deactivation of the corre-

English
Installation and operating instructions Wilo-Control CC-Booster 9
sponding pump and activation of the SSM. After
the cause of the fault has been rectified, it is nec-
essary to acknowledge the fault.
The motor protection is also active in emergency
operation, and leads to deactivation of the corre-
sponding pump.
In the CCe version, the pump motors protect
themselves by mechanisms integrated in the fre-
quency converters. The error messages from the
frequency converters are handled in the switch-
gear as described above.
6.2.3 Operation of the switchgear
Operating elements
•Main switch on/off (lockable in "Off" position)
•The touch display (graphics-capable) shows the
operating statuses of the pumps, the controller,
and the frequency converter. Additionally, all
switchgear parameters can be set using the
display.
The relevant operating elements appear context-
related on the touch display and can be selected
directly. Input fields for parameters are marked
with a line at the bottom.
The basic layout of the user interface is shown
below:
1 - Current user status display; access to login
page
2 - Navigation bar: Current screen display; press
for direct navigation
3 - Quicklinks/main menu:
a - Home (return to main menu screen)
b - Control (e.g. setpoints)
c - Interaction (e.g. HMI, BMS)
d - System (e.g. pump data, sensors)
e - Current alarms
f - Help (e.g. online manual)
4 - Pressing an arrow leads to the next operation
level
More information on operation can be found in the
online manual on the user interface

English
10 WILO SE 12/2020
User levels
Operation and parameterisation of the switchgear
is protected by a three-stage security system.
After the user level is selected and the corre-
sponding password is entered (user symbol on
main screen or INTERACTION->HMI->LOGIN), the
system is released on the relevant user level.
User 1 (standard user – no login):
The display of almost all menu items is released in
this level (typical: local user, e.g. building care-
taker). Parameter input is limited.
User 2:
The display of almost all menu items is released in
this level (typical: operator). Parameter input is
possible with almost no limitations.
The password for this user level is 2222.
The other user levels are reserved for Wilo.
Selecting the display language
The user can select the display language
(INTERACTION->HMI->LANGUAGE).
7 Installation and electrical connection
Installation and electrical connection must be
carried out in accordance with local regulations
and only by qualified personnel.
WARNING! Risk of personal injury!
Existing accident prevention regulations must
be adhered to.
Warning! Danger of electric shock!
Danger due to electrical current must be elimi-
nated.
Local directives or general directives [e.g. IEC,
VDE etc.] and instructions from local energy
supply companies must be adhered to.
7.1 Installation
• Wall fixation, WM (wall mounted): For pressure-
boosting systems, the WM switchgears are
mounted on the compact unit. If the wall device
should be mounted separately from the compact
unit, this is done using 4 screws, Ø 8 mm. Suitable
measures should be used to ensure the protection
class.
• Floor model, BM (base mounted): The floor model
is set up free-standing on a level surface (with
sufficient bearing capacity). In the standard ver-
sion, there is an up-right panel support with a
height of 100 mm for the cable inlet. Other sup-
ports are available on request.
7.2 Electrical connection
WARNING! Danger of electric shock
Electrical connection must be carried out by an
electrician authorised by the local energy supply
company and in accordance with the applicable
local regulations [e.g. VDE regulations].
Mains connection
Warning! Danger of electric shock!
There is a potentially fatal voltage on the supply
side, even when the main switch is turned off.
• The mains type, current type and voltage of the
mains connection must match the details on the
rating plate of the switchgear.
• Mains requirements:
NOTICE:
In accordance with DIN EN / IEC 61000-3-11 (see
table below), the switchgear and pump with motor
power of ... kW (column 1) are provided for opera-
tion on a mains power supply with a system
impedance of Zmax at the house connection of
max. ... ohm (column 2) for a maximum number
of ... connections (column 3).
If the mains impedance and the number of con-
nections per hour are greater than the values
given in the table, the switchgear with the pump
may lead to temporary voltage drops and also to
disturbing voltage fluctuations (flickering) due to
the unfavourable mains conditions.
Therefore, measures may need to be taken before
the switchgear and the pump can be operated on
this connection as intended. The necessary infor-
mation must be obtained from the local energy
supply company and the manufacturer.

English
Installation and operating instructions Wilo-Control CC-Booster 11
NOTICE:
The maximum number of connections per hour
specified in the table for each power is determined
by the pump motor and must not be exceeded
(adjust the parameterisation of the controller
accordingly; see follow-up times, for example).
• Fuse on mains side in accordance with the infor-
mation in the circuit diagram.
• Feed the ends of the mains cable through the
threaded cable glands and cable inlets and wire
them according to the markings on the terminal
strips.
• The 4-wire cable (L1, L2, L3, PE) is to be provided
on-site. The connection is established at the main
switch (Fig. 1a – e, item 1) or for systems of
higher power at the terminal strips in accordance
with the circuit diagram, the PE is connected to
the earth rail.
Power [kW]
(Column 1)
System impedance [Ω]
(Column 2)
Connections per hour
(Column 3)
3~400 V 2.2 0.257 12
2-pole 2.2 0.212 18
Direct starting 2.2 0.186 24
2.2 0.167 30
3.0 0.204 6
3.0 0.148 12
3.0 0.122 18
3.0 0.107 24
4.0 0.130 6
4.0 0.094 12
4.0 0.077 18
5.5 0.115 6
5.5 0.083 12
5.5 0.069 18
7.5 0.059 6
7.5 0.042 12
9.0 – 11.0 0.037 6
9.0 – 11.0 0.027 12
15.0 0.024 6
15.0 0.017 12
3~400 V 5.5 0.252 18
2-pole 5.5 0.220 24
S-D starting 5.5 0.198 30
7.5 0.217 6
7.5 0.157 12
7.5 0.130 18
7.5 0.113 24
9.0 – 11.0 0.136 6
9.0 – 11.0 0.098 12
9.0 – 11.0 0.081 18
9.0 – 11.0 0.071 24
15.0 0.087 6
15.0 0.063 12
15.0 0.052 18
15.0 0.045 24
18.5 0.059 6
18.5 0.043 12
18.5 0.035 18
22.0 0.046 6
22.0 0.033 12
22.0 0.027 18
30.0 0.027 6
30.0 0.020 12
30.0 0.016 18
37.0 0.018 6
37.0 0.013 12
45.0 0.014 6
45.0 0.010 12

English
12 WILO SE 12/2020
Pump mains connections
CAUTION! Risk of damage to the product!
Observe the installation and operating instruc-
tions for the pumps!
Power connection
The pumps must be connected to the terminal
strips in accordance with the circuit diagram, PE
must be connected to the earth rail. Use shielded
motor cables.
Connecting cable shields to the EMC threaded
cable glands
(CC ... WM)
(1) or
(2)
(3)
Connecting cable shields to the shield clamps
(CC ... BM)
NOTICE:
The length of the cut (step 3) must be matched
exactly to the width of the clamp used!
NOTICE
If the pump connection cables are extended
beyond the dimension supplied ex-works, it is
necessary to comply with the EMC note in the
operating manual of the frequency converter (only
CC-FC version).
Connection of excess temperature protection/
pump fault
The thermal winding contacts or fault signal con-
tacts (CCe version) on the pumps can be con-
nected to the terminals in accordance with the
circuit diagram.
CAUTION! Risk of damage to the product!
Do not connect any external voltage to the
terminals!
Connection of pump control signal (CCe version
only)
Analogue control signals of the pumps (0 – 10V)
can be connected to the terminals in accordance
with the circuit diagram. Use shielded cables.
CAUTION! Risk of damage to the product!
Do not connect any external voltage to the
terminals!
(1)
(2)
(3)
(4)

English
Installation and operating instructions Wilo-Control CC-Booster 13
Sensors
Connect the sensor correctly to the terminals
according to the circuit diagram in the installation
and operating instructions.
Use a shielded cable, place the shield on one side
in the switchbox.
CAUTION! Risk of damage to the product!
Do not connect any external voltage to the
terminals!
NOTICE:
Observe the correct polarity of the pressure sen-
sor! Do not attach an active pressure sensor.
Analogue IN, setpoint remote adjustment/speed
remote adjustment
Remote adjustment of the setpoint or, in the
"constant speed" operating mode of the speed, is
possible using an analogue signal (0/4...20 mA or
0/2...10 V) by means of the corresponding termi-
nals in accordance with the circuit diagram. Use a
shielded cable, place the shield on one side in the
switchbox.
Setpoint changeover
Using the corresponding terminals in accordance
with the circuit diagram, it is possible to force a
switchover from setpoint 1 to setpoint 2 or 3 using
a potential-free contact (normally open contact).
x: Contact closed; o: Contact open
CAUTION! Risk of damage to the product!
Do not connect any external voltage to the
terminals!
External activation/deactivation
Using the corresponding terminals in accordance
with the circuit diagram, it is possible to connect a
remote activation/deactivation by means of a
potential-free contact (normally closed contact)
after removing the converter bridge (pre-
assembled as a factory setting).
CAUTION! Risk of damage to the product!
Do not connect any external voltage to the
terminals!
Protection against low water level
Using the corresponding terminals (in accordance
with the circuit diagram), it is possible to connect
a function for protection against low water level
by means of a potential-free contact (normally
closed contact) after removing the converter
bridge (pre-assembled as a factory setting).
CAUTION! Risk of damage to the product!
Do not connect any external voltage to the
terminals!
Collective run/collective fault signals (SBM/SSM)
Potential-free contacts (changeover contacts) for
external signals are available via the correspond-
ing terminals in accordance with the circuit
diagram.
Potential-free contacts, contact load:
– Minimum: 12 V, 10 mA
– Maximum: 250 V, 1 A
DANGER! Risk of fatal electrical shock!
There can be a potentially fatal voltage on these
terminals, even when the main switch is
switched off.
Display of actual pressure value
A 0 to 10 V signal for an external measurement/
display option of the current control variable
actual value is available via the corresponding ter-
minals in accordance with the circuit diagram.
0 to 10 V corresponds to the pressure sensor
signal 0 to pressure sensor limit value e.g.
CAUTION! Risk of damage to the product!
Do not connect any external voltage to the
terminals!
Actual frequency display
For switchgear with frequency converter (CC-FC
and CCe versions), a 0 to 10 V signal for an exter-
nal measuring/display option of the current actual
frequency of the base-load pump is available via
the corresponding terminals as per the circuit
diagram.
0 ... 10 V corresponds to the frequency range
0...fmax.
CAUTION! Risk of damage to the product!
Do not connect any external voltage to the
terminals!
Logic diagram
Contact Function
Setpoint 2 Setpoint 3
ooSetpoint 1 active
xoSetpoint 2 active
oxSetpoint 3 active
xxSetpoint 3 active
External activation/deactivation
Contact closed: Automatic ON
Contact open: Automatic OFF, signal by
symbol on the display
Contact load: 24 V DC/10 mA
Protection against low water level
Contact closed: No low water
Contact open: Low water
Contact load: 24 V DC/10 mA
Sensor Display pressure
range
Voltage/pressure
16 bar 0 ... 16 bar 1 V = 1.6 bar

English
14 WILO SE 12/2020
Field bus connection "ModBus TCP"
Connection to a building management system
using ModBus TCP takes place via the CPU’s
Ethernet interface:
Pass the cable through the special (dark grey)
threaded cable gland, fix and connect it as shown.
CAUTION! No external voltage may be applied.
NOTICE
The information for installation and for electrical
connection of optional inputs/outputs can be
found in the installation and operating instruc-
tions for these modules.
8 Commissioning
WARNING! Risk of fatal injury!
Commissioning by qualified personnel only!
Improper commissioning poses a risk of fatal
injury. Have commissioning performed by quali-
fied personnel only.
DANGER! Risk of fatal injury!
When working on the open switchgear, there is
a danger of electric shock from touching the live
components.
The work must only be carried out by qualified
personnel!
We recommend that you have the switchgear
commissioned by Wilo customer service.
Before switching on for the first time, the on-site
wiring must be checked to ensure it is correct, in
particular the earthing.
Tighten all connection terminals prior to
commissioning!
NOTICE:
In addition to the activities described in these
installation and operating instructions, it is neces-
sary to perform the commissioning measures in
accordance with the installation and operating
instructions of the overall system (pressure-
boosting system).
8.1 Factory setting
The switchgear is pre-set at the factory.
The factory settings can be restored by Wilo
Service.
8.2 Checking the motor direction of rotation
By briefly switching on each pump in the "Manual
mode" operating mode, check whether the direc-
tion of rotation of the pump in mains operation
corresponds to the arrow on the pump housing.
For the glandless pumps the correct or false direc-
tion of rotation is shown by an indicator LED in
terminal box (see installation and operating
instructions of the pump).
If the direction of rotation of all pumps in mains
operation is incorrect, swap over any 2 live wires in
the main mains cable.
Switchgear without frequency converter
(CC version):
• If the direction of rotation of only one pump in
mains operation is wrong, swap over any 2 phases
on motors P2 ≤ 4 kW (direct starting) in the motor
terminal box.
• If the direction of rotation of only one pump in
mains operation on motors P2 ≥ 5.5 kW (star-
delta starting) is wrong, swap over 4 connections
in the motor terminal box. In this case, swap the
winding start and winding end of 2 live wires (e.g.
V1 for V2 and W1 for W2).
Switchgear with frequency converter (CC-FC
version):
• Mains operation: Set each pump to "Manual mode"
individually in the menu. Afterwards, proceed like
with switchgear without frequency converter.
• Frequency converter mode: In the automatic with
FC operating mode, set each pump individually to
"Automatic" in the menu. The direction of rotation
in frequency converter mode is then checked by
briefly switching on the individual pumps. If the
direction of rotation of all pumps is incorrect,
swap over any 2 live wires at the frequency con-
verter output.

English
Installation and operating instructions Wilo-Control CC-Booster 15
8.3 Setting the motor protection
•WSK/PTC: No adjustment is required for the
excess temperature protection.
•Excess current: See section 6.2.2
8.4 Signal transmitters and optional modules
Comply with the installation and operating
instructions for signal transmitters and optional
additional modules.
9Maintenance
Have maintenance and repair work carried out
by qualified personnel only!
DANGER! Risk of fatal injury!
There is a risk of fatal injury from electric shock
when working on electrical devices.
• The switchgear should be voltage-free and
secured against unauthorised switch-on during
any maintenance or repair work.
• Any damage to the connection cable should only
ever be rectified by a qualified electrician.
• The switch cabinet must be kept clean.
• Clean the switch cabinet and fan if they are dirty.
The filter mats in the fans must be checked,
cleaned and replaced if necessary.
• If the motor power is 5.5 kW or more, check the
contactors for loss of contact material from time
to time and replace them if there is significant loss
of contact material.
• The charge level of the real-time clock backup
battery is registered by the system and reported, if
necessary. In addition, we recommend replacing it
every 12 months. For this purpose, change the
battery in the CPU assembly according to the fol-
lowing illustration.
10 Faults, causes and remedies
Have faults remedied by qualified personnel
only! Follow the safety instructions in
Chapter 2.
10.1 Fault display and acknowledgement
If a fault occurs, the background colour of the
main menu turns RED, the collective fault signal is
activated and the "Current alarms" page is dis-
played.
A signal is sent to the defined recipient(s) for sys-
tems equipped with remote diagnostics.
The fault can be acknowledged on the user inter-
face by remote diagnostics.
If the cause of the fault is removed before
acknowledgement, the background colour of the
main menu turns back to white. If the fault per-
sists after acknowledgement, the background
colour of the main menu changes to yellow and
the associated fault signal is marked yellow in the
list of alarms.
10.2 History memory for the faults
A history memory has been set up for the switch-
gear and operates according to the FIFO principle
(first in, first out). Each fault is stored with a time
stamp (date/time of day).
The list of alarms can be viewed on the "Alarm
history" page.

English
16 WILO SE 12/2020
The following table contains a list of all fault
signals.
* Fault must be reset manually
** You can adjust whether the error is reset manually or
automatically
If the fault cannot be remedied, please contact your nearest
Wilo customer service point or representative.
Code Alarm text Causes Remedies
E040.0 * Sensor faulty Pressure sensor defective Replace sensor
No electrical connection to the sensor Repair the electrical connection
E040.2 * Fault at input
"Analogue IN"
There is no signal at the input
(wire break or signal source error)
Repair the electrical connection
Check external signal source
E060 Output
pressure max
The output pressure of the system has risen
above the set limit value (e.g. due to a
controller fault)
Check controller function
Check installation
E061 Output
pressure min
The output pressure of the system has
dropped below the set limit value (e.g. due
to a burst pipe)
Check whether the default value corre-
sponds to local conditions
Check pipe and repair if necessary
E062 Low water Protection against low water level triggered Check inlet/break tank; pumps restart
automatically
E080.1 –
E080.6 *
(CC / CC-FC), **
(CCe)
Pump 1...6
Alarm
Winding excess temperature (WSK/PTC) Clean cooling fins; motors are designed
for an ambient temperature of +40°C
(see also installation and operating
instructions of the pump)
Motor protection triggered (excess current
or short-circuit in the supply line)
Check the pump (in accordance with the
installation and user manual for the
pump) and the supply line
Collective fault signal for the pump fre-
quency converter has been activated (CCe
version only)
Check the pump (in accordance with the
installation and user manual for the
pump) and the supply line
E082 ** FC Error Frequency converter has signalled a fault Read off fault in the list of alarms or on
frequency converter and act in accord-
ance with FC installation and operating
instructions
Electrical connection disrupted Check connection to frequency
converter and repair if necessary
Motor protection of the frequency converter
has tripped (e.g. short-circuit of the FC
mains power cable; overload of the con-
nected pump)
Check mains power cable and repair it if
necessary; check pump (in accordance
with the installation and operating
instructions of the pump)
E100 Battery error The battery charge has decreased to mini-
mum level; an additional buffering of the
real time clock is not guaranteed
Replace battery (see section 9)
E109 ** External error The fault in an external device is reported to
the switchgear via a digital input
Check external device and act according
to its installation and operating instruc-
tions
This manual suits for next models
2
Table of contents
Other Wilo Control Panel manuals
Popular Control Panel manuals by other brands
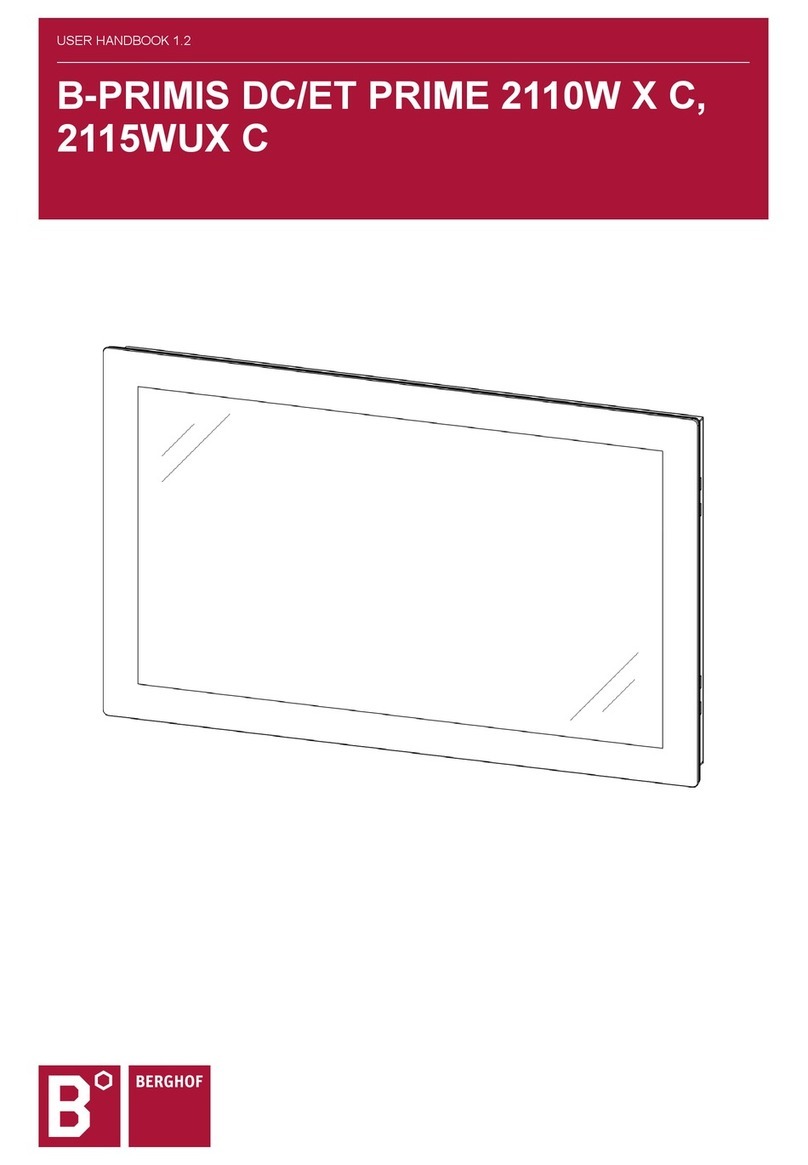
BERGHOF
BERGHOF B-PRIMIS ET-PRIME ET2115WUX CS User handbook
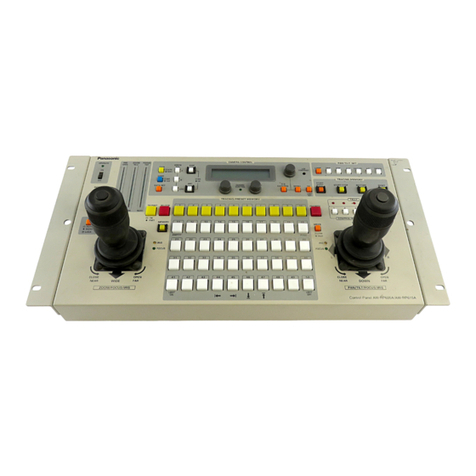
Panasonic
Panasonic AWRP655N - MULTI FUNCTION CONTROLLER Mechanical Parts
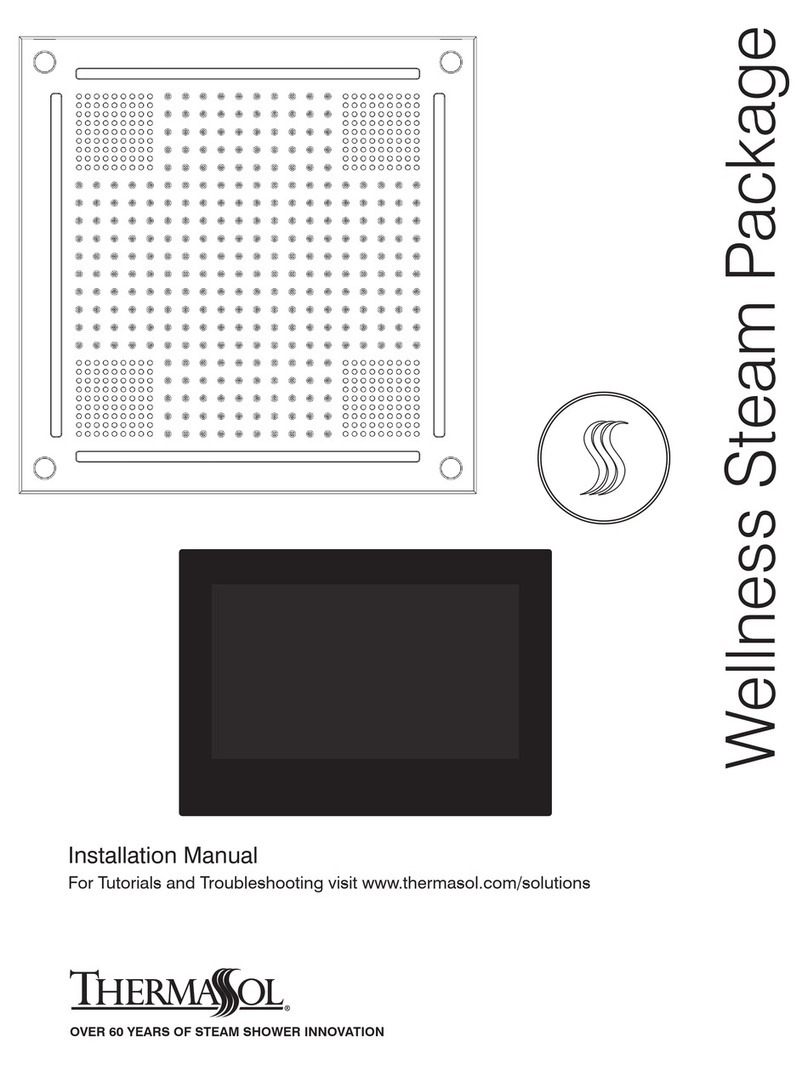
Thermasol
Thermasol TT10 Series installation manual
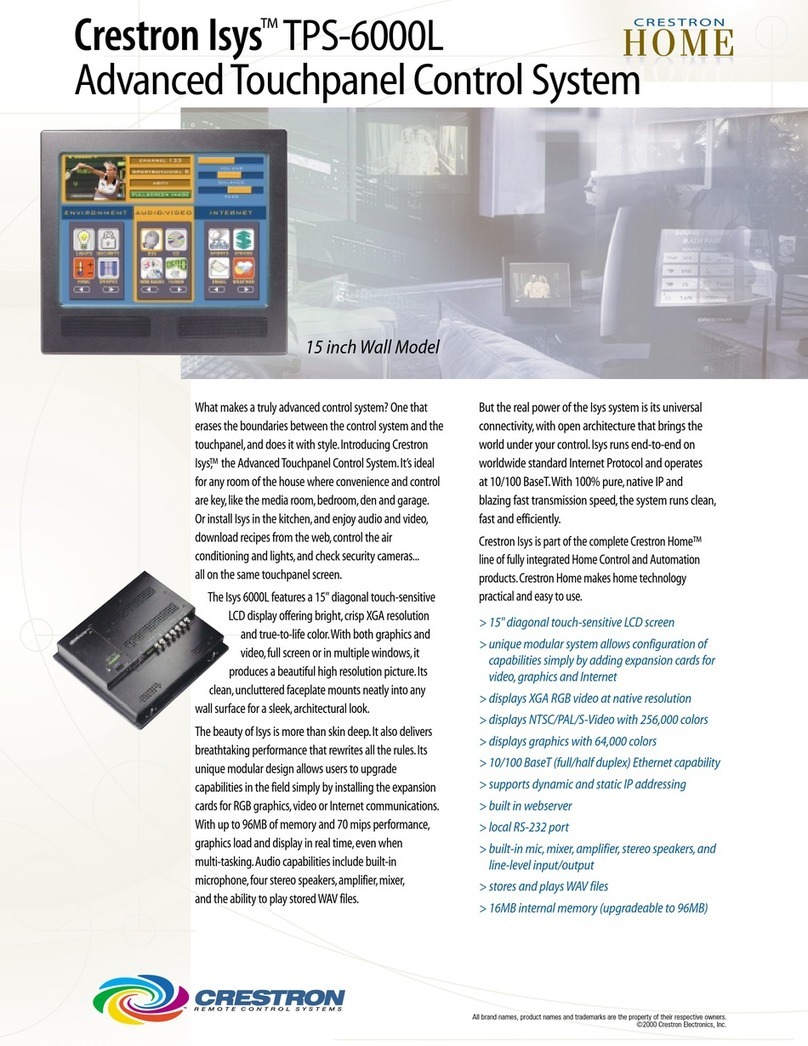
Crestron
Crestron Crestron Isys TPS 6000L Brochure & specs
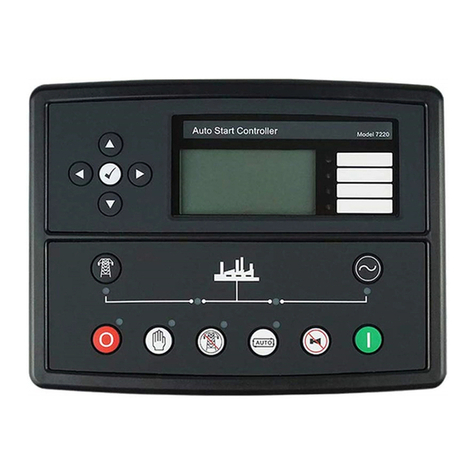
DSE
DSE 7220 installation instructions
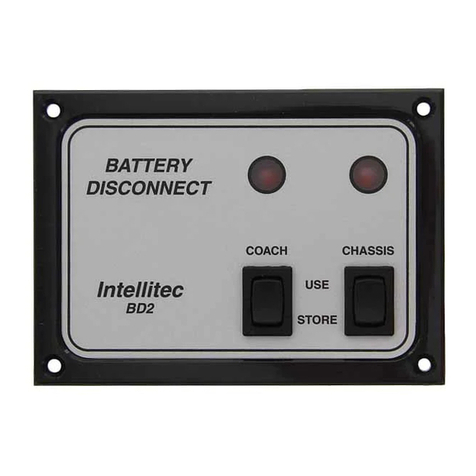
Intellitec
Intellitec Battery Disconnect BD0 Service manual
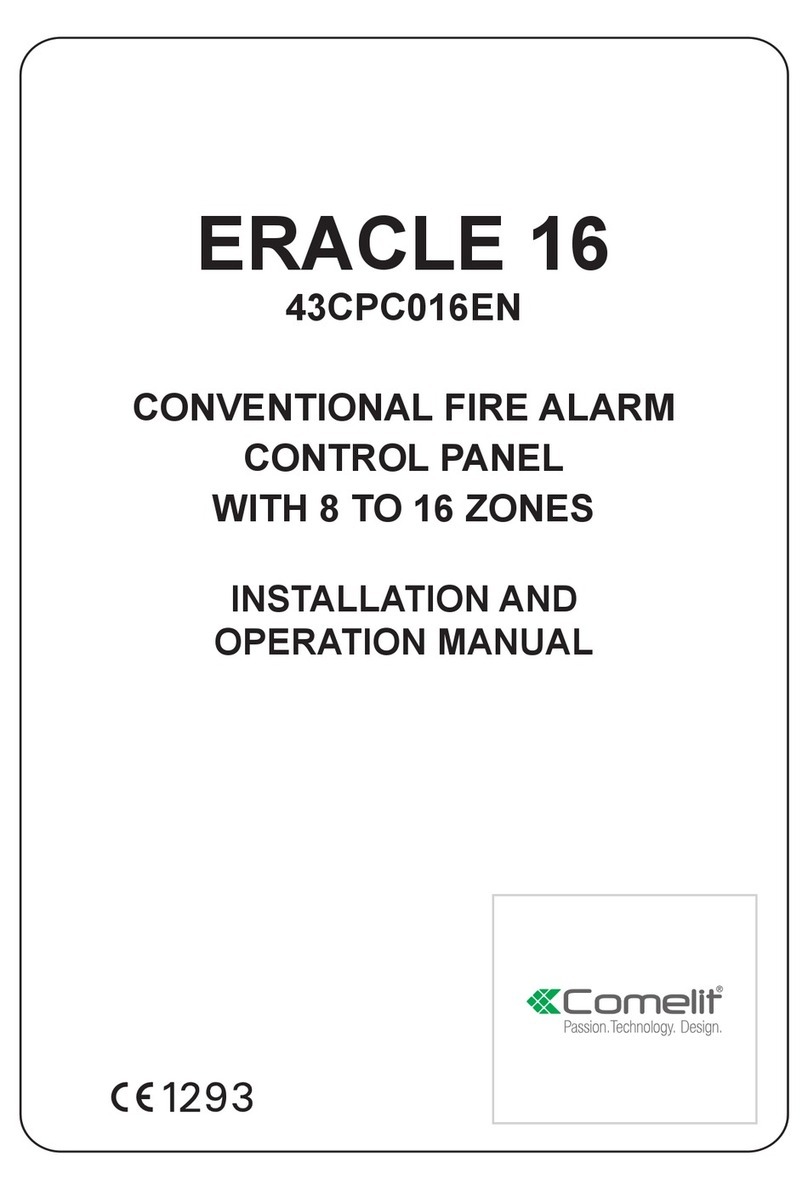
Comelit
Comelit ERACLE 16 Installation and operation manual
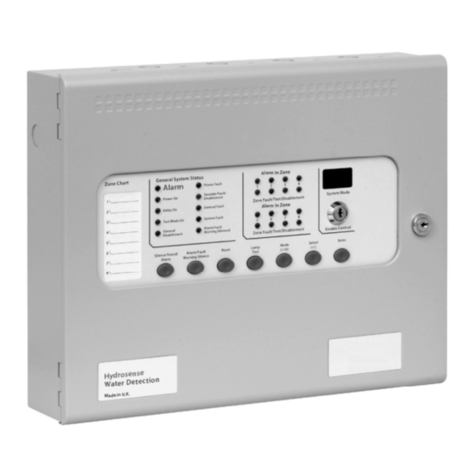
Vimpex
Vimpex Hydrosense HSCP Operation and maintenance manual
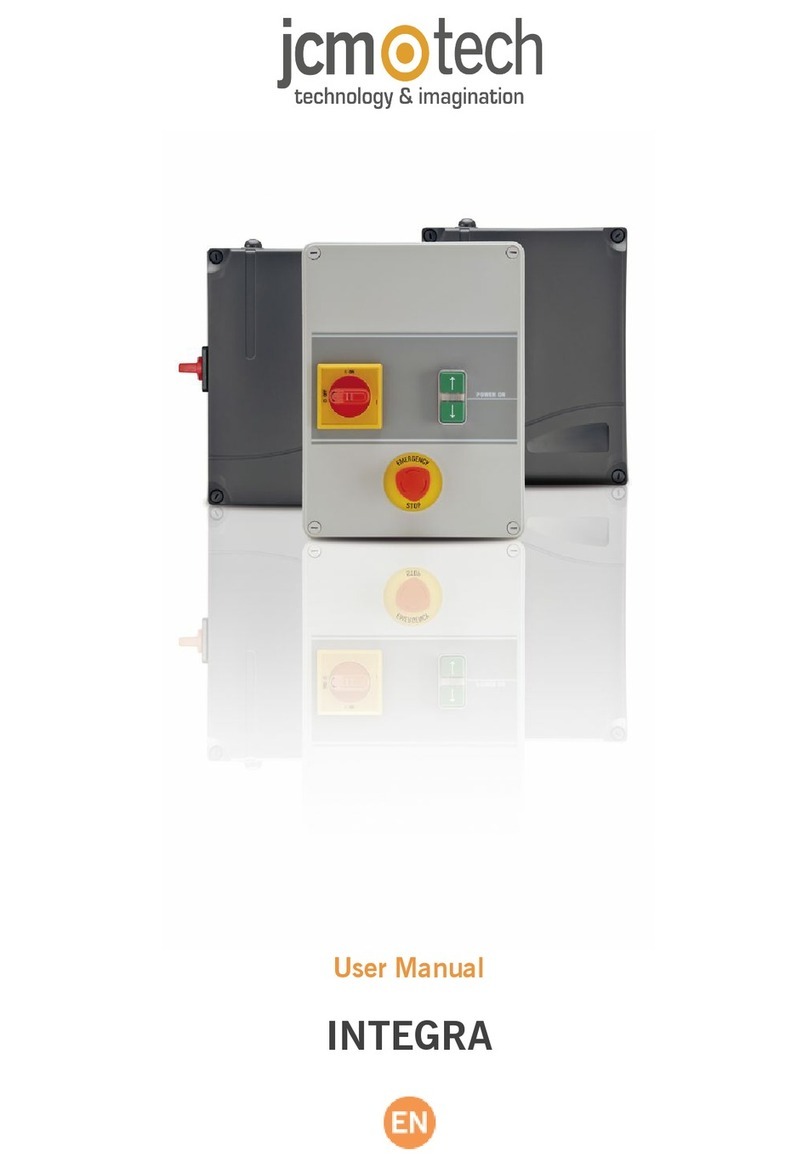
JCM Technologies
JCM Technologies INTEGRA user manual

Eminent
Eminent e-Domotica e-Centre 2 manual
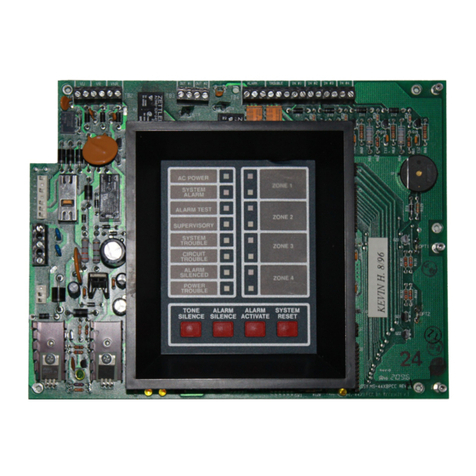
System Sensor
System Sensor Fire-Lite Alarms MRP-4424 instruction manual
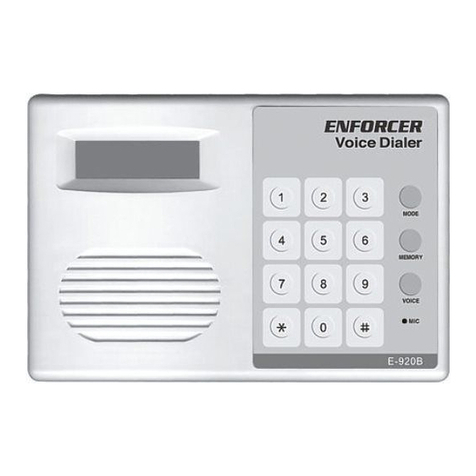
ENFORCER
ENFORCER E-920B installation manual