3T-Components 3T-MOTORS 3T45-RB Manual

Motor type 3T45-RB
(For shafts from 60 mm)
3T45-10RB
3T45-20RB
3T45-30RB
3T45-40RB
Motor type 3T35-RB
(For shafts from 40 mm)
3T35-10RB
3T35-13RB
www.3t-components.de |WEEE-Reg.-Nr.: DE 77028333
Smart Home Ready with everHome
Control via smart phone, tablet, PC or via
voice commands with Alexa or Google Assistant
INTELLIGENT
DRIVES &
CONTROLS
FOR SHUTTERS
AND AWNINGS
INSTALLATION &
OPERATING INSTRUCTIONS
Instructions and notes for installation and operation
3T-MOTORS Radio shutter / awning motors
with electronical limit switches
Attention:
It is important for the safety of persons
to follow these instructions.
Keep these instructions for future reference.

2
TABLE OF CONTENTS
3T-MOTORS Radio shutter motors / Radio awning motors with electronical limit switches
Guideline / Determine torque Page 3
Safety instructions Page 4
Function overview
Scope of delivery Page 5
Technical data Page 5
Installation notes Page 6
Installation instructions
Installation radio shutter motor Page 7 – 11
•Installation situation Page 7
•1) Prepare power connection Page 7
•2) Select motor bearing Page 7 – 8
•3) Remove shutter shaft Page 9
•4) Prepare motor for installation Page 9
•5) Mount bearings Page 9
•6) Mount motor with shaft unit Page 9 – 10
•7) Shutter motor wiring Page 10
•Mounting instructions for motor type 3T35-RB Page 11
Installation radio awning motor Page 12 – 13
•1) Preparation Page 12
•2) Prepare motor for installation Page 12
•3) Installing radio awning motor Page 12 – 13
•4) Radio awning motor wiring Page 13
Notes on the setting of the motor
Programming notes Page 14
Functions P1 button Page 14
Programming
Pairing handheld transmitter Page 15
Changing the direction of rotation of the radio motor Page 15
Programming end positions Page 16 – 17
Programming Intermediate position Page 17
Programming handheld transmitter + settings Page 18 – 20
Rocker switch Page 21
Troubleshooting Page 21
EU Declaration of Conformity Page 22
Hotline
06732 600 0369
© Copyright notice
All contents of these instructions, in particular texts, photographs and graphics, are protected by copyright.
Unless expressly indicated otherwise, the copyright is held by 3T-Components GmbH & Co. KG. Please ask us
if you wish to use the contents of this document. 3T-MOTORS Radio tubular motors | Table of contents
CONTACT
3T-Components GmbH & Co. KG
Bahnhofstr. 34
55578 Wallertheim
Email: info@3t-components.de
Tel: +49 (0) 6732-600 03 69
Fax: +49 (0) 6732-600 54 30
Opening hours:
Monday – Friday
8:00 – 17:00
www.3t-components.de
Learn more about us:

3
3T-MOTORS Radio tubular motors | Guideline
GUIDELINE
With this guide, you can determine the ideal torque in Newton meters (Nm) for the shutter motor.
DETERMINE WEIGHT ROLLER SHUTTER
1.) Determine roller shutter area
(Height + 150 mm) x Width = Roller shutter area (m²)
2.) Determine weight roller shutter material
Take approximate weights per m² of roller shutter area
from the table.
3.) Determine weight roller shutter
Roller shutter area (m²) x weight roller shutter material (m²)
4.) Calculate required traction force
Friction losses must be taken into account
(rail guidance) of approx. 10%!
Roller shutter area (m²) x Weight roller shutter material (m²) = Weight roller shutter (kg) + 10% Friction losses = Required traction force (kg)
Example:
PVC-Roller shutter area 3,00 m² x Weight roller shutter material 5 kg = 15 kg Weight roller shutter + 10% Friction losses = 16,5 kg Required traction force
Material
PVC
Aluminum Light
Aluminum Heavy
Steel
Wood
kg /m²
5
6
9
11
11
DETERMINE SHUTTER MOTOR TORQUE
100
90
80
70
60
50
40
010 20 30 40 50 60 70 80 90 100
515 25 35 45 55 65 75 85 95
10 Nm 13 Nm 30 Nm 40 Nm 50 Nm
Traction force (kg)
ØShaft (mm)
Torque (Nm): 20 Nm
Roller shutter box
Bottom edge
Roller shutter box
Window sill
Height
Width

4
3T-MOTORS Radio tubular motors | Safety instructions
GENERAL SAFETY INSTRUCTIONS
IMPROPER USE
PROPER USE
•WARNING: Important safety instructions.
Follow all instructions as incorrect installation may result in serious injury.
•WARNING: The drive must be disconnected from the power source during cleaning, maintenance and replacement of parts.
•Danger to life from electric shock when working on electrical equipment.
• The electrical connection, installation and commissioning of the receiver may only be carried out by qualied personnel.
•Before installing the drive, remove all unnecessary cables and disable all devices,
that are not required for operation with power.
•The relevant regulations and guidelines must be followed without fail, to avoid damage to persons and objects.
•Observe safety instructions according to EN 60 335-2-97: The power supply cable of the drives must be laid internally.
•Installation according to DIN 18073: The roller shutter box cover must be easily accessible and removable.
•Installation according to EN 60335: Only switches / pushbuttons / switching devices with a minimum contact opening
of 3 mm may be used, furthermore the up and down direction must be interlocked against each other.
•When installing in damp rooms, observe regulations (VDE 0100, part 701 and 702).
•These drives can be connected in parallel without an isolating relay or central control.
In this case, the max. output power of the command transmitter (timer or otherwise) must be observed.
•Do not use defective devices: Never use defective equipment.
Periodically inspect the equipment for imbalance and signs of wear or damage to cables and suspension springs.
Do not use equipment if repair or touch-up is necessary.
There is a risk of personal injury and property damage due to electric shock or short circuit.
•Retain the instructions for future reference.
•Use tubular motors only for automating shutters.
•Only use original components and original accessories from the manufacturer.
•The mains connection cable of the drives must be laid internally in the empty conduit up to the junction box.
The local electrical regulations must be observed.
•For the electrical connection of the tubular motors, a 230 V / 50 Hz
power connection with fuse must be available at the installation site.
•Inspect the installation frequently for imbalance and signs of wear or damage to cables and springs.
Do not use if repairs or adjustments are required.
Please read these important safety instructions before commissioning!
Incorrect installation can cause serious personal injury and damage to property.
The warranty claim expires in case of non-observance of this user information with all contained notes and regulations.
In case of non-observance of these instructions, the manufacturer or supplier shall not be liable for any personal injury or property damage incurred.
SAFETY INSTRUCTIONS
This symbol indicates danger due to electrical energy.
Danger to persons and objects may arise if the
associated information is not observed!
This symbol indicates information about general danger.
Non-observance can mean danger to
persons and objects!
This symbol indicates important information that can
ensure safe and proper use of the device.
•Persons are to be instructed with the correct operation of the tubular motor.
•The roller shutter movement must be monitored in order not to endanger persons.
•Do not allow children to play with motor controls.
•Store the handheld transmitter in such a way that unintentional operation is prevented (e.g. by children playing).
•The device can be used by children aged 8 years and above and persons with reduced physical, sensory or mental
capabilities or lack of experience and knowledge, if they have been given supervision and instruction concerning use
of the appliance in a safe way and are aware of the hazards involved.
•Children are not allowed to play with the equipment.
•If the power supply cord of this device is damaged, it must be replaced by the manufacturer or its customer service
or a similarly qualied person to prevent hazards.

5
APPLICATION
Motorized radio shutters
APPLICATION
Motorized radio shutters & awnings
SCOPE OF DELIVERY – MOTOR TYPE 3T45-RB
1Motor
2Limit switch adapter
3Shaft adapter
4Connection cable 3 meters
5Universal bearing & cotter pin
6Cover cap bearing (3T45-30RB/-40RB)
7Clip bearing (3T45-10RB/-20RB)
8Securing bracket
9 Wire end cap x 2
10 Manual
SCOPE OF DELIVERY – MOTOR TYPE 3T35-RB
1Motor
2Limit switch adapter
3Shaft adapter
4Connection cable 3 meters
5Universal bearing & cotter pin
6Clip bearing
7Securing bracket
8Wire end cap x 2
9Manual
3T45-10RB
10 Nm
25 kg
4,5 m²
3 m²
113 W
4 W
15 U/min
22 U
230 V
608 mm
587 mm
3 m
4 min
IP44
4260601764084
3T45-20RB
20 Nm
40 kg
6 m²
4,7 m²
161 W
4 W
15 U/min
22 U
230 V
608 mm
587 mm
3 m
4 min
IP44
4260601764091
3T45-30RB
30 Nm
60 kg
9 m²
7 m²
200 W
4 W
15 U/min
22 U
230 V
656 mm
635 mm
3 m
4 min
IP44
4260601764107
3T45-40RB
40 Nm
80 kg
11 m²
9,5 m²
228 W
4 W
15 U/min
22 U
230 V
656 mm
635 mm
3 m
4 min
IP44
4260601764114
3T35-10RB
10 Nm
25 kg
5,25 m²
4,2 m²
144 W
4 W
17 U/min
30 U
230 V
584 mm
568 mm
3 m
4 min
IP44
4260601764060
3T35-13RB
13 Nm
40 kg
7 m²
5,5 m²
144 W
4 W
14 U/min
30 U
230 V
584 mm
568 mm
3 m
4 min
IP44
4260601764077
2 31
4
5 6 7 9
SUITABLE FOR
8-sided Shafts from 40 mm
Ø40 mm
P1 button P1 button
SUITABLE FOR
8-sided Shafts from 60 mm
Ø60 mm
2 31
4
5
6
810
7
Technical data
9
8
Emission sound pressure level LpA ≤70 dB(A)
FUNCTION OVERVIEW
3T-MOTORS Radio tubular motors | Function overview
Motor type
Torque (Nm)
Traction power (kg)
Max. PVC shutter area (m²)
Max. ALU shutter area (m²)
Power (W)
Standby consumption (W)
Turn Speed (U/min)
Limit switch capacity (min)
Operating voltage (V AC)
L1 Total motor length (mm)
L2 Installation length (mm)
Connection line (m)
Max. Runtime (min)
Protection class
EAN

6
•Do not expose the tubular motor to crushing, impact, falling or contact with any liquids.
Do not punch holes in the entire length of the tube (motor casing) or attach screws to it.
•Please use suitable suspension springs to fasten the roller shutter curtain to the roller shutter shaft.
You will nd suitable suspension springs on page 23 and in our store under mounting accessories.
•Important for motor type 3T35-RB (SW40):
It is essential to use mini suspension springs for motor operation. These special mini springs protrude only approx.
1 mm into the shaft. This allows the shaft to rotate freely. When using commercially available suspension springs
the motor housing is left with grinding marks because the suspension pin protrudes too far into the roller shutter shaft,
which leads to damage and destruction of the motor.
•For steel shafts with a width across ats of 40 mm (SW40), only use shafts with
an external fold. Steel shafts with an internal fold will damage and destroy the motor.
•Grinding marks of any kind on the motor housing will void the warranty.
•The inspection cover of the roller shutter box must be easily accessible and removable.
•We recommend using a tubular motor with a power 10% higher than the weight of the shutter,
to compensate for the frictional resistance of the rail guide. > See Guideline / Determine torque (page 3)
•The motor is designed for short-time operation (4 min). It has an internal thermal circuit breaker which interrupts
the power supply in the event of overheating, e.g. as a result of continuous operation. The cooling phase is min. 10 min,
the thermal switch resets automatically. Regular operation is only possible after the the motor has cooled down completely.
Mini suspension springs (Page 23)
8-sided shaft SW40
with external fold
Do not use
8-sided shaft SW40
with internal fold!
Before installation, all non-essential electrical wiring must be removed, all mechanisms
that are not necessary for motorized operation must be deactivated.
INSTALLATION NOTES
3T-MOTORS Radio tubular motors | Installation notes

7
INSTALLATION RADIO SHUTTER MOTOR
Installation situation
1Counter bearing*
2Ball bearing*
3Roller capsule*
4Shutter shaft*
5Suspension spring*
6Shaft adapter
7Tubular motor
8Limit switch adapter
10 Limit switches
10 Engine mount
11 Shutter curtain*
* Accessories; not included
1Prepare power connection:
•The mains connection cable of the drive must be laid internally in the empty conduit up to the junction box.
The local electrical regulations must be observed.
2Select motor bearing:
•Two motor bearings are supplied: Universal bearing and cover cap bearing (3T45-30RB, 3T45-40RB) / clip bearing.
•Use one of the two motor bearings depending on the installation situation.
1 2 3 4 5 6 7 8 9 10
11
Please note:
•The motor can be installed on the right-hand side as well as on the left-hand side.
If the direction of rotation is reversed, please exchange the wires for the up and down direction.
•The setting of the end positions is only possible in the installed state (motor in shutter shaft).
•Never place screws in the area of the tube motor, as they will damage the motor.
•Engine damage caused by improper use or unprofessional installation,
lead directly to loss of warranty.
INSTALLATION INSTRUCTIONS
3T-MOTORS Radio tubular motors | Installation instructions

8
Motor type 3T35-RB
Installation with universal bearing or clip bearing
Installation with universal bearing:
•Push the motor with the square into the opening of the bearing
and secure with cotter pin.
Installation with clip bearing:
•Remove screws from metal plate on motor head >g. 2.5
•Remove metal plate >g. 2.6
•Remove motor square spigot >g. 2.7
•Reattach metal plate >g. 2.8
•Engage motor type 3T35-R without square spigot in clip bearing.
Motor type 3T45-RB
Installation with universal bearing or cover cap bearing / clip bearing
Installation with universal bearing:
•Push the motor with the square into the opening of the bearing
and secure with cotter pin.
Installation with cover cap bearing:
•Remove screws from metal plate on motor head >g. 2.1
•Remove metal plate >g. 2.2
•Remove motor square spigot >g. 2.3
•Reattach metal plate >g. 2.4
•Slide motor type 3T45-R without square spigot into cover cap bearing
and secure with both securing clips. / Engage motor in clip bearing
2.62.5
2.82.7
Universal bearing Clip bearing
2.1 2.2
2.3 2.4
Clip bearing
3T-MOTORS Radio tubular motors | Installation instructions
INSTALLATION INSTRUCTIONS
Universal bearing
Cover cap bearing
Cotter pin Cotter pin
Square spigot Square spigot
Securing clips

9
3Remove shutter shaft:
•Lower the roller shutter.
•Open the cover of the roller shutter box.
•Release the suspension springs from the roller shutter shaft.
•Lift roller shutter shaft incl. ball bearing out of the holder.
4Prepare motor for installation:
•Push limit switch adapter ush against motor head. >g. 4.1 / 4.2
•Secure the shaft adapter with the supplied securing bracket. >g. 4.3 / 4.4
•Push the motor into the roller shutter shaft without using force (never knock it in). The fold of the shaft must lie over the recess in the shaft adapter. >g. 4.5 / 4.6
•Make sure that the roller shutter shaft is ush with the motor head limit switch adapter. >g. 4.7 / 4.8
5Mount bearings:
•Remove old wall bearing on motor side (left or right installation possible).
•Mount motor bearing at this point.
(2 mounting options: Universal bearing & cotter pin and cover cap bearing & securing clips (3T45-30RB/3T45-40RB) / clip bearing).
•Please mount the bearings so that the limit switches are freely accessible.
•Make sure that the roller shutter motor with the shaft unit sits horizontally in the roller shutter box.
6Mount motor with shaft unit:
•Insert the motor head (with the entire shaft unit) into the motor bearing and secure it with the supplied cotter pin or securing clips (Cover cap bearing)..
4.1 4.2 4.3 4.4
4.5 4.6 4.7 4.8
3T-MOTORS Radio tubular motors | Installation instructions
INSTALLATION INSTRUCTIONS
Limit switch adapter
Motor head
Securing bracket
Click
Shaft adapter
Roller shutter shaft
Fold
Recess
wrong right

10
Shutter motor
230 V / 50 Hz
Power grid
230 V / 50 Hz
1) white = Control line downward or upward
2) black = Pole contact rocker switch
3) brown = L1 / Phase
4) blue = N Neutral conductor
5) green/yellow = PE Protective conductor
1) brown / black = L1 / Phase
2) blue = N Neutral conductor
3) green/yellow = PE Protective conductor
1 (L1)
2 (N)
3 (PE)
2
3 (L1)
4 (N)
5 (PE)
•On the opposite side of the motor, push the roller capsule out of the roller shutter shaft until it ts into the ball bearing inserted in the wall bearing.
•Fix roller capsule to roller shutter shaft with self-tapping screw. Position the screw at a punched hole. This prevents the screw from slipping.
7Shutter motor wiring:
•Connect the radio shutter motor to the mains and, if necessary, connect the rocker switch to the motor cable.
•The electrical connection of the roller shutter motor and control unit may only be carried out by qualied personnel.
1
8Programming radio transmitter:
•Pair the radio handheld transmitter to the shutter motor. See Programming radio transmitter (page 15).
•If the direction of rotation is reversed, please change it with the paired radio handheld transmitter.
> Changing the direction of rotation of the radio motor (Page 15).
Wire end caps
•Use the enclosed wire end caps to insulate free wire ends of the
motor cable. If no rocker switch is connected the black and white
wires are unused and must be insulated. To do this, slide the wire
end caps onto the wire ends and press them together with crimping
pliers or combination pliers.
9Setting the end positions:
•The end points are set by radio handheld transmitter.
•See programming end positions (page 16).
Rocker switch
3T-MOTORS Radio tubular motors | Installation instructions
INSTALLATION INSTRUCTIONS
Roller capsule
Wall bearing +
Ball bearing

11
MOUNTING INSTRUCTIONS FOR 3T-MOTORS MINI-TUBE MOTORS MOTOR TYPE 3T35-RB
Use proper suspension springs:
•To fasten the roller shutter curtain to the roller shutter shaft, please be sure to use
suitable suspension springs for motor operation. These special mini suspension springs only protrude
approx. 1 mm into the shaft. This allows the shaft to rotate freely. When commercially
springs are used, there will be grinding marks on the motor housing because the suspension pin
protudes too far into the roller shutter shaft, which leads to damage and destruction of the motor.
In case of any kind of grinding marks on the motor housing, the warranty claim is void.
•Mini suspension springs > Optional tubular motor accessories (page 23)
Use correct roller shutter shaft with external fold:
•For steel shafts with a width across ats of 40 mm (SW40), only use shafts with
an external fold. Steel shafts with an internal fold will damage and destroy the motor.
Explanation:
•Avoid overstressing and resulting premature aging of the motor by using the correct suspension
springs and the correct roller shutter shaft with external fold!
•Keep in mind that the motor housing has a diameter of 35 mm and the roller shutter shaft SW40
has an outer diameter of 40 mm. When using commercially available springs or roller shutter shafts
with internal fold, the motor housing will be left with grinding marks, since the suspension pin or the
fold protrude too far into the roller shutter shaft. Contrary to its intended use, the motor runs
permanently against an overload and outside its characteristic data.
•Matching roller shutter shafts SW40 > Optional tubular motor accessories (page 23)
Mini Suspension spring
8-sided shaft SW40
with external fold
Do not use
8-sided shaft SW40
with internal fold!
Suspension spring
INSTALLATION INSTRUCTIONS
3T-MOTORS Radio tubular motors | Installation instructions

12
INSTALLATION RADIO AWNING MOTOR
1Preparation:
•Screw in awning & secure with straps or ropes.
•Remove awning from wall bracket & place on safe surface.
2Prepare motor for installation:
•Slide limit switch adapter ush against motor head. >g. 2.1 / 2.2
•Secure the shaft adapter with the supplied securing bracket. >g. 2.3 / 2.4
3Installation awning motor:
•Remove the cover to access the side bearing (also awning bracket)
and fastening screws. >g. 3.1
•Loosen the screw that secures the side bearing to the support tube. >g. 3.2
•Remove all screws connecting the side bearing
and the crank mechanism. >g. 3.3
•Remove the side bearing from the support tube. >g. 3.4
•Remove the crank mechanism. >g. 3.5
Attention:
Awning arms are under strong tension!
2.1 2.2 2.3 2.4
3.1 3.2 3.2 3.4
•Remove the shaft capsule from the shaft. >g. 3.6
If the shaft capsule is tight, use a hammer and screwdriver.
Be careful not to damage the shaft.
•Push the awning motor with shaft adapter rst into the shaft. >g. 3.7
•Make sure motor head & limit switch adapter are ush in shaft.
•Screw the universal bearing onto the side bearing on the side
facing the awning shaft. >g. 3.8
3.5 3.6 3.7 3.8
INSTALLATION INSTRUCTIONS
3T-MOTORS Radio tubular motors | Installation instructions
Limit switch adapter
Motor head
Securing bracket
Click
Shaft adapter
Side bearing
Cover
Support tube
Side bearing
Crank mechanism
Support tube
Shaft capsule
Shaft &
wound up
Awning
Universal
bearing
Shaft &
wound up
Awning

13
•Slide the side bearing with universal bearing onto the support tube & fasten. >g. 3.9
•Ensure that the motor square spigot is properly engaged in the universal bearing. >g. 3.10
•Secure the motor square spigot with the supplied cotter pin. >g. 3.11
•Attach the cover to the side bearing. >g. 3.12
•Install awning & release fuses.
4Awning motor wiring:
•Connect the radio awning motor to the mains and, if necessary, connect the rocker switch to the motor cable.
•The electrical connection of the roller shutter motor and control unit may only be carried out by qualied personnel.
3.9 3.10 3 .11 3.12
1 (L1)
2 (N)
3 (PE)
2
3 (L1)
4 (N)
5 (PE)
1
•Use the enclosed wire end caps to insulate free wire ends of the
motor cable. If no rocker switch is connected the black and white
wires are unused and must be insulated. To do this, slide the wire
end caps onto the wire ends and press them together with crimping
pliers or combination pliers.
5Programming radio transmitter:
•Pair the radio hand-held transmitter to the awning motor. See Programming radio transmitter (page 15).
•If the direction of rotation is reversed, please change it with the paired radio hand-held transmitter.
> Changing the direction of rotation of the radio motor (Page 15).
INSTALLATION INSTRUCTIONS
3T-MOTORS Radio tubular motors | Installation instructions
Side bearing &
Universal bearing
Support tube
Cotter pin Side bearing
Cover
Rocker switch
Shutter motor
230 V / 50 Hz
Power grid
230 V / 50 Hz
1) white = Control line downward or upward
2) black = Pole contact rocker switch
3) brown = L1 / Phase
4) blue = N Neutral conductor
5) green/yellow = PE Protective conductor
1) brown / black = L1 / Phase
2) blue = N Neutral conductor
3) green/yellow = PE Protective conductor Wire end caps
6Setting the end positions:
•The end points are set by radio hand-held transmitter.
•See programming end positions (page 16).

14
Programming:
•The programming interval for radio transmitters is 6 seconds. After 6 seconds, the radio transmitter terminates programming.
•The radio motor conrms programming steps with beeps and a short down and up , perform the next step after the hint.
Setting the end positions:
•After the end points have been set, they cannot be saved at the same position when readjusting.
•After setting the endpoints, they are saved in case of power failure.
•When the endpoints are deleted, the upper and lower endpoints are deleted.
•The programming of the end points is terminated after 2 minutes if no commands are received.
Number of programmable radio hand-held transmitters:
•The radio motor can store up to 20 radio handheld transmitters / radio transmitters.
•If additional transmitters are stored, the transmitter that was paired rst will be overwritten.
Important explanations on setting and programming the motor.
Please read carefully before setting the motor.
NOTES ON THE SETTTING OF THE MOTOR
FUNCTIONS P1 BUTTON
1. Pairing handheld transmitter / Pairing additional handheld transmitters:
The motor is ready
for pairing a handheld
transmitter / further
handheld transmitters
3 x beep from motor (pairing of further handheld transmitters)
Press button P1 once
1 x long beep from motor + down and up (no handheld transmitter paired)
+
2. Change the direction of rotation of the radio motor:
Press P1 button for 5 sec. + keep pressed
+
3 x beep from motor + down and up
Release P1 button
The direction of rotation
of the motor is changed
Keep P1 button pressed
+
3 x beep from motor + down and up (after 5 Sec.)
Release P1 button
(after 8 Sec.)
All motor settings
are reset
down and up
3. Reset motor settings:
after that 3 x beep from motor + down and up
+
3T-MOTORS Radio tubular motors | Notes on the setting of the motor

15
+
Pairing handheld transmitters
with Radio motor Type RB:
The motor conrms
the programming
with 3 beeps and
down and up
OK
Beep from motor
+ down and up
Change direction of rotation
of radio motor:
The motor conrms
the programming
with 3 beeps and
down and up
OK
1 x Press button
P2 / Set Up
After switching on the power supply / Pressing P1 button the programming (pressing the
buttons) must be done within 10 sec. otherwise the motor returns to its original state.
1 x Press P1 button
or
1 x Press button
P2 / Set Up
1 x Press Up-button
or Down-button
+
+
Beep from motor
+ down and up
+
The motor conrms
the programming
with 3 beeps and
down and up
OK
+
++
Switch on power supply.
Only switch the affected motor
to voltage.
1 x Long beep from motor
+ down and up
+
1 x Long beep from motor
+ down and up
+
Press Up-button + Down-button
simultaneously for 2 sec.
If the up and down buttons triggers the wrong direction of travel, you can
change the direction of rotation of the radio motor with this programming.
Check whether the direction of rotation is correct before setting the end
points. A later change of the direction of rotation is only possible via the P1
button on the motor head!
PROGRAMMING RADIO TRANSMITTER
3T-MOTORS Radio tubular motors | Programming radio transmitter
Important when teaching, changing or deleting transmitters:
Only one relevant motor may be switched to voltage!
Several radio motors or radio receivers can be programmed to form a group with the same transmission channel.
For multi-channel transmitters, channel by channel must be taught or transferred.
1 x Press button
P2 / Set Up
1 x Press button
P2 / Set Up
1 x Press Up-button
or Down-button
Beep from motor
+ down and up
Beep from motor
+ down and up

16
Press and hold
Stop-button for 5 sec.
Press Up-button*,
Move roller shutter to desired position
1 x Press
Up-button
PROGRAMMING END POSITIONS
Attention! If the upper end point is set, do not move the motor
upwards! The motor will not stop at the upper end point until the
lower end point has also been set.
1. Initialization of the
end point setting:
Beep from motor
+ down and up
1 x Press button
P2 / Set Up
1 x Press button
P2 / Set Up
+
Beep from motor
+ down and up
+
+
The motor conrms
the programming
with 3 beeps and
down and up
OK
2. Setting upper end point:
1 x Press Stop-button
to stop motor
+
The motor conrms
the programming
with 3 beeps and
down and up
OK
3. Setting lower end point:
Press and hold
Stop-button for 5 sec.
Press Down-button*,
Move roller shutter to desired position
1 x Press Stop-button
to stop motor
+
The motor conrms
the programming
with 3 beeps and
down and up
OK
When setting the upper and lower end points, the motor can be switched to jog mode
during travel. To do this, press the P2 button during upward or downward travel. The motor
then moves up or down in small steps, which facilitates the precise setting of the end
points.
*
Activate jog mode:
During ascent or descent
1 x Press
button P2 / Set Up
3T-MOTORS Radio tubular motors | Programming end positions

17
1 x Press
Stop-button
Hold down Up- + Down-button
simultaneously for 5 sec.
Move to end point with
Up- or Down-button
PROGRAMMING END / INTERMEDIATE POSITIONS
Change end points: 3 x Beep from motor
+ down and up
+
+
The motor conrms
the programming
with 3 beeps and
down and up
OK
Move to new end point with
Up- or Down-button
Press and hold
Stop-button for 5 sec.
1 x Press
Stop-button
Setting intermediate position:
+
The motor conrms
the programming
with 3 beeps and
3 x down and up
OK
Move to intermediate position
with Up- or Down-button
1 x Press
Stop-button
1 x Press button
P2 / Set Up
1 x Press
Stop-button
Beep from motor
+ down and up
+
Beep from motor
+ down and up
+
Move to intermediate position:
The motor moves
to the set
intermediate position
and stops
Press and hold
Stop-button for 2 sec.
1 x Press
Stop-button
Beep from motor
+ down and up
1 x Press button
P2 / Set Up
+
Beep from motor
+ down and up
+
+
The motor conrms
the programming
with a long beep
and down and up
OK
Delete intermediate position:
3T-MOTORS Radio tubular motors | Programming end / intermediate positions

18
1 x Press
Stop-button
1 x Press button
P2 / Set Up
a
Hold down Up- + Down-button
simultaneously
1 x Press button
P2 / Set Up
1 x Press button
P2 / Set Up
Pairing another handheld transmitter:
Beep from motor
+ down and up
1 x Press button
P2 / Set Up
+
Beep from motor
+ down and up
+
+
The motor conrms
the programming
with 3 beeps and
down and up
OK
aHandheld transmitter already paired
bNew handheld transmitter / not paired
ab
or
+
The motor conrms
the programming
with 7 beeps and
down and up
OK
b b
1 x Press P1 button
3 x Beep
from motor
Note: The endpoints must already be programmed
to be able to use this method.
1 x Press button
P2 / Set Up
Delete handheld transmitter:
Beep from motor
+ down and up
1 x Press button
P2 / Set Up
+
Beep from motor
+ down and up
+
+
The motor conrms
the programming
with 3 beeps and
down and up
OK
abHandheld transmitter already paired
bHandheld transmitter to be deleted
ab
1 x Press button
P2 / Set Up
Delete all handheld transmitter:
Beep from motor
+ down and up
1 x Press button
P2 / Set Up
+
Beep from motor
+ down and up
+
+
The motor conrms
the programming
with 3 beeps and
down and up
OK
a
PROGRAMMING RADIO TRANSMITTER
3T-MOTORS Radio tubular motors | Programming radio transmitter

19
1 x Press button
P2 / Set Up
PROGRAMMING
Jog mode: Note: In jog mode, press and hold the up or down button
for 2 seconds to activate continuous up or down travel.
1 x Press
Down-button
1 x Press
Up-button
Beep from motor
+ down and up
1 x Press button
P2 / Set Up
+
Beep from motor
+ down and up
+
+
The motor conrms
the programming
with a long beep
and down and up
OFF
The motor conrms
the programming
with 3 x beep
and 3 x down and up
ON
+
Delete end
points:
1 x Press
Down-button
Beep from motor
+ down and up
1 x Press button
P2 / Set Up
+
Beep from motor
+ down and up
+
+
The motor conrms
the programming
with 3 x beep
and down and up
OK
Activate / deactivate initialization of the
pairing process by switching on the power
supply:
ON: Initialization of the pairing process for handheld transmitters via
P1 button or switching on the power supply.
OFF: Initialization of pairing process for handheld transmitter only via
P1 button
1 x Press
Up-button
1 x Press
Up-button
Beep from motor
+ down and up
1 x Press button
P2 / Set Up
+
Beep from motor
+ down and up
+
+
The motor conrms
the programming
with a long beep
and down and up
OFF
The motor conrms
the programming
with 3 x beep
and 3 x down and up
ON
+
Note: The intermediate position is removed by deleting
the end points and must be reset if necessary.
3T-MOTORS Radio tubular motors | Programming

20
Note:
The following 3T-MOTORS transmitters do not have a P2 / Set Up button:
Setting
Pairing handheld transmitter
Change direction of rotation
Setting end points
Changing end points
Intermediate position
Pairing another handheld
transmitter
Delete handheld transmitter
Delete all handheld transmitter
Jog mode
Delete end points
Activate / deactivate
initialization of the pairing
process by switching on the
power supply
Programming
P1 or switch on power supply > P2 > P2 > Up oder Down
Up + Down simultaneously (2 sec.)
Initialization of the end point setting
Setting upper end point
Setting lower end point
Jog mode
Changing upper end point
Changing lower end point
Setting intermediate position
Move to intermediate position
Delete intermediate position
P2 (a) > P2 (a) > P2 (b)
P1 > Up (b) + Down (b)
P2 (a) > P2 (a) > P2 (b)
P2 > Stop > P2
P2 > Up > Ab
P2 > Down > P2
P2 > Up > Auf
P2 > Up > P2
Up > Stop > Stop (5 sec.)
Down > Stop > Stop (5 sec.)
During ascent or descent > P2
Up > Up + Down simultaneously (5 sec.) > Up or Down > Stop (5 sec.)
Down > Up + Down simultaneously (5 sec.) > Up or Down > Stop (5 sec.)
Up or Down > Stop > P2 > Stop > Stop
Stop (2 sec.)
P2 > Stop > Stop
a = transmitter already paired / b = transmitter to be deleted
b = new handheld transmitter
a = transmitter already paired / b = transmitter to be deleted
Quick overview programming commands
1
2
3
4
5
6
7
8
9
10
11
PROGRAMMING
3T-MOTORS Radio tubular motors | Programming
Radio wall transmitter
WS1
Radio wall transmitter
WS2
Radio wall transmitter
WSE2
Radio timer
WSTF1
Radio timer
WSTF5
Radio mini transmitter
FMSF
Button combination:
Press Up + Stop buttons simultaneously (FMSF / WS1 / WS2 / WSE2).
Press the Set and Mode buttons simultaneously (WSTF1 / WSTF5).
This manual suits for next models
7
Table of contents
Other 3T-Components Engine manuals
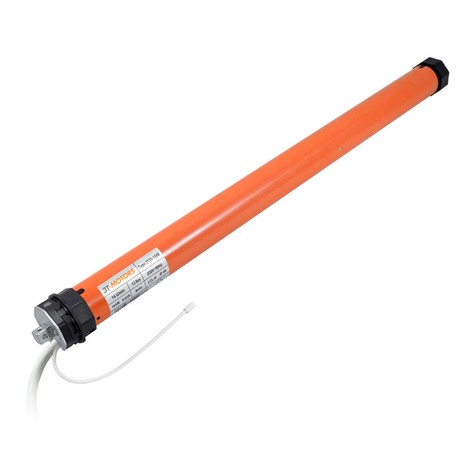
3T-Components
3T-Components 3T-MOTORS 3T45 Manual
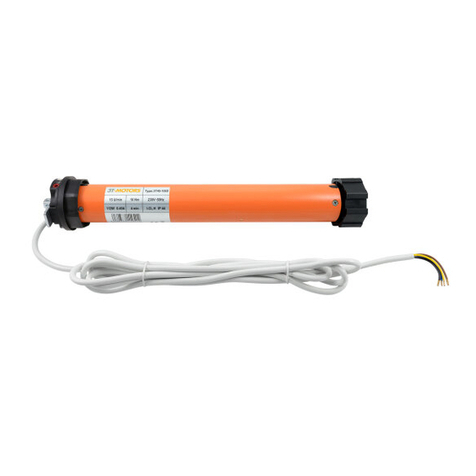
3T-Components
3T-Components 3T-MOTORS 3T45-SD Manual
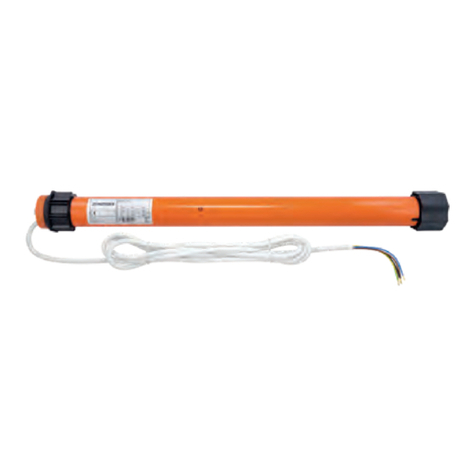
3T-Components
3T-Components 3T-MOTORS 3T45-E Manual

3T-Components
3T-Components 3T-MOTORS 3T35-R Manual
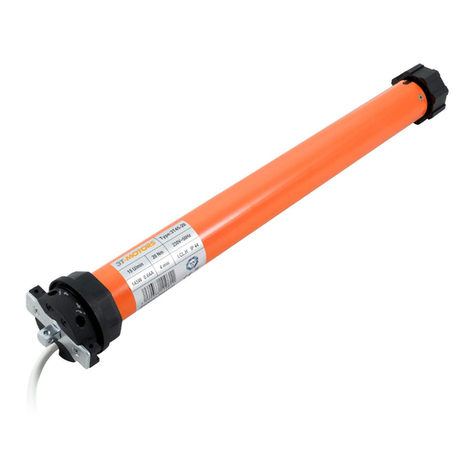
3T-Components
3T-Components 3T-MOTORS 3T45-20 Manual
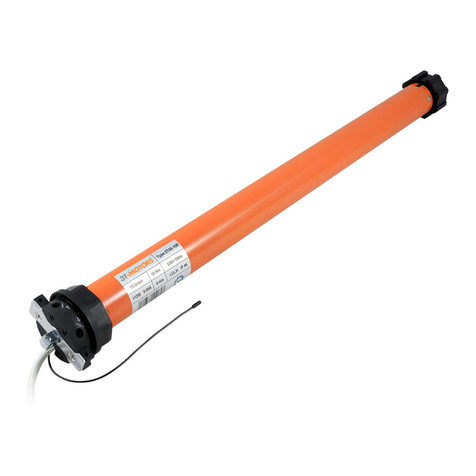
3T-Components
3T-Components 3T-MOTORS 3T45-10R Manual