ABB VMS User manual

Modular Insulated Distribution System - VMS
User manual

VMS user manual
2
Table of contents
1. Introduction …………………………………………………..…..3
2. Dimensions and Technical Spec ………………………………………...…………….3
3. Shipping, Packing, Lifting …………………………………..…….…….………4
4. Installation ……………………………….……………..….……5
5. Working with the system ……..……………………………………….……....9
6. Maintenance ……………………………………..…………….….10
7. Contact details ……………………………………………………….12

VMS user manual
3
Introduction
The Modular Insulated Distribution System - VMS consists of 5 standard dimensions
(H x W from 320 x 220mm up to 640 x 440mm) in one depth 180mm with the possibility
to add depth extension frames for each size with 75mm depth
The system can be provided as loose components or factory assembled.
Designed for wall mounting or floor standing installation
Modular coupling possibilities in width and height.
Standards: EN/IEC 61439-2
EN/IEC 60529
EN/IEC 62262
Dimensions and Technical Specifications
Type Designation : VMS
Type of material : Glass fiber reinforced Polycarbonate
Method of fixing : Wall, floor
Intended location : Indoor & Limited Outdoor
Degree of protection
IP-code : Up to IP65
IK-code : Up to IK07

VMS user manual
4
Shipping, Packing and Lifting
1) A knife or a pair of scissors should be used to cut the non-metallic packing of the
enclosure. Be aware not to damage the enclosure itself by opening the packaging
with a sharp tool.
2) Check the enclosure for any kind of damage as soon as it is unpacked. If found
damaged, immediately contact the manufacturer at the numbers mentioned in
‘contact details’ section.
3) The company cannot be held responsible for any damage caused due to improper
storing.
CAUTION:
Improper storing can cause damage to the enclosure.
Do not stack one enclosure over another while storing or during transportation.
4) Use a pallet truck for transportation of the enclosure. It is advised to unpack the
pedestal only at the time of final installation.

VMS user manual
5
Installation
The enclosure is a modular type distribution system, designed for wall mounting or floor
standing for use indoor and outdoor (with limited exposure to UV radiation).
The enclosure is designed with covers that can be opened by authorized operating
personnel only.
Procedure for installing the enclosure on a wall:
-Remove any obstruction, dirt etc. from the location.
-Make sure the floor- and wall surface is levelled
-The enclosure can be mounted on a wall by using brackets (up to 5 enclosures) or
a supporting frame. The brackets can be positioned 0°, 45°, 90°, screw through the
base corner holes.
Installation of the mounting brackets:

VMS user manual
6
Installation of the supporting frame:
Wall mounting of small units can be made using stainless steel fixing brackets. For
mounting and handling of units of more than five enclosures, a supporting frame is
compulsory.
- The supporting frame consists of at least two horizontal C-profiles (= the length of the
assembly width) and a number of two vertical C-profiles (equal to the number of vertical
sections +1).
- If the unit height is greater than 1000 mm, three horizontal C-profiles will be used.
- The vertical C-profiles are 140 mm longer than the height of the assembled panel.
- The frame and the enclosure assembly should be mounted simultaneously.
Horizontal and vertical C-profiles of the first row of enclosures are assembled together
by clamping brackets and sliding nuts. The next clamping brackets are mounted on the
horizontal profile.
The first row of enclosures is then mounted on the vertical profiles with the clamping
plates.

VMS user manual
7
Following rows are then assembled the same way.
Frame and enclosure assemblies are mounted simultaneously.

VMS user manual
8
Installation on the floor/wall:
Floor/wall mounting can be performed by using the vertical Z-profiles at each
partition/extension.
The Z-profiles are bolted together by means of 2 C-profiles and sliding nuts + M8 bolts
for fixation. The VMS boxes can be mounted directly on the front of the Z-profiles by
means of M5 x 16 Torx screws . The Z-profiles can be mounted on the floor using the
stand supports + .

VMS user manual
9
Working with the distribution system
In general, all operations of switches and breakers can be performed in front of the
covers. In cases where feeder switches are located behind the covers (or for
replacement of fuses) the cover should be opened.
Opening the covers:
1. Unlock the cover(s). Use an appropriate screwdriver that matches the cover
screws.
2. Remove the cover(s).
3. Feeder switches can be operated / Fuses can be replaced
In cases where access to the busbar system is required, additionally the cover plates can
be removed by using a slotted screw driver
The protective space is now accessible and all necessary service and administrating
operations can be performed.

VMS user manual
10
Maintenance
Maintenance intervals:
The maintenance intervals depend on the intensity of use of the switchgear
installed in the switchboard and can be either preventive or repair work, but should
always be in accordance with local regulations and standards (i.e. NEN3140).
Attention:
Observe all relevant operating instructions of the electrical components as well as
local requirements, regulations and standards (i.e. NEN3140).
Inspection interval:
A visual inspection as well as a control of mechanical functions (e.g. interlocks etc.)
of the assembly should be done every 4 years as a minimum.
An interval of <= 1 year is recommended.
The following checklist can be applied as a guideline during inspection.
#
Inspection / corrective action
1
inspection of service conditions
2
(visual) inspection of the assembly
3
inspection of the ventilation openings clean ventilation openings / change dust
filters
4
inspection of measures to achieve IP rating, no ingress of condensation. Unused
gland opening
5
inspection of cables & glanding’s
6
inspection on the effects of pollution, clean with dry piece of cloth or use
vacuum cleaner / do not use high pressure air!
7
inspection for damages
8
inspection on the effects of corrosion, repair failures on surface / make dry if
necessary
9
inspection of sub-assemblies & electrical components maintenance in
accordance with relevant component manuals
10
inspection of connectors & terminals
11
check correct protection of electrical components & cables, change fuses if
necessary (decoloring, correctly placed)
12
check settings of electrical components (e.g. overload & short circuit protection)
correct settings according the documentation of the electrical component. Test
Residual Current (earth leakage) devices.
13
inspection of plug-in contacts remove old grease, put new grease on
14
inspection of measures against electrical shock (PE conductor, PE connections)
check insulation resistance (earth resistance /dielectric testing).
15
check torque values for electrical connections (see torque values for electrical
connections), µΩ testing of busbar system

VMS user manual
11
GE Odink & Koenderink shall not be responsible for any undesirable situation arising due
to the above-mentioned reasons or improper or no maintenance, cleaning or inspection
as specified in this manual.
WARNINGS, CAUTIONS, NOTES
WARNING
Warning notices are used to emphasize that hazardous voltage, currents, or other
conditions that could cause personal injury are present in this equipment or may be
associated with its use.
Warning notices are also used for situations in which inattention or lack of
equipment or knowledge could cause either personal injury or damage to equipment.
CAUTION
Caution notices are used for situations in which equipment might be damaged if
care is not taken.
NOTE
Notes call attention to information that is especially significant to understanding
and operating the equipment.
This document is based on information available at the time of its publication.
While efforts have been made to ensure accuracy, the information contained herein does
not cover all details or variations in hardware and software, nor does it provide for every
possible contingency in connection with installation, operation, and maintenance.
Features may be described herein that are not present in all hardware and software
systems. GE assumes no obligation of notice to holders of this document with respect to
changes subsequently made.
GE makes no representation or warranty, expressed, implied, or statutory, with
respect to, and assumes no responsibility for the accuracy, completeness, sufficiency, or
usefulness of the information contained herein. No warrantees of merchantability or
fitness for purpose shall apply.
Table of contents
Other ABB Home Automation manuals
Popular Home Automation manuals by other brands
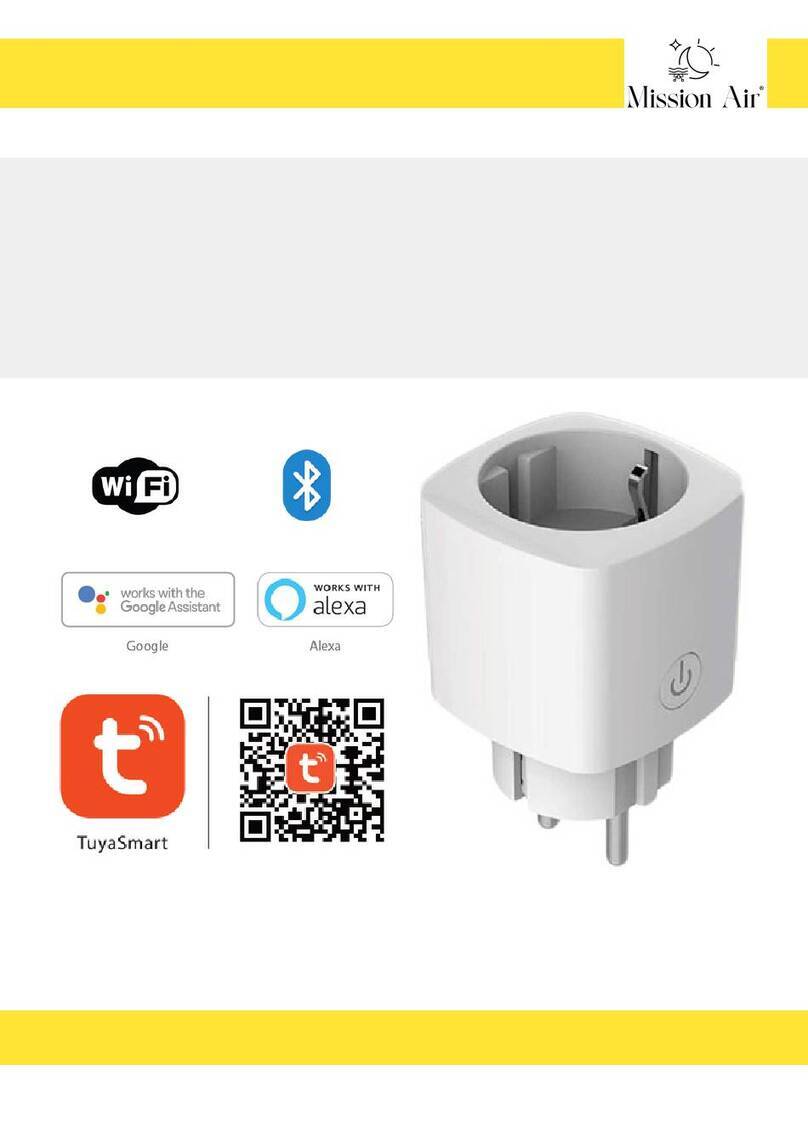
Mission Air
Mission Air SMART PLUG user manual

Dome
Dome WR01Z manual

nVent Hoffman
nVent Hoffman RackChiller CDU800 Operation and instruction manual
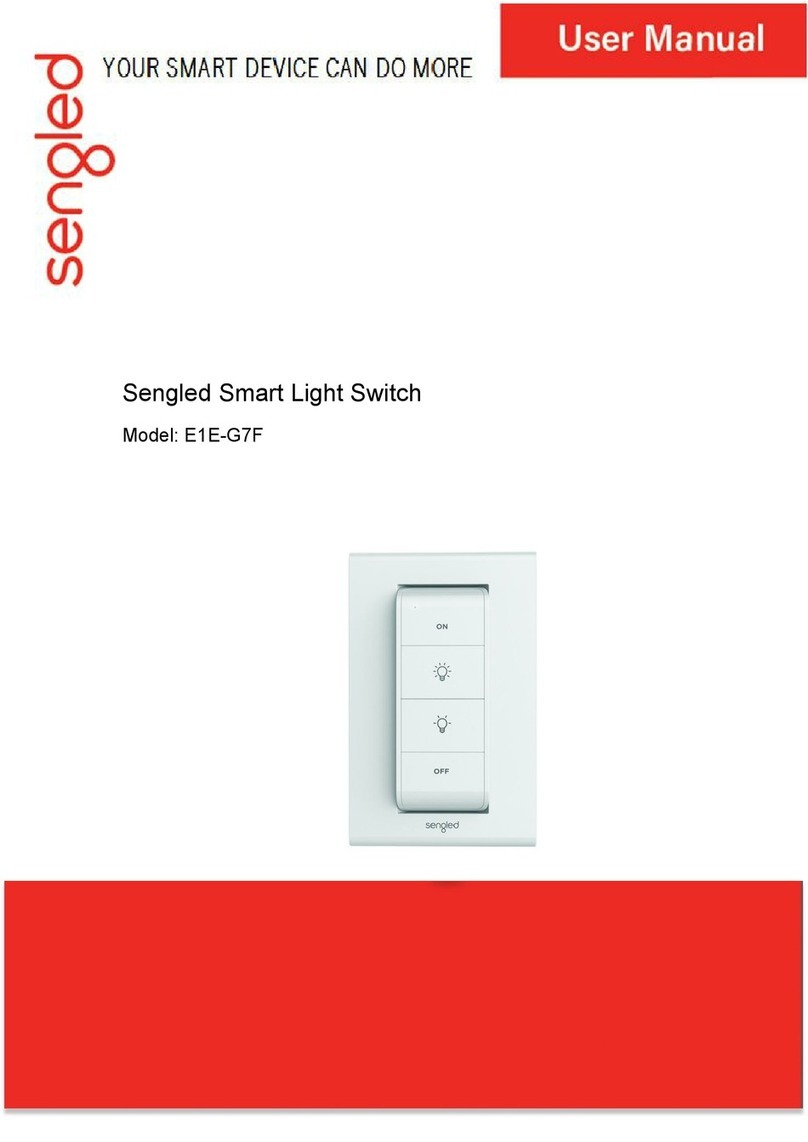
Sengled
Sengled E1E-G7F user manual
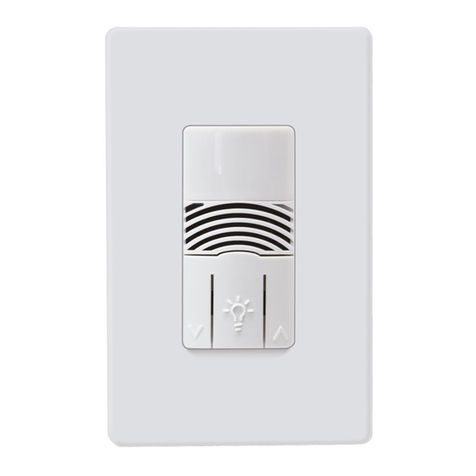
Cooper Lighting
Cooper Lighting Greengate NeoSwitch ONW-D-1001-MV-W installation instructions
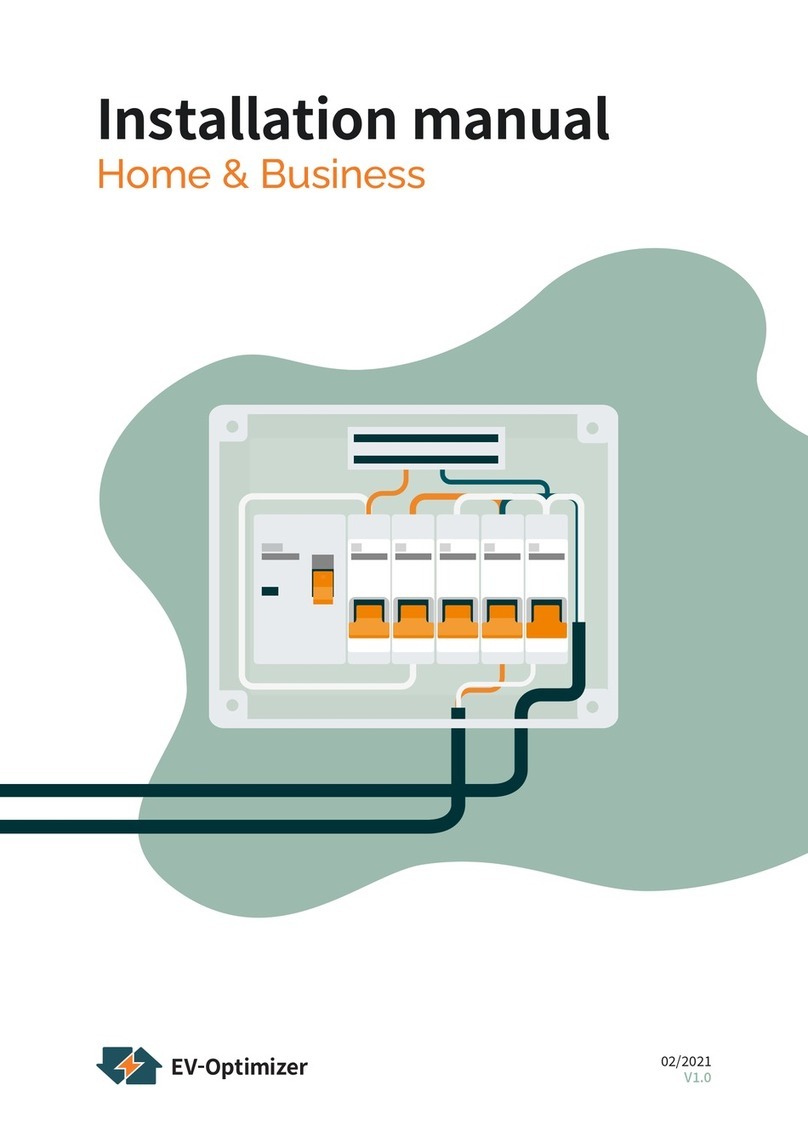
EV-OPTIMIZER
EV-OPTIMIZER EV-OPTIMIZER manual