ABB 2600T Series Guide

- 1 -
Instruction for installation
and commissioning
PED/262_4D_9
FieldIT
2600T Series Pressure Transmitters
Models 264B/D/V/P

- 2 -
Health and Safety
To ensure that our products are safe and without risk to health, the following points must be noted:
1. The relevant sections of these instructions must be read carefully before proceeding.
2. Warning labels on containers and packages must be observed.
3. Installation, operation, maintenance and servicing must only be carried out by suitably trained personnel and in accordance with the
information given. Any deviation from these instructions, will transfer the complete liability to the user.
4. Normal safety precautions must be taken to avoid the possibility of an accident occurring when operating in conditions of high
pressure and/or temperature.
5. Chemicals must be stored away from heat, protected from temperature extremes and powders kept dry. Normal safe handling
procedures must be used.
6. When disposing of chemicals ensure that no two chemicals are mixed.
Safety advice concerning the use of the equipment described in this manual or any relevant hazard data sheets (where applicable) may
be obtained from the Company address on the back cover, together with servicing and spares information.
The Company
We are an established world force in the design and manufacture of
instrumentation for industrial process control, flow measurement, gas and
liquid analysis and environmental applications.
As a part of ABB, a world leader in process automation technology, we offer
customers application expertise, service and support worldwide.
We are committed to teamwork, high quality manufacturing, advanced
technology and unrivalled service and support.
The quality, accuracy and performance of the Company’s products result from
over 100 years experience, combined with a continuous program of innovative
design and development to incorporate the latest technology.
The NAMAS Calibration Laboratory No. 0255(B) is just one of the ten flow
calibration plants operated by the Company, and is indicative of our dedication
to quality and accuracy.
Use of Instructions
Warning.
An instruction that draws attention to the risk of injury or
death.
Caution.
An instruction that draws attention to the risk of damage
to the product, process or surroundings.
Although Warning hazards are related to personal injury, and Caution hazards are associated with equipment or property
damage, it must be understood that operation of damaged equipment could, under certain operational conditions, result in
degraded process system performance leading to personal injury or death. Therefore, comply fully with all Warning and
Caution notices.
Information in this manual is intended only to assist our customers in the efficient operation of our equipment. Use of this manual
for any other purpose is specifically prohibited and its contents are not to be reproduced in full or part without prior approval
of Technical Communications Department, ABB.
✶
Note.
Clarification of an instruction or additional information.
Information.
Further reference for more detailed information or
technical details.
ABB
EN ISO 9001: 1994
Cert. No. Q5907
ISO 9001: 2000
Cert. No. 9/90A
Cert. No. 0255
0255

- 3 -
Section Page
1. INTRODUCTION........................................................ 3
2. PHASE 1 - PRELIMINARY CHECKS
2.1 EXPLOSION PROTECTION ............................ 4
2.2 PRESSURE AND TEMPERATURE LIMITS .... 5
2.3 OPERATING VOLTAGE LIMITS ...................... 5
2.4 ENVIRONMETAL LIMITS ................................. 6
2.4.1 Electromagnetic compatibility (EMC) ........ 6
2.4.2 Humidity .................................................... 6
2.4.3 Vibration resistance .................................. 6
2.4.4 Shock resistance ...................................... 6
2.4.5 Wet and dust-laden atmospheres ............. 6
2.4.6 Fill fluid warning ........................................ 6
2.5 CORROSION ................................................... 6
2.6 SPECIAL SERVICES ....................................... 6
3. PHASE 2 - TRANSMITTER INSTALLATION
3.1 TRANSMITTER LOCATION ............................. 7
3.2 TRANSMITTER MOUNTING .......................... 12
3.3 PROCESS CONNECTIONS ........................... 14
3.4 ROTATION ..................................................... 15
4. PHASE 3 - TRANSMITTER WIRING
4.1 PROTECTIVE GROUNDING ......................... 16
4.2 ELECTRICAL CONNECTIONS ...................... 16
4.3 SUPPLY WIRING REQUIREMENTS ............. 17
5. PHASE 4 - TRANSMITTER OPERATION
5.1 FLOW MEASUREMENT ................................ 18
5.2 LEVEL MEASUREMENT ................................ 19
5.3 PRESSURE MEASUREMENTS ..................... 20
CONTENTS 1. INTRODUCTION
This document provides basic instruction for the installation
and commissioning of the ABB 2600T differential pressure
transmitter. This transmitter is connected to a process by
means of impulse lines and can measure Pressure, Differential
pressure or Absolute pressure. The measurement is transmitted
to a control system by means of a 4-20 mA signal with a
superimposed digital signal (Hart) or by means of a digital
transmission protocols (PROFIBUS or FOUNDATION
Fieldbus). The measure can also be indicated by means of one
of the (optional) local or remote displays.
Instructions for preliminary checks, proper transmitter location,
installation, wiring, power-up and zero calibration (trimming) of
the transmitter are listed in the following.
In order to assure operator and plant safety it is essential that
the installation is carried out by personnel suitably trained on
the local applicable codes on hazardous location, electrical
wiring and mechanical piping. Please read these instructions
carefully before installing the transmitter. The protection
provided by the equipment may be impaired if the equipment
is used in a manner not specified.
For more information refer to the reference manual (document
26X B/V/D/P HART Pressure Transmitters - Operating
Instruction ) and, where applicable, the manuals relevant to
PROFIBUS or FOUNDATION Fieldbus transmitters. These
manuals are available also in electronic format on www.abb.com
searching for the keyword “IM/*26*” or from local ABB
representatives.

- 4 -
Fig. 1 - Product identification
Ref. B
Primary Unit
Ref. A
2. PRELIMINARY CHECKS
Before mounting the transmitter, check the compatibility with
the following measurement and safety requirements:
-Explosion protection
-Pressure rating
-Operating voltage limits
-Process and ambient Temperature limits
-Environmental limits
-Corrosion
2.1 EXPLOSION PROTECTION
Explosions could result in death or serious injury. Installation
of this transmitter in a Hazardous Area (i.e. a potentially
explosive atmosphere) must be in accordance with the
appropriate local, national, and international standards, codes,
and practices. Please review the approvals and marking of the
transmitter shown on the label attached to the transmitter (see
figure 1 - Ref. C), note that this is a sample, read the values on
the real label; if this label is not present, the instrument is not
suitable for installation in Hazardous Areas. It is necessary to
Ref. C
Ref. D
Ref. D
Ref. A
DIN TYPE
HOUSING
BARREL TYPE
HOUSING
SERIAL
NUMBER
URL
DIAPHRAGM
MATERIAL
FILL
FLUID
check that all the parameters listed on this label (or on the
certificates enclosed with the transmitter) are in accordance
with the requirements of the area where the transmitter is going
to be installed. See the reference manual for an explanation of
each parameter related to "EX SAFETY". In case of any
discrepancy do not install the transmitter.
For pressure transmitter with ATEX combined approval, before
installation, the transmitter should be permanently marked with
the selected Protection Concept (e.g. intrinsically safe or
explosion proof) on the safety label. The transmitter can be
used only in accordance with this Protection Concept for its
whole life.
Note - The transmitter may be used as a safety
accessory (as defined by the Pressure Equipment
Directive 97/23/EC) i.e. as part of a shutdown system. In
this case it is recommended to select the correct fail safe
mode for the 4-20 mA signal (as per Namur NE43
recommendation). See also the instructions relevant to
fail safe selection (Up/Down scale mode) in the addendum
to the instruction manual on "Use of hardware links on the
secondary electronics" .
PHASE 1 - PRELIMINARY CHECKS
not available for U.S.

- 5 -
2.2 PRESSURE AND TEMPERATURE LIMITS
The maximum allowable pressure (PS) and maximum/minimum
allowable temperature (TS) of the pressure transmitter, for
the European market are indicated on the tag plate (ref. D of
Figure 1), in the U.S. please refer to the instrument data sheets
available at: http://138.221.224.36 searching for "264 and
sheet" or from local ABB representatives.
PS and TS are defined according to the European Pressure
Equipment Directive 97/23/EC (PED). For Temperature, the
listing is for the min and max process temperature limits at
which the instrument can be exposed, for Pressure this listing
should be considered the maximum working pressure limit to
which the transmitter can be exposed without damage (to the
transmitter). These limits are valid when the transmitter is
installed according to the instructions in this manual.
WARNING !
For potentially explosive atmosphere applications see the
temperature range specified in the certificate/approval
relevant to the intended type of protection.
PS values
The transmitter can be exposed without leaking to line pressure
of up to:
Models 264DS, 264PS, 264VS, 264DF, 264PF, 264VF
- 2MPa, 20bar, 290psi for sensor code A
- 7MPa, 70bar, 1015psi for sensor code B
- 16MPa, 160bar, 2320psi for sensor code E
- 21MPa, 210bar, 3045psi for sensor codes F to S
- 1MPa, 10bar, 145psi for Kynar-PVDF
- 16MPa, 160bar, 2320psi for AISI 316 ss NACE bolting
Model 264BS
- 41MPa, 410bar, 5945psi
Model 264DH
- 230psi for ASME CL150 flange
- 600psi for ASME CL300 flange
The pressure limit decreases with increasing temperature
above 100°F (38°C), according to ASME B16.5 standards.
- 13.5bar for EN PN16 flange
- 33.8bar for EN PN40 flange
The pressure limit decreases with increasing temperature
above 50°C according to EN 1092-1 standards.
Proof pressure
The transmitter can be exposed without leaking to line pressure
of up to:
Models 264DS, 264PS, 264VS, 264DF, 264PF, 264VF
- 48MPa, 480bar, 6960psi
Model 264BS
- 61.5MPa, 615bar, 8917psi
Model 264DH
- up to two times the flange rating.
Meet ANSI/ISA–S 82.03 hydrostatic test requirements and
SAMA PMC 27.1.
Other 264Dx models using direct mount and/or remote
seal(s) are compliant to SEP (Sound Engineering Practice).
PHASE 1 - PRELIMINARY CHECKS
WARNING !
In order to assure the proper containment of the process
fluid by the transmitter, it is recommended that any part,
related to process fluid containment, be supplied only by
ABB or authorized agents.
The spare parts list is available at: http://138.221.224.36
searching for “SL/26*” or from local ABB representatives.
The storage conditions must be within the following limits,
Lower limit: –50°C (–58°F); –40°C (–40°F) for LCD indicators
Upper limit: +85°C (+185°F) otherwise some material such as
gaskets may be damaged and cannot assure proper fluid
containment.
2.3 OPERATING VOLTAGE LIMITS
The transmitter is designed to provide a current transmission
signal of 4 to 20 mA dc on the same wires that are carrying the
power supply (two-wire transmitter).
The transmitter operates on a minimum voltage of 10.5 Vdc to
a maximum of 42 Vdc and is protected against polarity inversion.
The transmitter operates from 10.5 to 42 Vdc with no load.
The operating voltages range for fieldbus versions, both polarity
independent, are as follows:
-PROFIBUS PA from 9 to 32 Vdc (17.5 Vdc for EEx ia)
-FOUNDATION Fieldbus from 9 to 32 Vdc (for EEx ia
applications 24 Vdc max with entity or 17.5 Vdc max with
FISCO)
Some communication problems may occur, in cases the loop
resistance is increased by long wires or additional devices like
meters, safety barriers, surge protection, remote indicators,
etc.
If this is the case, please refer to the reference manual for
further details (the manual is available at www.abb.com inserting
in the “search” tool the keyword “IM/26X”) or from local ABB
representatives.
For EEx ia and intrinsically safe (FM, CSA and SAA) approvals,
the power supply must not exceed 30 Vdc. In some countries
the maximum power supply voltage is limited to a lower value.
The transmitter insulation resistance (terminals to earth) is
>100MΩat 1000VDC.
CAUTION Do not arc-weld any pipe-connected to
the transmitter as this could break the electrical insulation
and damage the electronic part of the transmitter.

- 6 -
2.5 CORROSION
Be sure that the process fluid is compatible with the material of
the process flanges and sensor diaphragm.
A fluid / material compatibility table is available at www.abb.com
(inserting in the “search” tool the keyword “TB/COR”) or from
local ABB representatives.
NOTE
Data of the table are based on information from
manufacturers.
All data is based on a temperature of 20°C, 70°F unless
noted otherwise.
Since corrosion involves many more variables than this
table considers, such as trace contaminants, aeration or
temperature-concentration profile, stress corrosion cracking
and pitting, the table should be used only as a reference in
narrowing the choice of materials that merit further
investigation. Suitability of a particular material is best
determined by field test. At this purpose, please contact our
local ABB representatives.
WARNING
For safety purpose the design corrosion allowance of
differential pressure instrument flanges is of about 1.5 mm
0.04 in. Therefore from the viewpoint of safe containment
of liquids compatible with a specific material according to
the table, the expected instrument lifetime is more than 10
years, but the previous note apply.
2.6 SPECIAL SERVICES
In case of Oxygen or Hydrogen or other special services, the
transmitter has to be handled with a special care in order to
prevent contamination with impure substances. It is
recommended to use “sterile” gloves and that the removal of
protection bags be done only immediately before the installation.
Do not flush with impure fluids.
PHASE 1 - PRELIMINARY CHECKS
2.4 ENVIRONMENTAL LIMITS
2.4.1 Electromagnetic compatibility (EMC)
Complies with EN 50081–1 for emission and EN 50082–2 for
immunity requirements and test;
Radiated electromagnetic immunity level: 30V/m (according to
IEC 1000-4-3, EN61000-4-3).
Conducted electromagnetic immunity level : 30V (according to
IEC 1000-4-6, EN 61000-4-6).
Surge immunity level (with surge protector): 4kV (according to
IEC 1000-4-5 EN 61000-4-5).
Fast transient (Burst) immunity level: 4kV (according to IEC
1000-4-4 EN 61000-4-4).
2.4.2 Humidity
Relative humidity: up to 100% annual average
Condensing, icing: admissible
2.4.3 Vibration resistance
Accelerations up to 2g at frequencies up to 1000Hz
(according to IEC 60068-2-26)
2.4.4 Shock resistance
Acceleration: 50g
Duration: 11ms (according to IEC 60068-2-27)
WARNING !
Transmitters located in hazardous areas must be installed
in such a way to prevent the ignition of explosive atmosphere
because of impact and friction, even in case of rare events.
2.4.5 Wet and dust-laden atmospheres
The transmitter is dust and sand tight and protected against
immersion effects as defined by IEC EN 60529 (1989) to IP 67
(that can be considered equivalent to NEMA 4X and JIS
C0920).
2.4.6 Fill fluid warning
Be sure that the fill fluid (indicated on label Ref. B) can mix
safely with the process fluid in case of rupture of the sensor
membrane.

- 7 -
LH
AB
C
H L
B
A
C
Orifice plate
PHASE 2 - TRANSMITTER INSTALLATION
3. TRANSMITTER INSTALLATION
The following examples are standard mounting locations for instrumentation suitable for these main types of applications:
3.1 TRANSMITTER LOCATION
Flow gate valves
filling tees
vent valve
3-valve
manifold
Flow measurement with clean liquids or steam
(condensable vapor)
1. Place taps to the side of the line.
2. Mount beside or below the taps.
3. Mount the drain/vent valve upward.
4. In case of steam application fill the vertical section of the
connecting lines with a compatible fluid through the
dedicated filling tees.
C

- 8 -
Min. Level
H
L
Max. Level
L
H
A
C
B
A B
C
H L
L H
C
A
B
A B
C
H L
PHASE 2 - TRANSMITTER INSTALLATION
Flow measurement with gas or liquids with solids in suspension
1. Place the taps to the top or side of the line.
2. Mount the transmitter above the taps.
Level measurement with open tanks
1. Mount the transmitter at the same height or below the lowest level to be measured.
2. Connect the + (H) side of the transmitter to the bottom of the tank.
3. Vent the - (L) side of the transmitter to the atmosphere.
Flow
3-valve
manifold
gate valve
gate
valves
3-valve
manifold
drain
valve
Flow

- 9 -
Max. Level
Min. Level
H
L
E
Max. Level
Min. Level
H
L
PHASE 2 - TRANSMITTER INSTALLATION
Level measurement with closed tanks and non
condensable fluids (dry leg)
1. Mount the transmitter at the same height or below the
lowest level to be measured.
2. Connect the + (H) side of the transmitter to the bottom of the
tank.
3. Connect the - (L) side of the transmitter to the upper part of
the tank, above the maximum level of the tank.
Condensate trap
(optional)
Filling
tee
Level measurement with closed tanks and condensable
fluids (wet leg)
1. Mount the transmitter at the same height or below the
lowest level to be measured.
2. Connect the + (H) side of the transmitter to the bottom of the
tank.
3. Connect the - (L) side of the transmitter to the upper part of
the tank.
4. Fill the vertical section of the connecting line to the upper
part of the tank with a compatible liquid through the dedicated
filling tee.
Drain valve
Gate
valve
Gate
valve
Gate
valve
Gate
valve
Drain
valve
Wet
leg

- 10 -
E
S
PHASE 2 - TRANSMITTER INSTALLATION
Pressure or absolute pressure measurement of a tank
1. Select a tap in the upper part of the tank.
2. Mount the transmitter above the elevation of the process
tap.
3. Connect the + (H) side of the transmitter to the tank.
gate valve
Dirty fluids
Pressure or absolute pressure measurement of a liquid in
a pipe
1. Place the tap at the side of the line.
2. Mount the transmitter beside or below the tap for clean
fluids, above the tap for dirty fluids.
3. Connect the + (H) side of the transmitter to the pipe.
gate valve
Clean
fluids
H
L

- 11 -
PHASE 2 - TRANSMITTER INSTALLATION
Pressure or absolute pressure measurement of a
condensable vapor in a pipe
1. Place the tap at the side of the line.
2. Mount the transmitter below the tap.
3. Connect the + (H) side of the transmitter to the pipe.
4. Fill the vertical section of the connecting line to the tap with
a compatible liquid through the dedicated filling tee.
gate
valve
Pressure or absolute pressure measurement of a gas in a
pipe
1. Place the tap at the top or side of the line.
2. Mount the transmitter beside or above the tap.
3. Connect the + (H) side of the transmitter to the pipe.
gate
valve
filling
tee
vent
valve

- 12 -
3.2 TRANSMITTER MOUNTING
Orient the process flanges to enable process connections to be
made.
It is important to mount the transmitter and to lay the process
piping so that gas bubbles, when measuring liquids, or
condensate when measuring gases, can flow back into the
process.
Vent/drain screw valves on the transmitter can be ordered on
the flange side (near the top or bottom part of the flange) or on
the process axis. The transmitter and these drain/vent valves
have to be located higher than the taps on liquid service in order
to allow the venting of entrapped gas or below the taps on gas
service in order to allow the air or condensate to vent off.
For safety reasons, orient the drain/vent valves so that process
fluid is directed down and away from technicians when the
valves are used. This can be accomplished by pointing the hole
in the outside valve body downward and away.
PHASE 2 - TRANSMITTER INSTALLATION
In addition, consider the need for a testing or calibration input,
and provide space for the housing covers to be removed for
electrical wiring and maintenance.
WARNING !
Process leaks may cause harm or result in death.
Install and tighten process connectors and all accessories
(including manifolds) before applying pressure.
In case of toxic or otherwise dangerous process fluid, take
any precautions as recommended in the relevant Material
Safety Data Sheet when draining or venting.
Use only a 12 mm (15/32 “) hexagonal spanner to tighten
the bracket bolts.
Traditional (Barrel) Housing horizontal mounting with bracket
for vertical or horizontal pipe (option B1 and B2).

- 13 -
PHASE 2 - TRANSMITTER INSTALLATION
Traditional (Barrel) housing vertical mounting with bracket for vertical or horizontal pipe (option B1 and B2).
DIN housing vertical mounting with bracket for vertical or horizontal pipe (option B1 and B2).

- 14 -
PHASE 2 - TRANSMITTER INSTALLATION
Traditional (Barrel) Housing horizontal mounting with flat bracket type (option B5, this is the only bracket suitable
for units quipped with Stainless Steel housing). Mounting to vertical or horizontal pipe
Traditional (Barrel) Housing horizontal mounting with wall mounting bracket (option B3 and B4)
3.3 PROCESS CONNECTIONS
Housing Rotation
Process connections on the transmitter flange are 1/4 - 18 NPT, with a centers distance of 54mm (2.13in) between the
connections. The process connections on the transmitter flange are on centers to allow direct mounting to a three-valve or five-
valve manifold.
Flange adapter unions with 1/2 - 14 NPT connections are available as an option. Rotate one or both of the flange adapters to
attain connection centers of 51mm (2.01in), 54mm (2.13in) or 57mm (2.24in).
To install adapters, perform the following procedure:
1. Position the adapters with the O-ring in place.
2. Bolt the adapters to the transmitter flange using the bolts supplied.
3. Tighten the bolts.
For model 264PS and 264VS it is only possible to have one adapter, with low pressure side flange without process connection
and drain/vent valve.

- 15 -
PHASE 2 - TRANSMITTER INSTALLATION
3.4 ROTATION
Housing Rotation
To improve field access to wiring or the readability of the
optional LCD meter it is possible to rotate the Housing and the
Meters or the Integral display.
Housing Rotation
1. Unlock the housing rotation set screw by turning it 1 turn
(use the 3 mm Allen key supplied with the instrument)
2. Turn the housing clock wise or counterclockwise up to
180°from its original position.
Caution: over rotating will damage the transmitter.
3. Tighter the set screw.
Output Meters rotation
In case an optional meter is installed, it is also possible to rotate
the meter 90°degree clockwise or 255°counterclockwise with
15°steps.
Just turn it in the required position gripping around the complete
meter to avoid pulling the cover from the base of the meter.
Integral Display rotation
In case an optional integral display meter is installed, it is
possible to mount the display in four different positions rotated
clockwise or counterclockwise with 90°steps.
This is possible by using one of the four connections located on
the back of the display at a 90°distance each from the other.
set
screw

- 16 -
PHASE 3 - TRANSMITTER WIRING
4. TRANSMITTER WIRING
4.1 PROTECTIVE GROUNDING
All transmitters are supplied with an external ground connection
for protective grounding.
Wire this ground connection marked with: to a suitable
earth ground.
For a transmitter measuring loop an earth ground should
maintain a resistance of 5 ohms or less.
Use a heavy conductor, at least 15 AWG / 1,6 mm2Ø
WARNING ! - A protective grounding connection is
absolutely necessary to insure personnel protection, to
protect against surge (in case of installation of this option)
and to prevent explosions in potentially explosive
environment.
WARNING ! - In case the surge protection option is
present and the transmitter is installed in a Hazardous
area, the transmitter has to be power supplied from a
voltage source isolated from mains (galvanic separation).
Furthermore the potential equalization for the entire
powering cable must be guaranteed since the intrinsic
safety circuit of the transmitter is grounded.
4.2 ELECTRICAL CONNECTIONS
WARNING ! - Do NOT make electrical connections
unless the electrical code designation stamped on the
transmitter data plate agrees with the classification of the
area in which the transmitter is to be installed. Failure to
comply with this warning can result in fire or explosion.
The 4 to 20 mA dc output signal and the dc power supply to the
transmitter are carried from the same pairs of wires. The supply
voltage at the transmitter terminals must be between the limits
of 10,5 and 42V dc.
For EEx ia and intrinsically safe (FM, CSA and SAA) approval
power supply must not exceed 30 Vdc. In some countries the
maximum power supply voltage is limited to a lower value.
WARNING ! - Electrical shock can result in death or
serious injury. Avoid contact with the leads and terminals.
High voltage that may be present on leads can cause
electrical shock.
Follow these steps to wire the transmitter:
1. Remove the temporary plastic cap from one of the two
electrical connection ports located at both sides in the
upper part of the transmitter housing.
2. These connection ports have a 1/2 inch internal NPT
threads. Various adaptors and bushings can be fitted to
these threads to comply with plant wiring (conduit)
standards.
3. Remove the housing cover of the “field terminals” side. See
the indication on the label on top of the housing.
Inan Explosion-Proof/Flame-Proofinstallation, donot remove
the transmitter covers when power is applied to the unit.
4. In case an Output meter is present it has to be removed by
pulling it out. Grip around the complete meter to avoid
pulling the cover from the base of the meter.
✶
5. Run the cable through the cable gland and the open port.
6. Connect the positive lead to the + terminal, and the negative
lead to the – terminal.
Note: Do not connect the power across the test
terminals. Power could damage the test diode in the test
connection.
7. Plug and seal the electrical ports. Make sure that when the
installation has been completed, the electrical ports are
properly sealed against entry of rain and corrosive vapors
and gases.
WARNING ! - Cable, cable gland and unused port
plug must be in accordance with the intended type of
protection (e.g. intrinsically safe, explosion proof, etc.) and
degree of protection (e.g. IP6x according to IEC EN 60529
or NEMA 4x). See also the addendum for "EX SAFETY"
ASPECTS AND "IP" PROTECTION. In particular, for
explosion proof installation, remove the red temporary
plastic cap and plug the unused opening with a plug
certified for explosion containment.

- 17 -
8. If applicable, install wiring with a drip loop. Arrange the drip
loop so the bottom is lower than the conduit connections
and the transmitter housing. In case an Output meter is
present, be sure that the by-pass connection is open, then
plug the meter into the appropriate socket.
9. Put back the housing cover, turn it to seat O-ring into the
housing and then continue to hand tighten until the cover
contacts the housing metal-to-metal.
In EEx-d (Explosion Proof) installation, lock the cover
rotation by turning the set nut (use the 2mm Allen key
supplied with the instrument).
In case of FF or Profibus connections see the relevant diagram.
For further information find the relevant instruction manuals
searching for the keyword "IM/*26*" on www.abb.com or from
local ABB representatives.
4.3 SUPPLY WIRING REQUIREMENTS
For signal/power connection use twisted, stranded pairs of
wiring no 18 to 22 AWG / 0.8 to 0.35mm2ø up to 5,000 feet
(1500 meters). Longer loops require larger wire.
If a shielded wire is used the shield should be grounded only at
one end, not both ends. In case of wiring at transmitter end, use
the terminal located inside the housing marked with:
PHASE 3 - TRANSMITTER WIRING
cover locking screw

- 18 -
L H
C
A
B
A B
C
H L
PHASE 4 - TRANSMITTER OPERATION
5. TRANSMITTER OPERATION
Use the following step to adjust the transmitter zero.
5.1 FLOW MEASUREMENT
1. The process fluid must enter the transmitter primary:
a. Close low pressure (B) and high pressure (A) valves
(fig. 5.2a and 5.2b).
b. Open gate valves and equalizing (C) valve.
c. Slowly open high pressure (A) valve to admit process
fluid to both sides of primary.
2. Vent (or drain) primary as follows:
a. Liquid service - Vent all entrapped air from both sides
of primary using vent/drain valves, then close them.
b. Gas service - Drain any condensate from both sides of
primary using vent/drain valves, then close them.
1 2 3 4 5 6
1
0
Fig. 5.2a - GAS Service Fig. 5.2b - Liquid or Vapor Service
Fig. 5.1 - Default Dip switches settings
3-valve manifold
Flow
3-valve manifold
Vent/drain
valve
Flow
Orifice plate
filling
tees
gate
valves
LH
AB
C
H L
B
A
C

- 19 -
Max. Level
Min. Level
H
L
PHASE 4 - TRANSMITTER OPERATION
Fig. 5.3 - Zero button
3. After venting or draining, output should be 4 mA dc.
If not:
a. Rotate the nameplate to get access to the external
push buttons.
b. Push the zero (Z) button on top of the transmitter
(figure 5.3) for at least 2 seconds.
c. The output goes to 4 mA, and if present the Integral
Display, the message “ZERO PASS” will appear.
d. If a “WRITE DISABLE” message appears on the
Integral Display, check the Dip switches settings (you
need to open the cover on the electronic side and to
pull out the integral display: see figure 5.1).
e. In case of other diagnostic messages, see the
reference manual.
4. Close equalizing (C) valve.
5. Open low pressure (B) valve.
5.2 LEVEL MEASUREMENT
1. Vent all entrapped air from primary using vent/drain
valves on the transmitter, then close them.
2. Make sure to have the level in the tank at the required
reference (minimum) level.
Note: In case it is not possible to empty the tank,
it is possible to follow the Zero Raise/Lower adjustment
procedure described in the reference manual.
3. In case of wet leg make sure to have it completely filled-
in with the proper liquid.
4. After venting, output should be 4 mA dc. If not:
a. Rotate the nameplate to get access to the external
push buttons.
b. Push the zero (Z) button on top of the transmitter
(figure 5.3) for at least 2 seconds.
c. The output goes to 4 mA, and if present the Integral
Display, the message “ZERO PASS” will appear.
d. If a “WRITE DISABLE” message appears on the
Integral Display, check the Dip switches settings (you
need to open the cover on the electronic side and to
pull out the integral display: see figure 5.1).
e. In case of other diagnostic messages, see the
reference manual.
Drain
valve
Vent/drain
valve
Gate
valve
Gate
valve
✶

- 20 -
PHASE 4 - TRANSMITTER OPERATION
5.3 PRESSURE MEASUREMENTS
1. Slowly open the gate valve to admit process fluid to primary
of side H.
2. Vent all entrapped air (liquid service) or drain any condensate
(gas service) from primary using the vent/drain valve.
3. Close the gate valve.
4. Bring the process to the desired zero reading condition, i.e.
as an example:
a. In case of dry leg open the drain valve to bring the
primary to atmospheric pressure.
b. In case of wet leg slowly open the filling tee (and make
sure to have the wet leg completely filled-in).
5. The output should be 4 mA dc. If not:
a. Rotate the nameplate to get access to the external push
buttons.
Gate
valve
Filling
tee
Vent/drain
valve
b. Push the zero (Z) button on top of the transmitter (figure
5.3) for at least 2 seconds.
c. The output goes to 4 mA, and if present the Integral
Display, the message “ZERO PASS” will appear.
d. If the output is not 4 mA or the message “WRITE
DISABLE” appears on the Integral Display, check the
Dip switches settings (you need to open the cover on the
electronic side and to pull out the integral display: see
figure 5.1).
e. In case of other diagnostic messages, see the reference
manual.
6. Close any open filling tee and drain valve.
7. Open the gate valve.
Other manuals for 2600T Series
6
This manual suits for next models
4
Table of contents
Other ABB Transmitter manuals
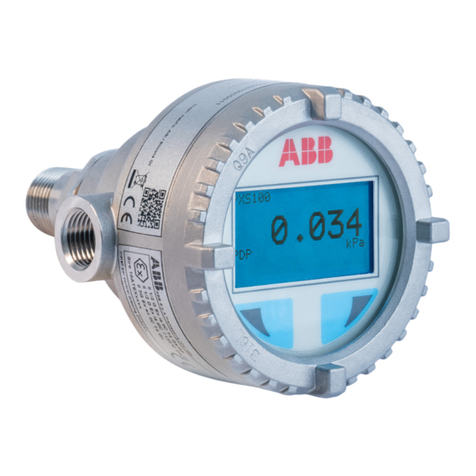
ABB
ABB PGS100 User manual
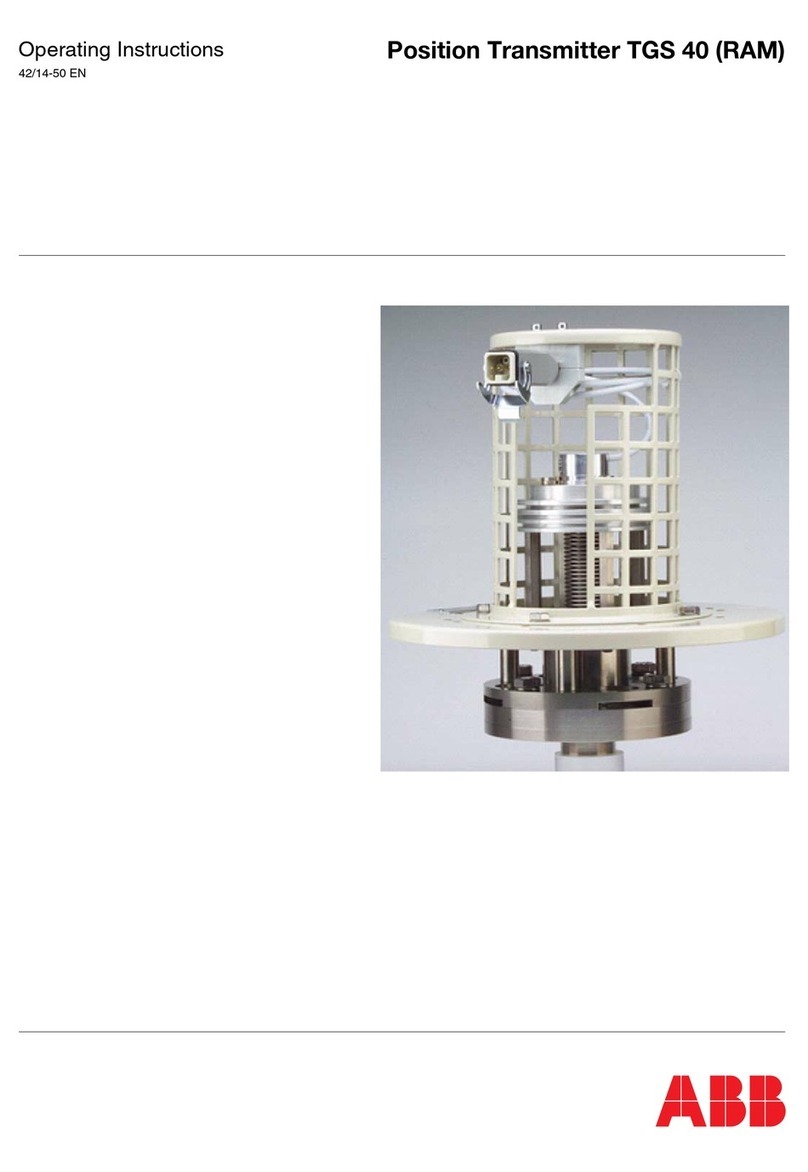
ABB
ABB TGS 40 User manual
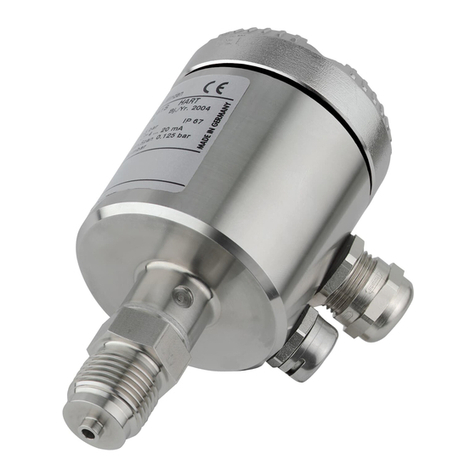
ABB
ABB 261GS User manual
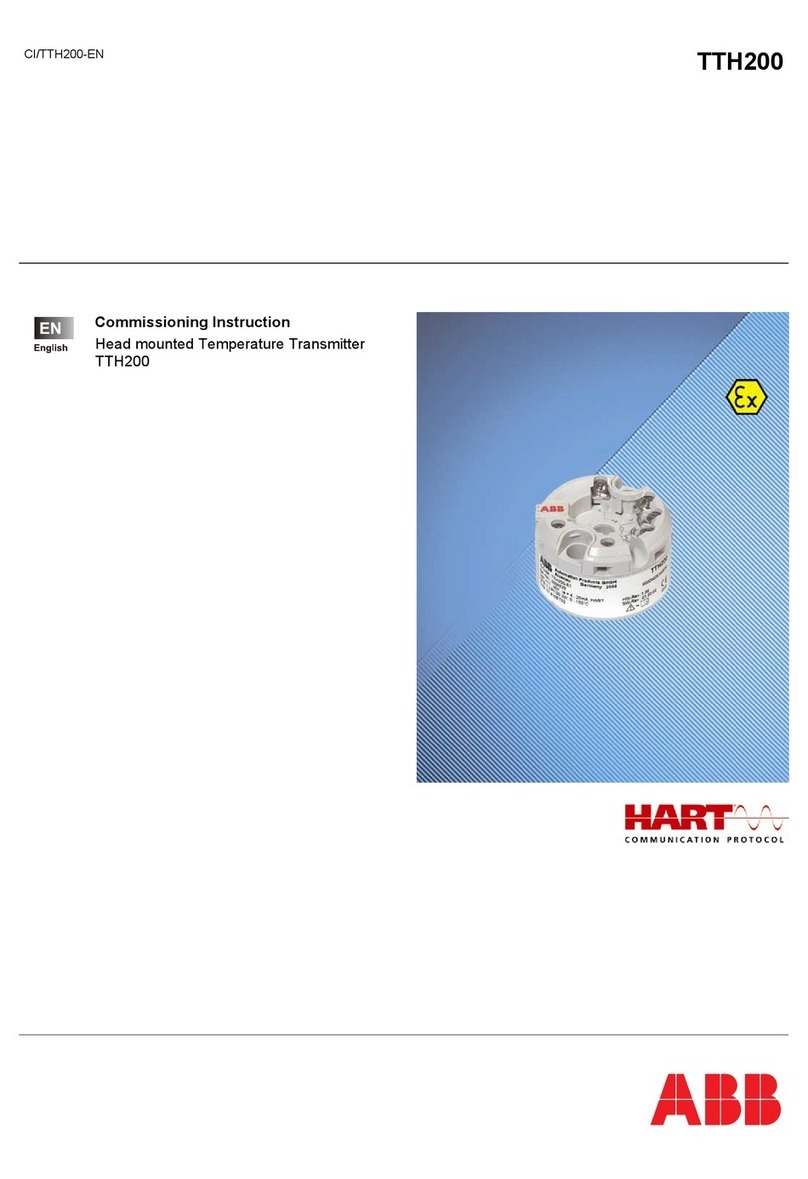
ABB
ABB TTH200 Installation and operation manual
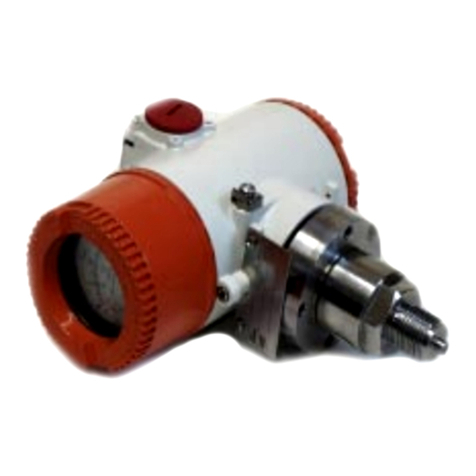
ABB
ABB 600T EN Series User manual
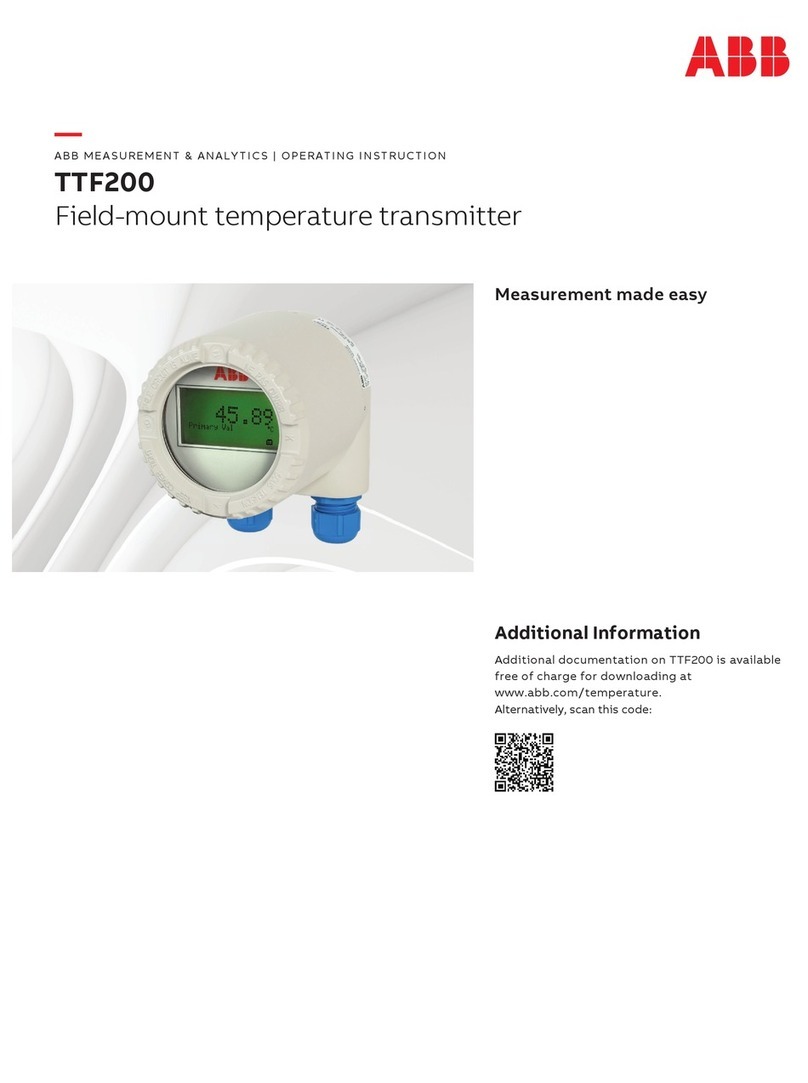
ABB
ABB TTF200 User manual
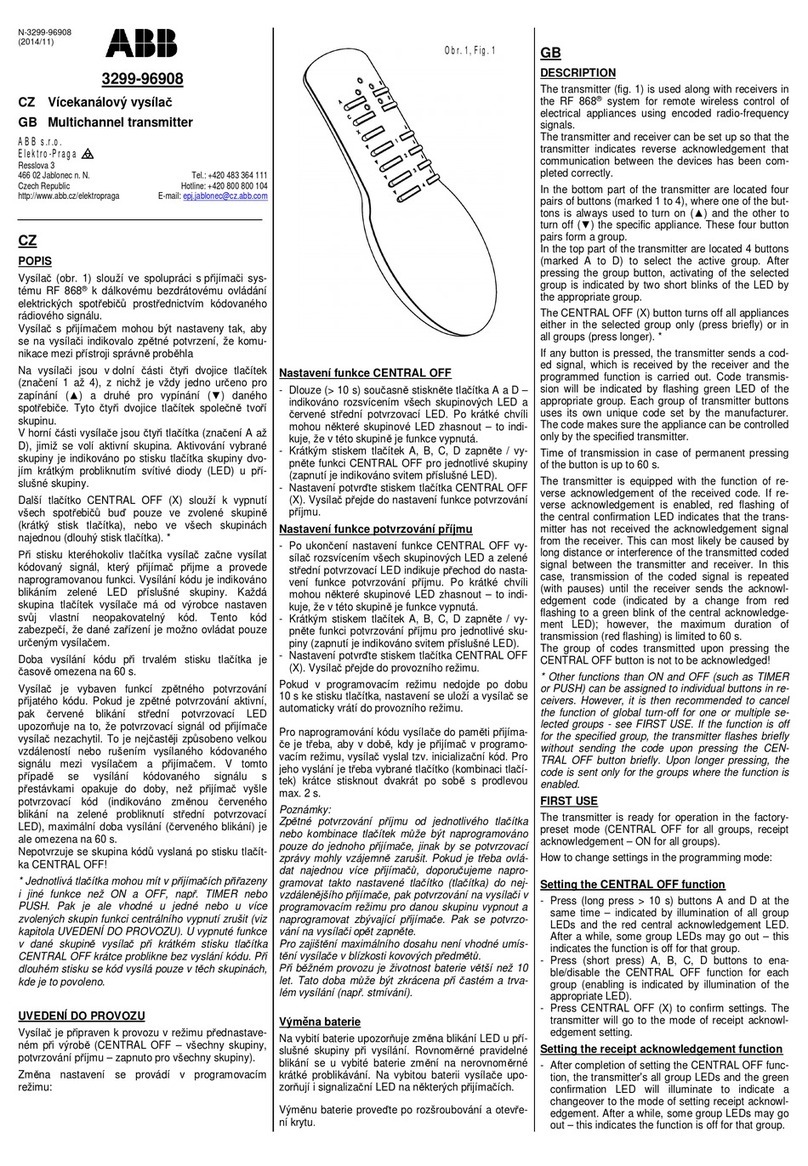
ABB
ABB 3299-96908 User manual
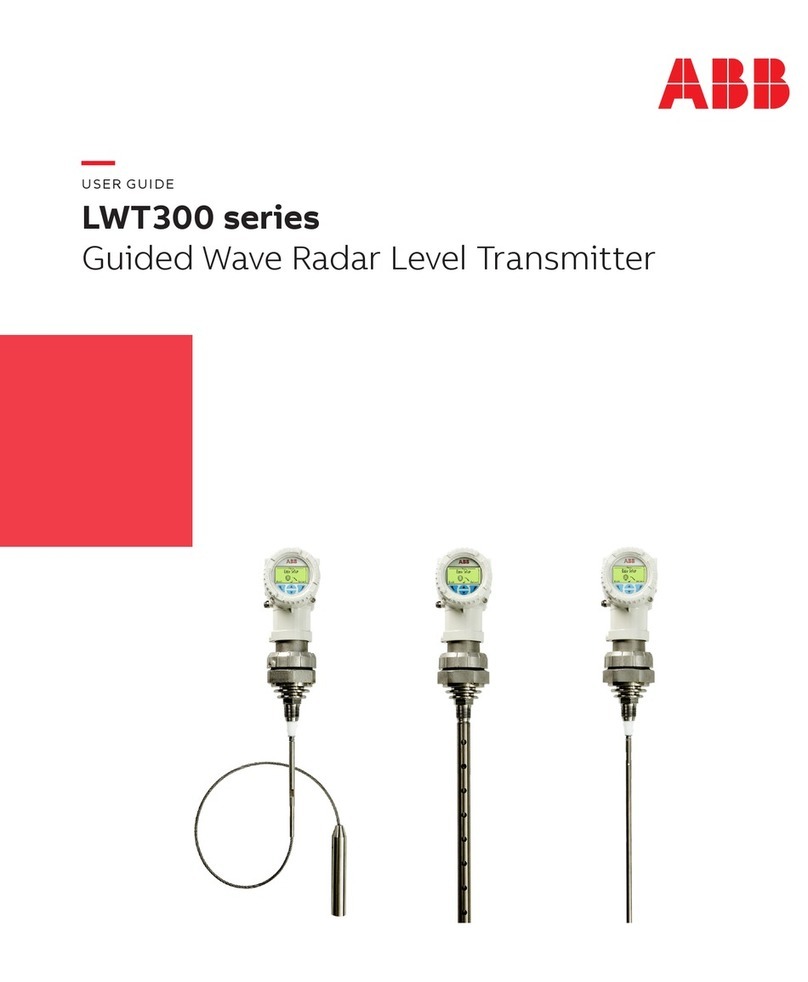
ABB
ABB LWT300 series User manual
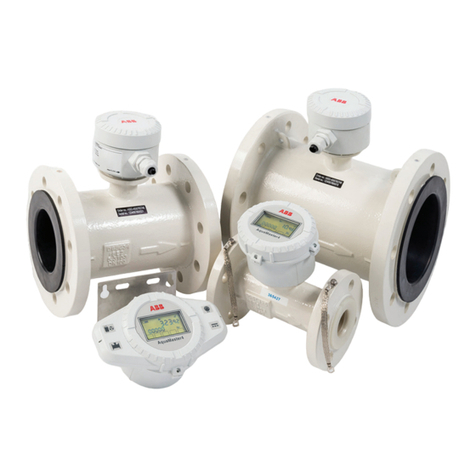
ABB
ABB AquaMaster4 User manual

ABB
ABB TTH200 Operating manual
Popular Transmitter manuals by other brands
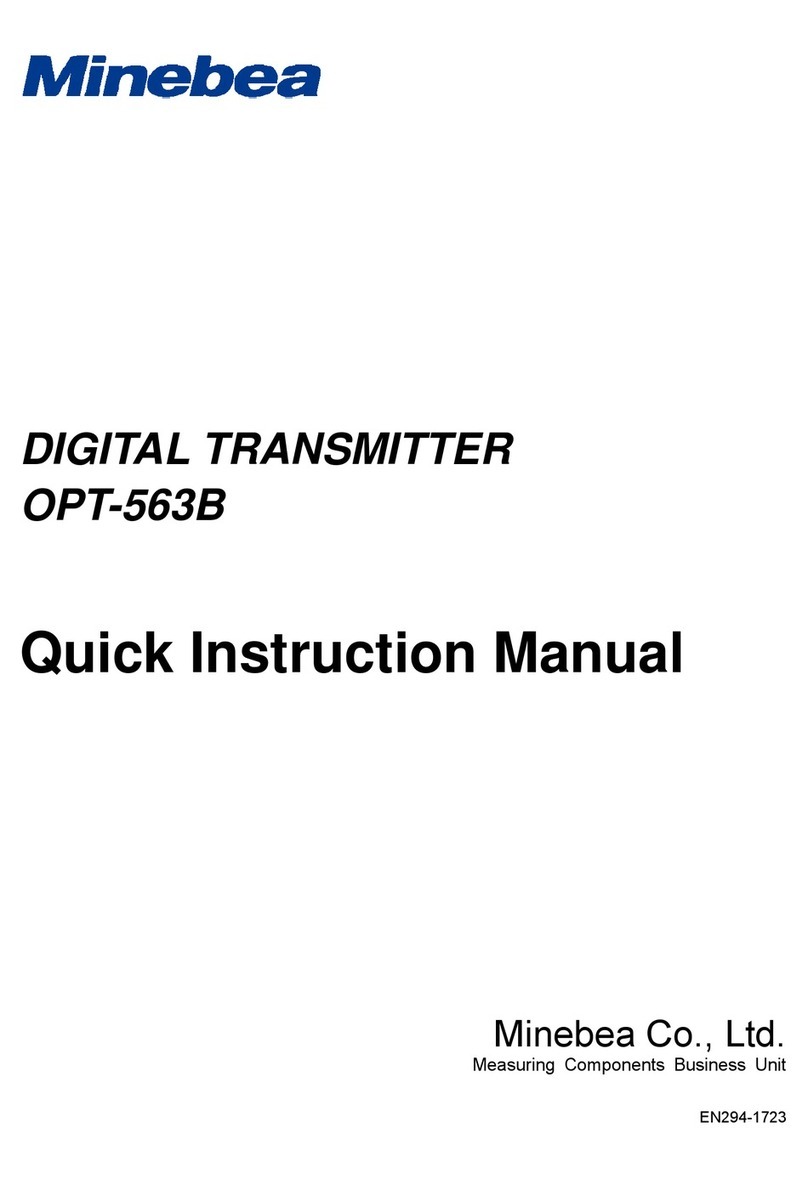
Minebea
Minebea OPT-563B Quick instruction manual
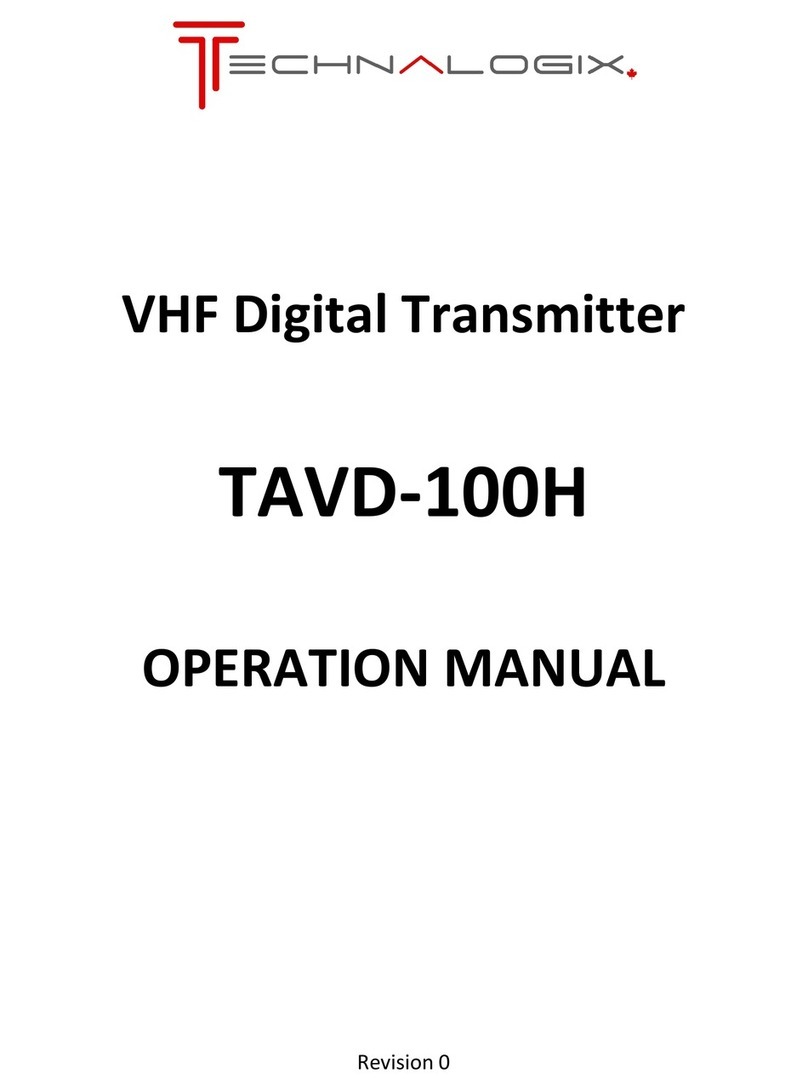
Technalogix
Technalogix TAVD-100H Operation manual
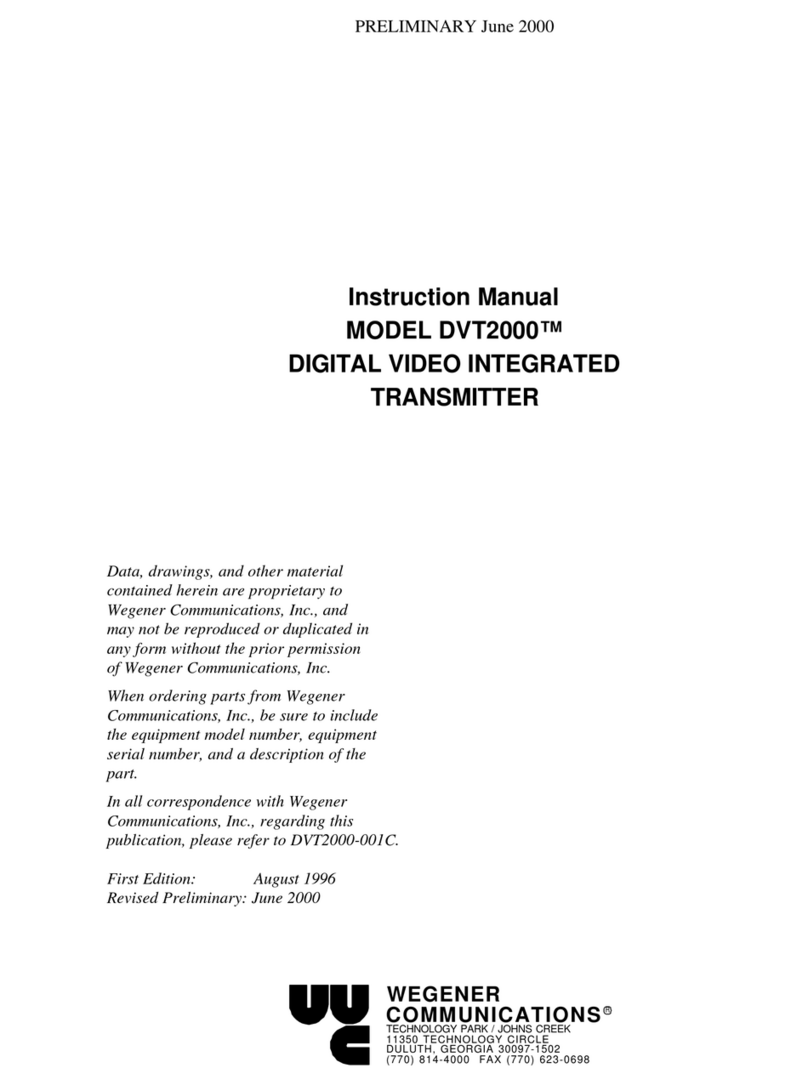
Wegener
Wegener DVT2000 instruction manual
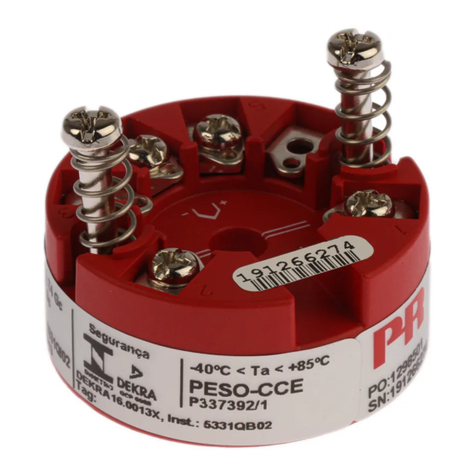
PR electronics
PR electronics PRetop 5334 Safety instructions
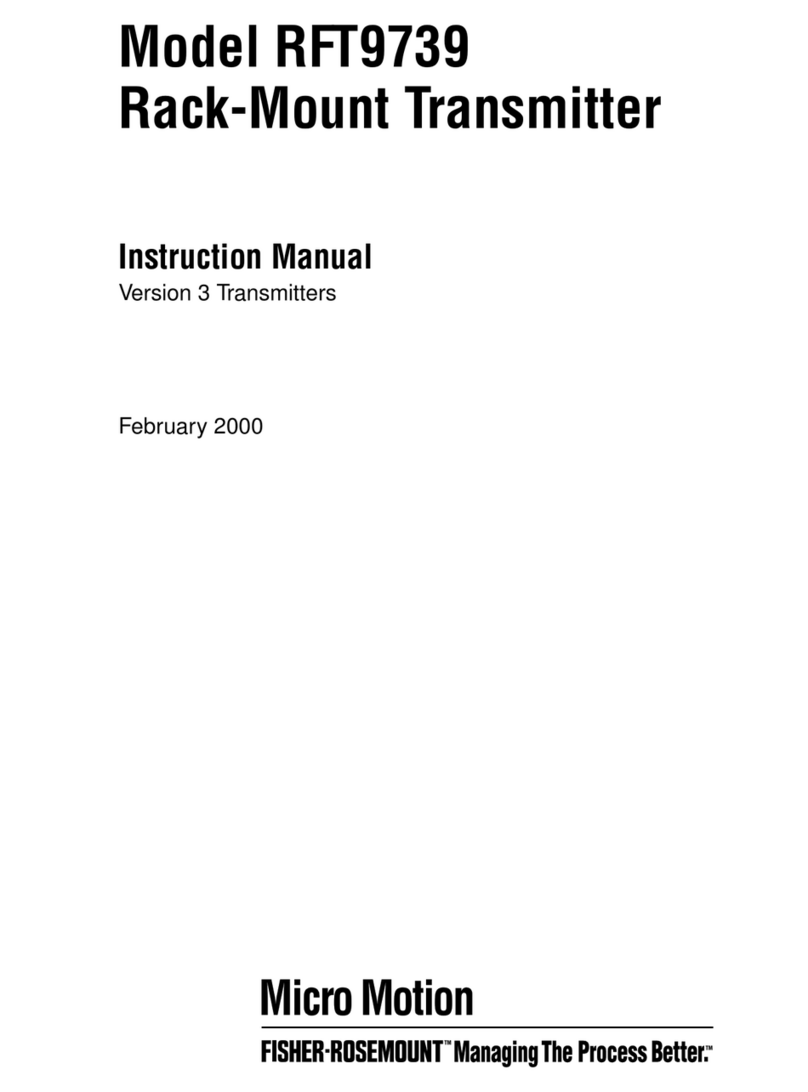
Micro Motion
Micro Motion Fisher Rosemount RFT9739 instruction manual
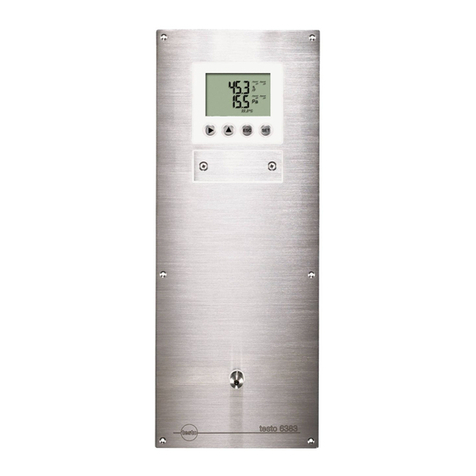
TESTO
TESTO 6383 instruction manual