Acromag APC8620 Series User manual

-~
ARTISAN
®
~I
TECHNOLOGY
GROUP
Your definitive source
for
quality
pre-owned
equipment.
Artisan Technology
Group
Full-service,
independent
repair
center
with
experienced
engineers
and
technicians
on staff.
We
buy
your
excess,
underutilized,
and
idle
equipment
along
with
credit
for
buybacks
and
trade-ins
.
Custom
engineering
so
your
equipment
works
exactly as
you
specify.
•
Critical
and
expedited
services
•
Leasing
/
Rentals/
Demos
• In
stock/
Ready-to-ship
•
!TAR-certified
secure
asset
solutions
Expert
team
ITrust
guarantee
I
100%
satisfaction
All
tr
ademarks,
br
a
nd
names, a
nd
br
a
nd
s a
pp
earing here
in
are
th
e property of
th
e
ir
r
es
pecti
ve
ow
ner
s.
Find the Acromag APC8620A at our website: Click HERE

Series APC8620/8621 Industrial I/O Pack
PCI Bus Non-Intelligent Carrier Board
USER’S MANUAL
ACROMAG INCORPORATED
30765 South Wixom Road
P.O. BOX 437
Wixom, MI 48393-7037 U.S.A.
Tel: (248) 624-1541
Fax: (248) 624-9234
Copyright 2000, Acromag, Inc., Printed in the USA.
Data and specifications are subject to change without notice.
8500-576-E01B010
Artisan Technology Group - Quality Instrumentation ... Guaranteed | (888) 88-SOURCE | www.artisantg.com

INDUSTRIAL I/O PACK SERIES APC8620/8621 PCI BUS CARRIER BOARD
___________________________________________________________________________________________
- 2 -
The information contained in this manual is subject to change
without notice. Acromag, Inc. makes no warranty of any kind with
regard to this material, including, but not limited to, the implied
warranties of merchantability and fitness for a particular purpose.
Further, Acromag, Inc. assumes no responsibility for any errors
that may appear in this manual and makes no commitment to
update, or keep current, the information contained in this manual.
No part of this manual may be copied or reproduced in any form,
without the prior written consent of Acromag, Inc.
Table of Contents Page
1.0 GENERAL INFORMATION........................................... 2
KEY APC8620/8621 FEATURES……..............….......... 2
PCI BUS INTERFACE FEATURES............................... 3
SIGNAL INTERFACE PRODUCTS............................... 3
IP MODULE OLE CONTROL SOFTWARE................... 3
2.0 PREPARATION FOR USE............................................ 3
UNPACKING AND INSPECTION.................................. 3
CARD CAGE CONSIDERATIONS................................ 4
BOARD CONFIGURATION…...................................…. 4
Interrupt Configuration…........................................... 4
CONNECTORS…......................................................... 4
Carrier Field I/O Connectors (IP modules A-E)…...... 4
IP Field I/O Connectors (IP modules A-E)…......….... 4
IP Logic Interface Connectors (IP modules A-E)...…. 4
IP Logic Strobe Connectors…………………………… 4
PCI BUS Connections.........................................…... 5
DATA TRANSFER TIMING.................................…....... 5
FIELD GROUNDING CONSIDERATIONS...........…...... 6
3.0 PROGRAMMING INFORMATION......................…....... 6
PCI Configuration Address Space............................. 6
Configuration Transactions........................................ 6
Configuration Registers….......................................... 7
MEMORY MAP......................................................….... 7
Carrier Board Status Register..............................….. 8
IP Interrupt Pending Register.................................... 8
IP Module Interrupt Space…..................................... 8
IP Module ID Space……..…...................................... 8
IP Module I/O Space…....…...................................... 9
GENERATING INTERRUPTS.................................…... 9
Sequence of Events for an Interrupt.....................…. 9
4.0 THEORY OF OPERATION....................................….... 9
CARRIER BOARD OVERVIEW...........................…...... 9
PCI BUS Interface..................................................... 9
Carrier Board Registers......................................…... 9
IP Logic Interface................................................…... 10
Carrier Board Clock Circuitry.............................…..... 10
PCI Interrupter…...............................................…..... 10
Power Failure Monitor...........................................…. 10
Power Supply Fuses………………………….............. 10
Power Supply Filters..............................................… 10
5.0 SERVICE AND REPAIR................................................ 10
SERVICE AND REPAIR ASSISTANCE........................ 10
PRELIMINARY SERVICE PROCEDURE...................... 10
6.0 SPECIFICATIONS........................................................ 11
GENERAL SPECIFICATIONS....................................... 11
PCI BUS COMPLIANCE............................................... 11
INDUSTRIAL I/O PACK COMPLIANCE........................ 11
ENVIRONMENTAL………………………........................ 12
APPENDIX.................................................................... 12
CABLE: MODEL 5025-550............................................ 12
CABLE: MODEL 5025-551............................................ 12
CABLE: MODEL 5029-943............................................ 12
TERMINATION PANEL: MODEL 5025-552................... 12
DRAWINGS Page
4501-671 APC8620 IP LOCATIONS…………………… 13
4501-676 APC8621 IP LOCATIONS…………………… 14
4501-672 MECHANICAL ASSEMBLY DRAWING........ 15
4501-673 APC8620/8621 BLOCK DIAGRAM.......….… 16
4501-462 CABLE 5025-550 (NON-SHIELDED)............ 17
4501-463 CABLE 5025-551 (SHIELDED)..................... 18
4501-464 TERMINATION PANEL 5025-552............…. 19
IMPORTANT SAFETY CONSIDERATIONS
It is very important for the user to consider the possible adverse
effects of power, wiring, component, sensor, or software failures
in designing any type of control or monitoring system. This is
especially important where economic property loss or human life
is involved. It is important that the user employ satisfactory
overall system design. It is agreed between the Buyer and
Acromag, that this is the Buyer's responsibility.
1.0 GENERAL INFORMATION
The APC8620/8621 card is a personal computer Peripheral
Component Interconnect (PCI) bus card and is a carrier for the
Industrial I/O Pack (IP) mezzanine board field I/O modules. The
carrier board provides a modular approach to system assembly,
since each carrier can be populated with any combination of
analog input/output, digital input/output, communication, etc. IP
modules. Thus, the user can create a board which is customized
to the application. This saves money and space - a single carrier
board populated with IP modules may replace several dedicated
function PCI bus boards. The APC8620/8621 non-intelligent
carrier board provides impressive functionality at low cost.
Model Board Size
(Length) Supported IP
Slots Operating
Temperature
Range
APC8620 Long (12.283”) 5(A,B,C,D,E) 0 to +70°C
APC8620E Long (12.283”) 5(A,B,C,D,E) -40 to +85°C
APC8621 Short (6.600”) 3(A,B,C) 0 to +70°C
APC8621E Short (6.600”) 3(A,B,C,) -40 to +85°C
KEY APC8620/8621 FEATURES
•PCI Specification Version 2.1 Compliant Slave Carrier: -
Provides a PCI bus interface to control and communicate
with industry standard IP modules.
•Interface for IP Modules – APC8620 provides an electrical
and mechanical interface for up to five industry standard IP
modules. APC8621 provides an electrical and mechanical
interface for up to three industry standard IP modules. IP
Modules are available from Acromag and other vendors in a
wide variety of Input/Output configurations to meet the
needs of varied applications.
•Plug-And-Play PCI bus Carrier - The carrier card contains
standard PCI bus configuration memory. Upon power-up
Artisan Technology Group - Quality Instrumentation ... Guaranteed | (888) 88-SOURCE | www.artisantg.com

INDUSTRIAL I/O PACK SERIES APC8620/8621 PCI BUS CARRIER BOARD
___________________________________________________________________________________________
- 3 -
the system auto-configuration process assigns the carrier’s
base address in memory space.
•Plug-And-Play Interrupt Support - The personal computer
system software will allocate one interrupt line to the carrier.
The carrier’s interrupt pending register can be used to
quickly identify IP module pending interrupts.
•Supports Two Interrupt Channels per IP - Up to two
interrupt requests are supported for each IP. Additional
registers are associated with each interrupt request for
control and status monitoring.
•Full IP Register Access - Makes maximum use of logically
organized programmable registers on the carrier boards to
provide for easy configuration and control of IP modules.
Supports accesses to IP input/output, interrupt, and ID ROM
data spaces. No hardware jumper settings are required on
the carrier board.
•IP Module Access Time Out - Allows access to empty IP
slots without system failure. If the IP module accessed does
not respond within 32u seconds the bus access is
terminated without system failure. This allows each IP slot
to be probed to determine if an IP is installed. A control
register bit will be set and/or issue of an interrupt request to
indicate IP module time out access has occurred.
•Optional Screw Termination Panel - Model supports field
connection via screw terminals using the optional DIN rail
mount termination panels.
•Connectors Access I/O - Access to field I/O signals is
provided via industry standard 50-pin headers with ejector
latches. A separate header is provided for each IP module.
•Supervisory Circuit for Reset Generation - A
microprocessor supervisor circuit provides power-on, power-
off, and low power detection reset signals to the IP modules
per the IP specification.
•Individually Filtered Power - Filtered +5V, +12V, and -12V
DC power is provided to the IP modules via passive filters
present on each supply line serving each IP. This provides
optimum filtering and isolation between the IP modules and
the carrier board and allows analog signals to be accurately
measured or reproduced on IP modules without signal
degradation from the carrier board logic signals.
•Individually Fused Power - Fused +5V, +12V, and -12V
DC power is provided. A fuse is present on each supply line
serving each IP module.
•OLE Control Software is Available - Acromag provides
Object Linking and Embedding (OLE) controls software for
Windows 95/98/NTTM. This software (Model IPSW-OLE-
PCI, MSDOS format) provides individual drivers that allow IP
modules and our personal computer carriers to be easily
integrated into Windows application programs, such as
Visual C++, Visual Basic, Borland DelphiTM, Microsoft
Office 97applications, and others.
PCI BUS INTERFACE FEATURES
•Slave Module- All read and write accesses are
implemented as either a 32-bit, 16-bit or 8-bit single data
transfer.
•Immediate Disconnect on Read - The PCI bus will
immediately disconnect after a read. The read data is then
stored in a read FIFO. Data in the read FIFO is then
accessed by the PCI bus when the read cycle is retried.
This allows the PCI bus to be free for other system
operations while the read data is moved to the read FIFO.
•Interrupt Support - PCI bus INTA# interrupt request is
supported. All IP module interrupts are mapped to INTA#.
Carrier board software programmable registers are utilized
as interrupt request control and status monitors.
SIGNAL INTERFACE PRODUCTS
(See Appendix for more information on compatible products)
This IP carrier board will mate directly to all industry standard
IP modules. Acromag provides the following interface products
(all connections to field signals are made through the carrier
board which passes them to the individual IP modules):
Cables:
Model 5025-551-X (Shielded Cable) or Model 5025-550-X
(Non-Shielded Cable): A Flat 50-pin cable with female
connectors at both ends for connecting carrier boards, to
Model 5025-552 termination panels. The unshielded cable is
recommended for digital I/O, while the shielded cable is
recommended for optimum performance with precision
analog I/O applications.
Model 5029-943 IP500 Serial Communication Cable: A 5 foot
long, flat 50-pin cable with a female connector on one end
(for connection to the carrier board) and four DE-9P
connectors (serial ports) on the other end. Also used for
interface with Acromag Model IP501 (RS-422) & IP502 (RS-
485) serial communication modules.
Termination Panel:
Model 5025-552: DIN-rail mountable panel provides 50
screw terminals for universal field I/O termination. Connects
to carrier boards, via flat 50-pin ribbon cable (Model 5025-
550-X or 5025-551-X).
IP MODULE OLE CONTROL SOFTWARE
Acromag provides a software product (sold separately)
consisting of IP module OLE (Object Linking and Embedding)
drivers for Windows 95/98/NT compatible application programs
(Model IPSW-OLE-PCI, MSDOS format). This software provides
individual drivers that allow Acromag IP modules and our
personal computer carriers to be easily integrated into Windows
application programs, such as Visual C++, Visual Basic, Borland
DelphiTM, MicrosoftOffice 97applications, and others. The
OLE controls provide a high-level interface to IP modules,
eliminating the need to perform low-level reads/writes of
registers, and the writing of interrupt handlersall the
complicated details of programming are handled by the OLE
controls. These functions are intended for use in conjunction with
an Acromag personal computer carrier and consist of a carrier
OLE control, and an OLE control for each Acromag IP module as
well as a generic OLE control for non-Acromag IP modules.
2.0 PREPARATION FOR USE
UNPACKING AND INSPECTION
Upon receipt of this product, inspect the shipping carton for
evidence of mishandling during transit. If the shipping carton is
badly damaged or water stained, request that the carrier's agent
be present when the carton is opened. If the carrier's agent is
absent when the carton is opened and the contents of the carton
are damaged, keep the carton and packing material for the
agent's inspection.
For repairs to a product damaged in shipment, refer to the
Acromag Service Policy to obtain return instructions. It is
suggested that salvageable shipping cartons and packing
material be saved for future use in the event the product must be
shipped.
Artisan Technology Group - Quality Instrumentation ... Guaranteed | (888) 88-SOURCE | www.artisantg.com

INDUSTRIAL I/O PACK SERIES APC8620/8621 PCI BUS CARRIER BOARD
___________________________________________________________________________________________
- 4 -
This board is physically protected with
packing material and electrically protected
with an anti static bag during shipment. It
is recommended that the board be visually
inspected for evidence of mishandling prior
to applying power.
The board utilizes static sensitive
components and should only be handled at
a static-safe workstation.
CARD CAGE CONSIDERATIONS
Refer to the specifications for loading and power
requirements. Be sure that the system power supplies are able
to accommodate the power requirements of the carrier board,
plus the installed IP modules, within the voltage tolerances
specified.
IMPORTANT: Adequate air circulation must be provided to
prevent a temperature rise above the maximum operating
temperature.
The lack of air circulation within the computer chassis is a
cause for some concern. Most, if not all, computer chassis do
not provide a fan for cooling of add-in boards. The dense
packing of the IP modules to the carrier board alone results in
elevated IP module and carrier board temperatures, and the
restricted air flow within the chassis aggravates this problem.
Adequate air circulation must be provided to prevent a
temperature rise above the maximum operating temperature and
to prolong the life of the electronics. If the installation is in an
industrial environment and the board is exposed to environmental
air, careful consideration should be given to air-filtering.
BOARD CONFIGURATION
The carrier board is plug-and-play compatible and, as such,
its board addresses are automatically assigned by the system
auto-configuration routine upon power-up. The base address of
the carrier board’s configuration registers in memory space and
I/O space is assigned. In addition, the base address of the IP
modules and carrier board registers are assigned in 32-bit
memory space.
Power should be removed from the board when installing IP
modules, cables, termination panels, and field wiring. Refer to
Mechanical Assembly Drawing 4501-672 and your IP module
documentation for specific configuration and assembly
instructions.
Interrupt Configuration
No hardware jumper configuration is required. All interrupt
enabling, and status are configured via programmable registers
on the carrier board (see Section 3 for programming details). The
carrier board passes interrupt requests from the IP modules to
the PCI bus. Refer to the IP modules for their specific
configuration requirements.
CONNECTORS
Connectors of the APC8620 carrier consist of five (three for
APC8621) carrier IP module field I/O connectors, five (three for
APC8621) IP module logic connectors, and one PCI bus interface
connector. These interface connectors are discussed in the
following sections.
Carrier Field I/O Connectors (IP modules A through E)
Field I/O connections are made via 50 pin ribbon cable
connectors A, B, C, D, and E (A, B, and C for APC8621) for IP
modules in positions A through E (A through C for APC8621). IP
module assignment is marked on the board for easy identification
(see IP location drawing 4501-671 or 4501-676 for physical
locations of the IP modules). Flat cable assemblies and
Acromag termination panels (or user defined terminations) can be
quickly mated to the field I/O connectors. Pin assignments are
defined by the IP module employed since the pins from the IP
module field side correspond identically to the pin numbers of the
50 pin connectors.
Carrier field I/O connectors A through E (A through C for
APC8621) are industry standard 50-pin low profile headers (male)
with short ejector latches (no ejector latches for APC8621) and
they mate to ribbon cable connectors (3M Type P/N 3425-6600).
IP Field I/O Connectors (IP modules A through E)
The field side connectors of IP modules A through E (A
through C for APC8621) mate to AMP 173280-3 connectors P4,
P5, P9, P12, and P15 (P3, P6, and P9 for APC8621)
respectively, on the carrier board. IP location is silk-screened on
the board for easy identification. Field and logic side connectors
are keyed to avoid incorrect assembly.
The AMP 173280-3 connectors mate to AMP 173279-3
connectors (or similar) on the IP modules. This provides
excellent connection integrity and utilizes gold plating in the
mating area. Threaded metric M2 screws and spacers (supplied
with Acromag IP modules) provide additional stability for harsh
environments (see Drawing 4501-672 for assembly details).
Pin assignments for these connectors are made by the
specific IP model used and correspond identically to the pin
numbers of the front panel connectors.
IP Logic Interface Connectors (IP modules A through E)
The logic interface sides of IP modules A through E (A
through C for APC8621) mate to AMP 173280-3 connectors P6,
P7, P10, P13, and P16 (P4, P7, and P10 for APC8621),
respectively, on the carrier board. IP location is silk-screened on
the board for easy identification. Field and logic side connectors
are keyed to avoid incorrect assembly.
The AMP 173280-3 connectors mate to AMP 173279-3
connectors (or similar) on the IP modules. This provides
excellent connection integrity and utilizes gold plating in the
mating area. Threaded metric M2 screws and spacers (supplied
with Acromag IP modules) provide additional stability for harsh
environments (see Drawing 4501-672 for assembly details).
Pin assignments for these connectors are defined by the IP
module specification and are shown in Table 2.1.
IP Logic Strobe Connectors
Each IP module has an uncommitted Strobe signal on the
logic interface connector (pin 46). The Strobe signal may be
used as an optional input or output from the IP module. On the
APC8620 the Strobe signals for each of the five IP modules are
routed on the printed circuit board to the location just above the
Artisan Technology Group - Quality Instrumentation ... Guaranteed | (888) 88-SOURCE | www.artisantg.com

INDUSTRIAL I/O PACK SERIES APC8620/8621 PCI BUS CARRIER BOARD
___________________________________________________________________________________________
- 5 -
IP module D and E field connectors (as shown in Drawing 4501-
671). On the APC8621 the Strobe signals for each of the three
IP modules are routed on the printed circuit board to the location
just above of IP module C field connector (as shown in Drawing
4501-676). The factory default is to leave these signals
unconnected.
Table 2.1: Standard IP Logic Interface Connections
Pin Description Number Pin Description Number
GND 1 GND 26
CLK 2 +5V 27
Reset* 3 R/W* 28
D00 4 IDSEL* 29
D01 5 DMAReq0* 30
D02 6 MEMSEL* 31
D03 7 DMAReq1* 32
D04 8 IntSel* 33
D05 9 DMAck0* 34
D06 10 IOSEL* 35
D07 11 RESERVED 36
D08 12 A1 37
D09 13 DMAEnd* 38
D10 14 A2 39
D11 15 ERROR* 40
D12 16 A3 41
D13 17 INTReq0* 42
D14 18 A4 43
D15 19 INTReq1* 44
BS0* 20 A5 45
BS1* 21 STROBE* 46
-12V 22 A6 47
+12V 23 ACK* 48
+5V 24 RESERVED 49
GND 25 GND 50
Asterisk (*) is used to indicate an active-low signal.
BOLD ITALIC Logic Lines are NOT USED by the carrier board.
PCI Bus Connections
Table 2.2 indicates the pin assignments for the PCI bus
signals at the card edge connector. Connector pins are
designated by a letter and a number. The letter indicates which
side of a particular connector the pin contact is on. “B” is on the
component side of the carrier board while “A” is on the solder
side. Connector “gold finger” numbers increase with distance
from the bracket end of the printed circuit board.
Refer to the PCI bus specification for additional information
on the PCI bus signals.
TABLE 2.2: PCI Bus P1 CONNECTIONS
Signal Pin Pin Signal
-12V B01 A01 TRST#
TCK B02 A02 +12V
Ground B03 A03 TMS
TDO B04 A04 TDI
+5V B05 A05 +5V
+5V B06 A06 INTA#
INTB# B07 A07 INTC#
INTD# B08 A08 +5V
PRSNT1# B09 A09 Reserved
Reserved B10 A10 +5V
PRSNT2# B11 A11 Reserved
Signal Pin Pin Signal
Ground B12 A12 Ground
Ground B13 A13 Ground
Reserved B14 A14 Reserved
Ground B15 A15 RST#
CLK B16 A16 +5V
Ground B17 A17 GNT#
REQ# B18 A18 Ground
+5V B19 A19 Reserved
AD[31] B20 A20 AD[30]
AD[29] B21 A21 +3.3V
Ground B22 A22 AD[28]
AD[27] B23 A23 AD[26]
AD[25] B24 A24 Ground
+3.3V B25 A25 AD[24]
C/BE[3]# B26 A26 IDSEL
AD[23] B27 A27 +3.3V
Ground B28 A28 AD[22]
AD[21] B29 A29 AD[20]
AD[19] B30 A30 Ground
+3.3V B31 A31 AD[18]
AD[17] B32 A32 AD[16]
C/BE[2]# B33 A33 +3.3V
Ground B34 A34 FRAME#
IRDY# B35 A35 Ground
+3.3V B36 A36 TRDY#
DEVSEL# B37 A37 Ground
Ground B38 A38 STOP#
LOCK# B39 A39 +3.3V
PERR# B40 A40 SDONE
+3.3V B41 A41 SBO#
SERR# B42 A42 Ground
+3.3V B43 A43 PAR
C/BE[1]# B44 A44 AD[15]
AD[14] B45 A45 +3.3V
Ground B46 A46 AD[13]
AD[12] B47 A47 AD[11]
AD[10] B48 A48 Ground
Ground B49 A49 AD[09]
KEYWAY KEYWAY
KEYWAY KEYWAY
AD[08] B52 A52 C/BE[0]#
AD[07] B53 A53 +3.3V
+3.3V B54 A54 AD[06]
AD[05] B55 A55 AD[04]
AD[03] B56 A56 Ground
Ground B57 A57 AD[02]
AD[01] B58 A58 AD[00]
+5V B59 A59 +5V
ACK64# B60 A60 REQ64#
+5V B61 A61 +5V
+5V B62 A62 +5V
(#) s used to indicate an active-low signal.
BOLD ITALIC Logic Lines are NOT USED by the carrier board.
DATA TRANSFER TIMING
All PCI bus read or write cycles to the APC8620/8621 are
typically implemented within 150n seconds (FRAME# active to
TRDY# active). After 150n seconds the PCI bus is available to
the system for other PCI bus activity. As the PCI bus is released,
the APC8620/8621 completes the read or write cycle to the
targeted IP module or carrier register within the access times
given in Table 2.3.
Bracket End
Artisan Technology Group - Quality Instrumentation ... Guaranteed | (888) 88-SOURCE | www.artisantg.com

INDUSTRIAL I/O PACK SERIES APC8620/8621 PCI BUS CARRIER BOARD
___________________________________________________________________________________________
- 6 -
TABLE 2.3: APC8620/8621 Write and Read Complete Time
Register Data Transfer Time
Carrier Registers Write 650nS, Typical1
8 and 16-bit IP Write 750nS, Typical1,2
32-bit IP Write 1250nS, Typical1,3
Carrier Register Read 500nS, Typical1
8 and 16-bit IP Read 650nS, Typical1,2
32-bit IP Read 1100nS, Typical1,3
Notes (Table 2.3):
1. The data transfer times given in table 2.3 are measured from
the falling edge of FRAME# to the falling edge of LRDYi#.
The PCI bus starts a data transfer cycle by driving FRAME#
low. The APC8620/8621 signals the completion of a read or
write cycle by driving LRDYi# low.
2. This access time assumes zero IP module wait states. For
each IP module wait state 125n seconds must be added to
this value.
3. This access time assumes zero IP module wait states. For
each IP module wait state 250n seconds must be added to
this value.
FIELD GROUNDING CONSIDERATIONS
Carrier boards are designed with passive filters on each
supply line to each IP module. This provides maximum filtering
and signal decoupling between the IP modules and the carrier
board. However, the boards are considered non-isolated, since
there is electrical continuity between the PCI bus and the IP
grounds. Therefore, unless isolation is provided on the IP
module itself, the field I/O connections are not isolated from the
PCI bus. Care should be taken in designing installations without
isolation to avoid ground loops and noise pickup. This is
particularly important for analog I/O applications when a high
level of accuracy/resolution is needed (12-bits or more). Contact
your Acromag representative for information on our many isolated
signal conditioning products that could be used to interface to the
IP input/output modules.
3.0 PROGRAMMING INFORMATION
This Section provides the specific information necessary to
program and operate the APC8620/8621 non-intelligent carrier
board.
This Acromag APC8620/8621 is a PCI Specification version
2.1 compliant PCI bus slave carrier board. The carrier connects
a PCI host bus to the IP module’s 16-bit data bus per the
Industrial I/O Pack logic interface specification on the mezzanine
(IP) boards which are installed on the carrier.
The PCI bus is defined to address three distinct address
spaces: I/O, memory, and configuration space. The IP modules
can be accessed via the PCI bus memory space only.
The PCI card’s configuration registers are initialized by
system software at power-up to configure the card. The PCI
carrier is a Plug-and-Play PCI card. As a Plug-and-Play card the
board’s base address and system interrupt request line are not
selected via jumpers but are assigned by system software upon
power-up via the configuration registers. A PCI bus configuration
access is used to access a PCI card’s configuration registers.
PCI Configuration Address Space
When the computer is first powered-up, the computer’s
system configuration software scans the PCI bus to determine
what PCI devices are present. The software also determines the
configuration requirements of the PCI card.
The system software accesses the configuration registers to
determine how many blocks of memory space the carrier
requires. It then programs the carrier’s configuration registers
with the unique memory address range assigned.
The configuration registers are also used to indicate that the
PCI carrier requires an interrupt request line. The system
software then programs the configuration registers with the
interrupt request line assigned to the PCI carrier.
Since this PCI carrier is relocatable and not hardwired in
address space, this carrier’s device drive provided by Acromag
uses the mapping information stored in the carrier’s Configuration
Space registers to determine where the carrier is mapped in
memory space and which interrupt line will be used.
Configuration Transactions
The PCI bus is designed to recognize certain I/O accesses
initiated by the host processor as a configuration access.
Configuration uses two 32-bit I/O ports located at addresses
0CF8 and 0CFC hex. These two ports are:
•32-bit configuration address port, occupying I/O addresses
0CF8 through 0CFB hex.
•32-bit configuration data port, occupying I/O addresses
0CFC through 0CFF hex.
Configuration space is accessed by writing a 32-bit long-word
into the configuration address port that specifies the PCI bus, the
carrier board on the bus, and the configuration register on the
carrier being accessed. A read or write to the configuration data
port will then cause the configuration address value to be
translated to the requested configuration cycle on the PCI bus.
Accesses to the configuration data port determine the size of the
access to the configuration register addressed and can be an 8,
16, or 32-bit operation.
Any access to the Configuration address port that is not a
32-bit access is treated like a normal computer I/O access.
Thus, computer I/O devices using 8 or 16-bit registers are not
affected because they will be accessed as expected.
Table 3.1: Configuration Address Port
BIT FUNCTION
31 Enables accesses to Configuration Data to be
translated to configuration cycles on the PCI bus.
30-24 Reserved, Return 0 when read.
23-16 Bus Number
Choose a specific PCI bus in the system. Zero
if only one PCI bus.
15-11 Device Number
Choose a specific device/PCI board on the
bus.
10-8 Function Number
Choose a specific function in a device.
Function number is zero for the APC8620/8621
7-2 Register Number
Used to indicate which PCI Configuration
Register to access. The Configuration
Registers and their corresponding register
numbers are given in Table 3.2.
1-0 Read Only bits that return 0.
Artisan Technology Group - Quality Instrumentation ... Guaranteed | (888) 88-SOURCE | www.artisantg.com

INDUSTRIAL I/O PACK SERIES APC8620/8621 PCI BUS CARRIER BOARD
___________________________________________________________________________________________
- 7 -
Configuration Registers
The PCI specification requires software driven initialization
and configuration via the Configuration Address space. This PCI
carrier provides 256 bytes of configuration registers for this
purpose. The PCI carrier contains the configuration registers,
shown in Table 3.2, to facilitate Plug-and-Play compatibility.
The Configuration Registers are accessed via the
Configuration Address and Data Ports. The most important
Configuration Registers are the Base Address Registers and the
Interrupt Line Register which must be read to determine the base
address assigned to the carrier and the interrupt request line that
goes active on a carrier interrupt request.
Table 3.2 Configuration Registers
Reg.
Num. D31
D24 D23
D16 D15
D8 D7
D0
0Device ID=1024 Vendor ID= 10B5
1Status Command
2Class Code Rev ID
3BIST Header Latency Cache
4Base Addr. Memory Mapped Configuration Registers
5Base Address for I/O Mapped Configuration Registers
632-bit Memory Base Address for APC8620/8621
7 : 10 Not Used
11 Subsystem ID Subsystem Vendor ID
12 Not Used
13 Reserved
14 Reserved
15 Max_Lat Min_Gnt Inter. Pin Inter. Line
MEMORY MAP
The 1K byte of memory consumed by the board is composed
of blocks of memory for the ID, I/O and INT spaces
corresponding to five IP modules. In addition, a small portion of
the 1K byte address space contains registers specific to the
function of the carrier board.
The carrier is configured to map this 1K byte block of memory
into 32-bit memory space. The system configuration software will
allocate space by writing the assigned address into the
corresponding Base Address register of the Configuration
Registers. The memory map for APC8620/8621 is shown in
Tables 3.3.
Table 3.3: APC8620/8621 Carrier Bd Memory Map
Base
Address +
(Hex) High Byte
D15 D08 Low Byte
D07 D00
Base
Address +
(Hex)
0001 Bit-8 Software
Reset Carrier Board
Status/Control 0000
0003 IP Interrupt Pending Register 0002
0005 IP A Interrupt 0 Select Space 0004
0007 IP A Interrupt 1 Select Space 0006
0009 IP B Interrupt 0 Select Space 0008
000B IP B Interrupt 1 Select Space 000A
000D IP C Interrupt 0 Select Space 000C
000F IP C Interrupt 1 Select Space 000E
0011 IP D Interrupt 0 Select Space 0010
0013 IP D Interrupt 1 Select Space 0012
0015 IP E Interrupt 0 Select Space 0014
0017 IP E Interrupt 1 Select Space 0016
Base
Address +
(Hex) High Byte
D15 D08 Low Byte
D07 D00
Base
Address +
(Hex)
0019
↓
↓↓
↓
003F Not Used Not Used 0018
↓
↓↓
↓
003E
0041
↓
↓↓
↓
007F
IP A
ID Space IP A
ID Space 0040
↓
↓↓
↓
007E
0081
↓
↓↓
↓
00BF
IP B
ID Space IP B
ID Space 0080
↓
↓↓
↓
00BE
00C1
↓
↓↓
↓
00FF
IP C
ID Space IP C
ID Space 00C0
↓
↓↓
↓
00FE
0101
↓
↓↓
↓
013F
IP D
ID Space IP D
ID Space 0100
↓
↓↓
↓
013E
0141
↓
↓↓
↓
017F
IP E
ID Space IP E
ID Space 0140
↓
↓↓
↓
017E
0181
↓
↓↓
↓
01FF
IP A
I/O Space IP A
I/O Space 0180
↓
↓↓
↓
01FE
0201
↓
↓↓
↓
027F
IP B
I/O Space IP B
I/O Space 0200
↓
↓↓
↓
027E
0281
↓
↓↓
↓
02FF
IP C
I/O Space IP C
I/O Space 0280
↓
↓↓
↓
02FE
0301
↓
↓↓
↓
037F
IP D
I/O Space IP D
I/O Space 0300
↓
↓↓
↓
037E
0381
↓
↓↓
↓
03FF
IP E
I/O Space IP E
I/O Space 0380
↓
↓↓
↓
03FE
Note: Shaded areas not used by ACP8621 carrier.
The APC8620/8621 base address is determined through the
PCI Configuration Registers. The addresses given in Table 3.3
are relative to the base address of the APC8620/8621 carrier.
The addresses within each IP’s own space are specific to that IP
module. Refer to the IP module’s User Manual for information
relating to the IP specific addressing.
The Carrier registers, IP Identification (ID) spaces, IP
Input/Output (IO), and IP Interrupt spaces are accessible via the
PCI bus space as given in Tables 3.3. A 32-bit PCI bus access
will result in two 16-bit accesses to the IP module. A 16-bit or 8-
bit PCI bus access results in a s-ingle 16-bit or 8-bit access to the
IP module respectively.
Artisan Technology Group - Quality Instrumentation ... Guaranteed | (888) 88-SOURCE | www.artisantg.com

INDUSTRIAL I/O PACK SERIES APC8620/8621 PCI BUS CARRIER BOARD
___________________________________________________________________________________________
- 8 -
Carrier Status/Control Register - (Read/Write, Base + 00H)
The Carrier Board Status Register reflects and controls
functions globally on the carrier board.
BIT FUNCTION
15-09 Not Used
08
Write
Only
Software Reset
Writing a “1” to this bit causes a software reset.
Writing a “0” or reading this bit has no effect.
When set, the software reset pulse will have a
duration of 1u second.
07-06 Not Used
05
Read
And
Write
IP Module Access Time Out Interrupt Pending
This bit will be "1" when there is a IP Module
Access Time Out interrupt pending. This bit
will be "0" when there is no interrupt pending.
Reset condition: Set to "0". Writing a “1” to
this bit will release the pending interrupt.
04
Read
Only
IP Module Access Time Out Status
Status bit to indicated that the last IP module
access has timed out. This bit only reflects the
last IP module access.
“0” if last IP module access did not time out.
“1” if last IP module access did time out.
03
Read
And
Write
Time Out Interrupt Enable
When set to “1”, this bit will enable the carrier
board to generate an interrupt upon time out of
an IP module access. The default setting or
reset condition is “0” (interrupt generation upon
time out disabled). The interrupt service
routine, in responding to the Time Out Access
interrupt, will need to set this bit to 0 to clear
the pending interrupt request.
02
Read
And
Write
IP Module Interrupt Enable
When set to “1”, this bit will enable the
generation of IP module interrupts. The default
setting or reset condition is “0” (IP module
interrupt generation disabled). Interrupts must
also be supported and configured at the IPs.
01
Read
Only
IP Module Interrupt Pending
This bit will be "1" when there is an interrupt
pending. This bit will be "0" when there is no
interrupt pending. Polling this bit will reflect the
IP Module’s pending interrupt status, even if
the IP Module Interrupt Enable bit is set to "0".
Reset condition: Set to "0".
00
Read
Only
IP Module Error
This bit will be "1" when there is an active IP
Module Error signal. This bit will be "0" when
all IP module Error signals are inactive. This
bit allows the user to monitor the Error signals
of IP modules A through E (A through C for
APC8621). The Industrial I/O Pack
specification states that the error signals
indicate a non-recoverable error from the IP
(such as a component failure or hard-wired
configuration error). Refer to your IP specific
documentation to see if the error signal is
supported and what it indicates. Reset
condition: Set to "0".
IP Interrupt Pending Register - (Read, Base + 02H)
The IP Interrupt Pending Register is used to individually
identify pending IP interrupts or a pending carrier generated
interrupt as a result of IP module time out access. If multiple IP
interrupts are pending, software must determine the order in
which they are serviced.
MSB
D7 D6 D5 D4 D3 D2 D1 LSB
D0
IP D
Int1
Pend
IP D
Int0
Pend
IP C
Int1
Pend
IP C
Int0
Pend
IP B
Int1
Pend
IP B
Int0
Pend
IP A
Int1
Pend
IP A
Int0
Pend
MSB
D15 D14 D13 D12 D11 D10 D9 LSB
D8
Not
Used Time Out
Interrupt
Pend
IP E
Int1
Pend
IP E
Int0
Pend
Note: Shaded areas not used by ACP8621 carrier.
Where:
All Bits
IP Interrupt
Pending
(Read)
A bit will be a “1” when the corresponding
interrupt is pending. A bit will be a “0”
when its corresponding interrupt is not
pending. Polling this bit will reflect the IP
module’s pending interrupt status, even if
the IP interrupt enable bit is set to “0”.
Reset Condition: Set to "0". An IP
module pending interrupt bit will be
cleared if its correspond interrupt request
signal is inactive.
IP Module Interrupt Space - (Read Only)
The Interrupt space for each IP module is fixed at two 16-bit
words. Interrupt 0 select space is read, typically by an interrupt
service routine, to respond to an interrupt request via the IP
Module’s INTREQ0* signal. Likewise interrupt 1 select space is
read to respond to an interrupt request via the IP Module’s
INTREQ1* signal. An access to an interrupt select space results
in the IP module serving up an interrupt vector. In addition,
access to the interrupt space will cause some IP modules to
release their interrupt request. See each IP module’s User
Manual for details.
IP Module ID Space- (Read Only)
Each IP contains identification (ID) information that resides in
the ID space per the IP specification. This area of memory
contains either 32 bytes (Format I ID) or 64 bytes (Format II ID)
of information, at most. Format I requires read of only the least
significant byte. Format II requires read of a 16-bit value. The
carrier will implement 16-bit reads to the ID space to allow
support for either Format I or Format II. Both fixed and variable
information may be present within the ID ROM. Variable
information may include unique information required for the
module. The identification Section for each IP module is located
in the carrier board memory map per Table 3.3. Refer to the
documentation of your IP module for specific information about
each IP module’s ID Space contents.
Artisan Technology Group - Quality Instrumentation ... Guaranteed | (888) 88-SOURCE | www.artisantg.com

INDUSTRIAL I/O PACK SERIES APC8620/8621 PCI BUS CARRIER BOARD
___________________________________________________________________________________________
- 9 -
IP Module I/O Space - (Read/Write Only, 256-Byte Addresses)
The I/O space on each IP module is fixed at 128, 16-bit
words (256 bytes). The five (three for APC8621) IP module I/O
spaces are accessible at fixed offsets for the APC8620/8621’s
Base Address. IP modules may not fully decode their I/O space
and may use byte or word only accesses. See each IP module’s
User Manual for details.
GENERATING INTERRUPTS
Interrupt requests originate from the carrier board in the case
of an access time out and from the IP modules. Each IP may
support 0, 1, or 2 interrupt requests. Upon an IP module interrupt
request the carrier passes the interrupt request onto the host,
provided that the carrier board is enabled for interrupts within the
Carrier Board Status Register.
Sequence of Events For an Interrupt
1. Clear the interrupt enable bits in the Carrier Board Status
Register by writing a "0" to bit 2/bit 3.
2. Write interrupt vector to the location specified on the IP and
perform any other IP specific configuration required - do for
each supported IP interrupt request.
3. Determine the IRQ line assigned to the carrier during
system configuration (within the configuration register).
4. Set up the PC/AT’s interrupt vector for the appropriate
interrupt.
5. Unmask the IRQ on the PC/AT’s 8259 interrupt controller.
6. The IP asserts an interrupt request to the carrier board
(asserts interrupt request line IntReq0* or IntReq1*).
7. The carrier drives PCI bus interrupt request signal INTA#
active.
8. PC/AT’s drives the IRQ line assigned to the active carrier.
9. The interrupt service routine pointed to by the vector set up
in step 4 starts.
10. Interrupt service routine determines which IP module caused
the interrupt by reading the carrier interrupt pending register.
If multiple interrupts are pending the interrupt service routine
software determines which IP module to service first. In a
PC interrupts are shared and can be from any slot on the
backplane or from the mother board itself. The driver must
first check that the interrupt came from the PCI carrier by
reading the carrier interrupt pending register.
11. The interrupt service routine accesses the interrupt space of
the IP module selected to be serviced. Note that the
interrupt space accessed must correspond to the interrupt
request signal driven by the IP module.
12. The carrier board will assert the INTSEL* signal to the
appropriate IP together with (carrier board generated)
address bit A1 to select which interrupt request is being
processed (A1 low corresponds to INTREQ0*; A1 high
corresponds to INTREQ1*).
13. The IP module receives an active INTSEL* signal from the
carrier and supplies its interrupt vector to the host system
during this interrupt acknowledge cycle. An IP module
designed to release its interrupt request on acknowledge will
release its interrupt request upon receiving an active
INTSEL* signal from the carrier. If the IP module is
designed to release it’s interrupt request on register access
the interrupt service routine must access the required
register to clear the interrupt request.
14. Write “End-Of-Interrupt” command to PC/AT’s 8259.
15. If the IP interrupt stimulus has been removed and no other
IP modules have interrupts pending, the interrupt cycle is
completed (i.e. the carrier board negates its interrupt request
INTA#).
4.0 THEORY OF OPERATION
This section describes the basic functionality of the circuitry
used on the carrier board. Refer to the Block Diagram shown in
the Drawing 4501-673 as you review this material.
CARRIER BOARD OVERVIEW
The carrier board is a PCI bus slave/target board providing up
to five (three for APC8621) industry standard IP module
interfaces. The carrier board’s PCI bus interface allows an
intelligent single board computer (PCI bus Master) to control and
communicate with IP modules that are present on the PCI bus
carrier. IP module field I/O connections link to the field I/O
connections of the carrier which in turn are used to connect field
electronic hardware to the carrier board via ribbon cable.
The PCI bus and IP module logic commons have a direct
electrical connection (i.e., they are not electrically isolated).
However, the field I/O connections can be isolated from the PCI
bus if an IP module that provides this isolation (between the logic
and field side) is utilized. A wide variety of IP modules are
currently available (from Acromag and other vendors) that allow
interface to many external devices for digital I/O, analog I/O, and
communication applications.
PCI Bus Interface
The carrier board’s PCI bus interface is used to program and
monitor carrier board registers for configuration and control of the
board’s documented modes of operation (see section 3). In
addition, the PCI bus interface is also used to communicate with
and control external devices that are connected to an IP module’s
field I/O signals (assuming an IP module is present on the carrier
board).
The PCI bus interface is implemented in the logic of the
carrier board’s PCI bus target interface chip. The PCI bus
interface chip implements PCI specification version 2.1 as an
interrupting slave including 8-bit and 16-bit data transfers to the
IP modules.
The carrier board’s PCI bus data transfer rates are shown in
Table 2.3.
Carrier Board Registers
The carrier board registers (presented in section 3) are
implemented in the logic of the carrier board’s FPGA. An outline
of the functions provided by the carrier board registers includes:
•Monitoring the error signal received from each IP module is
possible via the IP Error Bit.
•Enabling of PCI bus interrupt requests from each IP module
is possible via the IP Module Interrupt Enable Bit.
•Enabling of interrupt generation upon an IP module access
time out is implemented via the Time Out Interrupt Enable
Bit.
•Monitoring an IP module access time out is possible via the
IP Module Access Time Out Status Bit.
•Identify pending interrupts via the carrier’s IP Module
Interrupt Pending Bit.
•Lastly, pending interrupts can be individually monitored via
the IP Module Interrupt Pending register.
Artisan Technology Group - Quality Instrumentation ... Guaranteed | (888) 88-SOURCE | www.artisantg.com

INDUSTRIAL I/O PACK SERIES APC8620/8621 PCI BUS CARRIER BOARD
___________________________________________________________________________________________
- 10 -
IP Logic Interface
The IP logic interface is also implemented in the logic of the
carrier board’s FPGA. The carrier board implements ANSI/VITA
4 1995 Industrial I/O Pack logic interface specification and
includes five (three for APC8621) IP logic interfaces. The PCI
bus address and data lines are linked to the address and data of
the IP logic interface. This link is implemented and controlled by
the carrier board’s FPGA.
The PCI bus to IP logic interface link allows a PCI bus master
to:
•Access up to 64 ID Space bytes for IP module identification
via 8-bit or 16-bit data transfers using PCI bus.
•Access up to 128 I/O Space bytes of IP data via 8-bit or 16-
bit data transfers.
•Access IP module interrupt space via 8-bit or 16-bit PCI bus
data transfers.
•Respond to two IP module interrupt requests per IP module.
Carrier Board Clock Circuitry
A 16MHz clock is divided down by a clock driver to obtain the
IP module 8MHz clock signals. Separate IP clocks are driven to
each IP module. All clock lines include series damping resistors
to reduce clock overshoot and undershoot.
When an IP module places data on the bus, for all data read
cycles, any undriven data lines are read by the PCI bus as high
because of pull-up resisters on the carrier board’s data bus.
PCI Interrupter
Interrupts are initiated from an interrupting IP module.
However, the carrier board will only pass an interrupt generated
by an IP module to the PCI bus if the carrier board has been first
enabled for interrupts. Each IP module can initiate two interrupts
which can be individually monitored on the carrier board. After
interrupts are enabled on the carrier board via the Interrupt
Enable Bits (see section 3 for programming details), an IP
generated interrupt is recognized by the carrier board and is
recorded in the carrier board’s Interrupt Pending Register.
A carrier board pending interrupt will cause the board to pass
the interrupt to the PCI bus provided the Interrupt Enable bits of
the carrier’s Status Register have been enabled (see section 3 for
programming details). The PC interrupt request line assigned by
the system configuration software will then be asserted. The
PC/AT will respond to the asserted interrupt line by executing the
interrupt service routine corresponding to the interrupt line
asserted. The interrupt service routine is executed only if the IRQ
on the PC/AT’s 8259 interrupt controller has been previously
unmasked (see section 3 for programming details).
The interrupt service routine should respond to an interrupt by
accessing IP Interrupt Select (INTSEL*) space. The interrupt
service routine should also conclude the interrupt routine by
writing the “End-Of-Interrupt” command to the PC/AT’s 8259
interrupt controller (see section 3 for more details).
Power Failure Monitor
The carrier board contains a 5 volts undervoltage monitoring
circuit which provides a reset to the IP modules when the 5 volt
power drops below 4.27 volts typical / 4.15 volts minimum. This
circuitry is implemented per the Industrial I/O Pack specification.
Power Supply Fuses
The +5V, supply lines to each of the IP modules are
individually fused with a current limit of 2 amp imposed by the
fuses. In addition, the +12, and -12 supply lines to each of the
IP modules are individually fused with a current limit of 1 amp
imposed by the fuses. A blown fuse can be identified by visible
inspection or by use of an ohm meter. The fuses are located
under each IP slot near the “logic connectors” (see figure 4501-
671 or 4501-676).
Power Supply Filters
Power line filters are dedicated to each IP module for filtering
of the +5, +12, and -12 volt supplies. The power line filters are a
“T” type filter circuit comprising ferrite bead inductors and a feed-
through capacitor. The filters provide improved noise
performance as is required on precision analog IP modules.
5.0 SERVICE AND REPAIR
SERVICE AND REPAIR ASSISTANCE
Surface-Mounted Technology (SMT) boards are generally
difficult to repair. It is highly recommended that a non-functioning
board be returned to Acromag for repair. The board can be
damaged unless special SMT repair and service tools are used.
Further, Acromag has automated test equipment that thoroughly
checks the performance of each board. When a board is first
produced and when any repair is made, it is tested, placed in a
burn-in room at elevated temperature, and retested before
shipment.
Please refer to Acromag's Service Policy Bulletin or contact
Acromag for complete details on how to obtain parts and repair.
PRELIMINARY SERVICE PROCEDURE
Before beginning repair, be sure that all of the procedures in
Section 2, Preparation For Use, have been followed. Also, refer
to the documentation of your carrier board to verify that it is
correctly configured. Verify that there are no blown fuses.
Replacement of the carrier and/or IP with one that is known to
work correctly is a good technique to isolate a faulty board.
CAUTION: POWER MUST BE TURNED OFF BEFORE
REMOVING OR INSERTING BOARDS
Acromag’s Applications Engineers can provide further
technical assistance if required. When needed, complete repair
services are also available from Acromag.
Artisan Technology Group - Quality Instrumentation ... Guaranteed | (888) 88-SOURCE | www.artisantg.com

INDUSTRIAL I/O PACK SERIES APC8620/8621 PCI BUS CARRIER BOARD
___________________________________________________________________________________________
- 11 -
6.0 SPECIFICATIONS
PHYSICAL
Physical Configuration....................PCI 5V Card
Length (APC8620)...................12.283 inches (312.0 mm)
Length (APC8621)................... 6.600 inches (167.64 mm)
Height.......................................4.200 inches (106.68 mm)
Board Thickness.................…..0.063 inches (1.60 mm)
Max Component Height............0.380 inches (9.65 mm)
Max Component
Height Under IP Modules…......0.180 inches (4.57 mm)
Connectors:
P1 (PCI Bus)........................….PCI Specification 2.1 5V brd
card edge “finger” spacing
A-E (Carrier Field I/O).........…..50-pin Male Header with
(For APC8620) ejector latches.
A-C (Carrier Field I/O).........…..50-pin Male Header without
(For APC8621) ejector latches.
P4,5, 9, 12, 15 (IP Field I/O).....50-pin male plug header
(P3, 6, 9 for APC8621) (AMP 173280-3 or
equivalent).
P6, 7, 10, 13, 16 (IP Logic)…...50-pin male plug header (AMP
(P4, 7, 10 for APC8621) 173280-3 or equivalent).
Power:
Board power requirements are a function of the installed IP
modules. This specification lists currents for the carrier board
only. The carrier board provides +5V, +12V and -12V power
to each IP from the PCI bus. Each IP module supply line is
individually filtered and fused.
Fuses: +5 volts, 2 amp per slot
±12 volts, 1 amp per slot
The power failure monitor circuit provides a reset to IP
modules when the 5 volt power drops below 4.27 volts
typically / 4.15 volts minimum.
Currents specified are for the carrier board only for Models
AP8620/8621, add the IP module currents for the total
current required from each supply.
+5 Volts (±5%)...................…...210mA, Typical
300mA, Maximum.
+12 Volts (±5%)...........….........0mA (Not Used)
-12 Volts (±5%)................….....0mA (Not Used)
PCI BUS COMPLIANCE
Specification..................................This device meets or exceeds
all written PCI Local Bus
specifications per revision 2.1
dated June 1995.
Data Transfer Bus.........................Slave with 32-bit, 16-bit, and
8-bit data transfer operation.
32-bit read or write accesses
are implemented as two 16
bit transfers to the IP modules.
PCI bus Write Cycle Time.....…....150nS Typical measured from
falling edge of FRAME# to the
falling edge of TRDY#.
PCI bus Read Cycle Time………..150nS Typical; The carrier
issues a RETRY which frees
the PCI bus while the read
request is completed. The PCI
bus will repeat the same read
request until it completes with
the requested data.
Write Complete Time……..………Time from FRAME# active
until LRDYi# active.
650nS Typical carrier register
750nS Typical 8-bit and 16-bit
IP module write (assuming 0
IP module wait states).
1250nS Typical 32-bit IP
module write (assuming 0 IP
module wait states).
Read Complete Time…….……….Time from FRAME# active
until LRDYi# active.
500nS Typical carrier register
650nS Typical 8-bit and 16-bit
IP module read (assuming 0
IP module wait states).
1100nS Typical 32-bit IP
module read (assuming 0 IP
module wait states).
Interrupts...................................….PCIbus INTA# interrupt signal
Up to two requests sourced
from each IP mapped to
INTA#. Interrupt vectors
come from IP modules via
access to IP module INT
space.
32-bit Memory Space.....................Upon power-up the system
auto- configuration process
(plug & play) maps the
carriers base address (for a
1K byte block of memory)
into the PCI bus 32-bit
Memory Space.
INDUSTRIAL I/O PACK COMPLIANCE
Specification.............................….This device meets or exceeds
all written Industrial I/O Pack
specifications per ANSI/VITA 4
1995 for 8MHz operation, only.
Supports Type I and Type II ID
space formats.
Electrical/Mechanical Interface.....Carrier supports five single-
(For APC8620) size IP modules (A-E), or two
double-size and one single
size IP module. 32-bit IP
modules are not supported.
Electrical/Mechanical Interface.....Carrier supports three single-
(For APC8621) size IP modules (A-C), or one
double-size and one single
size IP module. 32-bit IP
modules are not supported.
I/O Space..................................…16-bit and 8-bit:
Supports 128 byte values per
IP module.
ID Space...................................…16 and 8-bit; Supports Type 1
32 bytes per IP (consecutive
odd byte addresses). Also
supports Type II 32 words per
IP via D16 data transfers.
Memory Space.........................….Not Supported.
Interrupts.................................…..Supports two interrupt requests
per IP and interrupt
acknowledge cycles via
access to IP INT space.
Artisan Technology Group - Quality Instrumentation ... Guaranteed | (888) 88-SOURCE | www.artisantg.com

INDUSTRIAL I/O PACK SERIES APC8620/8621 PCI BUS CARRIER BOARD
___________________________________________________________________________________________
- 12 -
ENVIRONMENTAL
Operating Temperature.................0 to +70°C;
-40 to +85°C (E Versions)
Relative Humidity..........................5-95% non-condensing
Storage Temperature....................-55 to +100°C.
Non-Isolated...........................…...PCI bus and IP module logic
commons have a direct
electrical connection. As such,
unless the IP module provides
isolation between the logic and
field side, the field I/O signals
are not isolated from the PCI
bus.
Radiated Field Immunity (RFI)......Designed to comply with
IEC1000-4-3 Level 3 (10V/m at
frequencies 27MHz to 500MHz)
and European Norm
EN50082-1.
Electromagnetic Interference
Immunity (EMI)…..............…........No digital upset under the
influence of EMI from
switching solenoids,
commutator motors, and drill
motors.
Electrostatic Discharge
Immunity (ESD)…..............….......Complies with IEC1000-4-2
Level 1 (2KV direct contact
discharge) at field input/output
terminals and European Norm
EN50082-1.
Surge Immunity…………………...Complies with IEC1000-4-5,
Level 2 (1KV) and European
Norm EN50082-1 at field input/
output terminals.
Electric Fast Transient
Immunity EFT..……………….......Complies with IEC1000-4-4
Level 2 (1KV power terminals;
0.5KV at field input and output
terminals) and European
Norm EN50082-1.
Radiated Emissions………..……..Meets or exceeds European
Norm EN50081-1 for class A
equipment.
APPENDIX
CABLE: MODEL 5025-550-x (Non-Shielded)
MODEL 5025-551-x (Shielded)
Type: Flat Ribbon Cable, 50-wires (female connectors at both
ends). The ‘-x’ suffix designates the length in feet (12 feet
maximum). Choose shielded or unshielded cable according
to model number. The unshielded cable is recommended for
digital I/O, while the shielded cable is recommended for
optimum performance with precision analog I/O applications.
Application: Used to connect Model 5025-552 termination panel
to carrier board 50-pin field connectors.
Length: Last field of part number designates length in feet (user-
specified, 12 feet maximum). It is recommended that this
length be kept to a minimum to reduce noise and power loss.
Cable: 50-wire flat ribbon cable, 28 gage. Non-Shielded cable
model uses Acromag Part 2002-211 (3M Type C3365/50 or
equivalent). Shielded cable model uses Acromag Part 2002-
261 (3M Type 3476/50 or equivalent).
Headers (Both Ends): 50-pin female header with strain relief.
Header - Acromag Part 1004-512 (3M Type 3425-6600 or
equivalent). Strain Relief - Acromag Part 1004-534 (3M Type
3448-3050 or equivalent).
Keying: Headers at both ends have polarizing key to prevent
improper installation.
Schematic and Physical Attributes: For Non-Shielded cable
model, see Drawing 4501-462. For Shielded cable model,
see Drawing 4501-463.
Shipping Weight: 1.0 pound (0.5Kg), packed.
CABLE: MODEL 5029-943
Type: Model 5029-943 IP500 Communication Cable: A five foot
long, flat 50-pin cable with a female connector on one end
(for connection to carrier board) and four DE-9P connectors
(serial ports) on the other end.
Application: Used to connect up to four DB-9 serial ports to
carrier board connectors. It is used primarily with Acromag
Model IP500, IP501, & IP502 serial communication modules.
Length: 5 feet.
Cable: 50-wire flat ribbon cable, 28 gage. Non-Shielded cable
model uses Acromag Part 2002-211 (3M Type C3365/50 or
equivalent).
Headers: 50-pin female header with strain relief. Header -
Acromag Part 1004-512 (3M Type 3425-6600 or equivalent).
Strain Relief - Acromag Part 1004-534 (3M Type 3448-3050
or equivalent).
Port Connectors: Four DE-9P (9-pin, D-SUB, Male) connectors
with strain relief (3M connector U89809-9000 with 3448-
8D09A strain relief, or equivalent).
Keying: 50-pin Header at one end has polarizing key to prevent
improper installation.
Shipping Weight: 1.0 pound (0.5Kg) packaged.
TERMINATION PANEL: MODEL 5025-552
Type: Termination Panel For Carrier Boards
Application: To connect field I/O signals to the Industrial I/O
Pack (IP). Termination Panel: Acromag Part 4001-040
(Phoenix Contact Type FLKM 50). The 5025-552 termination
panel facilitates the connection of up to 50 field I/O signals
and connects to the carrier boards via a flat ribbon cable
(Model 5025-550-x or 5025-551-x). The field connectors on
the carrier board connect the I/O signals to the P2 connector
on each of the Industrial I/O Pack modules. Field signals are
accessed via screw terminal strips. The terminal strip
markings on the termination panel (1-50) correspond to P2
(pins 1-50) on the Industrial I/O Pack (IP). Each Industrial I/O
Pack (IP) has its own unique P2 pin assignments. Refer to
the IP module manual for correct wiring connections to the
termination panel.
Schematic and Physical Attributes: See Drawing 4501-464.
Field Wiring: 50-position terminal blocks with screw clamps.
Wire range 12 to 26 AWG.
Connections to Carrier: P1, 50-pin male header with strain relief
ejectors. Use Acromag 5025-550-x or 5025-551-x cable to
connect panel to carrier board. Keep cable as short as
possible to reduce noise and power loss.
Mounting: Termination panel is snapped on the DIN mounting
rail.
Printed Circuit Board: Military grade FR-4 epoxy glass circuit
board, 0.063 inches thick.
Operating Temperature: -40°C to +100°C.
Storage Temperature: -40°C to +100°C.
Shipping Weight : 1.25 pounds (0.6kg) packed.
Artisan Technology Group - Quality Instrumentation ... Guaranteed | (888) 88-SOURCE | www.artisantg.com

INDUSTRIAL I/O PACK SERIES APC8620/8621 PCI BUS CARRIER BOARD
___________________________________________________________________________________________
- 13 -
APC8620 IP LOCATIONS
C
F7 F11
F9
F8
IPC
F10
F12
D E
F13 F15
IPD
BA
4.200
3.362
IPA
F2
F1
F3
F6
F5
IPB
F4
2.508 0.608
0.190
0.591
1.605
0.295
F14
3.525
IPE
0.200
0.150
0.325
4501-671B
FUSES
+5V(2 AMP)
+12V(1 AMP)
-12V(1 AMP) F3, 5, 8, 11 & 14
F2, 4, 7, 12 & 15
F1, 6, 9, 10 & 13
12.283
Artisan Technology Group - Quality Instrumentation ... Guaranteed | (888) 88-SOURCE | www.artisantg.com

INDUSTRIAL I/O PACK SERIES APC8620/8621 PCI BUS CARRIER BOARD
___________________________________________________________________________________________
- 14 -
APC8621 IP LOCATIONS
F4
F8
F5
F1
F3
F9
IPC
F2
F6
F7
C
FUSES
F1, 2 & 3
F4, 6 & 8
F5, 7 & 9
+5V(2 AMP)
+12V(1 AMP)
-12V(1 AMP)
0.325
0.608
3.362
4.200
ABIPA
IPB
2.508
1.605
0.591
0.295
0.190
6.600
4501-676A
Artisan Technology Group - Quality Instrumentation ... Guaranteed | (888) 88-SOURCE | www.artisantg.com

INDUSTRIAL I/O PACK SERIES APC8620/8621 PCI BUS CARRIER BOARD
___________________________________________________________________________________________
- 15 -
IP MODULE TO CARRIER BOARD MECHANICAL ASSEMBLY
ASSEMBLY PROCEDURE:
COMPONENT SIDE OF IP MODULE
SOLDER SIDE OF IP MODULE
1. THREADED SPACERS ARE PROVIDED BY ACROMAG IN TWO DIFFERENT
LENGTHS WITH IP MODULES. THE SHORTER LENGTH IS FOR USE WITH
APC8620 CARRIER BOARD (SHOWN).
2. INSERT FLAT HEAD SCREWS (ITEM A) THROUGH SOLDER SIDE OF
IP MODULE AND INTO HEX SPACERS (ITEM B) AND TIGHTEN (4 PLACES)
UNTIL HEX SPACER IS COMPLETELY SEATED.
M2 x 6
FLAT HEAD
SCREW
THREADED M2
3. CAREFULLY ALIGN IP MODULE TO CARRIER BOARD AND PRESS
TOGETHER UNTIL CONNECTORS AND SPACERS ARE SEATED.
4. INSERT PAN HEAD SCREWS (ITEM C) THROUGH SOLDER SIDE
OF CARRIER BOARD AND INTO HEX SPACERS (ITEM B) AND
TIGHTEN (4 PLACES).
COMPONENT SIDE OF CARRIER BOARD BRACKET
4501-672A
M2 x 6
PAN HEAD
SCREW
Artisan Technology Group - Quality Instrumentation ... Guaranteed | (888) 88-SOURCE | www.artisantg.com

INDUSTRIAL I/O PACK SERIES APC8620/8621 PCI BUS CARRIER BOARD
___________________________________________________________________________________________
- 16 -
4501-673B
Artisan Technology Group - Quality Instrumentation ... Guaranteed | (888) 88-SOURCE | www.artisantg.com

INDUSTRIAL I/O PACK SERIES APC8620/8621 PCI BUS CARRIER BOARD
___________________________________________________________________________________________
- 17 -
4501-462A
Artisan Technology Group - Quality Instrumentation ... Guaranteed | (888) 88-SOURCE | www.artisantg.com

INDUSTRIAL I/O PACK SERIES APC8620/8621 PCI BUS CARRIER BOARD
___________________________________________________________________________________________
- 18 -
4501-463A
Artisan Technology Group - Quality Instrumentation ... Guaranteed | (888) 88-SOURCE | www.artisantg.com

INDUSTRIAL I/O PACK SERIES APC8620/8621 PCI BUS CARRIER BOARD
___________________________________________________________________________________________
- 19 -
4501-464A
Artisan Technology Group - Quality Instrumentation ... Guaranteed | (888) 88-SOURCE | www.artisantg.com
This manual suits for next models
1
Table of contents
Other Acromag Carrier Board manuals
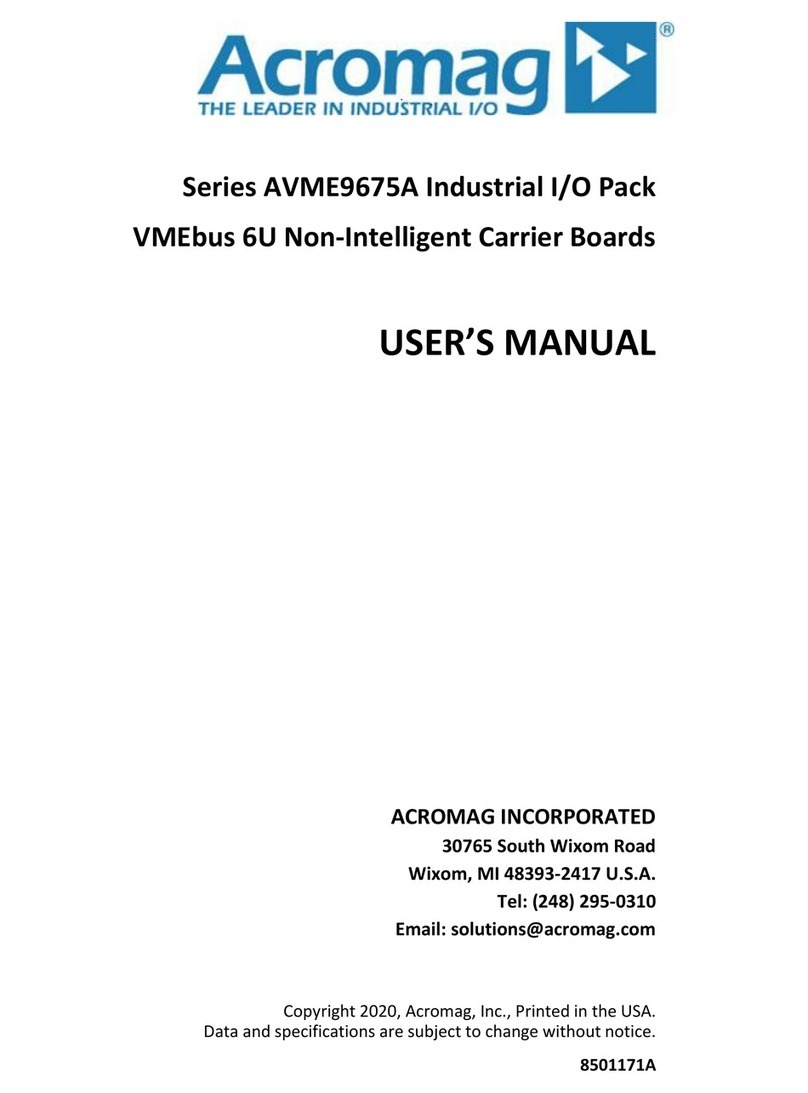
Acromag
Acromag AVME9675A Series User manual
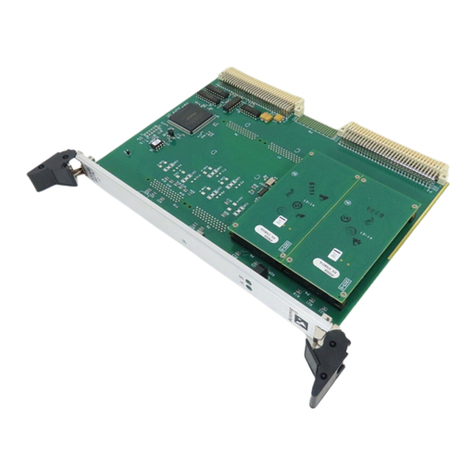
Acromag
Acromag AVME9675 Series User manual
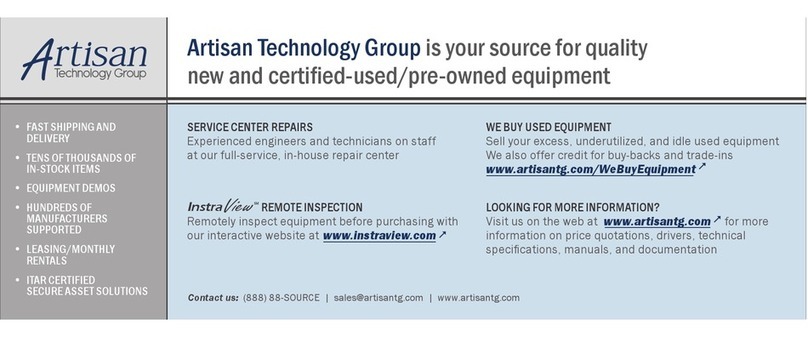
Acromag
Acromag ACPC4610E/CC User manual
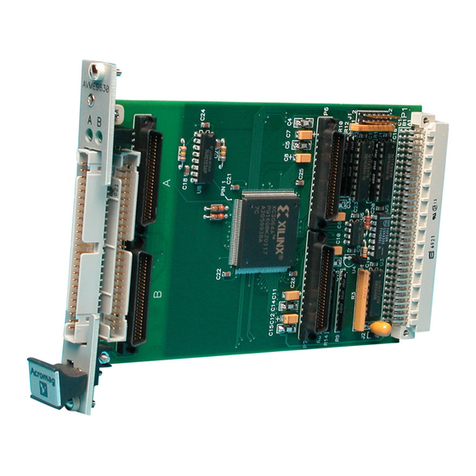
Acromag
Acromag AVME9630 Series User manual
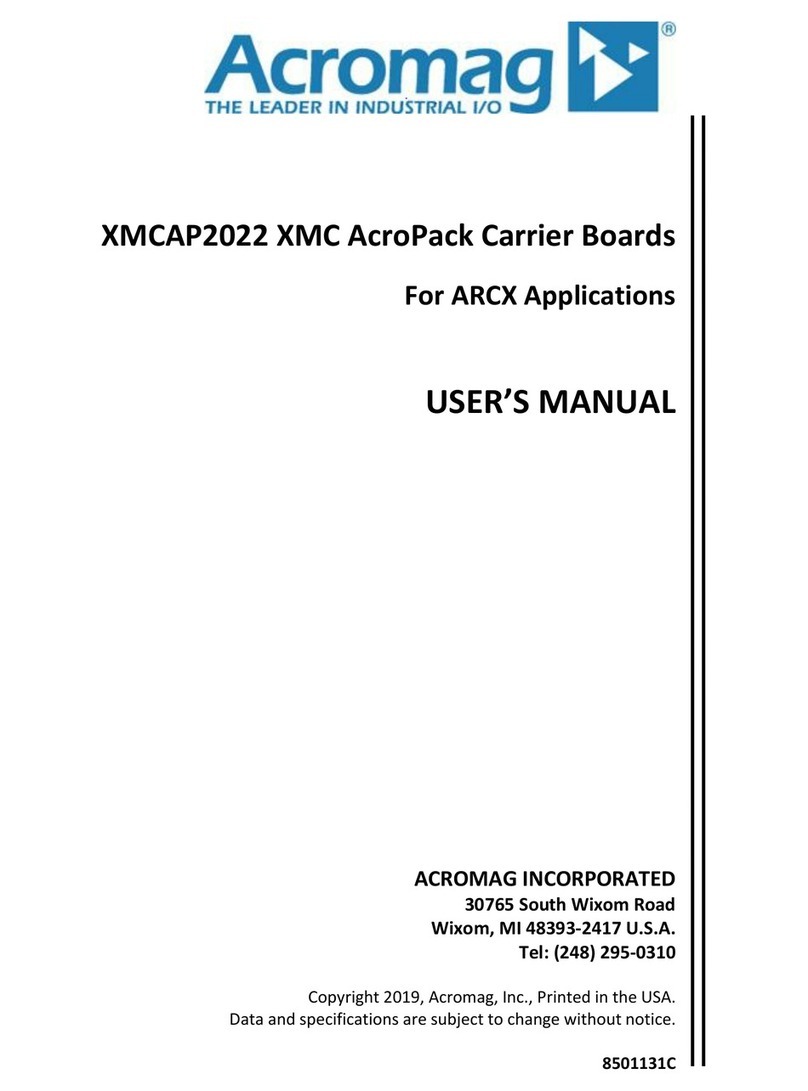
Acromag
Acromag XMCAP2022 User manual
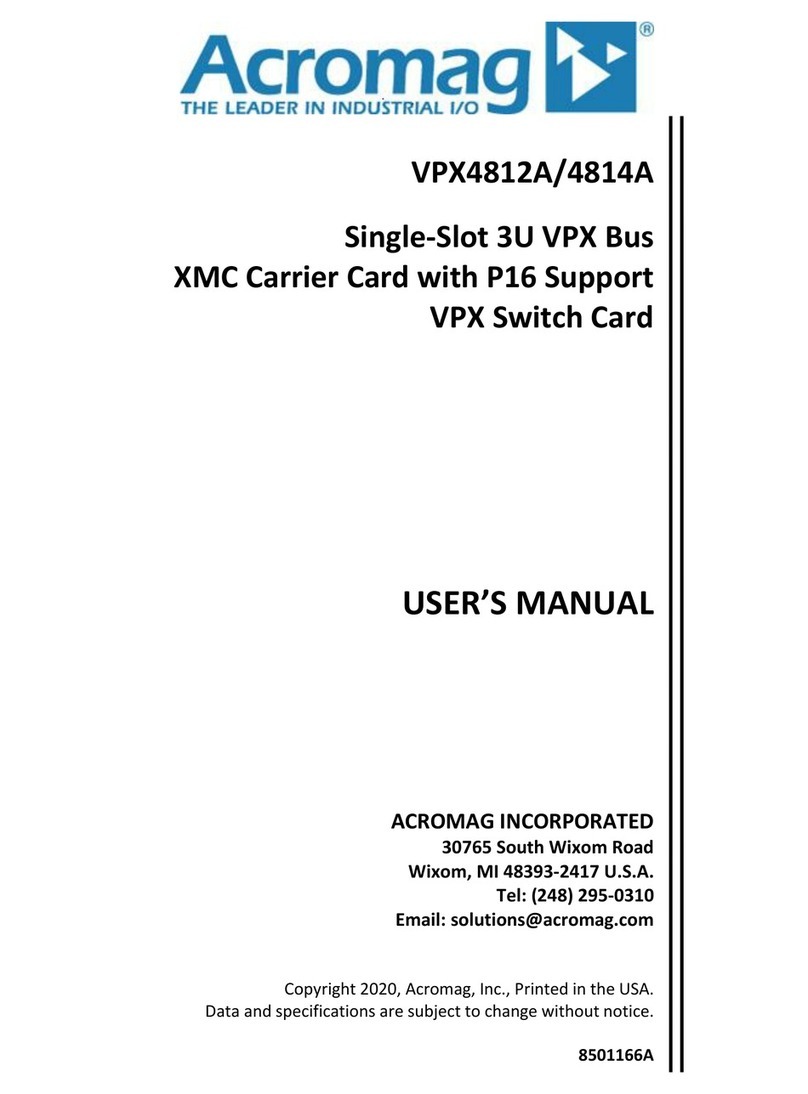
Acromag
Acromag VPX4812A User manual
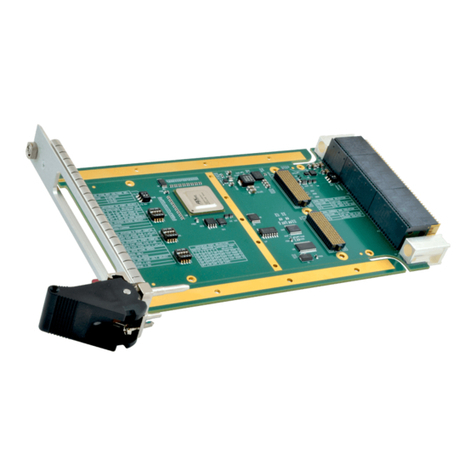
Acromag
Acromag VPX4812 User manual
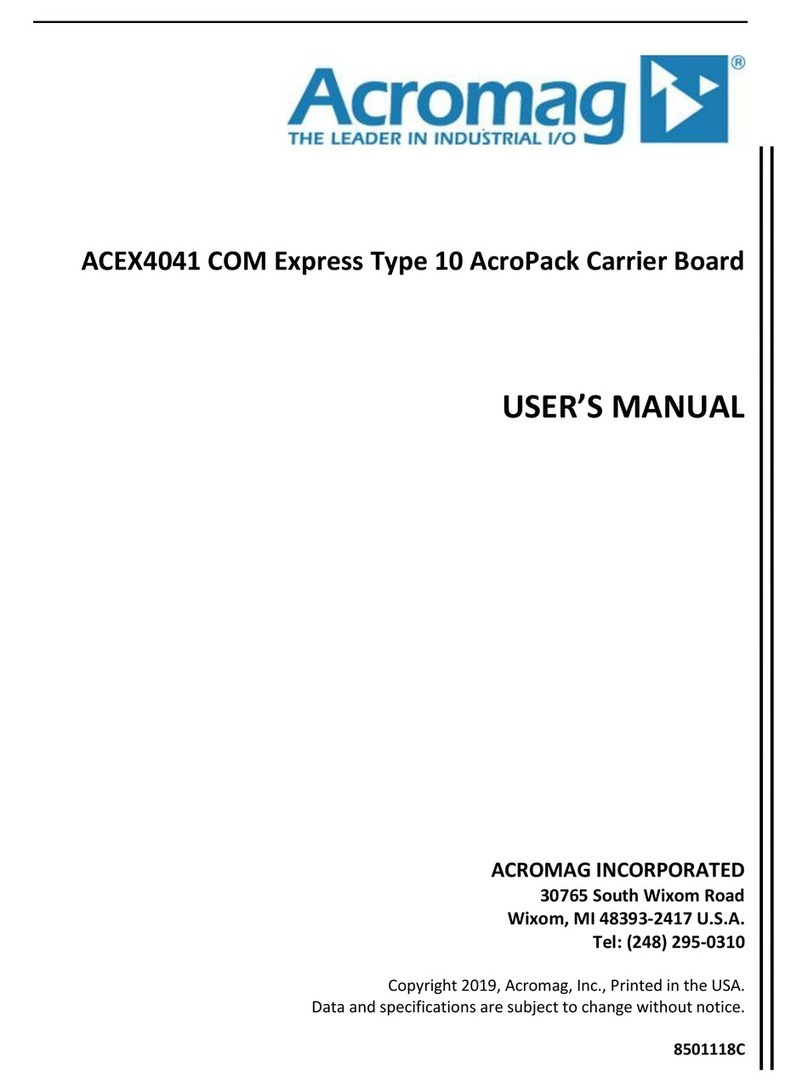
Acromag
Acromag ACEX4041 User manual