Allen-Bradley PLC-5 MAP/OSI User manual

Preface P1. . . . . . . . . . . . . . . . . . . . . . . . . . . . . . . . . . . . . . .
Manual Contents P1. . . . . . . . . . . . . . . . . . . . . . . . . . . . . . . . . . . .
Who Should Read This Manual P1
. . . . . . . . . . . . . . . . . . . . . . . . . .
What You Should Receive P2
. . . . . . . . . . . . . . . . . . . . . . . . . . . . .
The
Equipment Y
ou Will Need P2. . . . . . . . . . . . . . . . . . . . . . . . . . .
Related
Publications
P4. . . . . . . . . . . . . . . . . . . . . . . . . . . . . . . . . .
Overview of the MAP Communication Environment 11. . . . . .
Chapter
Objectives
11. . . . . . . . . . . . . . . . . . . . . . . . . . . . . . . . . . .
Open Systems Interconnect (OSI) 11
. . . . . . . . . . . . . . . . . . . . . . . .
Manufacturing Automation Protocol (MAP) 13
. . . . . . . . . . . . . . . . . .
Manufacturing Message Specification 14
. . . . . . . . . . . . . . . . . . . . .
The
MMS Modeling Concept
15. . . . . . . . . . . . . . . . . . . . . . . . . . . .
Implementing
MMS
110. . . . . . . . . . . . . . . . . . . . . . . . . . . . . . . . . .
The PLC-5 802.4 MAP/OSI Coprocessor 21. . . . . . . . . . . . . .
Chapter
Objectives
21. . . . . . . . . . . . . . . . . . . . . . . . . . . . . . . . . . .
Introduction to the OSI Coprocessor 21
. . . . . . . . . . . . . . . . . . . . . .
Non-volatile Memory and the Lithium Battery 24
. . . . . . . . . . . . . . . .
The LEDs 26
. . . . . . . . . . . . . . . . . . . . . . . . . . . . . . . . . . . . . . . . .
The Switches 27
. . . . . . . . . . . . . . . . . . . . . . . . . . . . . . . . . . . . . . .
MMS and Your OSI Coprocessor 31. . . . . . . . . . . . . . . . . . . .
Chapter
Objectives
31. . . . . . . . . . . . . . . . . . . . . . . . . . . . . . . . . . .
The Supported MMS Services 31
. . . . . . . . . . . . . . . . . . . . . . . . . . .
Mapping
MMS Data T
ypes onto PLC-5 Controller Data Files 36. . . . .
Additional Information on Using Data Types 318
. . . . . . . . . . . . . . . . .
MMS
Object Management
319. . . . . . . . . . . . . . . . . . . . . . . . . . . . . .
MMS Security 322
. . . . . . . . . . . . . . . . . . . . . . . . . . . . . . . . . . . . . .
Basic
Programming T
echniques 41. . . . . . . . . . . . . . . . . . . .
Chapter
Objectives
41. . . . . . . . . . . . . . . . . . . . . . . . . . . . . . . . . . .
Introduction 41
. . . . . . . . . . . . . . . . . . . . . . . . . . . . . . . . . . . . . . . .
Entering Commands 42
. . . . . . . . . . . . . . . . . . . . . . . . . . . . . . . . . .
What You Should Know Before You Program 45
. . . . . . . . . . . . . . . .
A Quick Reference Guide to the Commands 48
. . . . . . . . . . . . . . . . .
Managing Connections
(The OPEN, CLOSE and ABORT Commands) 411
. . . . . . . . . . . .
Defining
MMS Named V
ariables (The DEFVAR Command) 416. . . . . .
Deleting
MMS Named V
ariables (The DELVAR Command) 417. . . . . .
Table of Contents

Table of Contentsii
Reading and Writing Data (Using the SET Command) 418. . . . . . . . . .
Additional and Advanced Programming Techniques 51. . . . .
Chapter
Objectives
51. . . . . . . . . . . . . . . . . . . . . . . . . . . . . . . . . . .
Sending
Unsolicited V
ariable Information (The UINFO Command) 51.
Sending
Unsolicited Status Information (The UST
AT Command) 53. . .
Reading and Writing Data (Using the MOVE Command) 53
. . . . . . . .
Obtaining Status on a Connection (using CSTAT) 57
. . . . . . . . . . . . .
Specifying the Data Type of an MMS Named Variable
(using DTYPE) 58
. . . . . . . . . . . . . . . . . . . . . . . . . . . . . . . . . . .
Defining the Scope of an MMS Named Variable (using DEFVAR) 510
. .
Deleting
MMS Named V
ariable of a Particular Scope
(Using DELVAR) 513
. . . . . . . . . . . . . . . . . . . . . . . . . . . . . . . . . .
Specifying
MMS Named V
ariable Scope Within SET and MOVE 514. . .
Specifying
MMS Named V
ariable Scope Within UINFO 518. . . . . . . . .
Mapping MMS Data Types onto PLC-5/40, -5/60 File Types A1
Appendix Contents A1. . . . . . . . . . . . . . . . . . . . . . . . . . . . . . . . . . .
Error Codes B1. . . . . . . . . . . . . . . . . . . . . . . . . . . . . . . . . . . .
Protocol Implementation Conformance Statement (PICS) C1.
Appendix Contents C1. . . . . . . . . . . . . . . . . . . . . . . . . . . . . . . . . . .
PICS
Part 1: Implementation Information
C1. . . . . . . . . . . . . . . . . . .
PICS Part 2: Service CBBs C2
. . . . . . . . . . . . . . . . . . . . . . . . . . . . .
PICS Part 3: Parameter CBBs C4
. . . . . . . . . . . . . . . . . . . . . . . . . . .
PICS
Part 4: Local Implementation V
alues C5. . . . . . . . . . . . . . . . . .
The Communication Layers' Attributes D1. . . . . . . . . . . . . . .
Appendix Contents D1. . . . . . . . . . . . . . . . . . . . . . . . . . . . . . . . . . .
Introduction
to Attributes
D1. . . . . . . . . . . . . . . . . . . . . . . . . . . . . . .
Definition
of Defaults
D2. . . . . . . . . . . . . . . . . . . . . . . . . . . . . . . . .
Frequently Used Acronyms D2
. . . . . . . . . . . . . . . . . . . . . . . . . . . . .
System-Layer
Attributes
D3. . . . . . . . . . . . . . . . . . . . . . . . . . . . . . .
System-Load
Attributes
D4. . . . . . . . . . . . . . . . . . . . . . . . . . . . . . .
MMS
Attributes
D5. . . . . . . . . . . . . . . . . . . . . . . . . . . . . . . . . . . . .
ACSE-Layer
Attributes
D6. . . . . . . . . . . . . . . . . . . . . . . . . . . . . . . .
Presentation-Layer
Attributes
D7. . . . . . . . . . . . . . . . . . . . . . . . . . .
Session-Layer
Attributes
D7. . . . . . . . . . . . . . . . . . . . . . . . . . . . . .
Transport-Layer
Attributes
D8. . . . . . . . . . . . . . . . . . . . . . . . . . . . .
Network-Layer
Attributes
D10. . . . . . . . . . . . . . . . . . . . . . . . . . . . . .
LLC-Layer Counters D11
. . . . . . . . . . . . . . . . . . . . . . . . . . . . . . . . .
MAC Layer Attributes D12
. . . . . . . . . . . . . . . . . . . . . . . . . . . . . . . . .
RS-232 Port Parameters D14
. . . . . . . . . . . . . . . . . . . . . . . . . . . . . .
AB Parts

Preface
Allen-Bradley PLC-5 MAP/OSI Software
(Cat. No. 1785-OSI)
P-1
Preface
This manual provides information on the Allen–Bradley PLC–5
MAP/OSI Software (cat. no. 1785–OSI) and the PLC–5 MAP/OSI
Coprocessor (1785–O5G/B). It contains information on the following
topics:
For this type of information: See:
overview of Open System Interconnect (OSI), Manufacturing
Automation Protocol (MAP), and Manufacturing Message
Specification (MMS)
Chapter 1
introduction to the PLC-5 MAP/OSI Coprocessor Chapter 2
the MMS services supported by your PLC-5 MAP/OSI
Software and Coprocessor, examples of mapping MMS data
types onto PLC-5 controller data files, and how MMS relates to
your OSI coprocessor
Chapter 3
programming your PLC-5 MAP/OSI Coprocessor, including
rules for using MMS named variables and address strings
Chapter 4
advanced programming techniques Chapter 5
reference information on mapping MMS data types onto
PLC-5 controller data files, including default data types
Appendix A
a list of the PLC-5 MAP/OSI Software's error codes Appendix B
the PLC-5 MAP/OSI Coprocessor's PICS (Protocol
Implementation Conformance Statement)
Appendix C
a list of the OSI communication layers' parameters, statuses,
counters, and actions related to the PLC-5 MAP/OSI Software
Appendix D
a list of the OSI communications layer management options Appendix E
Important: This manual does not cover installation procedures for the
PLC–5 MAP/OSI software. You install the software via the Allen–Bradley
MAP Station Manager, refer to publication 6630–6.5.2 for installation
instructions.
We refer to the PLC–5 MAP/OSI Software as the OSI software, and the
PLC–5 MAP/OSI Coprocessor as the OSI coprocessor throughout this
manual.
You should read this manual before installing and using your
Allen–Bradley PLC–5 MAP/OSI Software. We assume you have
experience using and programming Allen–Bradley PLCControllers, and
some knowledge of the MAP 3.0 Specification.
Manual Contents
Who Should Read This
Manual AB Parts

Preface
Allen-Bradley PLC-5 MAP/OSI Software
(Cat. No. 1785-OSI)
P-2
With your order of the OSI software, along with this manual, you should
have received the OSI software on:
one 3 1/2” diskette and
one 5 1/4” diskette
If you did not receive these items, contact your local Allen–Bradley
integrator or sales office.
Your PLC–5 MAP/OSI Software is part of the Allen–Bradley PLC–5
MAP/OSI interface package. You must also have the following
Allen–Bradley equipment installed:
Product: Catalog Number:
PLC-5 Controllers 1785-L40L/B, -L40B/B, -L60L/B, -L60B/B,
-L30B/A, -L20B/A, -L11B/A. Contact your
local Allen-Bradley distributor or sales office
for a current list of compatible controllers.
PLC-5 Programming Software 6200-PLC5, version 4.3 or higher
PLC-5 802.4 MAP/OSI Broadband Modem or
PLC-5 802.4 MAP/OSI Carrierband Modem
1785-O5A, B, C (broadband) or
1785-O5CB (carrierband)
PLC-5 Connector Header 1785-CNH
Power Supply 1771-P7
1771 I/O Chassis (series B) Contact you local Allen-Bradley distributor of
sales office for the correct I/O chassis catalog
number for your application.
PLC-5 OSI Coprocessor Lithium Battery 1785-U1
You must have each of these products installed and running before using
the 1785–OSI software (see figure P.1). For installation and usage
instructions, refer to the installation instructions shipped with each of these
products.
What
Y
ou Should Receive
The Equipment Y
ou W
ill
Need

Preface
Allen-Bradley PLC-5 MAP/OSI Software
(Cat. No. 1785-OSI)
P-3
Figure P.1
You
Must Have This Equipment Installed Before Using the OSI Software
Allen-Bradley 6200 Software
OSI Network
Allen-Bradley MAP
Station Manager
1785-OSI
Software
IBM PC Compatible/DOS Computer
Allen-Bradley T47 Terminal or
FORCE
BATT
PROC
COMM
PROG
RUN
R
E
M
AB
A
B
1
2
1
2
CH2
CH0
AB
A
B
1
2
1
2
CH1
2A
2B
1A
1B
BATTERY
INSTALLED
DMY
PLC-5/40
PROGRAMMABLE
CONTROLLER
PASSPASS
MODE
ACT
BATT
802.4
STATUS
RS-232
BATTERY
INSTALLED
DMY
OSI
INTERFACE
802.4
INTERFACE
MODEM
The Connector Header
mates the PLC-5 controller
to the OSI coprocessor.
The PLC-5 OSI Coprocessor
Lithium Battery.
OSI Modem
PLC-5 802.4 MAP/OSI Coprocessor
Into an Allen-Bradley 1771 I/O Chassis
series B, install:
- the PLC-5 controller
- the OSI coprocessor
- the P7 power supply
- the modem
Allen-Bradley 6200 software
connects to the PLC-5 controller.
PLC-5/40, -5/60
controller
I
- 12405
If you need more information on these products, contact your local
Allen–Bradley integrator or sales office for assistance.
AB Parts

Preface
Allen-Bradley PLC-5 MAP/OSI Software
(Cat. No. 1785-OSI)
P-4
Refer to the following table for information on where to read more about
Allen–Bradley MAP/OSI products:
Product: Refer to this publication for
installation/usage instructions:
PLC-5 802.4 MAP/OSI Coprocessor 1785-2.23
PLC-5 802.4 MAP/OSI Broadband Modem 1785-2.12
PLC-5 802.4 MAP/OSI Carrierband Modem 1785-2.20
PLC-5 Connector Header 1785-2.23 and 1785-2.14
PLC-5 Lithium Battery 1785-2.23 and 1785-2.24
PLC-3MAP Interface 6632-6.5.2
Pyramid IntegratorOSI Interface Module 5820-6.5.1 and 6632-2.11
MAP Station Manager 6630-6.5.2 and 6632-2.11
Related
Publications

Chapter 1
1-1
Overview of the MAP Communication
Environment
This chapter introduces you to MAP communication and shows how it
relates to your OSI coprocessor. This chapter covers:
Open Systems Interconnect (OSI)
Manufacturing Automation Protocol (MAP)
Manufacturing Message Specification (MMS)
the MMS Modeling Concept
MAP communications and your OSI coprocessor
The following sections contain general overviews of these subjects and are
not meant to provide in–depth information. If you are already familiar
with these topics, you may want to proceed to Chapter 2.
The Open Systems Interconnect (OSI) is a standard that provides the
framework for defining the process of communication between nodes (i.e.,
computers, terminals, PLC controllers). There are many activities that
need to be accomplished when two nodes communicate with each other
over the network. The OSI standard defines these activities in its
seven–layer reference model (figure 1.1).
Figure 1.1
The
OSI Seven-layer Reference Model
Application
7
Presentation
6
Session
5
Transport
4
Network
3
Data Link
2
Physical
1I
- 12406
The seven layers define the:
Chapter
Objectives
Open Systems Interconnect
(OSI)
AB Parts

Chapter 1
Overview of the MAP Communication
Environment
1-2
activities involved in communicating on the network
services required to perform those activities
The individual layer specifications dictate how the functions are
accomplished. The tasks within the layers are carried out by protocols.
Protocols are rules for how information is coded and passed between two
nodes. The protocols are actually the part that is implemented, the OSI
model serves merely as a reference to discuss the different aspects of
communication between devices. The following table lists the functions
that the protocols at each layer must accomplish.
This layer:Contains the functions that:
7 Application manipulate information to support applications. This layer's protocols
contain the most functionality.
6 Presentation ensure information is delivered in a form the receiving system can
understand and use.
5 Session manage communications between two application processes.
4 Transport transfer reliable data between communicating nodes.
3 Network route communication between the communicating nodes.
2 Data Link perform synchronization and error control for information passed over
the physical link (manages the access to the medium).
1 Physical activate, maintain, and deactivate the physical connection.
The OSI system enables many different vendors’ devices on the same
network to communicate with each other. In other words, as long as two
different vendors construct protocols that ‘‘fit” in the seven layer model the
same way, those two devices will be able to communicate (figure 1.2).
Figure 1.2
Different
V
endors' Devices Can Communicate on OSI Networks
Allen-Bradley
PLC Controller OSI interface
with OSI protocol
Another Vendor's
device with OSI
protocol.
I
- 12407

Chapter 1
Overview of the MAP Communication
Environment
1-3
Each node on an OSI network is equipped with a layer mechanism that
incorporates the ‘‘rules” of the OSI standard. Each layer is able to ‘‘talk”
with only its counterpart within the node sending/receiving the data (figure
1.3).
Figure 1.3
Each
Layer Communicates W
ith its Counterpart W
ithin Another Node
Application
Presentation
Session
Transport
Network
Data Link
Physical
A node with OSI protocol
implementation.
Application
Presentation
Session
Transport
Network
Data Link
Physical
A node with OSI protocol
implementation.
OSI
Network
I
- 12408
Your OSI coprocessor implements Manufacturing Automation Protocol
(MAP). MAP is one set of OSI protocols.
Manufacturing Automation Protocol (MAP) is a set of protocols based on
the OSI seven–layer reference model described in the previous section.
MAP specifies a set of protocols that must accomplish certain tasks within
each of the model’s seven layers. Your OSI coprocessor implements the
MAP 3.0 Protocol.
The seventh and first layers of the reference model are the two layers that
are most distinct to your application. The seventh layer is the Application
layer, with which your OSI coprocessor first interacts with your application
program. The first layer is the Physical layer, with which your OSI
coprocessor connects to the network media (figure 1.4). Your OSI
coprocessor physically connects to MAP 802.4 network media.
Manufacturing Automation
Protocol (MAP)
AB Parts

Chapter 1
Overview of the MAP Communication
Environment
1-4
Figure 1.4
The
Layers 7 and 1 Are Most Distinct To Y
our Application
Application
7
Presentation
6
Session
5
Transport
4
Network
3
Data Link
2
Physical
1
Application Program
Layer 7 is where your application program first interacts
with the MAP protocol for transmission onto the network.
Layer 1 is where the message(s) from the program first
make a physical connection to the network media.
OSI
Network Media
I
- 12409
The Application Layer for the MAP 3.0 Specification contains a unique set
of services called Manufacturing Message Specification (MMS).
Manufacturing Message Specification (MMS) provides services directly
visible to (and used by) the user. MMS specifies a method for
communicating with intelligent plant–floor devices. MMS is not an
application program, it provides services to application programs. These
programs then use the services to communicate with devices on the
network (figure 1.5).
Figure 1.5
MMS
is a MAP 3.0 Layer Seven Protocol that Provides Services
Application7
Application Program
Services
MMS
I
- 12410
MMS gives MAP network devices a set of services that they can all access,
allowing them to communicate freely.
The following sections provide a brief overview of MMS. Note that this is
an introduction to the MMS communication environment. For detailed
information, refer to the ISO/IEC 9506 Part 1 (MMS –– Service
Manufacturing
Message
Specification

Chapter 1
Overview of the MAP Communication
Environment
1-5
Definition). For a complete listing of the MMS services supported by your
OSI coprocessor, refer to Chapter 3 of this manual.
The dominant aspect of MMS is the concept of modeling. MMS defines
models that describe the way in which resources are made available and
the way in which these resources are accessed. At the center of the MMS
modeling concept are:
the Virtual Manufacturing Device (VMD)
abstract object models
The VMD
The VMD describes the externally visible behavior of an MMS device
when it makes resources (i.e., data table memory, program files) available
to other MMS devices. Assume, for example, that an MMS device exists
and it makes system data table memory available to other MMS devices. It
is the VMD that describes the way in which that MMS device makes the
data table memory available (figure 1.6).
Figure 1.6
The
VMD Describes the Way a Device Makes its Resources A
vailable
OSI Network
VMD
data table memory
The way this MMS device makes its
resources available is described by the
VMD.
This MMS device has requested
information on data table memory
from another device.
I
- 1241
1
It is each vendor’s responsibility to associate the VMD model with their
device (figure 1.7).
The
MMS Modeling Concept
AB Parts

Chapter 1
Overview of the MAP Communication
Environment
1-6
Figure 1.7
Vendors
Must Map Their Devices to the VMD Model
VMD
Model
MMS
Device
Mapping a device to the VMD
establishes it as a virtual device
on the network.
The
mapping
concept. I
- 12412
This mapping of a device to the VMD model establishes a device as a
virtual device on the MAP network, allowing it to be accessed by other
virtual devices through the use of MMS services. Note that the VMD
model theoretically exists within an MMS device.
The MMS Abstract Object Models
MMS also defines a series of abstract object models that describe the
externally visible behavior associated with a particular MMS service or
group of services. The concept of object models is entirely abstract within
the MMS specification, but represents real resources within a system. This
results in a standard external view of all MMS devices that make system
resources available, but allows each MMS device to implement the model
in a manner that is appropriate for the system (figure 1.8).

Chapter 1
Overview of the MAP Communication
Environment
1-7
Figure 1.8
Abstract
Object Models are Part of the VMD Model
OSI Network
The OSI coprocessor
VMD
Resources
abstract
object models
I
- 12413
The models define abstract objects which are part of the VMD. An
application program calls on the MMS services associated with a particular
object to perform operations on that object. The objects implemented
within your OSI coprocessor are listed in the table below:
The: Are acted upon by MMS: And allow an MMS client1
to:
domain objects Domain Management Services upload or download a memory image
within the system associated within
an MMS server
program invocation
objects
Program Invocation
Management Services
control the operational state of the
program(s) associated with an MMS
server
variable objects Variable Access Services access data within the system
associated with an MMS server.
1Refer to the section titled Clients, Servers and the VMD, later in this chapter, for an
explanation of MMS clients and servers.
There are other object models within the MMS specification. The three
listed above are the only objects currently implemented by your OSI
coprocessor. The following sections briefly describe how the OSI
coprocessor implements them.
Domain Objects Implemented by the OSI Coprocessor
Your OSI coprocessor implements a single domain object that represents
the PLC–5 controller’s entire memory image.
Program Invocation Objects Implemented by the OSI Coprocessor
Your OSI coprocessor implements a single program invocation object,
which allows an MMS client to place the PLC–5 controller into different
modes (i.e., program, test, and run mode). A program invocation object is
AB Parts

Chapter 1
Overview of the MAP Communication
Environment
1-8
merely a grouping of domains within a system. Therefore, within the OSI
coprocessor, the single program invocation object is made up of a single
domain object.
Variable Objects Implemented by the OSI Coprocessor
Your OSI coprocessor implements the following types of variable objects:
Variable Object: Description:
Named Variables MMS allows you to associate a name with an address within the node
(i.e., `paint_station' for address N12:1). The names are identification
strings. To gain access to the address, simply specify the name.
Unnamed Variables (or
address strings)
Variables that do not have an identifier string associated with an
address. To access the location, you must specify the address.
Named Variable Lists This is a grouping of named and/or unnamed variables referenced by
a single identification string.
Named Types These are objects that pre-define a data-type template for use when
accessing unnamed variables or defining named variables. For
example, if a client has defined a template for an array of 100 integers
called 'int_array_100' within the OSI coprocessor, and the client sends
a read request for ``N7:0", specifying 'int_array_100' as the data type
to be returned, the client will receive an array of 100 integers starting
at ``N7:0".
Clients, Servers, and MMS Modeling
In the previous sections we covered the various concepts of MMS
modeling. It is important to note here that the MMS specification defines
models for the behavior of a device acting as a server, but not as a client.
Within the MMS specification, the terms client and server are used to
describe the tasks that a device performs when it carries out an MMS
service. An MMS device that makes resources available for use by another
MMS device is called a server. And the MMS device that makes use of
those resources to perform some type of application function is called a
client (figure 1.9).

Chapter 1
Overview of the MAP Communication
Environment
1-9
Figure 1.9
An
MMS Server Makes Resources A
vailable to an MMS Client
OSI Network
An MMS client device accesses
resources in the server device
using MMS services.
An MMS server device
makes
resources available for
the client to use. VMD
Resources
domain objects
program invocation objects
variable objects
MMS Client
MMS Server
I
- 12414
Clients, Servers, the VMD Model, and Your OSI Coprocessor
Your OSI coprocessor has the ability to act as both MMS server and client,
depending on the particular MMS service. It is your PLC–5 controller that
is modeled as a VMD.
The coprocessor and its OSI software make the PLC–5 controller’s
resources accessible to MMS client devices because the OSI software
supports the MMS VMD model (figure 1.10).
AB Parts

Chapter 1
Overview of the MAP Communication
Environment
1-10
Figure 1.10
An
Allen-Bradley PLC Controller as an MMS Server
OSI Network
MMS Client
An MMS client requests
resources from the PLC-5
controller.
The OSI interface (the coprocessor
and the modem) makes PLC-5
controller's
resources
available to the
client.
VMD
Resources
Resources
PLC-5 Controller
I
- 12415
Your Coprocessor's OSI Communication Layers
Each of the seven OSI communication layers has its own set of attributes
(characteristics) that in some way control or help to control the
communication process. These attributes include:
parameters
statuses
counters
actions
You can manipulate the values of many of the attributes. Your OSI
coprocessor is shipped with its attributes pre–set to Allen–Bradley default
settings. Some of these settings should not be changed. Refer to
Appendix D of this manual for a complete listing of the OSI coprocessor’s
attributes, including applicable warnings for those you should not change.
The formal description of the MMS options a vendor has implemented
comes in the form of a PICS (Protocol Implementation Conformance
Statement). The PICS for your Allen–Bradley OSI coprocessor is listed in
Appendix C of this manual.
Implementing
MMS

Chapter 2
2-1
The PLC-5 802.4 MAP/OSI Coprocessor
This chapter contains information on using the OSI coprocessor (cat. no.
1785–O5G). It covers the following topics:
introduction to the OSI coprocessor
non–volatile memory and the lithium battery
the LEDs
the switches
This chapter does not cover installation instructions. For installation
procedures, handling precautions, and additional information on the OSI
coprocessor, refer to the PLC–5 802.4 MAP/OSI Coprocessor Installation
Data (publication 1785–2.23 and 1785–2.24), shipped with the OSI
coprocessor.
The OSI coprocessor connects a PLC–5 controller to a MAP 802.4
network (figure 2.1).
Chapter
Objectives
Introduction to the OSI
Coprocessor
AB Parts

Chapter 2
The PLC-5 802.4 MAP/OSI Coprocessor
2-2
Figure 2.1
The
OSI Coprocessor
OSI
Coprocessor
FORCE
BATT
PROC
COMM
PROG
RUN
R
E
M
AB
A
B
1
2
1
2
CH2
CH0
AB
A
B
1
2
1
2
CH1
2A
2B
1A
1B
BATTERY
INSTALLED
DMY
PLC-5/40
PROGRAMMABLE
CONTROLLER
PASSPASS
MODE
ACT
BATT
802.4
STATUS
RS-232
BATTERY
INSTALLED
DMY
OSI
INTERFACE
802.4
INTERFACE
MODEM
802.4 (broadband or
carrierband) Modem
PLC-5/40, -5/60 Controller
I
- 12416
The coprocessor is only half of the controller’s connection to the network,
you also need a modem. The type of modem depends upon the type of
network you are using:
For
a:
You need an Allen-Bradley: Catalog Number:
broadband network PLC-5 802.4 MAP/OSI
Broadband Modem
1785-O5A, B, or C
carrierband network PLC-5 802.4 MAP/OSI
Carrierband Modem
1785-O5CB
Installing the OSI Software
You install the OSI software (cat. no. 1785–OSI) via your Allen–Bradley
MAP Station Manager (cat. no. 6630–PM, –PMC) (figure 2.2).
Table of contents
Other Allen-Bradley Computer Hardware manuals
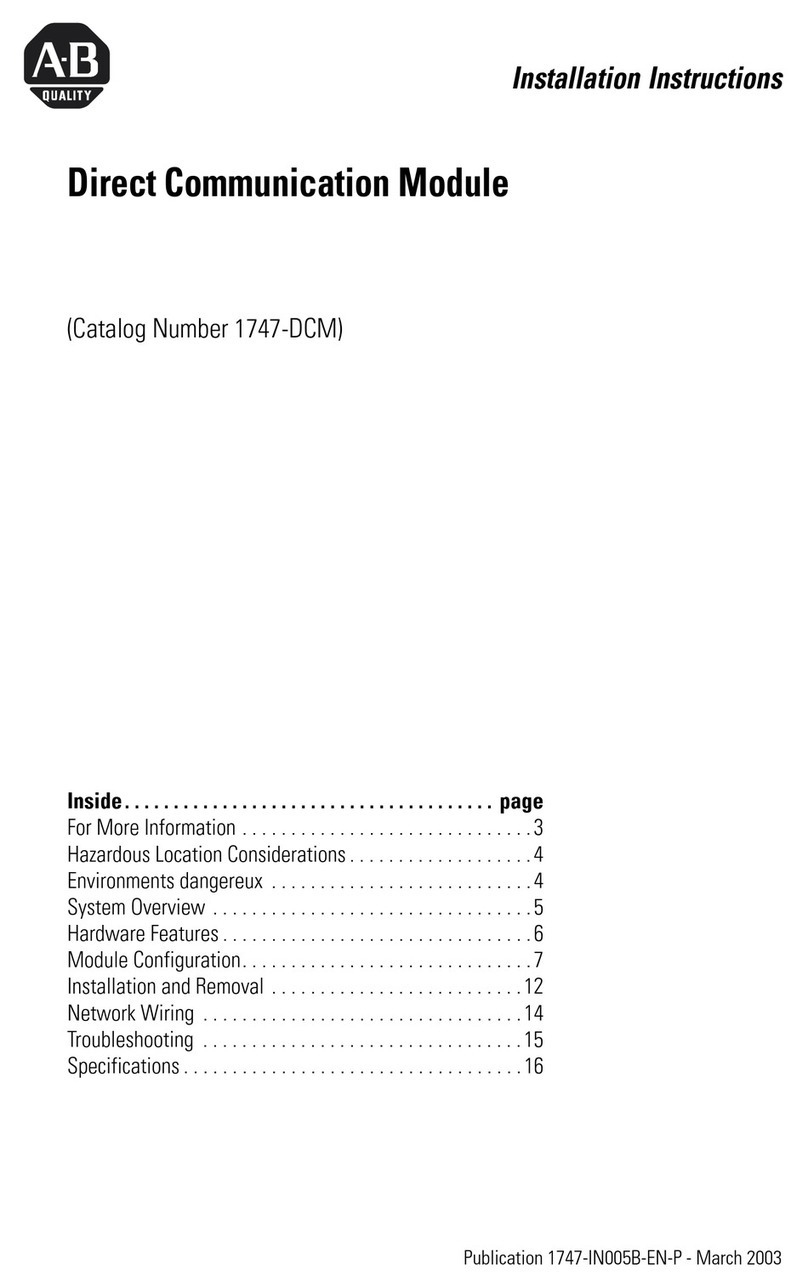
Allen-Bradley
Allen-Bradley 1747-DCM User manual
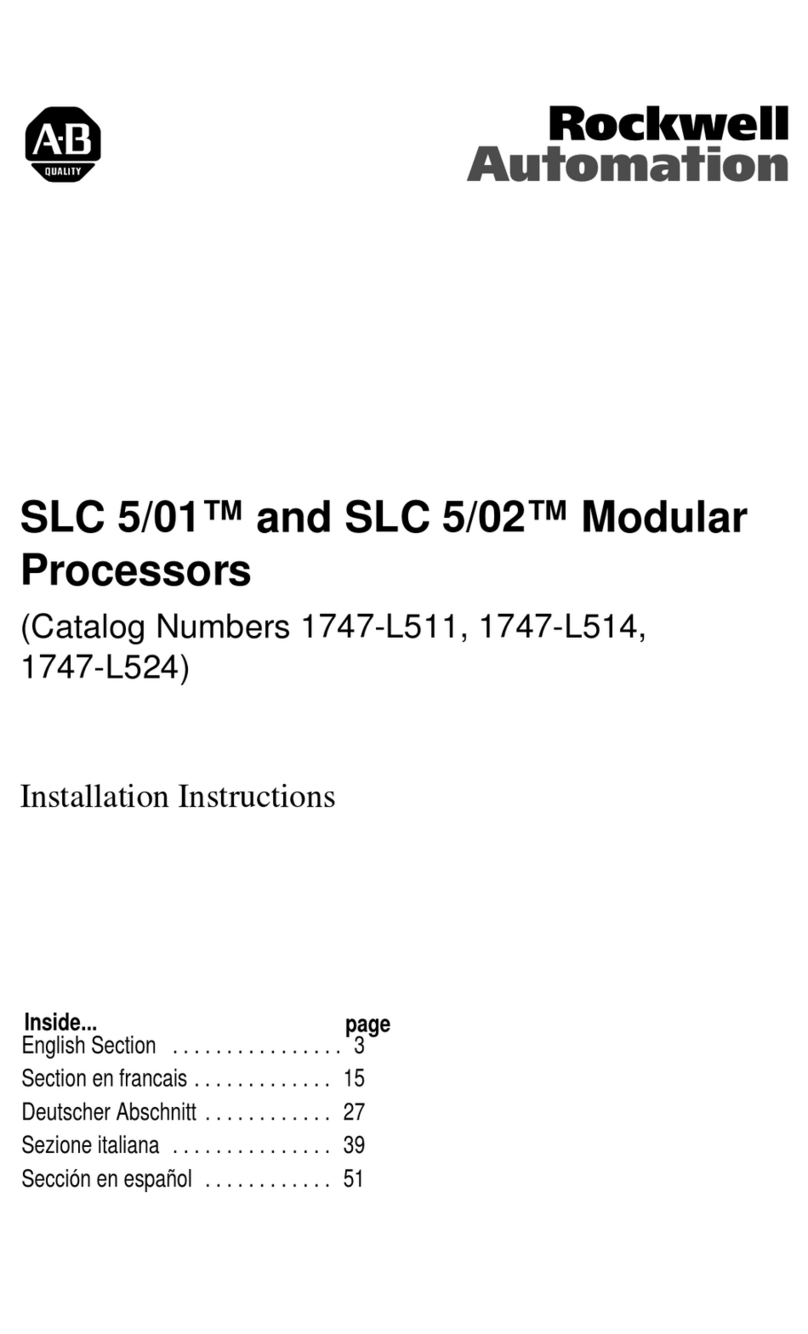
Allen-Bradley
Allen-Bradley SLC 5/01 User manual
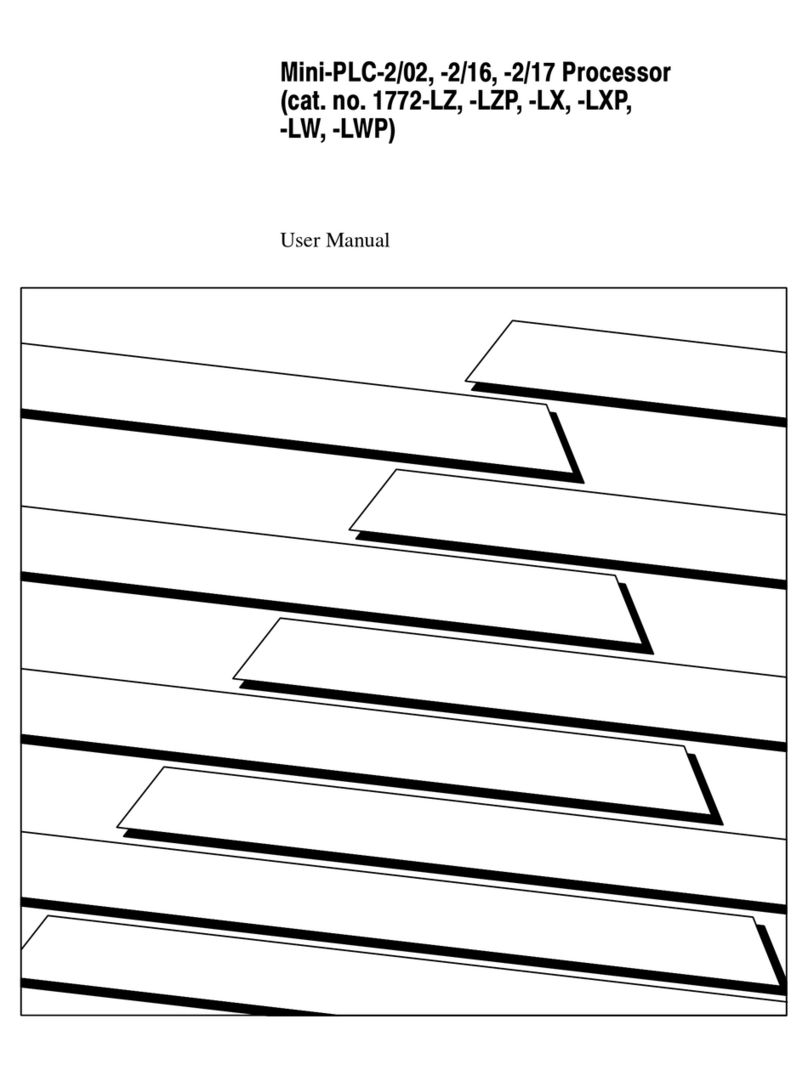
Allen-Bradley
Allen-Bradley Mini-PLC Mini-PLC-2/16 User manual

Allen-Bradley
Allen-Bradley 2707 User manual

Allen-Bradley
Allen-Bradley SLC 500 Series User manual
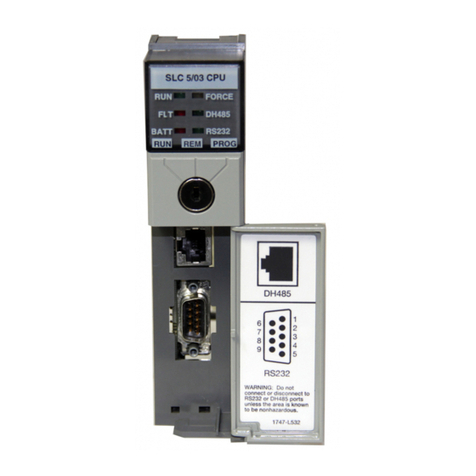
Allen-Bradley
Allen-Bradley SLC 5/03 User manual

Allen-Bradley
Allen-Bradley 2094-AL15S User manual
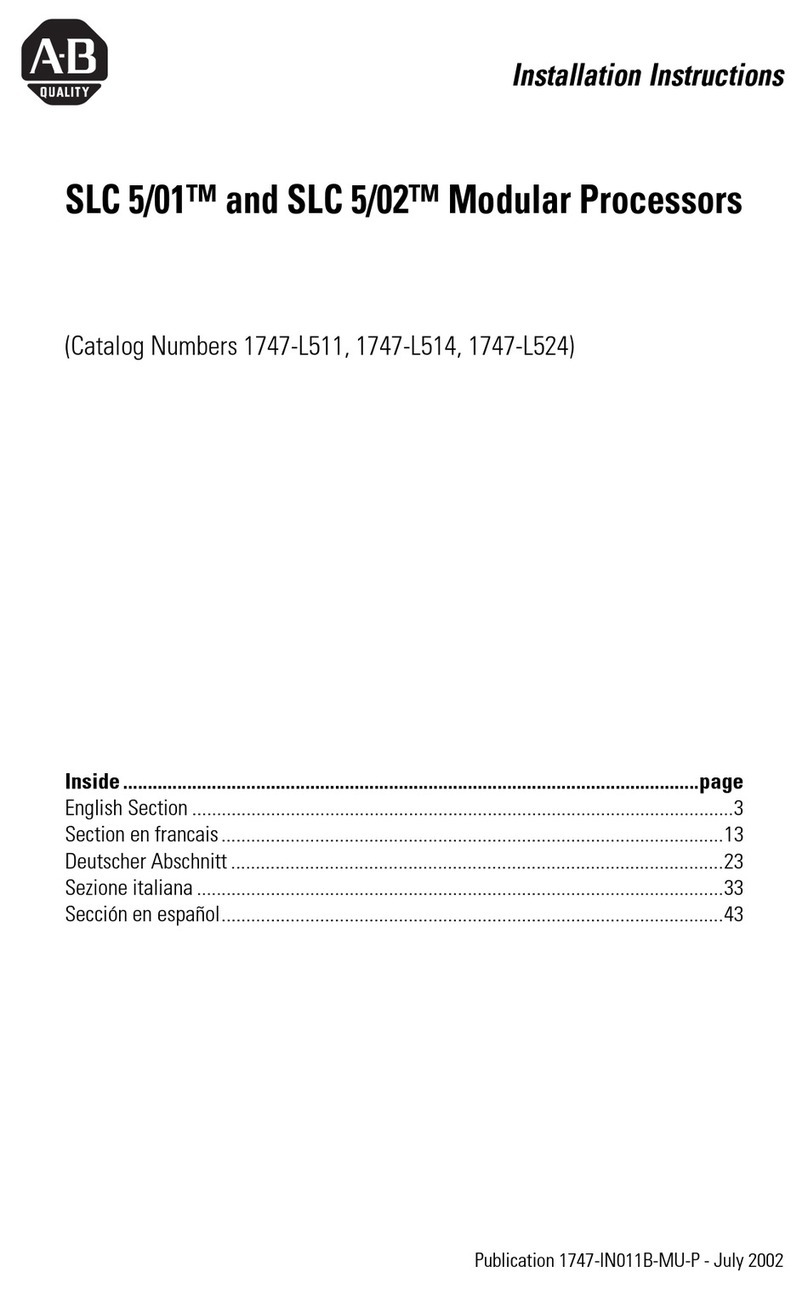
Allen-Bradley
Allen-Bradley SLC 5/01 User manual
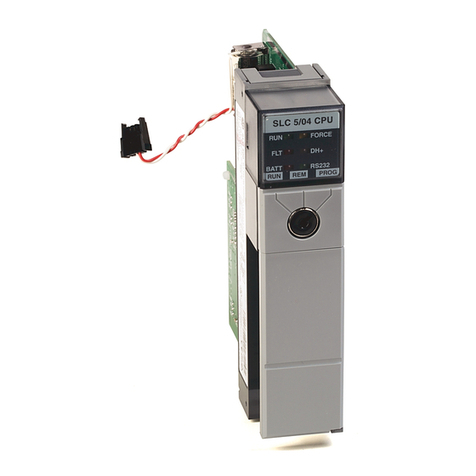
Allen-Bradley
Allen-Bradley SLC 5/04 User manual
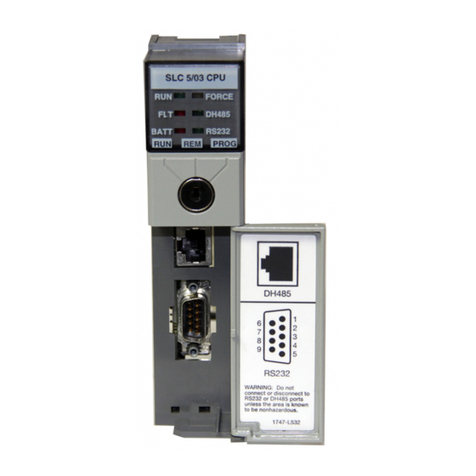
Allen-Bradley
Allen-Bradley SLC 5/03 User manual