Almex T4PGF1 User manual

T4PGF1 INSTRUCTION MANUAL Page 1
SHAW-ALMEX INDUSTRIES LIMITED June 14 2017
INSTRUCTION MANUAL
T4PGF1
30A
GROUND
FAULT CONTINUITY CHECKING
TEMPERATURE
CONTROL PANEL
WITH A PUMP RECEPTACLE.
This manual was prepared to present the correct methods and procedures of operating and
maintaining your ALMEX GROUND FAULT CONTINUITY CHECKING
TEMPERATURE CONTROL PANEL.
Read this manual carefully before operating your vulcanizer.
1.1. SHAW-ALMEX INDUSTRIES LIMITED
PO Box 430
Parry Sound, Ontario, Canada P2A 2X4
Phone:
705-746-5884 or 1-800-461-4351
Fax:
705-746-9484
e-mail:
SAIL@ALMEX.COM

T4PGF1 INSTRUCTION MANUAL Page 2
SHAW-ALMEX INDUSTRIES LIMITED June 14 2017
Table of Contents
1. RECORD OF PURCHASE.................................................................................................................................... 3
2. DECLARATION OF CONFORMITY .................................................................................................................... 4
3. SAFETY .................................................................................................................................................................. 5
3.1. Definition of Pictograms ...................................................................................................................5
3.1.1. Electrical Hazard ............................................................................................................................ 5
3.1.2. Burning Hazard .............................................................................................................................. 5
3.2. Limitation of use...............................................................................................................................5
4. ASSEMBLY............................................................................................................................................................ 6
4.1. Unpacking ........................................................................................................................................6
4.2. Functional Diagram ..........................................................................................................................6
4.3. Connection Assembly ......................................................................................................................7
5. OPERATION........................................................................................................................................................... 8
5.1. Safety Features And How To Operate .............................................................................................8
5.2. Temperature Controller Settings ......................................................................................................9
5.2.1. Setting the Platen Temperature ................................................................................................................. 9
5.2.2. Setting Temperature Units to °C or °F...................................................................................................... 9
5.2.3. Setting the Over Temperature Alarm........................................................................................................ 9
6. HEATING THE VULCANIZER............................................................................................................................ 10
6.1. Heating Up ....................................................................................................................................10
6.1.1. Manual Heating .......................................................................................................................................10
6.2. Temperature Control ......................................................................................................................10
7. REQUIRED DAILY TESTING ............................................................................................................................. 11
7.1. Required Daily Testing Before Use................................................................................................11
8. MAINTENANCE................................................................................................................................................... 12
8.1. Opening the Control Cabinet..........................................................................................................12
8.2. Overload Protection .......................................................................................................................12
8.3. Temperature Calibration ................................................................................................................12
8.3.1. Auto Tune................................................................................................................................................13
8.3.2. Input Shift................................................................................................................................................13
9. TROUBLESHOOTING ........................................................................................................................................ 14
9.1. No Display on Temperature Controller...........................................................................................14
9.2. Error Display on Temperature Controller .......................................................................................14
9.3. Platens Not Heating .......................................................................................................................14
9.4. Vulcanizer Over Heating ................................................................................................................15
9.5. Controller will not maintain Set Point Temperature ........................................................................15
10. REQUIRED MAINTENANCE SCHEDULE ....................................................................................................... 16
10.1. Daily Inspection Check Sheet ........................................................................................................16
10.2. Maintanence Schedule Check Sheet .............................................................................................17
11. RECEPTACLE PIN CONFIGURATION ............................................................................................................ 19
12. SERVICE .............................................................................................................................................................. 20
12.1. Emergency Service ........................................................................................................................20
12.2. Return of Goods Authorization.......................................................................................................20
12.3. Guarantee ......................................................................................................................................20
13. WARRANTY CARD AND INFORMATION........................................................................................................ 21
14. PARTS INFORMATION ...................................................................................................................................... 22
15. ELECTRICAL DRAWAINGS .............................................................................................................................. 25

T4PGF1 INSTRUCTION MANUAL Page 3
SHAW-ALMEX INDUSTRIES LIMITED June 14 2017
2. RECORD OF PURCHASE
Job Number
Date of Purchase
Model Number T4PGF1
Serial Number
Weight 45 lb. [21 kg}
Voltage 415 volt
Phase 3 phase
Cycle/Hertz 50/60
Amperage Maximum Per Platen 15 Amp
Total 30 Amp
Circuit Overcurrent Protection Required 30 Amp- 15 per platen, 10 amp pump
Temperature Sensor 100 Ωplatinum RTD
Index of Protection – with case closed IP 67
Design of Protection – with case open IP 66
Ancillary Items platen cables, power supply cable
Spare Parts Fuses: 3 x 10 Amp, 3 x 1 1/4 Amp
Operating Instructions June, 2014
Supplements Omron E5CN-H manual
Service Bulletins none
Warranty Card yes
Drawings Model T4PGF1 drawing W1158-02
Parts Diagrams T4PGF1 Main Assembly, T4PGF1 Internal Assembly

T4PGF1 INSTRUCTION MANUAL Page 4
SHAW-ALMEX INDUSTRIES LIMITED June 14 2017
3. DECLARATION OF CONFORMITY
We,
Shaw-Almex Industries Limited,
of
P.O. Box 430, Parry Sound, Ontario,
Canada,
declare that the machinery:
Product: Temperature Control
Panel
Model: T4PGF1
Year of Design: 2014
has been manufactured using the following transposed harmonized European Standards:
•EN 60204-1 Safety
•EN 50081-1 Emissions (EN55011)
•EN 50082-1 Immunity (EN61000-4-2/3/4/5)
is in conformity with the following Directives:
•73/23/EEC Low Voltage Directive + amendment
•93/68/EEC
89/336/EEC EMC Directive + amendment
•92/31/EEC
89/392/EEC Machinery Directive
and has been designed and assessed to comply with the following, in part or full where relevant:
•AS/NZS 3000:2007 - Electrical Installations (Australian/New Zealand Wiring Rules)
•AS/NZS 3007:2013 - Electrical equipment in mines and quarries (Surface installations and associated
processing plant)
•AS/NZS 2081:2011 - Electrical protection devices for mines and quarries
•AS/NZS 4871.1:2012 - Electrical equipment for mines and quarries (General requirements)
•AS/NZS 4871.4:2010 - Electrical equipment for mines and quarries (Mains powered electrical mobile
machines)
•AS 4242-1994 - Earth-moving machinery and ancillary equipment for use in mines (Electrical wiring
systems at extra-low voltage)
•MDG15:2012 - Guideline for Mobile and Transportable Equipment for Use in Mines
•MDG41:2010 - Guideline for fluid power systems safety at mines
Signed in: Parry Sound, Ontario, Canada
on
Name: Mark Dudas, Eng.
Position: Manager of
Engineering

T4PGF1 INSTRUCTION MANUAL Page 5
SHAW-ALMEX INDUSTRIES LIMITED June 14 2017
4. SAFETY
Shaw Almex Highly recommends that all operators be properly trained by an Almex representative before using
any Almex equipment. This guarantees the full understanding of all safe operating procedures and functions of
the equipment. The material that is presented in this operating manual has been compiled to provide direction
for operating personnel so that the maximum effectiveness of the temperature control panel can be achieved and
so that there is a complete understanding of correct operating procedures. There is a key required to operate the
control panel and it should be in the possession of a qualified person. Unqualified personnel must not open or
work on these units. Any unauthorized work or adjustments immediately VOIDS warranty.
PLEASE READ CAREFULLY
The following safety precautions should be read carefully and understood thoroughly before you set-up or
operate your temperature control panel. Failure to follow these precautions may result in personal injury and/or
equipment damage. All operating personnel should be trained in the proper operation of the temperature control
panel.
The risks associated with operating the temperature control panel are identified throughout this manual with
pictograms.
4.1. Definition of Pictograms
Electrical Hazard Burning Hazard
4.1.1. Electrical Hazard
1. A qualified electrician should perform all maintenance of the electrical components of the temperature
control panel.
2. All of the electrical components contain live circuits. Do not open or service any of the electrical
equipment without disconnecting the main power supply.
3. Incorrect voltage and phase may result in component damage and create a fire hazard. Check the serial
plate for ratings.
4. Equipment power supplies must be properly grounded or a severe shocking hazard may result.
5. Avoid using equipment in wet surroundings or a severe shocking hazard may result.
6. If any cable or connectors are damaged, they must be replaced or a fire and shock hazard may result.
4.1.2. Burning Hazard
There is not a burning hazard with the temperature control panel itself, however, improper use or component
failure could result in the vulcanizer overheating. Always use an Almex temperature control panel when
operating the vulcanizer and never leave the vulcanizer operating while unattended.
4.2. Limitation of use
This equipment has been designed to control the temperature of an AS/GF ALMEX conveyor belt vulcanizer
with the letters AS/GF in the model. The process of vulcanizing is done by applying a combination of heat and
pressure on the product for a certain period of time.
The T4PGF1 temperature control panel operates within a range of 32°F (0°C) to a maximum of 325 °F (163°C).
Refer to the vulcanizer manual for platen limitations. An Almex temperature control panel must be used with an
Almex AS/GF vulcanizer and the vulcanizer should never be allowed to operate while unattended. Other use is
not allowed without the written permission of Shaw-Almex.

T4PGF1 INSTRUCTION MANUAL Page 6
SHAW-ALMEX INDUSTRIES LIMITED June 14 2017
5. ASSEMBLY
5.1. Unpacking
Carefully unpack temperature control panel from the crate and inspect for damage.
Any damages or shortages should be reported to the carrier and / or Shaw-Almex Industries Limited.
5.2. Functional Diagram
T4PGF1 – Face Component Locations
1. Power Supply Connector (1REC) 2. Main Breaker (1CB)
3. Platen Switch (x2) (24-30SS) 4. Platen Temperature Control (x2) (18-25TC)
5. Platen Connector (x2) (5-11REC) 6. Alarm - over temperature audible (73ABU)
7. Emergency Stop Switch (23PB) 8. Keyed Reset / Start Switch (18PB)
9. Ammeter (AM1) 10. Phase Indicator Lights (PL1-3)
11. Pump Plug (39REC 12. Pump Earth Indication Light (PL80)
13. Platen Earth Indicator Light (PL79) 14. Earth Fault Test and Indication Light (47PB)
15. Face Plate Removal Handles (HN) 16. Face Mounting Screws, ( not shown )
See Page 22 For Parts List And Descriptions
Y

T4PGF1 INSTRUCTION MANUAL Page 7
SHAW-ALMEX INDUSTRIES LIMITED June 14 2017
T4PGF1 – Internal Component Locations
1.
Earth fault Current Transformer (9CT) 2. Control Power Transformer (12T)
3. Platen Contactors (22-39CON) 4. Platen Thermal Overloads (22-39CON)
5. Pump Contactor (22-39CON 6. Load Current Transformer (1AM)
7. Power Transformer and Phase Light Fuses (9FU) 8. Pump Fuses (39FU)
9. Terminal Blocks (*STER) 10. Ground/Earth Terminals (*GTER)
11. High Voltage Terminal Blocks (*TER) 12. Detecting Relays and Resistors (R85-104)
13. Power Transformer 120 to 12v DC (80PS) 14. Earth Leakage Detector Relay (47MON)
15. Terminal Locks (*LCK) 16. Transformer Output Fuse (15-82FU)
17. 12 DC Transformer Output Fuse (15-82FU) 18. Earth Leakage Fault Resistor and Base (9R)
19. Ground/Earth Lugs 20. Base to Face Aluminum Standoffs (*ST)
See Page 22 For Parts List And Descriptions.
5.3. Connection Assembly
SAFETY- Ensure the voltage, phase and cycle on the temperature control panel is the same as the power
supply.
Turn the top and bottom platen switches to the 0(off) position.
1. Install a suitable electrical connector to the power supply cable. Refer to the electrical specifications
indicated on the serial plate and in the record of purchase. Connect the GREEN and SILVER wire to earth.
2. Connect the power supply cable to the power supply receptacle on the center face of the temperature
control panel. This is an Arc Flash and Switch rated type of connector that is used for ground fault
protected Almex control systems.
3. The platen connectors are on the face of the temperature control panel. Connect the platen cables by
pressing the plugs firmly into the receptacles and rotate the latches to secure the plugs. Please note: GF
platen and cable male plugs will have pin #6 shorter than the rest. This allows the pilot circuit to break first
removing the power eliminating arc flash, power to disconnect second and earth or ground to disconnect
last.
4. Connect the temperature control panel to the power supply. The phase indication lights will show that
power is supplied to the lines lit. If all line Indicators do not illuminate, have a qualified person check the
problem.

T4PGF1 INSTRUCTION MANUAL Page 8
SHAW-ALMEX INDUSTRIES LIMITED June 14 2017
5. Turn the RESET Key Switch and the temperature controllers will indicate the actual platen temperature and
the set point temperature. The platens cannot be switched on until the MAIN BREAKER is switched fully
OFF and then ON. The system is set to trip at or below 30 ma of current leakage in under 50 ms.
6. OPERATION
6.1. How to Operate and Understand the Safety Features
When power is connected to the panel L1, L2, L3 pilot lights will illuminate. The box will need to be reset
using the keyed reset switch. Once reset a qualified person should take possession of the key so the control box
cannot be randomly reset in the case of an earthing failure. If a failure occurs only qualified personnel can
examine repair or diagnose and reset the control box. The MAIN BREAKER can then be reset. The earth
condition indicators will illuminate and show one of three colours.
Switch the MAIN BREAKER fully OFF (0 or green) with some force and then back ON (1 or red) to reset.
There are 2 indicator lights, one for the platens and one for the pump. If either indicator shows Red there is a
ground wire short. This means a wire has crossed and is giving a false earth signal. The earth connection is not
confirmed as proper. If either indicator shows Yellow, a cable or ground wire may be disconnected or
registering too high a resistance to be sensed properly. This could occur if the pump or platen cable is not
plugged in or if an earth wire is not attached or corroded. If the cables are plugged in and this Yellow indicator
is showing shut down the press and inspect immediately. If a Yellow or Red indication is on the affected plugs
will have power removed immediately by the safety circuits of the T4P-GF box. Power will not be supplied to
the plugs until a Green indicator light is associated with the plug, or plugs. If either indicator shows Green the
system is ready to go. If a pump is not used the pump indicator will show Yellow or no earth/ground attached.
On the face is a Red push button. This is used to test the earth fault system by producing a 30ma signal to
ground. This should trip the earth fault system and turn the main breaker off. Once tripped the push button
will light up Red to indicate an earth fault problem and the power will be removed in under 55ms. If the earth
fault system does not trip, LOCK this box out and have it repaired immediately. This should be checked every
time the T4P-GF system is used. If the system has been tripped on its own and the main breaker is turned off
and/or the push button is illuminated Red, an earth fault condition has occurred. Stop use immediately and have
a qualified person check the problem.
The T4PGF1 temperature control panel has two solid state temperature controllers, one for the top platen and
one for the bottom platen. If one platen cable becomes disconnected, both platens and temperature indicators
will switch OFF. The MAIN BREAKER will remain ON.
The T4PGF1 also has a single auxiliary receptacle for operating an HPP20-4 GF pressure pump. The
connections and coding block will be designed to accept only the voltage the GF box has been built to. The
receptacle is designed to have no power supplied to it unless a properly grounded HPP20-4 GF pump has been
installed and the ground continuity check shows the pump system is functioning properly by indicating a Green
light.
Each temperature controller displays the process value (PV) which is the actual platen temperature, and the set
value (SV) which is the desired temperature. As the platens are heating and coming up to temperature the
controllers will indicate this by running with a Green colour display. As the platen temperatures come close to
the set point they will change to an Amber colour to signify that attention should be paid to the temperatures. If
the platen temperature set point is exceeded the controllers will show a Red display colour and sound a 90 dB
alarm to signify a problem. Correct the problem immediately before damage occurs to the belt splice, or
equipment.
IMPORTANT: The platens must be ground fault ready as identified by an AS/GF in the model type (e.g. SVP-
AS/GF or RAB4-AS/GF) or the T4PGF1 control panel will not function. Most Almex vulcanizer platens can be
easily converted to work with the T4PGF1 control panels. Contact Shaw-Almex Service for information.
The control system is factory set to trip in the case of an earth fault failure below 30ma at or less than 55ms. If
resistance to the earth increases to an unsafe level, the system is designed not to allow power to the platens and
or pump. Each circuit is fused or thermally protected to the appropriate load capability of the parts. “Do not
replace with larger fuses”. The main breaker is rated at 30 amps. The pump is protected at 10 amps. Platen
plugs are protected at 15 amps each.

T4PGF1 INSTRUCTION MANUAL Page 9
SHAW-ALMEX INDUSTRIES LIMITED June 14 2017
6.2. Temperature Controller Settings
The average user need only adjust the temperature set point. The temperature
controller has many other settings that have been set by the factory. All
adjustments other than temperature set point can be protected to avoid making
adjustments that might adversely affect the operation of the controller. See
Protecting Temperature Controller Settings.
In the description of temperature controller settings, the display key is
described with the ↵symbol.
6.2.1. Setting the Platen Temperature
1. The SET VALUE indicator on each controller displays the set point
temperature of the platen. You may change this setting for your
application by pressing the ∧or ∨key to raise or lower set point. This can
be changed anytime but should be done before beginning to heat.
2. After changing the SET VALUE, Turn the RESET Switch to off then back
on. Failure to do this may cause the temperature to overshoot the set point.
Important: The maximum recommended operating temperature for most belts is 325°F (163°C).
6.2.2. Setting Temperature Units to °
°°
°C or °
°°
°F
1. Press and hold the Level key for at least three seconds until IN-t appears in the PV display.
2. Press the Mode key momentarily until d-U appears in PV display.
3. Press the ∧
∧∧
∧or ∨
∨∨
∨key to select C (Celsius) or F (Fahrenheit) in the SV display.
4. Press and hold the Level key until the Operation level screen appears. The setting will be maintained
6.2.3. Setting the Over Temperature Alarm
This feature of the controller will give the operator an audible alarm if the platen temperature rises 20 °F (11°C)
above the SET VALUE. Use the following procedure on each controller:
1. From the Operation level press the Mode key until AL-2 appears in the PV display.
2. Press the ∧or ∨key to set 20 °F or 11 °C in the SV display.
3. Press the Mode key until the Operation screen appears. The setting will be maintained.

T4PGF1 INSTRUCTION MANUAL Page 10
SHAW-ALMEX INDUSTRIES LIMITED June 14 2017
7. HEATING THE VULCANIZER
7.1. Heating Up
Safety: Never heat the vulcanizer unattended and do the Pre-use Inspection before starting.
1. There are three positions on the platen switch as follows:
1A - On Automatic. For automatic temperature control to SET VALUE.
0- Off. Switches power to platens off. Controller remains energized.
1M - On Manual. Override temperature controller and switch power to platen on. This position has a
spring return to off, a Safety Feature so the heat will shut off if the vulcanizer is left unattended.
2. The vulcanizer should be pressurized to at least 5 psi (0.3 kg/sq.cm) before heating.
3. Turn the keyed RESET button to switch power on. Remove the key and have a qualified person hold it.
Then switch the MAIN BREAKER fully OFF (0 or green) with some force and then back ON (1 or red) to
reset. Then turn the keyed RESET button to switch power on. This sets the temperature controllers to
begin the heat cycle. The controllers display will turn Green.
4. Turn the switches to the 1A (on automatic) position to begin heating the vulcanizer. The Ammeter will read
the current for each platen as they are switched on. The OUT 1 light emitting diode on the controller will
light until the process value is close to the set value and then begin to flash. At this point the controllers
display will turn Amber. The platen temperature indicator value will begin to increase as the platen
temperature rises.
Safety: The platen will begin to get hot.
5. Stem thermometers should be inserted into the hole in the platen edge as a secondary means of monitoring
the temperature. The temperature will not necessarily be the same as the temperature control because of
differences in calibration.
6. When the set point is reached, the OUT 1 light emitting diode will continue to flash on and off to maintain
SET VALUE temperature. Start timing the cure when SET VALUE is reached.
7. After the cure time, turn the controller switches to the 0(off) position.
8. Turn the RESET Key Switch before the next heat cycle.
7.1.1. Manual Heating
If there is a temperature controller malfunction or platen temperature sensor failure, the platen can be heated
manually by turning the platen switch to the 1M (on manual) position.
Safety: This switch has a spring return to off, a Safety Feature so the heat will shut off if the vulcanizer is
left unattended. When using this function, the platen temperature will have to be monitored by an external
temperature indicator such as a stem thermometer.
7.2. Temperature Control
1. A P.I.D (Proportional Integral Derivative) solid state temperature controller that senses the resistance
change in an RTD (Resistance Temperature Device) sensor in each platen effects temperature control. The
controller should maintain temperature at the set point +-3 °F (2 °C) at 300 °F (150 °C).
2. The temperature controller incorporates a proportioning circuit that causes the platens to reach set point
temperature in a minimum of time with less than 2 °F (1.1 °C) of temperature overshoot. In operation, the
controllers will begin cycling off and on slightly below set point. During this initial cycling period, the
temperature will continue to rise to the set point as indicated by the temperature controllers. This early
cycling is a normal function of the controller and should not be reset, otherwise excessive temperatures will
occur.
3. The parameters can be adjusted so that set point is reached in the fastest possible time (straight line heating)
but this will cause the temperature to overshoot the set point by several degrees. Alternatively, the
parameters can be adjusted so there is zero overshoot but the rate of heating will decrease as the set point is
reached. If you wish to fine-tune your controller in either of these ways contact Shaw-Almex for advice.

T4PGF1 INSTRUCTION MANUAL Page 11
SHAW-ALMEX INDUSTRIES LIMITED June 14 2017
8. Required Daily Testing
8.1. Required Daily Testing Before Use
This Control system requires daily inspections before use, to confirm full functionality of all safety
features. Failure to do so could put an operator or bystander’s life at risk. Be aware that all safety features
must function as described below. If one system is not operating correctly it could have deadly consequences.
Make sure that the reset key is controlled by ONLY the authorized person on sight. The key allows the T4P-
GF-1U panel to be started, and reset in the case of an earth/ground fault failure. Allowing the key to remain
with the panel while being operated allows anyone to turn on and reset the box without authorization. Take the
key out once the unit is started.
This procedure will require the test plug to complete. The test plug is designed so when installed in the
locations listed below if the switches are both in the center position all receptacles will show a green indicator
because of the 300 ohm resisters used to simulate the pump and platens. If any switch is pushed down the plug
will have its resistance decreased and will generate the platen indicator to indicate a red. This will check each
platen receptacle if done one at a time. If either switch is pushed up it will decrease the resistance to the pump
receptacle and generate a red indication on the pump indicator. Any plug removed will generate a lost pilot and
give a yellow indication.
1. Check the serial plate to confirm the voltage, amperage and phase are correct for the power being
used.
2. Confirm that the platens being used match the power being used.
3. Confirm that the platens are GF compatible by inspecting the serial plate on the platen, (the model
should end in GF).
4. Inspect all cables for damage, wear or unsafe conditions. If you are not familiar with what is
safe for cords and cables get someone who is. Think safety first. If any of the cables are not safe
to use contact your maintenance department and/or Shaw Almex for repair or replacement
instructions.
5. Check the cable plugs and receptacles for signs of wear or conditions that would make them
unsafe to use. If you are not familiar with what is safe for cords and cables get someone who is.
Think safety first. If any of the cables are not safe to use contact your maintenance department
and/or Shaw Almex for repair or replacement instructions.
6. Connect the main power supply cord to the appropriate receptacle and the T4P-GF-1U box.
7. Make sure the E-Stop is reset before continuing.
8. When power is ON the Test Button Fault Indicator and three phase indication lights, L1, L2, and
L3 should be illuminated. There should be no other lights or temperature controllers on at this
time. If this doesn’t occur remove the key and lockout and tag out the unit. Services will be
required.
9. Plug the test plugs into the platen and the pump receptacle, (these must be purchased with every
order of T4P-GF-1U boxes). Make sure the switches are in the center position.
10. Turn the reset key and the temperature controllers should turn on and indicate about 80 F or 27 C
11. At this point the green light should indicate a proper earth/ground connection. If this doesn’t
occur remove the key and lockout and tag out the unit. Services will be required.
12. Reset the main breaker and turn each platen switch to 1M and then O. You should hear the
contactors in the box engage and disengage. If this doesn’t occur remove the key and lockout
and tag out the unit. Services will be required.
13. Place the test cord plug into the pump and platen receptacles. When each toggle switch is used in
the down position it will generate a red light. If either switch is pushed up it will generate a red
pump indicator. If the plugs are removed this will generate a yellow indication. If this doesn’t
occur remove the key and lockout and tag out the unit. Services will be required.
14. Place the test cord plug into the platen receptacles. When the toggle switch is used in the center it
generates a red. When the switch is put in one position it generates a green light on the platen

T4PGF1 INSTRUCTION MANUAL Page 12
SHAW-ALMEX INDUSTRIES LIMITED June 14 2017
indicator, at this point the controllers should light. When the switch is put in the other position it
generates a red light on the pump indicator. When the plugs are removed a yellow indication will
be on. If this doesn’t occur remove the key and lockout and tag out the unit. Services will be
required.
15. If the control box functions as described push the E-Stop button. This should immediately drop
off the main breaker, earth/ ground indicators and temperature controllers, and leave only the
phase indication lights. If this doesn’t occur remove the key and lockout and tag out the unit.
Services will be required.
16. Turn the reset key and reset the main breaker and all of the controllers and indication lights should
return as before. If this doesn’t occur remove the key and lockout and tag out the unit.
17. Press the Test Button Fault Indicator and again immediately drop off the main breaker, earth/
ground indicators and temperature controllers, and leave only the phase indication lights and Test
Button Fault Indicator light on. If this doesn’t occur remove the key and lockout and tag out
the unit. Services will be required. Repeat for the E-Stop button.
18. The box is now ready to be used for belt repair or splicing control. If any of the above features do
not respond as described remove the key and lockout tag out the unit. Contact your maintenance
department and/or Shaw Almex for repair instructions.
Use the Pre-Inspection check Sheet on page 18 for this check list and documentation for your records.
9. MAINTENANCE
9.1. Opening the Control Cabinet
To access the circuits in the control panel, a + screw driver is required. Unqualified personnel must not open or
work on these units. Any unauthorized work or adjustments immediately VOIDS warranty.
SAFETY: Disconnect The Power Supply.
1. Remove the 8 screws around the perimeter of the face panel and carefully lift the chassis out of the case.
The chassis fits very closely into the mounting frame in the case.
2. All fuses are accessible without separating the top from the bottom of the chassis.
3. The chassis is symmetric so it can be placed into the case with the lid at the top or at the bottom. With the
lid at the top, the case can be positioned on the side and the lid will provide shade to make the controllers
more visible.
9.2. Overload Protection
There is overload, ground leakage and continuity check protection for the control circuits and platens inside the
control cabinet. The system is set to trip at or below 30ma of current leakage within 55ms using its internal
ground / earth fault protection system.
The control circuit is protected with a 60 amp circuit breaker that can be reset. The circuits are protected with
fuses and thermal overload switches. The breaker and fuses are clearly labeled.
The top and bottom component panels must be separated to inspect the circuits. Fuses are easily accessed when
the case is removed.
9.3. Temperature Calibration
After replacing a temperature controller, a platen temperature sensor or a platen heating element, the
temperature controller should be calibrated to achieve the best performance. Failure to calibrate the controller
with the vulcanizer will result in temperature over shoot and the temperature control will be less precise.
Note: The temperature controller is a snap in module that can be replaced with a + screwdriver, and is a
recommended spare part. If you have ordered a spare controller, it will be factory set to an average value that
will control your platen reasonably well. Auto Tune the controller as follows.
An external means of checking the platen temperature is required. A portable temperature test meter with at
least two leads is best to conduct the calibration tests. These may be purchased from Shaw-Almex.

T4PGF1 INSTRUCTION MANUAL Page 13
SHAW-ALMEX INDUSTRIES LIMITED June 14 2017
1. Install a section of belting large enough to cover the platen area.
2. Install the temperature meter sensors above and below the belting, 8 inches (200 mm) from the electrical
connector. That is where the platen temperature sensor is located. Cut a groove in the belting to prevent
damage to both sensors and platens.
3. Assemble the vulcanizer and pressurize to 5 psi (0.3 kg/cm2) maximum.
9.3.1. Auto Tune
Each temperature controller has an AUTO TUNE (AT) function that calibrates the controller with the heating
element and the temperature sensor. The controller has been calibrated at the factory and will not require
calibration unless the controller, the heating element or the temperature sensor are changed. Auto Tune the
controller as follows:
1. Connect the power supply and switch the platens to 1A.
2. Turn the Keyed RESET Switch.
3. Press the level key momentarily until.Adj appears in the PV display.
4. Press the mode key once, until the At appears in the PV display.
5. Using the ∧key, select At-2. The AT diode will flash until auto tuning is complete. After set point has
been reached, it may take approximately 20 minutes for the AT diode to stop flashing. It is necessary to
wait for the AT diode to stop flashing before proceeding to return to the temperature display.
6. Press and hold the level key until the CN-t appears in the PV display.
7. Press and hold the level key until the temperature display appears.
9.3.2. Input Shift
If the external temperature meter reading and the temperature controller value are not the same, the controller
should be adjusted. Subtract the controller reading from the external temperature meter reading and record this
difference. Adjust the controller as follows:
1. From the Operation level display press the Level key for one second until LAdJ appears in the PV display.
2. Press the Mode key until INS appears.
3. If the temperature difference is positive, use the ∧key to select the difference.
4. If the temperature difference is negative, use the ∨key to select the difference.
5. Press the Level key and hold until IN-t appears, press and hold the level key until the Operation level
display appears.
6. Insert the stem thermometer and adjust the thermometer dial until the reading is the same as the test meter.
See directions on stem thermometer.

T4PGF1 INSTRUCTION MANUAL Page 14
SHAW-ALMEX INDUSTRIES LIMITED June 14 2017
10. TROUBLESHOOTING
The controller has many capabilities other than those used for the Almex Temperature control panel. Adjust
only those settings described above. Other adjustments may result in the control panel being inoperable. For
detailed instruction of the E5CN-H controller, refer to the OMRON instruction manual supplied with this
temperature controller. Unqualified personnel must not open or work on these units. Any unauthorized work or
adjustments immediately VOIDS warranty.
10.1. No Display on Temperature Controller
FAULT CORRECTION
1.
Power supply is faulty. No phase
lights are on.
2.
Phase lights are on, no power to
system.
1.
Check all cables and power supply connection, and reset the
main feed power breaker.
2.
Check the main breaker on the control box. The temperature
controllers (or pair of controllers) will turn off when the platen
and/or cable is disconnected. Check the indicator lights for
diagnoses. Check the earth fault indication light.
3.
Control circuit fuse has opened.
3.
Disconnect power supply, open the control cabinet, replace 10
or 15FU fuse in the circuit and reset the breaker.
10.2. Error Display on Temperature Controller or Indication Lights
FAULT
CORRECTION
1.
SERR Is indicated on the
temperature controller.
2.
Red push button indicator light on
face.
3.
Pilot indication lights will not
show GREEN and allow operation
of the press.
4.
Loose connection in cable or
platen connector.
1.
This usually means an RTD probe is an incorrect type, has failed
or the signal is not getting to the temperature controller.
2.
This shows earth fault condition has occurred. Have a qualified
person repair the problem. This will also light when the test
button is pushed.
3.
Check the platen and / or pump earth to pilot pins for a 300 to
345 ohm resistance. If close to 0 ohms you have a short between
the pilot and ground and needs IMMEDIATE repair before use.
If the resistance is above 345 and a yellow light is being
indicated your earth is faulty and needs IMMEDIATE repair
before use. If you have 300 to 345 ohms and the green
indication will not come on the pilot system has failed and needs
IMMEDIATE repair before use. Contact Shaw Almex for repair
information.
4.
Remove electrical connector insert from housing and tighten all
connections.
5.
RTD temperature sensor is faulty.
5.
Measure the resistance between pins 4-5 on the platen electrical
connector. Depending on the platen temperature, the resistance
should be between 100-170 Ohms. Replace sensor as described
in the vulcanizer manual.
10.3. Platens Not Heating
FAULT CORRECTIONS
1.
Power supply faulty.
1.
Check that all three phases are powered.
2.
Platen switch OFF.
2.
Turn platen switch ON.
3.
Temperature set improperly.
3.
Ensure that controller set point is correct.
4.
No continuity between power
supply and platen.
4.
Check thermal overloads on the output relays.
5.
Loose connection in control panel.
5.
Disconnect power supply, open the control cabinet and check for
loose wire connections.
6.
Faulty temperature controller.
6.
Refer to Omron instruction manual.

T4PGF1 INSTRUCTION MANUAL Page 15
SHAW-ALMEX INDUSTRIES LIMITED June 14 2017
7.
Faulty relay.
7.
Disconnect power supply, and open control cabinet. Very
carefully connect power supply and switch the platen on. The
temperature controller OUT 1 light should be ON. Check for
line voltage between line side (L1, L2 and L3) and ground on
the contactor. If there is voltage, check voltage between load
side (T1, T2 and T3) on the contactor and ground. If line voltage
is not measured, be sure the contactor is being called down. If it
is the contactor is faulty and must be replaced.
8.
Loose connection in cable or
platen connector (breaker will trip)
8.
Remove electrical connector insert from housing and tighten all
connections.
9.
Faulty RTD temperature sensor.
9.
Measure the resistance between pins 4-5 on the platen electrical
receptacle. Depending on the platen temperature, the resistance
should be between 100-170 Ohms.
10.
Faulty heating element.
10.
Measure the resistance between pins 1-2, 2-3 and 1-3 on the
platen electrical receptacle. Compare the reading with the value
in your Record of Purchase, Element Resistance, Coils
Connected. If the values are not close and the wires and
connections are good, the element must be replaced. The leads
should be protected from moisture by using a small amount of
silicone in the back of the insert terminal to seal the connection.
10.4.Vulcanizer Over Heating
FAULT CORRECTION
1. Temperature set improperly. 1. Ensure that controller set point is correct.
2. Faulty temperature controller. 2. Refer to Omron instruction manual.
3. Faulty relay. 3. Disconnect power supply, and open control cabinet. Using an
Ohmmeter, check for continuity between terminals L and T on
the suspect relay. If there is continuity, relay must be replaced.
4. Faulty RTD temperature sensor. 4. Measure the resistance between pins 4-5 on the platen electrical
receptacle. Depending on the platen temperature, the resistance
should be between 100-170 Ohms.
10.5. Controller will not maintain Set Point Temperature
FAULT CORRECTION
1. Controller not calibrated properly. 1. Follow calibration procedure.
2. Faulty temperature controller. 2. Refer to Omron instruction manual. Replace temperature
controller or call for assistance.
10.6. Yellow or Red on Platen Indicator Light
FAULT CORRECTION
1. Plugs not in tightly enough and
a yellow light is showing.
2. The Pilot end resistor has
failed.
1. Be sure plugs are push in and clamped securely.
2. Check from pin 4 to earth. You should have a reading of
300 ohms. If not replace resistor using the Pilot kit
available form Shaw Almex.
3. End pilot resistor not present in
the platen and a yellow light is
showing.
4. A red light is indicated on the
Platen Indicator due to weak
earth wires.
5. The pilot Checking Circuit has
failed.
3. Purchase a GF Pilot kit to install in the platen to correct
the situation or use the correct platens.
4. Repair the ground/earth line or the pilot line so the correct
resistance is present. With the pilot kit installed the pilot
pin to ground must read 300 +- 10% ohms.
5. The Red light is preprogramed to be on from an input of 0
ohms to 250 ohms from pin 4 to ground. The Yellow
light is preprogramed to be on from an input of 340+
ohms from pin 4 to ground. For instructions or
replacement parts contact Shaw Almex.

T4PGF1 INSTRUCTION MANUAL Page 16
SHAW-ALMEX INDUSTRIES LIMITED June 14 2017
11 Required Maintenance Schedule.
11.1 Daily Inspection Check Sheet
The below pre-use inspection check sheet provides an outline of all components used in the safe operation of Shaw Almex
GF vulcanizing equipment. Survey the Control panel to insure all components are functioning properly and are in good
working order. Before operating the vulcanizer verify that all systems is operating properly. During the pre-use inspection of
equipment, items below can be check marked upon completion. If any of the check boxes fail Lock-Out Tag-Out the control
box immediately until completely restored to original operational OEM specification.
Unqualified personnel must not
open or work on these units. Any unauthorized work or adjustments immediately VOIDS warranty.
DAILY INSPECTION CHECK SHEET
*
All information to be printed and completed in ink.
Company Performing Inspection:
Location of Inspection:
Initial boxes if the item passes. Lock-out Tag-out immediately if not!
EQUIPMENT/ASSEMBLY Mon Tues Wed Thur Fri Sat Sun
Complete system functionality check, ( see Daily Prestart Inspections Sec
8)
Electrical cable and cords are in good orking order and not damaged.
Receptacle and locking clamp condition inspection
Case condition, (no damage or loose scre s).
All arning labels / serial label inspection for voltage, phase and Hz
information clear and readable.
All controls must be free of visual damage and leaks
Check Earth / Ground fault system ith the test button and test cable. Look
for visual indication.
Confirm that all indication light functionality, as per section 8.1. Required
daily testing Before Use
Check platen after control box function is confirmed ith the test plug.
Confirm Earth / Ground light is functioning as described in Sec 7, ( platen
out a yello indication, platen in, if good, a green indication. Red should
have been confirmed ith the test plug
Check E-Stop operation.
Po er supply verified/correct to equipment design and description on the
serial label.
Name of person performing inspection:
Date of Inspection:
Time Inspection Completed:
Initialed by person performing inspection:
Serial number of equipment inspected:
If any component is found to be unserviceable, tag the component out of service and notify the Supervisor in charge immediately.

T4PGF1 INSTRUCTION MANUAL Page 17
SHAW-ALMEX INDUSTRIES LIMITED June 14 2017
11.2 Maintenance Schedule Check Sheet
Maintenance Schedule
*
All information to be printed and completed in ink.
Company Performing Inspection:
Location of Inspection:
EQUIPMENT/ASSEMBLY Prior
to
each
use
Every
month
or 30
cycles
Every
6 th
month
or
180
cycles
Every
Year
Please
initial if
the item
passed the
inspection
COMMENTS
Having an Almex technician inspect the control
panel to verify original operation, design, and
function, is highly recommended.
X
X
Complete system operation check, (see Daily
Testing Sec 8)
X X X X
Electrical cable and cords are in good orking
order and free of damage and visibly labeled.
check continuity of the cables
X
X
X
X
Receptacle and Locking Clamp Condition
Inspection
X
X
X
X
Case Condition, (Damage or loose scre s). X X X X
All arnings and Indication / Serial Label
inspection for Voltage, Phase and Hz
Information are Easily Visible.
X
X
X
X
All controls must be free of damage and leaks.
X
X
X
X
Check Earth / Ground Fault System ith the
Test Button And look for Visual Indication.
X
X
X
X
Confirm All Indication Lights Function. X X X X
Check All Earth Resistance values by Checking
Resistance Continuity from The Main Incoming
Earth To the Receptacle Earths, face plate and
cases. All Earths/Grounds MUST be belo 0.5
Ohms.
X X X X

T4PGF1 INSTRUCTION MANUAL Page 18
SHAW-ALMEX INDUSTRIES LIMITED June 14 2017
EQUIPMENT/ASSEMBLY
Prior
to
each
use
Every
month
or 30
Cycles
Every
6 th
month
or
180
cycles
Every
Year
Please
initial if
the items
passed
inspection
COMMENTS
Check All Earth Resistance values by Checking
Resistance Continuity from The Main Incoming
Earth To the Receptacle Earths. All
Earths/Grounds MUST be belo 0.5 Ohms.
X
X
X
X
Check E-Stop operation. X X X X
Open case and check for loose or damaged
parts
X X
Inspect ALL ires and terminations and
terminals for tightness, (contact Almex for
instructions or have The technician check
during inspection).
X
X
Run a complete cycle to check the operation of
the unit under normal electrical ork loads and
conditions, (Contact Almex for instructions).
X
X
Check for proper temperature controller
readings (Contact Almex for instructions or
have The Technician check during inspection).
X
X
Check for proper resistance settings on the
pilot checking circuits. Yello light must
indicate belo 350 ohms. Red must be
indicating above 440 ohms. Contact Shaw
almex for proper testing.
X
X
Use a Mega Ohm tester to test L1 to L2, L2 to
L3, L3 to L1, and all lines to Earth. The test
Must sho a resistance higher than 1 Meg.
X
Name of person performing inspection:
Date of Inspection:
Time Inspection Completed:
Signed by person performing inspection:
Serial number of equipment inspected:
If any component is found to be unserviceable, tag the component out of service and notify the Supervisor in charge immediately. Replace
with ONLY Exact Replacement Parts. check with Shaw Almex for Exact Part Numbers if there is any Doubt At All.

T4PGF1 INSTRUCTION MANUAL Page 19
SHAW-ALMEX INDUSTRIES LIMITED June 14 2017
12. RECEPTACLE PIN EXPLANATION
Platen receptacle
Pump Receptacle
Ground Pin
Pilot Pin
Power Pins
Voltage Coding Pin

T4PGF1 INSTRUCTION MANUAL Page 20
SHAW-ALMEX INDUSTRIES LIMITED June 14 2017
13. Service
12.1.Emergency Service
Contact: Service Department
Telephone: 705 746 5884
1 800 461 4351 (Canada and U.S. only)
Fax: 705 746 9484
Mail: SHAW-ALMEX INDUSTRIES LIMITED
P.O. Box 430
Parry Sound, Ontario
Canada, P2A 2X4
e-mail: service@almex.com
12.2.Return of Goods Authorization
The service department of Shaw-Almex Industries Limited MUST be contacted for the necessary authorization
and documentation prior to returning goods to the factory.
The service department may be reached at the above numbers.
12.3.Guarantee
Your ALMEX vulcanizing equipment is guaranteed against defective parts, material and workmanship for a
period of 12 months from the date of purchase. For complete details, refer to the Warranty Card. Please
complete the Warranty card and return it to register your product with Shaw Almex.
12.4.Safety Notifications
All registered owners of Almex equipment will be notified either directly, or through an authorized distributer
of a product recall or upgrade. If there are concerns please check with your local distributer.
Table of contents
Other Almex Control Panel manuals
Popular Control Panel manuals by other brands

Bosch
Bosch Radionics D8024 Operator's guide
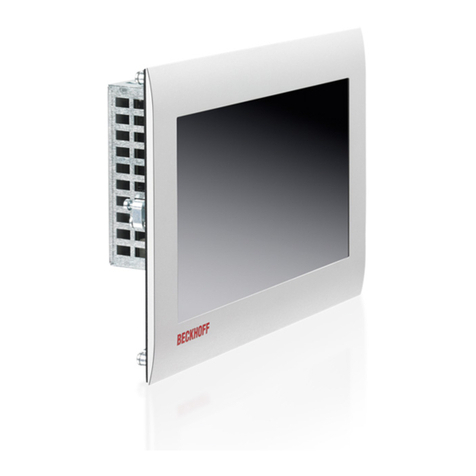
Beckhoff
Beckhoff CP6900-0001-0000 Installation and operating instructions

Satel
Satel PERFECTA 16-WRL Programming manual
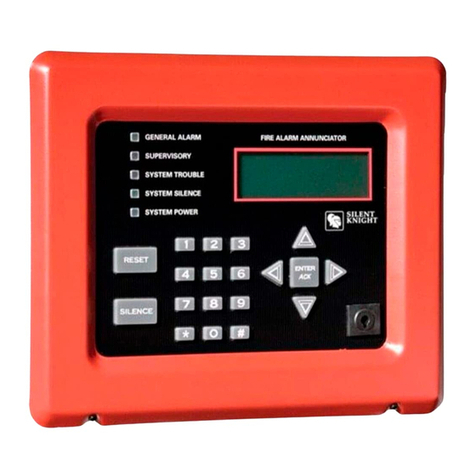
Honeywell
Honeywell Silent Knight 5860 Product installation document
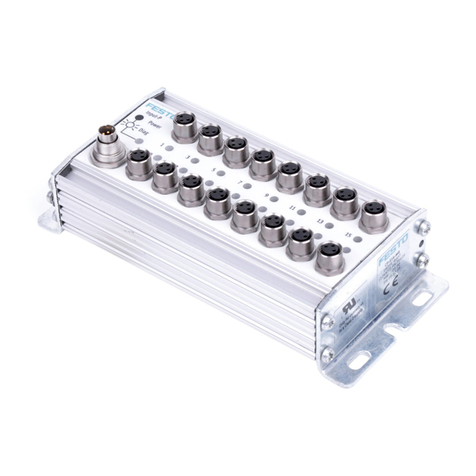
Festo
Festo CP-E16-M8 manual

Sunricher
Sunricher SR-2831DMX quick start guide