Alstom M65D User manual

M6xx
Measurement Centre and Transducer
DNP3 Manual
M6xx
Measurement Centre and Transducer
Publication Reference: M6xxD/EN/M/B
M6xxD/EN/M/B © 2014. ALSTOM, the ALSTOM logo and any alternative version thereof are trademarks and service marks of ALSTOM. The other names
mentioned, registered or not, are the property of their respective companies. The technical and other data contained in this document is provided for information only.
Neither ALSTOM, its officers or employees accept responsibility for, or should be taken as making any representation or warranty (whether express or implied), as to
the accuracy or completeness of such data or the achievement of any projected performance criteria where these are indicated. ALSTOM reserves the right to revise or
change this data at any time without further notice.
GRID


DNP3 Manual
M6xxD/EN M/B
M6xx Page 1
TABLE OF CONTENTS
CERTIFICATION..........................................................................................................................................3
INSTALLATION AND MAINTENANCE.......................................................................................................3
ASSISTANCE...............................................................................................................................................3
COPYRIGHT NOTICE..................................................................................................................................4
SAFETY SECTION.......................................................................................................................................4
1.0 DNP INTERFACE...................................................................................................................................5
1.1 Description.........................................................................................................................................5
1.2 DNP Address.....................................................................................................................................5
1.3 Transaction Timing ............................................................................................................................5
1.4 Object Format....................................................................................................................................5
1.4.1 DNP3 Calculation-Type Codes ..................................................................................................6
1.5 Configuration .....................................................................................................................................9
1.5.1 Setting CT and VT Ratios ..........................................................................................................9
1.5.2 Resetting Energy and Demands ................................................................................................9
1.5.3 Tag Registers ...........................................................................................................................10
1.6 Converting Data to Engineering Units .............................................................................................10
1.7 Primary Units ...................................................................................................................................12
1.8 Data Sets and Data Types ..............................................................................................................14
1.8.1 Configuring the Class-0 Response ..........................................................................................14
1.8.2 Configuring Class-1, Class-2 and Class-3 Events ..................................................................15
1.9 Health Check ...................................................................................................................................16
1.10 Heartbeat State Counter................................................................................................................16
1.11 Meter ID Register ..........................................................................................................................16
1.12 Custom Points Lists.......................................................................................................................16
2.0 DNP PROTOCOL................................................................................................................................20
2.1 Introduction......................................................................................................................................20
2.2 Overall Protocol Structure ...............................................................................................................20

DNP3 Manual
M6xxD/EN M/B
M6xx Page 2
2.3 DNP Request/Response Overview .................................................................................................20
3.0 DNP3 OVER ETHERNET (TCP).........................................................................................................21
3.1 DNP/IP.............................................................................................................................................21
4.0 DNP3 EVENTS OVERVIEW ...............................................................................................................22
4.1 ANALOGUE CHANGE EVENTS.....................................................................................................22
4.2 FROZEN COUNTER EVENTS........................................................................................................23
4.3 BINARY INPUT CHANGE EVENTS ...............................................................................................23
Appendix A: Bitronics Legacy DNP3 Point Assignments....................................................................24
Appendix B: DNP3 Configuration Parameters......................................................................................31
Appendix C: DNP3 Device Profile ..........................................................................................................36

DNP3 Manual
M6xxD/EN M/B
M6xx Page 3
CERTIFICATION
Alstom Grid certifies that the calibration of the products is based on measurements using equipment
whose calibration is traceable to the United States National Institute of Standards Technology (NIST).
INSTALLATION AND MAINTENANCE
Alstom Grid products are designed for ease of installation and maintenance. As with any product of this
nature, installation and maintenance can present electrical hazards and should be performed only by
properly trained and qualified personnel. If the equipment is used in a manner not specified by Alstom
Grid, the protection provided by the equipment may be impaired.
ASSISTANCE
For assistance, contact Alstom Grid Worldwide Contact Centre:
http://www.alstom.com/grid/contactcentre/
Tel: +44 (0) 1785 250 070
M6xx Manual Set
M65x User Manual
M6xx Modbus Protocol Manual
M6xx DNP3 Protocol Manual

DNP3 Manual
M6xxD/EN M/B
M6xx Page 4
COPYRIGHT NOTICE
This manual is copyrighted and all rights are reserved. The distribution and sale of this manual is
intended for the use of the original purchaser or his agents. This document may not, in whole or part,
be copied, photocopied, reproduced, translated or reduced to any electronic medium or machine-
readable form without prior consent of Alstom Grid, except for use by the original purchaser.
This manual incorporates information protected by copyright and owned by
Bitronics LLC, 261 Brodhead Road, Bethlehem, PA 18017.
Copyright © 2014 Bitronics, LLC. All rights reserved.
The product described by this manual contains hardware and software that is protected by copyrights
owned by one or more of the following entities:
Bitronics, LLC, 261 Brodhead Road, Bethlehem, PA 18017
Schneider Automation, Inc., One High Street, North Andover, MA 01845
Triangle MicroWorks, Inc., 2213 Middlefield Court, Raleigh, NC 27615
Freescale Semiconductor, Inc., 6501 William Cannon Drive West, Austin, TX 78735
gzip inflation uses code Copyright 2002-2008 Mark Adler
inarp uses WinPcap, which is Copyright 1999-2005 NetGroup, Politecnico di Torino (Italy), and 2005-
2010 CACE Technologies, Davis (California).
TRADEMARKS
The following are trademarks or registered trademarks of Alstom Grid:
Alstom Grid the Alstom Grid logo
The following are trademarks or registered trademarks of Bitronics LLC:
The Bitronics logo Bitronics
The following are trademarks or registered trademarks of the DNP User's Group:
DNP DNP3
The following are trademarks or registered trademarks of Schneider Automation, Inc.:
MODSOFT Modicon Modbus Plus ModbusCompact 984 PLC
SAFETY SECTION
Please refer to the M65x or M66x User Manual for information regarding safety, installation,
commissioning and decommissioning.

DNP3 Manual
M6xxD/EN M/B
M6xx Page 5
1.0 DNP INTERFACE
1.1 Description
The DNP network is a "MASTER" to "SLAVE" network; that is to say, one node asks a question and a
second node answers. A NODE is a DNP device (RTU, Computer, M65x, M66x, etc.) that is connected to
the network. Each DNP NODE has an ADDRESS in the range of 0 to 65519, and it is this address that
allows a MASTER to selectively request data from any other device. DNP uses the address range 65533-
65536 for broadcast functions. Broadcast requests never generate DNP responses.
The DNP implementation in the M6xx conforms to DNP3 specifications as defined by DNP.org (derived
from the Harris IED (Intelligent Electronics Devices) implementation guidelines). Data obtained by the
DNP READ CLASS 0 command is configurable. Individual items can also be read using READ BINARY
OUTPUT STATUS or READ ANALOGUE INPUT or READ COUNTER or READ ANALOGUE OUTPUT
STATUS or READ BINARY INPUT or READ FROZEN COUNTER commands.
The Energy values can be reset to zero by issuing the DIRECT OPERATE, DIRECT OPERATE NO
ACKNOWLEDGE, or SELECT BEFORE OPERATE by using the CONTROL RELAY OUTPUT BLOCK
object.
The Demand values can be reset by issuing the same DIRECT OPERATE, DIRECT OPERATE NO
ACKNOWLEDGE, or SELECT BEFORE OPERATE command to the other points of this object.
M6xx ANALOGUE OUTPUTS have two read/write values: Tag and Tag1. They can be changed by
issuing DIRECT OPERATE, DIRECT OPERATE NO ACKNOWLEDGE, or SELECT BEFORE
OPERATE by using the ANALOGUE OUTPUT BLOCK object. Due to the limited number of FLASH write
cycles, they SHOULD NOT be written continuously.
Four legacy values are also presented. They are CT Scale Factor Normalized Ratio and Divisor, and VT
Scale Factor Normalized Ratio and Divisor. They are derived from the PT scale and CT scale configured
through the browser interface.
The SELECT BEFORE OPERATE arm timeout value is configurable from zero to 64 seconds.
1.2 DNP Address
The serial port in the M65x can be set up to be RS-232 or RS-485, and support baud rates from 9600 to
115200. Configuring the Serial Ports can be accomplished by using the display buttons or via a standard
web browser while setting the address is done via a web browser only.
Each DNP instrument responds to a single destination address in the range 0-65519. Each instrument on
a DNP link must have a unique address. M6xx meters will allow any of the 65520 addresses to be
selected. DNP instruments also use a BROADCAST address range of 65533-65535. Requests sent to a
BROADCAST address cause the instrument to execute the function but not generate a response.
1.3 Transaction Timing
M6xx meters complete a set of calculations approximately every 100ms. Incoming messages are parsed
every 50ms.
1.4 Object Format
M6xx meters report all static measurements via the use of three static objects. These objects include
COUNTER (object 20, variations 1, 2, 5 and 6), ANALOGUE INPUT (object 30, variations 1, 2, 3 and 4)
and BINARY INPUT (object 2, variations 1 and 2). These objects are read only and cannot be modified
by DNP MASTER devices.
ANALOGUE OUTPUT STATUS (object 40, variation 2) can read CT and VT configuration information and
two tag registers. ANALOGUE OUTPUT BLOCK (object 41, variation 2) can be used to write the
Tag/Tag1 register through DNP. Due to the limited number of FLASH write cycles, Tag/Tag1 SHOULD

DNP3 Manual
M6xxD/EN M/B
M6xx Page 6
NOT be written continuously. Pseudo output points (such as demand and energy resets) are reported
using the BINARY OUTPUT STATUS (object 10, variation 2).
M6xx meters are capable of reporting ANALOGUE CHANGE EVENTS (object 32, variations 1 through 4).
Any ANALOGUE INPUT can be configured to report as a CLASS-1, CLASS-2, or CLASS-3 ANALOGUE
CHANGE EVENT. Point, Class, Analogue Deadband Values and Object Variation are all selectable by
use of the Ethernet service port and web browser. The default Object Variations are selectable by Object
(not by point). All ANALOGUE CHANGE EVENTS can be configured to report with or without time.
M6xx meters support frozen counter events (object 21, variations 1, 2, 5 and 6 which are 16 or 32-bit with
or without time).
M6xx meters support one BINARY INPUT (object 1, variations 1 and 2) and one BINARY INPUT
CHANGE event (object 2, variations 1, 2, and 3). The single binary input is derived from the OR of the
bits from the Health status word.
The DNP protocol allows each device to determine the best method of data transfer. The M6xx meters
support this by selecting the most appropriate response variation when either the requested variation is 0
or a CLASS-0 read is requested. Both COUNTER and ANALOGUE INPUT objects allow optional flags to
be used. If a value is requested as variation 0, the M6xx meter responds as selected with the default
variation selected through the browser.
When reading objects, the Health Check point (object 30, point 0) should always be read and checked
before interpreting data, since some failure modes will cause erroneous data to be presented (See
Section 1.8). The majority of the points are represented in Normalized 2's complement format. For
conversion of the point data into engineering units, please refer to Section 1.6. Appendix A provides the
Legacy or Bitronics Legacy Fixed (BiLF) point set used in the M6xx.
NOTE: Unless otherwise specified, all points are READ ONLY.
1.4.1 DNP3 Calculation-Type Codes
The DNP3 Type codes for Optimal Resolution that are applicable to the point assignments in the
appendix tables are highlighted within the following Calculation Type table:

DNP3 Manual
M6xxD/EN M/B
M6xx Page 7
Type Description
T1 Unsigned 16-Bit Integer
T2 Signed 16-Bit Integer - 2's Complement - Saturation 10
Float Value = ( (Integer Value) / 32768) * Scale * 10)
Example: 5.0 A stored as 16384 when Amp Scale = 1:1
T3 Signed 16-Bit Integer - 2's Complement - Saturation 15
Float Value = ( (Integer Value) / 32768) * Scale * 15)
Example: 150 A stored as 16384 when Amp Scale = 20:1
T4 Signed 16-Bit Integer - 2's Complement - Saturation 150
Float Value = ( (Integer Value) / 32768) * Scale * 150)
Example: 119.998 V stored as 26214 when Volt Scale = 1:1
T5 Signed 16-Bit Integer - 2's Complement - Saturation 1500
Float Value = ( (Integer Value) / 32768) * Scale * 1500)
Example: -750.0 W stored as -16384 when Volt Scale = 1:1, Amp Scale 1:1
T6 Signed 16-Bit Integer - 2's Complement - Saturation 4500
Float Value = ( (Integer Value) / 32768) * Scale * 4500)
Example: -90.0 kW stored as -8192 when Volt Scale = 20:1, Amp Scale 4:1
T7 Signed 16-Bit Integer - 2's Complement - 3 Decimal Places
Example: -12.345 stored as -12345
T8 Signed 16-Bit Integer - 2's Complement - 2 Decimal Places
Example: 123.45 stored as 12345
T9 Signed 16-Bit Integer - 2's Complement -1 Decimal Place
Example: -1234.5 stored as -12345
T10 Unsigned 16-Bit Integer - Normalized Ratio
ratio = (Normalized Ratio / Ratio Divisor)
Example : 1.234, 12.34, 123.4, and 1234 are all stored as 1234
T11 Unsigned 16-Bit Integer - Ratio Divisor
ratio = (Normalized Ratio / Ratio Divisor); valid Ratio Divisors are 1,10,100,1000
Example: X.XXX stored as 1000, XX.XX stored as 100, XXX.X stored as 10
T12 Signed 16-Bit - 2's Complement - Saturation 2
Gain Value = Integer Value /16384)
Example: -0.250 stored as -4096
T13 Unsigned 16-Bit Integer - 12 Bit Offset Binary - Saturation 10
Float Value =( (Integer Value - 2047) / (2048) ) * Scale * 10

DNP3 Manual
M6xxD/EN M/B
M6xx Page 8
Type Description
Example: 5.0 A stored as 3071 when Amp Scale 1:1
T14 Unsigned 16-Bit Integer - 12 Bit Offset Binary - Saturation 150
Float Value =( (Integer Value - 2047) / (2048) ) * Scale * 150
Example: 119.97 V stored as 3685 when Volt Scale 1:1
T15 Unsigned 16-Bit Integer - 12 Bit Offset Binary - Saturation 1000
Float Value =( (Integer Value - 2047) / (2048) ) * Scale * 1000
Example: -500 W stored as 1023 when Volt Scale = 1:1, Amp Scale = 1:1
T16 Unsigned 16-Bit Integer - 12 Bit Offset Binary - Saturation 3000
Float Value =( (Integer Value - 2047) / (2048) ) * Scale * 3000
Example: 349.10 kW stored as 3040 when Volt Scale = 6:1, Amp Scale = 40:1
T17 Unsigned 16-Bit Integer - 12 Bit Offset Binary - Saturation 15
Float Value =( (Integer Value - 2047) / (2048) ) * Scale * 15
Example: 11.79 A stored as 2369 when Amp Scale 5:1
T18 Unsigned 16-Bit Integer - 12 Bit Offset Binary -1 Decimal Place
Float Value = ( (Integer Value - 2047) / (10) )
Example: 121.4 degrees stored as 3261
T19 Unsigned 16-Bit Integer - 12 Bit Offset Binary -3 Decimal Place
Float Value = ( (Integer Value - 2047) / (1000) )
Example: 0.978 Power Factor stored as 3025
T20 Unsigned 16-Bit Integer - Bit Control/Status
0' - stored as zero; '1' - stored as 65536
T21 Unsigned 16-Bit Integer - 3 Decimal Places
Example: 54.321 stored as 54321
T22 Bit
Example: 1-bit is set, 0-bit is clear
T23 Signed 16-Bit Integer – 2’s complement – Saturation 300
Float Value = ( ( Integer Value)/32768) * Scale * 300)
Example: 207.846 V stored as 22702 when Volt Scale = 1:1
T24 Signed 16-Bit Integer – 2’s Complement – 3 Decimal Places, offset by 60
Float Value = (Integer Value)/1000) + 60.0)
Example: 60.005Hz stored as 5

DNP3 Manual
M6xxD/EN M/B
M6xx Page 9
1.5 Configuration
1.5.1 Setting CT and VT Ratios
M6xx meters are capable of internally storing and recalling CT and VT ratios. The CT and VT ratios
are configured through the Web interface or front panel, and are stored in non-volatile memory on the
CT/VT section of the power supply board Each ratio is stored in two points, one for the Normalized
Ratio and the other for the Ratio Divisor. Allowable constants for the normalized ratios are 1000 to
9999. The Ratio Divisors may be 1, 10, 100, or 1000 only. The number stored will be the high side
rating of the CT Ratio or VT Ratio. Both a 500:5 ratio CT and a 100:1 CT will have a value of 100
stored. For example, to calculate a CT and VT ratio for Phase A from the data stored in the M6xx
meters, use the following equation:
(:)
(:)
(:)
(:)
RATIO
RATIO
Phase A CT Value AO 21
Phase A CT Phase A CT RatioDivisor AO 22
Phase A VT Value AO 05
Phase A VT PhaseAVT RatioDivisor AO 06
M6xx meters calculate all measured quantities in secondary units (except energy). The CT and VT
ratio information is used to calculate the primary values.
In the event of a CT/VT Ratio Checksum Failure, the value in the Normalized CT Ratio and
Normalized VT Ratio points default to 1000, and the value in the CT Ratio Divisor and VT Ratio Divisor
default to 1000. This results in a 1:1 CT Ratio and 1:1 VT Ratio.
1.5.2 Resetting Energy and Demands
The Energy and Demand registers can be reset by issuing a CONTROL RELAY OUTPUT BLOCK to
the appropriate BINARY OUTPUT.
Reset Functions
Reset Energy
Reset Demand Amps
Reset Demand Volts
Reset Demand Power

DNP3 Manual
M6xxD/EN M/B
M6xx Page 10
1.5.3 Tag Registers
The M6xx meters provide a "TAG" BINARY OUTPUT for user identification purposes. DNP sessions
have an additional tag register (“Tag Register 1”). An ANALOGUE OUTPUT BLOCK can be issued to
either point to write a number from 0 to 65,535 in a tag register. Tag registers are also writeable
through the web interface.
1.6 Converting Data to Engineering Units
As mentioned in Section 1.5, the majority of the data is stored in a normalized 2's complement format.
When displaying these values at another location, it may be desirable to convert this format into
engineering units. This conversion is readily accomplished using the following simple scaling
equations:
BASIC EQUATION FOR NORMALIZED ANALOGUE INPUTS:
32768 SECONDARY
Value Normalized Scale Factor
Engineering Units Default Full Scale Scale Factor Divisor
The Value referred to in the equations would be the value stored in the point that you wished to
convert to engineering units. For example if you wanted to convert Phase A Amperes into engineering
units, Value would be the value in ANALOGUE-INPUT point.
ENERGY is stored as 32-BIT values in static COUNTER points. Energy values are in units of
PRIMARY kWh or kVARh.
FREQUENCY is stored as a single binary value that is the actual frequency times 100.
POWER FACTOR is stored as the value times 1000. Negative power factors indicate that the VARs
are positive. The sign of the Power Factor is the inversion of the Exclusive-OR of the Watts and VARs
(i.e. if either or both of the Watts or VARs are negative, then the Power Factor will be negative).

DNP3 Manual
M6xxD/EN M/B
M6xx Page 11
3 and 2 ½ ELEMENT EQUATIONS (5Amp CTs):
Max
Max
Min Max
*
(Inst,Fund,Demand, ) RATIO
*
N (Inst,Fund,Demand, ) RATIO
RATIO
L-N (Inst,Fund,Demand, , )
L-L(Ins
Value
= x x
AMPEREs 10 CT
32768
Value
= x x
AMPEREs 15 CT
32768
Value
= x 150 x
VOLTs PT
32768
Min Max
Min Max
RATIO
t,Demand, , )
*RATIO
R
ATIO
TOTAL(Inst,Demand, , )
PER PHASE (Inst)
Value
(SCALED)= x 150 x x 3
VOLTs PT
32768
Value
WATTs (VARs)(VAs = x x x
)4500 CT
PT
32768
Value
WATTs(VARs)(VAs =
)32
Max
*RATIO RATIO
(True,Displacement)
(Amps,Volts,Inst,Demand, )
x x x
1500 CT
PT
768
Value
FREQUENCY = 100 Value
POWER =
FACTOR 1000
kWh(kVARh)=Value
Value
THD, =
TDD 10
Value
K-Factor= 100
* For One Amp CT Option,dividethis valueby 5

DNP3 Manual
M6xxD/EN M/B
M6xx Page 12
2 ELEMENT EQUATIONS (5Amp CTs) :
The above equations provide answers in fundamental units (VOLTs, AMPs, WATTs, VARs, VAs and Hz).
If the user desires other units such as KILOVOLTS, KILOWATTS or KILOVARS, the answers given by
the equations should be divided by 1,000. If the user desires MEGAWATTS or MEGAVARS, the answers
given by the equations should be divided by 1,000,000. Energy values are in units of kWh or kVARh.
1.7 Primary Units
An option exists to choose Primary Units instead of the pre-existing scaling mode, 'Optimal Resolution'
adding the concept of 'scaling modes' to M6xx. The pre-existing scaling mode is called 'Optimal
Resolution' on the basis that resolution of the protocols are optimized based on secondary full scale and
therefore independent of CT and VT settings. The 'Primary Units' mode creates protocol values that
include CT and VT settings, which requires the user to choose a scaling factor (in multiples of 10). The
scaling factor must be selected such that it achieves the desired resolution and does not cause an
overflow in the protocol value. The Scaling mode selection and the scaling factors are maintained
separately for both Modbus and DNP and are configured on the Settings/Protocol webpage. Below is a
screen shot and explanation of the Primary Units mode:
Max
Min Max
Min Max
*
(Inst,Fund,Demand, ) RATIO
RATIO
L- L (Inst, Demand, , )
*RAT
TOTAL(Inst,Demand, , )
Value
= x x
AMPEREs 10 CT
32768
Value
= x 150 x
VOLTs PT
32768
Value
WATTs(VARs)(VAs = x x
)3000
32768
Max
IO
R
ATIO
(True,Displacement)
(Amps,Volts,Inst,Demand, )
x CT
PT
Value
FREQUENCY = 100 Value
POWER =
FACTOR 1000
kWh(kVARh)=Value
Value
THD, =
TDD 10
Value
K-Factor= 100
* For One Amp CT Option,dividethis value by 5

DNP3 Manual
M6xxD/EN M/B
M6xx Page 13
There are three new configurable parameters:
Amps per count – APC
Volts per count – VPC
Watts per count - WPC
There are three new calculation types:
Currents - B16_2S_PRIMARY_I
Voltages - B16_2S_PRIMARY_V
Powers - B16_2S_PRIMARY_P
When Primary Unit mode is selected, appropriate calculation types are substituted per the following table.
This substitution occurs across all pre-defined and user configured register sets. Note, other calculation
types are unaffected as they represent their values (such as Frequency, Power factor) in primary units
even in Optimal Resolution mode. Also, since the 12-bit calculation types are not included in the
substitution this means that the Modbus BiLF12 register set is not affected.
Modbus
Manual DNP
Manual Optimal Resolution
Calculation Type Replaced by
Calculation Type Note
T2 T2 B16_2S_10_M10 B16_2S_PRIMARY_I
T3 T3 B16_2S_15_M15 B16_2S_PRIMARY_I
T4 T4 B16_2S_150_M150 B16_2S_PRIMARY_V
T23 T23 B16_2S_300_M300 B16_2S_PRIMARY_V
na na B16_2S_600_M600 B16_2S_MULT_10 Power supply voltage
T5 T5 B16_2S_1500_M1500 B16_2S_PRIMARY_P
T6 T6 B16_2S_4500_M4500 B16_2S_PRIMARY_P

DNP3 Manual
M6xxD/EN M/B
M6xx Page 14
1.8 Data Sets and Data Types
The M6xx meters are shipped with a pre-defined set of data points and data types. These fixed points do
not change. The List of Available Measurements may be found in the M65x or M66x User Manual. The
Ethernet port and web browser are required to create the configurable points list. See section 1.11 for
more detail.
For users who wish to use M6xx meters on systems configured for other Bitronics products, a Legacy
point list may be selected. This Legacy list cannot be modified, and will cause the M6xx to emulate the
response of a Bitronics MultiComm or PowerPlex unit.
1.8.1 Configuring the Class-0 Response
The Class-0 request is a very short request to “give all essential data”. Since the M6xx is capable of
providing a significant amount of data, provisions have been made to tailor the response to this request.
A web browser interfacing to the Ethernet service port is required to change the Class-0 response. The
Legacy Class-0 response can also be configured.
When selecting a Legacy points list, the user will be prompted to enter a BiLF Class0 mask. The following
table shows what bits must be set to get the legacy class0 response.
In Legacy mode, a zero BiLF Class0 mask returns a fairly small collection of points. As each bit is set,
more points are added to the response.

DNP3 Manual
M6xxD/EN M/B
M6xx Page 15
BiLF Class0 Bitmask
Configuration Bit
Description Objects
Always included in
Class0 scan.
Resets C
L
A
S
S
0
R
E
S
P
O
N
S
E
C
O
N
F
I
G
U
R
A
T
I
O
N
BO:0-3
Health, Volts, Amps, Watts, VARs,
Frequency AI:0-20
Configuration Settings AO:4, 6
Bit 0
Energy & Heartbeat (Counter
Objects)
CT:0,1,2,3,4
Bit 1
Instantaneous VA & PF AI:21 - AI:28
Bit 2
RMS Demands AI:29 - AI:54
Bit 3
Maintenance Information AI:55 - AI:58
AO:0-3, 10 – 14
Bit 14
Include all data in Class0 poll
Include all data in
Class0 poll
1.8.2 Configuring Class-1, Class-2 and Class-3 Events
ANALOGUE INPUT points can be monitored for ANALOGUE CHANGE EVENTs by assigning the point to
CLASS-1, CLASS-2, or CLASS-3.
ANALOGUE INPUT events are logged when a change in the input exceeds the DEADBAND associated
with the point. DEADBANDs can be adjusted through the browser.
FROZEN COUNTERS can be assigned to CLASS-1, 2, or 3.
FROZEN COUNTER events are logged and enabled when a running counter is frozen.
BINARY INPUT events are logged and enabled whenever an enabled binary input changes state.

DNP3 Manual
M6xxD/EN M/B
M6xx Page 16
1.9 Health Check
The M6xx meters have several self-tests built in to ensure that the instrument is performing accurately.
The results of these self-tests are available in the Health Check register (AO:00), which is a simple 16-bit
binary value. Each bit represents the results of a particular self-test, with "0" indicating the test was
passed, and "1" indicating the test was failed. If Health status failures occur, the meter may have
experienced an operational failure. The table below provides a reference of error codes. Contact the
factory for further instructions.
A logical OR of the individual health check bits is available as a Binary input, with “0” indicating that all
tests have passed, and “1” indicating that at least one test failed.
Health Check Error Codes
Bit Description
0 Checksum error on analogue output (either 0-1mA or 4-20mA) calibration constants
2 Checksum error on gain calibration of inputs
4 Checksum error on phase calibration of inputs
12 Indicates firmware download in progress and measurements are offline
15 Protocol configuration error
1.10 Heartbeat State Counter
M6xx meters provide a Heartbeat State Counter Register that allows the user to determine the time
between successive polls. This counter will increment by the number of milliseconds that have elapsed
since the last time the data was updated. Another use of this register is as a visual indicator that the data
is changing; it allows users of certain MMIs to identify disruption in the polling of the instrument. The
Heartbeat State Counter is a full 32-bit counter that rolls over at 4,294,967,295 (4,294,967 seconds). The
counter starts at zero on power-up, and is NOT stored in non-volatile memory.
1.11 Meter ID Register
M6xx meters provide a "Meter Type ID" register for model identification purposes (AI:55) which returns a
value of 600 (BiLF12 Modbus, BiLF DNP), 601 (BiLF16 Modbus), or 602 (TUC DNP/Modbus).
1.12 Custom Points Lists
A custom points list can be defined for each DNP session. Select the session from the Session dropdown
box and click the “Edit Points List” button to begin editing the selected session’s points list.

DNP3 Manual
M6xxD/EN M/B
M6xx Page 17
The DNP Points List Configuration summary page is displayed by object. Select the DNP object you
would like to edit from the “DNP Type” dropdown box. The properties of the selected object appear in
separate columns in the summary list.

DNP3 Manual
M6xxD/EN M/B
M6xx Page 18
Click on the “Edit List” button to modify the list.
This manual suits for next models
7
Table of contents
Other Alstom Measuring Instrument manuals
Popular Measuring Instrument manuals by other brands
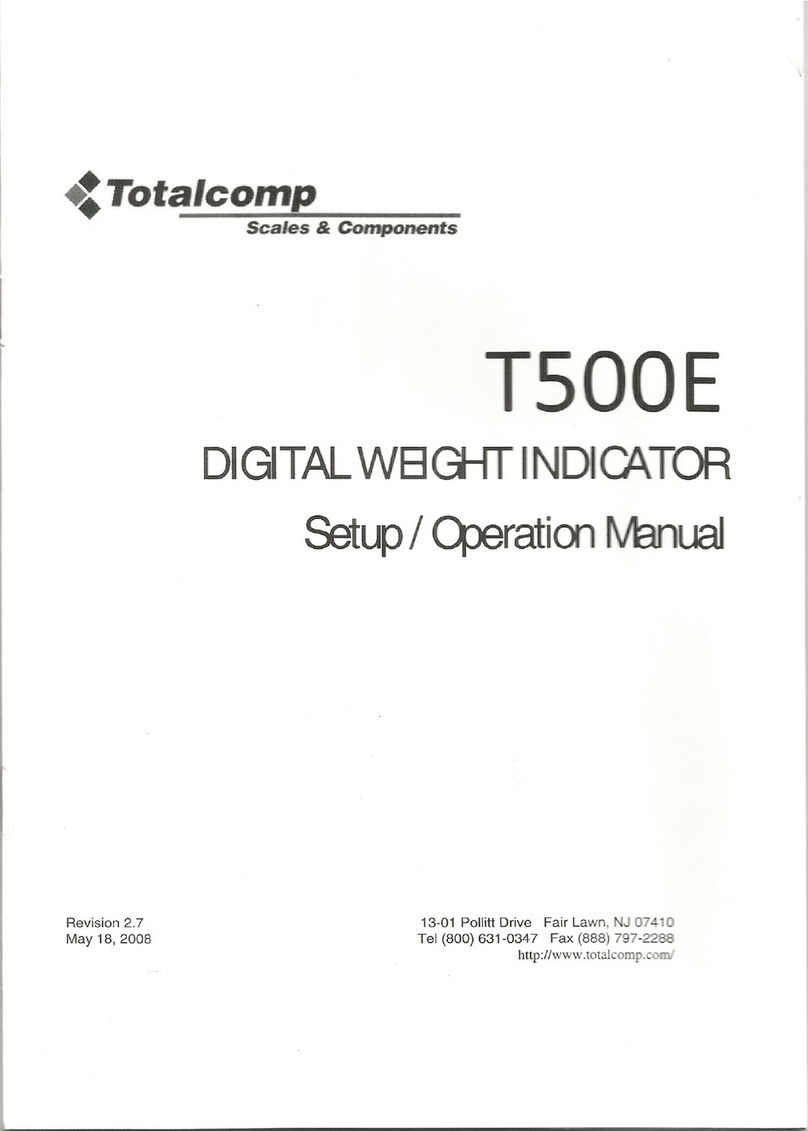
Totalcomp
Totalcomp T500E Setup & operation manual
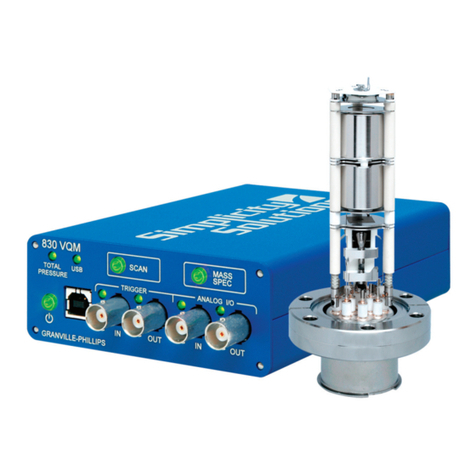
Granville-Phillips
Granville-Phillips 830 VQM quick start guide
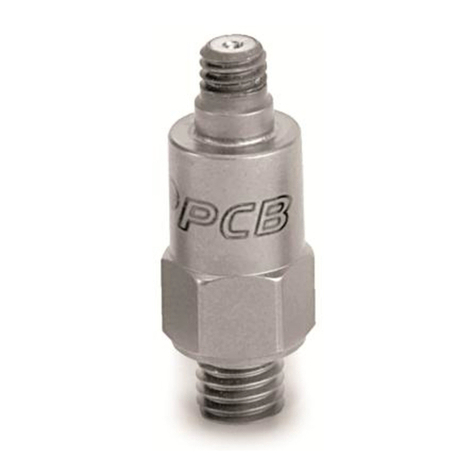
PCB Piezotronics
PCB Piezotronics 352C68 Installation and operating manual
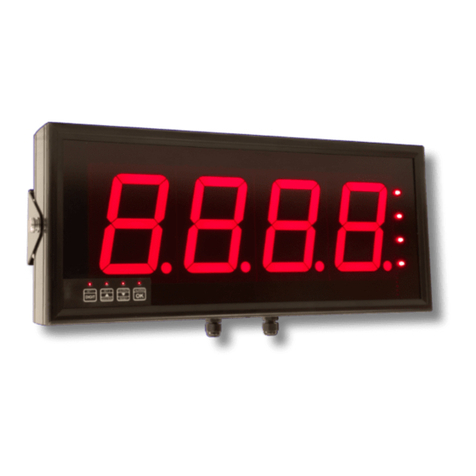
London Electronics
London Electronics Fusion Series Connection details, scaling and general information

Biogents
Biogents BG-Counter 2 troubleshooting guide
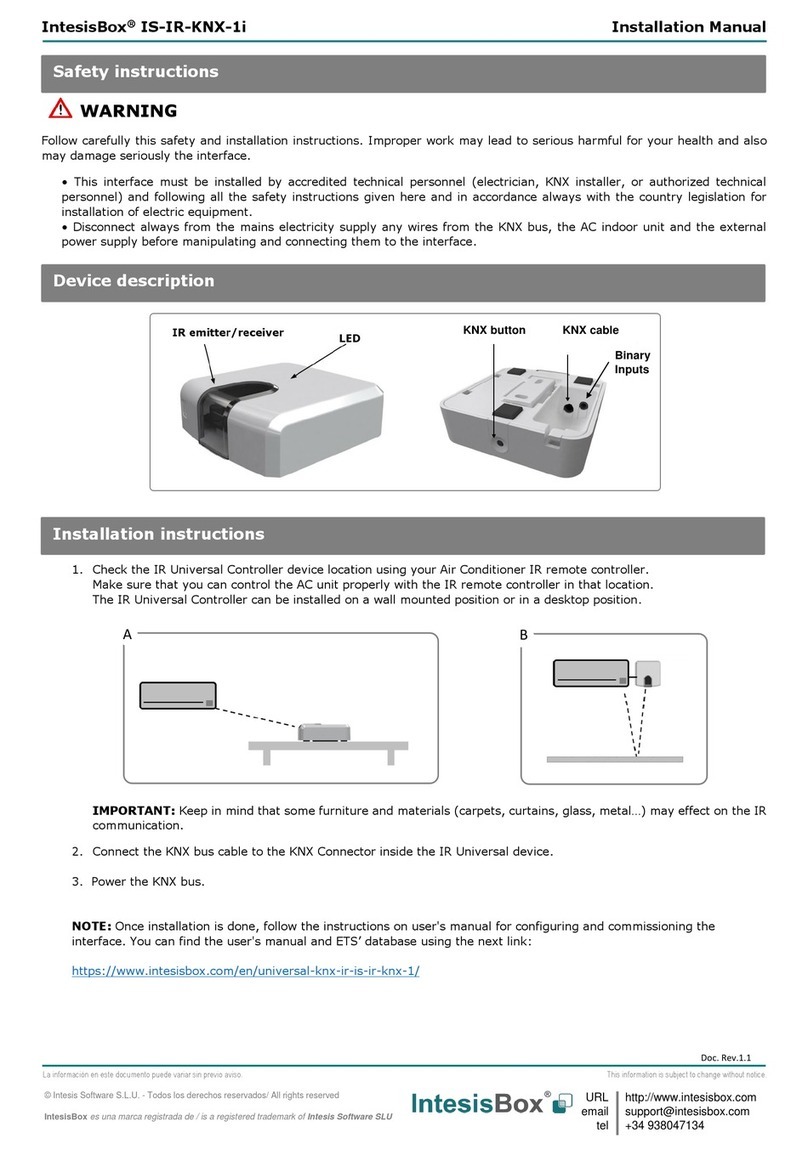
IntesisBox
IntesisBox IS-IR-KNX-1i installation manual