AMCI SD4840EK User manual

M
ICRO CONTROLS INC.
ADVANCED
U
s
e
r
M
a
n
u
a
l
Manual #: 940-0S310

ADVANCED MICRO CONTROLS INC.
GENERAL INFORMATION
Important User Information
The products and application data described in this manual are useful in a wide variety of different applica-
tions. Therefore, the user and others responsible for applying these products described herein are responsible
for determining the acceptability for each application. While efforts have been made to provide accurate infor-
mation within this manual, AMCI assumes no responsibility for the application or the completeness of the
information contained herein.
UNDER NO CIRCUMSTANCES WILL ADVANCED MICRO CONTROLS, INC. BE RESPONSIBLE OR
LIABLE FOR ANY DAMAGES OR LOSSES, INCLUDING INDIRECT OR CONSEQUENTIAL DAM-
AGES OR LOSSES, ARISING FROM THE USE OF ANY INFORMATION CONTAINED WITHIN THIS
MANUAL, OR THE USE OF ANY PRODUCTS OR SERVICES REFERENCED HEREIN.
No patent liability is assumed by AMCI, with respect to use of information, circuits, equipment, or software
described in this manual.
The information contained within this manual is subject to change without notice.
This manual is copyright 2020 by Advanced Micro Controls Inc. Y
ou may reproduce this manual, in whole or
in part, for your personal use, provided that this copyright notice is included. You may distribute copies of this
complete manual in electronic format provided that they are unaltered from the version posted by Advanced
Micro Controls Inc. on our official website: www.amci.com. You may incorporate portions of this documents
in other literature for your own personal use provided that you include the notice “Portions of this document
copyright 2020 by Advanced Micro Controls Inc.” You may not alter the contents of this document or charge a
fee for reproducing or distributing it.
Standard Warranty
ADVANCED MICRO CONTROLS, INC. warrants that all equipment manufactured by it will be free from
defects, under normal use, in materials and workmanship for a period of [18] months. Within this warranty
period, AMCI shall, at its option, repair or replace, free of charge, any equipment covered by this warranty
which is returned, shipping charges prepaid, within eighteen months from date of invoice, and which upon
examination proves to be defective in material or workmanship and not caused by accident, misuse, neglect,
alteration, improper installation or improper testing.
The provisions of the "STANDARD WARRANTY" are the sole obligations of AMCI and excludes all other
warranties expressed or implied. In no event shall AMCI be liable for incidental or consequential damages or
for delay in performance of this warranty.
Returns Policy
All equipment being returned to AMCI for repair or replacement, regardless of warranty status, must have a
Return Merchandise Authorization number issued by AMCI. Call (860) 585-1254 with the model number and
serial number (if applicable) along with a description of the problem during regular business hours, Monday
through Friday, 8AM - 5PM Eastern. An "RMA" number will be issued. Equipment must be shipped to AMCI
with transportation charges prepaid. Title and risk of loss or damage remains with the customer until shipment
is received by AMCI.
24 Hour Technical Support Number
24 Hour technical support is available on this product. If you have internet access, start at www.amci.com.
Product documentation and FAQ’s are available on the site that answer most common questions.
If you require additional technical support, call (860) 583-1254. Your call will be answered by the factory dur-
ing regular business hours, Monday through Friday, 8AM - 5PM Eastern. During non-business hours an auto-
mated system will ask you to enter the telephone number you can be reached at. Please remember to include
your area code. The system will page an engineer on call. Please have your product model number and a
description of the problem ready before you call.
Waste Electrical and Electronic Equipment (WEEE)
At the end of life, this equipment should be collected separately from any unsorted municipal waste.

20 Gear Drive, Plymouth Ind. Park, Terryville, CT 06786
Tel: (860) 585-1254 Fax: (860) 584-1973 http://www.amci.com 3
TABLE OF CONTENTS
General Information
Important User Information .... ................. 2
Standard Warranty ................................... 2
Returns Policy .......................................... 2
24 Hour Technical Support Number ........ 2
WEEE Statement ..................................... 2
About this Manual
Audience . ................................................. 7
Applicable Units ...................................... 7
Navigating this Manual ............................ 7
Manual Conventions ................................ 7
Trademark Notices ................................... 7
Revision Record ....................................... 8
Revision History ............................ 8
Where To Go From Here ......................... 8
Reference: Introduction to the
SD4840EK
The SD4840EK ........................................ 9
Conformance Markings ........................... 10
UL .................................................. 10
CE .................................................. 10
RoHS .. ........................................... 10
Specifications ........................................... 11
Indexer Functionality ............................... 12
Synchronizing Moves .................... 13
Encoder Functionality ... ................ 13
Stall Detection .................... 14
Encoder Registration
Move . ............................... 14
Electronic Gearing ............. 14
Driver Functionality ................................. 15
Idle Current Reduction .................. 15
Current Loop Gain ......................... 15
I/O Connector .......................................... 16
Available Discrete Inputs ......................... 16
Home Input .................................... 16
CW Limit Switch or
CCW Limit Switch ...................... 16
Start Indexer Move Input ............... 16
Emergency Stop Input ................... 16
Stop Jog or
Registration Move Input .............. 17
Capture Encoder Position Input ..... 17
General Purpose Input ................... 17
Available Discrete Output ....................... 17
Reference: Introduction to the
SD4840EK (continued)
Ethernet Ports ........................................... 17
Motor Connector ...................................... 18
Front Panel ............................................... 18
Status LED .................................... 18
EtherCAT Run LED ........... 18
EtherCAT ERR LED .......... 18
Reference: Move Profiles
Definitions ................................................ 19
Units of Measure ........................... 19
Distance .... .......................... 19
Speed ... ............................... 19
Acceleration ........................ 19
Motor Position .............................. 19
Home Position ............................... 19
Count Direction ............................. 19
Starting Speed ............................... 20
Target Position .............................. 20
Relative Coordinates .......... 20
Absolute Coordinates ......... 20
Definition of Acceleration Types ............. 20
What is jerk? ................................. 20
Constant Acceleration ................... 21
S-Curve Accelerations .................. 21
Trapezoidal S-Curve
Acceleration .... ................. 21
Triangular S-Curve
Acceleration .... ................. 22
A Simple Move ........................................ 22
Controlled and Immediate Stops .............. 23
Host Control .................................. 23
Hardware Control ......................... 23
Basic Move Types .................................... 24
Relative Move ............................... 24
Controlled Stops ................. 24
Immediate Stops ................. 24
Absolute Move .............................. 25
Controlled Stops ................. 25
Immediate Stops ................. 25
CW/CCW Jog Move ..................... 26
Controlled Stops ................. 26
Immediate Stops ................. 27
CW/CCW Registration Move ....... 27
Controlled Stops ................. 28
Immediate Stops ................. 28

TABLE OF CONTENTS
SD4840EK User Manual
ADVANCED MICRO CONTROLS INC.
4
Reference: Move Profiles
(continued)
Encoder Registration Moves .................... 29
Controlled Stops ........................... 29
Immediate Stops ........................... 29
Assembled Moves .................................... 29
Blend Move ................................... 30
Controlled Stops ................. 31
Immediate Stops ................. 31
Dwell Move .................................. 31
Controlled Stops ................. 32
Immediate Stops ................. 32
Assembled Move Programming ............... 33
Control Bits – Output Data ........... 33
Control Bits – Input Data .............. 33
Programming Routine ................... 33
Saving an Assembled
Move in Flash ............................. 33
Indexed Moves ......................................... 34
Controlling Moves In Progress ................ 35
Jog Moves ..................................... 35
Registration Moves ....................... 35
Absolute, Relative and
Encoder Registration Moves ....... 35
Assembled Moves ......................... 35
Electronic Gearing .................................... 36
Motor Steps/Turn .......................... 36
ELGearing Multiplier
and Divisor .................................. 36
How It Works ................................ 36
Controlled Stops ........................... 36
Immediate Stops ........................... 36
Advanced Ratio Control ............... 37
Reference: Calculating Move
Profiles
Constant Acceleration Equations ............. 39
Variable Definitions ...................... 39
Total Time Equations .................... 41
S-Curve Acceleration Equations .............. 42
Triangular S-Curve
Acceleration ................................ 42
Trapezoidal S-Curve
Acceleration ................................ 44
Determining Waveforms
by Values .................................... 46
Chapter 4: Homing the SD4840EK
Definition of Home Position .................... 49
Position Preset .......................................... 49
CW/CCW Find Home Commands ........... 49
Homing Inputs .......................................... 49
Physical Inputs .............................. 49
Backplane Inputs ........................... 49
Homing Configurations ............................ 50
Homing Profiles ........................................ 50
Home Input Only Profile ............... 50
Profile with Proximity Input ......... 51
Profile with Overtravel Limit ........ 52
Reference: Configuration Data
Format
CoE Registers ........................................... 53
Output Data Format .................................. 53
CFG_Word_0 Format ............................... 53
CFG_Word_1 Format ............................... 56
Current Loop Gain .................................... 57
Determining Current Loop Gain ... 58
Notes on Other Configuration Words ....... 58
Invalid Configurations .............................. 58
Reference: Command Data Format
Command Bits Must Transition ............... 59
Output Data Format .................................. 59
CMD_word0 ............................................. 60
CMD_word1 ............................................. 62
Command Blocks ..................................... 64
Absolute Move .............................. 64
Relative Move ............................... 64
Hold Move .................................... 65
Resume Move ................................ 65
Immediate Stop ............................. 66
Find Home CW ............................. 66
Find Home CCW ........................... 67
Jog CW .......................................... 67
Registration Move CW ................. 68
Jog CCW ....................................... 68
Registration Move CCW ............... 69
Encoder Follower Move ................ 70
Preset Position ............................... 70
Reset Errors ................................... 71
Run Assembled Move ................... 71
Preset Encoder Position ................. 72

20 Gear Drive, Plymouth Ind. Park, Terryville, CT 06786
Tel: (860) 585-1254 Fax: (860) 584-1973 http://www.amci.com
SD4840EK User Manual
TABLE OF CONTENTS
5
Reference: Command Data Format
Programming Blocks ............................... 73
First Block ..................................... 73
Segment Block ............................... 73
Input Data Format .................................... 74
STATUS_word0 Format ............... 74
STATUS_word1 Format ............... 76
Notes on Clearing a Driver Fault ............. 77
Reset Driver Fault .......................... 77
Task 1: Motor and Power Supply
Sizing
Sizing Your Motor 79
Determining Your Motor
Current Setting ....................................... 79
A Note on Microstepping .............. 79
Torque and Power Curves ........................ 80
Power Supply Sizing ................................ 82
Regeneration Effects ..................... 82
Task 2: Installing the SD4840EK
Safe Handling Guidelines ........................ 83
Prevent Electrostatic Damage ........ 83
Prevent Debris From
Entering the Module .................... 83
Remove Power Before
Servicing ...................................... 83
Mounting .................................................. 83
Dimensions .................................... 83
Minimum Spacing ......................... 84
Mounting the SD4840EK
Module .. ...................................... 84
I/O Connector Pin Out ............................. 85
Power Wiring ........................................... 85
Input Wiring ............................................. 87
Cable Shields ................................. 87
Output Wiring .......................................... 87
Encoder Wiring ........................................ 88
Differential Wiring ........................ 88
Single Ended Wiring ..................... 89
Installing the Stepper Motor .................... 89
Outline Drawings ........................... 89
Mounting the Motor ...................... 90
Connecting the Load ...................... 90
Extending the Motor Cable ........... 90
Installing the Motor Cable ............. 90
Connecting the Motor .............................. 91
Motor Connector ........................... 91
Motor Wiring ................................. 91
Ethernet Connections ............................... 93
Task 3: EtherCAT System
Configuration
Install the ESI file ..................................... 95
Obtain the ESI file ........................ 95
Install the ESI file ......................... 95
Restart the Programming
System If Needed ........................ 95
Add the SD4840EK to the Project ........... 95
Scan for the SD4840EK ................ 95
Rename the Device ....................... 95
Configure the SD4840EK ............. 96
Create a DUT ........................................... 97
Create Variables Based on the DUT ........ 97
Link Variable Names to I/O Words ......... 97
Task 4: Distributed Clock - SYNC0
Setup
Verify Main PLC Task Timing ................ 99
Create New PLC Task .............................. 100
Set Operational Mode .............................. 102
Set CFG_word1 Value to
Enable SYNC0 ....................................... 103

TABLE OF CONTENTS
SD4840EK User Manual
ADVANCED MICRO CONTROLS INC.
6
Notes

20 Gear Drive, Plymouth Ind. Park, Terryville, CT 06786
Tel: (860) 585-1254 Fax: (860) 584-1973 http://www.amci.com 7
ABOUT THIS MANUAL
Audience
This manual explains the set-up, installation, and operation of the SD4840EK Stepper Motor Indexer / Driver
from AMCI. It is written for the engineer responsible for incorporating these modules into a design, as well as
the engineer or technician responsible for its actual installation.
Applicable Units
This manual applies to the SD4840EK Networked Stepper Indexer/Driver with the EtherCAT® network inter-
face.
Navigating this Manual
This manual is designed to be used in both printed and on-line formats. Its on-line form is a PDF document,
which requires Adobe Acrobat Reader version 7.0+ to open it. The manual is laid out with an even number of
pages in each chapter. This makes it easier to print a chapter to a duplex (double sided) printer.
Bookmarks of all the chapter names, section headings, and sub-headings were created in the PDF file to help
navigate it. The bookmarks should have appeared when you opened the file. If they didn’t, press the F5 key
on Windows platforms to bring them up.
The PDF file is password protected to prevent changes to the document. You are allowed to select and copy
sections for use in other documents and you are allowed to add notes and annotations.
Manual Conventions
Three icons are used to highlight important information in the manual:
NOTES highlight important concepts, decisions you must make, or the implications of those
decisions.
CAUTIONS tell you when equipment may be damaged if the procedure is not followed
properly.
WARNINGS tell you when people may be hurt or equipment may be damaged if the pro-
cedure is not followed properly.
The following table shows the text formatting conventions:
Trademark Notices
The AMCI logo is a trademark of Advanced Micro Controls Inc. EtherCAT® is a registered trademark and
patented technology, licensed by Beckhoff Automation GmbH, Germany. “Adobe” and “Acrobat” are regis-
tered trademarks of Adobe Systems Incorporated.
All other trademarks contained herein are the property of their respective holders.
Read this chapter to learn how to navigate through this manual and familiarize
yourself with the conventions used in it.
Format Description
Normal Font Font used throughout this manual.
Emphasis Font Font used the first time a new term is introduced.
Cross Reference When viewing the PDF version of the manual, clicking on
the cross reference text jumps you to referenced section.
HTML Reference When viewing the PDF version of the manual, clicking on
the HTML reference text will open your default web
browser to the referenced web page.

ABOUT THIS MANUAL
SD4840EK User Manual
ADVANCED MICRO CONTROLS INC.
8
Revision Record
This manual, 940-0S310, is the first revision of this manual. It was first released December 14th, 2020.
Revision History
940-0S310 Initial Release.
Where To Go From Here
This manual contains information that is of interest to everyone from engineers to operators. The table below
gives a brief description of each chapter’s contents to help you find the information you need to do your job.
Section Title Page # Section Description
Introduction to the
SD4840EK 9Complete specifications for the SD4840EK product.
Move Profiles 19 Reference information on how the SD4840EK can be used to control
motion in your application.
Calculating Move
Profiles 39 Reference information on calculating detailed move profiles.
Homing the SD4840EK 49 Reference information on how to set the home position of the
SD4840EK.
Configuration Data
Format 53 Reference information on the format of the CANopen over Ether-
CAT (CoE) data that is used to configure the units.
Command Data Format 59 Reference information on the format of the network data to and from
the SD4840EK that is used to command it.
Motor and Power
Supply Sizing 79 Reference information and performance data on compatible AMCI
stepper motors and guidelines for using a foreign stepper motor.
Installing the
SD4840EK 83
Task instructions covering how to install an SMD23K or SMD24K
on a machine. Includes information on mounting, grounding, and
wiring specific to the units.
EtherCAT System
Configuration 95 Task instructions that covers how to add an SD4840EK to an
EtherCAT network.
Distributed Clock -
SYNC0 Setup 99 Task instructions that covers the optional task of using the Distrib-
uted Clock functionality of the EtherCAT protocol with the
SD4840EK.

20 Gear Drive, Plymouth Ind. Park, Terryville, CT 06786
Tel: (860) 585-1254 Fax: (860) 584-1973 http://www.amci.com 9
REFERENCE 1
INTRODUCTION TO THE SD4840EK
The SD4840EK
The AMCI SD4840EK is a DC powered, 4.0 Arms, micro-stepping driver with an internal bus voltage equal to
the supply voltage. The drive’s built-in indexer accepts configuration and command data from a host system.
The SD4840EK driver attaches to your Ethernet based network and communicates using the EtherCAT proto-
col.
EtherCAT uses standard Ethernet cabling, but forgoes the full TCP/IP stack typically associated with Ethernet
communications. The EtherCAT protocol transfers data to and from multiple slaves with a single packet of
information. Data for each slave is located at a known position within the packet. EtherCAT slave devices use
a hardware only solution to read and write data to the packet before transmitting the packet to the next slave.
This solution leads to a delay between nodes that is typically 4 microseconds or less. This results in a very fast
and deterministic network.
An EtherCAT Slave Information (ESI) file is available for the SD4840EK. The ESI file is required to add the
device to the network. Configuration of the SD4840EK is accomplished using the CANopen PDO and SDO
objects. EtherCAT supports CANopen through its CANopen over Ethernet (CoE) interface.
Motion commands and status information is transmitted using the output and input variables assigned to the
SD4840EK when the EtherCAT system is configured.
Each unit also supports the Distributed Clock (DC) functionality of the EtherCAT system. This allows you to
synchronize the start of moves across devices using the SYNC0 signal instead of the SyncManager 2 event.
The combination of host and driver gives you several advantages:
Sophisticated I/O processing can be performed in the host (PLC or other controller) before sending
commands to the Networked Indexer/Driver.
All motion logic is programmed in the host, eliminating the need to learn a separate motion control lan-
guage
Eliminating the separate indexer lowers Total System Cost
The SD4840EK is powered by a nominal 24 to 48 Vdc power source, and can accept surge voltages of up to
60Vdc without damage. The output motor current is fully programmable from 0.1 Arms to 4.0 Arms which
makes the SD4840EK compatible with the complete line of size 23 and size 34 stepper motors that are avail-
able from AMCI. In addition to the Motor Current setting, the Motor Steps per Turn, Idle Current Reduction,
and Anti-Resonance Circuit features are also fully programmable. If you have used other stepper indexer
products from AMCI you will find programming to be very similar to these products.
This manual is designed to get you quickly up and running with the SD4840EK
stepper indexer / driver. As such, it assumes you have some basic knowledge of
stepper systems. If stepper systems are new to you, we’re here to help. AMCI has
a great deal of information on our website and we are adding more all the time. If
you can’t find what you’re looking for at http:///www.amci.com, send us an e-mail
or call us. We’re here to support you with all of our knowledge and experience.

INTRODUCTION TO THE SD4840EK
SD4840EK User Manual
ADVANCED MICRO CONTROLS INC.
10
The SD4840EK (continued)
The SD4840EK is a true RMS motor current control driver. This means that you will always receive the
motor’s rated torque regardless of the Motor Steps/Turn setting. (Drivers that control the peak current to the
motor experience a 30% decrease in motor torque when microstepping a motor.) The SD4840EK automati-
cally switches from RMS to peak current control when the motor is idle to prevent overheating the motor.
In addition to power and motor hookups, the SD4840EK has three DC inputs and one DC output that are used
by the indexer. Configuration data from the host sets the function of these points. The output can be config-
ured to be a Fault Output or a general purpose output. Inputs accept 5 to 24 Vdc signals and they can be indi-
vidually configured as a:
CW or CCW Limit Switch
Home Limit Switch
Capture Encoder Position Input
Stop Jog or Registration Move Input
Start Indexer Move
Emergency Stop Input
General Purpose Input
Conformance Markings
The SD4840EK meets the requirements for the following conformance markings when installed and operated
in accordance with the instructions contained in their product documentation.
UL
Recognized component in the USA and Canada. UL file number is E231137.
US: UL 61800-5-1 Standard For Safety For Adjustable Speed Electrical Power Drive Systems - Part
5-1: Safety Requirements - Electrical, Thermal and Energy
Canada: CSA C22.2 No. 274 - Adjustable Speed Drives
CE
Directive 2014/30/EU of the European Parliament and of the Council (EMC), of 26 February 2014 on
the harmonisation of the laws of the Member States relating to electromagnetic compatibility; per EN
61800-3:2004/A1:2012.
Directive 2014/35/EU of the European Parliament and of the Council (Low Voltage), of 26 February
2014 on the harmonisation of the laws of the Member States relating to the making available on the
market of electrical equipment designed for use within certain voltage limits; per EN 61010-1:2010.
RoHS
Directive (EU) 2015/863 (RoHS 3) and Directive 2011/65/EU (RoHS 2)

20 Gear Drive, Plymouth Ind. Park, Terryville, CT 06786
Tel: (860) 585-1254 Fax: (860) 584-1973 http://www.amci.com
SD4840EK User Manual
INTRODUCTION TO THE SD4840EK
11
Specifications
Driver Type
Two bipolar MOSFET H-bridges with 20KHz
PWM current control.
Physical Dimensions
Width: 0.9 inches max.
Depth: 4.5 inches max.
Height: 3.9 inches
5.0 inches min. with mating connectors
Weight
0.38 lb. (0.17 kg) with mating connectors
Inputs
Electrical Characteristics: . . . . . . . . . . . . . . .
Differential. 560 Vac/dc opto-isolated. Can be
wired as single ended inputs.
DC Inputs accept 3.5 to 27 Vdc without the need
for an external current limiting resistor.
Encoder Inputs are designed for 5 Vdc differen-
tial (Operational range of 3 to 6 Vdc.) An exter-
nal current limiting resistor is required for 12 to
24 Vdc operation.
Output
Electrical Characteristics:
Open Collector/Emitter. 560 Vac/dc
opto-isolated. 30 Vdc, 20 mA max.
The Output can be programmed to be a general
purpose output or a Fault Output.
The Fault Output is normally on. Turns off under
the following conditions:
Reset ................. The driver initialization is not
yet complete on power up.
Short Circuit ..... Motor Phase to Phase or Phase
to Case
Over Temp ........ Heat Sink temperature exceeds
90° C (195° F)
Faults are reported in the Network Input Data and
can be cleared through the Network Output
Data.
Motor Current
Programmable from 0.1 to 4.0 Arms in 0.1 Amp
steps.
+Vdc Auxiliary Current
70 mA @ 24 Vdc, 40 mA @ 48 Vdc
Motor Resolution
Programmable to any value from 200 to 32,767
steps per revolution.
Idle Current Reduction
Programmable from 0% to 100% programmed
motor current in 1% increments. Motor current
is reduced to selected level if there is no motion
for 1.5 seconds. Current is restored to full value
when motion is started.
Internal Power Fuse
7 Amp Fast Blow. Fuse is not user replaceable.
Environmental Specifications
Input Power ....... 24 to 48 Vdc, surge to 60 Vdc
without damage to module.
Ambient Operating Temperature
............ -4° to 122° F (-20° to 50° C)
Storage Temperature
............ -40° to 185° F (-40° to 85° C)
Humidity ............ 0 to 95%, non-condensing
Motor Specifications
Type .............. 2 phase hybrid. 4, 6, or 8 lead motor
Inductance .... 0.3 mH minimum. 2.5 to 45 mH
recommended
Status LED’s
See Front Panel on page 18 for a complete
description.
Connectors
Mating connectors are supplied with the module
and are also available separately under the fol-
lowing AMCI part numbers.
.
Connector AMCI Part # Wire Strip Length Min. Tightening Torque
I/O MS-2x11 28 - 16 AWG 0.275 inches Spring Cage Connector
Motor MS-4M 28 - 12 AWG 0.394 inches 4.43lb-in (0.5 Nm)

INTRODUCTION TO THE SD4840EK
SD4840EK User Manual
ADVANCED MICRO CONTROLS INC.
12
Indexer Functionality
The table below lists the functionality offered by the indexer built into the SD4840EK.
Table R1.1 Indexer Functionality
Feature Description
Programmable Inputs
Each of the three inputs can be programmed as a Home Limit, Over Travel
Limit, Capture Input, Stop Jog or Registration Move, E-Stop Input, or a
General Purpose Input.
Programmable Output The single output on the SD4840EK can be programmed as a Fault Output
or as a general purpose DC output point.
Encoder Inputs Allows the SD4840EK to used a quadrature encoder for position verifica-
tion, stall detection, or Electronic Gearing.
Programmable Parameters Starting Speed, Running Speed, Acceleration, Deceleration, Distance to
Move, and Accel/Decel Types are fully programmable.
Homing Allows you to set the machine to a known position. The SD4840EK can
home to a discrete input or to an encoder marker pulse.
Synchronous Moves
Using the Distributed Clock functionality of the EtherCAT system, multiple
devices can synchronize the start of their moves to the SYNC0 signal. Moves
will begin within ±25 microseconds of each other.
Jog Move Allows you to jog the motor in either direction based on an input bit from
your host controller.
Relative Move Allows you to drive the motor a specific number of steps in either direction
from the current location.
Absolute Move Allows you to drive the motor from one known location to another known
location.
Registration Move Allows you to jog the motor in either direction based on an input bit from
your host controller. When a controlled stop is received, the move will out-
put a programmable number of steps before coming to a stop.
Blend Move Allows you to perform a sequence of relative moves without stopping
between them.
Dwell Move
Allows you to perform a sequence of relative moves with a stop between
each move that has a programmable length of time. Used to create highly
accurate move profiles that avoid network latency issues.
Indexer Move Allows you to program a move that does not start until one of the program-
mable inputs makes a transition.
Hold Move Allows you to suspend a move and restart it without losing your position
value.
Resume Move Allows you to restart a previously held move operation.
Immediate Stop Allows you to immediately stop all motion if an error condition is detected
by your host controller.

20 Gear Drive, Plymouth Ind. Park, Terryville, CT 06786
Tel: (860) 585-1254 Fax: (860) 584-1973 http://www.amci.com
SD4840EK User Manual
INTRODUCTION TO THE SD4840EK
13
Indexer Functionality (continued)
Synchronizing Moves
By default, the SD4840EK uses the SyncManager 2 event to control the transfer of data from the EtherCAT
Slave Controller (ECS) to the microprocessor that controls motion. This allows the SD4840EK to execute
commands as soon as new data arrives. When more than one axis is updated with a single EtherCAT packet,
the time difference between axis updates is very short. Updating multiple axes with a single packet allows the
EtherCAT network to out perform the update times of other industrial network protocols.
On very fast machines, or large machines that require more than one transfer to update all axes, the EtherCAT
Distributed Clock (DC) functionality can be used to closely synchronize motion over multiple axes if using
the SyncMaster2 event proves to be ineffective.
The EtherCAT Distributed Clock functionality is built into the ECS used by the
SD4840EK
product. The
SD4840EK
can act as the reference clock for the system if it is the first device in the EtherCAT network. The
SYNC0 signal, which is based off of the Distributed Clock, can be use to synchronize the start of moves over
multiple devices. The time between when the SYNC0 signal is received by the main processor of the
SD4840EK
and when the driver begins to cause motion is 520 ± 25 microseconds. The 520 microseconds is
the time required to read the data from the ECS once the SYNC0 signal becomes active. The ±25 microsec-
onds is caused by the 20 kHz update frequency of the PWM drivers.
For the
SD4840EK
, the minimum update time on the SYNC0 signal is two milliseconds. If the task time is
less than two milliseconds, the SYNC0 time must be a multiple of the task time.
Encoder Functionality
In addition to the discrete I/O points, the SD4840EK has three inputs for a 5Vdc differential quadrature
encoder. The inputs will also accept 12 to 24Vdc single ended encoder inputs with current limiting resistors.
These signals are always decoded using X4 decoding. When the incremental encoder is used, the indexer sec-
tion of the SD4840EK has the following additional functionality.
Table R1.2 Indexer Encoder Functionality
Feature Description
Position Verification
When mounted on the motor that is controlled by the SD4840EK, the
encoder can be used to verify motor position motion when a move command
is issued. The encoder position value can be preset to any value and it cam
be captured during a move.
Home to Z pulse
The Z pulse of the encoder can be used to home the machine. In this mode,
any discrete input that is configured as a home input will act as a home prox-
imity sensor.
Stall Detection
The encoder can be used to verify motion when a move command is issued.
An error is issued if the difference in motor and encoder positions is greater
that forty-five degrees.
Encoder Registration
Move
Uses the count from a quadrature encoder to determine when a move begins
to decelerate and stop. Commonly used in spooling/despooling applications.
Electronic Gearing The SD4840EK can be configured to control the position of a motor based
on feedback from an external encoder. The ratio of encoder pulses to motor
pulses is full programmable and can be changed on-the-fly.

INTRODUCTION TO THE SD4840EK
SD4840EK User Manual
ADVANCED MICRO CONTROLS INC.
14
Indexer Functionality (continued)
Encoder Functionality (continued)
Stall Detection
When Stall Detection is enabled, the SD4840EK monitors the encoder for position changes, regardless of
whether or not a move is in progress. If the error between the encoder position and the motor position exceeds
forty-five degrees, the SD4840EK responds in the following manner:
The stall is reported in the network input data.
The motor position becomes invalid. (The machine must be homed or the motor position preset before
Absolute moves can be run again.
If a move was in progress, the move is stopped.
Note that a move does not have to be in progress for stall detection to be useful. By enabling stall detection,
the SD4840EK can notify the system if the motor shaft moves more than forty-five degrees while the motor
should be holding the load. For example, if the motor should hold a load against gravity, but the Idle Current
Reduction parameter is set to high, the SD4840EK will issue a stall detection error if the load begins to fall.
Encoder Registration Move
The encoder position acts as a registration mark in an Encoder Registration Move. Typically, the encoder is
mounted separately from the motor. With this mode, the SD4840EK will drive the motor until the desired
encoder count is reached, at which time the motor begins to decelerate and stop. This functionality is useful in
spool winding or unwinding applications, where the motor drives the spool and the encoder measures the
material length as it enters or exits the spool. As the spool diameter increases or decreases, the programmed
distance remains the same because you are measuring material, not the number of turns.
Electronic Gearing
In this mode, the stepper motor follows the rotation of an external encoder. This encoder is typically attached
to another motor. The ratio of encoder pulses to stepper pulses is programmable over a wide range. This mode
electronically couples the two motors together through a programmable gear ratio.

20 Gear Drive, Plymouth Ind. Park, Terryville, CT 06786
Tel: (860) 585-1254 Fax: (860) 584-1973 http://www.amci.com
SD4840EK User Manual
INTRODUCTION TO THE SD4840EK
15
Driver Functionality
This table summarizes the features of the stepper motor driver portion of the SD4840EK.
Table R1.3 Driver Functionality
Idle Current Reduction
Idle Current Reduction allows you to prolong the life of your motor by reducing its idling temperature. Values
for this parameter range from 0% (no holding torque when idle) to 100%.
Idle current reduction should be used whenever possible. By reducing the current, you are reducing the I2R
losses in the motor. Therefore, the temperature drop in the motor is exponential, not linear. This means that
even a small reduction in the idle current can have a large effect on the temperature of the motor.
Note that the reduction values are “to” values, not “by” values. Setting a motor current to
4 Arms and the current reduction to 25% will result in an idle current of 1Apk. (The
SD4840EK always switch from RMS to peak current control when the motor is idle.)
Current Loop Gain
This feature gives you the ability to adjust the gain of the power amplifiers in the SD4840EK to match the
electrical characteristics of your motor. The value of this parameter can range from 1 to 80 with 80 represent-
ing the largest gain increase. In general, using a larger gain will increase high speed torque but the motor will
run louder. A lower gain will offer quieter low speed operation at the cost of some high speed torque.
The use of this feature is completely optional and you can leave the Current Loop Gain at its default setting of
“1” for standard motor performance.
For AMCI motors, use a value of “5” as a starting point.
High induction motors, often referred to as “tin can” steppers, need a higher Current Loop
Gain setting for normal operation. For these motors, start with a Current Loop Gain of “20”.
Feature Benefits
RMS Current Control
RMS current control give the SD4840EK the ability to drive the motor at its
fully rated power when microstepping. Peak current controllers typically
experience a 30% drop in power when microstepping a motor.
Programmable
Motor Current
RMS current supplied to the motor can be programmed from 0.1 to 4.0 amps
in 0.1 amp increments. This allows you to use the driver with the full line of
AMCI stepper motors.
Programmable Idle
Current Reduction
Extends motor life by reducing the motor current when not running. This
extends the life of the motor by reducing its operating temperature.
Programmable
Current Loop Gain
Allows you to tailor the driver circuitry to the motor’s impedance, thereby
maximizing your motor’s performance.
Programmable
Motor Steps/Turn
Allows you to scale your motor count to a real world value. (counts per inch,
counts per degree, etc.)
Anti-Resonance Circuitry
This circuitry gives the SD4840EK the ability to modify motor current
waveforms to compensate for mechanical resonance in your system. This
will give you smooth performance over the entire speed range of the motor.
Wiring Short Detection Safety feature that removes power from the motor if a short is detected in
one of its windings.
Over Temperature
Detection
The SD4840EK sets a warning bit in the network data when the temperature
of the module approaches its safe operating threshold.
Over Temperature
Protection
Protects the SD4840EK from damage by removing power from the motor if
the internal temperature of the driver exceed a safe operating threshold.

INTRODUCTION TO THE SD4840EK
SD4840EK User Manual
ADVANCED MICRO CONTROLS INC.
16
I/O Connector
As shown in figure R1.1, the I/O connector is located on the top of the
module. All digital I/O connections are made at this connector as well
as the power supply connections. The mating connector is supplied
with the SD4840EK and is also available from AMCI under the part
number MS-2X11. It is also available from Phoenix Contact under
their part number 173 88 98.
Available Discrete Inputs
The SD4840EK has three discrete DC inputs that accept 3.5 to 27 Vdc
signals. (5 to 24 Vdc nominal) They can be wired as differential, sink-
ing, or sourcing inputs. How the SD4840EK uses these inputs is fully
programmable as is their active states. (Inputs can be programmed as
Normally Open (NO) or Normally Closed (NC) inputs.)
Home Input
Many applications require that the machine be brought to a known
position before normal operation can begin. This is commonly called
“homing” the machine or bringing the machine to its “home” position.
The SD4840EK allows you to define this starting position in three
ways. The first is with a Position Preset Command. The second is with
a sensor mounted on the machine. When you define one of the inputs
as the Home Input, you can issue commands to the SD4840EK that
will cause the unit to seek this sensor. The third option is homing to
the Z pulse of a quadrature encoder. When using the Z pulse, you can
use one of the inputs or a network data bit as a home proximity sensor.
How the SD4840EK actually finds the Home sensor is described in
chapter 4, Homing the SD4840EK, starting on page 49.
CW Limit Switch or CCW Limit Switch
Each input can be defined as a CW or CCW Limit Switch. When configured this way, the inputs are used to
define the limits of mechanical travel. For example, if you are moving in a clockwise direction and the CW
Limit Switch activates, all motion will immediately stop. At this point, you will only be able to move in the
counter-clockwise direction.
Start Indexer Move Input
Indexer Moves are programmed through the Network Data like every other move. The only difference is that
Indexer Moves are not run until an input that is configured as a Start Indexer Move Input makes an inactive-
to-active state transition. This allows the SD4840EK to run critically timed moves that cannot be reliably
started from the network due to data transfer lags.
If the quadrature encoder is enabled and one of the discrete DC inputs is programmed as a Start Indexer Move
Input, then the quadrature encoder position data will be captured whenever the DC input makes a transition.
An inactive-to-active state transition on the DC input will also trigger an Indexer Move if one is pending.
Emergency Stop Input
When an input is defined as an Emergency Stop, or E-Stop Input, motion will immediately stop when this
input becomes active. The driver remains enabled and power is supplied to the motor. No move can begin
while this input is active.
Figure R1.1 I/O Connector
+Vdc Main
+VdcAuxiliary
GND
– Output 1
+ Output 1
– Input 3
+ Input 3
– Input 2
+ Input 2
– Input 1
+ Input 1
+Vdc Main
+Vdc Auxiliary
GND
No Connection
– Z Encoder
+ Z Encoder
– B Encoder
+ B Encoder
– A Encoder
+A Encoder
No Connection

20 Gear Drive, Plymouth Ind. Park, Terryville, CT 06786
Tel: (860) 585-1254 Fax: (860) 584-1973 http://www.amci.com
SD4840EK User Manual
INTRODUCTION TO THE SD4840EK
17
Available Discrete Inputs (continued)
Stop Jog or Registration Move Input
When an input is configured as a Stop Jog or Registration Move Input, triggering this input during a Jog
Move or Registration Move will bring the move to a controlled stop. The controlled stop is triggered on an
inactive-to-active state change on the input. Only Jog Moves and Registration Moves can be stopped this
way, all other moves ignore this input.
If the quadrature encoder is enabled, the quadrature encoder position data will be captured when the DC input
makes an inactive-to-active transition if it is configured as a Stop Jog or Registration Move Input. The
encoder position data is not captured if a Jog or Registration Move is not in progress. If you want to capture
encoder position data on every transition of a DC input, configure it as a Start Indexer Move Input.
Capture Encoder Position Input
As described in the Start Indexer Move Input and Stop Jog or Registration Move Input sections above, the
SD4840EK can be configured to capture the encoder position value on a transition of a discrete DC input.
General Purpose Input
If your application does not require all three inputs, you can configure the unused inputs as General Purpose
Inputs. The inputs are not used by the SD4840EK, but the input state is reported in the network data.
Available Discrete Output
The SD4840EK has a single DC output that has a maximum rating of 30 Vdc at 20 mA. The output can be
configured to be a general purpose output or a Fault Output. When configured as a Fault Output, the output
will conduct under normal conditions and will switch off when a fault occurs. The following faults affect the
Fault Output:
Reset ............... The driver initialization is not yet complete on power up.
Short Circuit ... Motor Phase to Phase or Phase to Earth Ground
Over Temp ..... Heat Sink temperature exceeds 90° C (195° F)
Faults are reported in the Network Input Data and can be cleared through the Network Output Data.
Ethernet Ports
The Ethernet Interface on the SD4840EK driver has two standard RJ-45 jacks that accept any standard
100Base-TX cable. Both ports are also auto MDI-X capable. This means that a standard cable can be used
when connecting the Ethernet Driver to any device. Crossover cables are never needed.
Figure R1.2 Location of Ethernet Ports and Motor Connector
The “IN” network jack in the diagram above must be attached to the upstream device in the EtherCAT net-
work. (Closer to the network master.) The “OUT” jack must be attached to the next (downstream) device in
the network of the Networked Driver is not the last device in the network.
There are two LED’s on each of the RJ-45 jacks. The amber LED is not used. The green LED shows the link
status of the Ethernet connection. They are on when there is a physical connection between the SD4840EK
and the previous or next device in the network. They blink when data is being transmitted over the network.
Stepper Motor Connector
IN Ethernet Port
OUT Ethernet Port
SD4840EK Bottom View
B–
A–
B+
A+

INTRODUCTION TO THE SD4840EK
SD4840EK User Manual
ADVANCED MICRO CONTROLS INC.
18
Motor Connector
Figure R1.2 also shows the location of the Stepper Motor Connector. The mate to this connector is included
with the SD4840EK and is also available from AMCI under the part number MS-4M. It is also available from
Phoenix Contact under their part number 187 80 37.
Front Panel
The front panel of the SD4840EK contains the drive status LED as well as
the two EtherCAT status LED’s.
Status LED
The Status LED is a bi-color red/green LED shows the general status of the
module.
Steady Green: Module OK
Steady Red: An Overtemperature Fault or Motor Short Circuit Fault
exists. Note that the SD4840EK will only detect short
circuit faults when the motor current is enabled.
Blinking Green: Successful write to flash memory. Power must be
cycled to the module before additional commands
can be written to it.
Blinking Red: Failed write to flash memory. You must cycle power
to the module to clear this fault.
Alternating Red/Green:
There is a communications error between the
main processor and the Ethernet co-proces-
sor within the drive. You must cycle power
to the module to attempt to clear this fault.
EtherCAT Run LED
The green RUN LED indicates the logical state of the device.
Table R1.4 Module RUN LED States
EtherCAT ERR LED
The red ERR LED indicates an error state in the EtherCAT protocol.
Table R1.5 Red ERR LED States
LED State Description
Off Device in the EtherCAT Init state
Fast Blink (4 Hz) Device in the EtherCAT Pre-Operational (Pre-Op) state
Slow Blink (1 Hz) Device in the EtherCAT Safe-Operational (Safe-Op) state
Steady Green Device in the EtherCAT Operational (Op) state.
Red LED State Description
Off No errors in device operation
Single blink
200 ms ON / 1 s OFF Problems with synchronization such as with the Distrib-
uted Clock (DC) PLL.
Double Blink
200 ms Pulses / 1 s between
SYNC manager watchdog timeout. The master has not
updated the output data in the configured time interval. The
Networked Driver has switched to the Safe-OP state.
Slow Blink
(1 Hz)
All other issues, such as cable disconnect. The Networked
Driver has switched to the Safe-OP state.
Figure R1.3 SD4840EK Front Panel
STATUS
RUN ERR
M
OTION
SD4840
STEPPER
DRIVER

20 Gear Drive, Plymouth Ind. Park, Terryville, CT 06786
Tel: (860) 585-1254 Fax: (860) 584-1973 http://www.amci.com 19
REFERENCE 2
MOVE PROFILES
Definitions
Units of Measure
Distance
Every distance is measured in steps. When you configure the unit, you will specify the number of steps you
want to complete one rotation of the motor shaft. It is up to you to determine how many steps are required to
travel the appropriate distance in your application.
Speed
All speeds are measured in steps/second. Since the number of steps needed to complete one shaft rotation is
determined by your programming, it is up to you to determine how many steps per second is required to rotate
the motor shaft at your desired speed.
Acceleration
The typical unit of measure for acceleration and deceleration is steps/second/second, or steps/second2. How-
ever, when programming an SD4840EK, all acceleration and deceleration values must be programmed in the
unit of measure of steps/second/millisecond.
To convert from steps/second2 to steps/second/millisecond, divide the value by 1000. This must be done
when converting from a value used in the equations to a value programmed into the unit.
To convert from steps/second/millisecond to steps/second2, multiply the value by 1000. This must be
done when converting from the value programmed into a unit to the value used in the equations.
Motor Position
Motor Position is defined in counts, and its limits are based on the data format you choose when configuring
the unit. The default multi-word format limits the Motor Position range from -32,768,000 to +32,767,999. If
you choose the thirty-two bit double integer format, the range is -2,147,483,648 to +2,147,483,647. In contin-
uous rotation applications, you should choose the double integer format.
Home Position
The Home Position is any position on your machine that you can sense and stop at. There are two ways to
defining the Home Position. The first is using the Preset Position command to set the Motor Position register
to a known value. The second method is using one of the Find Home commands. If you use the unit’s Find
Home commands, the motor position and encoder position registers will automatically be set to zero once the
home position is reached. Defining a Home Position is completely optional. Some applications, such as those
that use the SD4840EK for speed control, don’t require position data at all.
Count Direction
Relative moves with a positive offset will increase the motor position register reported back to the host. Some
of the moves, such as the Jog Move, have a positive and negative command. A positive command, such as the
CW Jog Move command, will result in an increase in the motor position value. If the motor is wired as shown
in this manual, these moves will result in clockwise rotation when looking at the motor shaft.
When a move command is sent to the SD4840EK, the module calculates the entire
profile before starting the move or issuing an error message. This chapter
explains how the profiles are calculated and the different available moves.

MOVE PROFILES
SD4840EK User Manual
ADVANCED MICRO CONTROLS INC.
20
Definitions (continued)
Starting Speed
The Starting Speed is the speed that most moves will begin and end at. This value is set while configuring the
unit and it has a valid range of 1 to 1,999,999 steps/second. This value is typically used to start the move
above the motor’s low frequency resonances and, in micro-stepping applications, to limit the amount of time
needed for acceleration and deceleration. AMCI does not specify a default value in this manual because it is
very dependent on motor size and attached load. With that said, a starting speed between 0.25 and 0.5 RPS is
usually a good starting point.
Target Position
The Target Position is the position that you want the move to end at. There are two ways to define the Target
Position, with relative coordinates or absolute coordinates.
Relative Coordinates
Relative coordinates define the Target Position as an offset from the present position of the motor. Most
SD4840EK moves use relative coordinates.
The range of values for the Target Position when it is treated as an offset is ±8,388,607 counts. Assum-
ing that the motor is wired to the SD4840EK as shown in this manual, positive offsets will result in
clockwise moves, while negative offsets result in counter-clockwise moves.
The Motor Position value reported back to the host can exceed ±8,388,607 counts. The only way to
move beyond ±8,388,607 counts is with multiple relative moves or jog commands.
Absolute Coordinates
Absolute coordinates treat the Target Position as an actual position on the machine. Note that you must set the
Home Position on the machine before you can run an Absolute Move. (See Home Position on the previous
page.)
The range of values for the Target Position when it is treated as an actual position on the machine is
±8,388,607 counts. The move will be positive if the Target Position is greater than the Current Position
and negative if the Target Position is less than the Current Position.
The Motor Position value reported back to the host can exceed ±8,388,607 counts. However, you can-
not move beyond ±8,388,607 counts with an Absolute Move. The only way to move beyond
±8,388,607 counts is with multiple relative moves or jog commands.
Definition of Acceleration Types
Most of the move commands allow you to define the acceleration type used during the move. The SD4840EK
supports three types of accelerations and decelerations. The type of acceleration used is controlled by the
Acceleration Jerk parameter.
What is jerk?
Just as speed is a measurement of change in position per unit time and acceleration is a measurement of
change in speed per unit time, jerk is a measurement of change in acceleration per unit time. Likewise, just as
a change in position equals speed * time, p = s(t), and a change in speed equals acceleration * time, s =
a(t), a change in acceleration equals jerk * time, a=j(t). Jerk has units of steps/sec3.
The SD4840EK uses the jerk property to smoothly change the acceleration applied during the move. In this
case, the speed of the move does not increase linearly, but exponentially, resulting in an “S” shaped curve.
This limits mechanical shocks to the system as the load accelerates.
Table of contents
Popular Control System manuals by other brands
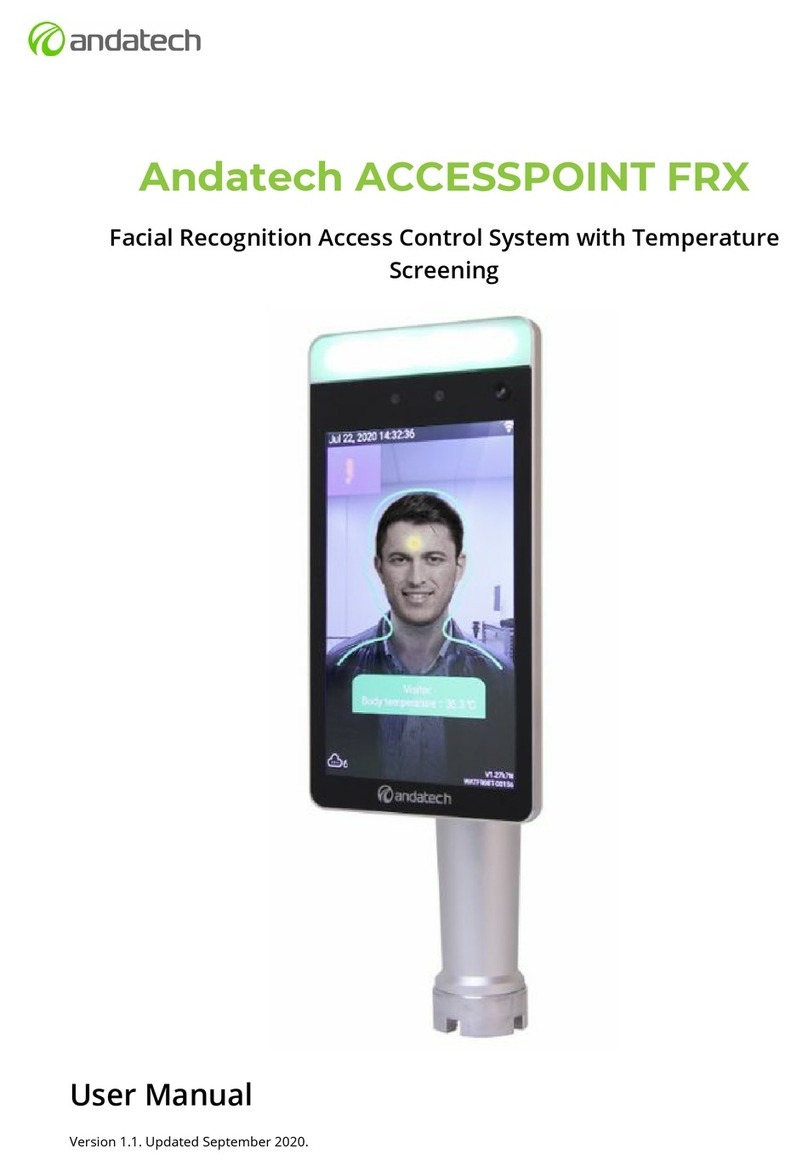
Andatech
Andatech ACCESSPOINT FRX user manual
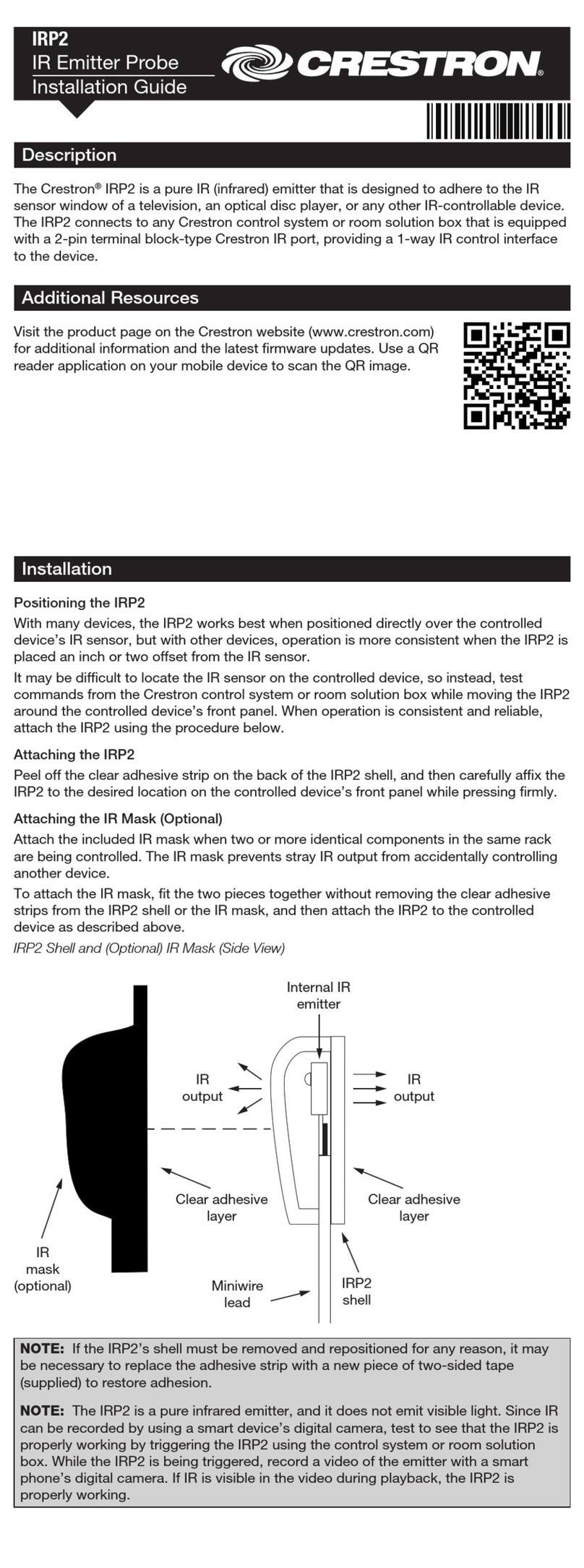
Crestron
Crestron IRP2 installation guide

Ferport
Ferport CB 8221 L Operating and installation instructions
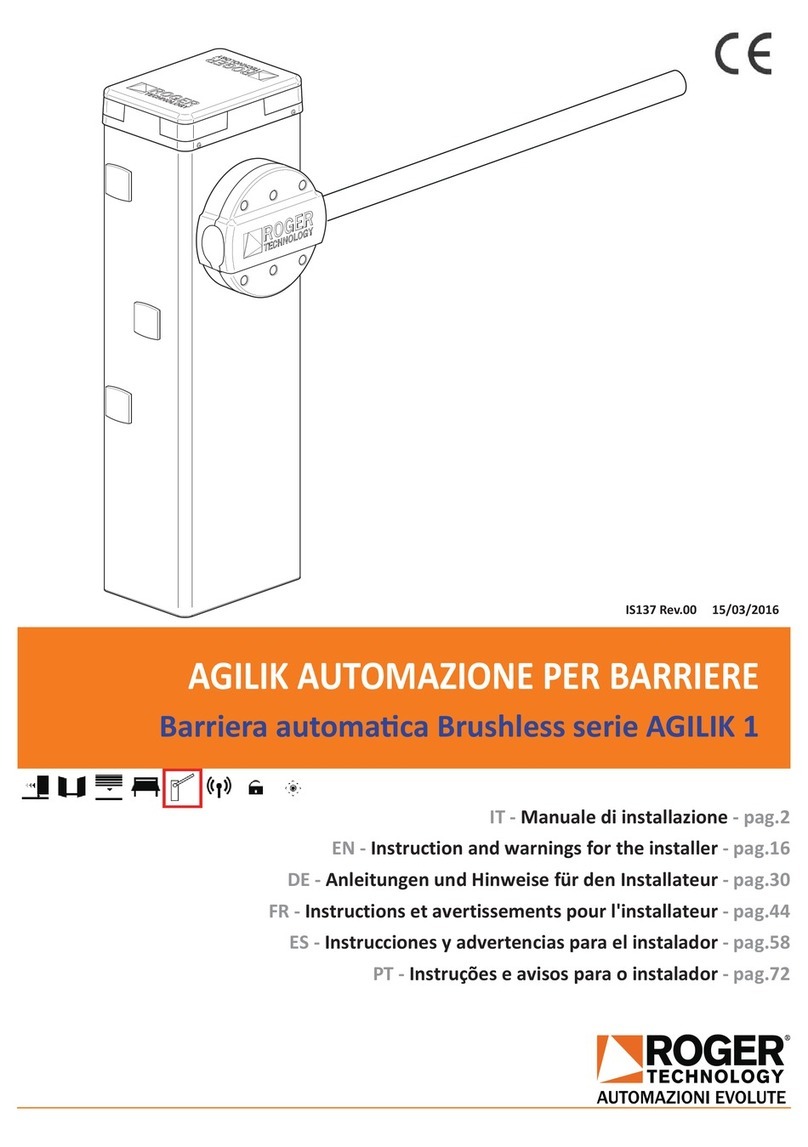
Roger Technology
Roger Technology AGILIK 1 Series Instruction and warnings for the installer
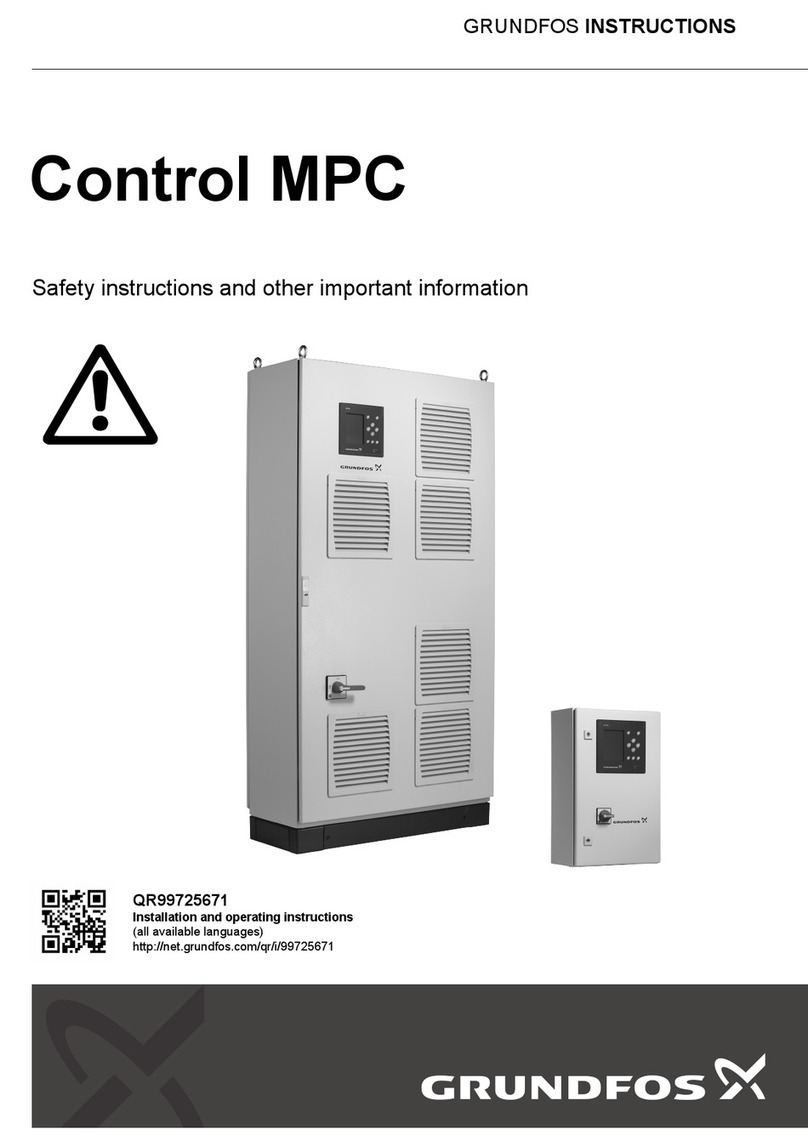
Grundfos
Grundfos CONTROL MPC Safety instructions and other important information
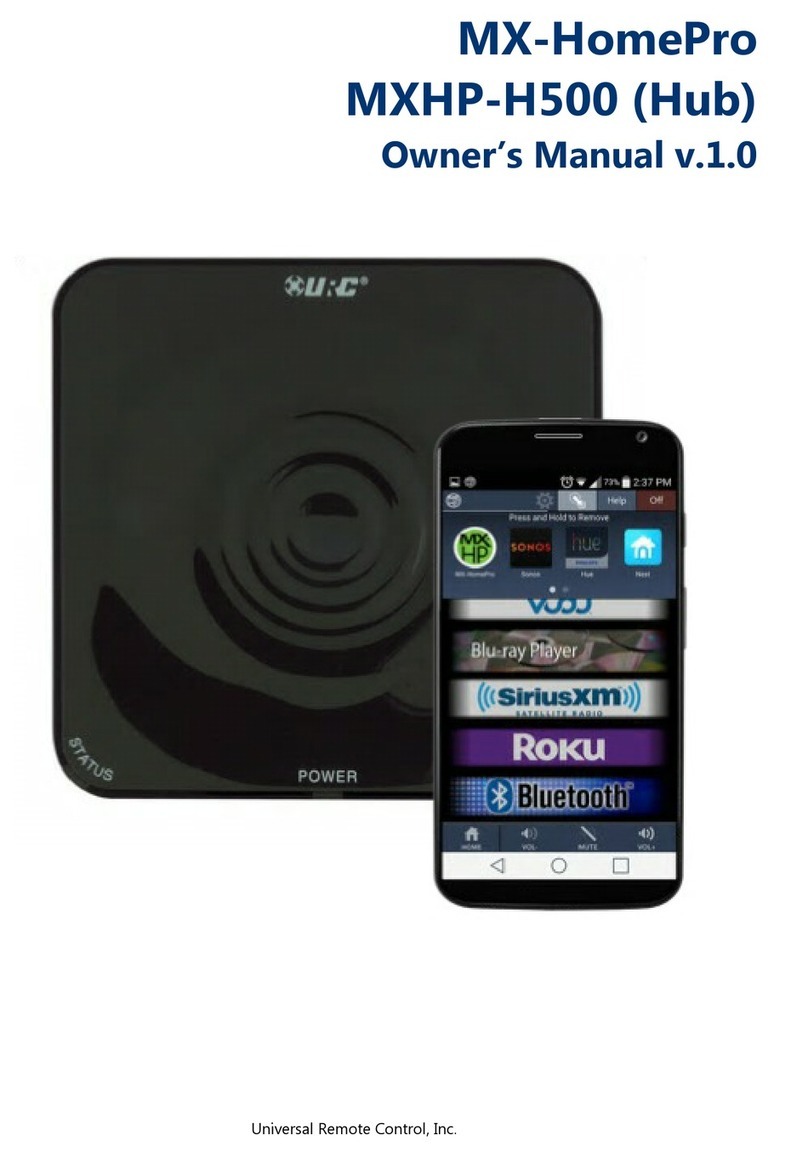
URC
URC MX-HomePro owner's manual